不锈钢切削用量表
车削切削用量选取参考表

0.40
0.1
外圆纵车
(Kr=0°)
YG6
(用切削液)
f≥αp
208
0.4
0.2
0.28
f>αp
208
0.2
0.4
0.28
切断及切槽
YG6(不用液)
?
?
高速钢(不用液)
?
18
?
可锻铸铁
外圆纵车
YG8
(不用切削液)
f≤
206
0.15
0.20
0.2
f>
140
0.15
0.45
0.2
高速钢
(用切削液)
速度计算的修正系数
切深αp(mm)
进给量f(mm/r)
kMv
ksv
kiv
kkr
k,krv
krεv
kBv
kkv
150
60
1
1
1
1
1
1
1
KV
Tm
αpxv
fyv
切削速度? v(m/min)
主轴转速(r/min)
128
270
注:1、有批注的所有表格均需录入数据。????????????????????????????????????????????????????????????
公式中的系数和指数
CV
XV
yV
m
碳素结构钢σb=
外圆纵车
(Kr>0°)
YT15
(不用切削液)
f≤
291
f≤
242
0.15
0.35
0.20
f>
235
0.15
0.45
0.20
切削用量推荐表

断续加工 粗加工 4 0.2 35 精加工 1.3 0.1 60
回转件切削点的回转直径(mm) 粗加工回转件最大允许转速值(rpm) 粗加工回转件最大允许转速值(rpm)
160 139 239
表4-3 刀具材 料 工件材料 碳钢 低合金刚 高合金钢 铸铁 硬质合 金或涂 层硬质 合金 不锈钢 钛合金 灰铸铁 球墨铸铁 铝合金
硬质合金刀具切削用量推荐表 粗 加 mm/r 0.2 0.2 0.2 0.2 0.2 0.2 0.2 0.3 0.2 0.3 0.3 0.2 0.3 0.2 工 背吃刀量 mm 3 3 3 3 3 3 2 1.5 1.5 2 2 2 1.5 切削速度 m/min 260 220 220 160 140 · 140 120 60 60 150 150 120 120 1600 精 加 mm/r 0.l 0.l 0.1 0.l 0.l 0.1 0.l 0.l 0.1 0.15 0.15 0.15 0.15 0.l 工 背吃刀量 mm 0.4 0.4 0.4 0.4 0.4 0.4 0.5 0.5 0.5 进给量
刀具材料
粗加工 碳素钢 精加工 σb >600M 钻中心孔 Pa 钻孔 切断(宽度 <5mm) 粗加工 铸铁 HBS<2 精加工 切断(宽度 00 <5mm)
YT类
W1算取值及回转件最大允许转速值计算公式 项目 背吃刀量不大于(mm) 进给量不大于(mm/r) 切削速度不大于 (m/min) 回转件切削点的回转直 径(mm) 回转件最大允许转速值 (rpm) ap f vc d n vc/(3.14*d)*1000 粗加工 6 0.3 70 精加工 2 0.15 120 0.15 30 钻孔
切削速度 进给量 m/min 220 180 120 80 80 40 120 100 1600
切削用量表格

高锰钢wmn13%
10-20
铜及铜合金
200-250
120-180
90-120
铝及铝合金
300-600
200-400
150-200
铸铝合金wsi13%
100-180
80-150
60-100
注:切削钢及铸铁时刀具耐用度约为60min。
表二:按表面粗糙度选择进给量的参考值
工件材料
表面粗糙度
Ra/μm
表三:硬质合金车刀粗车外圆及端面的进给量
工件材料
车刀刀杆
尺寸
B×H/mm
工件直径
dw/mm
背吃刀量ap/mm
≤3
>3~5
>5~8
>8~12
>12
进给量f(mm/r)
碳素结构钢、
合金结构钢
及耐热钢
16×25
20
40
60
100
400
0.3~0.4
0.4~0.5
0.5~0.7
0.6~0.9
0.8~1.2
—
碳钢
及
合金钢
>5~10
<50
>50
0.30~0.50
0.40~0.55
0.45~0.60
0.55~0.65
0.55~0.70
0.65~0.70
>2.5~5
<50
>50
0.18~0.25
0.25~0.30
0.25~0.30
0.30~0.35
0.30~0.40
0.30~0.50
>1.25~2.5
<50
50~100
铣削切削用量选择表

铣削平面及凸台
铣削速度 v(m/min)
铣刀直
径 d0 mm
每齿进给量 fa (mm/z)
20-27 25~50
0.075
32-46
10
0.025
24-34
10
0.05
21-29
10
0.025
18-24
10
0.018
32-46
12
0.05
24-34
12
0.075
21-29
12
0.05
18-24
12
0.025
铣削平面及凸台
铣削速度 v(m/min)
铣刀直
径 d0 mm
每齿进给量 fa (mm/z)
20-24
10
0.038
18-21
10
0.025
30-37
12
0.05
23-27
12
0.075
20-24
12
0.05
18-21
12
0.038
30-37
18
0.075
23-27
18
0.102
20-24
18
0.075
26-37
12
0.075
3
24~27
12
23-32
12
0.05
d0/2 21~24
12
20-27
12
0.025
d0 18~20
12
34-49
18
0.075
0.75 26~29
18
26-37
18
0.102
3
24~27
18
23-32
机械加工工种定额、工时(车、铣、镗)切削用量参考表(工时计算)

定额工时参照表
硬质合金车刀粗车外圆端面的进给量(参考值)
硬质合金外圆车刀精车的进给量(参考值) mm/r
注:1、加
工断续表面
及有冲击的
工件时,表
内进给量应
乘系数K=
0.65~
0.75;
2、在
无外皮加工
时,表内进
给量应乘第
数K=1.1;
3、加工耐热钢及其合金时,进给量不大于
0.6mm/r; 4、加工调质钢时,乘以系数K=0.8;
6、可转位刀片的允许最大进给量不应超过其刀尖圆弧半径数值的80%。
工件材 2、表中较小 3、 5、加工淬硬钢时,进给量应减小.当钢的硬度为44~56HRC时,乘系数K=0.7;当钢的硬度为57~62HRC时,乘系数K=0.5。
7、rε=0.5mm,用于12×12以下刀杆,rε=1mm,用于30×30以下刀杆,rε=2mm,用于30×45及以上刀杆。
车不锈钢的常用切削用量
铣刀每齿进给量fz的推荐值
或手动
和三面刃削速度及进给量均应适当减
小。
加工中心刀具切削用量表

线速度(米/分钟) 铝 高速钢铣刀 镀层硬质合金铣刀 硬质合金铣刀
加工中心刀具切削用量表
45# 60 100~300 100~300
淬硬钢 15~20
60
铸铁 15~20
30
15~20 60 30
S(转速)=线速度×1000/(直径×3.14) F(进给量)=刃数×每刃切削量×转速
每刃切削量 粗加 ~ 0.05
例:20MM硬质合金4刃铣刀精铣45#钢,线速度取60。每刃切0.05。则转速=60×1000/(20×3.14) =955,进给量=4×0.05×955=191。
以上是比较笼统的概括,适用于大多数铣刀、钻头、镗刀(不包括绞刀)加工工艺的计算。在实 际加工中还要针对不同实际情况做出调整。如:工件形状、余量大小、冷却条件、刀具磨损等。
每刃切削量参数的选择:如果太小小于0.02,那不是在切削,是在磨刀,如果太大大于0.2,那也 不是切削,是在撞击。所以并非转速越高,进给量越小越好切削,刀具必须处在一个合理的运动 状态下,才是均质、稳定的切削。
刀具加工中,对刀具寿命影响最大的是线速度,刀具商提供刀具的同时,应该会提供一份刀具针 对各种材料的线速度表,但刀具供应商的参数是在理想状态下得到的,在实际加工中,得打个 7~8折的。
常用切屑用量计算公式

�
N铝=2388rpm =2388rpm vf铝=2865mm/r vf铝=2865mm/r p铝=9.16kw =9.16kw T铝=36Nm =36Nm N不锈钢=597rpm 不锈钢=597rpm vf不锈钢=716mm/r vf不锈钢 不锈钢=716mm/r p不锈钢=6.87kw 不锈钢=6.87kw T不锈钢=109Nm 不锈钢=109Nm
P= Kc×f×Vc ×(D2-d2) D × 240000 × η
D: hole diameter d: core diamerer
T= F力 x(D/2) =P x9549/RPM 钻削功率P 钻削功率P=4500 × 0.07 ×40 ×20/240000 ×0.9=1.2KW 转速 n=40 ×1000/3.14 ×20=636rpm 扭矩 T=1.2 ×xD xRPM 1000 V=Vc xap xfr(mm3/min) L Time= fr xN Vc xap xfr xkc P= 60037.2 F力=Kc xfr xap
举例:车削奥氏体不锈钢外圆,工件硬度HB200, 工 件直径75mm,切深3mm,走刀量0.2mm/r, 切削速度 230m/min, 材料单位切削力为2900N/mm2,加工长度 为100mm RPM=(230X1000)/(3.14X75)=976转每分钟 金属去除率V=230x3x0.2=92 立方厘米每分 钟 每加工一个零件的时间=100/(0.2x976)=0.51 分钟 车削功率P=(230x3x0.2x2900)/60037.2=6.7 千瓦 车削力=2900 x0.2 x3=1740牛顿=177.5公斤 车削扭矩T=1740 x37.5=65牛顿米
U钻钻削功率和扭矩的计算 Power consuming and Torque force
车削切削用量选取参考表

三、按表面粗糙度选择进给量的参考值
工件材料
粗糙度等级(Ra)
切削速度(m/min)
刀尖圆弧半径
0.5
1
2
进给量f mm/r
碳钢及合金碳钢
10~5
≤50
0.3~0.5
0.45~0.6
1
0.3
1.1
0.3
—
—
—
—
>18~30
1
0.3
1
0.3
1.1
0.3
1.3
0.4
1.4
0.4
—
—
>30~50
1.1
0.3
1
0.3
1.1
0.4
1.3
0.5
1.5
0.6
1.7
0.6
>50~80
1.1
0.3
1.1
0.4
1.2
0.4
1.4
0.5
1.6
0.6
1.8
0.7
>80~120
1.1
0.4
1.2
0.4
1.2
铸铁及铜合金
16×25
40
0.4~0.5
—
—
—
—
60
0.6~0.8
0.5~0.8
0.4~0.6
—
—
100
0.8~1.2
0.7~1
0.6~0.8
0.5~0.7
—
400
1~1.4
1~1.2
0.8~1
0.6~0.8
不锈钢加工参数表

不锈钢加工参数表1. 切削速度:切削速度是指在切削过程中,刀具与工件接触点处的线速度。
不锈钢的切削速度通常在20-60m/min之间,具体数值取决于刀具材料、刀具几何形状、工件材料和加工要求等因素。
切削速度过高可能导致刀具磨损加快,切削力增大,加工精度降低;切削速度过低则可能导致刀具寿命降低,加工效率降低。
2. 进给速度:进给速度是指刀具在切削过程中沿工件进给方向的移动速度。
不锈钢的进给速度通常在0.1-0.5mm/r之间,具体数值取决于刀具材料、刀具几何形状、工件材料和加工要求等因素。
进给速度过高可能导致刀具磨损加快,切削力增大,加工精度降低;进给速度过低则可能导致刀具寿命降低,加工效率降低。
3. 切削深度:切削深度是指刀具在一次切削过程中切入工件的深度。
不锈钢的切削深度通常在0.1-0.5mm之间,具体数值取决于刀具材料、刀具几何形状、工件材料和加工要求等因素。
切削深度过大可能导致刀具磨损加快,切削力增大,加工精度降低;切削深度过小则可能导致刀具寿命降低,加工效率降低。
4. 切削宽度:切削宽度是指刀具在一次切削过程中切入工件的宽度。
不锈钢的切削宽度通常在2-10mm之间,具体数值取决于刀具材料、刀具几何形状、工件材料和加工要求等因素。
切削宽度过大可能导致刀具磨损加快,切削力增大,加工精度降低;切削宽度过小则可能导致刀具寿命降低,加工效率降低。
5. 切削油或冷却液:不锈钢加工过程中,为了降低切削温度,减少刀具磨损,提高加工精度和表面质量,通常需要使用切削油或冷却液。
切削油或冷却液的选择应根据不锈钢材料、刀具材料、加工条件等因素进行。
常用的切削油或冷却液有矿物油、乳化液、水溶性切削液等。
6. 刀具材料:不锈钢加工过程中,常用的刀具材料有高速钢、硬质合金、陶瓷、金刚石等。
不同材料的刀具对不锈钢的加工性能和加工效果有很大影响。
选择合适的刀具材料可以提高加工效率,延长刀具寿命,提高加工精度和表面质量。
不锈钢的铣削加工参数

不锈钢的铣削加工参数不锈钢是一种常用的金属材料,广泛应用于工业制造和建筑领域。
铣削加工是一种常见的金属加工方法,通过切削工具在工件表面进行旋转切削,从而得到所需形状和尺寸的工件。
在不锈钢的铣削加工过程中,需要考虑多个参数,以确保加工质量和效率。
以下将介绍一些常见的不锈钢铣削加工参数。
1. 铣削切削速度(Cutting Speed)铣削切削速度是指刀具在工件表面的切削速度。
对于不锈钢材料,由于其硬度较高,切削速度应相对较低。
通常,不锈钢的切削速度范围为30-60m/min,具体数值需要根据具体材料和刀具来确定。
2. 进给速度(Feed Rate)进给速度是指刀具在横向方向上的移动速度,即每刀齿每转所移动的距离。
对于不锈钢材料,进给速度应适中,过低容易造成切削过热,过高则会降低切削效率。
通常,不锈钢材料的进给速度范围为0.1-0.3mm/tooth。
3. 刀具转速(Spindle Speed)刀具转速是指刀具在加工过程中的旋转速度。
对于不锈钢材料,刀具转速应较低,避免因过高的转速导致切削过热。
通常,不锈钢材料的刀具转速范围为500-3000rpm。
4. 切削深度(Cutting Depth)切削深度是指每次切削时刀具进入工件的深度。
对于不锈钢材料,切削深度应适中,过深容易导致切削过热和刀具磨损加剧。
通常,不锈钢材料的切削深度范围为0.5-3mm,具体数值需要根据具体材料和刀具来确定。
5. 切削润滑方式(Coolant)切削润滑是指在铣削加工过程中使用润滑剂来降低切削温度和减少切削力。
对于不锈钢材料,由于其导热性较低,应使用润滑剂来改善切削状况。
常见的切削润滑方式包括湿式切削和干式切削。
湿式切削可以通过冷却剂或润滑油来降低切削温度,减少刀具磨损;干式切削则需要通过空气或其他方式来冷却切削区域。
6.刀具材料和刀具形状选择合适的刀具材料和刀具形状也是不锈钢铣削加工的关键。
不锈钢材料的硬度高,切削性能差,因此需要采用高硬度和高耐磨抗热的刀具材料,如硬质合金刀具。
不锈钢的铣削加工参数
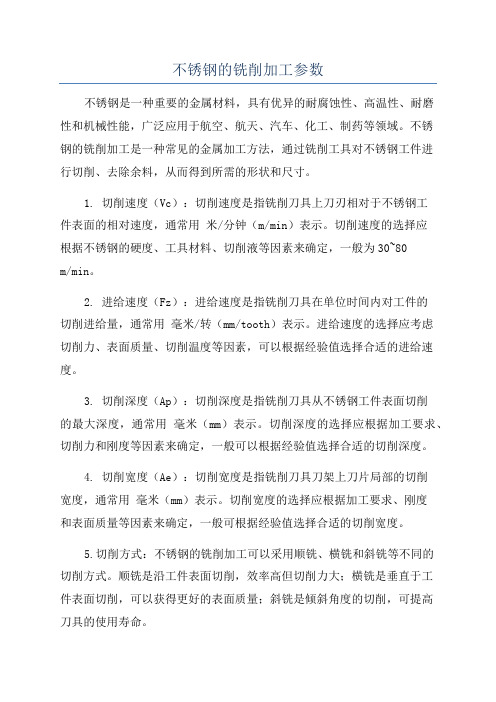
不锈钢的铣削加工参数不锈钢是一种重要的金属材料,具有优异的耐腐蚀性、高温性、耐磨性和机械性能,广泛应用于航空、航天、汽车、化工、制药等领域。
不锈钢的铣削加工是一种常见的金属加工方法,通过铣削工具对不锈钢工件进行切削、去除余料,从而得到所需的形状和尺寸。
1. 切削速度(Vc):切削速度是指铣削刀具上刀刃相对于不锈钢工件表面的相对速度,通常用米/分钟(m/min)表示。
切削速度的选择应根据不锈钢的硬度、工具材料、切削液等因素来确定,一般为30~80m/min。
2. 进给速度(Fz):进给速度是指铣削刀具在单位时间内对工件的切削进给量,通常用毫米/转(mm/tooth)表示。
进给速度的选择应考虑切削力、表面质量、切削温度等因素,可以根据经验值选择合适的进给速度。
3. 切削深度(Ap):切削深度是指铣削刀具从不锈钢工件表面切削的最大深度,通常用毫米(mm)表示。
切削深度的选择应根据加工要求、切削力和刚度等因素来确定,一般可以根据经验值选择合适的切削深度。
4. 切削宽度(Ae):切削宽度是指铣削刀具刀架上刀片局部的切削宽度,通常用毫米(mm)表示。
切削宽度的选择应根据加工要求、刚度和表面质量等因素来确定,一般可根据经验值选择合适的切削宽度。
5.切削方式:不锈钢的铣削加工可以采用顺铣、横铣和斜铣等不同的切削方式。
顺铣是沿工件表面切削,效率高但切削力大;横铣是垂直于工件表面切削,可以获得更好的表面质量;斜铣是倾斜角度的切削,可提高刀具的使用寿命。
6.刀具选择:不锈钢的铣削刀具应选择高硬度、高耐磨性的刀具材料,如硬质合金、高速钢等。
刀具的形状和刃数也应根据加工要求选择合适的类型。
在铣削不锈钢时,还需要注意以下几点:1.选择合适的切削液:切削液能够冷却刀具和工件,并降低切削温度,减少切削力和摩擦,改善表面质量。
常用的切削液有油基切削液和水溶性切削液,应根据切削工艺和加工要求选择合适的切削液。
2.注意切削力和切屑排除:不锈钢的铣削容易产生较大的切削力和切屑,需要加强刀具的刚度和排屑能力,避免卡刀和切削过程中产生的振动和噪声。
不锈钢的车削参数

不锈钢的车削参数不锈钢是一种耐腐蚀、耐高温的金属材料,常用于制造机械零件、压力容器、航空航天器械等领域。
在进行车削加工时,需要根据不锈钢的特性和要求选择合适的车削参数,以达到理想的加工效果。
一、切削速度(vc)切削速度是车刀在工件表面移动的速度,也是车削过程中最基本的参数。
不锈钢的切削速度较低,一般在30-60m/min之间。
过高的切削速度会导致刀具过热、磨损加剧,影响切削质量和加工效率;过低的切削速度则会造成切削力增大,刀具负荷过大,甚至造成刀具断裂。
二、进给速度(f)进给速度是指车刀在单位时间内向工件进给的量。
在车削不锈钢时,进给速度一般在0.05-0.15mm/r之间。
进给速度过高会造成刀具磨损加剧、表面质量下降;进给速度过低则会导致车削效率低下。
需要根据具体材料硬度和刀具的质量要求来确定合适的进给速度。
三、切削深度(ap)切削深度是指车刀在一次切削过程中,刀尖与工件表面的距离。
不锈钢的切削深度一般在0.5-4mm之间,具体取决于工件的硬度和刀具的强度。
切削深度过大会增加切削力,容易造成刀具断裂;切削深度过小则会导致车削效率低下。
四、切削角度(γ)切削角度是指车刀主切削刃与工件表面的切削角。
在车削不锈钢时,一般选择切削角较小的刀具,如30度左右。
切削角较小的刀具可以减小切削力,提高刀具的切削性能和寿命。
五、冷却液由于不锈钢的切削过程会产生较高的温度,因此在车削不锈钢时需要使用冷却液进行冷却和润滑。
冷却液的选择应根据不锈钢的材质和车削过程的具体要求来确定,以保证切削效果和刀具的使用寿命。
六、切削工具选择不锈钢的切削难度较大,对切削工具的要求也比较高。
一般采用硬质合金或散热钨钢制成的切削工具。
此外,还可以通过涂覆刀具和刀具几何形状的优化来提高不锈钢的切削效果。
总结起来,车削不锈钢需要根据不锈钢的特性和要求选择适当的车削参数,包括切削速度、进给速度、切削深度、切削角度等。
同时还需要选择合适的切削工具和冷却液,以保证切削效果和刀具的使用寿命。
刀具切削用量表

车削时,工件加工表面最大直径处的线速度称为切削速度,以v(m/min)表示。
其计算公式:v=πdn/1000(m/min) 式中:d——工件待加工表面的直径(mm)
n——车床主轴每分钟的转速(r/min)
工件每转一周,车刀所移动的距离,称为进给量,以f(mm/r)表示;车刀每一次切去的金属层的厚度,称为切削深度,以ap(mm)表示。
说明:①刀具材料代号说明
G —高速钢
YT —钨钛钴硬质合金
YG —钨钴类硬质合金
YS —超细硬质合金
YW —通用硬质合金
T —陶瓷
PCD —人造聚晶金刚石复合片
PCBN —立方氮化硼复合片
②参数选择说明
A、粗车时,选用低的切削速度,大的切削深度和进给量。
B、精车时,选用高的切削速度,小的切削深度和进给量。
C、高速钢刀具精车时采用Vc小于10m/min的切削速度以控制积屑瘤产生,降低钢件粗糙度。
D、对铸钢件,粗车应选比较低的切削速度。
E、断续切削时,刀具前角适当减小。
F、刀具材料抗弯强度低,γ0应减小到0~5°。
部分切削用量表

部分工件加工刀具切削用量表"Sheet1","部分工件加工刀具切削用量表(钢材)""刀具大小", "开粗下刀量", "光刀下刀量" ,"开粗进给", "精加工进给", "开粗转数","光刀转数""圆鼻刀","63R5" 0.5, "0.25-0.3", "3000以上", "2000-3000", 1000, 3000,"40R6", 0.5, "0.25-0.3" ,"3000以上", "2000-3000", 1200, 3000,"30R5", 0.5, "0.25-0.3", "3000以上", "2000-3000", "1800-2500","3000以上" ,"25R0.8", "0.3-0.35", "0.15-0.18", "3000以上", "2000-3000", "2200-2600","3000以上" ,"20R0.8", 0.3, "0.15-0.18", 3000, "2000-3000" , 2500, "3000以上" ,"16R0.8", 0.3, "0.15-0.18", 3000, "1800-2700", 2500, "3000以上" ,"12R0.8", "0.25-0.3", "0.15-0.18", "2500-3000", "2000 左右", "2800-3000", "3000以上" ,"刀具大小", "开粗下刀量", "光刀下刀量", "开粗进给", "精加工进给", "开粗转数", "光刀转数" "合金平底刀","D25","D20","D16","D12", 0.3, "大于0.1", 3000, "1800-2300", "2500-3000", "3000以上" ,"D10", 0.25,, "2500-3000", "1800-2300", "2500-3000", "3000以上" ,"D8", 0.2,, "2500-3000", "1800-2300", 3000, "3000以上" ,"D6", "0.15-0.18", ,"2300-2500", "1800-2300", 3000, "3000以上" ,"D5", 0.15,, "2300-2500", "1800-2300", 3200, "3000以上" ,"D4", 0.12,, "2000-2500", "1500-2000", 3200, "3500-4000" ,"D3" , 0.1,, "1800-2300", "1500-2000", 3500, "3500-4000" ,"D2.5", "0.08-0.1", ,1800, "1500-2000", 3500, "3500-4000" ,"D2" , 0.07, "0.05-0.07", "1800-2000", 1500, 4000, 4000 ,"刀具大小", "开粗下刀量", "光刀下刀量", "开粗进给" , "精加工进给", "开粗转数", "光刀转数" "球刀","R10","R8", "0.5-0.6", "0.2-0.25", 3000, "2000左右", 3000, 3500 ,"R6", "0.5-0.6", "0.18-0.2", 3000, "2000左右", 3000, 3500 ,"R5", 0.5, 0.15, 3000, "2000左右", 3000, 3500 ,"R4", 0.5, 0.14, 3000, "2000左右", 3000, 3500 ,"R3" , 0.3, 0.13, 3000, "2000左右", 3200, 3500 ,"R2.5", 0.2, 0.1, 2500, 1800, 3200, 3500 ,"R2", 0.15, 0.1, 2300, "1500-1800" ,3200, 3500 ,"R1.5", 0.1, 0.08, 2000, 1500, 3500, 3800 ,"R1",, 0.05, "1500-1800", "1200-1500", 3500, 4000 ,"R0.5",, "0.03-0.05", "1200-1500", 1000, 3800, 4000 ,"部分工件加工刀具切削用量表(铜料)","刀具大小","开粗下刀量","光刀下刀量","开粗进给","精加工进给","开粗转数","光刀转数""圆鼻刀","63R5","40R6","30R5","25R0.8","20R0.8","16R0.8","12R0.8","刀具大小","开粗下刀量","光刀下刀量","开粗进给","精加工进给","开粗转数","光刀转数" "白钢平底刀","D25","0.5-1",,"3000-6000",400,1000,500,"D20","0.5-1",,"3000-6000",400,1200,500,"D16","0.5-1",,"3000-6000",400,"1200-1500",500,"D12","0.3-0.5",,"2500-3000",400,1800,"700-1500","D10","0.3-0.5",,2500,"2000以内","2500-3000",3500,"D8","0.2-0.4",,2500,"2000以内",3000,3500,"D6","0.2-0.3",,2500,"2000以内",3200,3500,"D5",0.2,,2500,"2000以内",3200,3800,"D4","0.15-0.2",,2500,"1500-1800",3500,3800,"D3",0.15,,"2200-2500","1200-1500",3500,3800,"D2.5","0.12-0.15",,"2200-2500","1200-1500",3500,4000,"D2",0.07,,2000,1000,"3800-4000",4200,"刀具大小","开粗下刀量","光刀下刀量","开粗进给","精加工进给","开粗转数","光刀转数" "球刀","R10",,"0.25-0.3",,"2000以内",,3500,"R8",,"0.2-0.25",,"2000以内",,3500,"R6",,"0.15-0.18",,"2000以内",,3500,"R5",,0.15,,"2000以内",,3500,"R4",,0.14,,"2000以内",,3500,"R3",,0.13,,"1500-1800",,4000,"R2.5",,"0.1-0.12",,"1500-1800",,4000,"R2",,"0.08-0.1",,"1200-1500",,4000,"R1.5",,"0.05-0.07",,1200,,4200,"R1",,"0.03-0.05",,"1000-1200",,"4200-4500","R0.5",,0.03,,"800-1000",,"4500-5000"。
常用加工的切削参数参考表

工件磨削表面面直径D
mm
加工材料
非淬火钢及铸铁
淬火钢及耐热钢
V(m/min)
N(r/min)
V(m/min)
N(r/min)
30
18-35
191-382
22-35
243-382
50
20-40
127-254
25-40
159-254
80
25-50
100-200
30-50
120-200
常用加工的切削参数参考表
1、常用硬质合金或涂层硬质合金切削不同材料时的切削用量推荐值见下表
刀具材料
工件材料
粗加工
精加工
切削速度(m/min
进给量(mm/r)
背吃刀量mm
切削速度(m/min
进给量(mm/r)
背吃刀量mm
硬质合金或涂层硬质合金
碳钢
220
0.2
3
260
0.l
0.4
低合金刚
180
0.2
3
220
公制螺纹:t<1 dz=d-t
t>1 dz=d-(1.04-1.06)t
其中:t――螺距离d――螺纹公制直径dz――攻丝前钻头直径
7、铰孔余量见表
孔直径(mm)
<5
5-20
21-32
33-50
51-70
铰削余量(mm)
0.1-0.2
0.15-0.25
0.20-0.3
0.25-0.35
0.25-0.35
0.4
13
0.45
13
0.5
13
3-8
走刀量
切削速度
0.12
(完整版)钻削切削用量选择参考表

钻削切削用量选择参考表一、钻中心孔的切削用量钻中心孔公称直径钻中心孔的切削进给量钻中心孔切削速度刀具名称(mm) (mm/r) v(m/min) 中心钻 1 0.02 8~15中心钻 1.6 0.02 8~15中心钻 2 0.04 8~15中心钻 2.5 0.05 8~15中心钻 3.15 0.06 8~15中心钻 4 0.08 8~15中心钻 5 0.1 8~15中心钻 6.3 0.12 8~15中心钻8 0.12 8~1560 °中心锪钻及带锥柄 60 °中心锪钻 1 0.01 12 ~2560 °中心锪钻及带锥柄 60 °中心锪钻 1.6 0.01 12 ~2560 °中心锪钻及带锥柄 60 °中心锪钻 2 0.02 12 ~2560 °中心锪钻及带锥柄 60 °中心锪钻 2.5 0.03 12 ~2560 °中心锪钻及带锥柄 60 °中心锪钻 3.15 0.03 12 ~2560 °中心锪钻及带锥柄 60 °中心锪钻 4 0.04 12 ~2560 °中心锪钻及带锥柄 60 °中心锪钻 5 0.06 12 ~2560 °中心锪钻及带锥柄 60 °中心锪钻 6.3 0.08 12 ~2560 °中心锪钻及带锥柄 60 °中心锪钻8 0.08 12 ~25不带护锥及带护锥的60 °复合中心钻 1 0.01 12 ~25不带护锥及带护锥的60 °复合中心钻 1.6 0.01 12 ~25不带护锥及带护锥的60 °复合中心钻 2 0.02 12 ~25不带护锥及带护锥的60 °复合中心钻 2.5 0.03 12 ~25不带护锥及带护锥的60 °复合中心钻 3.15 0.03 12 ~25不带护锥及带护锥的60 °复合中心钻 4 0.04 12 ~25不带护锥及带护锥的60 °复合中心钻 5 0.06 12 ~25不带护锥及带护锥的60 °复合中心钻 6.3 0.08 12 ~25不带护锥及带护锥的60 °复合中心钻8 0.08 12 ~25二、高速钢钻头切削用量选择表钻孔的进给量 (mm/r)钻头直径钢σ钢σb(MPa) 钢σ铸铁、铜及铝合铸铁、铜及铝合金do(mm) b(MPa)<800 800 ~ 1000 b(MPa)>1000 金 HB ≤200 HB>200 ≤2 0.05 ~ 0.06 0.04 ~ 0.05 0.03 ~ 0.04 0.09 ~ 0.11 0.05 ~0.072 ~ 4 0.08 ~ 0.10 0.06 ~ 0.08 0.04 ~ 0.06 0.18 ~ 0.22 0.11 ~0.134 ~ 6 0.14 ~ 0.18 0.10 ~ 0.12 0.08 ~ 0.10 0.27 ~ 0.33 0.18 ~0.226 ~ 8 0.18 ~ 0.22 0.13 ~ 0.15 0.11 ~ 0.13 0.36 ~ 0.44 0.22 ~0.268~ 10 0.22 ~ 0.28 0.17 ~ 0.21 0.13 ~ 0.17 0.47 ~ 0.57 0.28 ~0.3410 ~13 0.25 ~ 0.31 0.19 ~ 0.23 0.15 ~ 0.19 0.52 ~ 0.64 0.31 ~0.3913 ~16 0.31 ~ 0.37 0.22 ~ 0.28 0.18 ~ 0.22 0.61 ~ 0.75 0.37 ~0.4516 ~20 0.35 ~ 0.43 0.26 ~ 0.32 0.21 ~ 0.25 0.70 ~ 0.86 0.43 ~0.5320 ~25 0.39 ~ 0.47 0.29 ~ 0.35 0.23 ~ 0.29 0.78 ~ 0.96 0.47 ~0.5625 ~30 0.45 ~ 0.55 0.32 ~ 0.40 0.27 ~ 0.33 0.9 ~ 1.1 0.54 ~0.6630 ~50 0.60 ~ 0.70 0.40 ~ 0.50 0.30 ~ 0.40 1.0 ~ 1.2 0.70 ~0.80注 :1.表列数据适用于在大刚性零件上钻孔,精度在H12 ~H13 级以下(或自由公差),钻孔后还用钻头、扩孔钻或镗刀加工,在下列条件下需乘修正系数;1).在中等刚性零件上钻孔(箱体形状的薄壁零件、零件上薄的突出部分钻孔)时,乘系数0.75 ;2).钻孔后要用铰刀加工的精确孔,低刚性零件上钻孔,斜面上钻孔,钻孔后用丝锥攻螺纹的孔,乘系数 0.50 ;2.钻孔深度大于 3 倍直径时应乘修正系数。