SCR
SCR

选择性催化还原系统(Selective Catalytic Reduction,SCR)是指在催化剂的作用下,"有选择性"的与烟气中的NOX反应,将锅炉烟气中的氮氧化物还原成氮气和水。
SCR催化剂最佳的活性范围在300~400 ℃,一般被安排在锅炉的省煤器与空气预热器之间,因此对于燃煤锅炉的烟气脱硝系统,SCR催化剂是运行在较高灰尘环境下。
SCR烟气脱硝技术最高可达到90%以上的脱硝效率,是最为成熟可靠的脱硝方法。
在保证SCR脱硝效率的同时还有控制NH3的逃逸率和SO2的转化率,以保证SCR系统的安全连续运行。
烟气流动的均匀性、烟气中NOX和NH3混合的均匀以及烟气温度场的均匀性是保证脱硝性能的关键,是设计中需要考虑的因素。
二、SCR烟气脱硝工艺流程三、SCR烟气脱硝的技术特点∙深入了解催化剂特性,针对不同的工程选择合适的催化剂,包括蜂窝、板式和波纹板式,不拘泥于某个种类或某个厂家的催化剂,并能通过优化催化剂参数,降低催化剂积灰风险,保持较低的烟气压降,博奇可以联合催化剂厂商给业主提供催化剂管理经验,方便业主对催化剂进行管理;∙与国外最专业的流场模拟厂家合作,使用物模与数模技术,精心设计SCR系统的烟道布置、烟道内导流板布置、喷氨格栅、静态混合器等,使催化剂内烟气的温度、速度分布均匀,烟气中NOX与NH3混合均匀,可以最有效的利用催化剂,最大程度的降低氨的消耗量,减少SCR系统积灰,并保持SCR系统较低的烟气压降;∙反应器的设计合理,方便安装催化剂,并可适应多个主要催化剂提供商生产的催化剂,方便催化剂厂商的更换;∙过程参数采用自动控制,根据锅炉的负荷、烟气参数、NOX含量以及出口NH3的逃逸率自动控制喷氨量,优先保证氨逃逸率的情况下,满足系统脱硝效率。
∙针对脱硝还原剂,可以提供多种系统:液氨系统和尿素系统,博奇所提供的尿素催化水解系统具有安全、响应快、起停迅速以及能耗低等特点,可以为重视安全的业主提供最佳的脱硝解决方案。
SCR系统的工作原理
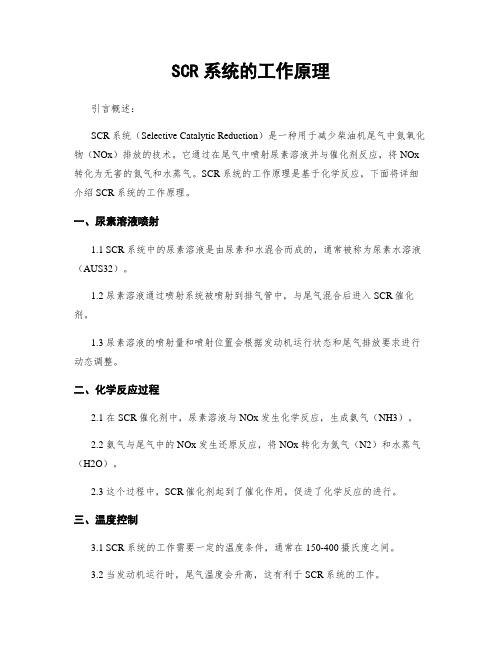
SCR系统的工作原理引言概述:SCR系统(Selective Catalytic Reduction)是一种用于减少柴油机尾气中氮氧化物(NOx)排放的技术。
它通过在尾气中喷射尿素溶液并与催化剂反应,将NOx 转化为无害的氮气和水蒸气。
SCR系统的工作原理是基于化学反应,下面将详细介绍SCR系统的工作原理。
一、尿素溶液喷射1.1 SCR系统中的尿素溶液是由尿素和水混合而成的,通常被称为尿素水溶液(AUS32)。
1.2 尿素溶液通过喷射系统被喷射到排气管中,与尾气混合后进入SCR催化剂。
1.3 尿素溶液的喷射量和喷射位置会根据发动机运行状态和尾气排放要求进行动态调整。
二、化学反应过程2.1 在SCR催化剂中,尿素溶液与NOx发生化学反应,生成氨气(NH3)。
2.2 氨气与尾气中的NOx发生还原反应,将NOx转化为氮气(N2)和水蒸气(H2O)。
2.3 这个过程中,SCR催化剂起到了催化作用,促进了化学反应的进行。
三、温度控制3.1 SCR系统的工作需要一定的温度条件,通常在150-400摄氏度之间。
3.2 当发动机运行时,尾气温度会升高,这有利于SCR系统的工作。
3.3 如果尾气温度过低,SCR系统可能需要加热以达到适宜的工作温度。
四、氨气浓度控制4.1 SCR系统需要保持适当的氨气浓度才干有效地将NOx转化为无害物质。
4.2 氨气浓度过高或者过低都会影响SCR系统的效率,因此需要进行精确控制。
4.3 通常通过传感器监测氨气浓度,并根据需要进行尿素溶液的喷射量调整。
五、催化剂维护5.1 SCR催化剂是SCR系统的核心组件,需要定期维护和更换。
5.2 催化剂表面可能会受到污染或者磨损,影响其催化性能,需要定期清洗或者更换。
5.3 定期检查SCR系统的各个部件,确保其正常运行和高效工作。
结论:SCR系统通过尿素溶液喷射、化学反应过程、温度控制、氨气浓度控制和催化剂维护等步骤,有效地减少柴油机尾气中的NOx排放。
SCR系统的工作原理

SCR系统的工作原理SCR(Selective Catalytic Reduction,选择性催化还原)系统是一种用于减少柴油发动机尾气中氮氧化物(NOx)排放的技术。
SCR系统通过将尿素溶液(也称为尿素水溶液或尿素SCR液)喷入到尾气中,与其中的NOx发生化学反应,将其转化为无害的氮气和水蒸汽。
SCR系统具有高效、高准确性和可靠性等优点,已广泛应用于柴油发动机和排放控制系统中。
1.尿素喷入:SCR系统中的尿素溶液储存在一个专用的尿素箱中,并通过管道输送到喷嘴。
喷嘴位于排气管的前部,将尿素溶液喷入排气管中。
2.尿素分解:喷入排气管中的尿素溶液先经过加热装置,将其加热到分解温度(通常为150-500摄氏度),使尿素溶解成氨和二氧化碳。
这一过程称为尿素分解反应。
3.氨与NOx反应:尿素分解后产生的氨与尾气中的NOx发生化学反应,生成氮气和水蒸汽。
这个反应称为SCR反应。
这个反应的催化剂是一个由铁、钒或铜等金属构成的催化剂,通常催化剂被涂覆在SCR系统的特殊陶瓷蜂窝体上,以增加反应的有效性。
4.尾气净化:SCR系统通过反应后,尾气中的NOx浓度大幅降低。
净化后的尾气释放到大气中,其中只含有少量的氮气和水蒸汽。
SCR系统的优点在于其高效性和准确性。
通过催化剂的作用,SCR系统可以在较低的温度下对NOx进行净化,而不同于其他排放控制技术需要较高的温度。
此外,SCR系统具有高准确性,因为可以根据发动机负载和排气温度来控制尿素喷射量,以适应不同的工况。
需要注意的是,SCR系统的正常运行需要保证尿素溶液的充足供应和定期的催化剂清洗和更换,以确保系统的长期稳定运行。
此外,SCR系统的运行可能受到环境温度和尿素溶液的氨浓度等因素的影响。
总结而言,SCR系统通过尿素分解和催化剂催化反应,将排气中的NOx转化为无害物质。
SCR系统具有高效、高准确性和可靠性等优点,已成为降低柴油发动机尾气排放中NOx的有效技术。
scr 工作原理

scr 工作原理
SCR(Silicon Controlled Rectifier)是一种控制型硅二极管,也称为可控硅。
它具有三个电极:阳极(A)、阴极(K)和控制极(G)。
SCR的工作原理如下:
1. 初始化:SCR处于非导通状态时,控制极与阴极之间施加的电压低于它的触发电压,阳极与阴极之间的电压为零。
2. 触发电压升高:当控制极与阴极之间的电压大于它的触发电压时,SCR会进入导通状态。
触发电压可由外部电压源或其他电子元器件提供。
3. 控制极信号:一旦SCR被触发,它将对外部的控制信号不再敏感。
这意味着,即使控制极与阴极之间的电压降低,SCR 仍然保持导通状态。
4. 正向偏压:在SCR导通状态下,阳极与阴极之间施加正向偏压有助于维持SCR的低电压降。
(注意:当阳极与阴极之间施加反向电压时,SCR将被关闭。
)
5. 关闭:为关闭SCR,需要降低阳极与阴极之间的电压。
这可以通过降低电流或改变外部电路中的元器件来实现。
总的来说,SCR的工作原理是通过对控制极施加足够的触发
电压,使之进入导通状态,并通过施加正向偏压来维持导通。
当需要关闭SCR时,只需降低阳极与阴极之间的电压即可。
SCR原理

• 1 晶闸管(SCR)晶体闸流管简称晶闸管,也称为可控硅整流元件(SCR),就是由三个PN结构成的一种大功率半导体器件。
在性能上,晶闸管不仅具有单向导电性,而且还具有比硅整流元件更为可贵的可控性,它只有导通与关断两种状态。
晶闸管的优点很多,例如:以小功率控制大功率,功率放大倍数高达几十万倍;反应极快,在微秒级内开通、关断;无触点运行,无火花、无噪声;效率高,成本低等。
因此,特别就是在大功率UPS供电系统中,晶闸管在整流电路、静态旁路开关、无触点输出开关等电路中得到广泛的应用。
晶闸管的弱点:静态及动态的过载能力较差,容易受干扰而误导通。
晶闸管从外形上分类主要有:螺栓形、平板形与平底形。
2 普通晶闸管的结构与工作原理晶闸管就是PNPN四层三端器件,共有三个PN结。
分析原理时,可以把它瞧作就是由一个PNP管与一个NPN管所组成,其等效图解如图1(a)所示,图1(b)为晶闸管的电路符号。
图1 晶闸管等效图解图2、1 晶闸管的工作过程晶闸管就是四层三端器件,它有J1、J2、J3三个PN结,可以把它中间的NP分成两部分,构成一个PNP型三极管与一个NPN型三极管的复合管。
当晶闸管承受正向阳极电压时,为使晶闸管导通,必须使承受反向电压的PN结J2失去阻挡作用。
每个晶体管的集电极电流同时就就是另一个晶体管的基极电流。
因此就是两个互相复合的晶体管电路,当有足够的门极电流Ig流入时,就会形成强烈的正反馈,造成两晶体管饱与导通。
设PNP管与NPN管的集电极电流分别为IC1与IC2,发射极电流相应为Ia与Ik,电流放大系数相应为α1=IC1/Ia与α2=IC2/Ik,设流过J2结的反相漏电流为ICO,晶闸管的阳极电流等于两管的集电极电流与漏电流的总与:Ia=IC1+IC2+ICO=α1Ia+α2Ik+ICO(1)若门极电流为Ig,则晶闸管阴极电流为:Ik=Ia+Ig。
因此,可以得出晶闸管阳极电流为:(2)硅PNP管与硅NPN管相应的电流放大系数α1与α2随其发射极电流的改变而急剧变化。
scr工作原理
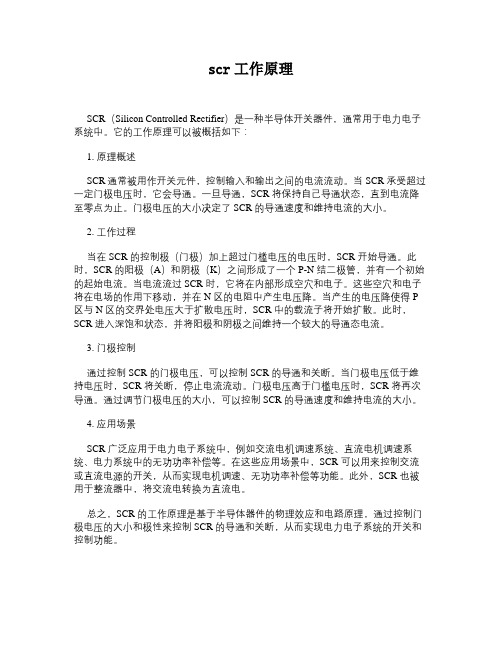
scr工作原理SCR(Silicon Controlled Rectifier)是一种半导体开关器件,通常用于电力电子系统中。
它的工作原理可以被概括如下:1. 原理概述SCR通常被用作开关元件,控制输入和输出之间的电流流动。
当 SCR 承受超过一定门极电压时,它会导通。
一旦导通,SCR 将保持自己导通状态,直到电流降至零点为止。
门极电压的大小决定了 SCR 的导通速度和维持电流的大小。
2. 工作过程当在 SCR 的控制极(门极)加上超过门槛电压的电压时,SCR 开始导通。
此时,SCR 的阳极(A)和阴极(K)之间形成了一个 P-N 结二极管,并有一个初始的起始电流。
当电流流过 SCR 时,它将在内部形成空穴和电子。
这些空穴和电子将在电场的作用下移动,并在 N 区的电阻中产生电压降。
当产生的电压降使得 P 区与 N 区的交界处电压大于扩散电压时,SCR 中的载流子将开始扩散。
此时,SCR 进入深饱和状态,并将阳极和阴极之间维持一个较大的导通态电流。
3. 门极控制通过控制 SCR 的门极电压,可以控制 SCR 的导通和关断。
当门极电压低于维持电压时,SCR 将关断,停止电流流动。
门极电压高于门槛电压时,SCR 将再次导通。
通过调节门极电压的大小,可以控制 SCR 的导通速度和维持电流的大小。
4. 应用场景SCR 广泛应用于电力电子系统中,例如交流电机调速系统、直流电机调速系统、电力系统中的无功功率补偿等。
在这些应用场景中,SCR 可以用来控制交流或直流电源的开关,从而实现电机调速、无功功率补偿等功能。
此外,SCR 也被用于整流器中,将交流电转换为直流电。
总之,SCR 的工作原理是基于半导体器件的物理效应和电路原理,通过控制门极电压的大小和极性来控制 SCR 的导通和关断,从而实现电力电子系统的开关和控制功能。
SCR简介

SCR简介SCR是Selective(选择性)、Catalytic(催化)、Reduction(还原)的英文缩写。
其他排气后处理主要有非选择催化还原、NOx吸附转化器、氧化催化器、微粒捕集器等。
各优缺点如下:此外与美国减排路线相比,我们选择SCR的决定因素如下:1、我国能源资源有限,50%以上依赖进口。
SCR技术比EGR技术节油5%~7%。
2、我国目前连有水平不高,硫含量在250ppm 以上。
EGR要求含硫量在50ppm以下。
3、SCR技术有达到国IV以上的排放标准潜力。
国IV机型和国V机型可选用同一发动机技术平台因此,SCR技术是我国柴油机实现国IV、国V标准的最佳选择。
一、SCR设计目标:1、基本控制目标减少NOx排放50%以上氨气泄露控制在10ppm以下2、控制对象尿素供给量控制辅助空气供给量控制二、工作原理该系统运用选择性催化还原反应解决尾气中NOx问题1、反应利用还原剂NH3和NOx进行反应,将NOx还原成N2和H2O;NO + NO2 + 2NH3 →2N2 + 3H2O4NO +O2 + 4NH3 →4N2 + 6H2O2NO2 + O2 + 4NH3 → 3N2 + 6H2OSCR系统目前采用的还原剂是32.5%的尿素溶液。
尿素NH2CONH2加H2O后在高温下分解成NH3 和CO2:NH2CONH2 + H2O →2 NH3 + CO2反应中,尿素喷射进入尾气管中在高温条件下,不断分解出氨气,供给还原反应。
2、NOx转化率的影响因素㈠催化剂V2O5/TiO2基金属氧化物型催化剂具有价格低、脱硝效率高、选择性强、较宽的活性温度窗口(260~425℃)、抗中毒能力强、运行稳定可靠等优点。
㈡温度和气流速度(接触时间)气体流速的影响(单位时间单位体积催化剂处理的气体量)NOx的转化效率随接触时间的增加而增加㈢NH3/NOx摩尔比可见在比例1.0到1.2时,转化效率较高,而氨气泄露比例较低。
scr工艺脱硝原理

scr工艺脱硝原理SCR工艺脱硝原理一、介绍SCR(Selective Catalytic Reduction)工艺是一种利用氨水或尿素作为还原剂,通过催化剂将NOx转化为N2和H2O的脱硝技术。
该技术具有高效、稳定、可靠等特点,在电力、石化、钢铁等领域得到广泛应用。
二、反应机理1. NOx的生成NOx是指氮氧化物,包括NO和NO2两种。
在燃烧过程中,空气中的氮和氧反应生成N2和O2,但当温度较高时,氮分子会与游离的氧原子相遇形成NO。
此外,在燃料中含有较多的有机物或硫时,也会产生NOx。
2. SCR反应SCR反应是指将NH3或尿素注入到烟道脱硝装置中,与NOx发生化学反应生成N2和H2O。
SCR反应需要催化剂的存在,在催化剂表面上进行。
3. 催化剂常用的SCR催化剂是钒钛催化剂。
该催化剂具有高活性、耐久性好等特点。
在催化剂表面上,NH3或尿素分解为NH2和NH4,NH2与NOx反应生成N2和H2O。
三、工艺流程1. 氨水或尿素的制备氨水或尿素是SCR脱硝过程中的还原剂。
氨水通过合成氨法制备,尿素则通过碳酸二铵和氨水反应得到。
2. 进出口烟气处理进入SCR反应器前,需要对烟气进行预处理。
主要包括除尘、脱硫等工艺。
出口烟气需要再次进行除尘处理,以保证排放标准。
3. SCR反应器SCR反应器是SCR脱硝过程的核心部件。
在该装置中,将制备好的氨水或尿素喷入烟道中,在催化剂表面上与NOx发生化学反应生成N2和H2O。
4. 氨水或尿素喷雾系统在SCR反应器中喷洒氨水或尿素需要使用喷雾系统。
该系统需要保证稳定、均匀的喷洒量,并且能够适应不同温度下的使用。
5. 余热回收系统SCR脱硝过程会产生大量废热,如果不能有效回收利用,则会造成能源浪费。
因此,在SCR脱硝过程中需要设计余热回收系统,将废热回收利用。
四、影响因素1. 温度SCR反应需要在一定温度范围内进行。
通常情况下,SCR反应的最佳温度为250℃~400℃。
scr催化剂类型

scr催化剂类型SCR催化剂类型催化还原技术(Selective Catalytic Reduction,SCR)是一种用于降低柴油车和燃煤电厂氮氧化物(NOx)排放的成熟技术。
在SCR 系统中,催化剂扮演着至关重要的角色,它能够催化氨气(NH3)与NOx发生反应,生成无害的氮气(N2)和水(H2O)。
根据催化剂的类型和组成,SCR催化剂可以分为多种不同的类型。
本文将介绍其中几种常见的SCR催化剂类型。
1. 钒基SCR催化剂钒基SCR催化剂是SCR系统中最常用的催化剂之一。
它主要由氧化钒(V2O5)和一些辅助氧化物组成。
钒基SCR催化剂具有较高的催化活性和良好的热稳定性,能够在较宽的温度范围内有效降低排放物。
此外,钒基SCR催化剂还具有较低的硫化物敏感性,能够减少硫化物对催化剂的毒化作用。
2. 钼基SCR催化剂钼基SCR催化剂是另一种常见的SCR催化剂类型。
它主要由氧化钼(MoO3)和一些辅助氧化物组成。
钼基SCR催化剂具有良好的催化活性和较高的选择性,能够在较低的温度下实现高效的NOx减排。
此外,钼基SCR催化剂还具有较高的硫化物抵抗能力,能够在高硫燃料条件下保持催化活性。
3. 铜铬基SCR催化剂铜铬基SCR催化剂是一种新型的SCR催化剂类型。
它主要由氧化铜(CuO)和氧化铬(Cr2O3)组成。
铜铬基SCR催化剂具有良好的催化活性和较高的选择性,能够在较宽的温度范围内实现高效的NOx减排。
此外,铜铬基SCR催化剂还具有较高的耐高温性能,能够在高温条件下保持催化活性。
4. 银基SCR催化剂银基SCR催化剂是一种高效的SCR催化剂类型。
它主要由氧化银(Ag2O)和一些辅助氧化物组成。
银基SCR催化剂具有较高的催化活性和较低的活化能,能够在较低的温度下实现高效的NOx减排。
此外,银基SCR催化剂还具有较高的耐硫性能,能够在高硫燃料条件下保持催化活性。
5. 铂基SCR催化剂铂基SCR催化剂是一种高性能的SCR催化剂类型。
scr的正常值
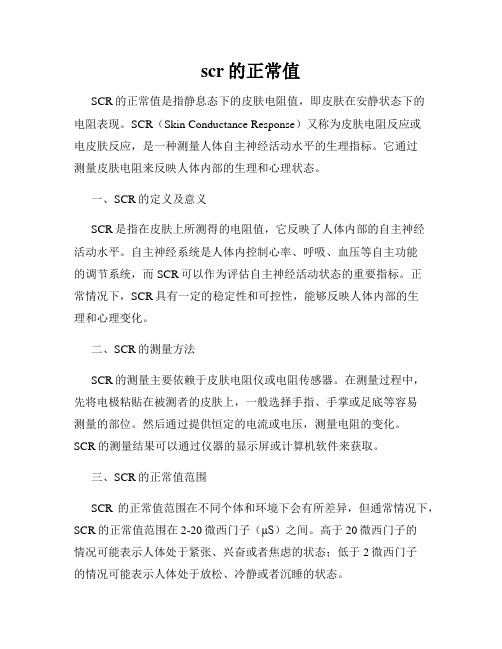
scr的正常值SCR的正常值是指静息态下的皮肤电阻值,即皮肤在安静状态下的电阻表现。
SCR(Skin Conductance Response)又称为皮肤电阻反应或电皮肤反应,是一种测量人体自主神经活动水平的生理指标。
它通过测量皮肤电阻来反映人体内部的生理和心理状态。
一、SCR的定义及意义SCR是指在皮肤上所测得的电阻值,它反映了人体内部的自主神经活动水平。
自主神经系统是人体内控制心率、呼吸、血压等自主功能的调节系统,而SCR可以作为评估自主神经活动状态的重要指标。
正常情况下,SCR具有一定的稳定性和可控性,能够反映人体内部的生理和心理变化。
二、SCR的测量方法SCR的测量主要依赖于皮肤电阻仪或电阻传感器。
在测量过程中,先将电极粘贴在被测者的皮肤上,一般选择手指、手掌或足底等容易测量的部位。
然后通过提供恒定的电流或电压,测量电阻的变化。
SCR的测量结果可以通过仪器的显示屏或计算机软件来获取。
三、SCR的正常值范围SCR的正常值范围在不同个体和环境下会有所差异,但通常情况下,SCR的正常值范围在2-20微西门子(μS)之间。
高于20微西门子的情况可能表示人体处于紧张、兴奋或者焦虑的状态;低于2微西门子的情况可能表示人体处于放松、冷静或者沉睡的状态。
四、SCR的影响因素SCR的数值会受到多种因素的影响,因此在测量SCR时应考虑以下因素:1. 温度:低温会导致SCR下降,而高温会导致SCR升高。
2. 湿度:潮湿的环境会导致SCR增加。
3. 环境噪音:噪音会干扰SCR的测量结果。
4. 情绪和心理状态:紧张、焦虑、兴奋等情绪或心理状态会导致SCR的升高。
五、SCR的临床应用SCR的测量在心理学、生理学、医学和人机交互等领域有着广泛的应用。
在心理学研究中,SCR可以用来评估情绪、压力和认知负荷等心理状态;在人机交互中,SCR可以被用作评估用户体验和情感反馈的指标;在临床医学中,SCR可以辅助诊断一些心理疾病,如焦虑症和自闭症等。
SCR系统的工作原理

SCR系统的工作原理SCR系统(Selective Catalytic Reduction,选择性催化还原)是一种用于减少柴油发动机尾气中氮氧化物(NOx)排放的先进排放控制技术。
它通过将尿素溶液(也称为尿素水溶液或尿素选择性催化还原剂)喷入排气管中,与尾气中的NOx 发生化学反应,将其转化为无害的氮气和水蒸气。
SCR系统由以下几个主要组成部分组成:储液器、尿素泵、尿素喷嘴、尿素溶液喷射系统、SCR催化剂和氨气传感器。
1. 储液器:储液器是用于存放尿素溶液的容器。
尿素溶液通常是在车辆加油站加注的,然后通过管道输送到储液器中。
储液器通常位于车辆底盘的某个位置,以便更换和维护。
2. 尿素泵:尿素泵是用于将尿素溶液从储液器中抽取并供给喷嘴的装置。
尿素泵通常由电动泵组成,可以根据需要调节尿素溶液的供给量。
3. 尿素喷嘴:尿素喷嘴是将尿素溶液喷射到排气管中的装置。
它通常位于排气管的某个位置,以确保尿素溶液能够与排气中的NOx充分混合。
4. 尿素溶液喷射系统:尿素溶液喷射系统是将尿素溶液从储液器经尿素泵输送到尿素喷嘴的管道系统。
它包括尿素泵、输送管道、过滤器等组件,以确保尿素溶液的稳定供给和清洁。
5. SCR催化剂:SCR催化剂是SCR系统的核心部分,它通常位于排气管中。
SCR催化剂由一种或多种金属催化剂组成,例如钒、钼或铈。
当尿素溶液喷射到SCR催化剂上时,催化剂会促使尿素溶液中的氨气与NOx发生还原反应,将其转化为氮气和水蒸气。
6. 氨气传感器:氨气传感器用于监测SCR系统中氨气的浓度。
它位于SCR催化剂附近,可以实时监测氨气的浓度,并将相关信息传输给发动机控制单元。
发动机控制单元可以根据氨气传感器的反馈信号来调节尿素溶液的供给量,以确保SCR系统的有效工作。
SCR系统的工作原理如下:1. 尿素溶液喷射:当发动机运行时,尿素泵会将尿素溶液从储液器中抽取,并通过喷嘴喷射到排气管中。
2. 氨气生成:尿素溶液在排气管中加热,分解为氨气(NH3)和二氧化碳(CO2)。
SCR系统的工作原理

SCR系统的工作原理SCR系统(Selective Catalytic Reduction System)是一种用于减少柴油机尾气中氮氧化物(NOx)排放的技术。
它通过将尿素溶液(也称为尿素水解液或者尿素SCR液)喷入尾气中,与氮氧化物发生化学反应,将其转化为无害的氮气和水蒸气。
下面将详细介绍SCR系统的工作原理。
1. SCR系统的组成SCR系统主要由尿素溶液供应系统、尿素喷射系统、催化剂和控制系统组成。
- 尿素溶液供应系统:负责储存和供应尿素溶液,通常使用尿素水解液,其主要成份为尿素和去离子水。
- 尿素喷射系统:将尿素溶液喷射到尾气中,通常使用喷射嘴进行喷射,喷射嘴的位置通常位于催化剂前方。
- 催化剂:SCR系统中的催化剂通常采用氨基酸盐,如氨基磺酸盐,催化剂的作用是加速尿素溶液与氮氧化物的反应。
- 控制系统:通过传感器监测尾气中的氮氧化物浓度和温度,并根据监测结果控制尿素喷射量,以保证SCR系统的工作效果。
2. SCR系统的工作原理SCR系统的工作原理基于尿素溶液(尿素水解液)与氮氧化物的化学反应。
具体的工作过程如下:- 尾气进入SCR系统:当柴油机运行时,尾气经过排气管进入SCR系统。
- 尾气预处理:在进入SCR系统之前,尾气经过一系列的预处理,如颗粒物过滤器(DPF)和氧化催化剂(DOC),以去除颗粒物温和体污染物。
- 尿素溶液喷射:尿素喷射系统根据控制系统的指令,将适量的尿素溶液喷射到尾气中。
尿素溶液在喷射过程中会迅速水解,生成氨气(NH3)。
- 氨气与氮氧化物反应:尾气中的氨气与氮氧化物发生化学反应。
在催化剂的作用下,氨气与氮氧化物发生选择性催化还原反应,将氮氧化物转化为无害的氮气和水蒸气。
- 尾气排放:经过SCR系统的处理,尾气中的氮氧化物被有效地减少,只剩下无害的氮气和水蒸气。
最后,处理后的尾气通过排气管排放到大气中。
3. SCR系统的优势和应用SCR系统具有以下优势:- 高效降低氮氧化物排放:SCR系统能够将柴油机尾气中的氮氧化物排放降低到较低水平,达到国家和地区的排放标准要求。
scr催化剂成分

scr催化剂成分
摘要:
1.SCR 催化剂的概述
2.SCR 催化剂的主要成分
3.SCR 催化剂的辅助成分
4.SCR 催化剂的制备方法
5.SCR 催化剂的应用领域
正文:
一、SCR 催化剂的概述
选择性催化还原(Selective Catalytic Reduction,简称SCR)是一种用于降低柴油车尾气排放中氮氧化物(NOx)的有效技术。
SCR 催化剂是这一技术的核心部分,其作用是在一定的温度和气氛下,将氮氧化物与还原剂(如尿素水溶液)发生反应,将其转化为无害的氮和水。
二、SCR 催化剂的主要成分
SCR 催化剂的主要成分通常包括两种,一种是载体,如氧化铝
(Al2O3)、二氧化钛(TiO2)和硅胶等;另一种是活性组分,如贵金属(Pt、Pd、Rh 等)和非贵金属(Cu、Fe、Co、Mn 等)。
三、SCR 催化剂的辅助成分
除了主要成分外,SCR 催化剂还包含一些辅助成分,如分散剂、稳定剂和载体改性剂等。
这些辅助成分可以提高催化剂的性能,如抗中毒能力、热稳定性和活性等。
四、SCR 催化剂的制备方法
SCR 催化剂的制备方法主要包括湿法、干法和溶胶- 凝胶法等。
这些方法的共同特点是将活性组分和载体混合,并通过一定的工艺过程形成具有良好分散性和稳定性的催化剂。
五、SCR 催化剂的应用领域
SCR 催化剂广泛应用于柴油车尾气净化领域,以满足严格的排放法规要求。
此外,SCR 催化剂还在其他领域有一定的应用,如工业废气处理、燃烧优化和氢气制备等。
总之,SCR 催化剂是一种具有重要应用价值的环保催化剂,其成分和制备方法对其性能和应用领域具有重要影响。
SCR系统的工作原理
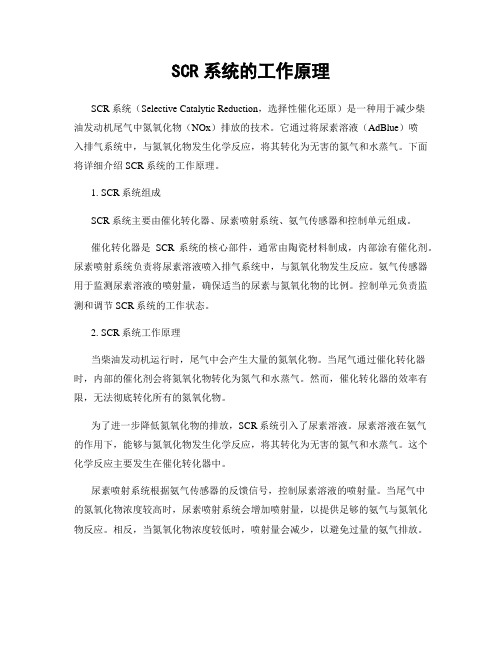
SCR系统的工作原理SCR系统(Selective Catalytic Reduction,选择性催化还原)是一种用于减少柴油发动机尾气中氮氧化物(NOx)排放的技术。
它通过将尿素溶液(AdBlue)喷入排气系统中,与氮氧化物发生化学反应,将其转化为无害的氮气和水蒸气。
下面将详细介绍SCR系统的工作原理。
1. SCR系统组成SCR系统主要由催化转化器、尿素喷射系统、氨气传感器和控制单元组成。
催化转化器是SCR系统的核心部件,通常由陶瓷材料制成,内部涂有催化剂。
尿素喷射系统负责将尿素溶液喷入排气系统中,与氮氧化物发生反应。
氨气传感器用于监测尿素溶液的喷射量,确保适当的尿素与氮氧化物的比例。
控制单元负责监测和调节SCR系统的工作状态。
2. SCR系统工作原理当柴油发动机运行时,尾气中会产生大量的氮氧化物。
当尾气通过催化转化器时,内部的催化剂会将氮氧化物转化为氮气和水蒸气。
然而,催化转化器的效率有限,无法彻底转化所有的氮氧化物。
为了进一步降低氮氧化物的排放,SCR系统引入了尿素溶液。
尿素溶液在氨气的作用下,能够与氮氧化物发生化学反应,将其转化为无害的氮气和水蒸气。
这个化学反应主要发生在催化转化器中。
尿素喷射系统根据氨气传感器的反馈信号,控制尿素溶液的喷射量。
当尾气中的氮氧化物浓度较高时,尿素喷射系统会增加喷射量,以提供足够的氨气与氮氧化物反应。
相反,当氮氧化物浓度较低时,喷射量会减少,以避免过量的氨气排放。
控制单元是SCR系统的大脑,它通过监测氨气传感器的反馈信号,实时调节尿素喷射系统的工作状态。
控制单元还可以与发动机控制单元进行通信,以实现更精确的控制和协调。
3. SCR系统的优势和局限性SCR系统具有以下优势:- 高效降低氮氧化物排放:SCR系统能够将尾气中的氮氧化物转化为无害物质,有效降低排放。
- 适应性强:SCR系统适合于各种柴油发动机,无论是小型车辆还是重型卡车。
- 长期稳定性:SCR系统的催化转化器具有较长的使用寿命,能够在长期内稳定工作。
scr指标 10
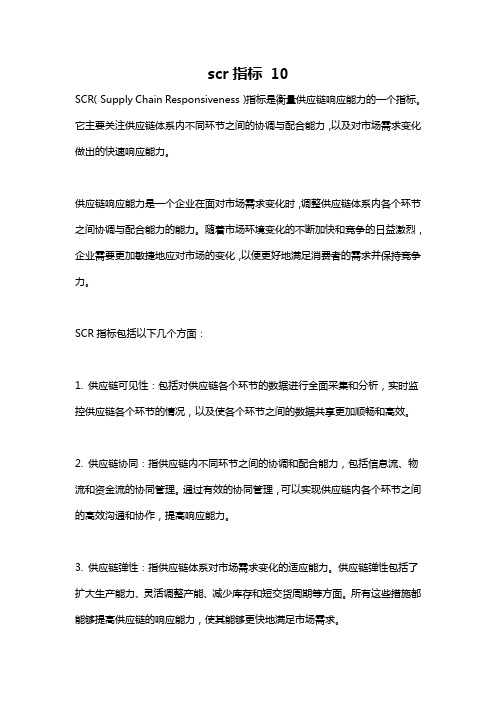
scr指标10SCR(Supply Chain Responsiveness)指标是衡量供应链响应能力的一个指标。
它主要关注供应链体系内不同环节之间的协调与配合能力,以及对市场需求变化做出的快速响应能力。
供应链响应能力是一个企业在面对市场需求变化时,调整供应链体系内各个环节之间协调与配合能力的能力。
随着市场环境变化的不断加快和竞争的日益激烈,企业需要更加敏捷地应对市场的变化,以便更好地满足消费者的需求并保持竞争力。
SCR指标包括以下几个方面:1. 供应链可见性:包括对供应链各个环节的数据进行全面采集和分析,实时监控供应链各个环节的情况,以及使各个环节之间的数据共享更加顺畅和高效。
2. 供应链协同:指供应链内不同环节之间的协调和配合能力,包括信息流、物流和资金流的协同管理。
通过有效的协同管理,可以实现供应链内各个环节之间的高效沟通和协作,提高响应能力。
3. 供应链弹性:指供应链体系对市场需求变化的适应能力。
供应链弹性包括了扩大生产能力、灵活调整产能、减少库存和短交货周期等方面。
所有这些措施都能够提高供应链的响应能力,使其能够更快地满足市场需求。
4. 供应链创新:指供应链体系内不断引入新的技术和方法,以提高响应能力。
供应链创新包括了信息技术的应用、供应链网络优化、物流管理创新等方面。
这些创新能够实现供应链内各个环节之间的快速信息传递,提高物流效率,从而提高供应链的响应能力。
以上是SCR指标的一些主要方面。
供应链响应能力对于企业来说至关重要,它不仅能够提高企业对市场需求的快速响应能力,还能够提高企业的生产效率和灵活性,降低企业的运营成本,提高企业的竞争力。
因此,企业应该重视SCR指标的改善,并积极采取措施来提高供应链的响应能力。
scr电气符号

scr电气符号SCR电气符号是指隔流触发晶闸管的电学符号,它是一种三极元件,用于实现潮流控制,广泛应用于电力电子和电机传动领域。
在电路设计和电子工程师的工作中,了解和掌握SCR电气符号的绘制方法和使用规范显得尤为重要。
以下是详细的步骤阐述。
第一步:打开电气符号绘制软件或应用首先,需要准备一款电气符号绘制工具或软件,例如AutoCAD、CorelDRAW等专业绘图软件,或者SolidWorks Electrical等电气CAD软件。
也可以使用在线绘制工具进行绘制,例如SmartDraw、Edraw等。
无论使用哪种软件,都需要打开软件并创建一个新的绘图页。
第二步:确定绘制比例和尺寸在绘制SCR电气符号之前,需要先确定绘制比例和尺寸。
比例是绘图中物体实际大小和图纸大小的比例,常用的比例有1:1、1:2和1:5等。
尺寸则是指实际物体的长度、宽度和高度等度量。
第三步:绘制SCR电气符号在绘图页上,使用线条、圆形、矩形等基本绘图工具,按照下列步骤绘制SCR电气符号:1.绘制基本形状,先绘制一个框框作为SCR电气符号的边框,并在框框内部绘制一个箭头。
2.添加标志,绘制三个箭头,分别排列在SCR符号的左侧、右侧和上方,表示控制电极(G),主电极(K)和阳极(A)。
3.添加注释,增加符号的易读性,可以在箭头上面或下面添加文字注释,“G”表示门极,“K”表示阳极,“A”表示主电极。
完成SCR电气符号绘制后,还需要进行检查和调整,确保符合规范和要求。
第四步:使用SCR电气符号在电路图或电子设备设计中,可以通过插入SCR电气符号的方式来使用它。
在插入时,需要根据实际需求对符号进行缩放和调整位置,以达到最佳的视觉效果和易读性。
总结以上是关于SCR电气符号绘制方法的步骤和规范。
熟练掌握SCR电气符号的绘制和使用,有助于电子工程师在电路设计和电子设备开发中更加高效地工作。
除此之外,还需要注意规范和标准化,以确保符号的可读性和可靠性。
scr指标
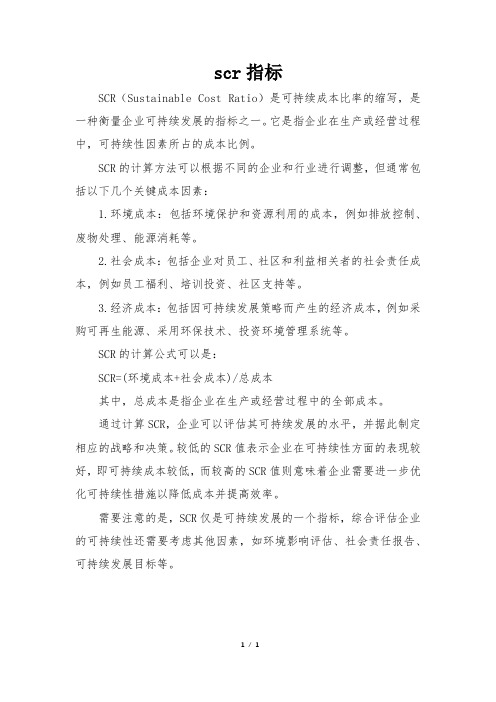
scr指标
SCR(Sustainable Cost Ratio)是可持续成本比率的缩写,是一种衡量企业可持续发展的指标之一。
它是指企业在生产或经营过程中,可持续性因素所占的成本比例。
SCR的计算方法可以根据不同的企业和行业进行调整,但通常包括以下几个关键成本因素:
1.环境成本:包括环境保护和资源利用的成本,例如排放控制、废物处理、能源消耗等。
2.社会成本:包括企业对员工、社区和利益相关者的社会责任成本,例如员工福利、培训投资、社区支持等。
3.经济成本:包括因可持续发展策略而产生的经济成本,例如采购可再生能源、采用环保技术、投资环境管理系统等。
SCR的计算公式可以是:
SCR=(环境成本+社会成本)/总成本
其中,总成本是指企业在生产或经营过程中的全部成本。
通过计算SCR,企业可以评估其可持续发展的水平,并据此制定相应的战略和决策。
较低的SCR值表示企业在可持续性方面的表现较好,即可持续成本较低,而较高的SCR值则意味着企业需要进一步优化可持续性措施以降低成本并提高效率。
需要注意的是,SCR仅是可持续发展的一个指标,综合评估企业的可持续性还需要考虑其他因素,如环境影响评估、社会责任报告、可持续发展目标等。
1/ 1。
简述scr的工作原理
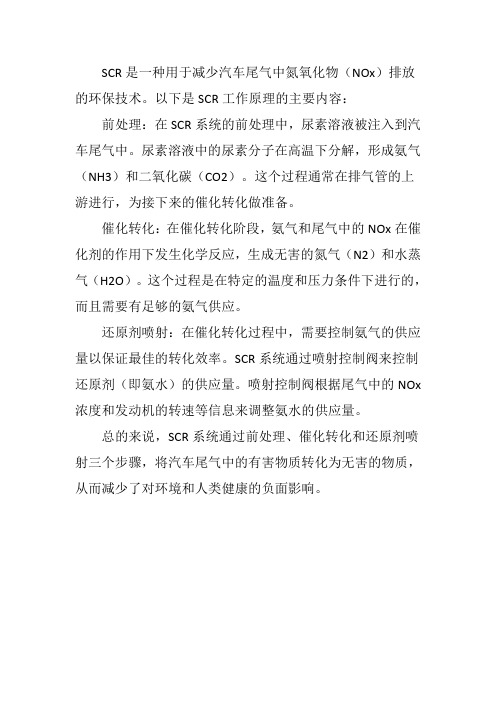
SCR是一种用于减少汽车尾气中氮氧化物(NOx)排放的环保技术。
以下是SCR工作原理的主要内容:
前处理:在SCR系统的前处理中,尿素溶液被注入到汽车尾气中。
尿素溶液中的尿素分子在高温下分解,形成氨气(NH3)和二氧化碳(CO2)。
这个过程通常在排气管的上游进行,为接下来的催化转化做准备。
催化转化:在催化转化阶段,氨气和尾气中的NOx在催化剂的作用下发生化学反应,生成无害的氮气(N2)和水蒸气(H2O)。
这个过程是在特定的温度和压力条件下进行的,而且需要有足够的氨气供应。
还原剂喷射:在催化转化过程中,需要控制氨气的供应量以保证最佳的转化效率。
SCR系统通过喷射控制阀来控制还原剂(即氨水)的供应量。
喷射控制阀根据尾气中的NOx 浓度和发动机的转速等信息来调整氨水的供应量。
总的来说,SCR系统通过前处理、催化转化和还原剂喷射三个步骤,将汽车尾气中的有害物质转化为无害的物质,从而减少了对环境和人类健康的负面影响。
- 1、下载文档前请自行甄别文档内容的完整性,平台不提供额外的编辑、内容补充、找答案等附加服务。
- 2、"仅部分预览"的文档,不可在线预览部分如存在完整性等问题,可反馈申请退款(可完整预览的文档不适用该条件!)。
- 3、如文档侵犯您的权益,请联系客服反馈,我们会尽快为您处理(人工客服工作时间:9:00-18:30)。
Two-stage catalyst system for selective catalytic reduction of NO x byNH 3at low temperaturesMin Kang a ,Dae Jung Kim b ,*,Eun Duck Park c ,Ji Man Kim a ,Jae Eui Yie d ,Seoung Hyun Kim e ,Louisa Hope-Weeks b ,Edward M.Eyring faDepartment of Chemistry and Sungkyunkwan Advanced Institute of Nano Technology,Sungkyunkwan University,Suwon 440-746,South KoreabDepartment of Chemistry and Biochemistry,Texas Tech University,Lubbock,TX 769409,USAcDepartment of Chemical Engineering and Division of Energy Systems Research,Ajou University,Suwon 443-749,South KoreadDepartment of Applied Chemistry,Ajou University,Suwon 443-749,South KoreaeDepartment of Environmental Engineering and Biotechnology,Myongji University,Yongin 449-728,South KoreafDepartment of Chemistry,University of Utah,Salt Lake City,UT 84112,USAReceived 27October 2005;received in revised form 30June 2006;accepted 19July 2006Available online 6September 2006AbstractThree catalysts,1wt.%Pt/Al 2O 3,20wt.%Cu/Al 2O 3,and 1wt.%Pt–20wt.%Cu/Al 2O 3were evaluated for the oxidation of NO by O 2and the selective catalytic reduction (SCR)of NO x by NH 3in the absence and presence of H 2O.The Pt/Al 2O 3catalyst exhibited the largest values in NO oxidation efficiency and NO x removal efficiency among the three catalysts.The presence of H 2O caused a drop in the NO oxidation and the SCR activities.The SCR performance was significantly improved when Pt/Al 2O 3and Cu/Al 2O 3catalysts were employed sequentially in a reactor.The highest SCR performance was achieved using two separate stages:oxidation of NO by O 2over the Pt/Al 2O 3catalyst followed by reduction of NO 2by NH 3over the Cu/Al 2O 3catalyst.Under the condition with H 2O,the two-stage catalyst system showed NO x removal efficiency over 80%at low temperatures below 2008C,which was the highest value among the catalyst systems used in this study.The physical and chemical properties of the catalysts were determined using nitrogen adsorption,XRD,TPR,and pulse CO chemisorption experiments.#2006Elsevier B.V .All rights reserved.Keywords:NH 3SCR;NO oxidation;Cu catalyst;Pt catalyst;Two-stage catalyst system1.IntroductionNO x including NO and NO 2impacts on the formation of tropospheric ozone,photochemical smog and acid rain,and thus NO x removal from combustion sources has been a major environmental concern for protecting air quality.A large number of research studies addressing the conversion of NO x into N 2and H 2O have focused on developing catalyst systems.Highly effective NO x removal can be achieved by noble metal based three-way catalysts,a technique now widely applied for the purification of automobile emissions.The three-way catalyst exhibits high NO x removal efficiency when a stoichiometric air-to-fuel ratio prevails while it is much lesseffective for controlling NO x emissions from combustion processes,when a large amount of oxygen is present [1,2].One of the most promising techniques for removing NO x in the presence of a great excess of oxygen is selective catalytic reduction (SCR),in which catalysts are generally employed with reducing agents such as hydrocarbons (HCs)or ammonia (NH 3)[3–6].The SCR performance over a catalyst can be improved when both NO and NO 2are present rather than when only NO is present in emissions.Furthermore,the NO x removal efficiency can be enhanced through the combination of an oxidation catalyst of NO to NO 2by O 2and a reduction catalyst of NO x (NO,NO 2)to N 2and H 2O by a reducing agent.Iwamoto et al.[7]reported that combined catalysts based on metal ion-exchanged zeolites were employed with C 2H 4as the reductant in an HC-SCR reaction,but the NO x removal efficiency was slightly improved by maintaining the same operating temperatures of the oxidation and reduction catalysts./locate/apcatbApplied Catalysis B:Environmental 68(2006)21–27*Corresponding author.Tel.:+18067425073x272;fax:+18067421289.E-mail address:kim8682@ (D.J.Kim).0926-3373/$–see front matter #2006Elsevier B.V .All rights reserved.doi:10.1016/j.apcatb.2006.07.013To enhance the SCR performance of the combined catalyst system,the oxidation and reduction catalysts should be operated at different temperatures to show their maximum activity because of the differences in the catalytic character-istics of the two catalysts.Recently,Madia et al.[8]applied this idea to an NH3-SCR process.They found that NO x conversion was increased when Pt/cordierite was used as an oxidation catalyst and V2O5–WO3/TiO2was employed as a reduction catalyst.Epling et al.[9]showed that the efficiency of NO x conversion was increased by using NO x storage/reduction (NSR)catalyst in which NO x storage materials such as Ba were added.Kim et al.[10]reported that NO x removal efficiency was increased using a combined system consisting of a pulse corona discharge and a Co-ZSM-5catalyst.They found that NO2 formed by the pulse corona discharge improved the NO x removal over the catalyst.Gieshoff et al.[11]claimed that the addition of the Pt-based oxidation catalyst to the V2O5based SCR catalyst increased the NO x removal efficiency.The present work reports a combined catalyst system having a high SCR performance at low temperatures through the combinations of the three catalysts,Pt/Al2O3,Cu/Al2O3,and Pt–Cu/Al2O3.Characteristics required for oxidation of NO by O2and conversion of NO x by NH3over the catalysts are studied. The impact of water vapor on the NO x oxidation and SCR performances of the catalyst system is investigated.The physical and chemical properties of the catalysts were evaluated using nitrogen adsorption,X-ray diffraction (XRD),temperature-programmed reduction(TPR)and pulse CO chemisorption experiments.2.Experimental2.1.Catalyst preparationAbout1wt.%Pt/Al2O3was a commercial catalyst (Aldrich),and it was used in this study after calcination in air at4508C for2h.About20wt.%Cu/Al2O3was prepared by an incipient wetness impregnation method.An ethanol solution containing copper nitrate hydrate(Aldrich,Cu(NO3)2Áx H2O) was mixed with g-alumina(BET surface area=201.9m2/g), and the mixture was evacuated in a rotary evaporator at608C for2h.The slurry obtained was dried at1008C for24h,and calcined in air at5008C for4h.The alumina supported Pt–Cu catalyst was prepared with the co-impregnation of1wt.%Pt and20wt.%Cu on the g-alumina.Precursors of Pt and Cu were copper nitrate hydrate and tetraammineplatinum nitrate (Aldrich,Pt(NH3)4(NO3)2).The drying and calcination conditions for the slurry obtained from this co-impregnation were the same as for the incipient wetness impregnation method.2.2.Characterization of catalystsNitrogen adsorption experiments were carried out using an Autosorb-1instrument(Quantachrom)at liquid nitrogen temperature.The catalyst samples were preliminarily degassed at1008C overnight.BET surface areas of the catalysts were calculated from the nitrogen adsorption isotherms obtained.X-ray diffraction(XRD)tests were performed on a Rigaku D/MAC-III instrument using Cu K a radiation.The samples were scanned in the2u range of10–808.The XRD patterns of the samples were analyzed by a reference library search.Temperature-programmed reduction(TPR)spectra were recorded with a Micromeritics ASAP2010C TPR instrument equipped with a TCD detector.The TPR experiments were carried out in the range of30–9008C at a temperature ramp of 58C/min in a30ml/minflow of10%H2in Ar.Pulse CO chemisorption tests were performed in the same instrument as used in the TPR tests.The catalyst samples were pre-reduced in a30ml/minflow of H2at1008C for1h.The samples were cooled down to308C,and the0.1cm3pulses of a mixture of5%CO in N2were supplied to the samples until saturation of CO was reached.The amounts of CO chemisorbed were calculated from the data obtained from the pulse CO chemisorption tests.2.3.Activity testsActivity tests for the catalysts were carried out in a tubular quartz reactor(8mm i.d.).Before activity tests,a catalyst sample was treated with a mixture of5%O2in N2(30ml/min) at4008C for2h,and purged with N2at the same temperature for1h.After that,the sample was set to a predetermined temperature for the activity test.The inlet gases supplied to the reactor containing the sample were500ppm NO,500ppm NH3,5%O2,and N2.Water vapor(3.5%H2O)was generated by passing N2through the heated saturator containing de-ionized water,and loaded in the gas stream.Theflow rates of the inlet gases were controlled by massflow controllers(MKS). The gas hourly space velocity(GHSV)for all catalysts and combined catalyst systems was constant set at25,000hÀ1.The concentrations of NO and NO2in the inlet and outlet of the reactor were analyzed using a NO/NO2combustion gas analyzer(Euroton).3.Results and discussion3.1.CharacterizationTable1reports BET surface areas of the three catalysts: 1wt.%Pt/Al2O3,20wt.%Cu/Al2O3and1wt.%Pt–20wt.% Cu/Al2O3.The Pt/Al2O3catalyst had a larger BET surface area than the other catalysts.The BET surface area of the Pt–Cu/ Al2O3catalyst was slightly higher than that of the Cu/Al2O3 catalyst.Fig.1shows XRD patterns for the three catalysts. XRD patterns of Pt species on the Pt/Al2O3catalyst were not detected,indicating that Pt species were well dispersed with small particle sizes.The XRD results of two Cu-based catalysts revealed that CuO crystallites were formed on the catalysts. The average diameters of CuO crystallites were calculated using the widths at half-height of the peaks at2u=35.488in the XRD patterns and the Scherrer equation.As presented in Table1,the average diameter of CuO crystallites formed on theM.Kang et al./Applied Catalysis B:Environmental68(2006)21–27 22Cu/Al 2O 3catalyst is obviously smaller than the Pt–Cu/Al 2O 3catalyst.Fig.2shows TPR profiles of the three catalysts.The Pt/Al 2O 3catalyst exhibited two reduction peaks in the TPR curves.The first peak having a maximum intensity at 1978C is probably due to the reduction of Pt oxides strongly interacting with the support [12,13].The second peak at about 3808C may be attributed to a strong H 2chemisorption on metallic Pt [12].The Cu/Al 2O 3catalyst showed a main reduction peak at 2138C with a shoulder peak at about 1138C.The shoulder peak may be the reduction of well dispersed copper oxides on alumina surface [14,15].The main peak can be attributed to the reduction of bulk CuO particles [15].Interestingly,the Pt–Cu/Al 2O 3catalyst shows the same TPR pattern as the Cu/Al 2O 3catalyst.This result suggests that the TPR profile for the Pt–Cu/Al 2O 3catalyst is dominated by the reduction of Cu oxides.The amount of CO chemisorbed on the Pt/Al 2O 3catalyst,as shown in Table 1,is higher than on the Pt–Cu/Al 2O 3catalyst.Rioux and Vannice [16]reported that the amount of CO chemisorbed was decreased with increasing doping of Cu to a Pt-based catalyst.They insisted that copper species covered the Pt surface and decreased the number of available surface Pt atoms.The results obtained from XRD,TPR,and CO chemisorption tests suggest that Pt species on the Pt–Cu/Al 2O 3catalyst may be covered by copper oxide particles.3.2.Catalytic activityThe oxidation tests of NO to NO 2over the three catalysts:1wt.%Pt/Al 2O 3,20wt.%Cu/Al 2O 3and 1wt.%Pt–20wt.%Cu/Al 2O 3,were conducted in a gas mixture of 500ppm NO,5%O 2,and N 2.Fig.3shows the conversion of NO to NO 2over the three catalysts in the absence and presence of H 2O and the ratio of NO 2/NO x obtained at the thermodynamic equilibrium of the following reaction [8]:2NO þO 2¼2NO 2(1)The molar ratio of NO 2/NO x is largely decreased at tempera-tures over 2008C with decreasing NO 2concentration.Under the feed gas without H 2O,the conversion of NO to NO 2over the Pt/Al 2O 3catalyst is increased with rising temperature in a range of 100–2508C,and it shows the highest value of 70%at 2508C.After that,the conversion is significantly decreased because of the restriction of the thermodynamic equilibrium (Fig.3a).The conversion of NO to NO 2over the Cu/Al 2O 3catalyst is slowly increased with increasing temperature,and the maximum conversion is 4%at 4008C (Fig.3b).The Pt–Cu/Al 2O 3catalyst behaves according to the same pattern as the Cu/Al 2O 3catalyst in the NO oxidation (Fig.3c),indicating that the addition of Pt to the Cu/Al 2O 3catalyst does not make any contribution to enhancing the NO oxidation.This result confirms that most Pt particles may not be exposed at the surface of the Pt–Cu/Al 2O 3M.Kang et al./Applied Catalysis B:Environmental 68(2006)21–2723Fig.1.XRD patterns of the three catalysts:(a)1wt.%Pt/Al 2O 3;(b)20wt.%Cu/Al 2O 3;(c)1wt.%Pt–20wt.%Cu/Al 2O 3.Fig.2.Temperature-programmed reduction of the three catalysts:(a)1wt.%Pt/Al 2O 3;(b)20wt.%Cu/Al 2O 3;(c)1wt.%Pt–20wt.%Cu/Al 2O 3.Table 1BET surface areas,average crystalline diameters of Pt and Cu compounds,and the amounts of CO chemisorbed on the three catalysts:(a)1wt.%Pt/Al 2O 3;(b)20wt.%Cu/Al 2O 3;(c)1wt.%Pt–20wt.%Cu/Al 2O 3CatalystS a (m 2/g)CuO crystallite diameter b (nm)Co chemisorbed c (m mol/g cat.)1wt.%Pt/Al 2O 3148–3820wt.%Cu/Al 2O 39045–1wt.%Pt–20wt.%Cu/Al 2O 3108542a BET surface areas calculated from nitrogen isotherms.b CuO crystallite diameters calculated using the widths at half-height of the peaks at 2u =35.488in the XRD patterns and the Scherrer equation.cThe amounts of CO chemisorbed obtained from the pulse CO chemisorption tests.catalyst.This is consistent with the results of the XRD,TPR,and pulse CO chemisorption experiments described earlier.To elucidate the effect of H 2O on the conversion of NO to NO 2,3.5%water vapor was added to the gas stream.As shown in Fig.3,the introduction of H 2O causes the maximum NOconversion to decrease on a catalyst.The NO conversion for Pt/Al 2O 3is greatly decreased with addition of H 2O at the temperature range of 150–2508C (Fig.3a).However,for two Cu-based catalysts,the NO conversion is almost unchanged in the presence of H 2O at the same temperature range (Fig.3b and c).This result indicates that the Pt catalyst is more affected by H 2O than the Cu catalyst.Crocoll and Kureti [17]have reported that the decrease in the NO conversion on the Pt/Al 2O 3catalyst in the presence of H 2O is attributed to the irreversible H 2O adsorbed on the Pt surface.Mulla et al.[18]have suggested that for the Pt/Al 2O 3catalyst,H 2O may make the migration of impurities from the support to block the Pt sites,and consequently reduce the NO conversion.The conversions of NO and NO x to N 2and H 2O by 500ppm NH 3over the three catalysts in the absence and presence of H 2O are shown in Fig.4.In this study,NO and NO x conversions on a catalyst are defined asNO conversion ð%Þ¼ 1ÀNO outNO in Â100(2)NO x conversion ð%Þ¼ 1ÀðNO out þNO 2out ÞNO in Â100(3)Here,NO in is the concentration of NO at the inlet of the reactor,and NO out and NO 2out are the concentrations of NO and NO 2formed by the oxidation of NO at the outlet of the reactor,respectively.As shown in Fig.4,all catalysts show a similar pattern in NO x conversion in the absence of H 2O.The NO x conversion is increased with temperature,and reaches the largest value at 2008C.The NO x conversion is largely decreased with increasing temperature at temperatures over 2008C.It can be seen in Fig.4that for all catalysts,the NO x conversion is smaller than the NO conversion at temperatures over 2508C.Slavinskaya et al.[19]have reported that ammonia over a catalyst is preferentially reacted with oxygen at high temperatures and converted to NO x such as NO and N 2O.This reaction has been reported to occur more easily over metals such as Pt,Pd,Ni,Fe and Cu [19,20].Therefore,the significant decrease in the NO x conversion at high temperatures can be attributed to the depletion of ammonia and the increase of NO x concentration by the oxidation of ammonia to NO x .Comparing Fig.4a with Fig.4b,the maximum value of the NO x conversion over the Pt/Al 2O 3catalyst in the absence of H 2O is larger than that over the Cu/Al 2O 3catalyst.However,the NO x conversions over the Pt/Al 2O 3catalyst at temperatures below 1508C or over 3508C are lower than over the Cu/Al 2O 3catalyst.The results indicate that the NO x removal window of the Pt/Al 2O 3catalyst is narrower than that of the Cu/Al 2O 3catalyst.In the standard SCR reaction,NO is easily converted to N 2and H 2O by NH 3:4NO þ4NH 3þO 2!4N 2þ6H 2O(4)When both NO and NO 2are present,the following reaction proceeds much more rapidly than the above reaction (4):4NH 3þ2NO þ2NO 2!4N 2þ6H 2O(5)M.Kang et al./Applied Catalysis B:Environmental 68(2006)21–2724Fig.3.NO oxidation over the three catalysts in the absence and presence of H 2O:(a)1wt.%Pt/Al 2O 3;(b)20wt.%Cu/Al 2O 3;(c)1wt.%Pt–20wt.%Cu/Al 2O 3.Wallin et al.[21]have reported that the presence of NO2in the gas mixture enhanced the SCR performance of a catalyst.Sun et al.[22]have also proposed a reaction mechanism for the reduction of a mixture of NO and NO2by NH3.They have investigated that the reaction proceeds swiftly through the formation of ammonium nitrite,NH4NO2,which easily decom-poses to N2and H2O near1008C.Blanco et al.[23]have reported that the SCR reaction is faster and the SCR perfor-mance is higher in a mixture of NO and NO2than in pure NO.Therefore,it can be inferred that the difference in the maximum NO x conversion between the two catalysts is probably due to the difference in the amount of NO2produced from the oxidation of NO by O2.The Pt–Cu/Al2O3catalyst shows lower NO x removal efficiency than the Cu/Al2O3 catalyst.It is probable that the decrease in the dispersion of CuO with the addition of Pt causes the decrease in the SCR performance of the Pt–Cu/Al2O3catalyst.As shown in Fig.4,for the three catalysts the maximum NO x conversions at2008C are slightly decreased in the presence of H2O,but the NO x conversions at temperatures below or above 2008C are significantly decreased with the addition of H2O. Ramis et al.[24]have proposed that ammonia is adsorbed and activated on Lewis acid sites of a catalyst in the standard SCR reaction.Many researchers[24–26]have found that the presence of H2O converts some of the Lewis acid sites of the catalyst to Brønsted acid sites.The loss of the Lewis acid sites by the addition of H2O may cause the decrease in the SCR performance at temperatures below2008C.Moreover,as shown in Fig.3,the presence of H2O inhibits the conversion of NO to NO2at the low temperatures.The side SCR reaction(5) in the presence of H2O is less effective than in the absence of H2O.This may contribute to the decrease in the SCR activity at the low temperatures.Madia et al.[26]has reported that H2O at high temperatures gives rise to the surface concentration of the Lewis acid sites. They have insisted that ammonia is selectively oxidized on the Lewis acid sites,and the SCR selectivity is decreased with the increase of the Lewis acid sites by the presence of H2O. Therefore,the partial loss of SCR activity at temperatures over 2008C could be due to the increase of selective catalytic oxidation(SCO)of ammonia.bined catalyst systemsTo enhance the SCR performance,various combined catalyst systems using two catalysts:1wt.%Pt/g-Al2O3and 20wt.%Cu/Al2O3,were tested.Fig.5shows the SCR performances of two-bed catalyst systems in the absence of H2O.For the catalyst system of Fig.5a(system A),thefirst bed and second bed consisted of the Cu/Al2O3catalyst and the Pt/ Al2O3catalyst,respectively.The catalyst system of Fig.5b (system B)was in the reverse order of Fig.5a.The two catalysts had the same loading in the reactor.Both catalyst systems showed a wider NO x removal window than the single catalyst system having only the Pt catalyst.It is likely that the Cu/Al2O3 catalyst played a key role in the improvement of the NO removal window.The system B,as shown in Fig.5,has a larger value in the maximum NO x conversion than the system A has.This result implies that NO2formed on the Pt/Al2O3catalyst promotes the NO x removal efficiency over the Cu/Al2O3catalyst.To substantiate this speculation,a two-stage catalyst system using the two catalysts was developed as shown in Fig.6.M.Kang et al./Applied Catalysis B:Environmental68(2006)21–2725 Fig.4.NO and NO x conversions over the three catalysts in the absence andpresence of H2O:(a)1wt.%Pt/Al2O3;(b)20wt.%Cu/Al2O3;(c)1wt.%Pt–20wt.%Cu/Al2O3.The Pt/Al 2O 3catalyst was employed as the oxidation catalyst for the oxidation of NO by O 2,and the Cu/Al 2O 3catalyst was used as the reduction catalyst of NO x by NH 3,which was injected after the Pt/Al 2O 3catalyst.The NO and NO x removal efficiencies in the two-stage catalyst system in the absence and presence of H 2O are shown in Fig.7.The reaction temperature in the oxidation catalyst (1wt.%Pt/Al 2O 3)was set at a predetermined temperature between 100and 2508C,and the reaction temperature in theSCR catalyst (20wt.%Cu/Al 2O 3)was subsequently varied in a temperature range of 100–4008C.The NO and NO x removal efficiencies over the Cu/Al 2O 3catalyst in the absence of H 2O were increased with increasing bed temperature of the Pt/Al 2O 3catalyst.According to the result of Fig.3,the oxidation efficiency of NO over the Pt/Al 2O 3catalyst in the absence of H 2O was increased with increasing temperature in a temperature range of 100–2508C.The results,as shown in Fig.7,clearly indicate that the SCR performance over the Cu/Al 2O 3catalyst is significantly influenced by the concentration of NO 2formed over the Pt/Al 2O 3catalyst.When the bed temperature of the oxidation catalyst was maintained at 2508C,the SCR catalyst showed the highest NO and NO x conversions at low temperatures below 2008C.The NO and NO x removal efficiencies of the two-stage catalyst system at low tempera-tures below 2008C was much higher than those of the two-bed catalyst systems shown in Fig.5.To investigate the effect of H 2O on the SCR performance of the two-stage catalyst system,water vapor was supplied to theM.Kang et al./Applied Catalysis B:Environmental 68(2006)21–2726Fig.5.NO and NO x conversions in the two-bed catalyst systems in the absence of H 2O:(a)20wt.%Cu/Al 2O 3in the first bed and 1wt.%Pt/Al 2O 3in the second bed;(b)1wt.%Pt/Al 2O 3in the first bed and 1wt.%Pt/Al 2O 3in the secondbed.Fig.6.The schematic diagram for a two-stage catalyst system:1wt.%Pt/Al 2O 3as an oxidation catalyst of NO by O 2in the first stage and 20wt.%Cu/Al 2O 3as a reduction catalyst of NO x by NH 3in the secondstage.Fig.7.NO and NO x conversions for a two-stage catalyst system with respect to the bed temperature of the oxidation catalyst in the absence and presence of H 2O:(a)1008C without H 2O;(b)2008C without H 2O;(c)2508C without H 2O;(d)2508C with H 2O.gas stream before the oxidation catalyst.The bed temperature of the SCR catalyst was maintained at a determined temperature in the range of100–4008C,while the bed temperature of the oxidation catalyst was set to2508C.As shown in Fig.5,for the two-stage catalyst system the maximum NO x conversion at2008C was unchanged in the presence of H2O,and the NO x conversions at temperatures below and over 2008C were slightly decreased.In particular,in the presence of H2O,the two-stage catalyst system showed NO x removal efficiency over80%at low temperatures below2008C,which was the highest value among the catalyst systems used in this study.4.ConclusionsIn this study,the three catalysts:1wt.%Pt/Al2O3,20wt.% Cu/Al2O3,and1wt.%Pt–20wt.%Cu/Al2O3were prepared to investigate the oxidation of NO and the selective catalytic reduction(SCR)of NO x by NH3in the absence and presence of H2O.The addition of Pt to the Cu/Al2O3catalyst increased the average crystallite size of CuO,and consequently decreased the SCR performance of the Cu/Al2O3catalyst.The Pt/Al2O3 catalyst showed the highest NO oxidation and NO x removal efficiencies among the three catalysts.The addition of H2O inhibited both the NO oxidation and the SCR reaction,and consequently led to a decrease in the SCR performance of the catalyst.The two-stage catalyst system,in which Pt/Al2O3and Cu/ Al2O3catalysts were employed as the oxidation catalyst of NO and the reduction catalyst of NO x by NH3,showed the highest SCR performance at low temperatures below2008C in the absence and presence of H2O among the catalyst systems used in this present work.The SCR performance of the two-stage catalyst system was strongly influenced by the concentration of NO2formed over the oxidation catalyst.AcknowledgementsDr.Dae Jung Kim and Prof.Edward M.Eyring are grateful for partialfinancial support by the U.S.Department of Energy through the Consortium for Fossil Fuel Science(Contract DE-FC26-02NT41594).References[1]S.Matumoto,Catal.Today90(2004)183.[2]H.Yahiro,M.Iwamoto,Appl.Catal.A:Gen.222(2001)163.[3]R.Heck,Catal.Today53(1999)519.[4]D.Sun,W.F.Schneider,J.B.Adams,D.Sengupta,J.Phys.Chem.A108(2004)9365.[5]H.Imai,T.Ogawa,K.Sugimoto,M.Kataoka,Y.Tanaka,T.Ono,Appl.Catal.B:Environ.55(2005)259.[6]C.Shi,M.Cheng,Z.Qu,X.Bao,Appl.Catal.B:Environ.51(2004)171.[7]M.Iwamoto,T.Zengyo,A.M.Hernandez,H.Araki,Appl.Catal.B:Environ.17(1998)259.[8]G.Madia,M.Koebel,M.Elsener,A.Wokaun,Ind.Eng.Chem.Res.41(2002)3512.[9]W.S.Epling,J.E.Parks,G.C.Campbell,A.Yezerets,N.W.Currier,L.E.Campbell,Catal.Today96(2004)21.[10]M.Kim,K.Takashima,S.Katasura,A.Mizuno,J.Phys.D:Appl.Phys.34(2001)604.[11]J.Gieshoff,A.Scha¨fer-Sindlinger,P.C.Spurk,J.A.A.van den Tillaart,SAE Paper,2000,2000-01-0189.[12]A.Borgna,T.F.Garetta,C.R.Apesteguı´a,F.L.Normand,B.Moraweck,J.Catal.186(1999)433.[13]C.Hwang,C.Yeh,J.Mol.Catal.A:Chem.112(1996)295.[14]rsson,A.Andersson,Appl.Catal.B:Environ.24(2000)175.[15]M.Luo,P.Fang,M.He,Y.Xie,J.Mol.Catal.A:Chem.239(2005)243.[16]R.M.Rioux,M.A.Vannice,J.Catal.233(2005)147.[17]M.Crocoll,S.Kureti,J.Catal.229(2005)480.[18]S.S.Mulla,N.Chen,L.Cumaranatunge,W.N.Delgass,W.S.Epling,F.H.Ribeiro,Catal.Today114(2006)57.[19]E.M.Slavinskaya,S.A.Veniaminov,P.Notte,A.S.Ivanova,A.I.Bor-onin,Yu.A.Chesalov,I.A.Polukhina, A.S.Noskov,J.Catal.222 (2004)129.[20]G.Olofasson,A.Hinz,A.Andersson,Chem.Eng.Sci.59(2004)4113.[21]M.Wallin,C.Karlsson,M.Skoglundh,A.Palmqvist,J.Catal.218(2003)354.[22]Q.Sun,Z.Gao,H.Chen,W.M.H.Sachtler,J.Catal.201(2001)89.[23]J.Blanco,P.Avila,L.Marzo,Catal.Today17(1993)325.[24]G.Ramis,L.Yi,G.Busca,M.Turco,E.Kotur,R.J.Willey,J.Catal.157(1995)523.[25]N.Y.Topsoe,J.Catal.128(1991)499.[26]G.Madia,M.Koebel,M.Elsener,A.Wokaun,Ind.Eng.Chem.Res.41(2002)4008.M.Kang et al./Applied Catalysis B:Environmental68(2006)21–2727。