锻造裂纹分析
自由锻造的主要缺陷是

自由锻件主要缺陷产生原因一、横向裂纹:1、表面横向裂纹缺陷现象:锻造时坯料表面出现较浅(约10mm深)的横向裂纹或较深的横向裂纹。
产生原因:较浅裂纹是钢锭皮下气泡未焊合形成的,较深裂纹是由钢锭浇注受锭模内壁质量,钢水摆动和钢锭与锭模铸合等因素形成的。
2、内部横向裂纹缺陷现象:在锻件内部产生横向裂纹。
产生原因:冷钢锭在低温区加热过快或中心引起较大拉力造成,高碳钢和高合金钢塑性较差,在锻造操作相对送进量过小造成的。
二、纵向裂纹1、表面纵向裂纹A缺陷现象:经常在第一次拔长或镦粗时出现。
产生原因:锭模内壁缺陷和新锭模未很好退火,操作不当,高温高速浇注,钢锭脱模冷却不当或脱模过早,倒棱时压下量过大,轧制钢锭时产生纵向划痕等。
B缺陷现象:在坯料近帽口中心出现。
产生原因:由于钢锭冷却时缩孔未集中于帽口部分,锻造帽口端切头量过少,使坯料近帽口端存在二次缩孔或残余缩孔,锻造时引起纵向裂纹。
2、内部纵向裂纹A缺陷现象:坯料内部出现的纵向裂纹。
产生原因:这是利用拔长圆截面坯料,金属中心部分受拉力作用所致,或者因坯料未加热透彻,内部温度过低,拔长时内部沿纵向开裂等。
B缺陷现象:坯料内部出现的纵向十字裂纹,一般出现于高合金钢中。
产生原因:这是由于拔长时送进量过大或在同一部位反复多次锻造。
三、炸裂:缺陷现象:一般在坯料锻造前加热时或锻件冷却热处理后,在表面或内部炸开而形成的裂纹。
产生原因:因为坯料具有较高的残余应力,在未予清除的情况下,错误的采用快速加热或不适当的冷却引起裂纹。
四、自行开裂缺陷现象:常常在锻件锻造后、热处理后或锻制拔长后发生。
产生原因:坯料在锻造过程中已经形成微小裂纹,冷却或热处理中使之加剧或由于锻件内部有较大残余应力所致。
五、龟裂缺陷现象:锻件在锻造时表面出现的龟甲状或裂纹,钢料表面较浅的龟裂应清除后再锻造。
产生原因:由于钢中Cu、Sn、As、S的含量较多,或者在加热炉中铜料渗入,熔化的铜渗入钢料晶界,造成钢料热脆或者由于坯料开始锻温度过高,开始锻造时锤击过重等原因造成。
锻造裂纹的原因分析及预防措施

说明
以上观点仅为个人看法。
应力状态如图示
防止裂纹再次产生的措施
从冶炼的角度讲,应从提高钢锭头尾部的冶金质量, 即提高钢的纯净度和细化晶粒、均匀结晶组织的角 度出发,改善冶炼条件,提高头尾部的可锻性;
从锻压方面讲,应从应力状态和减小锤击力出发, 即避免产生轴心径向拉应力和减小变形程度的方面 做文章,避免裂纹的产生。打击辊颈时,送进量应 限制在坯料直径的0.5~0.8倍之间,避免拔长辊颈时 出现径向展宽现象,既提高了拔长效率,又避免轴 心的径向拉应力。另外,限制锤的打击力,尽可能 在两吨锤上成形,并选择合适的压下量,以减轻心 部的变形程度。两方面入手,以避免裂纹的产生。
锻造裂纹的原因分析及预防措施
φ288mm冷轧辊尾部锻造裂纹 Nhomakorabea锻件成形及缺陷位置示意图
该件产品用1.75吨钢锭出3件产品,成形情况 及缺陷出现位置如图示
头 1
尾
2
3
裂纹形成原因分析
首先我们看缺陷产生的部位,在钢锭的头尾端。而 钢锭锭身却很少出现缺陷,钢锭的头尾部的冶金质 量不如锭身也是我们的共识,这应是裂纹产生的本 质上的原因。
自由锻常见缺陷裂纹的原因

自由锻常见缺陷裂纹的原因自由锻是一种常见的金属加工工艺,通过利用金属的塑性变形特性来加工成型各种零部件。
然而,在实际的生产过程中,由于材料属性、加工工艺等原因,常常会出现各种缺陷,其中最常见的就是裂纹。
裂纹的出现不仅会影响零部件的质量和性能,还可能导致工件失效,因此及时发现并采取措施是非常重要的。
下面将从几个方面介绍自由锻常见缺陷裂纹的原因。
1. 材料因素材料的质量和性能对自由锻过程的裂纹形成起着重要的作用。
首先,原材料的杂质和非金属夹杂物会降低金属的塑性,增加金属的脆性,从而容易形成裂纹。
其次,金属的晶粒度和组织结构也会对裂纹的产生起到影响作用。
晶粒度过大或过小都会导致金属的塑性不足,从而容易出现裂纹。
此外,金属中的残余应力也是裂纹产生的一个重要因素,过大的残余应力会在加工过程中导致金属局部应力集中,进而形成裂纹。
2. 加工工艺因素自由锻的加工工艺对裂纹的形成有着直接的影响。
例如,锻造温度过高或过低都会影响金属的塑性,从而容易形成裂纹。
此外,锻造的速度、变形量等参数设置也会对裂纹的形成起到影响。
如果变形量过大或变形速度过快,可能使金属的应力超过其承载能力,导致裂纹的产生。
还有一些其他因素,比如锻造过程中的冷却速度、锻后的热处理工艺等也会对裂纹的形成产生影响。
3. 设计因素零部件的设计也是影响裂纹产生的因素之一。
不合理的结构设计、过于尖锐的转角或者挤压形状等都可能会导致金属在锻造过程中产生应力集中,从而形成裂纹。
因此,在设计零部件时,应该尽量避免设计过于尖锐的结构,合理控制转角和挤压形状,以减少应力集中点的产生。
4. 操作因素操作人员的技术水平和操作规范也会对裂纹的产生起到影响。
不合理的操作方法、过于急躁的操作、缺乏经验的操作人员等都有可能导致裂纹的产生。
因此,操作人员需要具备良好的技术水平和严格的操作规范,以避免不必要的裂纹产生。
5. 设备因素锻造设备的状态和性能也会对裂纹产生起到影响。
例如,设备的润滑状态不良、设备磨损严重、设备结构设计不合理等都有可能导致应力集中,从而形成裂纹。
c17200铍铜合金锻造开裂原因分析

S 科学技术 cience and technology
C17200 铍铜合金锻造开裂原因分析
岳丽娟,张 勇,焦晓亮,曹虎成
(宁夏中色新材料有限公司,宁夏 石嘴山 753000)
摘 要 :通过对 C17200 铍铜合金锻造开裂的样品进行化学成分、微观组织及微区成分分析,利用扫描电镜和能谱分析手段,从
图 6 铸态金相 100X
图 4 裂纹宏观形貌 1000X
通过对锻造开裂样品进行扫描电镜和能谱分析可知,材料 内部存在金属 Co 的富集,并且存在 Ca、Al、Ba、O、Si、Fe 等杂 质元素。
表1??样品的化学成分elementsbecofealsipbgbt5231标准182102050150150150005开裂样品11880220067004300530002开裂样品21920210093003700620002开裂样品31870240058004900840002未开裂样品11850230072003200270002未开裂样品21890220045004200310002未开裂样品31840220051003300460002表2??样品的杂质含量elementscamgba总量开裂样品10025003500610284开裂样品20047003100240294开裂样品300280028000930256未开裂样品10022001100110175未开裂样品20019001900150171未开裂样品300260020000830184从表1的结果可以看出从化学成分上来讲开裂和未开裂处的成分均满足gbt52312012加工铜化学成分和产品形状中的要求
锻造和热处理过程中裂纹形成原因分析

锻造和热处理过程中裂纹形成原因分析摘要:在锻造以及热处理中极易出现裂纹,为此锻造以及热处理过程中的裂纹处理成为各个学者研究的重点,同时,构件尺寸、材质等之间的差异其所出现的裂纹几率也各不相同,基于此,本文通过对锻造以及热处理缺陷的相关分析,找出了锻造和热处理过程中裂纹形成的原因并提出了针对性的解决意见。
关键词:锻造热处理裂纹原因分析处理引言作为锻造以及热处理过程中最为常见的缺陷之一,裂纹的形成严重制约了锻造效率,并且对于大型锻件而言,其裂纹出现的几率则更高,所以加强对裂纹形成的原因分析对于减少裂纹产生,提升锻造效果具有重要意义。
1锻造缺陷与热处理缺陷第一,过热或者过烧。
具体表现形式为晶粒粗大并具有较为明显的魏氏组织;而造成过烧的情况则说明热处理过程中温度较高,断口晶粒凹凸不平,缺乏金属光泽,并且晶界周围具有氧化脱碳的情况;第二,锻造裂纹。
主要出现在组织粗大且应力较为集中处,裂纹内部往往呈现氧化皮情况。
在锻造过程中无论是温度过高,还是过低均会导致裂纹的出现;第三,折叠。
由于切料、冲孔、锻粗糙等原因而致使材料表面发生了缺陷,而此时一旦经过锻造自然其会由于表面氧化皮缺陷内卷而形成折叠。
通过显微镜的观察可以明显的发现折叠周围的脱碳情况较为严重;第四,淬裂。
该缺陷的明显特征就是刚健挺直且起始点较宽,尾部则细长曲直。
由于此缺陷往往是产生在马氏体转变发生以后,所以裂纹周围与其他区域没有明显的差别且无脱碳情况;第五,软点。
造成此种缺陷的原因主要是由于加热不足,保温时间不足而造成冷却不均匀导致的。
2实验方法2.1试样制备和宏观观察在开始试验之前只需要对构件毛坯裂纹进行简单的宏观观测并选择要进行实验的区域即可。
然后,在利用手边的工具来队选取的区域进行切割,需注意的是,切割方向必须要垂直镜像,切割长度要低于10mm。
可以通过多种方式进行取样但是一定要科学的选择取样的温度以及环境,如果实验温度较高,则可以通过凉水来进行冷却,进而防止在取样过程中构件内部结构遭到损坏。
锻造裂纹产生的原因及解决方法

锻造裂纹产⽣的原因及解决⽅法裂纹是锻压⽣产中常见的主要缺陷之⼀,通常是先形成微观裂纹,再扩展成宏观裂纹。
锻造⼯艺过程(包括加热和冷却)中裂纹的产⽣与受⼒情况、变形⾦属的组织结构、变形温度和变形速度等有关。
锻造⼯艺过程中除了⼯具给予⼯件的作⽤⼒之外,还有由于变形不均匀和变形速度不同引起的附加应⼒、由温度不均匀引起的热应⼒和由组织转变不同时进⾏⽽产⽣的组织应⼒。
应⼒状态、变形温度和变形速度是裂纹产⽣和扩展的外部条件;⾦属的组织结构是裂纹产⽣和扩展的内部依据。
前者是通过对⾦属组织及对微观机制的影响⽽对裂纹的发⽣和扩展发⽣作⽤的。
全⾯分析裂纹的成因应当综合地进⾏⼒学和组织的分析。
(⼀)形成裂纹的⼒学分析在外⼒作⽤下物体内各点处于⼀定应⼒状态,在不同的⽅位将作⽤不同的正应⼒及切应⼒。
裂纹的形式⼀般有两种:⼀是切断,断裂⾯是平⾏于最⼤切应⼒或最⼤切应变;另⼀种是正断,断裂⾯垂直于最⼤正应⼒或正应变⽅向。
⾄于材料产⽣何种破坏形式,主要取决于应⼒状态,即正应⼒σ与剪应⼒τ之⽐值。
也与材料所能承受的极限变形程度εmax 及γmax有关。
例如,①对于塑性材料的扭转,由于最⼤正应⼒与切应⼒之⽐σ/τ=1是剪断破坏;②对于低塑性材料,由于不能承受⼤的拉应变,扭转时产⽣45°⽅向开裂。
由于断⾯形状突然变化或试件上有尖锐缺⼝,将引起应⼒集中,应⼒的⽐值σ/τ有很⼤变化,例如带缺⼝试件拉伸σ/τ=4,这时多发⽣正断。
下⾯分析不同外⼒引起开裂的情况。
1.由外⼒直接引起的裂纹压⼒加⼯⽣产中,在下列⼀些情况,由外⼒作⽤可能引起裂纹:弯曲和校直、脆性材料镦粗、冲头扩孔、扭转、拉拔、拉伸、胀形和内翻边等,现结合⼏个⼯序说明如下。
弯曲件在校正⼯序中(见图3-34)由于⼀侧受拉应⼒常易引起开裂。
例如某⼚锻⾼速钢拉⼑时,⼯具的断⾯是边长相差较⼤的矩形,沿窄边压缩时易产⽣弯曲,当弯曲⽐较严重,随后校正时常常开裂。
镦粗时轴向虽受压应⼒,但与轴线成45°⽅向有最⼤剪应⼒。
锻造裂纹与热处理裂纹原理形态

一:锻造裂纹与热处理裂纹形态一:锻造裂纹一般在高温时形成,锻造变形时由于裂纹扩大并接触空气,故在100X或500X 的显微镜下观察,可见到裂纹内充有氧化皮,且两侧是脱碳的,组织为铁素体,其特征是裂纹比较粗壮且一般经多条形式存在,无明细尖端,比较圆纯,无明细的方向性,除以上典型外,有时会出现有些锻造裂纹比较细。
裂纹周围不是全脱碳而是半脱碳。
淬火加热过程中产生的裂纹与锻造加热过程形成的裂纹在性质和上有明显的差别。
对结构钢而言,热处理温度一般较锻造温度要低得多,即使是高速钢、高合金钢其加热保温时间则远远小于锻造温度。
由于热处理加热温度偏高,保温时间过长或快速加热,均会在加热过程中产生早期开裂。
产生沿着较粗大晶粒边界分布的裂纹;裂纹两侧略有脱碳组织,零件加热速度过快,也会产生早期开裂,这种裂纹两侧无明显脱碳,但裂纹内及其尾部充有氧化皮。
有时因高温仪器失灵,温度非常高,致使零件的组织极粗大,其裂纹沿粗大晶粒边界分布。
结构钢常见的缺陷:1 锻造缺陷(1)过热、过烧:主要特征是晶粒粗大,有明显的魏氏组织。
出现过烧说明加热温度高、断口晶粒粗大,凹凸不平,无金属光泽,晶界周围有氧化脱碳现象。
(2)锻造裂纹:常产生于组织粗大,应力集中处或合金元素偏析处,裂纹内部常充满氧化皮。
锻造温度高,或者终端温度低,都容易产生裂纹。
还有一种裂纹是锻造后喷水冷却后形成的。
(3)折叠:冲孔、切料、刀板磨损、锻造粗糙等原因造成了表面缺陷,在后续锻造时,将表面氧化皮等缺陷卷入锻件本体内而形成折缝。
在显微镜上观察时,可发现折叠周围有明显脱碳。
2 热处理缺陷(1)淬裂:其特点是刚健挺直,呈穿晶分布,起始点较宽,尾部细长曲折。
此种裂纹多产生于马氏体转变之后,故裂纹周围的显微组织与其它区域无明显区别,也无脱碳现象。
(2)过热:显微组织粗大,如果是轻度过热,可采用二次淬火来挽救。
(3)过烧:除晶粒粗大外,部分晶粒已趋于熔化,晶界极粗。
(4)软点:显微组织有块状或网状屈氏体和未溶铁素体等。
锻造和热处理过程中裂纹形成原因分析

Internal Combustion Engine&Parts0引言在进行锻造与热处理的过程中,裂纹的出现是很常见的事情,在所有的锻造与热处理的过程中,不可能不出现裂纹。
这就让裂纹在锻造这个行业中成为了一种讨论的焦点。
构件的尺寸大小,材质质地的不同,裂纹的出现几率也不同,裂纹的出现种类不同,裂纹出现的形状不同。
在本文中主要进行锻造和热处理过程中产生裂纹的原因进行研究。
在本文中通过大量对资料的收集进行了产生裂纹原因的阐述,也进行了防止裂纹产生举措的提出,对于减少构件在锻造和热处理的过程中出现裂纹带来了很大的帮助。
1锻造缺陷与热处理缺陷1.1过热、过烧主要特征是晶粒粗大,有明显的魏氏组织。
出现过烧说明加热温度高、断口晶粒粗大,凹凸不平,无金属光泽,晶界周围有氧化脱碳现象。
1.2锻造裂纹常产生于组织粗大,应力集中处或合金元素偏析处,裂纹内部常充满氧化皮。
锻造温度高,或者终端温度低,都容易产生裂纹。
还有一种裂纹是锻造后喷水冷却后形成的。
1.3折叠冲孔、切料、刀板磨损、锻造粗糙等原因造成了表面缺陷,在后续锻造时,将表面氧化皮等缺陷卷入锻件本体内而形成折缝。
在显微镜上观察时,可发现折叠周围有明显脱碳。
1.4淬裂其特点是刚健挺直,呈穿晶分布,起始点较宽,尾部细长曲折。
此种裂纹多产生于马氏体转变之后,故裂纹周围的显微组织与其它区域无明显区别,也无脱碳现象。
1.5软点显微组织有块状或网状屈氏体和未溶铁素体等。
加热不足,保温时间不够,冷却不均匀都会产生软点。
2实验方法在本文中的实验,采取了对锻造和热处理出现的裂纹范围划定。
在裂纹出现的范围内,采取裂纹邻近部位的显微组织,利用仪器进行晶相分析。
这样的实验方式可以让裂纹形成的内在原因通过机器进行分析,以数据的方式来进行裂缝产生原因的表述,这样的数据也是对裂纹进行鉴别的重要的依据。
在本次的实验中,采取了杆类件作为本次实验的研究对象,在采取裂纹附近部位的显微组织进行晶相分析。
锻件常见缺陷裂纹的原因

锻件常见缺陷裂纹的原因锻件常见缺陷裂纹的原因有很多,主要包括以下几个方面:1. 锻造前材料的缺陷:锻造前原材料中可能存在着各种缺陷,如夹杂物、气孔、夹渣等。
这些缺陷会在锻造过程中被拉长、扭曲或剪切,最终导致锻件出现裂纹。
2. 异常冷却方式:锻件在冷却过程中,如果冷却速度过快或不均匀,会导致锻件内部产生应力集中,从而引发裂纹。
尤其是在大尺寸、复杂形状的锻件中,由于其冷却速度不均匀,容易出现内部裂纹。
3. 冷、热变形不均匀:锻造过程中,如果材料的冷、热变形不均匀,会导致锻件内部应力分布不均匀,从而引发裂纹的产生。
尤其是在复杂形状、壁厚不一的锻件中,易出现材料贫化、过冷区和高应力区,容易引发裂纹。
4. 锻造温度过低或过高:锻造温度是影响锻件质量的关键因素之一。
如果温度过低,会导致材料的硬化能力不足,易发生塑性变形困难,从而引发裂纹;而温度过高,则会导致材料的焊接性能下降,也容易引发裂纹。
5. 压力不均匀:锻造过程中,如果锻压力不均匀,会使锻件中的应力分布不均匀,从而容易产生应力集中和裂纹。
尤其是在薄壁锻件中,容易出现锻压力不均匀的问题,导致裂纹的发生。
6. 锻件设计不合理:锻件的设计是影响锻件质量的重要因素之一。
如果锻件的形状、结构设计不合理,容易导致应力集中,从而引发裂纹的产生。
尤其是在复杂形状、尺寸大的锻件中,设计不合理会增加裂纹发生的概率。
7. 热处理不当:热处理是锻件制造过程中的关键环节,如果热处理不当,会导致锻件中的应力不释放或释放不充分,从而引发裂纹。
此外,热处理时的温度、时间等参数也需要合适,否则也可能导致裂纹的产生。
这些都是导致锻件常见缺陷裂纹的主要原因。
为了降低或避免裂纹的产生,需要从原材料选用、工艺控制、设备维护等方面做好控制和管理。
同时,制定合理的锻造工艺和热处理工艺,合理设计锻件形状和结构,对裂纹的产生起到有力的控制和避免作用。
还需要加强工作人员的培训和技能提升,提高他们的专业水平和质量意识,从而减少裂纹缺陷的发生,提高锻件的质量。
1Cr13钢锻裂原因分析

1Cr13钢锻裂原因分析1Cr13主要用于韧性要求较高具有不锈性的受冲击载荷的部件,如叶片、紧固件、阀门、热裂解设备备件等,也可用于常温下耐弱介质腐蚀的一些设备。
某厂经常生产轮盘用1Cr13钢锻件。
锻造过程中经常出现开裂的情况,开裂往往在钢锭拔长阶段就已出现,随着锻造的进行,裂纹迅速扩展。
采取退火后清理及车床加工去除裂纹再重新加热锻造的生产工艺路线,严重影响了产品制造成本和生产周期,裂纹废品时有发生。
为弄清1Cr13钢锻裂原因,从金相组织和生产实际等方面对该钢进行了广泛的研究。
1、化学成分1Cr13的化学成分如表1:(GB1220-92)C Si Mn Cr S P≤0.15≤1.00≤1.0011.5 –13.5 ≤0.035≤0.0352、铬不锈钢的相图从金相组织划分,1Cr13钢属于半马氏体钢,在常温下是铁素体和马氏体的混合组织。
从Fe-Cr-C 合金相图分析,在高温下(热加工温度)也存在α相(铁素体)和γ相(奥氏体)组织。
在两相共存区进行热加工时容易出现由于两相的变形率不同,造成应力集中,导致铁素体相晶界断裂。
因此,1Cr13钢由于成分设计的原因,使该钢很容易发生锻造开裂。
3、1Cr13钢高温塑性从塑性图上看,在1000及1100℃时,断面收缩率下降,而在1200℃则又重新升高。
结合相图分析,1000和1100℃断面收缩率所以降低,是因为在这一温度区域内,组织是由两相组成的。
两相的变形率不同,造成应力集中,导致铁素体相晶界断裂,表现为断面收缩率降低。
高温塑性实验证实1Cr13钢塑性降低是由于两相共存造成的。
4、提高1Cr13钢锻造塑性的途径已知1Cr13钢锻造塑性的降低主要是由于两相共存造成的,因此从消除两相共存入手行分析。
从图1(Fe-Cr-C相图)分析,有α、γ、δ三个单相区。
定性的分析,很低的C%含量(小于0.08%)高温时(大于1200℃)为δ单相区(高温铁素体)、低温时(小于1000℃)为α单相区(低温铁素体),较高的C%含量(大于0.15)在锻造温度区(1200-900℃)为γ单相区(奥氏体)。
0 Cr17 Ni4 Cu4 Nb钢锻造裂纹分析与控制
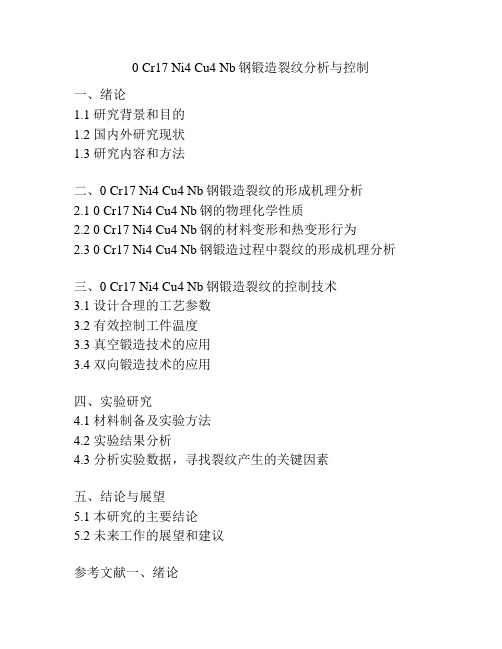
0 Cr17 Ni4 Cu4 Nb钢锻造裂纹分析与控制一、绪论1.1 研究背景和目的1.2 国内外研究现状1.3 研究内容和方法二、0 Cr17 Ni4 Cu4 Nb钢锻造裂纹的形成机理分析2.1 0 Cr17 Ni4 Cu4 Nb钢的物理化学性质2.2 0 Cr17 Ni4 Cu4 Nb钢的材料变形和热变形行为2.3 0 Cr17 Ni4 Cu4 Nb钢锻造过程中裂纹的形成机理分析三、0 Cr17 Ni4 Cu4 Nb钢锻造裂纹的控制技术3.1 设计合理的工艺参数3.2 有效控制工件温度3.3 真空锻造技术的应用3.4 双向锻造技术的应用四、实验研究4.1 材料制备及实验方法4.2 实验结果分析4.3 分析实验数据,寻找裂纹产生的关键因素五、结论与展望5.1 本研究的主要结论5.2 未来工作的展望和建议参考文献一、绪论在制造行业中,锻造是一种重要的金属成形加工方法,它可以将金属坯料加工成不同形状的零部件,具有高强度、高可靠性等优点。
0 Cr17 Ni4 Cu4 Nb钢是一种常用的合金钢,在航空航天、核工业等领域有着广泛的应用。
然而,在0 Cr17 Ni4Cu4 Nb钢锻造过程中,经常出现裂纹的问题,导致加工效率低下,成本增加等问题。
因此,本文通过对0 Cr17 Ni4 Cu4 Nb钢锻造过程中裂纹形成机理的分析与控制技术的研究,旨在提高锻造效率、降低成本,改善成品质量,从而为锻造行业的发展做出贡献。
1.1 研究背景和目的锻造作为一种重要的金属成形加工方法,其加工效率和成品质量的好坏直接影响着整个制造行业的发展。
0 Cr17 Ni4 Cu4 Nb 钢是一种常用的合金钢,其在航空、核工业等领域有着广泛应用。
然而在0 Cr17 Ni4 Cu4 Nb钢锻造过程中,经常会出现裂纹的问题,这会导致加工效率低下,成本增加,甚至严重影响产品的使用寿命。
因此,研究0 Cr17 Ni4 Cu4 Nb钢锻造过程中裂纹的形成机理和控制技术,对于提高加工效率,降低成本,改善成品质量有着重要的意义。
淬火裂纹、锻造裂纹的特性及区别

淬火裂纹、锻造裂纹的特性及区别一、材料方面1、碳是影响淬裂倾向的一个重要因素。
碳含量提高,MS点降低,淬裂倾向增大。
因此,在满足基本性能如硬度、强度的条件下,应尽量选用较低的碳含量,以保证不易淬裂。
2、合金元素对淬裂倾向的影响主要体现在对淬透性、MS点,晶l度长大倾向、脱碳的影响上。
合金元素通过对淬透性的影响,从而影响到淬裂倾向。
一般来说,淬透性增加,淬裂性增加,但淬透性增加的同时,却可以使用冷却能力弱的淬火介质以减少淬火变形的方法来防止复杂零件的变形与裂纹。
因此,对于形状复杂的零件,为了避免淬火裂纹,选择透性好的钢,并用冷却能力弱的淬火介质是一个较好的方案。
合金元素对MS点影响较大,一般来说,MS越低的钢,淬裂倾向越大,当MS点高时,相变生成的马氏体可能立刻被自回火,从而消除一部分相变应力,可以避免发生淬裂。
因此,当碳含量确定后,应用少量的合金元素,或者含对MS点影响较小的元素的钢种。
3、选择钢材时,应考虑过热敏感性。
过热较敏感的钢,容易产生裂纹,所以在选择材料时应引起重视。
二、零件的结构设计1、断面尺寸均匀。
断面尺寸急剧变化的零件,在热处理时由于产生内应力而产生裂纹。
故设计时尽量避免断面尺寸突变。
壁厚要均匀。
必要时可在与用途无直接关系的厚壁部位开孔。
孔应尽量做成通孔。
对于厚不同的零件,可进行分体设计,待热处理后,再进行组装。
2、圆角过渡。
当零件有棱角、尖角、沟槽和横孔时,这些部位很容易产生应力集中,从而导致零件淬裂。
为此,零件应尽量设计成不发生应力集中的形状,在尖角处和台阶处加工成圆角。
3、形状因素造成的冷却速度差异。
零件淬火时冷却速度的快、慢随零件形状的不同而不同。
即使在同一零件上不同的部位,也会因各种因素而造成蝗此俣鹊牟煌。
因此要尽量避免过大的冷却差异,以防止淬火裂纹。
三、热处理技术条件1、尽量采用局部淬火或表面硬化。
2、根据零件服役条件需要,合理调整淬火件局部硬度。
局部淬火硬度要求较低时,尽量不强求整体硬度一致。
锻造裂纹分析

锻造裂纹钢在锻造过程中形成的裂纹是多种多样的,形成原因也各不相同。
主要可分为原材料缺陷引起的锻造裂纹和锻造本身引起锻造裂纹两类。
属于前者的原因有残余缩孔、钢中夹杂物等冶金缺陷;属于后者的原因有加热不当、变形不当及锻后冷却不当、未及时热处理等。
有些情况下裂纹的产生可能同时含有几方面的原因。
锻造变形不当常引起裂纹。
最常见的是变形速度太大,钢的塑性不足以承受形压力而引起的破裂。
这种裂纹往往在锻造开始阶段就发生,并迅速扩展。
应及时采取措施纠正锻造工艺,并切除有裂纹的钢材或报废锻件。
另外一种是低温锻裂,在裂纹处往往有较多的低温相组织。
为避免这种裂纹产生,应使钢在锻造变形过程中不发生相变,要正确掌握和控制终锻温度。
鉴别裂纹形成的原因,应首先了解工艺过程,以便找出裂纹形成的客观条件,其次应当观察裂纹本身的状态,然后再进行必要的有针对性的显微组织分析,微区成分分析。
举例如下:对于产生龟裂的锻件,粗略分析可能是:①由于过烧;②由于易溶金属渗入基体金属(如铜渗人钢中);③应力腐蚀裂纹;④锻件表面严重脱碳。
这可以从工艺过程调查和组织分析中进一步判别。
例如在加热钢以后加热钢料或两者混合加热或钢中含铜量过高时,则有可能是铜脆。
从显微组织上看,铜脆开裂在晶界,除了能找到裂纹外,还能找到亮的铜网,而在单纯过烧的晶界只能找到氧化物。
应力腐蚀开裂是在酸洗后出现,在高倍观察时,裂纹的扩展呈树枝状形态。
锻件严重脱碳时,在试片上可以观察到一层较厚的脱碳层。
裂纹与折叠的鉴别,不仅可以从受力及变形的条件考察,亦可以低倍和高倍组织来区分。
一般裂纹与流线成一定交角,而折叠附近的流线与折叠方向平行,而且对于中、高碳钢来说,折叠表面有氧化脱碳现象。
折叠的尾部一般呈圆角,而裂纹通常是尖的。
具有裂纹的锻件经加热后,裂纹附近有严重的氧化脱碳,冷却裂纹则无此现象。
由缩管残余引起的裂纹通常是粗大而不规则的。
由冷校正及冷切边引起的裂纹,在裂纹的周围有滑移带等冷变形痕迹。
第四节:锻造裂纹

第四节锻造裂纹
因锻造工艺不当或在锻造过程中产生的裂纹都可以列入锻造裂纹。
一内部裂纹
1 锻造不当引起的内部裂纹
因锻造方法不当在锻造内部引起的裂纹容易产
生在加工温度过低或一次变形量过大以及加工过程中工件载面形状不当等情况下产生的内部裂纹。
图4-1表示加工过程中截面形状不当时内裂的形成机理。
由方料自由锻造成园棒时,如果采用A的方法不会引起内裂;但若用B方法就会使钢材内部产生剪切应力,而导致内裂。
图4-2为锻件心部的锻造裂纹。
图4-1 自由锻造内裂形成机理
图4-2 锻件心部的锻造裂纹
2 内应力引起的内部裂纹
这种裂纹主要产生在工件加热较快时,由于表面和心部之间存在较大的温差,表面的膨胀大于中心的膨胀,从而在中心部分形成较大的拉应力,这种应力和坯料原有的残余应力的共同作用,导致内部横裂。
3 缩孔残余引起的内裂纹
铸件缩孔未切干净,冒口切除不足,在锻造时产生裂纹。
二其它形式的裂纹
1 爆裂:由于错误地采用快速加热或因冷却不当残余应力过高引起的。
2 烧裂:主要是钢锭在加热过程中由于温度过高或在高温时停留时间过长发生过烧造成的。
3 纵裂:由于热加工后冷却不当或冷却过快,产生较大的内应力造成的。
4 表面裂纹:它是在钢材表面出现短细的纵向裂纹,主要是轧制后冷却不当,没有及时退火处理,它多发生在高碳钢和高合金钢中。
图4-3为锻造时易出现的几种裂纹形式。
图4-3 锻造时易出现的几种裂纹。
锻造开裂原因

锻造开裂原因
锻造开裂的原因可能有多种,以下是一些主要原因:
1. 原材料质量问题:原材料中可能存在的毛细裂纹、折叠、非金属夹杂物过多、碳化物偏析、异金属夹杂物、气泡、柱状晶体粗大、轴心晶间裂纹、粗晶环等缺陷,在锻造工序都可能引发锻造裂纹。
2. 锻造工艺不当:在锻造过程中,如果下料、加热、锻压、冷却及清理等环节出现不当操作,也可能导致锻件开裂。
3. 温度控制不当:在加热和冷却过程中,如果温度控制不当,可能导致材料内部应力过大,从而引发开裂。
4. 材料应力集中:如果锻件存在应力集中区域,如尖角、截面突变处,在应力超过材料承受能力时,可能导致开裂。
5. 锻造变形不当:如果变形速度太大,钢的塑性不足以承受形压力而引起的破裂。
6. 淬火裂纹:淬火裂纹往往是在马氏体转变开始进行后不久产生的,裂纹的分布则没有一定的规律,但一般轻易在工件的尖角、截面突变处形成。
大型钢锭锻造过程中裂纹原因分析

大型钢锭锻造过程中裂纹原因分析摘要:大型钢锭锻造过程中发生纵裂,对裂纹部位取样进行检测,对导致夹渣的原因进行分析,同时对可能对钢锭锻造产生裂纹的各种原因进行了分析。
关键词:钢锭;裂纹;夹渣钢锭锻造时产生裂纹与冶炼、加热、锻造有关。
虽然钢锭的裂纹有众多因素,但可归咎为两大原因,一是材料自身的内部缺陷;二是加热和锻造中产生的有害拉应力。
应力状态、变形温度和变形速度是裂纹产生和扩展的外部条件,钢锭组织结构、冶金质量是裂纹产生和扩展的内部依据。
1、钢锭裂纹及检测材质50Cr3MoV、重量55吨钢锭,镦粗时锭身中部有多处纵裂纹如下图1、2。
在钢锭裂纹开口处切一块下来,中间剖开做金相检测,发现有多处夹渣,如图3。
对试样抛光后的异常处进行电镜分析,如图4。
从裂纹处金相检测看,夹渣数量较多且尺寸较大,能谱检测夹渣成分看,夹渣中Fe、Si、Cr、Mn、和O含量较高,应为FeO、(FeMn)O、Cr2O3 、SiO2、类夹渣。
从检测分析看,产生裂纹的钢锭中存在的并非为内生的夹杂物,而是较大的外来夹渣,分析认为应该是浇注过程的某个环节带入了钢中,并且在浇注过程中无法上浮到冒口。
2、钢锭锻造裂纹产生原因分析2.1钢中第二相组织影响钢中第二相的力学性能往往和金属基体有很大的差别,因而在变形流动时会引起附加应力导致整体工艺塑性下降,一旦局部应力超过异相与基体间结合力时,则发生分离形成孔洞。
例如钢中的氧化物、氮化物、碳化物、硼化物、硫化物、硅酸盐等等。
假如这些相呈密集、链状分布,尤其在沿晶界结合力薄弱处存在,高温锻压就会开裂。
2.2大型夹杂物影响分布在钢锭表层的大型夹杂物是钢锭表面缺陷和加工时产生裂纹的重要原因。
分布在下部的大型夹杂物难于发现和消除,往往使产品报废。
钢锭中大型非金属夹杂的数量及分布决定于钢液中的夹杂物数量及其被凝固钢捕获的几率,后者则主要决定于钢液中夹杂物的上浮速度与钢液结晶速度的比值。
由于钢锭表层快速结晶,使接近模壁的钢液中的夹杂物来不及上浮而易被凝固壳捕获。
某产品零件导气箍锻造裂纹问题分析

析, 结果 如 下所述 。
1 )材 料牌 号 5 Z 化 学 成 分符 合 G B 2 2 —4 0 , J 7 09
规定 。
程上分 析 , 纹产 生 只 可 能 出现 在 锻造 和热 处 理 等 裂
2 工序 上 。从 开 裂 件 的 理 化 分 析看 , 裂 部 位 均 个 开 出现在 锻造 分模 面处 , 且裂 纹处存 在 大量氧 化物 , 第 2件尤其 明 显 。第 1 由于 裂纹 起 源处 受 到火 药气 件
C H E N iyo X — u
( iia y Re e e a i fc n N o 5 Plnt , M lt r pr s nt tve Ofie i .1 2 a Cho qig 4 ng n 011 0,Chi ) 2 na
Absr c :T h p r it o c s t e a l i orr a o fc a ks o asc i e a k t whih i c us he f r i g ta t e pa e n r du e h nayssf e s n o r c n g yl nd r br c e , c s be a eoft o g n
d fce c .Th sd f in y i c mmo n n v ia l .Th a e n r d c sa s l t n i ih mi r c a k r e v d b eiin y i e i e c s o c n a d u a o d be e p p ri to u e o u i n whc c o r c sa e r mo e y o s o h n n n h a t t r c s a e pc e u y d t c i n mo t e i g a d t e p r swi c a k r ik d O tb ee t ,wh c s p o e fe t et r u h p a tc la p ia i n h o ih i r v d e fc i h o g r cia p l to . v c
锻造和热处理过程中裂纹形成原因分析

锻造和热处理过程中裂纹形成原因分析发布时间:2021-05-20T10:33:30.803Z 来源:《基层建设》2020年第31期作者:裴一飞[导读] 摘要:裂缝很常见,生产过程往往是锻造和热处理过程。
航空工业哈尔滨飞机工业集团有限公司黑龙江哈尔滨 150000摘要:裂缝很常见,生产过程往往是锻造和热处理过程。
锻造裂纹通常在高温下发生,在锻造过程中会延伸并接触空气,形成裂纹中氧化的皮肤。
此框形成的裂纹不仅厚而且多,裂纹的两端不相连,尖端相对圆。
所处理的裂纹的形状和性能与锻造裂纹不同。
出现热处理后的裂纹是因为加热时该元素出现裂纹,导致在裂纹的咸晶方向上脱碳,最终结构比锻造裂纹厚。
对于和零件尤其如此本文收集了大量裂缝方式,分析总结了裂缝的原因。
最后,裂缝分为三类。
关键词:锻造、热处理;裂纹形成原因;过程;存在缺陷;前言裂纹是锻造和热处理中常见的缺陷之一,也是锻造行业中的热点和难点。
但是,锻造零件产生裂纹的可能性很大,因此必须研究锻造和热处理过程中的裂纹,并分析裂纹的原因。
一、锻造缺陷与热处理缺陷过热燃烧。
过度燃烧意味着加热温度高,切割机又大又不均匀,没有金属光泽,玻璃周围有氧化和渗碳。
造成裂缝。
当锻造温度较高或最终温度较低时,容易产生裂纹。
另一个裂缝是在水的钻井和冷却后形成的。
缩小范围。
表面缺陷是冲压、切割、板材磨损、穿孔等造成的。
在随后的钻孔中,观察到锻造体中存在表面氧化等缺陷以形成折弯。
通过显微镜观察,你可以看到弯曲周围明显的碳流失。
过火裂缝。
这些裂缝大多发生在MCU改造后,因此裂缝周围的微观结构与其他区域没有显着差异,也没有渗碳。
二、实验方法1.试样制备和宏观观察在试验前的第一阶段,只需对所选杆的工件裂纹进行宏观观察,在观察过程中,选择要测量的区域。
下一步是手动剪切选定区域,使其垂直于镜像且长度小于10 mm。
采样方法可能会有所不同,但在采样时必须选择温度和环境。
如果样品温度过高,可以使用冷水冷却样品,以免由于样品在回收过程中过热而改变事件的内部组织。
锻造常见缺陷及原因
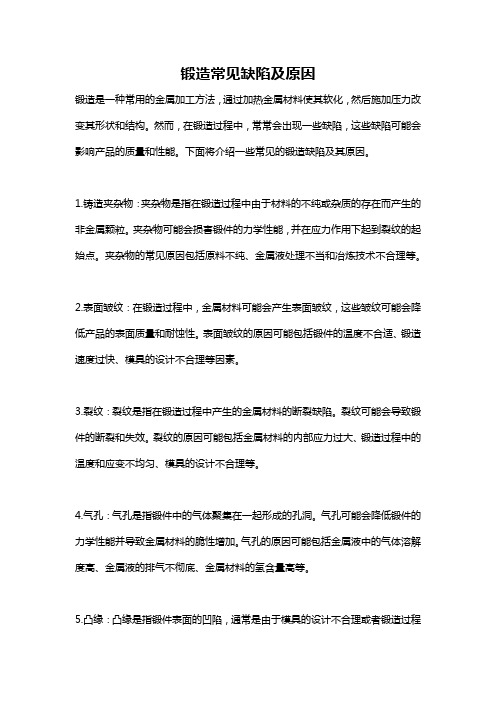
锻造常见缺陷及原因锻造是一种常用的金属加工方法,通过加热金属材料使其软化,然后施加压力改变其形状和结构。
然而,在锻造过程中,常常会出现一些缺陷,这些缺陷可能会影响产品的质量和性能。
下面将介绍一些常见的锻造缺陷及其原因。
1.铸造夹杂物:夹杂物是指在锻造过程中由于材料的不纯或杂质的存在而产生的非金属颗粒。
夹杂物可能会损害锻件的力学性能,并在应力作用下起到裂纹的起始点。
夹杂物的常见原因包括原料不纯、金属液处理不当和冶炼技术不合理等。
2.表面皱纹:在锻造过程中,金属材料可能会产生表面皱纹,这些皱纹可能会降低产品的表面质量和耐蚀性。
表面皱纹的原因可能包括锻件的温度不合适、锻造速度过快、模具的设计不合理等因素。
3.裂纹:裂纹是指在锻造过程中产生的金属材料的断裂缺陷。
裂纹可能会导致锻件的断裂和失效。
裂纹的原因可能包括金属材料的内部应力过大、锻造过程中的温度和应变不均匀、模具的设计不合理等。
4.气孔:气孔是指锻件中的气体聚集在一起形成的孔洞。
气孔可能会降低锻件的力学性能并导致金属材料的脆性增加。
气孔的原因可能包括金属液中的气体溶解度高、金属液的排气不彻底、金属材料的氢含量高等。
5.凸缘:凸缘是指锻件表面的凹陷,通常是由于模具的设计不合理或者锻造过程中的卡位不良而引起的。
凸缘会降低锻造件的密封性和耐蚀性。
6.尺寸偏差:尺寸偏差是指锻造件的实际尺寸与设计尺寸之间的差异。
尺寸偏差可能会影响锻件的装配和使用,降低产品的功能性。
尺寸偏差的原因可能包括模具的磨损、材料的收缩率不均匀、锻造机床的精度不高等。
以上是一些常见的锻造缺陷及其原因。
为了避免这些缺陷的出现,可以通过优化锻造过程,提高金属材料的质量,改进模具设计和锻造工艺等手段来减少缺陷的发生。
同时,对于已经出现的缺陷,可以通过修复和加工的方法来消除或者修复。
锻造表面裂纹的特征

锻造表面裂纹是指在金属材料经过锻造工艺后,出现在表面的裂纹。
这些裂纹在锻造过程中可能由于多种因素引起,如材料本身的问题、锻造工艺参数不当、工艺操作不当等。
锻造表面裂纹的特征可以包括以下几个方面:
1.形态:锻造表面裂纹通常呈线状,沿着材料表面延伸。
其长度、宽度和深度可以有所不同,取决于裂纹的产生原因和锻造条件。
2.分布:锻造表面裂纹通常不是均匀分布的,而是局部集中在某些区域。
这些区域可能是材料的薄弱区、变形不均匀区、工艺操作不当的区域等。
3.方向:锻造表面裂纹的方向可以有多种可能,取决于锻造过程中的应力分布和局部变形情况。
通常可以沿着材料的纵向、横向或斜向分布。
4.长度和宽度差异:锻造表面裂纹的长度和宽度可能会有一定的差异。
有些裂纹可能很短而浅,只在表面形成微小的开裂;而有些裂纹可能会更长、更深,并且可能会产生分叉。
5.表面变色和变形:由于裂纹的存在,锻造表面周围的金属可能出现颜色变化,如发黑、氧化等。
此外,裂纹周围的金属也可能出现变形或破坏的痕迹。
在实际生产中,及时发现并处理锻造表面裂纹非常重要。
对于成品产品,裂纹的存在可能会降低材料的强度和耐久性,甚至会导致产品的失效。
因此,在锻造过程中应严格控制工艺参数,确保材料的质量和工艺操作的正确性。
此外,质量检查和非破坏性检测等方法也可以用来检测和评估锻造表面裂纹的存在。
- 1、下载文档前请自行甄别文档内容的完整性,平台不提供额外的编辑、内容补充、找答案等附加服务。
- 2、"仅部分预览"的文档,不可在线预览部分如存在完整性等问题,可反馈申请退款(可完整预览的文档不适用该条件!)。
- 3、如文档侵犯您的权益,请联系客服反馈,我们会尽快为您处理(人工客服工作时间:9:00-18:30)。
锻造裂纹
钢在锻造过程中形成的裂纹是多种多样的,形成原因也各不相同。
主要可分为原材料缺陷引起的锻造裂纹和锻造本身引起锻造裂纹两类。
属于前者的原因有残余缩孔、钢中夹杂物等冶金缺陷;属于后者的原因有加热不当、变形不当及锻后冷却不当、未及时热处理等。
有些情况下裂纹的产生可能同时含有几方面的原因。
锻造变形不当常引起裂纹。
最常见的是变形速度太大,钢的塑性不足以承受形压力而引起的破裂。
这种裂纹往往在锻造开始阶段就发生,并迅速扩展。
应及时采取措施纠正锻造工艺,并切除有裂纹的钢材或报废锻件。
另外一种是低温锻裂,在裂纹处往往有较多的低温相组织。
为避免这种裂纹产生,应使钢在锻造变形过程中不发生相变,要正确掌握和控制终锻温度。
鉴别裂纹形成的原因,应首先了解工艺过程,以便找出裂纹形成的客观条件,其次应当观察裂纹本身的状态,然后再进行必要的有针对性的显微组织分析,微
区成分分析。
举例如下:
对于产生龟裂的锻件,粗略分析可能是:①由于过烧;②由于易溶金属渗入基体金属(如铜渗人钢中);③应力腐蚀裂纹;④锻件表面严重脱碳。
这可以从工艺过程调查和组织分析中进一步判别。
例如在加热钢以后加热钢料或两者混合加热或钢中含铜量过高时,则有可能是铜脆。
从显微组织上看,铜脆开裂在晶界,除了能找到裂纹外,还能找到亮的铜网,而在单纯过烧的晶界只能找到氧化物。
应力腐蚀开裂是在酸洗后出现,在高倍观察时,裂纹的扩展呈树枝状形态。
锻件严重脱碳时,在试片上可以观察到一层较厚的脱碳层。
裂纹与折叠的鉴别,不仅可以从受力及变形的条件考察,亦可以低倍和高倍组织来区分。
一般裂纹与流线成一定交角,而折叠附近的流线与折叠方向平行,而且对于中、高碳钢来说,折叠表面有氧化脱碳现象。
折叠的尾部一般呈圆角,
而裂纹通常是尖的。
具有裂纹的锻件经加热后,裂纹附近有严重的氧化脱碳,冷却裂纹则无此现
象。
由缩管残余引起的裂纹通常是粗大而不规则的。
由冷校正及冷切边引起的裂纹,在裂纹的周围有滑移带等冷变形痕迹。
锻造工艺不当常产生的缺陷
类型:其它点击次数:1423
锻造工艺不当产生的缺陷通常有以下几种
1.大晶粒
大晶粒通常是由于始锻温度过高和变形程度不足、或终锻温度过高、或变形程度落人临界变形区引起的。
铝合金变形程度过大,形成织构;高温合金变形温度过低,形成混合变形组织时也可能引起粗大晶粒,晶粒粗大将使锻件的塑性和韧性降低,疲劳性能明显下降。
2.晶粒不均匀
晶粒不均匀是指锻件某些部位的晶粒特别粗大,某些部位却较小。
产生晶粒不均匀的主要原因是坯料各处的变形不均匀使晶粒破碎程度不一,或局部区域的变形程度落人临界变形区,或高温合金局部加工硬化,或淬火加热时局部晶粒粗大。
耐热钢及高温合金对晶粒不均匀特别敏感。
晶粒不均匀将使锻件的持久性能、疲劳性能明显下降。
3.冷硬现象
变形时由于温度偏低或变形速度太快,以及锻后冷却过快,均可能使再结晶引起的软化跟不上变形引起的强化(硬化),从而使热锻后锻件内部仍部分保留冷变形组织。
这种组织的存在提高了锻件的强度和硬度,但降低了塑性和韧性。
严重的冷硬现象可能引起锻裂。
4.裂纹
裂纹通常是锻造时存在较大的拉应力、切应力或附加拉应力引起的。
裂纹发生的部位通常是在坯料应力最大、厚度最薄的部位。
如果坯料表面和内部有微裂纹、或坯料内存在组织缺陷,或热加工温度不当使材料塑性降低,或变形速度过快、变形程度过大,超过材料允许的塑性指针等,则在撤粗、拔长、冲孔、扩孔、弯曲和挤压等工序中都可能产生裂纹。
5.龟裂
龟裂是在锻件表面呈现较浅的龟状裂纹。
在锻件成形中受拉应力的表面(例如,未充满的凸出部分或受弯曲的部分)最容易产生这种缺陷。
引起龟裂的内因可能是多方面的:①原材料合Cu、Sn等易熔元素过多。
②高温长时间加热时,钢料表面有铜析出、表面晶粒粗大、脱碳、或经过多次加热的表面。
③燃料含硫量过高,有硫渗人钢料表面。
6.飞边裂纹
飞边裂纹是模锻及切边时在分模面处产生的裂纹。
飞边裂纹产生的原因可能是:①在模锻操作中由于重击使金属强烈流动产生穿筋现象。
②镁合金模锻件切边温度过低;铜合金模锻件切边温度过高。
7.分模面裂纹
分模面裂纹是指沿锻件分模面产生的裂纹。
原材料非金属夹杂多,模锻时向分模面流动与集中或缩管残余在模锻时挤人飞边后常形成分模面裂纹。
8.折叠
折叠是金属变形过程中已氧化过的表层金属汇合到一起而形成的。
它可以是由两
股(或多股)金属对流汇合而形成;也可以是由一股金属的急速大量流动将邻近部分的表层金属带着流动,两者汇合而形成的;也可以是由于变形金属发生弯曲、回流而形成;还可以是部分金属局部变形,被压人另一部分金属内而形成。
折叠与原材料和坯料的形状、模具的设计、成形工序的安排、润滑情况及锻造的实际操作有关。
折叠不仅减少了零件的承载面积,而且工作时由于此处的应力集中往往成为疲劳源。
9.穿流
穿流是流线分布不当的一种形式。
在穿流区,原先成一定角度分布的流线汇合在一起形成穿流,并可能使穿流区内、外的晶粒大小相差较为悬殊。
穿流产生的原因与折叠相似,是由两股金属或一股金属带着另一股金属汇流而形成的,但穿流部分的金属仍是一整体,穿流使锻件的力学性能降低,尤其当穿流带两侧晶粒相差较悬殊时,性能降低较明显。
10.锻件流线分布不顺
锻件流线分布不顺是指在锻件低倍上发生流线切断、回流、涡流等流线紊乱现象。
如果模具设计不当或锻造方法选择不合理,预制毛坯流线紊乱;工人操作不当及模具磨损而使金属产生不均匀流动,都可以使锻件流线分布不顺。
流线不顺会使各种力学性能降低,因此对于重要锻件,都有流线分布的要求。
11.铸造组织残留
铸造组织残留主要出现在用铸锭作坯料的锻件中。
铸态组织主要残留在锻件的困难变形区。
锻造比不够和锻造方法不当是铸造组织残留产生的主要原因。
铸造组织残留会使锻件的性能下降,尤其是冲击韧度和疲劳性能。
12.碳化物偏析级别不符要求
碳化物偏析级别不符要求主要出现于莱氏体工模具钢中。
主要是锻件中的碳化物分布不均匀,呈大块状集中分布或呈网状分布。
造成这种缺陷的主要原因是原材料碳化物偏析级别差,加之改锻时锻比不够或锻造方法不当,具有这种缺陷的锻件,热处理淬火时容易局部过热和淬裂,制成的刃具和模具使用时易崩刃。
13.带状组织
带状组织是铁素体和珠光体、铁素体和奥氏体、铁素体和贝氏体以及铁素体和马氏体在锻件中呈带状分布的一种组织,它们多出现在亚共折钢、奥氏体钢和半马氏体钢中。
这种组织,是在两相共存的情况下锻造变形时产生的带状组织能降低材料的横向塑性指针,特别是冲击韧性。
在锻造或零件工作时常易沿铁素体带或两相的交界处开裂。
14.局部充填不足
局部充填不足主要发生在筋肋、凸角、转角、圆角部位,尺寸不符合图样要求。
产生的原因可能是:①锻造温度低,金属流动性差;②设备吨位不够或锤击力不足;③制坯模设计不合理,坯料体积或截面尺寸不合格;④模膛中堆积氧化皮或焊合变形金属。
15.欠压
欠压指垂直于分模面方向的尺寸普遍增大,产生的原因可能是:①锻造温度低。
②设备吨位不足,锤击力不足或锤击次数不足。
16.错移
错移是锻件沿分模面的上半部相对于下半部产生位移。
产生的原因可能是:①滑块(锤头)与导轨之间的间隙过大;②锻模设计不合理,缺少消除错移力的锁口或导柱;③模具安装不良。