美军标Tests_System_Description_V20
美军标及国际防护标准简介

美军标及国际防护标准简介液体渗透防护侵入防护固体微粒防护海能达DMR对讲机可以耐受各种恶劣环境,比如极端的温度条件、跌落于仓库混凝土楼板,或需要防尘防湿的情况。
无论环境如何,海能达对讲机都可让您保持工作顺利进行,是您的最佳选择。
,所有海能达对讲机均采用美国军用标准 (MIL-STD) 及 IP 代码进行认证,您可以据此了解每种型号的坚固程度和防护等级。
那么,这些认证是什么?分别代表什么含义呢?MIL-STD-810美国MIL-STD-810 是为美国军方设计的一系列环境工程考量和实验室测试,用于测试设备在寿命期内各种预期使用条件下的环境设计及限制情况。
该标准还制定了模拟设备所受环境影响的测试方法。
MIL-STD-810 不禁旨在根据装备系统性能要求,提供切实可行的装备设计和测试方法。
虽然该标准最初用于军事应用,但现在也常常用于商业产品。
MIL-STD-810 已为商业对讲机行业广泛采用,为客户提供易于理解的评级系统,并使用独立的测试方法,确保可靠的对讲机环境性能和耐用性。
MIL-STD-810 标准指南和测试方法旨在:● 确定环境应力顺序、耐受度和设备寿命等级● 用于制定适合设备及其环境寿命的分析和测试标准● 评估环境应力寿命周期下的设备性能● 发现设备设计、材料、制造工艺、包装技术和维护方法的缺陷和不足● 体现产品的合规性。
MIL-STD-810 涵盖各种环境条件,包括:低压高度测试;高温、低温及热震试验(工作及存储);雨雪环境试验(包括大风和冻雨情况);湿度、霉菌、盐雾防锈测试;沙尘暴露;爆炸性气体环境;泄漏;加速度;冲击和运输冲击;炮振;以及随机振动。
在对讲机行业内,MIL-STD-810 常用于测试和指示对讲机对温度、跌落、冲击和振动的耐受程度。
IP 等级IP 代码(国际防护或异物防护)由国际电工委员会(IEC) 制定,“划分了机械和电子设备对异物入侵(如手和手指等身体部位)、灰尘、意外接触和液体渗入的防护程度”。
美军标883的对应国内标准-概述说明以及解释
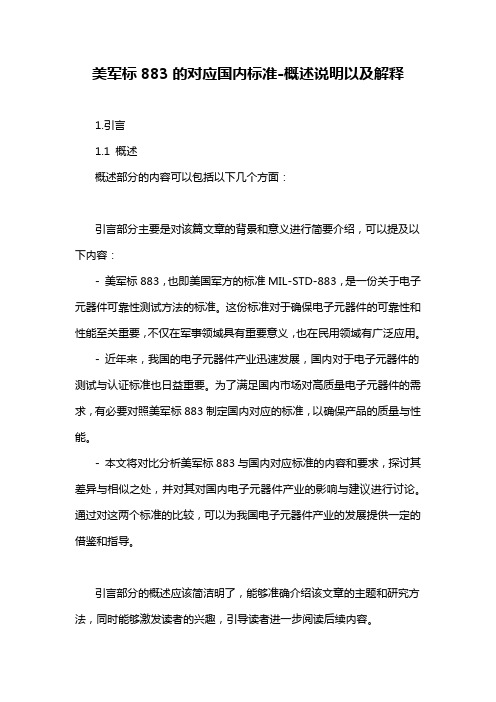
美军标883的对应国内标准-概述说明以及解释1.引言1.1 概述概述部分的内容可以包括以下几个方面:引言部分主要是对该篇文章的背景和意义进行简要介绍,可以提及以下内容:- 美军标883,也即美国军方的标准MIL-STD-883,是一份关于电子元器件可靠性测试方法的标准。
这份标准对于确保电子元器件的可靠性和性能至关重要,不仅在军事领域具有重要意义,也在民用领域有广泛应用。
- 近年来,我国的电子元器件产业迅速发展,国内对于电子元器件的测试与认证标准也日益重要。
为了满足国内市场对高质量电子元器件的需求,有必要对照美军标883制定国内对应的标准,以确保产品的质量与性能。
- 本文将对比分析美军标883与国内对应标准的内容和要求,探讨其差异与相似之处,并对其对国内电子元器件产业的影响与建议进行讨论。
通过对这两个标准的比较,可以为我国电子元器件产业的发展提供一定的借鉴和指导。
引言部分的概述应该简洁明了,能够准确介绍该文章的主题和研究方法,同时能够激发读者的兴趣,引导读者进一步阅读后续内容。
1.2文章结构文章结构部分的内容可以包括以下内容:文章结构部分的主要目的是介绍本文的组织结构和各个章节的内容,以便读者能够更好地理解和阅读文章。
本文分为引言、正文和结论三个部分。
第一部分是引言部分。
在引言部分,首先要对文章的主题进行概述,简要介绍美军标883以及国内对应的标准的背景和重要性。
其次,说明文章结构,即介绍各个章节的内容和安排。
最后,阐明本文的目的,即通过对比分析美军标883和国内对应标准的内容,探讨其差异和影响,并给出相关建议。
第二部分是正文部分。
在正文部分,首先要详细介绍美军标883的内容,包括其主要内容和要求。
可以列举一些关键点和具体规定,以帮助读者更好地理解。
然后,介绍国内对应的标准,包括其起草背景、内容和适用范围等方面。
可以结合实际案例和数据进行说明,以论证国内对应标准的有效性和实用性。
第三部分是结论部分。
美军无源射频识别标签数据格式分析

sc \ 8 \| \ 3 Sc 3
表6
限制 为9 位 , 6 即能用于全 球物 品惟一 识 别的编 码容量 为9位 , 6 其余 的存储 空 间不作 为物品识 别数 据 用 , 而是 用 于存储 用户 自 定义 的数据 。
需要 引起注 意 的是 美 军并没有 制定 有 关 射频 识 别标 签芯片 和读 写器等 硬 件方 面 的标准 , 这说 明美军对 设备方面 的标 准并不 关心。 主要 是 因为美 军 自己并 不生 产射频 这 识 别 的芯片 和 读 写器 等 硬 件 , 接 从市 场 直
标 签只 用于 价值 为5 0 美元 以上 的大型物 00 资、 装箱 、 集 托盘 和 装备 , 不用于小 件 物资
藉霾
阔 瀚
| |4 6
2
4 0
瘟 E P 襁 C
球 易 勇 s ) 应 删P标 贸 项 代码( N 供 商 三 签 G c
铃姜 赁 。 鼙饿
|8 4
6 4
供应 商 EC 全球 P 可回收资 产标识( A) G I R
供应商 EC 0 P 全球个人资产标识(if G A
军采 用通 用的E C 签和美 国防部专 P标
6
7 啦 曩
快 谪 EC P 快
全球个 产标t(I 人资 只G l A
8 | ≯
9 j 4 ‘ 6
移圣 E i 储 包 箱嘲 (e) £商 P 蒯 运 装 f s c e s
DD |姜 O 雷院 标整 数据雍梅 供应商 c 标 用Dl 签。 D
供应商 EC 系列储运包装箱代码fS c P Sc j
3 | |一6 4 5 。 9 6
MIL美国军用标准2010年最新目录

MIL美国军用标准标准2010年最新标准目录以下MIL美国标准化组织标准信息只供参考,具体情况,请咨询--中国标准信息网MIL-PRF-22684/8C (1) 2009.02.05 RESISTORS, FIXED, FILM, INSULATED, STYLE RL42鈥?TXMIL-PRF-19500/483D 2009.04.02 SEMICONDUCTOR DEVICE, SILICON, HIGH-POWER, THREE PHASE, FULL WAVE B RIDGE RECTIFIER, TYPES M19500/483-01 THROUGH M19500/483-04, JANTXMIL-PRF-27/111A 2009.09.29 TRANSFORMERS AND INDUCTORS, (AUDIO, POWER AND HIGH-POWER PULSE) INDU CTOR, AUDIOMIL-PRF-19500/169N 2009.11.02 SEMICONDUCTOR DEVICE, DIODE, SILICON, SWITCHING,TYPES 1N3070, 1N3070-1, 1N3070UR-1, 1N4938, 1N4938-1, 1N4938UR-1, JAN, JANTX, JANTXV, JANHC, AND JANKCMIL-PRF-27/79A 2009.11.09 TRANSFORMERS, AUDIO FREQUENCYMIL-DTL-3943/129C 2010.01.08 DECORATION, EXCEPTIONAL ENGINEERING ACHIEVEMENT MEDAL, NASAMIL-DTL-3943/145D 2010.01.15 DECORATION, MERITORIOUS CIVILIAN SERVICE AWARD, DEFENSE INFORMATION S YSTEMS AGENCYMIL-DTL-3943/139C 2010.01.26 DECORATION, NATIONAL COMMUNICATI***** SYSTEMS MEDALMIL-DTL-3943/153B 2010.01.15 DECORATION, SPECIAL ASSIGNMENT AWARD, U.S. PUBLIC HEALTH SERVICEMIL-DTL-3943/186A 2010.03.26 MEDAL, ARMY OF CUBAN OCCUPATIONMIL-PRF-55629/5G 2010.03.10 CIRCUIT BREAKERS, MAGNETIC, UNSEALED TRIP-FREE, THREE POLE (0.2 TO 50 A MPERES)MIL-DTL-11589/493A 2010.04.30 RIBBON, EXCEPTIONAL CIVILIAN SERVICE AWARD, CIVILIAN PERSONNEL MANAGE MENT SERVICE, DEPARTMENT OF DEFENSEMIL-DTL-3943/138D 2010.01.08 DECORATION, EXCEPTIONAL ACHIEVEMENT MEDAL, NASAMIL-DTL-11484/80E 2008.09.30 LAPEL BUTTON, DISTINGUISHED SERVICE AWARD, DEFENSE CONTRACT AUDIT AG ENCYMIL-DTL-11589/583 2003.03.20 RIBBON, EXCEPTIONAL ADMINISTRATIVE ACHIEVEMENT MEDAL, NASAMIL-PRF-914/4B (3) 2010.02.05 RESISTOR NETWORK, FIXED, FILM, SURFACE MOUNT, 20-PIN, LEADLESS CHIP CA RRIER, NONESTABLISHED RELIABILITY AND ESTABLISHED RELIABILITY, STYLE RNS040ARMY MIL-PRF-32271/14 2008.10.30 BATTERY, NON-RECHARGEABLE, LITHIUMMIL-PRF-62546C 2010.01.26 SENSOR, FIRE, OPTICALMIL-DTL-3922/62D 2010.01.08 FLANGES, WAVEGUIDE (CHOKE) (ROUND, 8 HOLE (2 HOLES CENTERED HORIZONTA LLY, 2 HOLES CENTERED VERTICALLY))MIL-DTL-8878K (1) 2009.02.17 TURNBUCKLES, POSITIVE SAFETYING, GENERAL SPECIFICATION FORMIL-DTL-21617/27 VALID NOTICE 1 2008.04.30 Connector, Female Plug Electrical, Rectangular, Polarized Shell, Miniature Type, Mixed Socket Contacts (Style 016C)MIL-M-38510/123B VALID NOTICE 1 2009.02.26 Microcircuits, Linear, Cmos, Negative Logic, Analog Switch, Monolithic SiliconMIL-PRF-19500/624D 2009.06.18 SEMICONDUCTOR DEVICE, DARLINGTON TRANSISTOR, NPN, SILICON, HIGH-POWE R, TYPE 2N7370, JAN, JANTX, JANTXV, AND JANSDOD-A-15707D (2) 1989.01.25 ANCHORS, NAVY, LIGHTWEIGHT TYPE (METRIC)DOD-A-17254A 1985.08.23 ANCHORS, NAVY, LIGHTWEIGHT (HADFIELD MANGANESE CAST STEEL LOW MAGNETIC PERMEABILITY) (METRIC)DOD-A-82720 NOTICE 3 2004.11.23 ADHESIVE, MODIFIED-EPOXY, FLEXIBLE, TWO-PART (METRIC)DOD-C-2687B VALID NOTICE 1 1987.06.02 COMPOUND, BATTERY-SEALING (METRIC)DOD-C-82656 (2) 1978.11.15 CARBON BLACK,THERMALMIL-C-82656 1977.01.31 CARBON BLACK,THERMALDOD-C-82660 (1) 1978.03.01 CHROMIUM 2 ETHYL HEXOATE, TECHNICALMIL-C-82660 1977.01.31 CHROMIUM 2 ETHYL HEXOATE, TECHNICALDOD-C-82665 (1) 1978.11.15 CARBON BLACKMIL-C-82665 1977.01.31 CARBON BLACKDOD-D-23443B (2) 1995.10.27 DI-(2-ETHYLHEXYL) ADIPATE, TECHNICAL (METRIC)DOD-E-8983C VALID NOTICE 1 1992.09.04 ELECTRONIC EQUIPMENT, AEROSPACE, EXTENDED SPACE ENVIRONM ENT, GENERAL SPECIFICATION FORDOD-G-24508A (4) 1998.09.23 GREASE, HIGH PERFORMANCE, MULTIPURPOSE (METRIC)DOD-G-82673 (1) 1978.06.15 GRAPHITE, NATURAL, POWERED, TECHNICALMIL-G-82673 1977.11.23 GRAPHITE, NATURAL, POWERED, TECHNICALDOD-L-25681D VALID NOTICE 2 1991.05.01 LUBRICANT MOLYBDENUM DISULFIDE, SILICONEDOD-L-81846B (2) 2000.03.02 LUBRICATING OIL, INSTRUMENT, BALL BEARING, HIGH FLASH POINTMIL-P-63464/6B VALID NOTICE 1 2005.07.01 PIN, GROOVED, HEADLESS-LONGITUDINAL CENTER GROOVE, CORRO SION-RESISTANT STEEL, METRICMIL-P-63464/6B 1992.01.17 PIN, GROOVED, HEADLESS-LONGITUDINAL CENTER GROOVE, CORROSION-RESISTANT STEEL, METRICDOD-R-23679F 1986.08.08 REAGENTS, STANDARD, WATER TEST CHEMICALS (METRIC)DOD-STD-1399 -301A 1986.07.21 INTERFACE STANDARD FOR SHIPBOARD SYSTEMS SECTION 301A SHIP MOTION AND ATTITUDE (METRIC)DOD-T-17412C 1978.09.20 TEST KIT, WATER, ENGINE COOLING SYSTEMS (METRIC)DOD-T-82666A VALID NOTICE 1 1987.05.13 TRIS-1-(2 METHYL AZIRIDINYL) PHOSPHINE OXIDEDOD-Z-82674 NOTICE 1 1999.07.10 ZIRCONIUM CARBIDE, POWERED, TECHNICALMIL-Z-82674 1977.11.23 ZIRCONIUM CARBIDE, POWERED, TECHNICALMIL-A-159D VALID NOTICE 1 1999.07.14 ANTIMONY SULFIDE (FOR USE IN AMMUNITION)MIL-A-159D 1972.05.16 ANTIMONY SULFIDE (FOR USE IN AMMUNITION)MIL-A-166C VALID NOTICE 2 1999.07.13 AMMONIUM PICRATE (EXPLOSIVE D)MIL-A-166C 1975.01.06 AMMONIUM PICRATE (EXPLOSIVE D)MIL-A-192B VALID NOTICE 2 1999.08.18 AMMONIUM PERCHLORATEMIL-A-192B 1965.09.02 AMMONIUM PERCHLORATEMIL-A-417G VALID NOTICE 1 1988.10.24 ADAPTER, PRIMING, M1A4MIL-A-417G 1983.02.27 ADAPTER, PRIMING, M1A4MIL-A-516J 1981.09.01 AUGER, EARTH, SKIDMOUNTED; AND AUGER, EARTH, TURNTABLE BASE MOUNTED, POWE R DRIVENMIL-A-2334J 1991.03.15 APRON, TOXICOLOGICAL AGENTS PROTECTIVE, M-2MIL-A-3316C (2) 1990.08.23 ADHESIVES, FIRE-RESISTANT, THERMAL INSULATIONMIL-A-3316C 1987.10.20 ADHESIVES, FIRE-RESISTANT, THERMAL INSULATIONMIL-A-3850 VALID NOTICE 1 1986.04.10 ACETYLENE BLACKMIL-A-3850 1952.12.24 ACETYLENE BLACKMIL-A-3962E 1986.05.19 ANCHORS, GROUND, ARROWHEAD WITH DRIVING EQUIPMENTMIL-A-5034B VALID NOTICE 1 1987.03.02 ADAPTER, BOMB RACK, 30 INCH, AERO 1AMIL-A-5034B 1979.11.02 ADAPTER, BOMB RACK, 30 INCH, AERO 1AMIL-A-6752A REINST NOTICE 2 1978.03.01 AMMETERS, VOLTMETERS, AND LOADMETERS; DIRECT CURRENTMIL-A-6752A (3) 1958.03.03 AMMETERS, VOLTMETERS, AND LOADMETERS; DIRECT CURRENTMIL-A-6752A 1953.12.24 AMMETERS, VOLTMETERS, AND LOADMETERS; DIRECT CURRENTMIL-A-6848 VALID NOTICE 1 1955.12.06 ACCELEROMETER; AIRCRAFTMIL-A-6848 1950.08.21 ACCELEROMETER; AIRCRAFTMIL-A-7237B (1) 1981.05.19 AIR INDUCTION SYSTEM, RECIPROCATING ENGINE, GENERAL SPECIFICATION FOR MIL-A-7237B 1975.02.04 AIR INDUCTION SYSTEM, RECIPROCATING ENGINE, GENERAL SPECIFICATION FORMIL-A-7647C VALID NOTICE 2 1971.10.12 AIR CONDITIONER, TRAILER MOUNTED, FREON CYCLE, GASOLINE ENGI NE DRIVEN, 4 TON REFRIGERATING CAPACITY, TYPE A-3MIL-A-7647C 1958.08.22 AIR CONDITIONER, TRAILER MOUNTED, FREON CYCLE, GASOLINE ENGINE DRIVEN, 4 TO N REFRIGERATING CAPACITY, TYPE A-3MIL-A-8625F (1) 2003.09.15 ANODIC COATINGS FOR ALUMINUM AND ALUMINUM ALLOYSMIL-A-8625F 1993.09.10 ANODIC COATINGS FOR ALUMINUM AND ALUMINUM ALLOYSMIL-A-8860B 1987.05.20 AIRPLANE STRENGTH AND RIGIDITY, GENERAL SPECIFICATION FORMIL-A-8861B (1) 1994.12.05 AIRPLANE STRENGTH AND RIGIDITY FLIGHT LOADSMIL-A-8861B 1986.02.07 AIRPLANE STRENGTH AND RIGIDITY FLIGHT LOADSMIL-A-8863C 1993.07.19 AIRPLANE STRENGTH AND RIGIDITY GROUND LOADS FOR NAVY ACQUIRED AIRPLANES MIL-A-8865B 1987.05.20 AIRPLANE STRENGTH AND RIGIDITY MISCELLANEOUS LOADSMIL-A-8866C VALID NOTICE 1 1994.10.03 AIRPLANE STRENGTH AND RIGIDITY RELIABILITY REQUIREMENTS, REPEATED LOADS, FATIGUE AND DAMAGE TOLERANCEMIL-A-8866C 1987.05.20 AIRPLANE STRENGTH AND RIGIDITY RELIABILITY REQUIREMENTS, REPEATED LOADS, FA TIGUE AND DAMAGE TOLERANCEMIL-A-8867C VALID NOTICE 1 1994.10.03 AIRPLANE STRENGTH AND RIGIDITY GROUND TESTSMIL-A-8867C (1) 1993.03.25 AIRPLANE STRENGTH AND RIGIDITY GROUND TESTSMIL-A-8867C 1987.06.10 AIRPLANE STRENGTH AND RIGIDITY GROUND TESTSMIL-A-8869B VALID NOTICE 1 1994.06.20 AIRPLANE STRENGTH AND RIGIDITY NUCLEAR WEAP***** EFFECTSMIL-A-8869B 1987.05.20 AIRPLANE STRENGTH AND RIGIDITY NUCLEAR WEAP***** EFFECTSMIL-A-8870C 1993.03.25 AIRPLANE STRENGTH AND RIGIDITY VIBRATION, FLUTTER, AND DIVERGENCEMIL-A-9132 1953.11.02 AMPLIFIER, STABILIZATION, BOMBING NAVIGATIONAL COMPUTER, TYPE B-1MIL-A-9207B (1) 1956.04.20 ANALYZER, IGNITION AND VIBRATION, AIRCRAFT RECIPROCATING ENGINEMIL-A-9207B 1955.10.12 ANALYZER, IGNITION AND VIBRATION, AIRCRAFT RECIPROCATING ENGINEMIL-A-9410 (1) 1954.06.18 ANTENNAS, FM COMMUNICATION EQUIPMENT, GENERAL SPECIFICATION FOR DESIGN AND PLACEMENT OFMIL-A-9410 1954.04.05 ANTENNAS, FM COMMUNICATION EQUIPMENT, GENERAL SPECIFICATION FOR DESIGN AN D PLACEMENT OFMIL-A-9457A (1) 1959.04.27 AMPLIFIER, ELECTRONIC CONTROL, BOMBING NAVIGATIONAL COMPUTER, TYPE MD-1 MIL-A-9457A 1959.04.27 AMPLIFIER, ELECTRONIC CONTROL, BOMBING NAVIGATIONAL COMPUTER, TYPE MD-1 MIL-A-10516 1950.09.14 ADAPTER, SKATE TEST CLUSTER (100-LB. SIZE)MIL-A-10593A 1953.02.04 AIR SAMPLER MX-1191 ( )/TDQ-1MIL-A-10982F (1) 1969.04.01 ARMING WIRE ASSEMBLIESMIL-A-10982F 1968.08.19 ARMING WIRE ASSEMBLIESMIL-A-11221A NOTICE 2 1997.02.27 ARMING PLUG, MINE, ANTITANK M4 (PRACTICE) AND M4A1MIL-A-11221A VALID NOTICE 1 1988.05.20 ARMING PLUG, MINE, ANTITANK M4 (PRACTICE) AND M4A1MIL-A-11221A (2) 1964.02.14 ARMING PLUG, MINE, ANTITANK M4 (PRACTICE) AND M4A1MIL-A-11221A 1962.02.22 ARMING PLUG, MINE, ANTITANK M4 (PRACTICE) AND M4A1MIL-A-11356F 1987.05.22 ARMOR, STEEL, CAST, HOMOGENEOUS, COMBAT-VEHICLE TYPE (1/4 TO 8 INCHES, INCL USIVE)MIL-A-11557A 1954.08.09 ANTENNA ASSEMBLY AS-574( )/URR (COMPONENTS OF)MIL-A-13338E VALID NOTICE 1 1988.10.24 AIMING CIRCLE, M2 AND M2A2, WITH EQUIPMENTMIL-A-13338E (1) 1983.08.11 AIMING CIRCLE, M2 AND M2A2, WITH EQUIPMENTMIL-A-13338E 1982.03.22 AIMING CIRCLE, M2 AND M2A2, WITH EQUIPMENTMIL-A-13374E NOTICE 4 1998.03.03 ADHESIVE, DEXTRIN, FOR USE IN AMMUNITION CONTAINERSMIL-A-13374E REINST NOTICE 3 1998.03.03 ADHESIVE, DEXTRIN, FOR USE IN AMMUNITION CONTAINERSMIL-A-13374E VALID NOTICE 1 1988.10.31 ADHESIVE, DEXTRIN, FOR USE IN AMMUNITION CONTAINERSMIL-A-13374E 1983.08.25 ADHESIVE, DEXTRIN, FOR USE IN AMMUNITION CONTAINERSMIL-A-13479 1954.06.18 ANEMOMETER ML-497( )/PMMIL-A-14178 1955.10.14 AMPLIFIER, AUDIO FREQUENCY AM-719( )/UMIL-A-14457 1957.12.31 ANTENNA AT-640( )/ARNMIL-A-14641B NOTICE 5 2001.07.21 AIGUILLETTE, AF COMMAND BANDSMIL-A-14641B 1981.06.30 AIGUILLETTE, AF COMMAND BANDSMIL-A-14897 NOTICE 2 1999.07.10 ACTUATOR, ROTARY 1000-34 ASSEMBLYMIL-A-14897 VALID NOTICE 1 1988.08.29 ACTUATOR, ROTARY 1000-34 ASSEMBLYMIL-A-14897 1969.07.20 ACTUATOR, ROTARY 1000-34 ASSEMBLYMIL-A-14898 NOTICE 2 1999.07.10 ACTUATOR, ROTARY 1000-34 REMANUFACTURED METAL PARTS ASSEMBLY MIL-A-14898 VALID NOTICE 1 1986.06.20 ACTUATOR, ROTARY 1000-34 REMANUFACTURED METAL PARTS ASSEM BLYMIL-A-14898 1969.07.20 ACTUATOR, ROTARY 1000-34 REMANUFACTURED METAL PARTS ASSEMBLYMIL-A-15303P 1986.11.19 AUDIBLE SIGNALS: ALARMS, BELLS, BUZZERS, HORNS, AND SIRENS, ELECTRONIC, SHIP BOARDMIL-A-15344J (2) 1990.11.02 AMPLIFIER, SYNCHRO SIGNALMIL-A-15344J 1963.06.07 AMPLIFIER, SYNCHRO SIGNALMIL-A-16749E (2) 1968.06.17 AMPLIFIER, AUDIO FREQUENCY, SOUND POWERED TELEPHONE SYSTEMMIL-A-16749E 1963.05.15 AMPLIFIER, AUDIO FREQUENCY, SOUND POWERED TELEPHONE SYSTEMMIL-A-17196E 1977.10.07 ALARM SWITCHBOARDS, ALARM PANELS, REMOTE SENTRY ALARM SWITCH, SIGNAL UN ITS, AND SPECIAL ALARM CONNECTION BOX, NAVAL SHIPBOARDMIL-A-17367D (1) 1978.09.11 ARMOR, BODY, FRAGMENTATION PROTECTIVE: UPPER TORSO (WITH COLLAR, M-195 5)MIL-A-17367D 1977.10.03 ARMOR, BODY, FRAGMENTATION PROTECTIVE: UPPER TORSO (WITH COLLAR, M-1955) NAVY MIL-A-18001K INT AMD 3 NOTICE 1 2008.08.28 ANODES, SACRIFICIAL ZINC ALLOYMIL-A-18194 1954.09.17 ATTACK DIRECTOR MARK 5 MOD 2MIL-A-18455C VALID NOTICE 1 1991.06.07 ARGON, TECHNICALMIL-A-18455C 1986.12.23 ARGON, TECHNICALMIL-A-18717C 1993.09.20 ARRESTING HOOK INSTALLATION, AIRCRAFTMIL-A-18924 1955.06.29 ARMING CELLS MK 1 MODS 5, 6, 7, AND 8MIL-A-19521B 1992.05.04 ANODE RETAINING SUPPORT PLUGS AND ANODE SELECTION AND INSTALLATION DESI GN CRITERIA FOR SHIPBOARD CONDENSERS AND HEAT EXCHANGERSMIL-A-19736A (2) 1966.03.16 AIR REFUELING SYSTEMS, GENERAL SPECIFICATION FORMIL-A-19736A 1960.08.05 AIR REFUELING SYSTEMS, GENERAL SPECIFICATION FORMIL-A-19865C 1990.03.20 AIR CONDITIONER, MECHANICALLY REFRIGERATEDMIL-A-19879B 1977.11.23 ARMOR, BODY, FRAGMENTATION PROTECTIVE: LOWER TORSOMIL-A-21016F 1990.05.21 ADHESIVE, RESILIENT DECK COVERINGMIL-A-21165A NOTICE 2 2004.08.23 ADAPTER, QUICK DISCONNECT, PASSENGER SEAT TO FLOORMIL-A-21165A 1965.08.27 ADAPTER, QUICK DISCONNECT, PASSENGER SEAT TO FLOORMIL-A-22262B (2) 1996.03.21 ABRASIVE BLASTING MEDIA SHIP HULL BLAST CLEANINGMIL-A-22262B 1993.04.05 ABRASIVE BLASTING MEDIA SHIP HULL BLAST CLEANINGMIL-A-23054A VALID NOTICE 1 1990.12.24 ACOUSTIC ABSORPTIVE BOARD, FIBROUS GLASS PERFORATED FIBRO US GLASS CLOTH FACEDMIL-A-23054A (1) 1984.06.25 ACOUSTIC ABSORPTIVE BOARD, FIBROUS GLASS PERFORATED FIBROUS GLASS CL OTH FACED。
美国军用标准
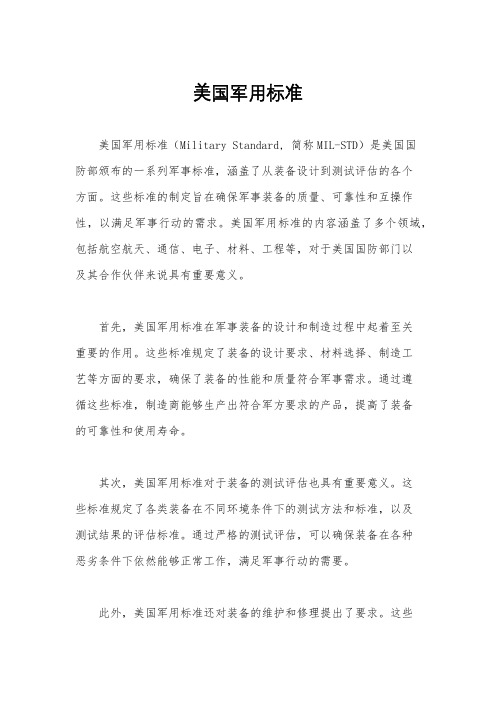
美国军用标准美国军用标准(Military Standard, 简称MIL-STD)是美国国防部颁布的一系列军事标准,涵盖了从装备设计到测试评估的各个方面。
这些标准的制定旨在确保军事装备的质量、可靠性和互操作性,以满足军事行动的需求。
美国军用标准的内容涵盖了多个领域,包括航空航天、通信、电子、材料、工程等,对于美国国防部门以及其合作伙伴来说具有重要意义。
首先,美国军用标准在军事装备的设计和制造过程中起着至关重要的作用。
这些标准规定了装备的设计要求、材料选择、制造工艺等方面的要求,确保了装备的性能和质量符合军事需求。
通过遵循这些标准,制造商能够生产出符合军方要求的产品,提高了装备的可靠性和使用寿命。
其次,美国军用标准对于装备的测试评估也具有重要意义。
这些标准规定了各类装备在不同环境条件下的测试方法和标准,以及测试结果的评估标准。
通过严格的测试评估,可以确保装备在各种恶劣条件下依然能够正常工作,满足军事行动的需要。
此外,美国军用标准还对装备的维护和修理提出了要求。
这些标准规定了装备的维护周期、维护方法、备件更换标准等,确保装备能够长期保持良好的工作状态。
同时,标准化的维护和修理流程也能够提高装备的可维护性,降低了维护成本,延长了装备的使用寿命。
总的来说,美国军用标准在军事装备的设计、制造、测试评估、维护修理等方面发挥着重要作用。
遵循这些标准能够确保装备的质量和可靠性,提高了装备在军事行动中的表现,保障了军事行动的顺利进行。
同时,这些标准也为美国国防部门和其合作伙伴提供了统一的标准,促进了军事装备的互操作性和国际间的合作。
总之,美国军用标准对于军事装备的设计、制造、测试评估、维护修理等方面都具有重要意义,对于确保军事装备的质量和可靠性起着至关重要的作用。
这些标准的制定和遵循,不仅提高了装备的性能和可靠性,也促进了国际间的军事合作和互操作性。
因此,美国军用标准在军事装备领域具有重要的地位和作用。
美国军用标准
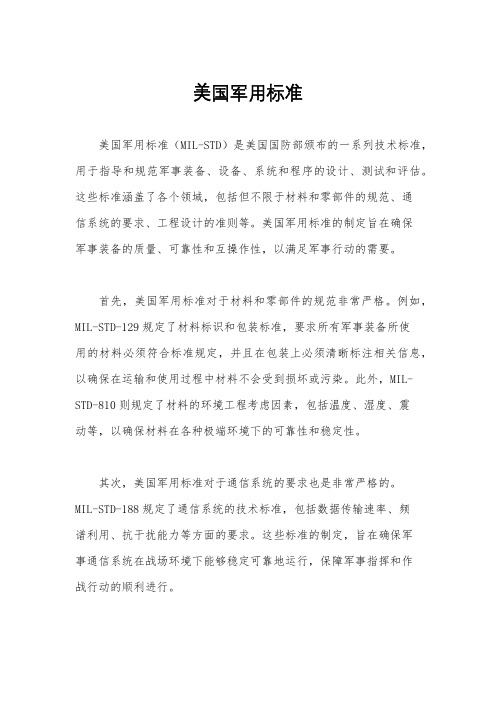
美国军用标准美国军用标准(MIL-STD)是美国国防部颁布的一系列技术标准,用于指导和规范军事装备、设备、系统和程序的设计、测试和评估。
这些标准涵盖了各个领域,包括但不限于材料和零部件的规范、通信系统的要求、工程设计的准则等。
美国军用标准的制定旨在确保军事装备的质量、可靠性和互操作性,以满足军事行动的需要。
首先,美国军用标准对于材料和零部件的规范非常严格。
例如,MIL-STD-129规定了材料标识和包装标准,要求所有军事装备所使用的材料必须符合标准规定,并且在包装上必须清晰标注相关信息,以确保在运输和使用过程中材料不会受到损坏或污染。
此外,MIL-STD-810则规定了材料的环境工程考虑因素,包括温度、湿度、震动等,以确保材料在各种极端环境下的可靠性和稳定性。
其次,美国军用标准对于通信系统的要求也是非常严格的。
MIL-STD-188规定了通信系统的技术标准,包括数据传输速率、频谱利用、抗干扰能力等方面的要求。
这些标准的制定,旨在确保军事通信系统在战场环境下能够稳定可靠地运行,保障军事指挥和作战行动的顺利进行。
另外,工程设计的准则也是美国军用标准的重要内容之一。
MIL-STD-1472规定了人因工程设计的要求,包括人体工程学、人机界面、工作环境等方面的规定,以确保军事装备的设计能够最大程度地适应人体特性和工作环境,提高操作效率和舒适性。
总的来说,美国军用标准的制定和执行,对于确保军事装备的质量和性能起到了至关重要的作用。
这些标准的严格要求和规范,不仅提高了军事装备的可靠性和稳定性,也为军事行动的成功提供了有力支持。
因此,对于军事装备的设计、制造和使用单位来说,严格遵守美国军用标准是至关重要的,只有这样才能确保装备的质量和性能达到国防部的要求,为国家安全和国防事业做出贡献。
美军标详解
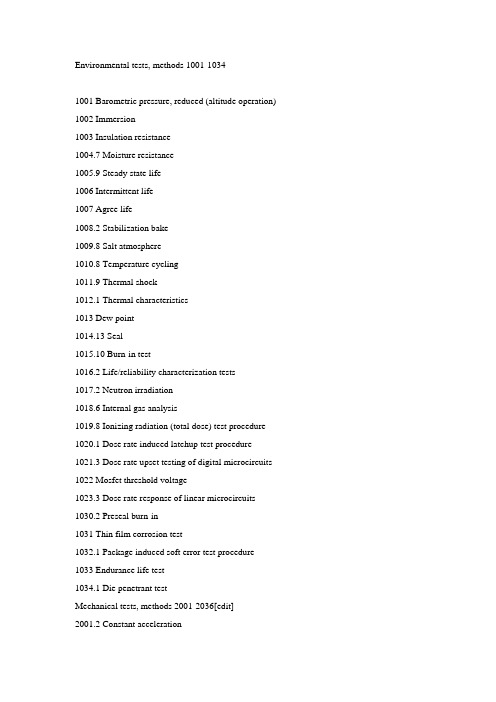
Environmental tests, methods 1001-10341001 Barometric pressure, reduced (altitude operation) 1002 Immersion1003 Insulation resistance1004.7 Moisture resistance1005.9 Steady state life1006 Intermittent life1007 Agree life1008.2 Stabilization bake1009.8 Salt atmosphere1010.8 Temperature cycling1011.9 Thermal shock1012.1 Thermal characteristics1013 Dew point1014.13 Seal1015.10 Burn-in test1016.2 Life/reliability characterization tests1017.2 Neutron irradiation1018.6 Internal gas analysis1019.8 Ionizing radiation (total dose) test procedure 1020.1 Dose rate induced latchup test procedure 1021.3 Dose rate upset testing of digital microcircuits 1022 Mosfet threshold voltage1023.3 Dose rate response of linear microcircuits 1030.2 Preseal burn-in1031 Thin film corrosion test1032.1 Package induced soft error test procedure 1033 Endurance life test1034.1 Die penetrant testMechanical tests, methods 2001-2036[edit]2001.2 Constant acceleration2002.3 Mechanical shock2003.7 Solderability2004.5 Lead integrity2005.2 Vibration fatigue2006.1 Vibration noise2007.2 Vibration, variable frequency2008.1 Visual and mechanical2009.9 External visual2010.10 Internal visual (monolithic)2011.7 Bond strength (bond pull test)2012.7 Radiography2013.1 Internal visual inspection for DPA2014 Internal visual and mechanical2015.11 Resistance to solvents2016 Physical dimensions2017.7 Internal visual (hybrid)2018.3 Scanning electron microscope (SEM) inspection of metallization 2019.5 Die shear strength2020.7 Particle impact noise detection test (PIND)2021.3 Glassivation layer integrity2022.2 Wetting balance solderability2023.5 Nondestructive bond pull2024.2 Lid torque for glass-frit-sealed packages2025.4 Adhesion of lead finish2026 Random vibration2027.2 Substrate attach strength2028.4 Pin grid package destructive lead pull test2029 Ceramic chip carrier bond strength2030 Ultrasonic inspection of die attach2031.1 Flip chip pull-off test2032.1 Visual inspection of passive elements2035 Ultrasonic inspection of TAB bonds2036 Resistance to soldering heatElectrical tests (digital), methods 3001-3024[edit]3001.1 Drive source, dynamic3002.1 Load conditions3003.1 Delay measurements3004.1 Transition time measurements3005.1 Power supply current3006.1 High level output voltage3007.1 Low level output voltage3008.1 Breakdown voltage, input or output3009.1 Input current, low level3010.1 Input current, high level3011.1 Output short circuit current3012.1 Terminal capacitance3013.1 Noise margin measurements for digital microelectronic devices3014 Functional testing3015.8 Electrostatic discharge sensitivity classification3016 Activation time verification3017 Microelectronics package digital signal transmission3018 Crosstalk measurements for digital microelectronic device packages3019.1 Ground and power supply impedance measurements for digital microelectronics device packages3020 High impedance (off-state) low-level output leakage current3021 High impedance (off-state) high-level output leakage current3022 Input clamp voltage3023.1 Static latch-up measurements for digital CMOS microelectronic devices3024 Simultaneous switching noise measurements for digital microelectronic devices Electrical tests (linear), methods 4001-4007[edit]4001.1 Input offset voltage and current and bias current4002.1 Phase margin and slew rate measurements4003.1 Common mode input voltage range, Common mode rejection ratio, Supply voltage rejection ratio4004.2 Open loop performance4005.1 Output performance4006.1 Power gain and noise figure4007 Automatic gain control rangeTest procedures, methods 5001-5013[edit]5001 Parameter mean value control5002.1 Parameter distribution control5003 Failure analysis procedures for microcircuits5004.11 Screening procedures5005.15 Qualification and quality conformance procedures5006 Limit testing5007.7 Wafer lot acceptance5008.9 Test procedures for hybrid and multichip microcircuits5009.1 Destructive physical analysis5010.4 Test procedures for custom monolithic microcircuits5011.5 Evaluation and acceptance procedures for polymeric adhesives5012.1 Fault coverage measurement for digital microcircuits5013 Wafer fabrication control and wafer acceptance procedures for processed GaAs wafers。
美军标简介
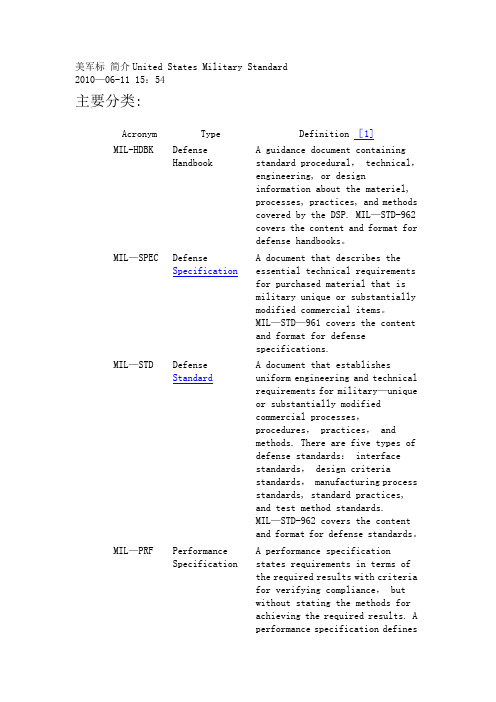
美军标简介United States Military Standard2010—06-11 15:54主要分类:Acronym Type Definition [1]MIL-HDBK DefenseHandbook A guidance document containing standard procedural, technical,engineering, or design information about the materiel, processes, practices, and methods covered by the DSP. MIL—STD-962 covers the content and format for defense handbooks。
MIL—SPEC DefenseSpecification A document that describes the essential technical requirements for purchased material that is military unique or substantially modified commercial items。
MIL—STD—961 covers the content and format for defense specifications.MIL—STD DefenseStandard A document that establishes uniform engineering and technical requirements for military—unique or substantially modified commercial processes,procedures, practices, and methods. There are five types of defense standards: interface standards, design criteria standards, manufacturing process standards, standard practices, and test method standards. MIL—STD-962 covers the content and format for defense standards。
ASTMD6749-2002 英文

Designation: D 6749 –02An American National StandardStandard Test Method forPour Point of Petroleum Products (Automatic Air PressureMethod)1This standard is issued under the fixed designation D 6749; the number immediately following the designation indicates the year oforiginal adoption or, in the case of revision, the year of last revision. A number in parentheses indicates the year of last reapproval. Asuperscript epsilon (e) indicates an editorial change since the last revision or reapproval. INTRODUCTIONThis test method covers an alternative procedure for the determination of pour point of petroleum products using an automatic apparatus.1. Scope1.1 This test method covers the determination of pour pointof petroleum products by an automatic apparatus that applies aslightly positive air pressure onto the specimen surface whilethe specimen is being cooled.1.2 This test method is designed to cover the range oftemperatures from −57 to +51°C; however, the range oftemperatures included in the (1998) interlaboratory test pro-gram only covered the temperature range from −51 to −11°C.1.3 Test results from this test method can be determined ateither 1 or 3°C testing intervals.1.4 This test method is not intended for use with crude oils.NOTE 1—The applicability of this test method on residual fuel sampleshas not been verified. For further information on the applicability, refer to13.4.1.5 The values stated in SI units are regarded as standard.1.6 This standard does not purport to address all of thesafety concerns, if any, associated with its use. It is theresponsibility of the user of this standard to establish appro-priate safety and health practices and determine the applica-bility of regulatory limitations prior to use.2. Referenced Documents2.1 ASTM Standards:D 97 Test Method for Pour Point of Petroleum Products2D 4057 Practice for Manual Sampling of Petroleum andPetroleum Products3D 4177 Practice for Automatic Sampling of Petroleum andPetroleum Products32.2 IP Standard:IP15 Test Method for Pour Point of Petroleum Products43. Terminology3.1 Definitions:3.1.1 pour point, n—in petroleum products, the lowesttemperature at which movement of the test specimen isobserved under prescribed conditions of test.3.2 Definitions of Terms Specific to This Standard:3.2.1 air pressure, n—a regulated slightly positive air pres-sure gently applied onto the specimen surface in the air-tighttest jar that causes upward movement of the specimen in thecommunicating tube, which has one end inserted into the testspecimen and the other end at atmospheric pressure.3.2.2 no-flow point, n—in petroleum products, the tempera-ture of the test specimen at which a wax crystal structure of thetest specimen or viscosity increase, or both, impedes move-ment of the surface of the test specimen under the conditions ofthe test.3.2.2.1 Discussion—The no-flow point occurs when, uponcooling, the formation of wax crystal structures or viscosityincrease, or both, has progressed to the point where the appliedobservation device no longer detects movement under theconditions of the test. The preceding observation temperature,at which flow of the test specimen is last observed, is the pourpoint.4. Summary of Test Method4.1 After inserting the test jar containing the specimen intothe automatic pour point apparatus and initiating the testprogram, the specimen is automatically heated to the desig-nated temperature and then cooled at a controlled rate. Attemperature intervals of 1 or 3°C, depending on the selectionmade by the user prior to the test, a slightly positive airpressure is gently applied onto the surface of the specimen1This test method is under the jurisdiction of ASTM Committee D02 onPetroleum Products and Lubricantsand is the direct responsibility of SubcommitteeD02.07on Flow Properties.Current edition approved Jan. 10, 2002. Published March 2002.2Annual Book of ASTM Standards, V ol 05.01.3Annual Book of ASTM Standards, V ol 05.02.4Available from Institute of Petroleum, 61 New Cavendish St., London, EnglandW1G 7AR.1Copyright © ASTM International, 100 Barr Harbor Drive, PO Box C700, West Conshohocken, PA 19428-2959, United States.which is contained in an air-tight test jar equipped with a communicating tube. Since one end of the communicating tubeis inserted into the specimen while the other end is maintainedat atmospheric pressure, a small amount of downward move-ment or deformation of the specimen surface, as a result of theapplication of air pressure, is observed by means of upwardmovement of the specimen in the communicating tube. Thisupward movement of the specimen is detected by a pressuresensor which is installed at the atmospheric end of thecommunicating tube. The lowest temperature at which defor-mation of the specimen is observed upon application of airpressure is recorded as the pour point, Test Method D 6749.5. Significance and Use5.1 The pour point of a petroleum product is an index of thelowest temperature of its utility for certain applications. Flowcharacteristics, like pour point, can be critical for the correctoperation of lubricating systems, fuel systems, and pipeline operations.5.2 Petroleum blending operations require precise measure-ment of the pour point.5.3 Test results from this test method can be determined ateither 1 or 3°C intervals.5.4 This test method yields a pour point in a format similarto Test Method D 97/IP15 when the 3°C interval results are reported. However, when specification requires Test MethodD 97/IP15, do not substitute this test method.NOTE 2—Since some users may wish to report their results in a format similar to Test Method D 97/IP15 (in 3°C intervals), the precision data were derived for the 3°C intervals. For statements on bias relative to Test Method D 97/IP15, see 13.3.1.5.5 This test method has better repeatability and reproduc-ibility relative to Test Method D 97/IP15 as measured in the1998 interlaboratory test program.56. Apparatus6.1 Automatic Apparatus6,7—The automatic pour point ap-paratus described in this test method is a microprocessorcontrolled apparatus that is capable of heating and cooling a specimen, applying air pressure onto the specimen’s surface, detecting the specimen’s surface movement, and then comput-ing and reporting the pour point (see Fig. 1). The detail isdescribed in Annex A1.6.2 Test Jar, clear cylindrical glass with a flat bottom withan approximate capacity of 12 mL. Approximately 4.5 mL ofsample specimen is contained when filled to the scribed line.The test jar is fitted with a test jar cap assembly on its top toform an air chamber over the test specimen.6.3 Test Jar Cap Assembly—A plastic cap is installed on topof the test jar with the provision of sealing air.Aglass tube witha metallic tip shall be inserted from underneath the plastic capinto the round hole in the center of the test jar cap. The top endof the round hole is connected to an air pressure sensor by wayof a vinyl tube. To supply air pressure to the specimen’ssurface, a vinyl tube connected to an air syringe is locatedadjacent to the glass tube through an orifice in the plastic cap.When a specimen is to be tested, the test jar cap assembly isinstalled on the test jar with the lower end of the glass tubeinserted into the specimen in the test jar. The glass tube and thetest jar form a communicating tube. A temperature sensor in asmall diameter metallic sheath shall be installed in the center ofthe glass tube.6.4 Metallic Block Bath, a metallic block with a cylindricalhole to fit the test jar. The metallic block assembly shall havea provision for cooling/heating. A temperature sensor is em-bedded in the metallic block to monitor its temperature.7. Reagents and Materials7.1 Cleaning Agents, capable of cleaning and drying the testjar, temperature sensor, and glass tube after each test. Chemicalagents such as alcohol, petroleum-based solvents, and acetonehave been found suitable to use. (Warning—Flammable.)(Warning—May be harmful by itself or when evaporated.)5Available from ASTM International Headquarters. Request RR:D02-1499.6Tanaka model MPC series Pour Point Analyzers available from TanakaScientific Limited, Adachiku, Tokyo, Japan, have been found suitable for use in this test method. Various models included in this model series are differentiated by their cooling capacities or number of test heads, or both.7This pour point analyzer is covered by a patent. If you are aware of analternative(s) to the patented item, please attach to your ballot return a descriptionof the alternatives. All the suggestions will be considered by the committee.FIG. 1 Automatic ApparatusD 674928. Sampling8.1 Obtain a sample in accordance with Practice D 4057 orby Practice D 4177.8.2 Samples of very viscous materials may be warmed untilthey are reasonably fluid before they are transferred; however,no sample shall be heated more than is absolutely necessary.The sample shall not be heated and transferred into the test jarunless its temperature is 70°C or lower.NOTE 3—In the event the sample has been heated above this tempera-ture, allow the sample to cool until its temperature is at least 70°C before transferring.9. Preparation of Apparatus9.1 Install the automatic apparatus for operation in accor-dance with the manufacturer’s instructions.9.2 Clean and dry the test jar, temperature sensor, and glasstube.9.3 Turn on the main power switch of the automaticapparatus.10. Calibration and Standardization10.1 Ensure that all of the manufacturer’s instructions forcalibrating, checking, and operating the automatic apparatusare followed.10.2 Check the position of the temperature sensor and glasstube according to the manufacturer’s instructions and, whennecessary, make appropriate adjustments.10.3 A sample with a well documented pour point can beused to verify the performance of the automatic apparatus.Alternatively, a sample which has been extensively tested in apour point interlaboratory study can be used.11. Procedure11.1 Pour the sample specimen into the test jar to the scribedmark. When necessary, heat the sample in a bath or oven untilit is just sufficiently fluid to pour into the test jar. Samples withan expected pour point above 36°C or samples which appearsolid at room temperature can be heated above 45°C, but shallnot be heated above 70°C.11.2 Insert the charged test jar into the metallic block bathand install the test jar cap assembly snugly.11.3 Select the desired test mode, including the pour pointtesting interval, according to the manufacturer’s instructions. Should the user wish to provide results with a similar format toTest Method D 97/IP15, then testing at a 3°C interval shall be selected. Start the automatic sample preheating function, andthen enter the expected pour point (EPP).When the 3°C testing interval is chosen, the EPP needs to be a multiple of 3°C.11.4 Start the test program. The sample is automaticallypreheated by the automatic apparatus to 45°C or to EPP + 9°C, whichever is higher, but no higher than 70°C, by maintainingthe bath temperature at 48°C or EPP + 12°C, whichever is higher.11.5 After the preheating is completed, the specimen iscooled down automatically.11.5.1 The metallic block bath is cooled down at a rate of 3to 4°C/min, to the EPP + 40°C.11.5.2 From the EPP + 40°C to the no-flow point, themetallic block bath is cooled at a rate of 0.8 to 1.1°C/min.11.6 As the specimen temperature reaches a predetermined temperature, which is dependent on the EPP, the automatic apparatus starts testing for no-flow state by applying airpressure to the specimen surface at the programmed testing interval. When the specimen is still in a fluid state, thespecimen level moves up in the glass tube as air pressure isapplied on the specimen surface; when the specimen reaches ano-flow state, the specimen level does not move at all in theglass tube. Upon detecting the no-flow point, the automatic apparatus computes and displays the pour point, which is t97hesum of the no-flow point temperature and the testing interval. Also, the automatic apparatus stops cooling and starts heatingthe specimen.11.6.1 Specimen Having Expected Pour Point Equal To orAbove +36°C—The automatic apparatus starts testing for theno-flow state at EPP + 9°C.11.6.2 Specimen Having Expected Pour Point Equal To or Between +31°C and +35°C—The automatic apparatus starts testing for the no-flow state at 45°C.11.6.3 Specimen Having Expected Pour Point Equal To orBelow +30°C—The automatic apparatus starts testing for theno-flow state at EPP + 15°C.11.7 Remove the test jar cap assembly and clean the test jarand test jar cap assembly.NOTE 4—Residual fuels have been known to be sensitive to thermal history. In the case where a residual fuel sample is tested, refer to Test Method D 97 for sample treatment.12. Report12.1 Report the temperature recorded in 11.6 and the testing interval as the pour point in accordance with Test MethodD 6749.13. Precision and Bias13.1 Precision—The precision of this test method as deter- mined by statistical examination of interlaboratory test results is as follows:13.1.1 Pour Point at 3°C Testing Intervals (Test MethodD 6749):13.1.1.1 Repeatability—The difference between successive test results, obtained by the same operator using the same apparatus under constant operating conditions on identical test material, would in the long run, in the normal and correct operation of this test method, exceed the following, only in one case in twenty.2.5°C13.1.1.2 Reproducibility—The difference between twosingle and independent test results, obtained by different operators working in different laboratories on identical test material, would in the long run, in normal and correct operation of this test method, exceed the following, only in one case in twenty.3.1°C13.1.2 Pour Point at 1°C Testing Intervals (Test MethodD 6749):13.1.2.1 Repeatability—The difference between successive test results, obtained by the same operator using the same apparatus under constant operating conditions on identical test D 67493material, would in the long run, in the normal and correct operation of this test method, exceed the following, only in one case in twenty.1.1°C13.1.2.2 Reproducibility—The difference between twosingle and independent test results, obtained by different operators working in different laboratories on identical test material, would in the long run, in normal and correct operation of this test method, exceed the following, only in one case in twenty.2.2°C13.2 Bias—Since there is no accepted reference material suitable for determining the bias for the procedure in this test method, bias has not been determined.13.3 Relative Bias:13.3.1 Pour point results at 3°C testing intervals were compared to the pour point results from Test Method D 97. Relative bias among certain samples was observed; however, the observed bias does not appear to be of a systematic nature. Biases relative to Test Method D 97/IP15 may conceivably occur for sample types not included in the 1998 interlaboratory test program.NOTE 5—Large differences in results were observed between methods for one sample in the 1998 interlaboratory test study. The sample was a high-sulfur winter diesel. When cooled during the performance of a test method, this sample formed thin, but very large crystals, that could be described as large plates. These crystals formed wherever sample-glass contact was made as well as covered the top surface of the sample. The entire sample, except for this all encasing thin skin of crystals, remained liquid with apparent low viscosity.When this occurred and the sample was handled gently, the sample did not pour, but with rougher handling, the crust broke and the sample poured readily. Users of this method are advised to be alert for differences in results between test methods when this behavior is observed in the sample being tested.13.3.2 Pour points results at 1°C testing intervals wereexamined for bias relative to the pour point results at 3°Ctesting intervals.Abias of 1.1°C in average was observed in the1998 interlaboratory test program.NOTE 6—It shall be noted that when a specimen is tested at 1°C intervals, statistically the results will be 1°C lower than the results produced by 3°C testing intervals. This is due to test increment and reporting differences. Differences greater than 1°C over a number of samples would be from another cause. In the interlaboratory test program, the tests at 1°C intervals yielded pour points lower than those obtained from the tests at 3°C intervals by 1.1°C in average.13.4 The precision statements and the relative bias informa-tion were derived from a 1998 interlaboratory test program. Participants analyzed two sets of duplicate distillate dieselfuels, five sets of duplicate base oils, three sets of duplicate multigrade lubricating oils, and one set each of duplicatehydraulic oils and automatic transmission fluid in the tempera-ture range of −51 to −11°C. Nine laboratories participated withthe automatic apparatus, testing at 1°C and 3°C intervals, andseven laboratories participated with the manual Test MethodD 97 apparatus. Information on the types of samples and theiraverage pour points are available in the form of a researchreport.514. Keywords14.1 automatic air pressure method; petroleum products;pour pointANNEX(Mandatory Information)A1. DETAILED DESCRIPTION OF APPARA TUSA1.1 Test Jar, clear cylindrical glass with a flat bottom, 216 0.2 mm outside diameter, 45 6 0.5 mm height, and 1 6 0.2mm wall thickness. A scribed line is permanently marked at 166 0.3 mm from the bottom of the jar.NOTE A1.1—A round aluminum seal may be stuck on the bottom surface for optical cloud point detection.A1.2 Test Jar Cap Assembly, consists of the following:A1.2.1 A plastic cap with a provision to make the test jarairtight.A1.2.2 A glass tube with a metallic tip, 8 6 0.2 mm outsidediameter, 55 6 1 mm long, and a wall thickness of 1 6 0.1mm. When the test jar cap assembly is installed on the test jar,approximately 9 mm of the tip of the glass tube is inserted intothe test specimen.A1.2.3 A temperature sensor such as platinum resistanceprobe in a small diameter stainless steel sheath, typically 2 mmin outside diameter, to read the specimen temperature to 0.1°C.The tolerance of the temperature sensor shall be less than 1 %.A1.3 Air Pressure Sensor, an electric transducer connectedto the glass tube through a vinyl tube to detect upwardmovement of the specimen in the glass tube by sensing theincrease of air pressure in the glass tube. The sensor shall behighly sensitive and accurate to at least 21 Pa (2 mm H2O).A1.4 Air Syringe, a syringe driven by an electric actuatorcapable of applying a weak positive air pressure, such as 310Pa (30 mm H2O), to the specimen surface at a controlled rate.A1.5 Metallic Block Bath, a metallic block with a cylindri-cal hole to fit the test jar. The metallic block is equipped witha provision for cooling/heating the sample specimen in the testjar. The cooling system shall be capable of maintaining thecooling at a controlled rate as prescribed in 11.5.1 and 11.5.2.A1.6 Manometer—A U-tube manometer can be installedbetween the air syringe and the glass tube for verifying, andcalibrating as needed, the air pressure generated by the airsyringe.D 67494ASTM International takes no position respecting the validity of any patent rights asserted in connection with any item mentionedin this standard. Users of this standard are expressly advised that determination of the validity of any such patent rights, and the riskof infringement of such rights, are entirely their own responsibility.This standard is subject to revision at any time by the responsible technical committee and must be reviewed every five years andif not revised, either reapproved or withdrawn. Your comments are invited either for revision of this standard or for additional standardsand should be addressed to ASTM International Headquarters. Your comments will receive careful consideration at a meeting of theresponsible technical committee, which you may attend. If you feel that your comments have not received a fair hearing you shouldmake your views known to the ASTM Committee on Standards, at the address shown below.This standard is copyrighted by ASTM International, 100 Barr Harbor Drive, PO Box C700, West Conshohocken, PA 19428-2959,United States. Individual reprints (single or multiple copies) of this standard may be obtained by contacting ASTM at the aboveaddress or at 610-832-9585 (phone), 610-832-9555 (fax), or service@ (e-mail); or through the ASTM website().D 67495。
美军标跌落测试标准 -回复
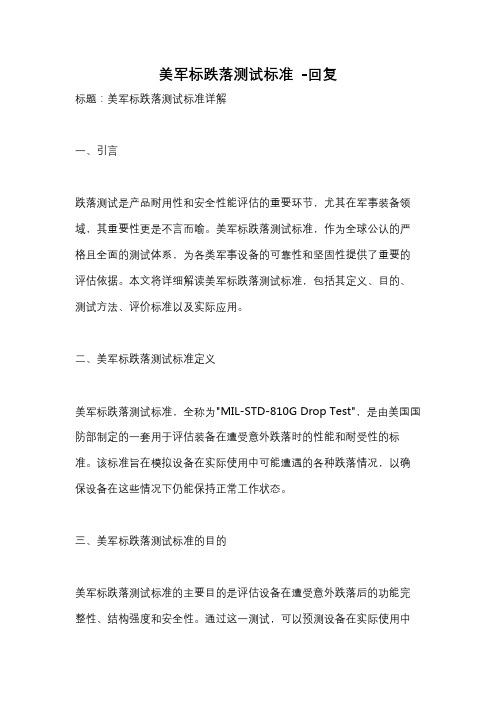
美军标跌落测试标准-回复标题:美军标跌落测试标准详解一、引言跌落测试是产品耐用性和安全性能评估的重要环节,尤其在军事装备领域,其重要性更是不言而喻。
美军标跌落测试标准,作为全球公认的严格且全面的测试体系,为各类军事设备的可靠性和坚固性提供了重要的评估依据。
本文将详细解读美军标跌落测试标准,包括其定义、目的、测试方法、评价标准以及实际应用。
二、美军标跌落测试标准定义美军标跌落测试标准,全称为"MIL-STD-810G Drop Test",是由美国国防部制定的一套用于评估装备在遭受意外跌落时的性能和耐受性的标准。
该标准旨在模拟设备在实际使用中可能遭遇的各种跌落情况,以确保设备在这些情况下仍能保持正常工作状态。
三、美军标跌落测试标准的目的美军标跌落测试标准的主要目的是评估设备在遭受意外跌落后的功能完整性、结构强度和安全性。
通过这一测试,可以预测设备在实际使用中可能出现的问题,从而提前进行改进和优化,提高设备的可靠性、耐用性和用户安全性。
四、美军标跌落测试方法1. 测试准备:首先,需要明确设备的预期使用环境和可能的跌落情况,然后选择相应的测试条件和方法。
2. 测试环境:根据设备的使用环境,可以选择在室内或室外进行测试,同时考虑温度、湿度、风速等环境因素的影响。
3. 跌落高度和角度:根据设备的尺寸、重量和预期使用情况,确定合适的跌落高度和角度。
一般来说,跌落高度越高,设备受到的冲击力越大。
4. 跌落表面:选择与预期使用环境相符的跌落表面,如混凝土、沙土、草地等。
5. 测试过程:将设备从预定的高度和角度自由落下,记录设备的状态和性能变化。
五、美军标跌落测试评价标准1. 功能完整性:设备在跌落后能否正常工作,包括但不限于开关、按键、显示屏、接口等功能是否正常。
2. 结构强度:设备在跌落后是否有明显的变形、破裂、脱落等现象。
3. 安全性:设备在跌落后是否存在电击、火灾、爆炸等安全隐患。
六、美军标跌落测试的实际应用美军标跌落测试标准广泛应用于各种军事装备的开发和测试中,包括但不限于通信设备、导航设备、武器系统、防护装备等。
美军空军自动测试设备与测试程序管理政策-军事技术论文-军事论文
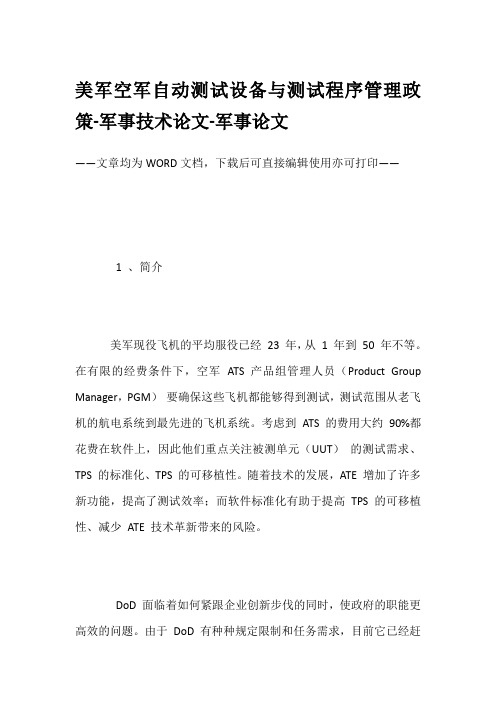
美军空军自动测试设备与测试程序管理政策-军事技术论文-军事论文——文章均为WORD文档,下载后可直接编辑使用亦可打印——1 、简介美军现役飞机的平均服役已经23 年,从1 年到50 年不等。
在有限的经费条件下,空军ATS 产品组管理人员(Product Group Manager,PGM)要确保这些飞机都能够得到测试,测试范围从老飞机的航电系统到最先进的飞机系统。
考虑到ATS 的费用大约90%都花费在软件上,因此他们重点关注被测单元(UUT)的测试需求、TPS 的标准化、TPS 的可移植性。
随着技术的发展,ATE 增加了许多新功能,提高了测试效率;而软件标准化有助于提高TPS 的可移植性、减少ATE 技术革新带来的风险。
DoD 面临着如何紧跟企业创新步伐的同时,使政府的职能更高效的问题。
由于DoD 有种种规定限制和任务需求,目前它已经赶不上企业的发展速度。
在一个日新月异的时代,很难辨别哪种技术会集成到DoD TPS 管理体系中。
在一项新技术出现后,DoD 要决定是否采用这项技术。
DoD 不断发掘、采用新技术的政策为美军空军ATS 的发展提供了先机,也给政府采购体系带来有效和快速的更新。
但与此同时,还带来一个问题:如何评定这些新技术的寿命周期和收益。
2、减少专用ATS 开发的相关政策2.1 背景在空军历史上,针对每种武器系统都有专用的ATS,导致ATS 的种类繁多。
2003 年,一份美国国家审计总署(GAO)评估报告显示,空军维持着一个庞大的ATS 体系。
在报告中还指出:维持众多陈旧的非标准测试仪器耗费了大量经费,且对战机的保障不利。
2.2 空军采购保障体系特点按美军空军的传统,有采购机构和保障机构。
这两个机构分布在不同的地方,相互之间的联系存在困难。
ATS和保障设备主要由系统计划局(System Program Office,SPO)根据原始设备制造商的建议(OEM)选择,而没有经过PGM 的评估,这就导致采购到大量的专用ATS。
想要通过美军标检测,产品要经受哪些“煎熬” (上)
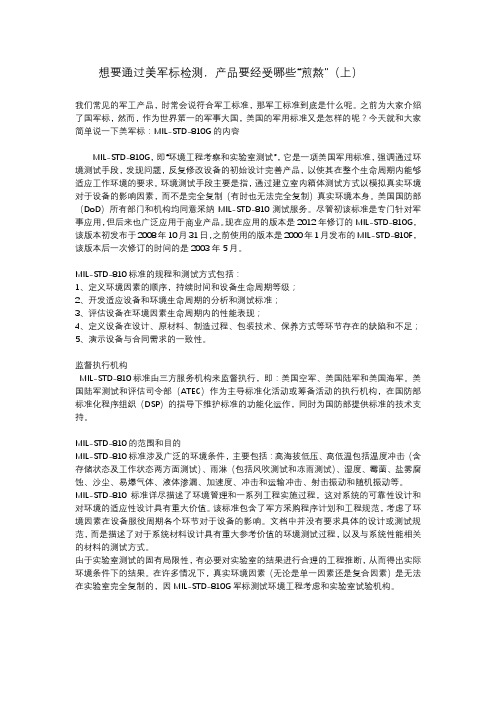
想要通过美军标检测,产品要经受哪些“煎熬”(上)我们常见的军工产品,时常会说符合军工标准,那军工标准到底是什么呢。
之前为大家介绍了国军标,然而,作为世界第一的军事大国,美国的军用标准又是怎样的呢?今天就和大家简单说一下美军标:MIL-STD-810G的内容MIL-STD-810G,即“环境工程考察和实验室测试”,它是一项美国军用标准,强调通过环境测试手段,发现问题,反复修改设备的初始设计完善产品,以使其在整个生命周期内能够适应工作环境的要求。
环境测试手段主要是指,通过建立室内箱体测试方式以模拟真实环境对于设备的影响因素,而不是完全复制(有时也无法完全复制)真实环境本身。
美国国防部(DoD)所有部门和机构均同意采纳MIL-STD-810测试服务。
尽管初该标准是专门针对军事应用,但后来也广泛应用于商业产品。
现在应用的版本是2012年修订的MIL-STD-810G,该版本初发布于2008年10月31日,之前使用的版本是2000年1月发布的MIL-STD-810F,该版本后一次修订的时间的是2003年5月。
MIL-STD-810标准的规程和测试方式包括:1、定义环境因素的顺序,持续时间和设备生命周期等级;2、开发适应设备和环境生命周期的分析和测试标准;3、评估设备在环境因素生命周期内的性能表现;4、定义设备在设计、原材料、制造过程、包装技术、保养方式等环节存在的缺陷和不足;5、演示设备与合同需求的一致性。
监督执行机构MIL-STD-810标准由三方服务机构来监督执行,即:美国空军、美国陆军和美国海军。
美国陆军测试和评估司令部(ATEC)作为主导标准化活动或筹备活动的执行机构,在国防部标准化程序组织(DSP)的指导下维护标准的功能化运作,同时为国防部提供标准的技术支持。
MIL-STD-810的范围和目的MIL-STD-810标准涉及广泛的环境条件,主要包括:高海拔低压、高低温包括温度冲击(含存储状态及工作状态两方面测试)、雨淋(包括风吹测试和冻雨测试)、湿度、霉菌、盐雾腐蚀、沙尘、易爆气体、液体渗漏、加速度、冲击和运输冲击、射击振动和随机振动等。
美军标跌落测试标准
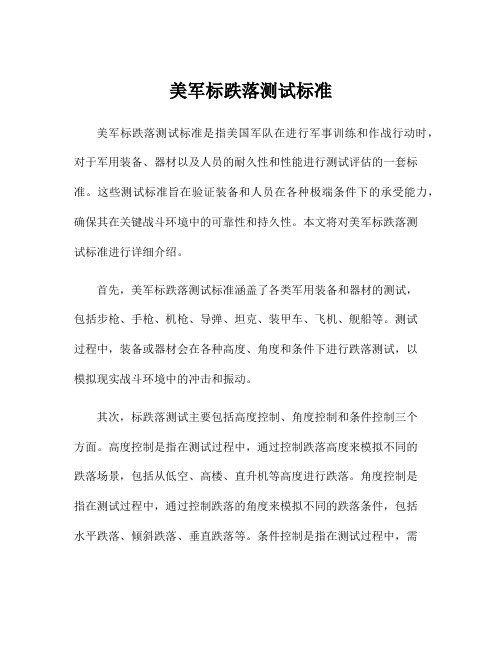
美军标跌落测试标准美军标跌落测试标准是指美国军队在进行军事训练和作战行动时,对于军用装备、器材以及人员的耐久性和性能进行测试评估的一套标准。
这些测试标准旨在验证装备和人员在各种极端条件下的承受能力,确保其在关键战斗环境中的可靠性和持久性。
本文将对美军标跌落测试标准进行详细介绍。
首先,美军标跌落测试标准涵盖了各类军用装备和器材的测试,包括步枪、手枪、机枪、导弹、坦克、装甲车、飞机、舰船等。
测试过程中,装备或器材会在各种高度、角度和条件下进行跌落测试,以模拟现实战斗环境中的冲击和振动。
其次,标跌落测试主要包括高度控制、角度控制和条件控制三个方面。
高度控制是指在测试过程中,通过控制跌落高度来模拟不同的跌落场景,包括从低空、高楼、直升机等高度进行跌落。
角度控制是指在测试过程中,通过控制跌落的角度来模拟不同的跌落条件,包括水平跌落、倾斜跌落、垂直跌落等。
条件控制是指在测试过程中,需要满足特定的条件,比如跌落前需要给装备或器材加装不同的重量或填充物,以模拟现实战斗中的情况。
在跌落测试中,主要考察装备或器材的以下几个方面:首先是装备或器材的耐久性。
通过跌落测试,可以验证装备或器材在承受冲击和振动的情况下是否能够保持其原有的结构完整性和功能性,防止出现断裂、变形、功能失效等问题。
其次是装备或器材的防护性能。
通过跌落测试,可以验证装备或器材在跌落过程中对其内部部件和使用者的防护能力,确保其能够有效保护装备内部零件不受损坏,并保护使用者免受伤害。
此外,还可以通过跌落测试来评估装备或器材的可靠性和持久性,以及其在极端条件下的性能表现。
在测试过程中,美军还对人员进行了跌落测试。
这些测试旨在验证士兵在进行跳伞行动、空投作战或高空救援等任务时的安全性和配合性。
测试内容包括对人员在跌落过程中的身体保护能力、跌落后自行解脱和快速恢复行动能力的评估。
通过这些测试,可以对士兵在空中落地后的应对能力进行全面评估,为实战提供保障。
总体来说,美军标跌落测试标准是一套验证军用装备、器材和人员耐久性和性能的重要标准。
关于re102适用范围的权威解释
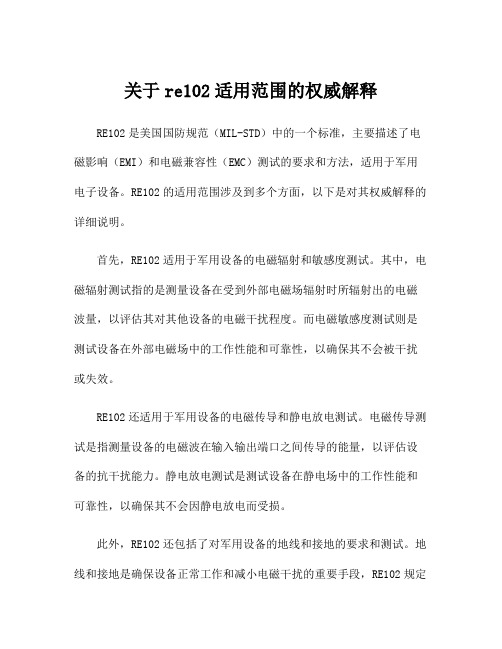
关于re102适用范围的权威解释RE102是美国国防规范(MIL-STD)中的一个标准,主要描述了电磁影响(EMI)和电磁兼容性(EMC)测试的要求和方法,适用于军用电子设备。
RE102的适用范围涉及到多个方面,以下是对其权威解释的详细说明。
首先,RE102适用于军用设备的电磁辐射和敏感度测试。
其中,电磁辐射测试指的是测量设备在受到外部电磁场辐射时所辐射出的电磁波量,以评估其对其他设备的电磁干扰程度。
而电磁敏感度测试则是测试设备在外部电磁场中的工作性能和可靠性,以确保其不会被干扰或失效。
RE102还适用于军用设备的电磁传导和静电放电测试。
电磁传导测试是指测量设备的电磁波在输入输出端口之间传导的能量,以评估设备的抗干扰能力。
静电放电测试是测试设备在静电场中的工作性能和可靠性,以确保其不会因静电放电而受损。
此外,RE102还包括了对军用设备的地线和接地的要求和测试。
地线和接地是确保设备正常工作和减小电磁干扰的重要手段,RE102规定了设备的地线系统和接地系统的布置和性能要求,并对其进行测试验证。
RE102还适用于军用设备的电源线和信号线的测试。
电源线测试是指测量设备的电源线上电磁波的幅度和频率分布,以评估其对其他设备的干扰程度。
信号线测试是指测量设备的信号线上电磁波的耐受度和传输能力,以确保设备在信号传输过程中不会受到电磁干扰的影响。
另外,RE102还适用于设备外壳的电磁屏蔽性能测试。
设备外壳的电磁屏蔽性能对于防止设备的电磁辐射泄漏和对外部电磁场的敏感度具有重要意义,RE102规定了外壳的电磁屏蔽性能测试的方法和要求。
此外,RE102还包括对设备辐射电磁场强度的限制。
该规范设定了设备所辐射的电磁场强度的上限,以确保设备在使用过程中不产生过高的电磁辐射,对人体健康和其他设备的安全不会造成危害。
尽管RE102主要适用于军用设备,但其测试方法和要求对其他领域的电子设备也具有指导意义。
许多民用电子设备也需要进行EMI和EMC测试,以确保其在正常使用过程中不会受到电磁干扰的影响或对其他设备造成干扰。
MIL-STD-167-1A-2005
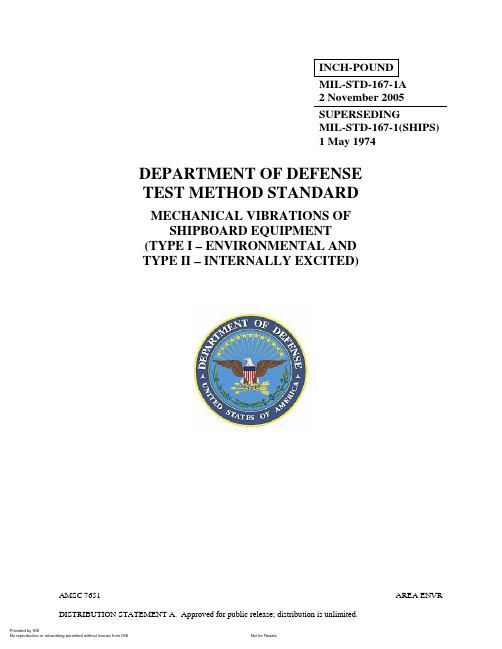
INCH-POUNDMIL-STD-167-1A2 November 2005SUPERSEDINGMIL-STD-167-1(SHIPS)1 May 1974DEPARTMENT OF DEFENSETEST METHOD STANDARDMECHANICAL VIBRATIONS OFSHIPBOARD EQUIPMENT(TYPE I – ENVIRONMENTAL ANDTYPE II – INTERNALLY EXCITED)AMSC 7651 AREA ENVR--`,,```,,,,````-`-`,,`,,`,`,,`---FOREWORD1. This standard is approved for use by the Naval Sea Systems Command, Department of the Navy, and is available for use by all Departments and Agencies of the Department of Defense.2. This standard establishes requirements and acceptance criteria for:a.Environmental vibration testing of shipboard equipment.b.Balancing shipboard rotating equipment subjected to internally induced vibration duringoperation.3. Shipboard equipment that conforms to the requirements of MIL-STD-167-1A is found to satisfactorily perform its functions aboard ship. Equipment for which compliance with MIL-STD-167-1A is not specified or is waived could experience failures induced by vibration in shipboard service.4. MIL-STD-167-1A, environmental vibration testing, and MIL-S-901D, equipment shock testing, provide complementary requirements for the survivability of shipboard equipment.5. This specification was revised to address the following:a.Requirements for test instrumentation and testing machines.b.Guidance in the selection of response prominences for endurance testing.c.Revisions to requirements for applicable frequency ranges.d.Revisions to attachment methods for equipment.e.Updated for conformance with MIL-STD-962D, “Defense Standards Format and Content”.6. Comments, suggestions, or questions on this document should be addressed to Commander, Naval Sea Systems Command, ATTN: SEA 05Q, 1333 Isaac Hull Avenue, SE, Stop 5160, Washington Navy Yard DC 20376-5160 or emailed to commandstandards@, with the subject line “Document Comment”. Since contact information can change, you may want to verify the currency of this address information using the ASSIST Online database atCONTENTSPARAGRAPH PAGE 1. SCOPE (1)1.1 Scope (1)1.2 Applicability (1)1.3 Classification (1)2. APPLICABLE DOCUMENTS (1)2.1 General (1)2.2 Government documents (1)2.2.1 Specifications, standards, and handbooks (1)2.3 Order of precedence (1)3. DEFINITIONS (1)3.1 Acceptance authority (1)3.2 Amplitude, single (2)3.3 Amplitude, vibratory displacement (2)3.4 Balancing (2)3.4.1 Balancing, multi-plane (2)3.4.2 Balancing, single-plane (static) (2)3.4.3 Balancing, two-plane (dynamic) (2)3.5 Critical speed (2)3.6 Environmental vibration (2)3.7 Equipment (2)3.8 Grade, balance quality (2)3.9 Internally excited vibration (2)3.10 Isolation mount (2)3.11 Mass unbalance (2)3.12 Maximum design rpm (2)3.13 Method of correction (2)3.14 Mode (2)3.15 Plane, correction (2)3.16 Plane, measuring (3)3.17 Residual unbalance (3)3.18 Resonance (3)3.19 Response prominence (3)3.20 Rotor, flexible (3)3.21 Rotor, rigid (3)3.22 Simple harmonic motion (3)3.23 Test fixture resonance (3)3.24 Transmissibility (3)4. GENERAL REQUIREMENTS (3)4.1 Notification of tests (3)4.2 Identification of component compliance (3)4.3 Disposition of tested equipment (3)5. DETAILED REQUIREMENTS (4)5.1 Type I – environmental vibration (4)PARAGRAPH PAGE5.1.1 Basis of acceptability (4)5.1.2 Test procedures (4)--`,,```,,,,````-`-`,,`,,`,`,,`---5.1.2.1 Testing machine (4)5.1.2.2 Additional test instrumentation (4)5.1.2.3 Methods of attachment (5)5.1.2.3.1 Shipboard equipment (5)5.1.2.3.2 Shipboard portable and test equipment (5)5.1.2.3.3 Orientation for vibration test (5)5.1.2.3.4 Isolation mountings (5)5.1.2.3.5 Internal isolation or shock mountings (5)5.1.2.4 Vibration tests (5)5.1.2.4.1 Equipment operation (6)5.1.2.4.2 Exploratory vibration test (6)5.1.2.4.3 Variable frequency test (6)5.1.2.4.4 Exception (6)5.1.2.4.5 Alternative test amplitudes (6)5.1.2.4.6 Endurance test (6)5.1.2.4.7 Endurance test for mast mounted equipment (7)5.1.2.5 Test documentation (7)5.1.2.5.1 Test plan (7)5.1.2.5.2 Test report (7)5.1.3 Exemption (7)5.1.4 Extension of previous testing (8)5.1.4.1 Extension documentation (8)5.2 Type II – internally excited vibration (8)5.2.1 Basis of acceptability (8)5.2.2 Balance procedure for rigid rotors (8)5.2.2.1 Balancing methods for rigid rotors (8)5.2.2.2 Balance limits for rigid rotors (9)5.2.3 Balance procedure for flexible rotors (9)5.2.3.1 Balance limits for flexible rotors (9)5.2.3.2 Vibration test procedure (9)5.2.3.2.1 Mounting (9)5.2.3.2.2 Measurements (9)5.2.3.2.3 Instruments (9)6. NOTES (10)6.1 Intended use (10)6.2 Acquisition requirements (10)6.3 Associated Data Item Descriptions (DIDs) (11)6.4 Tailoring guidance for contractual application (11)6.5 Superseding data (11)6.6 Subject term (key word) listing (11)6.7 Changes from previous issue (11)6.8 Guidance documents (12)TABLES PAGEI. Vibratory displacement of environmental vibration (6)II. Duration of endurance test in a given orthogonal direction at each test frequency (7)III. Vibratory displacement of environmental vibration for mast mounted equipment (7)IV. Types of balancing..........................................................................................................................................8 FIGURES PAGE1. Type I environmental vibration limits (black bars represent a graphical presentation of table I expressedin displacement, velocity, and acceleration) (13)2. Vibration acceptance criteria for Type II vibration (14)3. Minimum static deflection of mounting for Type II vibration test (15)Appendix A (16)A.1 SCOPE (16)A.1.1 Scope (16)A.2 PROCEDURE (16)A.2.1 Determining and displaying transmissibility (16)A.2.1.1 Transmissibility magnitudes (16)A.2.1.2 Transmissibility and frequency (16)A.2.2 Identifying response prominences (16)A.2.3 Selecting endurance test frequencies (17)A.2.3.1 Non-response prominence frequencies where functional or structural integrity is affected (17)A.2.3.2 Frequencies where response prominences have been identified (17)A.2.4 Guidance for specifiers (18)--`,,```,,,,````-`-`,,`,,`,`,,`---1. SCOPE1.1 Scope. This standard specifies procedures and establishes requirements for environmental and internallyexcited vibration testing of Naval shipboard equipment installed on ships with conventionally shafted propulsion (see 6.1.e and 6.1.f).1.2 Applicability. The test methods specified herein are applicable to shipboard equipment subjected tomechanical vibrations from the environment and from internal excitation caused by unbalanced rotating components of Naval shipboard equipment. For those mechanical vibrations associated with reciprocating machinery and lateral and longitudinal vibrations of propulsion system and shafting, see MIL-STD-167-2.1.3 Classification. The following types of vibration are covered in this standard:Type I - Environmental vibrationType II - Internally excited vibration2. APPLICABLE DOCUMENTS2.1 General. The documents listed in this section are specified in sections 3, 4, or 5 of this standard. Thissection does not include documents cited in other sections of this standard or recommended for additionalinformation or as examples. While every effort has been made to ensure the completeness of this list, document users are cautioned that they must meet all specified requirements of documents cited in sections 3, 4, or 5 of this standard, whether or not they are listed.2.2 Government documents.2.2.1 Specifications, standards, and handbooks. The following specifications, standards, and handbooks form apart of this document to the extent specified herein. Unless otherwise specified, the issues of these documents are those cited in the solicitation or contract.DEPARTMENT OF DEFENSE SPECIFICATIONSMIL-M-17191 - Mounts, Resilient: Portsmouth Bonded Spool Type MIL-M-17508-Mounts, Resilient: Types 6E100, 6E150, 7E450, 6E900, 6E2000,5E3500, 6E100BB, 6E150BB, 7E450BB, and 6E900BBMIL-M-19379 - Mounts, Resilient, Mare Island Types 11M15, 11M25, and 10M50MIL-M-19863 - Mount, Resilient: Type 5B5, 000HMIL-M-21649 - Mount, Resilient, Type 5M10, 000-H-MIL-M-24476Mounts, Resilient: Pipe Support, Types 7M50, 6M150, 6M450, 6M900,and 5M3500(Copies of these documents are available online at oror from the Standardization Document Order Desk, 700 Robbins Avenue, Building 4D, Philadelphia, PA 19111-5094.)2.3 Order of precedence. In the event of a conflict between the text of this document and the references citedherein, the text of this document takes precedence. Nothing in this document, however, supersedes applicable laws and regulations unless a specific exemption has been obtained.3. DEFINITIONS3.1 Acceptance authority. As used in this standard, the term “acceptance authority” means the governmentactivity (or its designated representative) having approval authority to determine vendor compliance with therequirements of this standard.--`,,```,,,,````-`-`,,`,,`,`,,`---3.2 Amplitude, single. See amplitude, vibratory displacement.3.3 Amplitude, vibratory displacement. Vibratory displacement amplitude is the maximum displacement ofsimple linear harmonic motion from the position of rest. This is also referred to as single amplitude. It is expressed in inches, mils (0.001 inch), or mm (0.001 meter).3.4 Balancing. Balancing is a procedure by which the radial mass distribution of a rotor is adjusted so that themass centerline approaches the geometric centerline of the rotor, and, if necessary, adjusted in order to ensure that the vibration of the journals and/or forces on the bearings, at a frequency corresponding to operational speed, are within specified limits.3.4.1 Balancing, multi-plane. Multi-plane balancing refers to any balancing procedure that requires unbalancecorrection in more than two axially separated correction planes.3.4.2 Balancing, single-plane (static). Single-plane (static) balancing is a procedure by which the massdistribution of a rigid rotor is adjusted in order to ensure that the residual static unbalance is within specified limits and which requires correction in only one plane. (Note: Single-plane balancing can be done on a pair of knife edges without rotation of the rotor but is now more usually done on centrifugal balancing machines.)3.4.3 Balancing, two-plane (dynamic). Two-plane (dynamic) balancing is a procedure by which the massdistribution of a rigid rotor is adjusted in order to ensure that the residual unbalance in two specified planes is within specified limits.3.5 Critical speed. Critical speed is the speed of a rotating system that corresponds to a natural frequency ofthe system.3.6 Environmental vibration. Environmental vibration is vibratory force, which is imposed on equipmentinstalled aboard ships, caused by the hydrodynamic forces on the propeller blades interacting with the hull and by other sources.3.7 Equipment. Equipment is any machine, subsystem, or part thereof, which is intended to be installed aboardship.3.8 Grade, balance quality. Balance quality grade, G, refers to the amount of permissible unbalance of a rotor.The balance quality grade is the product of the maximum permissible eccentricity (distance between the shaft axis and the rotor center of gravity (in mm)) and the rotational velocity (radians/sec). The units for balance quality --`,,```,,,,````-`-`,,`,,`,`,,`---grade, G, are mm/sec. By this definition, a particular grade rotor will be allowed a mass eccentricity (e=G/ω), which is inversely proportional to the operating speed.3.9 Internally excited vibration. Internally excited vibration is vibration of machinery generated by massunbalance of a rotor.3.10 Isolation mount. An isolation mount is a device used to attenuate the force transmitted from theequipment to its foundation.3.11 Mass unbalance. Mass unbalance occurs when the mass centerline does not coincide with the geometriccenterline of a rotor.3.12 Maximum design rpm. Maximum design rpm is the highest shaft rpm for which the ship is designed.3.13 Method of correction. A method of correction is a procedure whereby the mass distribution of a rotor isadjusted to reduce unbalance, or vibration due to unbalance, to an acceptable value. Corrections are usually made by adding material to, or removing it from, the rotor.3.14 Mode. Mode is the manner or pattern of vibration at a natural frequency and is described by its naturalfrequency and relative amplitude curve.3.15 Plane, correction. A correction plane is a plane transverse to the shaft axis of a rotor in which correctionfor unbalance is made.--`,,```,,,,````-`-`,,`,,`,`,,`---3.16 Plane, measuring. A measuring plane is a plane transverse to the shaft axis in which the amount and angle of unbalance is determined.3.17 Residual unbalance. Residual unbalance is unbalance of any kind that remains after balancing.3.18 Resonance. Resonance is the magnification of structural response, which occurs when a linear lightly damped system is driven with a sinusoidal input at its natural frequency. Resonances are the cause of many, but not all, response prominences.3.19 Response prominence. Response prominence is a general term denoting a resonance or other distinct maximum, regardless of magnitude, in a transmissibility function, including local maxima which may exist at the frequency endpoints of the transmissibility function. Typically, a response prominence is identified by the frequency of its maximum response, which is the response prominence frequency. A response prominence of a system in forced oscillation exists when any change, for both plus and minus increments however small, in the frequency of excitation results in a decrease of the system response at the observing sensor registering the maximum. A response prominence may occur in an internal part of the equipment, with little or no outward manifestation at the vibration measurement point, and in some cases, the response may be detected by observing some other type of output function of the equipment, such as voltage, current, or any other measurable physical parameter. Instruction on how to identify response prominences is provided in Appendix A.3.20 Rotor, flexible. A flexible rotor is one that does not meet the criteria for a rigid rotor. The unbalance of a flexible rotor changes with speed. Any value of unbalance assigned to a flexible rotor must be at a particular speed. The balancing of flexible rotors requires correction in more than two planes.3.21 Rotor, rigid. A rotor is considered to be rigid when its unbalance can be corrected in any two arbitrarily selected planes. After correction, its residual unbalance does not exceed the allowed tolerance, relative to the shaft axis, at any speed up to the maximum service speed and when running under conditions which approximate closely to those of the final supporting system.3.22 Simple harmonic motion. A simple harmonic motion is a motion such that the displacement is a sinusoidal function of time.3.23 Test fixture resonance. A test fixture resonance is any enhancement of the response of the test fixture to a periodic driving force when the driving frequency is equal to a natural frequency of the test fixture.3.24 Transmissibility. Transmissibility is the non-dimensional ratio of the response amplitude in steady-state forced vibration to the excitation amplitude. The ratio may be one of forces, displacements, velocities, or accelerations. Transmissibility is displayed in a linear-linear plot of transmissibility as a function of frequency, or in tabular form. Instructions for determining and displaying transmissibility are given in A.2.1 of Appendix A.4. GENERAL REQUIREMENTS4.1 Notification of tests. When specified (see 6.2.b), notification of Type I or Type II testing shall be made in accordance with DI-MISC-81624 (see 6.3).4.2 Identification of component compliance. When specified (see 6.2.c), the information verifying that the component complies with Type I and Type II testing shall be identified on the component drawing, the Test Report (DI-ENVR-81647) (see 6.3), or an identification plate attached to the component.4.3 Disposition of tested equipment. The requirements for tested equipment, fixturing, associated test records, and other documentation shall be as specified (see 6.2.d).5. DETAILED REQUIREMENTS5.1 Type I – environmental vibration. When Type I vibration requirements are specified (see6.2.e), the equipment shall be subjected to a simulated environmental vibration as may be encountered aboard naval ships. This standard provides an amplitude sufficiently large within the selected frequency range to obtain a reasonably high degree of confidence that equipment will not malfunction during service operation.a. For Type I vibration testing, this standard shall be used for equipment subjected to the vibrationenvironment found on Navy ships with conventionally shafted propeller propulsion. Type I vibrationtesting shall not be applicable to high-speed or surface-effect ships that are subject to vibrations from high-speed wave slap, which produce vibration amplitudes and frequencies in excess of the levels onconventional Navy ships.b. This standard applies to Type I vibration testing for equipment used in Navy ships with conventionallyshafted propeller propulsion, and is not necessarily applicable to waterjet, podded, or other propulsor types, including those that have been designed to minimize blade-rate forces.c. For equipment installed on ships with propulsion systems with frequency ranges not covered by Table I,this standard shall not apply.5.1.1 Basis of acceptability. For equipment that can be vibration tested, acceptability shall be contingent upon the ability of the equipment to withstand tests specified in 5.1.2 and the ability to perform its principal functions during and after vibration tests. Minor damage or distortion will be permitted during the test providing such damage or distortion does not in any way impair the ability of the equipment to perform its principal functions (see6.2.f(1) and 6.2.f(6)). Because of the numerous types of equipment covered by this standard, a definite demarcation between major and minor failures cannot be specified. Therefore, during testing a determination shall be made whether a failure is minor or major to determine whether testing should continue (see 6.2.f(2)). In general, a major failure is one that would cause maloperation or malfunction of the item of equipment for a long period. Non-repetitive failures of such parts as connectors, knobs/buttons, certain fasteners, and wiring, which can be easily replaced or repaired, are generally considered minor failures. As such, the repair could be made and the test continued with nopenalty to the remainder of the equipment. The critical use of the equipment shall be considered when determining the category of failure; that is, a failure of a part in a lighting circuit may be considered minor. The same failure in a control circuit may be major.5.1.2 Test procedures. The tests specified herein are intended to expose equipment to:a. Vibration magnitudes in prescribed frequency and amplitude ranges to reveal any critical responseprominences (see 3.19) or potential deficiencies.b. A 2-hour minimum endurance test at the response prominence frequency or frequencies most seriouslyaffecting its functional and/or structural integrity.5.1.2.1 Testing machine. Vibration tests shall be made by means of any testing machine capable of meeting the conditions specified in 5.1.2.4, and the additional requirements contained herein. Means shall be provided for controlling the direction of vibration of the testing machine and for adjusting and measuring its frequencies and amplitude of vibration to keep them within prescribed limits. It is acceptable to utilize different machines for the vertical and horizontal directions. The testing machine, including table, actuator, and attachment fixtures, shall be rigid within the frequency range to be tested. This includes test fixture resonances that may result from interaction between the table and mounted equipment. Testing machine rigidity shall be demonstrated by analysis or by measuring transmissibility in accordance with 5.1.2.2.d.5.1.2.2 Additional test instrumentation. Vibration measurement transducers, such as accelerometers, shall be installed on the test equipment to aid in the determination of response prominences during the exploratory and variable frequency vibration tests of 5.1.2.4.2 and 5.1.2.4.3. The number, orientation, and placement of vibration transducers will depend upon the equipment under test and should be sufficient to provide a suitable survey for identifying response prominences of the tested equipment and testing machine. When required, approval of transducer locations shall be obtained from the procuring activity (see6.2.f(3)). Guidance below shall be used in selection of measurement locations: --` , , ` ` ` , , , , ` ` ` ` -` -` , , ` , , ` , ` , , ` ---a. Measurements shall be made at locations corresponding to components or areas on the equipment ofparticular concern for operation of the equipment, whose failure would impair the ability of the equipment to perform its principal function. Such locations shall be determined prior to test.b. A sufficient number of measurement locations should be selected such that the response of the equipment ismeasured at locations near the base, top, and center of the equipment to measure response prominencesassociated with global motion of the equipment. These transducers should be attached to rigid areas of the equipment representing major structural components such as the housing, shell, or body of the equipment.c. The transducers shall be oriented to measure vibration in the direction of the vibration excitation providedfor any given test. Transducers may be re-oriented between tests to accomplish this.d. If the testing machine rigidity has not been demonstrated by analysis, a sufficient number of transducersshall be located on the testing machine to demonstrate that the testing machine is rigid over the frequency range of the test. At a minimum, these transducers should be located at the point of force application to the table and at the equipment attachment interface(s) to the testing machine.5.1.2.3 Methods of attachment.5.1.2.3.1 Shipboard equipment. For all tests, the equipment shall be secured to the testing machine at the same points or areas of attachment that it will be secured shipboard. In case alternate attachment points or areas are specified, tests shall be performed using each attachment configuration. Equipment that is hard mounted (i.e., not isolation mounted) aboard ship shall be hard mounted to the testing machine. For equipment designed to be secured to a deck and a head brace support, a vertical bracket shall be used to simulate a bulkhead. The bracket shall be sufficiently rigid to ensure that its motion will be essentially the same as the motion of the platform on the testing machine. For isolation mounted shipboard equipment, see 5.1.2.3.4.5.1.2.3.2 Shipboard portable and test equipment. Portable and test equipment that is designed for permanent or semi-permanent attachment to ship structure shall be attached to the vibration testing machines in the same manner it is attached to the ship. Equipment that is not designed for permanent or semi-permanent attachment shall be secured to the testing machine by suitable means.5.1.2.3.3 Orientation for vibration test. Equipment shall be installed on vibration testing machines in such a manner that the direction of vibration will be in turn along each of the three rectilinear orientation axes of the equipment as installed on shipboard – vertical, athwartship, and fore and aft. On a horizontal vibration-testing machine, the equipment may be turned 90 degrees in the horizontal plane in order to vibrate it in each of the two horizontal orientations. At no time shall the equipment be installed in any other way than its normal shipboard orientation.5.1.2.3.4 Isolation mountings. For Type I testing of equipment to be installed shipboard on isolation mounts, the testing shall be performed on isolation mounts or hard mounted to the testing machine or as specified (see6.2.f(4)). Type I testing of a particular piece of equipment on isolation mounts is valid only for the isolation mount type and configuration used during testing. Type I vibration testing may be performed hard mounted at some frequencies and isolation mounted at others. For example, the isolation mounts can be removed during the variable frequency and/or the endurance test at resilient mount resonance frequencies determined during the exploratory test, and the equipment can be tested hard mounted at these frequencies. If equipment is tested for Type I vibrations hard mounted to the test fixture throughout the duration of the test, the test is valid for either hard mounted or isolation mounted shipboard installations provided the isolation mounts are Navy standard mounts contained in MIL-M-17191, MIL-M-17508, MIL-M-19379, MIL-M-19863, MIL-M-21649, MIL-M-24476 (see 2.2.1), or distributed isolation material (DIM).5.1.2.3.5 Internal isolation or shock mountings. Equipment that incorporates other isolation mountings integrally within the equipment box (such as electronic cabinets) shall be tested with the internal mountings in the normal shipboard configuration or as specified (see6.2.f(5)).5.1.2.4 Vibration tests. Each of the tests specified herein shall be conducted separately in each of the three principal directions of vibration. All tests in one direction shall be completed before proceeding to tests in another direction. The equipment shall be secured to the vibration table as specified in 5.1.2.3. If major damage (see 5.1.1) occurs, the test shall be discontinued and the entire test shall be repeated following repairs or correction of deficiencies.--`,,```,,,,````-`-`,,`,,`,`,,`---5.1.2.4.1 Equipment operation. Except as noted below, equipment shall be energized or operated to perform its normal functions (see6.2.f(6)). Equipment that is difficult to operate on the testing machine shall be energized and subjected to operating conditions during the test. The equipment shall then be operated after the test to demonstrate that there is no damage from the test (see 6.2.f(1)).5.1.2.4.2 Exploratory vibration test. To determine the presence of response prominences (see 3.19) in the equipment under test, the equipment shall be secured to the vibration table and vibrated at frequencies from 4 Hz to 33 Hz, at a table vibratory single amplitude of 0.010 ± 0.002 inch (see 5.1.2.4.4 and 5.1.2.4.5 for exceptions). The change in frequency shall be made in discrete frequency intervals of 1 Hz and maintained at each frequency forabout 15 seconds. Alternately, a continuous frequency sweep with a rate of change of frequency not to exceed 0.067 Hz/second can be used. The frequencies at which functional or structural requirements are affected or violated and frequencies and locations at which response prominences occur shall be recorded, and these frequencies (rounded to the nearest integer frequency if discrete frequency intervals were not used) shall be considered as candidates for endurance testing (see Appendix A).5.1.2.4.3 Variable frequency test. The equipment shall be vibrated from 4 Hz to 33 Hz in discrete frequency intervals of 1 Hz at the amplitudes shown in Table I (see 5.1.2.4.4 and 5.1.2.4.5 for exceptions). At each integral frequency, the vibration shall be maintained for 5 minutes. The frequencies at which functional or structural requirements are affected or violated and frequencies and locations at which response prominences occur shall be recorded. Note that because of increased amplitudes compared to those mandated by 5.1.2.4.2, responseprominences and effects on or violations of functional or structural requirements may show up in this test that were not uncovered in the exploratory vibration test. Therefore, the frequencies at which these response prominences and effects on or violations of functional or structural requirements occur shall also be considered as candidates for endurance testing (see Appendix A).5.1.2.4.4 Exception. Equipment intended for installation solely on a particular ship class need only be vibrated in the exploratory and variable frequency tests from 4 Hz to (1.15 x maximum design rpm x number of propeller blades/60) rounded up to the nearest integer frequency or the maximum test frequency as specified (see6.2.f(7)). 5.1.2.4.5 Alternative test amplitudes. For equipment installed on ships with advanced isolation systems or low vibration propellers, alternative test amplitudes from Table I shall be used when specified (see 6.2.f(8)).5.1.2.4.6 Endurance test. Endurance test frequencies are selected from the candidate list of endurance test frequencies developed during exploratory and variable frequency testing (see 5.1.2.4.2 and 5.1.2.4.3). Whenspecified (see 6.2.f(9)), selection of these frequencies is subject to approval. The equipment shall be vibrated for a total period of at least 2 hours at the frequency determined to most seriously affect the functional or structural integrity of the equipment. Guidance for selecting response prominences from exploratory or variable frequency testing, for determining whether a response prominence is significant, and if the more serious response prominences can be identified, is given in Appendix A. In cases where there are multiple response prominence frequenciesselected, the duration of vibration testing at each frequency shall be in accordance with Table II. If neither response prominences nor effects on equipment structural/functional performance are observed, this test shall be performed at 33 Hz or at the upper frequency as specified in 5.1.2.4.4. The amplitudes of vibration shall be in accordance with Table I, unless otherwise specified (see 5.1.2.4.5). See Figure 1 for a graphical representation of the amplitudes in Table I.TABLE I. Vibratory displacement of environmental vibration.Frequency range(Hz)Table single amplitude(inch)4 to 15 0.030 ±0.006 16 to 25 0.020 ±0.004 26 to 330.010 ±0.002--`,,```,,,,````-`-`,,`,,`,`,,`---。
浅谈国军标和美军标元器件质量分级
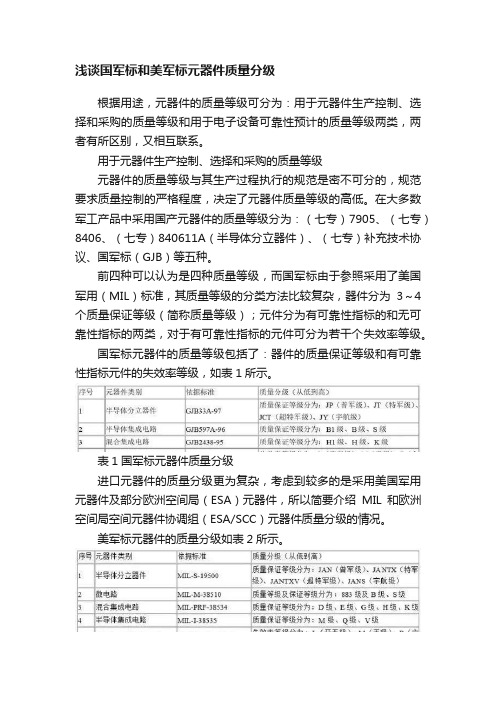
浅谈国军标和美军标元器件质量分级根据用途,元器件的质量等级可分为:用于元器件生产控制、选择和采购的质量等级和用于电子设备可靠性预计的质量等级两类,两者有所区别,又相互联系。
用于元器件生产控制、选择和采购的质量等级元器件的质量等级与其生产过程执行的规范是密不可分的,规范要求质量控制的严格程度,决定了元器件质量等级的高低。
在大多数军工产品中采用国产元器件的质量等级分为:(七专)7905、(七专)8406、(七专)840611A(半导体分立器件)、(七专)补充技术协议、国军标(GJB)等五种。
前四种可以认为是四种质量等级,而国军标由于参照采用了美国军用(MIL)标准,其质量等级的分类方法比较复杂,器件分为3~4个质量保证等级(简称质量等级);元件分为有可靠性指标的和无可靠性指标的两类,对于有可靠性指标的元件可分为若干个失效率等级。
国军标元器件的质量等级包括了:器件的质量保证等级和有可靠性指标元件的失效率等级,如表1所示。
表1国军标元器件质量分级进口元器件的质量分级更为复杂,考虑到较多的是采用美国军用元器件及部分欧洲空间局(ESA)元器件,所以简要介绍MIL和欧洲空间局空间元器件协调组(ESA/SCC)元器件质量分级的情况。
美军标元器件的质量分级如表2所示。
表2美军标元器件质量分级从1994年6月美国宣布对军用标准实行改革以来,表2中涉及的美军标中,MIL-M-38510已并入MIL-I-38535,而且都已改成性能规范(规范代号的字母改为MIL-PRF-,以后的数字不变,如MIL-PRF-38535C),内容也有较大的变化,例如采用统计过程控制(SPC)技术后,原来军用规范规定要100%做的筛选项目,允许减少甚至可以全部免除。
因此,在选择和采购元器件时,必须加以注意。
这里特别要对微电路(包括:半导体集成电路及混合集成电路)的质量等级作些说明,其中B级与S级是微电路的质量保证等级,此外凡符合MIL-STD-883《微电路试验方法和程序》1.2.1条规定的微电路,属于质量等级为883级的微电路。
美国UL认证标志及常用标准1新

UL508
包括整套机器设备,断路器,接触器,继电器等
工业机器控制板
UL 508A
电容1
UL810
普通电容
电容2
UL1414
影音产品跨线电容
电容3
UL1283
电磁滤波电容
马达
UL2111,1004
马达温度保险丝
UL2111
气泵
UL1450
潜水泵
UL778
滤水泵
UL1081
家用煮食用具
UL1026
包括电饭锅,面包机,多士炉,烤炉,暖瓶器,烤架等
电动类食品加工器具
UL982
揽拌机,榨汁机等
咖啡壶和液体加热类器具
UL1082
包括咖啡机,电热水壶,豆浆机等
油炸器具
UL1083
油炸锅,烙饼机
电动工具
UL745
电钻等
卷发器
UL1028
立式蒸汽熨斗
UL141
温控器
UL873
UL安全认证分三种:认可,列名,分级,三种方式标志不一样
UL列名标志UL分级标志UL认可零部件标志
性质:自愿性自愿性自愿性
标准要求:安全安全安全
工厂检查:需要需要需要
电压:120/240V (单相)208/240V (三相)
频率:60Hz
常用标准
产品名称
UL标准
附注
电线、电缆、通讯线
UL1582
电线插头
UL1418
可移动灯饰
UL153
包Hale Waihona Puke 台灯,落地灯固定灯饰UL1598
包括天花灯,壁灯,吊灯等
圣诞灯
UL588
包括配件
柔性霓虹灯
美国军用自动测试系统(ATS)的发展趋势
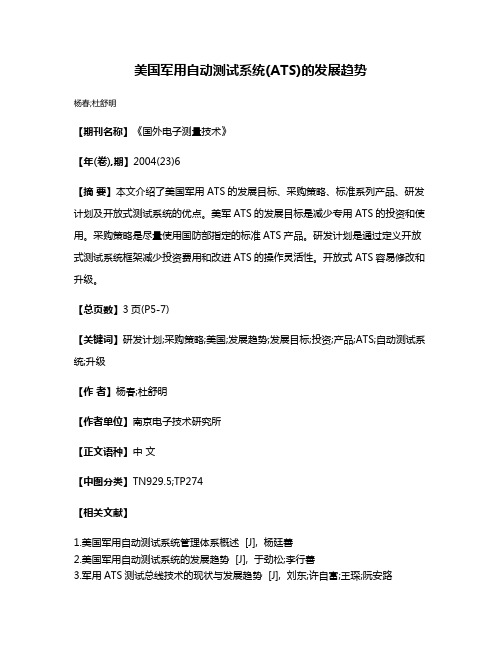
美国军用自动测试系统(ATS)的发展趋势
杨春;杜舒明
【期刊名称】《国外电子测量技术》
【年(卷),期】2004(23)6
【摘要】本文介绍了美国军用ATS的发展目标、采购策略、标准系列产品、研发计划及开放式测试系统的优点。
美军ATS的发展目标是减少专用ATS的投资和使用。
采购策略是尽量使用国防部指定的标准ATS产品。
研发计划是通过定义开放式测试系统框架减少投资费用和改进ATS的操作灵活性。
开放式ATS容易修改和升级。
【总页数】3页(P5-7)
【关键词】研发计划;采购策略;美国;发展趋势;发展目标;投资;产品;ATS;自动测试系统;升级
【作者】杨春;杜舒明
【作者单位】南京电子技术研究所
【正文语种】中文
【中图分类】TN929.5;TP274
【相关文献】
1.美国军用自动测试系统管理体系概述 [J], 杨廷善
2.美国军用自动测试系统的发展趋势 [J], 于劲松;李行善
3.军用ATS测试总线技术的现状与发展趋势 [J], 刘东;许自富;王琛;阮安路
4.军用自动测试系统(ATS)技术综述 [J], 王厚铿;王俊刚;孙勇
5.美国军用ATS技术的发展趋势 [J], 方葛丰;宋斌
因版权原因,仅展示原文概要,查看原文内容请购买。
- 1、下载文档前请自行甄别文档内容的完整性,平台不提供额外的编辑、内容补充、找答案等附加服务。
- 2、"仅部分预览"的文档,不可在线预览部分如存在完整性等问题,可反馈申请退款(可完整预览的文档不适用该条件!)。
- 3、如文档侵犯您的权益,请联系客服反馈,我们会尽快为您处理(人工客服工作时间:9:00-18:30)。
Pulsed Current Injection Test Systemaccording toMIL-STD-188-125/1 & 2System DescriptionVersion 2.0Montena EMCTable of content1.Montena emc (3)1.1P RODUCTS (4)1.2NEMP TEST INSTALLATIONS (4)1.3O THER MIL-STD REFERENCES (6)2.PCI test system description (7)3.Pulse generators and control units (8)3.1S HORT PULSE GENERATORS & CONTROL UNITS (8)3.2I NTERMEDIATE PULSE GENERATOR & CONTROL UNIT (11)3.3C HARGE LINE PULSER (12)4.Pulse coupling devices (13)4.1I NDUCTIVE COUPLER (14)4.2C APACITIVE COUPLERS (14)5.Isolating devices (16)6.Termination loads (17)7.System monitoring (18)8.Control and data acquisition system (19)8.1D ATA ACQUISITION SOFTWARE (19)9.Shielded container (21)10.Electric POE protective devices (23)11.Services & Support (24)11.1M ANUALS AND DOCUMENTATION (24)11.2O NSITE INSTALLATION AND TRAINING (24)11.3S YSTEM ACCEPTANCE (24)11.4M AINTENANCE (24)V:\Marketing\Prospectus_produits\SystemDescriptionDocuments\PCI_Tests_System_Description_V20.doc1. Montena emcSince its foundation in 1978, montena emc has earned a worldwide reputation for its leading-edge skills in the fields of high voltage, high frequency and electromagnetic fields.Montena emc is number one EMC test lab in Switzerland. With two large anechoic chambers, an open area test site and multiple shielded rooms, montena can test and validate all kinds of equipment.Figure 1 : Montena emc headquarters - helicopter in an anechoic chamberMontena emc laboratory is accredited by SAS (Swiss Accreditation Service) for the calibration of EMC measuring devices as well as for the verification of the electrical safety of equipment and devices according to European Union directives and to the Swiss legislation.Montena can count on highly specialized specialised know-how in the field of electromagnetic compatibility. These skills are put to good use in the EMC laboratories as well as in the development and construction of various kinds of equipment. In the field of high voltage and high frequencies, montena's engineers are masters of the techniques used to generate rapid pulses with very fast rise time.1.1 ProductsMontena emc designs, builds and markets equipment and accessories for EMC tests. The range of products includes antennas, TEM cells, striplines, field sensors, all kind of pulse generators, test benches, etc.Montena's high voltage pulse generators are mainly used for EMC tests, ultra-rapid imaging and pulsed light decontamination. Montena also builds pulse generators according the custom specific needs.Figure 2 : some montena emc products1.2 NEMP test installationsIn the past years montena has designed, build and delivered many test installations for both conducted and radiated susceptibility NEMP tests. The list below shows typical examples of delivered test installations.NEMP test generator 320 kV2.8/25 ns with control unitNEMP test generator 12kV5/200 nsNEMP test generator 75 kV 2.8/25 ns with radiation line 1.8 m high for test according to MIL 461E RS105NEMP test radiation line 12 m highNEMP test generator 120 kV 2.8/25 ns with radiation line 2.7 m highNEMP test generator 230 kV2.8/25 ns with radiation line3.6 m highHigh voltage pulse generatorsfor Pulse Current Injection testsetup1.3 Other MIL-STD referencesMontena has developed and sold turnkey test setups for other MIL-STD 461 test systems as RS 101, CS 101, CS 114, CS 115 and CS 116.Figure 3 : Combined fully automated CS114 + CS115 + CS116 test setup2. PCI test system descriptionMontena's EMP PCI test system is designed to perform Pulsed Current Injection (PCI) tests according MIL-STD 188-125-1 & 2: “PCI acceptance testing is used to demonstrate that electrical POE (Point Of Entry) protective devices, as-installed, perform in accordance with the transient suppression/ attenuation requirements of this standard. PCI verification testing confirms the transientsuppression/attenuation performance in operational circuit configurations and demonstrates that mission-critical systems (MCS) are not damaged or upset by residual internal transient stresses.”The test setup comprises following elements.3. Pulse generators and control unitsThe test system described in this document comprises four pulse generators designed and built by Montena. Each generators can be either directly controlled or remotely controlled via its RS232 or USB interface.3.1 Short pulse generators & control unitsTo fulfil the MIL-STD test specifications (>5000A with 60 Ohm), the short pulse generator has to deliver more than 300 kV. Additionally, to be able to test different type of POE protecting devices, it should be possible to perform tests at lower voltage (some tens of kV).It is physically not possible to design a Marx generator for the whole required voltage range (10 kV– 300 kV). Two generators are proposed :•EMP80K-5-500 : a 80kV direct discharge pulse generator (10kV – 80 kV)•EMP300K-5-500 : a 350kV high voltage Marx generator (~50 kV – 350 kV)80kV Short Pulse GeneratorThis generator is built around one single stage of high voltage capacitors directly charged from a high voltage power supply. The system comprises the high voltage unit and the control unit.Figure 5 : Picture of an EMP80K-5-500 with its control unitSpecificationsType EMP80K-5-500Standard MIL-STD-188-125-1 and -2 / short pulsePeak open circuit voltage ≤ 5 kV to 80 kV, positive onlySource impedance 60 ohmPeak short circuit current 1.33 kARise time of the current (short circuit) < 20 nsPulse length (FWHM) (short circuit) 500 - 550 nsCharging time < 1 minOutput connectors connecting bar with different drilling diameters Insulation oilInterface RS 232 / USBPower rating 85 - 264 V ac / 50 - 60 Hz / 150 VAStorage / working temperature 5 - 50 °C / 15 - 45 °CDimensions (control unit / generator) 56 x 19 x 45 cm / 92 x 38 x 55 cm (L x H x W) Weight (control unit / generator) 11 kg / 80 kg (with oil)350 kV Short Pulse GeneratorThis generator is built around a Marx generator delivering up to 350 kV in open circuit and more than 5 kA in short circuit. It comprises the high voltage Marx unit and the control unit.Figure 6 : Picture of an EMP300K-5-500 with its control unitSpecificationsType EMP300K-5-500Standard MIL-STD-188-125-1 and -2 / short pulseType Marx + peakingPeak erected voltage 50 to 350 kV, positive onlyPeak short circuit current 5 kA maxSource impedance 60 ohmCurrent rise time (short circuit) < 20 nsCurrent pulse length (short circuit) 500 - 550 ns (FWHM)Repetition frequency 1 pulse every 30 secInsulation SF6 and N2Output connector custom (connecting bar)Interface RS 232 and USBPower rating 210 - 250 V ac / 50 - 60 Hz / 600 VAStorage / working temperature 5 - 50 °C / 10 - 45 °CDimensions (control unit / generator) 45 x 19 x 56 cm / 60 x 42 x 188 cm (W x H x L) Weight (control unit / generator) 13 / 175 kg3.2 Intermediate pulse generator & control unitThis generator is built using a direct discharge of high voltage capacitors.Figure 7 : Picture of an IPP3K-4MS pulse generatorSpecificationsType IPP3K-4MSStandard MIL-STD-188-125-1 and -2 / intermediate pulse Charging voltage 3.0 kV max, positive onlyPeak short circuit current 260 A maxSource impedance > 10 Ω (typically 11 Ω)Pulse shape double exponential waveformCurrent rise time (short circuit) 0.6 µsCurrent pulse length (short circuit) 3.4 ms (FWHM)Repetition frequency 1 pulse every 45 secOutput connectors Multicontact (safety connectors)Interface RS 232 / USBPower rating 200 V to 264 V / 50 / 60 Hz / 1.6 kVA peak Storage / working temperature 5 - 50 °C / 10 - 45 °CDimensions (L x H x W) 55 x 40 x 51 cmWeight 42 kg3.3 Charge line pulserThis generator is based on a variable charge line. In order to adjust the length of the charge line to the quarter-wavelength of the applicable frequency, special coaxial cables must be connected to the pulse generator. A set of 9 cables are supplied with the generator to cover the frequency range of 30 to 300 MHz.Figure 8 : Picture of an CLP40k pulse generatorSpecificationsType CLP40KStandard MIL-STD-188-125-2 / charge lineCharging voltage 0.2 - 25 kV, positive onlyPeak short circuit current ≥ 400 ASource impedance 50 ohmRise time of the current, on 50 ohm < 5 nsLoading time < 30 secCharge line and output connectors HVMEM50K (proprietary)Interface RS 232 / USBPower rating 85 - 264 Vac / 50 - 60 Hz / 150 VAStorage / working temperature 5 - 50 °C / 10 - 45 °CDimensions (control unit / HV unit) 56 x 19 x 45 cm / 30 x 12 x 20 cm (L x H x W) Weight (control unit / HV unit) 15.1 / 3.2 kg4. Pulse coupling devicesThe pulse generator have to be somehow connected to the cable under test as shown in Figure 4 : Schematic of a typical PCI test setup installation.In this document we propose some solutions for a coupling on following typical types of cables / connexions:•shielded cables•mains AC / DC supply, 2 wires, 50 A, 230 V ac or 60 V dc•signal / data / telecom cables, 4 wires, 1 A, 60 V dc.A) Short pulse couplingThe coupling can be direct, inductive or capacitive, depending from the type of cable to be tested and if the cable has to be tested when in-service.The output of the short pulse generators (EMP300K-5-500 and EMP80K-5-500) are acting as mechanical switches. This means the output can be connected to any kind of cable even if this cable is carrying a signal or power.See the different types of proposed couplers in the next paragraphs.B) Intermediate pulse couplingBecause of the low frequency content of the intermediate pulse neither capacitive nor inductive coupling is possible. Very high capacitance / inductance would be required for the coupling efficiency. And these very high capacitance / inductance would drain high current from the device or from the source connected to the line under test.The intermediate pulse generator (IPP3K-4MS) has 4 independent outputs which can be connected to 4 independent wires, even if those are carrying power or signals. Following methods are then recommended:•On shielded cables: direct connection to the generator.•On mains AC / DC supply connections: direct coupling to the pulse generator. The mains source or the auxiliary test equipment must be powered through an isolating transformer inorder to force the current of the pulse to flow in the protective device. In this way, the "external load" is isolated.The intermediate pulse generator is equipped with 4 independent outputs which will allow the coupling on 4 lines. The pulse will be injected on 1 (wire-to-ground) or 2, 3 or 4 lines (common mode).•On signal / data / telecom cables 1 A / 4 wires / 60 V dc / 1 A a direct coupling is carried out through the 4 outputs of the generator.A transformer could also be used to isolate the connected equipment from the external world. Summary: we recommend to use direct coupling. No specific coupling device is proposed. Eventually a A 60 A / 230 V ac isolating transformer could be proposed as an option.C) Charge line pulser couplingThe coupling of the charged line pulse is carried out by direct connection of the coaxial cable / connection to test to the pulse generator. No coupling device is proposed..4.1 Inductive couplerThe inductive coupler shown below can be used for the short pulse common mode coupling on any type of cable bundle. It allows the injection of the pulsed current without interrupting the cable bundle to test.Figure 9 : Picture of the inductive couplerSpecificationsType IC3BFrequency range 500 kHz - 30 MHzMaximum peak voltage (1/500 ns) 100 kVMaximum peak current ≥ 5 kAMax. diameter of the tested cable about 100 mmConnector proprietaryWeight 60 kgDimensions (W x H x L) 22 x 27 x 63 cm4.2 Capacitive couplersThe capacitive couplers shown below can be used for the wire-to-ground coupling of the short pulse on any type of cables. They allow the injection of the pulsed current when the cables are in services. The different versions are adapted to the signal or to the mains supply connexions.The capacitive coupling can be combined with the isolating network in a same cabinet (version: - IS). See the chapter 5 Isolating devices for more information on the isolation network.Figure 10 : Picture of a capacitive couplerSpecificationsType CCS3 CCS3-IS CCL3 CCL3-ISType of signal signal signal mains supply mains supply Decoupling network not included included not included included230 / 400 V 60 V 230 / 400 V 230 / 400 V Nominal voltage(50 / 60 Hz / DC)Nominal voltage (400 Hz) 110 V ac60 V ac110 V ac110 V ac60 A 10 A 60 A 60 ANominal current(50 / 60 / 400 Hz / DC)Number of lines 4 4 2 2Max pulse voltage (500 ns) > 100 kV 15 kV > 100 kV 15 kVMax DC voltage > 35 kV dc> 35 kV dc> 35 kV dc> 35 kV dc Maximum peak current > 5 kA > 5 kA > 5 kA > 5 kASignal cut-off frequency - 10 kHz (- 3 dB) - 10 kHz (- 3 dB) Connector connecting bars connecting bars connecting bars connecting bars Weight 14 kg 42 kg 8.6 kg 35 kg Dimensions (L x H x W) 60 x 24.5 x 42 cm 70 x 24.5 x 42 cm 60 x 24.5 x 42 cm 70 x 24.5 x 42 cm5. Isolating devicesThe purpose of these decoupling devices is to isolate the "external load" (= the mains, the auxiliary equipment, etc.) from the pulses injected by the generators.Unfortunately using isolating devices is not always possible due to the fact that these devices can also block the signal if their frequency is in the same range than the pulse. So we generally recommend to inject the pulses only on lines and connections which are not connected to active auxiliary equipment.A) Short pulse decouplingDue to the high voltage of the short pulse generator, the decoupling requires capacitors and inductances of large dimensions. In addition, the rather high value of the decoupling components will exhibit a low pass filter behaviour not compatible with most of the ordinary data signals. Other coupling / isolating methods must be used in these cases.We propose some isolating devices included in the capacitive coupling cabinet (version: - IS of the capacitive coupler). See specifications in chapter 4.2 Capacitive couplers.B) Intermediate pulse decouplingBecause the frequency content of the pulse is the range of some Hz to some kHz, it is not possible to use isolating devices. The signals and even the mains 50 / 60 Hz will be blocked by the decoupling devices. Finally the size, weight and price of these devices will be prohibitive.C) Charge line pulser decouplingBecause the pulse is injected directly on the coaxial connection, isolating devices are neither possible nor needed.6. Termination loadsA set of 2, 50 and 300 ohm termination loads are usually proposed as option. These loads can be connected to the end of the tested lines, inside or/and outside the protected area to terminate the line and absorb the injected current pulse.They are not applicable to the AC / DC supply.The termination loads consist of a box containing 4 resistors for 4 independent lines. The specifications are the following:Maximum peak voltage 25 kVMaximum energy 1.8 kJ4Number of channels(= number of resistors per box)Resistance 2 or 50 or 300 ohmConnector proprietaryThe set of termination load consists of:• 2 boxes of 4 resistors of 2 ohm for signal / data / telecom;• 2 boxes of 4 resistors of 50 ohm for signal / data / telecom;• 2 boxes of 4 resistors of 300 ohm for signal / data / telecom.7. System monitoringThe recommended test monitoring comprises current and voltage sensors, an oscilloscope and a PC with its software for automatic control, data acquisition and automatic report generation.Current sensorsRequired are at least two current sensors: one measuring the injected current and one for the residual current.Residual voltage sensorIn order to have a good measurement sensitivity, two residual voltage sensors are recommended: one 1000x voltage probe and one 100x voltage probe.Optical link transmissionFor reliable measurement, the transmission between the sensors and the control room has to be immune to the generated field. A fibre optic link is recommended for each sensor. The proposed optical transmission comprises 4 links:• 2 x Acquisition Module (50 Ohm) for current sensors• 1 x Acquisition Module (1MOhm) for voltage sensorsDigital OscilloscopeWe recommend a digital oscilloscope with following characteristics:• 4 channels digital oscilloscope• 2 GHz bandwidth• 5 Gs/s (10Gs/s max)It has to be noticed that the oscilloscope has to be integrated in the control and measurement software.8. Control and data acquisition system8.1 Data acquisition softwareMontena proposes a customized data and acquisition software to ease the test procedure and to reduce the risk of human errors. This software is developed by montena with Labview, specifically for this test setup.Figure 11 : Example of Montena's LabView based program (here a CS116 calibration panel)Figure 12 : Example of a automatically generated test reportThe proposed software is built with the existing basic blocks developed by montena to control the generators and the measurement equipments, to collect measured data, and to process the data for display and automatic report generation.The software contains calibration panels to set the correction factors of sensors and transmission links. The software can be designed according to the specific customers needs of the PCI test system operation and will be presented to the end customer for approval before its final implementation. Montena delivers the software as well as the source code. The end customer has then the possibility to extend / modify this software according future needs. Of course montena can also be mandated forthese eventually future adaptations.9. Shielded containerOptionally montena can propose a shielded container to be used as control room and eventually toapplications.The container is a standard (8 ft x 8 ft x 20ft) transportable container as shown in the picture below.Figure 13 : Typical NEMP proof container from RUAGThe container has the following equipment•Walls and ceiling are made of steel•Door without window•Wooden floor with non-slip and abrasion resistant vinyl flooring•Under floor protection (outside)•Electrical installations (5 x double 230V and 5 x RJ45 – for 5 working places)•Air conditioning (4.5 kW)•External power supply through lightning protection box and insulating transformer 230V/35A •Coaxial feed through connector•Optical fibre cable entry•Standard locking systemand is delivered with following furniture:• 1 x 19" rack 600 x 700 x 1800 mm• 1 x table for 5 working places with 5 x chairs• 1 x 3 drawers file cabinetFigure 14 : Proposed internal furnitureIt remains always possible to define the exact internal configuration during the execution of the project.10. Electric POE protective devicesA set of NEMP filters can be optionally proposed to perform FAT, SAT and other types of calibration or reference tests. The recommend list of filter samples comprises:AC power line filtersOne NEMP AC power line filter for 4 lines (3L + 1N) 400/230V,50/60Hz for up to 40Amp.DC power line filtersTwo NEMP DC power line filters for a DCpowering up to 30V DC / 10A.Data line filtersTwo NEMP fast data protectors - (up to 155 MBit/s)(For a single Ethernet 10/100 MBit/s application two (2)protectors are necessary - one protector for one wire pair).Digital telephony line filtersTwo NEMP low to medium data rate protectors - (up to 2MBit/s).VHF test filtersTwo NEMP VHF antennas lines filter - (DC – 1000 MHz).11. Services & Support11.1 Manuals and documentationThe provided documentation comprises:• A system level installation and user manuals•Installation and user manuals of each delivered equipment•An installation and user manual for the data and acquisition software•Source code of the data and acquisition software11.2 Onsite installation and trainingMontena emc provides worldwide onsite installation performed by montena's engineers with help of skilled and unskilled workmen provided by the customer.A comprehensive training session is offered and will be given directly after installation. This training will be provided by an engineer from montena and includes the test system installation, operation and maintenance.The content of the training sessions will be defined according to the end customer desires.11.3 System acceptanceThe test system acceptance procedure is performed with a verification of the generated test pulses and comprises:• A measurement of the generated current and voltage pulses• A measurement of residual current and voltage pulses behind the provided NEMP filters• A comparison with the typical specifications of the filters.The acceptance comprises two phases:• A FAT (factory acceptance test) at Montena in Switzerland to demonstrate the system performance (one week for 2 people from the end customer)• A SAT (site acceptance test) performed at the end customer location, after the system installation. An acceptance report is delivered and signed by both the end customer andmontena. The warranty period starts at the signature of this acceptance document.11.4 MaintenanceNo periodical maintenance other than calibration of the measurement equipment is required.On customer request montena can offer this calibration service with support of montena's authorized local representative.。