加工中心积屑瘤与鳞刺
机械加工表面粗糙度的影响因素
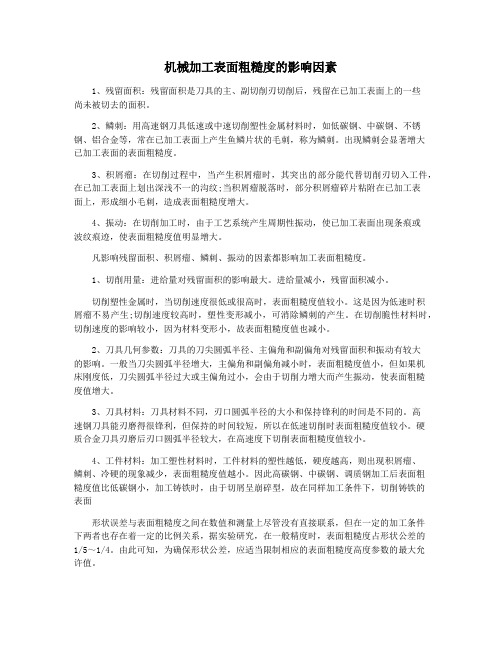
机械加工表面粗糙度的影响因素1、残留面积:残留面积是刀具的主、副切削刃切削后,残留在已加工表面上的一些尚未被切去的面积。
2、鳞刺:用高速钢刀具低速或中速切削塑性金属材料时,如低碳钢、中碳钢、不锈钢、铝合金等,常在已加工表面上产生鱼鳞片状的毛刺,称为鳞刺。
出现鳞刺会显著增大已加工表面的表面粗糙度。
3、积屑瘤:在切削过程中,当产生积屑瘤时,其突出的部分能代替切削刃切入工件,在已加工表面上划出深浅不一的沟纹;当积屑瘤脱落时,部分积屑瘤碎片粘附在已加工表面上,形成细小毛刺,造成表面粗糙度增大。
4、振动:在切削加工时,由于工艺系统产生周期性振动,使已加工表面出现条痕或波纹痕迹,使表面粗糙度值明显增大。
凡影响残留面积、积屑瘤、鳞刺、振动的因素都影响加工表面粗糙度。
1、切削用量:进给量对残留面积的影响最大。
进给量减小,残留面积减小。
切削塑性金属时,当切削速度很低或很高时,表面粗糙度值较小。
这是因为低速时积屑瘤不易产生;切削速度较高时,塑性变形减小,可消除鳞刺的产生。
在切削脆性材料时,切削速度的影响较小,因为材料变形小,故表面粗糙度值也减小。
2、刀具几何参数:刀具的刀尖圆弧半径、主偏角和副偏角对残留面积和振动有较大的影响。
一般当刀尖圆弧半径增大,主偏角和副偏角减小时,表面粗糙度值小,但如果机床刚度低,刀尖圆弧半径过大或主偏角过小,会由于切削力增大而产生振动,使表面粗糙度值增大。
3、刀具材料:刀具材料不同,刃口圆弧半径的大小和保持锋利的时间是不同的。
高速钢刀具能刃磨得很锋利,但保持的时间较短,所以在低速切削时表面粗糙度值较小。
硬质合金刀具刃磨后刃口圆弧半径较大,在高速度下切削表面粗糙度值较小。
4、工件材料:加工塑性材料时,工件材料的塑性越低,硬度越高,则出现积屑瘤、鳞刺、冷硬的现象减少,表面粗糙度值越小。
因此高碳钢、中碳钢、调质钢加工后表面粗糙度值比低碳钢小,加工铸铁时,由于切屑呈崩碎型,故在同样加工条件下,切削铸铁的表面形状误差与表面粗糙度之间在数值和测量上尽管没有直接联系,但在一定的加工条件下两者也存在着一定的比例关系,据实验研究,在一般精度时,表面粗糙度占形状公差的1/5~1/4。
浅析金属切削加工中鳞刺的形成原因及抑制措施

深入的研究, 并将鳞刺的形成过程划分为抹拭、 导裂、 层积和切项四个阶段, 示意图如图 2所示。尤其是在 切屑形状为节状或粒状的切削加工中这个四个阶段 最为典型。
图2 鳞刺形成的四个阶段示意图
抹拭阶段是鳞刺形成的第一阶段, 也就是前一鳞 刺已经形成, 新的鳞刺尚未出现的这一时间段。由于 切屑沿前刀面流出时在厚度方向上的流速不同, 贴近 前刀面的切屑流速等于零而成为“ 滞流层” , 在压力、 温度合适的条件下会形成粘屑现象; 导裂阶段是鳞刺
A n a l y s i s o nC a u s e s a n dS u p p r e s s i o nMe a s u r e s t oB u r ri nMe t a l C u t t i n gP r o c e s s L I J u n - t a o
( S h a a n x i D e f e n c e V o c a t i o n a l a n dT e c h n i c a l C o l l e g e ,X i ′ a nS h a a n x i 7 1 0 3 0 0 ,C h i n a ) A b s t r a c t :I nt h em e t a l c u t t i n gp r o c e s s ,s c a l yb u r r o f t h em a c h i n e ds u r f a c ew i l l h a v es e r i o u s i m p a c t o nt h es u r f a c eq u a l i t yo f w o r kp i e c e .B a s e do nt h ef o r m i n gp r o c e s s a n dm e c h a n i s mo f t h eb u r r ,t h ef a c t o r s t h a t w o u l di m p a c t i t s f o r m a t i o na n dg r o w t h a r ea n a l y z e di nt h i s p a p e r ,t h u s t h es u p p r e s s i o nm e a s u r e s t ot h ef o r m a t i o no f s c a l yb u r r a r ei d e n t i f i e d . K e yw o r d s :b u r r ;s u r f a c eq u a l i t y ;s u p p r e s s i o nm e a s u r e
积屑瘤形成过程、影响及预防措施

浅谈积屑瘤的形成过程、影响及预防措施摘要:在生产实习过程中,积屑瘤是一种很常见的现象。
积屑瘤的产生需要一定的条件。
产生积屑瘤对加工过程有积极的影响和消极的影响。
在生产时间过程中一般采取一定措施进行预防。
本文对上述问题进行了浅析。
关键字:积屑瘤;形成过程;影响;预防措施在切削钢、铝合金及铜或其他塑性材料是,当切削速度不太高而又能形成连续切削的情况下,常常在前刀面靠近刀尖处粘结着一块或几块“焊锡”一样的剖面有时呈三角状的金属,而且在刀具上粘结的非常牢固。
改小块金属比工件硬度高,在比较稳定的情况下,可代替刀刃进行切削。
这小金属块称为积屑瘤。
当积屑瘤不稳定时,在切削过程产生振动。
而且对加工质量、刀具耐用度、切削力、切削温度以及切屑的卷曲与折断都有着不同程度的影响。
由此可见,对积屑瘤进行一定的研究以及对积屑瘤有正确的认识对于学习和知道生产有着巨大的现实意义。
下面本文对与积屑瘤相关的问题进行简要浅析。
一、积屑瘤的形成过程在切削塑形金属的过程中,由于塑性变形,切屑与前刀面之间的压力很大,切屑沿前刀面流出,对前刀面形成强烈的挤压摩擦,再加上很高的温度,使前刀面上的氧化膜和润滑膜被破坏,前刀面变得很干净。
切屑上露出的崭新的金属原子与刀具原子接触紧密。
随着切削的进行,温度进一步升高,当达到合适温度,压力有较高时,产生“冷焊”现象。
此时,切屑与前刀面之间的摩擦就不是一般的摩擦,而是切屑和刀具的粘结层与其上的金属的“内摩擦”。
底层金属由于摩擦变形,发生加工硬化,被阻滞在底层,从而使粘结程度变大。
此时的加工硬化也正是积屑瘤硬度高于工件材料的主要原因。
随着切削逐渐进行,粘结层不断长大,知道温度和压力不足以继续粘结为为止。
从而形成了典型的积屑瘤。
然而,在切削过程中,积屑瘤是否稳定存在呢?不同的学者有不同的看法,有的学者认为积屑瘤是完全高频生灭的,频率可达每秒几十次,几百次,甚至上千次。
有的学者认为是头部高频生灭,即积屑瘤根部相对稳定,但头部高频生灭。
对影响机械加工表面质量因素讨论论文
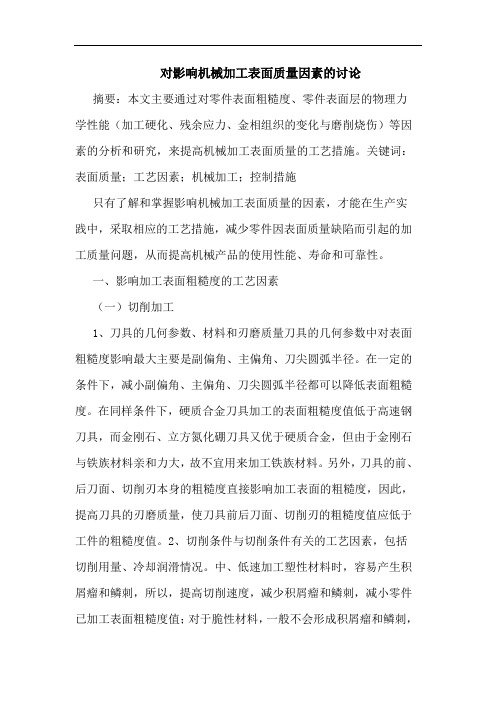
对影响机械加工表面质量因素的讨论摘要:本文主要通过对零件表面粗糙度、零件表面层的物理力学性能(加工硬化、残余应力、金相组织的变化与磨削烧伤)等因素的分析和研究,来提高机械加工表面质量的工艺措施。
关键词:表面质量;工艺因素;机械加工;控制措施只有了解和掌握影响机械加工表面质量的因素,才能在生产实践中,采取相应的工艺措施,减少零件因表面质量缺陷而引起的加工质量问题,从而提高机械产品的使用性能、寿命和可靠性。
一、影响加工表面粗糙度的工艺因素(一)切削加工1、刀具的几何参数、材料和刃磨质量刀具的几何参数中对表面粗糙度影响最大主要是副偏角、主偏角、刀尖圆弧半径。
在一定的条件下,减小副偏角、主偏角、刀尖圆弧半径都可以降低表面粗糙度。
在同样条件下,硬质合金刀具加工的表面粗糙度值低于高速钢刀具,而金刚石、立方氮化硼刀具又优于硬质合金,但由于金刚石与铁族材料亲和力大,故不宜用来加工铁族材料。
另外,刀具的前、后刀面、切削刃本身的粗糙度直接影响加工表面的粗糙度,因此,提高刀具的刃磨质量,使刀具前后刀面、切削刃的粗糙度值应低于工件的粗糙度值。
2、切削条件与切削条件有关的工艺因素,包括切削用量、冷却润滑情况。
中、低速加工塑性材料时,容易产生积屑瘤和鳞刺,所以,提高切削速度,减少积屑瘤和鳞刺,减小零件已加工表面粗糙度值;对于脆性材料,一般不会形成积屑瘤和鳞刺,所以,切削速度对表面粗糙度基本上无影响。
进给速度增大,塑性变形也增大,表面粗糙度值增大,所以,减小进给速度可以减小表面粗糙度值,但是,进给量减小到一定值时,粗糙度值不会明显下降。
正常切削条件下,切削深度对表面粗糙度影响不大,因此,机械加工时不能选用过小的切削深度。
合理选用切削液,对工件起到冷却、润滑作用,减少被加工材料的变形和摩擦,降低切削区温度,抑制积屑瘤和鳞刺的生成,是减少表面粗糙度值有效途径。
3、工艺系统的精度和刚度要想获得很小表面粗糙度,要求工艺系统具有足够的运动精度和刚度。
积屑瘤的影响

2.物理因素多数情况下是在已加工表面的残留面积上叠加着一些不规则的金属生成物、粘附物或刻痕。
形成它们的原因有积屑瘤、鳞刺、振动、摩擦、切削刃不平整、切屑划伤等。
3.积屑瘤的影响积屑瘤的生成、长大和脱落将严重影响工件表面粗糙度。
同时,由于部分积屑瘤碎屑嵌在工件表面上,在工件表面上形成硬质点。
见图11-11。
图11- 11 图11- 12鳞刺的影响鳞刺的出现,使已加工表面更为粗糙不平。
鳞刺的形成分为:抹拭阶段:前一鳞刺已经形成,新鳞刺还未出现;而切屑沿着前刀面流出,切屑以刚切离的新鲜表面抹拭刀——屑摩擦面,将摩擦面上有润滑作用的吸附膜逐渐拭净,以致摩擦系数逐渐增大,并使刀具和切屑实际接触面积增大,为这两相摩擦材料的冷焊创造条件,如图11-12(a)。
导裂阶段:由于在第一阶段里,切屑将前刀面上的摩擦面抹拭干净,而前刀面与切屑之间又有巨大的压力作用着,于是切屑与刀具就发生冷焊现象,切屑便停留在前刀面上,暂时不再沿前刀面流出。
这时切屑代替前刀面进行挤压,刀具只起支撑切削的作用。
其特点是在切削刃前下方,切屑与加工表面之间出现一裂口。
如图11-12(b)。
层积阶段:由于切削运动的连续性,切屑一旦停留在前刀面上,便代替刀具继续挤压切削层,使切削层中受到挤压的金属转变为切屑。
而这部分新成为切屑的金属,只好逐层的积聚在起挤压作用的那部分切屑的下方。
;这些金属一旦积聚并转化为切屑,便立即参与挤压切削层的工作;同时,随着层积过程的发展,切削厚度将逐渐增大,切削力也随之增大,如图11-12(c)。
刮成阶段:由于切削厚度逐渐增大,切削抗力也随之增大,推动切屑沿前刀面流出的分力Fy也增大。
当层积金属达到一定厚度后,Fy力便也随之增大到能够推动切屑重新流出的程度,于是切屑又重新开始沿前刀面流出,同时对切削刃便刮出鳞刺的顶部,如图11-12(d)。
至此,一个鳞刺的形成过程便告结束。
紧接着,又开始另一个新鳞刺的形成过程。
如此周而复始,在工件加工表面上便不断地生成一系列鳞刺。
切削加工中易出现问题的分析
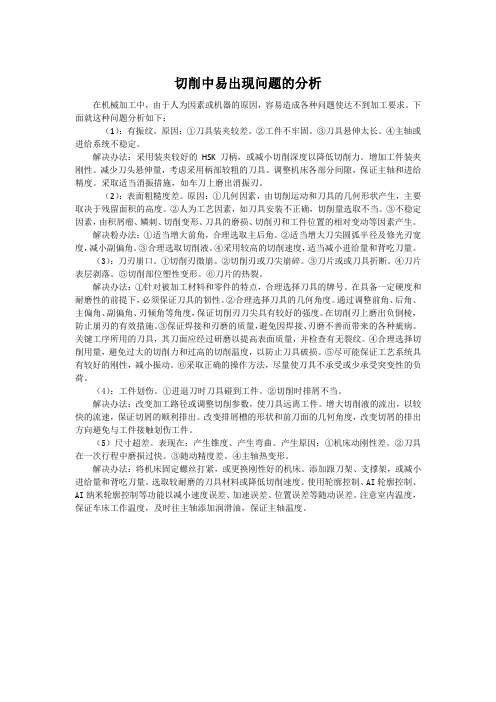
切削中易出现问题的分析在机械加工中,由于人为因素或机器的原因,容易造成各种问题使达不到加工要求。
下面就这种问题分析如下:(1):有振纹。
原因:①刀具装夹较差。
②工件不牢固。
③刀具悬伸太长。
④主轴或进给系统不稳定。
解决办法:采用装夹较好的HSK刀柄,或减小切削深度以降低切削力。
增加工件装夹刚性。
减少刀头悬伸量,考虑采用柄部较粗的刀具。
调整机床各部分间隙,保证主轴和进给精度。
采取适当消振措施,如车刀上磨出消振刃。
(2):表面粗糙度差。
原因:①几何因素,由切削运动和刀具的几何形状产生,主要取决于残留面积的高度。
②人为工艺因素,如刀具安装不正确,切削量选取不当。
③不稳定因素,由积屑瘤、鳞刺、切削变形、刀具的磨损、切削刃和工件位置的相对变动等因素产生。
解决粉办法:①适当增大前角,合理选取主后角。
②适当增大刀尖圆弧半径及修光刃宽度,减小副偏角。
③合理选取切削液。
④采用较高的切削速度,适当减小进给量和背吃刀量。
(3):刀刃崩口。
①切削刃微崩。
②切削刃或刀尖崩碎。
③刀片或或刀具折断。
④刀片表层剥落。
⑤切削部位塑性变形。
⑥刀片的热裂。
解决办法:①针对被加工材料和零件的特点,合理选择刀具的牌号。
在具备一定硬度和耐磨性的前提下,必须保证刀具的韧性。
②合理选择刀具的几何角度。
通过调整前角、后角、主偏角、副偏角、刃倾角等角度,保证切削刃刀尖具有较好的强度。
在切削刃上磨出负倒棱,防止崩刃的有效措施。
③保证焊接和刃磨的质量,避免因焊接、刃磨不善而带来的各种疵病。
关键工序所用的刀具,其刀面应经过研磨以提高表面质量,并检查有无裂纹。
④合理选择切削用量,避免过大的切削力和过高的切削温度,以防止刀具破损。
⑤尽可能保证工艺系统具有较好的刚性,减小振动。
⑥采取正确的操作方法,尽量使刀具不承受或少承受突变性的负荷。
(4):工件划伤。
①进退刀时刀具碰到工件。
②切削时排屑不当。
解决办法:改变加工路径或调整切削参数,使刀具远离工件。
增大切削液的流出,以较快的流速,保证切屑的顺利排出。
工件表面粗糙度的问题解析

关键词 : 加工 ; 工件 ; 表面粗糙度
中 图 分类 号 : H1 1 T 6 文献标识码 : B 文 章编 号 : 6 2 5 5 2 1 ) 1 0 3 - 2 1 7 — 4 X( 0 0 1 — 1 3 0
在机械加工过程 中, 由于切削分离 时的塑性变形 、 艺系 工
中 ,都可能出现鳞刺 。鳞刺 的晶粒和基体材料 的晶粒 相互 交 错, 鳞刺与基体材料 之间没有 分界线 。鳞刺 的出现 , 已加 工 使 表面的粗糙程 度增加 ; 因此 , 它是 塑性金属切削加工 中获得 良
毛 刺 ; 同时 积 屑 瘤 顶 部 的 不 稳 定 又 使 切 削 力 波 动 而有 可 能 引
由上 述分析 可知 , 要减小 表 面粗糙 , 必须 减小残 留面积 、
消 除 积 屑 瘤 和 鳞 刺 ,减 小 工 件 材 料 的 塑 性 变 形 及 切 削 过 程 中
的振 动等 。
在切 削加 工中 ,若发现工件表 面粗糙度值达不 到图样要
度增 大 。
() 2 积屑瘤 。当切削塑性金属时 , 常在靠近切削刃及刀尖 的前刀 面上 , 产生积屑瘤 , 积屑瘤 的硬度很高 , 在相对稳定 时 , 可 以代替切 削刃进行切削 。由于积 屑瘤会伸 出切削刃及刀尖
之 外 , 而 产 生 一 定 的 过 切 量 o , 以 积 屑 瘤 的形 状 不 规 则 , 从 。加
加工中心积屑瘤与鳞刺

加工中心积屑瘤与鳞刺(一)积屑瘤1.积屑瘤的形成切削塑性金属时,往往会在刀具切削刃口附近粘结着一块剖面呈三角状或鼻状的金属块,它包围着切削刃且覆盖部分前刀面,这种堆积物叫做积屑瘤。
2.积屑瘤对加工的影响(1)保护刀具。
积加工中心屑瘤包围着切削刃,同时覆盖着一部分前刀面,由于积屑瘤是材料剧烈变形强化后的产物,其硬度高达金属母体的2~3倍,故能代替切削刃和前刀面进行切削,所以切削刃和前刀面都得到了积屑瘤的保护,沈阳机床一厂减少了刀具的磨损。
(2)增大实际前角。
有积屑瘤的车刀,实际前角丁,可增大至30‘—35‘,因而减少了切屑的变形,降低了切削力。
(3)影响工件表面质量和尺寸精度。
由于积屑瘤总是极不稳定的,时生时灭,时大时小,在切削过程中,一部分积屑瘤被切屑带走,一部分嵌入工件已加工表面,使工件表面形成硬点和毛刺,表面粗糙度值变大。
因而有一层厚度为AH的金属层留下来,并被O点以下的刃口圆弧面挤压变形后成为已加工表面。
AH减薄到Ah。
.减薄的原因是因为刀具挤压变形后,金属塑性变形部分不能恢复,恢复的只是弹性变形部分(即AH—Ah)。
加工中心塑性变形愈大,表面变形硬化愈严重。
硬化层的硬度可达工件硬度的1.2~2倍,硬化层深度可达0.07—0.5mm。
切削加工造成的已加工表面硬化层常常伴随有表面裂纹,使表面粗糙度值增大,疲劳强度下降。
当以较小的切削深度再次切削时,则刀具不易切人,并且使刀具容易磨损,沈阳机床一厂因此应设法减轻这种现象。
切削过程中变形和摩擦所消耗功的绝大部分转变为热能。
切削热来源于三个变形区。
在第1变形区内被切材料发生弹性变形和塑性变形而产生的热量,分别用Ql和Q2表示;在第Ⅱ变形区有刀具前刀面与切屑摩擦而产生的热量,用Q,表示;在第Ⅲ变形区内有刀具后刀面与工件摩擦而产生的热量,用Q:表示。
切削时所产生的热量由切屑、工件、刀具及周围介质传出,加工中心分别用Q,、Q,、口,和Q8表示。
上述切削热的产生和传散的平衡关系式为Q二Q1+Q2+Q3+Qx二Q5+Q6+Q7+Qx例如不用切削液,以中等切削速度切削钢件时,切削热由各部分传出的比例:0,为50%-80%,Q,为10%—40%,Q,为3%—9%,Q。
机械制造技术基础(第2版)习题答案
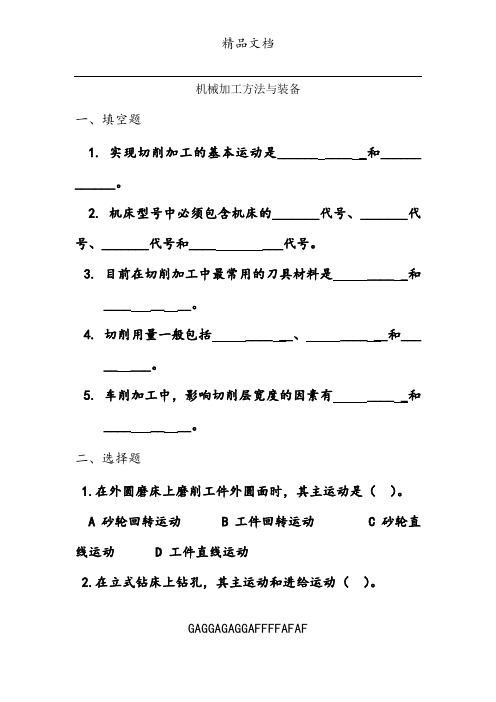
机械加工方法与装备一、填空题1. 实现切削加工的基本运动是______ ____ _和______ ______。
2. 机床型号中必须包含机床的_______代号、_______代号、_______代号和____ ___代号。
3. 目前在切削加工中最常用的刀具材料是 ____ _和____ __ __。
4. 切削用量一般包括 ____ __、 ____ __和_____ ___。
5. 车削加工中,影响切削层宽度的因素有 ____ _和____ __ __。
二、选择题1.在外圆磨床上磨削工件外圆面时,其主运动是()。
A砂轮回转运动 B工件回转运动 C砂轮直线运动 D 工件直线运动2.在立式钻床上钻孔,其主运动和进给运动()。
GAGGAGAGGAFFFFAFAFA均由工件来完成 B均由刀具来完成 C分别由工件和刀具来完成 D 分别由刀具和工件来完成3. 背吃刀量是指主切削刃与工件切削表面的接触长度()。
A 在切削平面的法线方向上测量的值 B在正交平面的法线方向上测量的值C在基面上的投影值 D在主运动和进给运动方向所组成平面的法线方向上测量的值4.普通车床的主参数是()。
A 车床最大轮廓尺寸B 主轴与尾座之间最大距离C 主轴中心高D 床身上工件最大回转直径5. 确定刀具标注角度的参考系选用的三个主要基准平面是()。
A 切削平面、已加工平面和待加工平面B 前刀面、主后刀面和副后刀面C 基面、切削平面和正交平面(主剖面)D 基面、进给GAGGAGAGGAFFFFAFAF平面和法平面6. 通过切削刃上选定点,垂直于主运动方向的平面称为()。
A 切削平面B 进给平面C 基面 D主剖面7. 刃倾角是在切削平面内测量的主切削刃与()之间的夹角。
A 切削平面 B基面C 主运动方向 D进给方向8. 刀具在基面内测量的角度有()。
A 前角和后角B 主偏角和副偏角C 刃倾角D 副后角9. 在正交平面内测量的角度有()。
A 前角和后角B 主偏角和副偏角C 副后角D 刃倾角10. 车外圆时若刀尖低于工件轴线,其工作角度与标注角GAGGAGAGGAFFFFAFAF度相比将会()。
机械制造工程单选题

一、单项选择题1、刃倾角是主切削刃与()之间的夹角。
(分数:1分)A。
切削平面B. 基面C. 主运动方向D. 进给方向标准答案是:B。
您的答案是:B2、关于刀具材料的选用,下列说法正确的是( )。
(分数:1分)A. 高速钢的热硬性好,适合制造用于高速切削的刀具B. YG类硬质合金比YT类硬质合金韧性好C. YG类硬质合金比YT类硬质合金硬度高D. 高速钢的导热系数比硬质合金小标准答案是:B。
您的答案是:B 3、安装外车槽刀时,刀尖低于工件回转中心时,与其标注角度相比。
其工作角度将会()。
(分数:1分)A。
前角不变,后角减小B。
前角变大,后角变小C。
前角变小,后角变大D。
前、后角均不变标准答案是:C。
您的答案是:C 4、进给运动通常是机床中( ).(分数:1分)A。
切削运动中消耗功率最多的B。
切削运动中速度最高的运动C. 不断地把切削层投入切削的运动D。
使工件或刀具进入正确加工位置的运动标准答案是:C。
您的答案是:C5、通过切削刃选定点,垂直于主运动方向的平面称为()。
(分数:1分)A. 切削平面B。
进给平面C. 基面D。
主剖面标准答案是:C。
您的答案是:C 6、硬质合金刀片是采用()方法生产出来的。
(分数:1分)A。
粉末冶金B。
钎焊C。
模锻D。
铸造标准答案是:A。
您的答案是:A 7、碳钢精车时宜用牌号为()的硬质合金作为刀具材料.(分数:1分)A。
YT5C。
vc→f→apD. ap→f →vc标准答案是:B。
您的答案是:B 3、刃倾角的功用之一是控制切屑流向,若刃倾角为负,则切屑流向为( ).(分数:1分)A。
流向已加工表面B。
流向待加工表面C. 沿切削刃的法线方向流出D。
流向后刀面标准答案是:A.您的答案是:A4、在切削塑性材料时,切削区温度最高点是在().(分数:1分)A. 刀尖处B。
前刀面上靠近刀刃处C。
后刀面上靠近刀尖处D。
主刀刃处标准答案是:B。
您的答案是:B 5、在车削细长轴时,为了减小工件的变形和振动,故采用较大()的车刀进行切削,以减小径向切削分力。
切削加工的积屑瘤解决方法

在进行切削加工的过程中,经常会发现刀尖附近有一个小块的金属,这种金属让操作人员十分苦恼,因为它对之后的加工精度有很大的影响。
所以,对于进行切削加工的大家来说,避免积屑瘤的出现是十分重要的。
积屑瘤的产生原因:它的形成主要是在切削开始不久,刀屑冷焊的条件也越来越成熟,切屑底层便容易和刀具的前面发生冷焊。
切屑底层金属因为与刀具前面冷焊而停留在刀具前面上,,但是由于切屑不断流出,在后面切屑的推动下,前面切屑的底层与上层发生了滑移进而分离,这就是积屑瘤成形的基础。
这样一来,逐层在上一层上进行集聚,最后就变成了我们所见到的积屑瘤了。
积屑瘤的都成,主要是来自于切屑,部分来自于工件。
由于有来自工件的材料,所以,积屑瘤才能伸出切削刃之外。
积屑瘤对于切削的影响:1、保护刀具。
积屑瘤保卫者切削刃,有时候还会覆盖着一部分刀具前面。
积屑瘤一旦形成,就会代替切削刃和前面进行切削。
切削刃和前面都可以得到积屑瘤的保护,在很大程度上减少了刀具的磨损。
2、增大前角。
积屑瘤具有30度左右的前角,这在一定程度上对于减少切屑变形,降低切削力有很大帮助。
3、增大背吃刀量。
积屑瘤的前段伸出切削刃之外,所以又积屑瘤时的背吃刀量增大,因而影响了工件的尺寸。
4、降低已加工表面粗糙度。
由于积屑瘤产生不稳定等因素;所以严重影响表面粗糙度。
如果有积屑瘤形成,已加工表面的粗糙度会大大增大,通常会增加二到三级。
因此,一般按照加工的种类和要求来进行积屑瘤的利弊判断,例如粗加工对于以加工表面的粗糙度要求不高,生成积屑瘤后切削力减小,从而降低了能量消耗,或者可加大切削用量,使切削率得到提高,积屑瘤还能保护刀具,减少磨损,提高刀具耐用度。
这样一来说明积屑瘤对于粗加工还是有很大帮助的。
而对于精加工来说则是相反的,精加工要求较小的粗糙度以及较高的尺寸精度,积屑瘤会增大已加工表面的粗糙度并降低尺寸精度。
所以这就说明积屑瘤对于精加工来说是不利的。
粗加工时,加工余量大,所用切削用量大,产生大量的切削热。
机床积屑瘤对切削加工的影响

机床积屑瘤对切削加工的影响
(1)增大实际切削前角黏附在刀具前面的积屑瘤,机床是比被切金属硬得多的硬化金属,能代替刀具进行切削,使实际
切屑前角增大到y。
机床从而减少了切削变形,降低了切削力。
(2)对刀具寿命的影响积屑瘤覆盖在刀具切削部位,参与切削,从而减少刀具的磨损,机床保护了刀具,不同程度地
提高了月具的使用寿命。
(3)影响工件的尺寸精度当积屑瘤增大到突出于切削刃之外时,改变了机床原来的背吃刀量,使切削厚度增大了,从
而影响了工件的尺寸精度。
(4)积屑瘤的不稳定性带来的影响积屑瘤是极不稳定的,在高温、振动或外力作用下,会发生局部的断裂或剥落,对
切削加工产生影响。
1)机床积屑瘤从产生到成长脱落的周期变化,使积屑瘤不能形成稳定的切削刃,刀具前角和背吃刀量总在变化,从而
引起切削状态不稳定,使总切削力忽大忽小,引起切削振动。
2)机床周期变化的积屑瘤使背吃刀量发生变化,会在已加工表面上划出纵向沟纹;机床脱落的积屑瘤,一部分被切屑
带走,一部分可能嵌入已加工表面,形成毛刺或硬点,使加工的表匝粗糙度值增大。
3)机床积屑瘤和刀具表面有很强的结合力,当频繁脱落时,会导致韧性较差的硬质合金刀具的颗粒随之脱落,影响刀
具的使用寿命。
浅谈积屑瘤的形成过程、影响及预防措施

浅谈积屑瘤的形成过程、影响及预防措施作者:李程辉来源:《商品与质量·消费视点》2013年第04期摘要:在生产实习过程中,积屑瘤是一种很常见的现象。
积屑瘤的产生需要一定的条件。
产生积屑瘤对加工过程有积极的影响和消极的影响。
在生产时间过程中一般采取一定措施进行预防。
本文对上述问题进行了浅析。
关键字:积屑瘤;形成过程;影响;预防措施在切削钢、铝合金及铜或其他塑性材料是,当切削速度不太高而又能形成连续切削的情况下,常常在前刀面靠近刀尖处粘结着一块或几块“焊锡”一样的剖面有时呈三角状的金属,而且在刀具上粘结的非常牢固。
改小块金属比工件硬度高,在比较稳定的情况下,可代替刀刃进行切削。
这小金属块称为积屑瘤。
当积屑瘤不稳定时,在切削过程产生振动。
而且对加工质量、刀具耐用度、切削力、切削温度以及切屑的卷曲与折断都有着不同程度的影响。
由此可见,对积屑瘤进行一定的研究以及对积屑瘤有正确的认识对于学习和知道生产有着巨大的现实意义。
下面本文对与积屑瘤相关的问题进行简要浅析。
一、积屑瘤的形成过程在切削塑形金属的过程中,由于塑性变形,切屑与前刀面之间的压力很大,切屑沿前刀面流出,对前刀面形成强烈的挤压摩擦,再加上很高的温度,使前刀面上的氧化膜和润滑膜被破坏,前刀面变得很干净。
切屑上露出的崭新的金属原子与刀具原子接触紧密。
随着切削的进行,温度进一步升高,当达到合适温度,压力有较高时,产生“冷焊”现象。
此时,切屑与前刀面之间的摩擦就不是一般的摩擦,而是切屑和刀具的粘结层与其上的金属的“内摩擦”。
底层金属由于摩擦变形,发生加工硬化,被阻滞在底层,从而使粘结程度变大。
此时的加工硬化也正是积屑瘤硬度高于工件材料的主要原因。
随着切削逐渐进行,粘结层不断长大,知道温度和压力不足以继续粘结为为止。
从而形成了典型的积屑瘤。
然而,在切削过程中,积屑瘤是否稳定存在呢?不同的学者有不同的看法,有的学者认为积屑瘤是完全高频生灭的,频率可达每秒几十次,几百次,甚至上千次。
拉削时容易出现的问题

拉削时容易出现的问题拉削加工具有生产率高、能稳定获得较高的尺寸加工精度和表面粗糙度,而拉削刀具两次重磨间的耐用度及总的使用寿命高,因此,在机械加工广泛采用。
但在拉削加工过程中,也会产生一些缺陷,如何分析这些缺陷,并在分析的基础上采取相应的措施,以确保拉削加工时获得较高的产品质量,本文就这方面的问题进行一些探讨。
由于拉刀设计不完善,制造质量不高,操作不正确,以及工件材料工艺准备不当等,都可能使拉削过程产生各种缺陷。
这些缺陷通常可以归纳为以下四个方面:(1)拉削表面粗糙度达不到要求:(2)被拉削工件尺寸、形状和位置发生偏差;(3)拉刀耐用度低;(4)拉刀的崩刃和断裂;为了尽可能避免上述缺陷的产生,以及在缺陷产生时能迅速找出原因并加以消除,现将各种缺陷产生的原因及消除方法介绍如下:一、拉削表面粗糙度达不到要求拉削时,拉削表面粗糙度的好坏,几乎与拉削过程中的所有因素都有关系。
一般说来,拉刀的齿升量及拉削速度越小。
同时工作齿数越多,刀齿前角选择适宜,刀齿表面粗糙越高,容屑槽形状越适当和粗糙度越高,工件材料的可加工性越好,拉床工作状态越好,拉削过程越平稳,拉削表面的粗糙度就越好。
另外,切削液和冷却方式对拉削表面质量也起着十分重要的作用。
但是,在实际操作中,由于拉削条件的不同,要完全合理地掌握各种因素,并不是一件容易的事。
因此,拉削表面粗糙度低,常常是生产中最突出的问题。
其中,最常见的缺陷主要有三种,既鳞刺、划痕和波纹,成为提高拉削表面粗糙度的最大障碍。
(一)拉削表面的鳞刺在被拉削工作的表面及键槽的侧面上,常常可以发现一些局部(靠工作拉出端)的鳞刺状毛刺,这就是所谓鳞刺或称为撕裂。
鳞刺出现时,往往会使拉削表面的粗糙度降低2—4级,因此,它对提高拉削表面粗糙度有严重的影响。
鳞刺形成的原因是:在拉削过程中,切屑由于摩擦力的变化而在刀齿前刀面上周期性停留,代替切削刃推挤被切削层,造成被切削层金属的聚集而使切削厚度向切削线以下增大,使已加工表面上产生应力而被挤裂;然后,切削刃擦过这部分金属继续切削,从而在已加工表面上留下鳞片朝向与拉刀运动方向相反的鳞刺。
积屑瘤的形成与切屑的类型

4.计算切削力的指数公式
式中 Fc、Fp、Ff——切削力,N; ap——吃刀深度; f——进给量;
vc——切削速度。
各系数CF值由实验时加工条件确定的,各指数xF,yF值表明
各参数对切削力影响程度,修正值KF是不同加工条件时对各 切削分力的修正数值。(在计算切削力时,考虑到各个参
数对切削力不同的影响,需对切削力数值进行相应的修正,
用功率表测出机床电机在切削过程中所消耗 的功率PE后,可算出切削功率Pc
在切削速度vc为已知的情况下,将Pc代入式
(即可求出主切削力Fc,这种方法只能粗略
估算切削力的大小,不够精确,所以通常采
用测力仪直接测量。
20
2.用测力仪测量切削力
电阻应变式测力仪 电阻应变式测力仪具有灵敏度高、线性度 好、量程范围大、使用可靠和测量精度较 高等优点,适用于切削力的动态和静态测 量。
45
作业: 3-2 3-3
46
3
(3) 积屑瘤具有一定的高度,其前端伸出切 削刃之外,如图 3.13 所示,使实际的切削 厚度增大。
4
(4) 在切削过程中积屑瘤是不断地生长和破 碎的,所以积屑瘤的高度也是在不断地变 化的,从而也导致了实际切削厚度地不断 变化,引起局部过切,使零件的表面粗糙 度增大。同时部分积屑瘤的碎片会嵌入已 加工表面,影响零件表面质量。 (5) 不稳定的积屑瘤不断地生长、破碎和脱 落,积屑瘤脱落时会剥离前刀面上的刀具 材料,造成刀具的磨损加剧。
(2)前刀面磨损会使刀具实际前角增大,切 削力减小。后刀面磨损,刀具与工件的摩
擦增大,切削力增大。前后刀面同时磨损 时,切削力先减小,后逐渐增大。Fp 增加 的速度最快,Fc 增加的速度最慢。
44
金属及加工表面粗糙度的影响因素

图1面粗糙度随前角的变化③切削液带来的影响。
在加工金属的过程中,选择合适的切削液,可以冷却金属的加工温度,润滑金属的加工,从而减少刀具与金属的摩擦,进而降低加工过程中带来的塑性形变,减少积屑瘤和鳞刺的发生,从而大幅度降低金属表面的粗糙度。
1.2磨削加工对于金属表面粗糙度的影响由于砂轮的运动滑擦、切划所造成的金属表面粗糙可以根据单位面积上的刻痕进行判断,刻痕越细腻均匀,属表面的粗糙程度就越低。
切削加工带来的影响,不仅是几何结构的原因,还有塑性形变等物理原因的影响。
金属加工表面的经常性挤压所带来的的塑性变形也会因为加工过程中的过高温度而大幅度提升金属表面的粗糙程度。
内燃机与配件因此,影响金属表面粗糙度的磨削加工原因主要有:①砂轮粒度、硬度带来的影响。
砂轮的粒度也会对金属表面粗糙程度造成影响。
金属表面的磨粒越多,粒度的程度越细致,金属表面加工留下的刻痕就会愈加致密,从而使得金属表面粗糙程度降低。
此外,砂轮的硬度也会对金属表面的粗糙度造成影响,砂轮的硬度适度,会在磨粒钝化使其自觉及时脱落,从而对新露出来的磨砺进行加工。
以上,就是金属具有的“自砺性”。
要注意砂轮不能使用过度,所以要注意在日常作业中进行及时、有效的检修,从而去掉已经被钝化的魔粒,这样做可以确保砂轮拥有正常的微刃性和等高性。
②工件材料带来的影响。
不同工件材料,他们在塑性、导热性、硬度和韧性上有很大区别,因此,工件材料的选择也会对金属表面的粗糙度造成影响。
比如,过硬会钝化磨粒,过软会堵塞砂轮;又比如,韧性大的会增加金属表面粗糙度,导热性能差的也是如此。
③磨削用量带来的影响。
砂轮提速,可以通过减少塑性形变而降低金属的表面粗糙度,这是因为,砂轮提速会导致磨削表面不能及时塑性变形。
若想要增加粗糙度,可以通过增加磨削深度和加工速度进行。
我们也可以通过使用更大的磨削深度去改进磨削效率,但要注意在降低表面粗糙时应该使用小的磨削深度进行。
④磨削液及其它原因带来的影响。
鳞刺对表面质量的影响及抑制措施

鳞刺对表面质量的影响及抑制措施1 鳞剌现象金属材料在切削过程中,往往在零件表面上出现不同程度的鳞刺现象,而且因材料不同、切削用量不同、刀具刃几何角度不同,表现出来的鳞刺高低程度也不同。
有资料表明,在较低的切削速度下,用高速钢、硬质合金或陶瓷刀具,切削一些常用的塑性金属材料时,在车、刨、插、钻、拉、滚齿、车螺纹、铰螺纹、板牙等加工工序中,都可能出现鳞刺。
鳞刺对零件表面质量有严重影响,使零件表面层产生残余应力,进而使零件表面容易产生微裂纹,降低零件的疲劳强度。
对于装配零件,装配后,实际接触表面减小、接触刚度降低,影响机器的工作精度。
由此可知,鳞刺是切削加工中获得较好的表面质量的一大障碍。
2 鳞刺的形成过程及原因鳞刺形成的开始是抹拭阶段,这时前一鳞刺已经形成,新鳞刺还未出现,切屑沿着前刀面流出,切屑以刚切离的新鲜表面抹拭刀的前面,将前刀面上起润滑作用的吸附膜逐渐拭净,切屑和前刀面的摩擦系数逐渐加大,切屑底层金属流速降低,金属纤维被拉长,出现“滞流”现象,当接触面间切削刃处的压力、温度增加到一定程度时,切屑底层中的切应力超过材料的剪切强度,滞流层金属流速为零,此时切屑和刀具就发生冷焊现象如图1(a)所示,切屑停留在前刀面上,暂时不沿前刀面流出,且代替前刀面挤压待切削层,这时切削刃的前下方切屑与加工表面之间出现一裂口,如图1(b)所示,由于切削运动的连续性,切屑一旦滞留在前刀面上,便代替刀具继续挤压切削层,使切削层中受到挤压的金属转化为切屑,而这部分新成为切屑的金属,将逐层地积聚在起挤压作用的那部分切屑的下方,这些金属一旦积聚并转化为切屑,便立即参加挤压切削层的作用,如图1(c)所示。
随着层积过程的发展,切削厚度将逐渐增大,切削力随之增大,切削抗力也随之增大,切屑沿前面流出时的水平推力也增大。
图1 鳞刺形成过程各阶段示意图当层积金属达到一定厚度后,水平分力也随之增大到能够推动切屑重新流出的程度,于是切屑又重新开始沿前刀面流出,同时切削刃便刮出鳞刺的顶部,一个鳞刺的形成过程使告结束,紧接着又开始另一个新鳞刺的形成过程,如图1(d)所示。
制造工艺学问答题机械工艺学Sky出品(华理的学弟学妹们,膜拜你

制造工艺学问答题机械工艺学Sky出品(华理的学弟学妹们,膜拜你工件的安装和夹具1、定位、夹紧、安装定位:机械加工前,使工件在机床或夹具中占据某一正确位置的过程。
夹紧:工件定位后,采用一定机构将其夹紧,使其定位不受切削加工影响的过程。
安装:工件从定位到夹紧的整个过程。
2、何谓夹具?其作用是什么?夹具:在机械加工中,依据工件的加工要求,使工件相对机床、刀具占有正确位置,并能迅速、可靠地夹紧工件的机床附加装置,称为机床夹具,简称夹具。
3、试述六点定位原则。
工件在空间具有六个自由度,即沿x、y、z三个直角坐标轴方向的移动自由度和绕这三个坐标轴的转动自由度。
用适当分布的六个支承点(即定位元件)来限制工件的六个自由度的原则称为六点定位原则。
4、完全定位、不完全定位。
完全定位:工件的六个自由度被不重复地完全限制的定位。
不完全定位:允许少于六点的定位,即工件的六个自由度不全都被限制的定位。
5、过定位、欠定位。
过定位:工件上的某个自由度被限制了两次以上的定位。
欠定位:工件的定位支承点数少于所应限制的自由度数,从而使应该限制的自由度没有被限制的定位6、什么是基本支撑?有哪些类型,各种基本支撑的使用特点?基本支撑:用于限制工件的自由度,即真正具有独立定位作用的定位元件类型:固定支撑、可调支撑、自位支撑固定支承(装上夹具后,一般不再拆卸或调节)1、支承钉:特点:平头,用于光滑平面定位;圆头,因接触刚性差,夹紧后会代来较大的安装误差,所以一般用于未经机加工的平面定位;网纹顶面,与定位面的摩擦力较大,可阻碍工件的移动,加强定位稳定性,常用于粗糙表面的侧面定位。
2、支承板:特点:应用于工件平面较窄,很难用支承钉布置成支撑三角形;或工件刚度不足,夹紧力和切削力又不能恰好落在支承点上时。
可调支承用于工件上未经机械加工的表面,当毛坯的尺寸变化较大时,便于调节。
自位支承特点:每一个自位支承只相当于一个定位点,限制一个自由度,但由于增加了与工件接触点的数目,可减少工件的变形。
- 1、下载文档前请自行甄别文档内容的完整性,平台不提供额外的编辑、内容补充、找答案等附加服务。
- 2、"仅部分预览"的文档,不可在线预览部分如存在完整性等问题,可反馈申请退款(可完整预览的文档不适用该条件!)。
- 3、如文档侵犯您的权益,请联系客服反馈,我们会尽快为您处理(人工客服工作时间:9:00-18:30)。
加工中心积屑瘤与鳞刺
(一)积屑瘤
1.积屑瘤的形成
切削塑性金属时,往往会在刀具切削刃口附近粘结着一块剖面呈三角状或鼻状的金属块,它包围着切削刃且覆盖部分前刀面,这种堆积物叫做积屑瘤。
2.积屑瘤对加工的影响
(1)保护刀具。
积加工中心屑瘤包围着切削刃,同时覆盖着一部分前刀面,由于积屑瘤是材料剧烈变形强化后的产物,其硬度高达金属母体的2~3倍,故能代替切削刃和前刀面进行切削,所以切削刃和前刀面都得到了积屑瘤的保护,沈阳机床一厂减少了刀具的磨损。
(2)增大实际前角。
有积屑瘤的车刀,实际前角丁,可增大至30‘—35‘,因而减少了切屑的变形,降低了切削力。
(3)影响工件表面质量和尺寸精度。
由于积屑瘤总是极不稳定的,时生时灭,时大时小,在切削过程中,一部分积屑瘤被切屑带走,一部分嵌入工件已加工表面,使工件表面形成硬点和毛刺,表面粗糙度值变大。
因而有一层厚度为AH的金属层留下来,并被O点以下的刃口圆弧面挤压变形后成为已加工表面。
AH减薄到Ah。
.减薄的原因是因为刀具挤压变形后,金属塑性变形部分不能恢复,恢复的只是弹性变形部分(即AH—Ah)。
加工中心塑性变形愈大,表面变形硬化愈严重。
硬化层的硬度可达工件硬度的1.2~2倍,硬化层深度可达0.07—0.5mm。
切削加工造成的已加工表面硬化层常常伴随有表面裂纹,使表面粗糙度值增大,疲劳强度下降。
当以较小的切削深度再次切削时,则刀具不易切人,并且使刀具容易磨损,沈阳机床一厂因此应设法减轻这种现象。
切削过程中变形和摩擦所消耗功的绝大部分转变为热能。
切削热来源于三个变形区。
在第1变形区内被切材料发生弹性变形和塑性变形而产生的热量,分别用Ql和Q2表示;在第Ⅱ变形区有刀具前刀面与切屑摩擦而产生的热量,用Q,表示;在第Ⅲ变形区内有刀具后刀面与工件摩擦而产生的热量,用Q:表示。
切削时所产生的热量由切屑、工件、刀具及周围介质传出,加工中心分别用Q,、Q,、口,和Q8表示。
上述切削热的产生和传散的平衡关系式为
Q二Q1+Q2+Q3+Qx二Q5+Q6+Q7+Qx
例如不用切削液,以中等切削速度切削钢件时,切削热由各部分传出的比例:0,为50%-80%,Q,为10%—40%,Q,为3%—9%,Q。
为1%。
(二)切削区温度的分布
切削区温度通常是指切屑、工件与刀具接触表面上的平均温度。
沈阳机床一厂实际上,切屑、工件和刀具上各点处的温度是不相同的。
例如,在切削低碳钢时,若u二200m/min、/:0.25mm/r,离切削刃1mill处,温度可达1000~C,它比切屑中平均温度高2—2.5倍,比工件中的平均温度约高20倍。
这是由于该处热量集中不易传散所致。
(三)切削温度对工件、刀具和切削过程的影响
1.切削温度对工件材料机械性能的影响, 切削时温度虽然很高,加工中心但对工件材料硬度、强度的影响并不很大,对剪切区应力的影响也不明显。
其原因是:切削速度较高时,变形速度很高,其对增加材料强度的影响足以抵消切削温度降低强度的影响;另外,切削温度是在切削变形过程中产生的,因此对剪切面上的应力应变状态来不及产生很大的影响,只对切屑底层的剪切强度产生影响。
实验表明:工件材料预热至500—800~C后进行切削,切削力下降很多。
但高速切削时温度达到800—900~C,切削力却下降不多,这是因为切削温度对剪切区工件材料强度影响不大。
沈阳机床一厂加热切削是切削难加工材料的一种好方法,被普遍应用,如等离子焰加热切削效果较好。
2.切削温度对刀具材料的影响
硬质合金的性质之一是在高温时,强度比较高,韧性比较好。
因此,适加工中心当提高切削温度以防止硬质合金崩刃,对提高其耐用度是有利的。
3.切削温度对工件尺寸的影响
工件受热膨胀,尺寸发生变化,切削后不能达到精度要求。
在加工细长轴时,工件因受热而变长,但因夹固在机床上不能自由伸长而发生弯曲,加工后使中部直径变大。
另外,刀杆受热膨胀,使实际背吃刀量增加,改变了工件的加工尺寸。
在精加工和超精加工时,切削温度对加工精度的影响十分突出,必须特别注意降低切削温度。
(四)影响切削温度的因素
1.切削用量
切削用量中以切削速度对切削温度的影响最大。
实验得出,沈阳机床一厂当切削速度增大一倍时,切削温度约增高20%—30%;当进给量增加一倍时,切削温度增高约15%-18%;当背吃刀量增加一倍时,加工中心切削温度增高10%左右。
2.刀具几何参数
凡是能减少切削过程产生热量的因素,都能降低切削温度;凡是能改善散热条件的因素,也都能降低切削温度。
前角增大、切削变形减小;切削力降低,消耗的功率减小,所以切削温度降低。
但前角又不宜过大,否则散热条件不好,切削温度反而增加。
主偏角减小,在相同的条件下,切削刃参加工作的长度增加,而切削厚度减薄,散热条件好,所以切削温度下降。
3.刀具磨损
磨损后的刀具,后刀面刀刃处形成后角等于零的棱边,使刀具与已加工表面摩擦加大,增加了功率的消耗。
刀具磨损后,切削刃变钝,刃区前方对切屑的挤压作用增大,沈阳机床一厂加工中心塑性变形增加,从而使切削力及功率的消耗增加。
上述原因均使产生的切削热增加,所以当刀具磨损严重后切削温度会急剧升高。
4.被加工材料
材料的强度高、硬度高,切削时消耗的切削功越多,产生的切削温度也越高。
材料的导热系数越低,切削区传出的热量越少,切削温度就越高。