锻造裂纹的原因分析及预防措施
锻件的层状断口

锻件的层状断口
锻件的层状断口是指在金属材料的拉伸、压缩或弯曲等力学加工过程中,材料发生断裂时,断口呈现出层状结构。
这种断口形貌类似于木材的剖面,由多条平行的层状裂缝组成。
锻件的层状断口形成的原因主要有以下几点:
1.金属材料在受到外力作用时,会在应力集中区域发生局部塑性变形。
当应力超过材料的屈服强度时,就会形成裂纹。
随着外力的继续作用,裂纹会逐渐扩展,形成层状断口。
2.金属材料的微观结构和组织也会影响层状断口的形成。
如果材料的结晶粒度较大,裂缝扩展路径较长,就容易形成层状断口。
3.材料的纯度、含气等也会影响层状断口的形成。
锻件的层状断口会导致钢的横向力学性能严重下降,特别是延伸率和断面收缩率。
这种层状断口在形变结构钢中经常出现,会显著降低钢的强度和韧性。
因此,在金属材料的加工过程中,应采取措施避免层状断口的形成,如优化加工工艺、控制材料纯度和组织结构等。
锻造裂纹分析

锻造裂纹钢在锻造过程中形成的裂纹是多种多样的,形成原因也各不相同。
主要可分为原材料缺陷引起的锻造裂纹和锻造本身引起锻造裂纹两类。
属于前者的原因有残余缩孔、钢中夹杂物等冶金缺陷;属于后者的原因有加热不当、变形不当及锻后冷却不当、未及时热处理等。
有些情况下裂纹的产生可能同时含有几方面的原因。
锻造变形不当常引起裂纹。
最常见的是变形速度太大,钢的塑性不足以承受形压力而引起的破裂。
这种裂纹往往在锻造开始阶段就发生,并迅速扩展。
应及时采取措施纠正锻造工艺,并切除有裂纹的钢材或报废锻件。
另外一种是低温锻裂,在裂纹处往往有较多的低温相组织。
为避免这种裂纹产生,应使钢在锻造变形过程中不发生相变,要正确掌握和控制终锻温度。
鉴别裂纹形成的原因,应首先了解工艺过程,以便找出裂纹形成的客观条件,其次应当观察裂纹本身的状态,然后再进行必要的有针对性的显微组织分析,微区成分分析。
举例如下:对于产生龟裂的锻件,粗略分析可能是:①由于过烧;②由于易溶金属渗入基体金属(如铜渗人钢中);③应力腐蚀裂纹;④锻件表面严重脱碳。
这可以从工艺过程调查和组织分析中进一步判别。
例如在加热钢以后加热钢料或两者混合加热或钢中含铜量过高时,则有可能是铜脆。
从显微组织上看,铜脆开裂在晶界,除了能找到裂纹外,还能找到亮的铜网,而在单纯过烧的晶界只能找到氧化物。
应力腐蚀开裂是在酸洗后出现,在高倍观察时,裂纹的扩展呈树枝状形态。
锻件严重脱碳时,在试片上可以观察到一层较厚的脱碳层。
裂纹与折叠的鉴别,不仅可以从受力及变形的条件考察,亦可以低倍和高倍组织来区分。
一般裂纹与流线成一定交角,而折叠附近的流线与折叠方向平行,而且对于中、高碳钢来说,折叠表面有氧化脱碳现象。
折叠的尾部一般呈圆角,而裂纹通常是尖的。
具有裂纹的锻件经加热后,裂纹附近有严重的氧化脱碳,冷却裂纹则无此现象。
由缩管残余引起的裂纹通常是粗大而不规则的。
由冷校正及冷切边引起的裂纹,在裂纹的周围有滑移带等冷变形痕迹。
自由锻常见缺陷裂纹的原因

自由锻常见缺陷裂纹的原因自由锻是一种常见的金属加工工艺,通过利用金属的塑性变形特性来加工成型各种零部件。
然而,在实际的生产过程中,由于材料属性、加工工艺等原因,常常会出现各种缺陷,其中最常见的就是裂纹。
裂纹的出现不仅会影响零部件的质量和性能,还可能导致工件失效,因此及时发现并采取措施是非常重要的。
下面将从几个方面介绍自由锻常见缺陷裂纹的原因。
1. 材料因素材料的质量和性能对自由锻过程的裂纹形成起着重要的作用。
首先,原材料的杂质和非金属夹杂物会降低金属的塑性,增加金属的脆性,从而容易形成裂纹。
其次,金属的晶粒度和组织结构也会对裂纹的产生起到影响作用。
晶粒度过大或过小都会导致金属的塑性不足,从而容易出现裂纹。
此外,金属中的残余应力也是裂纹产生的一个重要因素,过大的残余应力会在加工过程中导致金属局部应力集中,进而形成裂纹。
2. 加工工艺因素自由锻的加工工艺对裂纹的形成有着直接的影响。
例如,锻造温度过高或过低都会影响金属的塑性,从而容易形成裂纹。
此外,锻造的速度、变形量等参数设置也会对裂纹的形成起到影响。
如果变形量过大或变形速度过快,可能使金属的应力超过其承载能力,导致裂纹的产生。
还有一些其他因素,比如锻造过程中的冷却速度、锻后的热处理工艺等也会对裂纹的形成产生影响。
3. 设计因素零部件的设计也是影响裂纹产生的因素之一。
不合理的结构设计、过于尖锐的转角或者挤压形状等都可能会导致金属在锻造过程中产生应力集中,从而形成裂纹。
因此,在设计零部件时,应该尽量避免设计过于尖锐的结构,合理控制转角和挤压形状,以减少应力集中点的产生。
4. 操作因素操作人员的技术水平和操作规范也会对裂纹的产生起到影响。
不合理的操作方法、过于急躁的操作、缺乏经验的操作人员等都有可能导致裂纹的产生。
因此,操作人员需要具备良好的技术水平和严格的操作规范,以避免不必要的裂纹产生。
5. 设备因素锻造设备的状态和性能也会对裂纹产生起到影响。
例如,设备的润滑状态不良、设备磨损严重、设备结构设计不合理等都有可能导致应力集中,从而形成裂纹。
模锻件开裂原因

模锻件开裂原因模锻件开裂的背景和重要性模锻是一种重要的金属成形工艺,广泛应用于航空、汽车、船舶等领域。
然而,模锻件在生产过程中常常会出现开裂问题,这给工业生产带来了严重的经济损失和安全隐患。
因此,了解模锻件开裂的原因及其防范措施对于提高生产质量、降低生产成本具有重要的意义。
模锻件开裂的常见原因1. 材料因素模锻件开裂的一个主要原因是材料的性能不合理或材料质量不达标。
材料的选择应考虑到其热处理能力、塑性变形能力以及抗疲劳性能等。
如果材料的塑性变形能力不足,容易导致应力集中和应力过高,从而引发开裂。
此外,材料中的夹杂物和非金属夹杂物也会导致开裂,因为它们会成为内部的应力集中点。
2. 工艺因素工艺因素是模锻件开裂的主要原因之一。
不正确的锻造温度、锻造速度、锻造压力等参数都会导致模锻件的开裂。
过高的锻造温度和不足的锻造速度会导致过大的变形应力,从而引发开裂。
此外,如果锻造模具的形状和尺寸不合理,也容易导致开裂。
3. 模具设计因素模具设计是模锻件开裂的另一个重要因素。
模具的结构、尺寸以及表面处理对于模锻件的质量和开裂情况起着至关重要的作用。
如果模具的孔径设计过小或者过大,都会导致模锻件的应力不均匀,从而引发开裂。
另外,模具表面的磨损和腐蚀也会对模锻件的质量产生不利影响。
模锻件开裂的防范措施1. 合理选择材料在模锻件的生产过程中,应根据不同的要求选择合适的材料。
材料应具有足够的塑性变形能力和抗疲劳性能,以减少开裂的风险。
同时,应控制材料中的夹杂物和非金属夹杂物的含量,以避免其成为内部应力的集中点。
2. 优化工艺参数合理的工艺参数对于减少模锻件的开裂问题至关重要。
应选择适当的锻造温度、锻造速度和锻造压力,以保证模锻件的变形应力处于可控范围内。
此外,应根据模具的实际情况进行参数的调整和优化,确保模锻件的成形质量。
3. 合理设计模具模具的设计直接影响着模锻件的质量和开裂情况。
应根据模锻件的形状和尺寸合理设计模具,避免模具孔径过小或过大造成应力的集中。
锻件产品缺陷分析及防止方法
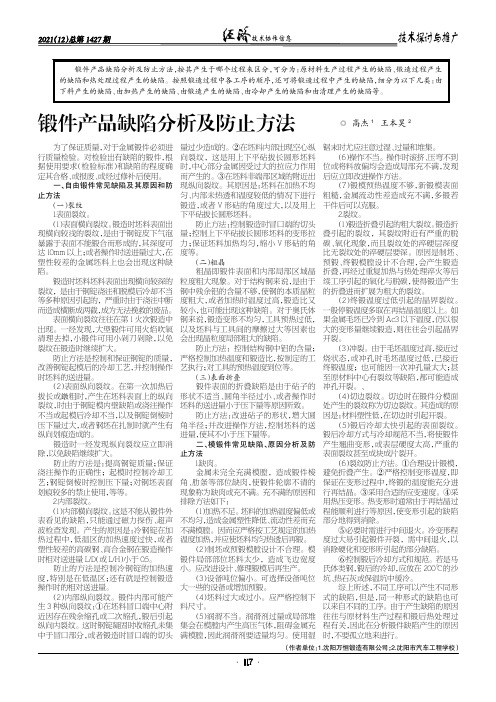
(作者单位:1.沈阳万恒锻造有限公司;2.沈阳市汽车工程学校)锻件产品缺陷分析及防止方法◎高杰1王本昊2为了保证质量,对于金属锻件必须进行质量检验。
对检验出有缺陷的锻件,根据使用要求(检验标准)和缺陷的程度确定其合格、或报废、或经过修补后使用。
一、自由锻件常见缺陷及其原因和防止方法(一)裂纹1.表面裂纹。
(1)表面横向裂纹。
锻造时坯料表面出现横向较浅的裂纹,是由于钢锭皮下气泡暴露于表面不能锻合而形成的,其深度可达10mm 以上;或者操作时送进量过大,在塑性较差的金属坯料上也会出现这种缺陷。
锻造时坯料坯料表面出现横向较深的裂纹,是由于钢锭浇注和脱模后冷却不当等多种原因引起的,严重时由于浇注中断而造成横断成两截,成为无法挽救的废品。
表面横向裂纹往往在第1火次锻造中出现。
一经发现,大型锻件可用火焰吹氧清理去掉,小锻件可用小剁刀剁除,以免裂纹在锻造时继续扩大。
防止方法是控制和保证钢锭的质量,改善钢锭起模后的冷却工艺,并控制操作时坯料的送进量。
(2)表面纵向裂纹。
在第一次加热后鐓拔长或粗时,产生在坯料表面上的纵向裂纹,时由于钢锭模内壁缺陷或浇注操作不当或起模后冷却不当,以及钢锭倒棱时压下量过大,或者钢坯在扎制时就产生有纵向划痕造成的。
锻造时一经发现纵向裂纹应立即消除,以免缺陷继续扩大。
防止的方法是:提高钢锭质量;保证浇注操作的正确性;起模时控制冷却工艺;钢锭倒棱时控制压下量;对钢坯表面划痕较多的禁止使用,等等。
2.内部裂纹。
(1)内部横向裂纹。
这是不能从锻件外表看见的缺陷,只能通过磁力探伤、超声波检查发现。
产生的原因是:冷钢锭在加热过程中,低温区的加热速度过快,或者塑性较差的高碳钢、高合金钢在锻造操作时相对送进量L/D (或L/H )小于0.5。
防止的方法是控制冷钢锭的加热速度,特别是在低温区;还有就是控制锻造操作时的相对送进量。
(2)内部纵向裂纹。
锻件内部可能产生3种纵向裂纹:①在坯料冒口端中心附近因存在残余缩孔或二次缩孔,锻后引起纵向内裂纹。
锻造裂纹的分析与防治研究

锻造裂纹的分析与防治研究裂纹是当前影响锻造生产发展和锻件质量的突出问题,也是锻造行业研究讨论的热点、难点课题。
随着科技的进步、社会经济的发展,新机器、新材料广泛应用,锻造中的新问题也不断涌现,比如高合金钢应用逐年增多,锻造裂纹频发也进一步突现,有的已经成为制约锻造生产发展的关键,引起了锻造厂家的普遍关注。
1 锻造裂纹特征、产生的原因传统的力学与材料学理论都认为裂纹由形核、扩展、微裂纹聚合直至断裂,是一个不可逆的热力学过程。
根据现有理论,在大型锻件的生产、使用、维护,乃至损伤容限评估等各方面,人们都假定微裂纹发展的必然趋势就是断裂。
实际上,任何成份与结构不均质,包括含微裂纹 ) 的材料,在热力学许可的条件下,都将趋于均匀化,这也同样是热力学的基本原理。
锻造裂纹的宏观特征 : 裂纹主要出现在锻造侧面的弧形处,裂纹比较粗大,一般以多条、多种特征的形式存在,无明显细尖端,比较圆钝,无明显的方向性,有时会出现一些较细的锻造裂纹。
肉眼可见裂纹走向基本都始于锻造面,呈垂直状或螺旋状向另一侧延伸,甚至有些锻造裂纹贯穿上下锻造面。
热处理裂纹的宏观特征: 裂纹刚健挺直,呈穿晶分布,起始点较宽,尾部细长曲折,常发生在工件的棱角槽口、截面突变处。
锻造过程 ( 包括加热、冷却 ) 中裂纹的产生与金属的受力情况、组织结构、变形温度和变形速度等有关。
除了工具给予工件的作用外,还有变形不均匀和变形速度不同引起的附加应力、温度不均匀引起的热应力和组织转变不同产生的组织应力。
金属的组织结构是裂纹产生和扩展的内部依据 ; 应力状态、变形速度和变形温度是裂纹产生和扩展的外部条件,通过对金属组织和微观机制的影响而对裂纹的发生和扩展发生作用。
4 修复内裂表明的原理和方法超声波探伤表明,大锻件内部存在裂纹与类孔隙缺陷是造成废品的重要原因,其中多数是由于坯料内部存在有疏松、夹杂物、粗晶和裂纹。
它们由于局部的不均匀变形,在巨大的集中应力和剪应力作用下,导致难以锻合、压实和生成变形损伤。
铸造裂纹产生的原因和避免的措施

铸造裂纹产生的原因和避免的措施铸造是一种重要的金属成型工艺,广泛应用于汽车、航空、航天、军工等领域。
然而,铸造件在生产中常常会出现裂纹缺陷,导致产品质量下降,甚至造成安全事故。
本文将就铸造裂纹的产生原因和避免措施进行简要介绍。
铸造裂纹产生的原因铸造裂纹主要有以下几个原因。
1. 材料缺陷铸造材料在生产过程中,常常会出现缺陷,如气孔、夹杂、杂质等,这些缺陷会在铸造冷却过程中形成应力集中区域,导致裂纹的产生。
2. 铸造工艺不合理铸造工艺不合理也是造成铸造件裂纹的重要原因。
如浇口不当、冷却不均、浇注速度过快等,都会导致铸造件的应力不均匀,从而形成裂纹。
3. 设计不合理铸造件的设计也会影响裂纹的产生。
当设计不合理时,会使铸造件应力分布不均匀,从而形成裂纹。
4. 环境因素环境因素也可能导致铸造件裂纹的产生。
如温度过高或过低、环境湿度过高、风力过大等,都会影响铸造件的冷却速度,从而形成裂纹。
避免铸造裂纹的措施为了避免铸造裂纹的产生,我们可以采取以下措施。
1. 优化材料在生产过程中,对铸造材料进行优化,去除缺陷,可以有效减少铸造裂纹的产生。
2. 检查工艺在生产过程中,对铸造工艺进行检查,保证浇口、浇注速度等符合要求,可以有效减少铸造件裂纹的产生。
3. 合理设计设计时要考虑到铸造件内部的应力分布,合理设计无疑可以减少铸造裂纹的产生。
4. 控制环境在铸造过程中,要控制环境温度、湿度和风力等因素,使铸造件冷却均匀,从而减少裂纹的产生。
结语本文介绍了铸造裂纹的产生原因和避免措施。
铸造件裂纹的产生很大程度影响了铸造件的质量和使用寿命,因此,为了提高产品质量,我们必须采取措施避免铸造裂纹的产生。
锻造和热处理过程中裂纹形成原因分析

锻造和热处理过程中裂纹形成原因分析摘要:在锻造以及热处理中极易出现裂纹,为此锻造以及热处理过程中的裂纹处理成为各个学者研究的重点,同时,构件尺寸、材质等之间的差异其所出现的裂纹几率也各不相同,基于此,本文通过对锻造以及热处理缺陷的相关分析,找出了锻造和热处理过程中裂纹形成的原因并提出了针对性的解决意见。
关键词:锻造热处理裂纹原因分析处理引言作为锻造以及热处理过程中最为常见的缺陷之一,裂纹的形成严重制约了锻造效率,并且对于大型锻件而言,其裂纹出现的几率则更高,所以加强对裂纹形成的原因分析对于减少裂纹产生,提升锻造效果具有重要意义。
1锻造缺陷与热处理缺陷第一,过热或者过烧。
具体表现形式为晶粒粗大并具有较为明显的魏氏组织;而造成过烧的情况则说明热处理过程中温度较高,断口晶粒凹凸不平,缺乏金属光泽,并且晶界周围具有氧化脱碳的情况;第二,锻造裂纹。
主要出现在组织粗大且应力较为集中处,裂纹内部往往呈现氧化皮情况。
在锻造过程中无论是温度过高,还是过低均会导致裂纹的出现;第三,折叠。
由于切料、冲孔、锻粗糙等原因而致使材料表面发生了缺陷,而此时一旦经过锻造自然其会由于表面氧化皮缺陷内卷而形成折叠。
通过显微镜的观察可以明显的发现折叠周围的脱碳情况较为严重;第四,淬裂。
该缺陷的明显特征就是刚健挺直且起始点较宽,尾部则细长曲直。
由于此缺陷往往是产生在马氏体转变发生以后,所以裂纹周围与其他区域没有明显的差别且无脱碳情况;第五,软点。
造成此种缺陷的原因主要是由于加热不足,保温时间不足而造成冷却不均匀导致的。
2实验方法2.1试样制备和宏观观察在开始试验之前只需要对构件毛坯裂纹进行简单的宏观观测并选择要进行实验的区域即可。
然后,在利用手边的工具来队选取的区域进行切割,需注意的是,切割方向必须要垂直镜像,切割长度要低于10mm。
可以通过多种方式进行取样但是一定要科学的选择取样的温度以及环境,如果实验温度较高,则可以通过凉水来进行冷却,进而防止在取样过程中构件内部结构遭到损坏。
轴锻件裂纹的措施

轴锻件裂纹的措施1. 引言轴锻件是机械传动装置中常用的重要零部件,其性能直接影响着设备的使用寿命和安全性。
然而,由于制造工艺、材料性能和使用差错等因素,轴锻件在使用过程中常常会出现裂纹的问题。
轴锻件的裂纹不仅会降低零部件的承载能力,还可能导致零部件的破坏性破裂。
因此,采取有效的措施来解决和预防轴锻件裂纹问题具有重要意义。
2. 形成裂纹的原因轴锻件裂纹的形成原因较为复杂,主要包括以下几个方面:2.1 制造工艺不当在制造过程中,如果对轴锻件的材料选择、加热温度和时间控制、锻造工艺参数等方面存在问题,就容易在零部件中形成内部缺陷,从而导致裂纹的形成。
2.2 材料性能不理想轴锻件的材料性能直接决定了其承载能力和抗裂纹能力。
如果选用的材料存在成分不均匀、夹杂物过多、强度不够等问题,则容易导致轴锻件在使用阶段产生裂纹。
2.3 使用及维护不当在使用和维护过程中,如果没有按照正确的方法和要求来操作,例如超负荷使用、频繁冲击加载、没有定期进行润滑和检查等,都可能加剧轴锻件的疲劳破坏,从而形成裂纹。
3. 解决轴锻件裂纹问题的措施针对轴锻件裂纹问题的原因,我们可以采取以下措施来解决和预防:3.1 加强制造工艺控制在轴锻件的制造过程中,应加强对材料选择、加热温度和时间控制、锻造工艺参数等方面的控制。
通过优化制造工艺,可以减少轴锻件内部的缺陷和应力集中,从而降低裂纹的形成概率。
3.2 提高材料质量选用具有良好材料性能的材料,提高轴锻件的抗拉强度和韧性,从而增加轴锻件的抗裂纹能力。
3.3 加强使用和维护管理在使用和维护过程中,要按照正确的方法和要求来操作,避免超负荷使用、频繁冲击加载等不合理的操作方式。
另外,要定期进行润滑和检查工作,及时发现和处理存在的问题,避免因疏忽而导致轴锻件裂纹的形成。
3.4 定期进行非破坏性检测为了及时发现轴锻件中的裂纹,可以定期进行非破坏性检测。
通过超声波、磁粉检测等技术手段,可以对轴锻件进行全面的检测,及时发现和处理存在的裂纹问题。
锻件常见缺陷裂纹的原因

锻件常见缺陷裂纹的原因锻件常见缺陷裂纹的原因有很多,主要包括以下几个方面:1. 锻造前材料的缺陷:锻造前原材料中可能存在着各种缺陷,如夹杂物、气孔、夹渣等。
这些缺陷会在锻造过程中被拉长、扭曲或剪切,最终导致锻件出现裂纹。
2. 异常冷却方式:锻件在冷却过程中,如果冷却速度过快或不均匀,会导致锻件内部产生应力集中,从而引发裂纹。
尤其是在大尺寸、复杂形状的锻件中,由于其冷却速度不均匀,容易出现内部裂纹。
3. 冷、热变形不均匀:锻造过程中,如果材料的冷、热变形不均匀,会导致锻件内部应力分布不均匀,从而引发裂纹的产生。
尤其是在复杂形状、壁厚不一的锻件中,易出现材料贫化、过冷区和高应力区,容易引发裂纹。
4. 锻造温度过低或过高:锻造温度是影响锻件质量的关键因素之一。
如果温度过低,会导致材料的硬化能力不足,易发生塑性变形困难,从而引发裂纹;而温度过高,则会导致材料的焊接性能下降,也容易引发裂纹。
5. 压力不均匀:锻造过程中,如果锻压力不均匀,会使锻件中的应力分布不均匀,从而容易产生应力集中和裂纹。
尤其是在薄壁锻件中,容易出现锻压力不均匀的问题,导致裂纹的发生。
6. 锻件设计不合理:锻件的设计是影响锻件质量的重要因素之一。
如果锻件的形状、结构设计不合理,容易导致应力集中,从而引发裂纹的产生。
尤其是在复杂形状、尺寸大的锻件中,设计不合理会增加裂纹发生的概率。
7. 热处理不当:热处理是锻件制造过程中的关键环节,如果热处理不当,会导致锻件中的应力不释放或释放不充分,从而引发裂纹。
此外,热处理时的温度、时间等参数也需要合适,否则也可能导致裂纹的产生。
这些都是导致锻件常见缺陷裂纹的主要原因。
为了降低或避免裂纹的产生,需要从原材料选用、工艺控制、设备维护等方面做好控制和管理。
同时,制定合理的锻造工艺和热处理工艺,合理设计锻件形状和结构,对裂纹的产生起到有力的控制和避免作用。
还需要加强工作人员的培训和技能提升,提高他们的专业水平和质量意识,从而减少裂纹缺陷的发生,提高锻件的质量。
锻造裂纹产生的原因及解决 方法

锻造裂纹产生的原因及解决方法锻造裂纹产生的原因及解决方法2011-04-2509:28裂纹是锻压生产中常见的主要缺陷之一,通常是先形成微观裂纹,再扩展成宏观裂纹。
锻造工艺过程(包括加热和冷却)中裂纹的产生与受力情况、变形金属的组织结构、变形温度和变形速度等有关。
锻造工艺过程中除了工具给予工件的作用力之外,还有由于变形不均匀和变形速度不同引起的附加应力、由温度不均匀引起的热应力和由组织转变不同时进行而产生的组织应力。
应力状态、变形温度和变形速度是裂纹产生和扩展的外部条件;金属的组织结构是裂纹产生和扩展的内部依据。
前者是通过对金属组织及对微观机制的影响而对裂纹的发生和扩展发生作用的。
全面分析裂纹的成因应当综合地进行力学和组织的分析。
(一)形成裂纹的力学分析在外力作用下物体内各点处于一定应力状态,在不同的方位将作用不同的正应力及切应力。
裂纹的形式一般有两种:一是切断,断裂面是平行于最大切应力或最大切应变;另一种是正断,断裂面垂直于最大正应力或正应变方向。
至于材料产生何种破坏形式,主要取决于应力状态,即正应力σ与剪应力τ之比值。
也与材料所能承受的极限变形程度εmax及γmax有关。
例如,①对于塑性材料的扭转,由于最大正应力与切应力之比σ/τ=1是剪断破坏;②对于低塑性材料,由于不能承受大的拉应变,扭转时产生45°方向开裂。
由于断面形状突然变化或试件上有尖锐缺口,将引起应力集中,应力的比值σ/τ有很大变化,例如带缺口试件拉伸σ/τ=4,这时多发生正断。
下面分析不同外力引起开裂的情况。
压力加工生产中,在下列一些情况,由外力作用可能引起裂纹:弯曲和校直、脆性材料镦粗、冲头扩孔、扭转、拉拔、拉伸、胀形和内翻边等,现结合几个工序说明如下。
弯曲件在校正工序中(见图3-34)由于一侧受拉应力常易引起开裂。
例如某厂锻高速钢拉刀时,工具的断面是边长相差较大的矩形,沿窄边压缩时易产生弯曲,当弯曲比较严重,随后校正时常常开裂。
锻造和热处理过程中裂纹形成原因分析李艳梅

锻造和热处理过程中裂纹形成原因分析李艳梅发布时间:2021-07-28T10:12:15.580Z 来源:《基层建设》2021年第13期作者:李艳梅[导读] 摘要:在锻造和热处理过程中,裂纹是非常常见的,不可能在所有的锻造和热处理过程中避免裂纹。
惠阳航空螺旋桨有限责任公司河北保定 071000摘要:在锻造和热处理过程中,裂纹是非常常见的,不可能在所有的锻造和热处理过程中避免裂纹。
这使得裂纹成为锻造行业讨论的焦点。
裂纹的发生概率、类型和形状因部件的尺寸和纹理而异。
关键词:锻造;热处理;晶相分析;裂纹形成原因;裂纹是在锻造和热处理生产过程中常见的缺陷之一,通过对裂纹产品试样进行收集、分析、整理,可将裂纹大致分为三类:锻造裂纹、折叠和淬火裂纹。
通过晶相实验分析,可获得三种类型裂纹的形成原因,有针对性的提出减少裂纹产生的建议性措施,从而提高产品的质量和性能。
一、锻造缺陷和热处理的缺陷1.过热和燃烧。
主要特点是谷物粗犷,具有明显的维氏结构。
过热表明加热温度高,碎粒粗糙不均匀,没有金属光泽,晶界周围存在氧化和脱碳现象。
2.钻孔裂纹。
通常发生在结构粗糙、应力集中或合金元素分离的地方,裂纹通常充满氧气槽。
钻孔温度高或终端温度低时容易出现裂纹。
另一种裂纹是通过喷水进行钻孔和冷却后形成的。
3.折叠起来。
曲面缺陷是由冲压、切削、切削板磨损、粗糙钻孔等引起的。
在随后的钻孔中,曲面比例等缺陷被包含在钻孔主体中以形成折弯。
当用显微镜观察时,你可以看到折痕周围有明显的渗碳现象。
4.淬裂。
其特点是强而直的颗粒间分布,起点广,尾巴薄而曲折。
此类裂纹主要发生在马氏体改造后,因此裂纹周围的微观结构明显与其他区域没有区别,没有渗碳现象。
5.软点。
微观结构由大块或星形托洛茨坦和未溶解的铁氧体组成。
供暖不足、维护时间不足和冷却不均衡都将导致薄弱环节。
二、实验的方法1.取样准备和宏观观察。
首先宏观观察杆的裂纹,然后手工切割试样,方向垂直于径向方向,长度小于8 mm。
铸造裂纹产生的原因和避免的措施

在所有的铸造缺陷中,对产品质量影响最大的是铸造裂纹,按照其特征可将其分为热裂纹和冷裂纹,它们是不允许存在的缺陷。
(1)热裂纹热裂纹是铸件在凝固末期或凝固结束后不久,铸件尚处于强度和塑性都很低的高温阶段,形成温度在1250~1450℃,因铸件固态收缩受阻而引起的裂纹。
热裂纹的主要特征有:•在晶界萌生并沿晶界扩展,形状粗细不均匀、曲折不规则;•通常呈龟裂的网状;•裂纹的表面呈氧化色,无金属光泽,铸钢件裂纹表面呈近似黑色;•裂纹末端圆钝,两侧有明显的氧化和脱碳,有时有明显的疏松、夹杂、孔洞等缺陷。
按照热裂纹在铸件中的形成位置,又可将其分为外裂纹和内裂纹。
•在铸件表面可以看到的热裂纹为外裂纹,外裂纹常产生在铸件的拐角或局部凝固缓慢、容易产生应力集中的位置,其特征是:表面宽,心部窄,呈撕裂状,有时断口会贯穿整个铸件断面。
•内裂纹一般发生在铸件内部最后凝固的部位,其特征是:形状不规则,裂纹面常伴有树枝晶。
通常情况下,内裂纹不会延伸到铸件表面,内裂纹的一个典型例子是冒口切除后根部所显露的裂纹。
热裂纹的形成原因可归纳为:1.浇铸冷却过程中收缩应力过大;2.铸件在铸型中收缩受阻;3.铸件冷却不均匀;4.铸件结构设计不合理,存在几何尺寸突变;5.有害杂质在晶界富集;6.铸件表面与涂料之间产生了相互作用。
(2)冷裂纹冷裂纹是铸件凝固结束后继续冷却到室温的过程中,因铸件局部受到的拉应力大于铸件本体的破断强度而引起的开裂。
冷裂纹的主要特征有:1.总是发生在承受拉应力的部位,特别是铸件形状、尺寸发生变化的应力集中部位;2.裂纹宽度均匀、细长,呈直线或折线状,穿晶扩展;3.裂纹面比较洁净、平整、细腻,有金属光泽或呈轻度氧化色;4.裂纹末端尖锐,裂纹两侧基本无氧化和脱碳,显微组织与基体的基本相同。
冷裂纹产生的原因,可归纳为:1.铸件结构系统设计不合理,铸件壁厚不均匀会导致铸造应力,有时会产生冷裂纹,刚性结构的铸件,由于其结构的阻碍,温度降低导致的收缩应力容易使铸件产生冷裂纹,薄壁大芯、壁薄均匀的铸件非常容易产生冷裂纹;2.浇冒口系统设计不合理,对于壁厚不均匀的铸件,如果内浇口设置在铸件的厚壁部分时,将使铸件厚壁部分的冷却速度更加缓慢,导致或加剧铸件各部分冷却速度的差别,增大了铸造热应力,容易使铸件产生冷裂纹,浇冒口位置设计不当时,也会直接阻碍铸件收缩,使铸件容易产生冷裂纹;3.型砂或型芯的强度太高,高温退让性差,或舂砂过紧,使铸件收缩受到阻碍,产生很大的拉应力,导致铸件产生冷裂纹;4.钢的化学成分不合格,有害元素磷含量过高,使钢的冷脆性增加,容易产生冷裂纹5.铸件开箱过早,落砂温度过高,或者在清砂时受到碰撞、挤压等都会引起铸件的开裂。
锻造裂纹的原因分析及预防措施

锻造裂纹的原因分析及预防措施
φ288mm冷轧辊尾部锻造裂纹
锻件成形及缺陷位置示意图
该件产品用1.75吨钢锭出3件产品,成形情况 及缺陷出现位置如图示
应力状态如图示
防止裂纹再次产生的措施
从冶炼的角度讲,应从提高钢锭头尾部的冶金质量, 即提高钢的纯净度和细化晶粒、均匀结晶组织的角 度出发,改善冶炼条件,提高头尾部的可锻性;
从锻压方面讲,应从应力状态和减小锤击力出发, 即避免产生轴心径向拉应力和减小变形程度的方面 做文章,避免裂纹的产生。打击辊颈时,送进量应 限制在坯料直径的0.5~0.8倍之间,避免拔长辊颈时 出现径向展宽现象,既提高了拔长效率,又避免轴 心的径向拉应力。另外,限制锤的打击力,尽可能 在两吨锤上成形,并选择合适的压下量,以减轻心 的变形程度。两方面入手,以避免裂纹的产生。
说明
以上观点仅为个人看法。
头 1
尾
2
3
裂纹形成原因分析
首先我们看缺陷产生的部位,在钢锭的头尾端。而 钢锭锭身却很少出现缺陷,钢锭的头尾部的冶金质 量不如锭身也是我们的共识,这应是裂纹产生的本 质上的原因。
其次,辊身与辊颈的台阶差较大。辊身的直径为 288mm,裂纹端辊颈才100mm,台阶差188。变形 过程中有两方面问题要说,一方面下圆弧砧的圆弧 大,击打辊颈时,近似于平砧,即料侧面未受力。 砧宽为250mm,若送进量过大,对于辊颈而言,轴 向拔长就变成了径向展宽,即应力状态为轴心径向 拉应力(如下图示),容易产生轴心纵向裂纹;另 一方面,因辊身与辊颈的台阶差大,操作时可能重 锤打击,造成心部变形量过大。头尾料差的塑性与 低的强度加之径向拉应力和重锤就可能导致裂纹的 产生,这应是裂纹产生的外因。
模锻在锻造过程中缺陷及预防措施

模锻在锻造过程中缺陷及预防措施引言模锻是一种常见的金属锻造工艺,具有高效、高精度的特点。
然而,在模锻过程中,由于各种因素的影响,常常会出现一些缺陷。
本文将详细介绍模锻过程中常见的缺陷及其预防措施,旨在帮助读者更好地理解模锻工艺,提高产品质量。
1. 毛刺毛刺是模锻过程中常见的缺陷之一,主要表现为锻件表面出现不规则的突起。
毛刺的产生主要与模具设计、焊缝准备不当、材料不合理等因素有关。
1.1 模具设计在模锻过程中,模具的设计起着至关重要的作用。
合理的模具设计可以减少毛刺的发生。
首先,要确保模具的表面光洁度,在模具表面涂覆一层光滑的润滑剂,减少锻件与模具的摩擦。
其次,要注意模具的边缘处理,采用倒角或圆弧等设计,减少锻件与模具接触时的边缘压力。
1.2 焊缝准备毛刺的另一个常见原因是焊缝准备不当。
焊缝处存在不均匀的应力分布,这会导致焊缝周围的材料在锻造过程中容易形成毛刺。
为了解决这个问题,我们可以通过提前进行焊缝的减薄和均匀化处理,确保焊缝处的应力分布更加均匀。
1.3 材料选择材料的选择对模锻过程中毛刺的发生起着重要作用。
某些材料在模锻时容易形成毛刺,这主要是因为其表面粗糙度较高或锻造温度过高。
合理选择材料,并严格控制锻造温度,可以有效预防毛刺的产生。
2. 气孔气孔是模锻过程中另一个常见的缺陷,主要由于锻件内部存在气体残留或吸附气体进入而引起。
气孔不仅影响锻件的外观质量,还会降低其力学性能。
2.1 真空处理为了减少气孔的产生,可以在模锻过程中采用真空处理技术。
真空处理可以有效地去除锻件内部的气体,减少气孔的形成。
在真空处理前,应注意确保锻件表面的净度,减少对气孔形成的影响。
2.2 材料处理合理的材料处理也是减少气孔的重要措施。
材料在模锻前,可以通过热处理、脱气等方式减少内部气体的含量。
同时,在材料的选择上,应尽量选择低气孔率的材料,以减少气孔的形成。
2.3 控制锻造参数控制锻造参数是减少气孔形成的关键。
首先,要合理控制锻造温度,确保材料能充分熔化并排出内部的气体。
锻造开裂原因

锻造开裂原因
锻造开裂的原因可能有多种,以下是一些主要原因:
1. 原材料质量问题:原材料中可能存在的毛细裂纹、折叠、非金属夹杂物过多、碳化物偏析、异金属夹杂物、气泡、柱状晶体粗大、轴心晶间裂纹、粗晶环等缺陷,在锻造工序都可能引发锻造裂纹。
2. 锻造工艺不当:在锻造过程中,如果下料、加热、锻压、冷却及清理等环节出现不当操作,也可能导致锻件开裂。
3. 温度控制不当:在加热和冷却过程中,如果温度控制不当,可能导致材料内部应力过大,从而引发开裂。
4. 材料应力集中:如果锻件存在应力集中区域,如尖角、截面突变处,在应力超过材料承受能力时,可能导致开裂。
5. 锻造变形不当:如果变形速度太大,钢的塑性不足以承受形压力而引起的破裂。
6. 淬火裂纹:淬火裂纹往往是在马氏体转变开始进行后不久产生的,裂纹的分布则没有一定的规律,但一般轻易在工件的尖角、截面突变处形成。
铸造裂纹的产生原因及种类

铸造裂纹的产生原因及种类铸造裂纹是指在铸造过程中,金属在凝固过程中出现的断裂缺陷。
它不仅会降低铸件的质量,还可能导致铸件的完全失效。
由于铸造裂纹的严重性,铸造厂必须采取一系列的措施来预防和控制裂纹的产生。
造成铸造裂纹的原因可以归结为以下几个方面:1.冷却速度过快:当金属液凝固的速度过快时,会导致铸件内部的应力积累,从而引发裂纹的产生。
这种裂纹被称为凝固裂纹。
2.热应力:当金属凝固收缩时,会产生内应力。
如果金属的强度不足以抵抗这种应力,就会发生裂纹。
3.不合理的铸造工艺:铸造过程中,如果温度、压力、冷却速度等参数的控制不当,也会导致铸造裂纹的产生。
4.金属含气量过高:金属中的气体,如氢、氧等,会导致金属的脆性增加,从而促使裂纹的产生。
5.内部缺陷:如果金属液中存在一定数量的夹杂物,如氧化物、硫化物等,也会导致裂纹的产生。
根据裂纹的形态和位置,铸造裂纹可以分为以下几种类型:1.凝固裂纹:凝固裂纹是指在金属凝固过程中形成的裂纹。
这种裂纹通常沿铸件的凝固方向延伸,形成内部裂纹。
2.热裂纹:热裂纹是指在金属冷却过程中形成的裂纹。
它通常发生在冷却速度不均匀的地方,如夹套液化井。
3.收缩裂纹:收缩裂纹是由于金属凝固收缩引起的内部应力积累。
这种裂纹通常发生在壁厚不均匀或设计不当的部位。
4.弯曲裂纹:弯曲裂纹是由于金属内部应力过大,导致铸件变形和裂纹的产生。
5.炸裂:炸裂是指由于金属液中的气体等不可溶性物质在铸件内部聚集形成气泡,而导致持续增大的内部压力,最终引发铸件的炸裂。
为了预防和控制铸造裂纹的产生,铸造厂需要采取一系列的措施:1.优化铸造工艺:合理控制金属的浇注温度、冷却速度等参数,确保金属在凝固过程中的均匀收缩。
2.提高金属质量:通过优化金属的成分和处理工艺,降低金属中的夹杂物和气体含量。
3.设计合理的铸件结构:合理设计铸件的壁厚和几何尺寸,避免出现应力集中的部位。
4.使用适当的冷却系统:采用高效的冷却系统,确保金属在冷却过程中获得均匀的温度分布。
连杆锻造裂纹的原因分析及纠正措施

连杆锻造裂纹的原因分析及纠正措施连杆是柴油机中重要的传动部件,由于受力复杂,要求具有良好的结构刚度和疲劳强度,以保证传动机构的可靠性。
柴油机连杆由于其重要性对原材料、锻压工艺及热处理要求都极为严格。
我公司开发的某型连杆在试制过程中,有三根连杆产生了表面裂纹。
本文通过宏观检验、金相分析、化学成分和硬度梯度分析,对裂纹产生的原因进行逐一排查,以避免类似的裂纹重复产生。
宏观检验三根连杆裂纹均产生于靠近大头端的分模面上。
裂纹的宏观形态为裂纹刚直,有次生裂纹产生,整体呈纵向分布。
裂纹整体与纤维流线重合,尾部较尖细。
根据连杆的剖切面,裂纹深度约10mm,属于裂纹的扩展造成。
金相分析在距加工区边缘约8mm处取样,见图1。
加工区一侧裂纹完整,与表面呈一定角度,深度约10mm,与锻造变形流线一致;而另一侧裂纹仅在次表层残留一小段,为裂纹的纵向尾部,见图2。
图1 裂纹分布形态图2 裂纹形态在未加工处制样后抛光状态观察,该处裂纹未贯穿连杆表面,距表面约0.2mm,见图3。
裂纹前端与表面呈大角度夹角,裂纹刚直,曲折分布,尾部较尖细,图3中残留裂纹尾部尖细,见图4。
腐蚀后观察,裂纹前端与连杆锻造纤维流线重合,未贯穿到连杆表面,见图5。
裂纹两侧无脱碳现象,前端较平直,中间部分有明显的曲折,尾部较尖细,两侧有较多氧化物,见图6。
残留裂纹的分布与连杆的带状组织一致,无脱碳现象,两头较尖细,见图7。
连杆基体组织为回火索氏体,而表层组织为细小均匀回火索氏体,见图8。
图3 裂纹靠表面处形态图4 裂纹尾部形态图5 裂纹靠表面处形态(腐蚀)图6 裂纹形态及组织图7 残留裂纹附近组织形态图8 连杆基体及表层组织由理化分析可知,连杆次表层组织基本为细针状马氏体回火组织,基体为板条状马氏体回火组织。
由于连杆表面有裂纹区域大部分已加工,取样位置位于裂纹的尾部,该处裂纹未贯穿表面,前端与纤维流线重合。
裂纹中部曲折,尾部较尖细,为典型的应力裂纹形态。
锻造和热处理过程中裂纹形成原因分析

锻造和热处理过程中裂纹形成原因分析发布时间:2021-05-20T10:33:30.803Z 来源:《基层建设》2020年第31期作者:裴一飞[导读] 摘要:裂缝很常见,生产过程往往是锻造和热处理过程。
航空工业哈尔滨飞机工业集团有限公司黑龙江哈尔滨 150000摘要:裂缝很常见,生产过程往往是锻造和热处理过程。
锻造裂纹通常在高温下发生,在锻造过程中会延伸并接触空气,形成裂纹中氧化的皮肤。
此框形成的裂纹不仅厚而且多,裂纹的两端不相连,尖端相对圆。
所处理的裂纹的形状和性能与锻造裂纹不同。
出现热处理后的裂纹是因为加热时该元素出现裂纹,导致在裂纹的咸晶方向上脱碳,最终结构比锻造裂纹厚。
对于和零件尤其如此本文收集了大量裂缝方式,分析总结了裂缝的原因。
最后,裂缝分为三类。
关键词:锻造、热处理;裂纹形成原因;过程;存在缺陷;前言裂纹是锻造和热处理中常见的缺陷之一,也是锻造行业中的热点和难点。
但是,锻造零件产生裂纹的可能性很大,因此必须研究锻造和热处理过程中的裂纹,并分析裂纹的原因。
一、锻造缺陷与热处理缺陷过热燃烧。
过度燃烧意味着加热温度高,切割机又大又不均匀,没有金属光泽,玻璃周围有氧化和渗碳。
造成裂缝。
当锻造温度较高或最终温度较低时,容易产生裂纹。
另一个裂缝是在水的钻井和冷却后形成的。
缩小范围。
表面缺陷是冲压、切割、板材磨损、穿孔等造成的。
在随后的钻孔中,观察到锻造体中存在表面氧化等缺陷以形成折弯。
通过显微镜观察,你可以看到弯曲周围明显的碳流失。
过火裂缝。
这些裂缝大多发生在MCU改造后,因此裂缝周围的微观结构与其他区域没有显着差异,也没有渗碳。
二、实验方法1.试样制备和宏观观察在试验前的第一阶段,只需对所选杆的工件裂纹进行宏观观察,在观察过程中,选择要测量的区域。
下一步是手动剪切选定区域,使其垂直于镜像且长度小于10 mm。
采样方法可能会有所不同,但在采样时必须选择温度和环境。
如果样品温度过高,可以使用冷水冷却样品,以免由于样品在回收过程中过热而改变事件的内部组织。
- 1、下载文档前请自行甄别文档内容的完整性,平台不提供额外的编辑、内容补充、找答案等附加服务。
- 2、"仅部分预览"的文档,不可在线预览部分如存在完整性等问题,可反馈申请退款(可完整预览的文档不适用该条件!)。
- 3、如文档侵犯您的权益,请联系客服反馈,我们会尽快为您处理(人工客服工作时间:9:00-18:30)。
说明
以上观点仅为个人看法。
应力状态如图示
防止裂纹再次产生的措施
从冶炼的角度讲,应从提高钢锭头尾部的冶金质量, 即提高钢的纯净度和细化晶粒、均匀结晶组织的角 度出发,改善冶炼条件,提高头尾部的可锻性;
从锻压方面讲,应从应力状态和减小锤击力出发, 即避免产生轴心径向拉应力和减小变形程度的方面 做文章,避免裂纹的产生。打击辊颈时,送进量应 限制在坯料直径的0.5~0.8倍之间,避免拔长辊颈时 出现径向展宽现象,既提高了拔长效率,又避免轴 心的径向拉应力。另外,限制锤的打击力,尽可能 在两吨锤上成形,并选择合适的压下量,以减轻心 部的变形程度。两方面入手,以避免裂纹的产生。
锻造裂纹的原因分析及预防措施
φ288mm冷轧辊尾部锻造裂纹 Nhomakorabea锻件成形及缺陷位置示意图
该件产品用1.75吨钢锭出3件产品,成形情况 及缺陷出现位置如图示
头 1
尾
2
3
裂纹形成原因分析
首先我们看缺陷产生的部位,在钢锭的头尾端。而 钢锭锭身却很少出现缺陷,钢锭的头尾部的冶金质 量不如锭身也是我们的共识,这应是裂纹产生的本 质上的原因。