薄壁深筒矩形件冲压工艺及级进模设计
筒形件的冲压工艺及模具毕业设计
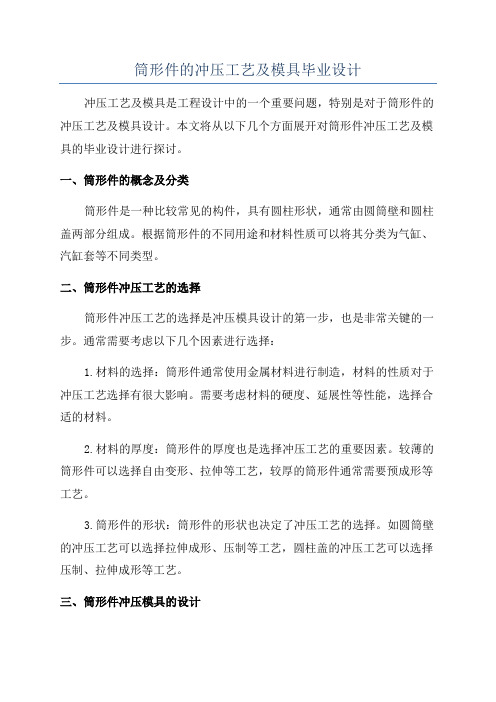
筒形件的冲压工艺及模具毕业设计冲压工艺及模具是工程设计中的一个重要问题,特别是对于筒形件的冲压工艺及模具设计。
本文将从以下几个方面展开对筒形件冲压工艺及模具的毕业设计进行探讨。
一、筒形件的概念及分类筒形件是一种比较常见的构件,具有圆柱形状,通常由圆筒壁和圆柱盖两部分组成。
根据筒形件的不同用途和材料性质可以将其分类为气缸、汽缸套等不同类型。
二、筒形件冲压工艺的选择筒形件冲压工艺的选择是冲压模具设计的第一步,也是非常关键的一步。
通常需要考虑以下几个因素进行选择:1.材料的选择:筒形件通常使用金属材料进行制造,材料的性质对于冲压工艺选择有很大影响。
需要考虑材料的硬度、延展性等性能,选择合适的材料。
2.材料的厚度:筒形件的厚度也是选择冲压工艺的重要因素。
较薄的筒形件可以选择自由变形、拉伸等工艺,较厚的筒形件通常需要预成形等工艺。
3.筒形件的形状:筒形件的形状也决定了冲压工艺的选择。
如圆筒壁的冲压工艺可以选择拉伸成形、压制等工艺,圆柱盖的冲压工艺可以选择压制、拉伸成形等工艺。
三、筒形件冲压模具的设计冲压模具是完成冲压工艺的关键设备,模具的设计直接关系到产品的质量和生产效率。
对于筒形件的冲压模具设计,主要包括以下几个要点:1.模具结构的设计:根据筒形件的形状和冲压工艺的选择,设计合适的模具结构。
通常包括上模、下模、导柱、导套等零件。
2.模具材料的选择:模具材料的选择对于模具的使用寿命和生产效率有很大影响。
需要选择耐磨、耐冲击的材料,如合金工具钢等。
3.模具加工工艺:模具的加工工艺对于模具的精度和质量有很大影响。
需要选择合适的加工工艺,如数控加工、磨削等。
四、筒形件冲压工艺及模具的应用筒形件冲压工艺及模具广泛应用于各个领域的制造业,如汽车、机械、电子等行业。
具体应用包括汽缸套的制造、气缸套的制造等。
总结起来,筒形件的冲压工艺及模具的设计是一个复杂而关键的问题,在毕业设计中需要考虑筒形件的材料性质、厚度、形状等因素进行工艺的选择,并设计合适的模具结构、材料和加工工艺。
深筒件的冲压工艺及模具设计
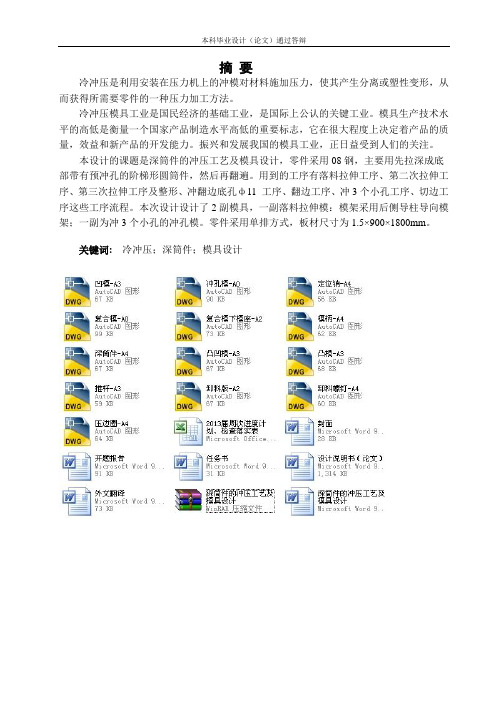
本科毕业设计(论文)通过答辩摘要冷冲压是利用安装在压力机上的冲模对材料施加压力,使其产生分离或塑性变形,从而获得所需要零件的一种压力加工方法。
冷冲压模具工业是国民经济的基础工业,是国际上公认的关键工业。
模具生产技术水平的高低是衡量一个国家产品制造水平高低的重要标志,它在很大程度上决定着产品的质量,效益和新产品的开发能力。
振兴和发展我国的模具工业,正日益受到人们的关注。
本设计的课题是深筒件的冲压工艺及模具设计,零件采用08钢,主要用先拉深成底部带有预冲孔的阶梯形圆筒件,然后再翻遍。
用到的工序有落料拉伸工序、第二次拉伸工序、第三次拉伸工序及整形、冲翻边底孔ф11 工序、翻边工序、冲3个小孔工序、切边工序这些工序流程。
本次设计设计了2副模具,一副落料拉伸模:模架采用后侧导柱导向模架;一副为冲3个小孔的冲孔模。
零件采用单排方式,板材尺寸为1.5×900×1800mm。
关键词: 冷冲压;深筒件;模具设计AbstractCold stamping is using presses installed in the die pressure on the material, make its produce a separation or plastic deformation, obtained from the required parts of a pressure processing method.Cold stamping die industry is the foundation of the national economy industry, is internationally recognized as one of the key industries. Mold production technology level of high and low is a measure of a national product manufacture level of important symbol, it largely determines the quality of products, and new product development capability. Revitalization and development of mould industry in China, are increasingly being people's attention.This design topic is Cold stamping technology and die design of tube parts, parts using 08 steel, mainly used to pull with pre punching deep into the bottom of the step cylinder, and then went through. Use process with blanking stretching process, the second stretching process, the t hird stretching process and plastic and flanging bottom hole ф 11 work procedure and three holes, flanging process, trimming process these processes. The two vice mould design design, a blanking tensile mold: mold frame with side guide column guide die set; A pair of blunt three holes of punching die. Parts adopt single method, board size is 1.5 * 900 * 1800 mm,Key words: cold stamping;tube pieces;the mold designII目录摘要 (I)ABSTRACT (II)目录........................................................................................................................................... I II 1 绪论. (1)1.1 本课题的研究内容和意义 (1)1.2国内外的发展概况 (1)1.3本课题应达到的要求 (2)2 深筒件的分析 (3)2.1深筒件的设计要求 (3)2.2深筒件的尺寸分析 (3)2.3深筒件材料的选用 (3)2.4深筒件圆孔加工计算 (3)2.5深筒件加工工艺的分析 (4)3 工艺方案的选择 (5)3.1毛坯直径计算 (5)3.1.1 翻边变形程度的计算 (5)3.1.2 深筒件翻边前半成品的尺寸计算 (5)3.1.3 深筒件毛坯直径的计算 (6)3.2拉伸次数计算 (6)3.3工序的组合和顺序的选定 (7)3.3.1 深筒件基本工序 (7)3.3.2 冲压方案选择 (7)3.3.3 方案比较 (11)4 深筒件数据计算 (12)4.1零件排样方式选择 (12)4.2板料尺寸的选择 (12)4.2.1 板料的利用率计算 (12)4.3材料消耗数据计算 (12)4.4各次拉伸是工件尺寸计算 (13)4.4.1 首次拉伸半成品尺寸 (13)4.4.2 二次拉深半成品尺寸 (14)4.4.3 第三次拉深半成品尺寸 (14)4.5工序的压力计算和压力机的选取 (15)4.5.1 落料拉深工序 (15)4.5.2 第二次拉深工序 (16)4.5.3 第三次拉深工序 (16)4.5.4 冲孔翻边工序 (17)4.5.5 翻边工序 (18)4.5.6 冲三个小孔工序 (18)4.5.7 切边工序 (19)5 深筒件的模具设计 (20)5.1落料拉深复合模 (20)5.1.1 模具结构形式 (20)5.1.2 卸料弹簧选取 (21)5.1.3 拉伸落料复合模模具相关尺寸设计 (21)5.2冲3个小孔模具设计 (24)6 结论与展望 (26)6.1结论 (26)6.2不足之处及未来展望 (26)致谢 (26)参考文献 (27)IV1 绪论1.1 本课题的研究内容和意义冷冲压是利用安装在印刷机上的材料上的压力的模具,以产生分离或塑性变形,从而获得所需的部分的压力加工方法。
基于DEFORM的薄壁深筒零件成形工艺及挤压模具设计

0引言冷挤压工艺是一种少无切削加工、效率高消耗低的金属精密成形工艺,应用冷挤压工艺制造金属成形零件,可一次成型,速度快,生产效率高,可以挤压形状比较复杂的零件,具有切削加工无可比拟的优越性。
本文基于DEFORM-3D仿真软件进行有限元分析,对选定的复杂零件所设计的模具进行挤压模拟,并根据模拟结果优化挤压参数。
1零件工艺性分析本文所指定的零件如图1所示。
①结构工艺性:该工件为轴对称零件,没有直角过度,没有深孔、环形槽,尺寸变化小于成形极限,但高径比较大,零件壁厚较薄,综合所有条件来看,适合挤压。
②精度:该工件尺寸精度均不超过IT9,因此可通过挤压成型来保证质量。
③原材料:该工件材料为FL21(3003),具有良好的塑性,屈服极限30MPa,适合挤压。
2模具结构设计冷挤压是在室温的条件下对金属材料施加压力,从而使之产生塑性变形,因此所产生的相对挤压力相当大,在反复作用的载荷下剧烈磨损,模具的工作环境十分恶劣。
且本文所指定的模具在内部有上下两个直径不同的孔,需要上下两个凸模对其进行挤压;外形结构上有一部分凸起,通常的推出结构无法正常推出,由此根据零件对模具结构进行改进:将凹模设计为开合式,并在其下方设置斜推机构,保证在挤压完成后凹模可以移开足够的空隙使工件被推出;又由于零件需双向挤压,下凸模限制了推出机构的结构,所以将推出机构设置为可套在下凸模上的圆环,使其在不影响下凸模工作的情况下能起到推出作用。
模具大体结构如图2;模具开模时,其关键部分(凹模、推出装置、挡板等)示意图如图3所示。
开模时,①号气缸带动传力杆推动斜推装置,使凹模分开一定距离,方便工件被推出;②号气缸带动牵引板向下移动,牵引板上斜导柱带动斜滑挡块向下移,在斜滑挡块下方斜面接触到推出环的斜面之后,斜滑挡块分开一段距离,使推出环可以通过;③号气缸推动推出环所连接的推板,带动推出环向上移动,将卡在下凸模上的工件推下。
———————————————————————课题项目:哈尔滨理工大学大学生创新创业训练计划项目,项目编号201910214297。
薄壁不锈钢筒形件级进模设计
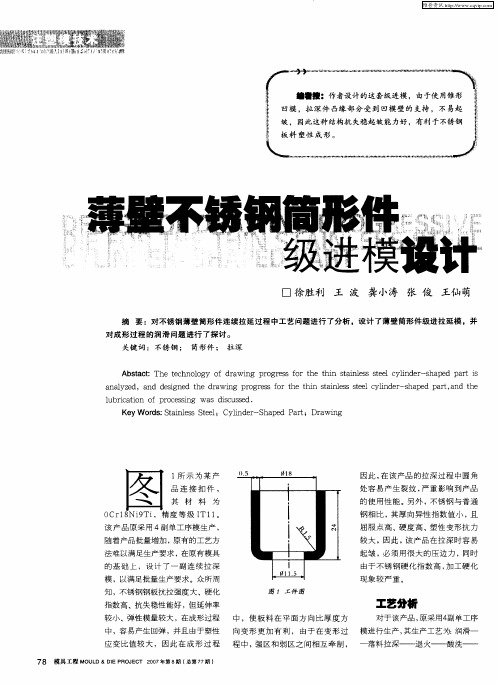
凸 模 采 用 台 阶型 式 , 固定 板 与
/ 配 凹模 采 用 分 体 式 , 时 , 品 的 废 品 率 达 8 , 经过 研 质量 ,降 低 废 品 率 ,增 加 了拉 深 的 按 H7 m6 合 , 产 % 后 究 ,增 加 了 中 间退 火工 序 ,产 品 的 次 数 ,将 原 来 的 两道 拉 深 工 序 改 为 将 侧 刃 冲 裁 凹 模 、工 艺 切 口凹 模 、
7 模 具工程 M L 8 OU D&DEP O E T 2 0 年第8 ( I R J C 0 7 期 总第7 期 7
维普资讯
8
7
6
5
4
3
2
1
二次 拉 深 — — 冲孔 —— 切 边_
该 退 拉 深 级 进 模 , 级进 模和 单 工 序模
度 等 级 I 。 T1 1
该 产 品 原 采 用 4副 单 工 序 模 生 产 , 随 着 产品 批 量 增 加 , 有 的 工 艺 方 原 法 难 以满 足 生 产 要 求 , 原 有 模 具 在
■■
1 l5 '
较大 ,因此 ,该产品 在拉深 时容易
_
起 皱 , 须 用 很 大 的 压 边 力 ,同 时 必 由于 不 锈 钢 硬 化 指 数 高 , 工硬 化 加
. . 经 过 生 产 实践 表 明 ,该 润 滑 剂使 用 工 艺 流 程 为 :软 化退 火— — 润 滑 一 序 组 成 ,分 别 为 :1侧 刃 冲 切 ;2 效 果 良好 , 使 用 过 程 中 ,有 效 地 在
一
次 拉 深— — 二 次 拉 深— — 三 次拉 冲 工艺 切 口 ;3 一 次 拉 深 ; . 次 . 4二
的基础 上 ,设计 了一 副连 续拉 深
筒形件的冲压工艺及模具毕业设计

筒形件的冲压工艺及模具设计摘要:本设计为小型的冲压模具,其质量和体积都较小。
结合本零件的特点确定合适的设计理念和设计思路,这样就不会产生设计出的模具无法使用或生产出的零件无法满足其使用性能等问题。
结合我国近年来模具的发展历史,虽然在设计制造方法和手段方面已经基本达到了国际水平,模具结构功能方面也接近国际水平,但在制造质量、精度、制造周期等方面,与国外相比还存在一定差距。
所以本次设计一定要尽可能考虑全面,结合实际情况和所学知识,这样不仅可以设计出合格的模具产品,还能提高自己的专业水平。
关键词:筒形件;冲压工艺;模具The Design of Stamping Process and Mold for the Cylindrical WorkpieceAbstract:This designed is a small stamping mould with small quality and little volume. Combining the characteristics of these parts to determine the appropriate design concept and design ideas,so it won’t produce some problems such as the mold can’t use after designed or the parts can’t satisfy the using performance. According to the history of our country in recent years,the methods in designing and manufacturing mould and the structure of mould have reached the international level,but there are certain gaps compared with the international level in manufacturing quality,accuracy and manufacturing cycle.So the mould I designed need to consider more aspects about combining my actual situation and finding the advantages of my own,as it can not only designed the qualified mouldproduct,but also can improve my ability.Key words: Cylindrical Workpiece; Stamping process; Mold1 引言目前我国模具工业与发达国家相比还相当落后。
薄壁桶形零件成形工艺与模具设计
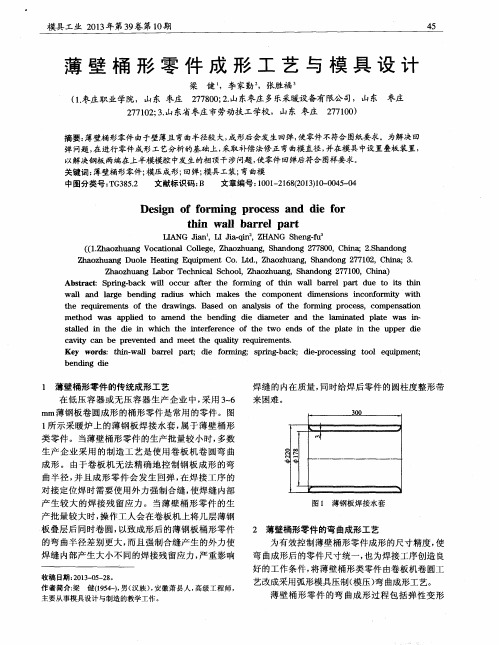
Z h a o z h u a n g L a b o r T e c h n i c l a S c h o o l ,Z h a o z h u a n g ,S h a n d o n g 2 7 7 1 0 0 ,C h i n a )
摘要: 薄壁桶 形零件 由于壁 薄且 弯曲半径较 大, 成形后会发 生回弹, 使零件不符合 图纸要求 。为解 决回 弹问题 , 在进行零件成形工艺分析的基础 上 , 采取 补偿 法修正弯 曲模 直径 , 并在模具 中设 置叠板装置 , 以解决钢板 两端在上半模模腔 中发生的相顶干涉问题 , 使零件 回弹后符合 图样要求。 关键词 : 薄壁桶形零件; 模压成形; 回弹; 模具工装; 弯曲模 中图分类号: T G 3 8 5 . 2 文献标识码 : B 文章编号 : 1 0 0 1 — 2 1 6 8 ( 2 0 1 3 ) 1 0 — 0 0 4 5 — 0 4
me ho t d Wa s a p pl i e d t o a me nd t he be n di ng d ie d ia m  ̄e r a nd t he l a mi n a t e d p l a t e wa s i n-
s t a l l e d i n t he d ie i n wh ic h he t nt i e r f e r e n c e o f he t t wo e nd s o f t he pl a t e i n t he u p pe r d ie
级进模冲压工艺设计简述
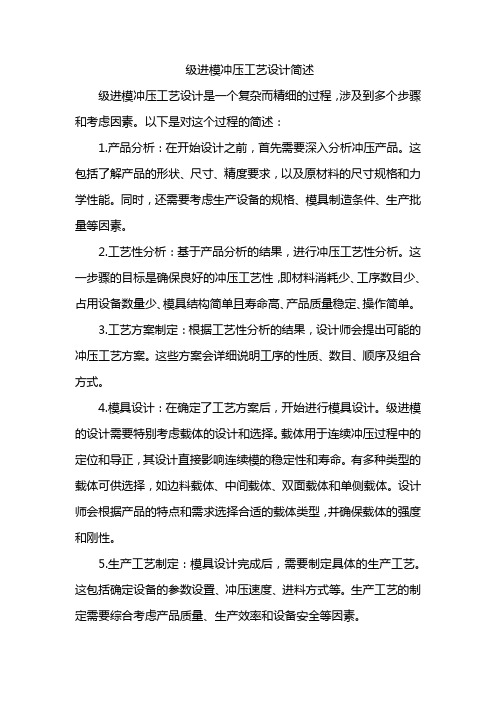
级进模冲压工艺设计简述
级进模冲压工艺设计是一个复杂而精细的过程,涉及到多个步骤和考虑因素。
以下是对这个过程的简述:
1.产品分析:在开始设计之前,首先需要深入分析冲压产品。
这包括了解产品的形状、尺寸、精度要求,以及原材料的尺寸规格和力学性能。
同时,还需要考虑生产设备的规格、模具制造条件、生产批量等因素。
2.工艺性分析:基于产品分析的结果,进行冲压工艺性分析。
这一步骤的目标是确保良好的冲压工艺性,即材料消耗少、工序数目少、占用设备数量少、模具结构简单且寿命高、产品质量稳定、操作简单。
3.工艺方案制定:根据工艺性分析的结果,设计师会提出可能的冲压工艺方案。
这些方案会详细说明工序的性质、数目、顺序及组合方式。
4.模具设计:在确定了工艺方案后,开始进行模具设计。
级进模的设计需要特别考虑载体的设计和选择。
载体用于连续冲压过程中的定位和导正,其设计直接影响连续模的稳定性和寿命。
有多种类型的载体可供选择,如边料载体、中间载体、双面载体和单侧载体。
设计师会根据产品的特点和需求选择合适的载体类型,并确保载体的强度和刚性。
5.生产工艺制定:模具设计完成后,需要制定具体的生产工艺。
这包括确定设备的参数设置、冲压速度、进料方式等。
生产工艺的制定需要综合考虑产品质量、生产效率和设备安全等因素。
总结起来,级进模冲压工艺设计是一个综合性的过程,涉及到产品分析、工艺性分析、工艺方案制定、模具设计和生产工艺制定等多个步骤。
这个过程的目标是确保冲压产品的高质量、高效率和低成本生产。
一种薄壁件加工方法
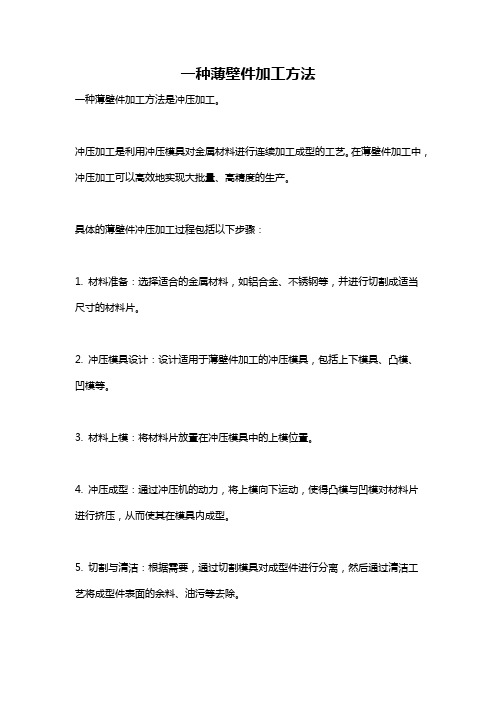
一种薄壁件加工方法
一种薄壁件加工方法是冲压加工。
冲压加工是利用冲压模具对金属材料进行连续加工成型的工艺。
在薄壁件加工中,冲压加工可以高效地实现大批量、高精度的生产。
具体的薄壁件冲压加工过程包括以下步骤:
1. 材料准备:选择适合的金属材料,如铝合金、不锈钢等,并进行切割成适当尺寸的材料片。
2. 冲压模具设计:设计适用于薄壁件加工的冲压模具,包括上下模具、凸模、凹模等。
3. 材料上模:将材料片放置在冲压模具中的上模位置。
4. 冲压成型:通过冲压机的动力,将上模向下运动,使得凸模与凹模对材料片进行挤压,从而使其在模具内成型。
5. 切割与清洁:根据需要,通过切割模具对成型件进行分离,然后通过清洁工艺将成型件表面的余料、油污等去除。
6. 检验与封装:对成型件进行质量检验,确保其尺寸和形状符合要求,然后进行包装封装。
薄壁件冲压加工方法具有加工效率高、成本低、质量稳定等优点,适用于汽车零部件、电子产品外壳、家用电器等领域的薄壁件生产。
薄壁盒体件的模内攻丝冲压模设计

薄壁盒体件的模内攻丝冲压模设计刘钧良,王文杰,赵宏宇,刘志刚中国华录松下电子信息有限公司模具部(辽宁大连110023)【摘要】介绍了BLD 下盖的薄壁盒体制件的模内攻丝冲压模具的排样设计技巧及结构设计的一些设计思路和设计技巧。
关键词:薄壁;模内攻丝;模具结构中图分类号:TG385.2文献标识码:BDesign of Stamping Die with Die Tapping for the Thin Wall Box Parts【Abstract 】The paper introduces the die layout and structure of BLD under the cover of thin wall box parts stamping die tapping some design ideas and design skills.Key words :thin wall ;die tapping ;die structure1引言冲压模的模内攻丝,是将传统的冲压和攻丝技术“整合”在一起,由于模内攻丝有效地避免了“二次加工”(先冲压,再攻丝),所以生产效率大大的得到了提高,降低了成本,提高成产效率,加工的螺纹精度好。
本文介绍了多头(8头)攻丝、薄壁(0.4mm )件攻丝模具的结构设计。
2制件结构分析图1为该制件的三维图形。
图2是该制件的二维图,壁厚0.4mm ,材料EGC QSI 20/20,外形尺145.6×142.2×20.8mm 。
共有8处攻丝,表面凸凹拉伸形状高低相差大,最低拉伸距离基准面-4.55mm ,最高拉伸距离基准面2.1mm ,相差6.65mm 。
图1制件三维图图2制件二维图3排样设计图3为该制件的排样图:①冲导正钉孔及工艺冲裁;②高底面拉伸;③、④冲裁、冲孔、打包;⑤冲底孔、翻边;⑥、⑦攻丝;⑧、⑨冲裁、折弯、拉包;⑩打包、倒角、折弯; 校平; 折回弯、切断。
薄壁深筒矩形件冲压工艺及级进模设计
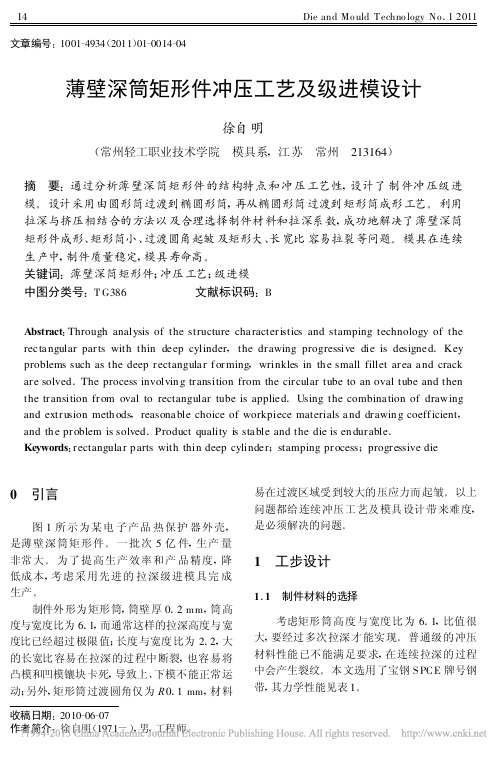
收稿日期:2010-06-07作者简介:徐自明(1971-),男,工程师。
文章编号:1001-4934(2011)01-0014-04薄壁深筒矩形件冲压工艺及级进模设计徐自明(常州轻工职业技术学院 模具系,江苏 常州 213164)摘 要:通过分析薄壁深筒矩形件的结构特点和冲压工艺性,设计了制件冲压级进模。
设计采用由圆形筒过渡到椭圆形筒,再从椭圆形筒过渡到矩形筒成形工艺。
利用拉深与挤压相结合的方法以及合理选择制件材料和拉深系数,成功地解决了薄壁深筒矩形件成形、矩形筒小、过渡圆角起皱及矩形大、长宽比容易拉裂等问题。
模具在连续生产中,制件质量稳定,模具寿命高。
关键词:薄壁深筒矩形件;冲压工艺;级进模中图分类号:T G386文献标识码:BAbstract :Through analysis of the structure character istics and stamping technology of the rectangular par ts with thin deep cylinder ,the dr awing progressive die is designed .Key problems such as the deep r ectangular f or ming ,wrinkles in th e small fillet ar ea and crack ar e solved .The process involvin g tr ansition from the cir cular tube to an oval tube and then the tr ansition fr om oval to rectangular tube is applied .Using the combination of drawing and extr u sion meth ods ,reasonable choice of workpiece materials and dr awin g coeff icient ,and th e pr oblem is solved .Product quality is stable and the die is en dur able .Keywords :r ectangular p arts with thin deep cylinder ;stamping pr ocess ;progr essive die0 引言图1所示为某电子产品热保护器外壳,是薄壁深筒矩形件。
薄壁零件冲床设计

图2 薄壁零件冲制工作原理图
2.设计条件与要求
动力源为电动机,上模做上下往复直线运动,其大致运动规律如图2b所示,要求有快速下沉、匀速工作进给和快速返回的特征。
上模工作段的长度L=40~100mm,对应曲柄转角φ=60º~90º;上模行程长度必须大于工作段长度的两倍以上,行程速比系数K≥1.5。
上模到达工作段之前,送料机构已将坯料送至待加工位置(下模上方),如图2a所示。
送料距离L=60~250mm。
要求机构具有良好的传力特性,特别是工作段的压力角α应尽可能小,一般取许用压力角[α]=50º。
生产率为每分钟70件。
按平均功率选用电动机。
需要5台冲床。
室内工作,载荷有轻微冲击,动力源为三相交流电动机。
使用期限为10年,每年工作250天,每天工作16小时。
每半年保养一次,每三年大修一次。
生产状况为中等规模机械厂,可加工7、8级精度的齿轮、蜗轮。
其他设计参数及要求见下表:
1)机构系统总体运动方案;画出系统运动简图,完成运动方案设计论证报告。
2)成传动系统或执行系统的结构设计,画出传动系统或执行系统的装配图。
3)设计主要零件,完成2张零件工作图。
4)编写设计说明书。
矩形盒冲压工艺分析及模具设计
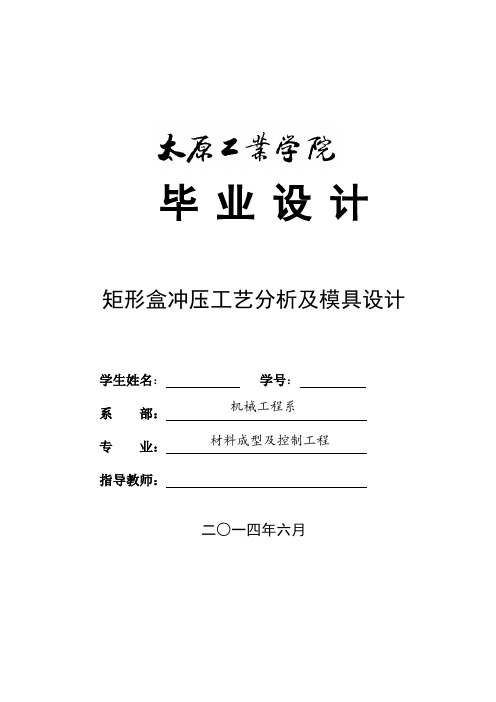
毕业设计矩形盒冲压工艺分析及模具设计学生姓名:学号:系 部:专 业:指导教师:二○一四年六月机械工程系 材料成型及控制工程诚信声明本人郑重声明:本论文及其研究工作是本人在指导教师的指导下独立完成的,在完成论文时所利用的一切资料均已在参考文献中列出。
本人签名:年月日毕业设计任务书设计题目:矩形盒冲压工艺分析及模具设计系部:机械工程系专业:材料成型及控制工程学号:学生:指导教师(含职称):专业负责人:1.设计的主要任务及目标(1)通过毕业设计能够巩固所学的各类基础知识、初步掌握冲压模具设计的流程,熟练掌握使用各类工具书籍。
(2)通过毕业设计使学生初步达到工程师所具备的基本素质。
2.设计的基本要求和内容(1)完成冲压件的工艺性分析(工艺分析、工艺方案确定、工艺计算)(2)进行冲压模具的结构设计和计算(主要零部件的结构设计、模具结构设计及模具工作部分尺寸计算等)(3)制定模具典型零件加工的工艺规程(4)完成模具总装配图及模具主要零部件图的绘制(5)编写模具毕业设计论文3.主要参考文献(1)冲压设计资料机械工业出版社王孝培主编(2)冲模图册机械工业出版社李天佑主编4. 进度安排设计(论文)各阶段名称起止日期1 开题报告2014.3.1——2014.3.152 工艺分析及计算2014.3.1——2014.4.153 模具结构设计及计算2014.4.1——2014.5.154 绘制图纸及编写设计说明书2014.5.1——2014.6.165 毕业答辩2014年6月中旬材料:08 厚度:1.5矩形盒冲压工艺分析及模具设计摘要:根据给定的具体零件图的尺寸和公差要求,并结合生产实际中的使用条件,设计了矩形盒落料拉深复合模以及切边模两套模具。
包括:冲裁工艺设计,复合模结构、形式的设计及主要工作部件设计等。
涉及模具方案的确定,材料的利用率,压力机的选择,模具正常工作时的情况,模具相应零部件的选取和制造。
完成了拉深力、冲裁力、切边力、卸料、定位零件、顶出装置等的计算,然后对主要零部件的设计和标准件进行选择,最后,阐述了对异形凸、凹模的加工过程。
薄壁筒型零件的工艺研究
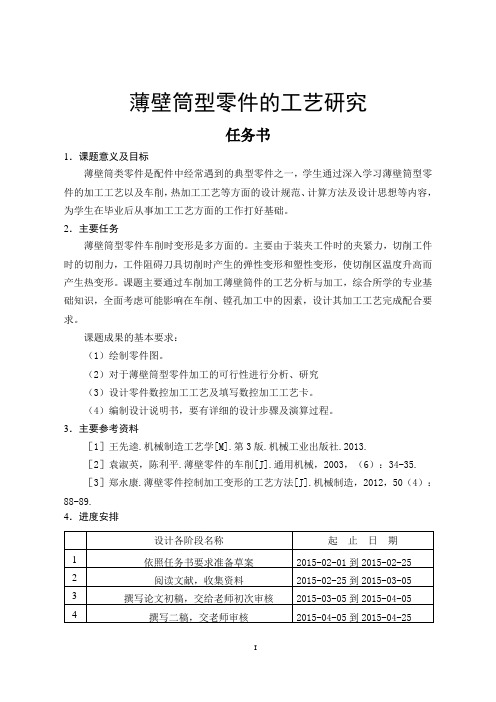
薄壁筒型零件的工艺研究任务书1.课题意义及目标薄壁筒类零件是配件中经常遇到的典型零件之一,学生通过深入学习薄壁筒型零件的加工工艺以及车削,热加工工艺等方面的设计规范、计算方法及设计思想等内容,为学生在毕业后从事加工工艺方面的工作打好基础。
2.主要任务薄壁筒型零件车削时变形是多方面的。
主要由于装夹工件时的夹紧力,切削工件时的切削力,工件阻碍刀具切削时产生的弹性变形和塑性变形,使切削区温度升高而产生热变形。
课题主要通过车削加工薄壁筒件的工艺分析与加工,综合所学的专业基础知识,全面考虑可能影响在车削、镗孔加工中的因素,设计其加工工艺完成配合要求。
课题成果的基本要求:(1)绘制零件图。
(2)对于薄壁筒型零件加工的可行性进行分析、研究(3)设计零件数控加工工艺及填写数控加工工艺卡。
(4)编制设计说明书,要有详细的设计步骤及演算过程。
3.主要参考资料[1]王先逵.机械制造工艺学[M].第3版.机械工业出版社.2013.[2]袁淑英,陈利平.薄壁零件的车削[J].通用机械,2003,(6):34-35.[3]郑永康.薄壁零件控制加工变形的工艺方法[J].机械制造,2012,50(4):88-89.4.进度安排薄壁筒型零件的工艺研究摘要:薄壁类零件刚度差、极易变形,并且在加工完成后短期或后期使用过程中,也会由于受到工件残余应力的影响从而导致二次变形,如何控制加工变形,成为了机械加工行业一个棘手的问题。
在目前的国内外研究中,薄壁筒型零件通常在刚加工完之后是符合精度要求的,但在过一段时间后,工件会由于自然变形过大从而导致失效。
通过对大量资料以及工厂加工过程中实际遇到的问题的总结分析,对薄壁筒型零件的结构特点和加工变形各种影响因素进行深入的探究发现,工件的结构与材料,装夹工艺、切削热、切削力等都是导致薄壁筒型零件变形的因素。
针对各种影响因素总结相应的控制方法。
分析多种加工方式,明确薄壁件的装夹方式和夹具、合理选择切削刀具、确定与之配套的切削工艺、实现薄壁筒型零件最大精度切削。
冲压级进模设计
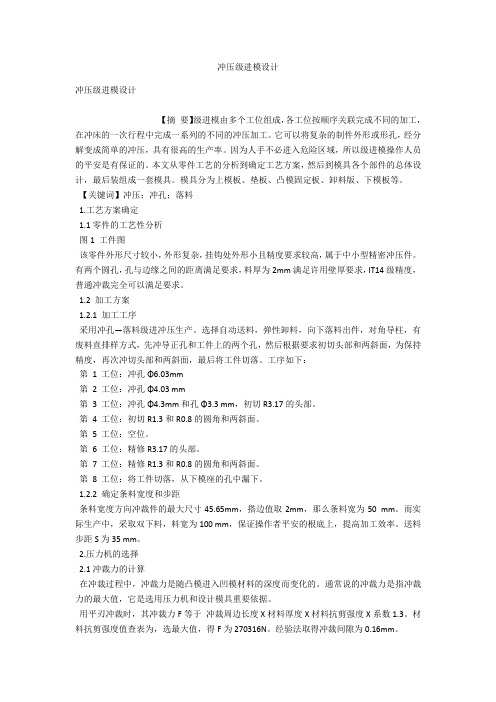
冲压级进模设计冲压级进模设计【摘要】级进模由多个工位组成,各工位按顺序关联完成不同的加工,在冲床的一次行程中完成一系列的不同的冲压加工。
它可以将复杂的制件外形或形孔,经分解变成简单的冲压,具有很高的生产率。
因为人手不必进入危险区域,所以级进模操作人员的平安是有保证的。
本文从零件工艺的分析到确定工艺方案,然后到模具各个部件的总体设计,最后装组成一套模具。
模具分为上模板、垫板、凸模固定板、卸料版、下模板等。
【关键词】冲压;冲孔;落料1.工艺方案确定1.1零件的工艺性分析图1 工件图该零件外形尺寸较小,外形复杂,挂钩处外形小且精度要求较高,属于中小型精密冲压件。
有两个圆孔,孔与边缘之间的距离满足要求,料厚为2mm满足许用壁厚要求,IT14级精度,普通冲裁完全可以满足要求。
1.2 加工方案1.2.1 加工工序采用冲孔―落料级进冲压生产。
选择自动送料,弹性卸料,向下落料出件,对角导柱,有废料直排样方式,先冲导正孔和工件上的两个孔,然后根据要求初切头部和两斜面,为保持精度,再次冲切头部和两斜面,最后将工件切落。
工序如下:第1 工位:冲孔Φ6.03mm第2 工位:冲孔Φ4.03 mm第3 工位:冲孔Φ4.3mm和孔Φ3.3 mm,初切R3.17的头部。
第4 工位:初切R1.3和R0.8的圆角和两斜面。
第5 工位:空位。
第6 工位:精修R3.17的头部。
第7 工位:精修R1.3和R0.8的圆角和两斜面。
第8 工位:将工件切落,从下模座的孔中漏下。
1.2.2 确定条料宽度和步距条料宽度方向冲裁件的最大尺寸45.65mm,搭边值取2mm,那么条料宽为50 mm。
而实际生产中,采取双下料,料宽为100 mm,保证操作者平安的根底上,提高加工效率。
送料步距S为35 mm。
2.压力机的选择2.1冲裁力的计算在冲裁过程中,冲裁力是随凸模进入凹模材料的深度而变化的。
通常说的冲裁力是指冲裁力的最大值,它是选用压力机和设计模具重要依据。
- 1、下载文档前请自行甄别文档内容的完整性,平台不提供额外的编辑、内容补充、找答案等附加服务。
- 2、"仅部分预览"的文档,不可在线预览部分如存在完整性等问题,可反馈申请退款(可完整预览的文档不适用该条件!)。
- 3、如文档侵犯您的权益,请联系客服反馈,我们会尽快为您处理(人工客服工作时间:9:00-18:30)。
收稿日期:2010-06-07作者简介:徐自明(1971-),男,工程师。
文章编号:1001-4934(2011)01-0014-04薄壁深筒矩形件冲压工艺及级进模设计徐自明(常州轻工职业技术学院 模具系,江苏 常州 213164)摘 要:通过分析薄壁深筒矩形件的结构特点和冲压工艺性,设计了制件冲压级进模。
设计采用由圆形筒过渡到椭圆形筒,再从椭圆形筒过渡到矩形筒成形工艺。
利用拉深与挤压相结合的方法以及合理选择制件材料和拉深系数,成功地解决了薄壁深筒矩形件成形、矩形筒小、过渡圆角起皱及矩形大、长宽比容易拉裂等问题。
模具在连续生产中,制件质量稳定,模具寿命高。
关键词:薄壁深筒矩形件;冲压工艺;级进模中图分类号:T G386文献标识码:BAbstract :Through analysis of the structure character istics and stamping technology of the rectangular par ts with thin deep cylinder ,the dr awing progressive die is designed .Key problems such as the deep r ectangular f or ming ,wrinkles in th e small fillet ar ea and crack ar e solved .The process involvin g tr ansition from the cir cular tube to an oval tube and then the tr ansition fr om oval to rectangular tube is applied .Using the combination of drawing and extr u sion meth ods ,reasonable choice of workpiece materials and dr awin g coeff icient ,and th e pr oblem is solved .Product quality is stable and the die is en dur able .Keywords :r ectangular p arts with thin deep cylinder ;stamping pr ocess ;progr essive die0 引言图1所示为某电子产品热保护器外壳,是薄壁深筒矩形件。
一批次5亿件,生产量非常大。
为了提高生产效率和产品精度,降低成本,考虑采用先进的拉深级进模具完成生产。
制件外形为矩形筒,筒壁厚0.2mm ,筒高度与宽度比为6.1,而通常这样的拉深高度与宽度比已经超过极限值;长度与宽度比为2.2,大的长宽比容易在拉深的过程中断裂,也容易将凸模和凹模镶块卡死,导致上、下模不能正常运动;另外,矩形筒过渡圆角仅为R 0.1mm ,材料易在过渡区域受到较大的压应力而起皱。
以上问题都给连续冲压工艺及模具设计带来难度,是必须解决的问题。
1 工步设计1.1 制件材料的选择考虑矩形筒高度与宽度比为6.1,比值很大,要经过多次拉深才能实现。
普通级的冲压材料性能已不能满足要求,在连续拉深的过程中会产生裂纹。
本文选用了宝钢S PCE 牌号钢带,其力学性能见表1。
图1 制件二维图及三维模型表1 宝钢SPC E 材料性能牌号材料状态屈服强度σs(不大于)/M Pa 抗拉强度σb(不小于)/M Pa 伸长率δ10(不小于)/%SPCE 已退火21027038从表1可以看出,S PCE 材料有较小的屈服强度σs ,σs 值不大于210M Pa 。
经过试验,屈服下限可以达到140M Pa ,屈服比值小,钢带的成形性能好,适合深筒拉深。
1.2 工序安排矩形件的多道拉深常用的有2种方法:一种是从腰圆形工序件直接拉成矩形工件,如图2(a )所示;另一种是有若干过渡的大圆角矩形工序件,最后拉成矩形工件,如图2(b )所示。
由于制件厚度小(δ=0.2mm )、侧面与侧面、侧面与底部过渡圆角非常小,仅为R 0.1mm 。
经过试验证明,该零件应用上述2种方法在过渡圆角区域都会产生起皱现象。
一方面是由于制件过渡圆角小壁薄,在拉深的过程中,圆角区域单位面积变形量大,材料在压应力的作用下失稳产生起皱;另一方面是由于腰圆形或过渡的大圆角在拉深成形为小圆角过程中产生了过多余材料,使得正常的向矩形两侧面的塑性流动受阻。
为了避免在过渡圆角区域会产生起皱,必须减小在圆角区域的单位变形量和多余材料。
本文采取如图2(c )所示的方法多道拉深。
在连续拉深的过程中,从圆形筒过渡到椭圆形筒,再从椭圆形筒过渡到矩形筒。
试验证明,采用这种方法批量生产出的拉深制件没有产生起皱。
图2 矩形件的多道拉深示意图1.3 毛坯直径D 的计算毛坯直径的计算以最后一次拉深成形的制件尺寸为基础,按拉深前毛坯面积与拉深后制件面积相等的等面积原则求出。
考虑到首次拉深拉入凹模的材料要比计算所需的多一些,故实际毛坯直径要比计算毛坯直径大,按式(1)计算: D =D 1+δ(1)式中:D ———实际毛坯直径D 1———计算毛坯直径δ———修边余量文献一般采用近似计算,将拉深制件分解成若干个简单几何形状,求出各部分的面积并相加,矩形拉深制件只能近似计算。
本文应用Pro /E 软件分析测量功能求得制件面积F 为572.6mm 2。
则D 1=4πF (2)=27mm式中:F ———制件面积取δ=1.5mm ,因此D =D 1+δ=28.5mm 。
1.4 拉深工序计算由极限拉深系数及工件毛坯直径,通过计算与调整,确定制件须经7次拉深方可成形,各次拉深相关数值如表2所示。
表2 拉深相关数值极限拉深系数[m n]实际拉深系数m n拉深系数差值Δ[m1]=0.43m1=0.51+0.08 [m2]=0.78m2=0.81+0.03 [m3]=0.80m3=0.86+0.06 [m4]=0.52m4=0.74+0.22 [m5]=0.54m5=0.75+0.21 [m6]=0.58m6=0.77+0.19 [m7]=0.60m7=0.62+0.021.5 工步设计工步如图3所示。
采用导正销定距,经双切口、多次拉深、整形和切边等冲压工序制成。
考虑切口凸模和卸料板安装固定位置(见图4),在工位3和5位置设置了2个空工位。
工步设有13个工位,各工位的冲压内容是:工位1,冲2-4mm导正孔;工位2,双切口;工位3,空位;工位4,拉深圆筒形;工位5,空位;工位6、7、8,连续拉深圆筒形;工位9,拉深椭圆形;工位10、11,连续拉深矩形;工位12,整形;工位13,切边。
图3 工步图2 模具结构及特点模具结构如图4所示,级进模具各部分的主要特点如下。
2.1 拉深凸模设计该深筒拉深级进模具冲压过程中拉深成形工作行程很大,凸模伸出凸模固定板部分较长。
为了提高凸模刚性和强度,结构设计成阶梯式,图5所示为工位10、11拉深凸模结构。
经过校核和试验,凸模在拉深力的作用下不会失稳。
1.下模座2.弹簧3、36.下垫板4.凹模固定板5.浮顶器6.切边凸模7、12、22、30.卸料板8、13、23.凸模固定板9、25.上垫板10.卸料板螺钉11.上模座14、16、17、18、20、21、24.拉深凸模15.检测销19.导正销26.脱料块27.刺破凸模28.导正销凸模29.压板31.浮动导料杆32.导料板33.浮动块34.切口凹模镶块35.切口入块37.顶杆38.托板39.橡胶40、43、45、48、50、52、54.拉深凹模镶块41.螺塞42、44、46、47、49、51、53.顶件杆55.弹簧图4 模具结构图5 阶梯式拉深凸模结构 设计凸模可以快速更换。
凸模与固定板的配合采用了0.020~0.025mm 小间隙配合,用螺钉、压板(图4件29)固定。
当凸模需要更换和修磨时,只要松动螺钉和压板,不必松动固定板和卸料板,这样更换凸模速度快,不会影响固定板的装配精度,延长了模具的使用寿命。
2.2 制件成形的关键点工位9、10完成了圆筒转变为椭圆筒拉深,又从椭圆筒过渡到矩形筒,是成形的关键点。
矩形长7.1mm ,宽3.3mm ,长宽比值为2.2,非常大,传统的拉深方法采用不变薄拉深。
凸模和凹模镶块之间的间隙是定值,如图6(a )所示,略大于材料厚度0.2mm 。
结果是:在工位10从椭圆筒过渡到矩形筒拉深过程中,长边承受拉应力,宽边承受压应力,材料流动量多,变形大,长边容易达到强度极限破坏拉裂,宽边材料受挤压涨大,导致在凸模和凹模镶块处卡死,上下不能运动。
本设计在传统方法基础上进行了改进,凸模和凹模镶块之间的间隙为变量,采用了拉深与挤压相结合的工艺。
如图6(b )所示,最大间隙在椭圆短轴方向,间隙值0.30mm ,最小间隙在椭圆长轴方向,间隙值0.21mm ,拉深系数控制在0.77左右,这样工位9得到的椭圆筒比厚是变化的,短轴处最厚,长轴处最薄,壁厚单边相差0.10mm 。
工位10拉深系数控制在0.62,保证了长边材料塑性变形量。
工位10成形的圆角半径比实际要求大,在工位12整形工位中再将圆角半径压到所要求的尺寸。
3 主要零件的材料由于制件批量大,尺寸稳定要求高,凸凹模图6 工位9凸凹模配合方案比较选用YG 8硬质合金制作。
YG8硬质合金具有高硬度、高耐磨性,能承受较大的应力,适合拉深级进模。
卸料板选用热处理变形小的合金工具钢Cr12,淬火至56~60HRC ;凸凹模固定板选用45﹟钢,调质处理至43~48HRC 。
模具凸凹模采用硬质合金后,寿命由采用Cr12M oV 钢模时的刃磨一次从55万次提高到200万次。
4 结论设计了一副薄壁深筒矩形件级进模。
建立了薄壁深筒矩形件成形工艺,成功地解决了深筒成形、小过渡圆角起皱及矩形大长宽比容易拉裂等问题。
模具在连续生产中,制件质量稳定,模具寿命高,刃磨一次达200万次以上。
参考文献:[1]陈炎嗣.多工位级进模设计与制造[M ].北京:机械工业出版社,2006.[2]胡世光.板料冷压成形原理[M ].北京:国防工业出版社,1979.[4]王孝培.冲压手册[M ].北京:机械工业出版社,2002.[5]王俊彪.多工位级进模设计[M ].北京:机械工业出版社,1999.[6]洪深泽.挤压工艺及模具设计[M ].北京:机械工业出版社,1996.。