各式各样的RTM成型技术
RTM成型工艺及分类介绍

RTM成型工艺及分类介绍1、RTM成型工艺与分类RTM是指低粘度树脂在闭合模具中流动、浸润增强材料并固化成形的一种工艺技术,属于复合材料的液体成形或结构液体成形技术范畴。
其具体方法是在设计好的模具中,预先放入经合理设计、剪裁或经机械化预成形的增强材料,模具需有周边密封和紧固,并保证树脂流动顺畅;闭模后注入定量树脂,待树脂固化后即可脱模得到所期望产品。
SMC、BMC模压、注射成型、RTM、VEC技术都属闭模成型工艺。
由于环境法的制定和对产品要求的提高使敞模成型复合材料日益受到限制,促使了闭模成型技术的应用,近年来尤其促进了RTM技术的革新和发展。
2、RTM的类型RTM工艺起始于上世纪50年代,目前,RTM成型工艺己广泛应用于建筑、交通、电讯、卫生、航天航空等领域。
下面介绍几种RTM技术。
01、RTM,树脂传递模塑。
该技术源自聚氨酯技术,成型时关闭模具,向预制件中注入树脂,玻纤含量低,约20-45%。
02、VARIT,真空辅助树脂传递注塑。
该技术利用真空把树脂吸入预制件中,同时也可压入树脂,真空度约10-28英寸汞柱。
03、VARTM,真空辅助树脂传递注塑。
制品孔隙一般较少,玻纤含量可增高。
04、VRTM,真空树脂传递模塑。
05、VIP,真空浸渍法。
06、VIMP,可变浸渍塑法。
树脂借助真空或自重移动,压实浸渍。
07、TERTM,热膨胀RTM。
在预制件中插入芯材,让树脂浸渍并对模具与成形品加热。
芯材受热膨胀,压实铺层。
利用这种压实作用,结合表面加压成型。
08、RARTM,橡胶辅助RTM。
在TERTM方法中不用芯材而用橡胶代之。
橡胶模具压紧成型品,使孔隙大大减少,玻纤含量可高达60-70%。
09、RIRM,树脂注射循环模塑。
真空与加压结合,向多个模具交替注入树脂,使树脂循环,直至预制件被充分浸透。
10、CIRTM,Co-Injection RTM。
共注射RTM,可注入几种不同的树脂,也可使用几种预制件,可利用真空袋和柔性表面的模具。
RTM成型学习资料
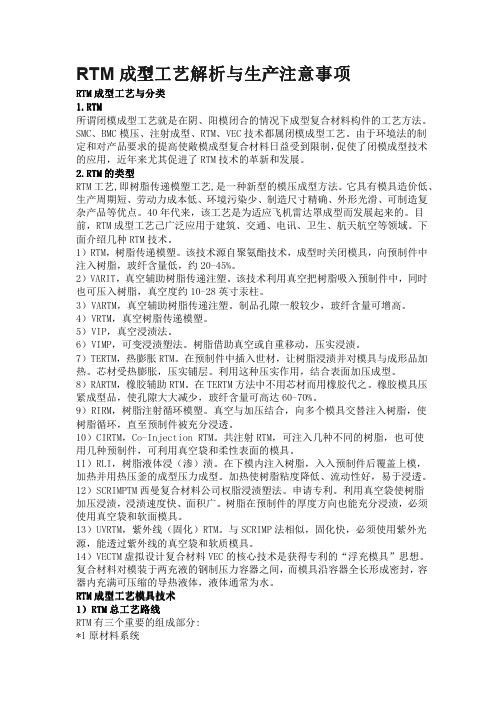
RTM成型工艺解析与生产注意事项RTM成型工艺与分类1.RTM所谓闭模成型工艺就是在阴、阳模闭合的情况下成型复合材料构件的工艺方法。
SMC、BMC模压、注射成型、RTM、VEC技术都属闭模成型工艺。
由于环境法的制定和对产品要求的提高使敞模成型复合材料日益受到限制,促使了闭模成型技术的应用,近年来尤其促进了RTM技术的革新和发展。
2.RTM的类型RTM工艺,即树脂传递模塑工艺,是一种新型的模压成型方法。
它具有模具造价低、生产周期短、劳动力成本低、环境污染少、制造尺寸精确、外形光滑、可制造复杂产品等优点。
40年代来,该工艺是为适应飞机雷达罩成型而发展起来的。
目前,RTM成型工艺己广泛应用于建筑、交通、电讯、卫生、航天航空等领域。
下面介绍几种RTM技术。
1)RTM,树脂传递模塑。
该技术源自聚氨酯技术,成型时关闭模具,向预制件中注入树脂,玻纤含量低,约20-45%。
2)VARIT,真空辅助树脂传递注塑。
该技术利用真空把树脂吸入预制件中,同时也可压入树脂,真空度约10-28英寸汞柱。
3)VARTM,真空辅助树脂传递注塑。
制品孔隙一般较少,玻纤含量可增高。
4)VRTM,真空树脂传递模塑。
5)VIP,真空浸渍法。
6)VIMP,可变浸渍塑法。
树脂借助真空或自重移动,压实浸渍。
7)TERTM,热膨胀RTM。
在预制件中插入世材,让树脂浸渍并对模具与成形品加热。
芯材受热膨胀,压实铺层。
利用这种压实作用,结合表面加压成型。
8)RARTM,橡胶辅助RTM。
在TERTM方法中不用芯材而用橡胶代之。
橡胶模具压紧成型品,使孔隙大大减少,玻纤含量可高达60-70%。
9)RIRM,树脂注射循环模塑。
真空与加压结合,向多个模具交替注入树脂,使树脂循环,直至预制件被充分浸透。
10)CIRTM,Co-Injection RTM。
共注射RTM,可注入几种不同的树脂,也可使用几种预制件,可利用真空袋和柔性表面的模具。
11)RLI,树脂液体浸(渗)渍。
RTM技术工艺详解
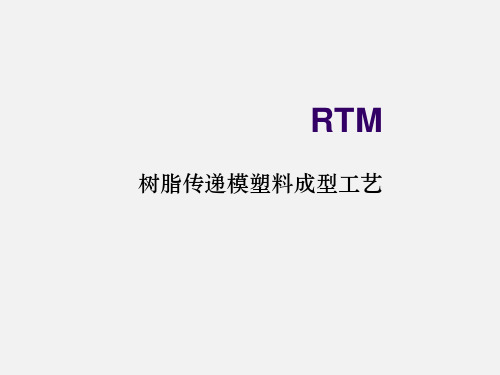
增强材料
由于在RTM成型过程中,增强材料在模具型腔 中要经过带压树脂流动充模过程,会带动或充 散纤维,造成制品出现“冲浪”或“跑道”现 象。因此,为保证制品质量,RTM工艺适用于 采用长纤维和连续纤维织物作为增强材料
工艺因素
影响RTM工艺的因素
VARTM(真空辅助RTM)工艺
一般RTM工艺在树脂注入时,模具型腔内可积起几吨压力。 通过使用了真空,模具内形成这种压力的趋势得到了减少, 因而增加了使用更轻模具的可能性,真空的使用也可提高 玻璃纤维的含量,而且有助于树脂对纤维的浸渍。纤维含 量可达65%以上,空隙率小于2%。
VARTM工艺过程
ห้องสมุดไป่ตู้合模
注射树脂
RTM – 脱模
RTM的优点
无需胶衣涂层即可为 构件提供光滑表面, 能制造出具有良好表 面的高精度复杂制品
模具制造及选材灵 活性大,设备及模 具投资小,产品只 需做小的修边
产品铺层过程中 可加入嵌件及对 局部进行加强
制品纤维含量高, 空隙率低(<0.2%)
成型过程中挥发物少, 车间环境及气味较好
在制作高质量RTM制品时,会让出口流出一定 量的树脂以后才结束充模。
目的是改善树脂对纤维的浸渍程度及排出微观 气泡。即改善了纤维与树脂的物理结合强度, 又改善了制品的密实程度。
一般浪费树脂量可达模制品重量的1/3~2/3。
注胶压力
压力的高低决定模具的材料要求和结构设计, 高压力需要高强度、高刚度和大的合模力。
基体树脂
室温或工作温度下具有低的粘度(小于1.0Pas) 及一定长的适用期
树脂对增强材料具有良好的浸润性、匹配性、 粘附性
树脂在固化温度下具有良好的反应性且后处理 温度不应过高
RTM工艺及模具

轻质RTM工艺及模具制作一.轻质RTM成型工艺原理及技术特点1.工艺原理轻质RTM就是真空辅助带压低粘度树脂在闭合模具中流动浸润增强材料并固化成型的一种工艺技术,其成型压力不足1kg/cm2。
树脂和固化剂通过注射机计量泵按配比输出带压液体在静态混合器中混合均匀,然后在真空辅助下注入已合理铺放好的纤维增强体的闭合模中,模具用真空对周边进行密封和合模,并保证树脂流动顺畅,然后进行固化。
该工艺需要二级真空,第一级真空(真空度为667毫米汞柱)完成上下模的闭合动作,第二级真空(真空度为376毫米汞柱)在树脂注射过程中辅助树脂的流动和对增强材料的浸润。
2.技术特点轻质RTM具有很多传统RTM相似的优点,比如生产效率和产品质量可以得以提高;可以得到两面光,大尺寸的产品;减少树脂有害成份对人体和环境的毒害。
由于轻质RTM是低压真空辅助成型工艺,所以与传统RTM相比,模具制作工艺大大简化,既方便又快捷。
模具无需如传统RTM那样进行钢结构的加强,下模为三明治夹芯结构,具有较高的刚度以防止树脂在注射过程中模具产生任何变形,同时三明治夹芯结构可以有效保存产品固化时产生的热量,有利于后续产品的快速固化,缩短生产周期。
而上模更为简单,可作成轻质、半刚性的结构,这样非常有利于频繁的脱模、合模的操作。
二.模具的制作1.模具制作环境的要求以及原料的选择a.环境环境温度:理想的范围为25±3℃。
相对湿度:不能大于60%。
制作车间:应保持比产品生产区更高的清洁度与日常维护。
b.材料对于该工艺所需要的材料我们推荐如下:①主要材料胶衣:ccp-071(具有优良的耐热能力,HDT为160-173℃)模具树脂:RM2000(快速固化,快速制造模具,低收缩,降低模具成本)F-010(环氧改性乙烯基树脂,良好的强度和耐热性,以及低收缩率)表面毡:300g/m2无碱短切毡:450g/m2轻木:用于提高模具的刚性并减轻重量蜡片:用于控制模腔的厚度,良好的厚度均匀性。
rtm工艺技术
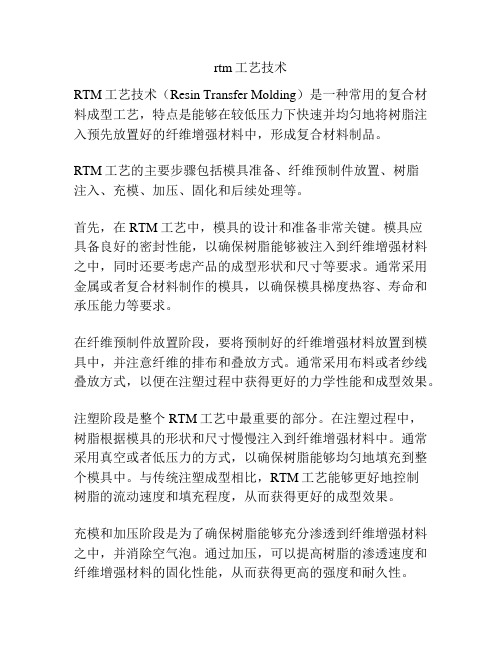
rtm工艺技术RTM工艺技术(Resin Transfer Molding)是一种常用的复合材料成型工艺,特点是能够在较低压力下快速并均匀地将树脂注入预先放置好的纤维增强材料中,形成复合材料制品。
RTM工艺的主要步骤包括模具准备、纤维预制件放置、树脂注入、充模、加压、固化和后续处理等。
首先,在RTM工艺中,模具的设计和准备非常关键。
模具应具备良好的密封性能,以确保树脂能够被注入到纤维增强材料之中,同时还要考虑产品的成型形状和尺寸等要求。
通常采用金属或者复合材料制作的模具,以确保模具梯度热容、寿命和承压能力等要求。
在纤维预制件放置阶段,要将预制好的纤维增强材料放置到模具中,并注意纤维的排布和叠放方式。
通常采用布料或者纱线叠放方式,以便在注塑过程中获得更好的力学性能和成型效果。
注塑阶段是整个RTM工艺中最重要的部分。
在注塑过程中,树脂根据模具的形状和尺寸慢慢注入到纤维增强材料中。
通常采用真空或者低压力的方式,以确保树脂能够均匀地填充到整个模具中。
与传统注塑成型相比,RTM工艺能够更好地控制树脂的流动速度和填充程度,从而获得更好的成型效果。
充模和加压阶段是为了确保树脂能够充分渗透到纤维增强材料之中,并消除空气泡。
通过加压,可以提高树脂的渗透速度和纤维增强材料的固化性能,从而获得更高的强度和耐久性。
固化阶段是将树脂完全固化,使纤维增强材料和树脂成为一个整体。
通常采用热固化或者光固化的方式,通过加热或者紫外线照射等方法,使树脂固化并与纤维增强材料牢固地结合在一起。
固化后的制品具有较高的强度、刚度和耐腐蚀性能,适用于各种工程应用。
最后,进行后续处理,如切割、修整、表面处理和涂装等,以获得符合要求的最终产品。
总之,RTM工艺技术是一种先进的复合材料成型工艺,具有成型效果好、成本低、产量高的优点。
通过合理选择纤维增强材料和树脂、优化模具设计、精确控制注塑和固化参数等,可以生产出符合要求的复合材料制品。
随着科学技术的不断发展,RTM工艺技术也将在航空航天、汽车工业、建筑业和体育用品等领域得到广泛应用。
rtm成型工艺在天线罩成型中的应用

RTM成型工艺在天线罩成型中的应用1. 应用背景天线罩是指用于保护和隔离天线的外壳,以提供对天线的机械保护和电磁屏蔽。
传统的天线罩制造工艺包括金属加工、注塑成型等,但这些方法存在一些局限性,如加工周期长、重量较大、成本较高等。
为了解决这些问题,RTM(Resin Transfer Molding)成型工艺被广泛应用于天线罩的制造中。
RTM是一种闭模复合材料成型技术,它通过将预浸料浸渍在纤维增强材料上,然后将其放置在封闭模具中,在模具内施加压力和温度来固化树脂,并形成最终产品。
相比传统方法,RTM成型工艺具有高效、低成本、质量稳定等优势,因此被广泛应用于各种领域,包括航空航天、汽车、电子设备等。
2. 应用过程RTM成型工艺在天线罩制造中的应用过程可以分为以下几个步骤:2.1 模具制备首先,根据天线罩的设计要求,制作一个与其形状和尺寸相匹配的模具。
模具通常由金属或复合材料制成,具有高温和高压的耐受能力。
模具的表面应光滑,以确保最终产品的外观质量。
2.2 纤维预浸料准备在RTM成型工艺中,纤维预浸料是关键材料之一。
预浸料是一种事先浸渍了树脂的纤维增强材料。
它可以是玻璃纤维、碳纤维等不同类型的纤维。
预浸料在制造过程中提供了强度和刚度,并且可以根据需要进行定制。
2.3 浸渍将事先准备好的纤维预浸料放置在模具中,并通过施加真空或压力来使树脂充分渗透到纤维增强材料中。
这个过程被称为浸渍。
浸渍后,纤维预浸料将变得湿润,并且包含足够的树脂以实现固化。
2.4 固化在完成浸渍后,将模具放置在热压机或烤箱中,施加适当的温度和压力来促进树脂的固化。
固化过程中,树脂会发生化学反应,形成坚固的结构。
根据具体的树脂系统和天线罩的要求,固化时间可能会有所不同。
2.5 后处理一旦天线罩完成固化过程,可以将其从模具中取出,并进行必要的后处理。
后处理可能包括去除模具残留物、修剪边缘、打磨表面等步骤,以确保最终产品符合设计要求。
3. 应用效果RTM成型工艺在天线罩制造中的应用具有以下优势和效果:3.1 重量轻相比传统金属加工方法,RTM成型工艺使用纤维增强材料和轻质树脂制造天线罩,从而使其重量大大减轻。
RTM成型工艺
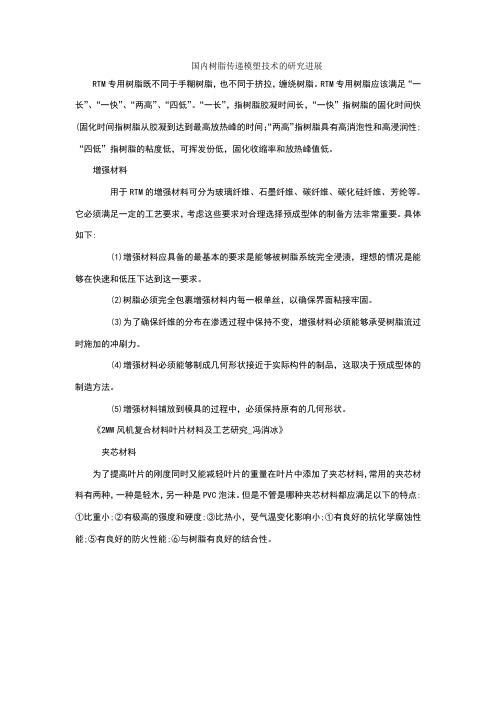
国内树脂传递模塑技术的研究进展
RTM专用树脂既不同于手糊树脂,也不同于挤拉,缠绕树脂。
RTM专用树脂应该满足“一长”、“一快”、“两高”、“四低”。
“一长”,指树脂胶凝时间长,“一快”指树脂的固化时间快(固化时间指树脂从胶凝到达到最高放热峰的时间;“两高”指树脂具有高消泡性和高浸润性;“四低”指树脂的粘度低,可挥发份低,固化收缩率和放热峰值低。
增强材料
用于RTM的增强材料可分为玻璃纤维、石墨纤维、碳纤维、碳化硅纤维、芳纶等。
它必须满足一定的工艺要求,考虑这些要求对合理选择预成型体的制备方法非常重要。
具体如下:
(1)增强材料应具备的最基本的要求是能够被树脂系统完全浸渍,理想的情况是能够在快速和低压下达到这一要求。
(2)树脂必须完全包裹增强材料内每一根单丝,以确保界面粘接牢固。
(3)为了确保纤维的分布在渗透过程中保持不变,增强材料必须能够承受树脂流过时施加的冲刷力。
(4)增强材料必须能够制成几何形状接近于实际构件的制品,这取决于预成型体的制造方法。
(5)增强材料铺放到模具的过程中,必须保持原有的几何形状。
《2MW风机复合材料叶片材料及工艺研究_冯消冰》
夹芯材料
为了提高叶片的刚度同时又能减轻叶片的重量在叶片中添加了夹芯材料,常用的夹芯材料有两种,一种是轻木,另一种是PVC泡沫。
但是不管是哪种夹芯材料都应满足以下的特点:①比重小;②有极高的强度和硬度;③比热小,受气温变化影响小;①有良好的抗化学腐蚀性能;⑤有良好的防火性能;⑥与树脂有良好的结合性。
RTM成型工艺学习资料
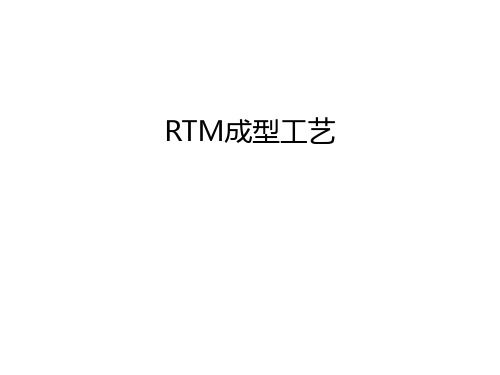
RTM-脱模
分离上下模
把产品与模具分离
RTM-检验
检查 产品 有无 缺陷、 模具 有无 损坏
产品展示
谢谢!
此课件下载可自行编辑修改,仅供参考! 感谢您的支持,我们努力做得更好!谢谢
合模类型
上下模完全靠螺栓锁 紧至上下定位销完全吻合
定位销完全吻合
油缸或气缸举升下模与上模合模
半圆支架可以使 上模360度旋转
油缸举升上模, 并限位
铰链式搭扣合模
铰链 搭扣紧固
铰链
油缸举升上模, 并限位
注胶口和排气口的位置
1、中心注入 2、四周注入
四周浇注可以比中心浇注充模时间减少60%以上,孔隙率可 以比之降低25%以上,同时也能提高一定的力学性能。 另外还有真空辅助和充模时间的控制。
模具的密封
密封是整个模具制作过程中较为关键的一步,根 据产品大小结构的不同大致分为以下7种方法: 矩形密封、半圆形密封、蘑菇形密封、半圆形+V 型两道密封、圆形真空密封、圆形充气密封、半 圆形两道密封。
矩形密封
半圆形密封
圆形真空密封
半圆形+V型两道密封
RTM工艺简介
RTM是先将增强织物置于模具中形成一定 的形状,再将树脂注射进入模具、浸渍纤维并 固化的一种复合材料生产工艺,是FRP的主要 成型工艺之一。其最大特点是污染小,为闭模 操作系统,另外在制品可设计性、可方向性增 强、制品综合性能方面优于SMC、BMC。
把胶衣均与涂刷到模具内表 面,不得有透光、流挂、堆 积现象
根据当日气温情况 加入适量固化剂, 搅拌均匀
RTM-铺层
修掉多余的边角料
根据产品制作工艺把相应的毡、 布铺放在模具面上
RTM-合模
rtm工艺流程
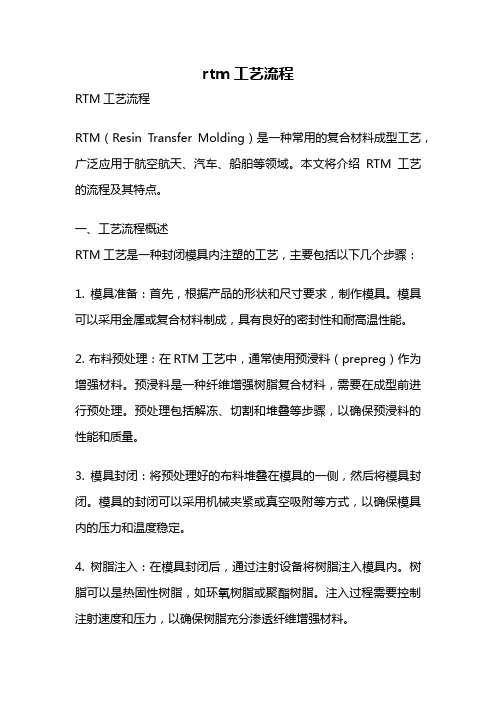
rtm工艺流程RTM工艺流程RTM(Resin Transfer Molding)是一种常用的复合材料成型工艺,广泛应用于航空航天、汽车、船舶等领域。
本文将介绍RTM工艺的流程及其特点。
一、工艺流程概述RTM工艺是一种封闭模具内注塑的工艺,主要包括以下几个步骤:1. 模具准备:首先,根据产品的形状和尺寸要求,制作模具。
模具可以采用金属或复合材料制成,具有良好的密封性和耐高温性能。
2. 布料预处理:在RTM工艺中,通常使用预浸料(prepreg)作为增强材料。
预浸料是一种纤维增强树脂复合材料,需要在成型前进行预处理。
预处理包括解冻、切割和堆叠等步骤,以确保预浸料的性能和质量。
3. 模具封闭:将预处理好的布料堆叠在模具的一侧,然后将模具封闭。
模具的封闭可以采用机械夹紧或真空吸附等方式,以确保模具内的压力和温度稳定。
4. 树脂注入:在模具封闭后,通过注射设备将树脂注入模具内。
树脂可以是热固性树脂,如环氧树脂或聚酯树脂。
注入过程需要控制注射速度和压力,以确保树脂充分渗透纤维增强材料。
5. 固化成型:树脂注入后,需要进行固化过程。
固化可以通过热固化或光固化等方式进行。
固化时间和温度需要根据树脂的性质和产品要求进行控制。
6. 模具开启:在树脂固化后,打开模具,取出成型件。
成型件具有优良的力学性能和表面质量。
二、RTM工艺的特点RTM工艺相比其他成型工艺具有以下特点:1. 成型件质量高:由于RTM工艺采用封闭模具,可以有效控制树脂的渗透和固化过程,从而获得高质量的成型件。
2. 复杂形状成型:RTM工艺适用于复杂形状的产品制造,可以满足各种工程要求。
3. 纤维含量高:RTM工艺可以实现高纤维含量的复合材料制造,提高产品的强度和刚度。
4. 自动化程度高:RTM工艺可以实现自动化生产,提高生产效率和一致性。
5. 环保节能:RTM工艺中的树脂可以回收再利用,减少了废料的产生,符合环保要求。
总结:RTM工艺是一种先进的复合材料成型工艺,具有高质量、适用于复杂形状、高纤维含量、自动化程度高和环保节能等特点。
rtm成型工艺技术

rtm成型工艺技术RTM(Resin Transfer Molding)成型工艺技术是一种在复合材料制造中常用的工艺技术,通过将预浸料注入模具中,使其在高压下固化成型。
以下是关于RTM成型工艺技术的详细介绍。
RTM成型工艺技术是一种集注塑成型和压缩成型为一体的复合材料成型工艺。
该工艺以模具为基础,通过将环氧树脂及其增强材料预浸料注入模具中,并施加一定的压力,使预浸料在模具内部充分浸透并固化。
与传统成型工艺相比,RTM成型具有高成型质量、高成型效率、低成本和环保等优点。
RTM成型工艺技术可以应用于各种复合材料制品的生产,特别是结构性和高强度要求的制品。
例如,飞机、汽车、船舶、建筑等领域的复合材料零部件都可以采用RTM成型工艺进行制造。
此外,RTM工艺还可以灵活地生产各种复材件,如复材齿轮、复材托架等。
RTM成型工艺的关键是模具的设计和制造。
模具必须具备良好的密封性和耐压性能,以确保预浸料在注入过程中不会泄漏。
此外,模具的开关设计也很重要,以确保成品能够顺利脱模。
因此,模具的制造需要高精度的加工和高耐磨的材料。
RTM成型工艺的关键步骤包括预浸料的配料、模具的准备、预热和注射、压力施加和固化等。
在制造过程中,预浸料需要在一定的温度下预热,以改善流动性并减少预浸料中的空气。
然后,预热的预浸料通过注射设备注入到模具中,同时施加一定的压力以保证预浸料充分浸透。
最后,固化过程中,通过加热或其他方法使预浸料固化,并获得最终产品。
RTM成型工艺技术具有许多优点。
首先,由于采用了大型模具和注射设备,RTM工艺可以高效地进行大规模生产,提高生产效率。
其次,由于预浸料中的树脂是事先注入的,可以较好地控制纤维的含量和取向,从而使得制品具有更高的强度和刚度。
此外,由于预浸料中的树脂经过事先预热,因此也能在注入过程中更好地充满空气孔隙,减少产品的缺陷率。
然而,RTM成型工艺也存在一些挑战和限制。
首先,由于需要大型模具和注射设备,设备投资和生产成本相对较高。
rtm成型工艺过程

rtm成型工艺过程
RTM(Resin Transfer Molding)是一种常用的复合材料成型工艺,主要用于生产复材零部件。
RTM成型工艺包含以下几个步骤:
1.模具制备:根据产品的设计要求,制作适用于RTM成型的模具。
通常使用金属或者复合材料制造的模具。
2.面层制备:将预浸料(prepreg)或者无纺布等面层材料剪裁成所需形状和尺寸。
3.模具装备:将面层材料放置在模具的一侧,保持模具清洁。
4.预制:将需要使用的纤维束定位在模具中,并按照设计要求进行预配置,通常采用预定位工具如夹具等,以确保纤维束的定位精准。
5.闭模:将两半模具闭合,并确保模具密封。
通常采用安全和可控的方法进行模具闭合,以防止树脂泄漏。
6.树脂注入:在成型开始前,通过开启充注阀门,将树脂注入模具中。
注入时使用低压或者真空吸引树脂进入纤维束,以确保树脂充分浸润纤维。
7.充注:树脂在模具内浸润纤维的过程中,需要保持一定的注入压力和速度,以确保树脂充分填充整个模具。
8.固化:树脂在充注完成后开始固化。
根据树脂的性质和设计要求,可以通过提高温度、加热模具或者添加固化剂等方法来促进树脂的固化。
9.开模:待树脂完全固化后,打开模具,取出成型件。
10.修整:对成型件进行修整,如去除多余的材料、修整边缘等。
RTM成型工艺

作者:京华RTM 工艺具有成型性好,增强材料和基体树脂的复合自由度宽,并能改善操作环境等特点,并且没有有机溶剂和玻璃纤维的挥散问题。
但由于该工艺方法,所用的增强材料在放入成形模前,必须进行预成形,因此该工艺方法普及得比较晚。
为了解决增强材料的预成形问题,国外正在开发各种预成形技术甚至开发不需要预成形的RTM方法。
这些改良型RTM法,不但可大幅度提高可操作性,并且能进一步改善操作环境。
本文将介绍日本富山县工业技术研究所开发的,能够提高生产能力的一种改良型的RTM方法。
改良型RTM方法的原理,是利用增强材料编织物具有较好的伸缩性,合模后,增强材料在模腔内可以自行伸长,并且封闭固定,以此来达到增强材料预成型的目的。
玻璃纤维、芳纶纤维、碳纤维等增强材料的增强性好,伸缩性低。
但其编织物本身具有伸缩性,因此可以用低伸缩性的纤维,纺织出具有伸缩性的布。
若将增材编织物,放入成型模的阴模上,然后固定其端部。
阳模合模后,增强材料在模腔内伸长成型,然后注入树脂,固化成型。
采用这种方法,可在任何形状的成形模内,封闭固定住增强材料,不会由于成形模的不同,而变更预成形设备,并且还能制成形状较为复杂的玻璃钢制品。
一般来讲,编织物纤维束的构造,对其伸缩性有较大的影响,根据纤维束的方向,可将编织物分为横编和纵编两大类。
家庭常用的编机均为横编机,毛衣、袜子等都属于横编类织物。
纵编需要纵丝的准备工作,生产机器很大,具有一定规模的工厂才能生产,比起横编,它的生产率较高。
目前生产速度最快的纵编编机,每分钟转数为2000转(一般编机每分钟为1.2转)。
纵编织物,不会出现象横编那样线的脱解问题。
对于RTM工艺所用的编织物,横编织、纵编织物都可以。
该改良型RTM方法,应用的是纵编织物。
纵编机能织出厚度为几毫米,到50毫米的半立体构造的织物。
这些编织物均可用作RTM的增强材料。
由于这种编织物不再需要叠层,用一张编织物即可成形,因而不存在增强材料的层间剥离现象。
rtm工艺和模压法

rtm工艺和模压法
RTM工艺是指树脂传输模塑工艺(Resin Transfer Molding),是一种用于复合材料制造的成型工艺。
在RTM工艺中,预先铺设好
的纤维增强材料(如玻璃纤维、碳纤维等)被放置在模具中,然后
通过负压将树脂注入到模具中,使得树脂浸透纤维增强材料,最终
形成所需的零件或构件。
RTM工艺通常用于制造复杂形状的零件,
具有成本低、生产周期短、成型精度高等优点。
而模压法是一种常见的塑料成型工艺,也被称为压缩成型。
在
模压法中,塑料颗粒被加热至熔化状态后,被注入到模具中,然后
施加压力使其充分填充模具并冷却固化,最终得到所需的塑料制品。
模压法适用于生产各种尺寸和形状的塑料制品,具有成本低、生产
效率高、制品密度均匀等优点。
从工艺原理来看,RTM工艺注重树脂的浸透和充填,适用于复
合材料的生产;而模压法则是通过加热塑料颗粒使其熔化后填充模具,适用于塑料制品的生产。
从应用领域来看,RTM工艺主要应用
于航空航天、汽车、船舶等领域,而模压法则广泛应用于塑料制品
制造行业。
总的来说,RTM工艺和模压法都是常见的成型工艺,它们各自适用于不同的材料和产品领域,具有各自独特的优点和适用范围。
rtm成型工艺流程

rtm成型工艺流程
RTM(Resin Transfer Molding)成型工艺流程是一种通过成型
覆膜技术,使用压力将预浸层纤维材料浸渍于合适的树脂中来制造复合材料制品的工艺。
RTM成型工艺流程一般包括以下几个步骤:
1. 制备模具:根据产品设计要求,制作出适合的模具。
模具可以包括一个或者多个腔室,根据产品的复杂程度决定。
2. 准备纤维预浸料:将纤维材料与树脂进行匹配,并将其浸泡在树脂中,以获取预浸层纤维材料。
3. 关闭模具:将两个模具部分合拢,确保密封。
4. 注入树脂:通过在模具中施加压力,将树脂从预先确定的入口注入模具中。
5. 充填纤维:随着树脂的注入,树脂会在模具中渗透纤维材料,充填整个模腔。
6. 固化树脂:当树脂注入完毕后,施加固化条件,例如温度和压力等,使树脂固化。
7. 模具开启:固化完毕后,打开模具,取出模具中的复合材料制品。
8. 整理和加工:对取出的复合材料制品进行必要的整理和加工,例如去除闪烁,修整边缘等。
RTM成型工艺可以生产具有较高性能和复杂形状的复合材料
制品。
由于该工艺的成本较低,制造周期较短,并且适用于大批量生产,因此在航空航天、汽车、建筑等领域得到了广泛应用。
rtm 工艺技术
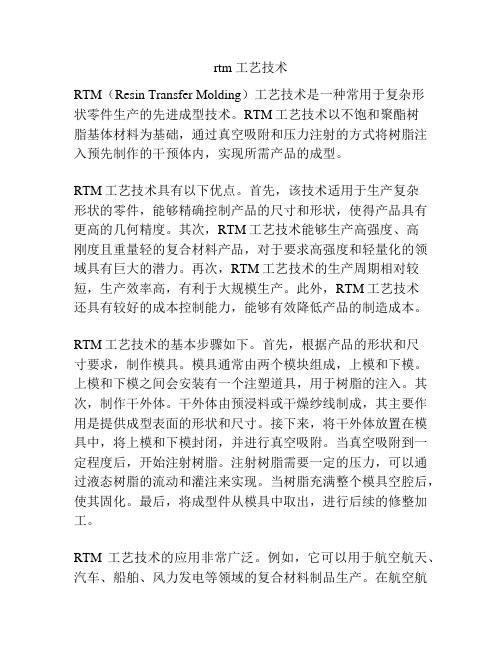
rtm 工艺技术RTM(Resin Transfer Molding)工艺技术是一种常用于复杂形状零件生产的先进成型技术。
RTM工艺技术以不饱和聚酯树脂基体材料为基础,通过真空吸附和压力注射的方式将树脂注入预先制作的干预体内,实现所需产品的成型。
RTM工艺技术具有以下优点。
首先,该技术适用于生产复杂形状的零件,能够精确控制产品的尺寸和形状,使得产品具有更高的几何精度。
其次,RTM工艺技术能够生产高强度、高刚度且重量轻的复合材料产品,对于要求高强度和轻量化的领域具有巨大的潜力。
再次,RTM工艺技术的生产周期相对较短,生产效率高,有利于大规模生产。
此外,RTM工艺技术还具有较好的成本控制能力,能够有效降低产品的制造成本。
RTM工艺技术的基本步骤如下。
首先,根据产品的形状和尺寸要求,制作模具。
模具通常由两个模块组成,上模和下模。
上模和下模之间会安装有一个注塑道具,用于树脂的注入。
其次,制作干外体。
干外体由预浸料或干燥纱线制成,其主要作用是提供成型表面的形状和尺寸。
接下来,将干外体放置在模具中,将上模和下模封闭,并进行真空吸附。
当真空吸附到一定程度后,开始注射树脂。
注射树脂需要一定的压力,可以通过液态树脂的流动和灌注来实现。
当树脂充满整个模具空腔后,使其固化。
最后,将成型件从模具中取出,进行后续的修整加工。
RTM工艺技术的应用非常广泛。
例如,它可以用于航空航天、汽车、船舶、风力发电等领域的复合材料制品生产。
在航空航天领域,复合材料产品具有高强度、高刚度、耐高温等特点,能够满足飞机零件对于性能要求的同时,减轻飞机自身的重量,提高燃油经济性和航空器的使用寿命。
在汽车领域,RTM工艺技术可以用于制作车身、底盘等零部件,使得汽车更轻、更稳定、更节能。
在船舶领域,RTM工艺技术可以制作船体、罩壳等结构件,提高船舶的承载能力和耐候性。
在风力发电领域,RTM工艺技术可以制作复合材料叶片,提高风力发电机组的效率。
总之,RTM工艺技术是一种先进的复合材料成型技术,通过树脂的注入和固化,可以生产出具有复杂形状、高强度、高刚度的复合材料产品。
rtm成型工艺过程
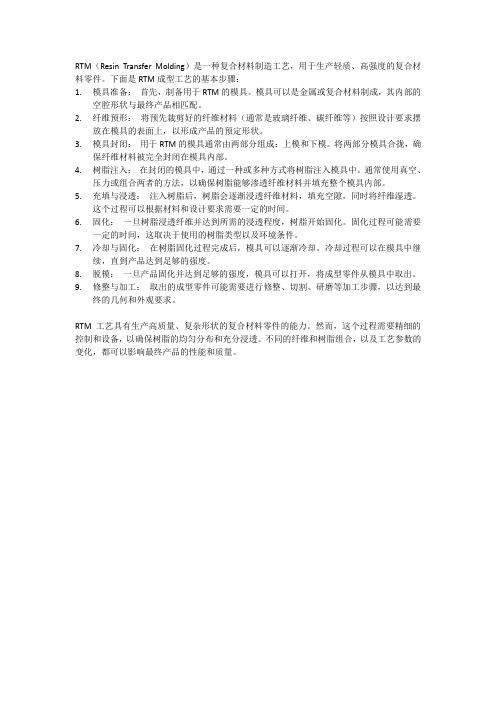
RTM(Resin Transfer Molding)是一种复合材料制造工艺,用于生产轻质、高强度的复合材料零件。
下面是RTM成型工艺的基本步骤:1.模具准备:首先,制备用于RTM的模具。
模具可以是金属或复合材料制成,其内部的空腔形状与最终产品相匹配。
2.纤维预形:将预先裁剪好的纤维材料(通常是玻璃纤维、碳纤维等)按照设计要求摆放在模具的表面上,以形成产品的预定形状。
3.模具封闭:用于RTM的模具通常由两部分组成:上模和下模。
将两部分模具合拢,确保纤维材料被完全封闭在模具内部。
4.树脂注入:在封闭的模具中,通过一种或多种方式将树脂注入模具中。
通常使用真空、压力或组合两者的方法,以确保树脂能够渗透纤维材料并填充整个模具内部。
5.充填与浸透:注入树脂后,树脂会逐渐浸透纤维材料,填充空隙,同时将纤维湿透。
这个过程可以根据材料和设计要求需要一定的时间。
6.固化:一旦树脂浸透纤维并达到所需的浸透程度,树脂开始固化。
固化过程可能需要一定的时间,这取决于使用的树脂类型以及环境条件。
7.冷却与固化:在树脂固化过程完成后,模具可以逐渐冷却。
冷却过程可以在模具中继续,直到产品达到足够的强度。
8.脱模:一旦产品固化并达到足够的强度,模具可以打开,将成型零件从模具中取出。
9.修整与加工:取出的成型零件可能需要进行修整、切割、研磨等加工步骤,以达到最终的几何和外观要求。
RTM工艺具有生产高质量、复杂形状的复合材料零件的能力。
然而,这个过程需要精细的控制和设备,以确保树脂的均匀分布和充分浸透。
不同的纤维和树脂组合,以及工艺参数的变化,都可以影响最终产品的性能和质量。
RTM工艺
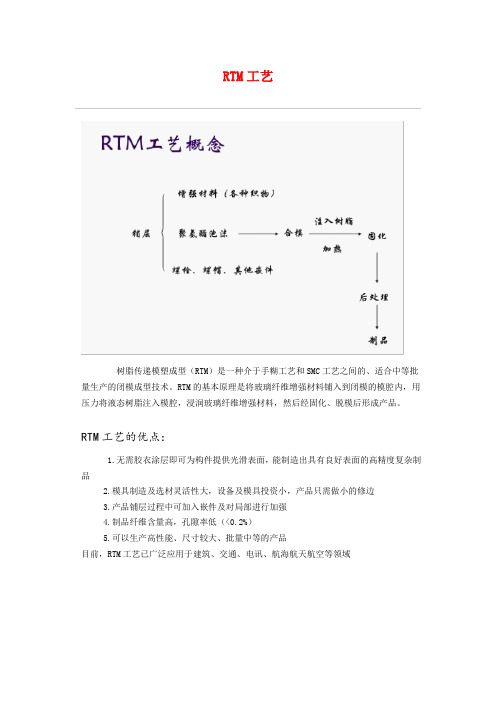
RTM工艺
树脂传递模塑成型(RTM)是一种介于手糊工艺和SMC工艺之间的、适合中等批量生产的闭模成型技术。
RTM的基本原理是将玻璃纤维增强材料铺入到闭模的模腔内,用压力将液态树脂注入模腔,浸润玻璃纤维增强材料,然后经固化、脱模后形成产品。
RTM工艺的优点:
1.无需胶衣涂层即可为构件提供光滑表面,能制造出具有良好表面的高精度复杂制品
2.模具制造及选材灵活性大,设备及模具投资小,产品只需做小的修边
3.产品铺层过程中可加入嵌件及对局部进行加强
4.制品纤维含量高,孔隙率低(<0.2%)
5.可以生产高性能、尺寸较大、批量中等的产品
目前,RTM工艺已广泛应用于建筑、交通、电讯、航海航天航空等领域
RTM模具、制品(高铁VIP座椅模具、制品):
高铁VIP座椅(扶手)上模高铁VIP座椅(扶手)下模
高铁VIP座椅高铁VIP座椅
地铁高压接线盒模具、制品:
地铁高压接线盒(盖板)模具地铁高压接线盒(底座)模具
地铁高压接线盒(防弧罩)模具
地铁高压接线盒制品
地铁高压接线盒制品
地铁高压接线盒制品。
RTM成型工艺

胶衣准备
铺层
合模
模具 准备
脱模
固化
树脂 注射
后处理
检验
制品
RTM成型工艺流程图
.
RTM-模具准备
1.检查模具有无缺损,并 用压缩空气把模具表面的 杂志清楚干净。注射口、 排气口设计是否合理。
2. 疏
进料口
通 进 料
口
和
排
气
口
是
重
.点
排气口
.
.
上 模
.
上 模
.
下 模
.
下 模
.
RTM-胶衣准备
定位销完全吻合
.
油缸或气缸举升下模与上模合模
半圆支架可以使 上模360度旋转
油缸举升上模, 并限位
.
铰链式搭扣合模并限位
注胶口和排气口的位置
1、中心注入 2、四周注入 四周浇注可以比中心浇注充模时间减少60%以上,孔隙率可 以比之降低25%以上,同时也能提高一定的力学性能。 另外还有真空辅助和充模时间的控制。
.
RTM-脱模
分离上下模
把产品与模具分离
.
RTM-检验
检查 产品 有无 缺陷、 模具 有无 损坏
.
产品展示
.
.
.
.
.
.
谢谢!
.
在RTM模具中限位销是控制产品的厚度和上下模吻合的
工具,目前根据模具的大小和应用范围大概分为锥形和
球形两种
锥形限位销
.
限位套(下摸用)
限位销(上模用)
.
球形限位销
.
限位套(下摸用)
限位销(上摸用)
.
紧固的方式通常有两种 1.搭扣紧固 2.螺栓紧固
- 1、下载文档前请自行甄别文档内容的完整性,平台不提供额外的编辑、内容补充、找答案等附加服务。
- 2、"仅部分预览"的文档,不可在线预览部分如存在完整性等问题,可反馈申请退款(可完整预览的文档不适用该条件!)。
- 3、如文档侵犯您的权益,请联系客服反馈,我们会尽快为您处理(人工客服工作时间:9:00-18:30)。
R TM 技 术 本 身 的革 新 在 持 续 进 行 ,而 另 一 方 面 还 出现 了 意 外 的动 向 。这 就 是 R M 与 T
其 它成 型方法 的结 合 。简而 言之 ,就是 以其它成 型方法 的设备 ( 例如 缠绕 机 、拉 挤机等 )
作 为预成 型设备 ,将制得的预制件 在 R M 模 具 中用 注入 的树脂迅速浸 渍成 型 。这可说是 当 T
今 F 成 型技 术 的 一 种 重 大 革 新 。 I
.
( 叶鼎 铨 摘 译 自 《 化 塑 料 》2 0 ,No9 强 01 .)
6.
Resn Li d nf i i gui I uson
可 注人 几 种 不 同 的树脂 ,也 可 使用 几 种 预制 件 。
可 利用 真空 袋 和有柔 软 表 面的模 具 。 在 下 模 内注 人 树 脂 ,放 人 预 制 件 后 覆 盖 上模 。
树 脂液体 渗渍
S CRI pr M M S e n ’ Co e ma n S mp st Re i I f so oi e sn nuin
R M 技 术 在 不 断 革 新 。 现在 ,若 周 游 欧 洲 的 F P工 厂 现 场 就 可 以 看 到 ,即 使 同样 使 用 T R
R M 技术 ,各公 司却都 有各 自的诀窍 。说得极 端一点 ,有 多少工 厂 ,就有 多少 种 R M 。 T T 在美 国也 是如此 。知名 专家 S o B cw t ctW.ek i t h博士在其 著作 《 树脂 传递模塑 》中论述 了 R M T
捻纱 横截面积 。
()这种方法既简便又 准确得 到单 向碳纤 维无捻布强度和 弹性模 量 。 3
参 考 文 献
1 王 善元 ,张 汝光 等.纤 维增 强复 合材 料 .中 国纺织 大学 出版 社 , 19 9 8年 1 月 1
C R M IT
RL I
C — jcinR M oI et n o T 共 注射 R M T
M ol i oc s d ng Pr es
加 热 并 用 热 压 釜 的 成 型 压 力 成 型 。加 热 使 树脂 粘度 降 低 ,流动 性好 ,易 于浸 透 。 专 利 方 。利 用 真 空 袋 使 树 脂 加 压 浸 渍 。浸 渍
速 度 快 ,面 积 广 。树 脂 在 预 制 件 的 厚 度 方 向也 能充 分 浸渍 。必 须使 用 真空 袋 和软 面模 具 。
西曼 复合 材料 公 司树脂 浸 渍模 塑法
UV RTM
U t — ilt Cue R M l aVoe ( r) T r
紫外 线 ( 固化 )R M T
与 S I CR MP 法相 似 , 固化 快 。必须 使 用 紫外 光 源 、能透 过 紫外 线 的真 空袋 和软 质模 具 。
维普资讯
玻 璃 钢
20 年 期 02 第3
各 式 各 样 的 RT 成 型 技 术 M
约 3 年前 ,从 事 F P 成 型 的人 士 常 用 “ 压 ” 注 塑 ”等 术 语 交 流 。而 今 天 ,他 们 0 R 模 、“
却几乎 每天埋头 于 R M、渗渍法这类技 术之 中。 T 目前 ,R M 技 术的位置居 于手糊法与 S T MC成 型法之间 。从经 济上 看 ,R M 适 合于 中 T 等规模 的生产 。从 苯 乙烯 挥发量着 眼 ,该技术作 为一种能 减少苯 乙烯 挥发量的闭模成 型法 , 在欧美 备受关注 。此 外 ,从 2 0世 纪末 开始 ,F P行业从 “ R 大量生产 ,大量消费 ”的时代转 向 “ 量 生 产 个 性 化 高 级 产 品 ”的 时 代 ,这 一 动 态 也 使 人 们 趋 向于 R M 这 种 成 型技 术 。 中 T
技 术 的各 种 形 式 ( 下 表 ) 见 。
( 下转第 6页 )
.
4 . 6
、
!
I
f
一 … … — _’一 ■■■’’ -
维普资讯
R : —50 3 0- 3 5 . 4 04 x l 0: 14% 0 .
—
—
—
—
j _)UU
尺 = —3 2 4 6- 2 0 . 3
x l 0 =1 7 % 0 .0
尺。 : : 二 :
15 .
×l 0o: 17%
.
式 中 尺 ——测 得的拉伸强度与技 术指标的相对差 ;
尺 m—— 测得的拉伸弹性模 量与技术指标 的相 对差 ; 估算 断裂延伸率与技 术指标的相对差 。
— —
可见 ,测得 的拉 伸强度 、拉 伸 弹性 模 量 以及 断裂延伸 率与该 单 向碳 纤维 无捻 布的技术 指标 相 吻合 。表明采用本文单 向碳纤维 无捻 布强度 和弹性模量测试 方法既简便 又准确 。
5 结 论
()把单向碳纤维无捻布和环氧树脂制成复合材料试样,测试出其拉伸破坏载荷和变形 。 1 ()又假设在单 向碳纤 维无 捻布 中某 根无 捻纱上任何地方 横截面都是等 横截面 ,每根无 2 捻 纱 横 截 面 都 相 同 。测 出 等 效 无 捻 纱 的 长 度 和 质 量 , 由碳 纤 维 密 度 得 到 碳 纤 维 无 捻 布 的 无