锻压成型1
材料成型及控制工程导论1
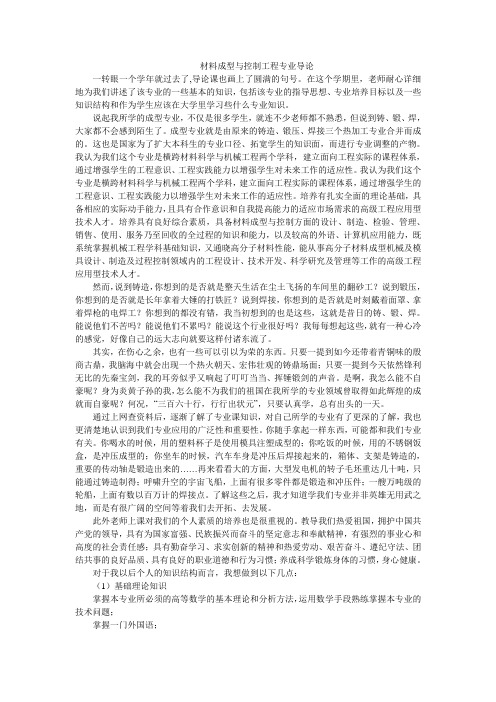
材料成型与控制工程专业导论一转眼一个学年就过去了,导论课也画上了圆满的句号。
在这个学期里,老师耐心详细地为我们讲述了该专业的一些基本的知识,包括该专业的指导思想、专业培养目标以及一些知识结构和作为学生应该在大学里学习些什么专业知识。
说起我所学的成型专业,不仅是很多学生,就连不少老师都不熟悉,但说到铸、锻、焊,大家都不会感到陌生了。
成型专业就是由原来的铸造、锻压、焊接三个热加工专业合并而成的。
这也是国家为了扩大本科生的专业口径、拓宽学生的知识面,而进行专业调整的产物。
我认为我们这个专业是横跨材料科学与机械工程两个学科,建立面向工程实际的课程体系,通过增强学生的工程意识、工程实践能力以增强学生对未来工作的适应性。
我认为我们这个专业是横跨材料科学与机械工程两个学科,建立面向工程实际的课程体系,通过增强学生的工程意识、工程实践能力以增强学生对未来工作的适应性。
培养有扎实全面的理论基础,具备相应的实际动手能力,且具有合作意识和自我提高能力的适应市场需求的高级工程应用型技术人才。
培养具有良好综合素质,具备材料成型与控制方面的设计、制造、检验、管理、销售、使用、服务乃至回收的全过程的知识和能力,以及较高的外语、计算机应用能力,既系统掌握机械工程学科基础知识,又通晓高分子材料性能,能从事高分子材料成型机械及模具设计、制造及过程控制领域内的工程设计、技术开发、科学研究及管理等工作的高级工程应用型技术人才。
然而,说到铸造,你想到的是否就是整天生活在尘土飞扬的车间里的翻砂工?说到锻压,你想到的是否就是长年拿着大锤的打铁匠?说到焊接,你想到的是否就是时刻戴着面罩、拿着焊枪的电焊工?你想到的都没有错,我当初想到的也是这些,这就是昔日的铸、锻、焊。
能说他们不苦吗?能说他们不累吗?能说这个行业很好吗?我每每想起这些,就有一种心冷的感觉,好像自己的远大志向就要这样付诸东流了。
其实,在伤心之余,也有一些可以引以为荣的东西。
只要一提到如今还带着青铜味的殷商古鼎,我脑海中就会出现一个热火朝天、宏伟壮观的铸鼎场面;只要一提到今天依然锋利无比的先秦宝剑,我的耳旁似乎又响起了叮叮当当、挥锤锻剑的声音。
机械制造基础教案(1)

《机械制造基础》第一讲绪论一、案例导入:本课程题目为《机械制造基础》,因此我们研究的内容都是围绕机械制造过程展开的。
那么到底机械制造过程有哪些呢?二、教学内容:1.本课程学习意义熟悉各种工程材料性能,合理选择材料;初步掌握和选用毛坯或零件的成形方法及机械零件表面加工方法;选用公差配合了解工艺规程制订的原则与方法2.本课程知识体系“工程材料”部分:以剖析铁碳合金的金相组织为基础,以介绍工程材料的性质和合理选材为重点;热加工工艺基础:“铸造”、“锻压”、“焊接”,认识这些加工方法的用途和实现方法;互换性与测量技术:理解公差配合概念与选用;机械加工工艺基础:“毛坯选择”、“金属切削加工技术”、“机械零件表面加工技术”、“机械加工工艺规程编制”特殊加工与先进制造技术:了解用途与应用场合3.学习方法总结归纳各章节学习目的,形成完整知识体系(宏观)突出各章重点与细节,加深对知识点的深入认识(微观)在相关生产实习过程中,遇到实际问题,结合课本知识,继续自学4.机械制造的概念将原材料(毛坯)和相关辅料转变成为成品(机械零件)的过程5.机械制造主要过程技术准备毛坯制造零件加工产品检验和装配产品检验和装配(1)技术准备阶段制订工艺规程原材料选则与供应刀具、夹具、量具的配备热处理设备和检测仪器的准备(2)毛坯制造阶段方法多种,常见的有铸造、锻压、焊接和型材铸造:金属液态成形,各种尺寸、形状复杂的毛坯或零件。
(适应性广、成本低廉)锻压:用外力对金属坯料施压使其产生塑性变形(锻造与冲压,改善金属的力学性能,生产效率高、节省材料)焊接:相互分离的金属材料借助于原子间的结合力连接起来。
(连接性好、省工省材料、结构重要轻)型材:直接从型材厂购买(3)零件加工阶段金属切削加工是主要加工手段。
(车、铣、钻、镗、磨、刨、插、拉)等特种加工应用日趋广泛(电火花、电解、超声波、激光、电子束、离子束、等离子弧、化学等等)选择原则:零件批量、精度、表面粗糙度、技术实现方式,价格成本等等综合考虑 (4) 产品检验和装配零件检验目的:使零件加工误差在允许范围内零件检验对象:一般场合,工序、加工过程中的尺寸变化、加工完成后几何形状误差;在要求高的场合(重载、高压、高温、可靠性要求很高)内部性能(缺陷检验、力学性能、金相组织检验)装配:遵守严格的装配规范。
第三章 模锻成形工序分析和模锻-1

2)精密成形时还应该考虑模具的弹性变形。
11
控制金属的流动方向
流动规律:塑性变形时金属主要向着最大主应力增大的方向 流动。在三向压应力下,金属主要是向着最小阻力增大的方 向流动。 通过不同的工具,采取不同的加载方式,在变形体内建立不 同的应力场来得到不同的变形和流动情况。
流动分 界面
流动分界 面外移
第三章 模锻成形工序分析和模锻工艺
开式模锻 模锻 成形 工序 分析 闭式模锻 挤 压 顶 镦 模锻工艺及模锻件分类 锻件图设计
模锻 工艺
模锻工艺过程制定内容 及工艺方案选择 模锻变形工步的确定
1
一、概述
发展过程:自由锻→胎模锻→模锻 自由锻:将加热好的金属坯料放在锻造设备的上,下砥铁之间, 施加冲击力或压力,直接使坯料产生塑性变形,从而获得所需锻 件的一种加工方法。 胎模锻:胎模锻是在自由锻设备上采用不与上、下砧相接的活 动模具成型的方法称为胎模锻。它是介于自由锻与模锻之间的 锻造工艺方法。 模锻:将加热后的坯料放置在固定于模锻设备上的锻模内锻造 成形的。
●
●
● ●
节省切边设备;
有利于金属充满模膛,有利于进行精密模锻;
闭式模锻时金属处于明显的三向压应力状态,有利于 低塑性材料的成形。
42
第三节
闭式模锻
闭式模锻进行的必要条件:
● ● ●
坯料体积准确; 坯料形状合理并能在模膛内准确定位; 能够较准确地控制打击能量或模压力;
●
有简便的取件措施或顶料机构。
19
一、开式模锻各阶段的应力应变分析
●
第Ⅱ阶段
20
一、开式模锻各阶段的应力应变分析
第Ⅲ阶段:主要是将多余金属排入飞边,此时流动分界面 已不存在。变形区的应力应变状态与薄件镦粗一样。
零件毛坯成型工艺基础

9.1 铸造成型工艺
• (3)应用离心铸造广泛用于大口径铸铁管、缸套、双金属轴承、活塞 环、特殊钢无缝管坯等的生产。
• 4.熔模铸造 • 熔模铸造是用易熔材料制成模样,在模样上涂挂若干层耐火涂料,
待硬化后熔出模样形成无分型面的型壳,经高温焙烧后即可浇注获并 获得铸件的方法。由于易熔材料通常采用蜡 • 料,故这种方法又称为“失蜡铸造”。 • (1)工艺过程熔模铸造的主要工艺过程如图9一11所示。说明如下:
• (4)应用范围目前金属型铸造主要用于大批量生产形状简单的铝、 铜、镁等非铁金属及合金铸件,如铝合金活塞、油泵壳体,铜合金轴 瓦、轴套等
上一页 下一页 返回
9.1 铸造成型工艺
• 2.压力铸造 • 压力铸造是指熔融金属在高压下被快速压入铸型中,并在压力下凝
固的铸造方法,简称“压铸”。常用的压射压力为5一150 MPa,充 型速度为0. 5一50 m/s,充型时间为0. 01~ 0. 2 s • (1)工艺过程压铸工艺是在专门的压铸机上完成的,压铸机的主要 类型有冷压室压铸机和热压室压铸机两类。图9一8为卧式冷室压铸机 工艺过程示意图,冷室压铸机的熔化炉与压室分开,压室和压射冲头 不浸于熔融金属中,浇注时将定量的熔融金属浇到压室中,然后进行 压射。压铸机主由合型机构、压射机构和顶出机构组成,压铸机的规 格通常以合型力的大小来表示的。
上一页 下一页 返回
9.1 铸造成型工艺
• 9.落砂、清理及检验 • (1)落砂用手工或机器使铸件与型砂、砂箱分开的操作 • (2)清理采用铁锤敲击、机械切割或气割等方法清除铸件表面粘砂、
型砂、多余金属(包括浇冒口、飞翅和氧化皮)的过程 • (3)检验用肉眼或借助于尖嘴锤找出铸件表层或皮下的铸造缺陷,
锻压的心得体会(精选14篇)

锻压的心得体会(精选14篇)心得体会是表达个人主观体验和观点的一种方式,可以让他人更加了解我们的思考和想法。
通过阅读以下的心得体会范文,大家可以更好地理解这一写作形式的要点和特点。
锻压事故心得体会锻压作为一种常见的金属加工工艺,在工业生产中发挥着重要作用。
然而,由于操作不慎、设备故障等原因,锻压事故时有发生。
通过参与一次锻压事故的整治工作,我深刻认识到了事故的危害和预防的重要性。
在这次工作中,我对锻压事故有了全新的认识,获得了宝贵的经验和教训。
首先,锻压事故给人们带来了巨大的伤害。
在锻压事故中,我亲眼目睹了工人的严重受伤。
在一次锻造过程中,由于操作不当,工人的手被机械装置夹住,手指被剥落。
这一幕让我震惊不已。
工人的手指是他们生活和工作的重要工具,一旦受伤,不仅给他们带来巨大的痛苦,也会对他们的生活造成极大的影响。
这次事故还给工厂造成了经济损失,并对生产进程造成了延误。
因此,锻压事故不仅会给人们的身体健康带来损害,还会对企业带来重大的影响。
其次,锻压事故的发生大多是由于操作不当所致。
在整治工作中,我发现许多事故的发生是由于工人在操作设备时不规范、不谨慎所导致的。
有的时候,工人没有正确地佩戴个人防护装备,没有将手指和其他身体部位远离机械装置,更没有对设备进行及时检查和维护。
这些操作上的差错给工人的安全埋下了隐患。
因此,我深刻认识到,只有严格遵守操作规程,正确使用设备,才能减少事故的发生。
第三,预防是减少锻压事故的关键。
在整治工作中,我了解到预防是减少锻压事故的关键。
首先,有关方面应该加强对从业人员的培训和教育,提高他们对安全生产的认识和重视。
只有加强学习,掌握安全生产知识,才能在实际操作中做到临近事故时懂得应对。
其次,企业应定期对设备进行维护和检修,确保设备的正常运转。
此外,对设备操作规程也需要进行适时的调整和完善,以适应生产工艺的需求。
通过这些预防措施,可以有效减少锻压事故的发生,维护工人的安全和企业的利益。
3-1锻压生产—塑态成型
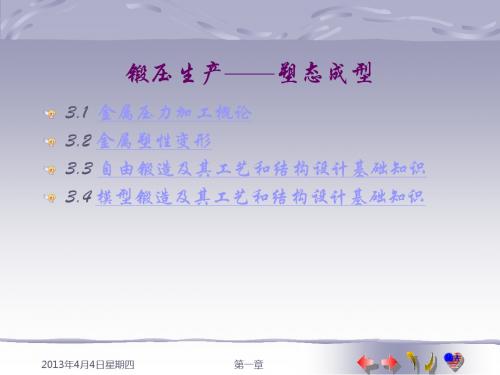
2012年2月17日星期五
第一章
3.自由锻件工艺设计及示例
绘制锻件图 锻件图是以零件图为基础,按照自由锻造工 艺特点,考虑下列几个因素绘制而成的. (1)加工余量; (2)敷料——为了简化零件的形状和结构、便 于锻造而增加的一部分金属,称为敷料。
2012年2月17日星期五
第一章
(3)锻件公差 锻件的基本尺寸为零件的基本尺寸加上加工 余量。而锻件的实际尺寸与其基本尺寸之间所 允许的偏差,称为锻性公差。
第一章
纤维组织
热变形时,晶粒和晶界上的杂质都被压扁、 拉长,随即再结晶而得细小晶粒。而杂质沿着被 拉长的方向保留下来,形成了纤维组织。 纤维组织稳定性很高,不能用热处理和其它 方法消除它,只有通过金属的塑性变形,方能改 变其方向和形状。因此,在设计和制造零件时, 应使零件工作时的最大正应力与纤维方向重合, 最大切应力与纤维方向垂直,并使纤维分布与零 件的轮廓相符合而不被切断。
2012年2月17日星期五
第一章
由零件图绘制锻制图 锻件图是确定模锻工步、设计和制造锻模, 计算坯料尺寸以及检验锻件的重要技术文件。
模锻件工艺设计及示例
2012年2月17日星期五
第一章
绘制模锻件图时应考虑的问题如下:
分模面的选择原则: (1).易于取出锻件。 (2).应使模膛深度最小,宽度最大。 (3).易发现错模。 (4).分模面应尽量平直简单。 (5).使敷料最少。
2012年2月17日星期五
第一章
金属的加工硬化
金属的机械性能取决于其组织。组织改变, 则性能也随之变化。随着变化程度地增加,强 度和硬度的提高,塑性和韧性下降。这种现象 称为加工硬化。
2012年2月17日星期五
第一章
锻造工培训
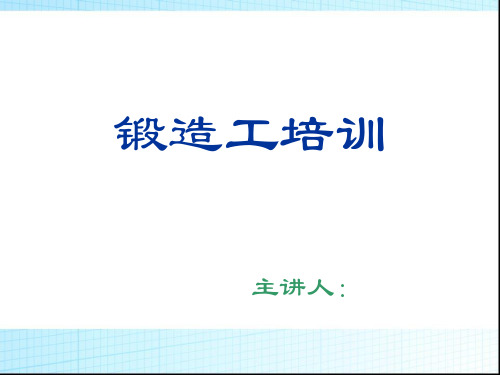
提起重锤再自由落下的方法锻打坯料。14世纪以后出现了畜力和水
力落锤锻。
左图为锻铜浮雕。 是手工锻造作品。 手工锻造是一种 古老的金属加工 工艺,是以手工 锻打的方式,在 金属板上锻锤出 各种高低凹凸不 平的浮雕效果。
1842年,英国的内史密斯制成第一台蒸汽锤,使锻造进入应用 动力的时代。以后陆续出现锻造水压机、电机驱动的夹板锤、空气
一、锻造工艺的发展简史及其发展趋势
(一)锻造技术的发展简史 人类在新石器时代末期,已开始以锤击天然红铜来制造装饰品 和小用品。中国约在公元前2000多年已应用冷锻工艺制造工具,如 甘肃武威皇娘娘台齐家文化遗址出土的红铜器物,就有明显的锤击 痕迹。 最初,人们靠抡锤进行锻造,后来出现通过人拉绳索和滑车来
根据设备结构特性和工艺特性的不同,分为锤上模锻(自 由锻锤上模锻、高速锤上模锻)、摩擦压力机上模锻、热 模锻压力机上模锻、液压机上模锻、平锻机上模锻、专用 锻压机上模锻等。 模锻适用于形状复杂,尺寸精度较高,加工余量小,批量 生产的中、小型锻件。 形状和尺寸靠模具保证,人为影响因素小。 精密锻件的成形也要通过模锻来实现。
• • • • •
目录 第一章 第二章 第三章 第四章
锻造概述 锻造用原材料及下料方法 锻造的热规范 自由锻工艺
•第一章 锻造概述
什么是锻造?——金属塑性加工方法之一
锻造是利用手锤、锻锤或压力设备上的模具对加热的 金属坯料施力,使金属材料在不分离条件下产生塑性 变形,以获得形状、尺寸和性能符合要求的零件。为 了使金属材料在高塑性下成型,通常锻造是在热态下 进行,因此锻造也称为热锻。
铸造毛坯的组织性能差,只适用于性能要求低的零、部
件
锻造:
纤维组织--变形后 的杂质仍具有方向性,呈 现纤维状条纹 锻造流线--变形后 杂质的纤维分布,使组织、 性能呈方向性
1模锻方法与工艺

2 锻造种类
(三)按行业应用
■柴油机锻件 柴油机是动力机械的一种,它常用来作发动机。以大
型柴油机为例,所用的锻件有汽缸盖、主轴颈、曲轴端 法兰输出端轴、连杆、活塞杆、活塞头、十字头销轴、 曲轴传动齿轮、齿圈、中间齿轮和染油泵体等十余种。
■船用锻件 船用锻件分为三大类,主机锻件、轴系锻件和舵系锻
件。主机锻件与柴油机锻件一样。轴系锻件有推力轴、 中间轴艉轴等。舵系锻件有舵杆、舵柱、舵销等。
模闭式精密模锻还可锻出垂直于锻击方向的孔或凹坑,材料 利用率平均提高20%左右; ▼毛坯在封闭的模膛内成形,变形金属处于更加强大的三向压 力状态,有利于提高金属材料的塑性和产品的力学性能; ▼可分凹模闭式精密模锻可减少甚至取消制坯工步,省去切边 和辅助工序,生产率平均可提高25%~50%。 闭式精密模锻主要问题:对于一些大中型锻件模具寿命低,需 采取多种措施逐步解决。
5 模锻件类型
(1)饼盘类
❖ 外形为圆形面,高度较小
5 模锻件类型
(2)法兰凸缘类
其外形为回转体,带有圆形或长宽尺寸相差不大的 法兰和凸缘。
5模锻件类型
(3)轴杆类
其杆部为圆形,带有圆形或非圆形头部,或中间局 部粗大的直长杆类。
(4)杯筒类
5 模锻件类型
5 模锻件类型
(5)枝芽类
包括单枝芽、多枝芽的实心和空心类锻件。
■石油化工锻件 锻件在石油化工设备中有着广泛的应用。如球形储罐的人孔、
法兰,换热器所需的各种管板、对焊法兰催化裂化反应器的整锻 筒体(压力容器),加氢反应器所用的筒节,化肥设备所需的顶 盖、底盖、封头等均是锻件。
2 锻造种类
(三)按行业应用
■矿山锻件 按设备重量计算,矿山设备中锻件的比重为12-24%。矿山设
机械制造基础 第2章-锻压1可锻性
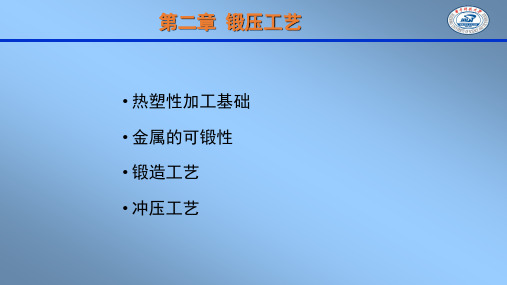
2.1 热塑性加工基础
2.1.3 纤维组织、流线与锻造比
➢ 钢锭开坯 热加工生产采用的原始坯料是铸锭。其内部组织很不均匀,晶粒较粗大,并存
在气孔、缩松、非金属夹杂物等缺陷。铸锭加热后经过热加工,由于塑性变形及再 结晶,从而改变了粗大、不均匀的铸态结构,获得细化了的再结晶组织。同时还可 以将铸锭中的气孔、缩松等压合在一起,使金属更加致密,力学性能得到很大提高 。
第二章 锻压工艺
• 热塑性加工基础 • 金属的可锻性 • 锻造工艺 • 冲压工艺
概述
1. 你知道枪管、炮管是如何制造的吗?什么是来复线?它是如何制造的? 来复线是径向锻造的。
概述
利用金属在外力作用下所产生的塑性变形,来获得具有一定形状、尺 寸和机械性能的原材料、毛坯或零件的生产方法,称为金属塑性成型(也 称为压力加工)。
压力加工中作用在金属坯料上的外力主要有两种:冲击力和静压力。 锤类设备产生冲击力,轧机与压力机设备产生静压力。 金属塑性成型的基本生产方法有以下几种:
压力加工工艺
各种块体压力加工工艺
各种板料冲压工艺
各种加工方法的应用范围
• 轧制、挤压、拉拔
主要用于金属型材、板材、
钢材和线材等原材料。
• 锻造 用于承受重载荷的机器零件,如机器的 主轴、重.1.2 冷变形与热变形
2.热变形: 在再结晶温度以上的变形。变形后,金属具有再结晶组织、而无加工硬化痕迹。
也称热加工。 ➢ 优点:金属能以较小的功达到较大的变形,加工尺寸较大和形状比较复杂的工件, 同时获得具有高机械性能的再结晶组织。 ➢ 缺点:金属表面容易形成氧化皮,而且产品尺寸精度和表面质量较低,劳动条件 和生产率也较差。
• 板料冲压 广泛用于汽车制造、电器、仪表及日 用品工业等方面。
热模锻工艺介绍 180813
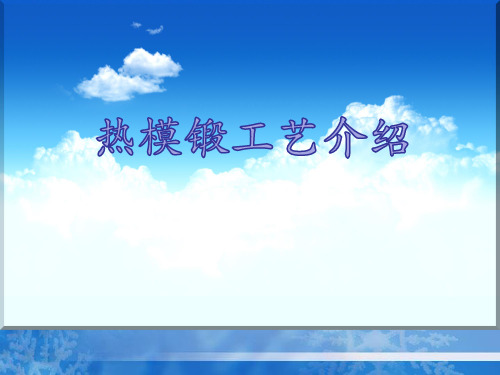
1)模锻锤: G=(3.5~6.3)KF(公斤) 2)热模锻压力机 P=(6.3~7.4)F(吨) 圆形锻件:P=8(1-0.001D)(1.1+20/D)2 FБbt 非圆形:P=8(1-0.001D)(1.1+20/D)2 (1+0.1 )FБbt 3)平锻机 P=5(1-0.001D)(D+10)2Бbt 4)螺旋压力机 P=KБbtF
热模锻压力机 (曲柄压力机)
和同样能力的模锻锤相比, 热模锻压力机的初次投资 大,但维护费用低,动力 消耗小。
和摩擦压力机模锻相比, 生产率较高,便于自动化。
热模锻压力机结构复杂, 制造条件要求高。
螺旋压力机种类:
摩擦螺旋压力机 电动螺旋压力机 离合器螺旋压力机 液压传动螺旋压力机
1、摩擦压力机靠飞轮积蓄 的能量工作,原则上可多次打击 干大活。实际有效打击次数不超 过3次。
键块分别紧固在锤头和下模座
的燕尾槽中。
•
燕尾使模块固定在锤头
(或砧座)上,使燕尾底面与
锤头(或砧座)底面紧密贴合。
•
楔铁使模块在左右方向定
位。键块使模块在前后方向定
位。
热模锻压力机与模锻锤相比,其 工作特性为: (1)静压成形,无震动和噪音; (2)机架和曲柄连杆机构的刚性 大,工作时弹性变形小; (3)滑块行程一定,每一模锻工 步只要一次行程完成; (4)导向精度和承受偏载的能力 强; (5)有上下顶件装置,便于锻件 脱模。
部分汽车件产品
转向系统 Steering System
制动系统 Braking System
传动系统 Drive System
➢ 转向系统 Components of Steering System
金属材料与热加工基础知识巩固与能力训练题附答案第2章

第二章知识巩固与能力训练题一、填空题1.常见的金属晶格类型有体心立方、面心立方、密排六方三种,锌属于密排六方晶格,铬属于体心立方晶格,铜于面心立方晶格。
2.晶体缺陷的存在都会造成晶格畸变,从而使金属的强度提高。
3. 理论结晶温度和实际结晶温度之差称为过冷度。
过冷度的大小与冷却速度有关,冷却速度越快,金属的实际结晶温度越低,过冷度也就越大。
4.细化晶粒的根本途径是控制结晶时的形核率及长大速度。
5.金属结晶时,形核率越大,晶体长大速度越快,单位体积内的晶核就越多,晶粒就越细。
6.金属液内部最先形成的结晶核心的微小晶体称为晶核,包括自发形核和非自发形核。
7.金属化合物是指合金的组元间发生互相作用而生成的一种新相,通常其性能特点是具有很高的熔点、硬度和脆性。
8.碳溶于α-Fe中形成的间隙固溶体称为铁素体,用F表示。
9.碳溶于γ-Fe中形成的间隙固溶体称为奥氏体,用A表示。
10. 渗碳体为铁和碳形成的金属化合物,用Fe3C表示。
二、选择题1.γ-Fe转变为α-Fe时,纯铁的体积会 B 。
A.收缩B.膨胀C.不变D.无法判断2.金属发生结构改变的温度称为 A 。
A.临界点B.凝固点C.熔点D.结晶点3.晶体中某处的一列或若干列原子有规律的错排现象称为B 。
A.同素异构转变B.位错C.晶格畸变D.亚晶界4.同种元素具有不同的晶格类型的晶体称为B 。
A.同位素B.同素异晶体C.同素异性体5.金属经剧烈冷变形后,位错密度 C 。
A.降低B.稍有变化C.大大提高D.没有变化6.同素异构转变可以改变金属的 D 。
A.晶粒形状B.晶粒大小C.化学成分D.晶格类型7.多晶体是由许多原子排列位向不同的 C 组成。
A.晶格B.晶胞C.晶粒D.亚晶粒8.铸造生产中,由砂型铸造改为金属铸模是利用 C 细化晶粒的事例。
A.变质处理B.机械振动C.增大过冷度D.电磁搅拌9.合金固溶强化的基本原因是 C 。
A.晶格的类型改变B.晶粒细化C.晶格发生畸变D.增加了原子结合力10.固溶体具有 B 的晶格类型。
锻造的危害与预防(三篇)

锻造的危害与预防锻造是一种常见的金属加工技术,通过加热、塑形和冷却等工序对金属材料进行形状改变和强度提升。
在工业生产和个人使用中,锻造具有广泛的应用,但同时也伴随着一些危害性因素。
本文将探讨锻造的危害,并提出相应的预防方法。
一、锻造的危害1. 高温危害锻造过程中,金属材料需要加热到较高的温度,因此操作者容易受到高温的伤害。
高温可以导致皮肤烫伤、中暑和脱水等问题。
另外,高温环境下,操作者容易因为出汗过多而导致失水和电解质紊乱。
2. 烟尘危害锻造过程中,金属材料可能产生烟尘和有害气体。
这些烟尘和气体含有大量的金属颗粒和化学物质,对人体健康有危害。
长时间接触这些烟尘和气体会导致呼吸道感染、肺部疾病和呼吸系统过敏反应。
3. 噪音危害锻造设备在运行过程中会产生噪音。
长期暴露在高噪音环境下,会引起噪音性聋和其他听力损害。
此外,噪音还可能引发精神压力、消化系统疾病和心理健康问题。
4. 机械伤害锻造过程中使用的机械设备具有很高的运动速度和力量,如果没有正确的操作和保护措施,操作者容易发生机械伤害。
例如,手被夹伤、压伤或切割伤等。
5. 电击危害在锻造过程中,设备和工件可能接触到高电压和电流。
如果操作者没有正确的绝缘防护措施,容易发生电击伤害。
二、锻造的预防方法1. 使用个人防护设备操作者在锻造过程中应佩戴适当的个人防护设备,包括防热手套、防火眼镜、耳塞或耳罩、防护面具和耐热服装等。
这些设备可以有效地防止高温、烟尘和噪音对操作者的危害。
2. 维护和保养设备锻造设备在使用前应进行检查和保养,确保设备的正常运行和安全性能。
定期更换磨损严重的零件,确保设备的稳定性和操作的安全。
3. 加强员工培训为操作者提供必要的培训和指导,确保他们了解锻造过程中的危害以及预防方法。
操作者应具备必要的专业知识和技能,能够正确使用设备和采取适当的安全措施。
4. 控制作业环境在锻造车间中应采取必要的控制措施,减少高温、烟尘和噪音对操作者的影响。
锻造工艺复习题

一选择题1下列是自由锻造特点的是 (B)A 精度高B 精度低 C生产效率高 D 大批量生产2下列是锻造特点的是 (A)A 省料 B生产效率低 C降低力学性能 D 适应性差3下列是模锻特点的是 (D)A成本低 B效率低 C 操作复杂 D 尺寸精度高4锻造前对金属进行加热,目的是 (A)A提高塑性 B 降低塑性 C 增加变形抗力 D 以上都不正确5空气锤的动力是 (A)A 空气 B电动机 C 活塞 D 曲轴连杆机构6为防止坯料在镦粗时产生弯曲,坯料原始高度应小于其直径A 1倍B 2倍C 2.5倍D 3倍7镦粗时,坯料端面、应平整并与轴线 (A)A垂直 B平行 C 可歪斜 D 以上都不正确8圆截面坯料拔长时,要先将坯料锻成 (C)A圆形 B 八角形 C方形 D 圆锥形9利用模具使坯料变形而获得锻件的方法 (C)A机锻 B手工自由锻 C 模锻 D 胚模锻10锻造前对金属毛坯进行加热温度太高,锻件 (C)A质量好 B 质量不变 C 质量下降 D 易断裂11使坯料高度缩小,横截面积增大的锻造工序是 (B)A冲孔 B 镦粗 C 拔长 D 弯曲二判断题1、钢锭内空洞类缺陷的内表面已经被氧化,不能通过锻造将这些空洞类缺陷锻合。
(对)2、为使锻件获得较高的力学性能,锻造应达到一定的锻造比。
(对)3、毛边槽仓部的容积应按上下模打靠后,尚未完全被多余金属充满的原则来设计。
(对)4、闭式模锻比开式模锻的金属利用率高。
(对)5、闭式模锻件没有毛边。
(对)6、闭式模锻时,当金属充满型槽各处,锻造结束。
(错)7、模锻工艺和模锻方法与锻件的外形密切相关。
(对)8、在保证锻件顺利取出的前提下,模锻斜度尽可能取小值。
(对)9、模锻斜度的大小与分模线位置有关。
(对)10、为了便于选择标准刀具,模锻斜度和模锻圆角半径应从标准系列数值中选择。
(对)11、锻件的内圆角半径对应模具型槽的外圆角半径,如果选的过小可导致锻模在热处理和模锻过程中因应力集中使其开裂。
- 1、下载文档前请自行甄别文档内容的完整性,平台不提供额外的编辑、内容补充、找答案等附加服务。
- 2、"仅部分预览"的文档,不可在线预览部分如存在完整性等问题,可反馈申请退款(可完整预览的文档不适用该条件!)。
- 3、如文档侵犯您的权益,请联系客服反馈,我们会尽快为您处理(人工客服工作时间:9:00-18:30)。
m1<m2< … <mn
n
n
n-1
◎弯曲处的圆角半径不宜过小
翻边:将工件上的孔或边缘翻出竖立或有一定角度的直边 胀形:利用模具使空心件或管状件由内向外扩张的成形方法。 缩口:利用模具使空心件或管状件的口部直径缩小的局部成形工艺
冲模 冲压模具是冲压生产中必不可少的工艺装备,按冲压工序的组合程度不 同可分为简单冲模、连续冲模和复合冲模三种。
(4)锻压主要生产承受重载荷零件的毛坯 如机器中的主轴、齿轮等,但不能获得形状复杂的毛坯或零件。
四、金属的锻造性能
1.锻造性能←塑性、变形抗力 2.影响锻造性能的因素 1)金属本质的影响 ①化学成分 ②金属组织 2)变形条件的影响 ①变形温度 ②变形速度 ③应力状态
几种常用锻压方法的应力状态
实践证明,拉应力的存在会使金属的塑性降低,三向受拉金属的塑性最差。 三个方向上压应力的数目越多,则金属的塑性越好。因此,塑性较好的材 料可选用拉应力状态下变形(如拉拔等),塑性较差的材料应选用压应力 状态下变形(如挤压、模锻等)
⑶ 超塑性成型的工艺
◎模锻和挤压 为了保证模具坯料在锻造过程 中恒温,超塑性模锻的锻模中 设置了感应加热圈2及隔热垫1。 超塑性模锻目前主要应用于航 天、仪表、模具等行业中生产 高温合金以及钛合金等难以加 工成形的高精度零件。如高强 度合金的飞机起落架、涡轮盘、 注塑模等。
图3-49 超塑性模锻
◎板料深冲 板料深冲时需先将超塑性板料的法兰部分加热到一定温度,并在外围加 油压,即可一次深冲出薄壁深冲件。板料深冲件的深冲比H/d0可为普通 拉深件的15倍,且工件壁厚均匀、无凸耳、无各向异性。
拉伸过程示意图 1—凸模 2—压边圈 3—坯料 4—凹模
◎起皱是拉深时板料失稳造成的。当拉应力超过材料的抗拉强度时,此 处将被拉裂
拉伸废品件
拉深工序对零件的要求 ◎合理设置拉深系数与拉深次数 拉深系数(0.5-0.8):m=d/D0 多 m1=d1/D0 次 m2=d2/d1 拉 … 深 m =d /d
三、锻压的特点
(1)改善金属组织、提高力学性能 锻压的同时可消除铸造缺陷,均匀成分,形成纤维组织,从而提高锻件 的力学性能。 (2)节约金属材料 比如在热轧钻头、齿轮、齿圈及冷轧丝杠时节省了切削加工设备和材料 的消耗。 (3)较高的生产率 比如在生产六角螺钉时采用模锻成形就比切削加工效率约高50倍。
作用及用途
特
点
弯曲模膛
弯曲坯料,使之获得 近似于模锻模膛在分 模面上的轮廓形状
结构特点与成形模膛相 似,但无聚料作用,且 变形量比成形模膛大
切断模膛
切断已锻好的锻件。
多工位锻模的最后一个 工步,常置于锻模的前 角或后角上
(二)模锻模膛
①预锻模膛: 作用是使坯变形到接近于锻件的形状和尺寸。使金属更易充满模 膛。减少模膛的磨损,延长锻模的使用寿命。 ②终锻模膛: 其形状和锻件相同。考虑到锻件冷却时的收缩,终锻模膛的尺寸 应比锻件尺寸放大一个收缩量,使坯料最后变形到锻件所要求的形状和尺寸。 终锻模膛分模面上有一圈飞边槽,作用是增加金属从模膛中流出的阻力,促使金 属充满模膛,容纳多余的金属。模膛周围设飞边槽,通孔锻件需留冲孔连皮。
1-锤头 9-模膛
锻模模膛:制坯模膛和模锻模膛 (一)制坯模膛 对于形状复杂的模锻件,为了使坯料基本接近模锻件的形状,以便模锻时金属 能合理分布,并很好地充满模膛,必须预先在制坯模膛内制坯。 制坯模膛有以下几种:
模膛名称 图 例 作用及用途 特 点
锤上模锻工艺规程的制定 : 锤上模锻工艺规程的制定主要包括绘制模锻件图、计算坯料尺寸、 确定模锻工步、选择锻造设备、确定锻造温度范围等。 1.分模面 (1)要保证模锻件能从模膛中 顺利取出 (2)应使上下模沿分模面的模 膛轮廓一致 (3)最好使分模面为一个平面, 并使上下锻模的模膛深度 基本一致 (4)分模面应使零件上所加的 敷料最少。 (5)把分模面选取在能使模膛 深度最浅处
◎冲床:冲床将完成除剪切以外的其他冲压工作。
板料冲压基本工序 a、分离工序 落料和冲孔(冲裁) b、成形工序 弯曲 拉深 缩口 胀形 翻边 ⑴.冲孔和落料 落料和冲孔一般称为冲裁,是使坯料沿封闭轮廓分离的工序。
⑵.弯曲 弯曲是利用模具或其他工具将坯料一部分相对另一部分弯曲成一定的角度和 圆弧的变形工序。 弯曲工序对零件的要求: ◎模具的角度应比成品角度小一个回弹角 ◎应使板料纤维方向与弯曲件的弯曲线垂直
锻压成型
一、什么是锻压加工
锻压是金属塑性加工方法之一,是借助于外力作用,使金属坯料产生塑性 变形,从而获得所要求形状、尺寸和力学性能的毛坯或零件的一种压力加 工方法。 它是最古老的金属加工方法之一,可以追溯到公元前4000年——甚至8000 年。其生产广泛应用于机械、冶金、造船、航空、航天、兵器以及其它许 多工业部门。
(a) 自由锻 (b) 模锻 (c) 板料冲压
六、各锻压生产方法详细介绍
1、自由锻造 定义: 金属在捶面和砧面之间受压变形的加工方法。 金属沿变形方向可以自由流动,不受限制。 自由锻设备: ◎空气锤:自由落体,落重40~750kg,锻100kg以下。 ◎蒸汽-空气锤:落重0.63 ~5t,锻几十~几百kg ◎电液液压自由锻锤 :震动、噪声小 ◎水压机:静压力
五、锻压生产的分类
(1)自由锻造 利用冲击力或静压力使经过加热的金属在锻压设备的上、下砧铁之间塑 性变形、自由流动称为自由锻造。 (2)模样锻造 把金属坯料放在锻模模膛内施加压力使其变形的锻造方法,又简称模锻。 (3)板料冲压 将金属板料置于冲模之间,使板料产生分离或变形的加工方法。通常在 常温下进行,也称冷冲压。
古代铸剑
为锻铜浮雕。是手工锻造作 品。手工锻造是一种古老的 金属加工工艺,是以手工锻 打的方式,在金属板上锻锤 出各种高低凹凸不平的浮雕 效果。
1842年,英国的内史密斯制成第一台蒸汽锤,使锻造进入应用动力的 时代。以后陆续出现锻造水压机、电机驱动的夹板锤、空气锻锤和机械压 力机。夹板锤最早应用于美国内战(1861~1865)期间,用以模锻武器的零 件,随后在欧洲出现了蒸汽模锻锤,模锻工艺逐渐推广。到19世纪末已形 成近代锻压机械的基本门类。 20世纪初期,随着汽车开始大量生产,热模锻迅速发展,成为锻造的 主要工艺。 锻压经过1 0 0多年的发展,今天已成为一门综合性学科。它以塑性成 形原理、金属学、摩擦学为理论基础,同时涉及传热学、物理化学、机械 运动等相关学科,以锻造、冲压等为技术,与其它学科一起支撑机器制造 业。
3、模锻 定义: 使金属坯料在锻模膛内,承受冲击力或压力作用而被迫塑性变形,获得 锻件的成形方法。 模锻设备 ◎模锻锤: 模锻锤 程控全液压锻锤 ◎压力机 曲柄压力机 摩擦压力机 液压压力机 ◎平锻机
程控全液压锻锤
摩擦压力机
优点: ◎锻件表面光洁、尺寸精度高; ◎可锻形状复杂的锻件; ◎生产率高,大批量生产成本低。 缺点: ◎投资大(设备、模具); ◎工艺复杂。 适用:大批量生产中、小锻件 分类介绍 1.锤锻模 常用设备:蒸汽—空气锤 分类:模锻模膛、制坯模膛
模锻件结构工艺性 1)零件的外形应力求简单、平直、对称,避免零件截面间差别过 大,或具有薄壁、高肋等不良结构。 2)在零件结构允许的条件下,应尽量避 免有深孔或多孔结构
3)对复杂锻件,应采用锻造—焊接或锻造—机械联接组合工艺
4、板料冲压 定义 板料冲压:通常在室温下进行,所以又称冷冲压,简称冲压。 特点: ◎不需要对毛坯加热,是节约能源的加工方法 ◎生产操作简单,生产率高 ◎尺寸精度较高,质量稳定 ◎制造费用高。用于大批量生产条件下 冲压设备 ◎剪床:把板料切成一定宽度的条料,以供下一步冲压工序之用。
拔长模膛
减少毛坯某部分的横截面积, 是制坯的第一步, 增加毛坯长度,用于长轴类 通常模膛安放在 锻件的制坯 模具的边角处
滚挤模膛
减少毛坯某一部分的横截面 积,以增加另一部分的横截 面积,从而使金属按锻件形 状分布,适用于横截面积相 差较大的锻件的制坯
坯料不轴向送进, 仅反复绕轴线翻 转
模膛名称
图
例
自由锻工序
确定变形工序的依据是锻件的形状、尺寸、技术要求、生产批量和生产条 件等。一般自由锻件大致可分为六类,其形状特征及主要变形工序如表 ◎基本工序:镦粗、拔长、冲孔、弯曲、切割、扭转、错移等 ◎辅助工序:倒棱、压肩等 ◎精整工序:修平面、校直等。
自由锻件的结构工艺性 ◎应避免锥面和斜面的结构;
2.加工余量和锻件公差 为了达到零件尺寸精度及表面粗糙度的要求,锻件加工而去除的金属 层,称为锻件的加工余量。 3.模锻斜度 为便于从模膛中取出锻件,模锻件上平行于锤击方向的表面必须具有 斜度,称为模锻斜度 4.模锻圆角半径 模锻件上所有两平面转接处均需圆弧过渡,此过渡处称为锻件的圆角 5.冲孔连皮 由于锤上模锻时不能靠上、下模的突起部分把金属完全排挤掉,因此 不能锻出通孔,终锻后,孔内留有金属薄层,称为冲孔连皮
七、锻压新工艺简介
1、超塑性成形 ⑴超塑性成形的概念 金属及合金在0.5~5μm的超细等轴晶粒,温度控制在(0.5~0.7)T熔, 变形速度控制在10-2~10-4 m/s的低应变速率下进行变形时,可呈现出异 乎寻常的塑性,而变形抗力则大大降低,这种现象称为超塑性。 ◎超塑性成形就是对超塑性状态的坯料进行锻造、冲压、挤压等加工,以 制出高质量、高精度复杂零件的方法。 ⑵超塑性成形的特点 ◎超塑性金属材料具有极其优异的塑性,成形性好。有些无法进行常规锻 压制造的金属及合金材料也可采用超塑性成形,从而扩大了锻压材料的 范围。 ◎超塑性金属材料变形抗力很小,可以在吨位较小设备上锻压出较大的制 品,并且降低了模具的磨损,延长了模具的寿命。 ◎超塑性金属材料内部晶粒细小、组织均匀、力学性能较好,并且具有各 向同性的特性。可获得尺寸精密、形状复杂的制品,是材料实现净成形、 净终成形加工的新途径。
◎冲模的结构组成和作用 a、工作部分:凸模、凹模 b、定位部分:导板、定位销 c、卸料部分:卸料板、顶板 d、导向部分:导柱、导套 e、模体部分:上下模板、