热处理原理与工艺第二章教案
金属热处理原理与工艺课件

奥氏体等温形成动力学的分析 (1)奥氏体的形核率 (2)奥氏体晶体的长大速度G 影响奥氏体形成速度的因素 (1)温度 (2)碳含量 (3)原始组织的影响 (4)合金元素的影响
金属热处理原理与工艺课 件
连续加热时奥氏体的形成 实验表明连续加热时奥氏体形成的基本过程和等
温转变相似,也是由奥氏体的形核、长大、残留碳化 物溶解和奥氏体成分均匀化四个阶段组成。
金属热处理原理与工艺课 件
退火
正火
普通(整体)热处理
淬火 回火
热
固溶时效
处
感应加热表面淬火
理
表面淬火 火焰加热表面淬火
激光加热表面淬火等
表面热处理
渗碳
表面化学热处理
渗氮 碳氮共渗
金属热处理原理与工艺课 件
渗金属等
钢的分类方法 按化学成分分类 碳素钢按含碳量多少可分为 合金钢按合金元素的含量又可分为 合金钢按合金元素的种类可分为 ……
A形核
AA形晶核成包括四个剩阶余段:
长大
Fe3C溶解
A 均匀化
未溶Fe3C
未溶Fe3C
金属热处理原理与工艺课 件
奥氏体形成动力学可分为等温形成动力学和连续加热 形成动力学。 奥氏体等温形成动力学 等温形成动力学即在一定温度下的转变量和转变时间 的关系(即在一定温度下的转变速度)。
金属热处理原理与工艺课 件
金属热处理原理与工艺课 件
奥氏体晶粒度 晶粒度:是表示晶粒大小的一种尺度。 1、起始晶粒度: 2、实际晶粒度: 3、本质晶粒度:
金属热处理原理与工艺课 件
影响奥氏体晶粒度的因素 1、加热温度和保温时间 2、加热速度 3、钢的含碳量的影响 4、脱氧剂及合金元素
金属热处理原理与工艺课 件
热处理原理和工艺
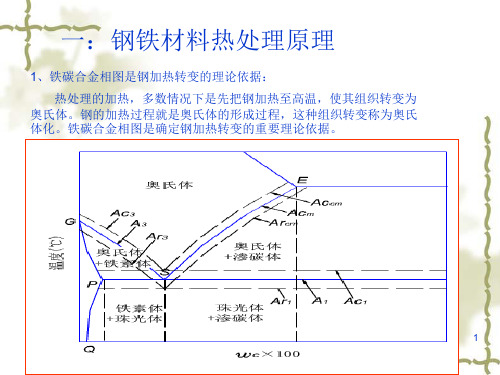
上贝氏体
下贝氏体
11
过冷奥氏体连续冷却转变曲线(CCT曲线)
700 A1
600
温PS K Pf
(3)影响淬透性的 因素:化学成分, 奥氏体化条件
(4)选材与淬透性
15
回火(与淬火配合)
目的:
a、降低脆性,减少或消除内应力防止工件变形和开裂。 b、 获得所需的力学性能。 c、 稳定工件的尺寸。 d、 获得马氏体。
回火的类型
低温回火:
温度:150—200°C ;得到的组织:M回;内应力和脆性降低,保持了
一:钢铁材料热处理原理
1、铁碳合金相图是钢加热转变的理论依据: 热处理的加热,多数情况下是先把钢加热至高温,使其组织转变为
奥氏体。钢的加热过程就是奥氏体的形成过程,这种组织转变称为奥氏 体化。铁碳合金相图是确定钢加热转变的重要理论依据。
1
2、奥氏体化过程
共析钢加热到727°C(A1)以上,珠光体转变成奥氏体,经历了奥 氏体形核、长大、残余渗碳体的溶解和奥氏体成分均匀化四个阶段。如 下图所示:
CCT
P P+M+A'
300 Ms
200 A→A1 VK' VK
TTT M+A'
100
23 4 56
1 10 10 10 10 10 10
时间(s)
1、CCT曲线及分析
2、CCT曲线与C曲线的比较
a、位置关系 b、转化的成分 c、得到的组织
3、过冷奥氏体转变曲线的应用
热处理课程教案(模板)

课程教案
课程名:金属热处理工艺学
专业:金属材料
班号:B100210 B100211
主讲教师:侯丽丽
学年:2013-2014
学期:第一学期
系主பைடு நூலகம்(教研室主任):
2013年8月23日
共5页
第1章金属的加热
项目
内容
教学目的
让学生了解加热时的物理过程,掌握加热介质的选择
本章教学重点
钢的退火、正火工艺
本章教学难点
退火、正火工艺及缺陷分析
本章讲授技巧注意事项
结合图形及相关实验进行退火、正火工艺在实际生产中的选用原则。
备注
第2页共5页
第3章钢的淬火及回火
项目
内容
教学目的
熟练掌握钢的淬火、回火工艺的确定原则,并了解生产中具体制定热处理工艺的影响因素。
本章教学重点
淬火、回火工艺的确定
本章教学难点
不同介质中加热
本章教学难点
加热介质的选择
本章讲授技巧注意事项
加热过程中的氧化与脱碳内容的讲授,可用实际生产中的脱碳现象进行分析
备注
第1页共5页
第2章钢的退火正火
项目
内容
教学目的
熟练掌握钢的退火、正火工艺,掌握钢退火、正火后的组织和性能,了解退火、正火易出现的缺陷,并能分析其原因和防止方法。
本章教学重点
淬火、回火工艺的确定
本章讲授技巧注意事项
淬火温度的确定原则与实际生产中灵活调整原则。
备注
第3页共5页
第4章钢的表面处理
项目
内容
教学目的
了解常用的表面淬火方法,掌握表面淬火的组织与性能及表面淬火工艺的应用范围。
热处理 教案
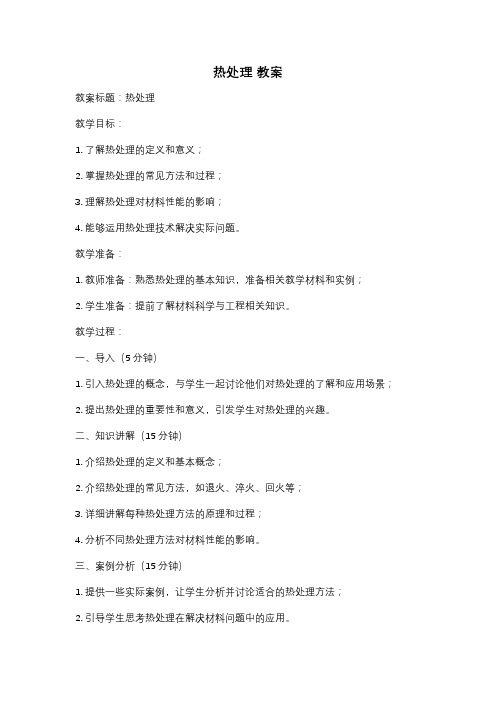
热处理教案教案标题:热处理教学目标:1. 了解热处理的定义和意义;2. 掌握热处理的常见方法和过程;3. 理解热处理对材料性能的影响;4. 能够运用热处理技术解决实际问题。
教学准备:1. 教师准备:熟悉热处理的基本知识,准备相关教学材料和实例;2. 学生准备:提前了解材料科学与工程相关知识。
教学过程:一、导入(5分钟)1. 引入热处理的概念,与学生一起讨论他们对热处理的了解和应用场景;2. 提出热处理的重要性和意义,引发学生对热处理的兴趣。
二、知识讲解(15分钟)1. 介绍热处理的定义和基本概念;2. 介绍热处理的常见方法,如退火、淬火、回火等;3. 详细讲解每种热处理方法的原理和过程;4. 分析不同热处理方法对材料性能的影响。
三、案例分析(15分钟)1. 提供一些实际案例,让学生分析并讨论适合的热处理方法;2. 引导学生思考热处理在解决材料问题中的应用。
四、实验演示(20分钟)1. 进行一个简单的热处理实验演示,展示不同热处理方法对材料性能的影响;2. 引导学生观察实验现象,分析实验结果。
五、讨论与总结(10分钟)1. 学生交流观察到的实验现象和结果;2. 总结不同热处理方法的优缺点;3. 引导学生思考如何选择合适的热处理方法解决材料问题。
六、作业布置(5分钟)1. 布置相关的课后作业,如阅读相关文献、解答问题等;2. 提醒学生按时完成作业并准备下节课的讨论。
教学反思:教案中通过导入、知识讲解、案例分析、实验演示等多种教学方法,使学生全面了解热处理的定义、方法和影响,培养学生运用热处理技术解决问题的能力。
同时,通过实验演示和讨论,增强了学生的实践操作和团队合作能力。
在教学过程中,教师应充分引导学生思考和讨论,促进他们的自主学习和思维发展。
热处理原理与工艺课程设计

* * 大学热处理原理与工艺课程设计题目: 50Si2Mn弹簧钢的热处理工艺设计院(系):机械工程学院专业班级:**学号:*******学生姓名:**指导教师:**起止时间:2014-12-15至2014-12-19课程设计任务及评语目录一、概述---------------------------------------------------------11.课程设计的目的--------------------------------------------------12.课程设计的任务--------------------------------------------------13.课程设计的题目--------------------------------------------------14.课程设计的内容及步骤--------------------------------------------1二、热处理工艺课程设计的内容及要求--------------------------------11、零件的技术要求及选材-------------------------------------------12、化学特点和性能-------------------------------------------------23、制定热处理工艺路线---------------------------------------------34、工艺参数-------------------------------------------------------35、热处理工艺曲线-------------------------------------------------76、分析各热处理工序中材料的组织和性能-----------------------------77、缺陷分析-------------------------------------------------------88、选择热处理设备-------------------------------------------------109、测温仪器和温度控制方式-----------------------------------------10三、收获和体会----------------------------------------------------11四、参考文献------------------------------------------------------11第一部分概述1、课程设计的目的热处理工艺课程设计是高等学校金属材料工程专业一次专业课设计练习,是热处理原理与工艺课程的最后一个教学环节。
热处理原理和工艺培训课件
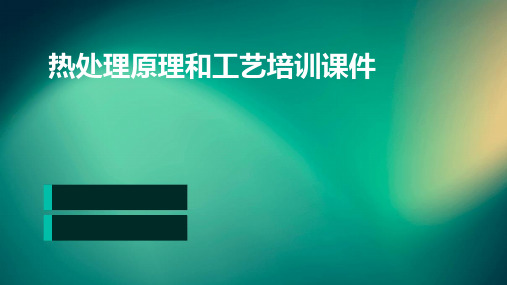
刀具热处理
刀具热处理
01
刀具的热处理可以提高其硬度和耐磨性,从而提高切削效率和
刀具寿命。
高速钢刀具
02
高速钢刀具在热处理后具有较高的硬度和良好的耐磨性,适用
于加工硬度较高的材料。
硬质合金刀具
03
硬质合金刀具的热处理可以进一步提高其硬度和耐热性,适用
于高速切削和加工高温合金等难加工材料。
模具热处理
模具热处理
模具的热处理可以提高其硬度和耐磨性,延长模具使用寿命,保 证产品质量。
冷冲模具
冷冲模具需要进行表面强化处理,以提高其耐磨性和抗冲击性。
塑料模具
塑料模具需要进行适当的热处理,以提高其抗腐蚀性和耐热性。
精密零件热处理
精密零件热处理
精密零件的热处理可以提高其尺寸稳定性和机械性能,保证产品 质量和精度。
热处理质量检测与评估
硬度检测
采用硬度计对热处理后 的产品进行硬度检测,
以评估热处理效果。
金相组织分析
通过金相显微镜观察热 处理后的产品组织结构, 分析热处理对组织的影
响。
力学性能测试
对热处理后的产品进行 拉伸、冲击、弯曲等力 学性能测试,以评估其
机械性能。
不合格品处理
对不合格的热处理产品 进行追溯和处理,分析 原因并采取相应的纠正
工艺中具有重要意义。
03
应力与应变原理
金属材料在加热和冷却过程中会产生热应力、组织应力和相变应力等。
这些应力会导致材料变形和开裂。因此,在热处理过程中需要采取措施
控制应力与应变,以获得良好的热处理效果。
02 热处理工艺
预处理工艺
01
02
03
清理
去除工件表面的油污、锈 迹和氧化皮,确保工件表 面干净,以便进行后续的 热处理工艺。
《热处理原理及工艺》课程教学大纲

《热处理原理及工艺》课程教学大纲1.课程编号:1000951082.课程名称:热处理原理及工艺3.高等教育层次:本科4.课程在培养方案中的地位:课程性质:必修对应于材料科学与工程专业;属于:BZ专业课程基本模块5.开课学年及学期本科三年级第2学期6.先修课程(a必须先修且考试通过的课程,b必须先修过的课程,c建议先修的课程)a材料科学基础,b 力学性能,c金属材料学7.课程总学分:4,总学时:64;8.课程教学形式:0普通课程9.课程教学目标与教学效果评价10.课程教学目标与所支撑的毕业要求对应关系11.教学内容、学时分配、与进度安排12.考核与成绩评定:平时成绩、期末考试在总成绩中的比例,平时成绩的记录方法。
考核方式:闭卷考试成绩构成:平时考查:原则上4次作业(3次作业+1次报告),每次2.5分,(课堂提问、研讨可适度奖励加分,每次1分,不能超过此项上限)共10分;随堂测验(2次,每次5分,共10分;实验表现与实验报告成绩:10分;期末考试:70分。
13.教材,参考书:教科书:陆兴热处理工程基础[M]. 北京:机械工业出版社,2007参考书:[1]赵乃勤热处理原理与工艺[M]. 北京:机械工业出版社,2012[2]《热处理手册》1:工艺基础. 北京:机械工业出版社,2012[3]《热处理手册》2:零件热处理. 北京:机械工业出版社,2012[4]《热处理手册》3:热处理设备和工辅材料. 北京:机械工业出版社,2012[5]《热处理手册》4:热处理质量控制和检验. 北京:机械工业出版社,201214.大纲说明:本课程的学习可以培养学生运用所学数理知识和方法认识和分析相变原理、热处理工艺方法的能力和创新意识,提高学生对热处理工艺、组织性能关系的认识,为他们走上工作岗位从事相关工作奠定基础。
通过课程对本学科相变原理与热处理技术相关的新理论、新方法的介绍,还可以使学生了解本学科的最新发展动态和技术前沿。
热处理工艺教案

第 1 次课 2 学时授课时间第9 周教案完成时间第1 周
第 2 次课 2 学时授课时间第9 周教案完成时间第 1 周
第 3 次课 2 学时授课时间第10 周教案完成时间第 1 周
第 4 次课 2 学时授课时间第10 周教案完成时间第 1 周
第 5 次课 2 学时授课时间第11 周教案完成时间第 1 周
第 6 次课 2 学时授课时间第11 周教案完成时间第 1 周
第7 次课 2 学时授课时间第12 周教案完成时间第 1 周
第8 次课 2 学时授课时间第12周教案完成时间第1周
第9 次课 3 学时授课时间第13周教案完成时间第1周
第 10
次课 2 学时 授课时间 第13周 教案完成时间 第1周
第11 次课 2 学时授课时间第14周教案完成时间第1周
第12 次课 2 学时授课时间第14周教案完成时间第1周
第13 次课 2 学时授课时间第14 周教案完成时间 1。
热处理原理与工艺 教学课件 赵乃勤 第2章 钢在高温加热时的奥氏体转变

图2-5 碳原子在γ-Fe中可能的间隙位置a)
b)
2.1.2 奥氏体晶体结构
图2-6 奥氏体的点阵常数与碳含量 (包括过饱和含量)
2.1.3 奥氏体的性能
奥氏体是碳钢中的高温稳定相,当加入适量的 合金元素时,可以使奥氏体在室温成为稳定相。 因此,奥氏体可以是钢在使用时的一种组织状 态,在奥氏体状态使用的钢称为奥氏体钢。
2.奥氏体化温度和奥氏体化后的停留温度
非平衡组织是通过淬火得到的,淬火加热时的 奥氏体化温度越高,碳化物溶解得就越充分, 碳及合金元素分布就越均匀,奥氏体晶粒越粗 大,奥氏体晶界上的偏聚也就越少。
3.加热速度
图2-33
4.原始组织
•原始非平衡组织包括马氏体、贝氏体等淬火组 织和回火马氏体等不充分回火组织。这些不同 的组织以相同的加热速度加热到转变开始温度 时,由于加热过程中的转变程度不同,奥氏体 转变开始时的组织状态也不同,形成的奥氏体 组织有较大差异。
2.1.1 奥氏体定义
图2-1 Fe-F C合金平衡相图
2.1.1 奥氏体定义
图2-2 合金元素对Fe-F C a) 铬的影响 b) 锰的影响
2.1.1 奥氏体定义
图2-3 304
2.1.1 奥氏体定义
图2-4 奥氏体的光学显微组织(NF709奥氏体不锈钢,10%草酸
2.1.2 奥氏体晶体结构
(1) 对碳在奥氏体中扩散系数的影响 强碳化物形成元素如Cr、Mo、W、V等,降低 碳原子在奥氏体中的扩散系数,因而显著推迟珠光体转变为奥氏体的过程;非碳化物 形成元素Co、Ni增大碳原子在奥氏体中的扩散系数,因而增大奥氏体的形成速度;Si、 Al对扩散系数的影响较小,对奥氏体形成速度没有太大的影响。 (2) 对碳化物溶解度的影响 合金元素与碳形成的碳化物向奥氏体中溶解的难易程度 不同也会影响奥氏体的形成速度。 (3) 对相变临界点的影响 合金元素改变临界点A1、A3、Acm的位置,并使它们成为 一个温度范围。 (4) 对原始组织的影响 合金元素通过对原始组织的影响来影响奥氏体的形成速度。
热处理基本知识及工艺原理学习教案

2021/10/1
25
第24页/共106页
第二十五页,编辑于星期二:三点 十分。
2
钢的热处理工艺
(3)均匀化退火
工艺规范:
特点:(1)高温、长时间 (2)需再经重结晶工艺(完全退火或正火)以细化晶粒
目的:消除或减轻偏析、带状组织等 适用范围:合金钢锭、大型铸钢件
2021/10/1
第25页/共106页
A1
2021/10/1
第10页/共106页
11 第十一页,编辑于星期二:三点 十分。
1
金属学与热处理原理
(1)过冷奥氏体等温转变图
(C曲线或TTT曲线)
2021/10/1
共析钢C曲线
第11页/共106页
12
第十二页,编辑于星期二:三点 十分。
1
金属学与热处理原理
2021/10/1
亚共析钢和过共析钢的C曲线
2 目的:① 细化晶粒,消除铸锻焊件组织缺陷; ② 提高低碳钢硬度,改善切削加工性能;
③ 消除高碳钢网状二次渗碳体,为球化退火作组织准备; ④ 型材或大型复杂铸钢件的最终热处理
2021/10/1
第30页/共106页
31 第三十一页,编辑于星期二:三点 十分。
2
钢的热处理工艺
3 正退火区别
区别
正火
退火
15
第十五页,编辑于星期二:三点 十分。
1
金属学与热处理原理
(3)几种转变的特点
转变温度
珠光体转变
高温
(Ar1-550℃)
扩散性 Fe、C、Me扩散
组织(图片见下页)
珠光体 (α+Fe3C)
贝氏 体转 变
上贝 (550-350℃) C扩散; Fe、 Me不扩散 氏体
《热处理原理及工艺》课件
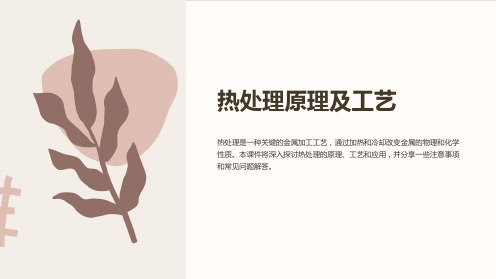
热处理的基本原理
热处理基于材料的相变和晶体结构变化。通过控制加热温度、保温时间和冷 却速率,可以调控晶粒尺寸、相组成和硬度。
热处理工艺流程
热处理工艺包括加热、保温和冷却阶段。常见的工艺流程包括退火、淬火、 回火和表面处理。
热处理常用的设备和工具
热处理设备包括炉子、加热器、冷却介质和测温仪器。常用的工具有夹具、 夹具和渗碳等。每种方法具有不同的应用场景和效果。
热处理的应用范围和优势
热处理广泛应用于航空航天、汽车制造、机械加工等领域。它能够提高材料 的强度、硬度、耐磨性和耐腐蚀性。
热处理的注意事项和常见问题解答
热处理过程中需要注意温度控制、冷却方式和工艺参数的选择。课件中还将解答常见问题,帮助您更好地理解 和应用热处理技术。
热处理原理及工艺
热处理是一种关键的金属加工工艺,通过加热和冷却改变金属的物理和化学 性质。本课件将深入探讨热处理的原理、工艺和应用,并分享一些注意事项 和常见问题解答。
热处理的定义和作用
热处理是通过加热和冷却控制材料的结构和性能,从而改变其力学性质、导 热性、电性能等。它广泛应用于金属加工、材料改良和工业制造。
热处理原理与工艺

• 1.热处理的 工艺过程 • 热处理三步 曲:“加热、 保温、冷却”。
T℃
保温 A1
加热
冷却
Time
1. 钢在加热的组织转变
• 一、目的 • 加热至临界点以上: 使钢的组织A 化,获得A,称为A化。 • 加热至临界点以下: 没有组织转变, 消除应力等。 • 二、A的形成 • 当加热到临界点以上时,发生重新结 晶(包括原子的扩散和晶格的改组)。
合金元素不扩 散 主要在连续冷 却过程中进行, 相变不能进行 到底,有残余 奥氏体存在。
相变可在恒温下充分 进行,相变完成的程 度与转变温度有关, 温度越低,转变越不 充分,有残余奥氏体
3 热处理工艺
• 一、退火(Annealing) • 将钢加热到临界点以上或以下,保温 一定时间后缓慢冷却的一种操作,称 为~。 实质:使A 发生P转变
扩散性
Fe 、C原子都扩散
Fe不扩散 、C原子扩 散
两相组织 A─→(F+Fe3C )(>350℃) A─→(F+FexC )(<350℃) 合金元素不扩散
Fe 、C原子都 不扩散
单相组织 A─→F(过 饱和C)
组成相
两相组织 A─→(F+Fe 3C)
合金元素的分 布 相变的完全性
合金元素扩散重新 分布 相变在衡温下进行 到底
温,使介质中的活性原子渗入零件表面层的 一种热处理工艺。
• 目的:通过改变表面层的化学成分和显 微组织,来提高表面的性能(机械和理 化性能),实际上使同一零件由两种成 分的材料制成。 • 与表面淬火的区别:既有组织转变,又 有成分改变,而后者只有组织转变。 • (一)渗碳(carburizing)
热处理原理与工艺第二章教案

第二章珠光体转变共析碳钢加热奥氏体化后,在共析温度以下冷却时,奥氏体可发生三种基本的转变:珠光体转变、贝氏体转变和马氏体转变。
这三种转变得到的组织中,马氏体硬度最高,贝氏体次高,珠光体最低。
图2-1是实测的共析钢奥氏体等温冷却转变曲线的示意图(也称等温C曲线),图中三条线分别表示转变开始线、转变终了线和马氏体转变开始温度。
奥氏体在A以下不同温度等温冷却时,将发生以下转变:A1~550C珠光体转变,550C ~Ms之间为贝氏体转变。
在Ms以下则发生马氏体转变。
珠光体区又分为粗珠光体P、细珠光体S (也称索氏体)、极细珠光体T (也称托氏体);贝氏体区分为上贝氏体B上和下贝氏体B下。
如将共析钢工件冷至650 C并等温,当等温时间与珠光体转变开始曲线相交时,奥氏体将开始发生珠光体转变,转变为细珠光体S;此后,随等温时间延长,奥氏体不断减少、S不断增多,当等温至与珠光体转变终了曲线相交时,奥氏体全部转变为So. 丄一iLLI IIIQ3 2 8 50 2 B 30 2 £ |5s nun h时间图2-1共析碳钢等温转变曲线示意图本章主要介绍珠光体组织形态、形成过程、影响因素及力学性能等。
第一节珠光体组织形态和力学性能一、珠光体组织形态当含碳量为0.77%的奥氏体冷却到A i温度以下时,发生共析转变,分解为片状的铁素体和渗碳体交替重叠组成的共析组织(见图2-2)。
这种组织经浸蚀后,在光学显微镜下观察,其金相形态酷似珍珠母产生的光学效果,故而得名珠光体。
珠光体组织中铁素体和渗碳体的体积比约为7:1,故铁素体片总是比渗碳体厚。
图2-2 共析碳钢片状珠光体500X珠光体的金相组织中有许多片层排列位向大致相同的小区域(见图2-3 ),称为珠光体领域或珠光体团。
在一个原奥氏体晶粒内,可形成几个位向不同的珠光体团。
相邻两渗碳体(或铁素体)片中心之间的距离虫称珠光体片层间距(见图2-3a所示)。
片层间距S o是影响珠光体力学性能的一个重要参数。
热处理原理与工艺

学习的意义
✓ 系统地掌握金属热处理的基本原理和工艺方法 ;
✓ 加深对热处理规律的认识,了解热处理主要设备; ✓ 培养学生应用所学知识去分析和解决实际问题的
能力。
学习的方法
理论联系实际
参考书:
1. 田荣璋. 金属热处理. 冶金工业出版社,1985年; 2. 王希琳. 金属材料及热处理. 水利电力出版社,
N • N expG k T Q
N ---- 单位体积母相中的原子数 ν---- 原子振动频率 ∆G* ---- 形核功 Q ---- 原子扩散激活能
(14)
➢ 固态相变较难均匀形核
1.3.2 非均匀形核 晶体缺陷储存的能量可使形核功降低,促进形核
∆G = V ∆Gv + S σ+ εV -∆Gd
成分 工艺 性能
材料的三要素
1.3 热处理的发展概况
民间技艺阶段 实验技术科学阶段
西汉时代已有淬火处理的钢 剑(辽宁三道壕出土)
理论科学阶段 炼钢赤刀,用之切玉如泥焉
明代宋应星《天工开物》 十九世纪后期,钢加热/冷却时,内部组织变化— 性能变化的内部原因
英国 Robert Austen Fe-C相图 德国 Adoph Martens 金相显微镜
austenite → martensite 马氏体相变理论 → 新的强韧化工艺
1.4 本课程的主要内容,学习的意义,目的,方法
主要内容
➢ 金属固态相变基础 ➢ 钢中奥氏体的形成 ➢ 珠光体,马氏体,贝氏体转变 ➢ 钢的过冷奥氏体转变图 ➢ 钢的回火转变 ➢ 钢的退火,正火,淬火与回火 ➢ 钢的化学热处理 ➢ 加热设备 ➢ 冷却设备
设形成的新相晶核为球形
对于 r 求导:
d(G) 0 dr
《金属热处理原理与工艺》课程设计

2.1、什么是热处理所谓钢的热处理,就是对于固态范围内的钢,给以不同的加热、保温和冷却,以改变它的性能的一种工艺。
钢本身是一种铁炭合金,在固态范围内,随着加温和冷却速度的变化,不同含炭量的钢,其金相组织发生不同的变化。
不同金相组织的钢具有不同的性能。
因此利用不同的加热温度和冷却速度来控制和改变钢的组织结构,便可得到不同性能的钢。
例如,含炭量百分之0.8的钢称为共析钢,在723摄氏度以上十时为奥氏体,如果将它以缓慢的速度冷却下来,它便转变成为珠光体。
但如果用很快的速度把它冷却下来,则奥氏体转变成为马氏体。
马氏体和珠光体在组织上决然不同,它们的性能差别悬殊,如马氏体具有比珠光体高的多的硬度和耐磨性。
因此,钢的热处理在钢的使用和加工中,占有十分重要的地位。
2.2、热处理的作用机床、汽车、摩托车、火车、矿山、石油、化工、航空、航天等用的大量零部件需要通过热处理工艺改善其性能。
拒初步统计,在机床制造中,约60%~70%的零件要经过热处理,在汽车、拖拉机制造中,需要热处理的零件多达70%~80%,而工模具及滚动轴承,则要100%进行热处理。
总之,凡重要的零件都必须进行适当的热处理才能使用。
材料的热处理通常指的是将材料加热到相变温度以上发生相变,再施以冷却再发生相变的工艺过程。
通过这个相变与再相变,材料的内部组织发生了变化,因而性能变化。
例如碳素工具钢T8在市面上购回的经球化退火的材料其硬度仅为20HRC,作为工具需经淬火并低温回火使硬度提高到60~63HRC,这是因为内部组织由淬火之前的粒状珠光体转变为淬火加低温回火后的回火马氏体。
同一种材料热处理工艺不一样其性能差别很大。
热处理工艺(或制度)选择要根据材料的成份,材料内部组织的变化依赖于材料热处理及其它热加工工艺,材料性能的变化又取决于材料的内部组织变化,材料成份-加工工艺-组织结构-材料性能这四者相互依成的关系贯穿在材料加工的全过程之中。
2.3、热处理的基本要素热处理工艺中有三大基本要素:加热、保温、冷却。
热处理工艺2-绪论

各种组织的机械性能
• • • • • • 奥氏体:塑性好,强度低,滑移系多。 铁素体:塑性好,强度低。 珠光体:塑性好但低于铁素体,强度低。 上贝氏体:强度中等,韧性差。 下贝氏体:强度中等,韧性好。 马氏体:板条状具有高强度和一定韧性,片状具 有高硬度和低韧性。 • 回火马氏体:硬度最高。 • 回火屈氏体:弹性极限最好。 • 回火索氏体:最佳的强度和韧性组合。
• 决定材料能否加工成型和最终性能 • 科普知识需要:市场上销售的钢材一般都标记有 最终的热处理状态——交货状态。
九、《热处理原理及工艺》课程的 性质、任务以及目的
• 性质:《热处理原理及工艺》是金属材料工程专业的重要 专业课。通过这门课程的学习,为将来从事热处理研究与 生产工作打下必要的理论与技术基础。 • 本课程的任务:是阐明黑色金属和有色金属热处理的基本 理论、介绍各种热处理工艺方法,并介绍一些热处理设备。 • 本课程的目的:是使大家通过学习,能够根据不同的金属 材料、不同零部件的工作条件或者加工需要,合理选择、 制定合适的热处理工艺,并通过相应的热处理设备进行处 理,从而获得所需要的性能。
φ500
φ10
工件比炉膛长不超过1/3
工件与炉膛长度刚好相等
对铸件进行热处理
铸件温度:700°c 热处理工艺要求:900°c,恒温3小时;在炉中随炉冷却10小时到300°c出
炉。
请思考:怎样使用炉子最节约能源?
二、 什么叫热处理?
热处理 冷处理 都涉及到通过温度的改变来处理 什么东西的过程。 [金属材料的热处理工艺]: • 将金属材料在一定的介质中,加热到一定 的温度,保温一段时间,然后以不同的方 式冷却以使性能改变的一种热加工工艺。
• 3.从汉代开始,我国的热处理技术已经有文字记 载,内容包括一般淬火技术、淬火介质以及渗碳 工艺等等,几乎涉及热处理技术的各个方面。例 如《史记、天官书》当中记载有“火与水合为火 卒 ”、《汉书、王褒传》当中记载有“……清水 淬其锋”,——二者都记载有淬火工艺。 在《晋 书》当中所记载的“大夏龙雀”的兵器,与西汉 中期的刀剑相比,其组织均匀、含碳量适中(均 为0.65~0.7%), • 经淬火,它的刀口锋利,表面经过氧化处理,抗 腐蚀性能良好。
《金属热处理原理与工艺》课程设计

《金属热处理原理与工艺》课程设计材料:结构钢40Mn2B主要特性这是一种中碳调质锰钢,钢的强度、塑性和耐磨性都较高,可切削性及热处理工艺性能亦好,在油中临界淬透直径达8.5~23mm,在水中临界淬透直径达20~42mm;但存在回火脆性和过热敏感性,而且淬火时易于开裂。
此钢有白点敏感性,冷变形塑性不高,焊接性差,需要预热到100~425℃后方可焊接。
应用举例一般在调质状态下使用,可用于制造重负荷条件下工作的零件,如轴、曲轴、车轴、活塞杆、蜗杆、杠杆、连杆、有负荷的螺栓、螺钉、加固环、弹簧以及其它调质件。
一般用于直径小于50mm的小截面重要零件时,这种钢的静强度及疲劳性能均与40Cr钢相当,故可作40Cr的代用钢。
4-1材料分析40Mn2B钢是一种合金钢,其中各元素含量为碳 C :0.36~0.44%硅 Si:0.17~0.37%锰 Mn:1.50~2.49%硼 B:0.0005%~0.0030%硫 S :≤0.030%磷 P :≤0.030%铬 Cr:0.80~1.10%镍 Ni:≤0.35%钒 V:0.10~0.20%。
1、Si:常用的脱氧剂,有固溶强化作用,提高电阻率,降低磁滞损耗,改善磁导率,提高淬透性,抗回火性,对改善综合力学性能有利,提高弹性极限,增强自然条件下的耐蚀性。
含量叫干事,降低焊接性,且易导致冷脆。
中碳钢和高碳钢易于在回火时产生石墨化。
2、Mn:降低钢的下界临点,增加奥氏体冷却时的过冷度,细化珠光体组织以其改善其力学性能,为低合金钢的重要合金元素,能明显提高钢的淬透性,但有增加晶体粗化和回火脆性的不利影响。
3、B:微量硼能提高钢的淬透性,但随钢种含碳量的增加,淬透性的提高逐渐减弱以致完全消失。
钢中加入微量的硼就可改善钢的致密性和热轧性能,提高强度。
具体有:(1(1)提高淬透性的能力极强。
0.0010%~0.0030%硼的作用可分别相当于0.6%锰、0.7%铬、0.5%钼和1.5%镍,因此其提高淬透性的能力为上述合金元素的几百倍乃至上千倍,故此只需极少量硼即可节约大量的贵重合金元素。
- 1、下载文档前请自行甄别文档内容的完整性,平台不提供额外的编辑、内容补充、找答案等附加服务。
- 2、"仅部分预览"的文档,不可在线预览部分如存在完整性等问题,可反馈申请退款(可完整预览的文档不适用该条件!)。
- 3、如文档侵犯您的权益,请联系客服反馈,我们会尽快为您处理(人工客服工作时间:9:00-18:30)。
第二章珠光体转变共析碳钢加热奥氏体化后,在共析温度以下冷却时,奥氏体可发生三种基本的转变:珠光体转变、贝氏体转变和马氏体转变。
这三种转变得到的组织中,马氏体硬度最高,贝氏体次高,珠光体最低。
图2-1是实测的共析钢奥氏体等温冷却转变曲线的示意图(也称等温C曲线),图中三条线分别表示转变开始线、转变终了线和马氏体转变开始温度。
奥氏体在A1以下不同温度等温冷却时,将发生以下转变:A1~550℃珠光体转变,550℃~Ms之间为贝氏体转变。
在Ms以下则发生马氏体转变。
珠光体区又分为粗珠光体P、细珠光体 S (也称索氏体)、极细珠光体T (也称托氏体);贝氏体区分为上贝氏体B上和下贝氏体B下。
如将共析钢工件冷至650℃并等温,当等温时间与珠光体转变开始曲线相交时,奥氏体将开始发生珠光体转变,转变为细珠光体S;此后,随等温时间延长,奥氏体不断减少、S不断增多,当等温至与珠光体转变终了曲线相交时,奥氏体全部转变为S。
图2-1 共析碳钢等温转变曲线示意图本章主要介绍珠光体组织形态、形成过程、影响因素及力学性能等。
第一节珠光体组织形态和力学性能一、珠光体组织形态当含碳量为0.77%的奥氏体冷却到A1温度以下时,发生共析转变,分解为片状的铁素体和渗碳体交替重叠组成的共析组织(见图2-2)。
这种组织经浸蚀后,在光学显微镜下观察,其金相形态酷似珍珠母产生的光学效果,故而得名珠光体。
珠光体组织中铁素体和渗碳体的体积比约为7:1,故铁素体片总是比渗碳体厚。
图2-2 共析碳钢片状珠光体 500X珠光体的金相组织中有许多片层排列位向大致相同的小区域(见图2-3),称为珠光体领域或珠光体团。
在一个原奥氏体晶粒内,可形成几个位向不同的珠光体团。
相邻两渗碳体(或铁素体)片中心之间的距离S0,称珠光体片层间距(见图2-3a所示)。
片层间距S0是影响珠光体力学性能的一个重要参数。
实验表明,珠光体团的尺寸随原奥氏体晶粒尺寸减小而减小。
图2-3 珠光体片层间距和珠光体团示意图a)珠光体片层间距S。
b)珠光体团通常所说的珠光体组织粗细,是指组织中渗碳体和铁素体片层厚薄程度不同,也就是珠光体片层间距大小的不同。
如前已述及的组织中的珠光体、索氏体和托氏体组织,实质上都是渗碳体和铁素体交替重叠组成的片状组织,只是片层间距大小不同而已(见表2-1)。
由表中数据可以看出,转变温度愈低,片间距愈小(即珠光体组织愈细),硬度愈高。
较高温度下,形成的珠光体组织,片间距较大,在通常光学显微镜下观察,就能清楚分辨片层组织形态。
在较低温度形成的索氏体组织,在显微镜放大至600倍以上,才能分辨其片层组织形态。
如果转变温度更低,形成托氏体组织,其片层组织更细小,即使在高倍的光学显微镜下也分辨不出其片层形态,只能看到其总体是一团黑,必须用高倍率的电子显微镜才能分辨出极薄的渗碳体和铁素体片。
在工业用钢中,还可见到另一种形态的珠光体组织,在铁素体上均匀分布着球粒状碳化物,称为粒状珠光体,见图2-4。
粒状珠光体一般是经球化退火后获得的组织。
球化退火工艺不同,获得渗碳体球粒的尺寸、形状和分布不同。
珠光体的形态除片状和粒状外,还有一些特殊形态如碳化物呈纤维状和针状的珠光体的珠光体。
二、珠光体片间距及与过冷度的关系珠光体的片间距主要决定于珠光体的形成温度。
冷却速度愈大,珠光体形成温度愈低(过冷度愈大),则片间距愈小,也即铁素体和渗碳体片的厚度愈薄。
在连续冷却过程中,珠光体转变是在一个温度范围内进行的。
在较高温度形成珠光体比较粗,低温形成的珠光体较细。
这种粗细不均匀的珠光体,将引起力学性能的不均匀,对切削加工也有不利影响。
为取得粗细相近的珠光体组织,可采用等温热处理的方法,如等温退火等。
三、珠光体的力学性能珠光体是铁素体和渗透体组成的两相混合物,其力学性能主要决定于两相界面积的大小和渗碳体的形状和分布等。
片状珠光体的强度主要取决于片间距的大小。
片层间距愈小、屈服强度σ0.2愈高。
根据实验,片间距的影响可表达为下式σ0.2∝1/S0式中σ0.2——屈服强度(Mpa)S0——珠光体片间距(μm)珠光体片间距减小,表明渗碳体和铁素片变薄,相界面积相应增多,相界面增多,将使铁素体内的滑移过程变得困难,塑性变形抗力升高。
珠光体的塑性主要受片间距和珠光体团尺寸的影响。
珠光团尺寸和珠光体片间距减小,均使断面收缩率增加,尤其在团尺寸和片间距较小时,影响更为明显。
粒状珠光体的力学性能主要决定于渗碳体颗粒大小和分布。
渗碳体体积分数相同时,其颗粒愈小,界面愈多,产生强化作用越显著,故硬度和强度较高。
反之则硬度和强度较低。
粒状珠光体与片状珠光体比较,在碳含量相同的钢中,粒状珠光体组织中铁素体呈连续分布,位错运动阻力较小,故粒状珠光体的硬度和屈服强度略低于片状珠光体,但塑性较好。
实践证明,粒状珠光体的切削加工性能、冷挤压成形性能和热处理工艺性能等比片状珠光体好。
所以高碳钢通常采用球化退火为预先热处理,以获得粒状珠光体组织,这种组织既改善切削加工性能,又可减少淬火畸变、开裂的倾向,同时也改善了塑性。
冷挤压成形的中碳钢件,也进行球化退火,以取得粒状碳化物分布,提高塑性,改善冷挤压成形性。
亚共析钢组织中,除珠光体外,还有先共析铁素体,其力学性能取决于铁素体和珠光体的相对含量及粗细等。
必须指出,如果亚共析钢的先共析铁素体及过共析钢的渗碳体以网状分布,不仅降低了钢的强度,而且还使钢的塑性和韧性明显下降。
想一想:能否说“由于珠光体的强度大大高于铁素体,所以亚共析钢的强度主要由珠光体决定”?第二节珠光体形成过程一、片状珠光体的形成过程珠光体形成过程也是由形核和长大两个阶段组成。
(一)珠光体形核共析钢珠光体转变时,通常优先在奥氏体晶界上形核,这是因为晶界能量较高,形核所需形核功较小,同时晶界有利原子扩散,是扩散的快速通道。
如果奥氏体内碳浓度不均匀,有偏离共析成分的区域存在;或者有夹杂物(工业用钢中脱氧后存留下来的A12O3、SiO2等)存在,这些区域也容易形成珠光体晶核。
图2-10表示珠光体在原奥氏体晶界上形核情形(图中黑色球团是珠光体、基体是马氏体)。
珠光体是由渗碳体和铁素体两相组成。
一般认为,亚共析钢是以铁素体为领先相,过共析钢以渗碳体为领先相;共析钢中,则渗碳体和铁素体都有可能作为形核的领先相,过冷度小时,渗碳体为领先相;过冷度大时,铁素体为领先相。
(二)珠光体的长大讲图2-11:(略)。
上述珠光体晶核长大机制,不是珠光体唯一生长方式。
观察发现,有时在一个珠光体团中的渗碳体,都是从同一渗碳体主干分枝出来的,并且同一珠光体团中的渗碳体,其晶体学位向相同,因此认为珠光体成长是渗碳体向前长大过程中,不断分枝,而铁素体则协同地在渗碳体枝间形成,见图2-12。
这样形成的珠光体团是由一个渗碳体晶粒和一个铁素体晶粒互相穿插起来的。
(三)珠光体长大过程中的碳扩散讲图2-13-珠光体长大过程:略二、粒状珠光体形成过程粒状珠光体的形成过程与片状珠光体不完全相同。
讲图2-15:(略)网状渗碳体,虽也可溶断并逐渐球化,但热处理实践表明,其球化效果并不好,即使经长时间球化处理,其渗碳体仍呈“人字形”或“一字形”(见图2-15b)。
含网状渗碳体的钢件,需通过正火将网状渗碳体消除后,再进行球化退火。
钢中碳化物的球化,主要决定于加热时奥氏体化温度,冷却条件也对其球化有一定影响。
实验证明,如奥氏体化温度过高,由于碳化物大部分溶解于奥氏体中,奥氏体成分也较均匀,在随后缓慢冷却时,常形成片状珠光体。
只有在奥氏体化温度较低(碳钢通常为Ac1+20~30℃)、并且冷却较慢时,才可能获得粒状珠光体。
如果冷却太快,或者在A1以下等温温度过低,则碳化物也不容易球化,往往得到点状碳化物和片状珠光体的混合组织,不能取得良好的球化效果。
【想一想】:球状碳化物是由什么变来的?第三节珠光体转变速度及影响因素一、珠光体转变速度珠光体转变速度通常用单位时间在单位体积内形成的珠光体体量(体积分数)来表示。
珠光体转变是通过形核和长大过程,因此,珠光体转变速度取决于形核率和长大速度。
形核率是指单位时间、单位体积中生成的珠光体晶核数目,其单位为1/(mm3·S)。
珠光体长大速度是指单位时间内,珠光体团直径的增加速度,其单位为mm/s。
共析钢的珠光体形核率和长大速率与转变温度的关系,如图2-16所示。
讲图2-16中形核率与长大速度在550℃附近达到最大值的解释:(略)。
研究表明,珠光体等温转变量与等温时间关系如下:转变初期的转变量增加较慢,即转变速度较慢,中期转变速度较快,后期又变慢,如图2-17所示。
二、影响珠光体转变速度的因素除过冷度外,还有以下因素影响珠光体转变速度:1)含碳量的影响对亚共析钢,随奥氏体含碳量提高,珠光体转变速度减慢。
2)合金元素溶入奥氏体的大多数合金元素(除Co外),都使珠光体转变速度下降。
3)其他方面的影响:①奥氏体晶粒越细小,则珠光体形核部位越多,从而加快珠光体转变;②奥氏体成分越不均匀,则贫碳区和富碳区越多,这有利于铁素体或渗碳体形成,从而有利于珠光体转变;③未溶碳化物与奥氏体界面可作为珠光体择优形核地点,加快珠光体转变;④原始组织越细,同样加热后,奥氏体成分越均匀,珠光体转变速度越慢;⑤提高加热温度或延长保温时间使奥氏体成分变得较均匀,也使珠光体转变速度减慢;⑥在奥氏体状态下进行塑性变形可加快珠光体转变。
第四节非共析钢的珠光体转变一、非共析碳钢的珠光体转变对于亚共析钢或过共析钢,当奥氏体被过冷至A1温度以下转变时,有先共析铁素体或渗碳体先于珠光体形成。
然而,若以较快速度冷却,使奥氏体在较大过冷度下转变,则先共析相析出将受到抑制甚至不能析出而直接转变成珠光体。
这可由图2-19来说明:讲图2-19(略)由以上看出,成分靠近共析点的合金,在较小过冷度下即可得到全部共析组织,而离共析点远的合金,则需较大的过冷度;随冷却速度增大,先共析相被抑制的程度增大。
【想一想】:能否说伪共析珠光体的碳含量也是0.77%,为何?二、先共析相的组织形态在亚析共钢中,先共析铁素体的组织形态主要有三种,即块状铁素体、网状铁素体和魏氏组织,过共析钢中先共析渗碳体有两种形态,即渗碳体网和魏氏组织。
先共析相的组织形态与其形成条件有关。
形成条件包括钢的成分、形成温度、冷却速度以及奥氏体晶粒等。
图2-20为不同含碳量的钢,形成各种不同形态先共析相的大致温度范围。
可以看出,含碳量较低(<0.25%)的钢,在A3以下较大过冷度时,铁素体容易形成块状。
在亚共析钢和过共析钢中,尤其含碳量靠近共析成分时,在较小过冷度下,先共析相在原奥氏体晶界上形核,并以较快的长大速度沿晶界成长,形成仿晶界形貌的铁素体网或渗碳体网。
含碳量在中碳范围(wc=0.2%~0.5%)的亚共析钢或大于1.1%的过共析钢,在A3或Acm以下较大过冷度下,先析析相倾向于呈针状或片状沿奥氏体晶界形成并长大即形成魏氏组织(见图2-21)。