药品生产洁净区
药品生产洁净厂房设计

Q=U×A
其中Q:管道流量:m3/秒或m3/分
U:水的流速,在自然流动下,取0.8米/秒平均值
A:管道截面积:m2。圆型管:A= π d 2d:直径。
当排水地漏直径为d=25mm(即1“管径)时,
4
管道流量:Q=U×A= π d2U= π ×0.0252×0.8
=0.000394 24m3/4秒=0.023544m3/分
300,000级 10500000
≥5um 0 2000 20000 60000
浮游菌/立方米 5 100 500 1000
沉降菌/皿 1 3
10 15
药品生产洁净厂房设计
二、无菌药品 无菌药品是指法定药品标准中列有无菌检查项目的制剂。 1、无菌药品生产环境的空气洁净度级别要求: (1)最终灭菌药品: 100级或10,000级监督下的局部100级:大容量注射剂(≥50亳升)的灌封; 10,000级:注射剂的稀配、滤过: 小容量注射剂的灌封: 直接接触药品的包装材料的最终处理。 100,000级:注射剂浓配或采用密闭系统的稀配。 (2)非最终灭菌药品: 100级或10,000级背景下局部100级: 灌装前不需除菌滤过的药液配剂; 注射剂的灌封、分装和压塞; 直接接触药品的包装材料最终处理后的暴露环境。 10,000级:灌装前需除菌滤过的药液配制。 100,000级:轧盖,直接接触药品的包装材料最后一次精洗的最低要求 (3)其它无菌药品: 10,000级:供角膜创伤或手术用滴眼剂的药配品生制产和洁净灌厂装房设。计
(d)本附录中“静态”及”动态“条件下尘粒最大允许数基本上对应于与ISO 14644-1 0.5um的洁净级别。
(e)这些区域应完全没有大于或等于5um的粒子,由于无法从统计意义上证明不存在任何粒子,因 此将标准设成1个/米3,但考虑到电子噪声、光散射及二者并发所致的误报因素,可取20个/m3 的限度标准。在洁净区确认时,应达到规定的标准。
药品生产洁净区域划分说明

药品生产洁净区域划分说明
药品生产洁净区域划分说明如下:
1. 室外区:该区域是厂区内部或外部无生产活动和更衣要求的区域。
通常包括与生产区不连接的办公室、机加工车间、动力车间、化工原料储存区、餐厅、卫生间等。
2. 一般区和保护区:一般区和保护区是厂房内部产品外包装操作和其他不将产品或物料明显暴露操作的区域。
一般区:没有产品直接暴露或没有直接接触产品的设备和包材内表面直接暴露的环境,如无特殊要求的外包装区域,环境对产品没有直接或间接的影响,环境控制只考虑生产人员的舒适度。
保护区:没有产品直接暴露或没有直接接触产品的设备和包材内表面直接暴露的环境,但该区域环境或活动可能直接或间接影响产品,如有温湿度要求的外包装区域、原辅料及成品库房、更衣室等。
3. A级:高风险操作区,如灌装区、放置胶塞桶、敞口安瓿瓶、敞口西林瓶的区域及无菌装配或连接操作的区域。
通常用层流操作台(罩)来维持该区的环境状态。
层流系统在其工作区域必须均匀送风,风速为0.36-0.54 m/s(指导值)。
应有数据证明层流的状态并须验证。
在密闭的隔离操作器或手套箱内,可使用单向流或较低的风速。
4. B级:指无菌配制和灌装等高风险操作A级区所处的背景区域。
5. C级和D级:指生产无菌药品过程中重要程度较低的洁净操作区。
其中C级对应万级,静态条件下符合万级标准,动态条件下符合D级标准,即十万级;D级对应十万级。
医药洁净室的标准

GMP对洁净厂房的标准GMP的厂房设施原则:1)、空间面积适应生产需要,布局合理。
2)、能有效控制差错和污染。
3)、便于维护和清洁。
一,企业的生产环境应整洁;厂区地面、路面及运输等不应对药品生产造成污染;生产、行政、生活和辅助区总体布局应合理,不得互相妨碍。
●地面、路面硬化;绿化不起尘;设物流运输通道。
●生产区与生活区分开(倒班宿舍、工间食堂与行政管理为生产服务施,可设在行政区)。
●总布局洁净厂房置上风向,锅炉、提取、生物脏器处理、动物房等置下风向;危险品、化学品库独立设置。
二,厂房应按生产工艺流程及所要求的空气洁净度级别进行合理布局。
●厂房内按工艺中物流最短路线,顺流布局。
●辅助间位置合理,洁净生产区的级别划分应符合GMP附录的要求,布局尽可能做到“同一级别集中在同一个区,同一个级别在同一个平面。
”三,同一厂房内的生产操作和相邻厂房之间的生产操作不得相互防碍。
●厂房按洁污合理分隔(高致敏类产品设专用厂房;毒、麻类产品厂房;激素类、抗肿瘤类产品厂房;生物制品、血液制品厂房设专用车间或专用厂房)●厂房内应按工序合理分隔操作间原则:1)、对产尘、产湿及工艺对温、湿度有特殊要求的操作工序作重点分隔;2)、同一操作间内不得同时进行不同批次产品的生产操作。
四,厂房应有防止昆虫和其它动物进入的有效设施。
●厂房直通外界的门、窗设有防止昆虫、动物进入的有效设施●(防止进入有效设施:档鼠板h≥30mm、电驱鼠(20m有效)、风帘、金属沙窗、粘鼠胶×、鼠药×、捕鼠器×、灭蚊器)。
●厂房≠仓库1,洁净室(区)的内表面应平整光滑、无裂缝、接口严密、无颗粒物脱落、耐受清洗和消毒。
2,洁净室(区)的墙壁与地面的交界处应成弧形或采取其他措施,以减少积聚和便于清洁。
3,洁净室(区)的窗户、天棚及进入室内的管道、风口、灯具与墙壁或天棚的连接部位应密封。
●对洁净室(区)内表面要求:墙面、地面平整无缝、光滑耐磨、易清洁。
中国药品生产洁净室(区)空气洁净度标准

中国药品生产洁净室(区)空气洁净度标准
中国药品生产洁净室(区)空气洁净度标准是根据《药品生产质量管理规范》(GMP)制定的,主要规定了药品生产洁净室(区)空气洁净度的要求和标准。
具体来说,中国药品生产洁净室(区)空气洁净度标准主要包括以下几个方面:
1.空气洁净度级别:根据药品生产洁净室(区)的用途和生产工艺,将空气洁净度分为A级、B级、C级、D级四个级别。
2.空气洁净度检测:要求对药品生产洁净室(区)的空气洁净度进行定期检测和监测,检测频率为每月一次,检测方法包括尘埃粒子计数、浮游菌检测等。
3.空气净化系统:要求对药品生产洁净室(区)的空气净化系统进行定期维护和保养,包括空气过滤器的更换、空气净化设备的清洗等。
4.空气污染控制:要求对药品生产洁净室(区)的空气污染进行控制,包括防止外部污染进入洁净室(区)、防止内部污染扩散等。
5.空气质量管理:要求对药品生产洁净室(区)的空气质量进行管理和监控,包括建立空气质量管理制度、制定空气质量管理计划等。
总之,中国药品生产洁净室(区)空气洁净度标准的目的是为了保证药品生产洁净室(区)的空气洁净度符合相关要求和标准,从而保证药品的生产质量和安全性。
无菌药品生产所需的洁净区可分为以下4个级别

无菌药品生产所需的洁净区可分为以下4个级别:
A级
高风险操作区,如:灌装区、放置胶塞桶、敞口安瓿瓶、敞口西林瓶的区域及无菌装配或连接操作的区域。
通常用层流操作台(罩)来维持该区的环境状态。
层流系统在其工作区域必须均匀送风,风速为0.36-0.54m/s (指导值)。
应有数据证明层流的状态并须验证。
在密闭的隔离操作器或手套箱内,可使用单向流或较低的风速。
B级
指无菌配制和灌装等高风险操作A级区所处的背景区域。
C级和D级
指生产无菌药品过程中重要程度较低的洁净操作区。
制药车间洁净级别与生产区域划分的考虑点-精品

制药车间洁净级别与生产区域划分的考虑点关于洁净级别的划分,在2010版GMP正文中并没有详细描述,只是在第四十八条有一句“口服液体和固体制剂、腔道用药(含直肠用药)、表皮外用药品等非无菌制剂生产的暴露工序区域及其直接接触药品的包装材料最终处理的暴露工序区域,应当参照“无菌药品”附录中 D 级洁净区的要求设置。
附录2《原料药》第三条:非无菌原料药精制、烘干、粉碎、包装等生产操作的暴露环境应当按照D级洁净区的要求设置。
附录3《生物制品》第十四条:D级(原料血浆的合并、组分分离、分装前的巴氏消毒。
口服制剂其发酵培养密闭系统环境。
酶联免疫吸附试剂等体外免疫试剂的配液、分装、干燥、内包装)。
C级(体外免疫试剂的阳性血清的分装、抗原与抗体的分装)。
B+A(无菌药品中非最终灭菌产品规定的各工序,灌装前不经除菌过滤的制品其配制、合并等)。
附录4《血液制品》第十四条:原料血浆破袋、合并、分离、提取、分装前的巴氏灭活等工序至少在D级洁净区内进行。
附录5《中药制剂》第十一条:提取、浓缩、收膏工序密闭系统生产的,操作环境可在非洁净区,敞口方式生产的,操作环境应当与其制剂配制操作区的洁净级别相适应。
第十四条:中药注射剂浓配前的精制工序应当至少在D级洁净区内完成。
第十五条:非创伤面外用中药制剂及其他特殊的中药制剂可在非洁净厂房内生产。
那么对于制药厂房洁净级别的划分与使用,我们应该更多参照附录1《无菌药品》。
第三章《洁净度级别及监测》生产操作环境洁净度级别选择主要参照《第十三条》。
通过学习,我们不难发现:一、(B+A)环境的应用1、非最终灭菌产品的灌装(或灌封)、分装、压塞、轧盖等(未完全密封状态)。
2、非最终灭菌产品的灌装前无法除菌过滤的药液或产品的配制(非最终灭菌又无法除菌过滤的混悬剂、乳剂、植入剂、手术/创伤类膏剂、散剂、气雾剂……,可最终灭菌的除外)。
3、非最终灭菌产品(含无菌原料药)直接接触药品的包装材料、器具灭菌后的装配以及处于未完全密封状态下的转运和存放(隧道烘箱出口瓶暂存转盘、胶塞铝盖清洗灭菌后的暂存、器具灭菌后未完全密封状态下的暂存,最好还是密封,否则转运就要B+A了)。
中国新版GMP洁净度级别-2010新版GMP洁净区等级划分

中国新版 GMP 洁净度级别-2010 新版 GMP 洁净区等级划分《药品生产质量管理规范( 2010 年修订)》(新版 GMP)于 2011年 3 月 1 日起施行,本文主要介绍新版GMP 中关于洁净度等级中的A、B、C、D 四个级别,以及新版GMP 与 98 版中关于洁净度等级的区别。
GMP 中 A、B、C、D 级控制上有动静态之分,而百级、万级、十万级则基本无动静态之分,两者之间有着明显的差异。
新版GMP 参照 ISO14644 中规定具体标准如下:新版 GMP 采用了欧盟和最新WHO 的 A、B、C、D 分级标准,并对无菌药品生产的洁净度级别提出了非常具体的要求。
静态测量:是指所有设备均已安装就绪,但未运行且没有操作人员在现场的状态。
动态测量:是指生成设备均按预定的工艺模式运行且有规定数量的操作人员在现场操作的状态。
无菌药品的生产所需的洁净区可以分为 4 个级别: 2010 新版 GMP 洁净区等级划分A 级:高风险操作区,如灌装区、放置胶塞桶和与无菌制剂直接接触的敞口包装容器的区域及无菌装配或连接操作的区域,应当用单向流操作台(罩)维持该区的环境状态。
单向流系统在其工作区域必须均匀送风,风速为0.36-0.54m/s (指导值)。
应当有数据证明单向流的状态并经过验证。
在密闭的隔离操作器或手套箱内,可使用较低的风速。
B 级:指无菌配制和灌装等高风险操作 A 级洁净区所处的背景区域。
C 级和D 级:指无菌药品生产过程中重要程度较低操作步骤的洁净区中国 GMP(2010 修订)2010 年版 GMP 附录 1 无菌药品,第三章,第九条……洁净区各级别空气悬浮粒子的标准规定如下表:新版 GMP 洁净度等级 A、B、C、DA 级洁净区洁净操作区的空气温度应为20-24℃洁净操作区的空气相对湿度应为45%-60 %操作区的风速:水平风速≥0.54m/s垂直风速≥0.36m/s高效过滤器的检漏大于99.97%照度:> 300lx-600lx噪音:≤75db(动态测试 )B 级洁净区洁净操作区的空气温度应为20-24℃洁净操作区的空气相对湿度应为45%-60 %房间换气次数:≥25次/h 压差:B 级区相对室外≥10Pa,同一级别的不同区域按气流流向应保持一定的压差。
药品生产洁净区

药品生产洁净区(室)洁净度的保证出处:北京欣惠泽奥科技有限公司专营实验室仪器、分子生物学试剂、生物化学试剂、细胞培养基、实验室器材及玻璃器发布日期:2011-1-20 9:49:43 浏览次数:205近年来,随着GMP认证及复认证工作的进行,特别是GMP(2009年4月公示)专家讨论版的出台,进一步强调了“药品质量是设计和生产出来的”,保证药品质量的生产的环境要求也在提高,洁净技术工程受到制药企业的普遍关注。
下面将对药品生产中影响洁净度的因素进行分析,愿有助于大家更深刻了解微生物污染及其控制,以便在实际应用中有更进一步的提高。
药品生产中的洁净区(室)是指将一定空间范围内的空气中微粒子、有害气体、细菌等污染物排除,并将室内温度、洁净度、室内压力、气流速度与气流分布、噪音振动及照明、静电控制在某一需求范围内,而所给予特别设计的房间。
也就是说不论外在空气条件如何变化,其室内均能具有维持原先所设定要求的洁净度、温湿度及压力等性能特性。
根据以上功能按洁净程度要求不同又分为100级、1万级、10万级、30万级4个级别(或A、B、C、D4个级别)。
1 合理选择洁净室送(回)风方式1.1 送风方式的选择1.1.1 乱流式(TurbulentFlow)空气由空调箱经风管与洁净室内的高效空气过滤器(HEPA)进入洁净室,并由洁净室两侧隔间墙板或高架地板回风。
气流非直线型运动而呈不规则之乱流或涡流状态。
优点:构造简单、系统建造成本低,洁净室之扩充比较容易,在某些特殊用途场所,可并用无尘工作台,提高洁净室等级。
1.1.2 层流式(Laminar)层流式空气气流运动成一均匀的直线形,空气由覆盖率100%的过滤器进入室内,并由高架地板或两侧隔墙板回风,此型式适用于洁净室等级较高的环境。
其型式可分为水平层流式和垂直层流式2种。
(1)水平层流式:水平式空气自过滤器单方向吹出,由对边墙壁的回风系统回风,尘埃随风向排出室外,一般在下流侧污染较严重。
药品生产洁净区工作总结

药品生产洁净区工作总结
在药品生产过程中,洁净区的工作至关重要。
洁净区是指在生产过程中需要保
持高度清洁和无菌环境的区域,以确保药品的质量和安全。
在过去的一段时间里,我有幸在洁净区工作,积累了一些经验和体会,现在我想对这段时间的工作进行总结。
首先,洁净区工作需要高度的责任心和细心。
在洁净区工作,我们需要时刻保
持警惕,确保工作过程中不会出现任何可能影响药品质量的因素。
每一步操作都需要严格按照标准操作程序进行,不能有丝毫马虎。
只有这样,才能保证生产出的药品符合质量标准。
其次,洁净区工作需要团队合作。
在洁净区工作,每一个环节都需要多人协作,任何一环出现问题都有可能影响整个生产流程。
因此,团队合作至关重要。
在工作中,我们需要相互配合,互相监督,确保每一个细节都得到严格执行。
此外,洁净区工作需要不断的学习和提高自身素质。
随着科技的不断发展,洁
净区的工作标准也在不断提高,我们需要不断学习新知识,提高自身技能,以适应新的工作要求。
只有不断提高自身素质,才能更好地适应洁净区工作的需要。
总的来说,洁净区工作是一项重要而且复杂的工作,需要我们时刻保持警惕,
团队合作,不断学习和提高自身素质。
只有这样,才能确保生产出的药品符合质量标准,为人们的健康保驾护航。
希望在未来的工作中,我能够继续努力,不断提高自身素质,为洁净区的工作贡献自己的力量。
药品生产洁净区域划分说明

药品生产洁净区域划分说明【原创版1篇】目录(篇1)一、药品生产洁净区域的划分二、洁净级别的选择与应用三、无菌药品的生产洁净区域划分四、非无菌药品的生产洁净区域划分五、洁净区域的监测与控制正文(篇1)在药品生产过程中,洁净区域的划分是非常重要的一环,它直接影响到药品的质量和安全性。
本文将对药品生产洁净区域的划分进行详细说明,包括洁净级别的选择与应用,无菌药品和非无菌药品的生产洁净区域划分等。
一、药品生产洁净区域的划分药品生产洁净区域是指在生产过程中,需要对环境中的尘埃、微生物、温度、湿度等因素进行控制的区域。
根据药品的性质和生产工艺的不同,洁净区域可以分为无菌药品生产洁净区域和非无菌药品生产洁净区域。
二、洁净级别的选择与应用洁净级别的选择主要根据药品的性质、生产工艺和生产环境的要求来确定。
常见的洁净级别有 A 级、B 级、C 级和 D 级。
其中,A 级洁净区主要用于无菌药品的生产,B 级洁净区主要用于非无菌药品的生产,C 级洁净区主要用于原料药的生产,D 级洁净区主要用于药品的包装和装配。
三、无菌药品的生产洁净区域划分无菌药品的生产洁净区域主要包括无菌药品的制备、灌装、分装、装配和包装等工序。
根据无菌药品的生产工艺和要求,无菌药品的生产洁净区域应至少划分为 A 级洁净区、B 级洁净区和 D 级洁净区。
四、非无菌药品的生产洁净区域划分非无菌药品的生产洁净区域主要包括原料药的精制、粉碎、混合、分装和包装等工序。
根据非无菌药品的生产工艺和要求,非无菌药品的生产洁净区域应至少划分为 C 级洁净区和 D 级洁净区。
五、洁净区域的监测与控制洁净区域的监测与控制是保证药品质量的重要环节。
企业应定期对洁净区域进行监测,确保洁净区域的环境符合要求。
制药车间洁净区域划分

制药车间洁净区域划分
制药车间洁净区域划分是根据药品生产质量管理规范(GMP)的相关规定和要求,将车间按照洁净度等级划分为不同的区域,以确保药品生产过程中的环境控制和产品质量。
一般来说,制药车间的洁净区域可以分为以下四个级别:
1.A级:属于高风险操作区域,如灌装区、放置胶塞桶、敞口安瓿瓶、敞口西林瓶的区域及无菌装配或连接操作的区域。
在无菌装配或连接操作区域,需要用单向流操作台来维护该区域的环境状态,只有在密闭的隔离操作区或手套箱内,方可使用较低的风速。
2.B级:一般指无菌配制、灌装等高风险操作A级洁净区所处的背景区域。
3.C级和D级:通常指无菌药品生产过程中重要程度较低的操作步骤的洁净区。
对于不同级别的洁净区域,洁净度的控制要求也有所不同。
一般来说,A级洁净区是最高的洁净度等级,需要用单向流操作台来维持环境状态,风速控制在一定范围内;B级洁净区背景区域则需要在静态条件下满足百级即可,动态条件下可以符合万级标准;C级和D级
洁净区则分别对应万级和十万级标准。
此外,制药车间的洁净区域还可以根据生产工艺和产品特点进行进一步的划分和控制,如根据产品种类、生产流程、洁净度等级、操作方式等因素进行划分,以满足药品生产的质量和安全要求。
总之,制药车间的洁净区域划分是药品生产质量管理的重要环节之一,需要根据具体情况进行科学合理的划分和控制,以确保药品生产过程中的环境控制和产品质量。
药品生产洁净室
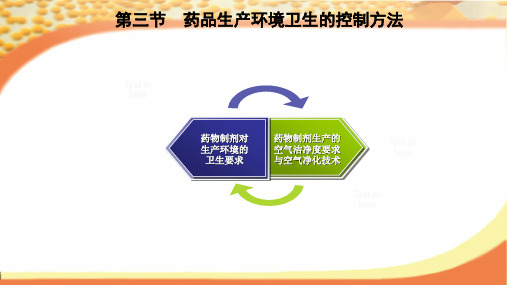
B级:指无菌配
制和灌装等高风 险操作A级洁净
区所处的背景区 域。
A级:高风险操 作区,如灌装区、 放置胶塞桶和与 无菌制剂直接接 触的敞口包装容 器的区域及无菌 装配或连接操作 的区域
药品生产洁净室(区)空气洁净度级别表
洁净度级别
A级 B级 C级 D级
≥0.5μ m 3520 3520 352000 3520000
C级 体外免疫诊断试剂的阳性血清的分装、抗原 与抗体的分装。
D级 原料血浆的合并、组分分离、分装前的巴氏 消毒,口服制剂其发酵培养密闭系统环境(暴露部分 需无菌操作),酶联免疫吸附试剂等体外免疫试剂的 配液、分装、干燥、内包装。
【血液制品】
原料血浆破袋、合并、分离、提取、分装前的巴氏灭活工 序至少在D级洁净区内进行。
悬浮粒子最大允许数/立方米
静态 20
≥5.0μ m
≥0.5μ m 3520
29 2900 29000
352000 3520000
不作规定
动态 ≥5.0μ m
20 2900 29000
不作规定
药物制剂生产的空气洁净度要求与空气净化技术
【不同药物制剂对生产环境的空气洁净度要求】
【无菌制剂】
Ⅰ. 最终灭菌药品
空气净化技术
空气净化技术
【空气滤过器】
空气滤过器常由单元滤过器(滤材装进金属或木质框 架内制成的滤过单元)组成,用时将单个或多个单元 滤过器组装到通风管或通风柜的空气滤过箱内。
板式空气过滤器 空气滤过器 楔式和袋式空气滤过器
折叠式空气滤过器
【空气滤过器的性能参数】
1)面速 2)滤速 3)滤过效率η 4)穿透率K 5)净化系数Ke 6)滤过阻力 7)容尘量
制药车间洁净区标准

制药车间洁净区标准制药车间洁净区标准通常按照GMP(药品生产质量管理规范)规定,根据药品的生产工艺和生产环境的洁净度要求,将制药车间划分为不同的洁净区。
以下是一些常见的制药车间洁净区标准和要求:1. 洁净度级别:根据药品生产工艺和生产环境的洁净度要求,将制药车间划分为不同的洁净度级别,如A级、B级、C级和D级。
其中,A级为高风险操作区,如灌装区、放置胶塞桶、敞口安瓿瓶、敞口西林瓶的区域及无菌装配或连接操作的区域;B级为无菌配制和灌装等高风险操作A级区所处的背景区域;C级和D级为生产无菌药品过程中重要程度较低的洁净操作区。
2. 空气洁净度:制药车间洁净区的空气洁净度需要达到一定的标准。
通常采用洁净室(区)标准,即用悬浮粒子浓度这个主要指标,来划分洁净室(区)及相关受控环境中空气洁净度的等级。
这个标准通常由美国联邦政府洁净室标准委员会(FED)提出,并在ISO 14644-1中进行了修订。
3. 温度和湿度控制:制药车间洁净区需要控制温度和湿度,以保障药品生产的稳定性和质量。
通常,洁净区的温度应控制在20-25℃,相对湿度控制在45-60%。
4. 照明和通风:制药车间洁净区需要保持良好的照明和通风。
照明强度应符合相关规定,通风系统则需要根据药品生产工艺要求进行设计,保证空气流通和防止交叉污染。
5. 设备和人员管理:制药车间洁净区需要严格控制人员进出和物料管理。
人员进出需要经过严格的清洁和消毒程序,物料进出也需要经过严格的检查和消毒程序。
此外,制药车间洁净区的设备也需要进行定期维护和保养,以保证其正常运转。
总之,制药车间洁净区标准是保障药品质量和安全的关键因素之一。
通过合理的规划和设计,以及严格的设备和人员管理,可以确保药品生产环境的洁净度和安全性,从而保障患者的健康和安全。
药品生产洁净区域划分说明

药品生产洁净区域划分说明摘要:I.药品生产洁净区域划分的重要性A.确保药品质量和安全B.符合法规要求C.降低污染和交叉感染的风险II.洁净区域的等级和划分A.洁净区域的等级1.等级1: 高度洁净区2.等级2: 中度洁净区3.等级3: 低度洁净区B.洁净区域的划分1.一般生产区2.洁净生产区3.控制区4.洁净室III.洁净区域划分的考虑因素A.药品类型和生产工艺B.生产设备和操作流程C.人员培训和操作规范IV.洁净区域的管理和监测A.洁净区的管理1.人员管理2.物料管理3.设备管理B.洁净区的监测1.空气质量监测2.微生物监测3.定期检查和审计正文:药品生产洁净区域划分说明在药品生产过程中,洁净区域的划分至关重要。
它不仅有助于确保药品的质量和安全,而且符合法规要求,降低污染和交叉感染的风险。
本文将详细介绍药品生产洁净区域的划分说明。
首先,我们需要了解洁净区域的等级和划分。
洁净区域的等级主要分为三类:等级1(高度洁净区)、等级2(中度洁净区)和等级3(低度洁净区)。
这些等级的划分取决于洁净区域内空气中的颗粒物数量、微生物数量以及温度和湿度等因素。
此外,洁净区域还可以根据功能划分为一般生产区、洁净生产区、控制区和洁净室。
在划分洁净区域时,需要考虑多种因素。
首先是药品类型和生产工艺。
不同的药品在生产过程中可能产生不同的污染,因此需要采取不同的洁净措施。
其次是生产设备和操作流程。
生产设备和操作流程的复杂程度直接影响到洁净区域的大小和形状。
最后是人员培训和操作规范。
在洁净区域内操作的人员需要接受专门的培训,了解洁净区域的重要性以及如何正确操作。
为了保证洁净区域的有效运行,还需要对其进行严格的管理和监测。
洁净区的管理包括人员管理、物料管理和设备管理。
人员管理需要确保在洁净区域内操作的人员具备必要的知识和技能,物料管理需要控制物料的进出以防止污染,设备管理需要定期对生产设备进行维护和清洁。
此外,洁净区的监测也是必不可少的。
制药企业空调净化和洁净级别

中文字数用计算机统计,欧盟GMP通则不包括原料药 显而易见,我国《规范》篇幅过短
中外GMP篇幅比较(中文字数)
分类
通则
无菌药品
小计
WHO GMP
2.6
~ 1万
3.6万
EU GMP
~ 2
~ 1万
~3万
FDA CGMP
~ 2
7万
~9万
中国GMP
0.74
0.15万
~1万
FDA 无菌药品GMP指南
范围
级 别 名 称
≥ 0.5μm
电 子 工 业
国际制(公)
美国惯用(英)
粒子数 /m3
粒子数/ ft3
M1
-
10.0
0.283
M1.5
1
35.3
1.00
M2
-
100
2.8
M2.5
10
353
10.0
M3
-
1 000
28.3
制 药 工 业
M3.5
100
3 530
100
M4
-
10 000
283
M4.5
初级隔离系统-1
LABS 工艺操作被PC-聚碳酸酯组成的帘膜-墙/门所保护 必要时可将门帘打开 通常通过手套管操作 减少对层流的干扰 以B级作为背景
LAF-天花板
工艺 -灌装 -传输
聚碳酸酯的可开启门 控制工艺周围的层流 正常操作通过手套管
操 作 人 员
中级隔离系统-2
RABS 工艺操作被PC-聚碳酸酯组成的帘膜-墙/门所保护 只有应急才能打开 开门必须有记录 通常通过手套管操作 物料通过物料口进 对层流的干扰须作解释 以B级作为背景
药厂洁净区个人工作总结

时光荏苒,转眼间我在药厂洁净区工作已有一年的时间。
在这一年的工作中,我始终秉持着严谨、负责的态度,认真履行自己的职责,努力提高自己的业务水平。
现将我的工作总结如下:一、工作职责作为一名药厂洁净区员工,我的主要工作职责是负责洁净区的日常维护、设备操作及药品生产过程中的质量控制。
具体包括:1. 负责洁净区的环境卫生,确保生产环境的洁净度;2. 按照操作规程进行设备操作,确保生产设备的正常运行;3. 监督生产过程中的质量控制,确保药品质量符合国家标准;4. 参与生产过程中的突发事件处理,确保生产安全。
二、工作体会1. 学习与成长:在洁净区工作的一年里,我逐渐熟悉了药厂的生产流程,掌握了药品生产的基本知识和技能。
通过不断学习和实践,我的业务水平得到了显著提高。
2. 团队协作:洁净区工作需要各部门的紧密协作,我在工作中学会了与同事沟通交流,共同解决问题。
在团队协作中,我体会到了团队的力量,也提高了自己的沟通能力。
3. 责任与担当:洁净区工作关系到药品质量,我深知自己肩负的责任重大。
在工作中,我始终保持严谨的态度,对待每一个环节都精益求精,力求做到最好。
三、工作中存在的问题1. 理论知识储备不足:虽然我在工作中积累了实践经验,但理论知识储备仍有待提高。
为了更好地胜任工作,我需要在今后的工作中加强学习,提升自己的综合素质。
2. 应对突发事件的能力有待提高:在工作中,我遇到了一些突发事件,虽然能够及时处理,但应对能力仍有待提高。
为了更好地应对各种情况,我需要在今后的工作中积累经验,提高自己的应变能力。
四、今后工作计划1. 加强理论学习:为了提高自己的业务水平,我计划在业余时间学习相关专业知识,充实自己的理论知识储备。
2. 提高应变能力:在工作中,我将不断总结经验,提高应对突发事件的能力,确保生产安全。
3. 优化工作流程:针对工作中存在的问题,我将与同事共同探讨,优化工作流程,提高工作效率。
总之,过去的一年我在药厂洁净区工作取得了一定的成绩,但也存在一些不足。
药品生产技术《制药企业洁净区人员行为规范要求》

制药企业洁净区人员行为标准要求一、洁净区级别划分标准及要求制药企业洁净区划分-GM〔二〕洁净区微生物监测动态标准二、洁净区〔间〕主要污染·工作人员:约占50~80%或更高·生产设施及物料:约占15 ~30% ·环境设施:约占5% ~2021〔一〕尘粒和微生物的进入和产生1、不合规的更衣及外装2、不标准的操作行为3、生产线的“动态〞生产4、环境屏障净化系统失控失效〔二〕尘粒和微生物散播1、触摸接触污染2、空气流动污染〔三〕主要污染源1、人是最大的污染源人体、内衣、工服外饰、卫生、习惯和行为均会产生大污染;其中皮肤、头发、口、鼻〔眼等〕、工服工鞋和化装品等均是主要污染源;研究资料介绍:咳嗽/次:散发约70万个尘粒喷嚏/次:散发约1 40万个尘粒交谈/分钟:万~万尘粒头及皮肤上有几万个到几百万个微生物指夹污垢中有几千万个到几十亿个微生物每只手可携带40万个细菌;刚洗过的手,每平方厘米也可检验出32021细菌洁净室内人员穿无菌服时,静止时发菌量一般为10~300个/分钟,躯体一般活动时的发菌量为150~1000个/分钟,快步行走时发菌量为900~2500个/分钟;洁净区人员培训不标准或考核确认不达标,内衣和卫生不符合要求,操作人员不熟练或素质低进入洁净区后,其习惯和行为不标准,会产生新的大量污染源〔连续不断产生和散发大量微粒和微生物进入空间〕,导致洁净区/室洁净度大大降低,直接污染药品;高素质、技术熟练的操作人员是控制污染和洁净生产最重要的保证条件之一;洁净室内人员有更大的责任去理解、接受和执行GM〕,不跺脚;定期对手进行消毒;不操作时,应将前臂和双手放在前面,不接触衣服及任何物品;区内身体一直站立,不能斜靠或靠触任何设备设施;平时双手高度不应低于腰部,不得搓手;手接触任何物品前后,均进行手消毒,平时要定时消毒;防止不必要的移动、转身和大动作;按清洁顺序及标准〔SOP〕要求进行入区人员不得化装;手套出现破损不得继续操作;不得拣所有掉在地面上的物品〔落地即被污染〕;不应用手触摸本人外装任何局部如口罩、揉鼻子等〕;防止从层流区附近走动,严禁将手伸进层流区〔除非必要时〕;操作行为不得在处理点上方或影响产品层流保护;无菌装配试验应有层流保护,从低处开始向上安装;工作其间不得直接去更衣室更换手套和口罩;必要时才讲话,不得面对生产区打喷嚏,并立即消毒处理任何操作方式不得影响产品的无菌性;生产线灌装区出现故障影响产品无菌性时不得维修〔调量除等外〕;离开层流的无菌工器具等必须在有保护的情况下转移;2、洁净区----行为标准要求除无菌区药品生产必须遵守的款项外,均适用其它洁净区;不得坐靠一切设施;不得靠肘休息;不得通过气锁讲话;搬运物料时,手宜放在非污染部位搬运物料时轻拿轻放;人身不得处在翻开物料口的上方;保持口罩紧度,减少口腔对洁净区污染;自觉保持洁净间和区内物品清洁;工器具清洗后要立即进行枯燥对洁布分类清洗并枯燥放置防止着装不正确,导致散播身体微粒严禁不戴手套用手接触外表及物料严禁在洁净室内脱去洁净服严禁用手指擦头发或身体其他部位严禁在洁净室内戴首饰和手表严禁在洁净室作剧烈活动,轻拿轻放。
医药洁净室的标准

GMP对洁净厂房的标准GMP的厂房设施原则:1)、空间面积适应生产需要,布局合理。
2)、能有效控制差错和污染。
3)、便于维护和清洁。
一,企业的生产环境应整洁;厂区地面、路面及运输等不应对药品生产造成污染;生产、行政、生活和辅助区总体布局应合理,不得互相妨碍。
●地面、路面硬化;绿化不起尘;设物流运输通道。
●生产区与生活区分开(倒班宿舍、工间食堂与行政管理为生产服务施,可设在行政区)。
●总布局洁净厂房置上风向,锅炉、提取、生物脏器处理、动物房等置下风向;危险品、化学品库独立设置。
二,厂房应按生产工艺流程及所要求的空气洁净度级别进行合理布局。
●厂房内按工艺中物流最短路线,顺流布局。
●辅助间位置合理,洁净生产区的级别划分应符合GMP附录的要求,布局尽可能做到“同一级别集中在同一个区,同一个级别在同一个平面。
”三,同一厂房内的生产操作和相邻厂房之间的生产操作不得相互防碍。
●厂房按洁污合理分隔(高致敏类产品设专用厂房;毒、麻类产品厂房;激素类、抗肿瘤类产品厂房;生物制品、血液制品厂房设专用车间或专用厂房)●厂房内应按工序合理分隔操作间原则:1)、对产尘、产湿及工艺对温、湿度有特殊要求的操作工序作重点分隔;2)、同一操作间内不得同时进行不同批次产品的生产操作。
四,厂房应有防止昆虫和其它动物进入的有效设施。
●厂房直通外界的门、窗设有防止昆虫、动物进入的有效设施●(防止进入有效设施:档鼠板h≥30mm、电驱鼠(20m有效)、风帘、金属沙窗、粘鼠胶×、鼠药×、捕鼠器×、灭蚊器)。
●厂房≠仓库1,洁净室(区)的内表面应平整光滑、无裂缝、接口严密、无颗粒物脱落、耐受清洗和消毒。
2,洁净室(区)的墙壁与地面的交界处应成弧形或采取其他措施,以减少积聚和便于清洁。
3,洁净室(区)的窗户、天棚及进入室内的管道、风口、灯具与墙壁或天棚的连接部位应密封。
●对洁净室(区)内表面要求:墙面、地面平整无缝、光滑耐磨、易清洁。
- 1、下载文档前请自行甄别文档内容的完整性,平台不提供额外的编辑、内容补充、找答案等附加服务。
- 2、"仅部分预览"的文档,不可在线预览部分如存在完整性等问题,可反馈申请退款(可完整预览的文档不适用该条件!)。
- 3、如文档侵犯您的权益,请联系客服反馈,我们会尽快为您处理(人工客服工作时间:9:00-18:30)。
出处:北京欣惠泽奥科技有限公司专营实验室仪器、分子生物学试剂、生物化学试剂、细胞培养层流式空气气流运动成一均匀的直线形,空气由覆盖率100%的过滤器进入室内,并由高架地板或两侧隔墙板回风,此型式适用于洁净室等级较高的环境。
其型式可分为水平层流式和垂直层流式2种。
(1)水平层流式:水平式空气自过滤器单方向吹出,由对边墙壁的回风系统回风,尘埃随风向排出室外,一般在下流侧污染较严重。
优点:构造简单,运转后短时间内即可达稳定状态。
缺点:建造费用比乱流式高,室内空间不易扩充。
(2)垂直层流式:房间天花板完全以ULPA过滤器覆盖,空气由上往下吹,可得较高的洁净度,在生产中或工作人员所产生的尘埃可快速排出室外而不会影响其他工作区域。
优点:管理容易,运转开始短时间内即可达稳定状态,不易受作业状态或作业人员影响。
缺点:构造费用较高,弹性运用空间困难,天花板吊架相当占空间,维修更换过滤器较麻烦。
1.1.3 复合式(MixedType)所谓复合式即为将乱流式及层流式予以复合或并用,可提供局部超洁净的空气。
(1)洁净隧道(CleanTunnel),以HEPA或ULPA过滤器将工作区域100%覆盖,使洁净度等级提高至100级以上,可节省安装运转费用。
此型式需将作业人员的工作区与产品和机器维修隔离,以避免机器维修时影响工作及产品品质。
洁净隧道还有弹性扩充容易、维修设备时可在维修区轻易执行等优点。
(2)洁净管道(CleanTube),将产品流程经过的自动生产线包围并净化处理,将洁净度等级提至100级以上。
因产品和作业员及发尘环境相互隔离,少量送风即可得到良好洁净度,可节省能源,不需人工的自动化生产线最适宜使用。
药品、食品业界及半导体业界均适用。
(3)并装局部洁净室(CleanSpot),将洁净室等级10000~100000之乱流洁净室内之产品制程区的洁净度等级提高为10~1000级以上,以为生产之用;洁净工作台、洁净工作棚、洁净风柜即属此类。
根据实际生产的需要可以选择不同的送风方式来满足生产,保证产品质量。
1.2 洁净室内气流影响洁净室的洁净度1.2.1 洁净室的气流方向影响其洁净度人、机器间隔、建筑结构等所产生的尘埃移动、扩散受到气流的支配。
洁净室利用高效HEPA过滤空气,其尘埃阻隔率达99.97%~99.99995%之多,因此经过此过滤器过滤的空气可以说十分干净。
然而洁净室内除了人以外,尚有机器等发尘源,这些发生的尘埃一旦扩散,即无法保持洁净空间,因此必须利用气流将发生的尘埃迅速排出室外。
1.2.2 气流速度左右洁净室洁净性能0.3~0.5m/s的气流速度为一般洁净室所选择,此气流速度属微风区域,易受人、机器等的运动引起的干扰而趋于混乱,即使提高风速可抑制此影响以保持洁净度,但提高风速,将导致运转成本增加。
所以,应在满足要求的洁净度水平下,能以最适宜的风速供应,减少能源消耗。
另一方面,欲稳定洁净室的洁净度,始终均一气流为重要因素,均一气流若无法保持,表示风速有异,特别是在壁面,气流会沿着壁面发生涡流作用,此时要实现高洁净度事实上很困难。
垂直层流式要保持气流均一必须做到以下几点:(1)进风面的风速不可差异;(2)地板回风板回风不可有速度上的差异。
速度过低(<0.2m/s)或过高(>0.7m/s)均有涡流现象发生,而0.5m/s的速度,气流则较均一,目前一般洁净室,其风速均取在0.3~0.5m/s之间。
影响洁净室的气流因素很多,如生产设备、人员、洁净室装材、照明器具工作桌等障碍物,在相接处均会有涡流现象发生,其附近的洁净度将会较差,同时对于生产设备上方气流的分流点,亦应列入考虑因素。
2 理顺生产工艺,合理布置空间2002年实施的《洁净厂房设计规范》明确指出,洁净厂房“工艺平面布置应合理、紧凑。
洁净室或洁净区内只布置必要的工艺设备以及有空气洁净度要求的工序和工作室”。
合理布局首先要理顺工艺流程,避免迂回往返。
工作室的平面空间应合理,既有利于操作,又便于维修,不应预留闲置面积和空间。
合理的空间与面积,也有利于合理的分区,防止混杂事故。
洁净室面积和空间的大小关系着送风量的多少,决定着空调能耗的大小,影响工程的投资,并非越大越好。
但洁净室的空间面积太小可能不便于操作、维修。
所以,设计合理的空间面积应考虑到设备操作、维修的需要。
生产区和储存区应有与生产规模相适应的空间面积,用以安置设备、物料,便于操作和维修。
一般洁净室高度控制在2.20~2.60m,对个别较高的设备可在局部加高,而不宜全面提高洁净区的高度。
车间内部应设有物料的中间站,其面积足以存放物料、中间产品、待验品和成品,且便于明确分区,以最大限度地减少差错和交叉污染。
3 控制人流、物流,阻止带入微生物或微粒杂质洁净室应设专用的人流、物流通道。
人员应按规定的净化程序进入,并应严格控制人数。
对于物料可在除去浮尘后拆去外包通过缓冲间或传递柜送入。
不同洁净等级的洁净区物品则通过传递窗传送。
中间站宜设在中心位置,以便缩短运送距离。
洁净区内不设与本岗位无关的管道。
充分利用上下或周围的技术夹层,所有公用管道、工艺管道的主干管均在技术夹层安装。
穿越地面、隔墙的管道尽可能靠近使用点并敷设套管,套管内的管道不应有焊缝,管道与套管之间应有可靠的密封措施。
进入洁净室的管道应为不锈钢材质。
4 完善设备功能,减少污染机会设备的材质、加工精度、密闭程度以及管理制度都与交叉污染有关。
所以除了合理布局外,提高设备的自动化水平和组成联动的生产线,以减少操作人员,降低人员的活动频率,也是防止交叉污染的必要措施。
产尘量较大的固体制剂车间,要防止发生交叉污染。
(1)选购的设备应有防护罩及携带有除尘装置;(2)要采取隔离措施,将其分成操作室和前室或操作室和辅机室。
前室在平面布置上一般采用单机单室,辅机室可设在非洁净区,检修门设在走廊一侧。
如压片、自动包衣、胶囊分装等设备可采用此类分隔方法;(3)对于有些不带除尘辅机设备又不密封的单机,如粉碎机、粉剂或颗粒包装机,则可把隔离区内的排风经过滤后再送回隔离区,即形成自循环。
在生产过程中,有些药品引湿性强,当要求空气相对湿度低于50%甚至45%时,冷冻除湿很难达到要求。
在许多除湿措施中,氯化锂转轮除湿较适用。
除湿机可装在有特殊除湿要求的洁净室或单独设置空调送回风,以净化的空气作为该岗位低湿的保护性空气,自成一个循环系统。
5 科学设置空调净化系统5.1 根据洁净度等级分设空调净化系统对生产β-内酰胺类、避孕药品、激素类、强毒微生物及抗肿瘤药品、放射性药品等的洁净室,要单独设置空调系统,室内要保持正压,与相邻房间或区域之间要保持相对负压,送风口和排风口均应安装高效空气过滤器,以将这些药物的污染降至最低限度。
其排风口与其他药物净化空调系统的新风口之间应相隔一定的距离。
送风、回风和排风的启闭应有连锁装置。
下列情况的空气净化系统,如经处理仍不能避免交叉污染时,则不应利用回风。
应单独设局部排风系统,洁净室的排风口应有防倒灌装置。
(1)固体物料的粉碎、称量、配料、混合、制粒、压片、包衣、灌装等工序;(2)固体口服制剂的颗粒、成品干燥设备所使用的净化空气;(3)用有机溶媒精制的原料药精制、干燥工序;(4)凡工艺过程中产生大量有害物质、挥发性气体的生产工序。
对面积较大、空气洁净度较高,位置集中及消声、振动控制要求严格的洁净室宜采用集中式净化空调系统。
反之,可采用分散式净化空调系统。
根据生产工艺要求设置值班风机,并保持室内空气洁净度和正压,防止室内结露。
风管断面尺寸应考虑对内壁的清洁处理,并在适当位置设清扫口。
净化空气调节系统的新风管、回风总管,应设密闭调节阀。
送风机的吸入口处和需要调节风量处,应设调节阀。
洁净室内的排风系统,应设置调节阀、止回阀或密闭阀。
总风管穿过楼板和风管穿过防火墙处,必须设置防火阀。
净化空气调节系统的风管和调节阀以及高效空气过滤器的保护网、孔板和扩攻孔板等附件的制作材料和涂料,应根据输送空气的洁净度要求及其所处的空气环境条件确定。
在中效和高效的空气过滤器前后,应设置测压孔。
在新风管和送回风总管以及需要调节风量的支管上,应设置风量测定孔。
风管以及风管的保温、消声材料及其粘结剂,应采用非燃烧材料或难燃烧材料。
将高效过滤器设置在围护结构的进风口上,其本意是防止污染进入生产系统(包括管路与机组)。
由于高效过滤器承担了阻止微生物向洁净区渗漏的重责,一旦产生泄漏,就无法保证产品质量。
为了防止在长期运行过程中因高效过滤器表面密封条弹性降低或老化,还要求定期测试,因此对进风口内高效过滤器要求泄漏检查。
另外还要强调的是,在更换高效过滤器时最好先将管路进行消毒。
5.2 选用适宜的空气过滤器空气过滤器(以下简称“过滤器”)的不当使用,也直接关系到洁净效果,影响着药品的质量。
选择过滤器要确定过滤器效率:终级过滤器(高效或亚高效)的性能可靠性强,初级过滤器和中效过滤器维护方便。
过滤器的过滤面积大,能容纳的粉尘就多,其寿命就长。
而且过滤面积大,气流穿过材料的速度就低,过滤器的阻力就小。
研究表明,对于同种结构、同样滤材的过滤器,当阻力确定时,过滤面积增加50%,过滤器的使用寿命会延长70%~80%;面积增加1倍,过滤器的使用寿命约增加2倍。
增加过滤面积时,显然要考虑过滤器的结构和现场条件。
例如袋式过滤器,可以通过增加滤袋的数量和滤袋的长度来增加过滤面积;对于传统有隔板过滤器,可以减小隔板间距以增加滤纸褶数的可能性。
初效滤器的过滤效率偏低也能影响其使用寿命。
因此,应首先根据送风的洁净要求确定末级过滤器的效率,然后选择起保护作用的过滤器(预过滤器),如果这级过滤器亦需保护,再在它的上风端增设过滤器。
应妥善匹配各级过滤器的效率,若相邻两级的效率相差太大,则前一级起不到保护后一级的作用。
因挡风板故障或设计失误,使风机直吹过滤器,造成过滤器非正常损坏的事时有发生。
虽然能杀菌的新滤材不断推出,但其杀菌功能再强,也难以调动过滤器上的灰尘去杀菌。
如果确实需要消灭混在过滤器积灰中的微生物,就要采取相应的手段,而对过滤器本身不应寄予过高希望。
5.3 过滤效果也受气候因素影响杨柳树较多的地区,在空调设计时就应该采取相应措施,如改变进风口高度或在进风口加护网。
若措施不当,那就只剩一招:在飘絮的季节勤换过滤器。
初春的早晨,北方气温往往很低,雨水在地面可以结成薄冰。
滤材上的雨滴在这时有可能结冰,并迅速地将过滤器封堵。
由蓬松材料制成的过滤器(大多数低效率过滤器)能挺一阵子。
当滤材为致密的滤纸时,1h就足以将过滤器封死。
雾滴是更小、更轻的液态颗粒物,它在0℃以下的物体表面结成冰晶。
过滤器会因冰晶附身而透不过气来。
如果可能出现冰雨或树挂,最好留有一套过滤器备件,以备应急使用。