消失模粘沙气孔 夹渣 的缺陷防治
消失模铸件出现气孔或者夹砂怎么解决
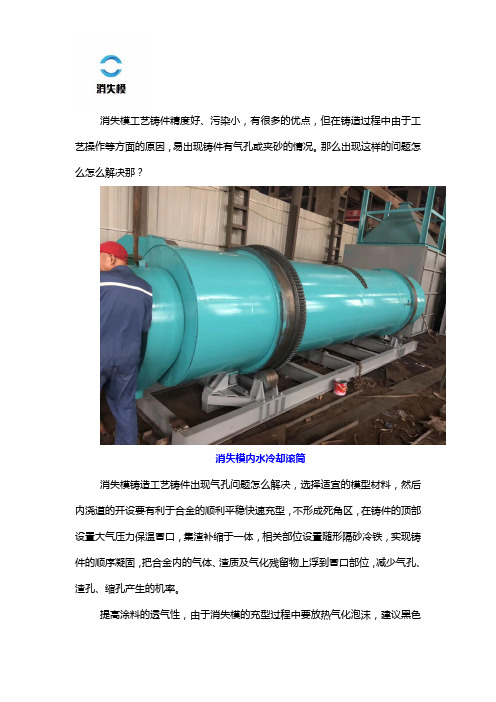
消失模工艺铸件精度好、污染小,有很多的优点,但在铸造过程中由于工艺操作等方面的原因,易出现铸件有气孔或夹砂的情况。
那么出现这样的问题怎么怎么解决那?
消失模内水冷却滚筒
消失模铸造工艺铸件出现气孔问题怎么解决,选择适宜的模型材料,然后内浇道的开设要有利于合金的顺利平稳快速充型,不形成死角区,在铸件的顶部设置大气压力保温冒口,集渣补缩于一体,相关部位设置随形隔砂冷铁,实现铸件的顺序凝固,把合金内的气体、渣质及气化残留物上浮到冒口部位,减少气孔、渣孔、缩孔产生的机率。
提高涂料的透气性,由于消失模的充型过程中要放热气化泡沫,建议黑色
合金的浇注温度较砂型铸造高30-50℃。
铸件的浇注位置是充型时获得良好的气化条件及排气条件。
自动线液压翻箱机
想要解决消失模铸造遇到的夹砂问题,都需要知道原因,浇口杯与直浇道以及浇注系统之间的连接处密封不好,尤其是直浇道与浇口杯的连接密封不好,在负压的作用下很容易形成夹砂及气孔。
型砂的粒度太细,粉尘含量高,透气性差,负压管道内部堵塞造成负压度失真,使砂箱的负压值远远低于指示表负压值,气化物不能及时排出涂层而形成气孔或皱皮。
浇注温度低,充型前沿金属液不能使泡沫充分气化,未分解的残余物质太多,来不及浮集到冒口而凝固在铸件中。
以上的有一些问题在铸造过程中就需要注意了,注意一些就会很少出现的。
消失模系统设备包括:真空负压系统、三维振动台、空壳振动浇注台、负压砂箱、高速涂料搅拌机,落砂床、振动沸腾冷却床、振动粗细
筛、滚动冷却床、管冷式砂温调节器、链斗式提升机、气箱脉冲除尘器,磁选风选机、液压自动翻箱机等。
恒盛机械制造有限公司主要从事消失模设备制造、消失模工艺研究、消失模铸件生产为一体的综合性公司。
消失模铸造缺陷产生的原因及解决措施

消失模铸造缺陷产生的原因及解决措施一、消失模铸造缺陷的原因:1.模具设计不合理:模具的设计不合理是导致消失模铸造缺陷的主要原因之一、例如,模具的冷却系统设计不良或者模具结构不稳定,都会对铸件的形状和内部结构造成影响。
2.熔融金属冷却不均匀:熔融金属冷却不均匀也是导致消失模铸造缺陷的一个重要原因。
由于冷却速度不均匀,可能会导致铸件中出现热裂纹、气孔等缺陷。
3.模芯破损或散粘:消失模铸造过程中,如果模芯破损或散粘,会导致熔融金属进入模芯使其变形或者破裂。
4.硅溶胶合成不当:硅溶胶在消失模铸造中被用于形成陶瓷壳体,如果硅溶胶的合成过程不当,可能会导致模具的整体性能下降,从而产生各种缺陷。
5.炭化物形成不完全:在消失模铸造中,树脂炭化后形成的剩余炭化物对于确保铸件的完整性非常重要。
如果炭化物形成不完全,可能会导致铸件出现裂纹、气孔等缺陷。
二、消失模铸造缺陷的解决措施:1.设计合理的模具:在消失模铸造过程中,通过合理设计模具的冷却系统,可以提高铸件的冷却均匀性,减少缺陷的发生。
此外,模具的结构也应当稳定,以确保铸件形状和内部结构的准确性。
2.控制熔融金属温度和冷却速度:通过控制熔融金属的温度和冷却速度,可以减少热裂纹和气孔等缺陷的发生。
合理的工艺参数能够提高铸件的材质均匀性和密度。
3.检查模芯质量:在消失模铸造过程中,应该定期检查模芯的质量,以确保其完整性和稳定性。
如果发现模芯破损或者散粘,应及时更换或修复。
4.合理合成硅溶胶:在合成硅溶胶的过程中,应严格按照工艺要求进行操作。
确保硅溶胶的质量和性能,以避免模具整体性能下降。
5.控制炭化物的形成:合理控制炭化物的形成可以避免铸件的裂纹和气孔等缺陷的发生。
在树脂炭化的过程中,应注意控制炭化的温度和时间,确保炭化物的形成充分和均匀。
综上所述,消失模铸造缺陷的产生原因有模具设计不合理、熔融金属冷却不均匀、模芯破损或散粘、硅溶胶合成不当以及炭化物形成不完全等因素。
消失模铸造缺陷及解决措施

铸造缺陷及解决措施:1、砂眼(或白灰):是铸件的致命缺陷,重则报废。
要做到:①、浇口杯、直浇道、横浇道、内浇道与铸件封闭结合严密。
如不严密,在负压的作用下就会吸入砂子,所以装箱者一定要精心操作,把好各关口。
任何一个薄弱环节或疏忽都会造成此类缺陷。
②浇注系统多刷一遍涂料以增强其强度。
③涂料的强度、透气性、刚度、耐火度、暴热抗烈性也很重要,因为在运输、装填砂、震动时都会出现破坏、变形、开裂、脱落。
④震实时,开始幅度要小,待填满砂时再振幅大些。
⑤浇口杯无浮砂、尘土等杂物。
⑥浇注时,浇包嘴尽量靠近浇口杯,以免压力头过大。
⑦负压过大,使金属液流经开裂、裂纹处时,吸入干砂和杂物可能性加大,粘砂严重。
⑧过快的充型速度使冲刷力加大。
2、气孔:①浇注温度低,充型前沿金属液不能使泡沫充分分解汽化,未分解的残留物质来不及浮集到上面及冒口中,汽化分解生成的气体及残留物不能及时排出铸型而凝固在铸件中,另外,摸样分解不充分,液相残留物会堵塞涂料层,使热解气体排出受阻,腔内形成反压力,充型流动性下降,凝固快。
②涂料透气性差或负压不足,砂子透气性差,不能及时排除型腔内的气体及残留物,在充型压力下形成气孔。
③浇注速度慢,浇口杯未充满,暴露直浇道卷入空气,吸入杂质,形成携裹气孔和渣孔。
④浇杯容量小,金属液形成涡流,侵入空气生成气孔。
⑤浇口杯及浇注系统之间的连接处密封不好,尤其是直浇道和浇口杯。
在负压作用下很容易形成夹砂及气孔。
⑥型砂粒度太细,粉尘含量高,透气性差,负压管道内部堵塞,造成负压度失真,使型腔周围的负压值远低于指示负压,汽化物不能及时排出涂料层而形成气孔或皱皮。
⑦合理的浇注工艺和负压度。
消失模浇注工艺是以充满封闭直浇道为原则,不能忽快忽慢、紊流、断流,更不允许暴露直浇道。
浇注速度,尤其是在行车提升停顿瞬间力求平衡,不断流。
进入尾期慢慢收包,使渣、气、及汽化残留物有充分时间浮集到浇冒口中。
负压度过大,加剧金属液渗透粘砂,并造成附壁效应,不利于液相泡沫被涂层吸附,生成很多气孔。
消失模铸件粘砂缺陷成因及预防措施
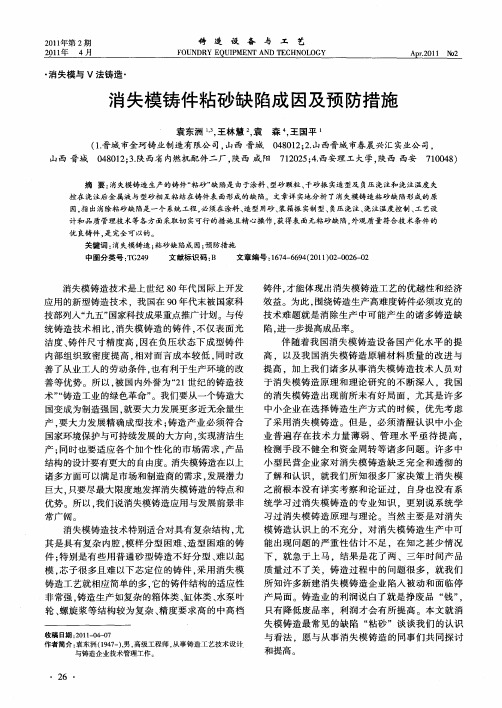
控 在浇注后金属液 与型砂相 互粘结在铸件表 面形成 的缺 陷。文章详 实地分析 了消失模铸 造粘砂缺 陷形成的原
因. 出消除粘砂缺 陷是一个 系统工程 . 指 必须在涂料 、 造型用砂 、 箱振 实制型 、 装 负压浇注 、 注温度控 制、 艺设 浇 工
计 和品质管理技术等各 方面采取 切 实可行 的措施且精 心操 作 , 获得表 面无粘砂缺 陷, 外观质量符合技 术条件的
产 局面。铸造业 的利润说 白了就是挣废 品 “ ” 钱 , 只有降低废 品率 ,利 润才会有 所提高 。本文就消 失模铸造最 常见 的缺 陷 “ 粘砂 ”谈谈我们 的认识 与看法 ,愿与从 事消失模铸 造的 同事们共 同探讨 和提 高
作者简介 : 袁东洲 (9 7 ) , 14一, 高级工程师 , 事铸造工艺 技术设计 男 从
消失模铸造工艺一般先在加工好 的塑料 泡沫
模 样表 面 涂刷 一 定 厚度 的耐 火涂 料 , 后 放人 砂 箱 然
为涂层越厚越容易产生裂纹 , 裂纹就给粘砂创造 了 条件。 依据所生产 的铸件提高涂料的耐火度是绝不 可忽视 的重要 因素。严把涂料配制和涂刷质量关 , 尤其是对涂料层厚度 的监控 , 要因件 、 因料 、 因时进 行严格又灵活的作业 , 确保涂层满足工艺要求。 2 造型时紧实力不可过大 , 防造型时涂层受 ) 预 到破坏 。添砂后振动力过大或振动时间过长 。 涂层 容易开裂 。干砂振动造型的经验是 : 频率 5 z 0H 左
优 良铸 件 。 完全 可以的。 是 关键词 : 消失模铸造 ; 粘砂缺 陷成因; 预防措施 中图分类号 :G 4 T 29 文献标识码 : B 文章编号 :6 4 6 9 (0 0 — 0 6 0 1 7 — 6 4 2 1) 2 0 2 — 2 1
消失模铸件夹砂和夹渣缺陷的成因及对策

文 献 标识 码 : B
文 章编 号 :0 3 8 4 (0 0)6 0 5 03 10 — 3 5 2 1 0 — 0 6
—
D :036 /i n10 — 3 52 1.6 1 OI1 . 9 .s. 3 84 .0 0 . 3 9 js 0 00
Sa nd ncuso a I l i n nd ag I l in Sl ncuso For ato Re o m i n as nsand Co unt r e ur so e m as e fLos o m s i s tf a Ca tng W ANG n— t Li hu I ZHANG o i g , Ba —q n 2 YUAN m g z o 3 PEIH u i g W ANG o D( - h u , —p n 4 Gu —pi ’ ng
、
、
用正 确 的 负 压 浇 注 T 艺参 数 , 渣 挡 渣撇 渣 技 术 以及铁 液 过 滤 、 化 技 术 等 , 以减 少 和 消 除 夹砂 夹渣 缺 陷 。 集 净 可 关键 词 : 消失 模 铸 造 ; 砂 、 渣 缺 陷 ; 策 夹 夹 对
、
0 NC 类 号 : G 4 .;G 5 . 0 - y T 2 95T 2 06
.
4 0 5 C i a 3Jn e F u d n f cu e Co L d ,i c e g 0 8 1 C i a 4 J c e gX  ̄i F u d o Ld , 5 0 2, h n ; . k o n r Ma u a tr . t .Jn h n 4 0 h n ; i h n i n o n r C . t. i y 2, n y
.
o t h t t e a d n sa i cu i n d fc s o l b r d c d n ei n td y d p i g ( r c v c u u t a h s n a d lg n l s s e e t o c u d e e u e a d l mi ae b a o t 。 r t a u m p u i g n 0 e 0 rn
消失模铸钢件气孔缺陷及解决措施
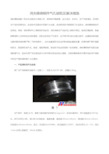
消失模铸钢件气孔缺陷及解决措施消失模铸造是一种近无切削加工铸造工艺,具有铸件精度高、设计灵活、无砂芯、生产环境清洁、投资和生产成本低等优点。
此项技术在国内外发展十分迅速,各项相关技术都取得了长足进步。
消失模铸造技术在铸铝、铸铜、铸铁等材料上得到较好的应用,但在铸钢生产的应用上则相对滞后。
虽然在高锰钢、耐磨钢等钢种上也有成功应用的报道,但在实际的生产过程中,由于铸件在浇注充型过程中,金属液的流动前沿是热解的消失模产物(气体和液体),会与金属液发生反应并影响到金属液质量,如果热解产物不能顺利排出,就容易引起气孔、增碳、增氢等缺陷,使该技术的应用受到一定的限制。
消失模铸钢件的常见缺陷就是气孔,因此对其产生的原因进行分析并提出相应的防止措施,为消失模铸造技术更好地应用于铸钢件的生产提供指导是十分必要的。
一、产品现状及气孔成因我厂生产的铸钢件迷宫环(见图1),材质为ZG270-500,质量为35kg。
生产条件:每箱10件、聚苯乙烯泡塑料的密度为22g/cm3,采用水基涂料,烘干室温度为45℃左右,烘干时间为48h,冒口用AB胶粘接,垂直放置,直浇道45mm×45mm,横浇道40mm×25mm,内浇道为20mm×15mm。
底注,负压度为0.05MPa,浇注温度为1550℃,浇注时间为13~17s,浇注3min后停止抽真空,30min后落砂。
机加工后在补缩冒口处发现大量分散性气孔,出现在铸件内部和铸件表面上(见图1),最大的直径达3mm,深度达4mm,不合格品率达60%。
我们对气孔缺陷进行系统的整理和分析,认为形成的气孔主要是侵入性气孔和析出性气孔,并对产生的原因进行了较深入的探讨。
气孔的形成来源于气体。
消失模铸造铸钢迷宫环上的气孔主要是由泡沫汽化产生的气体侵入金属液析出而形成的侵入性气孔,以及钢液中带入的析出性气孔。
1.侵入性气孔的成因侵入性气孔是消失模铸钢件气孔产生的主要形式,其形成原因有以下几方面。
浅析消失模铸造中进砂夹渣缺陷的预防措施

2 预 防控 制进 砂夹渣 类缺 陷的措 施 用 消 失模 铸 造生 产制 造 的渣 浆 泵 叶轮 、 出 口 进
Th e e tv e s e fDe e t n Lo tFo m si g e Pr v n i e M a ur so f c si s a Ca tn
G DⅣ G yh
(h i h agIdsr l u p FcoyC . , S ( M H b i 5 10 C ia S  ̄a un uta P m atr o, J c z n i f , e e 0 0 0 , hn )
A bsr t n l s o m a tng,h e e t f s nd n sa ic u ins we e o c r d e a s t o tng l y r wa s d y t ac :I o tf a c si t e d f cs o a a d l g n l so r c u e b c u e he c a i a e s wa he b
在 生 产 中验 证 ,当使用 的造 型 干砂 为宝 珠砂 时 , 加 工 后 呈 现 的斑 点 为黑灰 色 , 当使 用 的 干砂 为 石英 而
砂时 , 斑点 为 白色 , 称 “ 俗 白点 ” 。我 们把 这类 缺陷称
造的铸件近无加工余量 、 且尺寸结构精确等诸多优 点, 备受 铸造 企业 的青 睐 。近 几年 , 为 了不少铸 造 成
2 1 第 3期 0 2年
21 0 2年 6月
铸
造
设
备Hale Waihona Puke 与工艺 Jn2 1 N3 u . 2 o 0
F U D YE U P E TA DT C O O Y O N R Q IM N N E HN L G
消失模铸件易出现的缺陷及消除措施

消失模铸件易出现的缺陷及消除措施―攀枝花钢铁研究院试验中心陈建钢1、粘砂金属液渗入型砂中,形成金属与型砂的机械混合物,其中有两种情况:一种是金属液通过涂层开裂处渗入型砂中,形成铁包砂(即机械粘砂),此种缺陷一般可以清除掉;另一种情况是金属透过涂层渗入型砂中,形成难以清除的化学粘砂。
(一)产生的原因(1)在涂层开裂的情况下,由于型砂紧实度不够,型砂颗粒过大及真空度过高产生第一种粘砂情况;(2)在涂层过薄或局部未刷到的情况下,由于金属液温度较高,真空度较大时产生第二种粘砂。
(二)防止措施(1)提高涂层的厚度和耐火度。
(2)造型时紧实力不宜过大以免破坏涂层。
(3)选择合适的负压。
(4)选用较细的原砂。
(5)浇注温度不宜过高。
(6)选择合适的压力头。
2、气孔(一)气孔的分类(1)浇注时卷入空气形成的气孔。
(2)泡沫塑料模样分解产生的气孔。
(3)模样涂层不干引起的气孔。
(4)金属液脱氧不好引起的气孔。
(二)浇注时卷入空气形成的气孔消失模铸造浇注过程中如果直浇道不能充满就会卷入空气,这些气体若不能及时排出,就有产生气孔缺陷的可能。
防止卷入气体的措施:(1)采用封闭式的浇注系统。
(2)浇注时维持浇口盆内有一定的液体金属以保持直浇道处于充满状态。
(3)正确掌握浇注方法,采用慢—快—慢的浇注方法。
(三)泡沫塑料模样分解产生的气孔EPS和STMMA热解后产生大量的气体,如果充型平稳,金属与模样逐层置换,这些气体就会顺利通过液体前沿与模样间的气隙经铸型排出,特别在铸型处于负压状态下更有利气体排放,铸件不易产生气孔缺陷。
但是如果充型过程产生紊流或者顶注,侧注情况下、部分模样被金属液包围后进行分解产生的气体不能从金属液中排出时就会产生缺陷,这种气孔表面有炭黑存在。
防止措施:(1)改进浇注方案,使充型过程逐层置换,不产生紊流。
(2)提高浇注温度。
(3)在不发生紊流的情况下,适当提高真空度,如果发生紊流而产生气孔时,可适当降低真空度。
怎样消除消失模铸造中的夹渣
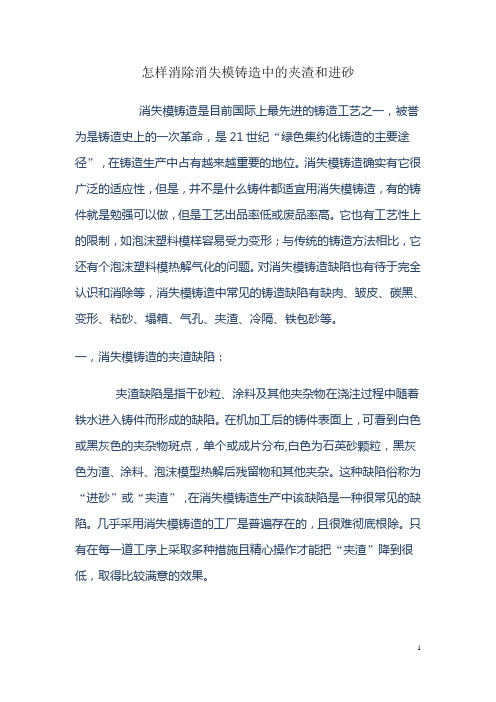
怎样消除消失模铸造中的夹渣和进砂消失模铸造是目前国际上最先进的铸造工艺之一,被誉为是铸造史上的一次革命,是21世纪“绿色集约化铸造的主要途径”,在铸造生产中占有越来越重要的地位。
消失模铸造确实有它很广泛的适应性,但是,并不是什么铸件都适宜用消失模铸造,有的铸件就是勉强可以做,但是工艺出品率低或废品率高。
它也有工艺性上的限制,如泡沫塑料模样容易受力变形;与传统的铸造方法相比,它还有个泡沫塑料模热解气化的问题。
对消失模铸造缺陷也有待于完全认识和消除等,消失模铸造中常见的铸造缺陷有缺肉、皱皮、碳黑、变形、粘砂、塌箱、气孔、夹渣、冷隔、铁包砂等。
一,消失模铸造的夹渣缺陷:夹渣缺陷是指干砂粒、涂料及其他夹杂物在浇注过程中随着铁水进入铸件而形成的缺陷。
在机加工后的铸件表面上,可看到白色或黑灰色的夹杂物斑点,单个或成片分布,白色为石英砂颗粒,黑灰色为渣、涂料、泡沫模型热解后残留物和其他夹杂。
这种缺陷俗称为“进砂”或“夹渣”,在消失模铸造生产中该缺陷是一种很常见的缺陷。
几乎采用消失模铸造的工厂是普遍存在的,且很难彻底根除。
只有在每一道工序上采取多种措施且精心操作才能把“夹渣”降到很低,取得比较满意的效果。
在消失模铸件冷却打箱后未清理前,根据铸件及浇注系统表面状况,即可以判定有没有进砂和夹渣缺陷。
如果浇口杯、直浇道、横浇道、内浇道和浇口表面或连接处以及铸件表面粘砂严重或有裂纹状粘砂存在,则基本可以肯定铸件有夹渣和进砂缺陷。
砸断浇道棒或浇道拉筋,可看到断口上有白色斑点,严重时断口形成一圈白色斑点。
这样的铸件,特别是板状、圆饼状铸件机加工后加工面上就会有白色、黑灰色斑点缺陷。
像制动鼓铸件是最易进砂的一类铸件,如果工序操作规程控制不严格,生产的铸件严重的影响了铸件质量和定单完成的进度。
二,造成夹渣和进砂缺陷的原因经过我们在生产实践中长期观察证明,从浇口杯、直浇道、横浇道、内浇道至铸件,所有部位都有可能造成进砂,特别是浇注系统与铸件的结合部位。
铸钢件的夹砂、粘砂、砂眼缺陷产生原因及防治措施

1.铸钢件的夹砂(1)夹砂缺陷产生的原因分析夹砂是表面缺陷,也是铸件常见的缺陷之一,生产中也常称为包砂、起皮子、夹层等。
夹砂的表现形式如图5-13所示。
夹砂在铸件上表现为高出铸件表面形状不规则的金属瘤状物或片状物,其表面粗糙,中间夹有砂层或涂料层。
清除后,铸件表面出现局部凹陷,夹砂严重时可能会把铸件壁厚穿透。
在浇注过程中,接触钢液的铸型表层型砂由于受到高温钢液的作用而急剧升温,由于型砂的导热性能不好,使高温的型砂表层与较低温度的型砂内层之间出现温度差,形成热应力。
同时表层型砂也因受热而膨胀,同时石英在573℃时出现晶格转变引起的膨胀,也会加剧表层型砂的膨胀和内外层型砂的热应力。
在热应力超过型砂的结合强度时,表层型砂与内层型砂之间将出现脱离,外层突起,以至翘裂,使钢液进入其中,而形成夹砂缺陷。
(2)夹砂缺陷的防止依据夹砂产生的原因,在生产中通常采用以下方法防止夹砂。
1)如果夹砂成批出现,可能是型砂性能不好,除了考虑改用膨胀系数小、导热性能好的型砂外,对石英为主的型砂来说还可以选择粒度分散的原砂。
2)在造型工艺和操作上力求舂砂均匀,防止局部过硬或过松;修型时应避免反复修抹砂型表面;应少用水,多扎气眼;在砂型工作表面插针子、刷涂料,使其渗入一定深度,增加表面层与内层的结合强度。
3)从工艺方案选择。
对大平面铸件采用倾斜浇注,减少钢液对上平面的热辐射,并注意使铸型能较快充满。
浇注时采用低温快注,减少型砂的受热强度和时间。
2.铸钢件的粘砂(1)粘砂缺陷产生的原因分析型砂粘在铸件表面不能脱落或难于脱落的现象称为粘砂,粘砂可能发生在任何部位,但在铸件的热节处、转角处和壁厚较厚的位置处比较容易发生粘砂。
粘砂按未脱落砂子(或砂层)与铸件表面联结性质的不同分为机械粘砂、化学粘砂和热粘砂。
粘砂一般不至于造成铸件报废,但会给生产带来许多不便,给清理工作增加了许多困难和工作量。
同时也给机加工带来许多困难,并加快刀具的磨损。
消失模铸件的缺陷与防治

消失模铸件的缺陷与防治铸件缺陷是导致铸件渗漏和报废的主要原因。
铸件缺陷主要有塌箱、抬箱、壁厚不均匀、变形、冷隔和浇不到、粘砂、气孔、缩孔和缩松、皱皮、珠粒状缺陷、节瘤等。
一、塌箱在浇注过程中铸型局部向下塌陷,金属液不能充满型腔,使铸件不能形成或局部缺肉称为塌箱。
(一)塌箱产生的原因(1)铸型顶部吃砂量过小,真空度不够,液体金属浮力使铸型顶部型砂溃散造成铸件成形不良。
(2)液体金属充型上升速度过慢或停流,使模样与金属前沿间隙过大,铸型内气压与砂型压力总和大于间隙内气压,造成铸型移动和坍塌使铸件成形不良。
(3)砂箱内的原始真空度定的太低,特别是深腔内由于模样壁的阻隔作用,其真空度更低。
(4)浇注过程中由于模样气化产生大量气体,排气过程中,真空度下降且造成砂子流动,损坏涂层使砂子进入型腔。
(5)砂温过高(大于70 C),把模样烫坏导致垮砂。
(二)主要防止措施(1)增加铸型顶部吃砂量及在铸型顶部放置压铁,防止液体金属浮力过大造成铸型上面溃散(2)采用合适的真空度(即浇注前真空度不低于-0.06MPa、浇注后真空度不低于-0.05MPa)及密封措施,以保证型砂的强度。
负压系统有足够大的排气能力。
(3)选用强度高透气好的涂料。
(4)选用较粗的原砂增加砂子的透气性。
(5)合理的设计浇注系统。
直浇道面积大于内浇道面积,直浇道不能与铸件距离太近,内浇道长度至少为25mm。
(6)选用低密度的泡沫塑料模(低于26kg/m3)和减少热熔胶的使用量,减少发气量。
(7)砂温不高于70C。
二、抬箱在浇注过程中铸型上表面向上移动,使铸件上部出现全部或局部多肉称为抬箱。
(一)抬箱产生的原因(1)砂箱内真空度偏低,型砂强度不够。
(2)浇注完后,真空度消失过早。
(3)铸件上面吃砂量太少,压力太小。
(二)主要防止措施(1)保证砂箱内有足够的真空度。
(2)浇注后,真空保持时间不少于3min。
(3)造型时,保证铸件上面的型砂高度大于200mm三、变形铸件几何形状与图样不符,诸如铸件弯曲弯曲变形、椭圆、壁厚不均等。
消失模铸造缺陷有

消失模铸造缺陷有:铸铁件表面皱皮( 积碳) ,铸钢件增碳,反喷、气孔,尺寸超差、变形,塌箱、溃型,粘砂。
节瘤、针刺,冷隔( 对火) 、重皮、浇不到( 足) ,渣孔、砂孔、缩孔、凹陷及网纹,内部夹杂物,缩松、组织不均等,其主要影响因素如下。
1 白模( 模样) 涂料1 .1 白模( 模样) 常见缺陷及防止1 .1 .1 模样成型不完整.轮廓不清晰产生原因:( 1 ) 珠粒量不足,未填满模具型腔或珠粒充填不均匀;( 2 ) 发泡的粒子粒度不合适,不均匀;( 3 ) 模具型腔的分布,结构不合理;( 4 ) 操作时进粒子不规范。
防止措施:( 1 ) 珠粒大小要与壁厚匹配。
薄壁模样,应该用小珠粒( 最好用E P MMA、S T MMA 粒子) ;( 2 ) 调整模具型腔内结构及通气孔的布置、大小、数量;( 3 ) 手工填粒时,适当震动或手工帮助填料;用压缩空气喷枪填料时,应适当提高压力和调整进料方向。
1 .1 .2 模样熔结不良.组合松散产生原因:( 1 ) 蒸汽的热量、温度不够。
熟化时间过长;( 2 ) 珠粒粒度太小,发泡或发泡剂含量太少;( 3 ) 珠粒充型不均匀或未填满模型。
防止措施:( 1 )控制预发泡粒子比重,控制熟化;( 2 ) 增加通气的温度、时间和压力;( 3 ) 改用粒度较小的珠粒。
1 .1 .3 模样外表正常.内部呈未曾熔结颗粒产生原因:( 1 ) 蒸汽压力不足,没能进入模型中心或冷气充斥型腔:( 2 ) 成型加热时间短.发泡剂含量太少;( 4 ) 粒子过期变质。
防止措施:( 1 ) 提高模具的预热温度,且使其整体均匀;( 2 ) 提高蒸汽的压力,延长成型时间;( 3 ) 控制粒子熟化时间及发泡剂的用量;( 4 )选用保质粒料。
1 .1 .4 模样熔融.软化产生原因:( 1 ) 成型温度过高,超过了粒子的工艺规范;( 2 )成型发泡时间太长;( 3 )模型通气孔太多,太大。
防止措施:( 1 ) 降低成型发泡温度、压力;( 2 ) 缩时间;( 3 ) 调整模具型腔通气孔大小、数量、分布;1 .5 模样增大。
消失模常见缺陷与对策

消失模常见缺陷与对策平台消失模常见缺陷与对策局部塌模:局部塌模特征:在内部或外部凹角处浇筑后出现包状突起物,突起物表面粘砂,这些看似沙包的突起物很难清理下来。
清理下来后发现有铁质断面与本体相连,同时在铸件外观上伴有涂料皮子渣孔。
产生原因:凹角处填砂不实,在负压的作用下形成空腔,铁水充型时,由于铁水压力,破坏了涂料层,流到空腔里。
预防方法:1. 改变埋箱角度,保证充型效果2. 使用树脂砂(潮模砂、糊精砂、干性油砂,)局部充填,保证干砂充填效果3. 必要时采用人工辅助填砂烫摸:缺陷特征:铸件局部透皮或局部壁厚变薄或变厚或表面有老鼠尾状条纹突起。
产生原因:1. 砂箱残砂没有扒开,过于集中,热砂子烫坏白膜。
2. 埋箱砂砂温过高,3. 摆模距离过近预防方法:1. 扒平沙箱内残留的热砂子,铺上埋箱砂,保持补填的埋箱砂有一定厚度2. 检测砂温,当埋箱砂温度大于75度时,应停止操作3. 控制摆模距离,防止在浇注第一件时,铁水的高温烫坏第二个白膜塌箱缺陷特征:浇注后铸件大面积塌陷产生原因:1、负压场分配不合理2、泄压过早3、浇注时间过慢4、负压没接上预防方法:1. 合理分配负压场,必要时使用蛇皮管及管路把负压引入黄模内腔2. 规定泄压时间,避免操作者提前泄压3. 浇注时满足工艺要求的时间4. 浇筑前使用手捅一下砂箱,如果发现密封薄膜下面砂子是软的,应立刻检查负压接口,处理好后,才能浇注。
粘砂:缺陷特征:铸件表面热区处,凹角处占有砂砾,抛丸后局部如同上了一层白霜。
清理困难。
如不能去除导致铸件报废产生原因:1、黄模涂层局部脱落2、浇注温度高3、涂层厚度不够4、骨料耐火度差预防方法:1、涂料的润湿性是涂料的一个重要指标,润湿性不好涂料起皮子2、挂涂工艺改进,要做到两点其一挂涂后滴流,涂料不流淌下滴时,应马上送进烘干房3、黄模转运工序要避免磕碰,磕碰后涂料与白膜分离4、架车应有防护装置,如捆绑空气棉条或保温海绵管5、补涂是发现涂层虚连,应去除后再补涂蚊咬缺陷特征:铸件上出现如同蚊子叮咬的包状凸起,多半出现在白膜挂涂时的水平方向产生原因:1. 涂料的润湿性较差,隔水性欠缺,挂涂后再滴流阶段本次挂涂的涂料把上一次的涂料浸湿,使上一次的涂层与白膜分离,在重力作用下局部下沉,形成包状空腔。
消失模工艺铸件气孔、渣孔缺陷,是怎么形成的?该如何防止?

消失模工艺铸件气孔、渣孔缺陷,是怎么形成的?该如何防止?本次疫情期间,罗通老师写了一篇关于铸件气孔、渣孔缺陷的文章,洲际铸造平台授权转载!许多消失模铸造厂在生产加工件时特别是碳钢不锈钢件,虽然抛丸后没有什么问题外观也比较理想,可是一加工就出现渣孔气孔,而产生的位置一般在产品的中上部及侧边和浇注系统的对面,夹渣是夹杂缺陷的铁液熔渣和模样残渣。
铸件上二者一般都呈黑色,大小不一,形状很不规则,有块状、片状、线条状等。
一般存在于铸件内部,多见于铸件上表面的皮下和拐角处。
那么泡沫模型气化分解生成大量的气体及残留物不能及时排出铸型,泡沫、涂料层填充干砂的干燥不良,在高温包围下,裂解出大量的氢气和氧气侵入铸件而形成气孔。
产生气孔渣孔的原因一般有以下几种:1,泡沫的水分干燥不透彻就去上涂料,涂料第一遍没干透就去上第二遍,在高温的液体浇注时产生的气孔,2,泡沫的密度过于太大使浇注时来不及气化而吐食泡沫产生的泡沫渣形成渣孔3,钢水脱氧不良、炉台、炉内、包内除渣不净,熔化铁水时,或多或少要产生熔渣,特别是炉料锈蚀严重或采用铁屑熔炼时,产生大量的金属熔渣。
在浇注时熔渣很容易随着铁水进入型腔,留在铸件内部,凝固后就形成黑色夹渣。
由于夹渣的密度比铁水小,一般要浮在铸件上面,铸件拐角处对熔渣有阻碍作用,熔渣上浮时易产生滞留,所以该部位也多见夹渣缺陷。
镇静时间过短,浇注过程中挡渣不力,浇注工艺不合理造成渣孔。
4,由于浇注系统设计不合理,大件小件混合搭配在一个砂型形成了纵横交错,钢水的充型速度大于泡沫气化退让及气体排出速度,造成充型前沿将气化残留物包夹在钢水中再次气化形成内壁烟黑色的分解气孔。
5,浇注温度低,充型前沿钢水不能使泡沫充分气化,未分解的残余物质来不及浮集到冒口而凝固在铸件中形成气孔。
5、内浇道开设位置不合理,充型时形成死角区,由于型腔内气体压力作用,使气化残留物积聚在死角处形成气孔,内浇道截面积过大,而且少使充型速度大于泡沫气化退让速度,吞食泡沫,在合金内部分解气化,而气体无法排出形成气孔。
消失模铸造工艺防止粘砂的措施

消失模铸造工艺防止粘砂的措施贾国芳1,李增民2,谭建波2摘要:粘砂是消失模铸件常见的铸造缺陷,造成粘砂的工艺因素多种多样。
防止铸件粘砂应从多方面着手,综合分析生产过程各工艺环节,抓住主要影响因素,理顺操作规范和工艺参数,有针对地采取防治措施才能收到良好效果。
本文结合消失模铸造铁套件产生粘砂部位和粘砂的形式,从多角度分析造成铸件粘砂的原因,提出防止措施和生产中的注意事项。
关键词:消失模铸造;铁套;防粘砂措施1 铁套的结构特点和易产生粘砂的形式铁套和钢背铜套装配后构成轴瓦,是车辆上重要的承载和传动部件。
铁套为回转体结构,有筒体和法兰组成,筒体上有储油凹槽和过油孔,其材质HT250,要求HB190~220。
铁套单重一般小于10kg,平均壁厚约25mm,最大轮廓尺寸不超过200mm,因而可以用“厚壁小件、结构紧凑”来形容铁套的结构特点。
采用消失模工艺铸造铁套,能够将油槽、油孔直接铸出,最大限度地减小加工余量,节省加工工时和成本。
为了提高铸造生产效率,充分利用砂箱容积,消失模工艺通常采用组树串铸方案以实现一箱多铸,但存在的突出问题是粘砂缺陷。
垂直串铸时粘砂部出现在下层铸件内浇口周围,往往是铁套法兰下面凹槽处、法兰与筒体拐角处及筒体内部。
粘砂层较厚,粘砂形式以机械粘砂为主,抛丸清理无法去处。
铁套粘砂情况如图所示。
2 造成粘砂的工艺因素分析粘砂是金属液渗入到涂层和型砂中形成的机械混合物,消失模工艺生产铁套造成粘砂的原因一般是多方面的:(1)涂层太薄不足以抵抗金属液的浸蚀和冲刷而形成机械粘砂;(2)涂层耐火度不够,涂料被高温金属液熔合而形成化学粘砂;(3)造型时型砂的紧实度不足,填充不满,金属液冲破涂层而机械粘砂;(4)内浇口引入位置太集中,容易造成局部过热而粘砂;(5)涂层干燥不透强度低、发气量大,被金属液冲蚀而粘砂;(6)浇注温度太高,浇注速度慢,铁水对局部(内角口周围)冲刷过热时间长;(7)原材料锈蚀和杂质多、铁水高温熔化时间长等原因,造成铁水氧化严重,容易和涂层和型砂反应,形成低熔点化合物,降低了涂料的耐火度而造成粘砂。
消失模铸造制动盘夹杂缺陷的防止
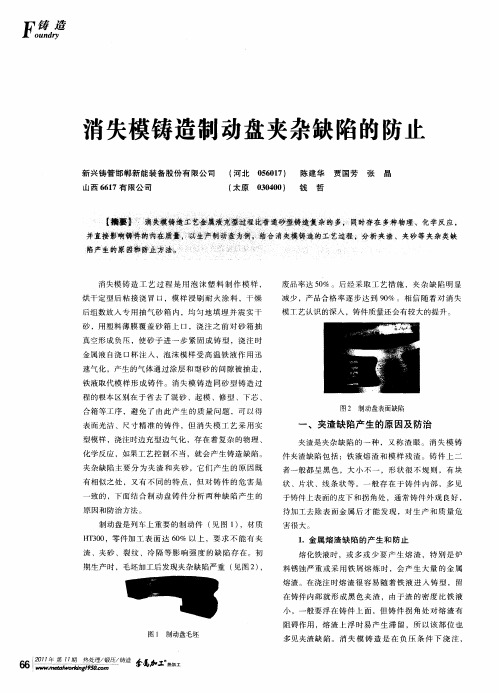
废 品率达 5 % 。后 经 采 取 工 艺措 施 ,夹 杂 缺 陷 明 显 0
2 模 样残渣缺陷的产生和防止 .
消 失模铸 造 在 浇 注 时 ,泡 沫 塑 料 模 样 与 高 温 铁
液发 生强 烈 的 物 理 化 学反 应 ,其 中 以泡 沫 模 样 剧 烈 的热 解气 化 为 主 ,产 生 的 气 体 被 真 空 泵 抽 走 。实 践
也证 明 ,任 何泡 沫塑 料热 解 反应 后 并 不能 全 部气 化 , 最终要 产 生 微量 的 固态 残 余 物 ,俗 称 残 渣 ,其 主 要
铁 液 温 度 提 高 ,有 利 于模
( ) 加强 扒 渣 和挡 渣 工 作 1
在 出 炉 前 ,铁 液 面
样 的充 分 气 化 分解 ,减少 残 渣 量 ,但 提 高 浇 注 温度 应 以防止铸 件粘砂 为前 提 。 ( )使 用 空心 浇 道 4 空 心 浇 道 有 利 于铁 液 的顺
观 区别在 于 :夹 砂 为 白色 颗粒 状 ,大 小 同 砂 粒 ,多 见于 铸件 浇 注位 置 的上 表 面皮 下 。 由于 夹砂 是 铁 液 流动 中冲破 型壁 带人 型砂 所 致 ,边 浇 注边 冲刷 带 人 , 因而铸 件 的其他 部位 往往 也 能 看到 夹 砂 。相 比之 下 ,
减少 ,产 品合 格率 逐 步 达 到 9 % 。相 信 随 着对 消 失 0 模T 艺认识 的深 入 ,铸件 质量 还会有 较大 的提 升 。
消失模铸造常见缺陷的分析与防止

消失模铸造常见缺陷的分析与防止2010-07-23 18:35:56| 分类:默认分类| 标签:|字号大中小订阅1.铸铁件表面皱皮(积碳)铸件表面有厚薄不同的皱皮,有波纹状、滴瘤状、冷隔状、渣状或夹气夹杂状等。
波纹状较浅,其余皱皮则较厚、较深。
其表面常呈轻质发亮的碳薄片(光亮碳膜),深凹沟陷处充满烟黑、碳黑等。
皱皮的厚度为0.1一1.0mm,甚至超过10mm,导致铸件报废。
这种缺陷往往在铁液最后流到的部位或液流的“冷端”部位。
大件出现在上部;15-20mm现在侧面或铸件的死角部位,这与浇注系统(顶注、底注、侧注、阶梯注)有关。
当1350-1420℃的铁液注人型内时,EPS或STMMA料模急剧分解,在模样与铁液间成气隙,料模热解形成一次气相、液相和固液气相主要由CO,CO2,H2,CH4,和分子量较小的乙烯及其衍生物组成;液相由苯、甲苯、乙烯和璃态聚苯乙烯等液态烃基组成;固相主要是由聚苯乙烯热解形成的光亮碳和焦油状残留物组成,因固相中的光亮碳与气相、液相形成熔胶粘着液相也会以一定速度分解形成二次气相和固液态中的二聚物、三聚物及存在再聚合物,这当中往往会出现一种粘稠的沥青状液体,这种液分解物残留在涂层内侧,一部分被涂层吸收分在铸件与涂层之间形成薄膜,这层薄膜在还原(CO)气氛下形成了细片状或皮屑状、波纹状的结晶残碳即光亮碳,此种密度较低(疏松)的光碳与铁液的润湿性很差,因此在此铸件表面形成碳沉积(皱皮)。
A.影响因素(1)泡塑模样:模料EPS比EPMMA,STMMA更容易形成皱皮,因为EPS含碳量比后二者高,其中EPS 含碳92% , STMMA(苯乙烯—甲基丙烯酸甲脂共聚树脂)含碳69.6% , EPMMA(可发性聚甲基丙烯酸甲脂)含碳60.0%;此外,模样密度越高体积越大,分解后液相产物越多,越容易产生皱皮。
(2)铸件材料成分的影响:含碳低的铸铁件(合金铸铁),模型分解产物中的碳可以部份溶解其中,不易产生皱皮;含碳高的铸铁(球铁)最易形成皱皮缺陷。
消失模铸件易出现的缺陷及消除措施
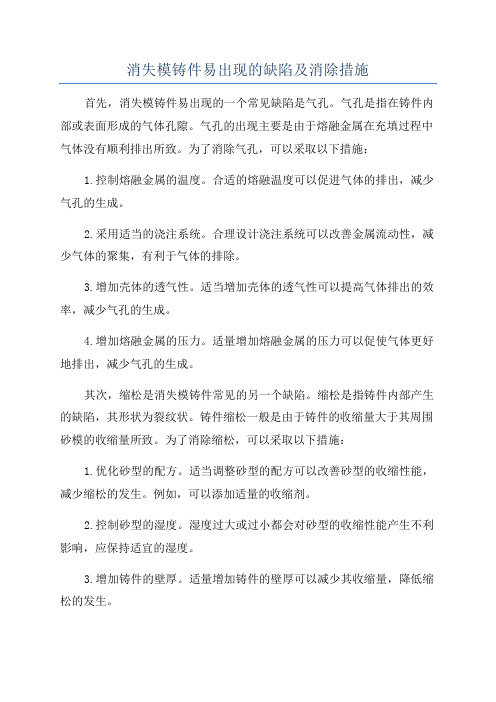
消失模铸件易出现的缺陷及消除措施首先,消失模铸件易出现的一个常见缺陷是气孔。
气孔是指在铸件内部或表面形成的气体孔隙。
气孔的出现主要是由于熔融金属在充填过程中气体没有顺利排出所致。
为了消除气孔,可以采取以下措施:1.控制熔融金属的温度。
合适的熔融温度可以促进气体的排出,减少气孔的生成。
2.采用适当的浇注系统。
合理设计浇注系统可以改善金属流动性,减少气体的聚集,有利于气体的排除。
3.增加壳体的透气性。
适当增加壳体的透气性可以提高气体排出的效率,减少气孔的生成。
4.增加熔融金属的压力。
适量增加熔融金属的压力可以促使气体更好地排出,减少气孔的生成。
其次,缩松是消失模铸件常见的另一个缺陷。
缩松是指铸件内部产生的缺陷,其形状为裂纹状。
铸件缩松一般是由于铸件的收缩量大于其周围砂模的收缩量所致。
为了消除缩松,可以采取以下措施:1.优化砂型的配方。
适当调整砂型的配方可以改善砂型的收缩性能,减少缩松的发生。
例如,可以添加适量的收缩剂。
2.控制砂型的湿度。
湿度过大或过小都会对砂型的收缩性能产生不利影响,应保持适宜的湿度。
3.增加铸件的壁厚。
适量增加铸件的壁厚可以减少其收缩量,降低缩松的发生。
4.增加充填缓慢度。
适当降低熔融金属的充填速度可以减少金属流动过快造成的收缩不均,减少缩松的发生。
此外,消失模铸件还可能出现其他缺陷,如未充填、冷隔离、裂纹等。
为了消除这些缺陷,可以采取以下措施:1.控制熔融金属的温度。
适当降低熔融金属的温度可以减少未充填和冷隔离的发生。
2.增加砂型的强度。
优化砂型的配方、增加砂型的固化时间和温度,以及采用合适的固化剂等措施可以提高砂型的强度,减少裂纹的发生。
3.控制熔融金属的充填速度。
适当降低金属的充填速度可以减少未充填和冷隔离的发生。
4.增加浇注口的大小。
适当增加浇注口的大小可以改善金属的流动性,减少未充填和冷隔离的发生。
综上所述,消失模铸件易出现的缺陷包括气孔、缩松、未充填、冷隔离等。
针对这些缺陷,可以采取相应的措施来消除,如控制熔融金属的温度和压力、优化砂型的配方和固化条件、增加浇注口的大小等。
消失模铸造薄壁复杂箱体类铸件变形及夹渣缺陷的防止措施

消失模薄壁复杂箱体类铸件变形及夹渣缺陷的解决措施一、铸件结构工艺性设计,发泡模具设计箱体类铸件塑料模样在加工制作、挂涂料、搬运、造型、振实、抽真空过程中,容易变形,因此要求铸件结构应尽可能紧凑、刚性好。
在进行工艺结构设计的时候,除考虑传统性铸造结构要求外,最重要一点就是重点考虑消失模铸造工艺的特殊性,在不影响使用的前提下,适当增加涂料、造型埋箱过程中受力部位壁厚、工艺补贴及设计反变形量,有利于防止工艺过程中的因变形而影响铸件尺寸。
同时铸件结构设计还应考虑成型发泡的泡塑珠粒可填料性及造型振实过程的干砂可填充性,防止因进料不足影响强度以及因填砂不均匀而造成变形。
ZL50变矩器壳体(见图三、四)结构工艺性设计时由于D面法兰、E面窗口、C处圆法兰,造型埋箱时以经常容易变形,所以结构设计作如下调整:D处法兰外型尺寸增加1mm,内型尺寸缩小1mm,使法兰由25mm增加为27mm;E处窗口及附处增加壁厚1mm;C处圆弧加工余量较其它处余量大1mm。
图一 图二ZL50E 箱体原发泡模具设计方案(部分) ZL50E 箱体现发泡模具设计方案(部分)发泡模具工艺设计的好与坏,直接影响产品质量。
分块越多,成型发泡相对容易,白模比重也可控制较轻,这就有利于减少铸件的夹渣等缺陷,但尺寸精度相对难控制;分块越少,尺寸相对较好控制,成型发泡就相对较难,白模比重势必也较高,这就容易造成铸件的夹渣等缺陷。
因此,优化发泡模具设计是整个工艺的关键环节之一。
我们刚试制ZL50E 箱体时,整套模具设计成18块,组合较复杂,经常因尺寸偏差造成铸件报废,见图一,外形由四大块组成。
所以,我们后来将整套模具设计成8块,见图二,外形减少为三大块,取消了部分组合工装,生产效率提高了,表面质量因也少一道分模面而提高了,更重要的是尺寸能很好控制,曾经几个月生产无一件ZL50E箱体铸件因尺寸原因而报废。
为了保证ZL50变矩器壳体铸件尺寸,发泡模具设计成两大块,见图三A、B两部分,两块模样采用圆形止口定位,分块少,组合效率高,尺寸能得到有效保证。
- 1、下载文档前请自行甄别文档内容的完整性,平台不提供额外的编辑、内容补充、找答案等附加服务。
- 2、"仅部分预览"的文档,不可在线预览部分如存在完整性等问题,可反馈申请退款(可完整预览的文档不适用该条件!)。
- 3、如文档侵犯您的权益,请联系客服反馈,我们会尽快为您处理(人工客服工作时间:9:00-18:30)。
3)在铸件的最高处或死角处设置集渣冒口;
4)制作模样时,加大模型顶部的加工余量,用金属切削的方法消除气和夹。
1)模样气化后生成大量气体和一定残渣,这是气孔和夹渣主要来源;
2)此外,浇注系统或内浇道结构不合理,容易使气体和残渣裹在铁水中,形成气孔和夹渣;
3)另外,浇注温度低,不能使气体和残渣充分排出也易产生气孔和夹渣。
解决措施
1)采用底注式浇注系统,提高浇注温度;
2)合理填砂造型,控制模样浇注时的发气量,提高涂层透气性,提高真空系统抽气能力,使气体及时排出;
解决措施
1)合理控制真空度和浇注温度,在保证浇注顺利进行的前提下,尽量降低真空度和浇注温度,以抑制高温金属液的穿透能力
2)应该分批加砂,改善振实设备,适当增加涂层厚度,提高涂层耐火度等。
2、气孔和夹渣
气孔和夹渣存在于铸件上部或死角处的表皮下,只有经过机械加工后才能看到。
产生原因
消失模铸造(简称EPC)是一种常见的铸造方式,但与普通砂型铸造相比,还有一些技术不成熟,易出现粘砂、气孔、夹渣缺陷。
粘砂
产生原因
1)浇注温度过高,实践证明适当的提高浇注温度有利于改善铸件表面质量,对于浇不足和表面皱皮也大有改善,但浇注温度太高会出现粘砂;
2)此外型砂充填紧实度不够,比如振实设备不理想、涂料透气性太高或涂层太薄等。