减少支承辊钢锭锻造裂纹的措施
冷轧工作辊裂纹及剥落原因及预防

图 4 表层裂纹引起的剥落 海滩痕
图 3 机械裂纹
预防机械裂纹的措施有 3 个。1)确保带钢表面清洁无 异物,减少杂物介入。2)提高轧材表面质量,减少氧化皮残 留。3)加强乳化液检测系统和平衡过滤系统的点检。总之, 通过控制酸洗原料、乳化液指标、轧辊冷却等,可以减少轧 制过程中出现打滑、辊印、局部热擦伤等缺陷,提高板材表 面质量,减少轧机事故停机,同时降低辊耗。
一般情况下,打滑、粘钢等轧制事故,会引起辊身一条 母线上或者辊身局部区域内深度和开口都较大的裂纹,一旦 发生该类事故,则必须马上停止轧制,将轧辊换下,并对事 故辊进行严格的超声波、涡流探伤和磨削处理,必须保证表 面裂纹完全消除,并利用超声波探伤,检测轧辊内部的情况。
伤。4)对每支磨削完成的轧辊采用涡流探伤或表波探伤进行 检测,要确保每支要上机的轧辊不存在任何导致疲劳剥落的 可能性。
1.2 热裂纹
在生产过程中由于辊面局部温升快,最高温度超过轧辊 材质热处理工艺的最终回火温度,冷却后相当于再次回火, 表面硬度下降形成软点区,由于其与周边热膨胀系数不同, 这部分应力叠加,导致薄弱环节产生细小的网状裂纹 [1]。一 般情况下网状裂纹深度较浅,约 1.2 mm 以下(如图 2 所示)。 虽然这些裂纹深度浅,但是如果不及时处理和维护,在后期 的生产轧制中,受到外力、热应力等综合影响,很容易发展 成为如辊面粗化、辊面小掉肉等缺陷,严重时会引起辊面剥 落或断辊,所以一旦发现该类缺陷,在使用过程中重点关注 并及时处理。
2.2 材质缺陷引发的剥落
在制造轧辊的过程中,一些不规则的材料在坯料内有 可能成为轧辊内部残留的夹杂物。这些夹杂物可能是耐火材 料、残渣,也可能是坯料本身的的局部偏析和孔隙等 [3]。这 些内部缺陷,在轧辊使用过程中,都可能成为应力集中的根 源,最终将导致轧辊辊身剥落严重,甚至会出现断辊。轧辊 表层下缺陷引发的剥落,大部分在断裂面上呈现出类似鱼眼 纹,很容易进行辨别,如图 5 所示。可以看出该疲劳是从单 点开始蔓延的,并产生波浪状近似椭圆形的疲劳痕迹。这种 疲劳痕迹只有内部材料缺陷引发的迹象,并没有任何其它剥 落的源头。
锻钢轧辊缺陷产生的原因及对策

锻钢轧辊在轧制中出现问题的原因及对策目录页数1. 引言 42. 轧辊表面迹象A. 夹杂5~6B. 橘皮状轧辊表面7~8C. 辊印9~12D. 软点13~18E. 热裂纹i. 热轧机工作辊19ii. 冷轧机工作辊20~273. 剥落A. 表面迹像28~46B. 表皮下引发i. 与材质有关47~49ii. 接触应力a. 一般机理50~52b. 冷轧机工作辊53~61c. 热轧机工作辊62~64d. 支撑辊65~704. 辊颈断裂A. 表面迹像71~72i. 辊颈应力计算73~77B. 表皮下引发i. 轧辊设计或材料质量78~81C. 辊颈修复82~85D. 瞬时发生i. 深置缺陷86~87ii. 轧机过载88~905. 辊身断裂A. 疲劳--- 深置缺陷91~93B. 瞬时i. 轧机过载94~95ii. 深置缺陷96~976. 轧辊检测98A. 涡流探伤99~100B. 表面波超声波探伤101~105C. 着色渗入探伤106~108D. 刻蚀探伤109~111E. 磁粉探伤112~113F. 硬度检验114~1187. 轧辊处理和储存1198. 轧辊各部位的英文名称120~121引言在轧钢生产中的轧辊性能及质量直接影响轧机产量和产品质量。
因为轧辊采购费用在轧钢厂生产成本中占有较大比重,也是影响轧制成本的重要因素。
本书的目的是针对锻钢轧辊在轧制中可能出现的相关问题,并就问题的类型,特徵,样例(照片,图解),产生机理及预防措施等进行分析。
仅供有关人员参考。
锻造轧辊的无损探伤(NTD)对轧辊生产厂家和轧辊用户都非常重要。
轧辊生产厂家在轧辊热处理以及随后的精加工之前用NDT无损探伤,来确认轧辊的表面和内部是否合格。
轧辊用户(轧辊车间)利用NDT无损探伤确保研磨切削部分满足进一步使用之前的轧辊表面要求。
NDT 无损探伤以及其应用,可以作为最佳化轧辊维护过程的管理方法之一。
轧辊的处理和储存也是轧辊问题发生的因素。
钢锭纵裂痕的影响因素及有效预防措施
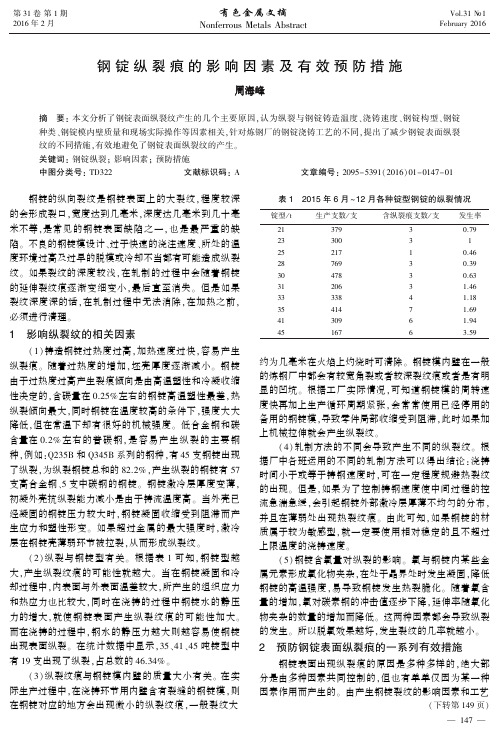
含纵裂痕支数 / 支
3 3 1 3 3 3 4 7 6 6
发生率
0.79 1
0.46 0.39 0.63 1.46 1.18 1.69 1.94 3.59
约为几毫米在火焰上灼烧时可清除。 钢锭模内壁在一般 的炼钢厂中都会有较宽角裂或者较深裂纹痕或者是有明 显的凹坑。 根据工厂实际情况,可知道钢锭模的周转速 度快再加上生产循环周期紧张,会常常使用已经停用的 备用的钢锭模,导致零件局部收缩受到阻滞,此时如果加 上机械拉伸就会产生纵裂纹。
(4)轧制方法的不同会导致产生不同的纵裂纹。 根 据厂中各班运用的不同的轧制方法可以得出结论:浇铸 时间小于或等于铸钢速度时,可在一定程度规避热裂纹 的出现。 但是,如果为了控制铸钢速度使中间过程的控 流急湍急缓,会引起钢锭外部激冷层厚薄不均匀的分布, 并且在薄弱处出现热裂纹痕。 由此可知,如果钢锭的材 质属于较为敏感型,就一定要使用相对稳定的且不超过 上限温度的浇铸速度。
Vol.31 №1 February 2016
= 1.45 + 5.826 ≈ 7 m
度的最终确定还需考虑很多因素,如主干路常与厂区的
由计算得出原料道路行车路面宽度为 7 m。
主要出入口相连接,在确定其宽度时需要考虑景观、视野
( 2) 成品道路行车路面宽度计算
和绿化的要求;若铁水采用汽车运输,在确定其道路宽度
(3)纵裂纹痕与钢锭模内壁的质量大小有关。 在实 际生产过程中,在浇铸环节用内壁含有裂缝的钢锭模,则 在钢锭对应的地方会出现微小的纵裂纹痕,一般裂纹大
表 1 2015 年 6 月 ~12 月各种锭型钢锭的纵裂情况
锭型 / t
21 23 25 28 30 31 33 35 41 45
锻造裂纹产生的原因及解决方法

锻造裂纹产⽣的原因及解决⽅法裂纹是锻压⽣产中常见的主要缺陷之⼀,通常是先形成微观裂纹,再扩展成宏观裂纹。
锻造⼯艺过程(包括加热和冷却)中裂纹的产⽣与受⼒情况、变形⾦属的组织结构、变形温度和变形速度等有关。
锻造⼯艺过程中除了⼯具给予⼯件的作⽤⼒之外,还有由于变形不均匀和变形速度不同引起的附加应⼒、由温度不均匀引起的热应⼒和由组织转变不同时进⾏⽽产⽣的组织应⼒。
应⼒状态、变形温度和变形速度是裂纹产⽣和扩展的外部条件;⾦属的组织结构是裂纹产⽣和扩展的内部依据。
前者是通过对⾦属组织及对微观机制的影响⽽对裂纹的发⽣和扩展发⽣作⽤的。
全⾯分析裂纹的成因应当综合地进⾏⼒学和组织的分析。
(⼀)形成裂纹的⼒学分析在外⼒作⽤下物体内各点处于⼀定应⼒状态,在不同的⽅位将作⽤不同的正应⼒及切应⼒。
裂纹的形式⼀般有两种:⼀是切断,断裂⾯是平⾏于最⼤切应⼒或最⼤切应变;另⼀种是正断,断裂⾯垂直于最⼤正应⼒或正应变⽅向。
⾄于材料产⽣何种破坏形式,主要取决于应⼒状态,即正应⼒σ与剪应⼒τ之⽐值。
也与材料所能承受的极限变形程度εmax 及γmax有关。
例如,①对于塑性材料的扭转,由于最⼤正应⼒与切应⼒之⽐σ/τ=1是剪断破坏;②对于低塑性材料,由于不能承受⼤的拉应变,扭转时产⽣45°⽅向开裂。
由于断⾯形状突然变化或试件上有尖锐缺⼝,将引起应⼒集中,应⼒的⽐值σ/τ有很⼤变化,例如带缺⼝试件拉伸σ/τ=4,这时多发⽣正断。
下⾯分析不同外⼒引起开裂的情况。
1.由外⼒直接引起的裂纹压⼒加⼯⽣产中,在下列⼀些情况,由外⼒作⽤可能引起裂纹:弯曲和校直、脆性材料镦粗、冲头扩孔、扭转、拉拔、拉伸、胀形和内翻边等,现结合⼏个⼯序说明如下。
弯曲件在校正⼯序中(见图3-34)由于⼀侧受拉应⼒常易引起开裂。
例如某⼚锻⾼速钢拉⼑时,⼯具的断⾯是边长相差较⼤的矩形,沿窄边压缩时易产⽣弯曲,当弯曲⽐较严重,随后校正时常常开裂。
镦粗时轴向虽受压应⼒,但与轴线成45°⽅向有最⼤剪应⼒。
14Cr1Mo钢锭开坯裂纹分析及预防措施

0. 45
0. 57 0. 003
P ≤0. 025 0. 004
Ni ≤0. 30 0. 16
Cr
Mo
As
1. 15 ~ 1. 50 0. 45 ~ 0. 65 ≤0. 012
1. 26
0. 45
0. 014
Sn ≤0. 010 0. 003
Sb ≤0. 003 < 0. 001
2. 2 硬度检测 分别 从 裂 纹 附 近 和 未 开 裂 部 位 取 样 ,依 据
No. 4 July 2019
《大型铸锻件》 HEAVY CASTING AND FORGING
DOI:10.14147/ki.51-1396/tg.2019.04.018
14Cr1Mo 钢锭开坯裂纹分析及预防措施
杨德生1,2 韩文科1,2 祁庆花1,2 曹 琨1,2
( 1. 兰州兰石能源装备工程研究院有限公司,甘肃 730314; 2. 甘肃省高端铸锻件工程技术研究中心,甘肃 730314)
without cracks
( a) 裂纹处
( b) 远离裂纹处
( c) 裂纹形貌
( d) 裂纹形貌
( e) 裂纹尖端暗场形貌
( f) 裂纹尖端明场形貌
( g) 锻件近表面组织
Key words: 14Cr1Mo steel ingot; crack; inclusion
14Cr1Mo 属于 Cr-Mo 抗氢钢,具有良好的综 面存在的缺陷属应力裂纹。
合性能,该钢种适用于石油化工、核电、汽轮机缸 体、火电等高温高压、与氢或氢混合介质接触的大
2 检测结果与分析
型设备。某铸造厂生产材质为 14Cr1Mo 的 19 t 2. 1 化学成分分析
不锈钢铸造工艺防止裂纹的措施
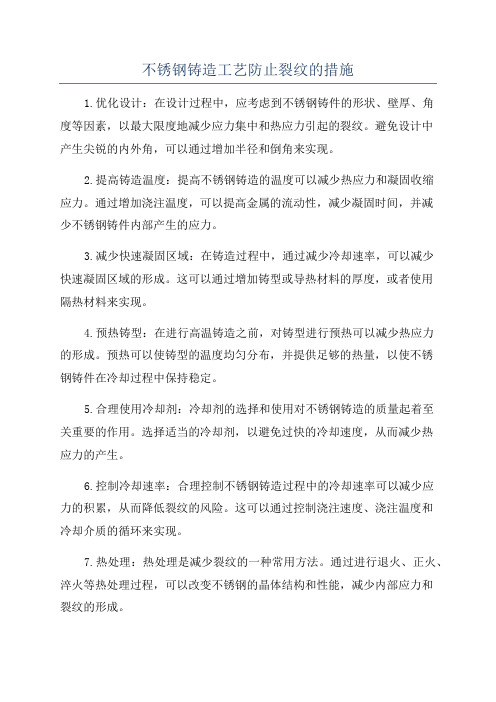
不锈钢铸造工艺防止裂纹的措施1.优化设计:在设计过程中,应考虑到不锈钢铸件的形状、壁厚、角度等因素,以最大限度地减少应力集中和热应力引起的裂纹。
避免设计中产生尖锐的内外角,可以通过增加半径和倒角来实现。
2.提高铸造温度:提高不锈钢铸造的温度可以减少热应力和凝固收缩应力。
通过增加浇注温度,可以提高金属的流动性,减少凝固时间,并减少不锈钢铸件内部产生的应力。
3.减少快速凝固区域:在铸造过程中,通过减少冷却速率,可以减少快速凝固区域的形成。
这可以通过增加铸型或导热材料的厚度,或者使用隔热材料来实现。
4.预热铸型:在进行高温铸造之前,对铸型进行预热可以减少热应力的形成。
预热可以使铸型的温度均匀分布,并提供足够的热量,以使不锈钢铸件在冷却过程中保持稳定。
5.合理使用冷却剂:冷却剂的选择和使用对不锈钢铸造的质量起着至关重要的作用。
选择适当的冷却剂,以避免过快的冷却速度,从而减少热应力的产生。
6.控制冷却速率:合理控制不锈钢铸造过程中的冷却速率可以减少应力的积累,从而降低裂纹的风险。
这可以通过控制浇注速度、浇注温度和冷却介质的循环来实现。
7.热处理:热处理是减少裂纹的一种常用方法。
通过进行退火、正火、淬火等热处理过程,可以改变不锈钢的晶体结构和性能,减少内部应力和裂纹的形成。
8.焊接接头设计:在设计焊接接头时,应选择合适的焊接方法和参数,以减少热影响区域的形成。
合理的焊接接头设计可以有效地分散和缓解焊接引起的应力,降低裂纹的风险。
9.质量控制和检测:在不锈钢铸造过程中,严格控制每个步骤的质量是十分重要的。
定期进行非破坏性和破坏性测试,以评估不锈钢铸件的质量和结构完整性。
总之,防止不锈钢铸造中的裂纹是一项重要的工艺措施。
通过合理的设计、优化的工艺参数、适当的热处理和严格的质量控制,可以有效地减少不锈钢铸件的裂纹风险,提高产品的可靠性和安全性。
平整机支承辊振纹产生机理及抑制措施
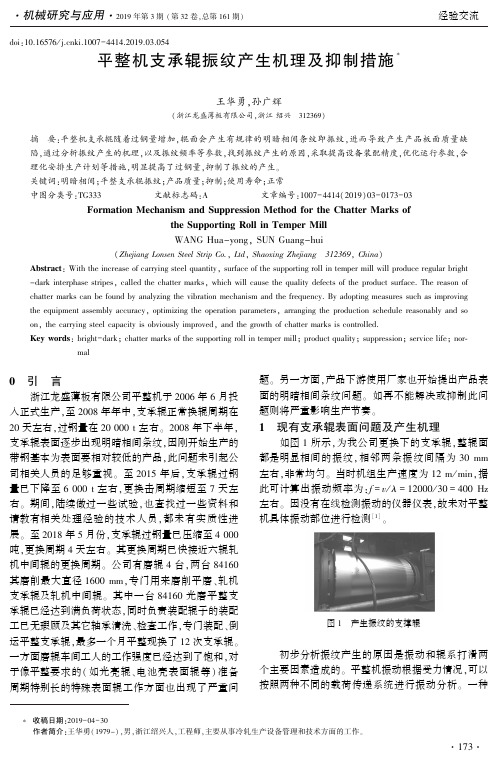
摘 要:平整机支承辊随着过钢量增加ꎬ辊面会产生有规律的明暗相间条纹即振纹ꎬ进而导致产生产品板面质量缺
陷ꎬ通过分析振纹产生的机理ꎬ以及振纹频率等参数ꎬ找到振纹产生的原因ꎬ采取提高设备装配精度ꎬ优化运行参数ꎬ合
理化安排生产计划等措施ꎬ明显提高了过钢量ꎬ抑制了振纹的产生ꎮ
机具体振动部位进行检测 [1] ꎮ
吨ꎬ更换周期 4 天左右ꎮ 其更换周期已快接近六辊轧
机中间辊的更换周期ꎮ 公司有磨辊 4 台ꎬ两台 84160
其磨削最大直径 1600 mmꎬ专门用来磨削平磨、轧机
支承辊及轧机中间辊ꎮ 其中一台 84160 光磨平整支
承辊已经达到满负荷状态ꎬ同时负责装配辊子的装配
工已无瑕顾及其它轴承清洗、检查工作ꎬ专门装配、倒
辊等ꎬ供电电网的频率ꎬ变频控制的调节频率和特征
2019 年第 3 期 ( 第 32 卷ꎬ总第 161 期) 机械研究与应用
推拉力都是与工作辊中心重合ꎬ又花费 50 万重新设
计制造了一台换辊车ꎬ避免换辊车推拉力与工作辊中
频率ꎬ主传动机械扭转系统的固有频率都会产生振动生产ꎬ至 2008 年年中ꎬ支承辊正常换辊周期在
题ꎮ 另一方面ꎬ产品下游使用厂家也开始提出产品表
面的明暗相间条纹问题ꎮ 如再不能解决或抑制此问
题则将严重影响生产节奏ꎮ
20 天左右ꎬ过钢量在 20 000 t 左右ꎮ 2008 年下半年ꎬ
1 现有支承辊表面问题及产生机理
带钢基本为表面要相对较低的产品ꎬ此问题未引起公
the Supporting Roll in Temper Mill
WANG Hua -yongꎬ SUN Guang -hui
( Zhejiang Lonsen Steel Strip Co.ꎬ Ltdꎬ Shaoxing Zhejiang 312369ꎬ China)
锻造裂纹的原因分析及预防措施

锻造裂纹的原因分析及预防措施
φ288mm冷轧辊尾部锻造裂纹
锻件成形及缺陷位置示意图
该件产品用1.75吨钢锭出3件产品,成形情况 及缺陷出现位置如图示
应力状态如图示
防止裂纹再次产生的措施
从冶炼的角度讲,应从提高钢锭头尾部的冶金质量, 即提高钢的纯净度和细化晶粒、均匀结晶组织的角 度出发,改善冶炼条件,提高头尾部的可锻性;
从锻压方面讲,应从应力状态和减小锤击力出发, 即避免产生轴心径向拉应力和减小变形程度的方面 做文章,避免裂纹的产生。打击辊颈时,送进量应 限制在坯料直径的0.5~0.8倍之间,避免拔长辊颈时 出现径向展宽现象,既提高了拔长效率,又避免轴 心的径向拉应力。另外,限制锤的打击力,尽可能 在两吨锤上成形,并选择合适的压下量,以减轻心 的变形程度。两方面入手,以避免裂纹的产生。
说明
以上观点仅为个人看法。
头 1
尾
2
3
裂纹形成原因分析
首先我们看缺陷产生的部位,在钢锭的头尾端。而 钢锭锭身却很少出现缺陷,钢锭的头尾部的冶金质 量不如锭身也是我们的共识,这应是裂纹产生的本 质上的原因。
其次,辊身与辊颈的台阶差较大。辊身的直径为 288mm,裂纹端辊颈才100mm,台阶差188。变形 过程中有两方面问题要说,一方面下圆弧砧的圆弧 大,击打辊颈时,近似于平砧,即料侧面未受力。 砧宽为250mm,若送进量过大,对于辊颈而言,轴 向拔长就变成了径向展宽,即应力状态为轴心径向 拉应力(如下图示),容易产生轴心纵向裂纹;另 一方面,因辊身与辊颈的台阶差大,操作时可能重 锤打击,造成心部变形量过大。头尾料差的塑性与 低的强度加之径向拉应力和重锤就可能导致裂纹的 产生,这应是裂纹产生的外因。
降低支承辊表面裂纹及辊面小剥落概率_喻尧
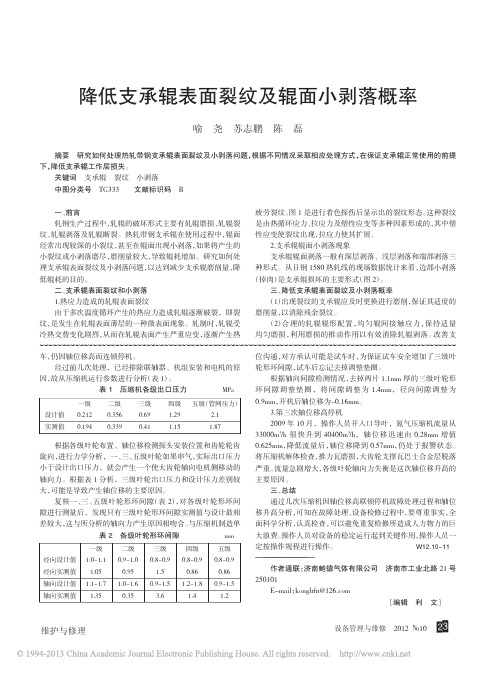
设备管理与维修2012№10车,仍因轴位移高而连锁停机。
经过前几次处理,已经排除联轴器、机组安装和电机的原因,故从压缩机运行参数进行分析(表1)。
根据各级叶轮布置、轴位移检测探头安装位置和齿轮轮齿旋向,进行力学分析,一、三、五级叶轮如果串气,实际出口压力小于设计出口压力,就会产生一个使大齿轮轴向电机侧移动的轴向力。
根据表1分析,三级叶轮出口压力和设计压力差别较大,可能是导致产生轴位移的主要原因。
复核一、三、五级叶轮形环间隙(表2),对各级叶轮形环间隙进行测量后,发现只有三级叶轮形环间隙实测值与设计最相差较大,这与所分析的轴向力产生原因相吻合。
与压缩机制造单位沟通,对方承认可能是试车时,为保证试车安全增加了三级叶轮形环间隙,试车后忘记去掉调整垫圈。
根据轴向间隙检测情况,去掉两片1.1mm 厚的三级叶轮形环间隙调整垫圈,将间隙调整为1.4mm ,径向间隙调整为0.9mm ,开机后轴位移为-0.16mm 。
3.第三次轴位移高停机2009年10月,操作人员开入口导叶,氮气压缩机流量从33000m 3/h 很快升到40400m 3/h ,轴位移迅速由0.28mm 增值0.625mm ,降低流量后,轴位移降到0.57mm ,仍处于报警状态。
将压缩机解体检查,推力瓦磨损,大齿轮支撑瓦巴士合金层脱落严重。
流量急剧增大,各级叶轮轴向力失衡是这次轴位移升高的主要原因。
三、总结通过几次压缩机因轴位移高联锁停机故障处理过程和轴位移升高分析,可知在故障处理、设备检修过程中,要尊重事实,全面科学分析,认真检查,可以避免重复检修所造成人力物力的巨大浪费。
操作人员对设备的稳定运行起到关键作用,操作人员一定按操作规程进行操作。
W12.10-11———————————————作者通联:济南鲍德气体有限公司济南市工业北路21号250101E-mail :konglrfn@〔编辑利文〕表1压缩机各级出口压力MPa一级二级三级四级五级(管网压力)设计值0.2120.3560.69 1.29 2.1实测值0.1940.3390.411.151.87表2各级叶轮形环间隙mm 一级二级三级四级五级经向设计值 1.0~1.10.9~1.00.8~0.90.8~0.90.8~0.9经向实测值 1.050.95 1.50.860.86轴向设计值 1.1~1.7 1.0~1.60.9~1.5 1.2~1.80.9~1.5轴向实测值1.350.353.61.41.2一、前言轧钢生产过程中,轧辊的破坏形式主要有轧辊磨损、轧辊裂纹、轧辊剥落及轧辊断裂。
中型轧钢厂减少断辊的措施
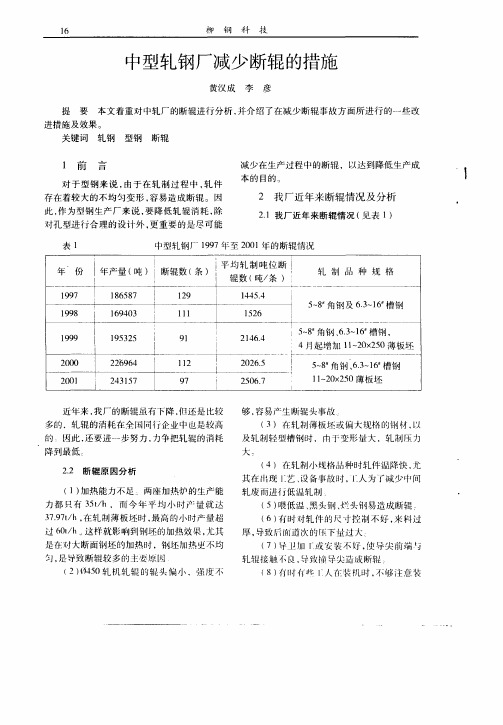
3 减 少 断 辊 的措 施
31改进 轧机 的零部 件 .
( 为提 高下 辊轧 槽 的冷却 效 果 , 们在 3) 我  ̄5  ̄ 0轧机 机座下安 装 了冷却 水管 , 5 以提 高轧槽 的冷 却效 果。
33 加大 辊头直 径 。 用材质 好 的轧 辊 _ 选
中型轧钢 厂 l9 9 7年至 2 0 年的断 辊情况 01 年 产量 ( ) 断辊数 ( ) 平 均 轧 制 吨 位 断 吨 条 辊数 ( 条 ) 吨/ 轧 制 品 种 规 格
l 97 9 l 98 9
l 65 7 8 8 l9 3 6 40
l9 2 ll l
( )针 对 某 些 品 种 的一 些 道 次 容 易造 成 1 撞 导尖的 问题 , 导尖进 行改 进 , 对 并制 定措施 严 格控 制导尖 的加工 制作 质量 。 ( ) 对胶木 瓦冷却 水槽 的形式 进行改 进 。 2 即将 原胶 木瓦 的 “ ” 形 冷却 水槽 改 为斜 交 井 字 叉 冷却水槽 , 对瓦 座及进水 孔 等进 行改进 , 并 以 避免 因冷却不 好而导 致烧坏 辊脖 或辊脖 产生裂 、
对 于 型 钢来 说 , 于 在轧 制 过 程 中 , 件 由 轧 存在着 较 大的 不 均匀 变 形 , 易造 成断 辊 。 因 容
2 我厂近年来断辊情况及分析
21我厂 近年来 断辊情 况 ( 表 1 . 见 )
此 , 为 型钢 生产 厂来 说 , 降低 轧辊 消耗 , 作 要 除
对孑 型进 行合 理 的设 计 外 , 重要 的是尽 可 能 L 更 表 l 年 份
、
1 - 0 2 0薄 板坯 2x5 1
近年来 , 厂的 断辊虽 有下 降 , 我 但还 是 比较 多的 ,轧辊 的消 耗在 全 闰同行 企业 中也是较 高 的:因此 , 还要进 一 步努 力 , 力争 把轧辊 的 消耗 降 到最低 :
铸钢件裂纹缺陷及预防措施
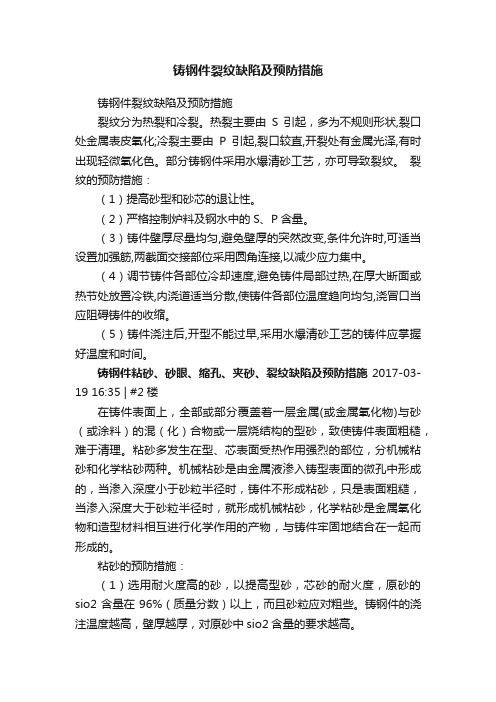
铸钢件裂纹缺陷及预防措施铸钢件裂纹缺陷及预防措施裂纹分为热裂和冷裂。
热裂主要由S引起,多为不规则形状,裂口处金属表皮氧化;冷裂主要由P引起,裂口较直,开裂处有金属光泽,有时出现轻微氧化色。
部分铸钢件采用水爆清砂工艺,亦可导致裂纹。
裂纹的预防措施:(1)提高砂型和砂芯的退让性。
(2)严格控制炉料及钢水中的S、P含量。
(3)铸件壁厚尽量均匀,避免壁厚的突然改变,条件允许时,可适当设置加强筋,两截面交接部位采用圆角连接,以减少应力集中。
(4)调节铸件各部位冷却速度,避免铸件局部过热,在厚大断面或热节处放置冷铁,内浇道适当分散,使铸件各部位温度趋向均匀,浇冒口当应阻碍铸件的收缩。
(5)铸件浇注后,开型不能过早,采用水爆清砂工艺的铸件应掌握好温度和时间。
铸钢件粘砂、砂眼、缩孔、夹砂、裂纹缺陷及预防措施2017-03-19 16:35 | #2楼在铸件表面上,全部或部分覆盖着一层金属(或金属氧化物)与砂(或涂料)的混(化)合物或一层烧结构的型砂,致使铸件表面粗糙,难于清理。
粘砂多发生在型、芯表面受热作用强烈的部位,分机械粘砂和化学粘砂两种。
机械粘砂是由金属液渗入铸型表面的微孔中形成的,当渗入深度小于砂粒半径时,铸件不形成粘砂,只是表面粗糙,当渗入深度大于砂粒半径时,就形成机械粘砂,化学粘砂是金属氧化物和造型材料相互进行化学作用的产物,与铸件牢固地结合在一起而形成的。
粘砂的预防措施:(1)选用耐火度高的砂,以提高型砂,芯砂的耐火度,原砂的sio2含量在96%(质量分数)以上,而且砂粒应对粗些。
铸钢件的浇注温度越高,壁厚越厚,对原砂中sio2含量的要求越高。
(2)适当降低浇注温度和提高浇注速度,减轻金属液对砂型的热力学和物理化学作用。
(3)砂型紧实度要高(通常大于85)且均匀,减少砂粒间隙;型、芯修补到位,不能有局部疏松。
(4)采用在高温下不开裂、不烧结成熔洞的涂料铸钢件砂眼缺陷及预防措施砂眼缺陷处内部或表面有充塞着型(芯)砂的小孔,砂眼是一种常见的铸造缺陷,往往导致铸件报废。
连铸机输送辊的裂纹分析与消除措施
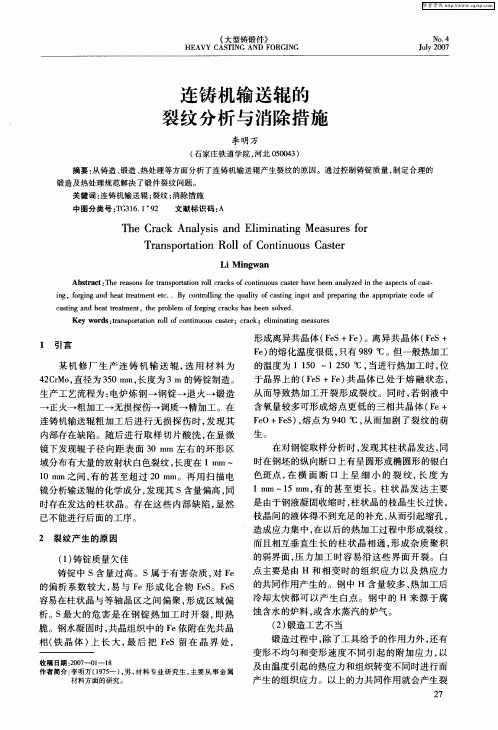
维普资讯
《 大型铸 锻件》
HE AVY C T NG AND F As I ORGI G N
No. 4
J l 0 7 uy2 0
连铸机输 送辊 的 裂纹分析 与消除措施
李 明万
( 家庄铁道学 院, 石 河北 0 04 ) 50 3
Th a k An lssa d Elmi aig Me s r sfr e Cr c ay i n i n tn a u e o
Tr n p Ia i n Ro lo n i u u se a பைடு நூலகம் 0r t0 l fCo tn o s Ca t r t
LiM i wa ng n
降低支承辊锻件外露夹杂缺陷的措施
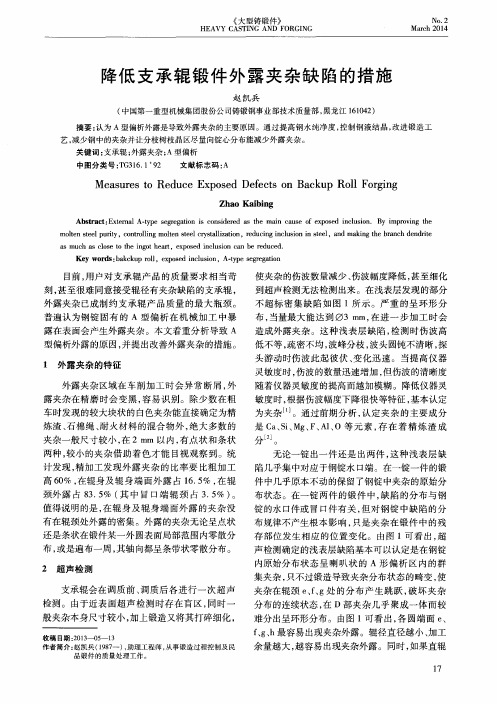
随着仪器灵敏度 的提高而越加模糊 。降低仪器灵
敏度 时 , 根 据伤 波 幅度下 降很快 等 特征 , 基 本认 定 为夹杂 … 。通过 前期 分 析 , 认 定 夹 杂 的 主要 成 分 是 c a 、 S i 、 Mg 、 F 、 A 1 、 O等元素 , 存 在 着 精 炼 渣 成
分 。
高6 0 %, 在辊身及辊 身端 面外露 占 1 6 . 5 %, 在辊
颈外露 占 8 3 . 5 %( 其 中 冒 口端 辊 颈 占 3 . 5 %) 。 值 得说 明的是 , 在 辊 身及 辊 身 端 面 外 露 的 夹 杂没 有 在辊 颈处 外露 的密 集 。外露 的夹 杂无 论呈 点状
型 偏析 外露 的原 因 , 并 提 出改 善外 露夹 杂 的措 施 。
1 外露 夹杂 的特 征
外露 夹 杂 区域 在 车削 加 工 时 会 异 常 断 屑 , 外 露夹 杂 在精 磨 时 会 变 黑 , 容 易识 别 。除少 数 在 粗
车 时发 现 的较 大块 状 的 白色夹杂 能直 接确 定 为精
艺, 减少 钢中的夹杂并让分枝树枝 晶区尽量 向锭心分 布能减 少外 露夹杂。 关键词 : 支承辊 ; 外露夹杂 ; A型偏析
中图 分 类 号 : T G 3 1 6 . 1 9 2 文献标志码 : A
Me a s u r e s t o Re d u c e Ex p o s e d De f e c t s o n Ba c k u p Ro l l F o r g i n g
目前 , 用户对支承辊产 品的质量要求相当苛 刻, 甚 至很难 同意接 受辊 径有 夹杂 缺 陷的支 承辊 ,
外 露夹 杂 已成 制 约支 承 辊 产 品质 量 的最 大瓶 颈 。 普 遍认 为 钢锭 固有 的 A 型 偏 析 在 机 械 加 工 中暴
高合金冷轧辊内部锻造裂纹控制
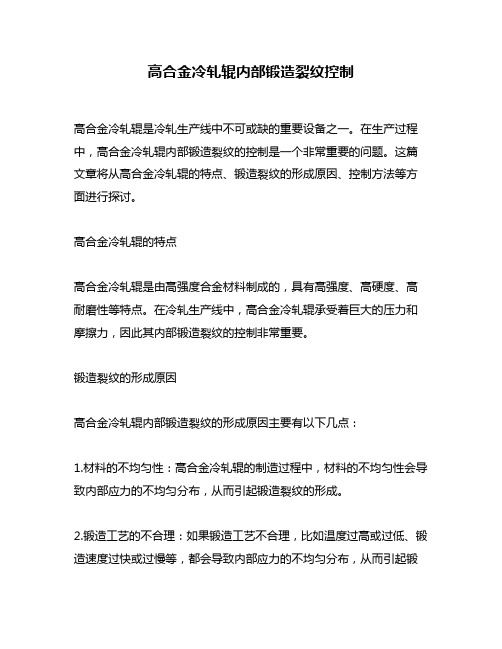
高合金冷轧辊内部锻造裂纹控制高合金冷轧辊是冷轧生产线中不可或缺的重要设备之一。
在生产过程中,高合金冷轧辊内部锻造裂纹的控制是一个非常重要的问题。
这篇文章将从高合金冷轧辊的特点、锻造裂纹的形成原因、控制方法等方面进行探讨。
高合金冷轧辊的特点高合金冷轧辊是由高强度合金材料制成的,具有高强度、高硬度、高耐磨性等特点。
在冷轧生产线中,高合金冷轧辊承受着巨大的压力和摩擦力,因此其内部锻造裂纹的控制非常重要。
锻造裂纹的形成原因高合金冷轧辊内部锻造裂纹的形成原因主要有以下几点:1.材料的不均匀性:高合金冷轧辊的制造过程中,材料的不均匀性会导致内部应力的不均匀分布,从而引起锻造裂纹的形成。
2.锻造工艺的不合理:如果锻造工艺不合理,比如温度过高或过低、锻造速度过快或过慢等,都会导致内部应力的不均匀分布,从而引起锻造裂纹的形成。
3.金属材料的疲劳:高合金冷轧辊在长期使用过程中,由于受到巨大的压力和摩擦力,会导致金属材料的疲劳,从而引起锻造裂纹的形成。
控制方法为了控制高合金冷轧辊内部锻造裂纹的形成,需要采取以下措施:1.优化材料:选择优质的高强度合金材料,确保材料的均匀性和稳定性,从而减少内部应力的不均匀分布。
2.优化锻造工艺:合理控制锻造温度、速度等参数,确保锻造过程中内部应力的均匀分布,从而减少锻造裂纹的形成。
3.加强维护:定期对高合金冷轧辊进行检查和维护,及时发现和处理锻造裂纹,从而延长其使用寿命。
总结高合金冷轧辊内部锻造裂纹的控制是冷轧生产线中非常重要的问题。
通过优化材料、锻造工艺和加强维护等措施,可以有效地减少锻造裂纹的形成,提高高合金冷轧辊的使用寿命和生产效率。
降低支承辊外露夹杂缺陷的措施
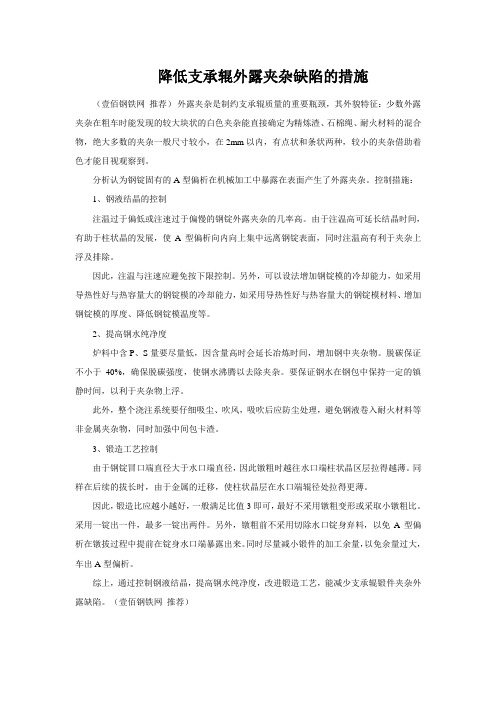
降低支承辊外露夹杂缺陷的措施(壹佰钢铁网推荐)外露夹杂是制约支承辊质量的重要瓶颈,其外貌特征:少数外露夹杂在粗车时能发现的较大块状的白色夹杂能直接确定为精炼渣、石棉绳、耐火材料的混合物,绝大多数的夹杂一般尺寸较小,在2mm以内,有点状和条状两种,较小的夹杂借助着色才能目视观察到。
分析认为钢锭固有的A型偏析在机械加工中暴露在表面产生了外露夹杂。
控制措施:1、钢液结晶的控制注温过于偏低或注速过于偏慢的钢锭外露夹杂的几率高。
由于注温高可延长结晶时间,有助于柱状晶的发展,使A型偏析向内向上集中远离钢锭表面,同时注温高有利于夹杂上浮及排除。
因此,注温与注速应避免按下限控制。
另外,可以设法增加钢锭模的冷却能力,如采用导热性好与热容量大的钢锭模的冷却能力,如采用导热性好与热容量大的钢锭模材料、增加钢锭模的厚度、降低钢锭模温度等。
2、提高钢水纯净度炉料中含P、S量要尽量低,因含量高时会延长冶炼时间,增加钢中夹杂物。
脱碳保证不小于40%,确保脱碳强度,使钢水沸腾以去除夹杂。
要保证钢水在钢包中保持一定的镇静时间,以利于夹杂物上浮。
此外,整个浇注系统要仔细吸尘、吹风,吸吹后应防尘处理,避免钢液卷入耐火材料等非金属夹杂物,同时加强中间包卡渣。
3、锻造工艺控制由于钢锭冒口端直径大于水口端直径,因此镦粗时越往水口端柱状晶区层拉得越薄。
同样在后续的拔长时,由于金属的迁移,使柱状晶层在水口端辊径处拉得更薄。
因此,锻造比应越小越好,一般满足比值3即可,最好不采用镦粗变形或采取小镦粗比。
采用一锭出一件,最多一锭出两件。
另外,镦粗前不采用切除水口锭身弃料,以免A型偏析在镦拔过程中提前在锭身水口端暴露出来。
同时尽量减小锻件的加工余量,以免余量过大,车出A型偏析。
综上,通过控制钢液结晶,提高钢水纯净度,改进锻造工艺,能减少支承辊锻件夹杂外露缺陷。
(壹佰钢铁网推荐)。
铝合金大直径园铸锭铸造时防止裂纹的方法
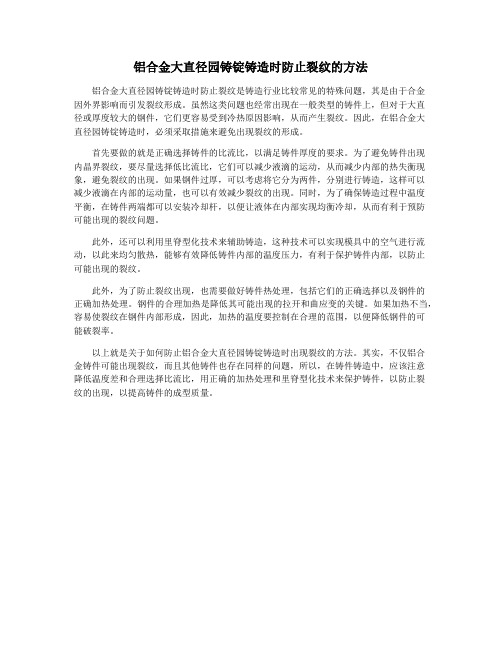
铝合金大直径园铸锭铸造时防止裂纹的方法铝合金大直径园铸锭铸造时防止裂纹是铸造行业比较常见的特殊问题,其是由于合金因外界影响而引发裂纹形成。
虽然这类问题也经常出现在一般类型的铸件上,但对于大直径或厚度较大的钢件,它们更容易受到冷热原因影响,从而产生裂纹。
因此,在铝合金大直径园铸锭铸造时,必须采取措施来避免出现裂纹的形成。
首先要做的就是正确选择铸件的比流比,以满足铸件厚度的要求。
为了避免铸件出现内晶界裂纹,要尽量选择低比流比,它们可以减少液滴的运动,从而减少内部的热失衡现象,避免裂纹的出现。
如果钢件过厚,可以考虑将它分为两件,分别进行铸造,这样可以减少液滴在内部的运动量,也可以有效减少裂纹的出现。
同时,为了确保铸造过程中温度平衡,在铸件两端都可以安装冷却杆,以便让液体在内部实现均衡冷却,从而有利于预防可能出现的裂纹问题。
此外,还可以利用里脊型化技术来辅助铸造,这种技术可以实现模具中的空气进行流动,以此来均匀散热,能够有效降低铸件内部的温度压力,有利于保护铸件内部,以防止可能出现的裂纹。
此外,为了防止裂纹出现,也需要做好铸件热处理,包括它们的正确选择以及钢件的正确加热处理。
钢件的合理加热是降低其可能出现的拉开和曲应变的关键。
如果加热不当,容易使裂纹在钢件内部形成,因此,加热的温度要控制在合理的范围,以便降低钢件的可能破裂率。
以上就是关于如何防止铝合金大直径园铸锭铸造时出现裂纹的方法。
其实,不仅铝合金铸件可能出现裂纹,而且其他铸件也存在同样的问题,所以,在铸件铸造中,应该注意降低温度差和合理选择比流比,用正确的加热处理和里脊型化技术来保护铸件,以防止裂纹的出现,以提高铸件的成型质量。
减少辊子轴头疲劳断裂的措施
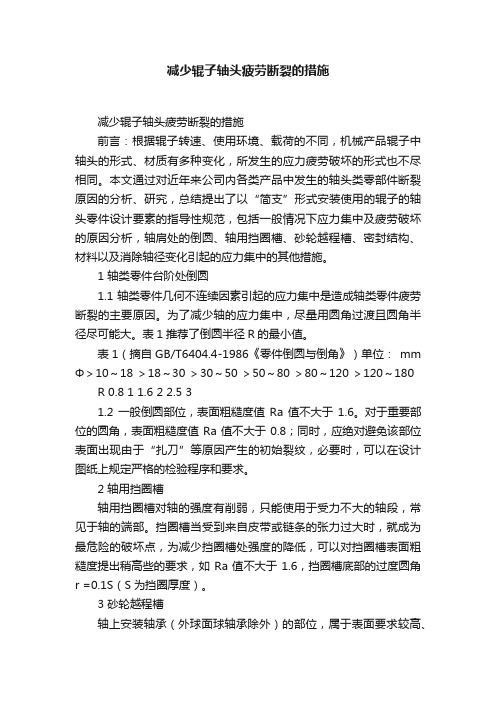
减少辊子轴头疲劳断裂的措施减少辊子轴头疲劳断裂的措施前言:根据辊子转速、使用环境、载荷的不同,机械产品辊子中轴头的形式、材质有多种变化,所发生的应力疲劳破坏的形式也不尽相同。
本文通过对近年来公司内各类产品中发生的轴头类零部件断裂原因的分析、研究,总结提出了以“简支”形式安装使用的辊子的轴头零件设计要素的指导性规范,包括一般情况下应力集中及疲劳破坏的原因分析,轴肩处的倒圆、轴用挡圈槽、砂轮越程槽、密封结构、材料以及消除轴径变化引起的应力集中的其他措施。
1 轴类零件台阶处倒圆1.1 轴类零件几何不连续因素引起的应力集中是造成轴类零件疲劳断裂的主要原因。
为了减少轴的应力集中,尽量用圆角过渡且圆角半径尽可能大。
表1推荐了倒圆半径R的最小值。
表1(摘自GB/T6404.4-1986《零件倒圆与倒角》)单位:mm Φ>10~18 >18~30 >30~50 >50~80 >80~120 >120~180 R 0.8 1 1.6 2 2.5 31.2 一般倒圆部位,表面粗糙度值Ra值不大于1.6。
对于重要部位的圆角,表面粗糙度值Ra值不大于0.8;同时,应绝对避免该部位表面出现由于“扎刀”等原因产生的初始裂纹,必要时,可以在设计图纸上规定严格的检验程序和要求。
2 轴用挡圈槽轴用挡圈槽对轴的强度有削弱,只能使用于受力不大的轴段,常见于轴的端部。
挡圈槽当受到来自皮带或链条的张力过大时,就成为最危险的破坏点,为减少挡圈槽处强度的降低,可以对挡圈槽表面粗糙度提出稍高些的要求,如Ra值不大于1.6,挡圈槽底部的过度圆角r =0.1S(S为挡圈厚度)。
3 砂轮越程槽轴上安装轴承(外球面球轴承除外)的部位,属于表面要求较高、需要磨削的轴段,轴肩处一般应设计砂轮越程槽。
图1和表2给出了GB/T6404.3-1986《砂轮越程槽》推荐的两种砂轮越程槽形式和尺寸。
也可加在保证轴肩过度圆角的情况下,通过加装过渡轴环保证零件轴向定位。
- 1、下载文档前请自行甄别文档内容的完整性,平台不提供额外的编辑、内容补充、找答案等附加服务。
- 2、"仅部分预览"的文档,不可在线预览部分如存在完整性等问题,可反馈申请退款(可完整预览的文档不适用该条件!)。
- 3、如文档侵犯您的权益,请联系客服反馈,我们会尽快为您处理(人工客服工作时间:9:00-18:30)。
三 ◆三
N o . 1
HEAV Y C AS r nNG A ND F0 RGI NG
J a n u a r y 2 0 1 4
~ 一 术 产 技~ 生 ~ 一
、三 ◆三
减 少支 承 辊 钢 锭 锻 造 裂 纹 的措 施
赵 凯兵 ( 中国第一重型机械集 团股份公 司铸锻 钢事业部 技术 质量部 , 黑龙 江 1 6 1 0 4 2 )
支承辊钢锭在锻造过程 中, 锭 身表面 出现 肉 眼可见 的裂 纹一直 是 困扰技 术人 员 的难题 或火焰 烧剥 清除 的方 式进 行 挽救 , 重 者则 直接 报废 , 经济 损失 十分 严重 。本 文 从 理论 角度 对导 致支 承辊钢 锭表 面裂 纹 的 因素 进
为确定裂纹究竟是钢锭本身原因还是锻造或加热 造成的, 我们从钢锭脱模 、 热送 , 到锻造整个过程 ,
对钢锭 的表 面质 量进 行 了仔 细 检查 。发 现个别 钢 锭 在脱模 后 表 面有 细 横 裂 或顺 裂 , 部 分 入 加 热 炉 前无表 面裂 纹 的钢 锭 , 在 压 钳 口时 锭身 表 面 会 发 现细顺 纹 或细横 纹 。可 以确定钢 锭锻 造过 程 中 出 现 的裂 纹 , 部分是 钢锭 本身 存在 的 , 只是未 发现 而
Y B . 7 5是 C r 5材 质 , Y B - 6 5是 C r 4材 质 , Y B - 6 5和 Y B - 7 5含 碳 量 为 0 . 4 5 % ~ 0 . 5 5 %, Y B - 7 0的 含 碳 量为 0 . 4 8 % ~ 0 . 5 8 % 。这 三 种 材 质 可 以看 成 是
已。由于不倒棱 , 压钳 口火次存在的裂纹绝大多 数 藏 匿在 氧 化 铁 皮 下方 , 同时 部 分 顺 裂 较 细 、 较
行初步分析 , 寻找有效的控制方法。
1 裂纹概 况
支 承辊 钢 锭 经 常在 镦 粗 时 出现 顺 裂 , K D 时 出现横 裂 , 甚 至在 压 钳 口时就 已经 出现 裂 纹 。 因 大钢锭 现 已取消倒 棱 工序 , 镦粗 前锭 身仍 未锻 压 ,
在 中碳 钢基 础上 添加 合金元 素 而成 。碳含 量处 于 0 . 4 %~ 0 . 6 %之 间的 中碳钢 材料铸 态 组织 的热 裂
Me a s u r e s t o Re d u c e F o r g e C r a c k s o f B a c k u p Ro l l I n g o t
Zha o Ka i bi n g
Ab s t r a c t : T h i s p a p e r a i ms a t s e v e r e f o r g e r a p t u r e ,f a c t o r s a f f e c t i n g t h e i n g o t s u r f a c e q u a l i t y a n d c a u s e s o f t h e f o r g e c r a c k,a r e a n a l y z e d i n t e r ms o f c h e mi c a l c o mp o s i t i o n,s me l t i n g, c a s t i n g o t ,i n g o t s t r i p p i n g,h o t d e l i v e y ,h r e a t i n g, a n d f o r g e,me a s u r e s t o r e d u c e t h e i n g o t f o r g e c r a c k a r e p u t f o r w a r d . Ke y wo r d s: b a c k u p r o l l i n g o t ,f o r g i n g c r a c k ,s t r e s s
抗力 比较 低 J , 同样 碳 含 量 居 于 这 一 区 间 的
4 2 C r Mo 、 4 5等 材质 的 中碳 钢 钢锭 也会 在 锻造 中出 现 严重 裂纹 , 只是生 产批量 少 而没引 起关 注而 已 。 实 际成 分统 计 中发现 Y B . 7 0的碳 含量 要 高于 Y B 一 6 5和 Y B - 7 5 , Y B 一 6 5的含 Mn量 比  ̄ B - 7 5高 。这 说 明 C、 Mn元素 影 响这三种 支 承辊材 质 的热 裂 抗 力, 对 钢锭 裂纹形 成 有一定 影 响 。因此 , 在 成分 规 格 范 围不变 的前 提下 , 运用计 算 材料学 的方 法 , 设 计 并调 整合 金成 分 , 有 利 于降 低 支 承辊 钢 锭 的 裂
摘要 : 针对支承辊钢锭出现的严重锻造裂纹 问题 , 从成分 、 冶炼 、 铸锭 、 脱模 、 热送、 加热和 锻造方 面分析影
响钢锭表 面质量 的因素和造 成锻造裂纹的原因 , 并提 出了减少 钢锭 锻造裂纹的措施。 关键词 : 支承辊钢锭 ; 锻造裂纹 ; 应力 中图分类号 : T G 3 1 6 . 1 9 2 文献标志码 : A
造 裂纹 的措 施 。
2 制造 过 程分析 2 . 1 化 学成 分
在 大批 量生 产 的工况 下 , 裂 纹集 中在 Y B - 6 5 、 Y B 一 7 0 、 Y B 一 7 5这 三 种 材质 的支 承 辊 钢 锭 上 。Y B . 7 5出现裂 纹 的 比例 最 高 , Y B 一 6 5次 之 。Y B . 7 0和