锻造裂纹与热处理裂纹原理形态
锻件的层状断口

锻件的层状断口
锻件的层状断口是指在金属材料的拉伸、压缩或弯曲等力学加工过程中,材料发生断裂时,断口呈现出层状结构。
这种断口形貌类似于木材的剖面,由多条平行的层状裂缝组成。
锻件的层状断口形成的原因主要有以下几点:
1.金属材料在受到外力作用时,会在应力集中区域发生局部塑性变形。
当应力超过材料的屈服强度时,就会形成裂纹。
随着外力的继续作用,裂纹会逐渐扩展,形成层状断口。
2.金属材料的微观结构和组织也会影响层状断口的形成。
如果材料的结晶粒度较大,裂缝扩展路径较长,就容易形成层状断口。
3.材料的纯度、含气等也会影响层状断口的形成。
锻件的层状断口会导致钢的横向力学性能严重下降,特别是延伸率和断面收缩率。
这种层状断口在形变结构钢中经常出现,会显著降低钢的强度和韧性。
因此,在金属材料的加工过程中,应采取措施避免层状断口的形成,如优化加工工艺、控制材料纯度和组织结构等。
自由锻常见缺陷裂纹的原因

自由锻常见缺陷裂纹的原因自由锻是一种常见的金属加工工艺,通过利用金属的塑性变形特性来加工成型各种零部件。
然而,在实际的生产过程中,由于材料属性、加工工艺等原因,常常会出现各种缺陷,其中最常见的就是裂纹。
裂纹的出现不仅会影响零部件的质量和性能,还可能导致工件失效,因此及时发现并采取措施是非常重要的。
下面将从几个方面介绍自由锻常见缺陷裂纹的原因。
1. 材料因素材料的质量和性能对自由锻过程的裂纹形成起着重要的作用。
首先,原材料的杂质和非金属夹杂物会降低金属的塑性,增加金属的脆性,从而容易形成裂纹。
其次,金属的晶粒度和组织结构也会对裂纹的产生起到影响作用。
晶粒度过大或过小都会导致金属的塑性不足,从而容易出现裂纹。
此外,金属中的残余应力也是裂纹产生的一个重要因素,过大的残余应力会在加工过程中导致金属局部应力集中,进而形成裂纹。
2. 加工工艺因素自由锻的加工工艺对裂纹的形成有着直接的影响。
例如,锻造温度过高或过低都会影响金属的塑性,从而容易形成裂纹。
此外,锻造的速度、变形量等参数设置也会对裂纹的形成起到影响。
如果变形量过大或变形速度过快,可能使金属的应力超过其承载能力,导致裂纹的产生。
还有一些其他因素,比如锻造过程中的冷却速度、锻后的热处理工艺等也会对裂纹的形成产生影响。
3. 设计因素零部件的设计也是影响裂纹产生的因素之一。
不合理的结构设计、过于尖锐的转角或者挤压形状等都可能会导致金属在锻造过程中产生应力集中,从而形成裂纹。
因此,在设计零部件时,应该尽量避免设计过于尖锐的结构,合理控制转角和挤压形状,以减少应力集中点的产生。
4. 操作因素操作人员的技术水平和操作规范也会对裂纹的产生起到影响。
不合理的操作方法、过于急躁的操作、缺乏经验的操作人员等都有可能导致裂纹的产生。
因此,操作人员需要具备良好的技术水平和严格的操作规范,以避免不必要的裂纹产生。
5. 设备因素锻造设备的状态和性能也会对裂纹产生起到影响。
例如,设备的润滑状态不良、设备磨损严重、设备结构设计不合理等都有可能导致应力集中,从而形成裂纹。
主轴锻件裂纹原因分析研究
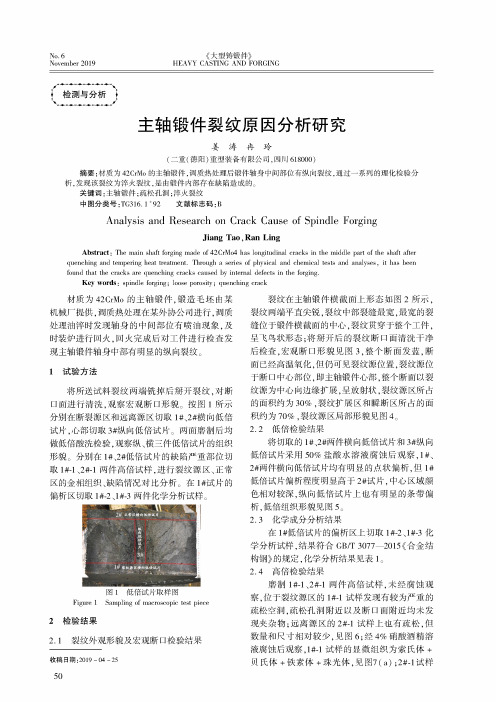
材质为42CrMo的主轴锻件,锻造毛坯由某 机械厂提供,调质热处理在某外协公司进行,调质 处理油淬时发现轴身的中间部位有喷油现象,及 时装炉进行回火,回火完成后对工件进行检查发 现主轴锻件轴身中部有明显的纵向裂纹。 1试验方法
图4宏观断口源区局部形貌
Fiaurc 4 Locci macroscopic morphology of fracture source roeion
(a) 1#横向试片
(b)2 •横向试片 图5低倍组织形貌 Fiauro 5 Macrostructure morphology
(c)3#纵向试片
表1主轴锻件的化学成分(质量分数,%) Table 1 Chemical compositiont of spindle forging
(a)1 #-l 试样
(b)2#-l 试样
图6高倍试样上的疏松空洞(50 X)
Fiauro 6 Loose porositr io microscopic specimens (50 X )
(a)1 #-l 试样 图7
Fiauro 7
(b)2#l1 试样 显微组织(500x) Microstructure ( 500 X )
(matt fraction, % )
试样1#-2 实测值
试样1#-2
C 0.43 0.42
Si 0.28 0.27
Mn P
S
Cr
0.66 0.020 0.025 1.06
0.65 0.019 0.026 1.08
Mo 0.20 0.19
标准要求值
锻造常见缺陷有哪些,你都知道吗?

锻造用的原材料为铸锭、轧材、挤材及锻坯。
而轧材、挤材及锻坯分别是铸锭经轧制、挤压及锻造加工成的半成品。
一般情况下,铸锭的内部缺陷或表面缺陷的出现有时是不可避免的。
再加上在锻造过程中锻造工艺的不当,最终导致锻件中含有缺陷。
以下简单介绍一些锻件中常见的缺陷。
由于原材料的缺陷造成的锻件缺陷通常有:表面裂纹表面裂纹多发生在轧制棒材和锻制棒材上,一般呈直线形状,和轧制或锻造的主变形方向一致。
造成这种缺陷的原因很多,例如钢锭内的皮下气泡在轧制时一面沿变形方向伸长,一面暴露到表面上和向内部深处发展。
又如在轧制时,坯料的表面如被划伤,冷却时将造成应力集中,从而可能沿划痕开裂等等。
这种裂纹若在锻造前不去掉,锻造时便可能扩展引起锻件裂纹。
折叠折叠形成的原因是当金属坯料在轧制过程中,由于轧辊上的型槽定径不正确,或因型槽磨损面产生的毛刺在轧制时被卷入,形成和材料表面成一定倾角的折缝。
对钢材,折缝内有氧化铁夹杂,四周有脱碳。
折叠若在锻造前不去掉,可能引起锻件折叠或开裂。
结疤结疤是在轧材表面局部区域的一层可剥落的薄膜。
结疤的形成是由于浇铸时钢液飞溅而凝结在钢锭表面,轧制时被压成薄膜,贴附在轧材的表面,即为结疤。
锻后锻件经酸洗清理,薄膜将会剥落而成为锻件表面缺陷。
层状断口层状断口的特征是其断口或断面与折断了的石板、树皮很相似。
层状断口多发生在合金钢(铬镍钢、铬镍钨钢等),碳钢中也有发现。
这种缺陷的产生是由于钢中存在的非金属夹杂物、枝晶偏析以及气孔疏松等缺陷,在锻、轧过程中沿轧制方向被拉长,使钢材呈片层状。
如果杂质过多,锻造就有分层破裂的危险。
层状断口越严重,钢的塑性、韧性越差,尤其是横向力学性能很低,所以钢材如具有明显的层片状缺陷是不合格的。
亮线(亮区)亮线是在纵向断口上呈现结晶发亮的有反射能力的细条线,多数贯穿整个断口,大多数产生在轴心部分。
亮线主要是由于合金偏析造成的。
轻微的亮线对力学性能影响不大,严重的亮线将明显降低材料的塑性和韧性。
锻造和热处理过程中裂纹形成原因分析

锻造和热处理过程中裂纹形成原因分析摘要:在锻造以及热处理中极易出现裂纹,为此锻造以及热处理过程中的裂纹处理成为各个学者研究的重点,同时,构件尺寸、材质等之间的差异其所出现的裂纹几率也各不相同,基于此,本文通过对锻造以及热处理缺陷的相关分析,找出了锻造和热处理过程中裂纹形成的原因并提出了针对性的解决意见。
关键词:锻造热处理裂纹原因分析处理引言作为锻造以及热处理过程中最为常见的缺陷之一,裂纹的形成严重制约了锻造效率,并且对于大型锻件而言,其裂纹出现的几率则更高,所以加强对裂纹形成的原因分析对于减少裂纹产生,提升锻造效果具有重要意义。
1锻造缺陷与热处理缺陷第一,过热或者过烧。
具体表现形式为晶粒粗大并具有较为明显的魏氏组织;而造成过烧的情况则说明热处理过程中温度较高,断口晶粒凹凸不平,缺乏金属光泽,并且晶界周围具有氧化脱碳的情况;第二,锻造裂纹。
主要出现在组织粗大且应力较为集中处,裂纹内部往往呈现氧化皮情况。
在锻造过程中无论是温度过高,还是过低均会导致裂纹的出现;第三,折叠。
由于切料、冲孔、锻粗糙等原因而致使材料表面发生了缺陷,而此时一旦经过锻造自然其会由于表面氧化皮缺陷内卷而形成折叠。
通过显微镜的观察可以明显的发现折叠周围的脱碳情况较为严重;第四,淬裂。
该缺陷的明显特征就是刚健挺直且起始点较宽,尾部则细长曲直。
由于此缺陷往往是产生在马氏体转变发生以后,所以裂纹周围与其他区域没有明显的差别且无脱碳情况;第五,软点。
造成此种缺陷的原因主要是由于加热不足,保温时间不足而造成冷却不均匀导致的。
2实验方法2.1试样制备和宏观观察在开始试验之前只需要对构件毛坯裂纹进行简单的宏观观测并选择要进行实验的区域即可。
然后,在利用手边的工具来队选取的区域进行切割,需注意的是,切割方向必须要垂直镜像,切割长度要低于10mm。
可以通过多种方式进行取样但是一定要科学的选择取样的温度以及环境,如果实验温度较高,则可以通过凉水来进行冷却,进而防止在取样过程中构件内部结构遭到损坏。
锻件常见缺陷裂纹的原因

锻件常见缺陷裂纹的原因锻件常见缺陷裂纹的原因有很多,主要包括以下几个方面:1. 锻造前材料的缺陷:锻造前原材料中可能存在着各种缺陷,如夹杂物、气孔、夹渣等。
这些缺陷会在锻造过程中被拉长、扭曲或剪切,最终导致锻件出现裂纹。
2. 异常冷却方式:锻件在冷却过程中,如果冷却速度过快或不均匀,会导致锻件内部产生应力集中,从而引发裂纹。
尤其是在大尺寸、复杂形状的锻件中,由于其冷却速度不均匀,容易出现内部裂纹。
3. 冷、热变形不均匀:锻造过程中,如果材料的冷、热变形不均匀,会导致锻件内部应力分布不均匀,从而引发裂纹的产生。
尤其是在复杂形状、壁厚不一的锻件中,易出现材料贫化、过冷区和高应力区,容易引发裂纹。
4. 锻造温度过低或过高:锻造温度是影响锻件质量的关键因素之一。
如果温度过低,会导致材料的硬化能力不足,易发生塑性变形困难,从而引发裂纹;而温度过高,则会导致材料的焊接性能下降,也容易引发裂纹。
5. 压力不均匀:锻造过程中,如果锻压力不均匀,会使锻件中的应力分布不均匀,从而容易产生应力集中和裂纹。
尤其是在薄壁锻件中,容易出现锻压力不均匀的问题,导致裂纹的发生。
6. 锻件设计不合理:锻件的设计是影响锻件质量的重要因素之一。
如果锻件的形状、结构设计不合理,容易导致应力集中,从而引发裂纹的产生。
尤其是在复杂形状、尺寸大的锻件中,设计不合理会增加裂纹发生的概率。
7. 热处理不当:热处理是锻件制造过程中的关键环节,如果热处理不当,会导致锻件中的应力不释放或释放不充分,从而引发裂纹。
此外,热处理时的温度、时间等参数也需要合适,否则也可能导致裂纹的产生。
这些都是导致锻件常见缺陷裂纹的主要原因。
为了降低或避免裂纹的产生,需要从原材料选用、工艺控制、设备维护等方面做好控制和管理。
同时,制定合理的锻造工艺和热处理工艺,合理设计锻件形状和结构,对裂纹的产生起到有力的控制和避免作用。
还需要加强工作人员的培训和技能提升,提高他们的专业水平和质量意识,从而减少裂纹缺陷的发生,提高锻件的质量。
锻造加热与热处理加热裂纹如何正确鉴别

锻造加热与热处理加热裂纹如何正确鉴别锻造裂纹一般在高温时形成,锻造变形时由于裂纹扩大并接触空气,故在1 00X或500X的显微镜下观察,可见到裂纹内充有氧化皮,且两侧是脱碳的,组织为铁素体,其形态特征是裂纹比较粗壮且一般经多条形式存在,无明细尖端,比较圆纯,无明细的方向性,除以上典型形态外,有时会出现有些锻造裂纹比较细。
裂纹周围不是全脱碳而是半脱碳。
淬火加热过程中产生的裂纹与锻造加热过程形成的裂纹在性质和形态上有明显的差别。
对结构钢而言,热处理温度一般较锻造温度要低得多,即使是高速钢、高合金钢其加热保温时间则远远小于锻造温度。
由于热处理加热温度偏高,保温时间过长或快速加热,均会在加热过程中产生早期开裂。
产生沿着较粗大晶粒边界分布的裂纹;裂纹两侧略有脱碳组织,零件加热速度过快,也会产生早期开裂,这种裂纹两侧无明显脱碳,但裂纹内及其尾部充有氧化皮。
有时因高温仪器失灵,温度非常高,致使零件的组织极粗大,其裂纹沿粗大晶粒边界分布。
结构钢常见的缺陷:1 锻造缺陷(1)过热、过烧:主要特征是晶粒粗大,有明显的魏氏组织。
出现过烧缺陷说明加热温度高、断口晶粒粗大,凹凸不平,无金属光泽,晶界周围有氧化脱碳现象。
(2)锻造裂纹:常产生于组织粗大,应力集中处或合金元素偏析处,裂纹内部常充满氧化皮。
锻造温度高,或者终端温度低,都容易产生裂纹。
还有一种裂纹是锻造后喷水冷却后形成的。
(3)折叠:冲孔、切料、刀板磨损、锻造粗糙等原因造成了表面缺陷,在后续锻造时,将表面氧化皮等缺陷卷入锻件本体内而形成折缝。
在显微镜上观察时,可发现折叠周围有明显脱碳。
2 热处理缺陷(1)淬裂:其特点是刚健挺直,呈穿晶分布,起始点较宽,尾部细长曲折。
此种裂纹多产生于马氏体转变之后,故裂纹周围的显微组织与其它区域无明显区别,也无脱碳现象。
(2)过热:显微组织粗大,如果是轻度过热,可采用二次淬火来挽救。
(3)过烧:除晶粒粗大外,部分晶粒已趋于熔化,晶界极粗。
淬火裂纹、锻造裂纹的特性及区别

淬火裂纹、锻造裂纹的特性及区别一、材料方面1、碳是影响淬裂倾向的一个重要因素。
碳含量提高,MS点降低,淬裂倾向增大。
因此,在满足基本性能如硬度、强度的条件下,应尽量选用较低的碳含量,以保证不易淬裂。
2、合金元素对淬裂倾向的影响主要体现在对淬透性、MS点,晶l度长大倾向、脱碳的影响上。
合金元素通过对淬透性的影响,从而影响到淬裂倾向。
一般来说,淬透性增加,淬裂性增加,但淬透性增加的同时,却可以使用冷却能力弱的淬火介质以减少淬火变形的方法来防止复杂零件的变形与裂纹。
因此,对于形状复杂的零件,为了避免淬火裂纹,选择透性好的钢,并用冷却能力弱的淬火介质是一个较好的方案。
合金元素对MS点影响较大,一般来说,MS越低的钢,淬裂倾向越大,当MS点高时,相变生成的马氏体可能立刻被自回火,从而消除一部分相变应力,可以避免发生淬裂。
因此,当碳含量确定后,应用少量的合金元素,或者含对MS点影响较小的元素的钢种。
3、选择钢材时,应考虑过热敏感性。
过热较敏感的钢,容易产生裂纹,所以在选择材料时应引起重视。
二、零件的结构设计1、断面尺寸均匀。
断面尺寸急剧变化的零件,在热处理时由于产生内应力而产生裂纹。
故设计时尽量避免断面尺寸突变。
壁厚要均匀。
必要时可在与用途无直接关系的厚壁部位开孔。
孔应尽量做成通孔。
对于厚不同的零件,可进行分体设计,待热处理后,再进行组装。
2、圆角过渡。
当零件有棱角、尖角、沟槽和横孔时,这些部位很容易产生应力集中,从而导致零件淬裂。
为此,零件应尽量设计成不发生应力集中的形状,在尖角处和台阶处加工成圆角。
3、形状因素造成的冷却速度差异。
零件淬火时冷却速度的快、慢随零件形状的不同而不同。
即使在同一零件上不同的部位,也会因各种因素而造成蝗此俣鹊牟煌。
因此要尽量避免过大的冷却差异,以防止淬火裂纹。
三、热处理技术条件1、尽量采用局部淬火或表面硬化。
2、根据零件服役条件需要,合理调整淬火件局部硬度。
局部淬火硬度要求较低时,尽量不强求整体硬度一致。
锻造工艺学-3-锻造的热规范

9
3-2 加热时产生的缺陷及防止措施
表层缺陷:氧化、脱碳、裂纹 内部缺陷:过热、过烧、裂纹
10
一、氧化
钢在加热时,表面上的合金元素与炉气中的氧化 性气体(O2,CO2,H2O和SO2)发生化学反应,形成氧 化皮。
氧化实质上是一种扩散过程:铁以离子状态从内 部向表面扩散,氧以原子状态吸附到钢坯表面,并向 内部扩散。
35
3-3 金属的加热规范
36
几个概念:
1)装炉温度 2)加热速度 3)均热保温 4)加热时间 5)始锻温度、终锻温度、锻造温度范围
37
3-4 锻造温度范围的确定
基本原则: 合理的锻造温度范围,应保证金属具有良好的塑
性和较低的变形抗力。并在此条件下尽量扩大锻造温 度范围,以减少加热火次。 ● 具体锻造温度范围应根据铁碳相图来确定
30
2、组织应力(相变应力)
具有相变的材料在加热过程中,表层先相变,心 部后相变,且相变前后组织的比容发生变化,由此引 起的应力叫组织应力。
31
加热过程中随着温度升高,表层先相变,由珠光 体转变为奥氏体,比容减小,表层受拉心部受压。此 时组织应力与温度应力反向,使总的应力数值减小。
随着温度的继续升高,心部相变,此时组织应力 心部受拉表层受压。组织应力方向与温度应力相同, 使总的应力数值增大,但此时钢料已接近高温,一般 不会造成开裂。
击韧性,因此要尽量避免产生魏氏组织。
43
44
终锻温度:
低碳钢:奥氏体、铁素体双相区 中碳钢:奥氏体单相区 高碳钢:奥氏体、渗碳体双相区
注意:高碳钢终端温度为何选在奥氏体、渗碳 体双相区?
45
3-5 锻后冷却
一、冷却方法
● 空冷 ● 坑冷(箱冷) ● 炉冷 各种冷却方法的根本区别在于冷却速度的不同
热处理变形及裂纹
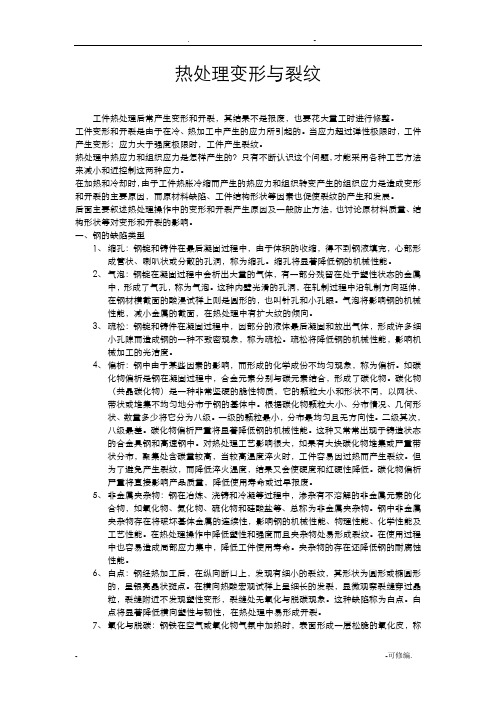
热处理变形与裂纹工件热处理后常产生变形和开裂,其结果不是报废,也要花大量工时进行修整。
工件变形和开裂是由于在冷、热加工中产生的应力所引起的。
当应力超过弹性极限时,工件产生变形;应力大于强度极限时,工件产生裂纹。
热处理中热应力和组织应力是怎样产生的?只有不断认识这个问题,才能采用各种工艺方法来减小和近控制这两种应力。
在加热和冷却时,由于工件热胀冷缩而产生的热应力和组织转变产生的组织应力是造成变形和开裂的主要原因,而原材料缺陷、工件结构形状等因素也促使裂纹的产生和发展。
后面主要叙述热处理操作中的变形和开裂产生原因及一般防止方法,也讨论原材料质量、结构形状等对变形和开裂的影响。
一、钢的缺陷类型1、缩孔:钢锭和铸件在最后凝固过程中,由于体积的收缩,得不到钢液填充,心部形成管状、喇叭状或分散的孔洞,称为缩孔。
缩孔将显著降低钢的机械性能。
2、气泡:钢锭在凝固过程中会析出大量的气体,有一部分残留在处于塑性状态的金属中,形成了气孔,称为气泡。
这种内壁光滑的孔洞,在轧制过程中沿轧制方向延伸,在钢材横截面的酸浸试样上则是圆形的,也叫针孔和小孔眼。
气泡将影响钢的机械性能,减小金属的截面,在热处理中有扩大纹的倾向。
3、疏松:钢锭和铸件在凝固过程中,因部分的液体最后凝固和放出气体,形成许多细小孔隙而造成钢的一种不致密现象,称为疏松。
疏松将降低钢的机械性能,影响机械加工的光洁度。
4、偏析:钢中由于某些因素的影响,而形成的化学成份不均匀现象,称为偏析。
如碳化物偏析是钢在凝固过程中,合金元素分别与碳元素结合,形成了碳化物。
碳化物(共晶碳化物)是一种非常坚硬的脆性物质,它的颗粒大小和形状不同,以网状、带状或堆集不均匀地分布于钢的基体中。
根据碳化物颗粒大小、分布情况、几何形状、数量多少将它分为八级。
一级的颗粒最小,分布最均匀且无方向性。
二级其次,八级最差。
碳化物偏析严重将显著降低钢的机械性能。
这种又常常出现于铸造状态的合金具钢和高速钢中。
轴类钢锻件磁粉检测中发纹与裂纹的鉴别

轴类钢锻件磁粉检测中发纹与裂纹的鉴别摘要:随着我国经济的不断发展,社会的不断进步,工业检测技术不断提高。
在轴类钢锻件的磁粉检测中,发纹与裂纹这两类缺陷的磁痕显示较为相似;但是两者对工件使用性能的影响存在较大的差别,其质量验收标准差异也较大。
提出了几种发纹与裂纹的实用鉴别方法,可供磁粉检测人员参考和借鉴。
关键词:轴类钢锻件;磁粉检测;发纹;裂纹;磁痕显示引言在轴类钢锻件的磁粉检测中,经常会遇到沿轴向分布,磁痕清晰而不浓密的线性缺陷显示,此类磁痕显示为发纹缺陷。
其是轴类钢锻件中比较常见的一类缺陷。
发纹的磁痕显示与裂纹的磁痕显示极为相似,不少检测人员常将发纹误判为裂纹。
发纹与裂纹这两类缺陷对工件使用性能的影响差别较大。
发纹对工件使用性能的影响较小,而裂纹的危害极大。
因此,掌握准确鉴别发纹与裂纹的方法,是检测人员必备的一项技能。
笔者提出了几种发纹与裂纹的实用鉴别方法,可供磁粉检测人员参考和借鉴。
1相关行业标准与企业标准对裂纹与发纹的验收要求1.1相关行业标准1.1.1NB/T47013.4-2015《承压设备无损检测第4部分磁粉检测》NB/T47013.4-2015标准对发纹与裂纹的要求为:(1)不允许任何裂纹和横向缺陷显示;(2)质量分级见表1。
表1NB/T47013.4-2015的质量分级mm注:L表示线性缺陷磁痕长度。
1.1.2JB/T5442-1991《压缩机重要零部件的磁粉检测》JB/T5442-1991标准对发纹与裂纹的要求为(1)不允许任何裂纹和横向缺陷显示;(2)质量分级见表2。
表2JB/T5442-1991的质量等级分类注:若缺陷磁痕数量超过表中规定时,则每增加2条等级下降1级,且最多不得超过两级,否则按不允许缺陷处理。
1.2相关企业标准或规范在国家标准指导下,旋转机械制造企业都会结合各自的产品特色及使用工况,并结合前期案例制定相应的标准或规范,如某旋转机械制造企业对主轴磁粉检测标准的质量分级为:(1)不允许裂纹缺陷;(2)质量分级见表3。
锻件缺陷的主要特征及其产生的主要原因

锻造件缺陷是指锻造过程中锻件上产生的外在的和内在的质量不合要求的各种毛病。
锻件缺陷如按其表现形式来区分,可分为:外部的、内部的和性能的三种。
外部缺陷如几何尺寸和形状不符合要求。
表面裂纹、折叠、缺肉、错差、模锻不足、表面麻坑、表面气泡和橘皮状表面等。
这类缺陷显露在锻件的外表面上,比较容易发现或观察到。
内部缺陷又可分为低倍缺陷和显微缺陷两类。
前者如内裂、缩孔、疏松、白点、锻造流纹紊乱、偏析、粗晶、石状断口、异金属夹杂等;后者如脱碳、增碳、带状组织。
铸造组织残留和碳化物偏析级别不符合要求等。
内部缺陷存在于锻件的内部,原因复杂,不易辨认,常常给生产造成较大的困难。
反映在性能方面的缺陷,如室温强度、塑性、韧性或疲劳性能等不合格;或者高温瞬时强度,持久强度、持久塑性、蠕变强度不符合要求等。
性能方面的缺陷,只有在进行了性能试验之后,才能确切知道。
值得注意的是内外部和性能方面的缺陷这三者之间,常常有不可分割的联系。
例如过热和过烧表现于外部常为裂纹的形式:表现于内部则为晶粒粗大或脱碳,表现在性能方面则为塑性和韧性的降低。
因此,为了准确确定锻件缺陷的原因,除了必须辨明它们的形态和特征之外,还应注意找出它们之间的内在联系。
锻造过程产生的缺陷和热处理过程产生的缺陷。
按照锻造过程中各工序的顺序,还可将锻造过程中产生的缺陷,细分为以下几类:由下料产生的缺陷;由加热产生的缺陷:由锻造产生的缺陷:由冷却产生的缺陷和由清理产生的缺陷等。
不同工序可以产生不同形式的缺陷,但是,同一种形式的缺陷也可以来自不同的工序。
由于产生锻件缺陷的原因往往与原材料生产过程和锻后热处理有关,因此在分析锻件缺陷产生的原因时,不要孤立地来进行。
大型锻件中常见缺陷

大型锻件中常见的缺陷与对策2010-5-27 8:49:16 来源:中国钢铁产业网信息中心编辑:王宝玉大型锻件中常见的缺陷与对策大型锻件中的缺陷,从性质上分为化学成分、组织性能不合格,第二相析出,类孔隙性缺陷和裂纹五大类。
从缺陷的产生方面可分为,在冶炼、出钢、注锭、脱模冷却或热送过程中产生的原材料缺陷及在加热、锻压、锻后冷却和热处理过程中产生的锻件缺陷两大类。
大型锻造中,由于锻件截面尺寸大,加热、冷却时,温度的变化和分布不均匀性大,锻压变形时,金属塑性流动差别大,加上钢锭大冶金缺陷多,因而容易形成一些不同于中小型锻造的缺陷。
如严重偏析和疏松,密集性夹杂物,发达的柱状晶及粗大不均匀结晶,敏感开裂与白点倾向,晶粒遗传性与回火脆性,组织性能的严重不均匀性,形状尺寸超差等等。
大型锻件中常见的主要缺陷有;1.偏析钢中化学成分与杂质分布的不均匀现象,称为偏析。
一般将高于平均成分者,称为正偏析,低于平均成分者,称为负偏析。
尚有宏观偏析,如区域偏析与微观偏析,如枝晶偏析,晶间偏析之分。
大锻件中的偏析与钢锭偏析密切相关,而钢锭偏析程度又与钢种、锭型、冶炼质量及浇注条件等有关。
合金元素、杂质含量、钢中气体均加剧偏析的发展。
钢锭愈大,浇注温度愈高,浇注速度愈快,偏析程度愈严重。
(1)区域偏析它属于宏观偏析,是由钢液在凝固过程中选择结晶,溶解度变化和比重差异引起的。
如钢中气体在上浮过程中带动富集杂质的钢液上升的条状轨迹,形成须状∧形偏析。
顶部先结晶的晶体和高熔点的杂质下沉,仿佛结晶雨下落形成的轴心∨形偏析。
沉淀于锭底形成负偏析沉积锥。
最后凝固上部区域,碳、硫、磷等偏析元素富集,成为缺陷较多的正偏析区。
图片6-1为我国解剖的55t34CrMolA钢锭纵剖面硫印低倍图片及区域偏析示意图。
图片6-1 钢锭区域偏析硫印示意图①“∧”型偏析带②“∨”型偏析带③负偏析区防止区域偏析的对策是:1)降低钢中硫、磷等偏析元素和气体的含量,如采用炉外精炼,真空碳脱氧(VCD)处理及锭底吹氩工艺。
锻造和热处理过程中裂纹形成原因分析

锻造和热处理过程中裂纹形成原因分析发布时间:2021-05-20T10:33:30.803Z 来源:《基层建设》2020年第31期作者:裴一飞[导读] 摘要:裂缝很常见,生产过程往往是锻造和热处理过程。
航空工业哈尔滨飞机工业集团有限公司黑龙江哈尔滨 150000摘要:裂缝很常见,生产过程往往是锻造和热处理过程。
锻造裂纹通常在高温下发生,在锻造过程中会延伸并接触空气,形成裂纹中氧化的皮肤。
此框形成的裂纹不仅厚而且多,裂纹的两端不相连,尖端相对圆。
所处理的裂纹的形状和性能与锻造裂纹不同。
出现热处理后的裂纹是因为加热时该元素出现裂纹,导致在裂纹的咸晶方向上脱碳,最终结构比锻造裂纹厚。
对于和零件尤其如此本文收集了大量裂缝方式,分析总结了裂缝的原因。
最后,裂缝分为三类。
关键词:锻造、热处理;裂纹形成原因;过程;存在缺陷;前言裂纹是锻造和热处理中常见的缺陷之一,也是锻造行业中的热点和难点。
但是,锻造零件产生裂纹的可能性很大,因此必须研究锻造和热处理过程中的裂纹,并分析裂纹的原因。
一、锻造缺陷与热处理缺陷过热燃烧。
过度燃烧意味着加热温度高,切割机又大又不均匀,没有金属光泽,玻璃周围有氧化和渗碳。
造成裂缝。
当锻造温度较高或最终温度较低时,容易产生裂纹。
另一个裂缝是在水的钻井和冷却后形成的。
缩小范围。
表面缺陷是冲压、切割、板材磨损、穿孔等造成的。
在随后的钻孔中,观察到锻造体中存在表面氧化等缺陷以形成折弯。
通过显微镜观察,你可以看到弯曲周围明显的碳流失。
过火裂缝。
这些裂缝大多发生在MCU改造后,因此裂缝周围的微观结构与其他区域没有显着差异,也没有渗碳。
二、实验方法1.试样制备和宏观观察在试验前的第一阶段,只需对所选杆的工件裂纹进行宏观观察,在观察过程中,选择要测量的区域。
下一步是手动剪切选定区域,使其垂直于镜像且长度小于10 mm。
采样方法可能会有所不同,但在采样时必须选择温度和环境。
如果样品温度过高,可以使用冷水冷却样品,以免由于样品在回收过程中过热而改变事件的内部组织。
金属零件裂纹类型及预防措施

金属零件常见裂纹类型和预防措施南京科润技术中心王学平裂纹是钢铁零件最为忌讳的破坏性缺陷。
在零件加工生产过程中,必然会经历锻造、铸造或轧制、热处理、机械加工、磨削等一系列的工艺过程,常因材料或操作不当等原因引起各类裂纹的产生,往往在零件加工制作完成后才得以发现,将直接造成零件报废,影响产品的正常安装使用,带来一定的经济损失。
因此,为了避免各类裂纹缺陷的发生,,我们针对原材料,热处理,机械加工等工序可能会出现的裂纹特征、预防措施进行了探讨,从而在生产过程中对裂纹进行预防与控制。
(一)原材料裂纹原材料裂纹是工件表面和内部因冶金因素或上道工序不当而存在的裂纹缺陷,常发生于原材料的供货状态。
原材料缺陷如缩孔,疏松,白点,夹杂物、偏析等在锻造时,都有可能形成裂纹,致使工件报废。
1、特征原材料裂纹一般深度较深,裂痕清晰,呈直线或弯曲线条。
1.1 宏观特征:非金属夹杂物引起的裂纹呈锯齿形,且裂纹两侧和尾部有夹杂物分布,裂纹有粗变细,尾端呈圆凸状。
折叠裂纹,锻造热裂纹、铸造热裂纹主要为沿晶扩展,其形状粗细不均,曲折而不规则,常伴有树晶枝;裂纹表面呈氧化色或深褐色,无金属光泽,铸造钢件裂纹表面近似黑色,而铝合金则呈暗灰色。
铸造,锻造冷裂纹往往为穿晶扩展,外形呈宽度均匀细长的直线或折线状,两端有尖角,端口表面清洁,有金属光泽或 轻度氧化色,裂纹走向平滑。
1.2 折叠、锻造、铸造裂纹微观特征:裂纹两侧的显微组织与基体明显不同,有脱碳和氧化现象存在,如图1所示45钢转轴锻件热裂纹形貌为典型的原材料裂纹特征形态。
2、预防措施:⑴材料的化学成分应严格复合标准。
对有害元素S、P、O、N等容易形成夹杂物的元素及 Sn、Sb等微量元素应加以控制。
⑵ 严格控制冶炼浇铸过程。
这是提高材料纯净度,消除冶金缺陷,防止裂纹产生的重要环节。
⑶ 选择正确的铸造、锻造工艺。
铸造零件时,合理设置浇冒口的位置和尺寸,使铸件壁厚不均匀的部位均匀过度,采用合理的圆角尺寸,控制好金属模具的工作温度,开箱时间,冷却速度,以及合适的抽芯开模,确保铸件各部分的冷却速度尽量均匀一致,实现内外同时凝固,有效地减少裂纹倾向。
锻造和热处理过程中裂纹形成原因分析

Internal Combustion Engine&Parts0引言在进行锻造与热处理的过程中,裂纹的出现是很常见的事情,在所有的锻造与热处理的过程中,不可能不出现裂纹。
这就让裂纹在锻造这个行业中成为了一种讨论的焦点。
构件的尺寸大小,材质质地的不同,裂纹的出现几率也不同,裂纹的出现种类不同,裂纹出现的形状不同。
在本文中主要进行锻造和热处理过程中产生裂纹的原因进行研究。
在本文中通过大量对资料的收集进行了产生裂纹原因的阐述,也进行了防止裂纹产生举措的提出,对于减少构件在锻造和热处理的过程中出现裂纹带来了很大的帮助。
1锻造缺陷与热处理缺陷1.1过热、过烧主要特征是晶粒粗大,有明显的魏氏组织。
出现过烧说明加热温度高、断口晶粒粗大,凹凸不平,无金属光泽,晶界周围有氧化脱碳现象。
1.2锻造裂纹常产生于组织粗大,应力集中处或合金元素偏析处,裂纹内部常充满氧化皮。
锻造温度高,或者终端温度低,都容易产生裂纹。
还有一种裂纹是锻造后喷水冷却后形成的。
1.3折叠冲孔、切料、刀板磨损、锻造粗糙等原因造成了表面缺陷,在后续锻造时,将表面氧化皮等缺陷卷入锻件本体内而形成折缝。
在显微镜上观察时,可发现折叠周围有明显脱碳。
1.4淬裂其特点是刚健挺直,呈穿晶分布,起始点较宽,尾部细长曲折。
此种裂纹多产生于马氏体转变之后,故裂纹周围的显微组织与其它区域无明显区别,也无脱碳现象。
1.5软点显微组织有块状或网状屈氏体和未溶铁素体等。
加热不足,保温时间不够,冷却不均匀都会产生软点。
2实验方法在本文中的实验,采取了对锻造和热处理出现的裂纹范围划定。
在裂纹出现的范围内,采取裂纹邻近部位的显微组织,利用仪器进行晶相分析。
这样的实验方式可以让裂纹形成的内在原因通过机器进行分析,以数据的方式来进行裂缝产生原因的表述,这样的数据也是对裂纹进行鉴别的重要的依据。
在本次的实验中,采取了杆类件作为本次实验的研究对象,在采取裂纹附近部位的显微组织进行晶相分析。
大型热作模具钢5CrNiMo开裂分析

表 3
非金 属夹杂物/ 级 部位 A类 B类 C类 D类 Ds 类
.
能 ,同时使材料的性 质变脆。大型平砧锻
组织 晶粒度/ 级
件淬 火 时 ,将 产 生较 大 的 热 应 力 ,特 别是
在心部将产生较大的轴 向拉应 力,在内部
检 测 ,防止 零 件 在加 工 或 使 用过 程 中失效 ,减 少 损
失 。MW ( 2 0 1 3 0 5 0 9 )
6 . 讨论 与分 析
( 1 )严重 的一般疏松和极粗 大枝 晶偏析可 降
跏 …
熬
_ 2 5
般疏松 中心疏松 区域偏析 点状偏析 缺陷
/ 级 / 级 / 级 / 级
的性质变脆 ,白点裂纹是钢 中不允许存在的缺陷。
有
4 . O
3 . 0
1 . O
>4 . O
( 2 )从 宏 观 到 微 观 试 验 结 果 均 表 明 ,钢 的 纯 净 度 很 差 ,微 观 夹 杂 物 大 干 3 级 ,属 不 合 格 。显 微
点缺陷和一处深棕色缺陷区 ,椭 圆形斑点内结 晶细
于 基 体 ,具 有 白点 裂 纹 断 口形 态 ,深 棕 色缺 陷 区系
裂 纹 酸浸 后 在 断 口上 反 映 。
( 4 )显微组 织分析
晶粒 度结 果 见表 3 。
非 金属夹杂物 、组 织 、
点状偏析和不允许存在的 白点裂纹缺陷 ,显著地降
因一般认为是结晶条件不 良所造成 ,当气体和夹杂 物大量存在时 ,点状偏析将更为严重。点状偏析的 存在 ,将显著地 降低钢的塑性及疲劳 强度 ,点状偏
工模具零件热处理开裂分析与对策

防止措施:1、不使用不符合技术标准要求的原盐;2、盐浴炉要认 真脱氧捞渣,不要只脱氧不捞渣,因为炉渣含有很多氧化物;3、零 件在电阻炉中加热要加以保护,以防脱碳;4、工件外表生锈或有氧 化皮,加热前去除干净;5、假设毛坯件有脱碳层存在,热处理前要 彻底加工去除掉;6、采用真空炉进行淬火加热。
尺寸较大的工件,淬火冷却后外表看 上去冷的差不多了,但其心部温度仍比较 高,仍在进行着马氏体转变。此时假设将 工件放入冷水中〔特别在冬季的冷水中〕 清洗,等于在马氏体转变区域内加速冷却, 产生的内应力将会增加,使工件发生开裂, 这种裂纹仍为淬火裂纹。因此,工件必须 完全冷透后再清洗。
九、萘状断口与淬火裂纹
防止措施:严格按工艺文件规定加热温度和保温时间生产;保 证控温仪表和加热设备始终处于正常运转;加强生产管理,不 要造成混料、错料事件发生;零件重新淬火前必须进行退火处 理,零件重复淬火只能进行一次;认真校直,防止返修。
十二、渗碳与淬火裂纹
零件渗碳后淬火,由于表层含碳量高,其表层马氏 体膨胀量比内部大,使外表受压应力,从而防止淬 火开裂;但当渗碳过度容易生成硬脆的碳化物层, 引起淬火开裂。
应采取下限的淬火加热温度,为保证加热充分,可
适当延长加热时间,对一些带尖角的零件应离炉内
加热体远一些,在盐浴炉中工件距电极距离不得小
于50mm,以免引起尖角过热;
防止工模具零件因淬火过热开裂主要措施:
锻造和热处理过程中裂纹形成原因分析李艳梅

锻造和热处理过程中裂纹形成原因分析李艳梅发布时间:2021-07-28T10:12:15.580Z 来源:《基层建设》2021年第13期作者:李艳梅[导读] 摘要:在锻造和热处理过程中,裂纹是非常常见的,不可能在所有的锻造和热处理过程中避免裂纹。
惠阳航空螺旋桨有限责任公司河北保定 071000摘要:在锻造和热处理过程中,裂纹是非常常见的,不可能在所有的锻造和热处理过程中避免裂纹。
这使得裂纹成为锻造行业讨论的焦点。
裂纹的发生概率、类型和形状因部件的尺寸和纹理而异。
关键词:锻造;热处理;晶相分析;裂纹形成原因;裂纹是在锻造和热处理生产过程中常见的缺陷之一,通过对裂纹产品试样进行收集、分析、整理,可将裂纹大致分为三类:锻造裂纹、折叠和淬火裂纹。
通过晶相实验分析,可获得三种类型裂纹的形成原因,有针对性的提出减少裂纹产生的建议性措施,从而提高产品的质量和性能。
一、锻造缺陷和热处理的缺陷1.过热和燃烧。
主要特点是谷物粗犷,具有明显的维氏结构。
过热表明加热温度高,碎粒粗糙不均匀,没有金属光泽,晶界周围存在氧化和脱碳现象。
2.钻孔裂纹。
通常发生在结构粗糙、应力集中或合金元素分离的地方,裂纹通常充满氧气槽。
钻孔温度高或终端温度低时容易出现裂纹。
另一种裂纹是通过喷水进行钻孔和冷却后形成的。
3.折叠起来。
曲面缺陷是由冲压、切削、切削板磨损、粗糙钻孔等引起的。
在随后的钻孔中,曲面比例等缺陷被包含在钻孔主体中以形成折弯。
当用显微镜观察时,你可以看到折痕周围有明显的渗碳现象。
4.淬裂。
其特点是强而直的颗粒间分布,起点广,尾巴薄而曲折。
此类裂纹主要发生在马氏体改造后,因此裂纹周围的微观结构明显与其他区域没有区别,没有渗碳现象。
5.软点。
微观结构由大块或星形托洛茨坦和未溶解的铁氧体组成。
供暖不足、维护时间不足和冷却不均衡都将导致薄弱环节。
二、实验的方法1.取样准备和宏观观察。
首先宏观观察杆的裂纹,然后手工切割试样,方向垂直于径向方向,长度小于8 mm。
- 1、下载文档前请自行甄别文档内容的完整性,平台不提供额外的编辑、内容补充、找答案等附加服务。
- 2、"仅部分预览"的文档,不可在线预览部分如存在完整性等问题,可反馈申请退款(可完整预览的文档不适用该条件!)。
- 3、如文档侵犯您的权益,请联系客服反馈,我们会尽快为您处理(人工客服工作时间:9:00-18:30)。
一:锻造裂纹与热处理裂纹形态
一:锻造裂纹一般在高温时形成,锻造变形时由于裂纹扩大并接触空气,故在100X或500X 的显微镜下观察,可见到裂纹内充有氧化皮,且两侧是脱碳的,组织为铁素体,其
特征是裂纹比较粗壮且一般经多条形式存在,无明细尖端,比较圆纯,无明细的方向性,除以上典型外,有时会出现有些锻造裂纹比较细。
裂纹周围不是全脱碳而是半脱碳。
淬火加热过程中产生的裂纹与锻造加热过程形成的裂纹在性质和上有明显的差别。
对结构钢而言,热处理温度一般较锻造温度要低得多,即使是高速钢、高合金钢其加热保温时间则远远小于锻造温度。
由于热处理加热温度偏高,保温时间过长或快速加热,均会在加热过程中产生早期开裂。
产生沿着较粗大晶粒边界分布的裂纹;裂纹两侧略有脱碳组织,零件加热速度过快,也会产生早期开裂,这种裂纹两侧无明显脱碳,但裂纹内及其尾部充有氧化皮。
有时因高温仪器失灵,温度非常高,致使零件的组织极粗大,其裂纹沿粗大晶粒边界分布。
结构钢常见的缺陷:
1 锻造缺陷
(1)过热、过烧:主要特征是晶粒粗大,有明显的魏氏组织。
出现过烧说明加热温度高、断口晶粒粗大,凹凸不平,无金属光泽,晶界周围有氧化脱碳现象。
(2)锻造裂纹:常产生于组织粗大,应力集中处或合金元素偏析处,裂纹内部常充满氧化皮。
锻造温度高,或者终端温度低,都容易产生裂纹。
还有一种裂纹是锻造后喷水冷却后形成的。
(3)折叠:冲孔、切料、刀板磨损、锻造粗糙等原因造成了表面缺陷,在后续锻造时,将表面氧化皮等缺陷卷入锻件本体内而形成折缝。
在显微镜上观察时,可发现折叠周围有明显脱碳。
2 热处理缺陷
(1)淬裂:其特点是刚健挺直,呈穿晶分布,起始点较宽,尾部细长曲折。
此种裂纹多产生于马氏体转变之后,故裂纹周围的显微组织与其它区域无明显区别,也无脱碳现象。
(2)过热:显微组织粗大,如果是轻度过热,可采用二次淬火来挽救。
(3)过烧:除晶粒粗大外,部分晶粒已趋于熔化,晶界极粗。
(4)软点:显微组织有块状或网状屈氏体和未溶铁素体等。
加热不足,保温时间不够,冷却不均匀都会产生软点。
二:锻造裂纹与热处理裂纹产生原因
锻造裂纹:钢在锻造过程中,由于钢材存在表面及内部缺陷,如发纹、砂眼、裂纹、夹杂物、皮下气泡、缩孔、白点和夹层等,都可能成为锻打开裂的原因。
另外,由于锻打工艺不良或操作不当,如过热、过烧或终锻温度太低,锻后冷却速度过快等,也会造成锻件开裂。
热处理裂纹:淬火裂纹是宏观裂纹,主要由宏观应力引起。
在实际生产过程中,钢制工件常由于结构设计不合理,钢材选择不当、淬火温度控制不正确、淬火冷速不合适等因素,一方面增大淬火内应力,会使已形成的淬火显微裂纹扩展,形成宏观的淬火裂纹,另一方面,由于增大了显微裂纹的敏感度,增加了显微裂纹的数量,降低了钢材的脆断抗力Sk,从而增大淬火裂纹的形成可能性。
影响淬裂的因素很多,这里仅将生产中常碰到的几种情况作一介绍:
1.原材料已有缺陷而导致的淬裂:
如果原材料表面和内部有裂纹或夹杂物等缺陷,在淬火之前未发现,有可能形成淬火裂纹。
2、夹杂物导致的开裂:
如果零件内部夹杂物严重,或本身因夹杂物严重已经隐藏有裂纹,淬火时将有可能产生裂纹
3、因原始组织不良而导致的淬裂
4、淬火温度不当造成的淬裂
淬火温度不当引起零件淬裂,一般有两种情况:
(1)仪表指示温度低于炉子的实际温度,使淬火温度偏高,造成淬火过热,导致工件发生开裂。
凡是过热淬火开裂的金相组织均存在晶粒粗大和粗大的马氏体。
(2)钢件实际含碳量高于钢材牌号所规定的含量,若按原牌号的正常淬火工艺淬火时,等于提高了钢的淬火温度,容易造成零件过热和晶粒长大,使淬火时应力增大而引起淬裂。
5、淬火冷却不当造成的淬裂
淬火时由于冷却不当,也会使零件产生淬裂事故。
6、机加工缺陷导致的淬裂
由于机加工不良,在零件表面留下了粗而深的刀痕,尽管是很简单的零件或不是应力集中的地方,也会在淬火时造成开裂,或在服役过程中发生早期损坏。
7、零件外形对淬火裂纹的影响
零件几何形状不合理,或截面过度区厚薄相差较大,在淬火时均易因应力集中产生裂纹8、不及时回火导致的开裂
淬火后不及时回火,将可能因淬火残余应力过大而导致裂纹产生。
总之,应用金相方法进行缺陷分析是一项较为复杂的工作,由于零件失效有时是由多种因素所造成的,所以在实际工作中,应做多方面调查,掌握实情,并从多方面进行分析,以确保缺陷分析的准确性。
三:热处理裂纹产生机理与磨削裂纹产生机理
热处理裂纹:
产生机理:工件淬火后出现开裂是由内应力引起的。
内应力分为热应力与相变应力。
1)工件在加热或冷却时,由于不同部位存在着温度差而导致热胀或冷缩不一致所引起的应力称为热应力。
2)淬火工件在加热时,铁素体和渗碳体转变为奥氏体,冷却时又由奥氏体转变为马氏体。
由于不同组织的比容不同,故加热冷却过程中必然要发生体积变化。
热处理过程中由于工件表面与心部的温差使各部位组织转变不同时进行而产生的应力称为相变应力。
淬火冷却时,工件中的内应力超过材料的屈服点,就可能产生塑性变形,如内应力大于材料的抗拉强度,则工件将发生开裂。
磨削裂纹:
产生机理:
高的磨削温度容易烧伤工件表面,使淬火钢件表面退火,硬度降低。
即使由于切削
液的浇注,可能发生二次淬火,也会在工件表层产生张应力及微裂纹,降低零件的表面质量和使用寿命。
1.零件热处理裂纹产生的原因
零件在热处理过程中会产生很大的内应力(组织应力和热应力),当这些应力超过钢的屈服强度时,会引起零件的变形;当应力更大,超过钢的抗拉强度时,则会造成零件的开裂。
作用在零件上的应力有两种:压应力和拉应力。
淬火时形成的拉应力是引起淬火裂纹的主要原因。
但是当钢的塑性较高时,即使有较大的拉应力也不会引起零件的开裂,比如没有发生组织转变的去应力退火,获得较多残留奥氏体的等温淬火等。
只有在应力较大,又具备了高硬度、脆性大的组织时,才容易造成零件的开裂。
故淬火裂纹的形成必须同时存在两个条件:一是具有脆性组织;二是拉应力超过了此时钢的抗拉强度(当然其他情况也能促使零件裂纹发生,比如原材料缺陷、设计及机械加工不当造成的缺陷等)。
2.关于裂纹的类型
裂纹的分类方法各种各样。
按裂纹的方向分,有纵向裂纹、横向裂纹、弧形裂纹和网状裂纹(又称龟裂)等;按裂纹发生的位置分,有表层裂纹(或称表面裂纹)和内部裂纹;按裂纹发生在不同的工序分,有锻造裂纹、焊接裂纹、淬火裂纹、回火裂纹、冷处理裂纹、酸洗裂纹及磨削裂纹等。
零件在热处理过程中以淬火裂纹为最多。
3.裂纹的分辨方法
如何区分究竟是淬火裂纹、回火裂纹、锻造裂纹还是磨削裂纹等是很重要的,这样便于准确查找裂纹发生在哪一工序,有利于分析裂纹产生的原因。
第一,注意淬火裂纹和磨削裂纹形态的不同。
对于淬火时未发现而在磨削后才发现的裂纹,要区别是淬火裂纹还是磨削裂纹。
在裂纹未附着污染物时比较容易,此时注意裂纹的形态,特别是裂纹发展的方向,磨削裂纹是垂直于磨削方向的,呈平行线形态,或呈龟甲状裂纹。
磨削裂纹的深度根浅,而淬火裂纹一般都比较深比较大,与磨削方同无关,多呈直线刀割状开裂。
第二,注意裂纹发生的部位。
尖锐的凹凸转角处、孔的边缘处、刻印处、打钢印处及机械加工造成的表面缺陷等部位,在这些部位发生的裂纹多属淬火裂纹。
第三,通过观察零件的裂断面来区分是淬火裂纹还是淬火前的锻造裂纹或其他情况造成的裂纹。
若裂纹断面呈白色或暗白色或浅红色(水淬时造成的水锈),均可断定为淬火裂纹,若裂纹断面呈深褐色,甚至有氧皮出现,那就不是淬火裂纹,系淬火前就存在的裂纹,是零件经过锻造或压延时形成的裂纹,这些裂纹都会因淬火而被扩大。
因淬火裂纹基本上是在MS点以下时形成的,其断面是不会被氧化的。
第四,在显微组织中,淬火裂纹是沿晶界断裂,若不是沿晶界断裂,而是沿晶内断裂,则属于疲劳裂纹。
第五,如果裂纹周围有脱碳层存在,那就不是淬火裂纹,而是淬火前就存在的裂纹,因为淬火裂纹是淬火冷却时产生的,绝不会发生脱碳现象。