铁精矿粉高铁低硅烧结技术
铁粉矿复合造块新工艺
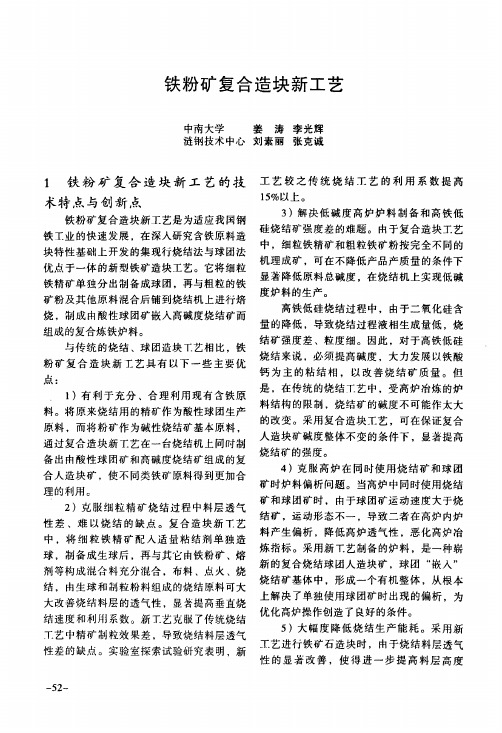
2.2方法与流程
以涟钢2005年3月烧结生产用配矿方案 为基础,将含铁原料中总比例为35.5%的铁 精矿按生产配比单独配料(用等用量的国内 精矿替代高品位富粉、中铁中硅粉以及利废 物等).在固盘造球机上制成直径为8—16 mm球团,将粉矿等含铁原料(配比64.5%)与 返矿、全部或绝大部分焦粉与熔剂一起配 料,并按传统丁艺进行~混、二混准备,将 造好的球团与二混后的原料混合后进行布 料、点火、烧结。 新T艺实验室试验流程如图l所示。烧
487
h).转鼓指数相应nI
60
40%提高到
64 00%。
表1复合造块实验室探索试验结果
说明:害妻答缫,j羞瑟嚣弩譬臻黼嘉嚣挚军龋猕溢赫尊嚣灰所。㈣舭删,
分配。
试验结果表明,当料层高度保持不变 时,采用复合造块j。艺需婴降低烧结负爪= 保持精矿中生石肛的配比(I o%)和碱 度(0
56—0
研究表明,在其它条件小变的情况下,
炉哇产 3.1显微结构分析・
总体上说,对于复合烧结块而言,无论 是矿物组成,还是显微结构都比较理想,尤 其是球团与球团之问,铁酸钙的形成、发育
完善,是一种以铁酸盐作为主要胶结相的高
质量炼铁炉料。
在复合人造块中大约有40%一50%的球
团,球团内部以结晶良好、晶形粗大互连的 Fe,O.为主,同时也有较多的橄榄石(主要是 钙铁橄榄石)粘结相生成。 在小球的中层,可清楚地看到由Fe,O。逐 渐氧化成Fe,O,的过渡带,此问Fe:0,与 Fe,O.交织混杂;小球的核心是橄榄石与 Fe,O。紧密胶结的区域;Fe,O,结晶良好,晶 形粗大互连,结构力好。橄榄石大部分为钙 铁橄榄石,但也可见少量的2FeO・SiO:生 成。
m2烧结机
为期1个月以上的1:业试验。 1)粉矿:由火车运到二烧熔剂仓,经 人l:卸料后,送至二烧配料仓(对现有配料 仓进行重新调整,一部分仓配粉矿,一部分 仓配精粉,熔剂只用生石灰一种)。 2)精矿:利用精粉料场精粉,经球团 精粉运输路线至二烧配料仓。从配料室开 始,再增加一套皮带系统,将精粉运至二烧 造球室造球。粉矿制粒与精矿造球后,通过 皮带系统运至二混混匀,进入烧结、冷却环 节。 3)成品矿:经小球烧结成品输送系统 送至低料仓,供4’高炉做:I二业扩大试验。
太钢实施高铁低硅烧结初步探讨

2003年l2月December2003钢铁研究Research on Iron &SteeI第6期(总第l35期)No.6(Suml35)太钢实施高铁低硅烧结初步探讨贺淑珍边建刚李铁(太原钢铁集团公司)摘要根据试验室试验和工业试验,讨论了太钢实施高铁低硅绕结的技术问题。
针对高铁低硅烧结矿存在的质量问题,提出了相应的改进措施。
关键词高铁低硅烧结矿质量参数A STUDY ON HIGH IRON AND LOW SILICA SINTER PRODUCTIONAT TAIYUAN IRON AND STEEL GROUP CO ,LTDHe Shuzhen Bian Jiangang Li Tie(Taiyuan Iron and SteeI Corp Co.)Synopsis Based on the Iaboratory and industriaI experiments carried out at Taiyuan SteeI ,this paper discusses technoIogicaI probIems encountered in the high iron and Iow siIica sinter pro-duction.To improve the sinter guaIity corresponding measures are put forward in the paper.Keywords high iron and Iow siIica sinter guaIity parameter联系人:贺淑珍,高级工程师,太原市(030003)太钢技术中心铁前工艺室1前言随着高炉冶炼技术的提高,精料技术进步显得尤为重要。
高铁低硅烧结技术正是目前高炉精料技术发展的趋势。
高铁低硅烧结矿入炉,使得炉渣渣量减少,炼铁焦比降低,高炉利用系数提高,冶炼成本降低。
2002年太钢,投资对自产精矿进行了降硅处理,铁系统资源将发生较大的变化,烧结原料由高硅烧结(烧结矿SiO 2=7%)转向低硅烧结(SiO 2=5%以下),烧结矿性能将发生变化。
低硅烧结技术的开发

的根本性 变化和 降本增 效 的生 产需 求 , 口富矿 粉使 进
用 比例逐步提高 。目前烧结用铁精粉和烧结矿 中 SO i
含 量 已经 降至低 硅烧 结水平 ,铁精 粉 中 S 量为 i 含 O
35 60 进 口富粉 中 SO 含量 为 28%~ .3 烧 . %一 . %。 i . 2 4 %, 0 结 矿 中 SO 含量为 45 6 %, i . %~ . 这就为天铁研 究开发 0 低 硅烧结 技 术提供 了技术 前 提 、原料 基础 和经 验 总
对高炉冶炼 的核心作用是 品位提高, 量明显下降 。 使渣 反映在 炉况顺 行过程 中, 因渣量 的下降, 善 了软 一是 改 熔带的透气性 ; 二是 因烧结矿 品位的提高, 炉料的软 使
熔温度上升, 高炉 内部的软熔带 下移 , 使 熔化温度 区间 缩小 ; 三是渣量 减少还有利 于喷煤 比的提 高。通常 , 1 k i gSO 在高炉 内要形成 2k 炉渣 , g 烧结矿 中 SO 含量 i
临 的主要技 术难题 是解 决 由于铁高 、 硅低 、 量少 所 渣 带来的强度显著下降问题 。低硅烧结 的关键在于形成
原率 和开始收缩温度 . 从而使软熔带变薄 。
t j
m一 7 发 技I 碹 嚏 Ⅱ 技I 与 了 一 w m c 开 c 改
维普资讯
维普资讯
⑨ ⑤ 第晷 总 @ ⑨ 年 期 第 固期
低 烧 技 的 发 硅 结 术 开
低 硅 烧 结 技 术 的 开 发
陈翔 勇 ( 津天铁 冶金 集 团有 限公 司科技 质量 部,54 4 天 0 60 )
[ 摘要 ] 系统地阐述 了低硅烧结技术的原理和上艺要求, 以及低硅烧结矿 的冶金性 能和存在的 问题 , 结合 当前 天铁烧结 生产 现状 , 了实施低硅烧结技术的技术定位 和指导原则, 论述 以及满足低硅烧结所必需 的丁艺技术条件和生产措施 。
国内外烧结技术发展现状资料

1-3园筒混合机的强化制粒
强化制粒技术不仅是小球烧结的关键技术,也是烧结生产
实现低C原料层的基础技术,它除了与上2节提到的原料粒度和
粘结剂有关外,更主要地由以下4个方面的内容:
1-3-1:园筒混合机及其工艺参数:
(1)园筒混合机的长度,直径和转速:
通过北京科技大学大量的研究得出,混合料在园筒内的最
细精矿粉烧结遇到的一个普遍技术问题,是混合料透气性的 问题。过去低料层(<350mm)烧结自焙性烧结矿时,这个问 题还不大突出,进入八十年代以来,要烧高碱度烧结矿提高 料层、改善烧结矿质量时,这个问题就很突出,降低FeO, 提高强度就要加原料层,原料层烧结的一个首要问题就是如 何改善混合料透气性的问题,也是球团烧结、小球烧结的一 项关键技术问题。这个问题既是实际问题,又是一项重大理 论问题。与强化制粒相关联的是一系列技术问题,诸如原燃 料的粒度和粒度组成问题,改善制粒的粘结剂问题,园简混 合机的内衬材料和工艺参数问题,混合料水份的配加及方式 问题等等。
1-1:原燃料的粒度及粒度组成问题:[1][2]
日本新日铁公司自七十年代末就开始研究原料粒度对混 合料制粒的影响,并且提出了“人造料粒”的概念,“料 粒”就是较细颗粒粘附到较粗(粒核)颗粒上,八十年代末 法国学士利特斯特提出一个与水分有关的中间颗粒粒度范 围,这个粒度范围一般为0.25~1.0mm,这种粒级从以 下两个方面影响混合料的透气性:
(1)作为粒核,这种粒级会减小料粒的平均粒度,因而 降低混合料的透气性。
(2)作为粘附细粉,这种粒级的粘附性差,很容易从干燥 中的料粒表面上脱落下来。
利特斯特的研究还发现,粒核结构(表石形状,气孔率 等)水分和细粉含量是影响在粒核上粘附细粉程度的三因 素。形状不规则的返矿,焦粉和针铁矿颗粒能成为良好的 粒核;表面平整,形状规则的石灰石,致密的赤铁矿颗粒 不能成为良好的粒核。
4号烧结机降硅烧结生产实践
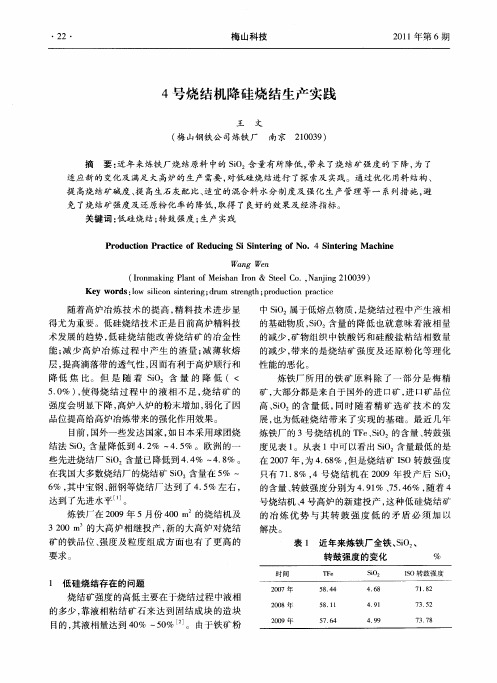
好操 作方 案 。
随着 高炉 冶炼 技 术 的提 高 , 料 技术 进 步 显 精 得尤 为重 要 。低硅烧 结技 术正 是 目前高 炉精料 技 术发 展 的趋 势 , 硅 烧结 能改 善 烧 结 矿 的 冶金 性 低
中 SO 属 于低熔 点物 质 , 烧 结过 程 中产 生 液相 i 是
的基础 物质 ,i, SO 含量 的降 低 也就 意 味 着 液 相量
低 到 。 . % 。 为 了强 化 制 粒 , 次 混 合 与 二 次 T6 7 一 混合 按 照 4 1的 比例 进行 加 水量 的控 制 , 本 能 : 基
升 了 0 4 ,R I .7 % D n R I 。分 别 上 升 了 D 05 % 、.5 。这说 明将 烧结 矿 SO .5 07 % i,含量 降 低
主要 由褐 铁 矿 组 成 , 有 较 多 的 结 晶 水 , 损 较 含 烧
在 对炼 铁 厂所 用 的各种 矿物 的理化性 能 进行 多项 指 标 的测试 后 , 矿 物 之 间 的 同化 性 能 及 促 从
进烧 结 液相 生成 的角 度 , 原料 矿 物进 行 了优 化 对
配 比。
大 , 利 于 形 成 致 密 的 宏 观 结 构 , 时 铁 品 位 不 同
的一 个关 键 因素 , 结矿粘 结 相 的抗 压强 度 、 烧 粘结 相 强度等 都会 随 着 碱度 的提 高 而 逐渐 增 强 , 高 提 碱度 有利 于促 进铁 酸钙 的生 成 , 结 矿 的宏 观 结 烧 构也 随之 由 自熔性 的多 空薄壁 结构 过渡 到高 碱度 的大孔厚 壁结 构 。有 研 究 表 明 j随 着烧 结 矿 碱 : 度 的提 高 , 结矿 矿物组 成 中 S C 明显增 多 , 烧 FA 玻 璃 相和残 余 脉 石减 少 , 结 矿 强 度 升高 。根 据 炼 烧 铁 厂 的生 产实 际 考 虑 , 将烧 结 矿 的碱 度控 制 由原
关于低硅烧结的探讨

关于低硅烧结的探讨【摘要】适当降低烧结矿SiO2,一方面能提高烧结矿品味进而提高高炉入炉品味,另一方面可减少高炉渣量,改善高炉冶炼条件,对降低焦比,提高利用系数和稳定炉况具有深远的意义。
【关键词】低硅高品位烧结矿;烧结性能;还原机理;节能降耗前言随着炼钢技术的发展,生铁中的硅作为发热剂的意义早已不很重要,为了满足无渣或少渣炼钢的需要,炼钢生铁含硅量逐渐降低。
同时,低硅生铁对于铁水炉外预处理(脱磷、脱硫)是有益的。
再者,冶炼低硅生铁对降低焦比提高产量也是很有益的。
一般生铁中硅(Si)每降低1%,焦比降低4~7kg/t铁。
最近l0年来,国内外高炉冶炼低硅生铁有新的进展和突破。
我国炼钢生铁含硅量在20世纪70年代ω(Si)为0.8%左右,现在也降低到0.6%左右,大型高炉铁水含硅量已降低到规(Si)为0.2%~0.4%。
1 还原机理高炉内硅的还原是按照SiO2→SiO→Si的顺序逐级进行的。
高炉中硅还原进入生铁的过程主要是在滴落带进行,并以SiO气体为中介还原转入铁水中。
(SiO2)+C=SiO+COSiO+[C]=[Si]+CO[Si]+2(MnO)=2[Mn]+SiO2[Si]+2(FeO)=2[Fe]+(SiO2)2 降低生铁含硅量的途径:(1)有效降低烧结矿含硅量,是降低高炉冶炼渣量,也就是减少SiO2的来源,抑制硅的还原反应,从而降低生铁[Si]含量。
(2)有效降低烧结矿含硅量,是提高烧结矿品味进而提高高炉入炉品味的最直接有效途径。
高炉冶炼表明:入炉品味每提高1%,焦比下降2%,产量提高3%。
可见低硅烧结对高炉冶炼中降低焦比,提高生铁产量有着客观的经济效益。
(3)有效降低烧结矿含硅量,是提高炉渣的二元和三元碱度炉渣的二元碱度指m(Cao)/m (SiO2),三元碱度指m(CaO+MgO)/m(SiO2)。
提高炉渣的二元和三元碱度,可降低炉渣中SiO2的反应性,从而可以抑制硅的还原。
,3 低硅烧结工艺优化探讨3.1 低硅烧结的意义低SiO2烧结矿,一般是指烧结矿中的SiO2含量低于5.0%的烧结矿,它具有以下优点:使入炉品位提高,渣量减少;改善烧结矿冶金性能,尤其是其软熔温度升高、软熔区间变窄,可使高炉的软熔带位置下移,厚度变薄,有利于高炉内间接还原发展和料柱透气性和透液性的改善。
铁精矿“提铁降硅”工艺技术探讨

铁精矿“提铁降硅”工艺技术探讨1 前言随着我国市场经济的形成和加入WTO,钢铁业对铁精矿的质量要求不断提高,特别是对硅含量的要求更加严格,一般要求sio2含量在4%以下。
我国磁铁精矿普遍存在着硅含量高的问题(平均6.3%左右),高硅铁精矿制约了炼铁经济效益的提高。
加入WTO后,国产磁铁精矿受到进口优质铁精矿的冲击,严重影响了我国铁矿山的可持续发展,这种严重的态势已经引起各矿山企业的高度重视,我国铁矿业已兴起铁精矿“提铁降硅”的技术改造高潮。
我们首钢水厂选矿厂虽然铁精矿品位达到了68%以上,但由于矿石性质问题sio2含量仍达3.99%,随已接近世界先进水平,硅含量仍然偏高。
为降低硅含量,必须从提高铁精矿品位入手。
“提铁降硅”技术实际就是如何解决铁精矿中贫连生体与单体矿物有效分离技术。
在许多选矿厂,尤其是磁选厂,由于缺乏有效的技术、工艺和设备将精矿中的贫连生体分离出去,使精矿品位迟迟得不到提高。
为此我们进行了“提铁降硅”工艺技术研究,提出了进一步降低硅含量的技术途径。
2 工艺技术现状2.1 概况首钢水厂选矿厂1971年5月投产,经过多年的技术改造和扩建挖潜,形成了设计年处理原矿1800万吨的生产能力,现有19个磨选系列,选矿工艺流程为阶段磨矿阶段选别磁选流程,经过细筛、磁滑轮干选工艺、磁团聚新工艺等一系列改造,精矿质量由投产时的63%左右逐步提高到79年以来的68.0%以上,精矿粉中SiO2含量由8.93%降到3.99%。
2.2原矿性质首钢水厂铁矿石属鞍山式贫磁铁矿,铁矿物以磁铁矿为主,其次为假象赤铁矿、褐铁矿和黄铁矿。
磁铁矿有四种类型:磁铁石英岩、辉石磁铁石英岩、磁铁-辉石石英岩及赤铁-磁铁石英岩。
脉石矿物以石英、角闪石为主,其次有方解石、绿泥石、黑云母,此外尚有极少量的磷灰石、尖晶石及碳酸盐矿。
矿石以条带构造为主,浸染状构造次之,矿石呈不均匀嵌布结构。
磁铁矿结晶粒度0.5-0.062mm,硬度8-12,矿石密度3.1-3.2吨/立方米。
5低硅烧结
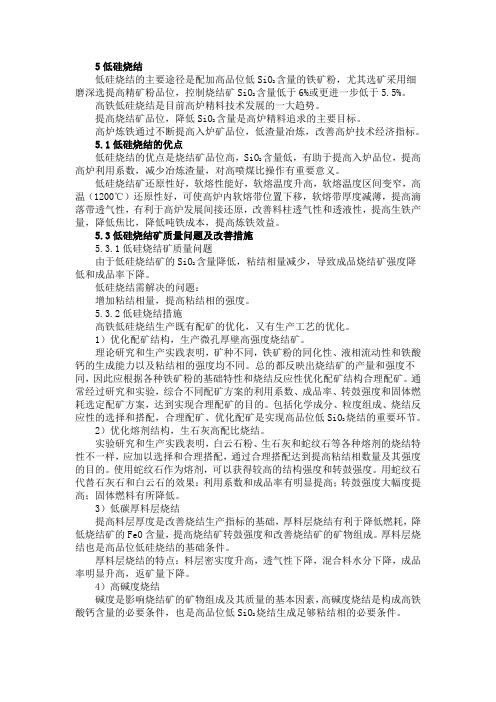
5低硅烧结低硅烧结的主要途径是配加高品位低SiO2含量的铁矿粉,尤其选矿采用细磨深选提高精矿粉品位,控制烧结矿SiO2含量低于6%或更进一步低于5.5%。
高铁低硅烧结是目前高炉精料技术发展的一大趋势。
提高烧结矿品位,降低SiO2含量是高炉精料追求的主要目标。
高炉炼铁通过不断提高入炉矿品位,低渣量冶炼,改善高炉技术经济指标。
5.1低硅烧结的优点低硅烧结的优点是烧结矿品位高,SiO2含量低,有助于提高入炉品位,提高高炉利用系数,减少冶炼渣量,对高喷煤比操作有重要意义。
低硅烧结矿还原性好,软熔性能好,软熔温度升高,软熔温度区间变窄,高温(1200℃)还原性好,可使高炉内软熔带位置下移,软熔带厚度减薄,提高滴落带透气性,有利于高炉发展间接还原,改善料柱透气性和透液性,提高生铁产量,降低焦比,降低吨铁成本,提高炼铁效益。
5.3低硅烧结矿质量问题及改善措施5.3.1低硅烧结矿质量问题由于低硅烧结矿的SiO2含量降低,粘结相量减少,导致成品烧结矿强度降低和成品率下降。
低硅烧结需解决的问题:增加粘结相量,提高粘结相的强度。
5.3.2低硅烧结措施高铁低硅烧结生产既有配矿的优化,又有生产工艺的优化。
1)优化配矿结构,生产微孔厚壁高强度烧结矿。
理论研究和生产实践表明,矿种不同,铁矿粉的同化性、液相流动性和铁酸钙的生成能力以及粘结相的强度均不同。
总的都反映出烧结矿的产量和强度不同,因此应根据各种铁矿粉的基础特性和烧结反应性优化配矿结构合理配矿。
通常经过研究和实验,综合不同配矿方案的利用系数、成品率、转鼓强度和固体燃耗选定配矿方案,达到实现合理配矿的目的。
包括化学成分、粒度组成、烧结反应性的选择和搭配,合理配矿、优化配矿是实现高品位低SiO2烧结的重要环节。
2)优化熔剂结构,生石灰高配比烧结。
实验研究和生产实践表明,白云石粉、生石灰和蛇纹石等各种熔剂的烧结特性不一样,应加以选择和合理搭配,通过合理搭配达到提高粘结相数量及其强度的目的。
烧结生产工艺技术讲课1

烧结介绍 烧结原料 烧结工艺及配置 烧结岗位设置 建72㎡烧结机缘由 打造绿色烧结
铁矿粉烧结是重要的造矿技术之一。由于开采时产生 大量的铁矿粉,特别是贫铁矿富选促进了铁精矿粉烧结的 生产和发展,使铁矿粉烧结成为规模最大的造块作业。其 物料的处理量约占钢铁联合企业的第二位(仅次于炼铁生 产),能耗仅次于炼铁及轧钢而居第三位,成为现代钢铁 企业的重要生产工序。铁矿粉烧结要求烧结矿具有很好的 物理、冶金性能。烧结矿经历冶炼高温过程,要求有一定 的热强度,即在高温还原气氛下耐压、耐磨及耐热爆裂性 能;烧结矿在高炉内经历物理化学反应,要求它具有良好 的冶金性能,如还原性、软化性、熔滴性等。铁矿粉烧结 技术的困难还在于追求合理的经济效果,因此,铁矿粉烧 结是一门技术复杂的专门学科。
需混合料7971t,按单一矿生产配比:镍
矿粉94%(7324t)、生石灰6%(478t)、
焦粉7%(558t)。
生灰消化除尘
本装置采用了粉尘迷宫运行和流体动力学技术,使
风机产生的有效风力均衡地分配到各除尘管道内部,
使生石灰在消化过程中所产生的热蒸汽和粉尘均匀
的全部经过高压水沫和水箱内部水的处理和过滤,
我厂烧结原料主要是红土镍矿,红土
镍矿资源是硫化镍矿岩体风化―淋滤―沉
积形成的地表风化壳性矿床,和普通铁矿
相比,红土镍矿品位低,二氧化硅含量高,
含水量大,一般都是毛矿,需要进行二次
加工方能使用。
世界上红土镍矿分布在赤道线南北30度以 内的热带国家,集中分布在环太平洋的热带 ――亚热带地区,主要有: 新喀里多利亚镍矿带 印度尼西亚:摩鹿加镍矿带、苏拉威西镍矿带; 菲律宾:巴拉望地区镍矿带; 澳大利亚:昆士兰镍矿带; 巴西:米纳斯吉拉斯镍矿带、戈亚斯镍矿带; 古巴:奥连特镍矿带等。
低硅烧结技术措施

低硅烧结技术措施
1.原料选择:选择低硅含量的铁矿石作为主要原料,降低烧结矿中的硅含量。
同时,还可以选择辅料中低硅含量的物料,如高品位矿石和高品位焙烧矿等。
2.混合配比优化:根据不同原料的硅含量和配比比例,优化混合配比,使得整个烧结料中的硅含量降低。
可以采用配料软件进行计算和优化,找到最佳的配比方案。
3.石灰石的添加:适当添加一定量的石灰石,可以通过与矿石中的硅反应生成易溶性的硅酸钙,从而减少烧结料中的硅含量。
4.过程控制:在烧结过程中,控制烧结温度、矿石粉末颗粒大小、烧结时间等参数,以最大程度地降低硅的渗透和扩散。
5.燃料选择:选择低硅含量的燃料,如选择低硫煤粉作为燃料,可以降低燃料中硅的含量,从而减少烧结料中的硅含量。
6.过滤及湿法处理:使用过滤和湿法处理技术,可以去除烧结矿中的硅质细粉,从而降低烧结料中的硅含量。
7.合理的工艺流程设计:通过合理的工艺流程设计,使得烧结过程中的硅质物质尽可能早地进入烧结矿的熔融相,从而减少硅的固溶和扩散。
FeSi磁性材料的烧结制备工艺

04
烧结fesi磁性材料的性能 表征
物理性质和显微结构分析
密度测量
使用比重瓶法或浮力法测量样 品的真实密度。
颗粒大小与形貌
通过扫描电子显微镜(SEM) 观察样品的颗粒大小和形貌。
晶相分析
通过X射线衍射(XRD)确定样 品的晶相结构。
磁学性能测试与表征
饱和磁化强度(Ms)
在给定的磁场强度下,材料被磁化的最大 程度。
研究;
性能关系研究;
学性能测试与分析。
02
fesi磁性材料的制备
fesi磁性材料的制备方法
01
02
03
熔炼法
将原料熔化并倒入水中, 得到粉末,然后进行烧结 。
喷雾干燥法
将原料溶液通过喷嘴雾化 ,得到粉末,然后进行烧 结。
溶胶凝胶法
将原料溶液加入到沉淀剂 中,得到凝胶,然后进行 烧结。
原料的选择与处理
fesi磁性材料的烧结制备工 艺
2023-11-07
目录
• 引言 • fesi磁性材料的制备 • fesi磁性材料的烧结工艺 • 烧结fesi磁性材料的性能表征 • 结论与展望 • 参考文献
01
引言
研究背景和意义
• 随着电子信息技术的飞速发展,磁性材料在信息存储、电磁屏蔽、电子通讯等领域的应用越来越广泛。其 中,铁硅(FeSi)合金因其具有高磁导率、低矫顽力等优良特性而备受关注。然而,FeSi合金的电阻率较低 ,在大电流作用下容易产生涡流损耗,限制了其在高频领域的应用。为了解决这一问题,研究者们提出了 一种新型的磁性材料——FeSi基磁性半导体(FeSi-based magnetic semiconductor,简称FESI)。
06
参考文献
铁精矿“提铁降硅”工艺技术探讨
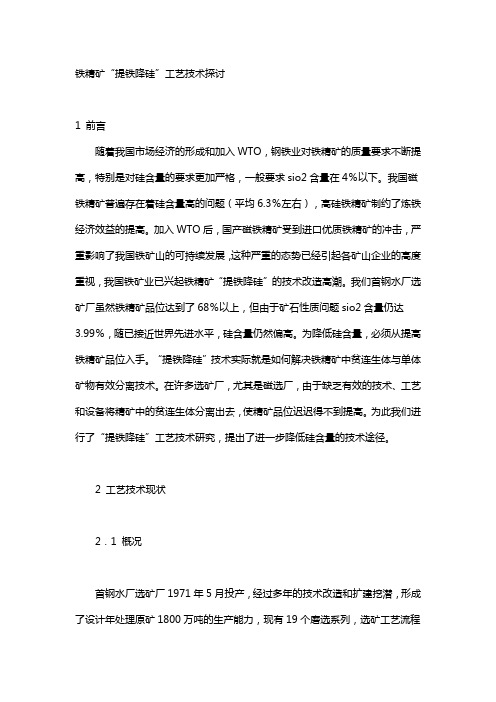
铁精矿“提铁降硅”工艺技术探讨1 前言随着我国市场经济的形成和加入WTO,钢铁业对铁精矿的质量要求不断提高,特别是对硅含量的要求更加严格,一般要求sio2含量在4%以下。
我国磁铁精矿普遍存在着硅含量高的问题(平均6.3%左右),高硅铁精矿制约了炼铁经济效益的提高。
加入WTO后,国产磁铁精矿受到进口优质铁精矿的冲击,严重影响了我国铁矿山的可持续发展,这种严重的态势已经引起各矿山企业的高度重视,我国铁矿业已兴起铁精矿“提铁降硅”的技术改造高潮。
我们首钢水厂选矿厂虽然铁精矿品位达到了68%以上,但由于矿石性质问题sio2含量仍达3.99%,随已接近世界先进水平,硅含量仍然偏高。
为降低硅含量,必须从提高铁精矿品位入手。
“提铁降硅”技术实际就是如何解决铁精矿中贫连生体与单体矿物有效分离技术。
在许多选矿厂,尤其是磁选厂,由于缺乏有效的技术、工艺和设备将精矿中的贫连生体分离出去,使精矿品位迟迟得不到提高。
为此我们进行了“提铁降硅”工艺技术研究,提出了进一步降低硅含量的技术途径。
2 工艺技术现状2.1 概况首钢水厂选矿厂1971年5月投产,经过多年的技术改造和扩建挖潜,形成了设计年处理原矿1800万吨的生产能力,现有19个磨选系列,选矿工艺流程为阶段磨矿阶段选别磁选流程,经过细筛、磁滑轮干选工艺、磁团聚新工艺等一系列改造,精矿质量由投产时的63%左右逐步提高到79年以来的68.0%以上,精矿粉中SiO2含量由8.93%降到3.99%。
2.2原矿性质首钢水厂铁矿石属鞍山式贫磁铁矿,铁矿物以磁铁矿为主,其次为假象赤铁矿、褐铁矿和黄铁矿。
磁铁矿有四种类型:磁铁石英岩、辉石磁铁石英岩、磁铁-辉石石英岩及赤铁-磁铁石英岩。
脉石矿物以石英、角闪石为主,其次有方解石、绿泥石、黑云母,此外尚有极少量的磷灰石、尖晶石及碳酸盐矿。
矿石以条带构造为主,浸染状构造次之,矿石呈不均匀嵌布结构。
磁铁矿结晶粒度0.5-0.062mm,硬度8-12,矿石密度3.1-3.2吨/立方米。
鞍山地区铁精矿提铁降硅工艺改进的思考

鞍山地区铁精矿提铁降硅工艺改进的思考
鞍山地区的铁精矿提铁降硅工艺技术在当前的发展中可以说是取得非常显著的进步。
然而,为了提高铁精矿提铁降硅的效率,要持续改进工艺。
首先,我们要在添加剂技术上做一些改进。
添加剂一般都会影响降硅过程中硅的形态,从而影响提铁速度和提高铁精矿提铁效率。
其次,要在提铁条件及技术改进方面做一些尝试。
可以在温度,pH值等条件上进行优化,让提铁过程更加顺利。
此外,还要重视装置的自动化程度,力求让操作更为高效。
例如,可以控制装置的温度和pH值,对结晶性、料厚度等也能产生较好的控制。
当然,对维护的重视也是非常重要的,如正常的润滑及维持设备清洁,这一点也非常重要。
总之,提高鞍山地区铁精矿提铁降硅工艺效率还有很大的空间,从添加剂技术方面,和从提铁条件及技术和自动化方面要对工艺进行优化,以达到更高效率。
铁矿石低温烧结技术

铁矿石低温烧结技术低温烧结是目前世界上烧结工艺中一项先进技术,它具有节能降耗和改善烧结矿冶金性能两大优点。
所谓低温烧结法,就是以较低的烧结温度(低于l300℃),使烧结混台料中部分矿粉起反应,产生一种强度好、还原性好的较理想矿物——针状铁酸钙,并以此去粘结、包裹那些未起反应的残余矿石(或叫未熔矿石),使其生成一种钙铝硅铁固溶体(又称SFCA)。
控制生产SFCA矿物结构的烧结工艺方法被称为低温烧结法。
它除了节能外,还可以明显改善烧结矿的冶金性能,大幅度提高烧结矿还原性,降低烧结矿FeO,并有利于降低烧结矿低温还原粉化率。
(1)低温烧结矿的矿物结构烧结矿的主要矿物组成大致可以分为赤铁矿、磁铁矿、铁酸钙和硅酸盐。
烧结矿的微观强度取决于其矿物组成的单质强度。
(2)细针状铁酸钙生成条件生产SFCA类型结构烧结矿取决于混合料的化学组成以及实际的烧结工艺条件,尤其是温度分布水平。
①烧结温度:烧结温度的高低直接影响铁酸钙的形成。
②烧结矿碱度:低温烧结矿转鼓强度随碱度的提高而得到改善。
③烧结气氛:烧结过程中较强的氧化气氛有利于复合铁酸钙的生成,不仅Fe3O4氧化需要氧化气氛,而且针状铁酸钙的生成也需要氧化气氛。
④烧结过程高温保持时间:一般低温烧结矿在1100℃以上,高温保持时间都在5min~8min,比熔融型烧结矿要长1min~3min,这对细针状铁酸钙的形成和发育十分有利。
⑤混合料SiO2含量:据有关资料介绍:SiO2含量在4%~8%范围内的高碱度烧结矿,都可以生成复合针状铁酸钙,SiO2含量高的烧结矿,其还原性略差一些。
⑥混料Al2O3含量:当烧结矿的碱度和SiO2含量一定时,改变Al2O3/ SiO2的比值,烧结矿中SFCA的含量将发生变化。
一般Al2O3/ SiO2应控制在0.1~0.2,从发展针状SFCA的角度来看,该比值以靠近0.1为宜。
低温烧结技术的工艺特点及措施:(1)原料准备原料准备包括原、燃料和熔剂的加工贮存和混匀。
- 1、下载文档前请自行甄别文档内容的完整性,平台不提供额外的编辑、内容补充、找答案等附加服务。
- 2、"仅部分预览"的文档,不可在线预览部分如存在完整性等问题,可反馈申请退款(可完整预览的文档不适用该条件!)。
- 3、如文档侵犯您的权益,请联系客服反馈,我们会尽快为您处理(人工客服工作时间:9:00-18:30)。
反应变缓, 可缩短液相烧结时间, 提高料层透气性, 从而改善烧结矿的矿物组织, 减小骸晶状赤铁矿生 成, 促进针状铁酸钙增多。另外, 石灰石粗粒化还可 使烧结过程中的液相量增加, 流动性增强, 使气孔形 状由凹凸不规则状转变为球状, 有利于烧结矿强度 和 RDI 指标的改善。 3 结语
烧结矿碱度是决定铁酸钙生成量的关键因素。 从对不同碱度烧结矿中分离出的粘结相性能测试结 果表明: 粘结相的抗压强度、粘结强度、还原性及抗 还原粉化性能都随碱度的提高而逐渐增强, 烧结矿 的宏观结构也随之由自熔性的多孔薄壁结构过渡到 高碱度的大孔厚壁结构, 因此, 强度得到提高。
厚料层烧结具有良好的蓄热作用, 可减少燃料 用量, 而且垂直烧结速度的减慢和烧结混合料中氧 化气氛的增强, 有利于铁酸钙液相的充分发展和析 晶, 从而提高烧结矿的转鼓指数和成品率[ 2] 。
低 硅 烧 结 面 临 的 主 要 技 术 难 题 是 由 于 硅 低 、渣 量少而产生强度低的问题。日本、瑞典主要采取提高 烧结矿碱度和生产复合优化烧结矿的方法来增加烧 结矿中铁酸钙含量, 达到提高烧结矿强度的目的。
发展以针状 SFCA 为主要粘结相的烧结矿是进 一步改善烧结矿质量的根本途径。随着烧结碱度的 提高, 烧结矿中 SiO2 由主要生成硅铁酸盐渣相变为
作者简介: 于强, 男, 1963 年生, 现为山西工程职业技术学院冶金系讲师。Tel: 0351- 3350420, E- mail: yh- yq@sxgy.cn
· 42 ·
山西冶金
第 29 卷
2.3 采用小球团燃料分加工艺 小球团烧结法是在普通烧结法的基础上结合球
团焙烧法的优点发展起来的一种新的造块工艺。它 将混合料全部造球, 燃料大部或全部外滚, 有很好的 料层透气性和产品性能。通过强化制粒, 使原料颗粒 间的结合力增强, 抑制了成品率和强度的下降, 实现 了高烧结生产率下的低 SiO2 烧结生产。 2.4 控制石灰石粒度
通过提高生石灰配比及优化生石灰消化与混合 料 制 粒 时 间 , 在 焦 粉 配 比 5% ̄6% , 混 合 料 水 分 8.0%, 生石灰配比 6.0%, 消化 10 min, 制粒 6 min 的 条件下进行强化制粒烧结, 可提高烧结矿成品率和 转鼓指数, 降低 Fe0 含量, 因此, 强化制粒能够改善 高铁低硅烧结矿质量。同时, 强化制粒所得高铁低硅 烧结矿铁酸钙含量增加, 且呈针状、条状及熔蚀状、 与 Fe3O4 和 Fe2O3 形成良好的交织结构, 其中铁橄榄 石、硅酸二钙、玻璃质较少, 因此, 强化制粒显著改善 了烧结矿矿物组成和显微结构。 2.2 实行高碱度厚料层烧结
总第 102 期 2006 年第 2 期
文章编号: 1672- 1152( 2006) 02- 0041- 02
山西冶金 SHANXI METALLURGY铁精矿粉Fra bibliotek铁低硅烧结技术
Total 102 No. 2, 2006
于强
( 山西工程职业技术学院, 山西 太原 030009)
摘 要: 通过对铁矿粉低硅烧结机理进行探讨和研究, 解决了低硅烧结带来的液相量少、强度低等技术问题, 取
主要生成铁酸钙。通过控制适宜的烧结温度、碱度、 烧结气氛和时间、SiO2 和 Al2O3 的比值, 可以生成强 度高、还 原 性 好 的 以 细 针 状 复 合 铁 酸 钙( SFCA) 为 主要粘结相的烧结矿。同时, 磁铁矿和赤铁矿都能很 好地与铁酸钙形成交织结构。 2 实现低硅烧结的工艺条件 2.1 加强混合料制粒
实施低硅烧结技术不仅能改善烧结矿的冶金性 能, 还可以降低高炉渣量, 减薄软熔带, 提高滴落带 透气性, 有利于高炉顺行和降低焦比。从目前高炉的 应用效果来看, w( SiO2) 为 4.5%左右的烧结矿可以 满足高炉正常生产的需要, 高炉总体透气性改善, 有 利于增加喷煤和提高焦炭负荷。低硅烧结是高炉精 料技术的发展方向。
得了可观的经济效益。
关键词: 精矿 低硅烧结 强度
中图分类号: TF521
文献标识码: A
收稿日期: 2006- 05- 15
随着我国高炉炼铁技术的不断进步, 对高炉原 料的含铁品位和 SiO2 含量的要求越来越高。众所周 知, 低硅烧结能改善烧结矿的冶金性能, 减少高炉冶 炼过程中产生的渣量, 减薄软熔带, 提高滴落带的透 气性, 因而有利于高炉顺行和降低焦比; 同时, 减少 渣量还有利于增加高炉的喷煤量。通常入炉矿含铁 品位每升高 1%, 焦比可降低 2%, 产量提高 3%,渣量 减少 20 kg/t 铁, 生铁成本下降 10 元 /t 铁。但随着烧 结矿含铁品位的提高, SiO2 含量降低, 液相减少, 烧 结矿强度和产量将受到影响, 因此, 高铁低硅烧结矿 的生产必须采取适宜的工艺和技术措施。
参考文献 [ 1] 朱德庆.强化制粒对高铁低硅烧结的影响[ J] .烧结球团, 2003
( 1) : 10- 11. [ 2] 周晓华.马钢三烧低 SiO2 烧结的生产实践[ J] .烧结球团, 2003
( 4) : 44- 46.
( 责任编辑: 胡玉香)
Low- SiO2 Sinter ing Technology of Ir on Or e Concentr ates
YU Qiang
( Shanxi Engineering Vocational Technology College,Taiyuan 030009)
Abstr act: Through the experimental study, some key technical problems of low-SiO2 iron ore concentrates sintering, e.g. little binder phase and lower strength etc. were solved. After the SiO2 content was decreased to 4.5%, the BF technico- economic indices were improved. Key wor ds: iron ore concentrate, low SiO2 sintering, strength !!!!!!!!!!!!!!!!!!!!!!!!!!!!!!!!!!!!!!!!!!!!!! ( 上接第 40 页)
Resear ch about Vir tual Modeling and Simulating of Planetar y Tr ansmission on ADAMS
HAN Xiying
( North University of China, Taiyuan 030051)
Abstr act: A dynamical model of the planetary transmission has been built in ADAMS Engine block, and the procedure of modeling of the planetary transmission in template has been introduced, and the dynamical simulation has been tried in the engine starting phase at last. Key wor ds: planetary transmission, dynamical model, simulating, ADAMS
石灰石粒度对烧结生产率和烧结矿质量有很大 的影响。粒度越粗, 料层的透气性越好, 烧结生产率 越高, 但过粗( 大于 3 mm) 时, 因其不能完全矿化将 会导致液相生成量不足, 且矿物中铁酸钙数量减少, 赤铁矿量增加, 使烧结矿质量下降; 而粒度过细( 小 于 0.25 mm) 时, 又会使生成的液相平均碱度降低而 促使渣的生成, 且矿物中铁酸钙数量减少, 赤铁矿和 磁铁矿数量增加, 同样降低烧结矿质量。
近年来, 国内外许多烧结厂一直致力于烧结矿 的提铁降硅研究与生产。日本在 20 世纪 90 年代烧 结矿中 w( SiO2) 已降至 4.5% ̄4.6%。瑞典、芬兰等国 家的钢铁企业目前已将烧结矿中 w( SiO2) 降到 4% 以下。我国大多数烧结厂的烧结矿中 w( SiO2) 为 6%  ̄8%, 近年来, 随进口矿粉的增多和选矿技术的进 步, w( SiO2) 降到了 5% ̄6%, 其中宝钢、太钢、莱钢、 韶钢烧结矿中 w( SiO2) 为全国最低( 4.5%以下) , 达 到了世界先进水平[ 1] 。 1 低硅烧结机理