加热炉控制技术的回顾与展望
加热炉燃烧控制技术的发展现状及方向
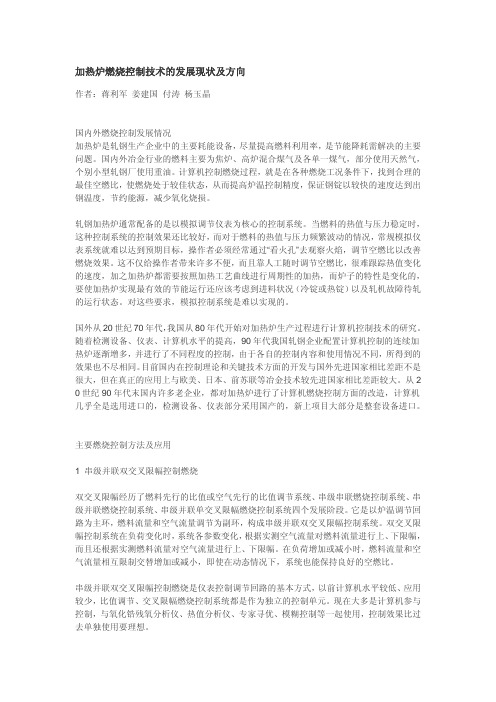
加热炉燃烧控制技术的发展现状及方向作者:蒋利军姜建国付涛杨玉晶国内外燃烧控制发展情况加热炉是轧钢生产企业中的主要耗能设备,尽量提高燃料利用率,是节能降耗需解决的主要问题。
国内外冶金行业的燃料主要为焦炉、高炉混合煤气及各单一煤气,部分使用天然气,个别小型轧钢厂使用重油。
计算机控制燃烧过程,就是在各种燃烧工况条件下,找到合理的最佳空燃比,使燃烧处于较佳状态,从而提高炉温控制精度,保证钢锭以较快的速度达到出钢温度,节约能源,减少氧化烧损。
轧钢加热炉通常配备的是以模拟调节仪表为核心的控制系统。
当燃料的热值与压力稳定时,这种控制系统的控制效果还比较好,而对于燃料的热值与压力频繁波动的情况,常规模拟仪表系统就难以达到预期目标,操作者必须经常通过“看火孔”去观察火焰,调节空燃比以改善燃烧效果。
这不仅给操作者带来许多不便,而且靠人工随时调节空燃比,很难跟踪热值变化的速度,加之加热炉都需要按照加热工艺曲线进行周期性的加热,而炉子的特性是变化的,要使加热炉实现最有效的节能运行还应该考虑到进料状况(冷锭或热锭)以及轧机故障待轧的运行状态。
对这些要求,模拟控制系统是难以实现的。
国外从20世纪70年代,我国从80年代开始对加热炉生产过程进行计算机控制技术的研究。
随着检测设备、仪表、计算机水平的提高,90年代我国轧钢企业配置计算机控制的连续加热炉逐渐增多,并进行了不同程度的控制,由于各自的控制内容和使用情况不同,所得到的效果也不尽相同。
目前国内在控制理论和关键技术方面的开发与国外先进国家相比差距不是很大,但在真正的应用上与欧美、日本、前苏联等冶金技术较先进国家相比差距较大。
从2 0世纪90年代末国内许多老企业,都对加热炉进行了计算机燃烧控制方面的改造,计算机几乎全是选用进口的,检测设备、仪表部分采用国产的,新上项目大部分是整套设备进口。
主要燃烧控制方法及应用1 串级并联双交叉限幅控制燃烧双交叉限幅经历了燃料先行的比值或空气先行的比值调节系统、串级串联燃烧控制系统、串级并联燃烧控制系统、串级并联单交叉限幅燃烧控制系统四个发展阶段。
2024年加热炉市场前景分析

2024年加热炉市场前景分析摘要本文通过对加热炉市场的市场规模、发展趋势、竞争格局等方面进行分析,以及对当前市场状况的调研,对加热炉市场的前景进行了评估。
研究表明,加热炉市场具有较大的发展潜力,但也面临一些挑战。
因此,在市场竞争中,企业需要应对市场变化,不断创新,以保持竞争优势。
1. 引言加热炉是一种用于加热物体的设备,广泛应用于冶金、化工、电力、建筑等行业。
随着工业生产的发展和技术的进步,加热炉市场呈现出良好的增长势头。
本文将对加热炉市场的前景进行深入的分析和评估。
2. 市场规模分析根据市场调研数据,加热炉市场在过去几年呈现出稳步增长的趋势。
据统计,2019年加热炉市场的规模达到500亿元,预计到2025年有望达到800亿元,年平均增长率约为6%。
这一增长趋势主要受到以下几个因素的影响:•工业生产的不断发展,特别是制造业的快速增长,促进了加热炉市场的需求。
•新兴行业的兴起,如新能源汽车、智能制造等,对加热炉市场的需求也在逐渐增加。
•技术创新的推动,新型加热炉设备的出现为市场带来了更多的机遇。
3. 发展趋势分析加热炉市场在未来几年将面临一些发展趋势和机遇:3.1 环保节能成为市场主流随着环境保护意识的增强和环保法规的不断加强,加热炉市场将更加注重节能环保。
新型的绿色加热炉设备将成为市场的主流产品,满足市场对环保节能的需求。
3.2 5G技术加速应用5G技术的发展将极大地推动智能制造和工业互联网的发展,加热炉市场也将受益于此。
通过应用5G技术,加热炉设备可以实现更高效的运行和更精细的控制,提高生产效率和产品质量。
3.3 自动化生产取代传统加热方式随着自动化技术的不断成熟和应用,传统的人工操作加热方式将被自动化生产所取代。
自动化加热炉设备具有高效、精准的优势,可以实现连续生产,提高生产效率和降低人工成本。
4. 竞争格局分析加热炉市场竞争激烈,主要竞争者包括国内外一些大型企业和中小型企业。
竞争格局主要表现为以下几个方面:•技术创新竞争:企业通过技术研发和创新来提高产品的性能和竞争力。
管式加热炉技术的现状、问题和发展方向

管式加热炉技术的现状、问题和发展方向管式加热炉是由排列成管状的焊缝管依次连接而成,是混合、熔炼或加热液体或气体、乳化物或固体悬液的常用设备。
管式加热炉具有通用性强、便于操作、易于调节等优点。
管式加热炉技术发展迅速,它的特点是用最低的熔炉量和热投入量来实现最好的熔炼效果。
然而,过去几十年来,管式加热炉使用范围受到一定限制,许多现有的设备结构较为粗糙,无法满足复杂的工业应用需求,容易发生熔炉破裂,热能利用率偏低等问题。
因此,管式加热炉技术发展存在一些潜在风险和挑战。
研究者正在尝试采用现代技术设备进一步完善管式加热炉技术,以提高熔炉性能,简化熔炉的操作,降低内部熔合点的温度差,并研制出能有效减少熔炉散热损失的加热炉。
在未来,管式加热炉技术将有望在冶金工业、石油化工、食品加工和航空航天等行业中得到广泛应用,研究者将继续研究加热炉的不同结构,研发更加高效率、安全性能更优秀的新型加热炉,促进管式加热炉技术在未来的发展。
Tube heating furnace is a commonly used equipment for mixing, melting or heating liquids or gases, emulsions or solid slurries, which is composed of welded tubes arranged in the form of pipes. Tube heating furnaces have the advantages of strong generality, easy operation and easy adjustment.The technology of tube heating furnace has developed rapidly, which is characterized by achieving the best melting effect with the lowest furnace capacity and heat input. However, in the past few decades, the application range of tube heating furnace has been limited, and many existingequipment structures are rough, which can not meet the complex industrial application requirements, and are easy to cause furnace rupture, low thermal energy utilization, etc.Therefore, there are some potential risks and challenges in the development of tube heating furnace technology. Researchers are trying to use modern equipment to further improve the technology of tube heating furnace, in order to improve the performance of the furnace, simplify the operation of the furnace, reduce the temperature differenceof the internal melting point, and develop heating furnaces that can effectively reduce the heat loss of the furnace.In the future, tube heating furnace technology is expected to be widely used in metallurgical industry, petrochemical industry, food processing and aerospace industry, researchers will continue to research the different structures of heating furnaces, develop more efficient and safer new heating furnaces, and promote the development of tube heating furnace technology in the future.。
炉修的工作总结(精选5篇)

炉修的工作总结(精选5篇)炉修的工作总结篇1炉修工作总结一、工作回顾在过去的一个月里,我们炉修团队在面临诸多挑战的情况下,成功地完成了任务,并取得了一定的成绩。
以下是对我们工作的一些回顾:1.任务完成情况:在本次炉修工作中,我们的主要任务是修复一台加热炉,并在规定时间内完成了所有维修工作。
我们的团队成功地解决了加热炉的各种问题,使其恢复了正常工作状态。
2.目标实现情况:我们的工作目标是确保加热炉在规定时间内恢复正常工作。
为了实现这一目标,我们制定了详细的计划,并采取了有效的措施。
最终,我们的工作目标得以顺利实现。
3.重点工作评价:在炉修工作中,我们重点关注了加热炉的维修质量和效率。
通过有效的沟通和协作,我们成功地确保了维修工作的顺利进行,并达到了预期的目标。
二、工作亮点在本次工作中,我们取得了一些工作亮点,以下是一些主要的亮点:1.团队协作:我们炉修团队在工作中展现出了高度的团队协作精神。
通过有效的沟通和协作,我们成功地完成了各项任务。
2.技术创新:在炉修工作中,我们团队成员提出了一些技术创新,并成功地应用到了实际工作中。
这些技术创新有效地提高了我们的工作效率和维修质量。
3.客户满意度:我们的工作重点在于满足客户需求,提高客户满意度。
通过本次炉修工作,客户对我们的工作给予了高度评价,并表示会继续与我们合作。
三、工作不足在本次工作中,我们也发现了一些不足之处,主要表现在:1.沟通不够顺畅:在工作中,我们发现沟通存在一些问题,有时会导致工作进度受阻。
为了改善这种情况,我们需要加强团队沟通,确保信息传递的畅通和准确。
2.细节处理不当:在工作中,我们有时会忽略一些细节问题,这可能会影响到整个维修工作。
为了提高工作质量,我们需要更加注重细节处理,加强对细节的把控。
四、未来展望在未来的工作中,我们将继续发扬优点,克服不足,并加强以下几个方面的工作:1.提高沟通能力:我们将加强团队沟通,提高信息传递的效率和准确性。
加热管道炉发展历程和未来预测三
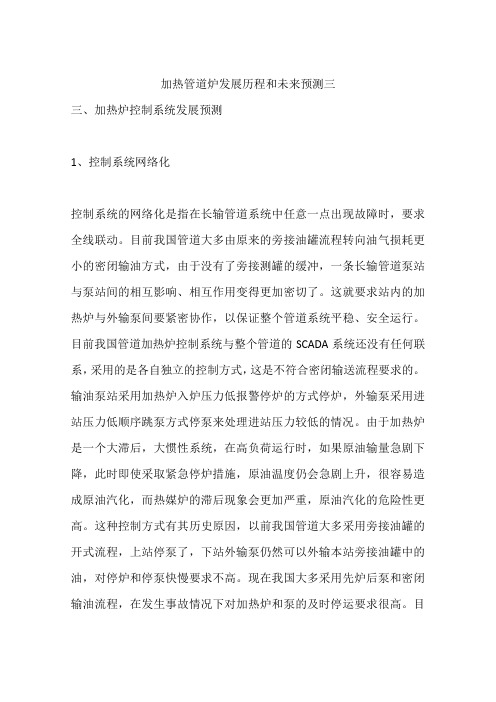
加热管道炉发展历程和未来预测三三、加热炉控制系统发展预测1、控制系统网络化控制系统的网络化是指在长输管道系统中任意一点出现故障时,要求全线联动。
目前我国管道大多由原来的旁接油罐流程转向油气损耗更小的密闭输油方式,由于没有了旁接测罐的缓冲,一条长输管道泵站与泵站间的相互影响、相互作用变得更加密切了。
这就要求站内的加热炉与外输泵间要紧密协作,以保证整个管道系统平稳、安全运行。
目前我国管道加热炉控制系统与整个管道的SCADA系统还没有任何联系,采用的是各自独立的控制方式,这是不符合密闭输送流程要求的。
输油泵站采用加热炉入炉压力低报警停炉的方式停炉,外输泵采用进站压力低顺序跳泵方式停泵来处理进站压力较低的情况。
由于加热炉是一个大滞后,大惯性系统,在高负荷运行时,如果原油输量急剧下降,此时即使采取紧急停炉措施,原油温度仍会急剧上升,很容易造成原油汽化,而热媒炉的滞后现象会更加严重,原油汽化的危险性更高。
这种控制方式有其历史原因,以前我国管道大多采用旁接油罐的开式流程,上站停泵了,下站外输泵仍然可以外输本站旁接油罐中的油,对停炉和停泵快慢要求不高。
现在我国大多采用先炉后泵和密闭输油流程,在发生事故情况下对加热炉和泵的及时停运要求很高。
目前,我国很多长输管道企业仍然没有重视这个问题,加热炉控制还是独立的,存在着在发生事故情况下引发其他大事故的安全隐患。
另外,由于很多管道埋设时间已有10年以上,老管道不同程度出现腐蚀穿孔,且目前管道盗油现象严重。
频繁的停输已经严重干扰了管道系统的平稳运行,但这也促使管道检漏技术的水平不断提高。
管道检漏方法已由原来采用负压力波、动态平衡方法等有损检测逐步过渡到声波无损检测,最近出现的光纤分布式检测技术(利用沿管道同轴埋设的光纤为传感器)已经可以定位出在管道附近动土、行走的行为,但其价格昂贵,目前还没有在我国管道上应用的报道。
检测技术的完善使得把全线泵站的加热炉控制系统纳入整个管道SCADA系统变得非常有意义。
加热炉应用现状及发展方向

加热炉应用现状及发展方向随着现代工业的发展,加热炉已成为工业热处理、烧结、晶体生长、玻璃加工、电子设备制造等各个领域的重要设备。
加热炉在温度控制、加热传热、反应控制、环境保护等方面的技术不断更新,同时应用范围也不断拓展。
本文将探讨加热炉应用现状及未来的发展方向。
一、加热炉应用现状1. 热处理加热炉是热处理加工中最常见的设备之一,热处理可通过高温改变物质的组织结构和性质,使其获得更高的强度、硬度、韧性等物理性能。
加热炉在冶金、机械制造、汽车等行业中被广泛运用。
2. 烧结烧结是将粉末材料在高温下烧结成实体的工艺过程。
加热炉可以控制材料的温度,使粉末在瞬间熔化成实体。
烧结设备还可以精确控制热循环、氧化还原等过程中制品的循环,从而制造出高质量的产品。
3. 玻璃加工玻璃材料具有优异的物理性质,但其制造过程较为复杂。
加热炉可以将玻璃材料在高温下加热、变形,从而达到精确的成型目的。
同时,加热炉可以提高玻璃的硬度、韧性等性质,为制造高质量玻璃产品提供保障。
4. 电子设备制造现代电子设备需要制造高精度、高性能的晶体管芯片等器件。
这些器件的制造过程需要在极高的温度下进行,而加热炉恰好可以提供这些高温环境。
加热炉还可以控制材料的温度和气氛,在控制反应过程的同时确保高品质的器件制品。
5. 其他应用领域加热炉在探测、生物制药、材料研究等多个领域中都能发挥重要作用。
例如,在生物制药过程中,加热炉可以提供精确的制药环境,保证生产过程的稳定性和产品的高质量。
二、加热炉发展方向1. 低碳经济加热炉正在朝着低碳经济的方向发展。
随着全球环境问题的日益突出,炉内燃烧产生的二氧化碳等污染物已受到广泛关注。
因此,许多加热炉制造商正在推出新型节能低碳化的加热炉,从而满足低碳经济的需求。
这些新型加热炉采用新技术,如烟气再循环、高效燃烧、废气回收等,进一步减少炉内环境对环境的影响。
2. 智能制造随着“工业4.0”等概念的普及,加热炉制造商正在致力于推行智能化制造。
加热炉控温技术影响因素分析及改进

加热炉控温技术影响因素分析及改进1. 引言1.1 背景介绍现代工业生产中,加热炉一直扮演着重要的角色,其控温技术直接影响着生产过程中的效率和质量。
在许多生产工艺中,需要对加热炉内部的温度进行精准控制,以确保产品的质量和稳定性。
由于加热炉控温技术受到多种因素的影响,其控制精度和稳定性往往会受到挑战。
加热炉控温技术的影响因素包括温度传感器的性能、加热炉的设计结构、控制系统参数的设定等。
这些因素相互作用,会直接影响到加热炉的控温效果。
对于加热炉控温技术影响因素的分析和改进至关重要。
本文将就加热炉控温技术的影响因素进行深入分析,并针对其中存在的问题提出改进措施。
通过对加热炉控温技术的影响因素进行全面研究,可以提高加热炉控温的精度和稳定性,进而提高生产效率和产品质量。
【200字】1.2 研究意义研究加热炉控温技术的影响因素具有重要的理论价值和实际意义。
加热炉在工业生产中扮演着至关重要的角色,控温技术的稳定性和精度直接影响产品的质量和生产效率。
通过对加热炉控温技术的影响因素进行分析,可以深入了解控温过程中的关键问题,为提高加热炉的控温能力提供理论支持。
加热炉控温技术的研究还可以促进工业生产的现代化和智能化进程。
随着科技的不断发展,工业生产对控温技术的要求也越来越高,需要更高精度、更稳定的控温系统来保证产品质量和生产效率。
通过对加热炉控温技术的研究,可以推动工业生产设备向智能化和自动化方向发展,提高生产效率和降低生产成本。
深入研究加热炉控温技术的影响因素,分析控温过程中的关键问题,提出改进措施,对于推动工业生产的现代化和智能化进程具有重要意义。
这也是当前工程技术研究中一个具有挑战性和前景广阔的课题。
【研究意义完】2. 正文2.1 加热炉控温技术影响因素分析加热炉控温技术的稳定性和准确性对生产过程至关重要。
影响加热炉控温技术的因素有很多,包括温度传感器性能、加热炉设计结构、控制系统参数设定等。
温度传感器的性能直接影响到控温的准确性。
加热管道炉发展历程和未来预测一

加热管道炉发展历程和未来预测一我国大型输油管道加热炉控制系统经历了三代发展过程,从开始的完全人工手动控制到多回路控制器自动控制,再到现在广泛采用的PLC 与工控机结合的自动控制。
随着现代控制理论、智能控制理论和图像处理方法的不断成熟和工业化,我国加热炉控制系统将在容错控制能力、故障诊断能力、系统集成分析能力、智能化、安全性、高效性、风险评估能力等方面不断提高和发展,从而使加热炉各项功能更趋完善。
一、我国管道加热炉发展历程由于国产原油具有粘度大、含蜡高、凝点高的特点,管道加热炉广泛应用于我国大型输油管道系统统中。
从我国管道加热炉系统建立至今,其发展过程可以归结为三代,即人工手动控制、多回路控制器自动控制、PLC与工控机结合的自动控制。
第一代加热炉称为方箱炉,原油管道直接从加热炉炉膛通过,采用火把人工点火,当时没有火焰监视设备,操作工人员能通过炉体前部的观察孔查看炉膛的燃油火焰情况。
由于燃油燃烧前没有雾化处理,因而火嘴容易结焦,很容易造成灭火。
炉膛火灭后,如果不采取手工断油,燃油仍然向炉膛中进油。
因此操作人员要经常巡检,可见加热炉的运行安全性很差。
20世纪80年代末,我国第二代加热炉实现了加热炉从手动到自动的飞跃。
以国产加热炉为例,DDZII、DDZIII仪表被广泛应用于加热炉,除了炉本体、燃油系统、助燃风系统外,又增加了热媒系统、冷却水系统、雾化风系统、原油/热媒换热系统、烟气换热器等设备;在控制上增加了温度、压力、氧量等参数的采集和控制。
控制系统采用多回路控制器(MiconP-200),从点炉、火焰监视、炉温调节、停炉、原油温度等方面都实现了自动控制。
控制系统功能非常完善,而且原油管道不再进入炉膛,大大提高了加热炉安全性。
这也是首次把串级控制、比例控制等经典PID控制和双交叉限幅控制思想引入热媒炉的控制,是我国加热炉自动动控制的一次革命。
在20世纪90年代中期,由于仪器仪表老化和DDZIII仪表的零点漂移大等缺点,影响了MiconP-200控制系统自动控制,其安全性高的特点也恰好成了加炉运行的瓶颈,后来许多泵站的仪表维修人员逐渐屏蔽了一些闭锁,使加热炉能勉强的维持半自动运行(风油配比固化在控制系统中)。
板坯加热炉控制技术现状和发展趋势
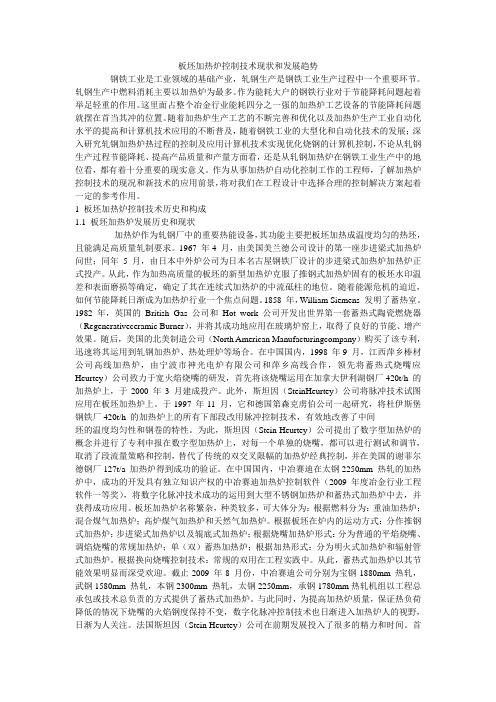
板坯加热炉控制技术现状和发展趋势钢铁工业是工业领域的基础产业,轧钢生产是钢铁工业生产过程中一个重要环节。
轧钢生产中燃料消耗主要以加热炉为最多。
作为能耗大户的钢铁行业对于节能降耗问题起着举足轻重的作用。
这里面占整个冶金行业能耗四分之一强的加热炉工艺设备的节能降耗问题就摆在首当其冲的位置。
随着加热炉生产工艺的不断完善和优化以及加热炉生产工业自动化水平的提高和计算机技术应用的不断普及,随着钢铁工业的大型化和自动化技术的发展;深入研究轧钢加热炉热过程的控制及应用计算机技术实现优化烧钢的计算机控制,不论从轧钢生产过程节能降耗、提高产品质量和产量方面看,还是从轧钢加热炉在钢铁工业生产中的地位看,都有着十分重要的现实意义。
作为从事加热炉自动化控制工作的工程师,了解加热炉控制技术的现况和新技术的应用前景,将对我们在工程设计中选择合理的控制解决方案起着一定的参考作用。
1 板坯加热炉控制技术历史和构成1.1 板坯加热炉发展历史和现状加热炉作为轧钢厂中的重要热能设备,其功能主要把板坯加热成温度均匀的热坯,且能满足高质量轧制要求。
1967 年4 月,由美国美兰德公司设计的第一座步进梁式加热炉问世;同年5 月,由日本中外炉公司为日本名古屋钢铁厂设计的步进梁式加热炉加热炉正式投产。
从此,作为加热高质量的板坯的新型加热炉克服了推钢式加热炉固有的板坯水印温差和表面磨损等确定,确定了其在连续式加热炉的中流砥柱的地位。
随着能源危机的迫近,如何节能降耗日渐成为加热炉行业一个焦点问题。
1858 年,William Siemens 发明了蓄热室。
1982年,英国的British Gas 公司和Hot work 公司开发出世界第一套蓄热式陶瓷燃烧器(Regenerativeceramic Burner),并将其成功地应用在玻璃炉窑上,取得了良好的节能、增产效果。
随后,美国的北美制造公司(North American Manufacturingcompany)购买了该专利,迅速将其运用到轧钢加热炉、热处理炉等场合。
加热炉电气自动控制技术发展探讨

加热炉电气自动控制技术发展探讨随着工业生产规模的不断扩大,加热炉控制技术要求也变得愈来愈高,这为加热炉电气自动控制技术提供了发展空间。
基于此,本文对加热炉电子自动控制技术进行了探讨,并提出了相关观点,以供参考。
标签:加热炉;自动化;电气;技术1 加热炉概述在现代工业生产过程中,加热炉是不可或缺的加工设备,在很多行业当中都有着广泛的应用。
加热炉主要包括连续加热炉与室式加热炉。
连续加热炉运行过程中,料坯会在炉内根据轧制的节奏进行连续运动,炉气也会在炉内进行连续流动[1]。
当炉料断面尺寸、产量机类型确定时,连续加热炉各部分温度并不会随时间变化而变化,只会沿长度方向发生变化;金属料的温度也不会随着时间变化而出现变化,仅沿长度方向发生变化。
室式加热炉主要用于金属坯加热或锻压前加热。
室式加热炉物料加热时并不会移动,并且炉内不分段,需保持炉内各处温度均匀。
对于部分大型钢锭加热则采取周期性的加热方式。
多数加热炉都属于高耗能窑炉,资源消耗较多,并且加热炉产生的烟气会散发出大量热量,会影响热能利用率。
因此,在加热炉应用过程中需采取一定节能措施来控制能源消耗,从而提升热能利用率,降低使用成本。
2 加热炉电气自动控制技术瓶颈分析以往加热炉控制偏重于常规燃烧控制。
一般会根据加热炉实际运行状况,采取针对性措施让加热炉始终维持稳定的工况,从而实现最佳燃烧,达到节能减耗的目的。
随着计算机技术及电气技术的不断成熟,为加热炉温控提供了极大的技术支持。
以计算机技术来控制加热炉各段炉温,可有效提升控制精度,并可得到较为理想的物料温度,在实现最佳燃烧的同时,也能保证加热炉安全性。
正是由于计算机技术与电气技术的不断发展,让加热炉自动化控制得以实现。
相对于欧美发达国家而言,我国加热炉电气自动控制技术起步较晚,并且普及面较窄。
部分工业生产企业尽管配备了较为先进的计算机硬件设施,但计算机主要用于简单的PID调节,只是用来替代普通测量仪表,并未将计算机的强大功能充分发挥出来。
板坯加热炉控制技术现状和发展

板坯加热炉控制技术现状和发展
国内钢板坯加热炉控制技术现状和发展
一、控制技术的现状
1、燃烧控制
1.1、目前采用最多的控制方式是门控式天然气调节,通过调节燃料天
然气流量,来实现火焰的多段控制和温度的平稳调节。
1.2、近年来,气体分子激光光谱技术也被广泛应用,激光光谱实时监
测火焰照度,及时能调整火焰的位置和强度,提高燃烧效率。
2、炉温控制
2.1、机械式温控仪,采用磁性材料和热敏电阻,实时定位探头,传感、比较、控制、调节,来控制炉子的温度。
2.2、微机温度控制,温度控制采用传感器,利用程序控制器检测温度,设置报警阈值,进行温度控制和调节。
三、发展趋势
1、加热速度控制,基于随着时间变化温度再次调整,逻辑运算控制技术,改进温度的稳定性,增加加热炉的质量和流程的可靠性。
2、智能控制技术,自适应控制技术克服了现有系统对环境变化敏感,
拥有改进热量优化、温度变化、熔渣分析等功能,达到更好的控制效
果。
3、熔化行为模型,模拟复杂的熔合过程,模拟不同温度、不同参数的影响,进行智能熔合,从而提高生产效率。
4、云计算技术,通过数据采集、传输、编译等技术,获取实时的工艺数据,实现远程控制,有效减少沉降现象。
总结:目前国内钢板坯加热炉控制技术有燃烧控制以及炉温控制,包括采用最多的控制方式:门控式天然气调节、利用激光光谱实时监测火焰照度、机械式温控仪、微机温度控制,以及随着时间变化温度再次调整,智能控制技术,熔化行为模型及云计算技术等。
由此可见,国内钢板坯加热炉控制技术不断发展,性能不断提高,也越来越趋向智能化,实现控制精细化.。
钢厂加热炉年度总结(3篇)
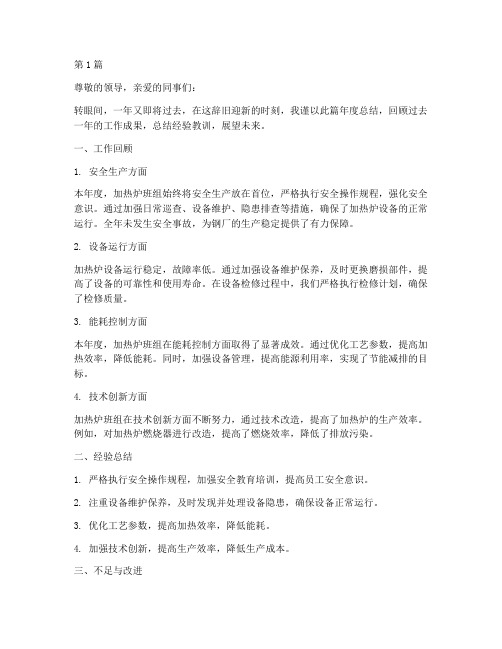
第1篇尊敬的领导,亲爱的同事们:转眼间,一年又即将过去,在这辞旧迎新的时刻,我谨以此篇年度总结,回顾过去一年的工作成果,总结经验教训,展望未来。
一、工作回顾1. 安全生产方面本年度,加热炉班组始终将安全生产放在首位,严格执行安全操作规程,强化安全意识。
通过加强日常巡查、设备维护、隐患排查等措施,确保了加热炉设备的正常运行。
全年未发生安全事故,为钢厂的生产稳定提供了有力保障。
2. 设备运行方面加热炉设备运行稳定,故障率低。
通过加强设备维护保养,及时更换磨损部件,提高了设备的可靠性和使用寿命。
在设备检修过程中,我们严格执行检修计划,确保了检修质量。
3. 能耗控制方面本年度,加热炉班组在能耗控制方面取得了显著成效。
通过优化工艺参数,提高加热效率,降低能耗。
同时,加强设备管理,提高能源利用率,实现了节能减排的目标。
4. 技术创新方面加热炉班组在技术创新方面不断努力,通过技术改造,提高了加热炉的生产效率。
例如,对加热炉燃烧器进行改造,提高了燃烧效率,降低了排放污染。
二、经验总结1. 严格执行安全操作规程,加强安全教育培训,提高员工安全意识。
2. 注重设备维护保养,及时发现并处理设备隐患,确保设备正常运行。
3. 优化工艺参数,提高加热效率,降低能耗。
4. 加强技术创新,提高生产效率,降低生产成本。
三、不足与改进1. 在设备维护方面,部分员工对设备原理和操作规程掌握不够熟练,导致设备故障处理不及时。
针对这一问题,我们将加强员工培训,提高员工的业务水平。
2. 在技术创新方面,我们还需进一步加大投入,提高技术创新能力。
在今后的工作中,我们将积极学习新技术、新工艺,提高加热炉的生产效率。
四、展望未来新的一年,我们将继续努力,紧紧围绕安全生产、设备运行、能耗控制、技术创新等方面,不断提高加热炉的生产水平。
具体措施如下:1. 加强安全生产管理,提高员工安全意识,确保全年无安全事故。
2. 优化设备维护保养制度,提高设备运行效率。
板坯加热炉控制技术现状和发展

板坯加热炉控制技术现状和发展
板坯加热炉是一种重要的金属冶炼装备,其在冶炼过程中承担着重要的作用。
板坯加热炉控制技术是控制板坯加热炉工作温度、耗时和升温合理衰减的重要技术手段。
现阶段,板坯加热炉控制技术大多存在一些问题,主要表现在控制精度较低、温度控制不准确等方面,影响了冶炼的质量和产量,因此需要进行技术改进和升级。
板坯加热炉控制技术主要由控制系统、温度传感器、温度调节器等组成,通过温度检测、计算机参数调整、数字控制器等来控制板坯加热炉的温度和计时。
热电偶传感器是板坯加热炉的温度检测的重要手段,可以快速准确地测量板坯的温度。
现代控制系统大多使用进口的控制器,具有自动保护、负荷补偿和信号稳定的特点,避免了因温度波动对制品质量的影响。
此外,近年来板坯加热炉控制技术还得到了新的发展,越来越多地开发应用了计算机辅助设计技术和高科技产品。
计算机辅助设计技术可以精确模拟不同参数下的加热炉温度变化,实现更精确的控制;而高科技产品如多参数控制器,可以同时监测、控制多个参数,大大提高了控制精度。
另外,可视化操作系统也已经兴起,其可以为操作者提供一个逼真的仿真环境,以及及时反馈的状态报告,进而实现对板坯加热炉的及时及准确控制,可以说可视化操作系统对提高板坯加热炉控制的精度有着重要的意义。
总的来说,板坯加热炉控制技术具有广泛的运用前景,同时也需
要进行持续的技术改进,以期望能够达到更高的控制精度,为金属冶炼行业带来更优质的产品。
油田用加热炉技术现状与发展方向

油田用加热炉技术现状与发展方向油田用加热炉技术现状与发展方向油田用加热炉是油田勘探开发中的重要设备之一,尤其是在我国东部油田大面积进入高含水期及稠油和天然气的开发,加热炉显得更为重要。
随着油气田勘探开发面积的增大、开发难度增大,油田用加热炉的数量越来越多。
截至2005年,中石油油田用加热炉在用数量18460台。
加热炉是油田的主要能耗设备,中石油油田用加热炉每年能耗总量折合成原油约170多万吨,耗能十分惊人。
目前,油田用加热炉主要存在设备老化(平均新度系数0.41)、小型加热炉较多、效率偏低、燃烧不充分、炉内腐蚀结垢等问题。
关注油田用加热炉技术和发展对安全生产、节能和提高生产效率有着重要的意义。
加热炉的结构形式与技术分析1.管式加热炉管式加热炉的火焰直接加热炉管中的生产介质,加热温差大,温升快,允许介质压力高,单台功率可以很大,能以较小的换热面积获得较大的加热功率;但在加热原油和易结垢介质时,管壁结垢快,严重影响换热,且结垢不均匀,会导致管壁局部过热、失效等,这样可能引起爆炸事故。
2.火筒式加热炉燃烧的热量直接通过火筒加热炉壳内的生产介质。
与管式加热炉相比,火筒结垢的敏感性低、对换热影响不太显著。
但是被加热的生产介质在炉壳内流速缓慢,结构件上仍然容易结垢。
因此,火筒式加热炉一般不用于加热易结垢生产介质,如稠油、三次采油污水等。
上述加热炉结构简单,耗材少、一次性投资成本低,最大的隐患就是燃烧筒与生产介质直接接触。
3.水套加热炉水套加热炉与火筒式加热炉的不同之处在于炉壳内与火筒接触的介质不是生产介质而是水,火筒加热水,炉壳内增加了盘管,通过盘管的生产介质由水加热。
其优点就是避免或减轻了火筒的结垢和腐蚀,更主要的是火筒不直接与生产介质接触,安全性好。
近年来,水套加热炉被广泛应用于油田生产。
但水套加热炉传热效率偏低、结构复杂、炉体钢耗量大,另外运行中易失水,需要经常补水。
4.相变加热炉相变加热炉是近年来研制的一种新型加热炉,主体结构包括火筒、炉体(蒸汽发生器)和换热盘管。
工业加热炉发展现状及未来趋势分析

工业加热炉发展现状及未来趋势分析摘要:工业加热炉是工业生产中常用的设备之一,其在矿石冶炼、金属加工、化工生产等领域起着重要的作用。
本文通过对工业加热炉的现状进行分析,揭示了工业加热炉存在的问题,并探讨了未来发展的趋势。
一、工业加热炉的现状1. 基本情况工业加热炉是一种将能源转化为热能,并通过传导、对流或辐射方式将热量传递给物体以实现加热的设备。
目前,工业加热炉的种类繁多,包括电阻炉、感应炉、燃烧炉等。
这些加热炉广泛应用于冶金、化工、建材等行业的生产过程中。
2. 存在问题虽然工业加热炉在工业生产中具有不可替代的作用,但也存在一些问题。
首先,能源利用效率较低,导致能源浪费严重。
其次,排放物大量产生,对环境造成污染。
另外,一些加热炉在运行过程中噪音较大,不利于工人的健康。
因此,需要采取有效的措施来解决这些问题。
二、工业加热炉的未来趋势1. 环保节能随着社会对环境保护意识的增强以及能源依赖问题的凸显,未来工业加热炉的发展将趋向环保节能。
通过改进燃烧炉结构、提高运行效率等措施,减少能源的消耗和排放物的产生将成为重要的发展方向。
此外,引入清洁能源如太阳能、地热能等也将逐渐成为趋势。
2. 智能化和自动化随着科技的不断进步,工业加热炉将迈向智能化和自动化的发展阶段。
通过引入物联网技术、传感器等,实现对加热炉的实时监控和优化控制,提高工业生产的效率和安全性。
同时,自动化系统能够提高加热炉的稳定性和可靠性,减少人为操作带来的风险。
3. 新材料和新工艺随着材料科学的发展,新材料在工业加热炉中的应用也将逐渐增多。
例如,高温合金、陶瓷材料等能够提高加热炉的耐高温性能和热传导性能,从而提高加热效率和使用寿命。
此外,新工艺的引入也将带来新的加热炉设计和应用领域,如微波加热、等离子体加热等。
4. 多功能和集成化未来的工业加热炉将越来越多地具备多功能和集成化的特点。
多功能指的是加热炉将不仅仅能够进行加热,还能够进行热处理、干燥、烟气净化等功能。
加热炉班长个人工作总结

一、前言在过去的一年里,我担任加热炉班长一职,深感责任重大。
在公司的领导和同事们的支持下,我努力工作,不断提高自己的业务能力和管理水平。
现将个人工作总结如下:二、工作回顾1. 安全第一,严守规程作为一名加热炉班长,我始终将安全生产放在首位。
在工作中,我严格执行各项安全规程,加强安全教育培训,提高班组员工的安全意识。
通过定期开展安全检查,及时消除安全隐患,确保了加热炉生产的安全稳定。
2. 技术创新,提高效率为了提高加热炉的生产效率,我积极学习和研究新技术、新工艺。
通过优化操作流程,改进设备性能,使得加热炉的运行更加稳定,产量得到了显著提升。
同时,我还鼓励班组员工提出合理化建议,共同为生产效率的提升贡献力量。
3. 团队建设,提升凝聚力作为班长,我深知团队协作的重要性。
在日常工作中,我注重加强班组建设,通过开展丰富多彩的团队活动,增进员工之间的感情,提高团队凝聚力。
同时,我还关心员工的生活,积极为员工解决实际困难,营造和谐的工作氛围。
4. 成本控制,开源节流在确保生产任务完成的同时,我高度重视成本控制工作。
通过合理调配资源,降低能源消耗,减少浪费,实现了开源节流。
在班组内部,我定期开展成本分析,找出成本控制的薄弱环节,并采取措施加以改进。
5. 质量管理,追求卓越我始终将产品质量视为企业的生命线。
在加热炉生产过程中,我严格要求班组员工按照质量标准操作,加强过程控制,确保产品质量符合要求。
对于出现的质量问题,我及时组织分析原因,采取措施进行整改,不断提高产品质量。
三、工作展望1. 持续学习,提升自身能力在今后的工作中,我将继续加强学习,不断提高自己的业务能力和管理水平,为班组建设贡献更多力量。
2. 加强团队建设,提高团队凝聚力我将进一步加强团队建设,通过开展更多的团队活动,提高团队凝聚力,为企业的长远发展奠定坚实基础。
3. 深化成本控制,实现经济效益最大化在确保生产任务完成的前提下,我将不断深化成本控制,努力实现经济效益的最大化。
加热炉个人工作总结范文
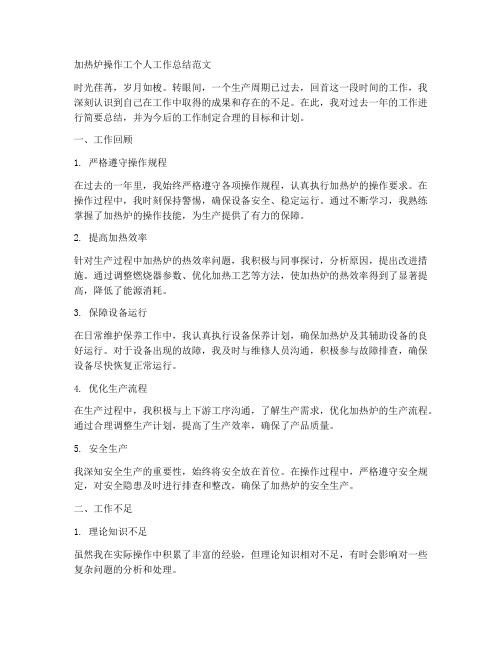
加热炉操作工个人工作总结范文时光荏苒,岁月如梭。
转眼间,一个生产周期已过去,回首这一段时间的工作,我深刻认识到自己在工作中取得的成果和存在的不足。
在此,我对过去一年的工作进行简要总结,并为今后的工作制定合理的目标和计划。
一、工作回顾1. 严格遵守操作规程在过去的一年里,我始终严格遵守各项操作规程,认真执行加热炉的操作要求。
在操作过程中,我时刻保持警惕,确保设备安全、稳定运行。
通过不断学习,我熟练掌握了加热炉的操作技能,为生产提供了有力的保障。
2. 提高加热效率针对生产过程中加热炉的热效率问题,我积极与同事探讨,分析原因,提出改进措施。
通过调整燃烧器参数、优化加热工艺等方法,使加热炉的热效率得到了显著提高,降低了能源消耗。
3. 保障设备运行在日常维护保养工作中,我认真执行设备保养计划,确保加热炉及其辅助设备的良好运行。
对于设备出现的故障,我及时与维修人员沟通,积极参与故障排查,确保设备尽快恢复正常运行。
4. 优化生产流程在生产过程中,我积极与上下游工序沟通,了解生产需求,优化加热炉的生产流程。
通过合理调整生产计划,提高了生产效率,确保了产品质量。
5. 安全生产我深知安全生产的重要性,始终将安全放在首位。
在操作过程中,严格遵守安全规定,对安全隐患及时进行排查和整改,确保了加热炉的安全生产。
二、工作不足1. 理论知识不足虽然我在实际操作中积累了丰富的经验,但理论知识相对不足,有时会影响对一些复杂问题的分析和处理。
2. 沟通协作能力有待提高在与其他部门的沟通协作中,有时出现信息传递不畅、沟通不及时等问题,影响了工作效率。
3. 自我要求不够严格在工作中,有时因为疏忽大意,导致一些本可以避免的错误发生。
这表明我在自我要求上还需要更加严格。
三、今后工作目标和计划1. 深入学习理论知识我将利用业余时间,深入学习加热炉相关的理论知识,提高自己的业务水平,为工作中的问题分析和处理提供有力支持。
2. 提高沟通协作能力我将加强与各部门的沟通协作,提高自己的沟通表达能力,确保工作顺利进行。
加热炉发展方向解析

加热炉发展方向解析
很多用户都在使用热炉,而热炉的发展方向是什么呢?答案其实很多,下面我们来具体看下热炉的发展方向有哪些。
一、发展更多的热能利用技术方向:
热能可以用来生产电力,而用热炉可以制造出更多的热力效率,比如
在热炉上进行热能回收可以减少能源消耗,并提高热炉的增温效率。
二、研发更多环保的热炉:
另外,我们还会发展更多环保的热炉,比如替代煤炉,不仅可以减少
对煤的需求,而且还可以减少对环境的污染,这样就可以更好的保护环境。
三、发展更多的智能热炉:
由于热炉往往经常会处于非工作状态,如果不能及时记录热炉运行情况,就容易造成许多危害,因此智能热炉的开发就变得更加重要。
智能热
炉可以将热炉的运行情况进行实时监测和记录,减少热炉出现的许多问题,让用户可以更加安心地使用。
四、技术开发:
在热炉的技术开发方面,我们还可以开发出更多高效、节能的热炉,
比如采用新的热热交换原理,提高热热利用率,提高热炉热能效率,让热
炉更加高效、节能。
综上所述,热炉的发展方向是非常广泛的,具体的发展路线还在不断
更新,只要根据用户的需求。
2017年加热炉工作总结

2017年加热炉工作总结
回首2017年,我们加热炉工作取得了一定的成绩,也遇到了一些挑战。
在这
一年里,我们不断努力,不断改进,取得了一定的进步。
接下来,让我们来总结一下2017年的加热炉工作。
首先,我们要感谢所有员工的辛勤劳动和付出。
在过去的一年里,大家齐心协力,共同努力,为加热炉的运行和维护做出了不懈的努力。
大家的团结和合作精神为加热炉的稳定运行提供了有力的保障。
其次,我们要总结一下2017年的工作成绩。
在这一年里,我们不断优化加热
炉的运行流程,提高了生产效率,降低了能源消耗。
同时,我们也加强了对加热炉设备的维护和保养,确保了设备的正常运行。
在安全生产方面,我们也加强了安全管理,保障了员工的人身安全。
然而,我们也面临了一些挑战和问题。
在2017年,我们也遇到了一些设备故
障和技术难题,这给我们的工作带来了一定的困难。
同时,市场竞争也越来越激烈,我们需要不断提高自身的竞争力,适应市场的变化。
在2018年,我们将继续努力,继续改进。
我们要进一步提高加热炉的运行效率,降低生产成本,提高产品质量。
我们还要加强技术创新,提高自身的技术水平,增强市场竞争力。
总的来说,2017年是我们加热炉工作的一年,我们取得了一定的成绩,也遇到了一些挑战。
在新的一年里,让我们继续努力,共同进步,为加热炉的发展做出更大的贡献。
加热炉的年总结

加热炉的年总结1. 引言加热炉作为一种重要的工业设备,在各类生产过程中起着至关重要的作用。
本文旨在对加热炉在过去一年的运行情况进行总结和分析,并提出改进和优化的建议。
2. 运行情况总结2.1 运行时间统计根据统计数据,加热炉在过去一年中累计运行时间为XXX小时,平均每天运行X小时。
运行时间的长短直接影响到生产效率和能源消耗。
2.2 故障和维修情况在过去一年中,加热炉共出现X次故障,其中X次属于大修,X次属于小修。
故障和维修情况的统计分析有助于我们了解设备的可靠性,为预防故障提供依据。
2.3 能源消耗情况加热炉在过去一年中消耗了XXX单位的能源,主要包括电力、燃气等。
能源消耗情况的分析对于制定合理的能源管理策略具有重要意义。
3. 问题分析3.1 故障原因分析针对加热炉在过去一年中出现的故障,我们进行了深入的原因分析。
其中,一些常见的故障原因包括电路故障、热风道堵塞、燃烧器失效等。
在今后的维护和保养中,需要加强对这些问题的排查和处理。
3.2 能源消耗分析通过对能源消耗情况的统计和分析,我们发现在加热炉的运行过程中存在一些能源浪费的现象,如热损失、不合理的调温控制等。
针对这些问题,我们应该采取相应的措施来减少能源消耗,提高能源利用效率。
4. 改进和优化建议4.1 维护和保养针对加热炉的故障情况,我们建议加强对设备的维护和保养工作,定期检查和更换易损件,提高设备的可靠性和稳定性。
4.2 能源管理在能源消耗分析的基础上,我们建议优化加热炉的调温控制策略,合理利用余热,减少热损失,并考虑使用更加高效的能源。
4.3 自动化控制引入自动化控制系统可以提高加热炉的运行效率和稳定性。
可以考虑引入温度传感器、流量计等设备,实现自动调节和控制。
5. 总结通过对加热炉的年总结和分析,我们了解了加热炉的运行情况和存在的问题,同时提出了一些改进和优化的建议。
未来,我们将密切关注这些问题的解决和改善,以提升加热炉的工作效率和能源利用率。
- 1、下载文档前请自行甄别文档内容的完整性,平台不提供额外的编辑、内容补充、找答案等附加服务。
- 2、"仅部分预览"的文档,不可在线预览部分如存在完整性等问题,可反馈申请退款(可完整预览的文档不适用该条件!)。
- 3、如文档侵犯您的权益,请联系客服反馈,我们会尽快为您处理(人工客服工作时间:9:00-18:30)。
加热炉控制技术的回顾与展望①柴天佑 王中杰 王 伟(东北大学自动化研究中心 沈阳 110006)摘 要 归纳和总结了加热炉控制技术的理论研究和工程应用状况,并指出了其中存在的主要问题和缺陷,同时分析了加热炉控制技术发展的趋势。
关键词 加热炉 最优控制 优化设定R evie w and prospect of control techniques for reheating f urnaceChai Tianyou Wang Zhongjie Wang Wei(Research Center of Automation,Northeastern University Shenyang 110006)Abstract The state of theoretical research and practical application of control techniques for reheating furnace is fully summarized,and the main problems and imperfection in existance are also pointed out.At the same time,the tendency of future development of control techniques for reheating furnace is analyzed.K ey w ords reheating furnace;optimum control;optimization setting0 引言加热炉控制主要是采用合理的控制策略,使炉内燃烧尽可能完全,以及恰当地使钢坯加热到目标温度。
早期的工作主要集中在常规燃烧控制上,其直接目标是获得较为稳定的炉子工况及追求最佳燃烧。
70年代以后,国际上对加热炉的最优控制进行了广泛研究,并且随着微型计算机技术的发展,加热炉计算机控制逐步进入实用化阶段[2~4][6][16~18]。
但总的来说,加热炉的高级计算机控制策略尚处在初级阶段,有关技术还不成熟。
1 加热炉控制技术的理论研究状况111 最佳燃烧控制11111 温度燃料空气流量串级调节在仪表控制系统中,处理燃料与空气的关系通常采用配比调节,由于燃料与空气调节回路的响应速度不一致,流量测量孔板也有误差,燃料的热值又不稳定以及烧嘴特性等的变化,这种配比关系难于保证。
特别是在燃烧负荷发生变化的情况下,更无法保持最佳配比。
为解决这些问题,产生了3种处理空燃关系的交叉限幅法:(1)单交叉限幅法;(2)双交叉限幅法;(3)改进型双交叉限幅法。
单双交叉限幅法有以下几个优点:(1)使系统在燃烧负荷增加或要求升温时,实现空气先行,燃料跟随;燃烧负荷降低或降温时,燃料先行,空气跟随,以达到防止黑烟污染环境的目的。
(2)使系统在调节的动态过程中,保持空气2燃料的相互跟随关系,控制空燃配比,特别是双交叉限幅的作用更好。
(3)使系统在供风设备一旦发生故障停风时,能自动关闭燃料调节阀,具有自保护功能。
但这两种方法的缺点是响应速度较慢,且偏置量在各种运行范围为恒定值K(满刻度流量的百分率),与温度偏差大小及运行范围无关,温度设定值越低,需要的燃料越少,偏置值K所占实际比值越大。
改进型双交叉限幅不但具有双交叉限幅的优点,实现双向限幅,空燃比范围精确,同时使偏置值与偏差大小成比例,提高系统的动态性能。
据报导,这种方法可节能4%~7%,其空燃比控制精度不超过±0102。
缺点是系统较复杂,用的运算模块多,但在现代的集散控制系统中实现是容易的。
①收稿日期:1997211211 修改稿收到日期:1998201212柴天佑 男 1947年生 教授(博士生导师) 主要研究方向是智能控制,自适应控制,复杂工业过程的建模、控制与优化等。
国家自然科学基金重点项目和辽宁省优秀青年科研人才培养基金资助项目。
11112 修正空燃比空燃比对于在加热炉各段内取得最佳的燃烧效率是重要的,正确地调整空燃比对于炉子安全及产品质量也是重要的。
在常规的仪表控制系统中,空燃比往往由人工设定,但在频繁调节状态下,即使是最灵敏的传感器和调节阀也很难保证精确的空燃比。
这是因为,流量测量孔板存在着误差,以及在燃料或空气的流速较低时,调节阀的位置及流速之间呈非线性关系。
为了解决这个问题,多数加热炉计算机控制系统对加热炉各段建立了空燃比设定值曲线,通过修正这些曲线可以保证在每个燃料流速下加热炉各段都能取得最大燃烧效率[7]。
目前残氧闭环控制是修正空燃比的一种非常重要的方法。
用氧化锆测定残氧量,用氧指示控制器调节输出修正空燃比,以达到低过剩空气量的燃烧。
,为此在各段都单设残氧量控制回路,并估算各段间的影响,采用多变量控制,通过计算求得加热炉各段残氧量调节回路的设定,修正各段的空燃比。
11113 附属回路调节及参数修正在加热炉燃烧控制中,除了温度流量串级及残氧修正空燃比主要回路外,还有为减少炉外冷空气侵入及火焰外喷的炉膛压力调节;保障流量调节回路稳定的燃气及空气总管压力调节以及为保证稳定的空燃比而进行的温度、压力及燃气的热值修正,这都是保证最佳燃烧所不可缺少的。
通过集散控制系统进行这些修正是轻而易举的,且多采用PI控制或PID控制。
112 加热炉升温过程的数学模型加热炉的生产节奏必须服从于轧机的生产安排,它应按轧机的要求适时地提供加热温度合适的钢坯。
钢坯升温过程的数学模型就是要根据变化着的轧制生产情况,估算钢坯在炉内的加热情况,控制燃烧过程。
过去这方面通常采用回归方法,如武钢引进的热连轧加热炉钢坯升温控制的数学模型[8]。
多元回归模型的缺点是准确性差,特别是在生产条件与轧制节奏发生变动时,其次是系数较多,而且这些系数不少没有直接的物理意义。
文献9以加热炉实时计算机控制为目的,以钢锭轧前过程单一数学模型的方法为基础,从描述钢坯内部不稳定导热的二维偏微分方程及相应的边界条件出发,把炉内的钢坯考虑为一股被加热的物料流,并按几何位置分解为一系列相互关联的子系统,从而研究开发了描述钢坯热状态的大规模离散状态空间模型,为实时计算机控制奠定了基础。
这种机理模型现在用得较为普遍[5][10],国外的绝大多数加热炉计算机控制系统以及重钢板坯加热炉和天津轧钢五厂步进式加热炉等都有过不同程度的应用。
113 加热炉优化控制策略11311 优化炉温设定值控制步进式加热炉传统的控制方法是设定炉温,由执行器自动调节,再配以空燃比,烟道残氧量及燃料流量与助燃空气流量的交叉限幅等辅助控制以提高燃料效率,其原理是基于经济的炉温设定可保证出炉钢坯正常轧制而不使轧机过荷受损。
但是一般人工炉温设定余量偏大,在生产工况波动的情况下,容易造成过烧,直接后果是热效率降低,钢耗上升,同时也加重了操作人员的劳动强度。
随着计算机技术的发展,人们开发了各种各样的优化设定炉温策略。
(1)二次型性能指标[11][15] min J=∑kf-1k=012‖u(k)2‖R(k) (1) T sp∈ΩT式(1)为加热炉最小能耗控制命题,通常以炉温极小化为间接命题。
其中J为钢坯从入炉到出炉的能耗指标;ΩT为炉温设定值允许区域;R(k)为性能指标的加权矩阵;k f为钢坯出炉时刻;T sp为炉温设定值向量;u(k)为炉温。
这种优化方法的优点是物理意义直接明了,也是工程上经常使用的一种方法。
但它只考虑了燃料消耗量,而没有考虑钢坯氧化烧损量。
(2)炉温优化给定模型考虑到炉温的滞后性和炉温设定的平稳性,文献12给出了一种新的炉温优化设定模型: min f(x)s.t Tl≤g k(x)≤Th k=0,1,2,…,m (2) -A≤x≤A其中 f(x)=CM N g m(x)+m(m+1)2P0x g0(x)=T0(m b) g k(x)=g k-1(x)+B0[(TS(0)+kx)4-g k-14(x)]+βq式(2)表示以假设将来m拍的炉温设定值TS(1)、TS(2)、…、TS(m)是以当前炉温测量点TS(0)为始点的线性等量递增或线性等量递减的直线段为前提的加热炉最小能耗控制命题。
其中f(x)为目标函数;[Tl、Th]为炉内所有钢坯的平均温度区域;A为炉子在一拍内的最大升温或降温速率;C和M为钢坯的比热和质量;N为炉内钢坯的个数,m和m b为优化炉温设定值的拍数和炉温滞后的拍数;B0、P0和β均为比例系数;g0为钢温迭代起点;g k为钢温更新算式;k为在m拍内控制炉温的变量;x为待优化的变量;q =(进炉钢坯温度-出炉钢坯温度)/炉内钢坯个数。
该优化目标函数是用热平衡方程直接推导出来的,且考虑了炉温设定的平稳性和炉温的滞后性,不仅便于工控机控制,而且将模型简化成了仅有一个变量x的非线性模型,从而大大提高了在线求解模型的实用性。
(3)多模式加热炉设定控制[14]在正常的加热炉生产工况下,炉温设定值优化算法能取得非常满意的控制效果。
但是,当加热炉处于不正常工况时,炉温设定值控制的性能就受到影响。
另外,当燃气供应不足,燃气压力较低时,实施炉温设定值控制将导致燃料流量调节阀的急剧动作和燃气压力的振荡,使控制无法平稳运行,这在实际生产过程中是不希望出现的。
为了提高控制系统的鲁棒性和可靠性,在炉温设定值优化控制的基础上增加燃料流量设定值控制,从而实现多模式的加热炉设定控制。
11312 加热炉优化控制的动态补偿炉温设定值的动态补偿,即基于前馈2反馈原理[13],根据选定的准稳态工况与当前实际工况的差异以及设定值控制的偏差对炉温设定值进行补偿。
所考虑的主要因素有轧钢节奏、预热段与加热段钢坯的平均温度差、钢坯估计温度分布与最佳温度分布的偏差以及轧钢机前钢坯表面温度检测信号等。
对于炉内钢坯移动速度的波动,引入前馈补偿予以校正,而对于其它因素引起的钢坯温度分布与最佳温度分布的偏离,采用状态反馈予以修正。
为了克服模型误差的影响,并使系统具有一定的适应性和鲁棒性,还引入了粗轧机前钢坯表面温度检测实时信号作为二次反馈信号进一步进行补偿。
对于炉内同时存在不同钢种及规格的钢坯加热情况,文献13提出了用重量加权法来处理各类钢坯对炉温设定值的影响。
2 加热炉控制技术的工程应用现状国际上从70年代就已开始加热炉计算机控制的研究,我国在这方面起步较晚,从80年代初才开始这方面的研究工作。
但近十多年来,由于计算机技术以及智能控制技术的迅速发展,加热炉计算机控制的应用日趋广泛,控制水平有明显提高,并且取得了一些应用成果[20]。
表1和表2分别介绍了国内、外加热炉计算机控制应用的现状。
表1 加热炉计算机控制在国内应用的现状厂名所用机型应用现状大连钢厂初轧分厂M6809油风自动配比、残氧闭环控制、炉温炉压控制攀钢初轧厂上位机IN TEL下位机单板机烧钢过程控制、钢锭烧好预报、事故处理、炉温显示、打印等功能莱钢轧钢厂TI565机DDC、SPC级控制采用自寻优技术并按照数学模型烧钢,均热期采用脉动供热技术,并计划投入SCC控制马钢初轧厂TMC280单板机过程控制与监视、残氧闭环控制、按加热曲线烧钢长城特钢厂四分厂上位机SERIES/1下位机DJ K/F210002D过程控制与监视、钢锭温度模型操作、生产数据打印、数据采集、DDC级控制太钢初轧厂TI565机煤气、空气流量以及炉压的PID控制、自寻优及专家控制算法、温度检测及越限报警首钢初轧厂TK280炉温、炉压、空气流量、煤气流量控制鞍钢第一初轧厂WDPF DDC、SPC、SCC级控制鞍钢线材厂SIGMA监控机炉温、油量、风量控制表2 加热炉计算机控制在国外应用的现状国家及厂名所用机型应用现状日本Kashima钢厂钢坯目标出炉温度计算、钢温预报、出料周期预报、钢温预报模型修正、空燃比控制、炉温最优控制瑞典DOMNARV ET厂确定最佳加热曲线和炉温控制美国Conshohochen厂DEC MICRO VAXII 空燃比控制、炉压控制、空气压力控制、热风放散控制、坯料跟踪、设定值选择、生产调度模型、加热炉温度模型美国内陆钢厂坯料跟踪、钢温预报模型最佳加热曲线、系统报警、加热炉的步进速率控制、人机界面、记录和报告、炉温控制美国Dofasco公司1级:PLC控制器Honeywell TDC230002级:DEC VAX8350空燃比控制、炉温控制、坯料跟踪、钢温预报、炉温设定值调节、待轧策略、加热炉步进速率控制、设备诊断、加热炉各区段热量平衡、系统报警、记录和报告、人机界面新西兰Hoogovens公司PDP11240计算机采用热传导微分方程进行钢温预报、炉温优化控制、空燃比控制、推钢速率控制、直接燃料控制美国Yamatake Honeywell公司TDC3000BASIC系统步进辐射式加热炉全自动燃烧控制系统具有过程控制、作业顺序管理、钢坯跟踪及生产管理功能3 展望国内的加热炉控制技术在理论上已达到先进国家的水平,但在工程应用上和发达国家相比还存在较大的差距,根据我国的实际情况,关于加热炉控制技术的发展提出以下几点建议:(1)国内有的企业虽然配有较先进的计算机系统,但只是作一些较简单的PID控制,计算机的潜能没有很好地发挥出来,而且国有企业缺乏既懂专业又会维护计算机的人才,因此导致加热炉的计算机控制效果不很理想,所以首先有必要把现有设备很好地利用起来。