注塑模具试模管理
试模有关规定
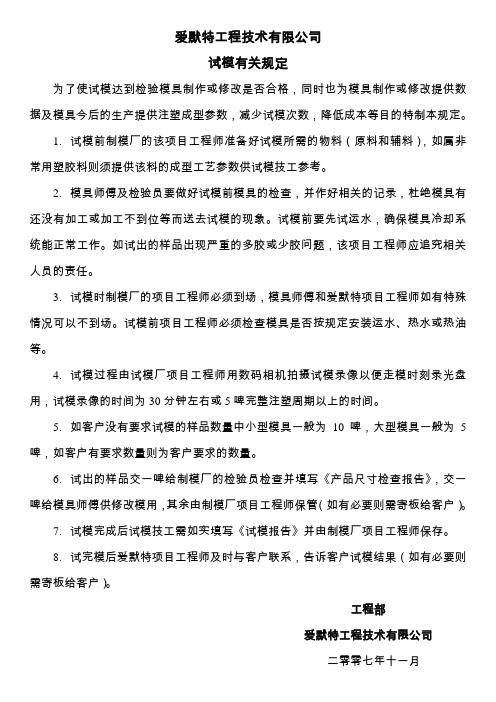
爱默特工程技术有限公司
试模有关规定
为了使试模达到检验模具制作或修改是否合格,同时也为模具制作或修改提供数据及模具今后的生产提供注塑成型参数,减少试模次数,降低成本等目的特制本规定。
1.试模前制模厂的该项目工程师准备好试模所需的物料(原料和辅料),如属非常用塑胶料则须提供该料的成型工艺参数供试模技工参考。
2.模具师傅及检验员要做好试模前模具的检查,并作好相关的记录,杜绝模具有还没有加工或加工不到位等而送去试模的现象。
试模前要先试运水,确保模具冷却系统能正常工作。
如试出的样品出现严重的多胶或少胶问题,该项目工程师应追究相关人员的责任。
3.试模时制模厂的项目工程师必须到场,模具师傅和爱默特项目工程师如有特殊情况可以不到场。
试模前项目工程师必须检查模具是否按规定安装运水、热水或热油等。
4.试模过程由试模厂项目工程师用数码相机拍摄试模录像以便走模时刻录光盘用,试模录像的时间为30分钟左右或5啤完整注塑周期以上的时间。
5.如客户没有要求试模的样品数量中小型模具一般为10啤,大型模具一般为5啤,如客户有要求数量则为客户要求的数量。
6.试出的样品交一啤给制模厂的检验员检查并填写《产品尺寸检查报告》,交一啤给模具师傅供修改模用,其余由制模厂项目工程师保管(如有必要则需寄板给客户)。
7.试模完成后试模技工需如实填写《试模报告》并由制模厂项目工程师保存。
8.试完模后爱默特项目工程师及时与客户联系,告诉客户试模结果(如有必要则需寄板给客户)。
工程部
爱默特工程技术有限公司
二零零七年十一月。
注塑模具试模时几种经常出现问题及解决方法
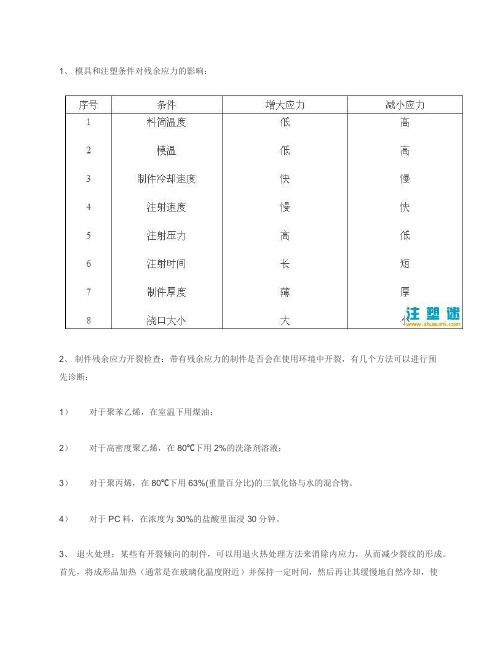
1、模具和注塑条件对残余应力的影响:
2、制件残余应力开裂检查:带有残余应力的制件是否会在使用环境中开裂,有几个方法可以进行预
先诊断:
1)对于聚苯乙烯,在室温下用煤油;
2)对于高密度聚乙烯,在80℃下用2%的洗涤剂溶液;
3)对于聚丙烯,在80℃下用63%(重量百分比)的三氧化铬与水的混合物。
4)对于PC料,在浓度为30%的盐酸里面浸30分钟。
3、退火处理:某些有开裂倾向的制件,可以用退火热处理方法来消除内应力,从而减少裂纹的形成。
首先,将成形品加热(通常是在玻璃化温度附近)并保持一定时间,然后再让其缓慢地自然冷却,使
发生裂纹处的大分子能自由活动、回复原来状态。
这种退火热处理法一般在成形后立即进行。
4、调湿处理:对于尼龙塑件,为了改善内应力分布状况及塑料内的晶体结构,提高制件韧性,保持尺寸相对稳定,可以进行调湿处理,其效果比退火处理更佳。
方法是将制件浸入沸水或醋酸钾水溶液(比例为 1.25:100,沸点121℃)中,浸泡时间视制件最大壁厚而定,从2小时至16小时不等。
注塑模具试模和修模流程
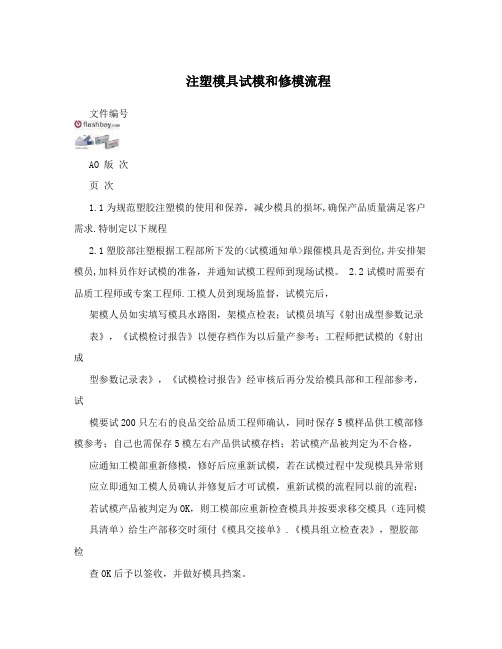
注塑模具试模和修模流程文件编号AO 版次页次1.1为规范塑胶注塑模的使用和保养,减少模具的损坏,确保产品质量满足客户需求.特制定以下规程2.1塑胶部注塑根据工程部所下发的<试模通知单>跟催模具是否到位,并安排架模员,加料员作好试模的准备,并通知试模工程师到现场试模。
2.2试模时需要有品质工程师或专案工程师.工模人员到现场监督,试模完后,架模人员如实填写模具水路图,架模点检表;试模员填写《射出成型参数记录表》,《试模检讨报告》以便存档作为以后量产参考;工程师把试模的《射出成型参数记录表》,《试模检讨报告》经审核后再分发给模具部和工程部参考,试模要试200只左右的良品交给品质工程师确认,同时保存5模样品供工模部修模参考;自己也需保存5模左右产品供试模存档;若试模产品被判定为不合格,应通知工模部重新修模,修好后应重新试模,若在试模过程中发现模具异常则应立即通知工模人员确认并修复后才可试模,重新试模的流程同以前的流程;若试模产品被判定为OK,则工模部应重新检查模具并按要求移交模具(连同模具清单)给生产部移交时须付《模具交接单》.《模具组立检查表》,塑胶部检查OK后予以签收,并做好模具挡案。
文件编号AO 版次页次2.3模具投产后,由架模员把模具从模架上领出至现场.按模具的水路图和架模点检表,技术员或领班按射出成型参数表进行生产,开机生产进行;如实填写模具保养点检表和模具的生产履历表,下模后由架摸员吹清水路喷上防锈剂保养把模具送至模具架上,如实填写模具管制表。
2.4生产中模具发生异常,如需要停机修模而下模维修时,须开立异常通知单。
停线通知单.修模通知单,通知相关人员和相关人员,经审签后需开立模具维修单连同要修模具送至工模部进行维修;修复后再进行试模,技术人员如实填写试模检讨报告,试模产品经品保工程师和研发设计工程师确认,如判定为OK 则可投入生产,如判定为NG则移交模具和该模具的试模报告,通知工模检讨,给予维修,如未下机台维修,可不用开立试模检讨报告,由塑胶部依照注塑的封样进行判定OK还是NG。
注塑试模参数设定流程及要求
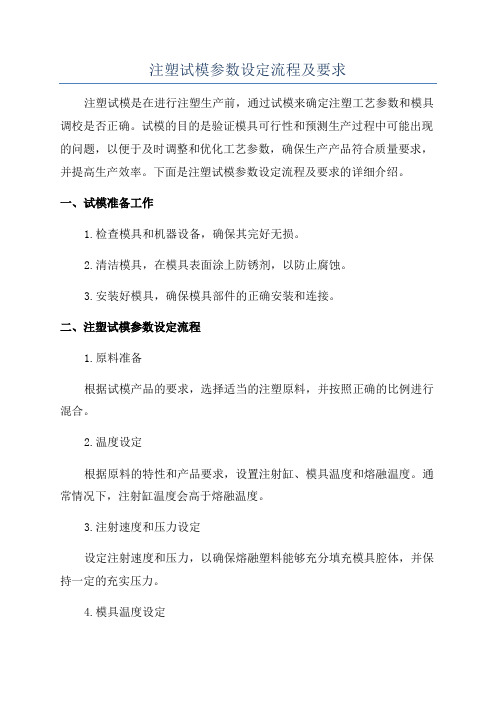
注塑试模参数设定流程及要求注塑试模是在进行注塑生产前,通过试模来确定注塑工艺参数和模具调校是否正确。
试模的目的是验证模具可行性和预测生产过程中可能出现的问题,以便于及时调整和优化工艺参数,确保生产产品符合质量要求,并提高生产效率。
下面是注塑试模参数设定流程及要求的详细介绍。
一、试模准备工作1.检查模具和机器设备,确保其完好无损。
2.清洁模具,在模具表面涂上防锈剂,以防止腐蚀。
3.安装好模具,确保模具部件的正确安装和连接。
二、注塑试模参数设定流程1.原料准备根据试模产品的要求,选择适当的注塑原料,并按照正确的比例进行混合。
2.温度设定根据原料的特性和产品要求,设置注射缸、模具温度和熔融温度。
通常情况下,注射缸温度会高于熔融温度。
3.注射速度和压力设定设定注射速度和压力,以确保熔融塑料能够充分填充模具腔体,并保持一定的充实压力。
4.模具温度设定根据试模产品的要求,设置合适的模具温度,以保证注塑成型后的产品质量。
5.冷却时间设定根据试模产品的要求,合理设定冷却时间,以保证熔融塑料充分冷却和凝固,以获得理想的产品质量。
6.射嘴和注射缸位置调整调整射嘴和注射缸的位置,以确保注塑过程中塑料能够均匀地填充模具腔体。
三、试模要求1.产品尺寸要求试模产品的尺寸要求应与产品设计要求一致,包括长度、宽度、高度和壁厚等。
2.产品外观要求试模产品的外观要求应与最终产品的外观要求一致,包括表面光滑度、色彩和纹理等。
3.产品物理性能要求试模产品的物理性能要求应与最终产品的物理性能要求一致,包括拉伸强度、冲击性能和硬度等。
注塑模具试模作业指导书

注塑模具试模作业指导书注塑模具试模作业指导书1.介绍注塑模具试模作业指导书旨在指导操作人员正确使用注塑模具进行试模操作。
本指导书详细描述了试模前的准备工作、试模步骤、常见问题及解决方法等内容,以确保试模作业的安全、高效进行。
2.准备工作2.1 材料准备2.1.1 确保所需注塑材料已经准备好,并进行质量检测。
2.1.2 检查注塑材料的储存条件,确保其干燥、无杂质。
2.1.3 将注塑材料按照要求放置在指定区域。
2.2 模具检查2.2.1 检查注塑模具的外观,排除表面污垢,确保模具干净。
2.2.2 检查模具零部件,确保其完整、无损。
2.2.3 清洁模具的冷却系统,确保其畅通无堵塞。
2.2.4 涂抹模具专用防锈剂,保持模具的表面光洁。
2.3 设备准备2.3.1 开启注塑机设备并进行预热。
2.3.2 检查注塑机的工作性能,确保其正常运转。
2.3.3 准备好所需的模具安装工具。
3.试模步骤3.1 模具安装3.1.1 将模具安装在注塑机上,并确保模具与机器连接紧密。
3.1.2 安装模具的保护装置,确保操作人员的安全。
3.2 调整注塑参数3.2.1 根据注塑产品的要求,调整注塑机的温度、压力、速度等参数。
3.2.2 进行注塑材料的预热和预塑。
3.3 开始试模3.3.1 打开注塑机的开关,将注塑材料注入模具中。
3.3.2 关注注塑机的工作情况,确保注塑过程顺利进行。
3.3.3 观察试模产品的质量,确保其满足要求。
4.常见问题及解决方法4.1 模具堵塞问题:模具冷却系统堵塞,导致注塑过程中温度过高。
解决方法:清洁模具冷却系统,确保其畅通无堵塞。
4.2 产品质量不合格问题:产品存在短射、气孔等缺陷。
解决方法:调整注塑参数,改善注塑过程中的温度、压力控制。
5.附件本文档附带以下附件供参考:- 注塑模具试模检查表- 注塑参数调整记录表6.法律名词及注释6.1 注塑材料:用于注塑过程中的塑料原材料。
6.2 模具:用于塑料制品成型的工装,包括模具本体及相关零部件。
模具管理制度
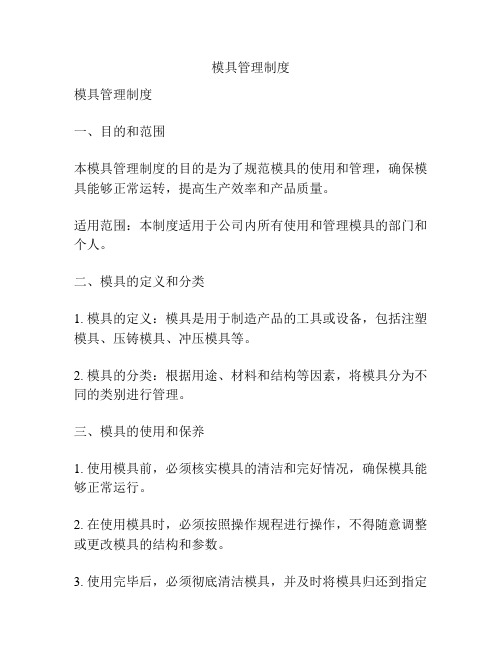
模具管理制度模具管理制度一、目的和范围本模具管理制度的目的是为了规范模具的使用和管理,确保模具能够正常运转,提高生产效率和产品质量。
适用范围:本制度适用于公司内所有使用和管理模具的部门和个人。
二、模具的定义和分类1. 模具的定义:模具是用于制造产品的工具或设备,包括注塑模具、压铸模具、冲压模具等。
2. 模具的分类:根据用途、材料和结构等因素,将模具分为不同的类别进行管理。
三、模具的使用和保养1. 使用模具前,必须核实模具的清洁和完好情况,确保模具能够正常运行。
2. 在使用模具时,必须按照操作规程进行操作,不得随意调整或更改模具的结构和参数。
3. 使用完毕后,必须彻底清洁模具,并及时将模具归还到指定的存放位置。
4. 定期对模具进行保养和维修,延长模具的使用寿命。
四、模具的保管和管理1. 对于模具的存放位置,必须专门设立仓库或指定的存放区域,确保模具的安全和完整。
2. 模具必须由专人负责保管,建立模具档案,记录模具的基本信息、使用情况和维修记录等。
3. 模具的借用和归还必须通过书面申请和审批,并填写借用和归还记录。
4. 对于损坏或报废的模具,必须及时进行报废处理,并填写报废记录。
五、模具的维修和维护1. 模具维修必须由专业的技术人员进行,不得随意进行维修操作。
2. 维修过程中,必须按照维修规程进行操作,确保模具的准确和安全。
3. 维修结束后,必须进行模具试模,并记录试模情况,确保模具的正常使用。
4. 模具维护包括定期清洁、润滑和更换易损件等,以保证模具的正常运转。
六、违反模具管理制度的处理对于违反模具管理制度的行为,将根据情节轻重进行相应的处理,包括口头警告、书面警告以及工资扣款等。
七、附件1. 模具操作规程:详细说明模具的使用方法和注意事项。
2. 模具保养表:记录模具的保养情况和维修记录。
3. 模具借用申请表:用于申请借用模具。
本模具管理制度自发布之日起生效,并向公司内所有部门和个人进行通知和培训。
注塑试模作业指导书
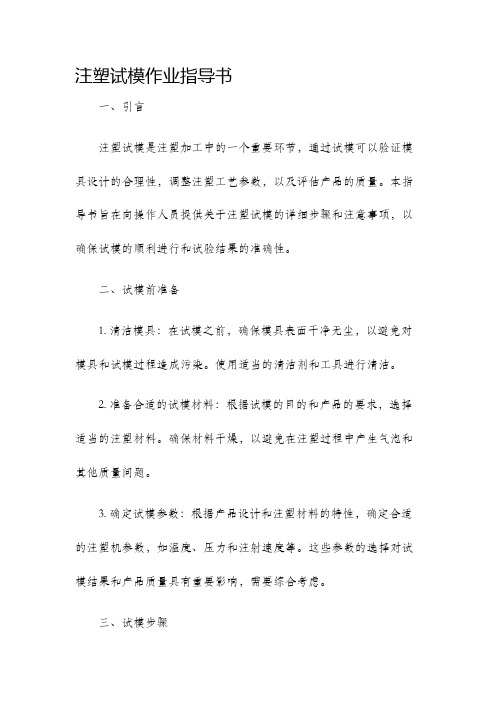
注塑试模作业指导书一、引言注塑试模是注塑加工中的一个重要环节,通过试模可以验证模具设计的合理性,调整注塑工艺参数,以及评估产品的质量。
本指导书旨在向操作人员提供关于注塑试模的详细步骤和注意事项,以确保试模的顺利进行和试验结果的准确性。
二、试模前准备1. 清洁模具:在试模之前,确保模具表面干净无尘,以避免对模具和试模过程造成污染。
使用适当的清洁剂和工具进行清洁。
2. 准备合适的试模材料:根据试模的目的和产品的要求,选择适当的注塑材料。
确保材料干燥,以避免在注塑过程中产生气泡和其他质量问题。
3. 确定试模参数:根据产品设计和注塑材料的特性,确定合适的注塑机参数,如温度、压力和注射速度等。
这些参数的选择对试模结果和产品质量具有重要影响,需要综合考虑。
三、试模步骤1. 安装模具:将试模所需模具安装到注塑机上。
确保模具位置正确,并通过紧固件固定模具,以确保稳定性。
2. 注塑机调试:启动注塑机,根据试模参数进行调试,调整温度、压力和速度等参数,并将试模材料导入注塑机料斗中。
3. 启动试模:按照注塑机操作步骤,启动注塑机进行试模。
注意观察注塑机和模具的运行状态,确保正常运转。
4. 观察注塑过程:在注塑过程中,注意观察注塑材料的熔融状态和充模情况。
根据需要进行调整,确保产品的尺寸和形状符合设计要求。
5. 停机观察:在试模过程中,及时停机观察和检查产品的质量。
尽量保留试模样品,以供后续评估和分析。
6. 试模结束:试模完成后,关闭注塑机,清理模具和注塑机设备。
将试模样品分类保存,并填写试模记录表,以备参考和进一步分析。
四、注意事项1. 安全第一:在进行注塑试模时,一定要遵守注塑机的安全操作规程,佩戴必要的防护装备,确保人身安全。
2. 精确记录:在试模过程中,准确记录注塑机参数、模具状态、试模材料和产品质量等信息。
这些记录是分析和评估试模结果的重要依据。
3. 合理调整:在试模过程中,根据观察和实际情况,及时调整注塑机参数和模具结构等,以获得更好的试模效果。
注塑模具试模作业指导书
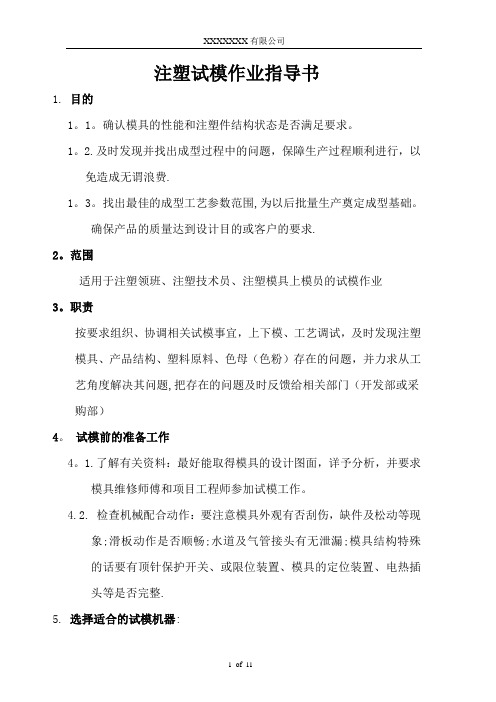
注塑试模作业指导书1. 目的1。
1。
确认模具的性能和注塑件结构状态是否满足要求。
1。
2.及时发现并找出成型过程中的问题,保障生产过程顺利进行,以免造成无谓浪费.1。
3。
找出最佳的成型工艺参数范围,为以后批量生产奠定成型基础。
确保产品的质量达到设计目的或客户的要求.2。
范围适用于注塑领班、注塑技术员、注塑模具上模员的试模作业3。
职责按要求组织、协调相关试模事宜,上下模、工艺调试,及时发现注塑模具、产品结构、塑料原料、色母(色粉)存在的问题,并力求从工艺角度解决其问题,把存在的问题及时反馈给相关部门(开发部或采购部)4。
试模前的准备工作4。
1.了解有关资料:最好能取得模具的设计图面,详予分析,并要求模具维修师傅和项目工程师参加试模工作。
4.2. 检查机械配合动作:要注意模具外观有否刮伤,缺件及松动等现象;滑板动作是否顺畅;水道及气管接头有无泄漏;模具结构特殊的话要有顶针保护开关、或限位装置、模具的定位装置、电热插头等是否完整.5. 选择适合的试模机器:5。
1.锁模力:產品透影面的最低要求鎖模力,以機器鎖模力的70% 为基准。
长×宽(cm)×0。
155(平方英寸in2)×各塑料锁模力系数(ton/in2)常用:ABS、PMMA、 2。
5—4.0 ton/in2; HIPS 、P S 1。
0-2。
0 ton/in2P C、POM 、 3。
0—5.0 ton/in2; GPPS(薄壁) 3。
0—4.0 ton/in2TPU、PP、PE、1。
5-2.5 ton/in2; POM 2.0—5。
0 ton/in25.2.射胶量:产品重量的30%~75%最合适.5.3。
导柱的宽度:装上模具并能安全的锁紧.5。
4.最大的开模行程:能方便取出产品和水口。
6. 原料准备:6。
1 依不同原料特性做正确的烘烤。
6.2 试模与将来量产尽可能采用同样的原料。
7。
安装模具:7。
1装模时注意在锁上所有夹模板及开模前吊钩不要取下,以免夹模板松动或断裂导致模具掉落。
注塑模具试模流程
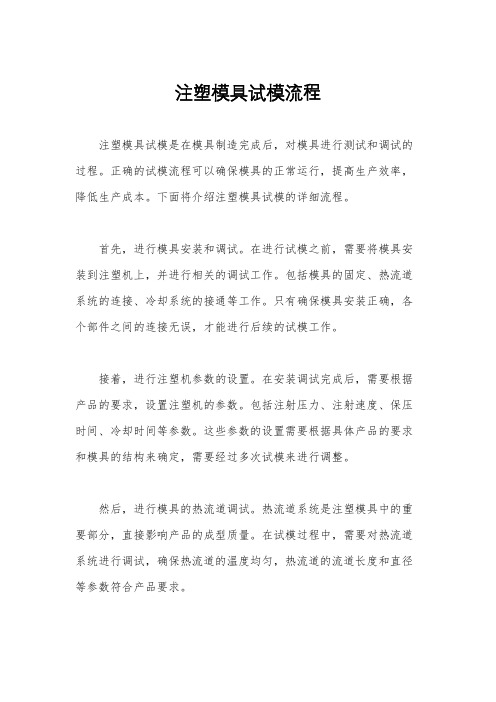
注塑模具试模流程注塑模具试模是在模具制造完成后,对模具进行测试和调试的过程。
正确的试模流程可以确保模具的正常运行,提高生产效率,降低生产成本。
下面将介绍注塑模具试模的详细流程。
首先,进行模具安装和调试。
在进行试模之前,需要将模具安装到注塑机上,并进行相关的调试工作。
包括模具的固定、热流道系统的连接、冷却系统的接通等工作。
只有确保模具安装正确,各个部件之间的连接无误,才能进行后续的试模工作。
接着,进行注塑机参数的设置。
在安装调试完成后,需要根据产品的要求,设置注塑机的参数。
包括注射压力、注射速度、保压时间、冷却时间等参数。
这些参数的设置需要根据具体产品的要求和模具的结构来确定,需要经过多次试模来进行调整。
然后,进行模具的热流道调试。
热流道系统是注塑模具中的重要部分,直接影响产品的成型质量。
在试模过程中,需要对热流道系统进行调试,确保热流道的温度均匀,热流道的流道长度和直径等参数符合产品要求。
接下来,进行模具的冷却系统调试。
冷却系统对模具的寿命和产品的成型质量有着重要影响。
在试模过程中,需要对冷却系统进行调试,确保冷却水的流动畅通,冷却效果良好,避免产品在成型过程中出现热缩等问题。
最后,进行产品的成型试验。
在完成以上调试工作后,就可以进行产品的成型试验。
通过试模,可以检验产品的尺寸精度、表面质量、收缩率等指标,同时也可以检验模具的运行稳定性和生产效率。
总之,注塑模具试模是一个非常重要的环节,直接关系到产品的质量和生产效率。
正确的试模流程可以确保模具的正常运行,提高生产效率,降低生产成本。
因此,对于模具制造厂家和注塑加工厂来说,都需要重视注塑模具试模工作,制定科学合理的试模方案,确保模具的顺利投产。
注塑模具的试模与维修

1 引 言
模 具 外 露 部 分 锐 角 应 倒 钝 ,喷 漆 、 打 印 模 具 名 称 、生 产
日期 、合 模 标 记 、装 模 方 向标 记 等 符 号 。
征一 — _
_
模具 制 造 基 本 完成 后 ( 面或 有要 求 的 表面 还 没 有 镜
模 具 吊 装 面 应 有 起 重 吊环 螺 纹 孔 , 动 、 定 模 锁 码 ,以 利
精抛光) ,必 先上 机 试 模 。其 目的 是 及 时发 现 模 具设 计 及 制 造 中 的 问题 ,以 便 及时 对 模 具 加 以 改进 和 修
t a iy o o e ta d a o d t q p e r pe s na c i e c r i g. he qu lt f t m de t s n v i he e ui m nt o r o la c d ntoc u r n he
注 塑 模 具 的 试 模 与 维 修
杨 海 鹋 ( 门职业 技 术学 院 , 广 东 江 门 ,59 4 ) 江 2 0 0
摘 要:本文通过 对注塑模具试模前的检查 ,模具 的安装 .注塑 机空运转 试车 ,注塑成型工 艺凋整.模 具维修及验收 几方面进行 r比较详细 的阐述 .指 导参 与试模 与维修 人员工作 内容 及应注意的 项 ,使少走弯路 ,减 少试模次数 ,提高试模质 ,同时避 免设 备或 人身事 故发生。
2 试模前模具检查
试模前主要从一下几方面检查模具外观质量 : 模 具 闭 合 高 度 ,与 机 床 各 部 位 配 合 尺 寸 ,顶 出 形 式 ,开
各 滑 动 零 件 配 合 间 隙适 当 ,避 免 卡 死 、咬 伤 。 起 止 位 置 的 定 位 准 确 可 靠 。 镶 嵌 零 件 应 紧 固 、无 松 动 且 结 构 合 理 ,便
注塑试模步骤及注意事项

注塑试模步骤及注意事项注塑试模步骤及注意事项注塑试模步骤及注意事项【全球塑胶网20__年3月12日网讯】1.欲试之原料务必先行干燥.2.模具挂上,中心孔要对准确无误,锁模力视模具大小及投射面积大小而进行调整.当射出时分模面不是因为射压过高而产生毛边,可逐渐加大锁模力,直到不起毛边为主,如此可延长模具使用寿命.锁模压力选在50-70之间,不得大于95为佳.3.开关模速度,压力,位置,距离调整妥当,低压保护必须调校好,这是基于对新模不了解,有滑块之模具开关模速不可太快,有抽心的模应用手先行试验其功能是否正常,否则因一时失误,将导致模具的损坏.4.设定成型条件,包括射出料温,压力,速度,时间,位置,计量距离等.射压,速度,计量由低而高依成型状况而定,射出时间,冷却时间由长至短,依成品情形而减速少,如此可防止粘模及过度充填.5.适当选调背压,注意垫料量在0.5CM-1.0CM为宜,这样无论是新模或产品品质及机台的安全使用都有必要.试模步骤及注意事项(二)1.注意肘节十字头是否伸直,以防射出时模具被逼退而溢出毛边造成模具损伤.2.前几模应喷脱模剂,如脱模顺利,不致产品顶白,变形则可免喷.3.依成品需要,修改各成型条件,如对压力,速度调整1-2模便可看出,如对模温,料温调整,要5分钟左右方可看出结果,避免因急燥而不断变更成形条件,影响试模质量.4.试模中应注意模温的上升,试多模时应加冷却水,依据料质选择料温.5.背压依成品状况而调整,松退距离以不介入空气为原则,储料中原料粘度低,转速可较快,原料粘度高应放慢,注意用背压时,转速越快,原料的熔融越均匀,但应注意其有无熔胶过热现象.6.料管的料要完全射完后方可停机,必要时必须清洗料管,吹干模具冷却水路之冷却水,擦干净模腔料屑,喷防锈油.7.填写试模报告,首件确认表,记录各成型条件,当第二次试模时,参考模具不良状况及欲修改的地方,均需作好记录射出成型的操作条件射出成型的操作条件一.关模压:原则上应大于塑胶射入模内的总压,以不出毛边为基准.二.压力和速度有部分相同的关系作用于模内,目的使原料进入模内能均匀,撤底,适量的充满各角落.太低会短射,缩水,太高有毛边,过饱,粘模.烧焦,易损模具及内应力高等不良现象.三.速度:速度的快慢决定原料在模具浇道内及成品中之状况,快有毛边,过饱.烧焦,粘模,慢了出现短射,缩水,结合不良易断等.四.温度:原料不同,温度各异太低溶胶颜色不均,成品内应力增大,因温度过低增压过高,可能引起螺杆断裂,过高,产品有毛边,又因冷却产生温差,引起收缩;原料会分解,变黄,变色,易断裂.冷却时间变长,气不容易排出,会有瓦斯气.五.背压:螺杆在旋转加料时后退之阴力称为背压.其作用使原料在输送压缩中更加紧密.能使原料的空气,水份从螺杆后排出,使溶胶中不含影响成品表面的气体成份.低会有气泡,表面银纹.高会过热,结块,溢胶,周期长,螺杆不退.同时松退的应用很重要:背压高时务必用松退并注意距离,要不介入空气及不溢胶为准则.六.模温高低及冷却时间的长短,影响成品的粘模,缩水,尺寸公差,表面亮度,周期等,应依实际情况而适时调整.另压克力,PC如成品肉厚时要有模温,才不会产生气泡及应力.(因肉厚冷热不均)BMC的成型要点BMC是以特殊途不饱和聚脂为主之热固硬化性树脂,具有优良的电气绝缘特性,耐热性,耐燃性,高机械强度尺寸安定性.耐蚀性,耐水性,收缩稳定性等.为各种热固硬化性成型材料中最高级品.其加工成型条件如下:1.成型温度:成型温度与MBC 热固性聚脂塑胶之流动性及其所选择加工成型机械加工方式有极度大之关系因素.温度在140℃-170℃2.成型时间:加工成型时间与当时模具正确温度及成品的肉厚,形状有关,一般硬化程度可由表面光泽予以段定,3.成型压力:成型压力视而不见所选择加工成型机械与方式而定,材料加工后,成品表面光泽时之压力,其压力在20-200KG/CM24.储存:MBC材料庆置18℃以下之冷暗处,使用后剩余品应予密闭保存,一般正常使用可存放一个月,外在之温度与MBC之软,硬将影响其储存期.如使用冷藏将延长BMC之寿命.5.用途:应用在各种电气产品,通信资问心无愧机零件,汽车类零件,电动工具绝缘披覆,超大型静音马达,食品餐具等均广泛应用.几种特殊原料的成型特性含玻纤的成型要点1.FRTP的流动性低于非强化料,所以常增加管温及模温,射出压力等.同理模子的浇口,横浇道,浇口等的尺寸,也须大天非强化料.2.成型收缩率甚大于非强化树酯,呈方向性的流动,所以浇口方向设法减少配向所致的不良影响.3.成型品的胶接线部强度,常低于其他部份,在设计制品模子时须加注意于熔接部设排气孔,不致包风现象4.模子各部份(特别是浇口)或螺杆组件,熔胶管等磨耗快,宜注意材质及表面的硬度处理低发泡的成型要决在射出计量终了,螺杆后退时,在等待次一射出开始的期间,管内的发泡剂也慢慢开始分解,其气体压力,却使螺杆后退,故宜在射出缸的油压回路设背压调整回路,抑止杆后退.同时射嘴漏料也增多,宜用弹簧阀的控制.模内排气孔不充份时,其花模和光泽不利.螺杆制造宜用稍有混练型的较易有发泡作用.电木尿素等成型1.换装另设计制造的电木射击出用熔胶管及螺杆,射嘴等.用油热循环式的加温,油温控制在80℃-100℃左右,模温控在160℃-180℃左右.2.模子两边各安装圆柱电热管,两面模板装硬质石棉板,它是和塑胶成相反的,必须在高温模内加热成型,所以模子必用用耐高温铁材,并电镀优良,浇口加大排气口加大,料管内绝对不能有滞料存在,一次定射完毕并到底.3.当温度达到开始第一次射入后,螺杆须等15-20秒开始加料动作.加完后把射座暂松退一下,让射嘴与母模暂分开一点,因母模温度高过射嘴,能便射嘴部硬化而射不出料.一模时间在45秒或55秒间(看成品厚薄),才开模取成品,依次完成二次射出.NL-9成型重点1.尼龙的成型,其成型厚度对收缩率有较大影响.模温高,收缩会增大.射压调整很重要,并应注意其前收缩和后收缩.对尺寸要求严格的成品更应重视.2.烘料:因尼龙的吸湿性最大.放置久了,极难烘干,原料应先进先用,避免放置过久.同时未烘干的原料切勿进入下料口.因会使原料在螺牙上卷曲卡住.造成不加料,所以说要常注意烘料桶的料是否低于警界线,如低于就得加料以免料烘不干.3.尼龙属高温水性,易熔解,但固化也快.其融点温度与成型温度相差5-10℃而己,因此造成其变化范围较窄.4.其粘度低,容易流涕,加热温度在控制要注意,防止固化溢料,松退要注意应用.勿用背压.5.尼龙对温度依存性很大,射出速度要快.防止原料的硬化.太薄处易冷化引起充填不饱.结晶化也低.造成成品有透明性.6.尼龙的润滑性好,耐冲击好,但尺寸安定较差,属于工程塑胶.7.尼龙成型螺杆选择上要压缩比大特别留意止逆环的磨损程度应低于5-10条,如磨损过多,造成加料不稳或不加料.影响原料的供输如果磨损要速更换止逆环.以免加长周期影响生产进度及浪费电源8.尼龙加色粉会造成加料不顺,应注意其有无色粉粘于螺牙上,必要时要加滑石粉给予排除,参考用量:1KG+0.5G滑石粉.9.尼龙参考成型条件:模温:60-80度,料管温220-260度,烘料80-110度,2-4H,软化点:220度。
注塑科学试模方法讲解(图文全)
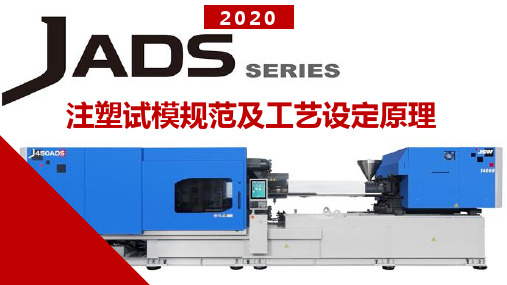
五,锁模力公式 锁模力公式:
P是模腔压力约等于射出峰压 S产品最大投影面积
PO是流程和最薄壁厚的比值
K是材质常数。
六,最佳锁模力确认
1.取最大锁模力的90%,成型3模,记录每模产品的重 量;
2.锁模力依次减少5Ton,每次成型3模,记录每模产 品重量,直到产品重量突然变大,重量增加5%左右 产品周边开始产生飞边时为止。
5.4
无
2
5.5
有
1
5.6
有
0
1
2
3
4
5
6
7
8
6.0
有
系列2
八,胶口冻结测试
2.设定一个较大的保压压力,保压时间先设定为1秒时,每次成型3模;如表格所示,依次增加保压时间,减少冷 却时间,使整个循环周期不变(一直到浇 口冷冻封胶,产品重量不增加为止);
N 保压 O 时间 .
11
22
43
冷却 第1模 第2
射出量公式 等于圆柱体 体积公式
1.连续依次打5模,称量其重量; 2.记录各模中每个产品的单件重量; 3.减少注塑量,依次充满20%、50%、90%的样品各3模; 4.称量并记录上述每个产品的重量; 5.如果产品最大的重量与最小的重量差异小于2%的重量则 可接受——若重量波动误差在2%以内,则表明型腔进胶平 衡,否则进胶就不平衡;
射出量公式
射出容积 V= π*(Do1/2)²*ST*损耗
V:射出容积 CM3 Do:螺杆直径 CM
。
例:螺杆直径 44mm 射出行程 45mm V= π*(4.4*1/2)²*4.5*0.98=67.27CM3 射出重量 G =V*η*δ V:射出容积 η:比重(密度) δ:机械效率
模具管理制度(注塑部管理)

6.相关记录
工模制造修改维修申请表
5.模具的管理
5.1注塑部模具管理人员负责对所有模具进行标识,标明客户名称、型间领用制度,模具管理人员做好模具投入使用的记录。模具使用过程中,生产车间必须做好所生产产品的首件和末件检验,以便于随时掌握模具的完好状况,确保产品质量和车间生产不受影响。
5.3模具在每批产品加工结束后,由模具管理人员对模具和末件产品进行检查,确认完好后,对模具进行清洁并擦油防锈,放入模具架,以便下次使用。
4.2模具的验证
新制作或购买的模具,交付后由注塑部按照要求对模具进行检验,检验合格后安排生产车间进行试模,试模产品交检验部门根据产品技术要求进行检验确认,试模产品检验合格后,填写“工模制造修改维修申请表”,凭“工模制造修改维修申请表”办理模具入库手续。
4.3模具的标识
本公司的所有模具必须有明显的客户和产品工序标识。
5.4模具管理人员、生产部门发现模具损坏或发现所加工产品不能达到规定的技术要求,应及时向工程部报告,由工程部组织相关人员对模具进行检查验证并进行修理。如本公司不能对损坏模具进行修理,需外送修理,必须填写“工模制造修改维修申请表”,注塑部和工程部签字后,由采购部负责到公司认可的模具加工单位修理。修复后的模具必须按〈4.2模具的验证〉程序进行验证。
1.目的
为加强模具的使用和管理,确保模具符合生产工艺要求、产品质量要求,确保生产顺利特制定本制度。
2.适用范围:适用于本公司的模具制作、购买、使用、维护、修理和报废。
3.工程部为本公司的模具管理部门,负责模具的所有管理工作。
注塑件试模常见问题与解决方法

注塑件试模常见问题与解决方法 2009年02月14日13:52 生意社生意社02月14日讯收縮痕一、注塑件缺陷的特征通常与表面痕有关,而且是塑料从模具表面收缩脱离形成的。
二、可能出现问题的原因(1).熔融温度不是太高就是太低。
(2).模腔内塑料不足。
(3).冷却阶段时接触塑料的面过热。
(4).流道不合理、浇口截面过小。
(5).模温是否与塑料特性相适应。
(6).产品结构不合理(加强进古过高,过厚,明显厚薄不一).(7).冷却效果不好,产品脱模后继续收缩。
三、补救方法(1).调整射料缸温度。
(2).调整螺杆速度以获得正确的螺杆表面速度。
(3).增加注塑量。
(4).保证使用正确的垫料;增加螺杆向前时间;增加注塑压力;增加注塑速度。
(5).检查止流阀是否安装正确,因为非正常运行会引致压力流失。
(6).降低模具表面温度。
(7).矫正流道避免压力损失过大;根据实际需要,适当扩大截面尺寸。
(8).根据所用塑料的特性及产品结构适当控制模温。
(9).在允许的情况下改善产品结构。
(10).设法让产品有足够的冷却。
包封一、注塑件缺陷的特征可以容易地在透明注塑件的“空气阱”内见到但也可出现在不透明的塑料中,这与厚度有关,而且常因塑料收缩离开注塑件中心而引起。
二、可能出现问题的原因(1).模具未充分填充。
(2).止流阀的不正常运行。
(3).塑料未彻底干燥。
(4).预塑或注射速度过快。
(5).某些特殊材料应用特殊的设备生产。
三、补救方法(1).增加射料量。
(2).增加注塑压力。
(3).增加螺杆向前时间。
(4).降低熔融温度。
(5).降低或增加注塑速度。
(例如对非结晶体类的塑料要增加45%速度)。
(6).检查止逆阀是否裂开或无法运作。
(7).应根据塑料的特性改善干燥条件,让塑料彻底干燥。
(8).适当降低螺杆转速和增大背压,或降低注射速度。
制品成型尺寸精度低注塑件缺陷的特征一﹐注塑过程中重量尺寸的变化超过了模具、注塑机、塑料组合的生产能力。
试模操作规程
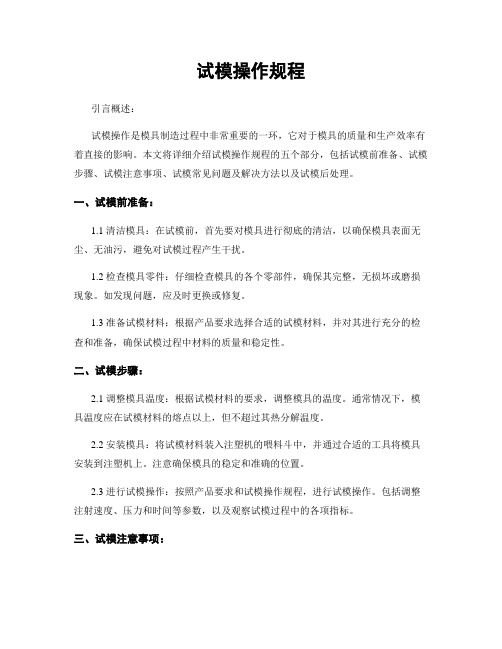
试模操作规程引言概述:试模操作是模具制造过程中非常重要的一环,它对于模具的质量和生产效率有着直接的影响。
本文将详细介绍试模操作规程的五个部分,包括试模前准备、试模步骤、试模注意事项、试模常见问题及解决方法以及试模后处理。
一、试模前准备:1.1 清洁模具:在试模前,首先要对模具进行彻底的清洁,以确保模具表面无尘、无油污,避免对试模过程产生干扰。
1.2 检查模具零件:仔细检查模具的各个零部件,确保其完整,无损坏或磨损现象。
如发现问题,应及时更换或修复。
1.3 准备试模材料:根据产品要求选择合适的试模材料,并对其进行充分的检查和准备,确保试模过程中材料的质量和稳定性。
二、试模步骤:2.1 调整模具温度:根据试模材料的要求,调整模具的温度。
通常情况下,模具温度应在试模材料的熔点以上,但不超过其热分解温度。
2.2 安装模具:将试模材料装入注塑机的喂料斗中,并通过合适的工具将模具安装到注塑机上。
注意确保模具的稳定和准确的位置。
2.3 进行试模操作:按照产品要求和试模操作规程,进行试模操作。
包括调整注射速度、压力和时间等参数,以及观察试模过程中的各项指标。
三、试模注意事项:3.1 安全操作:试模过程中,要严格遵守安全操作规程,佩戴个人防护装备,确保人身安全。
3.2 观察试模过程:密切观察试模过程中的各项指标,如温度、压力、速度等,并根据需要进行及时调整。
3.3 记录试模数据:及时记录试模过程中的各项数据,包括温度、压力、注射量等,以便后续分析和改进。
四、试模常见问题及解决方法:4.1 模具堵塞:如果在试模过程中发生模具堵塞,应立即停机检查,清除堵塞物,并调整注射参数。
4.2 产品缺陷:如果试模出现产品缺陷,需要仔细分析原因,如模具设计问题、材料问题等,并采取相应的解决措施。
4.3 模具损坏:如发现模具损坏情况,应停机检查,找出原因并进行修复或更换。
五、试模后处理:5.1 清洁模具:试模结束后,要对模具进行彻底的清洁,以防止杂质残留和腐蚀。
模具管理制度
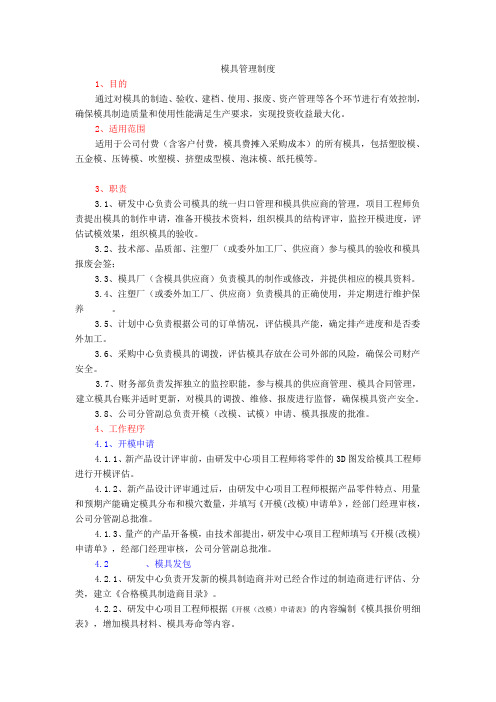
模具管理制度1、目的通过对模具的制造、验收、建档、使用、报废、资产管理等各个环节进行有效控制,确保模具制造质量和使用性能满足生产要求,实现投资收益最大化。
2、适用范围适用于公司付费(含客户付费,模具费摊入采购成本)的所有模具,包括塑胶模、五金模、压铸模、吹塑模、挤塑成型模、泡沫模、纸托模等。
3、职责3.1、研发中心负责公司模具的统一归口管理和模具供应商的管理,项目工程师负责提出模具的制作申请,准备开模技术资料,组织模具的结构评审,监控开模进度,评估试模效果,组织模具的验收。
3.2、技术部、品质部、注塑厂(或委外加工厂、供应商)参与模具的验收和模具报废会签;3.3、模具厂(含模具供应商)负责模具的制作或修改,并提供相应的模具资料。
3.4、注塑厂(或委外加工厂、供应商)负责模具的正确使用,并定期进行维护保养。
3.5、计划中心负责根据公司的订单情况,评估模具产能,确定排产进度和是否委外加工。
3.6、采购中心负责模具的调拨,评估模具存放在公司外部的风险,确保公司财产安全。
3.7、财务部负责发挥独立的监控职能,参与模具的供应商管理、模具合同管理,建立模具台账并适时更新,对模具的调拨、维修、报废进行监督,确保模具资产安全。
3.8、公司分管副总负责开模(改模、试模)申请、模具报废的批准。
4、工作程序4.1、开模申请4.1.1、新产品设计评审前,由研发中心项目工程师将零件的3D图发给模具工程师进行开模评估。
4.1.2、新产品设计评审通过后,由研发中心项目工程师根据产品零件特点、用量和预期产能确定模具分布和模穴数量,并填写《开模(改模)申请单》,经部门经理审核,公司分管副总批准。
4.1.3、量产的产品开备模,由技术部提出,研发中心项目工程师填写《开模(改模)申请单》,经部门经理审核,公司分管副总批准。
4.2 、模具发包4.2.1、研发中心负责开发新的模具制造商并对已经合作过的制造商进行评估、分类,建立《合格模具制造商目录》。
试模操作规程
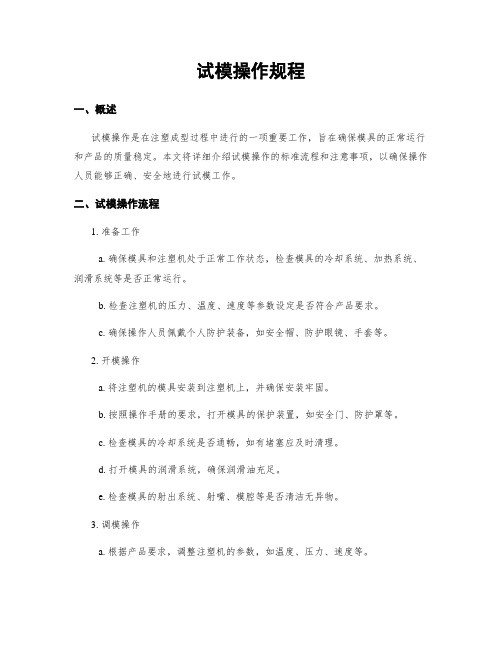
试模操作规程一、概述试模操作是在注塑成型过程中进行的一项重要工作,旨在确保模具的正常运行和产品的质量稳定。
本文将详细介绍试模操作的标准流程和注意事项,以确保操作人员能够正确、安全地进行试模工作。
二、试模操作流程1. 准备工作a. 确保模具和注塑机处于正常工作状态,检查模具的冷却系统、加热系统、润滑系统等是否正常运行。
b. 检查注塑机的压力、温度、速度等参数设定是否符合产品要求。
c. 确保操作人员佩戴个人防护装备,如安全帽、防护眼镜、手套等。
2. 开模操作a. 将注塑机的模具安装到注塑机上,并确保安装牢固。
b. 按照操作手册的要求,打开模具的保护装置,如安全门、防护罩等。
c. 检查模具的冷却系统是否通畅,如有堵塞应及时清理。
d. 打开模具的润滑系统,确保润滑油充足。
e. 检查模具的射出系统、射嘴、模腔等是否清洁无异物。
3. 调模操作a. 根据产品要求,调整注塑机的参数,如温度、压力、速度等。
b. 逐步调整模具的开合速度,观察模具的运行情况,如有异常应及时停机检查。
c. 调整模具的冷却水温和流量,确保模具温度均匀稳定。
4. 试模操作a. 将预热好的原料注入注塑机的料斗中。
b. 启动注塑机,进行首次射出,并观察产品的成型情况。
c. 根据产品要求,逐步调整注塑机的参数,如射胶压力、射胶时间、射胶速度等。
d. 进行多次射出,观察产品的质量和尺寸是否符合要求。
e. 根据试模结果,适时调整模具的参数,如开合力、冷却时间等。
5. 试模记录a. 在试模过程中,记录每次射出的参数和结果,包括射胶压力、射胶时间、射胶速度、产品质量等。
b. 如有异常情况或问题,及时记录并报告相关人员。
c. 根据试模记录,分析问题原因,并进行相应的改进措施。
三、注意事项1. 操作人员应熟悉注塑机的操作规程和安全要求,严格按照标准流程进行试模操作。
2. 在试模过程中,应随时关注注塑机和模具的运行情况,如有异常应及时停机检查。
3. 操作人员应定期检查模具的润滑系统、冷却系统等,确保其正常运行。
试模操作流程标准规范

试模操作流程试模主要分四部分:(1)试模前模具的检查(2)试模前的准备工作和调试(3)试模时的注意事项(4)试模后模具的检收一、试模前模具的检查模具做好后,需要对模具进行试模前的检查,以发现模具设计和制造中的问题,以便及时纠正,其具体步骤如下:(1)注塑模的外观检查1.成型零件、浇注系统等与熔料接触的表面应光滑、平整、无塌坑、伤痕等缺陷。
2.模具的闭合行程,安装于机器的各配合部位尺寸、脱模方式、开模距离、模具工件要求等应符合设备的相关条件。
3.模具上应有生产号和合模标志,各种接头、阀门、附件、备件应齐全。
4.各滑动零件的配合间隙应符合要求,起止位置定位正确,镶件紧固应紧固牢靠。
5.对于注塑腐蚀性较强的注塑模,其模具型腔的表面应镀铬和防腐处理。
6.模具的外观部分不应当有锐角,大、中型模具应有起吊用的吊孔、吊环。
7.互相接触的承压零件,应有合理的承压面积和承压方式,避免直接承受挤压。
8.模具的稳定性良好,有足够强度,工作时应受力匀衡,行动平稳。
(2)模具的空运转检查模具安装好后,必须经过空运转检查,经便进一步发现问题,进而解决问题。
1.将模具缓缓合拢,合模后各结合面均应接触紧密,不得出现间隙。
2.开模时顶出脱模机构应保证顺利脱模,以便取出塑件和浇注系统废料。
3.活动型芯,顶出及导向部分等运动时应滑动平稳、灵活、动作协调可靠。
4.检查各锁紧机构、应能可靠、稳妥地锁紧,各紧固件不得有任何松动现象。
5.各气动、液动控制系统动作正确,不泄漏、不产生过大振动,各阀门工作正常。
6.冷却系统的水路应畅通,不漏水,各种控制阀门控制正常。
二,试模前的准备工作及调试试模是为了检查模具制作的质量好坏,能否生产出合格产品来。
1.试模前,应检查所用原料是否符合要求,不符合要求的应进行处理或更换;欲试之原料先行干燥,PE、PP、PO M不需干燥其余均要,利用新料试才标准。
2•模具挂上中心孔要对准锁模力以总顿数的1/3即可,如射出时分模面不是因射压太高之关系起毛边,可渐渐增加锁模顿数直到不起毛边为至如此做法可增长模具使用寿命。
- 1、下载文档前请自行甄别文档内容的完整性,平台不提供额外的编辑、内容补充、找答案等附加服务。
- 2、"仅部分预览"的文档,不可在线预览部分如存在完整性等问题,可反馈申请退款(可完整预览的文档不适用该条件!)。
- 3、如文档侵犯您的权益,请联系客服反馈,我们会尽快为您处理(人工客服工作时间:9:00-18:30)。
注塑模具试模管理
1. 试模是指模具初装后进行的塑件生产试验,以考核模具的性能和塑件的质量。
如何控制和管理不同的试模申请,制定相应的试模计划,由注塑统一安排试模计划。
2. 试模通知:试模通知是提醒各参加试模部门、人员做好相应的准备工作以便能够合理的安排试模工作,其包括通知参加试模部门、模具编号、塑件编号、试模日期、试模用料、试模样板数量、试模类别、试模成本、试模状况、模具数据等信息。
3. 制模/改模管理:系统提供制模、改模等加工任务的管理,根据待排产的加工任务,优化工模车间能够进行合理化的生产排程,并计划其加工所需的费用、工时、人员和设备,确保加工任务能够顺利的完成。
4. 试模报告:试模完成后,需要质检部门出具试模报告,反映试模过程中出现的各种情况,包括模具注塑情况和塑件缺陷情况,并注明试模单号、模具编号、塑件名称、试模原因、试模次数、试模日期、塑件批号、试模机器等详细信息。
5. 模具试模合格率:试模合格率反映了模具试模的次数,以及模具试模成功的比率,是衡量模具加工师傅和设计部门的一个重要技术指标。
6. 模具验收管理:模具在试模成功后,客户需确认试模结果,并签收模具验收合格单。
客户签收的模具验收报告单中需从以下几方面考
核:塑件的质量、模具的性能、技术文文件(样板)、交货期等。
模具基础档案:标识模具的名称、型腔数、总装图、产品图以及相关的要求和技术说明(试模或原样品、材料及收缩率,装配要求、体积);模具状态(正常、在修、故障、损坏、报废)。
7. 模具试模记录:模具试模记录主要记录模具的试模日期、试模人员、试模地点、试模设备、试模用料、试模状况说明、试模样品、质检报告。
8. 模具验收记录:模具验收主要记录了该模具验收过程中的情况,包括验收人员、验收日期、验收地点、验收样板、试模报告、模具状况以及验收技术质量等。
9. 模具进厂(入库)记录:模具入库记录记录了该模具进厂(入库)情况,主要包括入库日期、供货商名称、地址、邮编、联系电话和负责人。