超声波于等轴晶
各种因素对铝合金超声波铸锭等轴晶占有率的影响
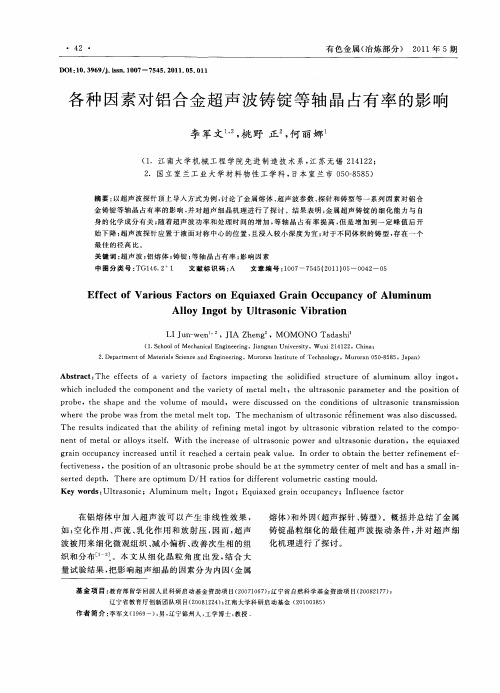
Ab t a t The fe t v re y f a t s m p c i he o i fe s r c u e f l m i m a l ng , sr c : e f c s of a a i t o f c or i a tng t s ldii d t u t r o a u nu loy i ot whih i l de he c m p ne n he v it t lme t h t a o c pa a e e nd t ston o c nc u d t o o nta d t are y ofme a l ,t e ulr s ni r m t r a he po ii f pr be,t ha e a t l o he s p nd he vo ume of mou d, we e d s us e o he c dii s of ulr s ni t a s s i n l r i c s d n t on ton t a o c r n mi so whe e t r r he p obewa r sf om hem e a e tt . The me ha s ofulr s i fne n salo dic s d. t t lm l op c nim t a on c r i me twa s s us e The r s t n c t d t t t biiy ofr fni t li go l r s ni br to e a e o t ompo e uls i dia e ha he a lt e i ng me a n t by u t a o c vi a i n r l t d t he c — n nto t lora l s is l.W ih t e i r a e o t a on c po r a d u t a o c d a i n,t q ax d e f me a loy t e f t h nc e s f ulr s i we n lr s ni ur to he e ui e gr i c up nc nc e s d u i tr a he e t i p a a ue I de o o an t t e e i e nte — an o c a y i r a e nt1i e c d a c r an e k v l . n or r t bt i he be t rr fn me f f c i e e s he p ii fa lr s ni o ho d be a he s m me r e e fme ta d ha ma li — e tv n s ,t oston o n u ta o cpr be s ul tt y t y c nt ro l n s a s l n
锻件与铸件超声波探伤详细教程(附实例解析)讲解
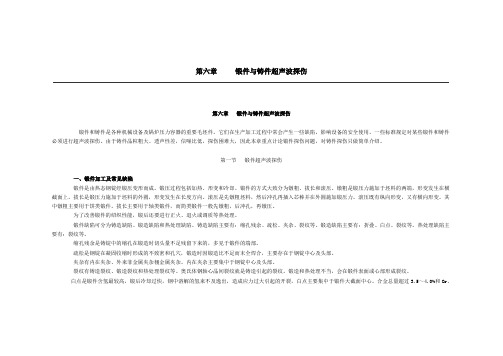
第六章锻件与铸件超声波探伤第六章锻件与铸件超声波探伤锻件和铸件是各种机械设备及锅炉压力容器的重要毛坯件。
它们在生产加工过程中常会产生一些缺陷,影响设备的安全使用。
一些标准规定对某些锻件和铸件必须进行超声波探伤。
由于铸件晶粒粗大、透声性差,信噪比低,探伤困难大,因此本章重点计论锻件探伤问题,对铸件探伤只做简单介绍。
第一节锻件超声波探伤一、锻件加工及常见缺陷锻件是由热态钢锭经锻压变形而成。
锻压过程包括加热、形变和冷却。
锻件的方式大致分为镦粗、拔长和滚压。
镦粗是锻压力施加于坯料的两端,形变发生在横截面上。
拔长是锻压力施加于坯料的外圆,形变发生在长度方向。
滚压是先镦粗坯料,然后冲孔再插入芯棒并在外圆施加锻压力。
滚压既有纵向形变,又有横向形变。
其中镦粗主要用于饼类锻件。
拔长主要用于轴类锻件,而简类锻件一般先镦粗,后冲孔,再镦压。
为了改善锻件的绍织性能,锻后还要进行正火、退火或调质等热处理。
锻件缺陷可分为铸造缺陷、锻造缺陷和热处理缺陷。
铸造缺陷主要有:缩孔残余、疏松、夹杂、裂纹等。
锻造缺陷主要有:折叠、白点、裂纹等。
热处理缺陷主要有:裂纹等。
缩孔残余是铸锭中的缩孔在锻造时切头量不足残留下来的,多见于锻件的端部。
疏松是钢锭在凝固收缩时形成的不致密和孔穴,锻造时因锻造比不足而末全焊合,主要存在于钢锭中心及头部。
夹杂有内在夹杂、外来菲金属夹杂栩金属夹杂。
内在夹杂主要集中于钢锭中心及头部。
裂纹有铸造裂纹、锻造裂纹和热处理裂纹等。
奥氏体钢轴心晶间裂纹就是铸造引起的裂纹。
锻造和热处理不当,会在锻件表面或心部形成裂纹。
白点是锻件含氢最较高,锻后冷却过快,钢中溶解的氢来不及逸出,造成应力过大引起的开裂,白点主要集中于锻件大截面中心。
合金总量超过3.5~4.0%和Cr、Ni、Mn的合金钢大型锻件容易产生白点。
白点在钢中总是成群出现。
二、探伤方法概述按探伤时间分类,锻件探伤可分为原材料探伤和制造过程中的探伤,产品检验及在役检验。
脉冲电流综述---PPT

6
2 脉冲电流凝固技术;
电流对液态金属主要有以下作用:电传输效应、Jouler 效应、Peltier 效应、起伏效应、趋肤 效应、电磁力效应、磁致收缩效应等。这些效应可以改变液体金属凝固时的传热、传质和动 量传输过程,进而影响金属的凝固组织及其形态和成分分布等。采用脉冲电流处理液态金属, 一方面可以减小电流细晶技术应用中电路负荷过大的问题,另一方面可减小电流在液态金属 中产生的焦耳热,并有效地利用脉冲电流对金属液的扰动作用。
5
20 世纪 80 年代,A.K.Mism 在 Pb—Sb—Sn 三元合金的凝固过程中使用了电流技术,通 过施加电流密度 30~40mA/cm2、电压约 30V 的直流电流,得到了均匀细小的凝固组织。 共晶片间距减小到原来的 1/4,共晶团数量增加,这说明电流对形核和生长两个阶段都有 作用。同样,把直流电流换成交流电流也可得到相同的结果(如图 2)。
图 5 为翟启杰等研究结果,表明超声波可细化 T10 钢凝固组织。在金属凝固过程中引入超 声振动,凝固组织从粗大的柱状晶变为均匀细等轴晶,金属的宏观及微观偏析均得到改善。
3 磁场在材料加工 磁场,与其它外场比较,有一个最大特点,即其非接触性,由于各相磁化率及介电常数不同, 相变中施加磁场,会影响各相稳定性,从而改变不同相的形貌,材料在磁场中的引入,最先 从普通磁场开始,并已进行了广泛的研究,目前,侧重于都材料在强磁场作用下的研究, 外加磁场包括稳恒、交变和脉冲磁场。用于细化金属凝固组织的方法主要包括外加交变磁场 和脉冲磁场。外加交变磁场即电磁搅拌,大量实践证明,电磁搅拌能细化金属凝固组织闭,
7
------试验研究中,研究者选择有代表性的试验金属,以求对其他金属有参考意义,从低熔点 到高熔点及单元单相到多元多相的原则,考虑工程实用性,对纯金属、二元合金和多元合金 都进行了探索性研究。 对纯金属,主要选择纯铝开展研究 对二元合金,主要选择低熔点、便于开展试验研究的 Pb—sn 合金和较高熔点、工业上广泛 应用的 A1-Si、A1-Cu 合金等结构材料开展研究 高熔点的高锰钢、碳钢、轴承钢、螺纹钢、电工钢、不锈钢和铸铁来开展研究
功率超声对纯铝凝固过程的影响及衰减特性分析
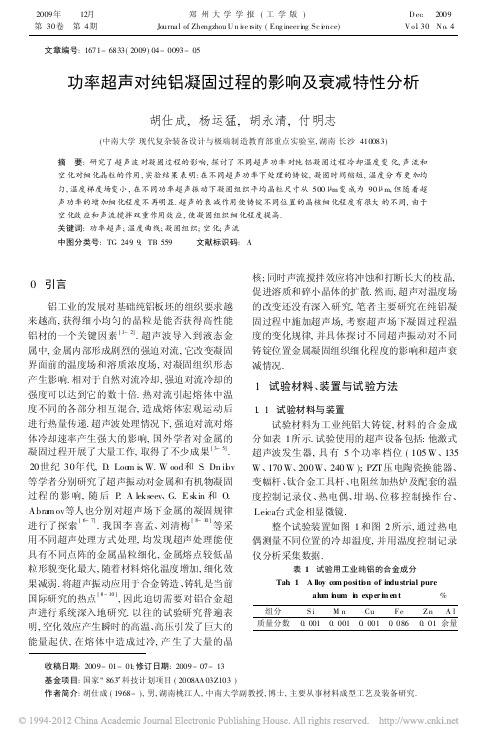
2009年 12月郑州大学学报(工学版)D ec 2009第30卷 第4期Journa l of Zhengzhou U n i ve rsity (Eng ineer i ng Sc i ence)V o l 30 N o 4收稿日期:2009-01-01;修订日期:2009-07-13 基金项目:国家 863 科技计划项目(2008AA 03Z103)作者简介:胡仕成(1968-),男,湖南桃江人,中南大学副教授,博士,主要从事材料成型工艺及装备研究.文章编号:1671-6833(2009)04-0093-05功率超声对纯铝凝固过程的影响及衰减特性分析胡仕成,杨运猛,胡永清,付明志(中南大学现代复杂装备设计与极端制造教育部重点实验室,湖南长沙410083)摘 要:研究了超声波对凝固过程的影响,探讨了不同超声功率对纯铝凝固过程冷却温度变化,声流和空化对细化晶粒的作用,实验结果表明:在不同超声功率下处理的铸锭,凝固时间缩短,温度分布更加均匀,温度梯度场变小,在不同功率超声振动下凝固组织平均晶粒尺寸从500 m 变成为90 m,但随着超声功率的增加细化程度不再明显.超声的衰减作用使铸锭不同位置的晶核细化程度有很大的不同,由于空化效应和声流搅拌双重作用效应,使凝固组织细化程度提高.关键词:功率超声;温度曲线;凝固组织;空化;声流中图分类号:TG 249.9,TB 559 文献标识码:A0 引言铝工业的发展对基础纯铝板坯的组织要求越来越高,获得细小均匀的晶粒是能否获得高性能铝材的一个关键因素[1-2].超声波导入到液态金属中,金属内部形成剧烈的强迫对流,它改变凝固界面前的温度场和溶质浓度场,对凝固组织形态产生影响.相对于自然对流冷却,强迫对流冷却的强度可以达到它的数十倍.热对流引起熔体中温度不同的各部分相互混合,造成熔体宏观运动后进行热量传递.超声波处理情况下,强迫对流对熔体冷却速率产生强大的影响,国外学者对金属的凝固过程开展了大量工作,取得了不少成果[3-5].20世纪30年代,D .Loo m is 、W.W ood 和S .Dn il o v 等学者分别研究了超声振动对金属和有机物凝固过程的影响,随后P .A lekseev 、G.E skin 和O.Abra m ov 等人也分别对超声场下金属的凝固规律进行了探索[6-7].我国李喜孟、刘清梅[8-10]等采用不同超声处理方式处理,均发现超声处理能使具有不同点阵的金属晶粒细化,金属熔点较低晶粒形貌变化最大,随着材料熔化温度增加,细化效果减弱.将超声振动应用于合金铸造、铸轧是当前国际研究的热点[8-10],因此迫切需要对铝合金超声进行系统深入地研究.以往的试验研究普遍表明,空化效应产生瞬时的高温、高压引发了巨大的能量起伏,在熔体中造成过冷,产生了大量的晶核;同时声流搅拌效应将冲蚀和打断长大的枝晶,促进溶质和碎小晶体的扩散.然而,超声对温度场的改变还没有深入研究,笔者主要研究在纯铝凝固过程中施加超声场,考察超声场下凝固过程温度的变化规律,并具体探讨不同超声振动对不同铸锭位置金属凝固组织细化程度的影响和超声衰减情况.1 试验材料、装置与试验方法1.1 试验材料与装置试验材料为工业纯铝大铸锭,材料的合金成分如表1所示.试验使用的超声设备包括:他激式超声波发生器,具有5个功率档位(105W 、135W 、170W 、200W 、240W );PZT 压电陶瓷换能器、变幅杆、钛合金工具杆、电阻丝加热炉及配套的温度控制记录仪、热电偶、坩埚、位移控制操作台、Leica 台式金相显微镜.整个试验装置如图1和图2所示,通过热电偶测量不同位置的冷却温度,并用温度控制记录仪分析采集数据.表1 试验用工业纯铝的合金成分Tab .1 A lloy co m positi on of indu strial purealu m i num i n exp er i m en t%组分S i M n Cu F e Z n A l质量分数0.0010.0010.0010.0860.01余量郑州大学学报(工学版)2009年1.2 试验方案将铝块置于石墨坩埚并放入电阻加热炉进行熔炼,待其完全熔化后,添加铝打渣剂打渣净化铝熔体.持续加热至850 ,移出石墨坩埚,在炉外自然空冷,待熔体温度降至785 时,对熔体进行超声处理.施振方式为铝熔体中心处顶部持续导入超声波.每次试验工作频率为19 0.5k H z,固定超声波发生器输出功率为:(a)自然冷却,(b)施加105W超声,(c)施加170W超声处理,(d)施加240W超声处理.分别测量不同功率超声振动对凝固温度曲线的变化,然后将不同功率超声下的样品从中间施振处对称切开,研磨、化学抛光后用强酸对观察面进行浸蚀处理,观察铸锭凝固组织.2 结果分析与讨论2.1 功率超声对冷却温度场的变化图2是实验测得的3条冷却曲线图.图中从上到下的冷却曲线依次代表3根不同的热电偶测出的温度变化数据,分别用T1~T3表示,最下方的曲线用T1表示,其最靠近埚壁,最上方的冷却曲线用T3表示,靠近超声波发生器.经过超声波处理的铝熔体比未经超声波处理的各点的时间差有很大的差距,第一拐弯处(液相线)到第二拐弯(固相线),在没有施加超声时凝固时间为572s,总凝固时间为2560s,坩埚壁到中心点最大温度差达到9 ;当施加超声功率105W时,第一拐弯处到第二拐弯凝固时间变化为370s,坩埚壁到中心点最大温度差减少到5 ;随着功率增加液相线到固相线时间变短,当94第4期胡仕成等 功率超声对纯铝凝固过程的影响及衰减特性分析功率增加到240W时,时间变化为260s,总的凝固时间为2020s,坩埚壁到中心点最大温度差减少到3 左右.这说明超声波的声流能有效改善熔体凝固温度场,当超声波导入到金属液中,由于在熔体中形成一定的声压喷流直接离开超声变幅杆的端面并在整个流体中形成环流,对金属液进行搅拌,提高了温度场分布的均匀性,减小了整体熔体的温度梯度. 2.2 功率超声对凝固组织的影响由图3可知,未加超声波形成的铸锭组织多为发达的树枝晶、柱状晶,晶粒尺寸粗大.引入功率超声波后,一次枝晶被打断,晶粒尺寸减小,但由于声功率较小,所形成的晶粒尺寸偏大,同时发现组织中仍存在许多枝晶网胞;当超声功率P= 170W时,二次枝晶也被打断,晶粒进一步细化,超声细化效果达到了最佳状态,若继续增大声功率,强烈的空化与声流效应使得铝熔体瞬时局部温度升高,延长了晶体的长大时间,晶粒尺寸变化不是很明显,超声细化效果没有增强.试验统计了单位面积上所有晶粒的线性尺寸,得到铸锭组织平均晶粒尺寸随超声功率变化的规律,如图4所示. 施加超声时,晶粒十分粗大,且组织分布较不均匀尺寸偏大.经超声波处理后铝凝固组织明显细化,随着超声功率的增加,组织细化程度明显提高,但功率提高到一定程度,超声波的细化作用不再明显增强.当超声波功率在135W时,凝固组织一部分转化为树枝晶,同时还有部分等轴晶,晶粒尺寸明显缩小,但此时组织仍为连成一体的枝晶网胞,同时存有少部分的粗大晶粒;超声波功率为170W时,其凝固组织完全成等轴晶,树枝晶进一步被打碎,晶粒尺寸取于均匀,组织细化非常明显,240W时,凝固组织进一步细化不再明显. 2.3 功率超声对凝固组织有效细晶范围图5是观察区域晶粒尺寸分布示意图.图6是在金属凝固过程中施加功率超声获得细化金属组织,从图6可以看出:B-1~B-6在不同位置凝固组织细化程度存在很大的不同,在靠近超声波施加的地方即B-1至B-4位置,B-1处因为超声波径向作用不是很明显,因此有粗大的树枝晶、柱状晶细化不是很明显,B-2、B-3、B-4组织中粗大的树枝晶、柱状晶已被细小等轴晶取代,在远离振动源处B-5和B-6,晶粒开始变得比较粗大,但它们的显微组织明显不同于B-2和B -4.在改变超声输出功率得到的铸锭组织中,发现当超声输出功率越大时时,B-6处晶粒细化效果越好.2.4 功率超声对熔体凝固有效作用范围分析高能超声在熔体中传播时,由于声波和铝熔体粘滞力的交互作用,有限振幅衰减使液体从声95郑州大学学报(工学版)2009年图7 功率超声细晶有效作用范围F ig .7 T he u ltrason ic fi n e-grai n ed range源处开始在导入杆周围形成一定声压梯度,导致超声波变幅杆前端熔液的流动,熔体在容器中的单项流动的速度为[11]:v x =P l 2yl x(1)声流的最大速度能达到:v max =2 fA (2)式中: P 为声压在X 方向的衰减量; 为熔体黏度;l x ,l y 分别为容器X 和Y 方向上的长度;f 为频率;A 为变幅杆端面最大振幅.超声波产生的声流速度比质点振动速度小的多但亦能达到熔体热对流速度的数10倍.当功率超声的导入,一定能量的超声波在传递过程中,由于散射、折射及分子间振动摩擦吸收声能等原因,必然会产生衰减,反映在声压上,就是从工具杆端面沿声波传播方向形成一定的压力梯度,因此顺着压力梯度方向引发了熔体的环向流动,声流与热对流将发生强烈的交互作用,同时空化泡在崩溃时,泡壁运动速度非常高,能形成速度极大的微射流,加强了声流的搅拌效应.能够显著改变熔体温度梯度,可以明显提高温度场的均匀性.图8 超声声流效应F i g .8 E ffec t of ultras on i c acoustic strea m超声波在介质中传播时,随着传播距离的增加,声束扩散和散射以及介质吸收等会使超声波在传播过程中引起衰减,超声波传播距离的声强能产生空化有效作用距离x 为[12]x =3 c30k T +Q KI 0I b(3)式中:I b 为空化阀声强;I 0为超声波输入强度; 为原子在平衡位置的震动周期;k 为波尔滋曼常数;T 为熔体的绝对温度; 为相邻原子平衡位置间的平均距离;Q 为原子移动的激活能.超声的扩散衰减可以忽略,假设沿超声波的方向上能量是均匀的,在金属熔体中的冲击力与传播的距离之间的关系式为:F r =I m S exp [-2ax ] e 1/c(4)式中:I m 为实际功率强度;e 1为金属熔体吸收的功率超声能量,a 为衰减系数;S 为单位面积,c 为超声波速度.因此一定距离内在超声波作用下空化和声流效应对温度场的均布起到重要的作用,功率超声在金属熔体中的衰减作用力是非常明显的,在靠近工具头端,力很强,可以产生强烈的空化效应,从而可以改善金属的组织、细化晶粒和提高力学性能.然而随着超声在金属熔体中的传播.力的作用产生衰减.当力小到不能使金属熔体产生空化效应时,功率超声就不能对金属的凝固组织产生较大的影响,从而达不到细化金属晶粒.2.5 超声对凝固组织细晶机理分析(1)超声波空化泡崩溃断裂理论.高能超声波形成了大量的空化气泡在一定的声压下崩溃,形成很高的激波和高速的微射流击碎正在长大的晶体或使较远处晶枝产生疲劳断裂,击碎的晶体散布在溶液中,成为新的晶体质点,通过声流和冲击波产生的搅拌力作用下又使其均匀弥散在熔体中,因此超声空化处理能明显细化金属组织晶枝,得到细化均匀的凝固组织.(2)空化泡长大和崩溃过程中形成有效过冷生核理论.超声波在产生空化泡半径在增大以及缩小过程中内部的蒸气由于从外部熔液中吸取热量而降低了空化泡的温度,这将导致空化泡表面的金属熔体温度降低,造成局部过冷,因此在空化泡附近形成晶核,使晶核的形核率增加;在空化气泡崩溃的过程中,会瞬间在极有限的体积内产生很大的温度梯度和压力梯度,空化效应产生瞬时的高温、高压引发了巨大的能量起伏,在这样复杂的条件下会形成局部过冷,生成晶粒.3 结论(1)超声空化和声流效应对凝固热过程的变96第4期胡仕成等 功率超声对纯铝凝固过程的影响及衰减特性分析化对金属形核和长大过程有很大的影响,最终在凝固组织中得到体现.(2)超声波在液体中传播时产生有限振幅衰减使介质从声源处开始形成一定的声压梯度,导致液体的快速流动.流动引起了质点快速传输和液态金属温度场的变化.由于压力梯度的改变,熔体在空间流动过程中形成了复杂的流动场和压力场分布,加强了声流的搅拌效应.能够显著改变熔体温度梯度,可以明显提高温度场的均匀和晶核的扩散性.(3)高能超声能制备出晶粒均匀分布、细化的金属组织是因为空化泡瞬时产生的高压作用下形成的强冲击波微射流使熔体中成团的晶枝被击碎,实现了微观的均匀分散,使金属组织得到细化.参考文献:[1] ESK IN G,G SM.E ffect o f cav itati on m e lt treat m ent onthe struct ure refi ne m ent and property i m prov e m ent incast and defo r med hypereutec ti c A l-Si all oys[J].M a teria l s Sc ience Fo ru m,1997,242:65-70[2] 李军文,桃野正,付莹.超声功率对铸镜内的气孔及组织细化的影响[J].铸造,2007,(2):70-73. [3] 范金辉,翟启杰.物理场对金属凝固组织的影响[J].中国有色金属学报,2002,12(1):11-15.[4] 马立群,舒光冀,陈 锋.金属熔体在超声场中凝固的研究[J].材料科学与工程,1995,13(4):2-7[5] 李英龙,李宝绵,刘永涛,等.功率超声对合金组织的影响[J].中国有色金属学报,1999,9(4):719-722.[6] ES K I N G I.U ltrasonic treat m ent o f li ght a lloy m e lts[M].Am sterda m:Go rdon&Breach,1998:1-5. [7] ESK IN G I.U ltrasonic treat m ent of m o lten a l u m i num[M].M osco w:M eta ll urg i ya,1985:1-10.[8] PAN I,YO S H IDA M,SA S AK I G.U ltrasonic i nsertcasti ng of alu m inu m all oy[J].Sc ri pta M ater i a li a,2000,43(2):155-159.[9] A BRAM OV O V.So li dificati on o f m eta ls in an ultra-son ic fi e l d[M].M oscow:M e tall urg iya,1972:154-168[10]I R SI D.U ltrason ic can replace m ou l d osc ill ation dur i ngb illet Casti ng[J].Stee l T i m es Int,1989,10(5),45.[11]D I NG L,Q I F P,ZHA I Q J,T her m a l ana l y si s on the-soli d ifi cation process of Sn-Sb a ll oy under po w er u-ltrasonic[J].T he Chinese Journal o f N onfe rrous M e-ta ls.2003,27(7):1-2.[12]刘青梅.超声波对金属凝固特性及组织影响的研究[D].长沙:中南大学材料工程学院,2007:101-102Effect of U ltrasonic Treat m ent on Solidification Characteristic andAnalysis the U ltrasonic Attenuation M echanis mHU Sh i-cheng,YANG Yun-m eng,HU Yong-qing,FU M ing-zh i(K ey Laboratory o fM ode rn Co m plex Equ i p m ent D esi gn and Ex tre m e M anufacturi ng,M i n i stry o f Education;Centra l Sout h U n-i versity,Changsha410083,Ch i na)Abst ract:U ltrason ic treat m ent on pure a l u m i n u m so li d ifi c ation process was studied.The coo li n g te m perature curves and cav itati o n and acoustic strea m refi n ed by u ltrason ic w as discussed.Experi m en tal resu lts sho w ed that so li d ification struct u res o f casti n g i n go t treated by u ltrasonic are re fi n ed si g nificantl y.The so li d ifi c ation process ti m e beco m es shorter and te m perature grad ient fi e l d s m aller,Average gra i n size w as90~500 m, W ith the i n creasing of u ltrason ic po w er,m ore refi n ed str ucture can be obtai n ed.H ow ever,w hen the ultrasonic po w er reaches a certain value and different positions o f the the casti n g ingo,t t h e effect o f re fi n i n g gra i n s does not increase sign ifi c antly.Cav itation effect can effecti v e l y functi o n and so li d ification str ucture can be refi n ed better a i d ed by ag itati n g effect of acousti c strea m.K ey w ords:po w er u ltrason ic;te mperature curve;so lidification str ucture;cav itati o n;acoustic strea m97。
超声波探伤标准GB11345-89
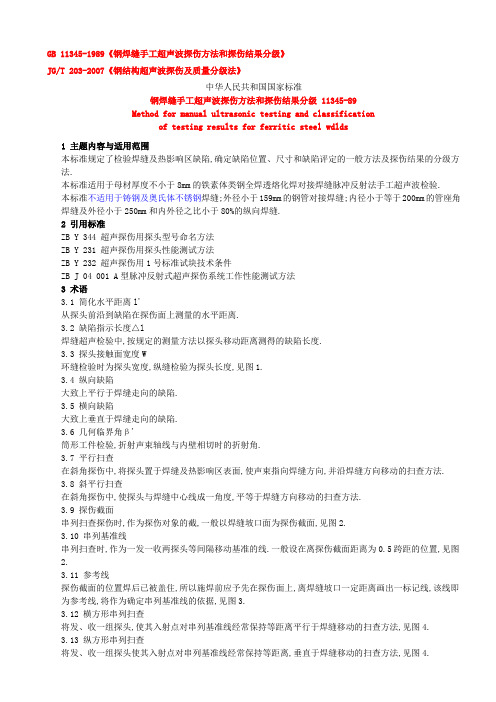
GB 11345-1989《钢焊缝手工超声波探伤方法和探伤结果分级》JG/T 203-2007《钢结构超声波探伤及质量分级法》中华人民共和国国家标准钢焊缝手工超声波探伤方法和探伤结果分级 11345-89Method for manual ultrasonic testing and classificationof testing results for ferritic steel wdlds1 主题内容与适用范围本标准规定了检验焊缝及热影响区缺陷,确定缺陷位置、尺寸和缺陷评定的一般方法及探伤结果的分级方法.本标准适用于母材厚度不小于8mm的铁素体类钢全焊透熔化焊对接焊缝脉冲反射法手工超声波检验.本标准不适用于铸钢及奥氏体不锈钢焊缝;外径小于159mm的钢管对接焊缝;内径小于等于200mm的管座角焊缝及外径小于250mm和内外径之比小于80%的纵向焊缝.2 引用标准ZB Y 344 超声探伤用探头型号命名方法ZB Y 231 超声探伤用探头性能测试方法ZB Y 232 超声探伤用1号标准试块技术条件ZB J 04 001 A型脉冲反射式超声探伤系统工作性能测试方法3 术语3.1 简化水平距离l'从探头前沿到缺陷在探伤面上测量的水平距离.3.2 缺陷指示长度△l焊缝超声检验中,按规定的测量方法以探头移动距离测得的缺陷长度.3.3 探头接触面宽度W环缝检验时为探头宽度,纵缝检验为探头长度,见图1.3.4 纵向缺陷大致上平行于焊缝走向的缺陷.3.5 横向缺陷大致上垂直于焊缝走向的缺陷.3.6 几何临界角β'筒形工件检验,折射声束轴线与内壁相切时的折射角.3.7 平行扫查在斜角探伤中,将探头置于焊缝及热影响区表面,使声束指向焊缝方向,并沿焊缝方向移动的扫查方法.3.8 斜平行扫查在斜角探伤中,使探头与焊缝中心线成一角度,平等于焊缝方向移动的扫查方法.3.9 探伤截面串列扫查探伤时,作为探伤对象的截,一般以焊缝坡口面为探伤截面,见图2.3.10 串列基准线串列扫查时,作为一发一收两探头等间隔移动基准的线.一般设在离探伤截面距离为0.5跨距的位置,见图2.3.11 参考线探伤截面的位置焊后已被盖住,所以施焊前应予先在探伤面上,离焊缝坡口一定距离画出一标记线,该线即为参考线,将作为确定串列基准线的依据,见图3.3.12 横方形串列扫查将发、收一组探头,使其入射点对串列基准线经常保持等距离平行于焊缝移动的扫查方法,见图4.3.13 纵方形串列扫查将发、收一组探头使其入射点对串列基准线经常保持等距离,垂直于焊缝移动的扫查方法,见图4.4 检验人员4.1 从事焊缝探伤的检验人员必须掌握超声波探伤的基础技术,具有足够的焊缝超声波探伤经验,并掌握一定的材料、焊接基础知识.4.2 焊缝超声检验人员应按有关规程或技术条件的规定经严格的培训和考核,并持有相考核组织颁发的等级资格证书,从事相对应考核项目的检验工作.注:一般焊接检验专业考核项目分为板对接焊缝;管件对接焊缝;管座角焊缝;节点焊缝等四种.4.3 超声检验人员的视力应每年检查一次,校正视力不得低于1.0.5 探伤仪、探头及系统性能5.1 探伤仪使用A型显示脉冲反射式探伤仪,其工作频率范围至少为1-5MHz,探伤仪应配备衰减器或增益控制器,其精度为任意相邻12dB误差在±1dB内.步进级每档不大于2dB, 总调节量应大于60dB,水平线性误差不大于1%,垂直线性误差不大于5%.5.2 探头5.2.1 探头应按ZB Y344标准的规定作出标志.5.2.2 晶片的有效面积不应超过500mm2,且任一边长不应大于25mm.5.2.3 声束轴线水平偏离角应不大于2°.5.2.4 探头主声束垂直方向的偏离,不应有明显的双峰,其测试方法见ZB Y231.5.2.5 斜探头的公称折射角β为45°、60°、70°或K值为1.0、1.5、2.0、2.5,折射角的实测值与公称值的偏差应不大于2°(K值偏差不应超过±0.1),前沿距离的偏差应不大于1mm.如受工件几何形状或探伤面曲率等限制也可选用其他小角度的探头.5.2.6 当证明确能提高探测结果的准确性和可靠性,或能够较好地解决一般检验时的困难而又确保结果的正确,推荐采用聚焦等特种探头.5.3 系统性能5.3.1 灵敏度余量系统有效灵敏度必须大于评定灵敏度10dB以上.5.3.2 远场分辨力a.直探头:X≥30dB;b.斜探头:Z≥6dB.5.4 探伤仪、探头及系统性能和周期检查5.4.1 探伤仪、探头及系统性能,除灵敏度余量外,均应按ZB J04 001的规定方法进行测试.5.4.2 探伤仪的水平线性和垂直线性,在设备首次使用及每隔3个月应检查一次.5.4.3 斜探头及系统性能,在表1规定的时间内必须检查一次.6 试块6.1 标准试块的形状和尺寸见附录A,试块制造的技术要求应符合ZB Y232的规定,该试块主要用于测定探伤仪、探头及系统性能.6.2 对比试块的形状和尺寸见附录B.6.2.1 对比试块采用与被检验材料相同或声学性能相近的钢材制成.试块的探测面及侧面,在以2.5MHz以上频率及高灵敏条件下进行检验时,不得出现大于距探测面20mm处的Φ2mm平底孔反射回来的回波幅度1/4的缺陷回波.6.2.2 试块上的标准孔,根据探伤需要,可以采取其他形式布置或添加标准孔,但应注意不应与试块端角和相邻标准孔的反射发生混淆.6.2.3 检验曲面工件时,如探伤面曲率半径R小于等于W2/4时,应采用与探伤面曲率相同的对比试块.反射体的布置可参照对比试块确定,试块宽度应满足式(1):b≥2λ S/De (1)式中 b----试块宽度,mm;λ--波长,mm;S---声程,m;De--声源有效直径,mm6.3 现场检验,为校验灵敏度和时基线,可以采用其他型式的等效试块.7 检验等级7.1 检验等级的分级根据质量要求检验等级分为A、B、C三级,检验的完善程度A级最低,B级一般,C级最高,检验工作的难度系数按A、B、C顺序逐级增高.应按照工件的材质、结构、焊接方法、使用条件及承受载荷的不同,合理的选用检验级别.检验等级应接产品技术条件和有关规定选择或经合同双方协商选定.注:A级难度系数为1;B级为5-6;C级为10-12.本标准给出了三个检验等级的检验条件,为避免焊件的几何形状限制相应等级检验的有效性,设计、工艺人员应考虑超声检验可行性的基础上进行结构设计和工艺安排.7.2 检验等级的检验范围7.2.1 A级检验采用一种角度的探头在焊缝的单面单侧进行检验,只对允许扫查到的焊缝截面进行探测.一般不要求作横向缺陷的检验.母材厚度大于50Mm时,不得采用A级检验.7.2.2 B级检验原则上采用一种角度探头在焊缝的单面双侧进行检验,对整个焊缝截面进行探测.母材厚度大于100mm时,采用双面双侧检验.受几何条件的限制,可在焊缝的双面半日侧采用两种角度探头进行探伤.条件允许时应作横向缺陷的检验.7.2.3 C级检验至少要采用两种角度探头在焊缝的单面双侧进行检验.同时要作两个扫查方向和两种探头角度的横向缺陷检验.母材厚度大于100mm时,采用双面侧检验.其他附加要求是:a.对接焊缝余高要磨平,以便探头在焊缝上作平行扫查;b.焊缝两侧斜探头扫查经过的母材部分要用直探头作检查;c.焊缝母材厚度大于等于100mm,窄间隙焊缝母材厚度大于等于40mm时,一般要增加串列式扫查,扫查方法见附录C.8 检验准备8.1 探伤面8.1.1 按不同检验等级要求选择探伤面.推荐的探伤面如图5和表2所示.8.1.2 检验区域的宽度应是焊缝本身再加上焊缝两侧各相当于母材厚度30%的一段区域,这个区域最小10mm,最大20mm,见图6.8.1.3 探头移动区应清除焊接飞溅、铁屑、油垢及其他外部杂技.探伤表面应平整光滑,便于探头的自由扫查,其表面粗糙度不应超过6.3μm,必要时应进行打磨:a.采用一次反射法或串列式扫查探伤时,探头移动区应大于1.25P:P=2δtgβ (2)或P=2δK (3)式中 P----跨距,mm;δ--母材厚度,mmb.采用直射法探伤时,探头移动区应大于0.75P.8.1.4 去除余高的焊缝,应将余高打磨到与邻近母材平齐.保留余高的焊缝,如焊缝表面有咬边,较大的隆起凹陷等也应进行适当的修磨,并作圆滑过渡以影响检验结果的评定.8.1.5 焊缝检验前,应划好检验区段,标记出检验区段编号.8.2 检验频率检验频率f一般在2-5MHz范围内选择,推荐选用2-2.5MHz公称频率检验.特殊情况下,可选用低于2MHz或高于2.5MHz的检验频率,但必须保证系统灵敏度的要求.8.3 探头角度8.3.1 斜探头的折射角β或K值应依据材料厚度,焊缝坡口型式及预期探测的主要缺陷来选择.对不同板厚推荐的探头角度和探头数量见表2.8.3.2 串列式扫查,推荐选用公称折射角为45°的两个探头,两个探头实际折射角相差不应超过2°,探头前洞长度相差应小于2mm.为便于探测厚焊缝坡口边缘未熔合缺陷,亦可选用两个不同角度的探头,但两个探头角度均应在35°-55°范围内.8.4 耦合剂8.4.1 应选用适当的液体或糊状物作为耦合剂,耦合剂应具有良好透声性和适宜流动性,不应对材料和人体有作用,同时应便于检验后清理.8.4.2 典型的耦合剂为水、机油、甘油和浆糊,耦合剂中可加入适量的"润湿剂"或活性剂以便改善耦合性能.8.4.3 在试块上调节仪器和产品检验应采用相同的耦合剂.8.5 母材的检查采用C级检验时,斜探头扫查声束通过的母材区域应用直探头作检查,以便探测是否有有探伤结果解释的分层性或其他缺陷存在.该项检查仅作记录,不属于对母材的验收检验.母材检查的规程要点如下:a.方法:接触式脉冲反射法,采用频率2-5MHz的直探头,晶片直径10-25mm;b.灵敏度:将无缺陷处二次底波调节为荧光屏满幅的100%;c.记录:凡缺陷信号幅度超过荧光屏满幅20%的部位,应在工件表面作出标记,并予以记录.9 仪器调整和校验9.1 时基线扫描的调节荧光屏时基线刻度可按比例调节为代表缺陷的水平距离l(简化水平距离l');深度h;或声程S,见图7. 9.1.1 探伤面为平面时,可在对比试块上进行时基线扫描调节,扫描比例依据工件工和选用的探头角度来确定,最大检验范围应调至荧光屏时基线满刻度的2/3以上.9.1.2 探伤面曲率半径R大于W2/4时,可在平面对比试块上或与探伤面曲率相近的曲面对比试块上,进行时基线扫描调节.9.1.3 探伤面曲率半径R小于等于W2/4时,探头楔块应磨成与工件曲面相吻合,在6.2.3条规定的对比试块上作时基线扫描调节.9.2 距离----波幅(DAC)曲线的绘制9.2.1 距离----波幅曲线由选用的仪器、探头系统在对比试块上的实测数据绘制见图8,其绘制方法见附录D,曲线由判废线RL,定量线SL和评定线EL组成,不同验收级别的各线灵敏度见表3.表中的DAC是以Φ3mm标准反射体绘制的距离--波幅曲线--即DAC基准线.评定线以上至定量线以下为1区(弱信号评定区);定量线至判废线以下为Ⅱ区(长度评定区);判废线及以上区域为Ⅲ区(判废区).9.2.2 探测横向缺陷时,应将各线灵敏度均提高6dB.9.2.3 探伤面曲率半径R小于等于W2/4时,距离--波幅曲线的绘制应在曲面对比试块上进行.9.2.4 受检工件的表面耦合损失及材质衰减应与试块相同,否则应进行传输损失修整见附录E,在1跨距声程内最大传输损失差在2dB以内可不进行修整.9.2.5 距离--波幅曲线可绘制在坐标纸上也可直接绘制在荧光屏刻度板上,但在整个检验范围内,曲线应处于荧光屏满幅度的20%以上,见图9,如果作不到,可采用分段绘制的方法见图10.9.3 仪器调整的校验9.3.1 每次检验前应在对比试块上,对时基线扫描比例和距离--波幅曲线(灵敏度)进行调节或校验.校验点沙于两点.9.3.2 检验过程中每4h之内或检验工作结束后应对时基线扫描和灵敏度进行校验,校验可在对比试块或其他儿试块上进行.9.3.3 扫描调节校验时,如发现校验点反射波在扫描线上偏移超过原校验点刻度读数的10%或满刻度的5%(两者取较小值),则扫描比例应重新调整,前次校验后已经记录的缺陷,位置参数应重新测定,并予以更正.9.3.4 灵敏度校验时,如校验点的反射波幅比距离--波幅曲线降低20%或2dB以上,则仪灵敏度应重新调整,并对前次校验后检查的全部焊缝应重新检验.如校验点的反射波幅比距离--波幅曲线增加20%或2dB以上,仪器灵敏度应重新调整,而前次校验后,已经记录的缺陷,应对缺陷尺寸参数重新测定并予以评定.10 初始检验10.1 一般要求10.1.1 超声检验应在焊缝及探伤表面经外观检查合格并满足8.1.3条的要求后进行.10.1.2 检验前,探伤人员应了解受验工件的材质、结构、曲率、厚度、焊接方法、焊缝种类、坡口形式、焊缝余高及背面衬垫、沟槽等情况.10.1.3 探伤灵敏度应不低于评定线灵敏度.10.1.4 扫查速度不应大于150mm/s, 相邻两次探头移动间隔保证至少有探头宽度10%的重叠.10.1.5 对波幅超过评定线的反射波,应根据探头位置、方向、反射波的位置及10.1.2条了解的焊缝情况,判断其是否为缺陷.判断为缺陷的部位应在焊缝表面作出标记.10.2 平板对接焊缝的检验10.2.1 为探测纵向缺陷,斜探头垂直于焊缝中心线在探伤面上,作锯齿型扫查见图11.探头前后移动的范围应保证扫查到全部焊缝截面及热影响区.在保持探头垂直焊缝作前后移动的同时,还应作10°-15°的左右转动.10.2.2 为探测焊缝及热影响区的横向缺陷应进行平行和斜平行扫查.a. B级检验时,可寅边缘使探头与焊缝中心线成10°-20°作斜平行的扫查(图12);b. C级检验时,可将探头放在焊缝及热影响区上作两个方向的平行扫查(图13),焊缝母材厚度超过100mm 时,应在焊缝的两面作平行扫查或者采用两种角度探头(45°和60°或45°和70°并用)作单面两个方向的平行扫查;亦可用两个45°探头作串列式平行扫查;c. 对电渣焊缝还应增加与焊缝中心线成45°的斜向扫查.10.2.3 为确定缺陷的位置、方向、形状、观察缺陷动态波形或区分缺陷讯号与伪讯号,可采用前后、左右、转角、环绕等四种探头基本扫查方式(图14).10.3 曲面工件对接焊缝的检验10.3.1 探伤面为曲面时,应按6.2.3和9.1.3条的规定选用对比试块,并采用10.2条的方法进行检验,C 级检验时,受工件几何形状限制,横向缺陷探测无法实施时,应在检验记录中予以注明.10.3.2 环缝检验时,对比试块的曲率半径为探伤面曲率半径0.9-1.5倍的对比试块均可采用.探测横向缺陷时按10.3.3条的方法进行.10.3.3 纵缝检验时,对比试块的曲率半径与探伤面曲率半径之差应小于10%.10.3.3.1 根据工件的曲率和材料厚度选择探头角度,并考虑几何临界角的限制,确保声束能扫查到整个焊缝厚度.条件允许时,声束在曲底面的入射角度不应超过70°.10.3.3.2 探头接触面修磨后,应注意探头入射点和折射角或K值的变化,并用曲面试块作实际测定. 10.3.3.3 当R大于W2/4采用平面对比试块调节仪器时,检验中应注意到荧光屏指示的缺陷深度或水平距离与缺陷实际的径向埋藏深度或水平距离孤长的差异,必要时应进行修正.10.4 其他结构焊缝的检验10.4.1 一般原则a.尽可能采用平板焊缝检验中已经行之有效的各种方法;b.在选择探伤面和探头时应考虑到检测各种类型缺陷的可能性,并使声束尽可能垂直于该结构焊缝中的主要缺陷.10.4.2 T型接头10.4.2.1 腹板厚度不同时,选用的折射角见表4,斜探头在腹板一侧作直射法和一次反射法探伤见图15位置2.10.4.2.2 采用折射角45°(K1)探头在腹板一侧作直射法和一次反射法探测焊缝及腹板侧热影响区的裂纹(图16).10.4.2.3 为探侧腹板和翼板间未焊透或翼板侧焊缝下层状撕裂等缺陷,可采用直探头(图15位置1)或斜探头(图16位置3)在翼板外侧探伤或采用折射角45°(K1)探头在翼板内侧作一次反射法探伤(图15位置3).10.4.3 角接接头角接接头探伤面及折射角一般按图17和表4选择.10.4.4 管座角焊缝10.4.4.1 根据焊缝结构形式,管座角焊缝的检验有如下五种探侧方法,可选择其中一种或几种方式组合实施检验.探测方式的选择应由合同双方商定,并重点考虑主要探测对象和几何条件的限制(图18、19). a.在接管内壁表面采用直探头探伤(图18位置1);b.在容器内表面用直探头探伤(图19位置1);c.在接管外表面采用斜探头探伤(图19位置2);d.在接管内表面采用斜探头探伤(图18位置3,图19位置3);e.在容器外表面采用斜探头探伤(图18位置2).10.4.4.2 管座角焊缝以直探头检验为主,对直探头扫查不到的区域或结构,缺陷向性不适于采用直探头检验时,可采用斜探头检验,斜探头检验应符合10.4.1条的规定.10.4.5 直探头检验的规程a.推荐采用频率2.5Mhz直探头或双晶直探头,探头与工件接触面的尺寸W应小于2√R;b.灵敏度可在与工件同曲率的试块上调节,也可采用计算法或DGS曲线法,以工件底面回波调节.其检验等级评定见表5.11 规定检验11.1 一般要求11.1.1 规定检验只对初始检验中被标记的部位进行检验.11.1.2 探伤灵敏度应调节到评定灵敏度.11.1.3 对所有反射波幅超过定量线的缺陷,均应确定其位置,最大反射波幅所在区域和缺陷指示长度. 11.2 最大反射波幅的测定11.2.1 对判定为缺陷的部位,采取10.2.3条的探头扫查方式、增加探伤面、改变探头折射角度进行探测,测出最大反射波幅并与距离--波幅曲线作比较,确定波幅所在区域.波幅测定的允许误差为2DB.11.3 位置参数的测定11.3.1 缺陷位置以获得缺陷最大反射波的位置来表示,根据相应的探头位置和反射波在荧光屏上的位置来确定如下全部或部分参数.a.纵坐标L代表缺陷沿焊缝方向的位置.以检验区段编号为标记基准点(即原点)建立坐标.坐标正方向距离L表示缺陷到原点之间的距离见图20;b.深度坐标h代表缺陷位置到探伤面的垂直距离(mm).以缺陷最大反射波位置的深度值表示;c.横坐标q代表缺陷位置离开焊缝中心线的垂直距离,可由缺陷最大反射波位置的水平距离或简化水平距离求得.11.3.2 缺陷的深度和水平距离(或简化水平距离)两数值中的一个可由缺陷最大反射波在荧光屏上的位置直接读出,另一数值可采用计算法、曲线法、作图法或缺陷定位尺求出.11.4 尺寸参数的测定应根据缺陷最大反射波幅确定缺陷当量值Φ或测定缺陷指示长度△l.11.4.1 缺陷当量Φ,用当量平底孔直径表示,主要用于直探头检验,可采用公式计算,DGS曲线,试块对比或当量计算尺确定缺陷当量尺寸.11.4.2 缺陷指示长度△l的测定推荐采用如下二种方法.a.当缺陷反射波只有一个高点时,用降低6dB相对灵敏度法测长见图21;b.在测长扫查过程中,如发现缺陷反射波峰值起伏变化,有多个高点,则以缺陷两端反射波极大值之间探头的移动长度确定为缺陷指示长度,即端点峰值法见图22.12 缺陷评定12.1 超过评定线的信号应注意其是否具有裂纹等危害性缺陷特征,如有怀疑时采取改变探头角度,增加探伤面、观察动态波型、结合结构工艺特征作判定,如对波型不能准确判断时,应辅以其他检验作综合判定.12.2 最大反射波幅位于Ⅱ区的缺陷,其指示长度小于10mm时按5mm计.12.3 相邻两缺陷各向间距小于8mm时,两缺陷指示长度之和作为单个缺陷的指示长度.13 检验结果的等级分类13.1 最大反射波幅位于Ⅱ区的缺陷,根据缺陷指示长度按表6的规定予以评级.13.2 最大反射波幅不超过评定线的缺陷,均应为Ⅰ级.13.3 最大反射波幅超过评定线的缺陷,检验者判定为裂纹等危害性缺陷时,无论其波幅和尺寸如何,均评定为Ⅳ级.13.4 反射波幅位于Ⅰ区的非裂纹性缺陷,均评为Ⅰ级.13.5 反射波幅位于Ⅲ区的缺陷,无论其指示长度如何,均评定为Ⅳ级.13.6 不合格的缺陷,应予返修,返修区域修后,返修部位及补焊受影响的区域,应按原探伤条件进行复验,复探部位的缺陷亦应按12章评定.14 记录与报告14.1 检验记录主要内容:工件名称、编号、焊缝编号、坡口形式、焊缝种类、母材材质、规格、表面情况、探伤方法、检验规程、验收标准、所使用的仪器、探头、耦合剂、试块、扫描比例、探伤灵敏度.所发现的超标缺陷及评定记录,检验人员及检验日期等.反射波幅位于Ⅱ区,其指示长度小于表6的缺陷也应予记录.14.2 检验报告主要内容:工件名称、合同号、编号、探伤方法、探伤部位示意图、检验范围、探伤比例收标准、缺陷情况、返修情况、探伤结论、检验人员及审核人员签字等.14.3 检验记录和报告应至少保存7年.14.4 检验记录和报告的推荐格式见附录F.附录A标准试块的形状和尺寸(补充件)注:尺寸公差±0.1;各边垂直度不大于0.05;C面尺寸基准面,上部各折射角刻度尺寸值见表A1,下部见表A2.附录B对比试块的形状和尺寸(补充件)B1 对比试块的形状和尺寸见表B1.注:①尺寸公差±0.1mm; ②各边垂直度不大于0.1; ③表面粗糙度不大于6.3μm; ④标准孔与加工面的平行度不大于0.05.附录C串列扫查探伤方法(补充件)C1 探伤设备C1.1 超声波探伤仪的工作方式必须具备一发一收工作状态.C1.2 为保证一发一收探头相对于串列基准线经常保持等距离移动,应配备适宜的探头夹具,并适用于横方型及纵方型两种扫查方式.C1.3 推荐采用,频率2-2.5Mhz,公称折射角45°探头,两探头入射点间最短间距应小于20mm.C2 仪器调整C2.1 时基线扫描的调节采用单探头按标准正文9.1 的方法调节,最大探测范围应大于1跨距声程.C2.2 灵敏度调整在工件无缺陷部位,将发、收两探头对向放置,间距为1跨距,找到底面最大反射波见图C1及式C1,调节增益使反射波幅为荧光屏满幅高度的40%,并以此为基准波高.灵敏度分别提高8dB、14dB和20dB代表判废灵敏度、定量灵敏度和评定灵敏度.C3 检验程序C3.1 检验准备a.探伤面对接焊缝的单面双侧;b.串列基准线如发、收两探头实测折射角的平均值为β或K值平均为K.在离参考线(参考线至探伤截面的距离L'-0.5P)的位置标记串列基准线,见图C2及式C2.0.5P=δtgβ (C1)或0.5P=δK (C2)C3.2 初始探伤C3.2.1 探伤灵敏度不低于评定灵敏度.C3.2.2 扫查方式采用横方形或纵方形串列扫查,扫查范围以串列基准线为中心尽可能扫查到整个探伤截面,每个探伤截面应扫查一遍.C3.2.3 标记超过评定线的反射波,被判定为缺陷时,应在焊缝的相应位置作出标记.C3.3 规定探伤C3.3.1 对象只对初始检验标记部位进行探伤.C3.3.2 探伤灵敏度为评定灵敏度.C3.3.3 缺陷位置不同深度的缺陷,其反射波均出现在相当于半跨距声程位置见图C3.缺陷的水平距离和深度分别为:(C3)(C4)C3.3.4 缺陷以射波幅在最大反射波探头位置,以40%线为基准波高测出缺陷反射波的dB数作为缺陷的相对波幅,记为SL±----dB.C3.3.5 缺陷指示长度的测定采用以评定灵敏度为测长灵敏度的绝对灵敏度法测量缺陷指示长度.即进行左右扫查(横方形串列扫查),以波幅超过评定线的探头移动范围作为缺陷指示长度.C4 缺陷评定所有反射波幅度超过评定线的缺陷均应按标准正文第12章的规定予以评定,并按第13章的规定对探伤结果作等级分类.附录D距离----波幅(DAC)曲线的制作(补充件)D1 试件D1.1 采用标准附录B对比试块或其他等效形式试块绘制DAC曲线.D1.2 R小于等于W2/4时,应采用探伤面曲率与工件探伤面曲率相同或相近的对比试块.D2 绘制步骤DAC曲线可绘制在坐标纸上(称DAC曲线),亦可直接绘制在荧光屏前透明的刻度板上(称DAC曲线板).D2.1 DAC曲线的绘制步骤如下:a.将测试范围调整到探伤使用的最大探测范围,并按深度、水平或声程法调整时基线扫描比例;b.根据工件厚度和曲率选择合适的对比试块,选取试块上民探伤深度相同或接近的横孔为第一基准孔,将探头置于试块探伤面声束指向该孔,调节探头位置找到横孔的最高反射波;c.调节"增益"或"衰减器"使该反射幅为荧光屏上某一高度(例如满幅的40%)该波高即为"基准波高",此时,探伤系统的有效灵敏度应比评定灵敏度高10dB;d.调节衰减器,依次探测其他横孔,并找到最大反射波高,分别记录各反射波的相对波幅值(dB);e.以波幅(dB)为纵坐标,以探沿距离(声程、深度或水平距离)为横坐标,将c、d记录数值描绘在坐标纸上;f.将标记各点连成圆滑曲线,并延长到整个探测范围,最近探测点到探距离O点间画水平线,该曲线即为Φ3mm横孔DAC曲线的基准线;g.依据标准正文表3规定的各线灵敏度,在基准线下分别绘出判废线、定量线、评定线,并标记波幅的分区;h.为便于现场探伤校验灵敏度,在测试上述数据的同时,可对现场使用的便携试块上的某一参考反射体进行同样测量,记录其反射波位置和反射波幅(dB)并标记在DAC曲线图上.D2.2 DAC曲线的绘制步骤如下:a.同D2.1a;b.依据工件厚度和曲率选择合适的对比试块,在试块上所有孔深小于等于探测深度的孔中,选取能产生最大反射波幅的横孔为第一基准孔;c.调节"增益"使该孔的反射波为荧光屏满幅高度的80%,将其峰值标记在荧光屏前辅助面板上.依次探测其它横孔,并找到最大反射波 ,地峰值点标记在辅助面板上,如果做分段绘制,可调节衰减器分段绘制曲线;d.将各标记点连成圆滑曲线,并延伸到整个探测范围,该曲线即为Φ3mm横孔DAC曲线基准线;定量灵敏度下,如分别将灵敏度提高或降低6dB,该线将分别代表评定或判废线.(A级检验DAC基准线即为判废线);。
超声波在铸造的应用
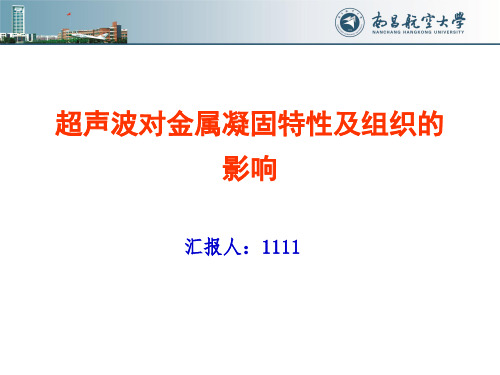
(3)超声波的吸收衰减:超声波的吸收是由介质的导热性、 粘滞性及弹性滞后造成的。声波的吸收将声能直接转换为 热能。这是超声波衰减的重要原因。
G.N.Kozhemyakin研究了功率超声波振动对Sn-Sb晶体 凝固过程生长的影响。结果表明,超声波振动能影响Sn-Sb晶 体的生长方向,择优的晶粒取向有利于提高晶体的性能。
下图为超声波处理对锡锑合金微观组织的影响。对此种合 金的研究结果表明,超声波处理能显著细化合金的微观组织, 改变β相形貌,使尖锐棱角的立方体刀相破碎为均匀细小的粒 状,棱角有钝化趋势,并可消除比重偏析。
C.K.Jen和H.Soda研究了超声振动对具有不同微观组织(胞 状、树枝状和多面体)的二元Al一Cu、Bi一Cd合金凝固过程 的作用。以前在这一领域内的研究仅限定在具有树枝状结构 的低熔点合金,此实验中选用具有不同成分、不同微观组织的 材料进行研究,深化了以前在这领域的研究。实验采用顶端导 入,在温度高于液相线10℃以上时,导入2OkHZ的超声振动,在 温度低于固相线10℃时停止导入。实验结果表明,这些合金重 熔凝固后,组织明显细化。然而对于合金重熔后是否还具有超 声波的影响,这个问题尚存在争议。
李军文等人研究了超声波处理时间对铝合金铸锭内气 孔的影响,结果表明,当以适当的超声波处理时间施加时 ,可以得到良好的除气效果;处理时间过长,会导致气孔 增加。随着超声波处理时间的增加,铸锭细化率呈急剧增 加的趋势,当增加到一定值后,细化率变化幅度变小。
罗执等人对Al-5.0Cu-1.0Fe合金进行超声处理,对比无超 声处理的Al-5.0Cu-1.0Fe合金,结果表明,超声波对合金微观 组织有显著影响。当施加超声波后,缩孔、缩松等缺陷减少
获得等轴晶的方法

获得等轴晶的方法
通过强化非均匀形核和促进晶粒游离以抑制凝固过程中柱状晶区的形成和发展,就能获得等轴晶。
等轴晶,通过改变熔体流动状态,在结晶开始时为固液两相同时,在液相中断电和机械搅拌等手段下,使晶核形成于流动状态下的熔体液相,随后晶粒在液相中等轴地长大,这样便可以得到等轴组织。
柱状晶,对于某些合金,只要在有晶核存在时恒定的方向上进行拉伸或挤压,就可以获得沿着拉伸或挤压方向生长的晶粒,形成柱状晶,在挤压中,柱状晶的生长仅限于应力方向,在单向拉伸中,柱状晶的主轴沿延伸方向。
等轴晶和柱状晶的应用。
等轴晶在高温合金的锻造、冶金、航空航天等领域得到了广泛应用,一些变形难度大的铸造件也可以采用等轴晶方法进行制造,柱状晶铸造可用于研究材料的组织与力学性能关系或制备高性能复合材料、热电材料等。
细化等轴晶的常用方法:
(1)合理的浇注工艺:合理降低浇注温度是减少柱状晶、获得及细化等轴晶的有效措施;通过改变浇注方式强化对流对型壁激冷晶的冲刷作用,能有效地促进细等轴晶的形成;
(2)冷却条件的控制:对薄壁铸件,可采用高蓄热、快热传导能力的铸型;对厚壁铸件,一般采用冷却能力小的铸型以确保等轴晶的形成,再辅以其它晶粒细化措施以得到满意的效果;
(3)孕育处理:影响生核过程和促进晶粒游离以细化晶粒。
(4)动力学细化:铸型振动;超声波振动;液相搅拌;流变铸造,导致枝晶的破碎或与铸型分离,在液相中形成大量结晶核心,达到细化晶粒的目的。
超声波振幅对铝合金微观组织的影响浅析
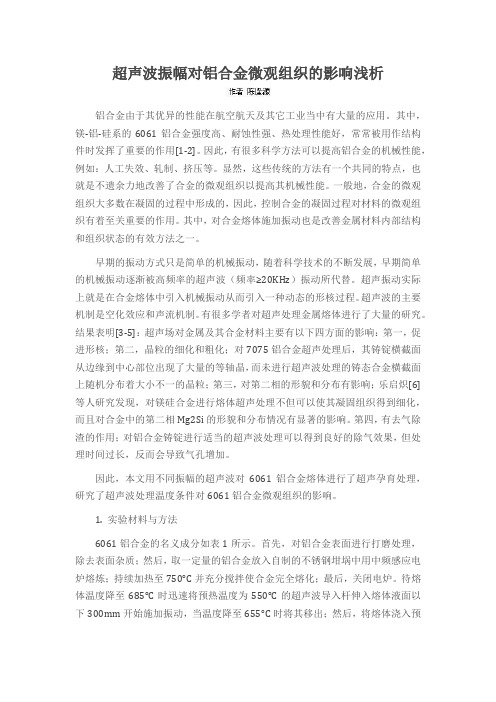
超声波振幅对铝合金微观组织的影响浅析铝合金由于其优异的性能在航空航天及其它工业当中有大量的应用。
其中,镁-铝-硅系的6061铝合金强度高、耐蚀性强、热处理性能好,常常被用作结构件时发挥了重要的作用[1-2]。
因此,有很多科学方法可以提高铝合金的机械性能,例如:人工失效、轧制、挤压等。
显然,这些传统的方法有一个共同的特点,也就是不遗余力地改善了合金的微观组织以提高其机械性能。
一般地,合金的微观组织大多数在凝固的过程中形成的,因此,控制合金的凝固过程对材料的微观组织有着至关重要的作用。
其中,对合金熔体施加振动也是改善金属材料内部结构和组织状态的有效方法之一。
早期的振动方式只是简单的机械振动,随着科学技术的不断发展,早期简单的机械振动逐渐被高频率的超声波(频率≥20KHz)振动所代替。
超声振动实际上就是在合金熔体中引入机械振动从而引入一种动态的形核过程。
超声波的主要机制是空化效应和声流机制。
有很多学者对超声处理金属熔体进行了大量的研究。
结果表明[3-5]:超声场对金属及其合金材料主要有以下四方面的影响:第一,促进形核;第二,晶粒的细化和粗化;对7075铝合金超声处理后,其铸锭横截面从边缘到中心部位出现了大量的等轴晶,而未进行超声波处理的铸态合金横截面上随机分布着大小不一的晶粒;第三,对第二相的形貌和分布有影响;乐启炽[6]等人研究发现,对镁硅合金进行熔体超声处理不但可以使其凝固组织得到细化,而且对合金中的第二相Mg2Si的形貌和分布情况有显著的影响。
第四,有去气除渣的作用;对铝合金铸锭进行适当的超声波处理可以得到良好的除气效果,但处理时间过长,反而会导致气孔增加。
因此,本文用不同振幅的超声波对6061铝合金熔体进行了超声孕育处理,研究了超声波处理温度条件对6061铝合金微观组织的影响。
1. 实验材料与方法6061铝合金的名义成分如表1所示。
首先,对铝合金表面进行打磨处理,除去表面杂质;然后,取一定量的铝合金放入自制的不锈钢坩埚中用中频感应电炉熔炼;持续加热至750°C并充分搅拌使合金完全熔化;最后,关闭电炉。
超声波物理

平方米 ) ,或Pa(帕斯卡)。超声在介质中传播,介质的密度随之做周期性变化,介质中的压强也就
随之变化。由声波的动力学方程可知,声压的表达式是:
p
Ac
c os t
x c
2
即p
pm
c os t
x c
2
其中pm Ac称为声压幅值。A是振幅,是密度,
B型:用平面图形的形式来显示被探查组织的具体情况。检查时,首先将人体界面的反射信号转变为强弱不同的光点,这些光点可通 过荧光屏显现出来,这种方法直观性好,重复性强,可供前后对比,所以广泛用于妇产科、泌尿、消化及心血管等系统疾病的诊断。
M型:是用于观察活动界面时间变化的一种方法。最适用于检查心脏的活动情况,其曲线的动态改变称为超声心动图,可以用来观察 心脏各层结构的位置、活动状态、结构的状况等,多用于辅助心脏及大血管疫病的诊断。
第一节 超声波的基本性质
一、超声波的分类
超声波按振动方式分类:纵波和横波。在固体中声振动可以传播纵波和横波,但一般在液体和气体中,由于介质没有切变弹性,只能
传播纵波。人耳只能感受纵波。
超声波在临床按频率分类:1、低频超声 1~2.75MHz频段;2、中频超声3~10MHz;
3、高频超声12~20MHz;
D型:是专门用来检测血液流动和器官活动的一种超声诊断方法,又称为多普勒超声诊断法。可确定血管是否通畅、管腔是否狭窄、 闭塞以及病变部位。新一代的D型超声波还能定量地测定管腔内血液的流量。近几年来科学家又发展了彩色编码多普勒系统,可在超 声心动图解剖标志的指示下,以不同颜色显示血流的方向,色泽的深浅代表血流的流速。现在还有立体超声显象、超声CT、超声内窥 镜等超声技术,并且还可以与其他检查仪器结合使用,使疾病的诊断准确率大大提高。
超声熔体处理技术对7075铝合金铸态组织及性能的影响

1C over Report封面报道超声熔体处理技术对7075铝合金铸态组织及性能的影响孟宪林(沈阳远大装备科技有限公司,辽宁 沈阳 110027)摘 要:通过对铝合金6063进行熔体处理后发现,处理后的铸件试样较未进行处理的试样有明显的晶粒细化,分布均匀程度提高,合金元素Mg、Zn、Cu 在合金晶粒内的析出被抑制,Mg-Zn-Cu 第二相的析出主要集中在晶界位置,力学性能及硬度均匀不同程度的提高,并且通过试验确定了优选的超声处理介入熔体内温度,为超声波在铸造生产中的应用提供了依据。
关键词:铝合金;熔体;超声处理;晶粒细化中图分类号:TG663 文献标识码:A 文章编号:11-5004(2020)22-0001-2 收稿日期:2020-11作者简介:孟宪林,男,生于1987年,汉族,辽宁辽阳人,硕士研究生,研究方向:超声辅助加工及金属材料生产研究。
铝合金晶粒的大小直接影响其力学性能,细晶强化可以提高铝合金的力学性能和改善铝合金变形的均匀性[1]。
铝合金细晶强化的方法有技术主要有熔体过热法、变质处理法、合金元素添加法和熔体搅拌法等。
超声(Ultrasonic)细化属于合金熔体搅拌法的一种方式,其原理是利用超声场在熔体中产生的声空化和声流效应达到除气和细化组织的目的[2,3]。
合金熔体在凝固过程中进行超声处理会使晶粒变细,改变其中一些物理机械性质,如延伸率,强度和变形特性等等。
1 实验设备及方法1.1 试验合金以航空航天领域常用的7075铝合金为研究对象,分别研究了单纯的重力铸造(无超声)和超声铸造的铸棒,通过对金相和力学性能的检测,定性研究超声对7075铝合金铸棒的影响,具体试验条件如表1所示。
表1 试验条件合金试验分组除气超声细化处理浇铸温度Al7075Test 1No No700ºC Test 2Yes/US Yes by US at 700ºC 700ºC Test 3Yes/USYes by US at 680ºC680ºC1.2 试验设备试验设备如下图1所示,采用井式坩埚炉将铝合金原料加热至熔融状态,采用沈阳远大装备科技有限公司自主研发的超声辅助铸造设备,将超声振动引入到熔融铝合金熔体当中。
超声波特性
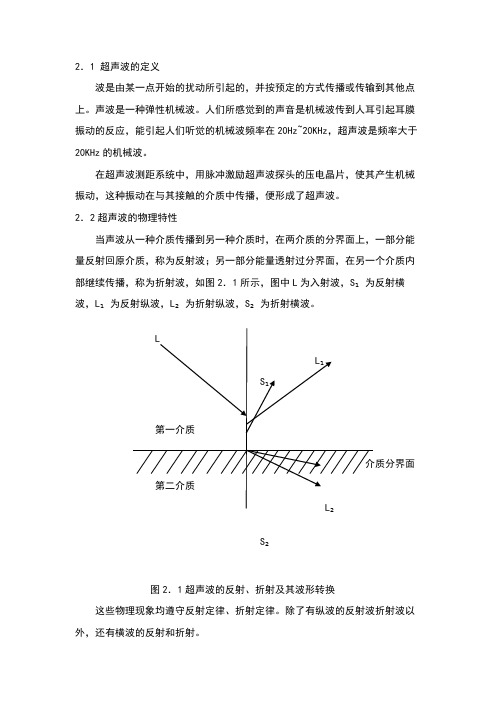
2.1 超声波的定义波是由某一点开始的扰动所引起的,并按预定的方式传播或传输到其他点上。
声波是一种弹性机械波。
人们所感觉到的声音是机械波传到人耳引起耳膜振动的反应,能引起人们听觉的机械波频率在20Hz~20KHz,超声波是频率大于20KHz的机械波。
在超声波测距系统中,用脉冲激励超声波探头的压电晶片,使其产生机械振动,这种振动在与其接触的介质中传播,便形成了超声波。
2.2超声波的物理特性当声波从一种介质传播到另一种介质时,在两介质的分界面上,一部分能量反射回原介质,称为反射波;另一部分能量透射过分界面,在另一个介质内部继续传播,称为折射波,如图2.1所示,图中L为入射波,S₁为反射横波,L₁为反射纵波,L₂为折射纵波,S₂为折射横波。
S₂图2.1超声波的反射、折射及其波形转换这些物理现象均遵守反射定律、折射定律。
除了有纵波的反射波折射波以外,还有横波的反射和折射。
因为声波是借助于传播介质中的质点运动而传播的,其传播方向与其振动方向一致,所以空气中的声波属于纵向振动的弹性机械波。
在理想介质中,超声波的波动方程描述方法与电磁波是类似的。
描述简谐声波向X 正方向传播的质点位移运动可表示为:()cos()A A x t kx ω=+ ()0()ax A x A e -= ()式中,()A x 为振幅即质点的位移,0A 为常数,ω为角频率,t 为时间,x 为传播距离,2/k πλ=为波数,λ为波长,α为衰减系数。
衰减系数与声波所在介质和频率关系:2af α= ()式(2.3)中,a 为介质常数,f 为振动频率。
2.2.1超声波的衰减从理论上讲,超声波衰减主要有三个方面:(1) 由声速扩展引起的衰减在声波的传播过程中,随着传播距离的增大,非平面声波的声速不断扩展增大,因此单位面积上的声压随距离的增大而减弱,这种衰减称为扩散衰减。
(2) 由散射引起的衰减由于实际材料不可能是绝对均匀的,例如材料中外来杂质金属中的第二相析出、晶粒的任意取向等均会导致整个材料声特性阻抗不均,从而引起声的散射。
等轴晶和纳米晶
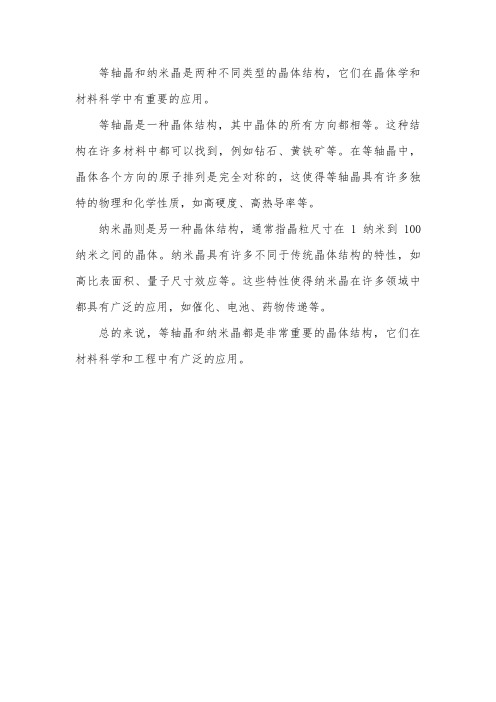
等轴晶和纳米晶是两种不同类型的晶体结构,它们在晶体学和材料科学中有重要的应用。
等轴晶是一种晶体结构,其中晶体的所有方向都相等。
这种结构在许多材料中都可以找到,例如钻石、黄铁矿等。
在等轴晶中,晶体各个方向的原子排列是完全对称的,这使得等轴晶具有许多独特的物理和化学性质,如高硬度、高热导率等。
纳米晶则是另一种晶体结构,通常指晶粒尺寸在1纳米到100纳米之间的晶体。
纳米晶具有许多不同于传统晶体结构的特性,如高比表面积、量子尺寸效应等。
这些特性使得纳米晶在许多领域中都具有广泛的应用,如催化、电池、药物传递等。
总的来说,等轴晶和纳米晶都是非常重要的晶体结构,它们在材料科学和工程中有广泛的应用。
减小晶粒尺寸的方法
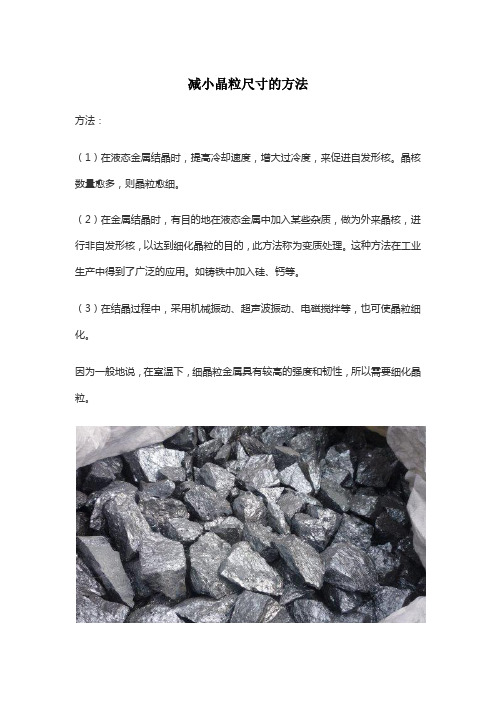
减小晶粒尺寸的方法方法:(1)在液态金属结晶时,提高冷却速度,增大过冷度,来促进自发形核。
晶核数量愈多,则晶粒愈细。
(2)在金属结晶时,有目的地在液态金属中加入某些杂质,做为外来晶核,进行非自发形核,以达到细化晶粒的目的,此方法称为变质处理。
这种方法在工业生产中得到了广泛的应用。
如铸铁中加入硅、钙等。
(3)在结晶过程中,采用机械振动、超声波振动、电磁搅拌等,也可使晶粒细化。
因为一般地说,在室温下,细晶粒金属具有较高的强度和韧性,所以需要细化晶粒。
扩展资料:理想的铸锭组织是铸锭整个截面上具有均匀、细小的等轴晶,这是因为等轴晶各向异性小,加工时变形均匀、性能优异、塑性好,利于铸造及随后的塑性加工。
要得到这种组织,通常需要对熔体进行细化处理。
都与过冷度有关,过冷度增加,形核率与长大速度都增加,但两者的增加速度不同,形核率的增长率大于长大速度的增长率。
在一般金属结晶时的过冷范围内,过冷度越大,晶粒越细小。
铝及铝合金铸锭生产中增加过冷度的方法主要有降低铸造速度、提高液态金属的冷却速度、降低浇注温度等。
但是,如果没有较多的游离晶粒的存在,增加激冷作用反而不利于细晶粒区的形成和扩大。
动态晶粒细化就是对凝固的金属进行振动和搅动,一方面依靠从外面输入能量促使晶核提前形成,另一方面使成长中的枝晶破碎,增加晶核数目。
当前已采取的方法有机械搅拌、电磁搅拌、音频振动及超声波振动等。
利用机械或电磁感应法搅动液穴中熔体,增加了熔体与冷凝壳的热交换,液穴中熔体温度降低,过冷带增大,破碎了结晶前沿的骨架,出现了大量可作为结晶核的枝晶碎块,从而使晶粒细化。
1.晶界上有界面能的作用,因此晶粒形成一个在几何学上与肥皂泡相似的三维阵列。
2.晶粒边界如果都具有基本上相同的表面张力,晶粒呈正六边形。
3.在晶界上的第二类夹杂物(杂质或气泡),如果它们在烧结温度下不与主晶相形成液相,则将阻碍晶界移动。
在烧结体内晶界移动有以下七种方式:气孔靠晶格扩散移动;气孔靠表面扩散移动;气孔靠气相传递;气孔靠晶格扩散聚合;气孔靠晶界扩散聚合;单相晶界本征迁移;存在杂质牵制晶界移动。
超声波探伤缺陷评定方法
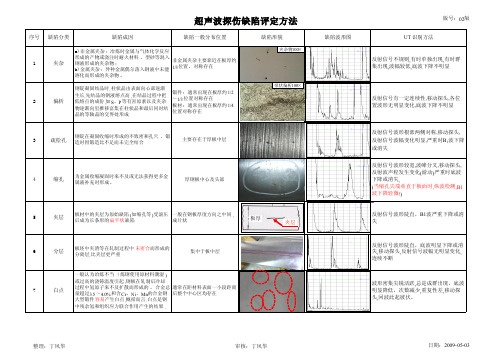
1夹杂a)非金属夹杂:冶炼时金属与气体化学反应形成的产物或浇注时耐火材料、型砂等混入钢液形成的夹杂物;b)金属夹杂:异种金属偶尔落入钢液中未能溶化而形成的夹杂物。
非金属夹杂主要靠近在板厚约1/3位置,对称存在反射信号不规则,有时单独出现,有时群集出现,波幅较低,底波下降不明显2偏析钢锭凝固结晶时,柱状晶由表面向心部逐渐生长,先结晶的钢液熔点高,在结晶过程中把低熔点的成份,如S、P等有害原素以及夹杂物逐渐向里推移富集在柱状晶和最后同时结晶的等轴晶的交界处形成锻件:通常出现在板厚约1/2~1/3位置对称存在板材:通常出现在板厚约1/4位置对称存在反射信号有一定连续性,移动探头,各位置波形无明显变化,底波下降不明显3疏松孔钢锭在凝固收缩时形成的不致密和孔穴,锻造时因锻造比不足而未完全结合主要存在于厚板中层反射信号波形根部两侧对称,移动探头,反射信号波幅变化明显,严重时B1波下降或消失4缩孔为金属收缩凝固时来不及或无法获得更多金属液补充时形成。
厚钢板中心及头部反射信号波形较宽,波峰分叉,移动探头,反射波声程发生变化(游动)严重时底波下降或消失,(当缩孔尖端垂直于板面时,纵波检测,B1波下降轻微!)5夹层板材中的夹层为原始缺陷(如缩孔等)受滚压后成为长条形的扁平状缺陷一般在钢板厚度方向之中间,成片状反射信号波形陡直,B1波严重下降或消失6分层板坯中夹渣等在轧制过程中未密合而形成的分离层,比夹层更严重集中于板中层反射信号波形陡直,底波明显下降或消失,移动探头,反射信号波幅无明显变化,连续不断7白点一般认为冶炼不当(炼钢使用原材料潮湿)或过高的浇铸温度引起,钢板在轧制后冷却过程中氢原子来不及扩散而形成的,合金总量超过3.5~4.0%和含Cr、Ni、Mn的合金钢大型锻件容易产生白点,概括而言:白点是钢中残余氢和组织应力联合作用产生的结果.通常在距材料表面一小段距离后整个中心区均存在波形密集尖锐活跃,总是成群出现,底波明显降低,次数减少,重复性差,移动探头,回波此起彼伏。
211243478_超声滚压微锻造增材件表面力学性能

的热传递自然边界条件可以描述为 [14]
元” 功能模拟材料的添加. 为保证计算精度ꎬ对网
格进行局部细化ꎬ同时将滚压头定义为刚体ꎬ模型
- k(Ñθe) = Pw - hc (θ - θ0 ) - εt σB (θ4 - θ40 ).
(5)
式中:Pw 为基板吸收总激光能量ꎻhc 为对流换热系
几何尺寸与网格划分如图 1 所示.
l = 1. b l 和 ω 则根据不同超声振动参数得到的波
Johnson - Cook 本构模型 [15] 能够很好地描述超声
形图算出. 静压力可由常数项 A0 进行施加ꎬ也可
滚压微锻造加工过程中材料的塑性力学性能. 因
此选择 Johnson - Cook 本构模型ꎬ其材料屈服极
单独作为集中力添加.
effectively reduces the risk of defects such as cracks in additive parts. Meanwhileꎬ the surface
equivalent plastic strain and surface micro ̄hardness of the processed additive increase. In additionꎬ
滚压头与被加工材料之间设置为面与面接触
限公式为
δ = ( A + Bε n ) (1 + C lnε∗ ) (1 - T ∗m ) . (7)
Copyright©博看网. All Rights Reserved.
第5 期
任朝晖等: 超声滚压微锻造增材件表面力学性能
635
和应变速率硬化效应建立了准静态模型与动态模
型ꎬ对 6061 - T6 铝合金进行了超声滚压模拟ꎬ并
超声波基础知识讲解
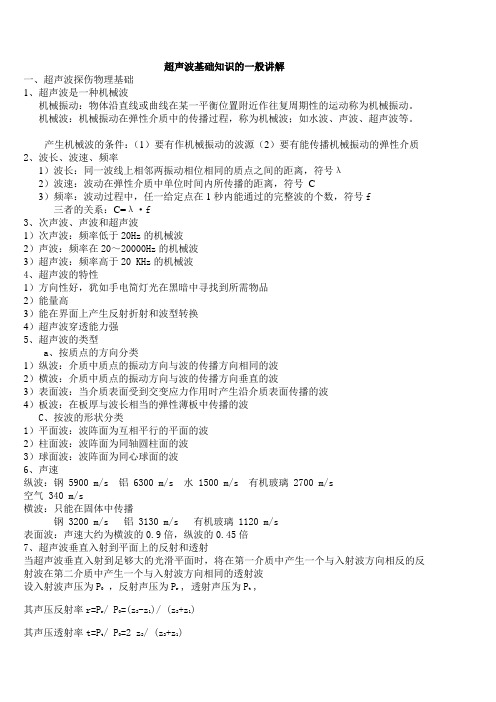
超声波基础知识的一般讲解一、超声波探伤物理基础1、超声波是一种机械波机械振动:物体沿直线或曲线在某一平衡位置附近作往复周期性的运动称为机械振动。
机械波:机械振动在弹性介质中的传播过程,称为机械波;如水波、声波、超声波等。
产生机械波的条件:(1)要有作机械振动的波源(2)要有能传播机械振动的弹性介质2、波长、波速、频率1)波长:同一波线上相邻两振动相位相同的质点之间的距离,符号λ2)波速:波动在弹性介质中单位时间内所传播的距离,符号C3)频率:波动过程中,任一给定点在1秒内能通过的完整波的个数,符号f 三者的关系:C=λ·f3、次声波、声波和超声波1)次声波:频率低于20Hz的机械波2)声波:频率在20~20000Hz的机械波3)超声波:频率高于20 KHz的机械波4、超声波的特性1)方向性好,犹如手电简灯光在黑暗中寻找到所需物品2)能量高3)能在界面上产生反射折射和波型转换4)超声波穿透能力强5、超声波的类型a、按质点的方向分类1)纵波:介质中质点的振动方向与波的传播方向相同的波2)横波:介质中质点的振动方向与波的传播方向垂直的波3)表面波:当介质表面受到交变应力作用时产生沿介质表面传播的波4)板波:在板厚与波长相当的弹性薄板中传播的波C、按波的形状分类1)平面波:波阵面为互相平行的平面的波2)柱面波:波阵面为同轴圆柱面的波3)球面波:波阵面为同心球面的波6、声速纵波:钢 5900 m/s 铝 6300 m/s 水 1500 m/s 有机玻璃 2700 m/s空气 340 m/s横波:只能在固体中传播钢 3200 m/s 铝 3130 m/s 有机玻璃 1120 m/s表面波:声速大约为横波的0.9倍,纵波的0.45倍7、超声波垂直入射到平面上的反射和透射当超声波垂直入射到足够大的光滑平面时,将在第一介质中产生一个与入射波方向相反的反射波在第二介质中产生一个与入射波方向相同的透射波设入射波声压为P0,反射声压为Pr, 透射声压为Pt,其声压反射率r=Pr / P=(z2-z1)/ (z2+z1)其声压透射率t=Pt / P=2 z2/ (z2+z1)8、超声波斜射到平面上的反射与折射波型转换:当超声波倾斜入射到异质界面时,除了产生与入射波同类型的反射波和折射波外,还会产生与入射波不同类型的反射波和折射波,称为波型转换,波型转换只可能在固体中产生。
超声波技术原理

质量目标:
合同履约率100%,顾客满意率 100%,产品交付合格率97%以上
超声波的基本物理量
振动 物体沿着直线或曲线在某一平衡位置附近做往复周期性的运动称为机械振动。 振动是往复周期性的运动。振动的快慢常用振动周期和振动频率两个物理量来描述。 周期T:振动物体完成一次全振动所需要的时间,常用单位为秒(s)。 频率f :振动物体在单位时间内完成全振动的次数,常用单位为赫兹(Hz) 二者互为倒数,既:T=1/f 如某人说话的频率f为1000Hz,表示其声带振动为1000次/秒,声带振动周期T=1/f=0.001秒 谐振动 最简单最基本的直线振动称为谐振动。任何复杂的振动都可视为多个谐振动的合成。 谐振动是一种理想条件下的振动,也就是无阻尼振动。 阻尼振动 由于克服阻力做功,振动物体的能量不断减少,同时,由于在振动传播过程中,伴随着 能量的传播也使振动物体的能量不断减少,这种振动称为阻尼运动。 受迫振动 物体受到周期性变化的外力作用时产生的振动。
t
可以看出: t-r=1
Pt 2Z 2 p0 Z 2 Z1
3、声强反射率 R 和 声强透射率 T 声强反射率:反射波声强与入射波声强之比: 声强透射率:透射波声强与入射波声强之比:
R
I2 Z Z1 2 ( 2 ) I1 Z 2 Z1
T
可以看出:T+R=1
It 4Z1 Z 2 I 0 ( Z 2 Z1 ) 2
4、板波。 在板厚与波长相当的薄板中传播的波称为板波。 (1)SH波是水平偏振的横波在薄板中传播的波。
(2)兰姆波: 对称型(S波)兰姆波的特点是薄板中心质点作纵向振动,上下表面质 点作椭圆运动、振动相位相反并对称于中心。 非对称型 (A型)兰姆波特点是薄板中心质点做横向振动。上下表面质 点作椭圆运动、振动相位相同,不对称。
浅谈镁合金晶粒细化的方法和意义

浅谈镁合金晶粒细化的方法和意义重庆大学材料科学与工程学院材料科学专业摘要 简述了镁合金的工程运用现状和细化晶粒的益处;以镁合金晶粒细化方法为主线,对镁合金在熔体阶段的过热处理、添加变质剂、物理场法、动态晶粒细化和快速凝固法,以及镁合金固态阶段的锻造、挤压、轧制和剧烈塑性变形等细化晶粒的方法进行了总结。
同时,归纳了镁合金细化晶粒的意义。
关键词 镁合金 晶粒细化 熔体 固态形变1 背景介绍纯镁是银白色金属,熔点651℃,密度为1.74×103kg/m3,是最轻的工程金属[1]。
镁合金具有密度低、比强度高、比刚度高、减振和抗冲击性能好等优点,而且还具有较好的尺寸稳定性和机械加工性能及低廉的铸造成本。
在汽车、电子、通信、航空航天、国防和3C 等行业都拥有广泛的应用前景。
但是镁合金密排六方的晶体结构特点,决定了在室温条件下独立滑移系少,导致室温塑性低、变形加工困难和变形容易开裂等阻碍了镁合金材料的广泛应用。
其次,镁合金强度偏低,无法应用于受力较大的工程环境,也成为镁合金大规模运用的一大瓶颈。
所有提高镁合金的室温塑性变形能力和强度有利于镁合金工程应用的普及和推广[2~5]。
细化晶粒是唯一可以提高金属构件强度的同时,又提高塑性的方法。
根据Hall-petch 公式210s -+=d k y σσ,材料的强度随着晶粒尺寸的减小而增大。
镁合金具有很大的系数k y ,所有,细化晶粒能够显著的提高镁合金的强度[6]。
而且,由于有细小均匀晶粒的材料发生塑性变形时,各晶粒分担一定的变形量,使变形更加均匀,位错在晶界处塞积少,应力集中小,材料开裂的倾向减小,从而提高材料的塑性。
2 晶粒细化方法目前用于工程和科研中有很多细化镁合金晶粒的方法,笔者综合相关论文报道将镁合金晶粒细化分为两个阶段细化:熔体阶段细化和固态形变处理细化。
2.1 熔体阶段细化2.1.1 过热处理法过热处理是浇注前将熔体温度升高并保持一段时间后再降温至浇注温度进行浇注的工艺过程。
无损检测Ⅱ级人员超声(UT)铸件门类专业知识试题
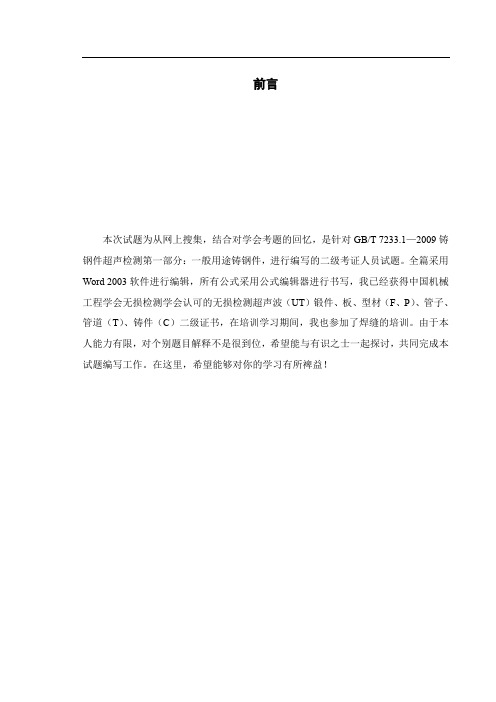
前言本次试题为从网上搜集,结合对学会考题的回忆,是针对GB/T 7233.1—2009铸钢件超声检测第一部分:一般用途铸钢件,进行编写的二级考证人员试题。
全篇采用Word 2003软件进行编辑,所有公式采用公式编辑器进行书写,我已经获得中国机械工程学会无损检测学会认可的无损检测超声波(UT)锻件、板、型材(F、P)、管子、管道(T)、铸件(C)二级证书,在培训学习期间,我也参加了焊缝的培训。
由于本人能力有限,对个别题目解释不是很到位,希望能与有识之士一起探讨,共同完成本试题编写工作。
在这里,希望能够对你的学习有所裨益!无损检测Ⅱ级人员超声(UT)铸件门类专业知识试题选择题,选择答案,请将你认为正确选项的序号字母填入试题之后的括号内,每个试题只有一个正确选项。
1.铸件探伤中,如果材料的晶粒粗大,通常会引起(D)A.底波降低或消失B.有较高的噪声显示C.使声波穿透力降低D.以上全部答案及解析:D 当材料晶粒粗大时,散射衰减严重,被散射的超声波沿着复杂的路径传播到探头,在示波屏上引起林状回波(草波),使信噪比下降,严重时,噪声淹没缺陷波。
2.下述与GB/T 7233.1-2009标准规定的适用范围不相符合的是(D)A.本标准规定了一般用途奥氏体铸钢件超声检测的术语和定义,一般要求和应用脉冲反射技术检测内部不连续的方法B.本标准适用于一般用途奥氏体铸钢件细化晶粒热处理后且厚度不超过mm600的铸钢件超声波检测C.本标准对于厚度大于mm600奥氏体钢铸钢件,应有协议规定检测方法和验收等级D.以上均不对答案及解析:D 依据铸钢件超声检测(第一部分:一般用途铸钢件)GB/T 7233.1-2009第一章范围,GB/T 7233的本部分规定了一般用途铸钢件(非奥氏体)超声检测的术语与定义、一般要求和应用脉冲反射技术检测内部缺陷的方法。
本部分适用于一般600铸钢件的超声检测。
对于用途铸钢件(非奥氏体)细化晶粒后且厚度不超过mm厚度大于mm 600的铸钢件,应有协议规定检测方法和记录限值。
- 1、下载文档前请自行甄别文档内容的完整性,平台不提供额外的编辑、内容补充、找答案等附加服务。
- 2、"仅部分预览"的文档,不可在线预览部分如存在完整性等问题,可反馈申请退款(可完整预览的文档不适用该条件!)。
- 3、如文档侵犯您的权益,请联系客服反馈,我们会尽快为您处理(人工客服工作时间:9:00-18:30)。
摘要:本文简要介绍了超声波及其基本特性,综述了高能超声对金属凝固过程作用的研究和应用状况,提出超声处理是改善金属凝固组织、提高力学性能的有效方法,并对21世纪超声凝固细晶技术的前景进行了展望。
关键词:超声波金属凝固
高能超声具有独特的声学效应。
在金属凝固过程中引入超声振动,凝固组织从粗大的柱状晶变为均匀细等轴晶,金属的宏观及微观偏析均得到改善[1]。
目前国外这方面的一些研究成果已经应用于生产中[ 2-3],而国内相关研究报道很少。
1 超声波及其特性
超声波通常指1秒内振动20000次以上的高频声波。
在强度较低时,超声波可以作为探测负载信息的载体与媒介,称为检测超声。
当其强度超过一定值,则与传声媒质相互作用,可以改变以至破坏传声媒质的状态、性质及结构,称为高能超声或功率超声。
本文涉及的主要是高能超声。
超声波具有以下四个基本特性:
(1) 束射特性。
超声波波长短,可以集中成一束射线。
(2) 吸收特性。
超声波在空气、液体和固体中均会被吸收。
空气中的吸收最强烈,固体中的吸收最微弱。
(3) 高功率。
由于频率高,超声波的功率比声波大得多,它不仅能使所作用的介质产生急速运动,甚至会破坏其分子结构。
(4) 声压作用。
声波振动使物质分子产生压缩和稀疏作用,这种由于声波振动引起的附加压力现象叫声压作用。
上述四个基本特性使超声波在媒体中导致如下五种效应:力学效应、热学效应、光学效应、电学效应和化学效应[4]。
2.2超声波对金属凝固组织的作用
2.2.1超声波对纯金属凝固组织的作用
Eskin用超声波处理高纯铝,处理后使晶粒度从3.1增加到37.5,拉伸强度从54MPa提高到70MPa,硬度从HB17.2提高到HB19.7,同时延伸率也得到了改善[10]。
Abramov和Gurevich 使用超声波处理具有不同点阵结构的纯金属[11],结果表明超声处理能使具有不同点阵结构的金属晶粒细化,力学性能提高。
2.2.2超声振动对低熔点合金凝固组织的作用
Eskin等人采用10kW的超声波对铝合金的凝固过程进行了较为深入的研究[5,12]。
试验表明,纯铝经过超声处理,拉伸强度可以提高6-10%,而含有微量元素的铝经过超声处理拉伸强度却可以提高20-25%。
在连续铸造中,用超声波处理Al-Si合金,也取得了良好的效果,对初生Si相的细化作用十分显著(见图1) [13]。
李英龙等人研究了全过程和结晶前超声处理对Al-Si合金组织和性能的影响 [14]。
实验结果表明,声强为3.5W/2的全过程超声处理使共晶Si相显著细化,断裂并呈粒状分布,断裂处有局部熔化现象,棱角变钝。
而以同样的声强结晶前超声处理虽然也能使共晶硅细化,但其仍呈针片状分布,晶粒没有断裂现象。
赵忠兴等人采用底部导入方式对铝合金进行超声处理[15]。
经超声处理的合金组织得到明显细化,树枝晶被打碎,形成均匀的等轴晶或粒状晶组织。
(a) 原始铝合金 (b) 经过超声处理的铝合金
图1 过共晶硅(36%Si)的微观组织[13]
赵忠兴等人采用底部导入方式对铝合金进行超声处理[15]。
经超声处理的合金组织得到明显细化,树枝晶被打碎,形成均匀的等轴晶或粒状晶组织。
2.2.3超声振动对钢和铁凝固组织的作用
超声处理对钢和铸铁的细化效果也是十分明显的。
研究表明,普通碳钢中含碳量越高,超声处理的效果就越明显。
对st40钢进行变质和超声振动的联合处理试验[16],不仅得到了晶粒细化的珠光体组织,而且铁素体网也被打碎。
超声处理使W18工具钢中碳化物偏析明显减轻,微观组织得到细化,共晶体碳化物也得到细化[17]。
Abramov研究了超声处理对钢力学性能的影响[18]。
对于铸态亚共析碳钢,超声处理后强度提高20-30%,塑性提高了30-40%;而过共析钢经超声处理后,屈服强度提高了75%,同时塑性也有增加。
经过超声处理的铁素体和奥氏体钢无论是在室温还是在工作温度下,强度和塑性同时得到了改善。
赵忠兴探讨了超声波对HT100灰铸铁凝固组织的影响[15],结果表明,超声处理使灰铁共晶石墨片变短、变粗。
2.3 超声细化的应用研究
Taha对影响超声细化的参数进行了研究[2]。
研究表明,细化程度和超声波的输入能量、合金成分和铸件厚度有关。
随着超声输入金属熔液中能量的增加,冷却速度被减缓,当冷却速度慢到一定程度时,凝固组织粗化。
对Pb-Sb合金,当Sb的含量为0.5%wt时,超声处理的作用并不显著。
而当Sb的含量大于2%wt时,超声处理的细化作用就非常显著。
对于厚度是10mm的Pb-4wt%Sb铸件,超声振动并不使整个铸件均匀细化。
在离振动源较远处,树枝状
组织仍然出现。
而对于4mm的铸件,在超声振动作用下,整个铸件得到了均匀细化。
Abdel -Rehim[3]在不同形状的铸件凝固过程中应用超声波,证明超声波对复杂件组织同样有细化作用。
2.4超声细化的机理研究
国外众多学者对超声细化的机理进行了探讨,提出了破碎理论和过冷生核理论[1,19,20],这些理论的核心主要是声空化现象。
(1)超声破碎理论。
该理论认为高能超声形成的大量空化气泡在超过一定阈值的声压下发生崩溃并产生激波,将已结晶长大的晶粒打碎,使晶粒得到细化[1,19,20]。
(2)过冷生核理论。
还有一些学者认为[1,20 ],超声波产生的空化泡的增大和内部液体的蒸发会降低空化泡的温度,这将导致空化泡表面的金属熔液温度降低,因此在空化泡的附近就可能形成晶核。
Abdel-Rehim根据前人的工作,超声处理的细晶作用归纳为以下四方面[19]:(1)空化现象引起的空冷;(2)振荡器的冷却和搅拌;(3)坩埚壁的冷却;(4)脉冲超声的时间延迟。
3 超声凝固细晶技术的前景
关于超声波对金属凝固过程作用的研究始于20世纪30年代,60年代出现了高潮,而70至90年代却无太大的进展。
这一方面是由于材料领域的孕育处理、变质处理、电磁搅拌和微合金化等凝固细晶技术在这一时期发展很快,人们更愿意接受工艺简单的凝固细晶技术。
另一方面对变幅杆耐高温性能和对超声波大功率的要求制约了该技术的应用。
值得注意的是,人类进入21世纪后,一方面,环保意识的提高呼唤着绿色材料的诞生。
绿色材料不仅要求减少材料制备对环境的污染,同时要求减少对材料本身的污染,即减少元素的含量,提高材料的可回用性。
无污染的物理细晶技术无疑将在新世纪备受关注。
另一方面,物理、材料和电子等领域科学技术的飞速发展使大功率超声设备和耐高温变幅杆的生产成为可能,特别是非接触式电磁超声波的诞生为该超声技术在金属制备中的应用开辟了更广阔的空间。
因此,我们相信超声凝固细晶技术将会再度成为材料领域的研究热点,而输出峰值高、负荷小的电磁脉冲超声波将会成为超声凝固细晶技术的新亮点。