高架桥式高速五坐标龙门加工中心动态仿真与结构优化
超重型龙门式加工中心的结构设计与优化
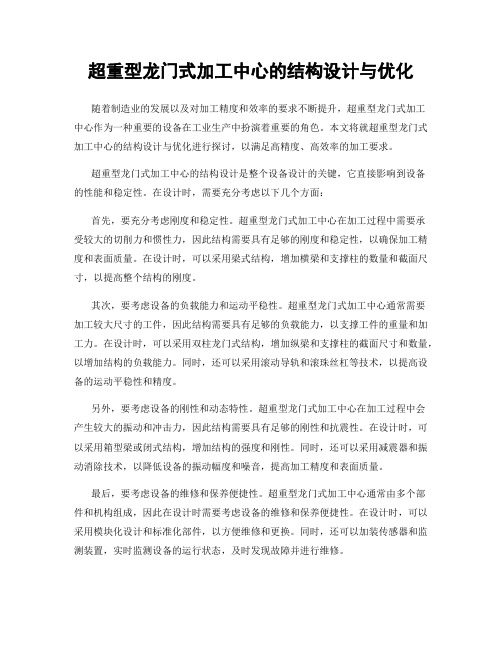
超重型龙门式加工中心的结构设计与优化随着制造业的发展以及对加工精度和效率的要求不断提升,超重型龙门式加工中心作为一种重要的设备在工业生产中扮演着重要的角色。
本文将就超重型龙门式加工中心的结构设计与优化进行探讨,以满足高精度、高效率的加工要求。
超重型龙门式加工中心的结构设计是整个设备设计的关键,它直接影响到设备的性能和稳定性。
在设计时,需要充分考虑以下几个方面:首先,要充分考虑刚度和稳定性。
超重型龙门式加工中心在加工过程中需要承受较大的切削力和惯性力,因此结构需要具有足够的刚度和稳定性,以确保加工精度和表面质量。
在设计时,可以采用梁式结构,增加横梁和支撑柱的数量和截面尺寸,以提高整个结构的刚度。
其次,要考虑设备的负载能力和运动平稳性。
超重型龙门式加工中心通常需要加工较大尺寸的工件,因此结构需要具有足够的负载能力,以支撑工件的重量和加工力。
在设计时,可以采用双柱龙门式结构,增加纵梁和支撑柱的截面尺寸和数量,以增加结构的负载能力。
同时,还可以采用滚动导轨和滚珠丝杠等技术,以提高设备的运动平稳性和精度。
另外,要考虑设备的刚性和动态特性。
超重型龙门式加工中心在加工过程中会产生较大的振动和冲击力,因此结构需要具有足够的刚性和抗震性。
在设计时,可以采用箱型梁或闭式结构,增加结构的强度和刚性。
同时,还可以采用减震器和振动消除技术,以降低设备的振动幅度和噪音,提高加工精度和表面质量。
最后,要考虑设备的维修和保养便捷性。
超重型龙门式加工中心通常由多个部件和机构组成,因此在设计时需要考虑设备的维修和保养便捷性。
在设计时,可以采用模块化设计和标准化部件,以方便维修和更换。
同时,还可以加装传感器和监测装置,实时监测设备的运行状态,及时发现故障并进行维修。
除了结构设计,超重型龙门式加工中心的优化也是提高设备性能的重要手段。
在优化过程中,可以从以下几个方面进行改进:首先,可以优化加工工艺和刀具选择。
通过合理选择加工工艺和刀具,可以降低切削力和热变形,提高加工精度和表面质量。
高速五轴动梁龙门加工中心滑枕及主轴设计-开题报告讲解

一、引言:开题报告主要由 A题目分析、B国内外技术资料、C主要设计内容、D方案、E设计日程安排、五个基本方面组成。
提纲:A题目分析B国内外技术资料 1、五轴介绍2、高速切削技术3、加工中心4、数控部分5、小结C主要设计内容 1、适用范围2、技术参数3、结构特点D 方案 1、整机设计方案2、具体设计方案(1)主轴部分(2)进给部分E 设计日程安排二、正文:A 题目分析:本次毕业设计题目为--五轴高速动梁龙门加工中心。
主要特点:本产品与传统的三轴联动数控龙门加工中心的最大区别是在刀头上增加了A 、C 轴的联动。
由于A、 C 轴联动的参入,实现五轴联动加工。
该机床具有很强的数控功能,可一次装夹工件在多种空间角度进行铣、镗、钻等工序加工,加工各种具有复杂轮廓表面或型腔的工件,广泛适用于多种机械加工领域。
特别适用于模具和凸轮及航天航空等超复杂零件的机械加工。
主要性能要求:1,整机采用龙门式结构,刚性好上下工件操作方便2,可实现五轴控制、五轴联动3,主轴采用高速电主轴、主轴转速高、加工效率高4,工作台面及三向行程大、加工范围广、整机刚性高、承载重量大B 国内外技术资料:本部分内容主要由五个方面组成:1、五轴的介绍 2、高速切削技术 3、加工中心 4、切削数据库 5、数控部分下面一一展开:1、五轴的介绍几十年来,人们普遍认为五轴数控加工技术是加工连续、平滑、复杂曲面的惟一手段。
一旦人们在设计、制造复杂曲面遇到无法解决的难题,就会求助五轴加工技术。
早在20世纪60年代,国外航空工业生产中就开始采用五轴数控铣床。
目前五轴数控机床的应用仍然局限于航空、航天及其相关工业。
五轴联动数控是数控技术中难度最大、应用范围最广的技术,它集计算机控制、高性能伺服驱动和精密加工技术于一体,应用于复杂曲面的高效、精密、自动化加工。
国际上把五轴联动数控技术作为一个国家生产设备自动化水平的标志。
由于其特殊的地位,特别是对于航空、航天、军事工业的重要影响,以及技术上的复杂性,西方工业发达国家一直把五轴数控系统作为战略物资实行出口许可证制度,对我国实行禁运。
高速桥式机床的结构设计与优化
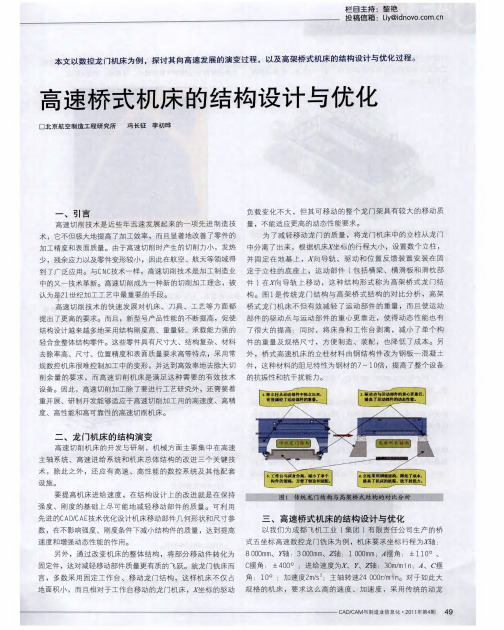
三维设计和有限元分 析的手段进行 了设计与优化 ,机床总体结 上角的材 料对结构 刚性 影响较 小 ,可剔除 ,如 图4 所示。
构如图2 所示。
对于 3 m m1 的高 速进给 ,导 向采 用高 精度 带预载 的滚 0 / n 柱直线导轨 ,传 动系统方面 ,肪 向采用齿轮齿条双边 同步驱 形状 及 尺寸 优 化是 在 保证 零 件 的拓 扑 结构 不 变 的前 提
表2 横梁 导轨 滑块 上的支反力
滑块
1
桥式 五坐标高 速数控 龙门铣床 的坐标 设计采 用笛卡 尔坐
标 方 式 ,各 坐 标 串联 式 叠 加 ,机 械 结 构 如 图 8 示 。 滑 板 在 横 所
/ N
—1 7 4 0
通过 优化计算 ,得出横梁 的变形 图和各 个 值 ,如 图6 和 到 明显优化 ,满足设计要 求。而受力最大的正是 两个内侧前滑 N 7 表1 所示。结果表 明 :在 质量不变的前提下 ,通过 形状优化使 块 ,约 1 k ,此数值为导轨的选择提供 了理论依据。 质量分布发生 变化 ,最终变形 比初始 结构变形降低 了2 % 7 ,而 结构上的最大应力和初 阶固有频率基本保持不变 ,因此通过形 状及尺寸优化 ,可使横梁 的静 、动态性能均有较大提高 。
孙
5 C D C M与制造业信 息化 -w w i o oc r. 0 A/ A w n v no d o n
( 2 3- - 1 1, , ・ ・而 0)≤ 6 ・・
栏 目主持 :黎艳 投稿信 箱 :L @ d o o o c i in v . m. y c n
XK5020动梁型高架桥式龙门加工中心的研制

!"#"$%&’"() %* +,-./. 0%#1(2 3 4"5’ 67"8)$" 971:2" 6;&" <= >5()7; 05?@1(1(2 ="()"7
()*+ ),-,.)/ 0-12,( 3-14, 356478921:9,;,-1<=255, $%%&’’ ,>)?) !"#$%&’$: @28 A-A8B :17B5C,98D 728 E892-1:9-6 D7B,97,B8 , 92-B-978B -1C F84 78921565<4 5G - F:1C 5G E5H:1< I J8-E 7B8D768 JB:C<8 74A8 <-17B4 E-92:1:1< 98178B ,-AA6:9-7:51 5G H:B7,-6 -DD8EJ64 78921565<4 :D -6D5 8KA5,1C8C C,B:1< AB5C,97 C8D:<1L /1 5BC8B 75 :EAB5H8 728 8GG:9:8194 -1C 68H86 5G 728 AB5C,97 C8D:<1 ,MNO 78921565P <4 :D -AA6:8C 75 728 C8D:<1 5G 95EA6878 E-92:18 C8D:<1L @28 C8H865A8C E-92:18 2-D D,998DDG,664 ,D8C :1 AB5C,97:51L ()*+,%-#: ;-17B4 Q-92:1:1< >8178B;Q5H:1< I J8-E @B8D768 RB:C<8 @4A8 Q-92:18 ;S8H865AE817 用于大型零件加工的龙门式高刚度机床大多采用 工作台固定、 龙门移动结构。相对于工作台移动的龙 门机床来说, 龙门移动式铣床采用的是固定工作台, 一 般与床身整体铸出, 龙门框架纵向运动的驱动力矩等 值不变, 不会因工件的承载重量的改变而变化, 从而保 证了加工精度和机床的响应性能。 笔者在为某机床企业主导设计的 TU$’"’ 龙门加 工中心上突破了传统机床的概念, 采用了新型的动梁 型高架桥式机床布置结构。 自安装两副直线导轨和滚珠丝杠, 通过连接板和横梁 连接, 组成龙门结构。横梁上设置有一对平行的直线 导轨和滚珠丝杠副, 十字滑座沿横梁左右运动。主轴 部件安装在十字滑座上, 十字滑座有 ! 轴导轨和丝杠 副, 形成主轴部件的上下运动。
五轴联动加工中心主轴系统的结构优化

!
! 竺
五轴联动加 工中心主轴 系统 的结构优化
佘 洋 ’张建 润 ’卢 , , 熹 ’孙 庆鸿 ’彭 , , 文 姚 树健 ,
(. 1 东南大学机械工程系, 南京 2 0 9 ;江苏 多棱数控机床股份有限公司, 10 6 常州 2 3 1 ) 1 0 2 摘 要 :对五轴联动加 工中心主轴系统进行动 力学仿真分析 ,对原主轴系统的轴承支承 系统和主轴结 构进行了动 态优 化设计 。 对主轴 前端 的单排轴 承的不足 , 出了双排轴承的设计 方案 。对于 针 提 主轴结构 , 论文建 立了以主轴前端动态变形最 小为目标 函数的优 化模 型 , 对主轴结构进行了优
电 主 轴套
动 加 工 中 心 的主 轴 系统 ,原 机 床 在 主 轴 转 速 高 于
8 0 r n 削加 工时 振动 剧烈 , 重影 响 了机床 的 0 0/ 切 mi 严
一
图 1 轴 系统 C 主 AD模 型
在建 立 有限 元数 字化模 型 时 ,对 原有模 型 进行 些必要 的 简化 ,如 省略 小 的倒 角 、沟槽 等 ,同时
ห้องสมุดไป่ตู้
YU Y n ’Z A G inr n, U X’ S N Qigh n ’P N We Y O Sh -a a g , H N Ja —u ’ L i U n — o g , E G n , A uj n , i
( o te s nv ri , a j g2 0 6 Chn ;2 J n s u l gN c a ia T o Ld 1 S uh a t iesy N ni 1 9 , i U t n 0 a . i g uD oi cMe h nc l o l t, a n C a g h u2 0 , ia h n z o 1 1 Chn ) 3 2
五轴联动数控加工中心仿真系统开发应用

五轴联动数控加工中心仿真系统开发应用摘要:本文所涉及的数控加工系统是基于CATIAV5的功能模块建立的,通过对动龙门五轴联动的实体测量、建模、组装和整机模拟,实现数控加工过程的仿真。
同时根据本行业实际生产技术需要,结合VER- ICUTR软件零件切削过程仿真验证优势,建立CATIA与VERICUT两软件平台之间的宏联结,实现将机床运行数控程序过程中的过切、干涉、碰撞和欠切等错误消除在设讣阶段的U的,提高数控加工过程的可靠性。
LI前大型数控五轴联动在科研生产过程中,主要用于进行大型复杂航空零部件与工艺装备制造加工,因空间结构复杂,外形体积大,常出现零件首件过切,未加工到位,机床与零件或工装干涉,模锻件装夹定位不准确和加工超行程等问题,仅凭借数控编程技术人员个人经验,工作量庞大且复杂,难以克服。
针对五坐标数控加丄机床控制系统不具有数控加丄过程的动态模拟仿真功能,笔者结合虚拟制造技术,在计算机辅助制造软件(VERICUT 5. 4)平台基础上,开发了数控加工机床仿真系统模块。
该仿真系统可以在\C代码的驱动下运行,用以观察数控机床部件运动和零件的加工成形过程中空间运动状况,验证加工程序G 代码的正确性,防止实际加工过程中干涉和碰撞等故障发生。
该系统旨在以五坐标数控机床为验证工作机,研究FIDIA C20控制系统的驱动工作原理,建立数控加工中心仿真工作平台,进行典型回转曲轮轴和蒙皮锻金工艺装备五轴联动铳切的加工过程模拟。
涉及到仿真工作环境下的大型工艺装备装夹定位,确定数控参数库,模拟数控加工程序的运行过程等。
一、开发研究过程1.五坐标数控加工中心加工仿真系统技术研究比较同类型仿真系统现状,LI前技术能力可以建立儿何仿真系统,模拟计算刀具切削速度、切削量和切削时间等。
(1)软件系统研究方案制定与基础工作调试准备。
①方案制定:首先将VERICUT与CATIA软件功能模块测试验证联接;然后建立五轴联动数控加工中心机床结构与运动关系分析;最后生成五轴联动数控加工中心模拟系统。
高架桥式龙门加工中心滑台结构的动态优化设计
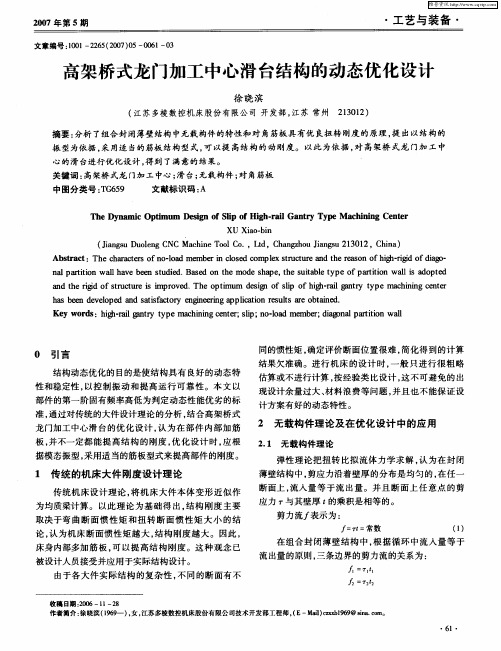
为 均质 梁计算 。 以此 理论 为基 础 得 出 , 构 刚度 主要 结
取 决于 弯 曲 断 面 惯 性 矩 和扭 转 断 面 惯 性 矩 大 小 的结
论 , 为 机床 断 面惯 性 矩 越 大 , 构 刚度 越 大 。 因此 , 认 结
床身内部多加筋板 , 可以提高结构刚度 。这种 观念已
n i f t t rv T eo t adter do rcuei ipoe. h pi m ei fspo i - ignr y em ci gcne h g i s r sm u d mu ds no i fh r l at tp ah i et g l h g a y n n r
被 设计 人员 接受并 应用 于实 际结 构设计 。 由于 各 大件 实 际 结 构 的 复杂 性 , 同 的断 面 有 不 不
收稿 日期 :0 6一I 一2 20 l 8
在组 合 封 闭薄 壁结 构 中 , 据循 环 中流 人 量 等 于 根 流 出量 的原则 , 三条 边界 的剪 力 流 的关 系 为 :
XU a . i Xio b n
( i gu D oegC C Mahn ol o , t ,C aghuJ ns 10 2, hn ) J n s u l N c ieT o C . Ld hn zo i gu2 3 1 C ia a n a
Ab ta t sr c :Th h rceso o la mb ri lsd c mpe rcu ea dt era o fhg - g fda - ec aa tr f - dme e co e o lxs u tr n es n o ih r i o ig n o n t h i d n
五轴联动加工中心主轴系统的结构优化

于 8 0 rmi 削 加工 时振 动剧 烈 , 重 影响 了机 床 0 0/ n切 严 的性 能 , 要 对 原 结 构 进 行 改 进 , 高 其 静 力 学 、 需 提 动 力学 性 能 , 其满 足设 计 的要求 ‘ 使 ¨ 。
2 主轴 系统 的动 力学 分析
原 主轴 系 统 C D模 型 如 图 1示 , A 主要 由箱 体 、
网格 , 主轴 系统 的有 限元模 型 如 图 3所 示 。
态 占机床 总位 移 的 3 % ~ 0 , 0 4 % 共振 状 态 时 则 高 达
6 % 一8 % … 。 随 着 现 代 机 床 的 主 轴 转 速 越 来 越 0 0
高, 切削 深度 越来 越大 , 主轴 系 统 的性 能 提 出 更 高 对 的要 求 。本文 研究 的对 象是 我 国 自主开 发 的 桥 式 五 轴联 动加 工 中心 的主轴 系 统 。原 机 床在 主轴 转 速 高
的所有 自由度 约束 。 图 4 56是 主轴 系统 的前 三 阶 、、 振型 , 其对 应 的频率 如 表 1 示 。 所
图 1 主轴 系统 C D模 型 A
在建立 有 限元 数 学 模 型 时 , 原 有 模 型 进 行 一 对
些必要的简化 , 如省略小 的倒 角、 沟槽等 , 同时考虑
( ) 5 1 l 2 0 25 30 0 O0 50 0 0 0
1 引 言
采用 等 刚度 的弹 簧单 元来 仿 真 轴 承 与主 轴 之 间 的连
接 。整个 系统 采用 8节点 3 自由度 的 15单元 划 分 8
主轴 系统 是机 床最 重 要 的部 件 之 一 。在 生 产加
工过 程 中 , 由主 轴 系 统 振 动 产 生 的位 移 在 非 共 振 状
基于有限元的高速龙门五轴加工中心动静态优化设计

g n r — y e ma h nn e t a e n F a ty t p c ii g c n er s d o EM b
高速龙门五轴加工中心静刚度分析与结构优化

做 z向运动 , 双摆头可 实现 A C轴摆 动 , 足复杂 曲 / 满
面 的 五 轴 联 动 加 工 。 由 于 有 限 元 分 析 软 件 A ss ny 提 供 的 建 模 工 具 相 对 较 弱 , 以 采 用 Po E软 件 先 将 各 所 r/ 部 件 建 立 三维 实 体 模 型 , 装 配 得 到 整 机 模 型 , 减 并 为 少 计算 负荷 , 对模 型 进 行 适 当 简 化 , 掉 螺 钉 、 母 、 去 螺
pr ve n r a a tc o d i e lpr c ie.
K e o ds g n r xs ma hn e tr FEM ;sa i ii i y w r : a ty 5 a i c ie c n e ; t tc rgdt y
0 引 言
高速龙 门五轴 加工 中心 主 要应 用 于复 杂模 具 制 造 以及 大 型铝 合金 结 构件 的高 速 、 效 、 精 加 工 , 高 高
c mp n n s Ac odn ote ea a s s t efal at ta i at h i dt f h oemahn ei o o e t . c r igt h s n l e , h iP rs h t mp c t er i o ewh l y l i g y t c iesr -
A b t a t:S a i ii i s o ft em o ti po t n n ia o sf rm a h n o l ’ pef r a c , n e d sr c t tc rgdt i neo h s m ra tid c t r o c i et o s ro m n e a d n e y t o e a t d i h a e ofd sg o be f rc se n t e ph s e in.I he d sg g pe d 5 a i a ty-ype m a h n e t r n t e i ofa hih s e ・ xs g n r t n c iecn e. sa i f r e a ayss i ro me ih t e h l o t tc o c n l i spef r d w t h ep fFEM s fw a e f r t e c mplt a h n n t an o t r o h o ee m c i e a d ism i
高速立式加工中心床身静动态特性分析及优化设计
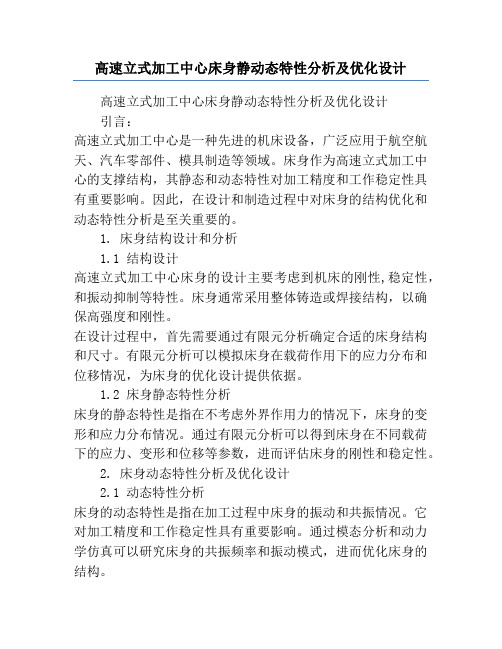
高速立式加工中心床身静动态特性分析及优化设计高速立式加工中心床身静动态特性分析及优化设计引言:高速立式加工中心是一种先进的机床设备,广泛应用于航空航天、汽车零部件、模具制造等领域。
床身作为高速立式加工中心的支撑结构,其静态和动态特性对加工精度和工作稳定性具有重要影响。
因此,在设计和制造过程中对床身的结构优化和动态特性分析是至关重要的。
1. 床身结构设计和分析1.1 结构设计高速立式加工中心床身的设计主要考虑到机床的刚性,稳定性,和振动抑制等特性。
床身通常采用整体铸造或焊接结构,以确保高强度和刚性。
在设计过程中,首先需要通过有限元分析确定合适的床身结构和尺寸。
有限元分析可以模拟床身在载荷作用下的应力分布和位移情况,为床身的优化设计提供依据。
1.2 床身静态特性分析床身的静态特性是指在不考虑外界作用力的情况下,床身的变形和应力分布情况。
通过有限元分析可以得到床身在不同载荷下的应力、变形和位移等参数,进而评估床身的刚性和稳定性。
2. 床身动态特性分析及优化设计2.1 动态特性分析床身的动态特性是指在加工过程中床身的振动和共振情况。
它对加工精度和工作稳定性具有重要影响。
通过模态分析和动力学仿真可以研究床身的共振频率和振动模式,进而优化床身的结构。
2.2 动态特性优化设计床身的动态特性可以通过以下几个方面进行优化设计:2.2.1 结构调整根据动态特性分析的结果,可以对床身的结构进行调整。
例如,通过改变床身的刚度分布或增加支撑梁的数量来改善床身的共振频率和振动模式。
2.2.2 材料选择选择合适的材料可以改变床身的动态特性。
比如采用高强度、低密度的材料可以提高床身的刚度和降低共振频率。
2.2.3 减振措施在床身设计中引入减振措施可以有效地降低振动幅度和共振频率。
例如,通过在床身中添加减振材料或减振结构实现振动的消除或抑制。
结论:通过对高速立式加工中心床身的静动态特性分析与优化设计,可以改善床身的结构刚性和振动特性,提高加工精度和工作稳定性。
高速龙门加工中心立柱静态设计与动特性分析
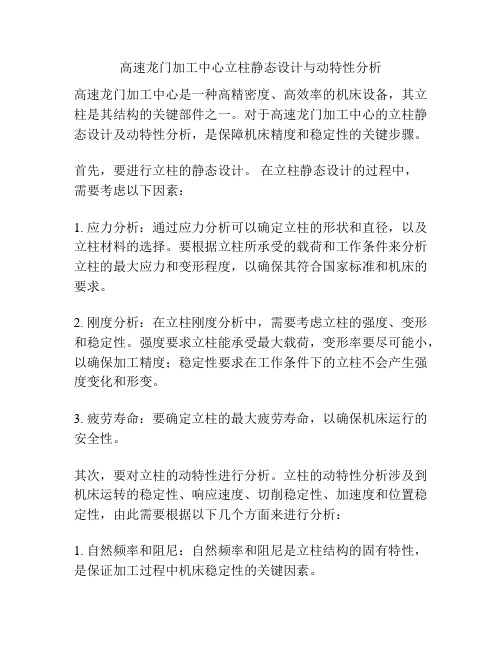
高速龙门加工中心立柱静态设计与动特性分析高速龙门加工中心是一种高精密度、高效率的机床设备,其立柱是其结构的关键部件之一。
对于高速龙门加工中心的立柱静态设计及动特性分析,是保障机床精度和稳定性的关键步骤。
首先,要进行立柱的静态设计。
在立柱静态设计的过程中,需要考虑以下因素:1. 应力分析:通过应力分析可以确定立柱的形状和直径,以及立柱材料的选择。
要根据立柱所承受的载荷和工作条件来分析立柱的最大应力和变形程度,以确保其符合国家标准和机床的要求。
2. 刚度分析:在立柱刚度分析中,需要考虑立柱的强度、变形和稳定性。
强度要求立柱能承受最大载荷,变形率要尽可能小,以确保加工精度;稳定性要求在工作条件下的立柱不会产生强度变化和形变。
3. 疲劳寿命:要确定立柱的最大疲劳寿命,以确保机床运行的安全性。
其次,要对立柱的动特性进行分析。
立柱的动特性分析涉及到机床运转的稳定性、响应速度、切削稳定性、加速度和位置稳定性,由此需要根据以下几个方面来进行分析:1. 自然频率和阻尼:自然频率和阻尼是立柱结构的固有特性,是保证加工过程中机床稳定性的关键因素。
2. 模态:通过模态分析可以得到机床载荷、切削力的作用下,立柱在运动过程中的振动特性。
模态分析可以帮助设计师确定在加工过程中如何控制立柱的振动,以保证加工精度和处理工件的质量。
3. 加速度和位置变化:加速度和位置变化是影响机床工作精度的因素之一,对于高速龙门加工中心来说,需要控制立柱的加速度和位置变化,在加工过程中控制立柱的精度和工作效率。
4. 切削力:切削力是机床加工时承受的一种力量,会对立柱产生振动和变形,因此需要对切削力进行分析和控制。
综上所述,高速龙门加工中心立柱的静态设计与动特性分析是保障机床精度和稳定性的重要步骤。
设计师需要根据机床的实际情况进行分析和控制,以满足机床的加工工艺和工艺要求,从而提高机床加工的稳定性和精度。
假设我们需要研究消费者对某种产品的购买意向和市场规模,我们可以收集相关的数据并进行分析。
高速龙门铣床五轴联动的结构设计_周晓平

第15卷第3期2010年6月 新 余 高 专 学 报J O U R N A L O F X I N Y U C O L L E G E V o l .15,N O .3J u n .2010—90 —高速龙门铣床五轴联动的结构设计○周晓平,朱双霞(新余学院 机电工程系, 江西 新余 338004)摘 要:对现在机床的五轴联动结构进行了结构分析、对比,设计出了高速龙门铣床五轴联动的结构。
五轴联动结构设计中又主要对五轴联动铣头(行业中称“五轴头”)进行了设计,结构中采用了精密齿轮啮合与双导程蜗轮蜗杆驱动,既保证了结构紧凑,精度也较高。
关键词:五轴联动;结构设计;五轴联动铣头;双导程蜗轮蜗杆中图分类号:T G 659 文献标识码:A 文章编号:1008-6765(2010)03-0090-03收稿日期:2010-03-15课题及第一作者简介:本文为校级课题“五轴联动高速龙门铣床结构设计的研究(项目编号:x j 0821)”系列研究成果之一。
周晓平(1979-),男,江西新余人,讲师。
1 前言数控机床是当代制造业的主流装备,是市场的热门商品。
我国数控机床经历30多年来的发展,现已颇具规模,机床已涉及超重型机床、高精度机床、特种加工机床、锻压设备、前沿高技术机床等领域。
但与机床高度发达的国家相比,我国机床的总体制作水平还是存在着一定的差距,相当明显的是:在我国,对于四轴联动以上的机床,大部分来自国外,再加上西方国家对我国在这方面的技术封锁,在一定程度上影响了我国数控机床的发展。
笔者在借鉴大量国内外机床资料的基础上,根据一特定方案设计出虚拟样机———五轴联动高速数控龙门铣床。
本文是就其中五轴联动的结构设计进行阐述。
2 五轴联动现状及其分析大多数高级的数控铣床的数控装置都可控六根基本轴,即X ,Y ,Z 三根运动轴和绕X ,Y ,Z 三根运动轴旋转的A 、B 、C 三根回转轴。
五轴联动指的是在六根基本轴中,机床数控装置能控制其中五根轴同时达到空间某一点,通俗的讲就是指其中五根轴能同时对某一点进行运动加工。
高速五轴动梁龙门加工中心滑枕及主轴设计-开题报告
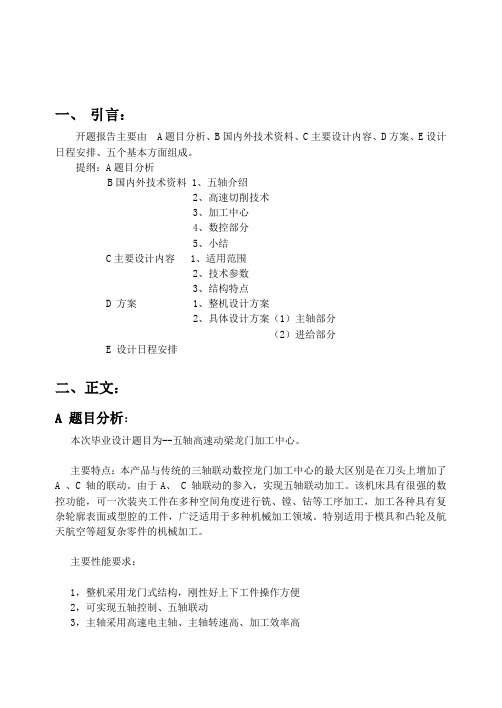
一、引言:开题报告主要由 A题目分析、B国内外技术资料、C主要设计内容、D方案、E设计日程安排、五个基本方面组成。
提纲:A题目分析B国内外技术资料 1、五轴介绍2、高速切削技术3、加工中心4、数控部分5、小结C主要设计内容 1、适用范围2、技术参数3、结构特点D 方案 1、整机设计方案2、具体设计方案(1)主轴部分(2)进给部分E 设计日程安排二、正文:A 题目分析:本次毕业设计题目为--五轴高速动梁龙门加工中心。
主要特点:本产品与传统的三轴联动数控龙门加工中心的最大区别是在刀头上增加了A 、C 轴的联动。
由于A、 C 轴联动的参入,实现五轴联动加工。
该机床具有很强的数控功能,可一次装夹工件在多种空间角度进行铣、镗、钻等工序加工,加工各种具有复杂轮廓表面或型腔的工件,广泛适用于多种机械加工领域。
特别适用于模具和凸轮及航天航空等超复杂零件的机械加工。
主要性能要求:1,整机采用龙门式结构,刚性好上下工件操作方便2,可实现五轴控制、五轴联动3,主轴采用高速电主轴、主轴转速高、加工效率高4,工作台面及三向行程大、加工范围广、整机刚性高、承载重量大B 国内外技术资料:本部分内容主要由五个方面组成:1、五轴的介绍 2、高速切削技术 3、加工中心 4、切削数据库 5、数控部分下面一一展开:1、五轴的介绍几十年来,人们普遍认为五轴数控加工技术是加工连续、平滑、复杂曲面的惟一手段。
一旦人们在设计、制造复杂曲面遇到无法解决的难题,就会求助五轴加工技术。
早在20世纪60年代,国外航空工业生产中就开始采用五轴数控铣床。
目前五轴数控机床的应用仍然局限于航空、航天及其相关工业。
五轴联动数控是数控技术中难度最大、应用范围最广的技术,它集计算机控制、高性能伺服驱动和精密加工技术于一体,应用于复杂曲面的高效、精密、自动化加工。
国际上把五轴联动数控技术作为一个国家生产设备自动化水平的标志。
由于其特殊的地位,特别是对于航空、航天、军事工业的重要影响,以及技术上的复杂性,西方工业发达国家一直把五轴数控系统作为战略物资实行出口许可证制度,对我国实行禁运。
基于VERICUT的大型五c轴龙门机床加工仿真技术研究

基于VERICUT的大型五c轴龙门机床加工仿真技术研究作者:王堃王业伟蹇悦来源:《中国科技纵横》2014年第14期【摘要】本文以GMC50100u五轴龙门加工中心为对象,分析了大型五轴龙门机床的结构及运动形式,并从仿真模型构建、机床参数设置、控制系统定制等方面详细讲述了大型多轴复杂机床的仿真环境建立过程和步骤。
并通过对偏心锥零件的试制,验证了自建仿真环境的可靠性和建立方法的正确性。
同时还介绍了Vericut软件仿真环境下对数控程序的优化应用。
【关键词】 Vericut 仿真五轴龙门机床复杂零件在多轴轴联动,尤其是五轴及以上联动的数控机床加工中,由于附加的一些刀具旋转或工件旋转非常容易发生碰撞和干涉现象,这样就可能造成工件、刀具甚至于机床的损坏。
为了避免以上问题的产生,在加工前往往需要在零件坯料上进行试加工,并通过对数控程序进行反复调试,确保加工程序的正确安全。
但这样的方式不但增加了劳动强度、降低了工作效率,造成了人力、时间、能源和物质的浪费,且在试加工过程中亦存在质量隐患。
Vericut 软件可以同时进行刀具轨迹和机床运动仿真。
通过这仿真,可以有效免碰撞、干涉等现象,规避试切安全风险,缩短产品加工周期。
本文以沈阳中捷机床厂GMC50100u大型龙门结构形式的五轴五联动加工中心为对象,讲述复杂多轴数控设备在VERICUT软件里仿真环境的建立和验证方法。
1 龙门五轴加工中心仿真环境建立机床仿真环境的建立主要包括机床结构模型构建和控制系统定制。
1.1 机床仿真模型构建1.1.1 机床结构分析及构件依附关系梳理VERICUT中机床模型以组件树的形式存在,组件树反映的是机床各部分之间的现对位置和运动依附关系。
GMC50100u五轴龙门加工中心,由三个线性轴和两个旋转轴组成,机床主要部件包括x横梁、y滑块、z滑块、c转头、a摆头、工作台。
根据GMC50100u机床实际结构、运动关系,确定机床各部分间的相互依附关系,见图1所示,图中箭头指向为下级子组件。
高架桥式龙门数控雕铣机的动态特性研究

( 西工学 院 机械 工程 系 , 广 柳州 5 50 ) 4 06
Dy a i ay i o a u t p o g n NC gr vn n ln c i e n m c An lss f r Vid c Ty e L n me En a ig a d Miig Ma hn l
csi ei o ret ea t o i a e d vl e yac m a yb iga td b c, A at gs ca frl g y uo bl p n l eeo d b o p n en asuy oj taC D n p l a p m e p s e m d l o e m c ieW s bi e y a ot g U X s t ae n mi c aatr t so e o e frt ahn a et lh db dp i G N o w r. n d a c h cei i t h s a s n f A dy r sc f h m d l eea a zdu i N Y otaetruh s p i igteoiia C D m d 1 s te r o e w r n ye s g A S Ss w r hog i lyn r n A o e Ert h s 6 l n f m f h gl . f t i
Ke o d Har o cRe po s ; od lAna y i ; y W r s: m ni s n e M a l ss CNC Eng a i n M ilngM a hi e r v ng a d li c n
中 图分 类 号 : H1 ,G 5 文献标 识码 : T 6T 4 7 A
Y N Hu-u , A G Pn — u , NJ n P N Y , E Y n fn I ijn Y N ig h i I i ,A u H u -e g J a
高架桥式五坐标龙门加工中心整机动特性分析

高架桥式五坐标龙门加工中心整机动特性分析东南大学机械工程系 (210096) 倪向阳 张建润江苏多棱数控机床有限公司 (213012) 彭 文摘 要 基于试验识别机床各结合面参数,本文建立了机床整机有限元模型,并进行了静态、动态和谐响应分析,在此基础上找出机床结构的薄弱环节,为机床结构优化设计提供技术支持。
关键词 有限元建模 有限元分析 模态分析 谐响应分析 结合面 在有关项目支持下东南大学与江苏多棱数控机床有限公司合作,开发大型高架桥式五坐标龙门加工中心,机床结构示意图如图1所示。
它主要用于航空航天工业中大型铝合金构件和复杂模具的高速、高效、高精度切削加工。
为保证该机床具有良好的动、静态特性,在设计阶段进行整机和零部件的动力学建模与动、静态特性分析,以确保机床具有良好的动态特性和优良的加工性能。
1.立柱;2.滑座;3.滑台;4.横梁;5.拖板;6.箱体;7.轴;8.电主轴架;9.电主轴图1 机床结构示意图对于这种大型机床的复杂结构,由于零部件装配结合面参数的不确定性,直接建立能描述结构动、静态特性的准确有限元模型是十分困难的[1]。
本文通过试验测试的方法识别出机床主要结合面参数,并应用到整机有限元建模中,得到了较准确的机床整机有限元模型,在此基础上进行机床动、静态特性分析,得到了可靠的分析结果[2][3]。
1 结合面参数识别与整机有限元建模1.1 结合面参数识别机床结合面是影响整个机床动、静态特性的关键,因此整机建模时结合面的参数正确与否,对整机有限元模型的建模精度具有举足轻重的作用。
本文针对影响整机建模精度的关键结合面———导轨副进行动态试验,识别出导轨结合面参数,把这些参数应用于整机建模,以确保整机的建模精度。
图2所示为测试系统示意图:测试时将滑台置于滑座上,由于滑座的质量远大于滑台质量,且滑座与滑台的刚度相对结合面刚度大得多,因此滑座与滑台系统可以近似为单自由度系统。
系统在各方向产生第一阶模态将由导轨结合面相应方向刚度单独决定,因此可以采用分量分析法来识别出该结合面参数[4]。
高速龙门五轴加工中心静刚度分析与结构优化_李焱

方向的力的 作 用,这 两 种 结 合 部 采 用 节 点 耦 合 的 接 触单元模拟; 螺栓连接的结合部全部采用接触单元 模拟。所有 接 触 单 元 接 触 刚 度、阻 尼 和 摩 擦 系 数 等 参数均依据公司参数库查询得到。
2 整机静力学分析
对于高速龙门五轴加工中心这样的大型机床, 在计算静力 变 形 时,不 能 忽 视 它 本 身 的 重 力 对 机 床 的变形和加工的影响。根据机床的结构可知当滑枕 沿机床 Z 坐标方向移动到最下端时,滑枕的伸出量 最长,此时的变形最大,所以整机的静力学分析将选 择此时机床的位姿来计算。首先计算机床在重力作 用下的变形情况,计算结果如图 3 所示,机床的最大 变形为 0. 34mm。将总变形分解到各个部件,结果如 图 4 所示,从计算的结果可以看出横梁的变形最大, 为 0. 13mm,为机床的薄弱环节,其引起的机床变形 占总变形的 38% ,主要原因是横梁在重力作用下发 生 YZ 平面的弯曲和 XZ 平面的扭转,带动主轴偏离 理想位置。
图 2 主机系统的网格划分模型
1. 3 结合面的处理
机床相邻部件间相互接触的区域称为结合部, 对机床整 机 特 性 有 重 要 影 响。 有 统 计 显 示,机 床 整 机静 刚 度 中 30% ~ 50% 取 决 于 结 合 部 的 刚 度 特 性[2],动柔度有 60% 以上是源自结合部,阻尼值的 90% 以上来源于结合部的阻尼[3]。因此,结合部的 建模是机床整机有限元建模的重要组成部分。机床 中主要的结合部包括直线电机初级-次级结合部、直 线滚动导轨滑块-轨道结合部、滚珠丝杠丝母-丝杠结 合部和螺栓连接的固定结合部。直线电机推动力很 大,初级相对次级运动时几乎没有弹性,在直线电机 运动方向上施加位移约束方程; 滑块可沿导轨运动, 在两个方向 上 承 受 力 的 作 用,滚 珠 丝 杠 只 承 受 轴 线
GMCU2060龙门加工中心横梁结构有限元分析

3
128
横梁 x 向前后摆动
4
158
横梁 z 向上下摆动
5
219
横梁底部沿 x 向振动
6
223
横梁沿 x 向前后扭振
图 4 横梁前 6 阶模态
·134·
机床与液压
第 39 卷
3 横梁结构改进设计 通过前面对横梁及其组件进行的静动态刚度分析
可知,当滑座位于横梁中央且滑枕降到最低点时横梁 变形最大,需提高横梁的抗弯和抗扭刚度。横梁 1 阶 固有频率为 96 Hz,反应为局部的加强筋颤振,说明 加强筋相对较薄弱,需要加强其刚度。鉴于此,作者 主要对横梁的外壁和加强筋的布局和尺寸做了相应改 进。在改进设计阶段,建立了横梁的板壳单元模型, 这样可以通过给板壳赋予不同的参数改变其属性,达 到参数化设计的目的。如图 5 所示是文中所研究横梁 的等效板壳单元模型。
图 1 GMCU2060 龙门加工中心结构 GMCU2060 龙门加工中心采用横梁移动方式,可 实现高速进给并在相同机床占地面积的情况下扩大零 件的加工尺寸范围。机床工作台和被加工零件均固定 不动,这样可以加工质量较大的零件,并且避免了质 量较大的工件和工作台在运动过程中对整机动态性能
高速桥式机床的结构设计与优化
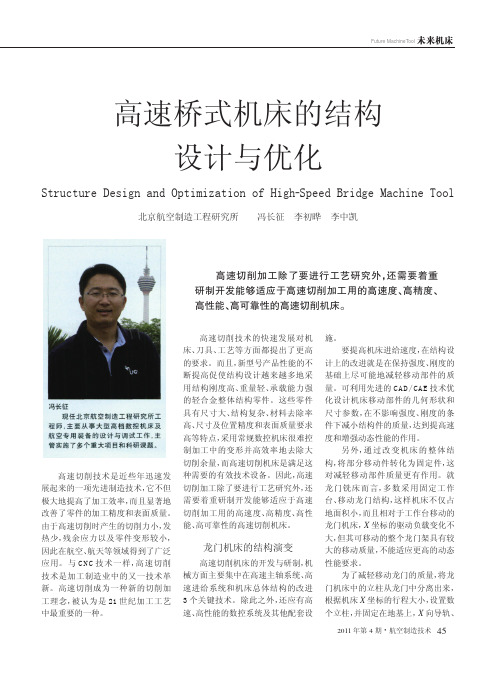
高速切削技术是近些年迅速发展起来的一项先进制造技术,它不但极大地提高了加工效率,而且显著地改善了零件的加工精度和表面质量。
由于高速切削时产生的切削力小,发热少,残余应力以及零件变形较小,因此在航空、航天等领域得到了广泛应用。
与C N C技术一样,高速切削技术是加工制造业中的又一技术革新。
高速切削成为一种新的切削加工理念,被认为是21世纪加工工艺中最重要的一种。
高速切削技术的快速发展对机床、刀具、工艺等方面都提出了更高的要求。
而且,新型号产品性能的不断提高促使结构设计越来越多地采用结构刚度高、重量轻、承载能力强的轻合金整体结构零件。
这些零件具有尺寸大、结构复杂、材料去除率高、尺寸及位置精度和表面质量要求高等特点,采用常规数控机床很难控制加工中的变形并高效率地去除大切削余量,而高速切削机床是满足这种需要的有效技术设备。
因此,高速切削加工除了要进行工艺研究外,还需要着重研制开发能够适应于高速切削加工用的高速度、高精度、高性能、高可靠性的高速切削机床。
龙门机床的结构演变高速切削机床的开发与研制,机械方面主要集中在高速主轴系统、高速进给系统和机床总体结构的改进3个关键技术。
除此之外,还应有高速、高性能的数控系统及其他配套设高速桥式机床的结构设计与优化北京航空制造工程研究所 冯长征 李初晔 李中凯高速切削加工除了要进行工艺研究外,还需要着重研制开发能够适应于高速切削加工用的高速度、高精度、高性能、高可靠性的高速切削机床。
Structure Design and Optimization of High-Speed Bridge Machine Tool冯长征现任北京航空制造工程研究所工程师,主要从事大型高档数控机床及航空专用装备的设计与调试工作,主管实施了多个重大项目和科研课题。
施。
要提高机床进给速度,在结构设计上的改进就是在保持强度、刚度的基础上尽可能地减轻移动部件的质量。
可利用先进的CAD/CAE技术优化设计机床移动部件的几何形状和尺寸参数,在不影响强度、刚度的条件下减小结构件的质量,达到提高速度和增强动态性能的作用。
- 1、下载文档前请自行甄别文档内容的完整性,平台不提供额外的编辑、内容补充、找答案等附加服务。
- 2、"仅部分预览"的文档,不可在线预览部分如存在完整性等问题,可反馈申请退款(可完整预览的文档不适用该条件!)。
- 3、如文档侵犯您的权益,请联系客服反馈,我们会尽快为您处理(人工客服工作时间:9:00-18:30)。
高架桥式高速五坐标龙门加工中心动态仿真与结构优化3 DY NAM I C S I M ULAT I O N AND STRUCTURE O PT I M IZAT I O N O FTHE H I GH SPEED5AXES GANTRY M ACH I N I NG CENTER张建润331 孙庆鸿1卢 熹1郑佳明1倪向阳1彭 文2姚树健2(1.东南大学机械系,南京210096)(2.江苏多棱数控机床股份有限公司,常州213012)ZHAN G J i anR un1 SUN Q ingHo ng1LU Xi1 ZHEN G J iaM ing1 N I XiangYang1P EN G W en2 Y AO S huJ i a n2(1.D epart m ent of M echanica l Eng ineering,S outheast U n iversity,N anjing210096,China)(2.J iangsu D uoling N C M echanical Tool L td.,Changzhou213012,China)摘要 在大型高架桥式、高速、高精度五坐标龙门加工中心的动态设计中,通过动态测试的方法获得导轨结合面的特性参数,并将其应用到数字仿真模型中,提高模型的精度。
在结构动态分析中采用刚体与柔性体结合的仿真方法,对加工中心的关键部件进行柔性化,分析其对系统相应的影响,并在此基础上对这些主要部件进行结构优化设计,提高系统的动态特性。
关键词 龙门加工中心 结合面参数 动态仿真 结构优化设计中图分类号 TG502 T H122Abstract I n the dyna m ic design of the high s peed and high p recisi on5axes gantry machining center,the contact parame2 ters of guide surface had been acquired by the dyna m ic test and they had been app lied t o the nu merical si m ulati on model.By this way,the accuracy of model was i m p r oved.I n the structure dyna m ic design,a si m ulati on method combining rigid body and flexi2 ble body is app lied.The main components are set t o flexible,and their influences are analyzed.The structure op ti m izati ons are made t o i m p r oved the dyna m ics of the machine on these analyses.Key words Gan try mach i n i n g cen ter;Param eters of con t act surfaces;D ynam i c si m ul a ti on;Structure opti m a l de2 si gnCorresponding auther:ZHAN G J ianRun,E2m ail:zhangir@,Tel:+86225283794144The p r oject supported by the Nati onal Natural Science Foundati on of China(50375026)and J iangsu Foundati on Pr ogra m of Science and Technol ogy Base Establish ment.Manuscri p t received20060123,in revised for m20060216.1 引言大型高架桥式、高速、高精度五坐标龙门加工中心主要用于航空航天工业中大型铝合金构件和复杂模具的高速、高效、高精度切削加工。
虽然,目前国内外有一系列关于机床动态设计与优化的理论和方法,但对于大型高架桥式五坐标龙门加工中心这样的机床,其结构形式和动态特性与传统的机床有很大区别[1]。
本文在该机床的设计过程中采用动态仿真技术,使得机床在设计中即发现问题、并通过结构优化设计,开发出具有良好的动、静态特性的机床。
本文首先对设计过程中的机床进行刚体和柔性体建模,针对机床中的主要导轨结合面,采用参数识别技术,将识别得到的物理参数应用到整机的有限元建模中,提高有限元模型的精度。
针对对整机性能有重要影响的横梁、滑座及主轴箱结构进行结构优化设计,提高机床的动态特性。
对于结构中不可避免的共振问题,巧妙采用机床原有附属装置设计减振调谐阻尼器,有效控制机床在工作频率下的振动问题,对机电产品的动态设计提供一个很好的思路。
Journa l of M echan i ca l Strength2006,28(S):01~043 3320060123收到初稿,20060216收到修改稿。
国家自然科学基金项目资助(50375026)、江苏省科技基础设施建设计划(BM2005003)资助。
张建润,男,1962年10月生,江苏镇江人,汉族。
东南大学机械系教授,博士,主要研究方向为机械动态设计、振动与结构声。
曾获国家教委科技进步一等奖、中国汽车工业科技进步二等奖、江苏省科学技术进步二等奖等,发表论文约30余篇。
2 加工中心的CAD 模型及导轨界面特性测试 图1是最初设计的五坐标龙门加工中心CAD(computer aided design )模型。
在整个机床中,有许多结合面,其中导轨结合面对动、静态特性有重要影响,而目前还没有一个很好的关于导轨结合面的理论建模方法,因此本文选择设计过程中采用的导轨进行模态试验,识别出界面的刚度和阻尼,然后将此结果应用到动态仿真模型中,提高模型的精度。
1.立柱2.滑座3.滑台4.横梁5.拖板6.箱体7.轴8.电主轴架 9.电主轴1.Post2.Slide seat3.Slide bedp late4.Trans om5.T ow p late6.Box7.Sp indle8.Support of electrical s p indle9.Electrical s p indle图1 整机CAD 模型Fig .1 The CAD model of machining center图2 导轨界面动态特性测试照片Fig .2 Phot o of the dyna m ic measure mentof he guide contacts 图2为加工中心横梁与滑台之间的导轨,横梁的两段各有8个此类导轨与滑台联接,为获得导轨界面动态特性,将其中一个导轨安装在巨大的测试台上(如图2),在滑块上放置加速度传感器,采用脉冲激励分别对导轨垂直向和侧向进行测试,此时系统表现出明显的单自由度特征,测试其传递函数,从而识别出系统的横向刚度和垂向刚度。
导轨的横向刚度为7.6496×107N ・m -1,垂向刚度为5.5221×108N ・m -1。
相对应的阻尼比分别为0.012和0.0168。
3 加工中心的刚柔动静态仿真与分析目前单纯刚体动力学分析方法和有限元分析法具有各自的特点,例如刚体动力学分析对结构的运动过程可以做到准确的仿真,而对过程中的应力和应变等的描述不是很清晰。
本文采用刚柔结合的方法,在多刚体动力学的分析过程中加入柔性体,使得部件在仿真正式运动的过程中,同时分析出系统的位移和应力特征。
该方法的基础是超单元分析法,首先将部件柔性化处理,再根据零件实际接触和约束条件,创建相应的界面点,用有限元法计算生成部件的模态中性文件。
在动力学仿真中,可以导入此模态中性文件,形成刚柔耦合的数字仿真模型,模拟机床切削,从而得到机床在加工过程中的振动和变形。
图3为立柱、滑座、横梁、主轴箱等主要部件柔性化后的整机模型。
图3 整机主要部件柔性化模型Fig .3 The whole model with main elasticized parts为分析立柱、滑座、横梁及主轴箱对加工中心动态特性的影响,分别用对立柱、滑座、横梁及主轴箱柔性化的模型进行动力学仿真,在仿真过程中取刀具所在位置点在三个方向上的位移为评价指标。
定义运动及载荷为,横梁沿滑座直线运动的传动副,匀速直线运动135mm /s;拖板沿横梁的传动副速度135mm /s;箱体沿托板竖直方向的传动副及相应的运动125mm /s;主轴的旋转副5r/s;主轴转速为8000r/s,在刀具端加切削力F x =F y =1500N ,F z =1000N,所加力及力产生的主轴转矩均与相应的运动速度方向相反,整个仿真切削时间为5秒。
各单件柔性化的模型仿真结果比较如表1。
02机 械 强 度2006年 表1 单件柔性化仿真计算结果Tab .1 S i m ul a ti on results w ith each flex i ble com ponen t柔性化零件Flexible componentx 向平均振动量D is p lace ment in x directi on /mmy 向平均振动量D is p lace ment in y directi on /mm z 向平均振动量D is p lace ment in z directi on /mm 立柱Post 0.0168 4.66×10-49.24×10-4滑座Slide seat 5.11×10-40.00123 2.59×10-4横梁Trans om 3.911×10-4 2.65×10-50.0011箱体Box0.010240.00397.7×10-4从上面的仿真分析结果可以看出,对加工中心x方向影响比较大的零件是箱体,对y 向影响比较大的零件为滑座,而横梁对z 轴的影响教大。
上面对主要部件柔性化处理仿真分析后,可以分析出各主要零件的影响,为更好理解这些件对加工中心的综合影响,在这里将所有主要部件同时柔性化后对机床进行动力学仿真,其结果如表2。
从计算结果可以发现,各部件柔性化综合后对加工中心的影响远远高于单件的影响。
表2 主要部件同时柔性化仿真计算结果Tab .2 S i m ul a ti on results w ith a ll ma i n flex i ble com ponen tsx 向平均振动量/mmD is p lace ment in x directi on /mm y 向平均振动量/mmD is p lace ment in y directi on /mm z 向平均振动量/mmD is p lace ment in z directi on /mm 0.05950.02010.02164 关键部件的结构优化设计根据上述动力学仿真分析,有必要对加工中心的主要结构件滑座、横梁、主轴箱进行优化设计。