零部件缩印改善方案汇总
汽车零部件生产工艺改进工作总结
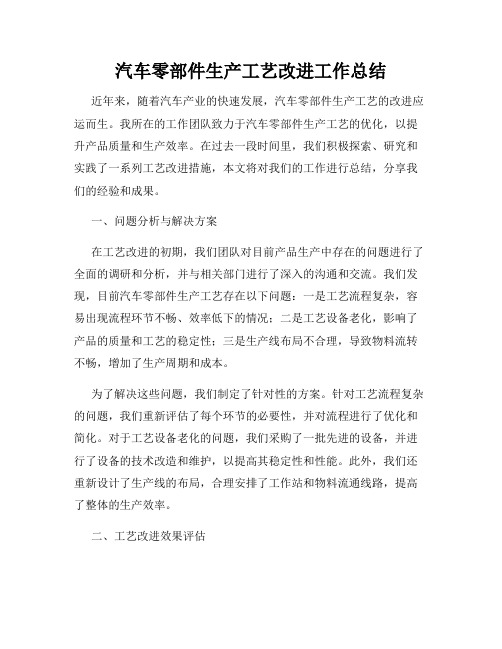
汽车零部件生产工艺改进工作总结近年来,随着汽车产业的快速发展,汽车零部件生产工艺的改进应运而生。
我所在的工作团队致力于汽车零部件生产工艺的优化,以提升产品质量和生产效率。
在过去一段时间里,我们积极探索、研究和实践了一系列工艺改进措施,本文将对我们的工作进行总结,分享我们的经验和成果。
一、问题分析与解决方案在工艺改进的初期,我们团队对目前产品生产中存在的问题进行了全面的调研和分析,并与相关部门进行了深入的沟通和交流。
我们发现,目前汽车零部件生产工艺存在以下问题:一是工艺流程复杂,容易出现流程环节不畅、效率低下的情况;二是工艺设备老化,影响了产品的质量和工艺的稳定性;三是生产线布局不合理,导致物料流转不畅,增加了生产周期和成本。
为了解决这些问题,我们制定了针对性的方案。
针对工艺流程复杂的问题,我们重新评估了每个环节的必要性,并对流程进行了优化和简化。
对于工艺设备老化的问题,我们采购了一批先进的设备,并进行了设备的技术改造和维护,以提高其稳定性和性能。
此外,我们还重新设计了生产线的布局,合理安排了工作站和物料流通线路,提高了整体的生产效率。
二、工艺改进效果评估经过一段时间的实践,我们对采取的工艺优化方案进行了全面的评估。
首先,我们对产品的质量进行了检测和测试,发现产品的合格率明显提升,不合格品数量减少。
此外,产品的外观和功能也得到了进一步改善。
其次,我们对生产周期和成本进行了统计和比较,发现生产周期在新工艺下明显缩短,成本也有所降低。
最后,我们也对员工的工作情况进行了调查和访谈,发现员工的工作负担减轻,工作环境更加舒适,生产效率也得到提升。
三、优化方案的展望和改进建议虽然我们的工艺改进方案取得了一系列显著的成果,但我们也意识到还有更多的工作需要继续完善。
首先,我们计划进一步优化工艺流程,以进一步提高生产效率和产品质量。
其次,我们将继续引进新的设备和技术,为工作团队提供更好的工具和设备支持。
此外,我们还将加强与供应商的合作,以确保原材料质量和供货的及时性。
解决铸件缩松的方法

解决铸件缩松的方法
摘要:铸件缩松是指铸件在使用过程中产生的尺寸变化,导致铸件尺
寸变大,从而降低它的使用性能。
为了解决这个问题,必须采取有效的措施,以防止铸件缩松或控制缩松程度。
本文综述了常用的解决铸件缩松的
方法,包括熔炼技术、浇铸技术、试验技术、材料强度、热处理和机械处
理等。
关键词:铸件缩松;熔炼技术;浇铸技术;试验技术;材料强度;热
处理;机械处理
1. Introduction
铸件缩松是指铸件在使用过程中产生的尺寸变化,导致铸件尺寸变大,从而降低它的使用性能。
铸件缩松通常会导致连接点的放电问题,损坏表
面外观,降低性能,甚至影响工作精度等问题。
因此,正确理解和控制铸
件的缩松现象对工程结构的质量安全十分重要。
为了解决这个问题,必须采取有效的措施,以防止铸件缩松或控制缩
松程度。
本文将简要介绍一些常用的解决铸件缩松的方法,以提高铸件的
质量与性能。
2.1 Melting Technology
熔炼技术是铸件缩松最重要的解决方法之一、采用熔炼技术可以改变
铸件材料的内部结构,从而降低铸件的体积,减少铸件的体积变化。
注塑件缩痕和缩孔的形成机理及其解决措施

F g 2 T ik w l l a i g t ik ma k o o d i h c al e dn o sn r rv i
模 具设 计 、成 型工 艺 和材料 等方 面都 有很 大关 系 。本 文 将分 别从 这 些方 面讨 论 ,提 出避免 或减 少缩 痕 和缩 孔 的解 决措 施 。
2 2 保证 壁厚 均 匀 .
制件 局部 壁厚 过 大时 ,容 易产生 缩 痕或缩 孔 ,可
作者 简介 :欧相麟 ,男 ,18 年生 ,硕士 ,工程师 ,从事注射成 型模 具及 成型应用行业 的工作 。oxag n6 6 .o 91 uinl 5 @13 tm i
OU a g ln。 W ANG h n Xi n 。i Da z o g。 GUAN An— a nn
( eerhadD vl met etr ao a E g er gL brt yfr l t o ictnadPoes g R sac n ee p n C ne,N t nl ni e n a o o a i M df a o n r si , o i n i a r o P sc i i c n
缩痕 产 生在 制件 的表 面 ,指在 制件 表 面形成 的局
部 凹陷 ;缩 孔 产 生 在 制 件 的 内 部 ,除 了 透 明 的 制 件 外 ,一般 难 以从 制件 表 面看到 缩孔 。缩 痕 和缩孔 都 是
图 1 注 塑过 程 的 喷泉 流
由于制件厚壁部分在冷却时没有得到足够的补偿而产
生 的 ,经 常 产生 在局 部壁 厚较 大 的区域 、筋 或 突起 物
的背 面 。
Fg1 F u t nf wi ei et n i ona o t jci il nh n o
零件的改进方案及措施怎么写

零件的改进方案及措施怎么写零件的改进方案及措施。
在制造业中,零件是产品的重要组成部分,其质量和性能直接影响着整个产品的质量和性能。
因此,对零件的改进方案及措施的研究和实施显得尤为重要。
本文将从材料选择、工艺改进、设计优化和质量控制等方面,探讨零件的改进方案及措施。
一、材料选择。
材料是零件的基础,对零件的性能和寿命有着重要影响。
因此,在进行零件改进时,首先要考虑材料的选择。
可以从以下几个方面进行改进:1. 优化材料性能,选择具有优良性能的材料,如高强度、耐磨、耐腐蚀等性能较好的材料,以提高零件的使用寿命和可靠性。
2. 降低成本,选择成本低廉的替代材料,以降低零件的制造成本,提高产品的竞争力。
3. 环保材料,选择符合环保要求的材料,以满足环保政策的要求,降低环境污染。
二、工艺改进。
工艺是零件制造的关键环节,对零件的质量和成本有着重要影响。
因此,在进行零件改进时,需要对工艺进行改进:1. 提高加工精度,采用先进的加工设备和技术,提高零件的加工精度,以满足产品对精度的要求。
2. 降低加工成本,优化加工工艺,降低能耗和材料损耗,降低加工成本。
3. 缩短加工周期,优化工艺流程,提高生产效率,缩短零件的加工周期,以满足客户对交货期的要求。
三、设计优化。
设计是零件的灵魂,对零件的性能和质量有着决定性的影响。
因此,在进行零件改进时,需要对设计进行优化:1. 提高结构强度,优化零件的结构设计,提高零件的强度和刚度,以提高零件的使用寿命。
2. 降低零件重量,采用轻量化设计,减少零件的重量,降低产品的能耗,提高产品的竞争力。
3. 提高装配性能,优化零件的设计,提高零件的装配性能,降低装配成本,提高产品的可靠性。
四、质量控制。
质量是产品的生命线,对零件的质量控制是零件改进的重要环节。
在进行零件改进时,需要加强质量控制:1. 强化检验手段,引入先进的检测设备和技术,提高零件的检测精度,确保零件的质量。
2. 加强过程控制,优化生产工艺,加强生产过程的控制,防止质量问题的发生,提高产品的一致性和稳定性。
零件缩水改善方法

零件缩水改善方法
零件缩水是指在塑胶件成型过程中,由于冷却速度和塑料收缩率的差异,导致塑胶件尺寸变小或内部产生空洞的现象。
下面是一些改善零件缩水的方法:
1. 调整模具温度:通过适当提高模具的温度,可以增加塑料的流动性,减少冷却速度,从而减少缩水问题。
2. 增加注塑压力和时间:增加注塑压力和时间可以促使塑料更充分地填充模具,减少内部空洞和收缩。
3. 优化塑料配方:通过调整塑料的配方,加入适量的填充剂或增强剂,可以改变塑料的收缩率,从而减少缩水问题。
4. 调整浇口位置和大小:浇口的位置和大小对塑料的填充和冷却有重要影响。
通过调整浇口的位置和大小,可以改变塑料的流动方向和冷却速度,从而减少缩水问题。
5. 增加后处理工序:在零件成型后进行后处理,如热处理、退火处理等,可以减小塑料的收缩率,提高零件尺寸的稳定性。
6. 使用气辅成型技术:气辅成型技术通过在注射过程中将气体注入模具中,形成气垫,使塑料在冷却过程中保持更好的形状,从而减少缩水问题。
以上方法仅供参考,建议根据具体情况进行选择和应用。
同时,也可以寻求专业人士的帮助,对模具和工艺进行更为精确的调整和优化。
产品缩印分析与改良
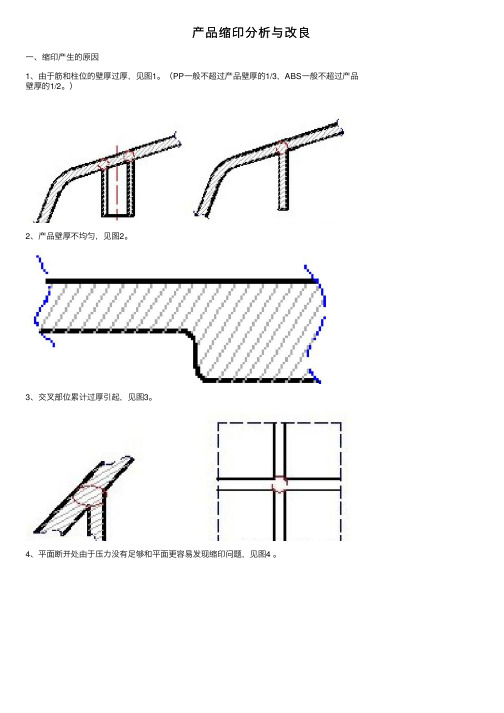
产品缩印分析与改良⼀、缩印产⽣的原因1、由于筋和柱位的壁厚过厚,见图1。
(PP⼀般不超过产品壁厚的1/3,ABS⼀般不超过产品壁厚的1/2。
)2、产品壁厚不均匀,见图2。
3、交叉部位累计过厚引起,见图3。
4、平⾯断开处由于压⼒没有⾜够和平⾯更容易发现缩印问题,见图4 。
5、浇⼝⼤⼩不合适以及注塑流程过长导致压⼒不到位和保压不能到位(压⼒不⾜、短射、保压不⾜、浇⼝过⼩导致浇⼝快速冷却,保压进不去)。
【最佳解决⽅案】在保证产品装配和强度的前提下尽量将引起缩印的筋减薄,但同时不能影响模具的加⼯。
【后备⽅案】(1)通过模具结构解决,通过斜顶、⽕⼭⼝、加胶、减胶、接顺等⽅案解决;(2)通过增加补料钉来解决;(3)通过⼯艺来解决。
在做模具设计时,如果没有厚度上的装配要求,所有卡扣座等和B⾯接触部分的壁厚不超过0.8mm,但有装配要求的BOSS和RIBE不能减薄的根据材料做⽕⼭后或者局部加胶,筋不超过1mm。
⼆、缩印的解决⽅案1、筋和柱位的壁厚过厚引起的缩印,尽量将背⾯的筋减薄以减轻缩印,但筋的厚度低于1mm就存在模具加⼯上的困难,boss壁厚低于1mm将导致推管壁厚过薄,容易断裂,模具寿命⽆法保证,例如:(1)筋厚低于1mm电极难以加⼯,线割或者CNC加⼯都将导致电极变形弯曲;(2)低于1mm的电极在EDM加⼯的时候容易因为发热⽽变形,损公也很厉害,将导致模具加⼯不良;(3)筋厚低于1mm,产品充模也⽐较困但,脱模容易出现断筋的现象。
从以上⼏点综合考虑,筋厚在1mm左右是⽐较经济的,同时⽐较有效解决缩印问题。
从我们的经验来看,如果塑胶材料不是很不理想,可以达到95%以上的筋都不会在表⾯产⽣不能接受的缩印。
⼀般情况下,缩印是⽆法彻底消除的,只能通过各种⼿段综合处理,将缩印减轻⾄能接受的范围内。
在某些(有设计空间的)不能减薄筋位的地⽅,模具设计过程中有以下⼏种⽅案可供选择,可以最⼤程度减轻缩印。
⽅案1:通过增加斜顶加以解决。
铸件缩孔缩松解决方法

铸件缩孔缩松解决方法铸件缩孔缩松是铸造过程中常见的缺陷问题,会对铸件的强度和密封性能造成影响。
为了解决这一问题,需要采取一系列的措施来减少或消除铸件的缩孔缩松现象。
合理设计铸件的结构是解决缩孔缩松问题的关键。
在铸件设计过程中,应尽量避免出现厚度不均匀、壁厚过大或过小等情况,以免产生应力集中和缩孔缩松的隐患。
同时,应留有足够的浇注系统和冷却系统,以保证铸件在凝固过程中有足够的液态金属供应和冷却条件,从而减少缩孔缩松的产生。
选择合适的铸造材料和工艺参数也是解决缩孔缩松问题的重要措施。
铸造材料的选择应考虑其流动性、凝固收缩率和气孔生成倾向等因素,以减少缩孔缩松的发生。
同时,通过优化浇注温度、浇注速度、浇注压力等工艺参数,可以改善铸件的凝固过程,减少缩孔缩松的产生。
加强铸造过程的控制和监测也是解决缩孔缩松问题的必要手段。
在铸造过程中,应严格控制浇注温度、铸型温度和冷却速度等参数,避免过热或过冷引起的缩孔缩松问题。
同时,通过使用合适的质量监测方法,如X射线探伤、超声波探伤等,及时发现和修复铸件中的缩孔缩松缺陷,确保铸件的质量。
可以采用一些特殊的工艺措施来解决铸件缩孔缩松问题。
例如,可以采用真空铸造、压力铸造或浸渍处理等方法,通过改变铸造环境或材料特性,减少缩孔缩松的发生。
此外,还可以在铸件表面施加压力或采用压力鼓包等方式,增加铸件的实体密度,减少缩孔缩松的存在。
铸件缩孔缩松是铸造过程中常见的缺陷问题,但通过合理的设计、选择合适的材料和工艺参数,加强铸造过程的控制和监测,以及采用特殊的工艺措施,可以有效地解决这一问题。
通过这些措施的综合应用,可以提高铸件的质量和性能,确保产品的可靠性和安全性。
注塑件缩痕产生原因及解决方案
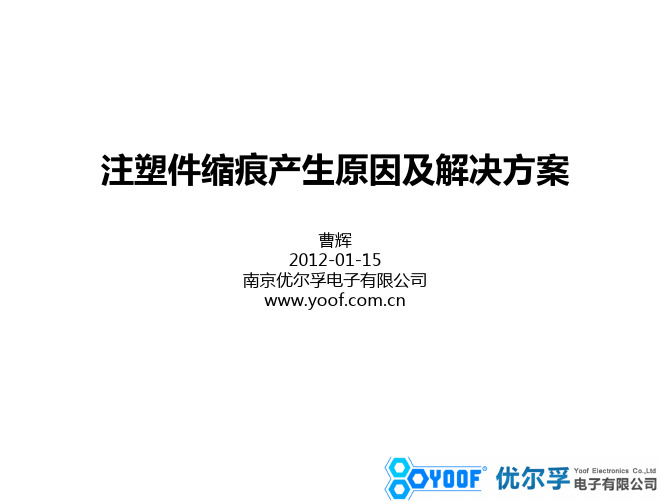
成型不良原因及对策—缩痕 注塑件缩痕产生原因及解决方案
沉孔设计要点(Ⅰ)
3mm3mm贡献 贡献
8
HIPS GROUP
更新日期:11-8-2002
成型不良原因及对策—缩痕 注塑件缩痕产生原因及解决方案
沉孔设计要点(Ⅱ)
3mm3mm贡献 贡献
为保证强度,沉孔的外径一般为内径的2倍
9
HIPS GROUP
11
HIPS GROUP
更新日期:11-8-2002
成型不良原因及对策—缩痕 注塑件缩痕产生原因及解决方案
减少缩痕的方法
成型工艺
3mm3mm贡献 贡献
a.提高注塑压力 b.增大后期保压压力 c.降低缩痕部分所对应的注 射速度 d.降低模具温度 e.降低注塑温度 模具设计 a.加大浇口 b.变短浇口 c.改变流道位置 d.加宽流道 e.减少流动阻力 f. 保证喷嘴和模具结合完好 制品设计 a.把筋、沉孔部位变细 b.在筋、沉孔部位加倒角 c.减小壁厚 d.把表 面设计为花纹以掩盖缩痕
更新日期:11-8-2002
成型不良原因及对策—缩痕 注塑件缩痕产生原因及解决方案
沉孔设计要点(Ⅲ)
3mm3mm贡献 贡献
以上两种方式均可以使沉孔结构得到加强
10
HIPS GROUP
更新日期:11-8-2002
成型不良原因及对策—缩痕 注塑件缩痕产生原因及解决方案
通过CAE分析以减少缩痕
3mm3mm贡献 贡献
成型不良原因及对策—缩痕
3mm3mm贡献 贡献
ቤተ መጻሕፍቲ ባይዱ
注塑件缩痕产生原因及解决方案
曹辉 2012-01-15 南京优尔孚电子有限公司
1
HIPS GROUP
解决铸件缩松的方法

解决铸件缩松的方法李德臣(沈阳鑫浩龙铸造材料公司沈阳110021)Solutions for Casting Shrinkage PorsityLi De-chen(Shenyang Xinhaolong Foundry Materials Co,Ltd.Shenyang · 110021 · China ·)许多铸造厂都普遍存在铸件缩松缺陷。
由此产生的废品率少者15~20%,多者50~70%。
这看似简单的缩松缺陷,却长期极大地影响着企业的成品率和经济效益。
那么,铸件的缩松缺陷是如何产生又如何解决呢?笔者有如下拙见。
一、缩松产生的原因铸件产生缩松的根本原因是“热不平衡”所致。
缩松的位置,产生在铸件的厚大中心部位,几何热节处,不同壁厚的交差处和人为热节处。
这些地方都因热量过高最后凝固又得不到充分补缩而产生了缩松,严重时产生集中性缩孔。
图1中各例分别标示了由铸件结构原因可能产生的缩松。
其次,铸造工艺设计不合理,人为地制造热节而产生缩松缺陷。
如图2中各例。
不少企业,无论铸件多重、多厚、多长,都只设一个内浇口,且设在铸件最厚处。
就是壁厚均匀者,内浇口设的位置与数量也不合理。
这样的工艺设计,落砂时内浇口往往不打自掉,集中性缩孔也是常见的。
第三,浇注温度过高和浇注时间过长。
第四,铸型的造型材料蓄热量小,散热性差,造成铸件凝固时间过长。
第五,一箱多件,件之间距离太近。
第六,球墨铸铁的铸型紧实度低,铸型强度小和表面硬度低,砂箱刚度弱,金属液中共晶团数多,铸件在凝固膨胀时推动着型壁向外移动。
第七,化学成分设计不当,合金化不足。
……二、解决方法解决缩松缺陷,最根本的着眼点就是“热平衡”。
其方法是:第一,在铸件结构形成的厚大处与热节处,实行快速凝固,人为地造成铸件各处温度场的基本平衡。
采用内外冷铁,局部采用蓄热量大的锆英砂、铬铁矿砂或特种涂料(见图3)。
图4是加拿大的QT450-10铸件,重35kg,须超声波探伤(6000m/s)达2级,任何部位都不得有缩松缺陷。
3D打印中常见材料收缩问题解决方案

3D打印中常见材料收缩问题解决方案在3D打印技术中,常常会遇到材料收缩的问题。
这对于3D打印的精度和制造质量来说是一个重要的挑战。
然而,通过一些解决方案和技巧,我们可以有效地解决这个问题,确保打印出高质量的产品。
首先,了解材料的特性是解决收缩问题的第一步。
不同的3D打印材料有不同的热膨胀系数和收缩率。
因此,在选择材料时,要注意查看材料的相关技术资料,并了解其收缩率。
其次,一个解决收缩问题的常用方法是使用支撑材料。
由于某些材料的收缩可能会导致打印出的物体变形或破裂,因此使用支撑材料可以提供额外的支撑和保持形状的稳定性。
根据打印模型的复杂程度和设计要求,可以选择适合的支撑材料,并根据需要将其加入到打印过程中。
第三,调整3D打印机的参数也是解决收缩问题的关键。
温度是一个重要的参数,可以影响材料的热膨胀和收缩。
通过调整打印机的温度,可以控制材料的热膨胀量,从而减少收缩问题。
此外,打印速度和填充率也是需要考虑的参数,它们会影响打印物体的整体收缩量。
此外,改进设计和支撑结构也可以有效地解决收缩问题。
合理的设计可以最大程度地减少收缩对打印物体造成的影响。
例如,在设计中使用圆角和梯度结构可以减少物体内部的应力集中,从而降低收缩导致的变形。
此外,合理设置支撑结构的位置和密度也可以提供额外的支撑和优化打印物体的形态。
此外,后处理过程也是解决收缩问题的一种方式。
对于一些塑料材料,可以在打印完成后进行修整和烘烤处理,以进一步减少收缩。
通过这些后处理过程,可以有效地改善打印物体的精度和尺寸稳定性。
最后,定期进行维护和保养也是解决收缩问题的重要步骤。
3D打印机的精密部件和运行机制需要保持良好的状态,以确保打印的精度和稳定性。
定期清洁和润滑打印机的部件,并进行必要的调整和修复,可以减少因机器问题导致的收缩。
综上所述,通过了解材料特性、使用支撑材料、调整3D打印机的参数、改进设计和支撑结构、后处理以及定期维护和保养,我们可以解决3D打印中常见的材料收缩问题。
零部件缩印改善方案汇总

1.0mm以上的厚度差没有认可。
1.0mm
15mm
30mm
8、缩印对策—加强筋引起1 --设定段差
辅助加强饰在反面,表面会发生缩印。在
辅助加强筋的位置设定段差。 注:PBT/PET材料时,即使有0.5mm的加 强筋,也会发生缩印,故必须设定段差。
因辅助加强 筋,在表面发 生缩印。
238L后灯 A配光镜
PMMA
热烫脚根部 产品表面出 现吸壁
t=3mm, T=2.64mm, t/T≤0.65 t/T=1.14
308前照灯饰圈
该产品为 PC材料
改善前
改善后
353后灯配光镜
改善前
该产品为 PMMA材料
改善后
985后灯饰圈
改善后
该产品为PC材料
353前照灯饰圈
浇口位置 变更
改善后
缩印与材料收缩率的关系
材料的收缩率与缩印的产生有着必然的联系,
一般,收缩率与缩印的程度成正比,即:材料 收缩率越大,缩印越大;材料收缩率越小,缩 印越小。 例如:PBT/PET时, 收缩率较大(1.8), 容易产生缩印,应为「D≤0.3t」 又例如: PC时, 收缩率较小(0.5), 可以为「D≤0.5t」
平面 端头壁厚, 会产生缩印。 基本 壁厚 一定
(大于基本壁厚)
为使保证具有基本壁厚,要确保端头的 宽度,此外,端头R角的大小可设计成一样。
只对端未部减薄单侧的厚度,通过减少壁的厚度,使缩印 不显眼。(这种处理只限于端末部,在端末部以外的部位出现 焦斑这种不良现象。)
端头壁厚, 会产生缩印。 (大于基本壁厚)
塑料收缩率的其他影响因素
对于成形件壁厚来说,一般由於厚壁的冷却时间较长, 因而收缩率也较大,如图1所示。 对一般塑件来说,当熔 料流动方向L尺寸与垂直於熔料流方向W尺寸的差异较大 时,则收缩率差异也较大。 从熔料流动距离来看,远离 浇口部分的压力损失大,因而该处的收缩率也比*近浇口 部位大。 因加强筋、孔、凸台和雕刻等形状具有收缩抗 力,因而这些部位的收缩率较小。 浇口形式对收缩率也有影响。用小浇口时,因保压结 束之前浇口即固化而使塑件的收缩率增大。 注塑模中的 冷却回路结构也是模具设计中的一个关键。冷却回路设计 得不适当,则因塑件各处温度不均衡而产生收缩差,其结 果是使塑件尺寸超差或变形。在薄壁部分,模具温度分布 对收缩率的影响则更为明显。
产品有缩印解决方案

产品有缩印解决方案篇一:药理缩印1. 药物的双重性:临床利用药物防治疾病时,可能产生多种药理效应,能够是有利于避免疾病的作用,也能够是与用药目的无关或对动物产生损害。
大多数药物会有伴随不良反映。
1. 医治作用:嗷呜防治疾病时产生的有利作用。
对因医治:药物作用在于排除疾病的原发致病因子。
对症医治:改善病症,治标。
2. 不良反映:副作用、醉前给药(抑制气管腺体分泌和减轻对心脏的抑制)、毒性反映、变态反映(过敏反映)、继发反映(药物医治作用引发的不良后果,又称医治矛盾)、后遗效应2.阻碍药物作用的因素:(药物对机体的阻碍或机体对药物的反映)1.药物方面:剂量、剂型、给药方案(静注、肌注、皮下注射、内服)2.动物方面:种属不同、生理因素、病理状态、个体不同3.合理饲养和环境因素3.麻醉与解热镇痛药的区别:麻醉性适用于剧锐痛,作用强度强,没有其他作用,有成瘾性。
解热镇痛适用于慢性钝痛,作用强度弱,有解热、抗炎、抗风蚀作用,无成瘾性。
4.局麻方式:表面麻醉、浸润麻醉、传导、硬膜外腔、封锁疗法。
5.复合麻醉:麻前给药、诱导麻醉、基础麻醉、配合麻醉、混合麻醉6.巴比妥类与苯二氮卓类区别:巴比妥:镇痛催眠、抗痉挛。
不良反映多,可产生宿醉现象,有成瘾性。
苯二氮卓;抗焦虑惊阙。
平安性高,不良反映小。
7.泻药的分类与比较:1.容积性泻药(盐类):硫酸钠、硫酸镁、NaCl。
不易被肠壁吸收,形成高渗溶液,软化粪便。
肠容积增大,刺激肠粘膜。
大肠便秘。
2.润滑性(油类):液体石蜡、动物植物油。
润滑肠管、软化粪便,阻止水分吸收,引发排便。
小肠便秘。
3.刺激性:在肠内代谢出有效成份,产生化学性刺激,肠管蠕动。
8.强心苷的药理作用:正性肌力、负性频率、对传导组织的阻碍、对心电图阻碍、利尿作用。
毒性反映:胃肠道反映(初期中毒病症)、C,N,S反映(眩晕、头痛、失眠、视觉障碍)、心脏反映(快速型心律失常、房室传导阻滞、窦性心动过缓)9.皮质激素的药理作用:抗炎、抗免疫、抗毒素、抗休克、阻碍代谢不良反映:急性肾上腺功能不全;多尿和饮欲亢进;水肿和低血钾;肌萎缩无力,骨质疏松,幼畜生长抑制;对感染性感型增强,引发二重感染。
注塑件缩痕产生原因及解决方案
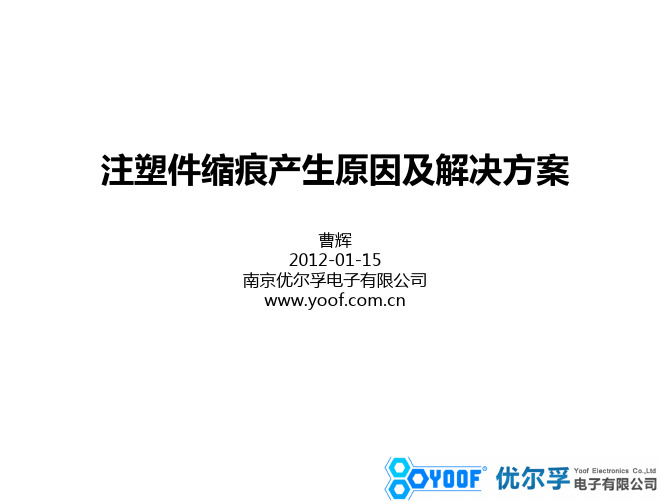
11
HIPS GROUP
更新日期:11-8-2002
成型不良原因及对策—缩痕 注塑件缩痕产生原因及解决方案
减少缩痕的方法
成型工艺
3mm3mm贡献 贡献
a.提高注塑压力 b.增大后期保压压力 c.降低缩痕部分所对应的注 射速度 d.降低模具温度 e.降低注塑温度 模具设计 a.加大浇口 b.变短浇口 c.改变流道位置 d.加宽流道 e.减少流动阻力 f. 保证喷嘴和模具结合完好 制品设计 a.把筋、沉孔部位变细 b.在筋、沉孔部位加倒角 c.减小壁厚 d.把表 面设计为花纹以掩盖缩痕
成型不良原因及对策—缩痕 注塑件缩痕产生原因及解决方案
沉孔设计要点(Ⅰ)
3mm3mm贡献 贡献
8
HIPS GROUP
更新日期:11-8-2002
成型不良原因及对策—缩痕 注塑件缩痕产生原因及解决方案
沉孔设计要点(Ⅱ)
3mm3mm贡献 贡献
为保证强度,沉孔的外径一般为内径的2倍
9
HIPS GROUP
原始设计 该设计可能出现 缩痕和气眼
改良后设计
5
HIPS GROUP
更新日期:11-8-2002
成型不良原因及对策—缩痕 注塑件缩痕产生原因及解决方案
加强筋的设计要点(Ⅰ)
3mm3mm贡献 贡献
6
HIPS GROUP
更新日期:11-8-2002
成型不良原因及对策—缩痕 注塑件缩痕产生原因及解决方案
加强筋的设计要点(Ⅱ)
3mm3mm贡献 贡献
• • • • • •
制件壁厚为T 拔模斜度(d)为0.5 ° ~1.5 ° 加强筋高度(H)小于5T,通 常为2.5T-3T 加强筋间距大于2T-3T 倒角半径(R)为0.25-0.40T 加强筋厚度(W)为0.4T-0.8T
零件的改进方案及措施有哪些

零件的改进方案及措施有哪些零件的改进方案及措施。
随着科技的不断发展和市场需求的不断变化,零件的改进已经成为制造业中的一项重要工作。
通过对零件的改进,可以提高产品的质量和性能,降低生产成本,提高生产效率,增强企业的竞争力。
因此,制造企业需要不断探索和实施零件的改进方案及措施,以适应市场的需求和企业的发展。
一、零件的改进方案。
1. 材料选择的优化。
材料是影响零件性能的重要因素,因此对于零件的改进来说,材料选择的优化是至关重要的。
通过选择合适的材料,可以提高零件的强度、硬度、耐磨性等性能,从而提高产品的质量和使用寿命。
2. 结构设计的优化。
结构设计是影响零件性能的另一个重要因素,通过对零件的结构进行优化,可以减少零件的重量、降低零件的成本、提高零件的刚度等,从而提高产品的性能和降低生产成本。
3. 工艺技术的改进。
工艺技术是影响零件加工质量的重要因素,通过改进工艺技术,可以提高零件的加工精度、提高零件的表面质量、降低零件的加工成本等,从而提高产品的质量和降低生产成本。
4. 表面处理的改进。
表面处理是影响零件使用寿命的重要因素,通过改进表面处理工艺,可以提高零件的耐腐蚀性、耐磨性、耐疲劳性等,从而提高产品的使用寿命和降低维护成本。
二、零件的改进措施。
1. 强化研发设计能力。
制造企业应该加强对研发设计能力的投入,通过引进先进的设计软件和设备,培养专业的设计人才,提高企业的研发设计水平,从而能够更好地进行零件的优化设计。
2. 加强材料研究与应用。
制造企业应该加强对材料的研究与应用,通过引进先进的材料测试设备和技术,开展新材料的研究与开发,优化材料选择,提高零件的性能。
3. 提高生产工艺水平。
制造企业应该加强对生产工艺的研究与改进,通过引进先进的加工设备和技术,优化生产工艺流程,提高加工精度和效率,降低生产成本。
4. 强化质量控制体系。
制造企业应该加强对质量控制体系的建设与管理,通过引进先进的质量管理技术和方法,建立完善的质量控制体系,提高产品的质量稳定性和一致性。
压铸件的缩孔缩松问题解决方案
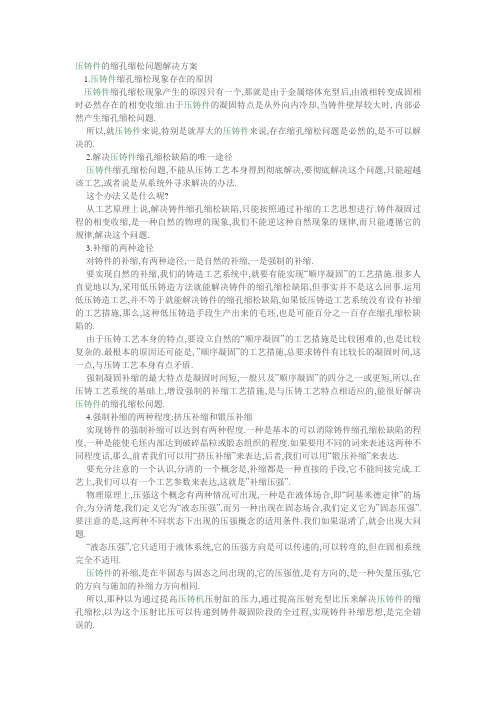
压铸件的缩孔缩松问题解决方案1.压铸件缩孔缩松现象存在的原因压铸件缩孔缩松现象产生的原因只有一个,那就是由于金属熔体充型后,由液相转变成固相时必然存在的相变收缩.由于压铸件的凝固特点是从外向内冷却,当铸件壁厚较大时, 内部必然产生缩孔缩松问题.所以,就压铸件来说,特别是就厚大的压铸件来说,存在缩孔缩松问题是必然的,是不可以解决的.2.解决压铸件缩孔缩松缺陷的唯一途径压铸件缩孔缩松问题,不能从压铸工艺本身得到彻底解决,要彻底解决这个问题,只能超越该工艺,或者说是从系统外寻求解决的办法.这个办法又是什么呢?从工艺原理上说,解决铸件缩孔缩松缺陷,只能按照通过补缩的工艺思想进行.铸件凝固过程的相变收缩,是一种自然的物理的现象,我们不能逆这种自然现象的规律,而只能遵循它的规律,解决这个问题.3.补缩的两种途径对铸件的补缩,有两种途径,一是自然的补缩,一是强制的补缩.要实现自然的补缩,我们的铸造工艺系统中,就要有能实现“顺序凝固”的工艺措施.很多人直觉地以为,采用低压铸造方法就能解决铸件的缩孔缩松缺陷,但事实并不是这么回事.运用低压铸造工艺,并不等于就能解决铸件的缩孔缩松缺陷,如果低压铸造工艺系统没有设有补缩的工艺措施,那么,这种低压铸造手段生产出来的毛坯,也是可能百分之一百存在缩孔缩松缺陷的.由于压铸工艺本身的特点,要设立自然的“顺序凝固”的工艺措施是比较困难的,也是比较复杂的.最根本的原因还可能是, ”顺序凝固”的工艺措施,总要求铸件有比较长的凝固时间,这一点,与压铸工艺本身有点矛盾.强制凝固补缩的最大特点是凝固时间短,一般只及”顺序凝固”的四分之一或更短,所以,在压铸工艺系统的基础上,增设强制的补缩工艺措施,是与压铸工艺特点相适应的,能很好解决压铸件的缩孔缩松问题.4.强制补缩的两种程度:挤压补缩和锻压补缩实现铸件的强制补缩可以达到有两种程度.一种是基本的可以消除铸件缩孔缩松缺陷的程度,一种是能使毛坯内部达到破碎晶粒或锻态组织的程度.如果要用不同的词来表述这两种不同程度话,那么,前者我们可以用“挤压补缩”来表达,后者,我们可以用“锻压补缩”来表达.要充分注意的一个认识,分清的一个概念是,补缩都是一种直接的手段,它不能间接完成.工艺上,我们可以有一个工艺参数来表达,这就是”补缩压强”.物理原理上,压强这个概念有两种情况可出现,一种是在液体场合,即“阿基米德定律”的场合,为分清楚,我们定义它为“液态压强”,而另一种出现在固态场合,我们定义它为”固态压强”.要注意的是,这两种不同状态下出现的压强概念的适用条件.我们如果混淆了,就会出现大问题.“液态压强”,它只适用于液体系统,它的压强方向是可以传递的,可以转弯的,但在固相系统完全不适用.压铸件的补缩,是在半固态与固态之间出现的,它的压强值,是有方向的,是一种矢量压强,它的方向与施加的补缩力方向相同.所以,那种以为通过提高压铸机压射缸的压力,通过提高压射充型比压来解决压铸件的缩孔缩松,以为这个压射比压可以传递到铸件凝固阶段的全过程,实现铸件补缩思想,是完全错误的.5.采用“先压铸充型,后模锻补缩”的工艺,是解决铸件缩孔缩松缺陷的有效途径,也是一种终极手段.“先压铸充型,后模锻补缩”的工艺,我们可简称为“压铸模锻”工艺.它的本质,是一种连铸连锻工艺,就是将压铸工艺与液态模锻工艺相结合,将这两种设备的最有效功能组合在一起,完成整个工艺过程.这种连铸连锻的“压铸模锻”设备,外型与普通立式或卧式的压铸机很相似,其实就是在压铸机上,增加了液压的锻压头.可以加上的最大锻压补缩力,能等于压铸机的最大锁模力.要注意的是,这种压铸模锻机最重要的公称参数,并不是锁模力,而是模锻补缩力,相当于四柱油压机的锻压力意义,这是我们在设备选择时必须充分留意的.不然,买了一台锁模力很大,但模锻补缩力很小的压铸模锻设备,其使用价值就大打折扣了.运用这种压铸模锻机生产的毛坯,尺寸精度很高,表面光洁度也极高,可以相当于6级以上机加工手段所能达到的精度与表面粗糙度水平.它已能归属于“极限成形”----的工艺手段,比“无切削少余量成形”工艺更进了一步研究对既定条件下压铸模具的压铸工艺参数进行快速择定。
解决产品缩水的参考方案

解决产品缩水的参考方案
在生产中经常会遇到产品收缩变形大,表面有凹陷,内部有气泡,缩孔等现象。
我们生产的耳勾系列产品中,像APHRODITE EARHOOK 经常出现表面凹陷(表面缩水明显),ARAGORN EARHOOK 的铁线位有气泡等。
产品出现上述问题涉及多方面原因。
就产品本身而言,产品的材料不同,产品各部分厚度不同,产品的成型质量要求导致产品的浇口位置设置局限性大都可能导致上述问题的发生。
从注塑工艺来分析,主要涉及到成型时的原料的成型温度,注射时间,注射压力和注射速度。
在成型温度保证达到,注射时间足够的前提下,产品缩水可能是注射压力和保压压力不够,可以尝试用加大注射压力和保压压力的方法来解决。
注射速度太快容易产生气泡,注射速度太慢又影响产品的充填质量。
针对我们的情况,生产时塑料的成型温度都能保证达到,但往往经过对产品成型参数多次更改调试,却依然会出现上述不良成型现象。
从模具方面入手,我们常用的方法是加大浇口入水位置的尺寸,希望通过这样延迟浇口冷却,使产品的保压效果更
好。
但是这样的做法往往令到产品的浇口入水位置发白,而且效果不是十分理想。
根据国外的一些先进经验,结合我们自己遇到的生产问题,可用下述方法尝试解决,如图1,在设计三板,点浇口模具时,在保证水口出模顺利的前提下,可以适当减小浇口的夹角,从常用的3○-4○改到2○。
在设计浇口时,应注意如图1中所示位置①的尺寸与产品壁厚尺寸相近。
图1 三板模点浇口设计。
2023年度注塑制品中影响缩痕深度的因素与解决措施
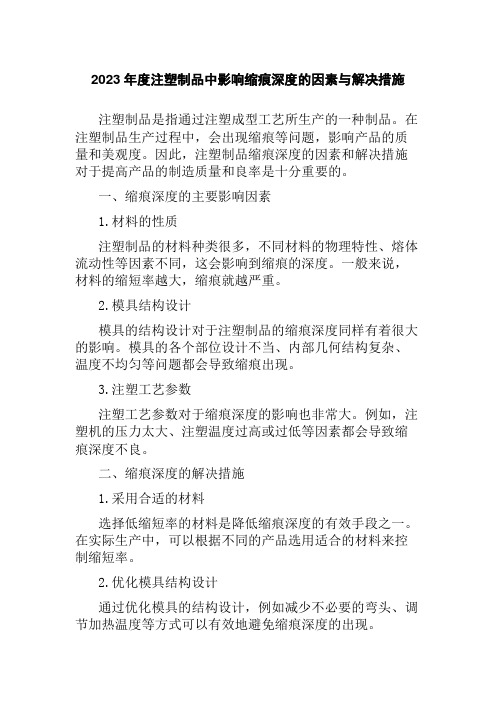
2023年度注塑制品中影响缩痕深度的因素与解决措施注塑制品是指通过注塑成型工艺所生产的一种制品。
在注塑制品生产过程中,会出现缩痕等问题,影响产品的质量和美观度。
因此,注塑制品缩痕深度的因素和解决措施对于提高产品的制造质量和良率是十分重要的。
一、缩痕深度的主要影响因素1.材料的性质注塑制品的材料种类很多,不同材料的物理特性、熔体流动性等因素不同,这会影响到缩痕的深度。
一般来说,材料的缩短率越大,缩痕就越严重。
2.模具结构设计模具的结构设计对于注塑制品的缩痕深度同样有着很大的影响。
模具的各个部位设计不当、内部几何结构复杂、温度不均匀等问题都会导致缩痕出现。
3.注塑工艺参数注塑工艺参数对于缩痕深度的影响也非常大。
例如,注塑机的压力太大、注塑温度过高或过低等因素都会导致缩痕深度不良。
二、缩痕深度的解决措施1.采用合适的材料选择低缩短率的材料是降低缩痕深度的有效手段之一。
在实际生产中,可以根据不同的产品选用适合的材料来控制缩短率。
2.优化模具结构设计通过优化模具的结构设计,例如减少不必要的弯头、调节加热温度等方式可以有效地避免缩痕深度的出现。
3.优化注塑工艺参数通过调整注塑机的参数来解决缩痕深度问题。
例如,将注塑温度调整到适宜的工艺温度、适当降低注塑机的压力等方式都可以有效避免缩痕出现。
4.提高模具制造精度在模具制造过程中,精细加工、均匀加热等措施可以保证模具的制造精度,从而减少缩痕等问题的出现。
综上所述,缩痕深度是一个影响注塑制品质量的重要因素,需要在材料选择、模具结构设计、注塑工艺参数和模具制造精度方面下功夫。
只有做好这些工作,才能使注塑制品制造的质量得到保障。
浅析汽车涂装过程中缩孔问题的解决思路构架

浅析汽车涂装过程中缩孔问题的解决思路构架汽车涂装过程中出现的缩孔问题是指在汽车喷漆过程中,出现漆面上出现了小小的凹陷或者坑洼,影响了汽车的外观质量。
缩孔问题给汽车生产制造过程带来了很大的隐患,因此如何有效解决汽车涂装过程中的缩孔问题,成为了汽车生产制造中亟待解决的技术难题。
本文将就汽车涂装过程中缩孔问题的解决思路构架进行深入的浅析。
汽车涂装过程中出现缩孔问题的原因可能有多种,其中包括漆料的质量、喷涂工艺的控制、工作环境的影响等。
解决汽车涂装过程中的缩孔问题,需要综合考虑相关因素,在实践中对不同的因素进行分析和控制。
1. 漆料的质量控制漆料是汽车喷漆的关键原材料,其质量直接影响到涂装效果。
首先要做的是对漆料的质量进行严格控制。
在选材过程中,应该选择符合国家标准的优质漆料,严格按照生产工艺规范进行生产,确保漆料的质量稳定。
在储存和运输过程中,也要注意避免漆料受到振动、温度变化等外界因素的影响,确保漆料的质量稳定。
2. 喷涂工艺的控制喷涂工艺是影响汽车涂装质量的另一个关键因素。
要解决缩孔问题,必须对喷涂工艺进行严格控制。
在喷涂设备的选择上,应该选择质量可靠的喷涂设备,并根据汽车的不同部位选择适合的喷涂设备。
在喷涂操作上,要严格按照操作规程进行操作,控制好喷涂速度、喷涂厚度、喷涂角度等关键参数,确保涂装整体均匀平稳。
在涂装过程中,要定时清洗喷枪和过滤器,保持喷涂设备的清洁,避免异物污染导致缩孔问题的出现。
3. 工作环境的影响工作环境的温湿度、尘埃等因素也可能影响汽车涂装质量。
在解决缩孔问题时,还需要对工作环境进行合理的管理。
在涂装车间的设计上,应该考虑到通风、湿度控制等因素,为涂装作业提供一个合理的工作环境。
要做好车间的清洁管理工作,定期清扫车间,保持车间的清洁卫生,避免灰尘等异物污染导致缩孔问题的出现。
除了上述几点外,对于汽车涂装过程中出现的缩孔问题,还可以结合先进的检测技术进行分析和解决。
可以利用数字显微镜、红外显微镜、扫描电子显微镜等高精度检测设备,对汽车漆面进行非破坏性检测,分析缩孔问题的原因,并进行针对性的改进措施。
汽车零部件整治方案

汽车零部件整治方案随着车辆数量的增加和汽车工业的迅速发展,汽车行业也面临着更严峻的安全和质量挑战。
汽车零部件是汽车的重要组成部分,对整车的安全和性能有着至关重要的影响。
因此,汽车零部件整治方案是非常重要的。
问题描述汽车零部件的生产、销售、使用环节存在一些问题:1.部分零部件生产厂家技术能力不足,生产过程中存在质量问题;2.部分经销商缺乏专业知识,销售假冒伪劣零部件;3.部分车主不重视保养和维修,使用老化的零部件导致危险;4.部分维修厂家存在不规范、不规范维修等问题。
解决方案汽车零部件整治方案应该从以下几个方面入手:生产环节对于汽车零部件的生产环节,应该加强质量管理,提高技术水平。
制定严格的生产标准和生产规程,对零部件的外观、性能、使用寿命等方面进行严格控制,确保零部件性能安全可靠,并对不合格的零部件及时淘汰。
同时,还应该加大对技术力量薄弱的生产厂家的培训和支持力度,提高生产厂家的技术能力和生产水平,加强对假冒伪劣零部件生产的打击力度,建立一套完整的生产管理体系。
销售环节对于汽车零部件销售环节,经销商应该加强对零部件的质量检测和甄别,对不合格的零部件予以淘汰。
对于假冒伪劣零部件要进行严厉打击,加强对零部件销售的监管。
同时,还应加大对经销商的管理和培训力度,提高其专业知识和市场服务能力。
购买和使用环节对于车主而言,他们应该加强对自己车辆的保养和维修,对老化的零部件要及时更换,确保车辆的安全可靠。
建立健全的维修保养体系,规范维修市场,加大对不规范维修行为的监管和打击力度,确保维修质量。
同时,宣传汽车零部件的安全知识,引导车主正确使用和维护车辆。
监管对于汽车零部件整治方案监管力度也要加大。
国家相关部门要出台相关政策法规,加强对汽车零部件生产、销售、维修等环节的监管力度,对违法违规行为进行严厉打击。
同时,加强对市场消费环节的监督,推动汽车消费市场良性发展。
总结汽车零部件整治方案是一个复杂的系统工程。
通过对汽车零部件的生产、销售、使用等环节的整治,可以有效提高汽车零部件的质量和安全性能。
- 1、下载文档前请自行甄别文档内容的完整性,平台不提供额外的编辑、内容补充、找答案等附加服务。
- 2、"仅部分预览"的文档,不可在线预览部分如存在完整性等问题,可反馈申请退款(可完整预览的文档不适用该条件!)。
- 3、如文档侵犯您的权益,请联系客服反馈,我们会尽快为您处理(人工客服工作时间:9:00-18:30)。
在形象面设定段差, 设定加强筋。段差需要 有1.2mm左右。
9、缩印对策—加强筋引起2 --在形象面折弯部作加强筋
辅助加强筋位置设定要和形象面的折弯 部相一致。 对于第8项,段差不是和加强筋相合, 要探讨在段差部是否能设定加强筋。
因加强筋在表 面产生缩印。
要与形象面折弯部相 合设置加强筋。
10、缩印对策—配光镜装配部
配光镜装配部的加强筋作为缩印防止 措施,有时会出现不能充填的部分,仅是 连接部分采取缩印防止措施。
减薄加强筋的 厚度来作为防止缩 印的措施,加强筋 没有充填成形。
仅与产品连接的部分为0.5mm的厚度。
11、缩印对策—采用滑块防止
第6项所示为因滑块产生缩印时的例子。 相反有时用滑块来防止厚壁的缩印。
238L后灯 A配光镜
PMMA
热烫脚根部 产品表面出 现吸壁
t=3mm, T=2.64mm, t/T≤0.65 t/T=1.14
308前照灯饰圈
该产品为 PC材料
改善前
改善后
353后灯配光镜
改善前
该产品为 PMMA材料
改善后
985后灯饰圈
改善后
该产品为PC材料
353前照灯饰圈
浇口位置 变更
改善后
个产品上怎样处理的问题。 饰圈形象面的滑块线原则上禁止采用。
7、缩印对策—设定渐变部分
因厚度变化,会发生缩印,只在端末部 设定渐变部分。 注:厚度变化只限于产品端末。在产品 内部进行的话,发生焦斑。
设定渐变部分 因Ret(回复顶杆)让位 等,产生厚度差,产生缩 印。
厚度差 (X )
1.0mm
渐变长度(Y)
作为滑块结构,切削厚壁部。(但即使 有0.5mm,也会产生缩印。)
12、缩印对策—螺钉安装柱的设计
防缩印的设计建议
典型案例分析
产品肉厚不良缺陷分析一览表
产品名 材料名 存在结构 存在缺陷
热烫脚根部 产品表面出 现吸壁 产品在注塑 末端的尖端 处,局部有 凸筋,造成 吸壁 热烫脚根部 产品表面出 现吸壁
允许设置凸台。
尽力做小斜度
2、缩印对策—安装部的截面形状
方案1 把底面移上, 减少壁厚
因壁厚,发生缩印。 相应措施 继续方案2,确保W宽。 方案2 减薄但仍有缩印
(但没有空间时,不可) 方案3 制作滑块结构
切削 (但可看见滑块线)
3、缩印对策—端末部的缩印1 --保证基本厚度
若是厚壁,必定会发生缩印。首先保证 端头宽度的基本壁厚
缩印产生的机理
热塑性塑料零件注塑加工的过程就是高分子聚合物被熔化后在型腔内从粘流态 向高弹态、玻璃态转变的过程,是大分子链段在运动中进行重新堆砌的过程。自由体 积理论认为,液体与固体的体积实际上是分子堆砌的体积,其中包括两部分:主要是 分子本身的实占体积。其余的则是堆砌的空隙或未占有的自由体积,包括具有分子尺 寸的空穴和堆砌缺陷。 定义可知,对于大多数能形成玻璃的高聚物,玻璃化转变后自由体积占总体积 分数的2.5嘶。理论计算和实验测定表明它是一个常数,这表明高聚物一旦变成玻璃, 其自由体积就停止随温度继续降低而变小。在玻璃化转变温度和熔化温度,自由体积 的变化比较明显。温度越低,自由体积就越小,材料的密度却越大。很多研究表明高 聚物在松弛过程中自由体积的变化,以依附于温度变化为特征零件在成形中体积冷缩 这一物理性质正是自由体积变化的宏观反映。 在松弛过程中,大分子链段为获得新的平衡,进行着复杂的运动和全新的堆砌。 链段间的拉应力和零件坯料表面的切向应力使零件的内部结构及表面状态都发生着变 化。零件的棱角和薄壁部分易于散热。注塑时这里的链段往往还未能达到真正的平衡 结构,就被冻结了。零件肥厚部分散热条件较差,冷却较慢,滞后堆砌结束的部分链 段。为完成自己平衡结构,对被冻结部分的表层施以内向拉力。结果,局部表面向内 陷,形成了常见的所谓的缩印。高聚物大分子本身的占有体积基本上是一定的。因而, 高聚物熔体在玻璃化转变时体积的变化主要是其自由体积的变化。二者总量必然基本 相等。 缩印,作为高聚物零件在成形过程中体积冷缩的陈迹,也包括在该变化量之内 。
附表 《塑料收缩率》
其它不同塑料的成型收缩率
序号/ 塑料名称 /代号/ 收缩率 1 丙稀腈、丁二稀、苯乙烯 ABS 0.3~0.8 2 氨基树脂 AF 3 氯化聚醚 CP 0.5 4 环氧树脂 EP 5 聚三氟氯乙烯 F3 6 聚四氟乙烯 F4 7 聚四氟乙烯 增强 F4+20%GF 8 聚全氟乙丙烯 F46 9 高密度聚乙烯 (孖力士) HDPE 2~5.0 10 高抗冲聚苯乙烯 (不脆胶) HIPS 0.2~0.6 11 硬质聚氯乙烯 HPVC 0.6~1.0 12 液晶聚合物 LCP 0.006 13 低密度聚乙烯 LDPE 1.5~5.0 14 改性聚苯醚 MPPO 15 聚酰胺6 PA6 0.6~1.4 16 聚酰胺6 增强 PA6+30%GF 0.3~0.7 17 聚酰胺66 PA66 0.8~1.5 18 聚酰胺66 增强 PA66+30%GF 0.2~0.8 19 聚芳砜 PASF 0.8 20 聚对苯二甲酸丁二醇酯 PBT 0.44 21 聚对苯二甲酸丁二醇酯 增强 PBT+30%GF 0.2 22 聚碳酸脂 (防弹胶) PC 0.5
改善前
该产品为PC材料
塑料收缩率对缩印 的影响
塑料收缩率及其影响因素
热塑性塑料的特性是在加热后膨胀,冷却后收缩,当然加 压以后体积也将缩小。 在注塑成形过程中,首先将熔融塑料 注射入模具型腔内,充填结束后熔料冷却固化,从模具中取出 塑件时即出现收缩,此收缩称为成形收缩。塑件从模具取出到 稳定这一段时间内,尺寸仍会出现微小的变化,一种变化是继 续收缩,此收缩称为后收缩。另一种变化是某些吸湿性塑料因 吸湿而出现膨胀。例如尼龙610含水量为3%时,尺寸增加量 为2%;玻璃纤维增强尼龙66的含水量为40%时尺寸增加量为 0.3%。但其中起主要作用的是成形收缩。 目前确定各种塑料收缩率(成形收缩+后收缩)的方法, 一般都推荐德国国家标准中DIN16901的规定。即以 23℃±0.1℃时模具型腔尺寸与成形后放置24小时,在温度为 23℃,相对湿度为50±5%条件下测量出的相应塑件尺寸之差 算出。 收缩率S由下式表示: S={(D-M)/D}×100% 其中:S-收缩率; D-模具尺寸; M-塑件尺寸。
平面 端头壁厚, 会产生缩印。 基本 壁厚 一定
(大于基本壁厚)
为使保证具有基本壁厚,要确保端头的 宽度,此外,端头R角的大小可设计成一样。
只对端未部减薄单侧的厚度,通过减少壁的厚度,使缩印 不显眼。(这种处理只限于端末部,在端末部以外的部位出现 焦斑这种不良现象。)
端头壁厚, 会产生缩印。 (大于基本壁厚)
缩印与材料收缩率的关系
材料的收缩率与缩印的产生有着必然的联系,
一般,收缩率与缩印的程度成正比,即:材料 收缩率越大,缩印越大;材料收缩率越小,缩 印越小。 例如:PBT/PET时, 收缩率较大(1.8), 容易产生缩印,应为「D≤0.3t」 又例如: PC时, 收缩率较小(0.5), 可以为「D≤0.5t」
成形条件对材料收缩率的影响
料筒温度:料筒温度(塑料温度)较高时,压力传递较好而使收缩力减小。
但用小浇口时,因浇口固化早而使收缩率仍较大。对於厚壁塑件来说,即使 料筒温度较高,其收缩仍较大。 补料:在成形条件中,尽量减少补料以使塑件尺寸保持稳定。但补料不足则 无法保持压力,也会使收缩率增大。 注射压力:注射压力是对收缩率影响较大的因素,特别是充填结束後的保压 压力。在一般情况下,压力较大的时因材料的密度大,收缩率就较小。 注射速度:注射速度对收缩率的影响较小。但对於薄壁塑件或浇口非常小, 以及使用强化材料时,注射速度加快则收缩率小。 模具温度:通常模具温度较高时收缩率也较大。但对於薄壁塑件,模具温度 高则熔料的流动阻抗小,而收缩率反而较小。 成形周期:成形周期与收缩率无直接关系。但需注意,当加快成形周期时, 模具温度、熔料温度等必然也发生变化,从而也影响收缩率的变化。在作材 料试验时,应按照由所需产量决定的成形周期进行成形,并对塑件尺寸进行 检验。用此模具进行塑料收缩率试验的实例如下。 注射机:锁模力70t 螺杆直径Φ35mm 螺杆转速80rpm 成形条件:最高注射压 力178MPa 料筒温度230(225-230-220-210)℃ 240(235-240-230-220)℃ 250(245-250-240-230)℃ 260(225-260-250-240)℃ 注射速度57cm3/s 注射 时间0.44~0.52s 保压时间6.0s 冷却时间15.0s
为了消除厚壁 减薄单侧壁厚度。 PC:L=10mm;最大t=2.0mm PBT/PET:L=15mm;最大t=1.5mm
4、缩印对策—端末部的缩印2 --减薄单侧厚度
(原理) a和b为相同厚度时,L尺寸变大, b侧有强度问题,可减薄厚度, 缩印变大。 缩印变小。 (L尺寸变小,减薄厚度。)
在产品内进行的话,会发生焦斑。
缩印发生的原理示意
树脂材料注入模具,冷却时,引起体积 收缩。如图所示那样,有加强筋时,A部体 积比周围B部体积大,即使收缩率相同,其 收缩量较大,会发生缩印。
缩印
改善缩印的几种对策
1、缩印对策—凸台部形状
比基本厚度薄,但影响模具顶杆的强 度时L尺寸有限制。 注:采用PBT/PET材料时,强度较差,不
序号/ 塑料名称 /代号/ 收缩率 23 聚碳酸脂 增强 PC+30%GF 0.2 25 聚醚醚酮 PEEK 26 聚醚酮 PEK 27 聚醚酮酮 PEKK 28 聚醚砜 PES 0.6 29 聚对苯二甲酸乙二醇酯 PET 1.8 30 (涤纶(的确凉)) PET+30%GF 0.2~0.9 31 酚醛塑料 (电木粉) PF 32 聚酰亚胺 PI 0.75 33 聚甲基丙烯酸酯 (亚加力) PMMA 0.2~0.8 34 聚甲醛 共聚 (赛钢) 共聚POM 1.5~3.5 35 聚甲醛 共聚 增强 共聚POM+25%GF 36 聚甲醛 均聚 均聚POM 1.5~3 37 聚丙烯 (百折胶) PP 1~2.5 38 聚丙烯 增强 PP+30%GF 0.4~0.8 39 聚苯醚 PPO 0.7 40 聚苯硫醚 增强 PPS+40%GF <0.12 41 聚苯乙烯 (硬胶) PS 0.4~0.7 42 聚砜 PSF 0.6 43 聚氨酯 PU 44 软质聚氯乙烯 SPVC 1.5~2.5 45 超高分子量聚乙烯 UHMWPE 2~3