蓄热式燃烧炉课件资料
蓄热式焚烧炉原理

蓄热式焚烧炉原理
蓄热式焚烧炉是一种利用高温燃烧废物的设备,其原理是通过将废物投入炉内进行燃烧,释放高温热量,并将炉体内的热量储存起来,以在需要时再次利用。
蓄热式焚烧炉的主要组成部分包括燃烧炉膛、燃烧器、炉膛内壁、蓄热体和烟气尾气处理系统。
废物被投入燃烧炉膛中,燃烧炉膛中的燃烧器会在适当的空气供给下点火,并使废物燃烧成灰渣和烟气。
燃烧废物释放出的高温热量会被燃烧膛内壁的蓄热体吸收。
蓄热体通常由高热容量和热导率的材料制成,例如陶瓷或金属。
当蓄热体吸收和储存热量时,它会慢慢释放储存的热能,以保持燃烧炉内的高温。
这使得炉膛能够连续进行燃烧,即使在废物输入量不稳定或间断的情况下也能保持高效运行。
燃烧过程结束后,蓄热体中的热量可以通过烟气尾气处理系统进一步利用。
烟气尾气处理系统常常包括余热回收装置,用于回收和利用烟气中的热能。
通过将余热用于预热气体或水,可以降低能源消耗和减少环境污染。
蓄热式焚烧炉的原理使其能够高效利用废物燃烧所产生的热能,帮助降低废物处理的能耗和污染排放。
同时,由于炉膛内的高温可以持续维持,蓄热式焚烧炉也适用于处理具有高湿度或可燃性低的废物。
rto蓄热式焚烧炉工作原理
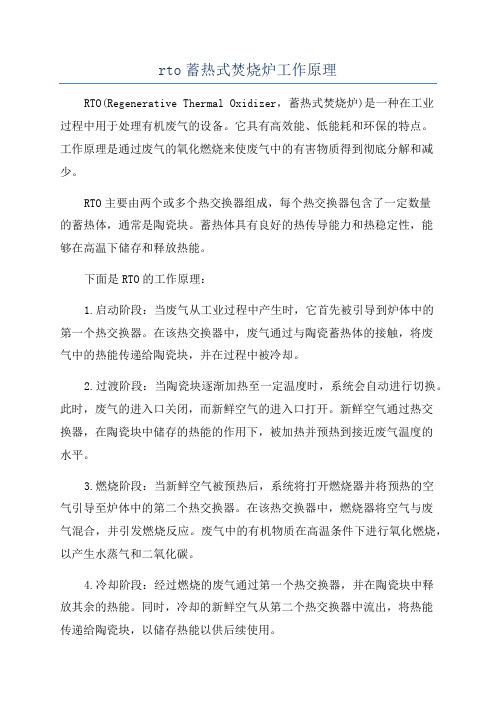
rto蓄热式焚烧炉工作原理RTO(Regenerative Thermal Oxidizer,蓄热式焚烧炉)是一种在工业过程中用于处理有机废气的设备。
它具有高效能、低能耗和环保的特点。
工作原理是通过废气的氧化燃烧来使废气中的有害物质得到彻底分解和减少。
RTO主要由两个或多个热交换器组成,每个热交换器包含了一定数量的蓄热体,通常是陶瓷块。
蓄热体具有良好的热传导能力和热稳定性,能够在高温下储存和释放热能。
下面是RTO的工作原理:1.启动阶段:当废气从工业过程中产生时,它首先被引导到炉体中的第一个热交换器。
在该热交换器中,废气通过与陶瓷蓄热体的接触,将废气中的热能传递给陶瓷块,并在过程中被冷却。
2.过渡阶段:当陶瓷块逐渐加热至一定温度时,系统会自动进行切换。
此时,废气的进入口关闭,而新鲜空气的进入口打开。
新鲜空气通过热交换器,在陶瓷块中储存的热能的作用下,被加热并预热到接近废气温度的水平。
3.燃烧阶段:当新鲜空气被预热后,系统将打开燃烧器并将预热的空气引导至炉体中的第二个热交换器。
在该热交换器中,燃烧器将空气与废气混合,并引发燃烧反应。
废气中的有机物质在高温条件下进行氧化燃烧,以产生水蒸气和二氧化碳。
4.冷却阶段:经过燃烧的废气通过第一个热交换器,并在陶瓷块中释放其余的热能。
同时,冷却的新鲜空气从第二个热交换器中流出,将热能传递给陶瓷块,以储存热能以供后续使用。
以上是RTO的一个循环。
RTO通过交替利用废气中的热能和新鲜空气之间的热交换,实现了高效率的热能利用,从而降低了能耗并节省了运行成本。
RTO同样也能有效地处理低浓度的有机废气,并通过废气处理的过程中产生的副产物进行排放控制,实现了环境友好。
此外,RTO还可以通过自动控制系统来监测和调节设备的运行状态,提高了设备的稳定性和安全性。
总而言之,RTO蓄热式焚烧炉通过利用陶瓷块的热储存和释放特性,实现了高效能、低能耗和环保的有机废气处理。
其工作原理有助于减少有机废气的排放量,改善环境质量,并提高工业过程的能源利用效率。
工业炉蓄热式燃烧技术ppt模板

➢2.蓄热式燃烧技术国内发展特点
(1)冶金行业是该项技术应用的先行者。轧钢连续加热炉 为最早的应用对象。
(2)民营公司和民营企业成为了该项技术推广和使用的先 行者。如北岛、神雾、力通、嘉德等民营工业炉企业, 萍乡、唐山国丰等民营钢铁企业。
(3)大型国有企业反应迟钝。如国内几个大型的工业炉公司, 大型国有钢铁企业。
(4)在机械、建材等其他行业起步略晚,推广应用程度不高。
➢3.蓄热式燃烧技术存在的问题
蓄热式燃烧技术在国内获得迅猛的发展,同时也带来了诸多负面问题。为 了深入了解国内蓄热燃烧技术的使用情况,对宝钢、马钢、济钢、首钢、首秦 5家企业的蓄热式炉进行了调研。
用户
炉型 燃料 燃烧方式 烧嘴型式 蓄热体 设计单位
使用情况及问题
宝钢热轧厂
步进炉
混合煤气
平焰烧嘴 +单蓄热烧嘴
美国套筒 式
小球
马钢中板厂 推钢炉 高炉煤气
双蓄热
左右喷混合煤气
双蓄热
左右喷口 布置
小球
单耗1.4GJ/t 问题:①煤气热值低,蓄热式效 果不明显②均热段大量平焰烧嘴
富氧助燃技术具有减少工业炉排烟的热损失、提高火焰温度、提高 工业炉产量、缩减设备尺寸、利于CO2和SO2的回收综合利用和封存等 优点。
③采用脉冲燃烧技术。 脉冲燃烧技术是高速气流燃烧技术与脉冲控制技术的联合应用,可
使燃烧器在燃烧过程始终在最佳状态下工作,通过控制实现炉内强烈 的气体循环,增加炉内对流传热量和炉温均匀温度,尤其适合中低热 处理炉子的应用。
蓄热式加热炉燃烧技术36页PPT

3.蓄热式燃烧(RCB 系统) 工作原
理及系统组成
RCB系统由两个烧嘴、两个蓄热室、一套换向装置和 相配套的控制系统组成(见图1)。模式A表示烧嘴A处于 燃烧状态,烧嘴B处于排烟状态:燃烧所需空气经过换向 阀,再通过蓄热室A,其预热后在烧嘴A中与燃料混合,燃 烧生成的火焰加热物料,高温废气通过烧嘴B进入蓄热 室B,将其中的蓄热球加热,再经换向阀后排往大气。持 续一定时间后(如20s),控制系统发出换向指令,操作进 入模式B所示的状态,此时烧嘴B处于燃料状态,烧嘴A处 于排烟状态:燃烧空气进入蓄热室B被预热,在烧嘴B中 与燃料混合,废气经蓄热室A,将其中蓄热球加热后排往 大气。持续与模式A过程相同的时间后,又转换到模式A 过程,如此交替循环进行。
பைடு நூலகம்
随着我国国民经济的飞速发展, 我国各行业工业炉窑的燃料消耗迅速增加, 绝大多数工业炉窑的燃料消耗长期高于国 际先进水平有害物的超标排放相当严重, 世界10个环境污染最严重的城市,我国已 占了7座。因此提高工业炉窑的燃料利用 率和大幅度降低氮化物的排放量,已成为 我国亟待解决的问题。
目前由于能源和环境问题日益突出,要 求各轧钢单位全面推行高效清洁生产技 术,而高效蓄热技术(简称HTAC式)目 前世界上先进的燃烧技术,可以从根本 上提高企业能源及用率,对低热值煤气 进行合理利用,最大限度地减少污染排 放,很好的解决燃油炉成本高、燃煤炉 污染中的问题。
为了解决这些问题,充分利用加热炉烟气的余热, 进 一步提高加热炉的热效率,大连北岛能源技术发展有限 公司研制出了高效蓄热式余热回收系统,并在加热炉上 应用,效果很好。如韶钢2019年7月投产的蓄热式加热炉, 炉内空气煤气可预热到1100℃,排放废气温度仅130℃, 这种炉子为全封闭的,热效率高,也不需要回收热能抚顺 特钢公司500分厂2# 炉于1993年8月结合大修,进行改造 后 , 单 耗 由 1879 m3/t 减 少 至 285197m3/t, 热 效 率 由 3185% 增至31149%,平均温度由58℃减少到9℃,节能率 为85172%,装炉量增加一倍, 生产率提高30%。包头钢铁 公司初轧厂新建2 座RCB 式长坑均热炉,使用高焦炉混 合煤气,空气和煤气均预热到900~1100℃,排烟温度低 于150℃,与该厂原有长坑均热炉相比,节约燃料41%,产 量提高了13%,减少基建投资200万元。
RTO蓄热式焚烧炉

RTO蓄热式燃烧炉:排放自工艺含VOCs的废气进入双槽RTO,三向切换风阀(POPPET VALVE)将此废气导入RTO的蓄热槽(Energy Recovery Chamber)而预热此废气,含污染的废气被蓄热陶块渐渐地加热后进入燃烧室(Combustion Chamber),VOCs在燃烧室被氧化而放出热能于第二蓄热槽中之陶块,用以减少辅助燃料的消耗. 陶块被加热,燃烧氧化后的干净气体逐渐降低温度, 因此出口温度略高于RTO入口温度. 三向切换风阀切换改变RTO出口/入口温度. 如果VOCs浓度够高,所放出的热能足够时, RTO即不需燃料. 例如RTO热回收效率为95%时,RTO出口仅较入口温度高25℃而已.蓄热式催化剂燃烧炉(RCO)排放自工艺含VOCs的废气进入双槽RCO,三向切换风阀(POPPET VALVE)将此废气导入RCO的蓄热槽(Energy Recovery Chamber)而预热此废气,含污染的废气被蓄热陶块渐渐地加热后进入催化床(Catalyst Bed), VOCs在经催化剂分解被氧化而放出热能于第二蓄热槽中之陶块,用以减少辅助燃料的消耗. 陶块被加热,燃烧氧化后的干净气体逐渐降低温度, 因此出口温度略高于RCO入口温度. 三向切换风阀切换改变RCO出口/入口温度. 如果VOCs浓度够高,所放出的热能足够时, RCO即不需燃料. 例如RCO热回收效率为95%时,RCO出口仅较入口温度高25℃而已.催化剂燃烧炉( Catalytic Oxidizer )换热器,废气经由换热换热器之壳侧(shell side)将管侧(tube side)未经处理的VOC废气加热,此换热器会减少能源的消耗,最后,净化后的气体从烟囱排到大气中.直燃式燃烧炉( Thermal Oxidizer )换热器,废气经由换热器管侧(Tube side)而被加热后,再通过燃烧器,这时废气已被加热至催化分解温度(650~1000℃换热器之壳侧(shell side)将管侧(tube side)未经处理的VOC废气加热,此换热器会减少能源的消耗(甚至于某ㄧ适当的VOCs浓度以上时便不需额外的燃料),最后,净化后的气体从烟囱排到大气中.直接燃烧燃烧炉( Direct Fired Thermal Oxidizer-DFTO )有时直接燃烧燃烧炉源于后燃烧器(After-Burner), 直接燃烧燃烧炉使用经特别设计的燃烧器以加热高浓度的废气到ㄧ预先设的温度,于运转时废气被导入燃烧室(Burner Chamber). 燃烧器将VOCs及有毒空气污染物分解为无毒的物质(二氧化碳及水)并放出热,净化后的气体可再由一热回收系统以达节能的需求. 恩国直接燃烧燃烧炉可达99%碳氢化合物破坏去除率,为达此去除率,高温的废气区在炉内保持一定的滞留时间.在入口处也须让废气有足够的扰流和氧产生充分的混合,充分的扰流不只提高去除破坏率,更是为平安考虑. 恩国的设计将爆炸风险降至最低以及最小的能源消耗.浓缩转轮/燃烧炉( Rotor Concentrator / Oxidizer )恩国浓缩转轮/燃烧炉系统吸附大风量低浓度挥发性有机化合物(VOCs). 再把脱附后小风量高浓度废气导入燃烧炉予以分解净化。
蓄热式燃烧技术(插图)
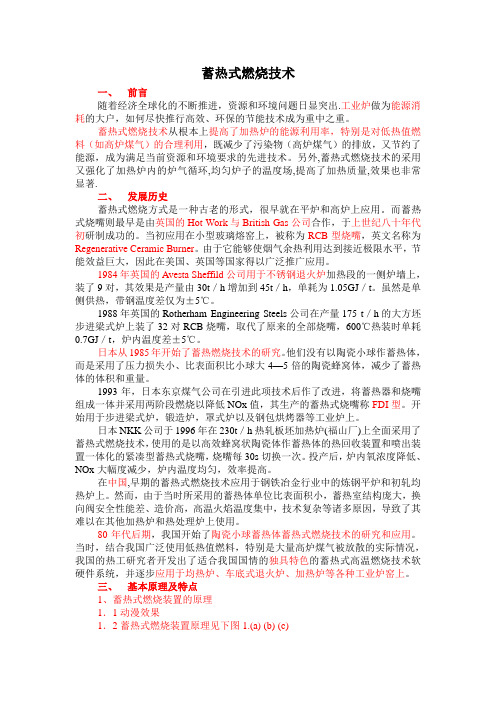
蓄热式燃烧技术一、前言随着经济全球化的不断推进,资源和环境问题日显突出.工业炉做为能源消耗的大户,如何尽快推行高效、环保的节能技术成为重中之重。
蓄热式燃烧技术从根本上提高了加热炉的能源利用率,特别是对低热值燃料(如高炉煤气)的合理利用,既减少了污染物(高炉煤气)的排放,又节约了能源,成为满足当前资源和环境要求的先进技术。
另外,蓄热式燃烧技术的采用又强化了加热炉内的炉气循环,均匀炉子的温度场,提高了加热质量,效果也非常显著.二、发展历史蓄热式燃烧方式是一种古老的形式,很早就在平炉和高炉上应用。
而蓄热式烧嘴则最早是由英国的Hot Work与British Gas公司合作,于上世纪八十年代初研制成功的。
当初应用在小型玻璃熔窑上,被称为RCB型烧嘴,英文名称为Regenerative Ceramic Burner。
由于它能够使烟气余热利用达到接近极限水平,节能效益巨大,因此在美国、英国等国家得以广泛推广应用。
1984年英国的Avesta Sheffild公司用于不锈钢退火炉加热段的一侧炉墙上,装了9对,其效果是产量由30t/h增加到45t/h,单耗为1.05GJ/t。
虽然是单侧供热,带钢温度差仅为±5℃。
1988年英国的Rotherham Engineering Steels公司在产量175 t/h的大方坯步进梁式炉上装了32对RCB烧嘴,取代了原来的全部烧嘴,600℃热装时单耗0.7GJ/t,炉内温度差±5℃。
日本从1985年开始了蓄热燃烧技术的研究。
他们没有以陶瓷小球作蓄热体,而是采用了压力损失小、比表面积比小球大4—5倍的陶瓷蜂窝体,减少了蓄热体的体积和重量。
1993年,日本东京煤气公司在引进此项技术后作了改进,将蓄热器和烧嘴组成一体并采用两阶段燃烧以降低NOx值,其生产的蓄热式烧嘴称FDI型。
开始用于步进梁式炉,锻造炉,罩式炉以及钢包烘烤器等工业炉上。
日本NKK公司于1996年在230t/h热轧板坯加热炉(福山厂)上全面采用了蓄热式燃烧技术,使用的是以高效蜂窝状陶瓷体作蓄热体的热回收装置和喷出装置一体化的紧凑型蓄热式烧嘴,烧嘴每30s切换一次。
蓄热式燃烧系统

蓄热式燃烧系统--高效节能蓄热式加热炉、热处理炉技术和工程蓄热式燃烧系统集燃烧、空煤气预热,烟气排放三大功能为一体,能最大限度地回收炉窑烟气的显热,降低能耗,改善炉内加热质量,使工业炉窑节能技术发展到一个新的阶段。
基于蓄热式热交换原理的高温空气燃烧技术(HTAC),是近年来在发达国家开始普遍推广应用的一种全部燃烧技术,它具有高效烟气余热回收、高温预热空气、低污染排放等多重优越性。
该项技术的应用可包括冶金行业中各类型烧燃料的加热炉(固体燃料除外),同时也可广泛应用于机械、石油、化工等行业各种燃料炉、利用燃烧、自动控制、耐火材料、空煤气预热等综合技术,结合工艺条件,我们提出针对现场实际情况的改造方案,做到紧密联系实际,高效、安全、可靠地完成工程项目,达到预期的社会和经济效益。
一座中型加热炉改造完成后从节约的燃料费、维护费及成材率提高,直接获得的经济效益为每年1000万元/座左右,投资回收期一年左右,不但每年每座加热炉可减少烟气排放有害成份,还可提高轧机作业率,改善操作环境,减轻劳动强度。
典型案例案例一:某厂天然气蓄热式带钢热处理炉,台车装炉量40t。
原来燃煤炉型燃料消耗125kg实物煤/t,由于温度均匀性差,加热速度慢,全处理周期24h,环保不达标。
改造后,采用蓄热式燃烧技术,炉温均匀性提高,加热速度快,现处理最周期缩短,单耗30立方米天然气/t,能耗大幅度下降,按年处理1万吨钢带计算,每年带来直接经济效益约130万元,改造投资回收期短,达到环保指标。
案例二:某厂燃烧发生炉煤气步进式加热炉,该炉产量100t/h。
原设计燃料为重油,由于重油质量连年下降,且价格不断上涨,因此该炉于05年燃料改为燃发生炉煤气。
改造后,炉温均匀性提高,单耗下降,连同发生炉本消耗在内,吨钢煤耗70kg以内,吨钢燃耗成本下降65元身。
按年产40万元计算,仅此一项,节约2600万元/年。
由于采取相应的燃烧控制和环保措施,该炉的排放达到国家相关环保规范要求。
蓄热燃烧技术简介

蓄热燃烧技术又称高温空气燃烧技术,全名称为:高温低氧空气燃烧技术(High Temperature and Low Oxygen Air Combustion-HTLOAC),也作HTAC(High Temperature Air Combustion)技术,也有称之为无焰燃烧技术(Flameless Combustion)。
通常高温空气温度大于1000℃,而氧含量低到什么程度,没有人去划定,有些人说应在18%以下,也有说在13%以下的。
蓄热燃烧技术原理如图所示:当常温空气由换向阀切换进入蓄热室1后,在经过蓄热室(陶瓷球或蜂窝体等)时被加热,在极短时间内常温空气被加热到接近炉膛温度(一般比炉膛温度低50~100℃),高温热空气进入炉膛后,抽引周围炉内的气体形成一股含氧量大大低于21%的稀薄贫氧高温气流,同时往稀薄高温空气附近注入燃料(燃油或燃气),这样燃料在贫氧(2-20%)状态下实现燃烧;与此同时炉膛内燃烧后的烟气经过另一个蓄热室(见图中蓄热室2)排入大气,炉膛内高温热烟气通过蓄热体时将显热传递给蓄热体,然后以150~200℃的低温烟气经过换向阀排出。
工作温度不高的换向阀以一定的频率进行切换,使两个蓄热体处于蓄热与放热交替工作状态,常用的切换周期为30~200秒。
简单说,就是先将蓄热体加热后,再通入空气,并将空气加热到高温,送入炉内与烟气混合(为降低氧气含量,目的是降低氧化氮的含量)后,再与燃料混合燃烧。
要注意的是,蓄热燃烧,蓄热室必须是成对的,其中一个用来加热空气,而另一个被烟气加热。
经过一个周期后,加热空气的蓄热室降温,而被烟气加热的蓄热室却升高温度,这样,通过换向阀,使两个蓄热室作用交换,这时原来是排烟口的,现在变成了烧嘴,而原来是烧嘴的,现在变成了排烟口。
高温空气燃烧技术的主要特点是:(1)采用高温空气烟气余热回收装置,交替切换空气与烟气,使之流经蓄热体,能够在最大程度上回收高温烟气的显热,即实现了极限余热回收;(2)将燃烧空气预热1000℃以上的温度水平,形成与传统火焰(诸如扩散火焰与预混火焰等)迥然不同的新型火焰类型,创造出炉内优良的均匀温度场分布;(3)通过组织贫氧状态下的燃烧,避免了通常情况下,高温热力氮氧化物NOx的大量生成。
蓄热式燃烧炉课件资料

一,设备简介蓄热式燃烧器是在极短期内把常温空气加热,被加热的高温空气进入炉膛后,卷吸周围炉内的烟气形成一股含氧量大大低于的稀薄贫氧高温气流,同时往稀薄高温空气附近注入燃料,燃料在贫氧( )状态下实现燃烧。
同时,炉膛内燃烧后的热烟气经过另一个蓄热式燃烧器排空,将高温烟气显热储存在另一个蓄热式燃烧器内。
工作温度不高的换向阀以一定的频率进行切换,常用的切换周期为秒。
两个蓄热式燃烧器处于蓄热与放热交替工作状态,从而达到节能目的。
1.实现了蓄热体温度效率、热回收率和炉子热效率三高作为一个回收烟气余热的燃烧系统,温度效率、热回收率和炉子热效率可以说是衡量它热工性能优劣的主要指标。
国内外大量生产实际的测试数据表明,在适当的换向周期下,经过蓄热体后的高温空气温度和进入蓄热体的烟气温度十分接近,仅差100℃摆布,温度效率高达95%摆布,热回收率为80%摆布。
炉子热效率得到了较大的提高。
2.加热质量好,氧化烧损小由于高温空气燃烧技术是属于低氧空气燃烧范畴,而且助燃空气的切入点和燃料切入点与传统的燃烧方法不一样,从而避免了高温火焰过分集中造成的炉内各区域温差大的弊病,同时也减少了高温氧化烧损的可能性。
由于炉温的均匀程度大大提高,被冶炼的物料加热质量得到了充分保证。
3.节能效果显著蓄热式燃烧系统与传统燃烧系统比,热回收率大大提高,节能效果特殊明显,其节能率往往达到40~50%。
这对于传统燃烧系统来说几乎是不可能的。
4.合用性较强,能用于多种不同工艺要求的工业炉由于蓄热式燃烧系统的炉温均匀性好,炉温波动小,不存在高温区过分集中及火焰对工件的冲刷等问题,所以它的合用范畴较宽。
目前己在大中型推钢式及步进式轧钢加热炉、均热炉、罩式热处理炉、辐射管气体渗碳炉、钢包烘烤炉、玻璃熔化炉、熔铝炉、锻造炉等工业炉上使用。
不管是采用蓄热式燃烧器的炉子或者蓄热式工业炉,在实际运行中都比较稳定可靠,取得了比较好的经济效益和社会效益。
5.建设投资相对不高,投资回收期短从全国冶金行业已经改造或者新建的二十余座蓄热式工业炉情况来看,将传统燃烧方式的工业炉改造为蓄热式工业炉的投资比仍采用传统燃烧方式的炉子要高,但是在同等要求下新建蓄热式工业炉与新建传统燃烧方式的工业炉投资基本相当或者略有上升。
蓄热式高温空气燃烧技术在锅炉上的应用精品PPT课件

发热值
相对锅炉热效率 能源单价
5000Kcal/Kg
字形耐火通道及下煤通道,因煤在下落受热的过程中容易 在耐火砖表面挂渣,时间长了以后,会造成耐火通道及下 煤通道堵塞,从而影响了炉体的寿命。
两段式煤气化装置介绍
一段半式两段炉 此炉型是在单段式煤气炉的基础上,加高 干燥段而得名,它的气化段和干馏段结构 不尽合理,下段煤气容易带出焦油,煤气 热值不如十字隔墙和中心管式两段炉。
29MW、58 MW锅炉运行费用比较
锅炉型号
锅炉效率
锅炉能耗m3(Kg)/h
锅炉运行时间(h) 两台锅炉总能耗量
m3(Kg) 燃料单价m3(Kg)/元
年燃料消耗总价 (万元)
锅炉投资(万元)
说明
29MW 58MW 29MW 58MW
29MW 58MW
/
/
/ 锅炉运行4个 月,每天运行 16小时
蓄热煤制气蓄热锅炉 101% 101% 16070 32140 1200
两段式煤气化装置介绍
中心管式两段炉 下段煤气由36个耐火通道提取,并有6个-12个底部煤气调节阀来调节整个炉
膛面的燃烧平衡,及上下段的煤气流量,同时此炉型可实现上、下段煤气单 独输出。 (1)底部煤气另设一路中心管提取,其作用为:
a. 与周边36个耐火通道共同组成干馏加热空间,形成内、外两层环形圈辐 射热源。
采用贫氧燃烧,降低了NOX的产生,使氮氧化物排放低于200ppm (ppm指百万分之一),CO2等有害气体的排放量比原来减少20%~ 40%,有效地减少了污染物的排放;
燃烧火焰稳定。
蓄热式热水、蒸汽锅炉
蓄 热 式 热 水、 蒸 汽 锅 炉
单蓄热冷凝式锅炉的工作原理
在PLC控制系统的控制下,启动风机,换向系统投入运行;经过 30s~180s的炉膛吹扫后,系统正常工作。燃烧器A工作,常温空气 经空气换向阀至燃烧器A,可空气温度预热至900℃左右,与燃料混 合后在炉膛内燃烧;同时高温烟气经过燃烧器B后,蓄热体蓄热,出 燃烧器B烟气温度降低到180℃左右,烟气再进入冷凝器热回收变为 70℃左右排出。一个换向周期后,换向阀改变空气和烟气流向,B燃 烧器工作,A燃烧器蓄热;如此反复周期性交替燃烧。
蓄热式燃烧加热炉PPT文档34页
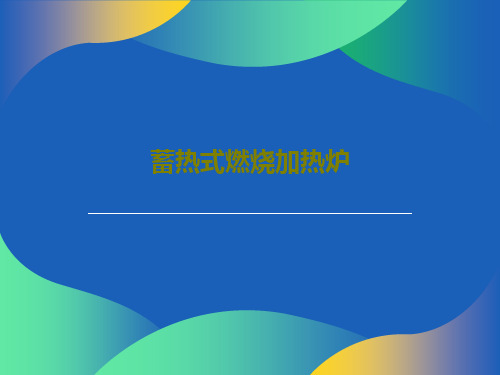
41、实际上,我们想要的不是针对犯 罪的法 律,而 是针对 疯狂的 法律。 ——马 克·吐温 42、法律的力量应当跟随着公民,就 像影子 跟随着 身体一 样。— —贝卡 利亚 43、法律和制度必须跟上人类思想进 步。— —杰弗 逊 44、人类受制于法律,法律受制于情 理。— —托·富 勒
45、法律的制定是为了保证每一个人 自由发 挥自己 的才能 ,而不 是为了 束缚他 的才能 。—— 罗伯斯 庇尔
31、只有永远躺在泥坑里的人,才不会再掉进坑里。——黑格尔 32、希望的灯一旦熄灭,生活刹那间变成了一片黑暗。——普列姆昌德 33、希望是人生的乳母。——科策布 34、形成天才的决定因素应该是勤奋。——郭沫若 35、学到很多东西的诀窍,就
RTO三室蓄热式燃烧炉介绍 PPT课件

• 风机两侧设置压差计,可对风机的故障及时报警。风机由 变频器控制,以适应不同的运行情况。
RTO三室蓄热式燃烧炉介绍
• 第一次循环 • 蓄热室C:有机废气经引风机进入蓄热室C的陶瓷蓄热体
(陶瓷蓄热体“贮存”了上一循环的热量,处于高温状 态),此时,陶瓷蓄热体释放热量,温度降低,而有机废 气吸收热量,温度升高,废气经过蓄热室C换热后以较高的 温度进入氧化室。 • 氧 化 室:经过陶瓷蓄热室C换热后的有机废气以较高的温 度进入氧化室反应,使有机物氧化分解成无害的CO2和H2O, 如废气的温度未达到氧化温度,则由燃烧器直接加热补偿 至氧化温度,由于废气已在蓄热室C预热,进入氧化室只需 稍微加热便可达到氧化温度(如果废气浓度足够高,氧化 时可以不需要天然气加热,靠有机物氧化分解放出的热量 便可以维持自燃),氧化后的高温气体经过陶瓷蓄热体A排 出。
RTO三室蓄热式燃烧炉介绍
燃烧机控制系统元件
RTU
RTO三室蓄热式燃烧炉介绍
RTO三室蓄热式燃烧炉介绍
• 蓄热室A: 氧化后的高温气体进入蓄热室A(此时陶瓷处于 温度较低状态),高温气体释放大量热量给蓄热陶瓷A,气 体降温,而陶瓷蓄热室A吸收大量热量后升温贮存(用于下 一个循环预热有机废气),经风机作用气体由烟囱排入大 气,排气温度比进气温度高约40℃左右。
- 1、下载文档前请自行甄别文档内容的完整性,平台不提供额外的编辑、内容补充、找答案等附加服务。
- 2、"仅部分预览"的文档,不可在线预览部分如存在完整性等问题,可反馈申请退款(可完整预览的文档不适用该条件!)。
- 3、如文档侵犯您的权益,请联系客服反馈,我们会尽快为您处理(人工客服工作时间:9:00-18:30)。
一,设备简介
蓄热式燃烧器是在极短时间内把常温空气加热,被加热的高温空气进入炉膛后,卷吸周围炉内的烟气形成一股含氧量大大低于21%的稀薄贫氧高温气流,同时往稀薄高温空气附近注入燃料,燃料在贫氧(2%~20%)状态下实现燃烧。
同时,炉膛内燃烧后的热烟气经过另一个蓄热式燃烧器排空,将高温烟气显热储存在另一个蓄热式燃烧器内。
工作温度不高的换向阀以一定的频率进行切换,常用的切换周期为
30~200秒。
两个蓄热式燃烧器处于蓄热与放热交替工作状态,从而达到节能目的。
1.实现了蓄热体温度效率、热回收率和炉子热效率三高
作为一个回收烟气余热的燃烧系统,温度效率、热回收率和炉子热效率可以说是衡量它热工性能优劣的主要指标。
国内外大量生产实际的测试数据表明,在适当的换向周期下,经过蓄热体后的高温空气温度和进入蓄热体的烟气温度十分接近,仅差100℃左右,温度效率高达95%左右,热回收率为80%左右。
炉子热效率得到了较大的提高。
2 . 加热质量好,氧化烧损小
由于高温空气燃烧技术是属于低氧空气燃烧范畴,而且助燃空气的切入点和燃料切入点与传统的燃烧方法不一样,从而避免了高温火焰过分集中造成的炉内各区域温差大的弊病,同时也减少了高温氧化烧损的可能性。
由于炉温的均匀程度大大提高,被冶炼的物料加热质量得到了充分保证。
3.节能效果显著
蓄热式燃烧系统与传统燃烧系统比,热回收率大大提高,节能效果特别明显,其节能率往往达到40~50%。
这对于传统燃烧系统来说几乎是不可能的。
4.适用性较强,能用于多种不同工艺要求的工业炉
由于蓄热式燃烧系统的炉温均匀性好,炉温波动小,不存在高温区过分集中及火焰对工件的冲刷等问题,所以它的适用范畴较宽。
目前己在大中型推钢式及步进式轧钢加热炉、均热炉、罩式热处理炉、辐射管气体渗碳炉、钢包烘烤炉、玻璃熔化炉、熔铝炉、锻造炉等工业炉上使用。
不论是采用蓄热式燃烧器的炉子或蓄热式工业炉,在实际运行中都比较稳定可靠,取得了比较好的经济效益和社会效益。
5.建设投资相对不高,投资回收期短
从全国冶金行业已经改造或新建的二十余座蓄热式工业炉情况来看,将传统燃烧方式的工业炉改造为蓄热式工业炉的投资比仍采用传统燃烧方式的炉子要高,但是在同等要求下新建蓄热式工业炉与新建传统燃烧方式的工业炉投资基本相当或略有上升。
蓄热式工业炉与传统燃烧方式工业炉在建设投资的比较上并没有显示较大的优势,但是在投资回收期的缩短上体现了强劲的优势。
如果考虑到由于炉温均匀而导致加热质量提高、氧化烧损减少,由于加热能力的提高导致产量的增加等方面的收益,则综合经济效益更加可观。
二,主要技术参数
炉子的主要尺寸:
炉底面积: 1.9 mm^2
炉膛温度:1200度
燃料名称:天燃气
炉前燃气压力:4-6KPa
最大天燃气消耗量;20-25Nm/h
烧嘴数量:1对
燃烧方式:对烧
蓄热体形式:高铝球
鼓风机压力:6000Pa
鼓风机流量:400m³/h
引风机压力;5000 Pa
引风机流量:650 m³/h
压缩空气压力0.6MPa
烧嘴排烟温度;<=100℃
三.工作原理
配备在工业炉上的蓄热式燃烧系统,由蓄热式烧嘴、换向系统和控制系统组成。
工作原理如上图所示
来自鼓风机的助燃空气经换向系统和燃料分别进入左侧烧嘴的各自通道,助燃空气由下向上通过蓄热室A。
预热后的空气从左侧通道喷出并与燃料混合燃烧。
燃烧产物对物料进行加热后进人右侧通道,在蓄热室B内进行热交换将大部分热量留给蓄热体后,以200℃以下的温度进入换向阀,经引风机排入大气。
设定的换向时间一到控制系统发出指令,换向机构动作,空气、烟气同时换向。
此时助燃空气从右侧通道喷口喷出并与燃烧器B的燃料混合燃烧,这时左侧喷口作为烟道。
在引风机的作用下,使高温烟气通过蓄热体、换向阀、引风机排出,一个换向周期完成。
采用蓄热式烧嘴可取消常规工业炉上的烧嘴、换热器、高温管道、地下烟道及高大的烟囱.操作及维护简单,无烟尘污染,换向设备灵活,控制系统功能完备,炉内温度均匀,节能30%~50%。
四,技术、结构特点
4.1 蓄热式燃烧器
加热炉外部安装2个空气蓄热式燃烧器,2个空气蓄热器对称安装,蓄热式燃烧器为单喷口。
一个空气喷口和天燃气喷口,组成一个燃烧单元。
蓄热器中的蓄热体采用陶瓷小球和陶瓷蜂窝体的复合蓄热结构,它具有换向时间适中(中型厂设计换向时间2min),耐急冷急热性好、导热性能好等优点;每个燃烧器前的天燃气和空气连接管上都安有手动调节阀,从而使得各个燃烧器、特别是上部与下部燃烧器的能力能够按需要进行调节;维修方便,可以在不影响炉子正常生产的情况下利用常规检修更换蓄热体。
4.2引火烧嘴
采用电子打火点燃,使用安全可靠。
4.3自动控制
炉温控制系统采用在工业炉窑控制中广泛使用的双交叉限幅控制方式,为保证供热区温度的可控性,首先设置独立的,以温度为主环,空煤气流量调节为副环的炉温控制回路。
根据工艺的供热分配情况,设有温度调节回路。
炉膛压力控制为减少换向对炉压调节的干扰采用手动调节煤气烟道及空气烟道的废气调节阀门,保证炉膛压力稳定在给定范围。
4.4换向控制
换向采用二腔二通换向阀,换向燃烧控制按定时的原则,并按规定的换向时序,控制2个天燃气换向阀和2个空气换向阀的动作,也可手动控制换向。
4.5安全保护系统
仪表控制安全连锁逻辑保护系统在天燃气总管压力过低、空气压力过低、仪表气源压力过低、电源故障情况下,发生自动停炉;当发生自动停炉时,系统完成如下动作:总管煤气立即切断,并在10min后停引风机,鼓风机则需要手动停止。
另外还有紧急手动停炉。
用于在特殊情况下,如控制系统故障时,由操作员通过操作台的急停按钮,完成停炉操作。
五,蓄热式燃烧系统操作流程
A操作前必须做的准备工作
1、仔细阅读《蓄热式自动燃烧控制系统操作说明书》,了解各部件的名称、功能和作用,清楚控制柜面板各按钮的功能。
牢记:任何时候,点火启动时,务必打开炉门!
2、保持冷却风机一直处于开启状态,直至炉膛温度低于750℃为止。
B冷炉运行操作流程(炉膛温度在900℃以下)
1、打开炉门60%以上开度;开启冷却风机;开启90%助燃风机;开启90%引风机;打开燃气总阀;调整1#燃气手动阀到50%开度;调整2#燃气手动阀到50%开度。
2、启动1#点火枪运行,并检查其火检状况;启动2#点火枪运行,并检查其火检状况;确认全部火检信号到位稳定,并肉眼观察到火焰明火。
如果火检信号不到位,请调节点火燃气手动球阀开度,直至火检信号稳定为止。
3、启动“自动运行”模式,严密观察1#大火和2#大火换向单枪燃烧是否正常;严密观察炉膛温度运行数据,逐渐加大1#燃气手动阀和2#燃气手动阀开度,直至开度90%左右。
系统正常运行至少六个周期后,炉膛温度在逐渐上升的前提下,调整炉门开度到15%左右,让系统自动运行。
正常运行45分钟后,炉膛温度达到900度以上时,方可关闭炉门运行。
4、中途出现火检报警停运时,只需按下“报警复位”按钮,报警即可消除,再次点火运行前,务必打开炉门点火,确认正常运行后,方可关闭炉门运行。
5、炉膛温度超过大火停止运行温度后,可将1#燃气手动阀和2#燃气手动阀调整到50%开度,一方面为下炉做准备,另一方面炉膛保温也无需太多燃料。
C热炉运行操作流程(炉膛温度在900℃以上)
1、炉膛温度在900℃以上,炉壁已经发红的前提下,可以启动“自动运行”模式运行。
2、加完冷料后,若炉膛温度低于“点火停止”温度,必须先打开炉门60%以上开度,再启动“自动运行”模式,并严密观察1#大火和2#大火换向单枪燃烧是否正常。
确认燃气喷到炉膛即可自燃后,方可关闭炉门运行。
3、派人值守炉旁。
一旦系统出现紧急情况,可立即按下急停按钮,系统会马上停止运行。
D系统停运操作流程
关闭“自动运行”模式,关闭鼓风机、引风机,务必记得关闭燃气总阀、1#燃气手动阀和2#燃气手动阀,但不能关闭冷却风机,因为炉膛温度高;也无需关闭点火燃气阀。
E系统设备维护保养
1、每炉运行完毕,小心取出点火枪,清理点火枪头上的积灰,保持良好点火状态。
2、每天检查二个气动换向阀、二台风机、二个燃气电磁阀的运行状况。
3、每周清理积尘室内的灰尘。
每月检查一次蓄热球集尘状况、主枪护套的烧损状况。
六、吊运、安装调试与维护操作
起吊装卸炉子时,必须注意重心使之平衡,钢丝绳不宜与机器接触,
建议用橡胶板、木头之类的较软物衬垫。
燃气炉在安装前需检查是否由于运输或其它原因造成损坏或配套不全,在完备的情况下,将零部件先行清除尘垢与修补好发现的缺陷,然后进行安装。
燃气炉烟囱出口连接尺寸,烟囱直径应不小于250mm,高度由出口起不小于6m。
操作与调试:
1、点炉前必须将炉门全开启,以免点炉时,爆燃发生危险。
2、第一次点火点燃时,应逐个燃烧机开机点火,间歇开机将未燃气体排净后,再重新点火,以免发生危险。
设备装箱单
设备名称:蓄热式燃烧炉
东营市宏宇精铸设备有限责任公司2013年月日
设备质检合格证
设备名称:蓄热式燃烧炉
东营市宏宇精铸设备有限责任公司2013年月日。