炼钢机械:转炉炼钢机械设备共28页文档
金属冶炼中的设备与工艺

高炉炼铁:将铁矿石、焦炭、石灰石等原料放入高炉中,通过高温冶炼 得到铁水
转炉炼铁:将铁水倒入转炉中,通过吹氧、搅拌等工艺得到钢水
电炉炼铁:利用电弧热将铁矿石熔化,得到铁水
连续铸造:将铁水倒入连续铸造机中,通过冷却、凝固等工艺得到钢坯
热轧:将钢坯加热到一定温度,通过轧辊轧制得到钢板
冷轧:将钢板加热到一定温度,通过轧辊轧制得到冷轧钢板
轧制设备主要包括 轧辊、轧机、轧制 线等
轧制设备的工作原理是 通过轧辊对金属材料进 行挤压,使其变形并达 到所需的形状和尺寸
轧制设备的应用广 泛,包括钢铁、有 色金属、合金等金 属材料的轧制
精炼炉:用于金属的精炼和提纯 真空炉:用于金属的脱气、脱氧和脱碳 电弧炉:用于金属的熔化和精炼 感应炉:用于金属的熔化和精炼 精炼设备:用于金属的精炼和提纯 精炼设备:用于金属的精炼和提纯
节能减排:降低能耗,减少排放,提高能源 利用效率
循环利用:提高废料、废气、废水的循环利 用,实现零排放
智能化:采用自动化、智能化技术,提高生 产效率,降低人工成本
环保材料:采用环保材料,减少对环境的影 响,提高产品的环保性能
绿色设计:在设计阶段就考虑环保因素,提 高产品的环保性能和寿命
汇报人:
,
汇报人:
01
03
05
02
04
高炉:用于炼铁的主要设备,可将铁矿石 转化为铁水
转炉:用于炼钢的主要设备,可将铁水转 化为钢水
电炉:用于炼钢的主要设备,可将废钢和 铁水转化为钢水
连铸机:用于将钢水连续铸造成钢坯的设备
加热炉:用于加热钢坯的设备,可提高钢 坯的塑性和韧性
轧钢机:用于将钢坯轧制成各种钢材的设备
精炼目的:去除杂质,提高金属纯度 精炼方法:电解法、化学法、物理法等 精炼设备:电解槽、反应器、离心机等 精炼过程:原料准备、反应、分离、净化等步骤
转炉炼钢设备
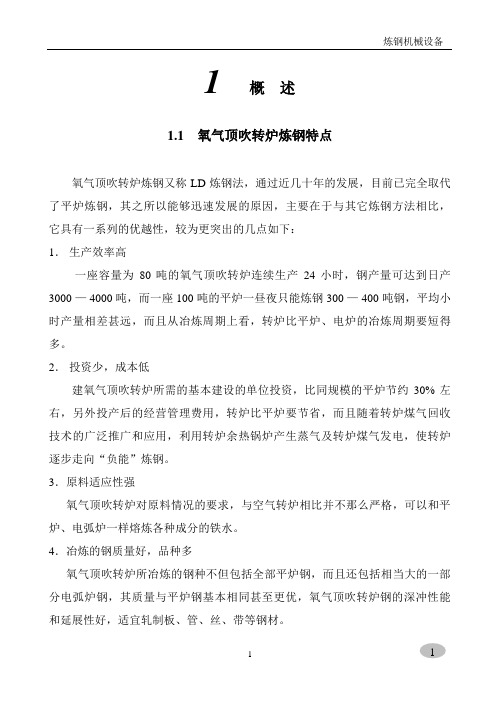
1 概述1.1氧气顶吹转炉炼钢特点氧气顶吹转炉炼钢又称 LD 炼钢法,通过近几十年的发展,目前已完全取代了平炉炼钢,其之所以能够迅速发展的原因,主要在于与其它炼钢方法相比,它具有一系列的优越性,较为更突出的几点如下:1.生产效率高一座容量为80 吨的氧气顶吹转炉连续生产24 小时,钢产量可达到日产3000 — 4000 吨,而一座 100 吨的平炉一昼夜只能炼钢 300 — 400 吨钢,平均小时产量相差甚远,而且从冶炼周期上看,转炉比平炉、电炉的冶炼周期要短得多。
2.投资少,成本低建氧气顶吹转炉所需的基本建设的单位投资,比同规模的平炉节约30% 左右,另外投产后的经营管理费用,转炉比平炉要节省,而且随着转炉煤气回收技术的广泛推广和应用,利用转炉余热锅炉产生蒸气及转炉煤气发电,使转炉逐步走向“负能”炼钢。
3.原料适应性强氧气顶吹转炉对原料情况的要求,与空气转炉相比并不那么严格,可以和平炉、电弧炉一样熔炼各种成分的铁水。
4.冶炼的钢质量好,品种多氧气顶吹转炉所冶炼的钢种不但包括全部平炉钢,而且还包括相当大的一部分电弧炉钢,其质量与平炉钢基本相同甚至更优,氧气顶吹转炉钢的深冲性能和延展性好,适宜轧制板、管、丝、带等钢材。
5.适于高度机械化和自动化生产由于冶炼时间短,生产效率高,再加转炉容量不断扩大,为准确控制冶炼过程,保证获得合格钢水成分和出钢温度,必须进行自动控制和检测,实现生产过程自动化。
另外,在这种要求下,也只有实现高度机械化和自动化,才能减轻工人的劳动强度,改善劳动条件。
1.2 转炉炼钢机械设备系统氧气顶吹转炉炼钢法,是将高压纯氧[压力为0.5~1.5MPa ,纯度99.5% 以上,(我厂为99.99% )],借助氧枪从转炉顶部插入炉内向熔池吹氧,将铁水吹炼成钢。
氧气顶吹转炉的主要设备有:1.转炉本体系统:包括转炉炉体及其支承系统——托圈、耳轴、耳轴轴承和支承座,以及倾动装置,其中倾动装置由电动机、一次减速机,二次减速机、扭矩缓冲平衡装置等组成。
炼钢机械: 转炉炼钢机械设备
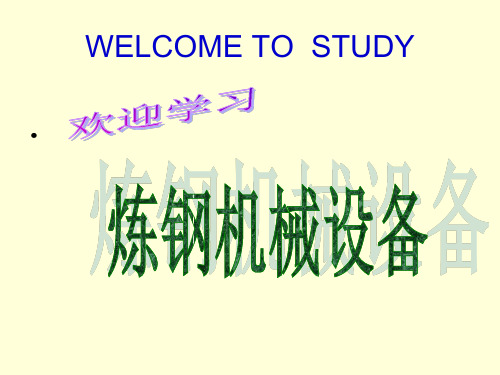
• 高级优质钢及合金钢
第一章、炼钢机械设备概述
• 3.炉外精炼方法
• 核心目的:脱气、除杂、调品、控温
• DH法:真空处理提升脱气法(1956年/德国/多特德 —胡德公司)
•
采取真空浇注时提出钢水中的气体
• RH法:真空处理循环脱气法(1957年/德国/Ruhrstahl——Heraeus
•
公司)利用Ar气气泡带动钢水连续通过真空室而循环脱气
• 结构:箱形断面、整体式或分段式
•
包括环形圈体、耳轴两大部分,水冷
• 材料:低合金钢
• 制造:铸造、焊接(一般采用)
• 工作特点:承载(静载)、受扭、冲击载荷
•
(频繁起动、制动、生产载荷变化)
第二章、转炉炼钢机械
• 二、炉体与托圈的联接装置P198图7-19
• 1.联接基本要求:满足热变形要求
•
•
底吹化渣、去磷的困难。
•
优点:金属收得率高,炉子可控性强、去磷能力强
第一章、炼钢机械设备概述
• 2.特殊钢冶炼基本工艺:
• (1)基本工艺
•
熔化 吹氧 处理、浇注
• 废钢/合金——钢液——钢水—————锭/坯
• (2)主要方法
• 电弧炉、感应炉、电阻炉、矿热炉、电子束
• 炉、等离子炉等
• (3)主要产品
• 二、炼钢工厂基本机械设备
• 1.炼钢工厂布置
•
讲读参考教材P185~186
•
300t转炉车间平面布置
•
• 2.炼钢机械设备
• (1)转炉炼钢机械设备按用途划分:
• 原料设备——铁水车、混铁炉、铁水预处理设备、吊
•
车、散料供应设备、称量设备
转炉炼钢设备和工艺
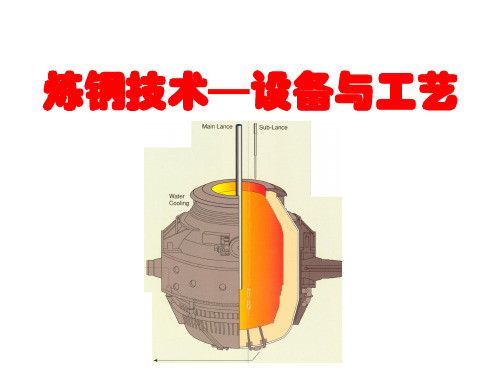
转炉炉型主要参数的确定
转炉的公称容量 炉型主要参数
炉容比 高宽比 熔池部分尺寸 炉身部分尺寸 炉帽部分尺寸 出钢口部分尺寸 炉衬部分
炉型主要尺寸
转炉的公称容量
转炉的公称容量又称公称吨位,是炉型设计、计算的重要依据,但 其含义目前尚未统一,有以下三种表示方法: (1)用转炉的平均铁水装入量表示公称容量; (2)用转炉的平均出钢量表示公称容量; (3)用转炉年平均炉产良坯(锭)量表示公称容量
炉口直径(d): 在满足兑铁水、加废钢出渣、修炉等操作要求的前提下,应 尽量缩小炉口直径,以减少喷溅、热量损失和冷空气的吸入量。 一般炉口直径为;
d (0.43 ~ 0.53) D
大转炉取下限,小转炉型
炉型类型: 按金属熔池形状的不同,转炉炉型可分为筒球型、锥球型和截锥 型三种,
转炉炉型
A 筒球型 熔池形状由一个球缺体和一个圆筒体组成。它的优点是炉型形 状简单,砌筑方便炉壳制造容易。熔池内型比较接近金属液循环流 动的轨迹,在熔池直径足够大时,能保证在较大的供氧强度下吹炼 而喷溅最小,也能保证有足够的熔池深度,使炉衬有较高的寿命。 大型转炉多采用这种炉型
炉底寿命短 炉容小 钢水含氮高 喷溅 污染 废钢比低
生产率高 N 、P 、 S 、 C 、 O 低 渣内FeO低 无喷溅 污染低 废钢比低 全 低 吹 O2+ 石 灰 粉
顶底复合吹氧+ 全量废钢 喷吹煤粉 大量高热值废 废钢预热 气 喷石灰粉 二次燃烧 很高废钢比 大量高热值废气
转炉炼钢车间设备组成
• 结果还应与容量相近、生产条件相似、技术经济指标 较好的炉子进行对比并适当调整 • 上述公式对中小炉子较为适用,对大型炉子有差距。
转炉机械设备讲义
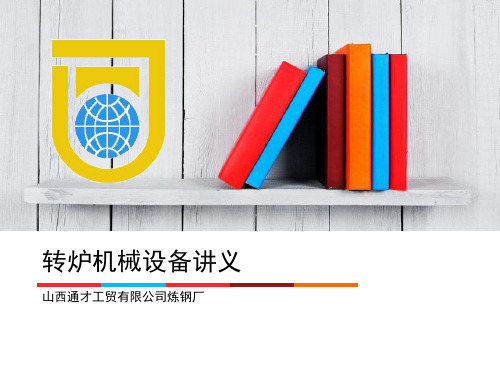
4.炉体支撑系统
(3)耳轴与托圈直接焊接。这种结构由于采用耳轴与托圈直接焊接, 因此,重量小、结构简单、机械加工量小。在大型转炉上用得较多。 为防止结构由于焊接的变形,制造时要特别注意保证两耳轴的平行度 和同心度。
图7-16 耳轴与托圈的焊接连接
4.炉体支撑系统
4.3炉体与托圈连接装置 ①支撑夹持器 法兰螺栓联接是早期出现的吊挂式联接装置,如图7—17a、b 所示。在炉壳上部周边焊接两个法兰,在两法兰之间加焊垂直 筋板加固,以增加炉体刚度。在下法兰上均布8~12个长圆形 螺栓孔,通过螺栓或销钉斜楔将法兰与托圈联接。在联接处垫 一块经过加工的长形垫板,以便使法兰与托圈之间留出通风间 隙。螺栓孔呈长圆形的目的是允许炉壳沿径向热膨胀并避免把 螺栓剪断。炉体倒置时,由螺栓(或圆锁)承受载荷。炉体处于 水平位置时,则由两耳轴下面的托架(见图7—8中的7)把载荷传 给固定在托圈上的定位块。而在与耳轴连接的托圈平面上有一 方块与大法兰方孔相配合,这样就能保证转炉倾动时,将炉体 重量传递到托圈上。
4.炉体支撑系统
(2)静配合连接。其耳轴具有过盈尺寸,装配时可将耳轴用液氮冷缩 或将轴孔加热膨胀,耳轴在常温下装入耳轴孔。为了防止耳轴与耳轴 座孔产生转动或轴向移动,在静配合的传动侧耳轴处拧入精制螺钉。 由于游动侧传递力矩很小,故可采用带小台肩的耳轴限制轴向移动。 这种连接结构比前一种简单,安装和制造较方便,但这种结构仍需在 托圈上焊耳轴座,故托圈重量仍较重。而且装配时,耳轴座加热或耳 轴冷却也较费事,故目前国内没广泛使用。
4.炉体支撑系统
炼钢生产有冶炼和浇铸两个基本环节。为了保证冶炼和浇
铸的正常运行,转炉车间主要包括原料系统(铁水、废钢和散 装料的存放和供应),加料、冶炼和浇铸系统。此外,还有炉
炼钢机械全
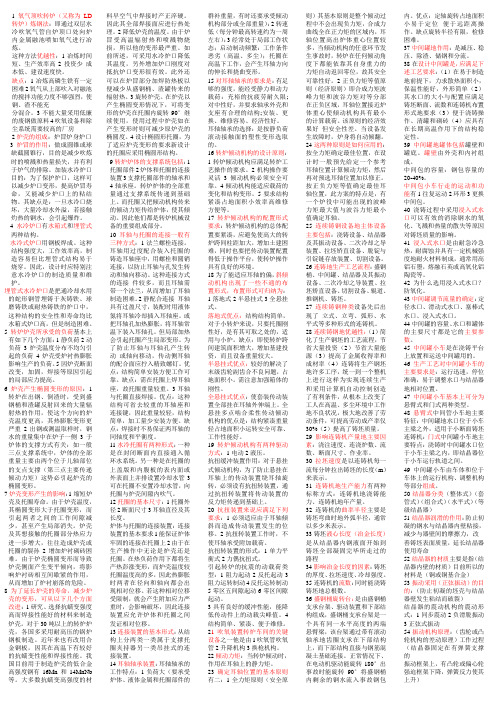
1氧气顶吹转炉(又称为LD转炉)炼钢法:即通过双层水冷吹氧气管自炉顶口处向炉内金属融池喷如氧气进行冶炼。
这种方法优越性:1冶炼时间短、生产效率高2投资少成本低、建设速度快。
缺点:1冶炼高磷生铁有一定困难2氧气从上部吹入对融池的搅拌功能力度不够强烈,使钢、渣不能充分混合。
3不能大量采用低廉的废钢做原料4吹氧设备和除尘系统需要较高的厂房2炉壳的组成:炉冒炉身炉口3炉冒的作用:做成圆锥或球缺截圆锥行,目的是减少吹炼时的喷溅和热量损失,并有利于炉气的排除。
加装水冷炉口目的:为了保护炉口,这样可以减少炉口变形,提高炉冒寿命,又能减少炉口上的粘结物。
其缺点是:一旦水冷口烧坏,大量冷却水外溢,若接触灼热的钢水,会引起爆炸。
4水冷炉口有水箱式和埋管式两种结构。
水冷式炉口用钢板焊成。
这种结构强度大,工作效率高,制造容易但比埋管式结构易于烧穿。
因此,设计时应特别注意水冷炉口的制造质量和维护。
埋管式水冷炉口是把通冷却水用的蛇形钢管埋铸于灰铸铁、球磨铸铁或耐热铸铁的炉口中,这种结构的安全性和寿命均比水箱式炉口高,但是制造困难。
5转炉炉壳所承受的负荷基本上有如下几个方面:1静负荷2动负荷3炉壳温度分布不均匀引起的负荷4炉壳受炉衬热膨胀影响生产的负荷。
5因炉壳断面改变,加固,焊接等原因引起的局部应力提高。
6炉壳产生椭圆变形的原因:1转炉在出钢、倒渣时,受到盛钢桶和渣罐反射回来的大量辐射热的作用,使这个方向的炉壳温度更高,其热膨胀变形更严重2出钢或测温取样时,钢水的重量集中在炉子一侧3于炉体的支撑方式有关:如一般三点支撑系统中,炉体的全部重量主要由两个位于儿轴部位的支点支撑(第三点主要传递倾动力矩)这势必引起炉壳的椭圆变形。
7炉壳变形产生的影响:1缩短炉壳及托圈寿命。
由于炉壳温度,其椭圆变形大于托圈变形,而引起两者之间的工作间隙减少,甚至产生局部消失。
炉壳及其想接触的托圈部分热应力进一步增大,往往造成炉壳或托圈的裂孙2增加炉衬砌砖困难。
炼钢主要工艺设备表
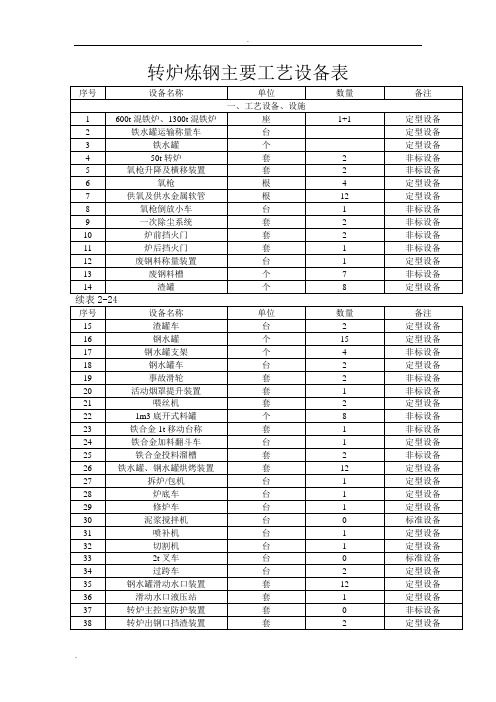
套
13
二冷喷水集管150x150
4
套
14
150 x150引锭头装配
2
套
表2-29 板坯连铸机主要设备表
序号
设备名称
数量
单位
备注
一
在线设备
1
操作平台
1
套
2
大包回转台(含加盖装置)
1
套
3
中间包
2
个
4
中间包盖
2
个
5
塞棒机构
4
个
6
浸入式水口夹持装置
4
套
7
中间包车
2
台
8
中间包预热站
2
套
9
浸入式水口烘烤装置
1
套
1
非标设备
21
喂丝机
套
2
定型设备
22
1m3底开式料罐
个
8
非标设备
23
铁合金1t移动台称
套
1
非标设备
24
铁合金加料翻斗车
台
1
定型设备
25
铁合金投料溜槽
套
2
非标设备
26
铁水罐、钢水罐烘烤装置
套
12
定型设备
27
拆炉/包机
台
1
定型设备
28
炉底车
台
1
定型设备
29
修炉车
台
1
定型设备
30
泥浆搅拌机
台
0
标准设备
31
序号
设备名称
数量
单位
备注
22
150×150引锭头装配
5
转炉设备概述
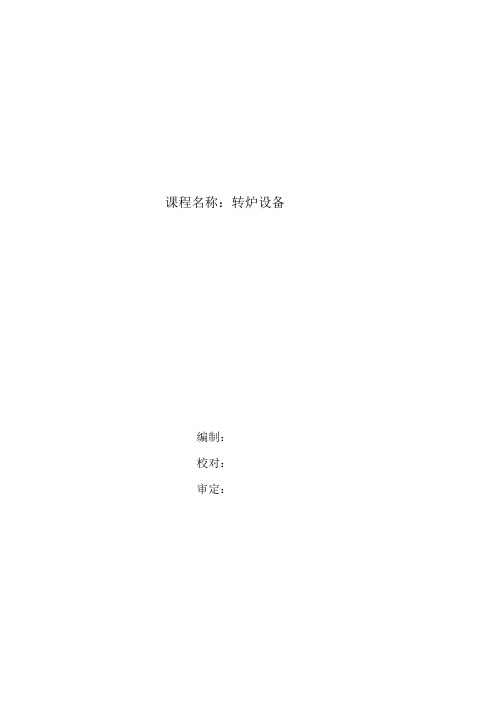
课程名称:转炉设备编制:校对:审定:目录:前言2页第一章:培训目的第一节基本知识目标2页第二节能力目标2页第二章:转炉设备第一节转炉炼钢设备组成方框图- 4页第二节顶底复吹转炉炼钢设备特点 5页第三节转炉生产工艺流程图 6页第四节转炉设备的组成 5页第四章转炉设备安装、试车第一节制作单位预装 15-16页第二节现场设备安装 16-17页第三节空载荷试运转 17-18页第四节转炉试运转应满足的条件和技术要求 18页第五章转炉开新炉和冶炼第一节转炉开新炉需要具备的条件 18页第二节冶炼过程中的操作要求 18-19页第三节设备动行中故障的排除方法 19页第四节操作过程中紧急状态下的处理方法 20页第五节设备交接班规定 21页第六章转炉设备常见问题和解决办法 21--23页前言根据分厂培训计划编写了这本教材,以便我们一起共同掌握转炉炼钢主要工艺设备和机械设备的相关知识和主要工艺操作技能、解决常见的故障处理方法,通过培训能够更进一步的提高使用和维护转炉炼钢设备的能力,并使我们的操作工人和点检员分析和排除故障的能力有所提高。
同时,通过学习,进一步让点检人员了解如何更好的与一线员工的沟通。
第一章培训目标第一节基本知识目标1.1.1了解氧气顶吹转炉设备组成和配套设备的构造。
1.1.2熟悉和掌握转炉设备结构、工艺参数、设备操作和维护。
第二节能力目标1.2.1了解转炉设备选型依据、设备结构特点等方面的能力。
1.2.2对转炉设备发生故障的问题点有准确判断能力。
1.2.3提高杜绝转炉设备故障、减少故障、处理故障的能力。
第二章转炉设备第一节转炉炼钢设备组成方框图第二节顶底复吹转炉炼钢设备特点1、冶炼时间短,生产效率高,一般20—40分钟吹氧即可完成一炉钢水的冶炼。
而平炉则需要5—6小时才能完成一炉钢的冶炼。
2、投资少、成本低、施工速度快。
一座顶底复吹转炉的投资只有平炉的70%左右。
冶炼的品种也比平炉广。
3、顶底复吹可以有效的改变熔池的搅拌力,可以减少喷溅,提高收得率。
炼钢设备doc
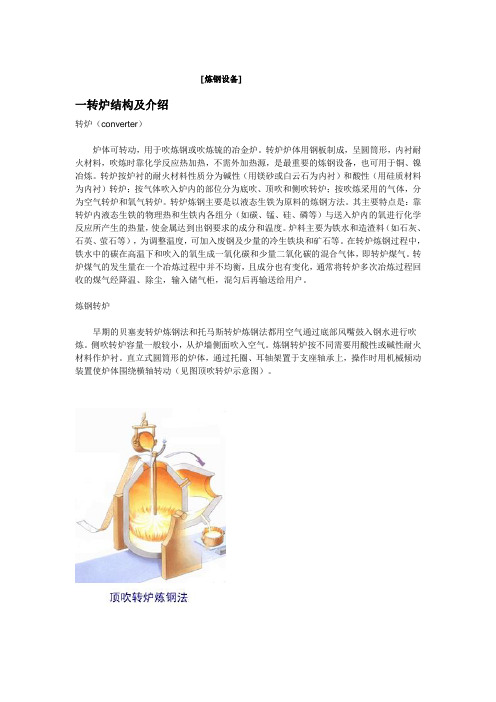
[炼钢设备]一转炉结构及介绍转炉(converter)炉体可转动,用于吹炼钢或吹炼锍的冶金炉。
转炉炉体用钢板制成,呈圆筒形,内衬耐火材料,吹炼时靠化学反应热加热,不需外加热源,是最重要的炼钢设备,也可用于铜、镍冶炼。
转炉按炉衬的耐火材料性质分为碱性(用镁砂或白云石为内衬)和酸性(用硅质材料为内衬)转炉;按气体吹入炉内的部位分为底吹、顶吹和侧吹转炉;按吹炼采用的气体,分为空气转炉和氧气转炉。
转炉炼钢主要是以液态生铁为原料的炼钢方法。
其主要特点是:靠转炉内液态生铁的物理热和生铁内各组分(如碳、锰、硅、磷等)与送入炉内的氧进行化学反应所产生的热量,使金属达到出钢要求的成分和温度。
炉料主要为铁水和造渣料(如石灰、石英、萤石等),为调整温度,可加入废钢及少量的冷生铁块和矿石等。
在转炉炼钢过程中,铁水中的碳在高温下和吹入的氧生成一氧化碳和少量二氧化碳的混合气体,即转炉煤气。
转炉煤气的发生量在一个冶炼过程中并不均衡,且成分也有变化,通常将转炉多次冶炼过程回收的煤气经降温、除尘,输入储气柜,混匀后再输送给用户。
炼钢转炉早期的贝塞麦转炉炼钢法和托马斯转炉炼钢法都用空气通过底部风嘴鼓入钢水进行吹炼。
侧吹转炉容量一般较小,从炉墙侧面吹入空气。
炼钢转炉按不同需要用酸性或碱性耐火材料作炉衬。
直立式圆筒形的炉体,通过托圈、耳轴架置于支座轴承上,操作时用机械倾动装置使炉体围绕横轴转动(见图顶吹转炉示意图)。
50年代发展起来的氧气转炉仍保持直立式圆筒形,随着技术改进,发展成顶吹喷氧枪供氧,因而得名氧气顶吹转炉,即L-D转炉(见氧气顶吹转炉炼钢);用带吹冷却剂的炉底喷嘴的,称为氧气底吹转炉(见氧气底吹转炉炼钢)。
在应用氧气炼钢的初期还使用过卡尔多转炉和罗托转炉,通过炉体回转改善炉内反应,但由于设备复杂,炉衬寿命短未能获得推广。
炼铜转炉一般为卧式转炉用于处理铜锍,通过鼓入空气把冰铜氧化吹炼成粗铜,也用于吹炼冰镍。
转炉自动化automation of converter氧气转炉冶炼周期短、产量高、反应复杂,但用人工控制钢水终点温度和含碳量的命中率不高,精度也较差。
金属冶炼的主要设备与工艺

出口市场:扩大出 口市场,提高国际 市场份额
技术引进:引进国 外先进技术和设备 ,提高生产效率和 质量
人才引进:引进国 外优秀人才,提高 研发和管理水平
高质量发展
智能化:采用自动化、智能 化技术,提高生产效率
绿色环保:减少污染,提高 能源利用效率
创新驱动:加强技术创新, 提高产品质量和竞争力
产业链整合:加强上下游产业 链整合,提高产业整体竞争力
冷轧机:用于将热轧后的 钢材进一步轧制成各种薄 板、带材等成品
轧制设备
轧制机:用于将金属材料轧制成各种形状和尺寸的设备
轧辊:用于轧制金属材料的主要部件,分为工作辊和支撑辊
轧制工艺:包括热轧和冷轧两种,热轧用于生产大型金属制品,冷轧用于生产小型金 属制品
轧制速度:影响轧制质量的重要因素,需要根据金属材料的性质和轧制要求进行调节
生物材料: 具有生物 相容性、 可降解性 等特性
智能材料: 具有自我 感知、自 我调节等 特性
环保材料: 具有可回 收、可降 解等特性
金属冶炼行业发 展趋势
绿色化发展
环保法规:政府对 环保的重视,推动 金属冶炼行业向绿 色化发展
技术进步:新技术、 新工艺的出现,使 得金属冶炼更加环 保、高效
市场需求:消费者 对环保产品的需求 ,推动金属冶炼行 业向绿色化发展
加热炉:用于加热钢坯的设备,可提高 钢坯的塑性和韧性
轧钢机:用于将钢坯轧制成各种钢材的 设备
炼钢设备
高炉:用于炼铁,将铁矿 石和焦炭等原料熔化成铁 水
转炉:用于炼钢,将铁 水转化为钢水
电炉:用于炼钢,利用电 弧热将废钢等原料熔化成 钢水
连铸机:用于将钢水连 续铸造成钢坯
热轧机:用于将钢坯轧 制成各种钢材
转炉炼钢工艺设备
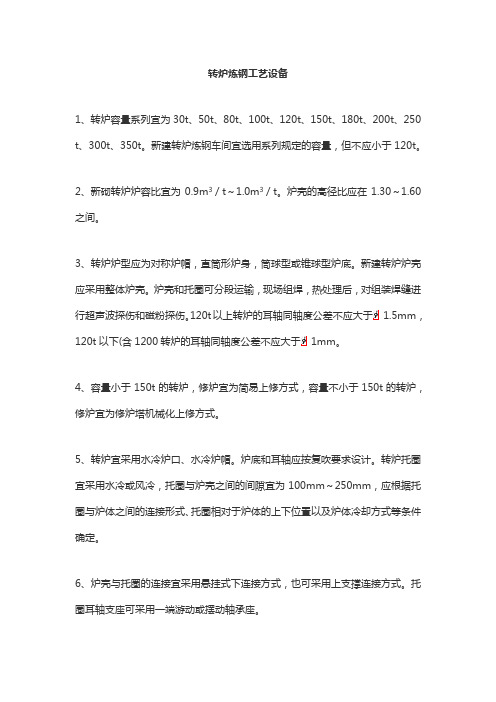
转炉炼钢工艺设备1、转炉容量系列宜为30t、50t、80t、100t、120t、150t、180t、200t、250 t、300t、350t。
新建转炉炼钢车间宜选用系列规定的容量,但不应小于120t。
2、新砌转炉炉容比宜为0.9m3/t~1.0m3/t。
炉壳的高径比应在1.30~1.60之间。
3、转炉炉型应为对称炉帽,直筒形炉身,筒球型或锥球型炉底。
新建转炉炉壳应采用整体炉壳。
炉壳和托圈可分段运输,现场组焊,热处理后,对组装焊缝进行超声波探伤和磁粉探伤。
120t以上转炉的耳轴同轴度公差不应大于 1.5mm,120t以下(含1200转炉的耳轴同轴度公差不应大于1mm。
4、容量小于150t的转炉,修炉宜为简易上修方式,容量不小于150t的转炉,修炉宜为修炉塔机械化上修方式。
5、转炉宜采用水冷炉口、水冷炉帽。
炉底和耳轴应按复吹要求设计。
转炉托圈宜采用水冷或风冷,托圈与炉壳之间的间隙宜为100mm~250mm,应根据托圈与炉体之间的连接形式、托圈相对于炉体的上下位置以及炉体冷却方式等条件确定。
6、炉壳与托圈的连接宜采用悬挂式下连接方式,也可采用上支撑连接方式。
托圈耳轴支座可采用一端游动或摆动轴承座。
7、转炉应采用全悬挂式倾动机构,平衡机构宜选用扭力杆型。
倾动宜采用交流变频技术,4台电机独立驱动,转速应为0.1r/min~1.5r/min。
转炉炉体可连续转动±360°。
能平稳倾动、准确停止在任意角度的位置上。
当出现冻炉塌炉事故时,4台电动机同时工作,转炉可以慢速倾动。
当1台电动机出现故障时,转炉以中等倾动速度倾动,可完成1天的生产。
当2台电动机出现故障时,转炉以慢速倾动,可完成1炉钢的生产。
8、转炉倾动力矩的设计应满足正常操作最大合成力矩的要求。
容量不大于200 t的转炉应按全正力矩设计,发生断电或机械故障时应能靠自重回复零位。
容量200t以上转炉宜采用正负力矩设计。
9、转炉应设置挡渣装置和出钢口衬砖更换设备,同时应配置机械化拆炉、补炉、修炉和溅渣护炉所需设施。
炼钢转炉设备
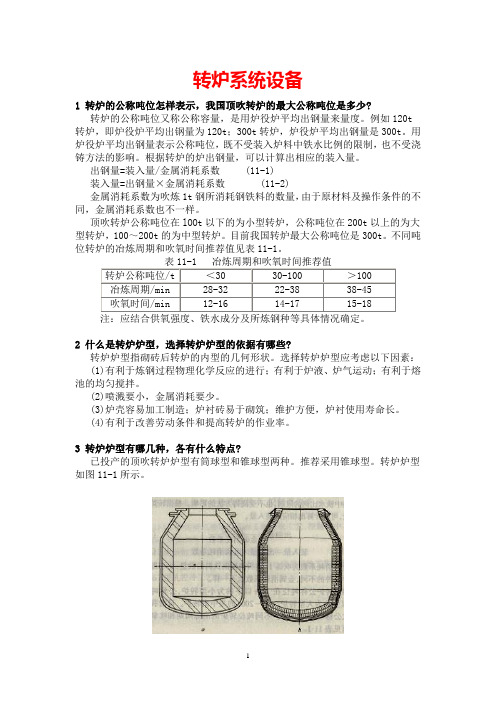
转炉系统设备1 转炉的公称吨位怎样表示,我国顶吹转炉的最大公称吨位是多少?转炉的公称吨位又称公称容量,是用炉役炉平均出钢量来量度。
例如120t 转炉,即炉役炉平均出钢量为120t;300t转炉,炉役炉平均出钢量是300t。
用炉役炉平均出钢量表示公称吨位,既不受装入炉料中铁水比例的限制,也不受浇铸方法的影响。
根据转炉的炉出钢量,可以计算出相应的装入量。
出钢量=装入量/金属消耗系数 (11-1)装入量=出钢量³金属消耗系数 (11-2)金属消耗系数为吹炼1t钢所消耗钢铁料的数量,由于原材料及操作条件的不同,金属消耗系数也不一样。
顶吹转炉公称吨位在lOOt以下的为小型转炉,公称吨位在200t以上的为大型转炉,100~200t的为中型转炉。
目前我国转炉最大公称吨位是300t。
不同吨位转炉的冶炼周期和吹氧时间推荐值见表11-1。
2 什么是转炉炉型,选择转炉炉型的依据有哪些?转炉炉型指砌砖后转炉的内型的几何形状。
选择转炉炉型应考虑以下因素: (1)有利于炼钢过程物理化学反应的进行;有利于炉液、炉气运动;有利于熔池的均匀搅拌。
(2)喷溅要小,金属消耗要少。
(3)炉壳容易加工制造;炉衬砖易于砌筑;维护方便,炉衬使用寿命长。
(4)有利于改善劳动条件和提高转炉的作业率。
3 转炉炉型有哪几种,各有什么特点?已投产的顶吹转炉炉型有筒球型和锥球型两种。
推荐采用锥球型。
转炉炉型如图11-1所示。
图11-1 顶吹转炉炉型示意图a一筒球型;b—锥球型(1)筒球型。
熔池由圆筒体与球缺体组合而成,如图11-1a所示。
它的特点是炉型简单,炉壳加工容易,内衬砌筑方便,有利炉内反应的进行。
如攀钢120t 转炉,太钢50t转炉等,都是筒球型的炉型。
(2)锥球型。
熔池由倒圆锥台体与球缺体组合而成,如图11-1b所示。
锥球型熔池更适合于炉液的运动,利于物理化学反应的进行,在熔池深度相同的情况下,若底部尺寸适当,熔池直径比筒球型相应大些,因而增加了反应面积,有利于脱除P、S。
转炉炼钢设备和工艺
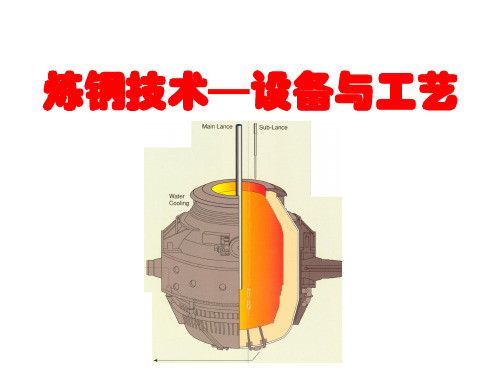
炉容比
选择炉容比时应考虑以下因素: (1)铁水比、铁水成分。随着铁水比和铁水中硅磷、硫含量的增 加炉容比应相应增大。若采用铁水预处理工艺时,炉容比可以小些 (2)供氧强度。供氧强度增大时,吹炼速度较快,为了不引起喷 溅就要保证有足够的反应空间,炉容比相应增大些。 (3)冷却剂的种类。采用铁矿石或氧化铁皮为主的冷却剂,成渣 量大,炉容比也需相应增大;若采用以废钢为主的冷却剂成渣量小, 则炉容比可适当选择小些 目前使用的转炉,炉容比波动在0.85 ~0.95之间(大容量转炉取 下限)。近些年来为了在提高金属收得率的基础上提高供氧强度,新 设计转炉的炉容比趋于增大,一般为0.9 ~1.05 。
炉型主要尺寸的确定
b)筒球形熔池: 圆柱体和球缺两部分组成。 考虑炉底稳定性和熔池适当深度,一般球缺体的半径R为熔 池直径的1.1~1.25倍。国外大于200t转炉为0.8~1.0倍。 当R=1.1D时,金属熔池的体积为:
V熔 0.79H0D2 0.046D3
因此:熔池深度为:
V熔 0.046D3 H0 0.79D 2
化学反应主要有: 2FeO+Si ——2Fe+SiO2 FeO+Mn—— Fe+MnO
生铁中硫、磷这两种元素在一般情况下对钢是有害的,在炼钢过 程中必须尽可能除去。在炼钢炉中加入石灰(CaO),可以去除硫、 磷: 2P+5FeO+3CaO—— 5Fe+Ca2(PO4)2(入渣) 在使碳等元素降到规定范围后,钢水中仍含有大量的氧,是有害 的杂质,使钢塑性变坏,轧制时易产生裂纹。故炼钢的最后阶段 必须加入脱氧剂(例如锰铁、硅铁和铝等),以除去钢液中多余的 氧: Mn+FeO ——MnO+Fe Si+2FeO—— SiO2+2Fe Al+3FeO ——Al2O3+3Fe 同时调整好钢液的成分和温度,达到要求可出钢,把钢水铸成连 铸坯或钢锭。
炼钢厂部分设备.doc

炼钢厂部分设备拉矫机拉矫机又叫拉弯矫直机组。
冷轧薄板经过退火后,往往会产生不佳的板形。
例如:带钢边部延伸比中部延伸大时就形成浪边;边部延伸比中部延伸小时就形成瓢曲。
为了达到后续加工要求,工厂里使用多种矫直方法,应用比较广泛的设备是多辊矫直机,薄板通过这种矫直机后,本身并不产生延伸,只是把大浪化为小浪,使板面近乎平直。
而对于板厚小于0.8mm的板材,用这种方法很难矫直。
而拉伸弯曲矫直机,可使薄板同时产生纵向和横向变形,从而充分改善薄板的平直度和材料性能,使薄板矫直技术大大提高了一步。
此外,由于通过弯曲产生了弯曲应力,大大减小了拉力,根据经验,采用拉伸弯曲矫直机时,要达到同样的矫直效果只需要纯拉伸矫直所需张力的1/3~1/5.而且它的矫直效果是迄今为止最好的。
拉伸弯曲矫直的主要作用是:1、可获得良好的板形。
通过拉伸弯曲矫直之后,可彻底消除板面的浪边、浪形、瓢曲及轻度的镰刀弯,从而,大大改善了薄板的平直度。
2、有利于改善材料的各向异性。
低碳钢的深冲薄板在纵向和横向上的屈服极限常常存在各向异性。
所以在薄板作深冲加工时,由于各部的延伸不同被冲件的各部厚度会产生不均,从而会使被冲件产生裙状花边缺陷,由此而导致冲废率的增高。
通过拉伸弯曲矫直之后,会使这种状况大大得到改善。
3、消除屈服平台、阻止滑移线的形成!拉矫机是用于连铸拉钢过程中给钢坯施加一个向前的拉力,钢水在结晶器里面一边凝固一边出钢坯,实现一个连铸的过程,不然钢坯不会自己走啊.转炉1)转炉炼钢法这种炼钢法使用的氧化剂是氧气。
把空气鼓入熔融的生铁里,使杂质硅、锰等氧化。
在氧化的过程中放出大量的热量(含1%的硅可使生铁的温度升高200摄氏度),可使炉内达到足够高的温度。
因此转炉炼钢不需要另外使用燃料。
转炉炼钢是在转炉里进行。
转炉的外形就像个梨,内壁有耐火砖,炉侧有许多小孔(风口),压缩空气从这些小孔里吹炉内,又叫做侧吹转炉。
开始时,转炉处于水平,向内注入1300摄氏度的液态生铁,并加入一定量的生石灰,然后鼓入空气并转动转炉使它直立起来。