小议炉渣脱硫及其影响因素
影响LF炉脱硫效率因素分析

影响LF炉脱硫效率因素分析相对转炉氧化性炉渣而言,LF炉脱硫是在还原渣条件下进行的,因而其脱硫效率要远远高于转炉,其反应主要发生在炉渣和钢水界面之间,通过钢渣反应,使硫由钢水向炉渣的扩散转移,其基本反应为:[FeS]+(CaO)=(CaS)+(FeO)。
LF炉精炼脱硫,首先要形成还原性的白渣,将氧化性钢包渣子进行还原,渣中w(FeOH-MnO)<1%原才比较充分,然后钢水和炉渣中的氧以FeO形式被渣子吸收,在白渣中还原,并达到一定的平衡值,这是脱硫去夹杂的基本条件,在一定碱度和氩气环境下,CaO被还原渣中A1、C、Si等元素还原出Ca与钢水中的硫反应形成高熔点CaS进入炉渣。
LF炉脱硫效率受钢水条件、炉渣状况、动力搅拌及操作多方面影响。
1.1转炉钢水氧化性转炉吹炼过程控制,终点加料、温度和C含量等因素直接影响钢水氧化性,从而影响钢水及炉渣脱氧还原时间及钢水夹杂物控制,对钢水精炼脱硫有所影响,实际操作中采取措施主要是根据钢种要求,优化合金结构,减少合金增c 来最大限度提高出钢c含量;通过合金烘烤、钢包烘烤、控制合适出钢时间来降低出钢温度,有效降低钢水初始氧化性。
1.2转炉出钢控制转炉钢渣含∑FeO在20%左右,不利于还原渣快速形成,同时易造成钢水回磷,影响钢水炉渣搅拌效果地提高和低P钢生产。
为防止下渣,一方面强化出钢操作,避免出钢夹渣,一方面强化挡渣操作,控制出钢下渣,同时为避免出钢口后期下渣量较大,钢水初始氧含量偏高现象,规定走LF炉次出钢时间控制在2min 以上。
1.3转炉脱氧合金化工艺控制钢水终脱氧直接影响LF炉钢水和炉渣还原效率,应强化LF炉钢种终脱氧,实际生产中对LF精炼钢水有效增加了终脱氧剂用量,同时对脱氧合金化操作严格控制程序符合规定。
1.4LF炉前期化渣慢LF炉进站钢水温度偏低,钢包未加顶渣是造成LF炉前期加料多化渣慢的主要原因,需要进行改进。
1.5精炼吹氩控制原钢包为单透气砖,由于透气砖质量原因,部分炉次底吹氩不透气或透气量太低,不能满足精炼强吹氩过程化渣脱硫要求,需要调整。
第三章 炉渣与脱硫

第三章炉渣与脱硫一、炉渣概述(一)炉渣的来源及主要成分:1、炉渣的来源:(1)矿石中的脉石:SiO2Al2O3(2)燃料中的灰分:SiO2Al2O3(3)熔剂中的氧化物:Ca O MgO(4)被侵蚀的炉衬:Al2O32、炉渣的主要成分:SiO2Al2O3CaO MgO用特殊矿石冶炼时,炉渣中还会含有CaF2TiO2BbO MnO等氧化物。
炉渣中总含有少量的FeO :0.5%(二)炉渣碱度:碱度:炉渣中的碱性氧化物和酸性氧化物的比值。
1、二元碱度:R2= CaO/ SiO2 一般为1.0-1.2之间2、三元碱度:R3=(CaO+ MgO )/ SiO2 一般为1.3左右3、四元碱度:R4=(CaO+ MgO )/(SiO2+Al2O3)(三)炉渣的作用1、炉渣具有熔点低,比重小,不熔于铁的特点,使渣铁分离,得到纯净的生铁。
2、去除生铁中的硫,并有利于选择或抑制Si Mn的还原,起控制生铁成分的作用。
3、炉渣的生成形成了高炉内的软熔带和滴落还,影响煤气流分布及炉料的下降。
4、炉渣附在炉墙上,形成渣皮,起保护炉衬的作用。
(四)酸性炉渣和碱性炉渣炉渣中主要氧化物有:K2O、Na2O、BaO、PbO、CaO、MgO、MnO、ZnO、FeO、CaF2 Fe2O3、Al2O3、TiO2、SiO2、P2O5其中:CaF2以前为碱性氧化物Fe2O3、Al2O3为中性氧化物TiO2、SiO2、P2O5为酸性氧化物碱性炉渣:以碱性氧化物为主的炉渣。
酸性炉渣:以酸性氧化物为主的炉渣。
按成渣过程分:初渣:开始形成的炉渣。
终渣:最后排出炉外的渣。
中间渣:化学成分和物理性质处于不断变化过程中的炉渣。
二、炉渣性能(一)炉渣的熔化性:表示炉渣熔化的难易程度。
炉渣熔化性常用熔化温度和熔化性温度来表示。
1、熔化温度:(1)定义:指过热的液体炉渣开始凝固的温度或炉渣加热时固体完全消失的温度。
(2)熔化温度是炉渣熔化性的标志之一①熔化温度高,表示炉渣难熔。
重钢五高炉炉渣脱硫能力影响因素的浅析

33 铁水 成分 -
铁水 中的非金属元素 ( C S、 元素 ) 如 、 iP 由于 要影响硫的活度 ,从而也会对炉渣的脱硫反应产生
一
般来讲 ,高炉利用系数越高 , 日 或 产量越高,则
定 的影 响 。
34 炉渣 粘度 .
高炉放铁放渣就越勤 , 炉渣与铁水接触时间就越短 , 就越不利于高炉脱硫。因此可以用 日 产量除时间, 即用单位生铁在炉内停 留时间来近似表示炉渣与铁
据高炉解剖研究证实,铁水进入炉缸前的含硫 量 比出炉铁水含硫量高得多 ,由此认为 ,正常操作
中主要 的脱硫 反应 是在铁 水滴 穿过炉 缸 时的渣层 和 炉 缸 中渣 铁相 互接 触 时发生 的 。
脱硫 反应 方程 式 : 【e](a )C (a)C +F ]19 k F S+C O + =C S+ O [e- 0 J 41 4 或 :【】( C ( )C S+O =S 十 O
括 :炉渣粘度以及渣铁接触条件 。 31温度 . 温度的升高有利于吸热反应 ,温度的降低有利 于放热反应。在高炉冶炼过程中 ,由于 s 和 T 的 i i
还原 都 是 吸热 反应 , 【 s [ ] i】与 L=S/ ) i( S 【 n[iT 】 L= ] i 与炉温具有很强 的相关性 ,而炉料 T/ ) ( 结构的变化可能会影响到生铁中【i s 和 i 】 】 的含量 ,
・
l ・ l
维普资讯
《 重钢五高炉炉渣脱硫能力影响因素的浅析 》
I = - 2 .4 + 9 .5 Xl 2 6 7 + 3 2 8 _ 6 4 40 0 0 + 6 .4 X2 3 . 6 X3
一
定系数 R= . , 2 6 调整后的决定系数 R= . , = . 00 0 6 F 3 9 4 9 > o ( ,1 = . ,表明上式在一定程度上 能解 F 8 ) 22 2 4 释硫在高炉渣铁间的分配 系数 I 与各因素之间比 _ 6
炉渣中al2o3含量与脱硫、脱氧关系剖析[资料]
![炉渣中al2o3含量与脱硫、脱氧关系剖析[资料]](https://img.taocdn.com/s3/m/55d7cc6e178884868762caaedd3383c4bb4cb4b7.png)
炉渣中Al2O3含量与脱硫、脱氧关系分析
随着炉渣中Al2O3浓度的增加,钢中Al含量也增加,并且随着碱度增加,钢液中有增铝的现象。
Al含量的增加,将导致钢中氧含量的减少,但并不是钢中Al含量越多越好,当钢中Al含量大于0.1%时,随着Al含量的增加,钢中氧含量也增加;随着钢中Al含量的增加,Al2O3夹杂物也相应增加,但是当钢中Al含量增加到0.03%是,随着钢中Al含量的增加,Al2O3夹杂物反而降低了。
所以控制好Al是降低夹杂的一个关键工艺。
研究结果显示,随着渣中Al2O3的值增加,夹杂物中Al2O3的值也是线型增加的。
随着夹杂物Al2O3含量的增加,夹杂物的不变形指数是先较小后增加的,当夹杂物中的Al2O3含量为20%,渣中Al2O3含量为8%时,不变性指数是最低的。
这为夹杂物塑性变形提供了依据。
Al2O3对脱硫效果的影响有两个方面。
一方面,随着Al2O3含量的增加,炉渣粘度降低,促进渣-钢反应,有利于脱硫;而另一方面,Al2O3含量增加会降低CaO的活度,抑制脱硫的进行。
有些研究者认为Al2O3含量在15~40%范围内,能取得较好的脱硫效果,但另外一些文献表明在此范围内,随Al2O3含量的增加,渣的粘度将增加,不利于脱硫。
近年来,CaO-Al2O3系精炼渣在炉外精炼过程中被广泛采用,但渣中Al2O3对脱硫效果的影响仍不十分清楚,尤其关于CaO-Al2O3为基的预熔渣中Al2O3的行为至今未见文献报道。
LF炉造渣及脱硫控制详解

以前所使用的合成渣是将所需的各种原料破碎后按一定 比例机械混合压球烧结而成,合成渣的成分含有Al2O3为20%, 其熔点较高,脱硫效果不稳定。相关资料表明这种渣在精炼 过程中,成渣速度慢,烟尘大,精炼时间长。 脱硫原理也表明,实现高效快速脱硫至目标要求,需要 快速形成特定组分的精炼渣。LF炉的处理过程有大约5-8分 钟送电时间在化渣(1500-2000kWh),成渣后才开始脱硫。 要加快LF炉处理节奏,必须使成渣时间缩短。需要使用熔点 更低的预熔渣实现快速成渣。成分如下。
影响脱硫的因素
4、渣量对脱硫率的影响 适当增加渣量,可以稀释渣中的CaS浓度,促进脱硫反 应式向右进行,对脱硫有明显的效果。但是大渣量使脱硫 反应不活跃,脱硫效果增加不明显,同时电耗和辅料消耗 增加。一般控制渣量为钢水量的1%-2%。
影响脱硫的因素
脱硫速度
从宏观理论分析,钢中S的物质移动支配整个反应速 度。 搅拌是促进物质移动速度加快的有效手段,加强搅 拌使渣粒卷入钢水,增加了渣与钢中硫接触的机会,使 反应速度加快,脱硫效率提高。 实验证明,脱硫速度大小依次为:喷吹脱硫剂 (CaO+CaF2)>吹氩搅拌>电磁搅拌(感应)。喷吹脱 硫剂能将钢中硫脱至5ppm以下,对于我厂品种结构来说, 正常情况下,吹氩搅拌完全能满足生产需求。
影响脱硫的因素
2、渣中Al2O3含量对LS的影响 对于铝脱氧钢,渣中的Al2O3与硫化 物容量(Cs)存在如图关系。研究发现, 渣中Al2O3含量大于30%时,随着渣中 Al2O3的增加,硫化物容量(Cs)减小, 同时也发现,随着温度的升高,同渣 系的硫化物容量(Cs)增大,也证明了 温度与脱硫存在线性关系。 在CaO-SiO2-Al2O3渣系中,当Al2O3 含量<30%时,增加渣中的Al2O3含量 可以降低渣的熔点,提高流动性。但 综合考虑炉渣对Al2O3夹杂和脱硫的影 响,一般选择20%-30%较好。
LF炉脱硫精炼渣的研究

LF炉脱硫精炼渣的研究摘要:LF钢包精炼炉是冶炼优质钢的常见设备,具有满意的生产能力,在本次研究中,本文通过分析影响LF炉脱硫的相关因素之后,通过开展实证分析的方法,进一步论证了CaO、氧化亚铁、氧化铝、二氧化硅等物质的影响进行阐述,希望为保证钢铁生产顺利进行奠定基础。
关键词:LF炉;脱硫精炼渣;实证分析前言:目前大气污染问题已经得到全社会的广泛关注,而硫则是大气污染的主要物质,为实现可持续发展的目标,很多钢铁企业都在对生产工艺进行完善,其中LF钢精炼炉可以保持炉内的还原环境,其中的合成渣精炼可以更好的实现脱硫脱氧,其中合成渣精炼效果与生产工艺之间存在之间关系,值得关注。
1.影响脱硫效果的相关因素分析1.1 CaO对脱硫率的影响在脱硫渣中,CaO是影响脱硫的重要因素,这是因为LF炉以CaO作为反应的原料直接完成脱硫,在与炉中的硫元素发生化学反应之后可以形成硫化钙,且随着反应的继续,该物质的脱硫率会有进一步提升,生产实践证明,随着炉渣中碱度较低的情况下,无论氧化铝以及二氧化硅等含量多高,其脱硫率的增长缓慢;但是随着碱度的上升,氧化铝以及二氧化硅的含量提升则可以显著提升脱硫率,其原因为:在二氧化硅以及氧化铝的含量增加可以改善炉渣粘度,最终有效改善脱硫动力学水平。
所以在理想的工况下,CaO的含量应控制在60%以上[1]。
1.2氧化铝与二氧化硅的影响根据上文介绍的内容可知,氧化铝以及二氧化硅会对CaO的脱硫效果产生影响,其中二氧化硅作为离子晶体,该物质含量的增加则可以显著提升渣中的F(-)离子水平,该物质与网状硅酸盐产生化学反应之后可以加快脱硫效率;再加之二氧化硅具有改善渣粘度的效果,可以提供理想的脱硫动力学条件。
同时在渣中添加二氧化硅后可以促进硫化钙的固体破坏提升液相,最终优化脱硫条件。
同时在特定的炉渣成分下,随着氧化铝的水平提升,则炉渣的流动性进一步增强,随着脱硫反应的深入,氧化铝水平与脱硫效果正相关。
脱硫效率影响因素和措施一览
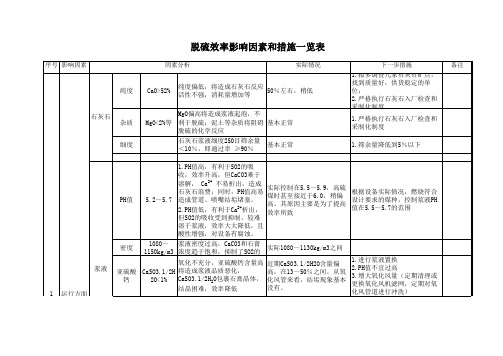
严格按照有关规定控制进浆 量,维持合适的PH值
根据化验结果,适时合理开启 废水,既控制氯离子浓度不超 标,又减少合格浆液排放
1.尽可能保证入炉煤含硫不要 入口SO2浓度升高,脱硫效率 入口SO2 <2700mg/Nm 实际入口SO2浓度有时超过 高于设计值; 下降。在校核含硫3200mg/Nm3 3 浓度 校核值;在控制PH情况下, 2.掺配高硫煤时尽量掺配均匀 (设计) 下,效率只保证90%。 。 原烟气 粉尘浓 粉尘浓度高,阻碍SO2吸收, <200mg/Nm3 基本正常 度 脱硫效率降低 烟气氧 烟气氧量高,风量大,风速 高负荷时烟气量和烟氧量偏 进行脱硫和电除尘试验时,测 量 高,脱硫效率下降 大 量出实际的风量数据作为参考 1.加强循环泵的检修维护,防 高负荷高硫时,3 台循环泵 止喷嘴、滤网堵塞,保证循泵 液气比增大,与烟气接触洗涤 运行效率仍无法达到90%, 液气比 14.65L/m3 出力。 的浆液量越多,脱硫效率越高 浆液循环量无法满足实际要 2.加强漏风治理、加强燃烧配 求 风方式调整,降低原烟气流量 因设备运行环境影响,测点 督促厂家维护人员定期进行标 CEMS系 CEMS测点不准或设备故障,造 不准或设备故障现象偶尔发 定,加强设备维护;热控人员 测点 统 成脱硫效率不准 生,维护人员不在厂时处理 加强CEMS相关设备维护技能的 比较困难。24日上午标定正 培训,确保设备运行正常。 目前喷嘴堵塞情况比较严 1、每次停机安排对浆液循环泵 重,部分已无法疏通,对脱 浆液循环泵喷嘴堵塞,浆液循 喷嘴进行检查、疏通,对已经 硫效率影响较大。其中#1 喷嘴 环量减少,气液接触反应机率 堵塞无法清通的喷嘴应安排在 塔至少有8个没有疏通,#2 减少,效率降低 大小修或长周期停机时进行更 塔至少5个没疏通(不包括A 换。2、PH不维持过高。 层)。 浆液循 环泵
高炉炼铁过程中的炉渣脱硫技术

资源回收:回收利用废渣, 减少资源浪费
提高产品质量:降低硫含 量,提高钢铁产品质量
经济效益:降低生产成本, 提高企业经济效益
4
炉渣脱硫技术的工艺流程
炉渣的形成与处理
炉渣的形成:高炉炼铁过 程中产生的废渣
炉渣的成分:主要包括铁、 硅、锰、磷等元素
炉渣的处理方法:包括物 理处理、化学处理和生物 处理等
物理处理:包括磁选、浮 选、重选等方法,用于分 离炉渣中的有用成分
化学处理:包括酸浸、碱 浸、氧化还原等方法,用 于改变炉渣的化学性质
生物处理:利用微生物对 炉渣进行生物降解,用于 处理有毒有害成分
脱硫剂的选择与添加
脱硫剂种类:石灰石、白云石、 氧化镁等
脱硫剂添加方式:直接添加、 预混合添加、喷射添加等
硫效率
优化炉渣脱硫 设备,降低能
耗和成本
采用新型脱硫 剂,提高脱硫 效果和稳定性
结合其他环保 技术,实现炉 渣脱硫与废气 治理的协同优
化
6
炉渣脱硫技术的发展趋势和未来展望
新型脱硫剂的研究与开发
研究背景: 随着环保 要求的提 高,传统 脱硫剂逐 渐被淘汰
研究目标: 开发高效、 环保、经 济的新型 脱硫剂
燃料:煤炭、焦 炭等燃料在燃烧 过程中会产生硫 化物
熔剂:石灰石、 白云石等熔剂在 熔化过程中会产 生硫化物
空气:空气中的 硫化物在燃烧过 程中会被氧化, 产生硫化物
硫对高炉炼铁的影响
硫是铁矿石中的 有害元素,会影 响铁的质量和产 量
硫与铁反应生成 硫化铁,降低铁 的熔点,影响铁 的流动性和渗透 性
未来炉渣脱硫技术的发展方向与趋势
提高脱硫效率:通过改进 工艺和设备,提高脱硫效
率,降低能耗和成本。
循环流化床锅炉炉内脱硫原理及影响因素浅析

循环流化床锅炉炉内脱硫原理及影响因素浅析作者:刘红娟来源:《科技与创新》2014年第03期摘要:众所周知,煤在燃烧过程中会产生污染性气体二氧化硫。
如果想要对产生的污染气体进行有效的控制,就需要找到工业生产中减少二氧化硫产生的方法。
目前,脱硫技术在实际的生产中得到了广泛的应用,循环流化床锅炉炉内脱硫就是一种有效脱硫方法。
关键词:循环流化床;炉内脱硫;锅炉;污染气体控制中图分类号:TK229.66 文献标识码:A 文章编号:2095-6835(2014)03-0005-02中国是能源生产量和消费量较大的国家,能源是日常生活中必不可少的。
目前,我国能源种类中煤炭所占比重非常大。
每年大量煤炭的燃烧对我国的生态环境造成了一定的影响,产生出的二氧化硫增强了降水中的酸性,为酸雨的形成提供了条件。
酸雨天气不仅影响到了人们的日常生活,造成了一些建筑物的损坏,更是导致了很多浮游生物的死亡。
较之于其他国家,我国受酸雨的危害更加严重。
因此,如何高效地使用能源、保护环境、降低成本,做到可持续发展,是我国在新世纪面临的重要问题。
如今,我国已经研究出一些减少二氧化硫产生的办法,但还在进行更深入的研究。
现在世界上使用的脱硫技术有很多,循环流化床锅炉炉内脱硫是目前比较不错的方法。
循环流化床锅炉技术的适应性较强,适用于很多种类的燃料,并且脱硫效果非常好,能够有效减少污染气体的排放。
循环流化床锅炉技术是当下大家比较认可的方法,现在已经在很多地方得到应用,而且技术日臻成熟。
如何进一步推动这一技术的进步,了解循环流化床锅炉炉内脱硫的原理以及影响炉内脱硫的因素有着至关重要的作用。
1 循环流化床锅近几年来,循环流化床锅应用非常广泛,这项技术被认为是一种高效清洁的技术,特别是它的炉内脱硫技术。
它所采用的低污染燃烧技术,目前也最符合中国的国情。
但是,我国对循环流化床锅炉炉内脱硫技术还存在一定的质疑。
我国现在很多企业二氧化硫的排放量达不到国家标准,需要进行二次脱硫。
LF脱硫分析

LF脱硫1影响LF炉脱硫效率因素分析相对转炉氧化性炉渣而言,LF炉脱硫是在还原渣条件下进行的,因而其脱硫效率要远远高于转炉,其反应主要发生在炉渣和钢水界面之间,通过钢渣反应,使硫由钢水向炉渣的扩散转移,其基本反应为:[FeS]+(CaO)=(CaS)+(FeO)。
LF炉精炼脱硫,首先要形成还原性的白渣,然后钢水和炉渣中的氧以FeO形式被渣子吸收,在白渣中还原,并达到一定的平衡值,这是脱硫去夹杂的基本条件,在一定碱度和氩气环境下,CaO被还原渣中A1、C、Si等元素还原出Ca与钢水中的硫反应形成高熔点CaS进入炉渣。
LF炉脱硫效率受钢水条件、炉渣状况、动力搅拌及操作多方面影响。
转炉炉渣FeO含量一般在15—20%左右,因此转炉炉渣脱硫能力较差,为提高LF炉脱硫能力,必须将炉渣中氧含量降低,实践证明当炉渣中FeO含量低于2.5%后,炉渣的脱硫能力逐步提高,特别是当FeO 含量低于1%后,炉渣脱硫能力显著提高。
精炼过程温度控制LF炉精炼初期采用边化渣边提温,最终达到出站温度的操作工艺,由于对精炼初期和过程无严格温度控制要求,造成实际钢水前期温度偏低,过程温度较不稳定,、影响了精炼脱硫效率,需要进行改进。
精炼还原气氛控制保持精炼过程钢包上面还原气氛有利于减少钢水二次氧化,保持炉渣还原状态,同时有效减少钢水吸氮现象,保证钢水纯净度。
LF炉采用罩式除尘,可有效将精练过程烟气排走,但相应造成钢水表面空气流动,炉盖内为氧化性气氛,不利于钢水质量控制。
喂线控制控制根据钢种需要精炼后期喂Ca线,统计喂Ca线100炉前后钢水硫含量,喂线脱硫率为5%,对脱硫有一定影响,但过分增加SiCa量严重增加生产成本,同时影响钢水成分稳定性,不作为重点改进方面。
2提高精炼脱硫效率的改进措施精炼过程温度控制LF炉提温是在非氧化性气氛下利用电弧加热来提高钢水温度,补偿处理过程钢水温降及造渣、合金化的吸热,便于形成有利于脱硫、脱氧、去除夹杂的钢包渣。
燃煤电厂脱硫废渣处理及其潜在风险分析

燃煤电厂脱硫废渣处理及其潜在风险分析随着全球环保意识的提高和对空气质量要求的增加,燃煤电厂脱硫装置的应用已成为处理煤燃烧废气中二氧化硫(SO2)排放的主要方法。
然而,燃煤电厂的脱硫废渣处理却面临着一系列挑战与风险。
本文将探讨燃煤电厂脱硫废渣处理的方法以及其潜在的环境和健康风险。
燃煤电厂脱硫废渣主要由二氧化硫吸收剂经过反应后形成。
这些废渣一般分为湿式废渣和半干式废渣两类。
湿式废渣是在脱硫过程中产生的高湿度的固体废物,含有大量的水分和可溶性盐等物质。
半干式废渣则是在脱硫过程中产生的低湿度的固体废物,较湿式废渣含水量较低。
处理燃煤电厂脱硫废渣的方法有多种选择。
其中一种常见的方法是将湿式废渣通过沉降、过滤等处理工艺进行脱水处理,然后送往填埋场进行处置。
这种方法相对简单,但其水分含量较高,增加了处理和运输成本。
另一种常见的方法是将废渣经过脱水处理后,利用其作为建材或道路基材料的补充物。
当然,废渣也可以送往特定的处理厂进行再利用或综合利用。
然而,燃煤电厂脱硫废渣处理也存在一些潜在的风险。
首先,湿式废渣中的水分含量较高,使其在填埋场中容易发生坍塌,从而导致环境污染和产生有害气体。
其次,废渣中可能存在一些有害物质,如重金属离子。
这些有害物质在长期填埋后可能渗出,并对地下水和土壤造成污染。
此外,有限的填埋场空间和日益增加的废弃物量也给废渣处理带来了挑战。
为了降低燃煤电厂脱硫废渣处理的风险,我们可以采取一系列的措施。
首先,应尽量减少废渣的产生量,这包括改进脱硫装置的设计和运行,提高脱硫效果,减少废渣量。
同时,应加强废渣的监测与管理,定期检测废渣中的有害物质含量,确保其不会对环境和人体健康造成危害。
此外,还应推广废渣的再利用,例如将其用作建材或道路基材料的补充物,降低对填埋场的依赖。
除此之外,政府、燃煤电厂和相关企业还应加强燃煤电厂脱硫废渣处理的法律法规和标准制定。
制定相关政策和法规,明确脱硫废渣的处理要求,加强监管与执法力度,促进废渣处理的规范化和标准化。
影响转炉脱硫率的原因分析_王建新

影响转炉脱硫率的原因分析王建新刘江伟薛 涛 (新疆八一钢铁集团公司行办)(新疆八一钢铁股份有限公司)(新疆八一钢铁集团公司技术开发中心)摘 要 转炉采用溅渣护炉工艺后,在炉龄大幅提高的同时,也出现了脱硫率明显下降的问题。
详细探讨影响转炉脱硫率的因素,并提出改进措施,取得了满意的效果。
关键词 转炉 脱硫率 碱度 M gO含量1 前言随着溅渣护炉工艺在全国大、中、小转炉的推广,八钢于1999年10月对两座转炉采用了改造,先在1号转炉采用溅渣护炉的工艺,12月在两座转炉上全面实施了溅渣护炉的试验,取得了较好的效果,平均炉龄由1000炉提高2000炉以上。
但是也暴露出一些问题,较明显的是脱硫率显著下降(脱磷率无明显变化),由30%~40%下降到20%以下,对于含硫量小于0.035%的铁水,几乎不脱硫,甚至由于炉料(废钢、石灰等)中的硫进入熔池,致使有些钢水成品的含硫量反而高于铁水含硫量,虽然对普通钢来说其含硫量未超出国际的规定,但对钢质量的不良影响是显而易见的,尤其是给优质钢的冶炼(如H08A)带来极大的困难,另外转炉冶炼过程喷溅增多,增大了钢铁料的消耗。
为解决这个问题,进行了深入地调查与试验分析。
2 转炉工艺简介八钢炼钢厂的二座转炉,设计公称容量12t,经扩容改造后平均出钢量达22t,年产钢90万t。
转炉采用分阶段定量装入制度,熔池深度为700~830mm。
氧枪喷头为4孔拉瓦尔喷头,氧气工作压力为0.75~0.93M Pa,平均氧耗为60m3/t,供氧时间为11~12min,冶炼周期20min。
石灰采用分批加料操作,第一批在开吹的同时加入,加入量约占石灰总加入量的12,第二批石灰视前期化渣情况,采用分批、少量、勤加的方式加入(必须在提枪前3min前加完);白云石在开吹时一次性加入。
出钢温度一般控制在1670~1710℃(高于1710℃的比例占29%),终点拉碳率平均为60%,一次倒炉率平均为85%。
试验方案按常规工艺进行,转炉实施溅渣护炉工艺前后各取样50炉,钢种Q235钢、20M nSi钢,化验终点渣样成分:CaO、SiO2、Mg O、TFe、FeO等。
大型转炉炼钢过程中炉渣脱硫的研究与应用

大型转炉炼钢过程中炉渣脱硫的研究与应用摘要:本文对大型转炉炼钢过程中炉渣脱硫的研究与应用进行了综述。
炉渣脱硫是转炉冶炼过程中关键的环节,可以有效降低钢中的硫含量,提高钢的质量。
炉渣脱硫的方法主要包括碱性炉渣脱硫、氧化性炉渣脱硫和还原性炉渣脱硫等。
本文介绍了这些方法的原理、优缺点以及在工业生产中的应用情况。
此外,还探讨了炉渣成分、温度、氧气供给、搅拌等因素对炉渣脱硫效果的影响。
最后,对当前炉渣脱硫技术存在的问题进行了分析,并提出了未来的研究方向。
关键词:大型转炉、炼钢、炉渣脱硫、炉渣成分、转炉冶炼引言:炉渣脱硫技术在大型转炉炼钢过程中扮演着关键角色,它能够显著影响钢质量的提升与性能的改善。
然而,这一技术仍面临一系列挑战与问题,如脱硫效率、副产物处理、能耗和成本等。
为了解决这些问题,未来的研究方向呼唤更多的创新和探索。
本文旨在综述炉渣脱硫技术的现状与发展,并深入探讨存在的问题和未来的研究方向。
通过优化脱硫效率、副产物处理和能耗控制,炉渣脱硫技术将为大型转炉炼钢行业提供更高效、环保和经济的解决方案,进一步推动钢质量的提升与行业的可持续发展。
一大型转炉炼钢过程中的炉渣脱硫方法炉渣脱硫在大型转炉炼钢过程中起着关键作用,对于降低钢中的硫含量、提高钢的质量具有重要意义。
在实践中,已经发展出多种炉渣脱硫方法,包括碱性炉渣脱硫、氧化性炉渣脱硫和还原性炉渣脱硫等。
(一)碱性炉渣脱硫是最常用的方法之一。
其原理是通过加入富含氧化钙或氧化镁的碱性物质,与炉渣中的硫发生反应生成硫化钙或硫化镁,从而实现脱硫。
碱性炉渣脱硫具有高效、稳定的特点,在工业生产中得到广泛应用。
(二)氧化性炉渣脱硫方法采用氧化性物质,如氧化铁或氧化锰,与炉渣中的硫反应生成氧化硫,然后通过氧化硫与炉渣中的碱金属氧化物或钙、镁等形成相对稳定的硫酸盐,实现脱硫。
这种方法在高硫钢炼制中具有一定的优势。
(三)还原性炉渣脱硫是近年来发展起来的新技术,其原理是通过加入还原剂,如硅、铝等,使炉渣中的氧化硫还原为硫化物,从而达到脱硫的目的。
影响脱硫效率的因素

影响脱硫效率的因素1、吸收塔浆料的pH值对脱硫效率的影响实验表明,浆料的pH值是影响脱硫效率和脱硫产物组成的关键参数。
当浆料的pH值较小时,有助于Ca2 +在石灰石中的溶解,但二氧化硫和SO2的吸收率也会降低,更难溶解在浆料中,效率为大大降低,pH值将逐渐降低,酸度增加,会出现一定程度的腐蚀;pH值越高,总传质系数越大,这会减慢CaSO3·1 / 2H2O转化为CaSO4·1 / 2H2O 的反应速率,这不利于SO2的吸收,从而形成液膜。
阻碍反应吸收进一步进行。
此外,过高的pH值可能会使管道或其他部件上的脱硫产物结晶,这会加剧管道和喷嘴的磨损。
建议根据脱硫吸收塔的实际情况和燃烧负荷设计所需的煤质参数,将浆液的pH值控制在5.5-5.7。
2、吸收塔浆液浓度对脱硫效率的影响影响脱硫效果的吸收塔浆液成分主要包括碳酸钙,盐酸不溶物和亚硫酸钙。
在现场脱硫系统中,吸收塔中浆料的浓度不断增加,这将逐渐减少亚硫酸钙CaSO3·0.5H2O与O2接触的机会。
泥浆量的不断增加将导致吸收剂过饱和积累,这将屏蔽和阻碍石灰石吸收液中二氧化硫和碳酸钙的接触。
另外,二氧化硫的积累导致pH降低,这减慢了吸收塔中SO 2的吸收速率并降低了脱硫效率。
通常,亚硫酸钙的质量分数应低于0.3%。
3、液气比对脱硫效率的影响SO2吸收过程在吸收塔中完成。
主要过程是烟道气中的二氧化硫与吸收浆液中的碳酸钙在空气的作用下发生化学反应,并被氧气氧化吸收。
SO 2的吸收效果与液气比有关。
所谓液气比(如图1所示)是指在一定时间内吸收装置中石灰石浆液的喷雾量与脱硫吸收反应装置的烟气量之比。
影响脱硫效率的关键参数。
在(WFGD)湿法脱硫系统中,增加液气比会使吸收塔中的浆料剧烈湍流,增加浆料的喷射密度,增加气液传质面积,并提高吸收塔的脱硫效率。
在正常情况下,操作人员应根据SO2吸收效果,出口数据和脱硫效率等因素,打开循环渣浆泵的数量,调整液气比,将液气比调整为合适的数据。
炼钢脱硫条件

炼钢过程中脱硫主要在转炉、电炉以及LF(钢包精炼炉)等设备中进行,其条件主要包括:
1. 温度:脱硫反应通常在较高的温度下进行,因为高温有利于硫化物的溶解和扩散。
在转炉冶炼阶段,一般要求温度保持在约1600℃以上;在LF精炼时,温度范围可能在1450℃至1700℃之间。
2. 碱度:炉渣的碱度是影响脱硫效果的重要因素。
高碱度渣能够提供更多的氧离子,与硫形成稳定的硫酸盐从而从钢液中去除硫。
常用的脱硫剂如石灰石(CaCO3)、白云石(CaMg(CO3)2)、镁砂(MgO)等可以提高炉渣的碱度。
3. 炉渣流动性及粘度:良好的炉渣流动性有助于增强硫化物与炉渣之间的接触和化学反应速率,降低粘度可增加传质效率,因此选择适当的助熔剂以维持适宜的炉渣性能是重要的脱硫条件之一。
4. 脱硫剂添加:通过向炉内添加专门的脱硫剂,如镁基合金(如FeMnSiAl)、钙基合金(如CaSi)或直接加入含钙、镁元素的材料,来增加脱硫能力。
5. 搅拌作用:通过吹氩等方式加强钢水与炉渣的混合,提高硫化物与炉渣反应界面处的浓度梯度,促进脱硫反应的进行。
6. 时间控制:脱硫是一个动态过程,需要适当的时间保证硫充分转化为炉渣中的硫酸盐并排出。
综上所述,炼钢脱硫的条件需综合考虑温度、碱度、炉渣性质、脱硫剂使用以及工艺操作等多个方面,确保高效、经济地完成脱硫工序,达到钢材所需的低硫含量目标。
炼铁原理剖析炉渣中硫的行为及其对铁水中硫含量的影响机制

炼铁原理剖析炉渣中硫的行为及其对铁水中硫含量的影响机制炼铁是将铁矿石还原成铁的过程,炼铁炉渣在这一过程中扮演着重要的角色。
炉渣中硫的行为对铁水中硫含量起着决定性的影响,因此研究炉渣中硫的行为及其对铁水中硫含量的影响机制具有重要意义。
本文将对炉渣中硫的行为及其对铁水中硫含量的影响机制进行剖析。
1. 炉渣中硫的行为炉渣中的硫主要来源于原料中的硫化物和含硫有机物。
在高温下,炉渣中的硫主要以化合物的形式存在,如硫化物和硫酸盐。
其中,硫化物主要有二硫化铁、二硫化锰等,硫酸盐主要有硫酸钙、硫酸钠等。
而有机物中的硫则在炼铁过程中发生燃烧,生成二氧化硫。
在炼铁过程中,炉渣中的硫会发生以下三种主要行为:a) 部分硫被还原为气态硫化物进入炉气中;b) 一部分硫形成硫化物嵌入渣体中;c) 余下的硫以硫酸盐的形式存在于炉渣中。
2. 炉渣对硫的影响机制炉渣在炼铁过程中对硫的行为具有重要的影响,主要体现在以下几个方面:a) 炉渣中硫酸盐的析出作用炉渣中的硫酸盐在冷却过程中会析出,形成硫酸钡、硫酸钙等固态硫化物。
这些硫酸盐的析出能有效降低炉渣中的硫含量,从而减少硫进入铁水的机会,对降低铁水中硫含量起到积极的影响。
b) 渣中硫化物的包裹作用炉渣中的一部分硫会以硫化物的形式嵌入渣体中。
这些硫化物能够有效地减少硫进入铁水的机会,从而减少铁水中硫含量。
此外,硫化物在渣中的存在还有利于提高铁水的流动性和洁净度。
c) 渣中硫化物的分配行为炉渣中的硫化物在炼铁过程中会发生分配行为,其中一部分硫化物随着渣液的倾倒而进入渣洞,再通过渣洞排出。
这种分配行为可以减少硫进入铁水的机会,对降低铁水中硫含量有一定的作用。
d) 炉渣中硫酸盐的还原作用炉渣中的硫酸盐在高温下会发生还原反应,生成二氧化硫。
这些生成的二氧化硫会从炉渣中挥发出来,并随炉气一同排出。
这一反应可以有效降低炉渣中的硫含量,从而减少硫进入铁水的机会。
综上所述,炉渣中硫的行为及其对铁水中硫含量的影响机制主要包括硫酸盐的析出作用、硫化物的包裹作用、硫化物的分配行为和硫酸盐的还原作用等。
高炉渣脱硫诸因素关系解析

高炉渣脱硫诸因素关系解析渣中硫含量是高炉渣配料与脱硫技术效果的关键性影响因素,因此,对于高炉渣中硫含量的控制对于钢铁行业而言非常重要。
要有效地控制高炉渣中的硫含量,必须深入地分析其影响因素之间的关系,并有效地控制这些因素的关系。
首先,煤的硫含量是影响高炉渣硫含量的主要因素之一。
煤燃烧时,煤中的硫化物会直接转化为化学态硫,然后加入高炉渣中。
在这一过程中,煤中的硫含量越高,高炉渣中的硫含量就越高。
因此,控制煤中硫含量的变化就是控制高炉渣硫含量的重要措施之一。
其次,炉前配料的组成也是影响高炉渣硫含量的重要因素之一。
炉前配料的产品量比、组成等因素都会对高炉渣的硫含量产生直接影响。
炉后脱硫技术的不同,也会影响高炉渣的硫含量。
具体而言,脱硫工艺技术的选择,会直接影响高炉渣中硫含量的高低。
此外,高炉风量的不同也会影响高炉渣硫含量的变化。
高炉风量越大,炉渣中的硫含量就会越低,而高炉风量越小,炉渣中的硫含量就会越高。
这是因为,大量的氧可以把熔渣中的硫化物氧化,从而减少炉渣中的硫含量。
此外,高炉温度也会影响高炉渣硫含量的变化。
高炉温度越高,炉渣中的硫含量就越低,反之,炉温越低,炉渣中的硫含量就越高。
高温可以把熔渣中的硫化物分解,从而减少高炉渣中硫的含量,而低温会促使硫化物未发生氧化,从而提高高炉渣中硫含量。
最后,高炉排放的气体组成也会影响高炉渣硫含量的变化。
炉烟中的硫化物有可能通过集尘器以液态形式加入到高炉渣中,从而提高高炉渣的硫含量。
因此,对炉烟的排放进行有效的控制,也是降低高炉渣硫含量的重要措施之一。
总之,煤中的硫含量、炉前配料的组成、炉后脱硫技术、高炉风量、高炉温度以及高炉排放的气体组成,是影响高炉渣硫含量的主要因素。
要有效控制高炉渣中硫含量,必须深入分析其影响因素之间的关系,并有效地控制这些因素的关系。
- 1、下载文档前请自行甄别文档内容的完整性,平台不提供额外的编辑、内容补充、找答案等附加服务。
- 2、"仅部分预览"的文档,不可在线预览部分如存在完整性等问题,可反馈申请退款(可完整预览的文档不适用该条件!)。
- 3、如文档侵犯您的权益,请联系客服反馈,我们会尽快为您处理(人工客服工作时间:9:00-18:30)。
小议炉渣脱硫及其影响因素
摘要:在高炉冶炼中,硫是主要的有害元素。
它在生铁中起热脆的破坏作用。
钢铁冶炼的脱硫是生产中获得优质产品的首要问题。
本文主要分析炉渣脱硫及其主要影响因素。
关键词:炉渣脱硫影响因素
高炉生产不仅要从铁矿石中还原出金属铁,而且还原出的铁与未还原的氧化物和其他杂质都能熔化成液态,并能分开,最后以铁水和渣液的形态顺利流出炉外。
炉渣数量及其性能直接影响高炉的顺行,以及生铁的产量、质量及焦比。
因此,选择合适的造渣制度是炼铁生产优质、高产、低耗的重要环节。
1高炉渣的来源
炉渣成分的来源主要是铁矿石中的脉石以及焦炭(或其他燃料)燃烧后剩余的灰分。
它们大多以酸性氧化物为主,即sio2及a12o3。
其熔点各为1728℃及2050℃。
即使混合在一起,它们的熔点仍很高(约1545℃)。
在高炉中只能形成一些黏稠的物质,这会造成渣铁不分,难于流动。
因此必须加入碱性助熔物质,如石灰石、白云石等作为熔剂。
尽管熔剂中的cao和mgo自身熔点也很高,分别为2570℃和2800℃,但它们能同sio2和al2o3结合成低熔点(低于1400℃)的化合物,在高炉内足以熔化,形成流动性良好的炉渣。
它与铁水的密度不同(铁水密度6.8~7.0,炉渣为2.8~3.0),渣铁分离而畅流,高炉正常生产。
高炉生产中总是希望炉渣愈少愈好,但完全没有炉渣是不可能的(也是不可行的),高炉工作者的责任是在一定的矿石和燃料条件下,选定熔剂的种类和数量,配出最有利的炉渣成分,以满足冶炼过程的要求。
2炉渣的作用
2.1成渣的过程
煤气与炉料在相对运动中,前者将热量传给后者,炉料在受热后温度不断提高。
不同的炉料在下降过程中其变化不同。
矿石中的氧化物逐渐被还原,而脉石部分首先是软化,而后逐渐熔融、滴落穿过焦炭层,汇集到炉缸。
石灰石在下降过程中受热后逐渐分解,到1000℃以上区域才能分解完毕。
分解后的cao参与造渣。
焦炭在下降过程中起料柱的骨架作用,一直保持固体状态下到风口,与鼓风相遇燃烧,剩下的灰分进入炉渣。
现代高炉多用熔剂性熟料冶炼,一般不直接向高炉加入熔剂。
由于在烧结(或球团)生产过程中熔剂已先矿化成渣,大大改善了高炉内的造渣过程。
高炉渣从开始形成到最后排出,经历了一段相当长的过程。
开始形成的渣称为“初成渣”,最后排出炉外的渣称“末渣”,或称“终渣”。
从初成渣到末渣之间,其化学成分和物理性质处于不断变化过程的渣称“中间渣”。
2.2高炉渣的作用
炉渣对高炉冶炼还有以下几方面的作用:
(1)在渣铁之间进行合金元素的还原及脱硫反应,起着控制生铁成分和质量的作用。
例如,高碱度渣能促进脱硫反应,有利于锰的还原,从而提高生铁质量;sio2含量高的炉渣能促进硅的还原,从而控制生铁的含硅量等。
(2)初渣的形成造成了高炉内的软熔带和滴落带,对炉内煤气流的分布及炉料的下降都具有很大的影响。
因此,炉渣的性质和数量,会对高炉操作产生直接作用。
(3)炉渣附着在炉墙上形成“渣皮”,一方面起到保护炉衬的作用,另一方面又可能侵蚀炉衬,起到破坏性作用。
因此,炉渣的成分和性质会直接影响高炉寿命。
总之,造渣过程是高炉内主要的物理化学变化过程之一,而且极为复杂。
造渣过程与高炉冶炼的技术经济指标有着密切的关系。
所以,在控制和调整炉渣成分和性质时,必须兼顾到上述几方面的作用。
3影响炉渣脱硫的因素
3.1炉渣成分
炉渣碱度(cao/sio2)是脱硫的重要因素。
碱度高则cao多,增加了渣中(o2-)的浓度,从而使炉渣脱硫能力提高。
但实践经验表明:在一定炉温下有一个合适的碱度,碱度过高反而降低脱硫效率。
其原因是碱度太高,炉渣的熔化性温度升高,在渣中将出现
2caosio2固体颗粒,降低炉渣的流动性,影响脱硫反应进行时离子
间的相互扩散。
再则高碱度渣稳定性不好,容易造成炉况不顺。
mgo、mno等碱性氧化物的脱硫能力较cao弱,但加入少量mgo、mno,能降低炉渣熔化温度和黏度,也有利于脱硫。
但以mgo、mno 代替cao,将降低脱硫能力。
feo不利于去硫,但在酸性渣中影响较小,而且在过酸的炉渣中,feo还有使脱硫能力增大的趋势。
3.2炉温
脱硫反应是吸热反应,温度升高有益于反应的进行;同时升高温度会改善脱硫的力学条件,即降低炉渣黏度,加速离子的扩散;此外,温度高能促进feo还原,降低渣中feo含量。
据实验,在小于1500℃时,渣温提高30℃,ls增大近一倍,从30提高到55。
3.3炉渣黏度
脱硫反应速率取决于化学反应速率和扩散速度。
一般碱性渣中限制脱硫反应速率的因素是s2-和o2-在炉渣中的扩散速度。
降低炉渣黏度将使扩散速度增加,因而促进了炉渣脱硫效率的提高。
3.4其他因素
高炉冶炼状况对脱硫也有影响。
高炉操作稳定,炉缸工作均匀,则有利于脱硫;而煤气分布失常,如管道行程、边缘气流发展、炉缸堆积以及结瘤等,都会导致脱硫效率降低,生铁含硫增加。
4 实际生产中有关脱硫问题的处理
处理脱硫问题有以下措施:
(1)如果炉渣碱度未见有较大波动,但炉温降低,[s]有上升出格趋势,此时首先解决炉温问题,如有后备风温时尽量提高风温,有加湿鼓风时要关闭。
如果下料过快要及时减风,控制料速。
如有长期性原因导致炉温降低,应考虑适当减轻焦炭负荷。
(2)炉渣碱度变低,炉温又降低时,应在提高炉缸温度的同时,适当提高炉渣碱度,待变料下达,看碱度是否适当。
也可临时加20~30批稍高碱度的炉料,以应急防止[s]的升高(但需注意炉渣流动性)。
(3)炉温高,炉渣碱度也高而生铁含[s]不低时,要校核硫负荷是否过高,如有此因,要及时调整原料。
如原料硫负荷不高,脱硫能力差,系因炉渣流动性差,炉缸堆积所造成,应果断降低炉渣碱度以改善流动性提高ls值。
(4)炉温高,炉渣碱度与流动性合适而生铁含[s]不低,主要原因是硫负荷过高。
应选用低硫焦炭,如是矿石硫高应先焙烧去硫或采用烧结、球团等熟料。
参考文献
[1]包燕平,冯捷主编.钢铁冶金学教程.冶金工业出版社,2008.7.
[2]人力资源和社会保障部教材办公室组织编写.冶金概论.中
国劳动社会保障出版社,2009.07.。