Quality Management(英文版)
英文翻译版质量管理制度及职责

英文翻译版质量管理制度及职责Quality Management System and Responsibilities1.0 IntroductionOur organization is committed to delivering high-quality products and services to our customers. In order to ensure consistent quality, we have implemented a Quality Management System (QMS) that fully complies with ISO 9001:2015 requirements. This QMS covers all aspects of our operations, from design and development to delivery and customer service.2.0 Quality PolicyOur Quality Policy is to provide products and services that meet or exceed customer expectations through the continual improvement of our QMS. We achieve this by:- Understanding and meeting customer requirements- Applying effective design and development processes- Implementing rigorous quality inspections at all stages of production- Continually reviewing and improving our processes and systems- Providing ongoing training and development to our employees- Meeting all legal and regulatory requirements3.0 QMS DocumentationOur QMS is documented in a Quality Manual, which outlines our policies, procedures, and processes. This manual is available to all employees and is updated as necessary to reflect changes in our operations or ISO requirements.4.0 QMS Responsibilities4.1 Top ManagementTop management is ultimately responsible for the success of our QMS. They are responsible for ensuring that:- The QMS is effectively implemented and maintained- The Quality Policy and objectives are established and communicated throughout the organization- Appropriate resources are allocated to the QMS- The QMS is regularly reviewed to ensure its effectiveness4.2 Quality ManagerThe Quality Manager is responsible for leading the implementation and maintenance of the QMS. Their responsibilities include:- Developing and maintaining the Quality Manual- Coordinating QMS training and education- Conducting internal audits and leading external audits- Managing and facilitating corrective and preventive actions- Providing feedback to top management on the effectiveness of the QMS4.3 EmployeesAll employees have a responsibility to ensure that the QMS is implemented and maintained. Their responsibilities include:- Understanding and following all QMS policies, procedures, and processes- Identifying and reporting quality issues or non-conformities- Contributing to the continuous improvement of the QMS5.0 ConclusionOur QMS is critical to the success of our organization. By adhering to ISO 9001:2015 requirements and following our Quality Policy, we are confident that we can consistently deliver high-quality products and services to our customers. By working together and fulfilling our QMS responsibilities, we can ensure the ongoing success of our organization.。
Quality Management(英文版)(ppt 40页)

– Prevention costs: Training, surveys, implementation of quality system
– Failure costs: Rework, rejects, scrap – External Costs: Warranty, recall, handling complaints – Note – 85 % of costs are responsibility of management
8.1 Quality Planning
8.2 Quality Assurance
8.3 Quality Control
Source: pmbok guide 2000
© 2002 Robbins-Gioia, Inc.
8-3
Quality Management
• Addresses both the management of the project and of the product of the project
© 2002 Robbins-Gioia, Inc.
8-12
Quality Planning
Tools & Techniques
• Benefit/cost analysis – Cost and benefit tradeoffs of
meeting quality requirements
• Benchmarking – Comparing actual or planned project
Source: pmbok guide 2000
© 2002 Robbins-Gioia, Inc.
8-11
Quality Planning
第八章-Project-quality-management项目管理知识体系(PMBOK)英文第六版

Cause-and-Effect Diagram
18
Design for X (DfX)
• Design for X (DfX) is a set of technical guidelines that may be applied during the design of a product for the optimization of a specific aspect of the design.
• Project Quality Management also supports continuous process improvement activities as undertaken on behalf of the performing organization.
• The Project Quality Management processes are:
– Confirm that the quality processes are used and that their use meets the quality objectives of the project, and
– Improve the efficiency and effectiveness of processes and activities to achieve better results and performance and enhance stakeholders’ satisfaction.
– Quality standards that will be used by the project; – Quality objectives of the project; – Quality roles and responsibilities; – Project deliverables and processes subject to quality review; – Quality control and quality management activities planned for the
质量管理体系术语中英文对照

质量管理体系术语中英文对照Quality Management System Terminology Chinese-English Comparison1. IntroductionQuality management systems (QMS) serve as a framework for organizations to ensure the consistent production of high-quality goods and services. In order to effectively implement QMS and communicate within a global context, it is essential to understand the terminology used. This article provides a comprehensive Chinese-English comparison of key terms commonly used in quality management systems.2. Quality Management System (质量管理体系)A QMS refers to the set of policies, processes, and procedures implemented by an organization to manage quality-related activities. The following table presents the Chinese-English comparison of some fundamental terminology used in QMS.Term / 术语 Chinese / 中文 English / 英文Quality Management System 质量管理体系Quality Management SystemQuality Policy 质量方针 Quality PolicyQuality Objectives 质量目标 Quality ObjectivesQuality Manual 质量手册 Quality ManualQuality Procedures 质量程序 Quality ProceduresInternal Audit 内审 Internal AuditManagement Review 管理评审 Management Review3. Document Control (文件控制)In order to maintain consistency and control over documentation within a QMS, document control procedures are established. The following table provides the Chinese-English comparison of terms related to document control.Term / 术语 Chinese / 中文 English / 英文Document Control 文件控制 Document ControlDocument Numbering 文件编号 Document NumberingDocument Revision 文件修订 Document RevisionDocument Approval 文件批准 Document ApprovalDocument Distribution 文件分发 Document DistributionDocument Retention 文件保留 Document Retention4. Corrective and Preventive Actions (纠正和预防措施)Continuous improvement is a key component of QMS. Corrective and preventive actions are taken to address non-conformances and prevent theirrecurrence. The following table presents the Chinese-English comparison of terms related to corrective and preventive actions.Term / 术语 Chinese / 中文 English / 英文Corrective Action 纠正措施 Corrective ActionPreventive Action 预防措施 Preventive ActionRoot Cause Analysis 根本原因分析 Root Cause Analysis Non-conformance 不符合项 Non-conformance Problem Solving 问题解决 Problem Solving5. Training and Competence (培训和能力)To ensure employees possess the necessary skills and knowledge, training programs are implemented. The following table provides the Chinese-English comparison of terms related to training and competence.Term / 术语 Chinese / 中文 English / 英文Training 培训 TrainingCompetence 能力 CompetenceSkills 技能 SkillsTraining Needs Analysis 培训需求分析 Training Needs AnalysisTraining Effectiveness 培训效果 Training Effectiveness6. Supplier Management (供应商管理)Effective supplier management is crucial for maintaining quality in the supply chain. The following table presents the Chinese-English comparison of terms related to supplier management.Term / 术语 Chinese / 中文 English / 英文Supplier 供应商 SupplierSupplier Evaluation 供应商评估 Supplier EvaluationSupplier Approval 供应商批准 Supplier ApprovalSupplier Performance 供应商绩效 Supplier Performance Supplier Audit 供应商审核 Supplier Audit7. ConclusionUnderstanding the terminology used in quality management systems is vital for effective communication and implementation of QMS practices. This article has provided a comprehensive Chinese-English comparison of key terms commonly used in QMS, covering areas such as quality management system, document control, corrective and preventive actions, training and competence, and supplier management. By familiarizing oneself with these terminologies, organizations can enhance their quality management practices and strengthen their ability to meet customer expectations and regulatory requirements.。
Supplier Quality Management Procedure(中英文)
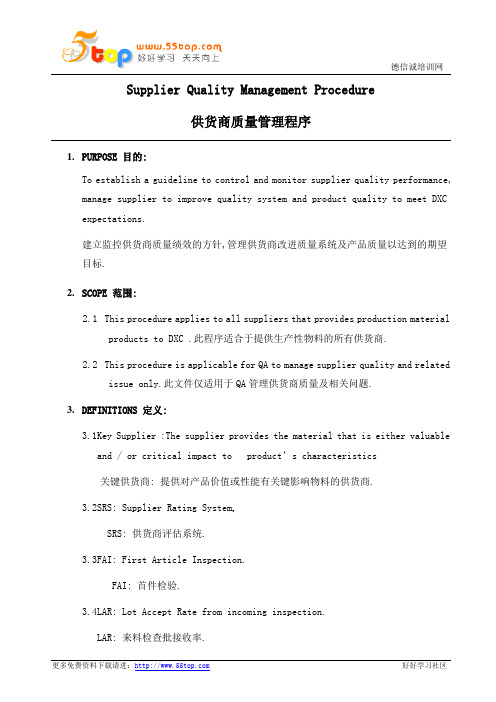
Supplier Quality Management Procedure供货商质量管理程序1.PURPOSE 目的:To establish a guideline to control and monitor supplier quality performance, manage supplier to improve quality system and product quality to meet DXC expectations.建立监控供货商质量绩效的方针,管理供货商改进质量系统及产品质量以达到的期望目标.2.SCOPE 范围:2.1This procedure applies to all suppliers that provides production materialproducts to DXC .此程序适合于提供生产性物料的所有供货商.2.2This procedure is applicable for QA to manage supplier quality and relatedissue only.此文件仅适用于QA管理供货商质量及相关问题.3.DEFINITIONS 定义:3.1Key Supplier :The supplier provides the material that is either valuableand / or critical impact to product’s characteristics关键供货商: 提供对产品价值或性能有关键影响物料的供货商.3.2SRS: Supplier Rating System.SRS: 供货商评估系统.3.3FAI: First Article Inspection.FAI: 首件检验.3.4LAR: Lot Accept Rate from incoming inspection.LAR: 来料检查批接收率.4.REFERENCE DOCUMENT 参考文件:4.1 BZQP-7-06 Supplier Rating System Procedure 供货商评估系统程序.4.2 BZQP-8-07 Corrective and preventive actions procedure 纠正及预防措施程序.5.RESPONSIBILITY 职责:5.1Purchasing staff 采购5.1.1 Arrange consolidation of the overall material supplierperformance and distribute to related parties.整理供货商质量绩效并发布给相关部门5.1.2Review the supplier performance and enhance supplier improvementmanagement.评估供货商绩效加强供货商改善管理.5.1.3 Coordinate an d plan supplier’s support both for ongoing & futureif necessary. 协调和规划供货商现在及将来的支持5.2QA质量工程师.5.2.1Follow supplier corrective action in line complaint. 跟进产线投诉问题和供货商的改善行动.5.2.2 Define key supplier for evaluation or assessment with purchasingstaff.与采购定义关键供货商以便评估.5.2.3 Review the assessment result for further improvement or supplierquality related matters..审核供货商质量相关的事项的评估结果,达到持续改善.5.3 ME制造工程If necessary, ME will support QA to perform supplier process audit and technology evaluation.必要时,ME将协助QA执行供货商制程审核及技朮评估.。
英文版 管理制度

英文版管理制度IntroductionA management system is a set of rules, practices, and procedures that are put in place to ensure that an organization operates in an efficient, effective, and ethical manner. It provides a framework for decision-making, resource allocation, and performance evaluation. A good management system can help an organization achieve its goals and objectives in a systematic and organized way.Types of Management SystemsThere are many different types of management systems, each designed to address a specific aspect of organizational operations. Some common types include:1. Quality Management System (QMS): A QMS is a set of policies, processes, and procedures that are implemented to ensure that products and services meet the required quality standards. It focuses on identifying and correcting quality issues to improve customer satisfaction and maintain consistency in product or service delivery.2. Environmental Management System (EMS): An EMS is a set of practices and procedures designed to minimize an organization's impact on the environment. It includes measures to reduce waste, conserve resources, and comply with environmental regulations.3. Occupational Health and Safety Management System (OHSMS): An OHSMS is a set of guidelines and procedures that are put in place to ensure the health and safety of employees in the workplace. It includes measures to prevent accidents, injuries, and illnesses, as well as safety training and compliance with relevant regulations.4. Information Security Management System (ISMS): An ISMS is a set of policies and procedures that are implemented to protect an organization's information assets from unauthorized access, use, disclosure, disruption, modification, or destruction. It includes measures to safeguard data, systems, and networks, and ensure the confidentiality, integrity, and availability of information.5. Risk Management System: A risk management system is a structured approach to identifying, assessing, and mitigating risks that may affect an organization's ability to achieve its objectives. It includes processes for risk identification, analysis, evaluation, treatment, monitoring, and communication.Benefits of a Management SystemImplementing a management system can provide a range of benefits to an organization, including:1. Improved efficiency and effectiveness: A management system provides a structured approach to managing resources, processes, and activities, which can help to streamline operations, reduce waste, and enhance productivity.2. Enhanced quality and consistency: A management system can help to ensure that products and services are delivered to a consistent standard, which can enhance customer satisfaction, loyalty, and trust.3. Better compliance and risk management: A management system can help an organization to comply with legal and regulatory requirements, as well as identify and mitigate risks that may impact its operations.4. Increased transparency and accountability: A management system can provide clear guidelines and procedures for decision-making and performance evaluation, which can improve transparency, accountability, and organizational governance.5. Enhanced reputation and competitive advantage: A management system can help an organization to build a positive reputation for quality, environmental responsibility, safety, security, and risk management, which can differentiate it from competitors in the marketplace.Implementation of a Management SystemImplementing a management system involves several key steps, including:1. Identification of requirements: The first step in implementing a management system is to identify the specific requirements and objectives of the organization. This may involve conducting a gap analysis to identify areas for improvement and establish performance benchmarks.2. Development of policies and procedures: Once the requirements have been identified, the next step is to develop policies, procedures, and guidelines that define how the management system will operate. This may involve creating documentation, training materials, and communication plans to ensure that all stakeholders are aware of their roles and responsibilities.3. Training and education: Successful implementation of a management system requires ongoing training and education to ensure that employees understand the system and how it impacts their roles and responsibilities. This may involve providing training on quality standards, environmental practices, health and safety procedures, information security protocols, and risk management processes.4. Monitoring and measurement: To ensure the effectiveness of a management system, it is essential to monitor and measure performance against established benchmarks and objectives. This may involve conducting audits, inspections, surveys, and reviews to identify areas for improvement and track progress over time.5. Continuous improvement: A management system should be dynamic and adaptable to changing circumstances, so it is essential to incorporate a process of continuous improvement. This may involve reviewing and updating policies and procedures, conducting regular evaluations, and soliciting feedback from stakeholders to identify opportunities for enhancement.ConclusionIn conclusion, a management system is a critical component of organizational success, providing a structured approach to decision-making, resource allocation, and performance evaluation. By implementing a management system, organizations can improve efficiency, quality, compliance, transparency, and reputation, gaining a competitive advantage in the marketplace. With the right tools, training, and commitment, any organization can establish and maintain a management system that aligns with its goals and objectives, driving sustainable growth and success.。
英语演讲稿-Quality Management
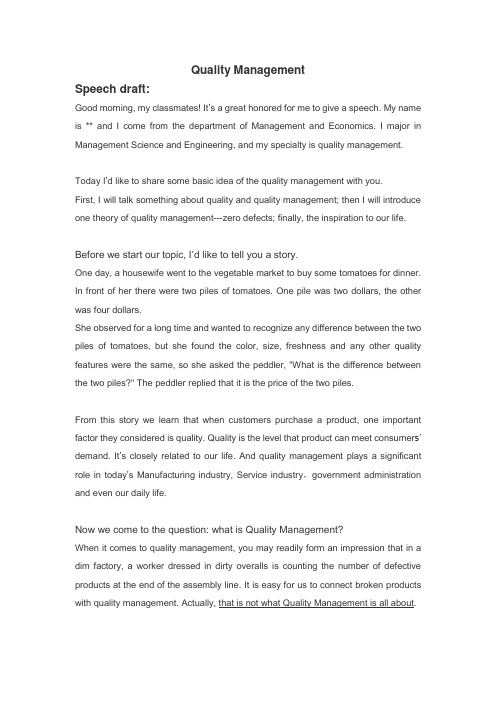
Quality ManagementSpeech draft:Good morning, my classmates! It’s a great honored for me to give a speech. My name is ** and I come from the department of Management and Economics. I major in Management Science and Engineering, and my specialty is quality management.Today I’d like to share some basic idea of the quality management with you.First, I will talk something about quality and quality management; then I will introduce one theory of quality management---zero defects; finally, the inspiration to our life.Before we start our topic, I’d like to tell you a story.One day, a housewife went to the vegetable market to buy some tomatoes for dinner. In front of her there were two piles of tomatoes. One pile was two dollars, the other was four dollars.She observed for a long time and wanted to recognize any difference between the two piles of tomatoes, but she found the color, size, freshness and any other quality features were the same, so she asked the peddler, "What is the difference between the two piles?" The peddler replied that it is the price of the two piles.From this story we learn that when customers purchase a product, one important factor they considered is quality. Quality is the level that product can meet consumer s’demand. It’s closely related to our life. And quality management plays a significant role in today’s Manufacturing industry, Service industry,government administration and even our daily life.Now we come to the question: what is Quality Management?When it comes to quality management, you may readily form an impression that in a dim factory, a worker dressed in dirty overalls is counting the number of defective products at the end of the assembly line. It is easy for us to connect broken productsQuality Management is the process of providing customers with high-quality, satisfactory products. During this process, we do some critical work to make better design and control the product as well as the production process to reduce defective products, which will increase the company’s profits. In addition, Quality Management has an implication that the company should pay close attention to their customer’s need as well as their employees and stakeholders.There are many management methods to help us to carry out the Quality Management process. For example, six sigma management, total quality management, benchmarking, control charts and so on. These methods or tools are based on a lot of statistical knowledge. I’d like to introduce ideas of a more interesting method today.That is ‘zero defects’.Literally, zero defects means a company produces products or services without making any mistake, that is to say, do it right the first time.This method was firstly developed by Mr. Crosby, who once had been a doctor. For some reason he quit his job and became a quality inspector in a factory. During his work, He found that it was worthless to sort out defects from a good one for we couldn’t change the fact that it’s a defective one. And prevention is more important than post supervision. We should utilize control tools or management techniques to do things right at first time.In order to give you a deep understanding of zero defects, let’s take an example.Imagine that you are now a patient and I’m your doctor. Before you taking the surgery, I tell you that: Oh, the surgery is risky, our pass rate is about 99%, and today we have already done 99 successful surgeries. So if you die, that is acceptable, because I’m not God, I’m allowed to make mistakes, I needn’t to do things right every time.If every doctor thinks in that way, I am afraid that no one would dare to go to the hospital. So we shouldn’t take for granted that customers will readily accept our tiny mistakes. What we should do is to stand on the position of our customers to recognize their need and provide them with perfect product. In addition, it tells us that once we strive ourselves to do things right at first time, we can do it.When a company carries out their Zero Defects management, four steps are needed.The first step is to determine the zero defect management objectives, the second is to do a Performance evaluation; next we should establish an appropriate way to feedback information; the last step is to establish a recognition system. If we carry out Zero Defects management, the cost saving will be significant.But, for a company or a person, to achieve Zero Defect is almost impossible. Zero defects philosophy is a state of the ideal. However, in addition to acts of god, there are some things we can control, our attitude, carelessness or diligent. Whether we can do it right does not depend on our ability, but on our mind and the attitude that governs our behavior.So if we firmly believe that 'the first time you can put things right'! ", we can avoid lots of unnecessary errors.Everyone, act now! Do your work right the first time and make efforts to make no mistakes.You will find you are making a big difference!Thank you!。
质量管理体系术语中英文对照

质量管理体系术语中英文对照以下是部分质量管理体系相关的基本术语中英文对照:1.质量管理体系(Quality Management System, QMS)o中文:质量管理体o英文:Quality Management System2.质量管理(Quality Control, QC)o中文:质量管理o英文:Quality Control3.持续改进(Continuous Improvement, CI)o中文:持续改进o英文:Continuous Improvement4.过程方法(Process Approach)o中文:过程方法o英文:Process Approach5.质量方针(Quality Policy)o中文:质量方针o英文:Quality Policy6.质量目标(Quality Objectives)o中文:质量目标o英文:Quality Objectives7.内部审核(Internal Audit)o中文:内部审核o英文:Internal Audit8.纠正措施(Corrective Action)o中文:纠正措施o英文:Corrective Action9.预防措施(Preventive Action)o中文:预防措施o英文:Preventive Action10.顾客满意度(Customer Satisfaction)o中文:顾客满意度o英文:Customer Satisfaction11.供方管理(Supplier Management)o中文:供应商管理o英文:Supplier Management12.产品实现(Product Realization)o中文:产品实现o英文:Product Realization13.设计和开发(Design and Development)o中文:设计与开发o英文:Design and Development14.测量、分析和改进(Measurement, Analysis andImprovement)o中文:测量、分析与改进o英文:Measurement, Analysis and Improvement 以上内容主要参考了ISO 9001:2015质量管理体系标准中的核心概念。
质量管理体系相关方的术语和定义英文版

质量管理体系相关方的术语和定义英文版English: Quality management system (QMS) is a set of processes, policies, and procedures for planning and execution in the core business area of an organization. It involves a systematic management of the activities and resources used to achieve quality objectives. There are several key terms related to QMS that are important for stakeholders to understand. Firstly, "Quality Policy" is a formal statement from management, setting out the organization's approach to quality. It provides a framework for establishing and reviewing quality objectives, in addition to requirements for quality improvement. Secondly, "Quality Objectives" are specific goals that an organization sets to achieve within a specified time frame. These objectives need to be measurable and aligned with the organization's quality policy. Another important term is "Quality Manual," which is a document that defines the QMS of an organization. It outlines the processes, procedures, and responsibilities for ensuring product and service quality. Finally, "Risk-based Thinking" is a term that refers to a proactive and systematic approach to managing risks across all aspects of the QMS.中文翻译: 质量管理体系(QMS)是组织核心业务领域规划和执行的一套过程、政策和程序。
质量管理(原书第7版)英文版教学课件 Chapter 1

commitment to performance excellence
11
Future Influences
❖ Global responsibility ❖ Consumer awareness ❖ Globalization ❖ Increasing rate of change ❖ Wing population ❖ 21st century quality ❖ Innovation
❖ Consumer expectations are high ❖ “We’ve made dependence on the quality of
our technology a part of life” – Joseph Juran
6
Examples of Successful QualityFocused Organizations
12
Quality in Manufacturing
❖ Performance – primary operating characteristics
❖ Features – “bells and whistles”
❖ Reliability – probability of operating for specific time and conditions of use
❖ delivery of ever-improving value to customers and stakeholders, contributing to organizational sustainability,
ISO9000英文版质量管理体系要求

NOTE In this International Standard,the term “product”applies only to the product intended for,or required by,a customer.
Quality management system - Requirement
4 Quality management system
4.1 General requirements The organization shall establish,document,implement and maintain a quality
management system and continually improve its effectiveness in accordance with the requirements of this International Standard.
Quality management system - Requirement
4.2 Documentation requirements
4.2.1 General The quality management system documentation shall include a) Documented statements of a quality policy and quality objectives, b) A quality manual, c) Documented procedures required by this International Standard, d) Documents needed by the organization to ensure the effective planning,and e) Records required by this International Standard(see 4.2.4)
品质管理培训计划英文版

品质管理培训计划英文版IntroductionQuality management is an essential aspect of any organization, as it directly affects the products and services delivered to customers. A well-implemented quality management system can help improve efficiency, reduce waste, and increase customer satisfaction. This training program aims to provide comprehensive knowledge and skills to employees, enabling them to understand the principles and practices of quality management and incorporating them into their daily work.ObjectivesThe main objectives of this training program are to:1. Provide a clear understanding of the principles and concepts of quality management2. Equip employees with practical tools and techniques for implementing quality management in their work3. Develop a mindset of continuous improvement and a commitment to delivering high-quality products and services4. Ensure employees are aware of the importance of quality management in achieving organizational goals and meeting customer expectationsTraining Program OutlineModule 1: Introduction to Quality Management- Understanding the concept of quality and its importance in business- The history and evolution of quality management- The role of quality management in achieving business successModule 2: Quality Management Principles- The principles of Total Quality Management (TQM)- The Deming Cycle (Plan-Do-Check-Act) and its application in quality management- The key principles of ISO 9001 and its relevance to quality managementModule 3: Quality Management Tools and Techniques- Problem-solving techniques: 5 Whys, Pareto Analysis, Fishbone Diagram- Statistical Process Control (SPC) and its application in quality monitoring- Lean, Six Sigma, and other quality improvement methodologiesModule 4: Quality Assurance and Control- Understanding the difference between quality assurance and quality control- The role of standards and procedures in ensuring product and service quality- Implementing quality control measures in different work processesModule 5: Customer Focus and Satisfaction- Understanding customer expectations and needs- The importance of customer feedback in improving quality- Developing a customer-centric approach to quality managementModule 6: Continuous Improvement- The concept of Kaizen and its application in quality management- Identifying and eliminating waste in work processes- Creating a culture of continuous improvement in the organizationModule 7: Leadership and Quality Management- The role of leaders in promoting a quality-focused culture- Leading by example and creating a quality-driven work environment- Developing and empowering employees to contribute to quality improvement Module 8: Implementing a Quality Management System- The steps and considerations for implementing a quality management system- The role of documentation, training, and communication in successful implementation - Measuring and evaluating the effectiveness of the quality management system Training MethodsTo ensure the effectiveness of the training program, a variety of methods will be used, including:- Lectures and presentations to introduce key concepts and principles- Case studies and group discussions to apply learning to real-life situations- Practical exercises and simulations to develop problem-solving and quality improvement skills- Interactive workshops to encourage active participation and collaboration among employees- Continuous assessment and feedback to monitor learning progress and address any gaps Training ScheduleThe training program will be conducted over a period of 12 weeks, with each module scheduled for one week. The sessions will be held twice a week, for a total of 24 sessions, each lasting 2 hours. This schedule allows for in-depth coverage of each topic while ensuring minimal disruption to employees' everyday work.Evaluation and CertificationAt the end of the training program, participants will be evaluated through a combination of quizzes, assignments, and a final examination to assess their understanding and application of quality management principles. Those who successfully complete the program will receive a certificate of completion, recognizing their commitment to continuous learning and quality improvement.ConclusionThe implementation of a comprehensive quality management training program is crucial for enhancing the effectiveness and efficiency of an organization. By equipping employees with the knowledge and skills necessary to understand and implement quality management principles, organizations can improve their products and services, gain a competitive edge, and ultimately achieve greater success. This training program aims to empower employees to become ambassadors of quality within their respective departments and contribute to the overall success of the organization.。
- 1、下载文档前请自行甄别文档内容的完整性,平台不提供额外的编辑、内容补充、找答案等附加服务。
- 2、"仅部分预览"的文档,不可在线预览部分如存在完整性等问题,可反馈申请退款(可完整预览的文档不适用该条件!)。
- 3、如文档侵犯您的权益,请联系客服反馈,我们会尽快为您处理(人工客服工作时间:9:00-18:30)。
PMP Preparation Training
Quality Management
Chapter 8
Quality Management
Processes necessary to ensure that the project will satisfy customer requirements
Outputs
• Quality management plan • Operational definitions • Checklists • Inputs to other processes
Quality Planning
Inputs
• Quality policy – “Overall intentions and direction of an organization with regard to quality as formally expressed by top management”
• Prevention over inspection – The cost of avoiding mistakes is much less than the cost of correcting them
• Management responsibility – Success requires participation of all members of the team, but it is the responsibility of management to provide resources needed
be borne by the performing organization
• Deming
• Japanese • Juran • Crosby
• Theory X • Theory Y
Philosophies
Leadership, long-term company position; continuous improvement; participatory; zero defects Similar to Deming Decrease cost of quality Decrease cost of quality; authoritarian; zero defects Workers lazy, motivated by money Workers good and trustworthy
• Delivery of both high quality and high grade of product • Quality is planned in, not inspected in • Investments in product quality improvement must often
• Processes within phases – Plan/Do/Check/Act cycle
Process Improvement
Act by correcting
Plan for Improvement
Process Improvement
Check the results
Do on a small scale
Quality Planning Quality Assurance Quality Control
Quality Management
Planning
Executing
Controlling
8.1 Quality Planning
8.2 Quality Assurance
8.3 Quality Control
ISO 9000
• ISO9000
– ISO9001 – Design/Develop/Produce/Install & Service – ISO9002 – Produce & Install – ISO9003 – Inspection & Testing
• Cost
– Prevention costs: Training, surveys, implementation of quality system
Project Management & Quality Management
• Customer satisfaction – Understanding, managing, and influencing needs so that customer expectations are met or exceeded
ቤተ መጻሕፍቲ ባይዱ
Quality Management
• Addresses both the management of the project and of the product of the project
• Improves project management as well as the quality of the product
Quality Planning
Identifying the quality standards that are relevant to the project and determining how to meet them
Quality is planned in – NOT inspected in
Quality Planning
Tools & Techniques
• Benefit/cost analysis • Benchmarking • Flowcharts • Design of experiments • Cost of quality
Inputs
• Quality policy • Scope statement • Product description • Standards & regulations • Other process outputs