wwei-材料成形技术(塑性)-1
装备制造业之塑性成形技术

装备制造业之塑性成形技术装备制造业是国民经济中的重要支柱产业之一,其发展与创新对于国家经济以及军事安全具有重要的战略意义。
而塑性成形技术是装备制造行业中的一项重要成果,在提高装备品质、降低生产成本以及提升市场竞争力等方面发挥着至关重要的作用。
塑性成形技术是指将金属等材料通过加热并施加一定的压力使其发生塑性变形,从而获得所需要的产品形状的一种制造技术。
塑性成形技术包括很多种形式,比如挤压、拉伸、冲压、滚压、压铸等,不同的成形方式可以适用于不同材料的制造,同时也会对产品的性能产生不同的影响。
塑性成形技术的应用范围非常广泛,可以在航空、汽车、机械、能源、建筑等多个领域中得到应用。
比如在航空航天领域中,许多零部件使用的铝合金、钛合金等材料就是通过塑性成形技术加工而成。
在汽车制造中,钣金冲压技术、汽车车轮轧辊技术等都是塑性成形技术的应用,让汽车生产更快、更便宜、更环保。
在机械制造领域中,CNC数控机床等设备也是利用塑性成形技术来制造的。
塑性成形技术的好处是显而易见的。
首先,采用塑性成形技术可以大幅度降低材料的浪费,保证物料的利用率。
其次,成形的过程中可以大大提高材料的强度、硬度和韧性等性能,使其具有更优异的物理性能。
最后,采用塑性成形技术可以大幅度节省制造成本,提高制造效率,节约人力资源。
然而,塑性成形技术也有其自身的难点和挑战。
首先,在材料的选择、加工方法的确定、生产设备的运行等方面都需要高度的技巧和经验。
其次,在实际应用中还需要充分考虑诸如材料的质量稳定性、生产成本等问题。
因此,塑性成形技术的应用需要专业技术人员在其运用前对其加工原理、机械构造和效果等进行充分的研究和了解。
总之,塑性成形技术在装备制造行业中占据着重要的位置。
它不仅可以使装备产品的品质得到大幅提升,而且还能够提高生产效率、降低生产成本、实现资源的实际应用。
在这个全球化的时代,如何不断创新、精益求精,才能在激烈的国际市场中占据一席之地。
塑性成形技术不仅是一种装备制造技术,更是一种精神和实践。
塑性成型原理
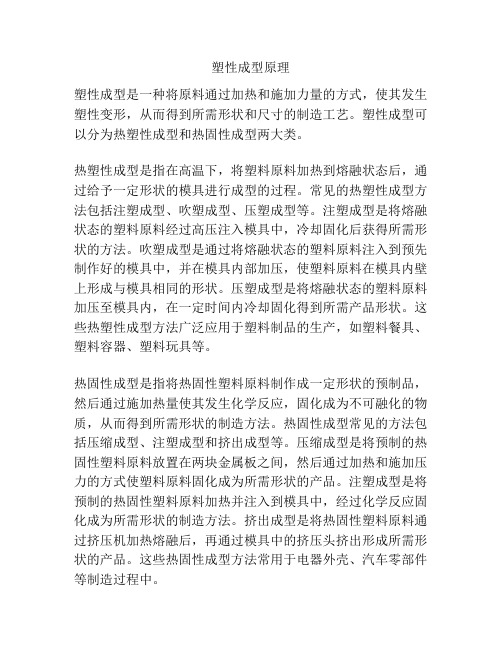
塑性成型原理塑性成型是一种将原料通过加热和施加力量的方式,使其发生塑性变形,从而得到所需形状和尺寸的制造工艺。
塑性成型可以分为热塑性成型和热固性成型两大类。
热塑性成型是指在高温下,将塑料原料加热到熔融状态后,通过给予一定形状的模具进行成型的过程。
常见的热塑性成型方法包括注塑成型、吹塑成型、压塑成型等。
注塑成型是将熔融状态的塑料原料经过高压注入模具中,冷却固化后获得所需形状的方法。
吹塑成型是通过将熔融状态的塑料原料注入到预先制作好的模具中,并在模具内部加压,使塑料原料在模具内壁上形成与模具相同的形状。
压塑成型是将熔融状态的塑料原料加压至模具内,在一定时间内冷却固化得到所需产品形状。
这些热塑性成型方法广泛应用于塑料制品的生产,如塑料餐具、塑料容器、塑料玩具等。
热固性成型是指将热固性塑料原料制作成一定形状的预制品,然后通过施加热量使其发生化学反应,固化成为不可融化的物质,从而得到所需形状的制造方法。
热固性成型常见的方法包括压缩成型、注塑成型和挤出成型等。
压缩成型是将预制的热固性塑料原料放置在两块金属板之间,然后通过加热和施加压力的方式使塑料原料固化成为所需形状的产品。
注塑成型是将预制的热固性塑料原料加热并注入到模具中,经过化学反应固化成为所需形状的制造方法。
挤出成型是将热固性塑料原料通过挤压机加热熔融后,再通过模具中的挤压头挤出形成所需形状的产品。
这些热固性成型方法常用于电器外壳、汽车零部件等制造过程中。
总之,塑性成型通过加热和施加力量的方式,使塑料原料发生塑性变形,得到所需形状和尺寸的制造工艺。
热塑性成型和热固性成型是常见的塑性成型方法,它们在各个工业领域中广泛应用,为我们生活提供了丰富多样的塑料制品。
wwei材料成形技术(塑性)1

二、金属塑性成形的基本生产方式 1、轧制:金属毛坯在两个轧辊之间受压变形而形成各 种产品的成形工艺,图6-1。 2、挤压:金属毛坯在挤压模内受压被挤出模孔而变形 的成形工艺,图6-3。 3、拉拔:将金属坯料拉过拉拔模的模孔而变形的成形 工艺,图6-5。 4、自由锻:金属毛坯在上下砥铁间受冲击或压力而变 形的成形工艺,图6-7(a)。 5、模锻:金属坯料在既有一定形状的锻模模膛内受击 力或压力而变形的成形工艺,图6-7(b) 。
塑性愈大、变形抗力愈小,材料的可锻性愈好
4、可锻性的影响因素
(1)化学成分 A、碳钢中碳和杂质元素的影响
C、H、P(冷脆)、S (热脆) B、合金元素的影响
塑性降低,变形抗力提高。
(2)内部组织
单相组织(纯金属或者固溶体)比多相组织塑性好。 细晶组织比粗晶组织好; 等轴晶比柱状晶好。 面心立方结构的可锻性最好,体心立方结构次之, 而密排六方结构可锻性最差。
冲击力和压力
锻压是锻造与冲压的总称。
★锻造:在加压设备及工(模)具作用下,使坯料、铸锭产生局 部或全部的塑性变形,以获得一定几何尺寸、形状和质量的锻件 的加工方法。锻造通常是在高温(再结晶温度以上)下成形的,
因此也称为金属热变形或热锻。
★锻造特点:1、压密或焊合铸态金属组 织中的缩孔、缩松、空隙、气泡和裂纹。 2、细化晶粒和破碎夹杂物,从而获得一 定的锻造流线组织。因此,与铸态金属 相比,其性能得到了极大的改善。 3、主要用于生产各种重要的、承受重载荷的机器零件或毛坯。 如机床的主轴和齿轮、内燃机的连杆、起重机的吊钩等。 4、高温下金属表面的氧化和冷却收缩等各方面的原因,锻件精度 不高、表面质量不好,加之锻件结构工艺性的制约。
2、晶粒和分布在晶界上的非金属夹杂物ห้องสมุดไป่ตู้沿变形方向被拉长, 但是拉长的晶粒可经再结晶又变成等轴细粒状,而这些夹杂物不能 改变,就以细长线条状保留下来,形成了所谓的纤维组织。 纤维组织的化学稳定性很高,只有经过锻压才能改变其分布方向, 用热处理是不能消除或改变纤维组织形态的。 纤维组织使金属的力学性能具有明显的方向性。
装备制造业之塑性成形技术

装备制造业之塑性成形技术随着现代工业的不断发展,各类装备制造业在实现高效生产和优质产品方面面临着日益严峻的挑战。
然而,塑性成形技术作为一种重要的制造工艺,正逐渐成为解决这些问题的关键。
本文将介绍塑性成形技术在装备制造业中的应用及其优势,并分析其未来发展趋势。
一、塑性成形技术在装备制造业中的应用1. 金属板材的压力成形金属板材压力成形技术是制造高强度、高精度零部件的重要手段。
通过将金属板材置于模具中,并施加压力,使金属板材发生弯曲、拉伸或冲裁等变形过程,从而得到所需形状的零部件。
该技术广泛应用于航空航天、汽车、电子等领域,并且可以生产出具有优良机械性能和表面质量的产品。
2. 金属管材的拉伸和冲压成形金属管材的拉伸和冲压成形技术主要用于制造管道、管接头和其他金属管材零部件。
通过控制拉伸和冲压力度,使金属管材在变形过程中逐渐改变截面形状,从而得到满足需求的产品。
该技术在石油化工设备、船舶制造等行业中得到广泛应用。
3. 塑性挤压技术塑性挤压技术是将金属坯料通过模具挤压成型,用于制造复杂截面的金属材料。
该技术具有高效率、节能和资源利用率高的特点,并且可以生产出优质的零部件。
在航空航天、铁路交通等领域,塑性挤压技术已成为制造高性能轻质构件的重要工艺。
二、塑性成形技术的优势1. 精度高塑性成形技术可以通过精确的模具设计和控制,实现对材料的精细加工,从而获得高度精密的零部件。
与传统加工工艺相比,塑性成形技术具有更低的工艺损失和变形量,可以提供更高的制造精度和表面质量。
2. 材料利用率高塑性成形技术将材料的变形过程与材料的剪切、挤压和拉伸等工艺相结合,可大幅提高材料的利用率。
与传统切削加工相比,塑性成形技术减少了材料废料的产生,并可在一次成形中得到复杂形状的零部件。
3. 生产效率高塑性成形技术具有高效率、批量生产的优势。
通过合理的设备配置和工艺优化,可以实现自动化、连续化生产,从而大幅提高生产效率。
此外,塑性成形技术还可以快速响应市场需求,缩短产品的开发周期。
【材料成型工艺--锻压】一、塑性成形理论基础(2014)

1.2 塑性变形后金属的组织和性能
1.冷变形及其影响 1)冷变形对金属性能的影响
① 冷变形强化/加工硬化(work hardening) 金属在塑性变形中随着变形程度的增加,强度、硬度升
高而塑性、韧性下降的现象称为加工硬化。
有利:很多热处理不能强化的金属 材料的主要强化方法
不利:进一步的塑性变形带来困难。
变形10% 100× 纤维组织
变形40% 100×
变形80% 100×
工业纯铁不同变形度的显微组织
具有纤维组织的金属,各个方向上的力学性能不相同。顺纤维 方向的力学性能比横纤维方向的好。
分析: 采用棒料直接经切削加工制造螺钉 采用同样棒料经局部镦粗方法制造螺钉
纤维组织的利用原则
➢ 力求流线沿工件外形轮廓连续分布而
材料塑性成形工艺
塑性成形 (Plasticity Forming) 是利用金
属材料所具有的塑性变形能力,在外力的作用下 使金属材料产生预期的塑性变形,从而获得具有 一定形状、尺寸和力学性能的零件或毛坯的加工
方法。工程上常称为压力加工。
金属塑性成形中作用在金属坯料上的外力主要有两种: 冲击力和压力。锤类设备产生冲击力使金属变形,轧机和 压力机对金属坯料施加静压力使金属变形。
1.单晶体的塑性变形 室温下,单晶体金属塑性变形是晶粒内变形的结果,主
要是通过滑移和孪生进行的。 1)滑移 晶体的一部分相对另一部分沿一定的晶面发生相对滑动。
晶体在切应力作用下的变形过程
4
2)孪晶
晶体的一部分相对一部 分沿一定的晶面发生相 对转动。
单晶体在切应力作用下的孪生变形过程
2. 多晶体的塑性变形
二、 冲压成形工艺 2.1 概述 2.2 冲裁 2.3 弯曲 2.4 拉深 三、 锻造成形工艺 3.1 自由锻 3.2 模锻
材料成型工艺技术

材料成型工艺技术材料成型工艺技术是指将材料通过一定的工艺方法,经过加工、成形、塑造等过程,使其达到特定的形状和性能要求的一种技术。
这种技术可以广泛应用于各个行业,如汽车、航空、电子、家电等领域。
材料成型工艺技术的发展,为各个行业提供了更多的可能性和选择。
材料成型工艺技术主要包括压力成型、热成型、造型、粉末冶金等多种方法。
其中,压力成型是一种将材料放入模具中,在给定的条件下施加一定的压力,使材料在模具内成型的方法。
这种方法适用于加工金属、塑料、陶瓷等材料。
压力成型工艺技术具有成形精度高、表面光洁度好等特点,被广泛应用于制造各种零部件。
热成型是一种通过加热材料使其变软,然后通过外界力的作用使其变形的方法。
这种方法适用于加工塑料、橡胶等材料。
热成型工艺技术能够使材料保持一定的形状稳定性,并且在加工过程中能够消除材料内部的应力,提高产品的性能。
造型是一种通过模板、模具等工具对材料进行塑造的方法。
这种方法适用于加工陶瓷、玻璃等材料。
造型工艺技术能够使材料呈现出各种复杂的形状,满足设计师的要求,并且能够提高生产效率。
粉末冶金是一种通过将金属粉末进行成型、烧结等处理,制造出具有特定形状和性能的材料的方法。
这种方法适用于生产精密零部件、高温合金等材料。
粉末冶金工艺技术能够扩大材料的应用范围,提高产品的性能。
在材料成型工艺技术中,工艺参数的控制是非常重要的。
工艺参数包括温度、压力、速度等多个方面。
通过合理控制这些参数,可以使成型产品具有更好的性能。
材料成型工艺技术的发展,对于提高产品质量、降低产品成本、增加产品种类等方面具有重要作用。
随着科技的不断进步,材料成型工艺技术也在不断创新和发展,为各行各业的发展提供更多的机会和挑战。
材料成型工艺基础-金属塑性成形课件.
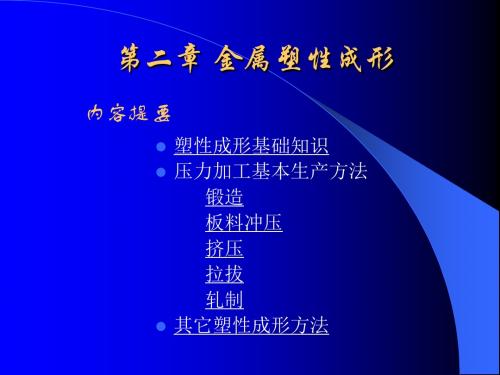
内容提要
塑性成形基础知识 压力加工基本生产方法 锻造 板料冲压 挤压 拉拔 轧制 其它塑性成形方法
本章要求 重点掌握: 自由锻、模锻、普通冲裁、拉深的原理 和应用场合 了解其他成形方法的原理、应用
§1 塑性变形基础知识
一、加工硬化
二、材料的压力加工性能
可 锻 性
加工前的钢锭 (铸造组织)
2.1塑变基础
钢 锭 在 压 力 机 上 开 坯
§2 锻造
自由锻 (手工、机器)
模锻
返回
连杆锻件
装饰锻件
自由锻
2.2自由锻
一、设备
空气锤 蒸汽锤 电液锤 水压机
冲击力,小型工件 冲击力,中型工件 冲击力,中型工件 静压力,大型、巨型工件
二、基本工序
1.镦粗 盘类、饼状工件主工序
连杆锻模
曲轴模锻
三、锻件图的制定
2.3模 锻
1. 分模面的确定
确保锻件能从模膛中取出,选最大截面。 上、下模膛结构应基本对称或相似。 模膛的深度应较浅。 尽量为一平面,便于锻模的生产。 尽量使敷料等最少,提高金属利用率,节
省后续加工工时。
2.3模 锻
2.敷料、加工余量和公差的确定 3.模锻斜度
2.5其他成形
超 塑 成 形 的 应 用
3.液态模锻
2.5其他成形
4.冷镦
2.5其他成形
冷镦机
2.5其他成形
连 杆 的 辊 锻
2.5其他成形
2.斜轧(螺旋斜轧)
轧 麻 花 钻
2.5其他成形
冷 轧 丝 杠
四、新工艺
1.精密模锻 优点:实现少、无切削加工 保证措施: 少氧化、无氧化加热工艺 精确计算坯料重量 高精度模膛 模膛应及时冷却和润滑
材料的塑性成形工艺

材料的塑性成形工艺引言塑性成形是一种常见的材料加工工艺,通过施加力量使材料发生形变,以获得所需的形状和尺寸。
塑性成形工艺包括冷拔、冷加工、锻造、挤压、拉伸等多种方法。
本文将介绍几种常见的材料塑性成形工艺及其特点。
一、冷拔1.1 工艺流程冷拔是一种拉伸加工的方法,主要用于金属材料。
其工艺流程包括以下几个步骤:1.选材:选择合适的原材料进行冷拔加工。
2.加热:将材料加热至适当的温度,以提高其塑性。
3.均质化处理:通过变形和退火等处理方法,使材料组织更加均匀。
4.拉拔:将材料拉伸至所需的形状和尺寸。
5.精整:通过切割、修整等方法,使成品达到要求的尺寸。
1.2 特点冷拔工艺具有以下特点:•成品尺寸精度高,表面质量好。
•可加工各种材料,包括金属和非金属材料。
•可以提高材料的强度和硬度。
二、冷加工2.1 工艺流程冷加工是一种在常温下进行的成形加工方法,常用于金属材料。
其工艺流程包括以下几个步骤:1.选材:选择合适的原材料进行冷加工。
2.切削:通过刀具对材料进行切削加工。
3.成型:通过冷加工设备对材料进行压制、弯曲、卷曲等成型操作。
4.精整:通过修整、研磨等方法,使成品达到要求的尺寸和表面质量。
2.2 特点冷加工具有以下特点:•成品尺寸精度高,表面质量好。
•可以加工多种材料,包括金属和非金属材料。
•部件形状复杂度高,适用于精密加工要求较高的产品。
三、锻造3.1 工艺流程锻造是一种通过施加压力将材料压制成所需形状的工艺方法。
其工艺流程包括以下几个步骤:1.选材:选择合适的原材料进行锻造。
2.加热:将材料加热至适当的温度,以提高其塑性。
3.锻造:通过锻造设备施加压力,将材料压制成所需形状。
4.精整:通过修整、热处理等方法,使成品达到要求的尺寸和性能。
3.2 特点锻造具有以下特点:•可以加工各种金属材料,包括高温合金和非金属材料。
•成品强度高,韧性好。
•高生产效率,适用于大批量生产。
四、挤压4.1 工艺流程挤压是一种将材料挤压成所需截面形状的塑性成形工艺。
塑性成形的特点与基本生产方式

塑性成形的特点与基本生产方式塑性成形是一种广泛应用于工程领域的加工技术,它通过对热软化塑料材料进行塑性变形,以获得各种复杂的形状和尺寸。
本文将介绍塑性成形的特点以及常见的基本生产方式。
1. 塑性成形的特点塑性成形具有以下几个特点:1.1 灵活性塑性成形可以根据需要灵活地加工出各种复杂形状的产品,例如各种外壳、管道、容器等。
通过改变模具和调整加工参数,可以满足不同产品的加工需求。
1.2 生产效率高相比于其他加工方法,塑性成形具有较高的生产效率。
一次成型可以同时加工多个产品,且生产周期较短。
同时,还可以进行自动化生产,提高生产效率。
1.3 材料利用率高塑性成形能够使材料得到充分利用。
由于材料在加工过程中可以被塑性拉伸、薄化,可以最大限度地减少材料的损耗。
1.4 加工成本低由于塑性成形生产工艺简单,设备投资与维护成本相对较低。
同时,生产过程中材料利用率高,可以降低材料成本。
2. 基本生产方式2.1 挤出成形挤出成形是最常见的塑性成形方式之一。
它通过将塑料材料加热熔融后,通过挤压机将熔融塑料挤出成型。
挤出成形常用于生产管道、板材、型材等产品。
2.2 注塑成形注塑成形是另一种常见的塑性成形方式。
它通过将塑料材料加热熔融后,将熔融塑料注入到闭合的模具中,并施加一定的压力进行冷却固化。
注塑成形适用于生产各种复杂形状的产品,如塑料零件、玩具等。
2.3 吹塑成形吹塑成形是一种特殊的塑性成形方式,常用于生产空心容器,例如瓶子、桶等。
它通过将熔融塑料放置在模具中,通过压缩空气将塑料吹膨为模具形状。
2.4 压延成形压延成形是将塑料热融化后,通过双辊或多辊挤压机将塑料挤压成特定形状和厚度的薄膜或板材。
压延成形适用于生产各种包装薄膜、塑料薄板等产品。
2.5 热压成形热压成形是将加热熔融的塑料放置于模具中,施加一定的压力进行冷却固化。
常用于生产较厚的塑料零件和产品。
总结塑性成形作为一种常见的加工技术,具有灵活性、高生产效率、材料利用率高和加工成本低的特点。
塑性成形技术讲解

塑性成形技术讲解第⼆章塑性成形技术※塑性成形技术:利⽤外⼒使⾦属材料产⽣塑性变形,使其改变形状、尺⼨和改善性能,从⽽获得各种产品的加⼯⽅法。
※主要应⽤:1)⽣产各种⾦属型材、板材和线材;2)⽣产承受较⼤负荷的零件,如曲轴、连杆等;※塑性成形特点:1)产品⼒学性能优于铸件和切削加⼯件;2)材料利⽤率⾼,⽣产率⾼;3)产品形状不能太复杂;4)易实现机械化、⾃动化※分类:1)轧制2)挤压3)拉拔4)锻压:a锻造(⾃由锻,模锻)。
b 冲压第⼀节⾦属塑性成形的物理基础⼀、塑性变形的实质●宏观:外⼒,弹性变形,塑性变形(分切应⼒作⽤)●微观(晶体内部):位错滑移和孪晶●多晶体:晶粒变形、晶界滑移、晶粒转动⼆、塑性变形的分类●冷塑性变形:低于再结晶温度以下时发⽣的变形钨的再结晶温度在1200度。
●热塑性变形:⾼于再结晶温度以上时发⽣的变形铅、锡等⾦属再结晶温度在零度以下。
三、冷塑性变形对⾦属组织和性能的影响产⽣加⼯硬化:随着变形程度的提⾼,⾦属的强度和硬度提⾼,塑性和韧性下降的现象。
原因:位错密度提⾼,亚结构细化2. 产⽣内应⼒:变形开裂,抗腐蚀性能降低,采⽤去应⼒退⽕进⾏消除。
3. 晶粒拉长或破碎,可能产⽣各向异性的塑性变形→晶格畸变→加⼯硬化→内能上升(不稳定)→加热→原⼦活⼒上升→晶格重组→内能下降(温度低时,回复。
温度⾼时,再结晶)四、热塑性变形对⾦属组织和性能的影响⼀)、五种形态:静态回复;静态再结晶;动态回复;动态再结晶;亚动态再结晶1、静态回复、静态再结晶:变形之后,利⽤热变形后的余热进⾏,不需要重新加热。
2、动态回复、动态再结晶:热变形过程中发⽣的。
3、亚动态再结晶:动态再结晶进⾏的热变形过程中,终⽌热变形后,前⾯发⽣的动态再结晶未完成⽽遗留下来的,将继续进⾏⽆孕育期的再结晶。
⼆)、热变形对⾦属组织和性能的影响1. 使铸锭或⽑坯中的⽓孔和疏松焊合,晶粒细化,改善夹杂物和第⼆相等形态和分布,偏析部分消除,使材料成分均匀。
《材料成型技术》课件

锻造
通过对金属进行加热和冷却,使其在压力下改变形 状,常用于制造零件和工具。
挤压
将材料穿过模具的缝隙,使其变形成所需形状,常 用于制造管道、线材等。
铸造
将液态材料注入模具中,待冷却后得到所需形状, 广泛应用于汽车、航空等行业。
成型
通过热塑性材料的加热和压力,将其形成所需形状, 常见于塑料制品生产。
常见的材料成型技术
局限性
• 材料限制 • 工艺复杂性 • 有限的成型尺寸
材料成型技术的发展趋势
1
智能化制造
通过引入自动化和智能化技术,提高生产效率和质量。
2
新材料应用
开发和使用新型材料,提高产品性能和使用寿命。
3
环保节能
减少能源消耗和废弃物产生,实现可持续发展。
总结和展望
材料成型技术在各个领域都扮演着重要角色,随着科学技术的进步,我们可以期待在未来看到更多创新和突破。
《材料成型技术》PPT课 件
材料成型技术是一门研究材料加工和加工工艺的学科,涵盖了大量不同类型 的材料和方法,对各个领域的工业和科研都具有重要的意义。
什么是材料成型技术
材料成型技术是通过加热、压力、变形等方式将原材料转变为所需形状和尺寸的工艺。它包括了常见的加工方法, 如锻造、铸造、挤压等。
不同类型的材料成型技术
航空航天领域对高强度和轻质的材料需求较高, 成型技术为其提供了多种解决方案。
3 电子产品
4 建筑领域
成型技术在电子产品制造中的应用包括电路板、 塑料外壳等部件的生产。
通过材料成型技术可以生产建筑中常见的构件, 如钢结构、玻璃幕墙等。
材料成型技术的优势与局限性
优势
• 高效生产 • 多样化的产品形状 • 成本效益
《塑性成型原理》课件
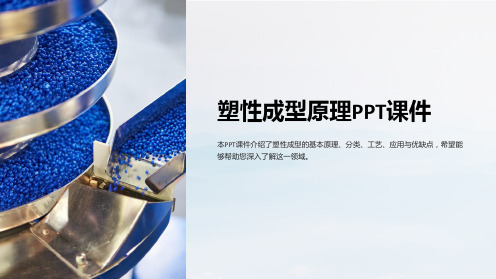
塑性变形过程
1
传递应力
材料在外力作用下,分子间开始进行运动
变形
2
并传递应力,从行改变材料的形态。
分子在传递应力的过程中发行应变,导致
塑性变形产行。
3
强度恢复
塑性变形结束后,材料开始回弹,进而 使应变减小,强度增加。
塑性成型的工艺与方法
挤压成型
通过挤出口产生的挤压力让高 温软化的材料变形成所需截面 形状。
吹塑成型
将加热的塑料片材放置在形状 符合需要的具有微小孔的模具 上,利用压缩空气把塑料片材 吹卡进去,达到成型的目的。
热成型
根据成型温度、压力或成型方 式不同,又可以分为真空吸塑 成型、热压成型、热拉伸成型 等。
塑性成型的应用领域
工业制造
塑性成型在工业制造领域的应用 十分广泛,如汽车、电器、玩具 等生产制造中都广泛使用。
塑性成型原理PPT课件
本PPT课件介绍了塑性成型的基本原理、分类、工艺、应用与优缺点,希望能 够帮助您深入了解这一领域。
塑性成型的定义让热塑性材料变形成所需形状的过程。
2 分类
根据加热方式,塑性成型可分为热成型和冷成型;根据材料的状态,塑性成型可分为固 态变形和热变形。
医疗器械
医疗器械需要塑性成型产生的材 料具有优良的耐腐蚀性,生物安 全性等特点。
塑料制品
如饮料瓶、打包盒、盆子、盘子 等的生产都需要塑性成型。
塑性成型工艺的优缺点
优点
生产效率高,成本低;制造出来的产品质量稳定,重复性好。
缺点
生产过程对环境污染大;材料无法回收利用,热变性能不稳定。
结论与总结
塑性成型是一种将热塑性材料通过加热或其他方式变形成所需形状的过程,其在生产制造、医疗器械、塑 料制品等领域都有广泛应用,但也存在污染、资源浪费等问题。因此在使用时需要注意环保措施和材料回 收。
塑性成形新技术及应用

塑性成形新技术及应用塑性成形是一种常见的加工方法,广泛应用于各行各业。
随着科技的发展和技术的进步,塑性成形也不断创新和改进,出现了许多新技术和应用。
首先,说到塑性成形的新技术,我们可以提到热成形技术。
热成形是一种通过控制金属的温度来实现形状改变的方法。
相比于常规的冷成形,热成形能够提高材料的塑性和可变形性,从而获得更复杂的形状和更高的尺寸精度。
热成形技术主要包括热锻、热轧、热拉伸等,广泛应用于航空航天、汽车制造、机械加工等领域。
其次,还可以提到微成形技术。
微成形是一种针对微米尺度工件的加工技术,主要通过微纳加工设备和精密控制技术来实现。
与传统的宏观成形相比,微成形具有尺寸小、精度高、工艺复杂等特点。
微成形技术在微机电系统(MEMS)、生物医学器械、微型传感器等领域有着广泛应用,如微型机械零件的制造、微流控芯片的加工等。
另外,值得一提的是增材制造技术在塑性成形中的应用。
增材制造技术是一种基于逐层堆叠的三维打印技术,通过逐层堆叠材料来构建复杂的工件形状。
在塑性成形中,增材制造可以实现一些传统加工方法无法完成的形状和结构,具有设计自由度高,制造成本低,能耗低等优势。
增材制造技术被广泛应用于航空航天、医疗器械、汽车制造等领域,如航空发动机叶片的制造、医学植入物的制备等。
除了以上所介绍的新技术,塑性成形还有许多其他的应用。
在汽车制造领域,塑性成形广泛应用于汽车车身板的制造。
汽车车身板材多采用薄板和超高强度钢,能够通过塑性成形来实现复杂的车身形状和结构。
在航空航天领域,塑性成形被用于制造飞机的轻质结构件,如航空发动机叶片、机翼等。
在电子设备制造领域,塑性成形被用于制造外壳、内部零件等。
在医疗器械领域,塑性成形被用于制造人工关节、骨刺钉等。
总而言之,塑性成形作为一种重要的加工方法,不断创新和改进,出现了许多新技术和应用。
热成形技术、微成形技术和增材制造技术都是其中的新技术,它们为塑性成形带来了更多的发展机遇和应用领域。
装备制造业之塑性成形技术

装备制造业之塑性成形技术在装备制造业中,塑性成形技术是一项重要的制造工艺,它通过对金属材料的塑性变形来实现对零件的成形。
塑性成形技术具有高效、精确、经济的特点,广泛应用于各个领域,如汽车制造、航空航天等。
本文将对塑性成形技术的概念、工艺流程以及在装备制造业中的应用进行论述,并重点介绍了其在汽车制造领域中的应用。
一、塑性成形技术概述塑性成形技术是利用材料在塑性变形过程中体积不变的特性,通过外力作用将材料加工成所需形状的一种成形工艺。
它能够更好地满足装备制造业对高强度、轻质材料的需求,并能够减少加工工序和材料浪费。
塑性成形技术包括热挤压、热轧、锻造、拉伸等多种方法,每种方法都有其适用的材料和成形形式。
二、塑性成形技术的工艺流程塑性成形技术的工艺流程一般包括材料准备、装配和调整、塑性成形、材料处理和成品制备等环节。
首先,需要选择合适的材料,并对其进行加热、退火等预处理,以提高材料的可塑性。
然后在成形装置中安装和调整模具,确保其能够进行准确的成形。
接下来,将加热后的材料放入成形装置中,通过外力的作用,使其发生塑性变形,并按照设计要求形成所需的零件形状。
最后,对成形后的零件进行处理和制备,如清洗、涂层等,以保证其质量和性能的稳定。
三、塑性成形技术在装备制造业中的应用1. 汽车制造领域塑性成形技术在汽车制造领域中得到了广泛的应用。
例如,汽车车身的制造中,通过冲压工艺将钢板进行成形,制作出车身外壳等零部件。
这种工艺具有高效、精确的特点,能够满足汽车制造行业对高强度、轻质材料的需求,并能够大批量生产,提高生产效率。
2. 航空航天领域在航空航天领域,塑性成形技术被广泛应用于飞机和火箭等装备的制造过程中。
例如,利用锻造技术可以制造出高强度、耐高温的发动机零部件,以提高发动机的性能和寿命。
此外,通过冲压工艺可以制造出轻质、高强度的飞机蒙皮和结构零件等。
3. 电子设备制造领域在电子设备制造领域,塑性成形技术也有着广泛的应用。
材料成型技术

材料成型技术
材料成型技术是一种将原材料加工成所需形状和尺寸的工艺方法。
它是制造业
中非常重要的一环,涉及到各种材料的加工和成型,包括金属、塑料、陶瓷等。
在现代工业生产中,材料成型技术的应用非常广泛,可以说是制造业的基础。
首先,材料成型技术可以分为传统成型技术和现代成型技术两大类。
传统成型
技术包括铸造、锻造、冲压等,这些技术已经有着悠久的历史,经过长期的发展和改进,已经非常成熟。
而现代成型技术则包括注塑成型、3D打印、激光切割等,
这些技术在近年来得到了快速的发展,为制造业带来了革命性的变化。
其次,材料成型技术的发展对制造业起到了至关重要的作用。
它不仅可以大大
提高生产效率,降低生产成本,还可以实现复杂产品的加工和成型。
比如,注塑成型技术可以生产出各种形状复杂的塑料制品,而3D打印技术更是可以实现个性化
定制,为制造业带来了更多的可能性。
此外,材料成型技术的发展也带动了材料科学的进步。
随着材料科学的不断发展,新型材料的涌现为材料成型技术的应用提供了更多的可能性。
比如,高强度、高韧性的新型金属材料可以大大提高传统成型技术的加工性能,而具有特殊功能的复合材料也为现代成型技术的发展带来了新的动力。
总的来说,材料成型技术是制造业发展的重要支撑,它的发展不仅可以提高生
产效率,降低生产成本,还可以推动材料科学的进步。
随着科技的不断进步和创新,相信材料成型技术在未来会有更加广阔的发展空间,为制造业带来更多的惊喜和可能性。
wwei材料成形技术液态.ppt

习题:第2、3、9、10题。P15
谢谢!
碳钢
铸铁
离共晶点C越远,结晶
温度区间越宽,流动
性C点就合成越分差金以。前的换的句化铁话碳学说合,成分决定了2种凝固模式
金,即亚共晶铸铁,
流加铁的呢动而合,性提金即随高,C含;流点纯 对 有碳过动成金 确应量共性分属 定A的晶随以点和 的增铸含后和共 熔C晶点点合,成金恒分,温, 碳 量 的 增 加结而晶下,降结。果在铸型中
化学成分
磷元素提高充型能力
硫降低充型能力 钢充型能力差
熔点高 结晶温度范围宽
结论:结晶温度范围越宽,合金 的充型能力越差。
浇注温度指的是浇注时熔融合金的温度,一般要求
比它的影液相响线熔温融度高合,金即存充在型过的热度工,艺推条迟它件的凝
固时间,以保持良好的流动性。但是也不能太高, 否则造成吸气,氧化,过收缩,粘砂,胀砂等不良 后果。①所浇以注,条每种件合:金主有要自指己浇的注合温理度浇,注浇温注度压范力围。。 参教材P5其。中最重要的是浇注温度。
三杆热应力分析模型
+- +
-+ -
两杆均处于塑性状态 2杆比1杆冷却快,应力通过塑性变形自 动消除
1杆 塑性状态,2杆 弹性状态 2 杆收缩大,产生变形,对1产生压力。图1-10b 1 杆受压产生变形,但内应力自动消除。图1-10c
1、2两杆均处于弹性状态 1杆收缩大,对2产生压力,但2不能消除内应力。 图1-10d
②铸型:导热能力,铸型温度(预热), 排气,铸型结构。参看P5-6。
1.2液态合金的收缩
收缩定义:在凝固和冷却过程中, 体积和尺寸减小的现象。
- 1、下载文档前请自行甄别文档内容的完整性,平台不提供额外的编辑、内容补充、找答案等附加服务。
- 2、"仅部分预览"的文档,不可在线预览部分如存在完整性等问题,可反馈申请退款(可完整预览的文档不适用该条件!)。
- 3、如文档侵犯您的权益,请联系客服反馈,我们会尽快为您处理(人工客服工作时间:9:00-18:30)。
Fundamental of Materials Forming
材料科学与工程系
Jiangsu Polytechnic University
第六章 金属塑性成形的工艺 理论基础
第一节 金属塑性成形的基本工艺
一、基本概念
金属的塑性成形工艺(压力加工工艺):利用金属在 压力加工工艺): ):利用金属在
第二节 金属的塑性变形
一、塑性变形的实质:在切应力的作用下,金属内部晶体沿 塑性变形的实质:在切应力的作用下, 某一平面产生滑移,实现了晶体的塑性变形。 某一平面产生滑移,实现了晶体的塑性变形。 二、金属塑性变形的类型 (1)冷变形:金属在再结晶温度以下的塑性变形称为冷变形。 冷变形:金属在再结晶温度以下的塑性变形称为冷变形。 冷变形过程中只产生加工硬化而无再结晶现象,因此变形过程中 冷变形过程中只产生加工硬化而无再结晶现象, 金属的变形抗力大,塑性低。若变形量过大,会引起金属的破裂。 金属的变形抗力大,塑性低。若变形量过大,会引起金属的破裂。 如钢丝的折断 就是这个道理 (2)热变形:金属在再结晶温度以上的塑性变形称为热变形。 热变形:金属在再结晶温度以上的塑性变形称为热变形。 变形过程中再结晶能及时克服加工硬化。 变形过程中再结晶能及时克服加工硬化。 因而变形过程中金属的塑性好,变形抗力低,不需要安排中间退火。 因而变形过程中金属的塑性好,变形抗力低,不需要安排中间退火。
外力作用下产生的塑性变形来获得具有一定形状、尺寸 外力作用下产生的塑性变形来获得具有一定形状、 作用下产生的塑性变形来获得具有一定形状 和力学性能的原材料、毛坯或零件的成形工艺。 和力学性能的原材料、毛坯或零件的成形工艺。
冲击力和压力
锻压是锻造与冲压的总称。 锻压是锻造与冲压的总称。
★锻造:在加压设备及工(模)具作用下,使坯料、铸锭产生局 锻造:在加压设备及工( 具作用下,使坯料、 部或全部的塑性变形,以获得一定几何尺寸、 部或全部的塑性变形,以获得一定几何尺寸、形状和质量的锻件 的加工方法。锻造通常是在高温(再结晶温度以上)下成形的, 的加工方法。锻造通常是在高温(再结晶温度以上)下成形的, 因此也称为金属热变形或热锻。 因此也称为金属热变形或热锻。 ★锻造特点:1、压密或焊合铸态金属组 锻造特点: 、 织中的缩孔、缩松、空隙、气泡和裂纹。 织中的缩孔、缩松、空隙、气泡和裂纹。 2、细化晶粒和破碎夹杂物,从而获得一 、细化晶粒和破碎夹杂物, 定的锻造流线组织。因此, 定的锻造流线组织。因此,与铸态金属 相比,其性能得到了极大的改善。 相比,其性能得到了极大的改善。 3、主要用于生产各种重要的、承受重载荷的机器零件或毛坯。 、主要用于生产各种重要的、承受重载荷的机器零件或毛坯。 如机床的主轴和齿轮、内燃机的连杆、起重机的吊钩等。 如机床的主轴和齿轮、内燃机的连杆、起重机的吊钩等。 高温下金属表面的氧化和冷却收缩等各方面的原因, 4、高温下金属表面的氧化和冷却收缩等各方面的原因,锻件精度 不高、表面质量不好,加之锻件结构工艺性的制约。 不高、表面质量不好,加之锻件结构工艺性的制约。 锻件通常只作为机器零件的毛坯。 锻件通常只作为机器零件的毛坯。
★冲压特点:1、冲压件刚性好、结构轻、 冲压特点: 、冲压件刚性好、结构轻、 特点 精度高、外形美观、互换性好等优点。 精度高、外形美观、互换性好等优点。 2、广泛用于汽车、拖拉机外壳、电器、仪表及日用品的生产。 、广泛用于汽车、拖拉机外壳、电器、仪表及日用品的生产。
二、金属塑性成形的基本生产方式 轧制: 1、轧制:金属毛坯在两个轧辊之间受压变形而形成各 种产品的成形工艺, 种产品的成形工艺,图6-1。 挤压: 2、挤压:金属毛坯在挤压模内受压被挤出模孔而变形 的成形工艺, 的成形工艺,图6-3。 拉拔: 3、拉拔:将金属坯料拉过拉拔模的模孔而变形的成形 工艺, 工艺,图6-5。 自由锻: 4、自由锻:金属毛坯在上下砥铁间受冲击或压力而变 形的成形工艺, 形的成形工艺,图6-7(a)。 模锻: 5、模锻:金属坯料在既有一定形状的锻模模膛内受击 力或压力而变形的成形工艺, 力或压力而变形的成形工艺,图6-7(b) 。
(3)变形温度 随着温度的升高,塑性增加,变形抗力降低。 随着温度的升高,塑性增加,变形抗力降低。 1)确定始锻温度与终锻温度 2)塑性成形应避免脆性区:(蓝脆区与热脆区) 塑性成形应避免脆性区:(蓝脆区与热脆区) :(蓝脆区与热脆区
(4)变形速度 一般变形速度增加则可锻性下降,故常用较小的变形速度。 一般变形速度增加则可锻性下降,故常用较小的变形速度。 (5)应力状态 1)应力状态对塑性的影响 在应力状态中,压应力个数 在应力状态中, 值越大, 越 多,数 值越大,则金属的塑性 越高。反之, 则拉应力个数越多, 越高。反之, 则拉应力个数越多, 数值越大,则金属的塑性越低。 数值越大,则金属的塑性越低。
四、影响塑Leabharlann 变形的因素1、塑性:在外力作用下产生永久变形而不破坏其完整 塑性:
性的能力。 性的能力。 2、变形抗力:金属对塑性变形的抵抗力。 金属对塑性变形的抵抗力。 3、可锻性:金属材料经受压力加工的难易程度。 可锻性:金属材料经受压力加工的难易程度。 它是用金属材料的塑性与变形抗力来衡量的。 它是用金属材料的塑性与变形抗力来衡量的。
1、回复;2、再结晶。 回复; 再结晶。
五、纤维组织 1、金属压力加工最原始的坯料是铸锭。 金属压力加工最原始的坯料是铸锭。 其内部组织很不均匀,晶粒粗大,且存在着许多其他缺陷: 其内部组织很不均匀,晶粒粗大,且存在着许多其他缺陷:如 气孔、缩松、偏析、非金属夹杂物等。将这种铸锭经热变形, 气孔、缩松、偏析、非金属夹杂物等。将这种铸锭经热变形, 粗大的铸状晶粒被打碎后,经过再结晶,就可形成细晶粒, 粗大的铸状晶粒被打碎后,经过再结晶,就可形成细晶粒,同 时在热变形过程中还可以将气孔、缩松等压合在一起, 时在热变形过程中还可以将气孔、缩松等压合在一起,使金属 的致密性提高。 的致密性提高。 2、晶粒和分布在晶界上的非金属夹杂物,沿变形方向被拉长, 晶粒和分布在晶界上的非金属夹杂物,沿变形方向被拉长, 但是拉长的晶粒可经再结晶又变成等轴细粒状, 但是拉长的晶粒可经再结晶又变成等轴细粒状,而这些夹杂物不能 改变,就以细长线条状保留下来,形成了所谓的纤维组织 纤维组织。 改变,就以细长线条状保留下来,形成了所谓的纤维组织。 纤维组织的化学稳定性很高,只有经过锻压才能改变其分布方向, 纤维组织的化学稳定性很高,只有经过锻压才能改变其分布方向, 用热处理是不能消除或改变纤维组织形态的。 用热处理是不能消除或改变纤维组织形态的。 纤维组织使金属的力学性能具有明显的方向性。 纤维组织使金属的力学性能具有明显的方向性。
三、常温下金属塑性变形后的变化 1、晶粒沿变形最大的方向伸长; 晶粒沿变形最大的方向伸长; 晶格与晶粒均发生扭曲,产生内应力; 2、晶格与晶粒均发生扭曲,产生内应力; 晶粒间产生碎晶。 3、晶粒间产生碎晶。 位错密度增多,强度、硬度提高而塑性、 4、位错密度增多,强度、硬度提高而塑性、韧性则下 产生加工硬化。 降,产生加工硬化。 四、加工硬化组织加热时组织和性能的变化
塑性愈大、变形抗力愈小,材料的可锻性愈好 可锻性愈好 塑性愈大、变形抗力愈小,材料的可锻性
4、可锻性的影响因素
(1)化学成分 A、碳钢中碳和杂质元素的影响 C、H、P(冷脆)、S (热脆) 冷脆)、 )、S 热脆) B、合金元素的影响 塑性降低,变形抗力提高。 塑性降低,变形抗力提高。 (2)内部组织
2)应力状态对变形抗力的影响: 应力状态对变形抗力的影响:
用相同材料在相同模具上进行挤压和拉拔, 用相同材料在相同模具上进行挤压和拉拔,其变形抗力前者 远比后者大,这是挤压时的应力 状态与拉拔时不同所致。 远比后者大, 状态与拉拔时不同所致。
习题: 习题:第1、2、6题。 、 、 题
3、纤维组织的利用原则 A、使纤维分布与零件的轮廓相符合而不被切断 B、使零件所受的最大拉应力与纤维方向一致,最大切应力与 使零件所受的最大拉应力与纤维方向一致, 纤维方向垂直
第三节 塑性变形 理论及假设
一、最小阻力定律 金属材料受外力作用发生塑性变形时, 金属材料受外力作用发生塑性变形时,若金属质点 在几个方向都可移动, 在几个方向都可移动,则金属质点就沿着阻力最小的方 向移动。 向移动。 按此定律,不论是圆形、 按此定律,不论是圆形、方形还是矩形的坯料在经 镦粗变形后,其最终都趋于圆形。 镦粗变形后,其最终都趋于圆形。
★冲压:板料在冲压设备及模具作用下,通过塑性变形产生分离 冲压:板料在冲压设备及模具作用下, 或成形而获得制件的加工方法,主要用于加工板料。 或成形而获得制件的加工方法,主要用于加工板料。 冲压通常是在再结晶温度以下完成变形的,因而也称为冷冲压。 冲压通常是在再结晶温度以下完成变形的,因而也称为冷冲压。
走最短的路,做最少的功。
开式模锻的金属流动
最小周边法则
二、金属经塑性变形前后体积不变假设
金属材料是连续的致密体,塑性变形前后体积变化很小, 金属材料是连续的致密体,塑性变形前后体积变化很小, 与形状变化相比可以忽略。 与形状变化相比可以忽略。
三、塑性变形程度的计算 1、锻造比(Y锻) 、锻造比( (1)拔长:Y锻=F0/F; )拔长: ; (2)镦粗:Y锻=H0/H )镦粗: 锻造时一般要求锻造比为2—2.5之间,而对于要求 之间, 锻造时一般要求锻造比为 之间 纵向性能的零件,锻造比则应适当增加。 纵向性能的零件,锻造比则应适当增加。 根据锻造比和体积不变假设可计算出坯料的尺寸。 根据锻造比和体积不变假设可计算出坯料的尺寸。 即: F坯料 = Y锻 F锻件;L坯料 = V坯料/ F坯料 。
单相组织(纯金属或者固溶体)比多相组织塑性好。 单相组织(纯金属或者固溶体)比多相组织塑性好。 细晶组织比粗晶组织好; 细晶组织比粗晶组织好; 等轴晶比柱状晶好。 等轴晶比柱状晶好。 面心立方结构的可锻性最好,体心立方结构次之, 面心立方结构的可锻性最好,体心立方结构次之, 而密排六方结构可锻性最差。 而密排六方结构可锻性最差。