炉渣冶金性能对高炉冶炼过程的影响
高Al2O3炉渣对高炉生产的影响1
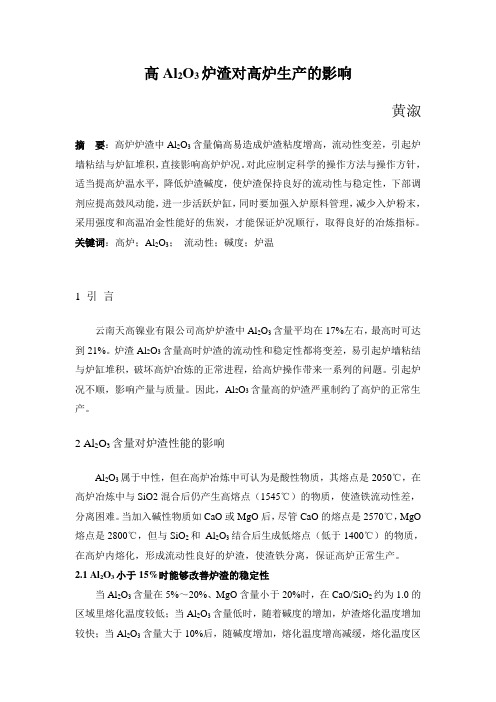
高Al2O3炉渣对高炉生产的影响黄溆摘要:高炉炉渣中Al2O3含量偏高易造成炉渣粘度增高,流动性变差,引起炉墙粘结与炉缸堆积,直接影响高炉炉况。
对此应制定科学的操作方法与操作方针,适当提高炉温水平,降低炉渣碱度,使炉渣保持良好的流动性与稳定性,下部调剂应提高鼓风动能,进一步活跃炉缸,同时要加强入炉原料管理,减少入炉粉末,采用强度和高温冶金性能好的焦炭,才能保证炉况顺行,取得良好的冶炼指标。
关键词:高炉;Al2O3;流动性;碱度;炉温1 引言云南天高镍业有限公司高炉炉渣中Al2O3含量平均在17%左右,最高时可达到21%。
炉渣Al2O3含量高时炉渣的流动性和稳定性都将变差,易引起炉墙粘结与炉缸堆积,破坏高炉冶炼的正常进程,给高炉操作带来一系列的问题。
引起炉况不顺,影响产量与质量。
因此,Al2O3含量高的炉渣严重制约了高炉的正常生产。
2Al2O3含量对炉渣性能的影响Al2O3属于中性,但在高炉冶炼中可认为是酸性物质,其熔点是2050℃,在高炉冶炼中与SiO2混合后仍产生高熔点(1545℃)的物质,使渣铁流动性差,分离困难。
当加入碱性物质如CaO或MgO后,尽管CaO的熔点是2570℃,MgO 熔点是2800℃,但与SiO2和Al2O3结合后生成低熔点(低于1400℃)的物质,在高炉内熔化,形成流动性良好的炉渣,使渣铁分离,保证高炉正常生产。
2.1 Al2O3小于15%时能够改善炉渣的稳定性当Al2O3含量在5%~20%、MgO含量小于20%时,在CaO/SiO2约为1.0的区域里熔化温度较低;当Al2O3含量低时,随着碱度的增加,炉渣熔化温度增加较快;当Al2O3含量大于10%后,随碱度增加,熔化温度增高减缓,熔化温度区域扩大,炉渣粘度随碱度变化也减缓,炉渣稳定性增加。
可以认为Al2O3的存在削弱了CaO/SiO2变化的影响。
2.2 高Al2O3炉渣对高炉冶炼的不利影响Al2O3小于15%时能够改善炉渣的稳定性,有利于高炉操作,但炉渣中Al2O3含量一般在15%~18%,原因是高Al2O3炉渣难以熔化,并且粘度增大,流动性变差,会产生以下负面影响:(1)高Al2O3炉渣的初渣堵塞炉料间的空隙,使料柱透气性变差,增加煤气通过时的阻力。
高炉装料、送风、造渣、热制度的调整技术(下)

目前,原燃料质量的不断恶化,有降低矿批量趋势。
大高炉的焦批厚在0.65~0.75m,不宜小于0.5m。
宝钢焦批在800mm。
调负荷一般不动焦批,以保持焦窗透气性稳定。
焦批的改变对布料具有重大影响,操作中最好不用。
高炉操作不要轻易加净焦,只有在出现对炉温有持久影响的因素存在才用(如高炉大凉、发生严重崩料和悬料,设备大故障等)。
而且只有在净焦下达炉缸时才会起作用。
加净焦的作用:有效提炉温,疏松料柱,改炉料透气性,改变煤气流分布。
跟据情况采取改变焦碳负荷的方法比较稳妥,不会造成炉温波动。
调焦炭负荷不可过猛,变铁种时,要分几批调剂,间隔最好1-2小时。
高冶炼强度,矿批重要加大。
喷煤比提高,要加大矿批重。
加大矿批重的条件:边缘负荷重、矿石密度大改用密度小时(富矿改贫矿)、焦炭负荷减轻。
减小矿批重的条件:边缘煤气流过分发展;在矿批重相同的条件,以烧结矿代替天然矿;加重焦炭负荷;炉龄后期等。
改变装料顺序的条件:调整炉顶煤气流分布,处理炉墙结厚和结瘤,开停炉前后等。
为解决钟阀式炉顶布料不均,使用布料器可消除炉料偏析。
布料器类型:马基式旋转布料器-可进行0?、60?、120?、180?、240?、360?六点布料。
仍有布料不均现象,易磨损。
快速旋转布料器-转速为10~20转/分,布料均匀,消除堆角。
空转螺旋布料器-与快速旋转布料器结构相同,旋转漏斗开口为单嘴,没有密封。
布料器不转时要减轻焦炭负荷1%~5%。
6.4.可调炉喉大型高炉有可调炉喉。
宝钢1号高炉有24块可调炉喉板,有11个档位,可使料面差由0.75m至3.58m,对炉内料面影响较大。
6.5.料线料线越高,则炉料堆尖离开炉墙远,故使边缘煤气流发展。
料线应在炉料碰炉墙的撞点以上。
每次检修均要校正料线0点。
中小高炉炉料线在1.2~1.5m,大型高炉在1.5m~2.0m。
装完料后的料线仍要有0.5m的余富量。
两个料R下降相差要小于0.3~0.5m。
料线低于正常规定的0.5m 以上时,或时间超过1小时,称为低料线。
钢铁冶金学基本问答题
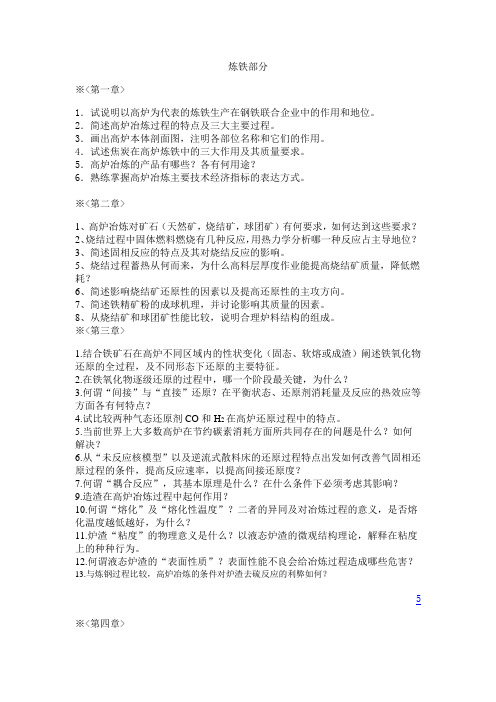
炼铁部分※<第一章>1.试说明以高炉为代表的炼铁生产在钢铁联合企业中的作用和地位。
2.简述高炉冶炼过程的特点及三大主要过程。
3.画出高炉本体剖面图,注明各部位名称和它们的作用。
4.试述焦炭在高炉炼铁中的三大作用及其质量要求。
5.高炉冶炼的产品有哪些?各有何用途?6.熟练掌握高炉冶炼主要技术经济指标的表达方式。
※<第二章>1、高炉冶炼对矿石(天然矿,烧结矿,球团矿)有何要求,如何达到这些要求?2、烧结过程中固体燃料燃烧有几种反应,用热力学分析哪一种反应占主导地位?3、简述固相反应的特点及其对烧结反应的影响。
5、烧结过程蓄热从何而来,为什么高料层厚度作业能提高烧结矿质量,降低燃耗?6、简述影响烧结矿还原性的因素以及提高还原性的主攻方向。
7、简述铁精矿粉的成球机理,并讨论影响其质量的因素。
8、从烧结矿和球团矿性能比较,说明合理炉料结构的组成。
※<第三章>1.结合铁矿石在高炉不同区域内的性状变化(固态、软熔或成渣)阐述铁氧化物还原的全过程,及不同形态下还原的主要特征。
2.在铁氧化物逐级还原的过程中,哪一个阶段最关键,为什么?3.何谓“间接”与“直接”还原?在平衡状态、还原剂消耗量及反应的热效应等方面各有何特点?4.试比较两种气态还原剂CO和H2在高炉还原过程中的特点。
5.当前世界上大多数高炉在节约碳素消耗方面所共同存在的问题是什么?如何解决?6.从“未反应核模型”以及逆流式散料床的还原过程特点出发如何改善气固相还原过程的条件,提高反应速率,以提高间接还原度?7.何谓“耦合反应”,其基本原理是什么?在什么条件下必须考虑其影响?9.造渣在高炉冶炼过程中起何作用?10.何谓“熔化”及“熔化性温度”?二者的异同及对冶炼过程的意义,是否熔化温度越低越好,为什么?11.炉渣“粘度”的物理意义是什么?以液态炉渣的微观结构理论,解释在粘度上的种种行为。
12.何谓液态炉渣的“表面性质”?表面性能不良会给冶炼过程造成哪些危害?13.与炼钢过程比较,高炉冶炼的条件对炉渣去硫反应的利弊如何?5※<第四章>1.风口前焦炭循环区的物理结构如何?风口前碳的燃烧在高炉过程中所起的作用是什么?2.什么叫鼓风动能?它对高炉冶炼有什么影响?3.什么叫理论燃烧温度?它在高炉冶炼中起何作用?4.什么叫水当量?沿高炉高度方向水当量的变化特征?5.高炉内三种传热方式各自进行的条件如何?在不同条件下哪一种方式为控制性环节?5※<第五章>1.写出欧根公式,说明式中各因子的物理意义,指出该式对高炉作定性分析时适用的区域,并从炉料和煤气两方面分析影响ΔP的因素及改善炉内透气性的主要途径。
如何优化高炉操作提高炼铁效率

如何优化高炉操作提高炼铁效率随着工业化进程的不断发展,炼铁产业在现代社会中扮演着重要的角色。
高炉作为炼铁过程中的关键设备,其操作效率直接关系到炼铁效果和生产成本。
因此,如何优化高炉操作以提高炼铁效率成为了一个重要课题。
本文将从多个方面探讨如何优化高炉操作并提高炼铁效率。
一、确保原料质量首先,高炉的原料质量对炼铁效率有着直接的影响。
在高炉操作之前,需要对原料进行准确的检测和分析,确保其符合要求。
特别是焦炭和铁矿石,其含碳量、含硫量、粒度以及矿物组成等都是重要的指标。
合理选择高质量的原料,不仅可以提高炼铁效率,还能提高炉渣融化性能,减少焦炭消耗。
二、优化冶炼冶程高炉的冶炼冶程也是优化操作的重要方面。
在高炉操作过程中,要合理掌握温度、气体流动和物料流动等参数。
具体来说,可以采取如下措施:1. 合理控制高炉温度:通过调节风量和煤气量,控制高炉温度在适当范围内,避免温度过高或过低导致冶炼效果不理想。
2. 优化气体流动:合理调节风口位置和布局,确保鼓风风量的均匀分布。
同时,注氧量和废气排放也需要进行合理的控制,以提高冶炼效率和燃烧效果。
3. 控制物料流动:通过调节料层的均匀厚度和抛料速度等参数,确保物料的合理流动,避免出现结渣堵塞等问题。
三、增加冶金反应速度为了提高炼铁效率,可以通过增加冶金反应速度来达到目的。
具体来说,可以采取如下措施:1. 加快还原反应速度:可以通过合理控制还原剂的加入和分布,提高还原反应速度。
此外,适当增加高炉温度和提高还原度也是有效的方法。
2. 促进熔渣生成:合理选择熔剂和添加剂,以促进熔渣的生成和融化。
同时,控制酸性熔渣和碱性熔渣的比例,能够提高冶炼效果。
四、精确监测和控制在优化高炉操作过程中,精确的监测和控制是非常重要的。
通过应用先进的监测仪器和控制系统,可以实时监测高炉的各项指标,并根据监测结果进行精确的控制。
例如,可以根据炉温、风量、煤气含量等参数,调节鼓风速度和料速,保持高炉的稳定和高效运行。
18烧结矿冶金性能对其质量和高炉指标的影响

T10
1091 1092 1085
T40
1134 1247 1227
ΔT
43 155 142
Ts
1267 1435 1448
Td
1333 1450 1464
ΔT
66 15 16
ΔPm·9.8pa
S值(Kpa℃)
33.63 11.76 21.64
102 130 188
济钢
75.1
74.6
42.3
- - - 63.96 39.5
主要参考文献
序言:
烧结矿的冶金性能包括 900℃还原性(RI)、500℃低温还原粉化性 能( RDI )、荷重还原软化性能( TBS 、 TBE 、Δ TB )和熔融滴落性能 (Ts、Td、ΔT、ΔPm、S值)。这四项性能中900还原性是基本性能, 它不仅直接影响煤气利用率和燃料比,同时由于还原程度的不同,还 影响其还原强度(RDI)和软熔性能。500℃低温还原性能是反映烧结 矿在高炉上部还原强度的,它是高炉上部透气性的限制性环节。在高 炉冶炼进程中,高炉上部的阻力损失约占总阻力损失的 15%。烧结矿 的荷重还原软化性能是反映其在高炉炉身下部和炉腰部分软化带透气 性的,这部分的透气阻力约占高炉总阻力损失的25% 。熔融滴落性能 是烧结矿冶金性能最重要的部分,因为它约占高炉总阻力损失的60%, 是高炉下部透气性的限制性环节,要保持高炉长期顺行稳定,必须十 分重视含铁原料在熔融带的透气阻力。烧结矿在高炉的块状带、软化 带和熔融滴落带不同部位的性状和透气阻力的变化(详见示图)决定 着高炉内不同部位顺行和稳定,因此研究和分析清楚冶金性能对烧结 矿质量和高炉主要操作指标的影响是十分重要和必要的。
烧结矿的荷重还原软化性能是指其装入高炉后,随炉料下降,温度上升不断被 还原,到达炉身下部和炉腰部位,烧结矿表现出体积开始收缩即开始软化(TBS) 和 软 化 终 了 ( TBE ) 的 特 性 , 高 碱 度 烧 结 矿 的 TBS 应 ≥ 1100 ℃ , 软 化 温 度 区 间 (ΔTB= TBE -TBS)应≤150℃,烧结矿开始软化温度的高低取决于其矿物组成和 气孔结构强度〔1〕开始软化温度的变化往往是气孔结构强度起主导作用的结果, 这就是说,软化终了温度往往是矿物组成起主导作用。由高炉内各带透气阻力的 示图可知,软化带的阻力损失约占25%,是反映炉料在炉身下部和炉腰部位顺行状 况的,当烧结矿的开始软化温度低于950℃,软化温度区间>300℃时,高炉必须会 产生严重的悬料,因此为了保持高炉顺行稳定,烧结矿应具有良好的荷重还原软 化性能。关于荷重还原性能对高炉主要操作指标的影响 ,意大利的皮昂比诺 ( Piombimo )公司 4# 高炉曾于 1980 年做过统计,含铁原料的 TBS 由 1285 ℃提高到 1335℃,高炉的透气性ΔP由5.2kpa降低到4.75kpa(下降8.7%),产量提高了 16%, 日本神户公司的加古川厂和新日铁的广畑厂均通过改善酸性球团矿的软熔性能有 效地改善了高炉操作指标〔7〕。
钢铁冶金部分课后作业题及答案
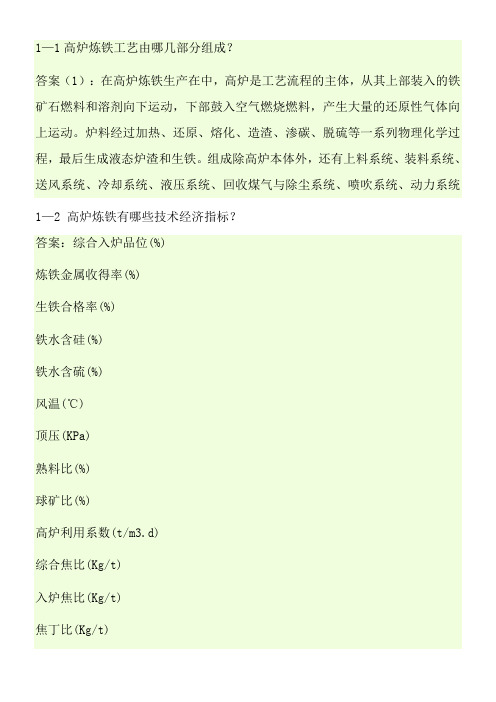
1—1高炉炼铁工艺由哪几部分组成?答案(1):在高炉炼铁生产在中,高炉是工艺流程的主体,从其上部装入的铁矿石燃料和溶剂向下运动,下部鼓入空气燃烧燃料,产生大量的还原性气体向上运动。
炉料经过加热、还原、熔化、造渣、渗碳、脱硫等一系列物理化学过程,最后生成液态炉渣和生铁。
组成除高炉本体外,还有上料系统、装料系统、送风系统、冷却系统、液压系统、回收煤气与除尘系统、喷吹系统、动力系统1—2 高炉炼铁有哪些技术经济指标?答案:综合入炉品位(%)炼铁金属收得率(%)生铁合格率(%)铁水含硅(%)铁水含硫(%)风温(℃)顶压(KPa)熟料比(%)球矿比(%)高炉利用系数(t/m3.d)综合焦比(Kg/t)入炉焦比(Kg/t)焦丁比(Kg/t)喷煤比(Kg/t)1—3 高炉生产有哪些特点?答案:一是长期连续生产。
高炉从开炉到大修停炉一直不停地连续运转,仅在设备检修或发生事故时才暂停生产(休风)。
高炉运行时,炉料不断地装入高炉,下部不断地鼓风,煤气不断地从炉顶排出并回收利用,生铁、炉渣不断地聚集在炉缸定时排出。
二是规模越来越大型化。
现在已有5000m3以上容积的高炉,日产生铁万吨以上,日消耗矿石近2万t,焦炭等燃料5kt。
三是机械化、自动化程度越来越高。
为了准确连续地完成每日成千上万吨原料及产品的装入和排放。
为了改善劳动条件、保证安全、提高劳动生产率,要求有较高的机械化和自动化水平。
四是生产的联合性。
从高炉炼铁本身来说,从上料到排放渣铁,从送风到煤气回收,各系统必须有机地协调联合工作。
从钢铁联合企业中炼铁的地位来说,炼铁也是非常重要的一环,高炉体风或减产会给整个联合企业的生产带来严重影响。
因此,高炉工作者要努力防止各种事故,保证联合生产的顺利进行。
1—5 高炉生产有哪些产品和副产品,各有何用途?答案:高炉冶炼主要产品是生铁,炉渣和高炉煤气是副产品。
(1)生铁。
按其成分和用途可分为三类:炼钢铁,铸造铁,铁合金。
(2)炉渣。
高铝对高炉炼铁的影响及优化
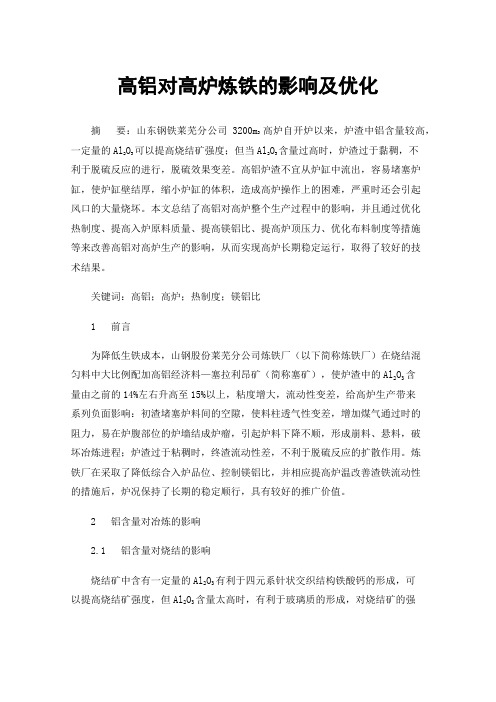
高铝对高炉炼铁的影响及优化摘要:山东钢铁莱芜分公司3200m3高炉自开炉以来,炉渣中铝含量较高,一定量的Al2O3可以提高烧结矿强度;但当Al2O3含量过高时,炉渣过于黏稠,不利于脱硫反应的进行,脱硫效果变差。
高铝炉渣不宜从炉缸中流出,容易堵塞炉缸,使炉缸壁结厚,缩小炉缸的体积,造成高炉操作上的困难,严重时还会引起风口的大量烧坏。
本文总结了高铝对高炉整个生产过程中的影响,并且通过优化热制度、提高入炉原料质量、提高镁铝比、提高炉顶压力、优化布料制度等措施等来改善高铝对高炉生产的影响,从而实现高炉长期稳定运行,取得了较好的技术结果。
关键词:高铝;高炉;热制度;镁铝比1 前言为降低生铁成本,山钢股份莱芜分公司炼铁厂(以下简称炼铁厂)在烧结混匀料中大比例配加高铝经济料—塞拉利昂矿(简称塞矿),使炉渣中的Al2O3含量由之前的14%左右升高至15%以上,粘度增大,流动性变差,给高炉生产带来系列负面影响:初渣堵塞炉料间的空隙,使料柱透气性变差,增加煤气通过时的阻力,易在炉腹部位的炉墙结成炉瘤,引起炉料下降不顺,形成崩料、悬料,破坏冶炼进程;炉渣过于粘稠时,终渣流动性差,不利于脱硫反应的扩散作用。
炼铁厂在采取了降低综合入炉品位、控制镁铝比,并相应提高炉温改善渣铁流动性的措施后,炉况保持了长期的稳定顺行,具有较好的推广价值。
2 铝含量对冶炼的影响2.1 铝含量对烧结的影响烧结矿中含有一定量的Al2O3有利于四元系针状交织结构铁酸钙的形成,可以提高烧结矿强度,但Al2O3含量太高时,有利于玻璃质的形成,对烧结矿的强度和低温还原粉化性能不利[1]。
实践证明,当烧结矿中铝含量>2.5%,对烧结矿强度和低温还原粉化性能影响较大。
2.2 铝含量对高炉生产的影响Al2O3在炉渣中有一定的脱硫效果,但弱于CaO和MgO。
对高炉生产的影响具体表现为:在炉内,压差升高,上部容易悬料,炉缸容易粘结堆积;在炉外,主沟内渣铁不易分离,渣中带铁,渣沟内炉渣流动性很差,容易结壳。
优化渣系,提高铁的回收率
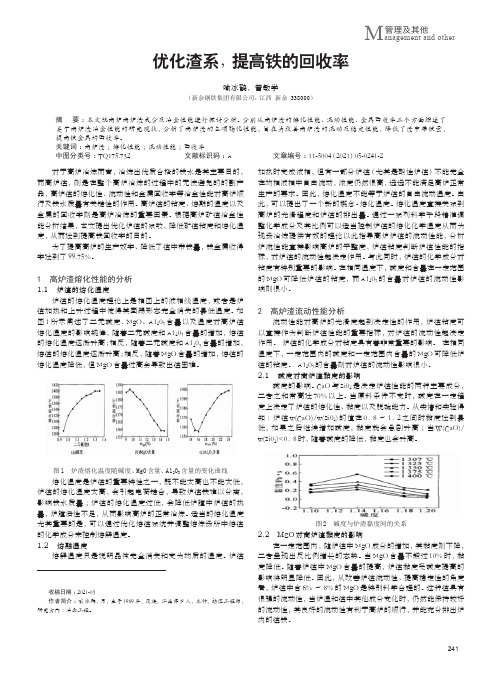
241管理及其他M anagement and other优化渣系,提高铁的回收率喻冰鹤,曾敏学(新余钢铁集团有限公司,江西 新余 338000)摘 要:本文就高炉高炉渣成分及冶金性能进行探讨分析。
分别从高炉渣的熔化性能、流动性能、金属回收率三个方面综述了关于高炉渣冶金性能的研究现状,分析了高炉渣的各项物化性能,旨在为改善高炉渣的流动及稳定性能,降低了渣中带铁量,提高铁金属的回收率。
关键词:高炉渣;熔化性能;流动性能;回收率中图分类号:TQ175.732 文献标识码:A 文章编号:11-5004(2021)05-0241-2收稿日期:2021-03作者简介:喻冰鹤,男,生于1989年,汉族,江西萍乡人,本科,助理工程师,研究方向:冶金工程。
对于高炉冶炼而言,冶炼出优质合格的铁水是其主要目的,而高炉渣,则是在整个高炉冶炼的过程中的无法避免的的副产品,高炉渣的熔化性、流动性和金属回收率等冶金性能对高炉顺行及铁水质量有关键性的作用。
高炉渣的粘度、熔融的温度以及金属的回收率则是高炉冶炼的重要因素。
根据高炉矿渣冶金性能分析结果,本文提出优化炉渣的系数,降低矿渣粘度和熔化温度,从而达到提高铁回收率的目的。
为了提高高炉的生产效率、降低了渣中带铁量,铁金属收得率达到了99.75%。
1 高炉渣熔化性能的分析1.1 炉渣的熔化温度炉渣的熔化温度理论上是相图上的液相线温度,或者是炉渣加热和上升过程中使得其固踢形态完全消失的最低温度。
如图1所示阐述了二元碱度、MgO、 A1203含量以及温度对高炉渣熔化温度的影响规律,随着二元碱度和A1203含量的增加,熔渣的熔化温度逐渐升高;相反,随着二元碱度和A1203含量的增加,熔渣的熔化温度逐渐升高;相反,随着MgO 含量的增加,熔渣的熔化温度降低,但MgO含量过高会导致出渣困难。
图1 炉渣熔化温度随碱度、MgO 含量、A1203含量的变化曲线熔化温度是炉渣的重要特性之一,既不能太高也不能太低,炉渣的熔化温度太高,会引起电荷键合,导致炉渣铁难以分离,影响铁水质量;炉渣的熔化温度过低,会降低炉膛中炉渣的热量,炉膛活性不足,从而影响高炉的正常冶炼。
冶金性能对高炉 的影响

还原软化-熔融特性
软化、熔融性能:炉料的荷重软化、熔融性能反映了炉料在高 炉下部的高温软化和熔化、滴落过程的特性。对高炉软熔带的 形成(位置、形状、厚度)和透气性起着决定性作用。 表征此特性的参数有炉料的软化开始温度、软化终了温度、熔 融温度、软化区间以及熔融区间。 高炉要求矿石具有合适的软化开始温度、熔化开始温度,窄的 软化和熔融温度区间,以使高炉软融带位置既为过高,也不过 低,处于适宜的位置,即能适当增加炉内块状带区域的高度, 利于改善上部透气性。 软熔带位置过低,熔融渣铁或炉墙周围熔化的粘结物易直接进 入炉缸,导致崩、滑料甚至炉凉。炉料的软化熔融温度区间较 宽,表明高炉软熔带较厚,煤气通过软熔带的阻力较大,高炉 透气性较差。
烧结矿冶金性能指标 影响因素及有关问题探讨
2013.11
内容
烧结矿的冶金性能指标 影响冶金性能指标的因素探讨 测定方法
高炉精料要求
入炉品位高,脉 石及杂质含量 低
提高入炉料强 度和粒度组成 合理
改善原燃料 高温冶金性能
烧结矿的冶金性能指标
900℃还原度 550℃低温还原粉化指数 荷重软化性能 软熔-滴落性能
影响因素: 1烧结矿化学成分 2 烧结矿矿相组成 3 工艺条件
再生赤铁矿形成 残余应力增大 区域结构弱化 原生褐铁矿大颗粒 后果: 产生粉末,恶化高炉 上部透气性
磁铁矿直接氧化生成
破坏性大
还原为磁铁矿体积膨胀25%
颗粒状次生赤铁矿 骸晶状赤铁矿
物铁 其 的纹 主 。酸 中 周和 要 钙 夹 围熔 分 和 杂 。蚀 布 磁着 状在 铁玻 残气 矿璃 存孔 等质 原、 矿、 矿裂
MgO含量对低温还原粉化的影响
高炉利用系数与冶炼强度的关系
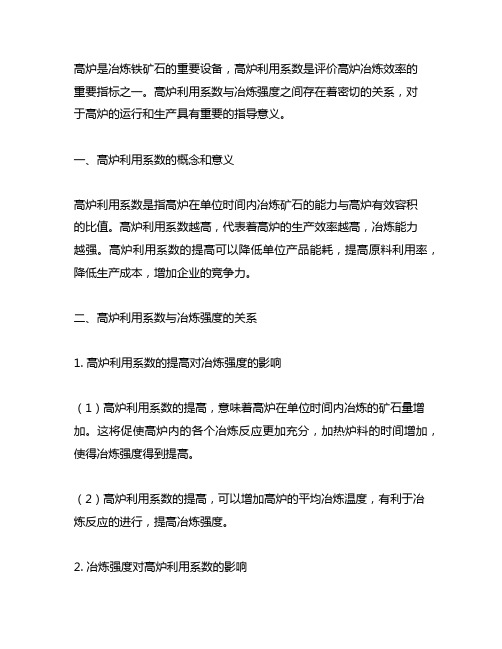
高炉是冶炼铁矿石的重要设备,高炉利用系数是评价高炉冶炼效率的重要指标之一。
高炉利用系数与冶炼强度之间存在着密切的关系,对于高炉的运行和生产具有重要的指导意义。
一、高炉利用系数的概念和意义高炉利用系数是指高炉在单位时间内冶炼矿石的能力与高炉有效容积的比值。
高炉利用系数越高,代表着高炉的生产效率越高,冶炼能力越强。
高炉利用系数的提高可以降低单位产品能耗,提高原料利用率,降低生产成本,增加企业的竞争力。
二、高炉利用系数与冶炼强度的关系1. 高炉利用系数的提高对冶炼强度的影响(1)高炉利用系数的提高,意味着高炉在单位时间内冶炼的矿石量增加。
这将促使高炉内的各个冶炼反应更加充分,加热炉料的时间增加,使得冶炼强度得到提高。
(2)高炉利用系数的提高,可以增加高炉的平均冶炼温度,有利于冶炼反应的进行,提高冶炼强度。
2. 冶炼强度对高炉利用系数的影响(1)冶炼强度的增加,可以提高高炉内的炉料流动性,有利于高炉的正常冶炼和操作。
(2)冶炼强度的增加,可以降低高炉炉料的堵塞现象,有利于提高高炉利用系数。
三、个人观点和理解高炉利用系数与冶炼强度之间存在着千丝万缕的联系。
高炉利用系数的提高可以促进高炉的冶炼强度,而冶炼强度的增加也能够反过来提高高炉的利用系数。
在实际生产中,企业需要综合考虑高炉的工艺参数、原料性能、操作技术等因素,不断优化调整高炉的运行方式,以达到高炉利用系数与冶炼强度的最佳匹配,从而提高生产效率和经济效益。
总结回顾:高炉利用系数与冶炼强度密不可分,两者相互影响、相互制约。
企业应该加强对高炉的监控和管理,优化高炉操作,提高高炉利用系数,从而提高冶炼强度,实现高效、稳定的生产。
对于高炉的运行管理和生产优化,我深切认识到其重要性和必要性,只有不断提高高炉利用系数与冶炼强度的匹配度,才能实现高炉的长期稳定、高效运行。
在此次的撰写过程中,通过对高炉利用系数与冶炼强度的关系进行深入探讨,我对高炉的冶炼过程和生产效率有了更加深刻的理解。
浅谈炉料质量对高炉冶炼的影响
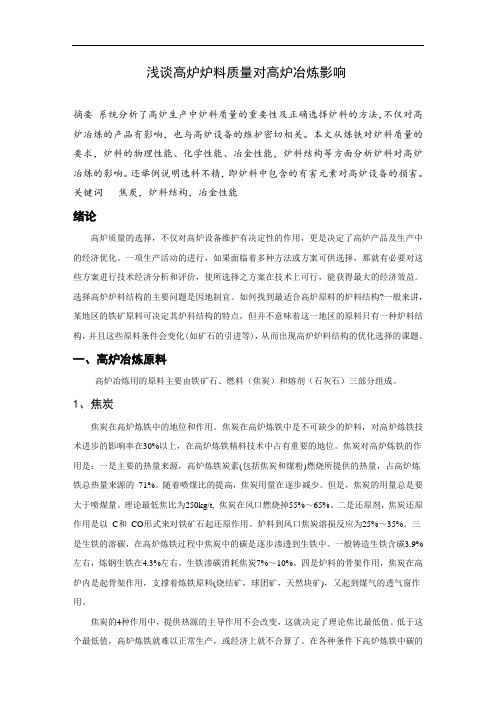
浅谈高炉炉料质量对高炉冶炼影响摘要系统分析了高炉生产中炉料质量的重要性及正确选择炉料的方法,不仅对高炉冶炼的产品有影响,也与高炉设备的维护密切相关。
本文从炼铁对炉料质量的要求,炉料的物理性能、化学性能、冶金性能,炉料结构等方面分析炉料对高炉冶炼的影响。
还举例说明选料不精,即炉料中包含的有害元素对高炉设备的损害。
关键词焦炭,炉料结构,冶金性能绪论高炉质量的选择,不仅对高炉设备维护有决定性的作用,更是决定了高炉产品及生产中的经济优化。
一项生产活动的进行,如果面临着多种方法或方案可供选择,那就有必要对这些方案进行技术经济分析和评价,使所选择之方案在技术上可行,能获得最大的经济效益。
选择高炉炉料结构的主要问题是因地制宜。
如何找到最适合高炉原料的炉料结构?一般来讲,某地区的铁矿原料可决定其炉科结构的特点,但并不意味着这一地区的原料只有一种炉料结构,并且这些原料条件会变化(如矿石的引进等),从而出现高炉炉料结构的优化选择的课题。
一、高炉冶炼原料高炉冶炼用的原料主要由铁矿石、燃料(焦炭)和熔剂(石灰石)三部分组成。
1、焦炭焦炭在高炉炼铁中的地位和作用。
焦炭在高炉炼铁中是不可缺少的炉料,对高炉炼铁技术进步的影响率在30%以上,在高炉炼铁精料技术中占有重要的地位。
焦炭对高炉炼铁的作用是:一是主要的热量来源,高炉炼铁炭素(包括焦炭和煤粉)燃烧所提供的热量,占高炉炼铁总热量来源的71%。
随着喷煤比的提高,焦炭用量在逐步减少。
但是,焦炭的用量总是要大于喷煤量。
理论最低焦比为250kg/t, 焦炭在风口燃烧掉55%~65%。
二是还原剂,焦炭还原作用是以C和CO形式来对铁矿石起还原作用。
炉料到风口焦炭溶损反应为25%~35%。
三是生铁的溶碳,在高炉炼铁过程中焦炭中的碳是逐步渗透到生铁中。
一般铸造生铁含碳3.9%左右,炼钢生铁在4.3%左右。
生铁渗碳消耗焦炭7%~10%。
四是炉料的骨架作用,焦炭在高炉内是起骨架作用,支撑着炼铁原料(烧结矿,球团矿,天然块矿),又起到煤气的透气窗作用。
Al2O3对高炉冶炼的影响--1三氧化二铝对烧结矿的影响
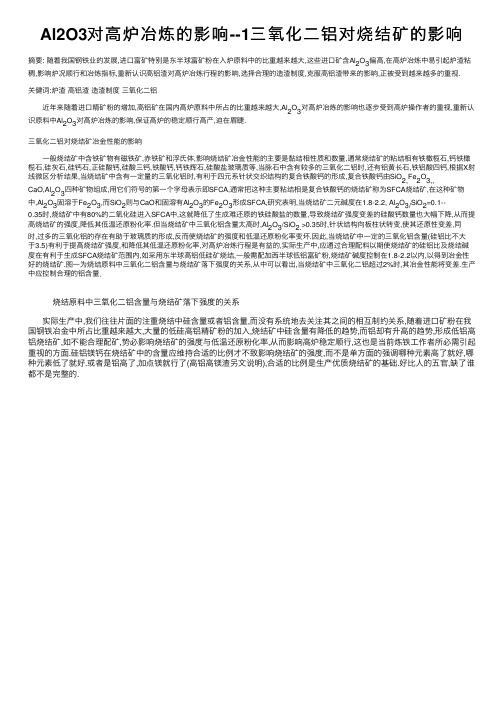
Al2O3对⾼炉冶炼的影响--1三氧化⼆铝对烧结矿的影响摘要: 随着我国钢铁业的发展,进⼝富矿特别是东半球富矿粉在⼊炉原料中的⽐重越来越⼤,这些进⼝矿含Al2O3偏⾼,在⾼炉冶炼中易引起炉渣粘稠,影响炉况顺⾏和冶炼指标,重新认识⾼铝渣对⾼炉冶炼⾏程的影响,选择合理的造渣制度,克服⾼铝渣带来的影响,正被受到越来越多的重视.关健词:炉渣⾼铝渣造渣制度三氧化⼆铝近年来随着进⼝精矿粉的增加,⾼铝矿在国内⾼炉原料中所占的⽐重越来越⼤,Al2O3对⾼炉冶炼的影响也逐步受到⾼炉操作者的重视,重新认识原料中Al2O3对⾼炉冶炼的影响,保证⾼炉的稳定顺⾏⾼产,迫在眉睫.三氧化⼆铝对烧结矿冶⾦性能的影响⼀般烧结矿中含铁矿物有磁铁矿,⾚铁矿和浮⽒体,影响烧结矿冶⾦性能的主要是黏结相性质和数量,通常烧结矿的粘结相有铁橄榄⽯,钙铁橄榄⽯,硅灰⽯,硅钙⽯,正硅酸钙,硅酸三钙,铁酸钙,钙铁辉⽯,硅酸盐玻璃质等,当脉⽯中含有较多的三氧化⼆铝时,还有铝黄长⽯,铁铝酸四钙,根据X射线微区分析结果,当烧结矿中含有⼀定量的三氧化铝时,有利于四元系针状交织结构的复合铁酸钙的形成,复合铁酸钙由SiO2,Fe2O3,,CaO,Al2O3四种矿物组成,⽤它们符号的第⼀个字母表⽰即SFCA,通常把这种主要粘结相是复合铁酸钙的烧结矿称为SFCA烧结矿,在这种矿物中,Al2O3固溶于Fe2O3,⽽SiO2则与CaO和固溶有Al2O3的Fe2O3形成SFCA,研究表明,当烧结矿⼆元碱度在1.8-2.2, Al2O3/SiO2=0.1--0.35时,烧结矿中有80%的⼆氧化硅进⼊SFCA中,这就降低了⽣成难还原的铁硅酸盐的数量,导致烧结矿强度变差的硅酸钙数量也⼤幅下降,从⽽提⾼烧结矿的强度,降低其低温还原粉化率.但当烧结矿中三氧化铝含量太⾼时,Al2O3/SiO2.>0.35时,针状结构向板柱状转变,使其还原性变差,同时,过多的三氧化铝的存在有助于玻璃质的形成,反⽽使烧结矿的强度和低温还原粉化率变坏.因此,当烧结矿中⼀定的三氧化铝含量(硅铝⽐不⼤于3.5)有利于提⾼烧结矿强度,和降低其低温还原粉化率,对⾼炉冶炼⾏程是有益的,实际⽣产中,应通过合理配料以期使烧结矿的硅铝⽐及烧结碱度在有利于⽣成SFCA烧结矿范围内,如采⽤东半球⾼铝低硅矿烧结,⼀般需配加西半球低铝富矿粉,烧结矿碱度控制在1.8-2.2以内,以得到冶⾦性好的烧结矿.图⼀为烧结原料中三氧化⼆铝含量与烧结矿落下强度的关系,从中可以看出,当烧结矿中三氧化⼆铝超过2%时,其冶⾦性能将变差.⽣产中应控制合理的铝含量.烧结原料中三氧化⼆铝含量与烧结矿落下强度的关系实际⽣产中,我们往往⽚⾯的注重烧结中硅含量或者铝含量,⽽没有系统地去关注其之间的相互制约关系,随着进⼝矿粉在我国钢铁冶⾦中所占⽐重越来越⼤,⼤量的低硅⾼铝精矿粉的加⼊,烧结矿中硅含量有降低的趋势,⽽铝却有升⾼的趋势,形成低铝⾼铝烧结矿,如不能合理配矿,势必影响烧结矿的强度与低温还原粉化率,从⽽影响⾼炉稳定顺⾏,这也是当前炼铁⼯作者所必需引起重视的⽅⾯.硅铝镁钙在烧结矿中的含量应维持合适的⽐例才不致影响烧结矿的强度,⽽不是单⽅⾯的强调哪种元素⾼了就好,哪种元素低了就好.或者是铝⾼了,加点镁就⾏了(⾼铝⾼镁渣另⽂说明),合适的⽐例是⽣产优质烧结矿的基础.好⽐⼈的五官,缺了谁都不是完整的.。
重钢高炉炉渣Al2O3升高的原因分析与应对措施

重钢高炉炉渣Al2O3升高的原因分析与应对措施摘要:针对重钢高炉渣中Al2O3含量的升高,分析了炉渣中Al2O3升高对高炉冶炼的不利影响,并通过统计对比分析,确定高炉入炉品位升高、渣铁比下降是导致渣中Al2O3升高的主要原因。
高炉经过采取切实可行的技术和管理措施,有效降低了渣中Al2O3含量,并在渣中Al2O3升高期间保持了高炉稳定顺行。
关键词:高炉;炉渣;Al2O3Cause Analysis and Countermeasures of Al2O3Increased in BF Slag in Chongqing SteelSHU Hao ;ZHANG Hai-feng; ZHANG Xiao-lin;YI Li(Chongqing Iron and Steel Co.Ltd)Abstract:The content of Al2O3 in Chongqing steel's BF slag increased , the adverse effect on the smelting of blast furnace was analyzed. Through statistical comparison and analysis, the increased BF charge grade and decreased slag-iron ration were the main cause leading to the Al2O3 rise in slag. Through feasible technology and management measures, it effectively reduced the Al2O3 content in slag, and maintained the stable smooth operation of the blast furnace during the increase of Al2O3 in the slag.Key words: blast furnace; slag; Al2O3在传统的高炉炼铁中,一般认为,高炉炉渣中Al2O3在15%以下为宜。
高炉炼铁过程中合理利用冶炼废渣的探讨

高炉炼铁过程中合理利用冶炼废渣的探讨炼铁是一项重要的冶金行业,其过程中产生大量的废渣。
为了实现资源的可持续利用和环境的可持续发展,合理利用冶炼废渣成为当前的研究热点。
本文将探讨高炉炼铁过程中合理利用冶炼废渣的方法与技术。
一、高炉炼铁过程中的冶炼废渣在高炉炼铁过程中,主要产生三种冶炼废渣:渣铁、炉渣和煤气灰。
渣铁是含有金属铁的固体废渣,炉渣是一种熔融物质,由铁矿石和燃料灰渣在高炉内反应生成,而煤气灰是煤气中的悬浮颗粒物在除尘系统中被捕集下来的废渣。
二、冶炼废渣的合理利用方法1. 渣铁的回收与利用渣铁是高炉中产生的含铁固体废渣,其中富含有有价值的铁资源。
因此,回收与利用渣铁是一种非常重要的方式。
渣铁可以经过磨碎、磁选等工艺,得到含铁粉末或颗粒,用于冶金、建材等领域,实现铁资源的再利用。
2. 炉渣的综合利用炉渣是高炉冶炼过程中产生的熔融物质,具有一定的水化硬化能力和活性,可以作为建筑材料的主要成分。
炉渣经过精细磨碎、分级、掺合等工艺,可以制成高性能水泥、水泥掺合料、水泥基复合材料等,应用于建筑工程中。
3. 煤气灰的资源化利用煤气灰是高炉冶炼过程中煤气中的悬浮颗粒物,通过除尘系统捕集下来的废渣。
煤气灰中含有多种有价值的元素,如锌、铅等。
通过酸浸、浸出等技术,可以将这些有价值的元素从煤气灰中提取出来,用于冶金、化工等领域。
三、冶炼废渣利用的挑战与对策在高炉炼铁过程中,冶炼废渣的合理利用还面临一些挑战。
首先,不同种类的冶炼废渣在成分和性质上存在差异,需要针对性地开展处理与利用。
其次,冶炼废渣中可能存在有害物质,需要进行安全环保的处理。
此外,废渣的处理与利用还需要考虑经济效益和可行性。
针对这些挑战,可以采取的对策包括:加强冶炼废渣的分类与分离,优化处理工艺与设备,确保废渣的纯度与安全性;开展研究与开发工作,推动冶炼废渣的资源化综合利用技术的创新与应用;加强政策引导,推动废渣资源化利用的产业化发展。
四、结语高炉炼铁过程中合理利用冶炼废渣是实现资源可持续利用和环境可持续发展的重要途径。
高Al2O3炉渣对高炉生产的影响

高Al2O3炉渣对高炉生产的影响随着我国钢铁产业的迅速发展,对炼铁原料的需求日益扩大,进口矿粉已占相当数量。
目前国内进口的矿粉主要是澳矿与印矿,这两种矿粉中Al2O3含量普遍偏高。
山东泰山钢铁集团(简称泰钢)高炉炉渣中Al2O3含量平均在18.2%左右,最高时可达到22%。
炉渣Al2O3含量高时炉渣的流动性和稳定性都将变差,易引起炉墙粘结与炉缸堆积,破坏高炉冶炼的正常进程,给高炉操作带来一系列的问题。
如不制定科学的操作方针与方法,将引起炉况不顺,影响产量与质量。
因此,Al2O3含量高的炉渣严重制约了高炉的正常生产。
2 Al2O3含量对炉渣性能的影响Al2O3属于中性,但在高炉冶炼中可认为是酸性物质,其熔点是2050℃,在高炉冶炼中与SiO2混合后仍产生高熔点(1545℃)的物质,使渣铁流动性差,分离困难。
当加入碱性物质如CaO或MgO后,尽管CaO的熔点是2570℃,MgO熔点是2800℃,但与SiO2和 Al2O3结合后生成低熔点(低于1400℃)的物质,在高炉内熔化,形成流动性良好的炉渣,使渣铁分离,保证高炉正常生产。
2.1 Al2O3小于15%时能够改善炉渣的稳定性当Al2O3含量在5%~20%、MgO含量小于20%时,在CaO/SiO2约为1.0的区域里熔化温度较低;当Al2O3含量低时,随着碱度的增加,炉渣熔化温度增加较快;当Al2O3含量大于10%后,随碱度增加,熔化温度增高减缓,熔化温度区域扩大,炉渣粘度随碱度变化也减缓,炉渣稳定性增加。
可以认为Al2O3的存在削弱了CaO/SiO2变化的影响。
2.2 高Al2O3炉渣对高炉冶炼的不利影响Al2O3小于15%时能够改善炉渣的稳定性,有利于高炉操作,但炉渣中Al2O3含量一般在15%~18%,原因是高Al2O3炉渣难以熔化,并且粘度增大,流动性变差,会产生以下负面影响:(1)高Al2O3炉渣的初渣堵塞炉料间的空隙,使料柱透气性变差,增加煤气通过时的阻力。
高炉炼铁中的炉渣控制策略减少炉渣对铁水质量的影响
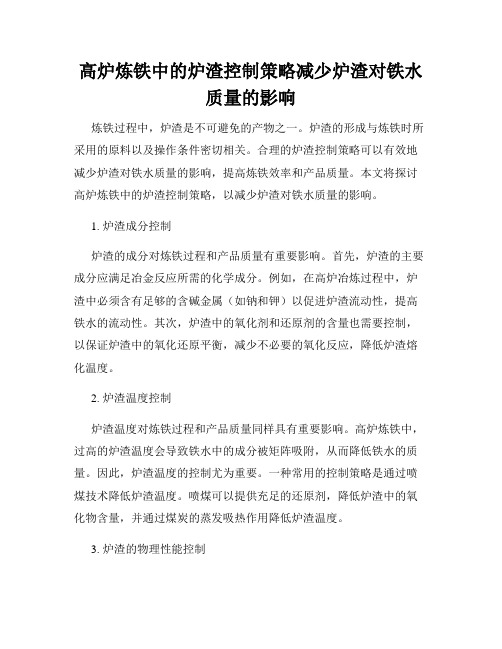
高炉炼铁中的炉渣控制策略减少炉渣对铁水质量的影响炼铁过程中,炉渣是不可避免的产物之一。
炉渣的形成与炼铁时所采用的原料以及操作条件密切相关。
合理的炉渣控制策略可以有效地减少炉渣对铁水质量的影响,提高炼铁效率和产品质量。
本文将探讨高炉炼铁中的炉渣控制策略,以减少炉渣对铁水质量的影响。
1. 炉渣成分控制炉渣的成分对炼铁过程和产品质量有重要影响。
首先,炉渣的主要成分应满足冶金反应所需的化学成分。
例如,在高炉冶炼过程中,炉渣中必须含有足够的含碱金属(如钠和钾)以促进炉渣流动性,提高铁水的流动性。
其次,炉渣中的氧化剂和还原剂的含量也需要控制,以保证炉渣中的氧化还原平衡,减少不必要的氧化反应,降低炉渣熔化温度。
2. 炉渣温度控制炉渣温度对炼铁过程和产品质量同样具有重要影响。
高炉炼铁中,过高的炉渣温度会导致铁水中的成分被矩阵吸附,从而降低铁水的质量。
因此,炉渣温度的控制尤为重要。
一种常用的控制策略是通过喷煤技术降低炉渣温度。
喷煤可以提供充足的还原剂,降低炉渣中的氧化物含量,并通过煤炭的蒸发吸热作用降低炉渣温度。
3. 炉渣的物理性能控制炉渣的物理性能对炼铁过程和产品质量同样具有重要影响。
一方面,炉渣的黏度和流动性影响了铁水的流动性,直接影响铁水的出渣和倾注质量。
因此,炉渣的黏度和流动性需要控制在合适的范围内,以确保铁水的正常冶炼和倾注。
另一方面,炉渣的稳定性也需要控制。
过于不稳定的炉渣容易生成气泡,降低铁水的质量。
因此,通过调整炉渣中的氧化剂和还原剂的含量来控制炉渣的物理性能是一种常用的策略。
4. 炉渣的排渣控制炉渣的排渣过程对炼铁过程和产品质量同样至关重要。
过早排渣或过晚排渣都会对铁水的质量造成不良影响。
合理的排渣策略可以减少炉渣对铁水的污染。
在高炉炼铁过程中,一种常用的排渣策略是通过控制炉渣中的钠和钾含量来调整炉渣的流动性,以实现合适的排渣速度。
总结:高炉炼铁中的炉渣控制策略是一个综合性的问题,需要考虑多个因素的综合影响。
金属冶炼中的炉渣特性研究

汇报人:可编辑
2024-01-06
CONTENTS
• 引言 • 金属冶炼基础知识 • 炉渣的物理特性 • 炉渣的化学ห้องสมุดไป่ตู้性 • 炉渣的冶金性能 • 实际应用与案例分析 • 结论与展望
01
引言
研究背景
01
金属冶炼是工业生产中的重要环 节,而炉渣作为冶炼过程中的副 产品,对冶炼效率和产品质量具 有重要影响。
02
随着工业技术的不断发展,对炉 渣特性的研究成为了提高冶炼效 率和资源利用率的关键。
研究目的与意义
研究目的
深入了解炉渣的物理、化学和机 械特性,为优化金属冶炼工艺和 提高资源利用率提供理论支持。
研究意义
通过研究炉渣特性,有助于提高 金属冶炼的效率、降低能耗、减 少环境污染,为工业生产的可持 续发展提供技术支持。
未来研究应进一步拓展不同 条件下炉渣特性的研究,以 更全面地了解炉渣在金属冶 炼过程中的作用。
9字
考虑实际生产过程中各种因 素对炉渣特性的影响,提高 研究的实用性和针对性。
9字
加强炉渣与金属之间相互作 用机制的研究,深入探讨其 微观过程和机理。
9字
结合现代科技手段如计算机 模拟和先进检测设备,对炉 渣特性进行更精确和深入的 研究。
稳定性与反应活性
稳定性
炉渣的稳定性对其在冶炼过程中的行 为具有重要影响。稳定性好的炉渣可 以保持较长时间的稳定状态,有利于 金属的提取和分离。
反应活性
炉渣的反应活性与其在金属冶炼过程 中的行为密切相关。具有较高反应活 性的炉渣可以促进金属的溶解、还原 和分离过程,提高金属回收率。
05
炉渣的冶金性能
研究局限与不足
当前研究主要集中在特定条件下炉渣特性的研究,对于不同冶炼条件下的 炉渣特性研究不够充分。
高炉矿渣的主要成分

高炉矿渣的主要成分高炉矿渣是高炉冶炼过程中产生的一种冶金废渣。
根据其主要成分的特点,可以将其分为多个组成部分。
本文将从主要成分的角度来详细介绍高炉矿渣。
高炉矿渣的主要成分包括氧化铁、硅酸盐、氧化钙、氧化镁等。
其中,氧化铁是高炉矿渣的主要成分之一。
在高炉冶炼过程中,铁矿石中的铁元素被氧化,形成氧化铁。
氧化铁是高炉矿渣的主要组成部分,其含量通常在40%至60%之间。
氧化铁具有良好的磁性和导电性,是高炉矿渣中重要的矿物成分。
硅酸盐是高炉矿渣的另一个主要成分。
在高炉冶炼过程中,铁矿石中的硅元素与氧化铁反应,形成硅酸盐。
硅酸盐在高炉矿渣中的含量较高,通常在20%至40%之间。
硅酸盐是一种具有硬度较高的矿物,具有良好的耐火性和耐腐蚀性,广泛应用于建筑材料和耐火材料等领域。
氧化钙和氧化镁是高炉矿渣中的另外两个重要成分。
在高炉冶炼过程中,石灰石和白云石等矿石中的钙和镁元素被氧化,形成氧化钙和氧化镁。
氧化钙和氧化镁在高炉矿渣中的含量通常在10%至20%之间。
氧化钙和氧化镁是一种具有碱性的物质,可以中和高炉冶炼过程中产生的酸性物质,提高高炉矿渣的碱度,有利于矿渣的稳定化和后续利用。
除了上述主要成分外,高炉矿渣中还含有少量的其他元素和化合物,如氧化铝、氧化钠、氧化钾等。
这些元素和化合物的含量较低,通常在1%以下。
它们对高炉矿渣的性质和性能影响较小,但在一些特殊情况下,如高炉渣水泥生产中,这些元素和化合物的含量对产品的品质和性能有一定的影响。
高炉矿渣的主要成分决定了其在实际应用中的性质和性能。
在建筑材料领域,高炉矿渣常用于制备水泥、混凝土等材料。
由于高炉矿渣中含有较高的硅酸盐和氧化钙等成分,使得高炉矿渣水泥具有较好的抗压强度和耐久性。
在冶金工业领域,高炉矿渣常用于制备耐火材料、脱硫剂等。
由于高炉矿渣中含有较高的氧化铁和硅酸盐等成分,使得高炉矿渣具有较好的耐火性和脱硫性能。
高炉矿渣的主要成分包括氧化铁、硅酸盐、氧化钙、氧化镁等。