quick start manual stim202 evaluation kit
ateq f620 快速入门指南说明书
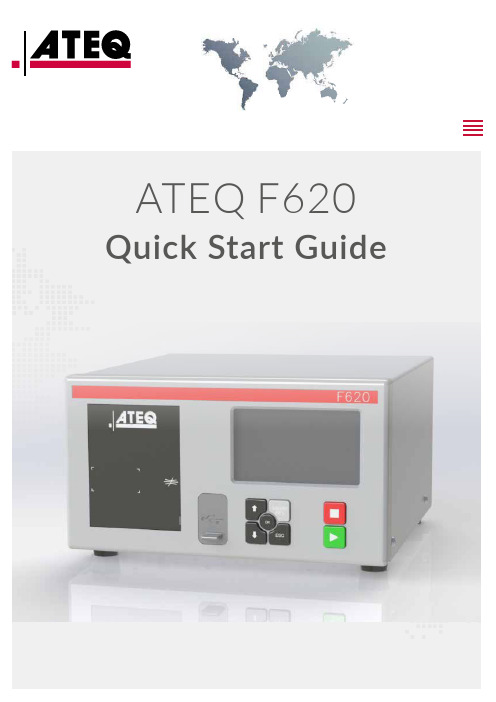
Quick Start Guide2 /02Table of contents Safety advisory / WarrantyGood practices and safety instructionsAir quality requirementsPreambleATEQ F620, a universal leak testerLeak testPrinciple of a cycleYour ATEQ F620Front panelConnectors on the back panel (with all options) Power supply connectorsDigital linksAnalog outputsDigital inputs/outputsPneumatic connectorsPneumatics configurationUser interfaceOverviewKeysDisplayStarting upPower upPreparing a programModifying a parameterSelecting a programStarting and stopping current cycleUser adjustmentsOptions of the menus SpecificationsCharacteristicsQSG_F620.283.00_EN_01 / 2019-02-20QSG_F620.283.00_EN_01 / 2019-02-203 /46ATEQ Manufacturer Plants - Measurement Solution, Global Leader.We continuously work on improving our products. This is why information contained in this manual, the device and the technical specifications may be modified without prior notification.Pictures and figures in this manual are non-contractual.Safety advisory / Warranty4 /46Safety recommendationsIf the device is supplied with 100 / 240 V AC, it is mandatory to connect it to the ground witha good link to the ground, to protect against electric hazard or electrocution.It is dangerous to change the status of the outputs.They can control power actuators or other equipment (mechanical, pneumatic, hydraulic,electrical or other) which can cause serious personal injury and damage to surrounding material.For safety and quality measurement reasons, it is important, before powering on the device,to ensure that it is air supplied with a minimum operating pressure (0.6 MPa (87 PSI) ± 15%).Recommendations for the test environmentKeep the test area as clean as possible.Recommendations for operatorsATEQ recommends that the operators who use the devices have training and a level ofqualification that correspond to the job to perform.General recommendations—Read the user manual before using the device.—All electrical connections to the device must be equipped with safety systems (fuses, circuit breakers, etc.) adapted to the needs and in accordance with the applicablestandards and rules.—To avoid electromagnetic interference, electrical connections to the device must be shorter than 2 meters.—Power supply plug must be grounded.—Disconnect the device from the mains before performing any maintenance work.—Shut off the compressed air supply when working on the pneumatic assembly.—Do not open a connected device.—Avoid splashing water on the device.ATEQ is at your disposal for any information concerning the use of the device undermaximum safety conditions.We draw your attention to the fact that ATEQ cannot be held responsible for anyaccident related to a misuse of the measuring instrument, the workstation or non-compliance of the installation with safety rules.In addition, ATEQ declines any responsibility for the calibration or the fitting of theirinstruments that is not done by ATEQ.ATEQ also declines any responsibility for any modification (program, mechanical orelectrical) of the device done without their written consent.QSG_F620.283.00_EN_01 / 2019-02-20QSG_F620.283.00_EN_01 / 2019-02-205 / 46The air supplied into the device must be clean and dry. Even though the device is provided with a filter, the presence of dust, oil or impurities may cause malfunction.Air quality requirements according to ISO standard 8573The air must be clean and dry.The presence of impurities, oil or humidity in the air may cause deterioration which will not be covered by the warranty.When the instrument is working in vacuum conditions, impurities must be prevented from being drawn into its internal components.For this purpose we strongly recommend that a suitable airtight filter is installed between the part under test and the instrument.ATEQ recommends the following characteristics for the air supplied into the device.Recommended additional equipmentATEQ recommends the installation of this additional equipment: —Air dryer to provide dry air at less than - 40°C dew point —25 micron and 1/100 micron double filter.Preamble6 /46ATEQ F620 is a leak detector that tests the airtightness of parts.ATEQ F620 can memorise 128 different test programs.QSG_F620.283.00_EN_01 / 2019-02-20QSG_F620.283.00_EN_01 / 2019-02-207 / 46Direct measurement principleThe part under test 3 and the reference part 5 are filled to an identical pressure.A differential sensor 4 measures the pressure variation between the part under test 3 and the reference part 5. In some applications, the reference part can be replaced by a cap.1 Device2 Pressure sensor3 Part under test4 Differential pressure sensor5 Reference partDesensitized testThis mode is used for the measurement of large leaks, when the reject level required isabove the full scale of the differential sensor.The test pressure is applied to the input of the test part 3.The measurement is performed by the pressure sensor 2.1 Device2 Pressure sensor3 Part under test4 Cap on the reference connectorOther types of test are available in option (Burst test, Volume, Operator...).The measurement cycle is made of 4 main phases: fill, stabilization, test, dumping.8 /460Waiting phase1Fill phase2Stabilization phase3 Test4 DumpingQSG_F620.283.00_EN_01 / 2019-02-20Your ATEQ F6209 /46 The user interface is located on the front panel.1 Display2Cycle keys3Navigation keys4USB connectors5Quick connector6Mechanical RegulatorFor more information, refer to User interfaceQSG_F620.283.00_EN_01 / 2019-02-2010 /46QSG_F620.283.00_EN_01 / 2019-02-2011 /46 * These connectors are not operational. They are provided for future development of ourdevices.12 /46The device can be connected to an external power supply (24 V DC - 2 A) or provided with an internal power supply (100 / 240 V AC) (option).External supply24 V DC connector (J7)The device can be connected to a 24 V DC - 2 A power supply through a M12 4 pins type connector.24 V DC on the relay board connector (J11) (option)The device can also be connected to a 24 V DC - 2 A power supply through J11 connector on the relay board.Apply 24 V DC to the pin 2 or 4.13 /46Internal supply only100 / 240 V AC connector (J7) (option)The device can be connected to a 100 / 240 V AC power supply (option).This connector has a ON/OFF button.It is mandatory to connect the device to the ground with a good link to the ground, to protectagainst electric hazard or electrocution.1 ON 0 OFF14 /46PC USB connectors (on front face)USB connectors can be used for connecting miscellaneous compatible USB devices.The USB connectors are located under the rubber cover 1 (see figure).1Rubber cover2USB connector to PC3USB connector to USB keyDo not connect two USB devices at the same time.Do not use a cable longer than 2 m.Push the rubber cover 1 slightly forward for an easy access to USB connectors 2 and 3.Only use this connection for temporary communication. Connection to a PC cannot be usedpermanently because the communication can be disconnected by the PC.Printer RS232 connector / Modbus (option) or Profibus (option)(J12)RS232 - SubD 9 pins male connector (printer)RS232 for printer, bar code reader, PC connection.15 / 46RS232 - SubD 9 pins female connector (Profibus) optionProfibus: SubD 9 pins female connector.Devicenet connectors (J5) (J6) (option)M12 type connector - 5 pins male connector (J5) (Devicenet input)For connection to others ATEQ devices.M12 type connector - 5 pins female connector (J6) (Devicenet output)For connection to others ATEQ devices.Profinet connectors (J5 + J6) (option)M12 D coded type connector - 4 pins female connector (J5 + J6)16 /46Standard connection Ethernet TCP / IP protocol.—Ethernet IP—Profinet—Ethercat (J5 = Input J6 = Output).M12 type connector - 8 pins female connector (J1)17 /4618 /46The 24V DC power supply for the digital inputs can be provided by 2 means:—The internal power supply of the device (0.3A max)—An external power supply provided by the customer.Inputs default mode is PNP. NPN mode is available on request.Relay board connector (J11) (option)Characteristics—Inputs• Activation: + 24 V DC.—Outputs• Dry contacts• 60 V AC / DC max - 200 mA max.19 /46The device can be energized through the J11 connector of the relay board (except if internal supply option):0 V to the pin 1624 V DC to the pin 2 or 4.Program selection extension connector (J10) (option)The J10 connector is an extension of the J11 connector that enables the selection of 128 programs.Characteristics—Inputs•Activation: + 24 V DC.20 /46Program selection (J11 and J10)The connectors J11 and J10 (option) enable you to select a program from digital inputs.Combinations of connector pins to activate for program selection* X is equal to 0 or 1 in function of the program number.21 /46Valve codes and auxiliary outputs board connector (J9) (option)Characteristics—Outputs:• 24 V DC - 100 mA max per output. —Inputs:•Activation: + 24 V DC.22 /46Pneumatic connectors used to connect the part under test are located on the back panel of the device.Pneumatic supplyThe pneumatic supply has to meet specific requirements recommended by ATEQ. Refer to Good practices and safety instructions section.A specific filter may be necessary.The air is supplied via the filter located on the back panel of the device.Metal air filterThe metal filter is used for 1 MPa(145 PSI) range.The maximum pressure admissible is1.2 MPa (174 PSI).Plastic air filterThe plastic filter is used for 0.5 MPa(72.5 PSI) range (direct and indirectmodes) or 2 MPa (290 PSI) range (forpilot valves input).The maximum pressure admissible is690 kPa (100 PSI).23 /46Quick connector (on front face) (option)Use this function to check the calibration.As this connector is part of the measurement circuit, all its connections must be air tight.Test and reference outputsThe outputs enables parts to be connected (test and reference)1 Test connector2 Reference connector3 Not used4 Exhaust output5 Pressurization outputMetallic fitting available for test (1) and reference (2) connectors: —2.7/4 mm —3/5 mm —4/6 mm —6/8 mmDifferential sealed part connectors (option) (V1 and V2)External volume (closed tube) connection.Metallic fitting available for V1 and V2 connectors: —2.7/4 mm24 /46Other inputs / outputsThe outputs enables parts to be connected (test and reference)1Pilot pressure input or test pressureinput (according configuration)2Test pressure output (indirect mode)(from 0.5 to 2 MPa (72.5 to 290 PSI)according configuration)3Pneumatic input or output (accordingconfiguration)4Exhaust output (indirect mode)Pneumatic output 0.6 MPa (87 PSI) (option)A and B: automatic connectors option. Theseconnectors are used to drive pneumaticcaps on the part under test.Air supply input for optionsInstant fitting: 6 mm diameter—Vacuum input for vacuum range—External regulated pressure (accordingconfiguration)Calibration check by volume variation connector (option) (V)External volume (closed tube) connection.25 /46 Direct mode - Low rangePressure: from 0 to 500 kPa (72.5 PSI)ConnectionsDirect mode - Medium rangeMaximum pressure: 1 MPa (145 PSI)26 /46ConnectionsDirect mode - High rangeMaximum pressure: 2 MPa (290 PSI)27 /46ConnectionsIndirect modeMaximum pressure: 1 MPa (145 PSI)28 /46Connections29 /46Direct mode - Sealed part testPressure: from 0 to 500 kPa (72.5 PSI)This configuration can be used for test of small test part volumes.Protect volumes and pipes from air blowing and temperature variations.ConnectionsDirect mode - Sealed part differential volume testPressure: from 0 to 500 kPa (72.5 PSI)30 /46ConnectionsDirect mode - Option test check by pressure dropPressure: from 0 to 500 kPa (72.5 PSI)31 /46ConnectionsUser interface32 /46The user interface comprises a display and user keys located on the front panel.1 Display2Cycle keys3Navigation keysKEYSCycle keysThe cycle keys are used to start and to stop a measurement cycle.33 /46Navigation keysThe navigation keys are used to select menus/options and change parameter values.Smart keySmart key is a programmable key that provides direct access to a function selected bythe user.This key is programmable through the MAIN MENU screen:MAIN MENU > CONFIGURATION > MISCELLANEOUS > SMART KEYDISPLAYThe device uses 4 main screens.The Program screenUse the Program screen to select a test program.1Current program name (here NAME )2 Current program number (here 001)3 Test type (here LEAK TEST )Access at start-up of the instrument or by pressing several times Esc .34 /46The Measurement cycle screenThe Measurement cycle screen displays the different values of the current test (or last one).1Test pressure measurement2Test result or step phase3Test reject value4Vertical line test result5Remaining time of the current phaseor ready status6Leak measurement7Measurement unit8Current program9Vertical line test resultA star (*) can be displayed after the measurement unit 7 when the standard conditions function is validated.Refer to the Reference Manual.The MAIN MENU screenThe MAIN MENU screen gives access to different sections for managing the device and the test parameters.Access: from the Program screen, press .MAIN MENUSPE CYCLEPARAMETERSCONFIGURATIONSERVICERESUL TSUSB35 / 46Starting up1. Make sure that all the necessary connections are in place.Electrical: such as power supply, inputs/outputs Pneumatic: including line pressure supply2. Power up your device.When power-up is completed, the Program screen is displayed with last program used on screen.Use this procedure to configure a new test program.On the MAIN MENU screen:ACCESSING THE PARAMETERS1.Select PARAMETERSusing the up/downkeys and press .MAIN MENUPARAMETERS CONFIGURATIONSERVICE RESUL The program list is displayed.SELECTING A PROGRAM NUMBER 2. Select the program to configure and press.A list of the available measurement types is displayed: —LEAK TEST type—BLOCKAGE type (option)—DESENSITIZED TEST type (option) —OPERATOR type (option) —BURST TEST type (option) —VOLUME type (option)36 /46CONFIGURING THE ASSOCIATED MEASUREMENTS3.Select a measurement type and press .The parameters of the selected measurement type aredisplayed.4. Define the measurement cycle parameters.See: Modifying a parameter.Use this procedure to complete the test program setup.The protection of the parameters is configurable. If the icon is displayed at the bottom of the screen, you must insert the USB unlocking device or enter a password before modifying a parameter.On the PARAMETERS screen of the program (see: Preparing a program):1. Press up/down to select the parameter tomodify, and press.An arrow is displayed on the right of the parameterbeing modified.2. Use the up/down up/down keysto modify the parameter value, and press tovalidate.The arrowreturns to the left of the modified parameter.3. Repeat these steps until all parameters are set.4. To return to the MAIN MENU screen, press Escas many times as necessary.37 / 46If necessary, you can select another program.1. Pressup/down.Use the front panel keys to start/stop a measurement cycle.With the desired program displayed on the Program screen:STARTING A MEASUREMENT CYCLE 1. Press Start.The cycle phases of the program are successively displayed:FILLSTABILISATION TEST DUMPAt the end of the cycle, the results are displayed and READY appears at the bottom right of the screen.During the measurement cycle, you may press to access the MAIN MENU screen and set parameters for a next measurement cycle.STOPPING A CYCLE2. Press Reset to immediately stop the current measurement cycle and return to the Program screen.User adjustments38 /46Different menus are accessible on the MAIN MENU screen.For more information, refer to the Reference Manual.SPE CYCLE menuUse this menu to carry out specific procedures necessary to ensure the proper operationof specific measurement cycles (for example, adjustment of pressure regulator).Some parameters are displayed when specific functions are activated.39 /46TO START SPECIAL CYCLES...1. On the SPECIAL CYCLE MENU screen, select acycle, and press to validate.2. PressStart to start the cycle.3. To stop the current cycle pressReset .PARAMETERS menuUse this menu to configure the measurement cycle associated to each test program.Default parameters of the LEAKtype testsSome parameters are displayed when specific functions are activated.40 /46Additional functions41 /46Some functions are available depending on software version.42 /46CONFIGURATION menuUse this menu to configure your ATEQdevice.Start on the instrument frontpanel. Programs can only be started from the instrumentConfiguration of the assigned function to theSmart key43 /46SERVICE menuUse this menu to do the maintenance of your device (status check, internal tests...).RESULTS menuIn this section, manage measurements results.44 /46USB menuThis section describes save and restore parameters on an external USB device.Specifications45 /46 Technical characteristics of the device.Main characteristics46 /46。
AIX 6.1快速入门指南说明书
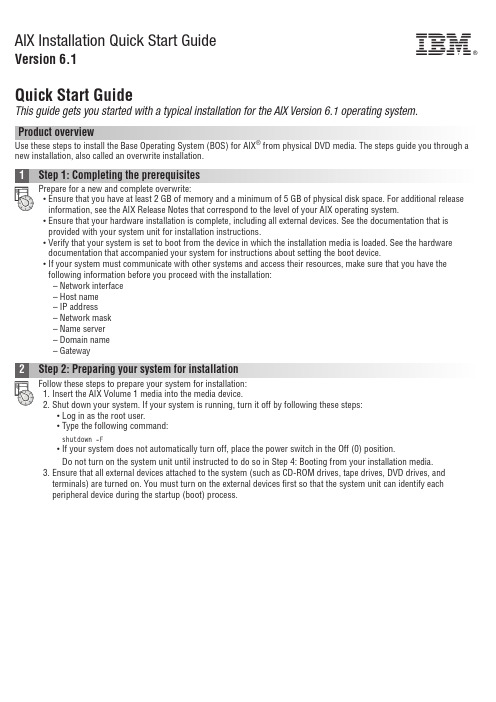
AIX Installation Quick Start GuideVersion 6.1Quick Start GuideThis guide gets you started with a typical installation for the AIX Version 6.1operating system.Product overviewUse these steps to install the Base Operating System (BOS)for AIX ®from physical DVD media.The steps guide you through a new installation,also called an overwrite installation.Prepare for a new and complete overwrite:v Ensure that you have at least 2GB of memory and a minimum of 5GB of physical disk space.For additional release information,see the AIX Release Notes that correspond to the level of your AIX operating system.v Ensure that your hardware installation is complete,including all external devices.See the documentation that is provided with your system unit for installation instructions.v Verify that your system is set to boot from the device in which the installation media is loaded.See the hardware documentation that accompanied your system for instructions about setting the boot device.v If your system must communicate with other systems and access their resources,make sure that you have the following information before you proceed with the installation:–Network interface–Host name–IP address–Network mask–Name server–Domain name–GatewayFollow these steps to prepare your system for installation:1.Insert the AIX Volume 1media into the media device.2.Shut down your system.If your system is running,turn it off by following these steps:v Log in as the root user.v Type the following command:shutdown -Fv If your system does not automatically turn off,place the power switch in the Off (0)position.Do not turn on the system unit until instructed to do so in Step 4:Booting from your installation media.3.Ensure that all external devices attached to the system (such as CD-ROM drives,tape drives,DVD drives,and terminals)are turned on.You must turn on the external devices first so that the system unit can identify each peripheral device during the startup (boot)process.If you have not set up your ASCII terminal,set the communications,keyboard,and display e the followingcriteria and your terminal reference documentation to set the communications,keyboard,and display options.The following settings are typical,but your terminal might have different option names and settings than these options: Communication Options:Options SettingsLine speed(baud rate)9600Word Length(bits per character)8Parity no(none)Number of stop bits1Interface RS-232C(or RS-422A)Line control IPRTSKeyboard and display options:Options SettingsScreen normalRow and Column24x80Scroll jumpAuto LF(line feed)offLine Wrap onForcing Insert line(or both)Tab fieldOperating Mode echoTurnaround Character CREnter returnReturn new lineNew Line CRSend pageInsert Character spaceFollow this procedure for booting from your installation media:1.Turn on the system unit power switch.2.When the system beeps twice,press5on your ASCII terminal.The word keyboard is shown when the beeps occur.3.If you have more than one console,each one might display a panel that directs you to press a key to identify yoursystem console.A different key is specified for each console that is displayed on this panel.If this panel opens,press the specified key only on the console that you want to use for the installation.(The system console is the keyboard and display device that is used for installation and system administration.)4.Select the language that you prefer to use during installation,and press Enter.1.Display the installation settings before you install the BOS,by typing2in the Choice field to select2Change/Show2.Verify the default installation settings from the Overwrite Installation and Settings panel.3.If the installation and system settings are correct,type0in the Choice field and press Enter.Confirm that theselections on the installation summary panel are correct,and press Enter to begin the BOS installation.The system automatically reboots after the system installation is complete.Go to Step9:Finishing the BOS installation.If your installation settings are not correct,or you want to change the installation settings,go to Step6.Changing the installation settings.To change the installation settings,complete the following steps:1.2.When the Change Method of Installation panel is displayed,type1New and Complete Overwrite Installation and pressEnter.When the Change Disk(s)Where You Want to Install panel is displayed,you can change the destination disk for the3.If the default settings shown are correct,type0in the Choice field and press Enter.To change the destination disk,complete the following steps:a.Type the number for each disk where you want to install the BOS in the Choice field and press Enter.Do not pressEnter a final time until you have finished selecting all disks.If you need to deselect a disk,type its number asecond time and press Enter.b.To finish selecting disks,type0in the Choice field and press Enter.The Installation and Settings panel is displayedwith the selected disks listed under System Settings.1.Type2(Primary Language Environment Settings)in the Choice field on the Installation and Settings panel.2.Select the appropriate set of cultural convention,language,and keyboard options.Most of the options are apredefined combination;however,you can define your own combination of options.3.To select a predefined Primary Language Environment,type the corresponding number in the Choice field and pressEnter.To configure your own Primary Language Environment,complete the following steps:a.Select More Choices.b.Page through the choices and select the Create Your Own Combination option.c.On the Set Primary Cultural Convention panel,type the corresponding number in the Choice field and press Enter.d.On the Set Primary Language panel,type the number in the Choice field that corresponds to your choice for theprimary language and press Enter.e.On the Set Keyboard panel,type the number in the Choice field that corresponds to the keyboard that is attachedto the system and press Enter.To verify your BOS installation settings:1.2.Press Enter to begin the BOS installation.installed.The system automatically reboots.The Installation Assistant guides you through the configuration tasks. Related informationFor more information,see the following resources:v For additional release information,see the AIX Release Notes that corresponds to your level of the AIX operatingsystem.v For late-breaking information,which might include information about the configuration process and installed software, see the readme files.v For more detailed installation notes,see the Installation and migration topic collection in the IBM®AIX6.1Information Center(/infocenter/aix/v6r1/index.jsp).AIX Version6.1Licensed Materials-Property of IBM.©Copyright IBM Corp.2012,ernment Users Restricted Rights-Use,duplication or disclosure restricted by GSA ADP Schedule Contract with IBM Corp.IBM,the IBM logo,and are trademarks or registered trademarks of International Business Machines Corp.,registered in many jurisdictions worldwide.Other product and service names might be trademarks of IBM or other companies.A current list of IBM trademarks is available on the web at“Copyright and trademark information”(/legal/copytrade.shtml).Document Number:SA23-2248-04Printed in USA。
ASUS F4A Motherboard 用户手册说明书
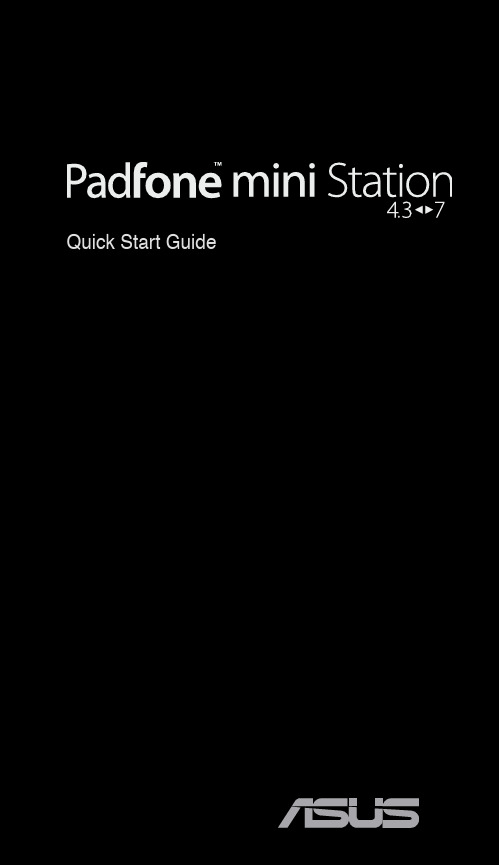
Quick Start GuideCopyright © 2013 ASUSTeK COMPUTER INC.All Rights Reserved.No part of this manual, including the products and software described in it, may be reproduced, transmitted, transcribed, stored in a retrieval system, or translated into any language in any form or by any means, except documentation kept by the purchaser for backup purposes, without the express written permission of ASUSTeK COMPUTER INC. (“ASUS”).Product warranty or service will not be extended if: (1) the product is repaired, modified or altered, unless such repair, modification of alteration is authorized in writing by ASUS; or (2) the serial number of the product is defaced or missing.ASUS PROVIDES THIS MANUAL “AS IS” WITHOUT WARRANTY OF ANY KIND, EITHER EXPRESS OR IMPLIED, INCLUDING BUT NOT LIMITED TO THE IMPLIED WARRANTIES OR CONDITIONS OF MERCHANTABILITY OR FITNESS FOR A PARTICULAR PURPOSE. IN NO EVENT SHALL ASUS, ITS DIRECTORS, OFFICERS, EMPLOYEES OR AGENTS BE LIABLE FOR ANY INDIRECT, SPECIAL, INCIDENTAL, OR CONSEQUENTIAL DAMAGES (INCLUDING DAMAGES FOR LOSS OF PROFITS, LOSS OF BUSINESS, LOSS OF USE OR DATA, INTERRUPTION OF BUSINESS AND THE LIKE), EVEN IF ASUS HAS BEEN ADVISED OF THE POSSIBILITY OF SUCH DAMAGES ARISING FROM ANY DEFECT OR ERROR IN THIS MANUAL OR PRODUCT.SPECIFICATIONS AND INFORMATION CONTAINED IN THIS MANUAL ARE FURNISHED FOR INFORMATIONAL USE ONLY, AND ARE SUBJECT TO CHANGE AT ANY TIME WITHOUT NOTICE, AND SHOULD NOT BE CONSTRUED AS A COMMITMENT BY ASUS. ASUS ASSUMES NO RESPONSIBILITY OR LIABILITY FOR ANY ERRORS OR INACCURACIES THAT MAY APPEAR IN THIS MANUAL, INCLUDING THE PRODUCTS AND SOFTWARE DESCRIBED IN IT.Products and corporate names appearing in this manual may or may not be registered trademarks or copyrights of their respective companies, and are used only for identification or explanation and to the owners’ benefit, without intent to infringe.E8431First Edition Model: T00CPThank you for purchasing an ASUS product! Before you start, read all the safety information and operating instructions in the User Manual bundled with your PadFone mini 4.3 to prevent injury or damage to your device.NOTE: This bundled Quick Start Guide isfor reference only and is subject to change without prior notice. For the latest updatesand additional information, please visit.23Power key 4Volume key5PadFone mini 4.3 6SpeakerCharging your PadFone mini StationFully charge your PadFone mini Station before connecting the PadFone mini 4.3.To charge your PadFone mini Station:1. Connect the USB connector into the poweradapter’s USB port.2. Connect the PadFone mini 4.3 cable toyour PadFone mini Station.3. Plug the power adapter into a wall socket.NOTES:• Use only the power adapter that camewith your ing a different poweradapter may damage your device.• Using the bundled power adapter andcable to connect your PadFone mini4.3 to a power outlet is the best way tocharge your PadFone mini Station.• The input voltage range between thewall outlet and this adapter is AC 100V- 240V. The output voltage of the microUSB cable is DC 5.2V, 1.35A.Inserting your PadFone mini 4.3 into the PadFone mini StationTo insert your PadFone mini 4.3 into your PadFone mini Station:1. Align your PadFone mini 4.3 into thePadFone mini 4.3 bay sliding track.CAUTION: We do not recommend adding a protective film or cover to your PadFone mini 4.3 as it can result in difficulty when inserting/removing the PadFone mini 4.3 to/from the PadFone mini Station.NOTE: Always keep the PadFone mini Station bay clean to prevent dust or dirt from scratching or damaging your PadFone mini 4.3.2. Insert your PadFone mini 4.3 all the way into the bay until it is securely connected to the PadFone mini Station.Your PadFone mini 4.3 briefly vibrates when the connection is secured.Removing your PadFone mini 4.3 from the PadFone mini StationGently slide the PadFone mini 4.3 out from theSafety informationPadFone mini Station care• Do not leave your PadFone mini Stationexposed to strong sunlight or excessiveheat for a prolonged period. This maydamage it.• Do not handle your PadFone mini Stationwith wet hands or expose it to moisture orliquids of any kind. Continuous changesfrom a cold to a warm environment maylead to condensation inside your PadFonemini Station device, resulting in corrosionand possible damage.• When traveling, avoid packing yourPadFone mini Station in a suitcase.Cramming the device into a suitcase maycrack the LCD display. Remember toswitch off your wireless connection duringair travel.• Use your PadFone mini Station in anenvironment with ambient temperaturesbetween -10 °C (14 °F) and 35 °C (95 °F).IMPORTANT! To provide electricalinsulation and maintain electrical safety,a coating is applied to insulate the ASUSPadFone mini Station body except on thesides where the I/O ports are located.The battery• Avoid charging in extremely high orlow temperature. The battery performsoptimally in an ambient temperature of +5°C to +35 °C.• Do not remove and immerse the battery inwater or any other liquid.• Never try to open the battery as it containssubstances that might be harmful ifswallowed or allowed to come into contactwith unprotected skin.• Do not remove and short-circuit thebattery, as it may overheat and cause afire. Keep it away from jewellery and othermetal objects.• Do not remove and dispose of the batteryin fire. It could explode and releaseharmful substances into the environment. • D o not remove and dispose of the batterywith your regular household waste. Take itto a hazardous material collection point.• Do not touch the battery terminals.CAUTION:• Risk of explosion if battery is replaced byan incorrect type.• Dispose of used batteries according tothe instructions.Prevention of Hearing LossWarning statement requirement under EN 60950-1:A12.WARNING: To prevent possiblehearing damage, do not listenat high volume levels for longperiods.NOTE: For France, headphones/earphones for this device are compliant with the sound pressure level requirment laid down in the applicable EN 50332-1: 2000 and/or EN50332-2: 2003 standard as required by French Article L.5232-1.15060-19700000。
FIFE-500 快速入门手册说明书

FIFE-500Quick-Start ManualMI 2-263 1 BINTRODUCTION ........................................................................................ 1-1 Copyright information ............................................................................................ 1-1 General information ............................................................................................... 1-1 Language ............................................................................................................... 1-1FEATURES ................................................................................................. 2-1 Display definitions ................................................................................................. 2-1 Button functions and definitions ............................................................................ 2-3 Status bar definitions ............................................................................................. 2-4OPERATION .............................................................................................. 3-1 System setup ......................................................................................................... 3-1 Auto setup configuration ....................................................................................... 3-3 Optional manual configuration ............................................................................... 3-5 Changing the guidepoint ........................................................................................ 3-6Copyright information All of the information herein is the exclusive proprietary propertyof Maxcess International, and is disclosed with the understandingthat it will be retained in confidence and will neither beduplicated nor copied in whole or in part nor be used for anypurpose other than for which disclosed.This Instruction Manual is intended to be used in addition to theFIFE-500 Web Guiding System User Manual, MI 2-262, whichcontains all safety warnings and complete customer servicecontact information.General information The instructions contained in this Quick Start Setup Manual arewritten to support operation of the FIFE -500 Web GuidingSystem.Language These are the original instructions, written in English.Display definitionsThe FIFE-500 uses a QVGA Touchscreen for Operator command inputs and status displays. This Control Panel is divided into 5 sections of information for which a brief description is listed below.Refer to the Figure 1, for the button locations in the standard, horizontal Control Panel. Also refer to the FIFE-500 Web Guiding System User Manual, MI 2-262 for complete display definitions.1.The vertical section on the left side contains the Operation Mode selection buttons(Automatic, Servo-Center, and Manual) and indicates the current Operation Modeselection by displaying the corresponding button in a green color. (Other buttons are blue).2.The horizontal section along the top, above the line, contains the status bar which alwayscontains the menu number. It may also indicate statuses, errors, and digital I/O.3.The middle section indicates the current Operation Mode, the selected sensor signal levelin a bar graph, and the level of Guidepoint Shift. This section also contains buttons for Guidepoint Shift and Guidepoint Reset.4.The lower middle section contains the Left and Right Jog buttons.5.The vertical section on the right side contains the Sensor Selection and Setup buttonsand indicates the current Sensor Mode selection by displaying the proper sensor symbol in the Sensor Select button.Figure 1.FIFE-500 CONTROL PANEL(0° AND 180° ROTATION)The Control Panel can also be configured in a vertical orientation. For the vertical orientation, the following display descriptions apply. Refer to Figure 2 for the button locations.1.The horizontal section along the top, above the line, contains the status bar which alwayscontains the menu number. It may also indicate statuses, errors, and digital I/O.2.The horizontal section near the top, just below the line, contains the Operation Modeselection buttons (Automatic, Servo-Center, and Manual) and indicates the currentOperation Mode selection by displaying that button in a green color.3.The section just below the Operation Mode buttons, indicates the current OperationMode, the selected sensor signal level in a bar graph, and the level of Guidepoint Shift.This section also contains the Guidepoint Shift buttons and the Guidepoint Reset button.4.The section below that, just above the Sensor Select and Setup buttons, contains the Leftand Right Jog buttons.5.The horizontal section along the bottom contains the Sensor Selection and Setup buttonsand indicates the current Sensor Mode selection by displaying the proper sensor symbol in the Sensor Select button.Figure 2.FIFE-500 CONTROL PANEL(90° AND 270° ROTATION)Button functions and definitions The table below gives the name along with an operational function description of each button displayed on the FIFE-500 Web Guiding System.AUTOMATIC This button initiates the Automatic mode. Correction isapplied to the web by moving the guide in response to the output ofthe sensor(s) that have been selected.SERVO-CENTER This button initiates the Servo-Center mode. Theguide is centered in its travel in response to the output of the internalServo-Center transducer.MANUALThis button initiates the Manual mode. No correction isapplied to the guide.SENSOR SELECTIONThis button is used to select the sensor(s) to beused for monitoring the web position when the system is inAutomatic mode. Sensor selection is allowed in Manual and Servo-Center modes only.SETUP This button is used to enter the Setup Menus for configuringand adjusting the guiding system.ARROWS These buttons are used to jog the guide. The direction ofguide movement is configurable.GUIDEPOINT ADJUST The two arrow buttons near the bar graph areused to adjust the System Guidepoint while in Automatic Mode orManual Mode. The button in the center is used to reset the SystemGuidepoint to the default value, which is 50% of the sensorbandwidth.BACK This menu navigation button is used to return to the previousmenu level.HOME This button is used to return to the Operator Level screen.MENU ARROWS These buttons are used in the menu system to pageforward/backward when multiple pages of menu choices areavailable. The arrows will appear disabled (grayed-out) when no morechoices are available in the respective direction.ACCEPT This button is used to save a changed value and return tothe previous screen.REJECT This button is used to discard a changed value and return tothe previous screen.Status bar definitionsThe status bar located horizontally across the top of the FIFE-500 Web Guide Operator Level screen remains visible at all times. The number on the left side of the status bar contains the numerical address of the connected motor controller. The number on the right side of the status bar indicates a hierarchical screen number. The first numerical value indicates the operation mode (1=Manual, 2=Servo-Center, 3=Automatic). The second alphabeticcharacter indicates the sensor mode (A=S1, B=S2, C=S1-S2). This screen number uniquely identifies each screen of the FIFE-500 Web Guiding System. The status bar also displays various icons, which are described on the following pages.OPERATION MODE One of these icons will appear to indicate theoperation mode of the FIFE-500 Web Guiding System. These do notappear on the Operator Level screen since the mode buttons alreadyindicate this information. These will only appear while in the setupscreens.SENSOR One of these icons will appear to indicate the currentlyselected sensor mode. These do not appear on the Operator Levelscreen since the SENSOR button already contains this information.MENU TIMEOUT The menu screens in the FIFE-500 Web GuidingSystem close automatically after 3 minutes of touch screen inactivity. The inactivity timeout option and the timeout value are configurable. The clock icons will appear during stages of the timeout process as the inactivity timer counts down. If a timeout occurs, the respective menu will abort any changes applied and return to the Operator Level screen. Some service-related screens are immune from the timeout option and are indicated by the presence of the orange clock icon.LOGIN AUTHORIZATION LEVEL When security has been configured, one of these icons will appear to indicate the authorization level of the current user. Security is disabled in the factory default configuration so these icons will not be displayed. All menu screens are accessible when security is disabled.READ ONLY MENU When security is enabled, options are available tomake menus “read only”, allowing an operator to view the settings but not change them. This icon will appear when the active menu is a “read only” menu.DIGITAL INPUT COMMAND This icon appears when a valid digital input command is present. Depending on the command, some touch panel controls may be disabled during this time. A red arrow in the down direction indicates digital input influence is disabled. A red up arrow indicates the digital outputs are disabled.GUIDEPOINT CHANGED This icon appears when a new SystemGuidepoint has been applied. This icon will appear on the status bar until the System Guidepoint remains unchanged for approximately 20 seconds.EXTERNAL LOCK This icon indicates the acceptance of the “ExternalLock” digital input command. Automatic guide movement is prohibited while in this state.ASC ON Automatic Sensor Control (ASC) is enabled for the current sensor mode. See the menu description in the FIFE-500 Web Guiding System User Manual, Figure Sheet 2-262.ASC ACTIVE Automatic Sensor Control (ASC) is enabled and the ASC state has been triggered. Automatic guide movement is prohibited. See the menu description for ASC in the FIFE-500 Web Guiding System User Manual, MI 2-262.MOTOR BLOCKED This icon indicates the motor is stalled.COMMUNICATION ERROR This error icon indicates communication is not working between the operator interface and the motor controller.VOLTAGE ERROR This error icon appears when the input voltage, motor rail voltage, or internal 12 volt power is outside acceptable range.NETWORK ERROR This icon appears when the operator interface is unable to gain network control.LINKED MODE This icon appears when the “linked mode” is active. Linked mode is used in networked systems to send the Automatic, Manual, and Servo-Center commands to all network devices simultaneously.MOTOR TYPE FAULT This icon appears when there is no motor type configured.COMMUNICATION FAULT This icon appears when a problem is detected with the communication signals. This can be caused by hardware or an addressing conflict in a networked system.LINE SPEED ZERO This icon appears when line speed control is enabled and the sensed line speed is zero. Guide correction is inhibited in Automatic mode under these conditions.MCP-05 SEEK If the MCP-05 option has been enabled, this icon will blink while a seek operation is in progress.System setupSetup screensFigure 3.FIFE-500 CONTROL PANELLEVEL 1 SETUP SCREENFigure 4.FIFE-500 CONTROL PANELSENSOR CALIBRATION SCREEN1.Connect +24 VDC Power to the input receptacle, located on the top side of theBase Assembly. Refer to MI 1-915, which is supplied with each system.2.Apply the proper power to the system.Continued next pageSystem setup3. Verify the system is in Manual Mode by pressing the MANUAL button on the Control Panel.4. Switch the system to Servo-Center Mode by pressing the SERVO-CENTER button.5. Thread the web/strip to be used, through the system and pull proper tension, ifpossible.6. Switch the system to Manual Mode by pressing the MANUAL button.7.Perform Sensor Calibration on the sensor(s) that will provide position feedback forthe web/strip. If two sensors are being used, they must be calibrated independently. Refer to Figures 3 and 4 shown on page 3-1. Be sure to use the web to be guided tocalibrate the sensor(s).a. Press the SETUP button to enter the Setup menus.b. Press the SENSOR SETUP icon to enter the Sensor Calibration menu.c. Select the desired sensor by pressing the SENSOR SELECTION button.d. Press the ‘Start Calibration’ button to begin the calibration.e.The Jog buttons at the bottom of the screen may be used to move theweb material in and out of the sensor as needed during calibration. f. Follow the instructions displayed on the Control Panel.g.When prompted to save the calibration, select YES or NO.h. Repeat this procedure for each sensor, if two sensors are to be used.i. Once this procedure has been completed, Press the ACCEPT (√) button tosave the changes.j. Press the BACK or HOME button to return to the Operator Level screen. Insimulation, these buttons are not available.Once this procedure has been performed for each sensor, it does not need to be repeated, unless the web/strip opacity has changed.Auto setup configurationNOTE: If Manual Configuration is desired, go to page 3-5.Figure 5.FIFE-500 CONTROL PANELAUTOSETUP SCREEN1.Place the web/strip in the proper position and then position the sensor(s) toalign the center of the sensor(s) bandwidth with the edge of the web/strip to beguided.2.Verify the system is in Manual Mode by pressing the MANUAL button. Refer toFigure 1 on page 2-1.Continued next pageAuto setup3. Perform Auto Setup to automatically determine the proper polarity and gain forthe system. If two sensors are being used, Auto Setup must be performed independently, in each sensor mode. Refer to Figure 3 on page 3-1 for button locations.a. Select the desired sensor mode by pressing the SENSOR SELECTIONbutton.b.Press the SETUP button to enter the Setup menus.c. Press the AUTOSETUP icon to enter the AUTOSETUP menu.d. Position the web edge near the center of the sensor proportionalband as indicated in Figure 5 on previous page.e.Press the Autosetup button to start. The guide will move a shortdistance and indicate the result as shown in Figure 6 below.Figure 6.FIFE-500 CONTROL PANELSUCCESSFUL AUTOSETUP COMPLETION4. Press the ACCEPT button to save the setting.5. Press the BACK or HOME button to return to the Operator Level Screen.6. Repeat this procedure for each sensor mode that will be used.7. Switch the system to Automatic Mode by pressing the AUTO button. This initiates the guiding function of the system. Once this procedure has been performed for each sensor mode, it does not need to be repeated.Optional manual configurationFigure 7.FIFE-500 CONTROL PANELSYSTEM GAIN SETUP SCREENSetting the gain1.Press the SETUP button to enter the Setup menus.2.Press the GAIN icon to enter the Gain menu.e the + and - ARROW buttons, or use the slider control to adjust the Gainto the desired level. (The display indicates the sensor signal stability toassist in the Gain adjustment).4.Press the ACCEPT (√) button to save the new Gain value.5.Press the BACK or HOME button to return to the Operator Level screen.Optional manual configurationFigure 8.FIFE-500 CONTROL PANEL GUIDEPOINT SETUP SCREENSChanging the guidepoint while in automatic or manual modeThe arrow controls shift the Guidepoint within the active sensor bandwidth.Press the center button near the bar graph to reset the Guidepoint to the default of 50%.Note: If the Guidepoint is changed while in Automatic Mode, the change is effectiveimmediately, but if the Guidepoint is changed while in Manual Mode or Servo-Center modes, the change is effective when Automatic Mode is initiated.NORTH, CENTRAL AND SOUTH AMERICATel +1.405.755.1600Fax +1.405.755.8425*********************EUROPE, MIDDLE EASTAND AFRICATel +49.6195.7002.0 Fax +49.6195.7002.933****************www.maxcess.euCHINATel +86.756.881.9398 Fax +86.756.881.9393 ********************.cn INDIATel +91.22.27602633 Fax +91.22.27602634 *********************www.maxcess.inJAPANTel +81.43.421.1622 Fax +81.43.421.2895 *********************www.maxcess.jpKOREA, TAIWAN, AND SE ASIATel +65.9620.3883 Fax +65.6235.4818 ********************© 2013 Maxcess。
创新CREATIVE INSPIRE T3200 quick Quick Start Guide说明书
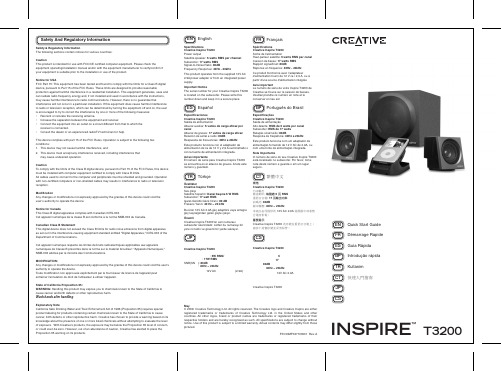
This device complies with part 15 of the FCC Rules. Operation is subject to the following two conditions: 1. This device may not cause harmful interference, and 2. This device must accept any interference received, including interference that
Modification Any changes or modifications not expressly approved by the grantee of this device could void the user’s authority to operate the device.
Notice for Canada This Class B digital apparatus complies with Canadian ICES-003. Cet appareil numérique de la classe B est conforme à la norme NMB-003 du Canada.
may cause undesired operation.
Caution To comply with the limits of the Class B digital device, pursuant to Part 15 of the FCC Rules, this device must be installed with computer equipment certified to comply with Class B limits. All cables used to connect to the computer and peripherals must be shielded and grounded. Operation with non-certified computers or non-shielded cables may results in interference to radio or television reception.
Quick Start Guide 快速入门指南说明书

40mm screws
3mm nuts
3. Propellers
The wings silver spinners spin clockwise and the pylons black spinners spin counter-clockwise. a) Unscrew the spinner and place the 10x5 props on the main wing motors, and the 10x5R on the pylon motors. b) Tighten the spinner by holding the motor still and spinning the spinner into place. Tighten firmly with fingers.
safety switch
c) (Ai Only) Ensure that the craft has a GPS signal by checking for a blue light inside the compass unit. d) Arm the motors by holding the throttle down and right.
*Always fly at locations that are clear of building and other obstacles. *DO NOT fly above or near large crowds. *Avoid flying at altitudes above 400 ft. *Be very careful when flying 19,600 ft. or more above sea level. *Fly in moderate weather conditions with temperatures between 32° F to 104° F.
TC21快速入门指南说明书
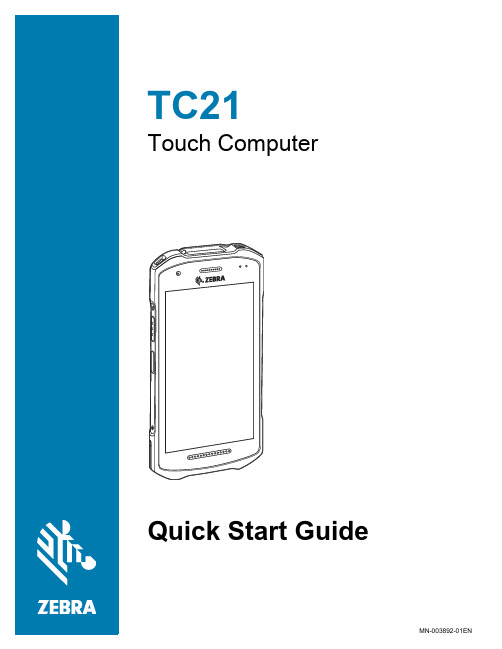
TC21Touch ComputerQuick Start GuideCopyrightZEBRA and the stylized Zebra head are trademarks of Zebra Technologies Corporation, registered in manyjurisdictions worldwide. All other trademarks are the property of their respective owners. ©2020 ZebraTechnologies Corporation and/or its affiliates. All rights reserved.COPYRIGHTS & TRADEMARKS: For complete copyright and trademark information, go to/copyright.WARRANTY: For complete warranty information, go to /warranty.END USER LICENSE AGREEMENT: For complete EULA information, go to /eula. Terms of Use•Proprietary StatementThis manual contains proprietary information of Zebra Technologies Corporation and its subsidiaries(“Zebra Technologies”). It is intended solely for the information and use of parties operating and maintainingthe equipment described herein. Such proprietary information may not be used, reproduced, or disclosed toany other parties for any other purpose without the express, written permission of Zebra Technologies.•Product ImprovementsContinuous improvement of products is a policy of Zebra Technologies. All specifications and designs aresubject to change without notice.•Liability DisclaimerZebra Technologies takes steps to ensure that its published Engineering specifications and manuals arecorrect; however, errors do occur. Zebra Technologies reserves the right to correct any such errors anddisclaims liability resulting therefrom.•Limitation of LiabilityIn no event shall Zebra Technologies or anyone else involved in the creation, production, or delivery of theaccompanying product (including hardware and software) be liable for any damages whatsoever (including,without limitation, consequential damages including loss of business profits, business interruption, or loss ofbusiness information) arising out of the use of, the results of use of, or inability to use such product, even ifZebra Technologies has been advised of the possibility of such damages. Some jurisdictions do not allowthe exclusion or limitation of incidental or consequential damages, so the above limitation or exclusion maynot apply to you.Unpacking1.Carefully remove all protective material from the device and save the shipping container for later storageand shipping.2.Verify that the following were received:•Touch computer•PowerPrecision Lithium-ion battery•Regulatory Guide.3.Inspect the equipment for damage. If any equipment is missing or damaged, contact the Global CustomerSupport center immediately.4.Prior to using the device for the first time, remove the protective shipping film that covers the scan window,display and camera window.FeaturesFigure 1 Front ViewTable 1 Front View FeaturesNumber Item Function1Front Camera Takes photos and videos (available on some models).2Receiver Use for audio playback in Handset mode.3Proximity/Light Sensor Determines proximity for turning off display when in handset mode.Determines ambient light for controlling display backlight intensity.4Data Capture LED Indicates data capture status.Figure 2 Rear View5Charging/Notification LED Indicates battery charging status while charging and application generated notifications.6Touch Screen Displays all information needed to operate the device.7SpeakerProvides audio output for video and music playback. Provides audio in speakerphone mode.8USB-C Connector Provides USB host and client communications, and device charging via cables and accessories.9Microphone Use for communications in Handset mode.10PTT Button Initiates push-to-talk communications (programmable).11Scan ButtonInitiates data capture (programmable).Table 2 Back View Features 12NFC AntennaProvides communication with other NFC-enabled devices.13Basic Hand Strap Mount Provides mounting point for Basic Hand Strap accessory.14Battery Release LatchesPress to remove the battery.15161317141819202113142212Setting Up the DeviceTo start using the device for the first time.1.Install a micro secure digital (SD) card (optional).2.Install hand strap (optional).3.Install the battery.4.Charge the device.5.Power on the device.Installing a microSD CardThe microSD card slot provides secondary non-volatile storage. The slot is located under the battery pack. Refer to the documentation provided with the card for more information, and follow the manufacturer’s recommendations for use.CAUTION : Follow proper electrostatic discharge (ESD) precautions to avoid damaging the microSD card. Proper ESD pre -cautions include, but are not limited to, working on an ESD mat and ensuring that the operator is properly grounded.15BatteryStandard - 3,300 mAh (typical) / 3,100 mAh (minimum) PowerPrecision Lithium-ion BatteryExtended - 5,400 mAh (typical) / 5,400 mAh (minimum), PowerPrecision Lithium-ion Battery.16Volume Up/Down Button Increase and decrease audio volume (programmable).17Scan Button Initiates data capture (programmable).18Camera Flash Provides illumination for the camera.19Rear Camera Takes photos and videos.20Power Button Turns the display on and off. Press and hold to reset the device or power off.21Exit Window Provides data capture using the imager.22MicrophoneUse for communications in Speakerphone mode.1.Lift the access door.Figure 3 Lift Access Door2.Slide the microSD card holder to the unlock position. Figure 4 Unlock microSD Card Holder3.Lift the microSD card holder.Figure 5 Lift the microSD Card Holder4.Insert the microSD card into the card holder door ensuring that the card slides into the holding tabs on eachside of the door.Figure 6 Insert microSD Card in Holder5.Close the microSD card holder and slide into the lock position.Figure 7 Re-install Access DoorCAUTION: Access door must be replaced and securely seated to ensure proper device sealing.6.Re-install the access door.Figure 8 Replace Access DoorInstalling the BatteryNOTE: User modification of the device, particularly in the battery well, such as labels, asset tags, engravings, stickers, etc., may compromise the intended performance of the device or accessories. Performance levels such as sealing (Ingress Pro-tection (IP)), impact performance (drop and tumble), functionality, temperature resistance, etc. could be effected. DO NOT put any labels, asset tags, engravings, stickers, etc. in the battery well.1.Insert the battery, bottom first, into the battery compartment in the back of the device.Figure 9 Insert Bottom of Battery into Battery Compartment2.Press the battery down into the battery compartment until the battery release latches snap into place.Charging the DeviceCAUTION: Ensure that you follow the guidelines for battery safety described in the device Product Reference Guide.Use one of the following accessories to charge the device and/or spare battery.Table 3 Accessories1-Slot Charge Only Cradle CRD-TC2Y-BS1CO-01Provides device charging only. RequiresUSB-C cable (CBL-TC5X-USBC2A-01) andpower supply (PWR-WUA5V12W0xx).1-Slot USB/Ethernet Cradle CRD-TC2Y-SE1ET-01Provides device charging and communication,and charging for Extended Power Pack.Requires power supply(PWR-BGA12V50W0WW), DC line cord(CBL-DC-388A1-01), and country-specific ACline cord.4-Slot Charge Only Cradle with Battery Charger Kit CRD-TC2Y-BS54B-01Charges up to four devices and four sparebatteries. Requires power supply(PWR-BGA12V108W0WW), DC line cord(CBL-DC-381A1-01), and country-specific ACline cord.5-Slot Charge Only Cradle CRD-TC2Y-BS5CO-01Charges up to five devices. Charges up tofour devices and four spare batteries.Requires power supply(PWR-BGA12V108W0WW), DC line cord(CBL-DC-381A1-01), and country-specific ACline cord.5-Slot Ethernet Cradle CRD-TC2Y-SE5ET-01Provides device charging and providesEthernet communication for up to fivedevices. Requires power supply(PWR-BGA12V108W0WW), DC line cord(CBL-DC-381A1-01), and country-specific ACline cord.4-Slot Battery Charger SAC-TC2Y-4SCHG-01Charges up to four battery packs. Requirespower supply (PWR-BGA12V50W0WW), DCline cord (CBL-DC-388A1-01), andcountry-specific AC line cord.Cigarette Light Adapter Auto Charge Cable CHG-AUTO-USB1-01Provides power to the device from a cigarettelighter socket. Requires USB-C cable(CBL-TC5X-USBC2A-01).USB-C Communication and Charge Cable CBL-TC5X-USBC2A-01Provides UBC-A to USB-C communicationand power to the device.Micro USB Communication Cable 25-124330-01R Provides USB communication for the 1-SlotUSB/Ethernet Cradle and the USB/EthernetModule.Main Battery ChargingTo charge a device:1.Insert the device into a slot to begin charging.2.Ensure the device is seated properly.The device’s Charging/Notification LED indicates the status of the battery charging in the device. The 3,220 mAh (typical) standard battery charges from fully depleted to 90% in approximately 2.5 hours and from fully depleted to 100% in approximately three hours. The 5,260 mAh (typical) extended battery charges from fully depleted to 90% in approximately four hours and from fully depleted to 100% in approximately five hours.NOTE: In many cases the 90% charge provides plenty of charge for daily use.To achieve the best fast charging results use only Zebra charging accessories and batteries. Charge batteries at room temperature with the device in sleep mode.Spare Battery ChargingTo charge a spare battery:1.Insert the battery into a battery charging well.2.Gently press down on the battery to ensure proper contact.The Spare Battery Charging LED on the cup indicates the status of the spare battery charging. The 3,220 mAh (typical) standard battery charges from fully depleted to 90% in approximately 2.5 hours and from fullydepleted to 100% in approximately three hours. The 5,260 mAh (typical) extended battery charges from fully depleted to 90% in approximately four hours and from fully depleted to 100% in approximately five hours.Table 4 Charging/Notification LED Charging IndicatorsOffDevice is not charging. Device is not inserted correctly in the cradle or connected to a power source. Charger/cradle is not powered.Slow Blinking Amber (1 blink every 4 seconds)Device is charging.Slow Blinking Red (1 blink every 4 seconds)Device is charging but the battery is at end of useful life.Solid Green Charging complete.Solid RedCharging complete but the battery is at end of useful life.Fast Blinking Amber (2 blinks/second)Charging error, for example:•Temperature is too low or too high.•Charging has gone on too long without completion (typicallyeight hours).Fast Blinking Red (2 blinks/second)Charging error but the battery is at end of useful life., for example:•Temperature is too low or too high.•Charging has gone on too long without completion (typicallyeight hours).NOTE: In many cases the 90% charge provides plenty of charge for daily use.To achieve the best fast charging results use only Zebra charging accessories and batteries.Table 5 Spare Battery LED Charging IndicatorsSolid Amber Spare battery is charging.Solid Green Spare battery charging is complete.Solid Red Spare battery is charging and battery is at the end of useful life.Charging complete and battery is at the end of useful life.Fast Blinking Red (2 blinks/second)Error in charging; check placement of spare battery and batteryis at the end of useful life.Off No spare battery in slot. Spare battery not placed in slotcorrectly. Cradle is not powered.Charging TemperatureCharge batteries in temperatures from 0°C to 40°C (32°F to 104°F). The device or cradle always performs battery charging in a safe and intelligent manner. At higher temperatures (for example: approximately +37°C (+98°F)) the device or cradle may for small periods of time alternately enable and disable battery charging to keep the battery at acceptable temperatures. The device and cradle indicates when charging is disabled due to abnormal temperatures via its LED.1-Slot Charge Only CradleFigure 10 1–Slot Charge Only Cradle1231-Slot USB/Ethernet CradleFigure 11 1–Slot USB/Ethernet Cradle SetupTable 6 1-Slot Charge Only Cradle Features 1Power Supply 2USB-C Cable 3USB-C PortTable 7 1-Slot USB/Ethernet Cradle Features Item1DC Line Cord 2Power Supply 3AC Line Cord 4USB micro-AB Port 5USB micro-B Connector 6USB-A Connector3152464-Slot Charge Only Cradle with Battery ChargerFigure 12 4-Slot Charge Only Cradle with Battery ChargerTable 8 4-Slot Charge Only Cradle with Battery Charger Features Item1Spare Battery Charging LED 2Device Charging Slot 3Spare Battery Slot 4Power LED14325-Slot Charge Only CradleFigure 13 5-Slot Charge Only CradleTable 9 5-Slot Charge Only Cradle Features Item1Device Charging Slot 2Power LED21Figure 14 5-Slot Ethernet CradleTable 10 5-Slot Ethernet Cradle Features Item1Device Charging Slot 21000 LED 3100/100 LED213Figure 15 4-Slot Battery ChargerUSB cableThe USB cable plugs into the bottom of the device. When attached to the device the cable allows charging, transferring data to a host computer, and connecting USB peripherals.Table 11 4-Slot Battery Charger Features 1Battery Slot2Battery Charging LED 3Power LED213Figure 16 USB cableFigure 17 Imager Scanning3.Press and hold the scan button.The red laser aiming pattern turns on to assist in aiming.NOTE: When the device is in Picklist mode, the imager does not decode the barcode until the crosshair or aiming dot touches the barcode.4.Ensure the barcode is within the area formed by the crosshairs in the aiming pattern. The aiming dotincreases visibility in bright lighting conditions.Figure 18 Aiming PatternFigure 19 Pick List Mode with Multiple Barcodes5.The Data Capture LED lights green and a beep sounds, by default, to indicate the barcode was decodedsuccessfully.6.Release the scan button.NOTE: Imager decoding usually occurs instantaneously. The device repeats the steps required to take a digital picture (im-age) of a poor or difficult barcode as long as the scan button remains pressed.7.The barcode content data displays in the text field.Ergonomic ConsiderationsCAUTION: Avoid extreme wrist angles.。
DEMO9S12PFAME 快速入门指南 Rev. 1.0说明书
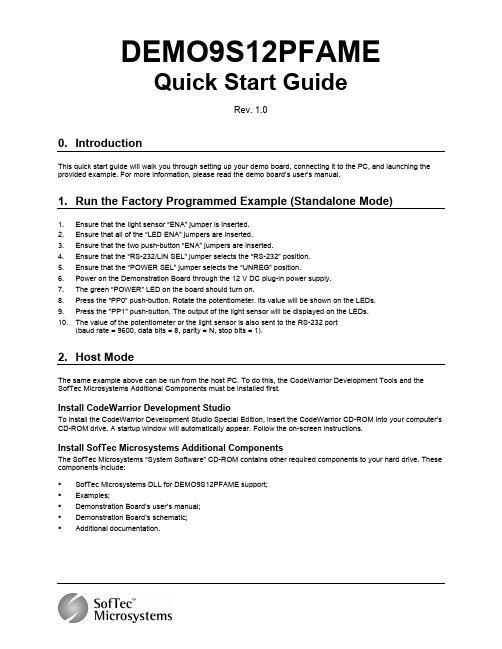
DEMO9S12PFAMEQuick Start GuideRev. 1.00. IntroductionThis quick start guide will walk you through setting up your demo board, connecting it to the PC, and launching the provided example. For more information, please read the demo board’s user’s manual.1. Run the Factory Programmed Example (Standalone Mode)1. Ensure that the light sensor “ENA” jumper is inserted.2. Ensure that all of the “LED ENA” jumpers are inserted.3. Ensure that the two push-button “ENA” jumpers are inserted.4. Ensure that the “RS-232/LIN SEL” jumper selects the “RS-232” position.5. Ensure that the “POWER SEL” jumper selects the “UNREG” position.6. Power on the Demonstration Board through the 12 V DC plug-in power supply.7. The green “POWER” LED on the board should turn on.8. Press the “PP0” push-button. Rotate the potentiometer. Its value will be shown on the LEDs.9. Press the "PP1" push-button. The output of the light sensor will be displayed on the LEDs.10. The value of the potentiometer or the light sensor is also sent to the RS-232 port(baud rate = 9600, data bits = 8, parity = N, stop bits = 1).2. Host ModeThe same example above can be run from the host PC. To do this, the CodeWarrior Development Tools and the SofTec Microsystems Additional Components must be installed first.Install CodeWarrior Development StudioTo install the CodeWarrior Development Studio Special Edition, insert the CodeWarrior CD-ROM into your computer’s CD-ROM drive. A startup window will automatically appear. Follow the on-screen instructions.Install SofTec Microsystems Additional ComponentsThe SofTec Microsystems “System Software” CD-ROM contains other required components to your hard drive. These components include:SofTec Microsystems DLL for DEMO9S12PFAME support;Examples;Demonstration Board’s user’s manual;Demonstration Board’s schematic;Additional documentation.To install the required components, do the following:1. Insert the SofTec Microsystems “System Software” CD-ROM into your computer’s CD-ROM drive. A startupwindow will automatically appear.2. Choose “Install Instrument Software” from the main menu.3. Click on the “Copy SofTec Microsystems DLL to \CodeWarrior for HCS12 V4.7\Prog\gdi” option. An Explorerwindow will open. Copy the “SofTec_BDM12.dll” file to your PC in the “\CodeWarrior for HCS12V4.7\Prog\gdi” folder, relative to the CodeWarrior installation path.4. Click on the “Copy examples for CodeWarrior for HCS12 V.4.7” option. An Explorer window will open. Copythe “DEMO9S12PFAME” folder to your PC, in a location of your choice. These are the examples specific for the demonstration board, and will be used later in the step-by-step tutorial.Note: to install the Additional Components on Windows 2000 or Windows XP, you must log in asAdministrator.First Connection with the PCNote: before to connect the board to the PC, it is important that you install the required system software asdescribed in the previous section.The Evaluation Board connects to a host PC through a USB port. Connection steps are listed below in therecommended flow order:1.Install all the required system software as described in the previous section. 2.Make sure the “POWER SEL” jumper is in the “USB” position. 3.Insert one end of the USB cable into a free USB port. 4.Insert the other end of the USB cable into the USB connector on the Demonstration Board. 5. The first time the Demonstration Board is connected to the PC, Windows recognizes the instrument and starts the“Found New Hardware Wizard” procedure, asking you to specify the driver to use for the instrument. Follow the wizard steps, choosing to install the software automatically when requested.The Evaluation Board’s USB driver is now installed on your system.Step-By-Step Tutorial1. Make sure that the “POWER SEL” jumper selects the “USB” position.2. Ensure that the Demonstration Board is connected to the PC (via the USB cable) and that the board is powered.3. Start CodeWarrior by selecting it in the Windows Start menu.4.From the CodeWarrior main menu, choose “File > Open” and choose the“DEMO9S12PFAME\C\Demo\Demo.mcp” file. This is the board example you copied from the SofTecMicrosystems “System Software” CD-ROM.5. Click “Open”. The Project window will open.6. The C code of this example is contained in the “main.c” file. Double click on it to open it.7. From the main menu, choose “Project > Debug”. This will compile the source code, generate an executable fileand download it to the demo board.8. A new debugger environment will open. From the main menu, choose “Run > Start/Continue”. The programwill be executed in real-time.9. From the main menu, choose “Run > Halt”. The program execution will stop. The next instruction to beexecuted is highlighted in the Source window.10. From the main menu, choose “Run > Single Step”. The instruction highlighted in the Source window will beexecuted, and the program execution will be stopped immediately after.11. From the main menu, choose “Run > Start/Continue”. The application will restart from where it was previouslystopped.TrademarksSMH Technologies is the licensee of the SofTec Microsystems trademark.Freescale™ and the Freescale logo are trademarks of Freescale Semiconductor, Inc.Copyright © 2008 SMH Technologies DC10008Microsoft and Windows are trademarks or registered trademarks of Microsoft Corporation.PC is a registered trademark of International Business Machines Corporation.Other products and company names listed are trademarks or trade names of their respective companies.。
ETR-5000快速启动指南说明书

ETR-5000 Quick Start Guide Effective May 2012The purpose of this Quick Start Guide is to guide the User through the essential steps required to commission an ETR-5000. This Quick Start Guide is not a replacement for the complete manual that can be found on the CD shipped with the ETR-5000. For wiring instructions and complete descriptions of the protective functions, please consult the complete instruction manual.This Quick Start Guide was developed using Simulation ETR-5000_V2.0.c and PowerPort-E V 3.3.ETR-5000Quick Start GuideIB02602016ERev. AContentsDescriptionPageSection 1: Navigation..................................3Section 2: Saving Parameters....................5Section 3: Device Setup Using the FrontPanel Soft Keys (7)Section 4: Assigning/Mapping Relay OutputsUsing the Front PanelSoft Keys (15)Section 5: Device Setup UsingPowerPort-E (18)Section 6: Assigning/Mapping Relay OutputsUsing PowerPort-E (24)2 ETR-5000Quick Start GuideCopyright © 2012 by Eaton Corporation. All rights reserved.Specifications and information contained herein are subject to change without notice.EATON CORPORATION - CONFIDENTIAL AND PROPRIETARY NOTICE TO PERSONS RECEIVING THIS DOCUMENTAND/OR TECHNICAL INFORMATIONTHIS DOCUMENT, INCLUDING THE DRAWING AND INFORMATION CONTAINED THEREON, IS CONFIDENTIAL AND IS THE EXCLUSIVE PROPERTY OF EATON CORPORATION, AND IS MERELY ON LOAN AND SUBJECT TO RECALL BY EATON AT ANY TIME. BY TAKING POSSESSION OF THIS DOCUMENT, THE RECIPIENT ACKNOWLEDGES AND AGREES THAT THIS DOCUMENT CANNOT BE USED IN ANY MANNER ADVERSE TO THE INTERESTS OF EATON, AND THAT NO PORTION OF THIS DOCUMENT MAY BE COPIED OR OTHERWISE REPRODUCED WITHOUT THE PRIOR WRITTEN CONSENT OF EATON. IN THE CASE OF CONFLICTING CONTRACTUAL PROVISIONS, THIS NOTICE SHALL GOVERN THE STATUS OF THIS DOCUMENT.DISCLAIMER OF WARRANTIES AND LIMITATION OF LIABILITYThe information, recommendations, descriptions, and safety notations in this document are based on Eaton Electrical Inc. and/or Eaton Corporation’s (“Eaton”) experience and judgment and may not cover all contingencies. If further information is required, an Eaton sales office should be consulted.Sale of the product shown in this literature is subject to the terms and conditions outlined in appropriate Eaton selling policies or other contractual agreement between Eaton and the purchaser.THERE ARE NO UNDERSTANDINGS, AGREEMENTS, WARRANTIES, EXPRESSED OR IMPLIED, INCLUDING WARRANTIES OF FITNESS FOR A PARTICULAR PURPOSE OR MERCHANTABILITY, OTHER THAN THOSE SPECIFICALLY SET OUT IN ANY EXISTING CONTRACT BETWEEN THE PARTIES. ANY SUCH CONTRACT STATES THE ENTIRE OBLIGATION OF EATON. THE CONTENTS OF THIS DOCUMENT SHALL NOT BECOME PART OF OR MODIFY ANY CONTRACT BETWEEN THE PARTIES. In no event will Eaton be responsible to the purchaser or User in contract, in tort (including negligence), strict liability, or otherwise for any special, indirect, incidental, or consequential damage or loss whatsoever, including but not limited to damage or loss of use of equipment, plant or power system, cost of capital, loss of power, additional expenses in the use of existing power facilities, or claims against the purchaser or User by its customers resulting from the use of the information, recommendations, and descriptions contained herein.ETR-5000 Quick Start GuideETR-5000 Quick Start Guide Effective May 20123Section 1: Navigation1.1 Basic NavigationNavigation through the ETR-5000 menus and settings is easily accomplished using the soft keys on the ETR-5000 control panel and their corresponding functions that appear near the bottom of the LED display (see Figure 1).Figure 1. ETR-5000 Basic Navigation.To select a function that appears in the function area, press the soft key that is directly under that function.Once the Menu soft key is pressed, the ETR-5000 utilizes arrows and tools that appear in the function area of the display and correspond to the soft keys directly below (see Figure 2). Table 1 gives a summary of the arrows and tools that may appear in the function area and a brief description of each.Figure 2.Arrows and Tools in the Function Area.ETR-5000 Quick Start Guide4Table 1. Arrows and Tools That Can Appear in the Function Area of the Display.Arrow/Tool DescriptionThe “Up” arrow scrolls up through the current menu.The “Down” scrolls down through the current menu.The ”Left” arrow takes the User one step back to the previous menu.The “Right” arrow takes the User to the next sub-menu.The “Top of List” arrow takes the User directly to the top of the current menu list.The “Bottom of List” arrow takes the User directly to the bottom of the current menu list.The “Increase” icon will increase the active digit by one.The “Decrease” icon will decrease the active digit by one.The “Left Movement” arrow will take the User one digit to the left in a value.The “Right Movement” arrow will take the User one digit to the right in a value.The “Wrench” icon will give the User access to the parameter setting mode for a function.The “Delete” icon allows the User to delete data or a value.1.2 Password EntryBefore any parameter of the ETR-5000 can be changed, the User must enter a valid password using the soft keys on the control panel. A password must be a user-defined, four digit combination of the numbers 1, 2, 3, and 4 (examples: 1224 or 2341).Note: A default password (1234) was set at the factory. If the password has been changed, contact your SystemAdministrator for the new password.To enter the password, simply press the soft keys corresponding with the numbers appearing in the function area near the bottom of the LED display. An asterisk (*) will appear in the display as each number is entered.Press the “OK” soft key after the password has been entered.Figure 3. Entering the Password.ETR-5000 Quick Start GuideETR-5000 Quick Start GuideEffective May 20125Section 2: Saving ParametersWhen the User makes changes to the parameters, the ETR-5000 DOES NOT automatically save the changes. Changes MUST BE explicitly saved by the User. There are two ways changes can be saved: saving individual changes or saving multiple changes. 2.1 Making and Saving Parameter Changes1. Use the soft keys under the display to access the parameter to be changed.2. Press the soft key under the wrench icon then enter the password.Figure 4.The Wrench Icon.3. Use the soft keys to change the parameter then press the soft key under “OK”. An asterisk appears in thedisplay indicating a parameter has been changed.Figure 5. The “OK” Soft Key and the Asterisk Denoting a Parameter Change.6 ETR-5000Quick Start GuideNote:If the User wishes to change multiple parameters, please skip to Step 5. If the User wishes to save the individual parameter made at this time, complete Step 4 then end the process.4. Press the “Ok” key. Then press the soft key under “Yes” to save the new value.To Make and Save Multiple Parameter ChangesNote:The ETR-5000 utilizes a timeout function. If the timeout time has expired, the User may be asked to re-enter the password.5. Use the soft keys to access and change the other parameters to be changed then press the soft key under“OK” after each change. An asterisk appears in the display indicating a parameter has been changed but not saved. Likewise, an asterisk next to a higher-level parameter menu implies that one of its constituent parameters has been modified but not saved.6. Once all the parameters have been changed, press the “Ok” key. Then press the soft key under “Yes” tosave the new values.ETR-5000 Quick Start GuideETR-5000 Quick Start Guide Effective May 20127Section 3:Device Setup Using the Front Panel Soft KeysWhen the ETR-5000 is first powered up, the protective elements listed in Table 2 are enabled in each setting group.Table 2. Default Protective Elements Enabled at Startup.Protective Element DescriptionWinding Assignment I-Prot 50P[1] DEFT Overcurrent Protection Wdg. 1 51P[1] INV Overcurrent Protection Wdg. 1 51P[3] INV Overcurrent Protection Wdg. 2 51X[2] INV Measured Ground Fault Protection Wdg. 2 50R[2] DEFT Calculated Ground Fault Protection Wdg. 2 51R[2] INV Calculated Ground Fault Protection Wdg. 2 51Q[1] Negative Sequence Overcurrent Protection Wdg. 1 51Q[2] Negative Sequence Overcurrent Protection Wdg. 2Tdiff-Prot87 Differential Protection N.A. 87H Unrestrained High Set Differential Current ProtectionN.A.Press the soft key under “Menu” to access the“Operation” screen.ETR-5000Quick Start Guide8From within the “Operation” screen, press the soft key under the down arrow to access the next parameter screen “System Para” (System Parameters).From the “System Para” screen, press the soft key under the right arrow to access the “System Para” menu.From the “System Para” menu, press the soft key under the right arrow to access the “General Settings” Configuration menu.ETR-5000 Quick Start GuideETR-5000 Quick Start Guide Effective May 20129To edit anyparameter, use the soft keys under the up or down arrows to highlight the parameter then press the soft key under the wrench icon. To edit parameters, the User must enter a valid password (see Section 1:Password Entry).Enter the four-digit password as described in Section 1:Password Entry. After the password has been entered, press the “Ok” soft key.Note: The ETR-5000 utilizes atimeout function. If the timeout time has expired, the User may be asked to re-enter the password.Select the desired parameter setting then press the “OK” soft key to activate the setting.This same procedure can be used to change any of the system parameters.ETR-5000Quick Start Guide10 Use the soft keys underthe arrows to navigateback to the SystemParameters screen.Select the next System Parameter that you wish to change using the soft keysunder the up and downarrows. The System Parameters that can bechanged are listed inTable 3.Note: Information about programming each System Parameter scrolls alongthe bottom of the LEDscreen for the Parameter selected.Table 3. System Parameters That Can Be Changed.General Settings Transformer VT CTW1 CTW2 DirectionPhase Sequence SN VT Winding Side CT pri CT pri Phase MTA f TrV W1 Main VT pri CT sec CT sec IR Dir Cntrl Program Mode TrV W2 Main VT sec CT dir CT dir IX Dir CntrlProgram Mode Bypass W1 Connection/ GroundingMain VT con XCT pri XCT pri 3V0 SourceTemperature Unit W2 Connection/ GroundingVX Winding Side XCT sec XCT sec Ground MTA Phase Shift Aux VT pri XCT dir XCT dirTap Changer Aux VT secThe procedures that follow demonstrate how to set some of the basic System Parameters.From the General Settings menu, select Phase Sequence then press the soft key under the wrench icon.Note: The ETR-5000 utilizes atimeout function. If the timeout time has expired, the User may be asked to re-enter the password.Select the desired Phase Sequence parameter setting using the soft keys under the up and down arrows. Press the soft key under “Ok”. Save the selected parameter (see Section 2 – Saving Parameters).The User may change thefrequency or, if the frequency iscorrect, use the soft keys under the up or down arrows to access additional system parameters.From the System Parameters menu, select the “CT W1” and “CT W2” (CT Winding 1” and “CT Winding 2) settings using the soft keys. When the appropriateparameter has have been selected, follow the same procedure tochange the settings: wrench ->select/change value -> soft key under “Ok”.Press the “Ok” key. Save the selected parameter (see Section 2 – Saving Parameters).The CT pri (primary external CT settings), CT sec (secondary external CT settings), and XCT (ground / neutral CT settings) should all be set using similar steps. When all the CT settings have been selected and saved, select the soft key under the left arrow to return to the “System Para” level.Use the soft keys under the left, up, and down arrows to reach the “Protection Para” (Protection Parameter) screen. To set the protection parameters, use the soft key under the right arrow to enter the “Protection Para” menu.Use the soft key under the down arrow to highlight Set 1.Use the soft key under the right arrow to enter the Set 1 setting group. Set 1 is the only active setting group when the ETR-5000 is first powered up.To program current protection, press the soft key under the right arrow while “Tdiff-Prot” is highlighted. This will display a list of current protection settings under “Tdiff-Prot.”Press the soft key under the right arrow to enter the settings area for 87. After choosing the applicable setting, press the “Ok” soft key to activate the selection.Congratulations! You have successfully setup the device using the front panel soft keys.Section 4: Assigning/Mapping Relay Outputs Using the Front Panel Soft KeysPress the soft key under “Menu”.Use the up and down arrow soft keys to access the “Device Parameters” screen. Then press the soft key under the right arrow to access the Device Parameters menu.Use the up and down arrow soft keys until “Relay Outputs” is highlighted. Then press the soft key under the right arrow to access the Relay Outputs menu.Use the up and down arrow soft keys to select the appropriate Relay Card then press the soft key under the right arrow.Use the up and down arrow soft keys to select the appropriate Relay then press the soft key under the right arrow.The Relay is set to operate for all protective functions “Bkr.TripCmd”. The User can change this setting by pressing the soft key under the “Wrench” icon.To edit parameters, the User must entera valid password (see Section 1: Password Entry).To block a protective function from operating the“Bkr.TripCmd”, activate the block function under the active setting group.In order to trip an output relay for a particular function, select “27M[1].Trip”. DO NOT select“27M[1].TripCmd” as this signal can be blocked.Once the assignments and settings are made, press the “OK” soft key twice then select the soft key under “Save” to save the settings.Section 5: Device Setup Using PowerPort-EWhen programming the unit throughPowerPort-E, start from an existing ordefault parameter file, or create a newparameter file. To create a new parameterfile, select “Create New Parameter File”from the pull-down menu as shown on theleft. This will lead to the dialog box shownbelow left.Select the device from the pull-down menuto load the default parameter file.Make sure the PowerPort-E Configurationmatches the Device Configuration andoptions ordered with the ETR-5000. If theconfiguration does not match, double clickon the option and select the setting thatmatches the device. Repeat the processuntil the PowerPort-E Configurationmatches the Device Configuration.Note: If the Device Configuration in setPowerPort-E does not match the device,PowerPort-E WILL NOT be able todownload files to the device.A parameter file can also be loaded from a connected device by selecting “Receive Data from Device” from the “Device” pull-down menu.Note that to load parameters from the device the User may need to set up the connection to the device through the “Settings -> Connection Settings” pull-down menu.The upper left portion of the PowerPort-E screen should now display:•Operation;•System Para (Parameters); •Protection Para (Parameters); •Device Para (Parameters);•SysA (System Alarms);•Control;•Logic;•Device Planning; and•Service.First, set up the System Parameters by double clicking on the “System Para” then “General Settings” as highlighted to the left. This will result in the dialog box shown. When the User double clicks on a parameter within the dialog box, an interface appears that will allow the parameters to be modified. For example, to modify the Phase Sequence System Parameter, double click “Phase Sequence.” This will result in the dialog box displayed to the left. The pull-down menu will allow the User to change the Phase Sequence setting. Note that although the value has been changed, it has NOT yet been saved.The “Previous” and “Next” buttons can be used to display the Previous and Next parameters within the System Parameter list.AsterisksFrom within the “87” dialog box, double click the parameter “t-Trans” to bring up the “Time of Temporary Restriction delay” dialog box. Set the value using the up and down arrows next to the time setting.As shown in the screen shot to the left, the time was changed from 2 to 3 seconds and, therefore, an asterisk appears next to both the “t-Trans” setting and the higher level “87” menu.To transfer parameters to the device, make the appropriate selection from the “Device” pull-down menu. The User has the option of downloading all settings or only those modified. Note that if settings were not originally uploaded from the device and the User downloads all parameters, then the defaults for the unmodified parameters will overwrite the parameters currently stored in the device. Transferring only modified parameters is the safer option.The pull-down allows for transfer of all parameters (including unmodifiedparameters) to the device. If the User is working with parameters that were notoriginally uploaded from the device, caution should be exercised when using this option.To download the parameters, the User must enter the password (default password is 1234). Note that until a local copy is saved to the User’s computer, the asterisksshowing modified parameters will continue to be displayed.Congratulations! You have successfully setup the device using PowerPort E.Section 6: Assigning/Mapping Relay Outputs Using PowerPort-EEither create a new parameter file or openand existing parameter file for the device(see Section 5 for details). Note that to loadparameters from the device the User mayneed to set up the connection to the devicethrough the “Settings -> ConnectionSettings” pull-down menu (see Section 5 fordetails).The left portion of the PowerPort-E screenshould now display:•Operation;•System Para (Parameters);•Protection Para (Parameters);•Device Para (Parameters)•SysA (System Alarms);•Control:•Logic;•Device Planning; and•Service.Double click on “Device Parameters” then“Relay Outputs”. This will display theavailable relay cards.Click on the “+” next to the appropriate relay card. The relays associated with the relay card will be displayed.Double click on relay to be modified and the Relay Dialog box will appear. When the User double clicks on a parameter within the dialog box, an interface appears that will allow the assignments to be modified.The interface will show that the relay is set to operate for all protective functions“Bkr/Con. TripCmd”. The User can change this setting by clicking on the down arrow and selecting the new assignment.AsterisksIn order to trip an output relay for a particularfunction, select “27M[1]. Trip” for“Assignment 2”. DO NOT select“27M[1].TripCmd” as this signal can beblocked.Once the assignments and settings aremade, click on “OK” to save theassignments and settings.Note: Please refer to Section 5 for information on how to save the modified settings and to upload the changesfrom PowerPort E to the device.Contact InformationPQTSC: 1-800-809-2772Email:*******************Internet:Eaton CorporationElectrical Group1000 Cherrington ParkwayMoon Township, PA 15108United States877-ETN-CARE (877-386-2273) © 2012 Eaton CorporationAll Rights ReservedPrinted in USAPublication No. IB02602016E, Rev. A Style No. 66A2496H01 / TBG000882 May 2012 PowerChain Management is a registered trademark of Eaton Corporation.All Other trademarks are property of their respective owners.。
Hella Gutmann mega macs 66快速启动指南说明书

mega macs66Quick Start Guide en QSMM66V5200EN0917S0Table of Contents mega macs66 Table of Contents1About this Quick Start Guide (4)1.1Reading the Manual (4)2Safety Precautions (5)2.1Safety Precautions–Risk of Injury (5)2.2Safety Precautions for the mega macs66 (6)3Product Description (7)3.1Delivery Contents (7)3.2Intended use (8)3.3Using the Bluetooth Function (9)3.4Scope of Functions (9)3.5Display (9)3.6Connections of the mega macs66 (10)4Installation of the Hella Gutmann Drivers Package (13)4.1System Requirements of Hella Gutmann Drivers (13)4.2Installation of the Hella Gutmann Drivers Package (13)5Putting Into Operation (14)5.1Charging the Battery (14)5.2Switching on the Device (14)5.3License Release (15)5.4Switching Off the Device (15)6Configuring the Device (17)6.1Configuring Interfaces (17)mega macs66Table of Contents7Working with the Device (21)7.1Icons (21)7.2Diagnostics (25)7.3Calling Up Vehicle Information (28)7.4Oscilloscope (28)About this Quick Start Guide mega macs66 Reading the Manual1About this Quick Start GuideThe quick start guide comprises the most important information in aclearly visible form to facilitate the start with the mega macs66.1.1Reading the ManualYou can find the manual with detailed information about the use of yourmega macs66in the device under or on the homepage of HellaGutmann /de/workshop-solutions/diagnose.This page provides the current download versions of the manuals andquick start guides as well as other valuable product leaflets for optionalaccessories and products of Hella Gutmann,which can support you in yourdaily work.mega macs66Safety PrecautionsSafety Precautions–Risk of Injury 2Safety Precautions2.1Safety Precautions–Risk of InjurySafety Precautions mega macs66 Safety Precautions for the mega macs662.2Safety Precautions for the mega macs66mega macs66Product DescriptionDelivery Contents 3Product Description3.1Delivery Contents3.1.1Checking delivery contentsPlease check the delivery contents upon receiving your device so thatcomplaints can be issued immediately regarding any potential damage.Product Description mega macs66 Intended useProceed as follows to check the delivery contents:1.Open the package supplied and check for completeness based on thedelivery slip.Should you identify any damage to the package,then open the packagein the presence of the delivery service and check the device for hiddendamage.Any transport damage to the package supplied and damageto the device shall be registered in a damage report by the deliveryservice.2.Take the device out of the packaging.3.Check the device for mechanical damage and shake it slightly toensure that there are no loose parts inside.3.2Intended useThe mega macs66is a mobile device for detecting and rectifying faults inautomotive electronic systems.The device enables access to extensive technical data such as wiringdiagrams and service data,set values and descriptions of vehicle systems.A lot of this data is transferred to the device directly from the HellaGutmann diagnostic database via online connection.Therefore,the devicemust be permanently online.The device is not suitable for repairing electrical machines and tools orhome electrics.Diagnostic devices from other manufacturers will not besupported.If the device is used in a way not authorized by Hella Gutmann,the safetyof the device may be influenced.mega macs66Product DescriptionUsing the Bluetooth Function The device is intended for industrial use.Outside of industrialenvironments,e.g.in commercial areas or in the center of a town,radiointerference suppression measures may be necessary.3.3Using the Bluetooth FunctionThe terms of use of the Bluetooth function may be restricted or prohibitedthrough law or corresponding legal regulations in certain countries.Pay attention to the provisions in force in the respective country beforeusing the Bluetooth function.3.4Scope of FunctionsThe range of functions of the mega macs66depends on the country,thelicenses acquired,and/or the optionally available hardware.Thisdocumentation may therefore describe functions that are not available onthe individual device.Missing functions can be enabled by acquiring acorresponding license subject to charge and/or additional hardware. 3.5DisplayProduct Description mega macs66 Connections of the mega macs663.5.1Operating the DeviceThe device is equipped with a touch screen display.All menus andfunctions can be selected and/or activated by slightly touching with thestylus or the finger or just by pressing the arrow keys.3.6Connections of the mega macs66mega macs66Product DescriptionConnections of the mega macs66Product Description mega macs66 Connections of the mega macs66mega macs66Installation of the Hella Gutmann Drivers PackageSystem Requirements of Hella Gutmann Drivers 4Installation of the Hella Gutmann Drivers Package 4.1System Requirements of Hella Gutmann Drivers•Microsoft Windows7or higher•Windows administrator rights4.2Installation of the Hella Gutmann Drivers PackageTo obtain all the data about the related vehicle provided by Hella Gutmann,the device requires a permanent online connection and the installed driverpackage Hella Gutmann Drivers.To keep the connection costs down,HellaGutmann recommends a DSL connection and a flat rate.1.Install the Hella Gutmann Drivers on the office or repair shop PC.The driver package Hella Gutmann Drivers program is on the suppliedHGS data carrier.2.Connect the device to a web-compatible PC.Once the connection symbol in the top symbol bar changes fromblack to green,the online connection has been set up successfully andis active.Putting Into Operation mega macs66 Charging the Battery5Putting Into OperationThis section gives a description of how to switch on and off the device aswell as all the necessary steps for the first use of the device.5.1Charging the BatteryPrior to putting the device into operation,charge the battery for at least8to10h(device is switched off meanwhile).Proceed as follows to charge the battery:1.Press in main switch until it locks into place.The electric circuit to the battery is now closed.2.Insert the voltage supply plug into the device's socket.3.Insert the power plug into the plug socket.The battery is charged.5.2Switching on the DeviceTo switch on the device:1.Press in main switch until it locks into place.The device switches to standby mode.2.Lightly touch the display.The general terms and conditions appear.3.Read the general terms and conditions and confirm them at the end ofthe text.A user selection window appears.The respective user name is saved for all data stored in the CarHistory.This enables quicker identification of the mechanic whoperformed the repair work if a query is subsequently made.4.Double-click.mega macs66Putting Into OperationLicense Release5.Enter the user name.6.Confirm your entry with.7.Activate the Stay logged in check box if necessary.If the Stay logged in check box is activated,you will not need to selecta user name when switching on in the future.8.Confirm your entry with.The input is saved automatically.The main menu appears.Now you can start working with the device.5.3License ReleaseProceed as follows to connect the device with the HGS server:1.Select Contracts under>Settings in the main menu.2.Select the>License<tab.3.Retrieve My licences with.Data is downloaded.Purchased licences are displayed.4.Switch the device off and on again.Now you can start working with the device.5.4Switching Off the Device.Proceed as follows to switch off the device:1.Switch off the device with.2.Observe the confirmation prompt.Putting Into Operation mega macs66 Switching Off the Device3.Switch off the device with.Abort the procedure with.After switching off,the device is in standby mode.mega macs66Configuring the DeviceConfiguring Interfaces6Configuring the DeviceConfigure all interfaces and functions under>Settings<in the main menu.6.1Configuring InterfacesSet the interfaces for the printer,BPC-Tool,Ethernet,Bluetooth,WLANand UMTS module here.Configure all interfaces of the device under Settings>Interfaces.If there are several possible connections to devices or tools,the fastestand most stable connection is always preferred.The hierarchy for connection is as follows:1.EthernetB3.Bluetooth4.WLAN6.1.1Configuring the EthernetYour network settings can be made here.Proceed as follows to connect the device to a network(router)via anEthernet interface:1.Insert the Ethernet cable(not included in the delivery contents)into theEthernet port of the device and the remote station.2.Select Interfaces under>Settings in the main menu.3.Select the>Ethernet<tab.4.Open a list under IP address mode with.If>Determine automatically(DHCP)<is set,then the deviceautomatically searches for the IP address.If>Determine manually<is selected,you must enter the address ofthe remote station under mega macs IP address,e.g.192.168.255.255.5.Select>Determine automatically(DHCP)<or>Determinemanually<.The selection will be saved automatically.Configuring the Device mega macs66 Configuring Interfaces6.1.2Configuring the Bluetooth AdapterHere you can configure the Bluetooth adapter.The integrated Bluetooth module enables a wireless connection to a PC onwhich the driver package Hella Gutmann Drivers is installed.Searching for the Bluetooth AdapterProceed as follows to search for the Bluetooth adapter:1.Insert the Bluetooth adapter into the USB port on the PC.2.Select Interfaces under>Settings in the main menu.3.Select the>Bluetooth<tab.4.Activate the check box to make settings.A confirmation prompt appears if WLAN was previously activated inthe device.5.Observe the confirmation prompt.6.Confirm the confirmation prompt with.7.Do this via Search for Bluetooth adapter.8.Observe the information window.9.Confirm the information window with.Connection is established and the search for a Bluetooth adapter is inprogress.Once the connection from the device to the Bluetooth adapter has beenset up successfully,a selection list of the Bluetooth adapters that havebeen found is then displayed.mega macs66Configuring the DeviceConfiguring Interfaces10.Select the desired Bluetooth adapter.The selection will be saved automatically.The automatically assigned Bluetooth adapter address appears in the fieldBluetooth adapter address.6.1.3Searching for and installing a WLAN interfaceProceed as follows to connect the device to a network(router)throughWLAN interface:1.Select Interfaces under>Settings in the main menu.2.Select the>WLAN<tab.3.Activate the check box to make settings.A confirmation prompt appears if either Bluetooth or UMTS waspreviously enabled on the device.4.Observe the confirmation prompt.5.Confirm the confirmation prompt with.6.Open a list under IP address mode with.A drop-down list appears.If>Determine automatically(DHCP)<is set,the device automaticallysearches for the IP address.This option is set ex works.If>Determine manually<is selected,you must enter the address ofthe remote station under mega macs IP address,e.g."192.168.255.255".7.Select>Determine automatically(DHCP)<or>Determinemanually<.The selection will be saved automatically.8.Create wireless network with.The device searches for wireless networks.Once the device has successfully finished searching for wirelessnetworks,a pick list of wireless networks found is displayed.9.Select the required wireless network.10.Regard the window with information and instructions.11.Confirm the info and instructions window with.12.Enter the WLAN password.Configuring the Device mega macs66 Configuring Interfaces13.Confirm the password with.The input is saved automatically.The following message appears if the wireless network has been setup successfully:•the name of the selected wireless network under Wirelessnetwork(SSID)•the security system of the selected wireless network under WLAN security•the IP address of the installed Hella Gutmann Driver underGutmann Portal IP address14.Click the symbol on the right of the header to check the connectionstatus.The device is connected to the Internet if Data server is displayed underConnection and connected under WLAN.You can use the WLAN connection now.mega macs66Working with the DeviceIcons 7Working with the Device7.1Icons7.1.1General SymbolsWorking with the Device mega macs66 Icons7.1.2Symbols in the Main Menumega macs66Working with the DeviceIconsWorking with the Device mega macs66 Icons7.1.3Symbols in the Vehicle Selection Menumega macs66Working with the DeviceDiagnostics7.2Diagnostics7.2.1Preparing Vehicle DiagnosticsThe selection of the correct vehicle is a basic precondition for trouble-freevehicle diagnostics.The device provides assistance to simplify theselection,e.g.indicating the installation position of the diagnostic port orvehicle identification through VIN.The following ECU functions are possible under>Diagnostics<in the mainmenu:•Trouble code reading•Parameter readout•Actuator test•Service reset•Basic setting•Coding•Test functionProceed as follows to prepare vehicle diagnostics:1.Select the desired vehicle under>Vehicle selection<in the mainmenu.2.Select>Diagnostics<in the main menu.Working with the Device mega macs66 Diagnostics3.Take the diagnostic module(DT66)out of the mega macs66.4.Insert the ST2connector into the ST2socket of the DT66.mega macs66Working with the DeviceDiagnostics5.Insert the OBD plug into the vehicle's diagnostic connector and placethe DT66inside the vehicle cabin.6.Select>Diagnostics<in the main menu.Now you can select the type of diagnostics.7.2.2Performing DiagnosticsProceed as follows to perform diagnostics:1.Perform steps1to5as described in section Preparing vehiclediagnostics(Page25).e to select the desired diagnostics under Function,Assemblyand System.3.Observe the information window,note window and instruction windowas applicable.4.Start the communication with.The diagnostic procedure between the device and the DT66takesplace via Bluetooth.The connection to the DT66is established if thesymbol changes from black to green.Working with the Device mega macs66 Calling Up Vehicle Information5.Repair the vehicle.Then delete the saved trouble codes from thevehicle system.7.3Calling Up Vehicle InformationHere you have an overview of the vehicle information including thefollowing:•Car History•Component Help•Service dataProceed as follows to call up vehicle information:1.Select>Vehicle information<in the main menu.2.Select the desired type of information using the symbols.Certain types of information may not be available depending on theselected vehicle.7.4OscilloscopeThe use of measuring technology requires the optionally availablemeasurement module(MT66).The oscilloscope can be used for measuring and/or depicting the followingmeasured variables:•Voltage•Current•Resistance•Temperature•PressureCurrent measurements are allowed exclusively using the clamp meterfrom Hella Gutmann.Depending on the required measurement,differentmeters are to be used.mega macs66Working with the DeviceOscilloscopeA light blue bar in the top toolbar indicates how much of the memoryspace reserved for this purpose in the Car History has been used.If theblue bar is complete,the oldest data is deleted from the Car Historymemory and the free memory is assigned new data.7.4.1Performing oscilloscope measurementsProceed as follows to perform oscilloscope measurements:1.Select>Measurements<in the main menu.2.Select the>Oscilloscope<tab.The window for measured variables and channels appears.3.Plug in the test lead and/or signal cable into the MT66.4.Connect the test lead to the component in question if necessary.5.Where necessary,connect the signal cable to the infrared thermometerof Hella Gutmann or the LPD kit.Working with the Device mega macs66 Oscilloscope6.Should you use the green current clamp(CP40),black current clamp(CP200),or blue current clamp(CP700),then connect it with thearrow pointing towards the battery around all positive cables,or withthe arrow pointing away from the battery around all negative cablesrespectively.7.Activate the check box for the desired measured variable and theoscilloscope channel.8.Confirm the selection with.Measurement will be started.e to set the time and measured variable ranges.The ideal measuring range of the device can alternatively bedetermined automatically with.10.Start Auto Set with>.mega macs66Notes31HELLA GUTMANN SOLUTIONS GMBHAm Krebsbach279241IhringenGERMANYPhone:+4976689900–0Fax:+4976689900–3999**********************©2017HELLA GUTMANN SOLUTIONS GMBH1STUECK/PIECE(S)���������������9XQ460986-341Made in Germany。
Shure WWB Wireless Workbench Quick Start Guide
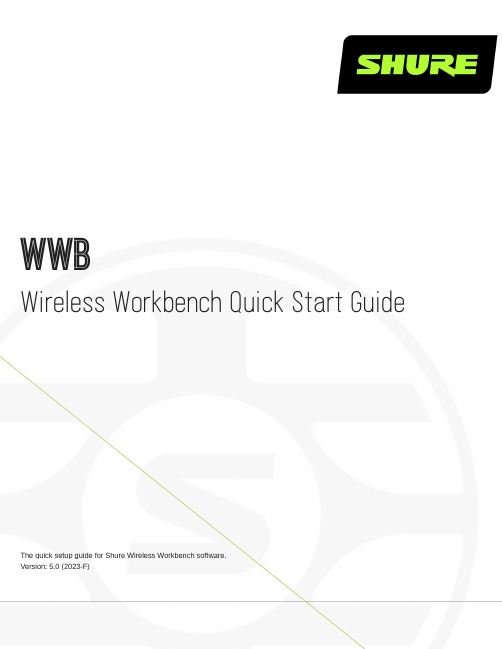
WWBWireless Workbench Quick Start GuideThe quick setup guide for Shure Wireless Workbench software.Version: 5.0 (2023-F)Table of ContentsWWB Wireless Workbench Quick Start Guide3 Overview3 Step 1: Download Wireless Workbench 3 Step 2: Connect Shure devices to your network 3 Automatic IP addressing 4 Manual IP addressing 4 Step 3: Configure the firewall 4 Mac 5Windows 5 Step 4: Open Wireless Workbench 5 Step 5: Verify your network connection 6 Network troubleshooting 6 Step 6: Coordinate frequencies7 Step 7: Set transmitter frequencies using IR sync7 Step 8: Monitor and control your system8 Step 9: Learn more 8••••••••••WWBWireless Workbench Quick Start GuideOverviewWireless Workbench (WWB) is free device management, coordination, and monitoring software that helps RF coordinators, touring, broadcast, theater and house of worship audio professionals manage everything from pre-show planning to frequency coordination, live channel monitoring, and post-performance analysis.Note: This is a quick setup guide for Wireless Workbench. For the full instruction manual, see the Wireless Workbench help page .By bringing together networkable and non-networkable Shure and third-party devices combined with RF data, this software al-lows you to quickly manage and coordinate your wireless devices so you can focus on mixing. Workbench facilitates quick and easy configuration, operation, and monitoring of your wireless devices, and is compatible with the following Shure networked systems:QLX-D Digital Wireless System ULX-D Digital Wireless System Axient Wireless Management Network PSM 1000 Personal Monitoring System UHF-R Wireless System Axient Digital Wireless System SLX-D Digital Wireless System ResourcesFor detailed help with Wireless Workbench, visit the Wireless Workbench Help page . To find the same help content within Wireless Workbench, press F1 or go to Help > Wireless Workbench help system .Other online resources:Workbench release notesWorkbench video tutorialsAnswers to frequently asked questionsStep 1: Download Wireless WorkbenchTo download Wireless Workbench, visit the Wireless Workbench page . Launch the installer and follow the steps to complete the installation.Note: You must be logged in to your computer as an administrator to install Wireless Workbench.®®®®®®®1.2.3.1.2.3.4.Step 2: Connect Shure devices to your networkWireless Workbench communicates with connected devices through an Ethernet network. Each device on the network must have a unique and valid IP address assigned to communicate with other devices on the network. IP addresses can be as-signed automatically by a computer, switch, or router that employs DHCP addressing.Automatic IP addressingTo take advantage of DHCP addressing, Shure devices have an automatic IP mode for quick and easy setup. If specific IP ad-dresses need to be assigned, the IP mode can be set to manual.Connect your computer and devices using CAT5 or better Ethernet cable. For multiple device systems, adding a routeror switch as shown in the diagram is recommended. Avoid using cross-over cables for any connections.Turn on your computer and all devices connected to the network.For each device, enter the network menu and set the IP address mode to Automatic to enable automatic IP addressing.Manual IP addressingAs an alternative to automatic IP addressing, a manual addressing option is available if you want to assign specific IP address-es to your devices.Connect your computer and devices using CAT5 or better Ethernet cable. For multiple device systems, adding a routeror switch as shown in the diagram is recommended. Avoid using cross-over cables for any connections.Turn on your computer and all devices connected to the network.For each device, enter the network menu and set the IP address mode to Manual.Assign unique IP addresses to each device. Assign the identical subnet mask to all devices.Step 3: Configure the firewallIf you have a firewall protecting your computer, you'll need to grant access to Wireless Workbench. Log in to your computer as an administrator to gain full access to your firewall settings or contact your IT administrator for help.For third-party firewall software, refer to the manufacturer's instructions for granting access to each instance of an application (there may be more than one instance).Note: If you receive an alert pop-up that blocks Wireless Workbench, check the boxes to allow access for all networks (Domain Networks, Private Networks, and Public Networks).1.2.3.◦◦1.2.◦◦1.2.MacFrom System Preferences , access firewall settings.If the firewall is on, open the Firewall Options to view the applications that request network access.For each of the following applications, select Automatically allow built-in software to receive incoming connections andAutomatically allow downloaded signed software to receive incoming connections :snetDameonWireless Workbench.appWindowsOpen the Windows Firewall on your computer.Place a check next to each instance of an application--there may be more than one instance--for the following applica-tions to allow access to Domain Networks, Private Networks, and Public Networks:snetDameonwireless workbenchRefer to the Microsoft Support website if you need more help with firewall configuration.Step 4: Open Wireless WorkbenchIn the welcome screen, set up a network connection and choose to create or open a show.Choose a network: Select the network that closely matches the numbering order and format of the IP address yourdevice is connected to. The first few numbers of the address shown in Wireless Workbench will match the first fewnumbers of the device's IP address.Tip: If you're not sure which IP address to choose, go to the network menu on the device to see what IP address it is using. Model-specific instructions for accessing the network menu are available in the hardware user guides, found on the user guide home page .Open an existing show or create a new show. If you create a new show, you are prompted to enter show informationand add devices to your show. Click Closewhen you are finished adding devices.1.2.3.• 1.2.• 1.Step 5: Verify your network connection Once you have selected a network, confirm the connection by looking for the network icon () on the display or front panel ofeach device.Devices connected to the network will automatically appear in the Inventory tab. To verify that your devices are connected:View the device ID, channel name, and other parameters.Click a device icon to flash the front panel of the device for remote identification.Verify that the devices online indicator is green. The number of devices listed should match the number of devices con-nected to the network.Network troubleshootingTry the following solutions for common problems. If the issue you're having doesn't appear here, see the Network Trou-bleshooting topic of the full Wireless Workbench help system .If the network icon doesn't appear on a device's screen:Check all cables and connections.Click the network status indicator and verify that the IP address of the network in your preferences correspondswith the IP addresses of your networked devices.If one of your devices doesn't appear in the Inventory tab:Check IP address to verify that device is on the same network as the computer network. Select Reports >Firmware and Network Summary for a report of the IP addresses of your computer and any discovered devices.2.•1.2.3.4.5.6.Open a terminal and try to ping the IP address of the device (to do this, type "ping" and enter the device's IP ad-dress).If the Device online indicator is gray, click the network status indicator and verify that the IP address of the network in your preferences corresponds with the IP addresses of your networked devices.Step 6: Coordinate frequenciesIn the Frequency coordination tab, you can organize, manage, and calculate frequencies for your system. As part of the coordi-nation, you can analyze the frequencies to make sure they are compatible with all the devices in your system and then deploy them to your devices.Perform a scan. In the scanning sidebar, select devices to scan with and start the scan.Add frequencies to the coordination. In the Add frequencies tab, choose to select frequencies from the inventory.Choose All frequencies from Inventory and click OK to bring frequencies into the coordination workspace.Select Analyze to check the compatibility of the current frequencies.Select Calculate to find compatible frequencies for all unlocked entries.Select Assign and Deploy to preview the assignments of channels and frequencies.Deploy the frequencies to your devices.Step 7: Set transmitter frequencies using IR syncPerforming an IR sync automatically tunes the portable device to the same frequency that was deployed to the networked de-vice. When the IR sync is complete, a wireless audio channel is formed between the two devices.Align the IR sync windows of the portable device and networked device, and then press sync or access the sync menu. Refer to the hardware user guides for details about IR sync for your model of transmitter and receiver.1.2.3.4.5.Step 8: Monitor and control your systemIn the Monitor tab, you can add channel strips and Mini-Timelines to monitor your devices. The properties panel displays RF and audio meters and allow you to adjust parameters in real-time.Add channel strips and a Mini-Timeline by dragging and dropping channels from the right pane. You can also use theStrip and Timeline checkboxes.Right-click a channel strip to see configuration options.Double-click a channel strip to see and change detailed device parameters.Click Auto to update the way your channel strip is arranged. Snap it to the frame or move it freely about the screen.Select the gear icon in the lower-right corner of the screen to customize channel strips.Step 9: Learn moreFor more information and support for Wireless Workbench, see the following resources: Shure Audio Institute - Trainings, educational materials, and other instructional content Wireless Workbench video tutorials on YouTubeWireless Workbench release notesAnswers to frequently asked questions。
维azor S2920w-C0 快速启动指南说明书

VIZIOQUICK START GUIDEModel: S2920w-C0IMPORTANT SAFETY INSTRUCTIONSThis QuickStart GuideRemote Control with Batteries High Definition Sound BarDigital OpticalCableStereo RCA to 3.5mmAudio Cable Coaxial AudioCable Power Adapter2 x Sound Bar Wall Mount BracketsWall Mount Template2 x Wall Mount Screws (Size: M4 x 10)CONTROLS & CONNECTIONSBack of Sound BarPower PortService Port*OPTICAL (4)Digital Optical Audio In DIGITAL (3)Coaxial In SUB OUTSubwoofer OutAUX (1)Analog Audio In AUX (2)Analog Audio In*For use by authorized service center only.FIRST-TIME SETUP*Not all TVs have the audio outputs shown above. To connect the Sound Bar directly to your other devices (Blu-ray player, game system, etc) see your device’s user manual.1AND CONNECT IT TO YOUR TVCHOOSE ONE CABLE:BETTER GOODGOODBETTER3.5MM TO RCA CABLE3.5MM TO RCA CABLEDIGITAL COAXIALCABLE**DIGITAL OPTICALCABLE****When using either of the Digital Inputs, if there is no audio: (A) try setting the TV output to PCM or (B) Connect directly to your Blu-ray/other source, some TVs do not pass through digital audio.BETTERGOODBack of Sound Bar3Connect the Power Adapter to the Sound Bar.Plug the Power Adapterinto a power outlet.2For the best surround sound experience, position the Sound Bar as shown.The Sound Bar should be close to ear level.9Remove the battery coverby gently sliding it awayfrom the remote.10Insert the included batteriesand gently slide the batterycover back into place.11Turn your TV on, then press the Power button on the remote to turn the Sound Bar on.Press the Input button to switch betweenaudio sources. For example, if youconnected your TV to Input 1, set the SoundBar to Input 1.Hardware setup is complete.PowerInputVolume +Press to increase volume.Volume –Press to decrease volume.USING THE REMOTEPreviousPress to return to previous track.(Changes Treble and Bass levels)PowerPress to turn on or off.MutePress to mute/unmute.InputPress to change input source.Enter/Play/PausePress to select an option.Press to play or pause.NextPress to skip to the next track.(Changes Treble and Bass levels)TreblePress to enter treble adjustment mode.BassPress to enter bass adjustment mode.TruVolumePress to enable/disable TruVolume.TruSurround HDPress to enable/disable TruSurround HD.BluetoothPress to enter Bluetooth input. (To enter force pair mode, press and hold for 5 seconds)LED INDICATORSbutton on the remote for five (5) seconds.USING BLUETOOTH MODEYour Sound Bar supports music streaming from smartphones, tablets, and computers with Bluetooth capability. Device compatibility will vary, see your device’s documentation for more information. Once you have paired your source device to the Sound Bar, as long as you stay within range of the Sound Bar, your device should remain paired, even if you change the input on the Sound Bar.Maximizing SignalA Bluetooth signal has a range of up to 30 feet. Keep in mind that Bluetooth is a compressed audio format, so streamed music may lose some integrity when compared to a wired connection.Try the following if your sound quality is less than optimal:• If you hear any break-up or disconnect while streaming music from your device, move the source device closer to the Sound Bar.• Be sure that there are no solid obstructions in the line-of-sight between the Sound Bar and the source device.•Other wireless devices can affect Bluetooth range, including wireless security cameras, wireless videobaby monitors, cordless phones, and microwave ovens. Turning off or moving these devices may improve Bluetooth range.Your Sound Bar is not equipped with a microphone, so it cannot operate as a hands-freedevice for a smartphone.Reduce the volume levels on your device and on the Sound Bar before pressing Play . High volume levels can damage your hearing.ADVANCED SETUPDIGITAL OPTICALCABLE Connect up to four (4) different devices to the Sound Bar (devices shown are examples you can use any device). To listen to a device, change the input source on the Sound Bar.Optical, Coaxial, and 3.5mm cables transmit audio only. If connecting a video device, you will need a separate video connection from the device to your TV .Game Console Network Media Player Tablet/MP3 Player/Laptop3.5mm AUDIOCABLEDIGITAL COAXIALCABLE RCA AUDIO CABLE Back of Sound BarCONNECTING A SUBWOOFERBack of Sound BarRCA Subwoofer Cable*Optional Subwoofer* For best results setting up an optional subwoofer, VIZIO suggests thefollowing procedure:1. Press the BASS button on the remote control to enter bassadjustment mode.2. Use the Previous/Next buttons to adjust the bass level to thecenter position.3. Power Off the Sound Bar and Subwoofer. Connect an RCAcable from the sound bar to the subwoofer.4. Power On the Sound Bar and Subwoofer.5. Manually adjust the SUB gain (Volume) and phase to yourpreference. See your subwoofer’s user manual for moreinformation.6. Use the BASS button on the remote control to adjust thesubwoofer’s output.*RCA subwoofer cable and subwoofer not included.WALL MOUNTING THE SOUND BAR1Back of Sound Bar Wall-MountScrew HolesInsert and tighten two Wall-Mount Screws with a Phillips-headscrewdriver into the Wall-Mount Screw Holes.2Place the included wall mounting template against the wallunder your TV. Mark the four bracket holes using a pencil.The remote isn’t working.• Replace the remote batteries with new ones.• Point the remote directly at the center of the Sound Bar when pressing a button.• If using a Bluetooth connection, some of the buttons on the remote may not be supported by the streaming application. (e.g., Pandora doesn’t support the Back button.)HELP & TROUBLESHOOTING• If using Bluetooth, ensure that the volume on your source device is turned up and that the device is not muted.DO YOU HAVE QUESTIONS?LET US HELP!YOUR PRODUCT INCLUDES FREE LIFETIME TECH SUPPORTPhone:Email:Web:(877) 878-4946 (TOLL-FREE)techsupport@VIZIO .com/support Hours of operation:Monday - Friday: 5 am TO 9 pm (pST) Saturday - Sunday: 8 am TO 4 pm (pST)The VIZIO support team is highly trained and is based in the United States. We can help with:• New Product Setup • Connecting Your Devices • Technical Problems • And MoreWe speak English • Se habla Español • Nous parlons FrançaisVIZIO RECOMMENDSIntroducing the new E-series slim frame design. The VIZIO E-series LED TV is shattering the mold in a way only VIZIO can, with high-quality design and picture at the best value. With a stunningly slim outer frame design – and LED with 1080p Full HD for rich colors and vivid details, this HDTV gives you the best picture at the best value.Available at This Product Sold SeparatelyVIZIO RECOMMENDSThe VIZIO Co-Star™ Stream Player merges live TV and streaming entertainment into one experience, turning any HDTV into the ultimate smart TV. Using the latest version of Google TV™, Co-Star decks out your existing HDTV with apps, full-screen Web browsing and the best in streaming entertainment. And with 1080p Full HD resolution, built-in Wi-Fi, and 3D-readiness, VIZIO Co-Star is the ultimate entertainment upgrade for any high-definition television.Available at This Product Sold SeparatelyON PARTS AND LABORCovers units purchased as new in United States and Puerto Rico OnlyVIZIO provides a warranty to the original purchaser of a new Product against defects in materials and workmanship for a period of one year of non-commercial usage and ninety (90) days of commercial use. If a Product covered by this warranty is determined to be defective within the warranty period, VIZIO will either repair or replace the Product at its sole option and discretion.Toobtainwarrantyservice,contactVIZIOTechnicalSupportviaemail:*******************************************(877.698.4946)from5:00AMto9:00PMMondaythrough Friday and 8:00AM to 4:00PM Saturday and Sunday, Pacific Time, or visit . PRE-AUTHORIZATION MUST BE OBTAINED BEFORE SENDING ANY PRODUCT TO A VIZIO SERVICE CENTER. Proof of purchase in the form of a purchase receipt or copy thereof is required to show that a Product is within the warranty period.Parts and LaborThere will be no charge for parts or labor during the warranty period. Replacement parts and Products may be new or recertified at VIZIO’s option and sole discretion. Replacement parts and Products are warranted for the remaining portion of the original warranty or for ninety (90) days from warranty service or replacement, whichever is greater.Type of ServiceDefective Products must be sent to a VIZIO service center to obtain warranty service. VIZIO is not responsible for transportation costs to the service center, but VIZIO will cover return shipping to the customer. PRE-AUTHORIZATION IS REQUIRED BEFORE SENDING ANY PRODUCT TO A VIZIO SERVICE CENTER FOR WARRANTY SERVICE.Product returns to VIZIO’s service centers must utilize either the original carton box and shipping material or packaging that affords an equal degree of protection. VIZIO Technical Support will provide instructions for packing and shipping the covered Product to the VIZIO service center.Limitations and ExclusionsVIZIO’s one-year limited warranty only covers defects in materials and workmanship. This warranty does not cover, for example: cosmetic damage, normal wear and tear, improper operation, improper voltage supply or power surges, signal issues, damages from shipping, acts of God, any type of customer misuse, modifications or adjustments, as well as installation and set-up issues or any repairs attempted by anyone other than by a VIZIO authorized service center. Products with unreadable or removed serial numbers, or requiring routine maintenance are not covered. This one year limited warranty does not cover Products sold “AS IS”, “FACTORY RECERTIFIED”, or by a non-authorized reseller.THERE ARE NO EXPRESS WARRANTIES OTHER THAN THOSE LISTED OR DESCRIBED ABOVE. ANY IMPLIED WARRANTIES, INCLUDING ANY IMPLIED WARRANTY OF MERCHANTABIL-ITY AND FITNESS FOR A PARTICULAR PURPOSE, SHALL BE LIMITED IN DURATION TO THE PERIOD OF TIME SET FORTH ABOVE. VIZIO’S TOTAL LIABILITY FOR ANY AND ALL LOSSES AND DAMAG ES RESULTING FROM ANY CAUSE WHATSOEVER INCLUDING VIZIO’S NEG LIG ENCE, ALLEG ED DAMAG E, OR DEFECTIVE G OODS, WHETHER SUCH DEFECTS ARE DISCOVERABLE OR LATENT, SHALL IN NO EVENT EXCEED THE PURCHASE PRICE OF THE PRODUCT. VIZIO SHALL NOT BE RESPONSIBLE FOR LOSS OF USE, LOSS OF INFORMATION OR DATA, COMMERCIAL LOSS, LOST REVENUE OR LOST PROFITS, OR OTHER INCIDENTAL OR CONSEQUENTIAL DAMAG ES. SOME STATES DO NOT ALLOW LIMITATIONS ON HOW LONG AN IMPLIED WARRANTY LASTS OR THE EXCLUSION OF INCIDENTAL OR CONSEQUENTIAL DAMAG ES, SO THE ABOVE LIMITATIONS OR EXCLUSIONS MAY NOT APPLY TO YOU. THIS WARRANTY G IVES YOU SPECIFIC LEG AL RIG HTS, AND YOU MAY ALSO HAVE OTHER RIG HTS, WHICH VARY FROM STATE TO STATE. THIS WARRANTY IS SUBJECT TO CHANG E WITHOUT NOTICE. CHECK FOR THE MOST CURRENT VERSION.ONE-YEAR LIMITED WARRANTYSound Bar: 2 x 23/4” High-Efficiency Full-Range Transducers Inputs: 1 x 3.5mm Stereo Audio1 x RCA Stereo Audio1 x Optical (Toslink)1 x Digital Coaxial AudioBluetooth (Wireless)Sound Pressure Level (System):95 dBFrequency Response (System):90 Hz - 19 KHzVoltage:100-240 VAC, 50/60 HzCompliances:UL, C-UL, FCCSPECIFICATIONSFCC Class B Radio Interference Statement NOTE: This equipment has been tested and found to comply with the limits for a Class B digital device, pursuant to Part 15 of the FCC Rules. These limits are designed to provide reasonable protection against harmful interference in a residential installation. This equipment generates, uses and can radiate radio frequency energy, and if not installed and used in accordance with the instructions, may cause harmful interference to radio communications. However, there is no guarantee that interference will not occur in a particular installation. If this equipment does cause harmful interference to radio or television reception, which can be determined by turning the equipment off and on, the user is encouraged to try to correct the interference by one or more of the following measures:1. Reorient or relocate the receiving antenna.2. Increase the separation between the equipment and receiver.3. Connect the equipment into an outlet on a circuit different from that to which the receiver is connected.4. Consult the dealer or an experienced radio/TV technician for help.This device complies with Part 15 of the FCC Rules. Operation is subject to the following two conditions: (1) this device may not cause harmful interference, and (2) this device must accept any interference received, including interference that may cause undesired operation.Notice:1. The changes or modifications not expressly approved by the party responsible for compliance could void the user’s authority to operate the equipment.2. Shielded interface cables and AC power cord, if any, must be used in order to comply with the emission limits.3. The manufacturer is not responsible for any radio or TV interference caused by unauthorized modification to this equipment. It is the responsibilities of the user to correct such interference.RF Exposure Information This device meets the government’s requirements for exposure to radio waves. This device is designed and manufactured not to exceed the emission limits for exposure to radio frequency (RF) energy set by the Federal Communications Commission of the U.S. Government. This device complies with FCC radiation exposure limits set forth for an uncontrolled environment.IC Statement Operation is subject to the following two conditions:1. This device may not cause interference, and2. This device must accept any interference, including interference that may cause undesired operation of the device.IC Radiation Exposure Statement This equipment complies with IC RSS-102 radiation exposure limits set forth for an uncontrolled environment. This equipment should be installed and operated with minimum distance 20cm between the radiator & your body.Disposal and Recycling You must dispose of this product properly, according to local laws and regulations. Because this product contains electronic components and a battery, it must be disposed of separately from household waste. Contact local authorities to learn about disposal and recycling options.Other:Image(s) used under license from LEGAL & COMPLIANCEFor DTS patents, see . Manufactured under license from DTS Licensing Limited. DTS, the Symbol, & DTS and the Symbol together are registered trademarks, and DTS TruSurround is a trademark of DTS, Inc. DTS, Inc. All Rights Reserved.For DTS patents, see . Manufactured under license from DTS Licensing Limited. DTS, the Symbol, & DTS and the Symbol together are registered trademarks, and DTS TruVolume is a trademark of DTS, Inc. © DTS, Inc. All Rights Reserved.This product qualifies for ENERG Y STAR in the “factory default” setting and this is the setting in which power savings will be achieved. Changing the factory default settings or enabling other features will increase power consumption that could exceed the limits necessary to qualify for ENERGY STAR rating.We want to help you save energy.© 2013 VIZIO INC. ALL RIGHTS RESERVED. 130429OC-NC。
Lenovo K5 Note用户指南说明书

Quick Start Guide INE-LX1Your Device at a GlanceBefore you start, let's take a look at your new device.To power on your device, press and hold the power button until the screen turns on.To power off your device, press and hold the power button, and then touch .To restart your device, press and hold the power button, and then touch .Press and hold the power button for 10 or more seconds to forcibly restart your device.Getting StartedDo not insert or remove the SIM card when your deviceis powered on.Ensure that the card is correctly aligned and that thecard tray is level when you insert it into your device.Be careful not to scratch your device or hurt yourselfwhen using the eject pin.Store the eject pin out of the reach of children toprevent accidental swallowing or injury.Do not use cut or modified SIM or microSD cards withyour device as these may not be recognized and coulddamage the card tray (slot).If your SIM card does not match your device, pleasecontact your carrier.Follow the instructions in the following figures to set up your device. Please use the eject pin included.Single-SIM:Dual-SIM:Dual Card Dual Standby Single Pass (dual-SIM devices only)Your device supports only dual card dual standby single pass, which means you cannot use both SIM cards for calls or data services simultaneously.When you are on a call using SIM card 1, SIM card 2 cannot be used to make or answer calls. If someone calls SIM card 2, the caller will hear a voice message similar to "The subscriber you dialed is out of the service area" or "The subscriber you dialed cannot be connected for the moment, please try again later." The actual message will vary by service provider.When you are using SIM card 1's data service, SIM card 2's data service will be disabled.Your device's single pass feature helps reduce power consumption and increase your device's standby time. It is not related to your service provider's network conditions.You can go to Settings > Wireless & networks > Dual SIM settings, and enable Enable call forwarding between SIMs to avoid the conflicts mentioned above.For More InformationIf you encounter any problems while using your device, you can obtain help from the following resources:Go to Tips for function details and usage tips.Visit /en to view device information, frequently asked questions and other information.Visit /en/support for the most up-to-date contact information for your country or region. Go to Settings and touch System > About phone > Legal to view legal information for your product.Go to Settings and touch System > About phone > Legal > Safety information to view safety information for your product.Go to Settings and touch System > About phone > Authentication info to view regulatory information for your product.All pictures and illustrations in this guide, including butnot limited to the device color, size, and display content,are for your reference only. The actual device may vary.Nothing in this guide constitutes a warranty of any kind,express or implied.Safety InformationPlease read all of the safety information carefully before using your device to ensure its safe and proper operation and to learn how to dispose of your device properly.Operation and safetyTo prevent possible hearing damage, do not listen at high volume levels for long periods.Using an unapproved or incompatible power adapter, charger, or battery may damage your device, shorten its lifespan, or cause a fire, explosion, or other hazards.Ideal operating temperatures are 0 °C to 35 °C. Ideal storage temperatures are -20 °C to +45 °C.Pacemaker manufacturers recommend that a minimum distance of 15 cm be maintained between a device and a pacemaker to prevent potential interference with the pacemaker. If using a pacemaker, hold the device on the side opposite the pacemaker and do not carry the device in your front pocket.Keep the device and the battery away from excessive heat and direct sunlight. Do not place them on or in heating devices, such as microwave ovens, stoves, or radiators.Observe local laws and regulations while using the device. To reduce the risk of accidents, do not use your wireless device while driving.While flying in an aircraft or immediately before boarding, only use your device according to instructions provided. Use of a wireless device in an aircraft may disrupt wireless networks, present a hazard to aircraft operation, or be illegal.To prevent damage to your device's parts or internal circuits, do not use it in dusty, smoky, damp, or dirty environments or near magnetic fields.When charging the device, make sure the power adapter is plugged into a socket near the devices and is easily accessible.Unplug the charger from electrical outlets and the device when not in use.Do not use, store or transport the device where flammables or explosives are stored (in a gas station, oil depot, orchemical plant, for example). Using your device in these environments increases the risk of explosion or fire.Dispose of this device, the battery, and accessories according to local regulations. They should not be disposed of in normal household waste. Improper battery use may lead to fire, explosion, or other hazards.Disposal and recycling informationThe crossed-out wheeled-bin symbol on your product, battery, literature or packaging reminds you that all electronic products and batteries must be taken to separate waste collection points at the end of their working lives; they must not be disposed of in the normal waste stream with household garbage. It is the responsibility of the user to dispose of the equipment using a designated collection point or service for separate recycling of waste electrical and electronic equipment (WEEE) and batteries according to local laws.Proper collection and recycling of your equipment helps ensure electrical and electronic equipment (EEE) waste is recycled in a manner that conserves valuable materials and protects human health and the environment, improper handling, accidental breakage, damage, and/or improper recycling at the end of its life may be harmful for health and environment. For more information about where and how to drop off your EEE waste, please contact your local authorities, retailer or household waste disposal service or visit the website http:// /en/.Reduction of hazardous substancesThis device and its electrical accessories are compliant with local applicable rules on the restriction of the use of certain hazardous substances in electrical and electronic equipment, such as EU REACH, RoHS and Batteries (where included) regulations. For declarations of conformity about REACH and RoHS, please visit our web site / certification.EU regulatory conformanceBody worn operationThe device complies with RF specifications when used near your ear or at a distance of 0.50 cm from your body. Ensure that the device accessories, such as a device case and deviceholster, are not composed of metal components. Keep the device away from your body to meet the distance requirement. The highest SAR value reported for this device type when tested at the ear isINE-LX10.79 W/kgINE-LX20.83 W/kgAnd when properly worn on the body isINE-LX1 1.27 W/kgINE-LX20.98 W/kgStatementHereby, Huawei Technologies Co., Ltd. declares that this device INE-LX1 / INE-LX2 is in compliance with the essential requirements and other relevant provisions of Directive2014/53/EU.The most recent and valid version of the DoC (Declaration of Conformity) can be viewed at / certification.This device may be operated in all member states of the EU. Observe national and local regulations where the device is used.This device may be restricted for use, depending on the local network.Restrictions in the 2.4 GHz band:Norway: This subsection does not apply for the geographical area within a radius of 20 km from the centre of Ny-Ålesund. Frequency Bands and Power(a) Frequency bands in which the radio equipment operates: Some bands may not be available in all countries or all areas. Please contact the local carrier for more details.(b) Maximum radio-frequency power transmitted in the frequency bands in which the radio equipment operates: The maximum power for all bands is less than the highest limit value specified in the related Harmonized Standard.The frequency bands and transmitting power (radiated and/or conducted) nominal limits applicable to this radio equipment are as follows:INE-LX1GSM 900: 35 dBm, GSM 1800: 32 dBm,WCDMA 900/2100: 25.7 dBm, LTE Band1/3/7/8/20: 25.7 dBm, Wi-Fi 2.4G: 20 dBm,Bluetooth: 10 dBmINE-LX2GSM 900: 35 dBm, GSM 1800: 32 dBm,WCDMA 900/2100: 25.7 dBm, LTE Band1/3/7/8/20/28/38/40: 25.7 dBm, Wi-Fi 2.4G: 20dBm, Bluetooth: 10 dBmAccessories and Software InformationSome accessories are optional in certain countries or regions. Optional accessories can be purchased from a licensed vendor as required. The following accessories are recommended: Adapters: HW-050200X02, HW-050200X01 (X represents the different plug types used, which can be either C, U, J, E, B, A, I, R, Z or K, depending on your region)Batteries: HB356687ECWEarphones: MEND1532B528A02, HA1-3P, EPAB542-2WH05-DH, 1293-3283-3.5MM-322The product software version is INE-LX1: INE-LX18.2.0.106(C900) / INE-LX2: INE-LX2 8.2.0.56M(SP2C900). Software updates will be released by the manufacturer to fix bugs or enhance functions after the product has been released. All software versions released by the manufacturer have been verified and are still compliant with the related rules.All RF parameters (for example, frequency range and output power) are not accessible to the user, and cannot be changed by the user.For the most recent information about accessories and software, please see the DoC (Declaration of Conformity) at /certification.Legal NoticeTrademarks and Permissions, , and are trademarks or registered trademarks of Huawei Technologies Co., Ltd. Android™ is a trademark of Google Inc.LTE is a trademark of ETSI.The Bluetooth® word mark and logos are registered trademarks owned by Bluetooth SIG, Inc. and any use of such marks by Huawei Technologies Co., Ltd. is under license.Wi-Fi®, the Wi-Fi CERTIFIED logo, and the Wi-Fi logo are trademarks of Wi-Fi Alliance.Privacy PolicyTo better understand how we protect your personal information, please see the privacy policy at http:// /privacy-policy.Copyright © Huawei Technologies Co., Ltd. 2018. All rights reserved.THIS DOCUMENT IS FOR INFORMATION PURPOSE ONLY, AND DOES NOT CONSTITUTE ANY KIND OF WARRANTIES.96725119_01。
Maestro E220系列产品快速使用指南说明书

E220 Series Quick Start GuideV3Table of Contents1.0Terms and Conditions (3)2.0E220 Series: (4)3.0Setup: (5)3.1Prerequisite (5)3.2Available Accessories (6)4.0Maestro Router Overview (7)4.1LAN Panel Details (7)4.2WAN Panel Details (9)4.3Front Panel Details (10)5.0Connecting Maestro Router (11)6.0Software Configuration (14)7.0Conformity (17)7.1Federal Communications Commission (FCC) Compliance Statement 17 7.2 FCC RF Exposure statement (17)7.3 ISED Notice (17)7.4 ISED RF Exposure Information (18)8.0Appendix: 08.1Pin Power Cable Schematic 08.2Power over Ethernet (1)8.3RS485 wiring diagram (2)8.4Certified antenna (3)8.5Selection of antenna (3)E220 Series| QUICK START GUIDE 1.0 Terms and Conditions1.1.1 This manual is written without warranty.1.1.2 Maestro Wireless Solutions Ltd. reserves the right to modify or improve the product andits accessories, which can also be withdrawn without prior notice.1.1.3 The company stresses the fact that the performance of the product and its accessoriesdepend on the proper use conditions as well as the surrounding environment.1.1.4 Maestro Wireless Solutions Ltd. assumes no liability for damage incurred directly orindirectly from errors, omissions or discrepancies between the router and this manual.1.1.5 Every effort is made to keep the product and its software up to date and running smoothly.However, Maestro Wireless Solutions Ltd. takes no responsibility for, and will not be liable forthe product or its software being temporarily unavailable due to technical issues beyond ourcontrol.1.1.6 The above terms and conditions are subject to change without prior notice. The presentuse of this product implies that the user approves and understands all the above terms andconditions.E220 Series| QUICK START GUIDE E220 Series| QUICK START GUIDE 2.0 E220 Series:Table 1: E220 Series compatible modelsProduct nameTerritories / Operators Bands Fall-back mode Bands Cellular Type E224 EMEA3/8/20 2G 3/8 LTE cat. 1 E224 AT&T, T-Mobile 2/4/12 None N/A LTE cat. 1 E225 Lite EMEA. Asia 1/8 2G 3/8 3G [1] E225 Lite World 1/2/5/6/8/19 2G 2/3/5/8 3G [1] E225 EMEA, Asia 1/8 2G 3/8 3G [1] E225 Worldwide 1/2/5/6/8/19 2G 2/3/5/8 3G [1] E228 Verizon Wireless 4/13 None N/A LTE cat. 4 E228 AT&T, Rogers 2/4/5/13/17 3G [2] 2/5 LTE cat. 4 E228 Telstra, Spark 3/7/28 None N/A LTE cat. 4 E228 NTT Docomo1/19/21 None N/A LTE cat. 4 E228Korea, Thailand, Brazil, etc.1/3/5/7NoneN/ALTE cat. 4[1] 7.2Mbps downlink; 5.76Mbps uplink; [2] 43.2Mbps downlink; 5.76Mbps uplinkFigure 1: E220 Series: High-speed 3G or LTE router3.0 Setup:3.1 Prerequisite3.1.1 Before installing your E220 Series router, verify you have the following:∙Router Hardware with:o Active sim cardo Ethernet cableo Wi-Fi and cellular antennas∙Computer equipped with:o Windows, Mac or Linux operating system.o Ethernet port or Wi-Fi connectivity and Internet serviceo Web browser such as Internet Explorer 8+ or Google Chrome, Mozilla Firefox or Safari to access the Maestro Web Admin Consoleo DHCP set to enable.3.1.2 To enable DHCP, do the following:∙From the Start menu, select Control Panel > Network and Sharing Center and then select the existing connection.∙The Network Connection Status dialog box appears. Click Properties > double click Internet Protocol Version 4 (TCP/IPv4).∙The Internet Protocol Version 4 (TCP/IPv4) Properties dialog box appears. Under the tab General, select Obtain an IP address automatically and Obtain DNSserver address automatically.E220 Series| QUICK START GUIDE 3.2 Available AccessoriesTable 2: The following accessories are available for purchase:Item DescriptionPower Supply / CableACC-CA30 2-pin Micro-Fit 3.0 (M) to stripped wire with 2.5 A fused, 1-metre long cable ACC-PS20 2-pin Molex 1.2A power adapter with Euro plug 2-pin - EuropeACC-PS21 2-pin Molex 1.2A power adapter with NEMA 2-pin plug - AmericaACC-PS22 2-pin Molex 1.2A power adapter with AS3112 3-pin plug – Australia / NZ ACC-PS23 2-pin Molex 1.2A power adapter with BS1363 3-pin plug - UKWi-Fi AntennaACC-A21 5-band 2.4 / 5.8GHz dipole antenna, hinged RP-SMA (M)Cellular / GPS AntennaACC-A11 or ACC-A17A 5-band 850 / 900 / 1800 / 1900 / 2100MHz magnetic mount antenna, 3-meter cable, SMA (M)ACC-A03 GPS 1575.42MHz Magnetic mount antenna, 3-meter cable, SMA (M)ACC-A22 Ultra-wide-band 698-960 / 1575.42 / 1710-2700MHz L-shaped antenna, hinged, SMA (M)MiscellaneousACC-DIN Metal DIN Rail clipACC-CA29 RJ45(M) to RJ45(M)-cable length=1000mm3.2.1 For a full list of Maestro Wireless accessories, refer to: http://www.maestro-/accessories/E220 Series| QUICK START GUIDE 4.0 Maestro Router Overview4.1 LAN Panel DetailsFigure 2: Maestro Router LAN Panel∙Orange - Reset Button: When pushed for 3 seconds the device will reset to default settings.∙Green - DC Power Supply: 2-pin Micro-fit 3.0 connector. Black (left) negative red (right) positive.∙Blue - Ethernet port (LAN): Ethernet cable connects to LAN∙Red - RS-485 & Digital input/output ports (see figure 3 next page):E220 Series| QUICK START GUIDE Figure 3: Maestro Router LAN Panel I/O connector Array∙Red - Top slots are release pins for bottom ports.∙Blue - RS-485o Full-duplex:▪B: Rx –▪A: Rx +▪G: Common Ground▪Y: Tx +▪Z: Tx –o Half-duplex▪A&Y: DATA +▪B&Z: DATA –▪G: Common Ground∙Green - DIO Ports configurable as input or output, 20 AWG (recommended).o Input detection: 5V, max. 48Vo Output: Open collector, max. current 200mA∙Yellow - Ground for both DIOsE220 Series| QUICK START GUIDE 4.2 WAN Panel DetailsFigure 4: Maestro Router WAN Panel Array∙Blue - Ethernet port: Can switch from WAN to LANSupports PoE (Power over Ethernet): PoE wired Ethernet LANs allow the electrical current necessary for the operation to be carried by the data cable rather than carried bypower cords thus removing the needs for an external power supply.∙Green – Mini SIM slot (2FF)∙Orange – GPS / Diversity SMA Antenna Connector: Female (GPS only on LTE version)∙Yellow - Cellular SMA Antenna Connector: FemaleE220 Series| QUICK START GUIDE E220 Series| QUICK START GUIDE 4.3 Front Panel DetailsFigure 5: Front Panel4.3.1 The top panel of Maestro’s E220 Series features 6 LEDs on the front to indicate criticalsystem information. Table 3: LED States and Description NameColor and State DescriptionWI-FIOFFWi-Fi network is inactive Blue Flashing Wi-Fi network connection traffic Blue ONWi-Fi network is up and activate ActivityOFF Cellular data service is not connected Amber ON Cellular data service is connectedNetworkOFFDevice is not registered on a cellular network Amber Flashing Registered on roaming cellular network Amber ON Registered on home cellular network SignalOFFNo signal (CSQ=0 to 5, 97, 98, 99) Amber ON Strong signal (CSQ > 12) Amber FlashingWeak signal (CSQ > 6 to 12) PowerOFF Power off Green ON Power onAlertOFFNo alert, device is running smoothly Red Flashing Software fault (crash, issues)Red ONHardware fault (high temperature, problem with module or SIM card)5.0 Connecting Maestro Router5.1.1 Insert the SIM card in the router as shown below.Figure 6: Inserting the SIM card in the Maestro router Array5.1.2 Connect the antenna to the main connector of the E220.IMPORTANT:Verify the antenna is tightly secured.5.1.3 Connect the Diversity antenna to the Diversity connector.E220 Series| QUICK START GUIDE E220 Series| QUICK START GUIDE Figure 7: Connecting the Wi-Fi & cellular antenna on Maestro router:5.1.4 If the Maestro Router package includes dual antenna’; connect the Diversity Antenna tothe Diversity Connector.NOTE: Dual antenna provides RF diversification, which allows for improved signalstrength and thus better performance for both Wi-Fi and cellular,Certain circumstances and environments may require the use of specific type of antenna or one mounted in a different location. In such case, Maestro has many antenna options to choose from, please contact Maestro Support at ****************************.Table 4: E220 series models and auxiliary antennas:MainModel Auxiliary CommentCellular onlyE225 Lite N/AE224 LiteCellular only Please ensure that the antenna used is suitable for the cellular frequencies in use, for both main and auxiliary connectors E225 GPS onlyE224 E2282-mode GPS and cellular Please ensure that the antenna used is suitable for the cellular frequencies in use, for both main and auxiliary connectorsE220 Series| QUICK START GUIDE 5.1.5 Connect the router LAN port with the computer LAN port.Figure 8: Connecting the router and computer LAN port5.1.6 Connect the AC power to the DC in connector, then connect the Micro-Fit connector tothe power input, located on the LAN-side panel of the Maestro Router.∙ Plug the AC cord into a standard AC receptacle as shown below. ∙The power LED will light when power is applied.Figure 9: Connecting the AC power connector5.1.7 An alternate option is to power the Maestro Router over Ethernet port as the WAN portsupports PoE (Power over Ethernet).NOTE: Please refer to the section Power over Ethernet on Appendix 1 for connections example.E220 Series| QUICK START GUIDE 6.0 Software Configuration6.1.1 On the computer, open a Web browser and then enter the Maestro routers LAN IPaddress. A login dialog window displays.NOTE: Username and Password are case sensitive.Figure 10: Login Dialog BoxTable 5: Web Admin Page Parameters Details IP Address (LAN)192.168.1.1 Username admin PasswordadminTable 6: Wi-Fi enabled, with WPA/WPA2 TKIP keyParameter Details SSIDMaestro WPA KeyW1rele$$6.1.2Click Next on the Quick Start Network Configuration Page (figure 11).6.1.2.1 Configure the network parameters for LAN , WAN , Cellular and Wi-Fi .6.1.2.2 Alternately, go to Management Settings , import and load predefined settings file. 6.1.2.3 Click Save & Apply to set the configuration.NOTE: Default WAN, LAN and cellular connection settings:6.1.2.4 WAN connection – Automatic (DHCP – Automatic IP address lookup). 6.1.2.5 Active DHCP with starting IP address: 192.168.1.100 with poll off 100 clients. 6.1.2.6 WAN as automatic IP, with Cellular backup.6.1.2.7 Cellular default APN is “internet”Figure 11: Quick Start Network Configuration PageE220 Series| QUICK START GUIDE Table 7: Quick Start Network Configuration PageScreen Element Description Local NetworkIPv4-Address Enter the IPv4 Address of LAN interface. The default IPv4 Address is 192.168.1.1IPv4-Netmask Enter the IPv4 Subnet Mask of LAN interface. The default Netmask is 255.255.255.0IPv4-Gateway Enter the Gateway IPv4 of the Gateway. WANProtocol Select the WAN protocol from the available options: ∙Manual∙Automatic∙PPPoEThe default WAN protocol is selected as Automatic.CellularAPN Enter the APN provided by the cellular network operator.Access Point Name (APN) is the name (Web address) of an access point for LTE data connection. Generally, wireless cellular network operator provides the APN to their end users.PIN Enter the PIN of the SIM card.SIM card Personal Identification Number (PIN) is used to lock the card, preventing unauthorized phone calls or access to cellular data.Username Enter the login name. Password Enter the password. Wi-FiEnable By default, Wi-Fi interface is enabled every time the Maestro Router reboots. Click and disable the Wi-Fi interface if you do not want to use them.SSID Service Set Identifier (SSID) is a sequence of characters, which uniquely names a wireless local area network (WLAN).The default SSID is Maestro.Password The default password is W1rele$$.E220 Series| QUICK START GUIDE 7.0 Conformity7.1 Federal Communications Commission (FCC) Compliance Statement7.1.1 This device complies with part 15 of the FCC Rules. Operation is subject to the followingtwo conditions:∙This device may not cause harmful interference.∙This device must accept any interference received, including interference that may cause undesired operation.7.1.2 This device has been tested and found to comply with the limits for a Class B digitalpursuant to Part 15 of the FCC Rules. These limits are designed to provide reasonableprotection against harmful interference in a residential installation. This equipment generates,uses and can radiate radio frequency energy.7.1.2.1 It not installed and used in accordance with the instructions, may cause harmfulinterference to radio communications. here is no guarantee that interference will notoccur in a particular installation.7.1.2.2 If this equipment does cause harmful interference to radio or television reception,which can be determined by turning the equipment off and on, the user isencouraged to try to correct the interference by one or more of the followingmeasures:∙Reorient or relocate the receiving antenna.∙Increase the separation between the equipment and receiver.∙Connect the equipment into an outlet on a circuit different from that to which thereceiver is connected.∙Consult the dealer or an experienced radio/TV technician for help.7.1.3 FCC Caution:7.1.3.1 Changes or modifications not expressly approved by the party responsible forcompliance could void the user’s authority to operate the equipment.7.2 FCC RF Exposure statementThis device complies with FCC radiation exposure limits set forth for an uncontrolled environment.In order to avoid the possibility of exceeding the FCC radio frequency exposure limits, human proximity to the antenna shall not be less than 20cm (8 inches) during normal operation.7.3 ISED NoticeThis device complies with Innovation, Science and Economic Development Canada license-exempt RSS standard(s). Operation is subject to the following two conditions:(1) this device may not cause interference, and(2) this device must accept any interference, including interference that may cause undesiredoperation of the device.E220 Series| QUICK START GUIDE Le présent appareil est conforme aux CNR Innovation, Sciences et Développement économique Canada applicables aux appareils radio exempts de licence. L'exploitation est autorisée aux deux conditions suivantes :(1) l'appareil ne doit pas produire de brouillage, et(2) l'utilisateur de l'appareil doit accepter tout brouillage radioélectrique subi, même si lebrouillage est susceptible d'enThis Class B digital apparatus complies with Canadian ICES-003.Cet appareil numérique de la classe B est conforme à la norme NMB-003 du Canada.IC: 20055-E228F7, 20055-E224LITEF2, 20055-E224LITEF4, 20055-E225LITEF3, 20055-E225F3, 20055-E228F2, 20055-E228F57.4 ISED RF Exposure InformationThis device complies with ISED radiation exposure limits set forth for an uncontrolled environment. In order to avoid the possibility of exceeding the ISED radio frequency exposure limits, human proximity to the antenna shall not be less than 20cm (8 inches) during normal operation.Cet appareil est conforme aux limites d'exposition aux rayonnements de la ISED CNR-102 définies pour un environnement non contrôlé. Afin d'éviter la possibilité de dépasser les limites d'exposition aux fréquences radio de la ISED CNR-102, la proximité humaine à l'antenne ne doit pas être inférieure à 20 cm (8 pouces) pendant le fonctionnement normal.E220 Series| QUICK START GUIDE 8.0 Appendix:8.1 Pin Power Cable SchematicFigure 12:8.2 Power over EthernetFigure 13: PoE_____________________________________________________________________________________8.3 RS485 wiring diagramFigure 14: Half Duplex (Left) RS485 Full Duplex (Right)8.4 Certified antennaDipole Wi-Fi antenna:∙ 5 dBi high performance antenna∙RP-SMA(M) hinged antenna∙RoHS compliant∙Peakgain:*************~2.5GHzWWAN antenna:∙Dipole 4G swivel blade antenna∙Performance across the LTE frequency bands∙698-960 / 1710-2170 / 2500-2700 MHz∙Up to 2 dBi gain∙SMA connector∙RoHS compliant product8.5 Selection of antennaSelection of Wi-Fi antenna:∙Dipole,PeakGain<*************~2.5GHzSelection of antenna type:∙Using the same dipole antenna type as certified module & Modem for FCC as above or external antenna with length > 20 cm.。
JBlQuick Start Guide 3.1CH Soundbar与无线子woofer 与Dol

2 Identifying the Parts
Identifying the Parts
Mai Control Sensor Receive signal from the remote control.
ends of the batteries match the (+)
and (–) ends indicated in the battery compartment.
3 Close the battery compartment cover.
- Do not mix old and new batteries; - Do not mix alkaline, standard (Carbon-Zinc) or
Digital / PCM format, the soundbar will
show DOLBY ATMOS / DOLBY AUDIO /
PCM AUDIO.
4. While the soundbar is using Dolby Atmos audio, you can only adjust the bass level of the subwoofer. All other EQ e ects will not be available.
11 BASS
Press to activate the bass setup.
12 TREBLE Press to activate the treble setup.
AC Power Cord x2
User Manual/Quick Start Guide/ Wall Mount Guide
Schneider Electric Altistart 22快速启动指南说明书

Quick start guide - Altistart 22Preliminary informationInformation below is designed to use for simple applications with 2-wire control mode and freewheel stop.If you need more information, or for other applications, see the User manual (BBV51330) on . For a hard copy, contact your local sales Office or Schneider Electric representative.Note:DO NOT USE this guide for Altistart 22 connected inside the delta of the motor (it means Altistart 22 connected to the motor with delta connections in series with each motor windings). In this case, see User manual on .Read and understand these instructions before performing any procedure with this soft starter.Electrical equipment should be installed, operated, serviced and maintained only by qualified personnel. No responsibility is assumed by SchneiderElectric for any consequences out of the use of this material.Check the delivery of the soft starterRemove Altistart 22 from the packaging and check that it has not been damaged.Ensure that the soft starter reference on the nameplate is similar to the purchase order delivery note.Write the soft starter model Reference: ATS22 ______and Serial Number :___________________Check the line voltage compatibilityCheck that the line voltage is compatible with the supply range of the soft starter. Line voltage __________ Volts Soft starter voltage range ______________ Volts Control voltage _______ Volts Soft starter control voltage range _______ VoltsMount the soft starter verticallyFor a surrounding air temperature up to 40 °C (104°F).For other thermal conditions, see user manual (BBV51330) on .WARNINGDAMAGED SOFT STARTER EQUIPMENTDo not operate or install any soft starter or soft starter accessory that appears damaged.Failure to follow these instructions can result in death, serious injury, or equipment dam-age.S1A1038804Connect the soft starter-Check that the control supplyis 230V for CL1 and CL2.-Remove the red sticker which covers the CL1-CL2 terminals.-Wire control supply: CL1 and CL2.-Wire logical inputs: LI1 and LI2.(1) Check the operating limits of the contact.(2) Select a voltage transformer in accordancewith the mains voltage.Note: For additional information in order to size the protective and control devices, refer to the catalog or the user manual available on Connect the soft starter-Check that the control supplyis 110V for CL1 and CL2.-Remove the red sticker which covers the CL1-CL2 terminals.-Wire control supply: CL1 and CL2.-Wire logical inputs: LI1 and LI2.-Wire the relay: R2A and R2C.(1) Check the operating limits of the contact.(2) Select a voltage transformer in accordance withthe mains voltage.Note: For additional information in order to size the protective and control devices, refer to the catalog or the user manual available on Apply power to the Altistart 22 and start the motor•Close the enclosure.•PushS2button.•The soft starter displays rdY.•Close S3, the motor starts.Factory settingsThe Altistart 22 is factory configured for most standard applications. If the factory configuration is not suitable for your application, refer to User manual (BBV51330) on . Here is the list of writable parameters in an “easy start up” mode.rdY: soft starter ready, when power and control voltage are present and the motor is not operating.nrdY: when power is not supplied and control voltage is supplied or when power and control voltage are present with LI1 not connected and LI2 present (run command).conFConfigurationICL Soft starter rated current According to the soft starter ratingdLtA Connection type (Line or delta)LInEUIn Line voltage ATS22ppp Q range:400 VacATS22ppp S6-S6U ranges:480 VacIn Motor rated current According to the soft starter ratingCod Setting lock nLoC (Not locked)LAC Advanced mode oFFSEtAdjustmentst90Initial voltage 30% of input voltageILt Current limit 350% of IntLSMax start time IS sACC Acceleration timeID sdEC Deceleration time FrEE (Freewheel)EdC Final torque OtHP Motor thermal protection IO(IEC class 10)Power on the control•Check that S3 is open.•Switch on: Q1, Q2, Q3 and Q4.•The soft starter displays nrdY.Adjust UIn line voltage•Push scroll down button to reach conF menu.•Pushbutton.•Push scroll down button to reach UIn parameter.•Set UIn to the main line voltage ac value, usingscroll Up/down.•Push button to validate the UIn value.Adjust In motor rated current•In conF menu•Push scroll down button to reach In parameter.•See Nominal Motor Current on Motor Nameplate(Motor Full Load Amps) in STAR connection, note the “Amps” value.•Set In to this value using scroll Up/down.•Push button to validate the In value.。
SISPM1040-382-LRT 高强度快速以太网交换机快速入门指南说明书

SISPM1040-382-LRT Quick Start Guide 33721 Rev. A https://Page 1 of 2SISPM1040-382-LRT Managed Hardened Fast Ethernet SwitchQuick Start GuideThe SISPM1040-382-LRT is a managed PoE switch for connecting and powering devices in challenging environments. Two gigabit speed combo ports are provided,allowing copper or fiber SFP uplink ports. The two uplink ports can also be used in a redundant ring for maximum network reliability. The switch has a PoE powerbudget of 240 Watts, provides up to 30 Watts per port on all ports simultaneously, has redundant input power connections, and a fault alarm relay to ensure safereliable operation in temperatures between -40°C and +75°C without SFPs. See the full User Guide for important information on Product Alerts, Hardware, LEDs,Cabling, SFPs, Web Management, Login, Command Line Interface (CLI), Technical Specifications, Power Supply specs, Service, Warranty & Compliance, and Regulatory Agency Information. Hardware InstallationDIN-Rail : Each switch has a DIN-Rail kit that can be mounted on the rear panel. Mount the DIN-Rail Clip. Wall Mount : A wall mount bracket can be used to mount the switch on a panel or wall. The bracket is mounted to the switch using the enclosed screws.PoE Ports : Port 1 ~ 8 contain PoE+ function. Compliant with IEEE802.3at PoE+ specifications. Compliant with 802.3at in Environment A when using an isolatedpower supply. For 802.3at Environment B applications: 1) use an isolated AC/DC power source, e.g. TN 25080, and/or 2) use mid-span injector (s), e.g. MIL-L100i,L1000i-at, between this switch’s PSE port and link partner PD port.SFPs : The switch has fiber optical ports with SFP connectors. See the Transition Networks SFP page for more information. See the related SFP manual for safety cautions and warnings. Status LEDs : Power (PWR, PWR1, PWR2), Ring Master (R.M.), Ring, Fault, Port Link/Act, and Port PoE.Reset button : Push the front panel Reset button for 2 to 3 seconds to reset the switch. Push the Reset button for 5 seconds to reset the switch to its Factory Default settings.Power Connection : Connect wires between the + terminals on the power supply and the + terminals on the switch terminal block. Do the same with the – terminals. Maintain correct polarity (not reverse polarity protected). Proper Earth Ground Isolation : For PoE applications, to achieve full isolation between PSE (switch port) and load (PD), the switch must be powered with a 1500 VAC / 2250 VDC isolated power supply. For applications requiring additional isolation, 1) use an isolated AC/DC power source, e.g. TN 25104, and/or2) use mid-span injector (s), e.g. MIL-L100i, L1000i-at, between this switch’s PSE port and link partner PD port. In addition, earth ground should be connected to the switch chassis.WARNING : This case must be earth grounded. No DC input may be earth grounded. Use an Isolated Power Supply. See the full User Guide for important details and Cautions and Warnings . Management SoftwareThe SISPM1040-382-LRT can be managed via the Web, TELNET, Console or other third-party SNMP software.Console Cable : The SISPM1040-382-LRT can be management via console port. A DB-9 to RJ-45 cable is included in the package. Connect the cable to a serial port on the PC via the RS-232 DB-9 female connector and the other end (RJ-45 connector) to the switch console port.SISPM1040-382-LRT Quick Start Guide33721 Rev. A https:// Page 2 of 2Command Line Interface (CLI): In addition to Web-base management, the SISPM1040-382-LRT also supports CLI management. Before configuring by RS-232 serial console, use an RJ45 to DB9-F cable to connect the switch’s RS-232 Console port to your PCs’ COM port. You can use HyperTerminal,PuTTY , Tera Term, Telnet, or similar program. The main CLI command line controls are: ?: List, <TAB>: Complete, <ctrl+z>: Up level,<ctrl+q>: LogoutThe main CLI commands include Enter Privileged EXEC mode (enable), Logout command line shell (logout), Ping function (ping), Logout commandline shell (quit), and Show (show).Config mode commands let you configure 8021x, admin, aggregator, auto-sfp, check-concurrence, defaults, dhcpserver, end, events, exit, fault-relay, igmp, interface, ip, lldp,mac-address-table, mstp, multi-ring, multicast-filtering, multiple-ring, no, ptp, qos, reload, rings, rstp, security, sfp-monitor, smtp, snmp, sntp, syslog, system details, tacacs+, and tftp. Web Management : The default values are IP Address: 192.168.1.77, Subnet Mask: 255.255.255.0, Default Gateway: 192.168.1.254, User Name: root , Password: root .System Login:1. Launch a web browser such as Internet Explorer.2. At the prompt http:// type the IP address of the switch and press “Enter”.3. At the login screen (shown right), enter thecurrent User name (root ) and Password(root ).4. Press “Enter”; the System Information page displays (below right).The Web GUI lets you configure, monitor, test, and report the many available functions. The top-level Web GUI menu items are:System Information, Front Panel, Basic Setting, DHCP Server, Port Setting, Redundancy, VLAN, SNMP, Traffic Prioritization, Multicast,Security, Warnings, Monitor and Diagnostics, Power over Ethernet (PoE), Save Configuration, Factory Defaults, and System Reboot.Related Information : For Transition Networks Drivers, Firmware, Manual, etc. go to the Product Support webpage (logon required). For Transition Networks Application Notes, Brochures, Data Sheets, Specifications, etc. go to the Support Library (no logon required).Trademarks : All trademarks and registered trademarks are the property of their respective owners. Copyright Notice/Restriction s: Copyright © 2013-2017 Transition Networks. All rights reserved.No part of this work may be reproduced or used in any form or by any means (graphic, electronic or mechanical) without written permission from Transition Networks. The information contained herein is confidential property of Transition Networks, Inc. The use, copying, transfer or disclosure of such information is prohibited except by express written agreement with Transition Networks, Inc. Transition Networks | 10900 Red Circle Drive | Minnetonka, MN 55343 USA | tel: +1.952.941.7600 | toll free: 1.800.526.9267 | fax: 952.941.2322 || ******************** | ************************** | ****************************** |。
FastTrak SX4000 Lite 快速启动指南说明书
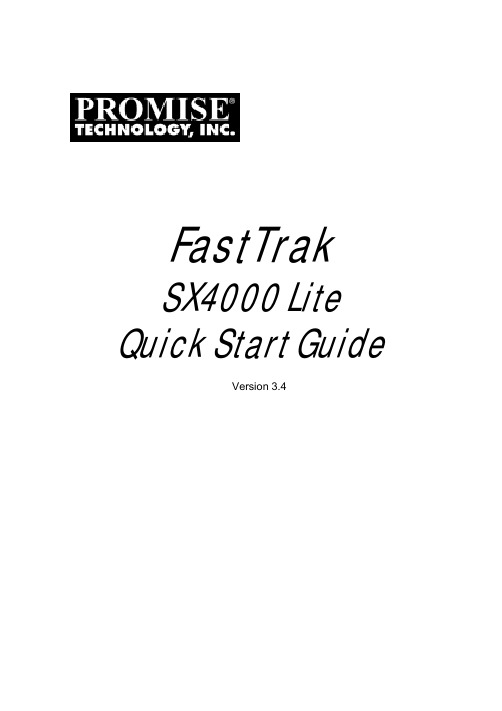
FastTrak SX4000 Lite Quick Start GuideVersion 3.4FastTrak SX4000 LiteCopyright© 2003, Promise Technology, Inc.Copyright by Promise Technology, Inc. (Promise Technology). No part of this manual may be reproduced or transmitted in any form without the expressed, written permission of Promise Technology.TrademarksPromise, and the Promise logo are registered in U.S. Patent and TrademarkOffice.All other product names mentioned herein may be trademarks or registeredtrademarks of their respective companies.Important data protection informationYou should back up all data before installing any drive controller or storageperipheral. Promise Technology is not responsible for any loss of data resulting from the use, disuse or misuse of this or any other Promise Technology product. NoticeAlthough Promise Technology has attempted to ensure the accuracy of thecontent of this manual, it is possible that this document may contain technical inaccuracies, typographical, or other errors. Promise Technology assumes no liability for any error in this publication, and for damages, whether direct, indirect, incidental, consequential or otherwise, that may result from such error, including, but not limited to loss of data or profits.Promise Technology provides this publication “as is” without warranty of any kind, either express or implied, including, but not limited to implied warranties ofmerchantability or fitness for a particular purpose.The published information in the manual is subject to change without notice.Promise Technology reserves the right to make changes in the product design, layout, and driver revisions without notification to its users.ContentsStep 1: Unpack Your FastTrak Card (3)Step 2: Memory Module Test (4)Step 3: Install the FastTrak Card (5)Step 4: Install the Hard Drives (6)Step 5: Create Your Disk Array (8)Step 6: Install Software Drivers (11)Quick Start Guide Step 1: Unpack Your FastTrak CardWhen you receive the FastTrak SX4000 Lite, the package should contain the items listed below:• FastTrak SX4000 Lite Controller Card• Quick Start Guide• FastTrak SX4000 Lite driver diskette• Four Internal 18 inch (46 cm) Ultra ATA, 80-wire/40-pin hard drive cables• Two Y-cable power splitters• CD with Drivers, Promise Array Management (PAM) utility, PAM User Manual and FastTrak S150 SX4 / SX4000 / SX4000 Lite User Manual If any of the items are missing or appear damaged, please contact your dealer or distributor immediately.NoteThe Promise card is a PCI Plug-n-Play (PnP) device. Nochanges are necessary in the motherboard CMOS/BIOS Setupfor resources or drive types in most applications.WarningBefore installing the adapter into an existing system, backup anyimportant or useful data. Failure to follow this accepted PCpractice could result in data loss.WarningThe FastTrak card, like other parts of your system, is subject todamage by static electricity. Be sure that you’re properlygrounded (Promise Technology recommends that you wear ananti-static strap or touch a grounded object) and that you unplugyour system before installing FastTrak.FastTrak SX4000 LiteStep 2: Memory Module TestThe FastTrak SX4000 Lite RAID Controller card ships without a Dual InlineMemory Module (DIMM) for Synchronous Dynamic Random Access Memory (SDRAM). A DIMM of 64 MB to 256 MB capacity must be installed in order for the FastTrak Card to function.The DIMM you select must pass a test prepared by Promise Technology toverify that your DIMM is fully compatible with the FastTrak card. An incompatible DIMM can appear to work properly, only to experience unexpected errors that may result in data loss or controller malfunction.Promise recommends testing for all DIMMs being used in a FastTrak controller, including those from the above list. Follow this procedure to verify your DIMM's compatibility with your FastTrak RAID Controller card.1. Prepare a DOS Boot diskette.2. Copy the Promise Test Utility files to a second diskette.3. Install your SDRAM DIMM into the Cache Memory socket of the FastTrakcard.4. Plug in FastTrak card into a PCI slot on a desktop PC or server.5. Boot the PC with the DOS Boot diskette.6. Remove the DOS Boot diskette and insert the diskette with the PromiseTest Utility files.7. At the DOS prompt, type memtest and press Enter. The test begins.• If the DIMM is OK, the program will show a PASS message similar to the one below:Promise Memory Test Utility V1.305/24/2003 18:07:50Controller Type.................: FastTrakSX4000Memory Speed....................: 100MHzMemory Size.....................: 128MBMemory Type.....................: Non-ECCMemory Test Result ( HOST ).....: PASSMemory Test Result ( HDMA ).....: PASSMemory Test Result ( XOR ).....: PASSThe PASS message means you can use the DIMM that is currentlyinstalled.• If there is any error, the program will stop and return to DOS and show error message. Do not use the DIMM.• If the program halts for more than 20 seconds, there may be an error.Check the FastTrak card, DIMM, and your system BIOS. Then run thetest again.Quick Start Guide Step 3: Install the FastTrak CardThe FastTrak RAID Controller card fits into any available:• 33-MHz, 32-bit PCI slot (must be PCI 2.2 compliant)• The 33-MHz, 32-bit portion of a 64-bit PCI sloton the PC’s motherboard (see Figure 1 below).1. Remove the cover of your system.2. Remove the inside slot cover of an available 33-MHz, 32-bit PCI slot on themotherboard.3. Install the FastTrak card into the open slot (see Figure 1 below). Secure thebracket to the system’s frame.4. Attach your system case’s 2- or 4-pin LED cable to the LED connector onthe FastTrak card (see Figures 2 and 3, below). Make sure that pin 1 on theconnector is aligned with pin 1 of the cable.5. Fasten the FastTrak card bracket to the system case (see below).Figure 1. Insert the FastTrak card into an open PCI slot.FastTrak SX4000 LiteStep 4: Install the Hard DrivesImportantIf you wish to include your current bootable Serial ATA driveusing the Windows XP operating system as part of a bootableMirrored (RAID 1) array on your FastTrak card, do NOT connectthe hard drive to the FastTrak yet.You MUST install the Windows XP driver software first onto thisdrive while it is still attached to your existing hard drive controller.The FastTrak SX4000 Lite RAID Controller card supports only (Parallel) ATA hard drives.If you are striping (RAID 0) for performance, use up to four new drives. Ifmirroring (RAID 1) for protection, you can use two new drives OR use anexisting drive and a new drive (the new drive must be the same size or larger than the existing drive). If you are planning a RAID 5 array, use three or four new drives.1. Set your hard drives to Master, Cable-Select or Single (depending on drivespecification).2. Install the hard drives into the hard drive bays of your system.CautionUse of removable hard drive enclosures other than PromiseTechnology’s SuperSwap is not supported and may result inperformance loss or other undesired results.3. Attach the black end of the Ultra ATA cable to each hard drive. Then attachthe blue end to the ATA connectors on the FastTrak card (see Figure 2,below).Quick Start GuideFigure 2. FastTrak SX4000 Lite card.4. Attach the Y-cable power splitters to each of the hard drives.Ch1 Ch2 Ch3 Ch4 Buzzer LED Pins (Not included. See Step 2)FastTrak SX4000 LiteStep 5: Create Your Disk ArrayYou will now use the onboard FastBuild BIOS utility to create your first arrayusing the attached drives. For an explanation of the array options, see Chapter 3 of the FastTrak S150 SX4 / SX4000 / SX4000 Lite User Manual.ImportantEven if you plan to use the Promise Array Management Utility tomanage your array, you must still create your first array usingthe FastBuild Utility, as described here.1. Boot your system. If this is the first time you have booted with the FastTrakcard and drives installed, the Promise onboard BIOS will display thefollowing screen.<2. Press the Ctrl-F keys to display the FastBuild Utility Main Menu (below).3. Press 2 on the Main Menu screen to display, the Define Array Menuappears (below).Quick Start Guide4. Press the arrow keys to highlight an array number you wish to define andpress Enter to select it. The Define Array Definition Menu will next appear (below).5. Choose the RAID Level you want. In the Define Array Definition Menusection, press the Spacebar to cycle through array types:•RAID 0 (Striping)•RAID 1 (Mirroring)•RAID 0+1 (Striping / Mirroring)•RAID 5 (Data / Parity Striping)•JBOD (Single Drive)FastTrak SX4000 Lite6. Press the arrow keys to move to the next option. Option choices depend onthe RAID Level you selected.•Initialize Array, zero the disk drives. RAID 5 only.•Stripe Block Size, the default 64KB is best for most applications.•Gigabyte Boundary, allows use of slightly smaller replacement drives.7. Press the arrow keys to move to Disk Assignments. Press the spacebar totoggle between N and Y for each available drive.Assign the appropriate number of disk drives to your array. Refer to thechart below:DrivesofLevel NumberRAID 0 2, 3 or 4RAID 1 2 onlyRAID 0+1 4 onlyRAID 5 3 or 4JBOD 1, 2, 3 or 4A disk drive that is not assigned to an array will automatically function as aHot Spare Drive.8. Press Ctrl-Y to save your array configuration.9. Press Esc to exit to the Main Menu. Press Esc again to exit the Utility.10. Press Y to confirm the new array and restart the computer.You have successfully created a new RAID array.ImportantYou must be partition and format your new array before you canuse it. Use the same method of partitioning and formatting on anarray as you would any other fixed disk added to your computersystem..Quick Start Guide Step 6: Install Software DriversDrivers for the Windows operating systems are included on the software CD and driver diskette that came with your FastTrak SX4000 Lite Controller. Please download the latest drivers from the Promise website at . Windows systems usually recognize the FastTrak Controller, prompt you for the CD or diskette and perform the driver installation automatically.If you are installing the FastTrak Controller at the same time as your operating system or you prefer to read step-by-step directions, see Chapter 4 of the FastTrak S150 SX4 / SX4000 / SX4000 Lite User Manual on the software CD.Drivers and installation instructions for other Operating Systems are downloadable from the Promise website at .11。
雷克斯摄像头系统LW2231快速启动指南说明书

garder la base de la caméra ras au mur ou au plafond lorsque montée.
d’ajustement afin de sécuriser la position de la caméra.
B. Installation du récepteur
1
Connectez le câble BNC à l’entrée vidéo de votre DVR.
Brancher l’adaptateur
3 d’alimentation électrique au récepteur. Brancher l’adaptateur d’alimentation électrique à une prise de 120V.
REMARQUE : Il n’est pas conseillé d’installer plus de 4 caméras de sécurité sans fil numérique dans un même endroit (2 récepteurs) afin de conserver les performances optimales de la fréquence d’image vidéo.
BNC pour la vidéo*
Lors de l’installation de plusieurs caméras de sécurité sans fil numériques dans un même endroit, garder une distance de 10 cm (4 po) entre les récepteurs afin d’optimiser les performances de la caméra.
- 1、下载文档前请自行甄别文档内容的完整性,平台不提供额外的编辑、内容补充、找答案等附加服务。
- 2、"仅部分预览"的文档,不可在线预览部分如存在完整性等问题,可反馈申请退款(可完整预览的文档不适用该条件!)。
- 3、如文档侵犯您的权益,请联系客服反馈,我们会尽快为您处理(人工客服工作时间:9:00-18:30)。
Table of contents:1INTRODUCTION (2)2KIT CONTENTS (2)3SYSTEM REQUIREMENTS (2)4GETTING STARTED (2)4.1I NSTALLATION OF NI-S ERIAL CABLE ASSEMBLY DRIVER (2)4.2I NSTALLATION OF STIM202 EVALUATION PROGRAM (3)4.3F IRST HARDWARE CONNECTION (4)4.4F IRST SOFTWARE START-UP (4)4.5I NTRODUCTION TO DIFFERENT PARTS OF PC SOFTWARE (7)4.6S AVE DATA TO FILE (8)4.7D EMONSTRATOR VIEW (9)5FILE DOWNLOAD AND CUSTOMER SUPPORT (9)6ORDERING INFORMATION (9)7REVISION HISTORY (9)Figure 1: STIM202 evaluation kitDate Sign Rev Reference Date Dok StampPrepared 100419 ROW 0 Archive 12812 100419 HKWChecked 100419 OF 1 EMApproved 100419 ROW 2 EM1 IntroductionThe STIM202 evaluation kit provides rapid measurement and configuration access to STIM202 gyro cluster fromSensonor Technologies. High data sampling frequencies, graphical presentation, and data log to file are supported for 1, 2 or 3 axes units.STIM202 requires a single voltage supply (5 VDC), and this is provided from a USB port with this setup.2 Kit ContentsKit contents:∙ Quick start manual (this document)∙ STIM202 (ordered separately, not included in the kit) ∙ Sensonor cable assembly, X-83932 ∙ NI cable assembly, X-83921∙ PC with STIM202 evaluation program (PC not included)Figure 2: STIM202 evaluation kit. Setup schematics3 System requirementsMinimum 2 free USB ports required; One for STIM202 communication, and one for STIM202 power.The STIM202 evaluation kit is supported (verified) by the following operating systems:∙ Windows Vista 32 bit ∙ Windows Xp 32 bit4Getting started4.1 Installation of NI-Serial cable assembly driverWithout connecting anything yet, install the NI-serial driver. Refer to the …Serial Installation Guide‟ sheet and CR-ROM in the included NI-serial driver box (X-83921) for instructions. During installation the following windows appear:Figure 3: NI-Serial installation (1 of 12)Figure 4: NI-Serial installation (2 of 12)Figure 5: NI-Serial installation (3 of 12). Selections can be left as default.Figure 6: NI-Serial installation (4 of 12)Figure 7: NI-Serial installation (5 of 12)Figure 8: NI-Serial installation(6 of 12)Figure 9: NI-Serial installation (7 of 12)Figure 10: NI-Serial installation (8 of 12)Figure 11: NI-Serial installation (9 of 12)Figure 12: NI-Serial installation (10 of 12)Figure 13: NI-Serial installation (11 of 12)Figure 14: NI-Serial installation complete (12 of 12)4.2 Installation of STIM202 evaluation program∙ Download the latest version of …Evaluation Kit STIM202 v.x.y .zip‟ from Sensonor FTP server (see chapter 5 for login details etc.). Consider the feature …Open FTP site i n Windows explorer‟ in the web browser if that is more convenient than the default view∙ Pack out the content of the zip-file to a local drive∙Run the installation file (setup.exe) and follow the on-screen instructionsFigure 15: PC software installation from a local driveDuring installation the following windows appear:Figure 16: PC software installation (1 of 6)Figure 17: PC software installation (2 of 6)Figure 18: PC software installation (3 of 6)Figure 19: PC software installation (4 of 6)Figure 20: PC software installation (5 of 6)Figure 21: PC softwareinstallation complete (6 of 6)4.3 First hardware connectionNI-Serial driver and PC software should already be installed at this point.Now, proceed to connect system hardware as follows:∙Connect a STIM202 to the Nicomatic connector of the STIM202 cable assembly. A small screw driver is needed for this (to rotate the fixing screws of the Nicomatic connector)∙Connect the 9 pin D-SUB connector on the opposite side of the STIM202 cable assembly to the NI cable assembly∙Insert the USB connector of the NI cable assembly in a free USB port of the PC. Verify that the device driver installation is completed successfully. The NI-Serial device should now be visible in device manager. Notice the COM-port numberFigure 22: Verification that NI USB-485 device is visible in device manger after first hardware connection ∙Leave the second USB connector (the one powering STIM202) unconnected at this point4.4 First software start-upProceed to first time start-up of PC software as follows:∙Navig ate to, and click on, …STIM202 Evaluation‟ in the Windows start menuFigure 23: Start-up of PC software from Windows start menu∙ A pop-up box will appear and ask for a parameter file (an .INI-file). Select the one available by default, called…STIM202 evaluation.INI‟Figure 24: INI-file selection at startup of PC software∙The software user interface appears after selecting the INI-fileFigure 25: User interface of PC software directly after startup∙Now, open PC serial connection to STIM202 evaluation kit hardware by clicking on …Connect to HW‟. A green light appears, and the message …Hardware connected OK‟ is shown in the lower right corner of the panel.Note: The COM-port in use is likely to be different from the default one of the parameter file (default is COM4) if the connection fails (indicated by red LED). If this is the case, the parameter file needs to be edited, and this can be done from the …Parameters‟ panel. Password to enable edit is …stim‟. See also Figure 34 showing the …paramters‟ panel. (Hint: Use the device manager to find the correct COM-port if this has to be changed to something different then the default value)Figure 26: Hardware connection OK∙Switch the ‟Apply voltage‟ control to ‟ON‟ and proceed to insert the USB connector for powering STIM202 intoa free USB port. Confirm voltage applied by clicking …OK‟ in the pop-up panel appearing (telling …Turn power(5.0V) to STIM ON‟). (This rather manual process controls some operations of the PC software.)Figure 27: Confirm power by USB is applied to STIM202∙Verify that the connection is established to STIM202 by asking for a …config DG‟. Thi s should look similar to below:Figure 28: Result of sending ’Request config DG’ to STIM202 The kit is now ready for use4.5 Introduction to different parts of PC softwareIn addition to what already has been shown, some functions and panels are available in PC software: Figure 29: Result of sending ’Request identity DG’Figure 30: Result of sending ’Request serial DG’Figure 31: After entering ’Service mode ’. Note that the ‘Enter Serv. mode’ button is activated from ‘Normal mode’ panel , and the that return to Normal mode is done by clicking ‘Exit to normal mode’Figure 32: ’Measure’ panel showing result of hands-on test (x, y and z axes are shown)Figure 33: ’Demo’ panel showing result of 3-axis hands-on test (x, y and z axes are shown)Figure 34: ’Parameters’ panel4.6 Save data to fileTest data can be logged to file from the …measurement panel‟ …by clicking “Save to f ile” button. Timetags and data with units, [s] and [°/s] respectively, are listed in this txt-file.Figure 35: Result file with time tags and measurement data4.7 Demonstrator viewA demonstrator part of the software is found i n the …demo‟ panel. Various reset times and axis scales can be selected. The STIM202 axes rate signals are handled and plotted axis by axis real-time in these windows. Curves shown are angular rate [°/s] in red, and increment angle [°] in blue.5 File download and customer supportCheck for the latest update of the STIM202 evaluation kit software package on Sensonor FTP server, or by addressing Sensonor customer support with an email to: customer.support@sensonor.noFTP server details:FTP address: ftp://195.1.76.74User name: senPassword: senFigure 36: Sensonor FTP server login6 Ordering informationExtra STIM202 cable assemblies (X-83932), and NI-serial cable assemblies (X-83921), are also available up-on request.7 Revision history。