浸泡式化学清洗技术在模块化不锈钢管道中的应用
不锈钢管酸洗钝化的8个操作步骤
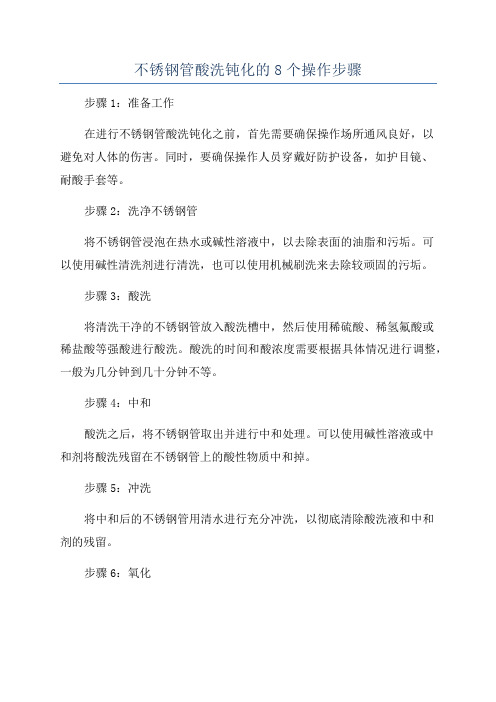
不锈钢管酸洗钝化的8个操作步骤步骤1:准备工作在进行不锈钢管酸洗钝化之前,首先需要确保操作场所通风良好,以避免对人体的伤害。
同时,要确保操作人员穿戴好防护设备,如护目镜、耐酸手套等。
步骤2:洗净不锈钢管将不锈钢管浸泡在热水或碱性溶液中,以去除表面的油脂和污垢。
可以使用碱性清洗剂进行清洗,也可以使用机械刷洗来去除较顽固的污垢。
步骤3:酸洗将清洗干净的不锈钢管放入酸洗槽中,然后使用稀硫酸、稀氢氟酸或稀盐酸等强酸进行酸洗。
酸洗的时间和酸浓度需要根据具体情况进行调整,一般为几分钟到几十分钟不等。
步骤4:中和酸洗之后,将不锈钢管取出并进行中和处理。
可以使用碱性溶液或中和剂将酸洗残留在不锈钢管上的酸性物质中和掉。
步骤5:冲洗将中和后的不锈钢管用清水进行充分冲洗,以彻底清除酸洗液和中和剂的残留。
步骤6:氧化将清洗干净的不锈钢管置于氧化槽中,通过升温和暴露在空气中使其氧化,形成一层保护性的氧化膜。
氧化的时间和温度需要根据具体要求来确定。
步骤7:冷却与冷水冲洗将氧化后的不锈钢管冷却至室温,然后进行冷水冲洗。
这样可以将不锈钢管表面的杂质彻底去除,净化表面。
步骤8:干燥和包装将冲洗干净的不锈钢管进行干燥处理,可以使用空气吹干或烘干设备。
然后进行包装,以防止不锈钢管在运输和储存过程中受到损坏。
总结:以上是不锈钢管酸洗钝化的八个操作步骤。
这些步骤的具体操作和要求可能因不同的工艺和设备而有所差异,但总体上可以作为一种参考,帮助进行不锈钢管酸洗钝化工艺。
浅谈不锈钢管道化学清洗

浅谈不锈钢管道化学清洗作者:***单位:******摘要:《工业金属管道工程施工及验收规范》GB50235-97 8.5.3 化学清洗液的配方必须经过鉴定,并曾在生产装置中使用过,经实践证明是有效和可靠的。
基于此,我就本人在碑林制药厂、赫尔制药厂、杨森制药厂对304卫生不锈钢管道化学清洗时的一点点经验和大家交流,不足之处还望指正。
在制药、食品行业,为了保证输送介质的洁净度,通常使用不锈钢管道。
为了达到使用要求,不锈钢管道从材料进场、保管、领料、焊材选用、焊接、安装、压力试验、化学清洗等各环节要严格执行《工业金属管道工程施工及验收规范》GB50235-97和《现场设备、工业管道焊接工程施工及验收规范》GB50236-98中的相关规定。
一般情况下,此这类管子进场时,包装还是很好,管子两头用塑料管帽进行了封堵,整根管子用塑料布包装。
保管时,管道要放在室内,封堵管帽不允许随便拆除,管子按规格、材质堆放整齐,并挂牌标示。
领料时,要对管子进行全面仔细的检查,有缺陷的管子不得使用。
这类管子一般为薄壁管,采用氩弧焊,焊丝选择H0Cr18Ni9Ti,焊接时,内部充氩气保护,并保证焊前充氩置换空气的时间,焊后保护的时间。
安装过程中,随时对敞开的管口进行封堵。
管道系统全部安装完成后,进行压力试验、清洗。
制药厂的不锈钢管道输送的介质洁净度高,经常采用化学清洗。
其中化学清洗是施工过程中最后一个环节,同时也是最为重要的一个环节,清洗好了,经化验一次合格,皆大欢喜。
但是,规范对化学清洗却无明确的规定,在施工中只具有指导性,不具备可操作性。
它是这样要求的:“8.5.3 化学清洗液的配方必须经过鉴定,并曾在生产装置中使用过,经实践证明是有效和可靠的。
”基于此,我就本人在几个制药厂对304卫生不锈钢管道化学清洗时的一点点经验和大家交流,不足之处还望指正。
首先,做好准备工作。
1、检查管道系统:管道系统全部按照施工图施工完毕,压力试验合格,并绘制完整的清洗流程图,图上应详细标注每一条系统的吹扫次序,清洗以前,必须组织清洗人员熟悉整个清洗流程。
管道酸洗钝化方案

管道酸洗钝化方案在工业生产中,管道是一种非常重要的组件,主要用于输送各种液体、气体和粉状物质。
然而,在使用过程中,管道表面可能会因为腐蚀、污垢或氧化而受损,从而影响管道的使用寿命和性能。
为了解决这个问题,一种常见的方法是对管道进行酸洗钝化处理。
酸洗钝化是一种通过使用酸性溶液将管道表面的腐蚀物质溶解掉,并形成一层保护膜,从而避免进一步的腐蚀和氧化。
具体的酸洗钝化方案可以根据管道材质和使用环境的不同而有所区别。
对于不锈钢管道而言,酸洗钝化处理主要是为了去除管道表面的氧化皮和焊渣。
一种常用的方案是使用稀硝酸或稀盐酸作为酸性溶液,将管道浸泡在溶液中一定时间,然后用水清洗干净。
硝酸和盐酸可以有效地溶解不锈钢表面的氧化物和污垢,使得管道表面恢复光亮,并有利于下一步的钝化处理。
在进行酸洗钝化处理之前,还需要注意选择合适的酸浓度和浸泡时间,以免酸洗过度导致管道表面损坏。
对于碳钢管道而言,酸洗钝化处理主要是为了去除管道表面的铁锈和污垢,以及形成一层钝化膜来防止进一步的腐蚀。
酸洗钝化碳钢管道的方案相对复杂一些。
首先,需要用酸性溶液(如稀盐酸)将管道表面的油污和焊缝处的氧化物溶解掉。
然后,通过使用酸性氧化剂(如浓硝酸)将管道表面的铁锈溶解掉。
最后,用碱性溶液(如氢氧化钠)进行中和处理,并用水彻底清洗管道表面。
通过这个过程,碳钢管道的表面将形成一层均匀的膜层,起到了防腐蚀的作用。
值得注意的是,在进行酸洗钝化处理过程中,安全性和环保性是至关重要的。
由于酸性溶液会产生腐蚀性气体和液体,所以操作人员必须佩戴适当的防护设备,如防酸涂层工作服、防酸手套和防护眼镜等。
同时,在处理后的酸溶液和废水处理上也需要格外注意,以防止对环境造成污染。
除了常见的酸洗钝化方案外,还有其他一些特殊情况下的处理方法。
例如,对于管道内部的腐蚀问题,可以采用高压水射流清洗技术。
这种方法通过将高压水射流喷射到管道内部,可以有效地清除管道内部的腐蚀物和沉积物。
不锈钢管道酸洗钝化方法
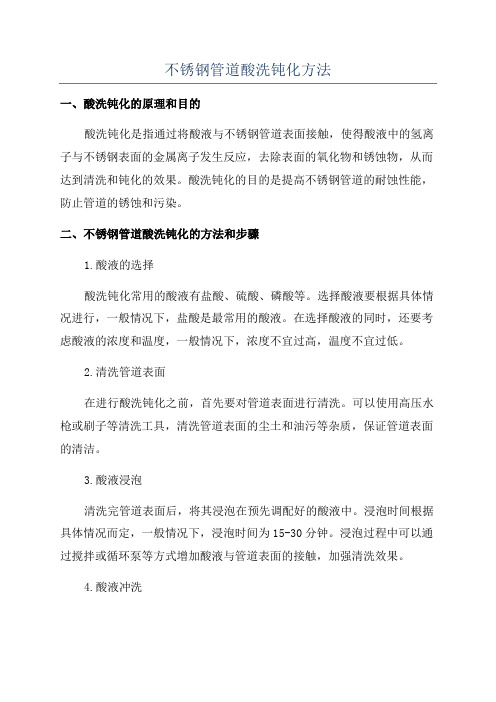
不锈钢管道酸洗钝化方法一、酸洗钝化的原理和目的酸洗钝化是指通过将酸液与不锈钢管道表面接触,使得酸液中的氢离子与不锈钢表面的金属离子发生反应,去除表面的氧化物和锈蚀物,从而达到清洗和钝化的效果。
酸洗钝化的目的是提高不锈钢管道的耐蚀性能,防止管道的锈蚀和污染。
二、不锈钢管道酸洗钝化的方法和步骤1.酸液的选择酸洗钝化常用的酸液有盐酸、硫酸、磷酸等。
选择酸液要根据具体情况进行,一般情况下,盐酸是最常用的酸液。
在选择酸液的同时,还要考虑酸液的浓度和温度,一般情况下,浓度不宜过高,温度不宜过低。
2.清洗管道表面在进行酸洗钝化之前,首先要对管道表面进行清洗。
可以使用高压水枪或刷子等清洗工具,清洗管道表面的尘土和油污等杂质,保证管道表面的清洁。
3.酸液浸泡清洗完管道表面后,将其浸泡在预先调配好的酸液中。
浸泡时间根据具体情况而定,一般情况下,浸泡时间为15-30分钟。
浸泡过程中可以通过搅拌或循环泵等方式增加酸液与管道表面的接触,加强清洗效果。
4.酸液冲洗酸液浸泡结束后,需要对管道进行酸液的冲洗。
冲洗时,可以使用清水进行多次冲洗,确保管道表面的酸液被彻底清除。
冲洗结束后,还要对管道表面进行干燥处理,可以利用风扇或高温炉等设备进行干燥。
5.钝化处理酸洗钝化的最后一步是进行钝化处理。
钝化液的选择和使用方法与酸液类似,一般使用稀硝酸或稀硫酸作为钝化液。
将钝化液涂覆在管道表面,静置一段时间后,再用清水冲洗干净。
6.相关注意事项在进行不锈钢管道酸洗钝化时,需要注意以下几点:(1)操作时需戴防腐手套、眼镜、防护服等个人防护设备,避免酸液对人体造成伤害。
(2)操作环境要通风良好,避免酸液蒸气的吸入。
(3)注意酸液的浓度和温度,过高或过低都会影响钝化效果。
(4)在处理过程中,尽量避免不锈钢管道的变形、变色等问题。
(5)处理完毕后要将酸液和废物进行妥善处理,防止对环境造成污染。
不锈钢管化学清洗标准

不锈钢管化学清洗标准一、引言不锈钢管在使用过程中可能会受到各种污染和腐蚀,为了保证其表面的光洁度和耐腐蚀性能,需要进行定期的化学清洗。
本文将介绍不锈钢管化学清洗的标准流程和要求。
二、清洗前的准备工作1.清洗设备和工具的准备:选择适合的清洗设备和工具,如清洗槽、刷子、喷枪等。
2.清洗剂的选择:根据不锈钢管表面的污染情况和材质特性,选择合适的清洗剂,如酸碱溶液、有机溶剂等。
3.清洗条件的确定:根据不锈钢管的材质和污染情况,确定清洗的温度、浓度、时间等条件。
三、清洗流程1.表面预处理:将不锈钢管表面的油污、尘土等物质用清洗剂或溶剂进行清洗,可以采用喷洗、刷洗等方法,确保表面干净。
2.酸洗:将清洗槽中的酸溶液预热至适当温度,将不锈钢管浸泡于酸溶液中,保持一定时间,使酸溶液彻底清除表面的氧化皮和污染物。
3.中和洗:将酸洗后的不锈钢管用水进行充分冲洗,将酸溶液中的残留物彻底冲洗干净。
4.碱洗:将清洗槽中的碱溶液预热至适当温度,将不锈钢管浸泡于碱溶液中,保持一定时间,使碱溶液中的碱性物质中和酸洗过程中产生的酸性物质。
5.再次中和洗:将碱洗后的不锈钢管用水进行充分冲洗,将碱溶液中的残留物彻底冲洗干净。
6.清洗剂去除:最后用清水对不锈钢管进行充分冲洗,彻底去除所有清洗剂的残留。
四、清洗质量要求1.表面光洁度:经过化学清洗后,不锈钢管表面应达到一定的光洁度要求,通常可以通过目测或检测仪器来评估。
2.腐蚀性能:清洗后的不锈钢管应具备良好的耐腐蚀性能,可以进行相应的腐蚀试验来评估。
五、安全注意事项1.清洗剂使用时应注意安全操作,佩戴防护手套、眼镜等个人防护装备。
2.清洗过程中应注意通风,避免酸碱气体的吸入。
3.清洗槽和设备应定期维护和清洁,避免污染物的积累。
六、总结本文介绍了不锈钢管化学清洗的标准流程和要求,包括准备工作、清洗流程、清洗质量要求和安全注意事项等。
在实际操作中,应根据具体情况选择合适的清洗剂和条件,并确保清洗后的不锈钢管表面光洁度和腐蚀性能符合要求。
不锈钢管道酸洗钝化 依据
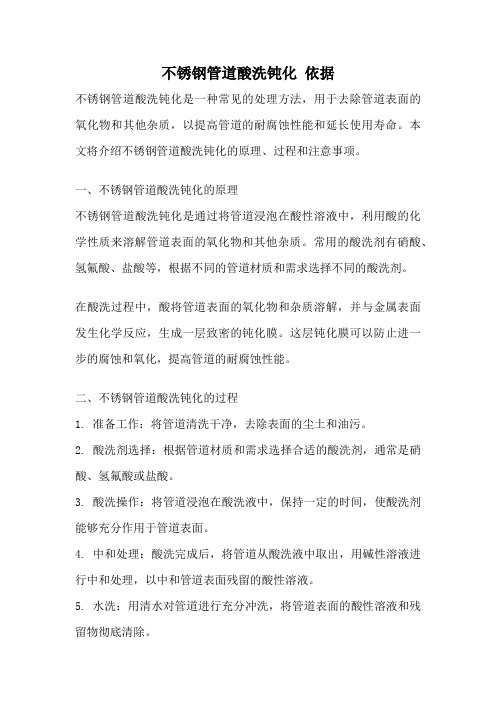
不锈钢管道酸洗钝化依据不锈钢管道酸洗钝化是一种常见的处理方法,用于去除管道表面的氧化物和其他杂质,以提高管道的耐腐蚀性能和延长使用寿命。
本文将介绍不锈钢管道酸洗钝化的原理、过程和注意事项。
一、不锈钢管道酸洗钝化的原理不锈钢管道酸洗钝化是通过将管道浸泡在酸性溶液中,利用酸的化学性质来溶解管道表面的氧化物和其他杂质。
常用的酸洗剂有硝酸、氢氟酸、盐酸等,根据不同的管道材质和需求选择不同的酸洗剂。
在酸洗过程中,酸将管道表面的氧化物和杂质溶解,并与金属表面发生化学反应,生成一层致密的钝化膜。
这层钝化膜可以防止进一步的腐蚀和氧化,提高管道的耐腐蚀性能。
二、不锈钢管道酸洗钝化的过程1. 准备工作:将管道清洗干净,去除表面的尘土和油污。
2. 酸洗剂选择:根据管道材质和需求选择合适的酸洗剂,通常是硝酸、氢氟酸或盐酸。
3. 酸洗操作:将管道浸泡在酸洗液中,保持一定的时间,使酸洗剂能够充分作用于管道表面。
4. 中和处理:酸洗完成后,将管道从酸洗液中取出,用碱性溶液进行中和处理,以中和管道表面残留的酸性溶液。
5. 水洗:用清水对管道进行充分冲洗,将管道表面的酸性溶液和残留物彻底清除。
6. 干燥:将管道晾干或用风机吹干,确保管道表面干燥。
三、不锈钢管道酸洗钝化的注意事项1. 安全操作:酸洗剂具有强腐蚀性和刺激性,操作时要佩戴防护手套、护目镜等安全装备,避免酸液接触皮肤和眼睛。
2. 通风环境:酸洗过程中产生的酸性气体有毒,应在通风良好的环境下进行操作,避免对人员造成伤害。
3. 控制酸洗时间:酸洗时间过长会导致管道表面钝化膜过厚,影响管道的质量和使用寿命;酸洗时间过短则不能完全去除管道表面的氧化物和杂质,影响钝化效果。
4. 控制酸洗温度:酸洗温度过高容易引起酸洗液的剧烈反应,产生危险物质;酸洗温度过低则影响酸洗效果。
5. 中和处理:酸洗后的管道表面仍残留有酸性溶液,需及时进行中和处理,以免对管道表面产生二次腐蚀。
6. 水洗彻底:水洗过程中要充分冲洗管道,确保管道表面没有残留的酸性溶液和残留物,以免对管道产生腐蚀。
不锈钢管道酸洗钝化工艺流程

不锈钢管道酸洗钝化工艺流程一、引言不锈钢管道是一种常用的管道材料,由于其抗腐蚀性能好、耐高温、耐压力等特点,在工业生产中得到广泛应用。
然而,不锈钢管道在使用过程中,可能会因为外界环境因素导致表面产生氧化膜、锈斑等问题,影响其美观性和使用寿命。
因此,对不锈钢管道进行酸洗钝化处理是必要的。
二、酸洗钝化的原理酸洗钝化是通过将不锈钢管道浸泡在酸性溶液中,利用酸的腐蚀性将管道表面的氧化膜、锈斑等物质去除,然后在管道表面形成一层致密、均匀的钝化膜,提高不锈钢管道的耐腐蚀性能。
三、酸洗钝化工艺流程1. 清洗准备:将待处理的不锈钢管道表面清洗干净,去除表面的油污、灰尘等杂质,以确保酸洗钝化效果良好。
2. 酸洗:将清洗后的不锈钢管道浸泡在稀硝酸、稀硫酸或混合酸中,时间根据管道表面的污染程度和要求的钝化膜厚度而定,通常为10-30分钟。
酸洗过程中需注意保持酸液的温度和浓度,避免过高或过低导致管道表面腐蚀或钝化效果不理想。
3. 中和洗净:将酸洗后的不锈钢管道用水洗净,去除残留的酸液,然后用中和剂中和管道表面的酸性物质,以保证管道表面的中性。
4. 钝化处理:将中和洗净后的不锈钢管道浸泡在钝化剂溶液中,使其与管道表面发生化学反应,生成致密、均匀的钝化膜。
钝化剂的选择根据不同的要求和材质而定,常用的有硝酸铬、硝酸亚铁、硫酸铜等。
钝化处理时间一般为20-60分钟。
5. 清洗干燥:将钝化处理后的不锈钢管道用水洗净,去除残留的钝化剂溶液,然后进行干燥处理,可采用自然干燥或烘干的方式。
四、注意事项1. 在进行酸洗钝化处理时,应采取必要的安全措施,如佩戴防护手套、护目镜等,避免酸液对皮肤和眼睛的伤害。
2. 酸洗钝化处理应在通风良好的环境下进行,以避免吸入有害气体对身体健康的影响。
3. 酸洗钝化剂的选择应根据不锈钢管道的材质和要求进行,以确保钝化膜的质量和效果。
4. 酸洗钝化处理后的不锈钢管道应避免与其他腐蚀性物质接触,以防止钝化膜的破坏。
不锈钢管道酸洗钝化方案

不锈钢管道酸洗钝化方案一、前期准备工作:1.确保操作人员具有相关的技术和安全培训,了解相关的安全操作规程和应急处理知识。
2.确保操作场所通风良好,以确保酸洗过程中产生的有害气体及时排除。
二、材料准备:1.酸洗液:选择合适的酸洗液进行酸洗,一般采用浓硝酸、氢氟酸和水的混合物,比例根据实际情况确定。
2.酸洗槽:根据管道的尺寸和数量选择合适的酸洗槽,确保管道完全浸泡在酸洗液中。
三、操作步骤:1.清洗管道表面:使用洗涤剂和清水清洗不锈钢管道表面,去除表面的油污和其他杂质。
2.酸洗处理:将清洗好的管道浸泡在酸洗槽中,保证管道完全浸泡在酸洗液中,然后根据实际情况确定酸洗时间,一般为10-60分钟。
酸洗液的浓度和温度也要根据实际情况确定。
3.中和处理:在酸洗完成后,及时将管道从酸洗槽中取出,用大量清水冲洗管道表面,将酸洗液中的残留物洗净。
然后使用碱性中和剂对管道进行中和处理,以中和酸洗液的残留物。
4.钝化处理:将中和处理完的管道再次进行清洗,确保管道表面无残留物。
然后使用适当的钝化剂涂覆在管道表面,生成一层钝化膜,增加管道的耐腐蚀性能。
四、安全措施:1.确保操作人员穿着安全防护装备,包括手套、护目镜、防护服等。
2.在酸洗过程中远离酸洗槽,以免吸入有害气体。
3.确保酸洗槽周围通风良好,及时排除产生的有害气体。
4.在操作过程中,禁止使用金属工具和容器来接触酸洗液,以免产生危险反应。
五、废液处理:1.酸洗液和中和液是有毒的废液,不能直接排放到环境中。
2.废液应收集到专门的废液容器中,然后由专业的废液处理公司进行处理。
六、总结:不锈钢管道酸洗钝化是一项非常重要的处理工艺,在操作过程中必须要遵守相关的安全操作规程和措施。
酸洗液的浓度、温度和浸泡时间都要根据实际情况来确定,以确保管道表面的氧化皮和杂质能够被彻底去除。
在酸洗完成后,及时进行中和处理和钝化处理,以提高不锈钢管道的耐腐蚀性能和美观度。
同时,废液的处理也是一个重要的环节,必须要找到合适的废液处理公司进行处理,以免对环境造成污染和危害。
化学清洗方案
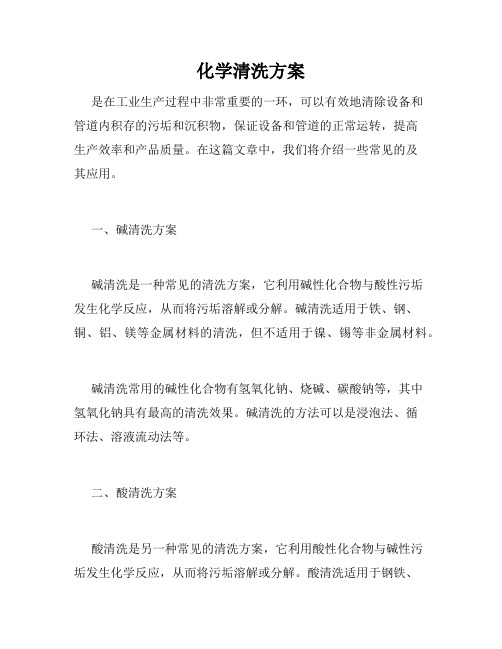
化学清洗方案是在工业生产过程中非常重要的一环,可以有效地清除设备和管道内积存的污垢和沉积物,保证设备和管道的正常运转,提高生产效率和产品质量。
在这篇文章中,我们将介绍一些常见的及其应用。
一、碱清洗方案碱清洗是一种常见的清洗方案,它利用碱性化合物与酸性污垢发生化学反应,从而将污垢溶解或分解。
碱清洗适用于铁、钢、铜、铝、镁等金属材料的清洗,但不适用于镍、锡等非金属材料。
碱清洗常用的碱性化合物有氢氧化钠、烧碱、碳酸钠等,其中氢氧化钠具有最高的清洗效果。
碱清洗的方法可以是浸泡法、循环法、溶液流动法等。
二、酸清洗方案酸清洗是另一种常见的清洗方案,它利用酸性化合物与碱性污垢发生化学反应,从而将污垢溶解或分解。
酸清洗适用于钢铁、铜、铝、锌、镍、镁等金属材料的清洗,但不适用于不锈钢和钛合金等耐腐蚀材料。
酸清洗常用的酸性化合物有盐酸、硝酸、磷酸等,其中盐酸的清洗效果最好。
酸清洗的方法可以是浸泡法、循环法、喷淋法等。
三、氧化剂清洗方案氧化剂清洗是一种利用氧化剂将污垢氧化分解的清洗方案。
氧化剂清洗适用于电器、电气部件、半导体器件、陶瓷材料等的清洗。
常用的氧化剂有过氧化氢、高锰酸钾、过氧化钠等,其中过氧化氢的清洗效果最好。
氧化剂清洗的方法可以是浸泡法、喷淋法等。
四、溶剂清洗方案溶剂清洗是利用可以溶解污垢的有机溶剂将污垢溶解并去除的清洗方案。
溶剂清洗适用于塑料、橡胶、油漆、油脂等材料的清洗。
常用的溶剂有酒精、丙酮、氯仿、甲苯等,其中甲苯的清洗效果最好。
溶剂清洗的方法可以是浸泡法、喷淋法、蒸发法等。
五、生物清洗方案生物清洗是利用微生物对污垢进行分解的清洗方案。
生物清洗适用于食品、医药、化妆品等行业的设备清洗。
生物清洗的方法可以是浸泡法、循环法、喷淋法等。
常用的微生物有酵母菌、乳酸菌、厌氧菌等,其中酵母菌的清洗效果最好。
以上就是常见的及其应用,不同的设备和材料需要选择不同的清洗方案进行清洗。
在清洗过程中,需要注意安全,配好适量的化学药剂,控制好温度和时间,以确保清洗效果和材料的安全。
不锈钢管酸洗钝化的8个操作步骤(精)
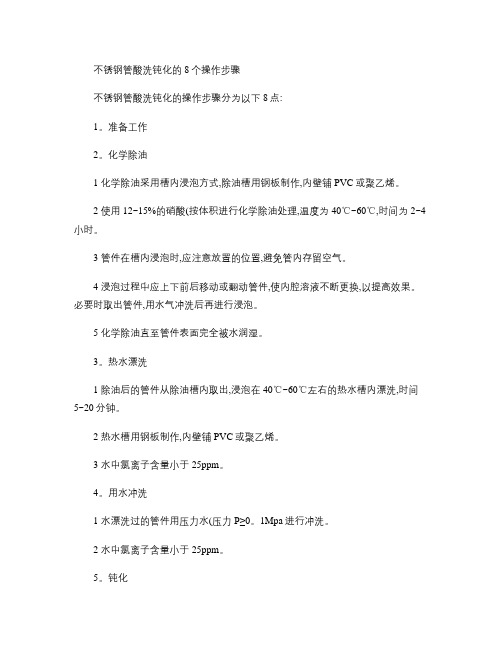
不锈钢管酸洗钝化的8个操作步骤不锈钢管酸洗钝化的操作步骤分为以下8点:1。
准备工作2。
化学除油1 化学除油采用槽内浸泡方式,除油槽用钢板制作,内壁铺PVC或聚乙烯。
2 使用12~15%的硝酸(按体积进行化学除油处理,温度为40℃~60℃,时间为2~4小时。
3 管件在槽内浸泡时,应注意放置的位置,避免管内存留空气。
4 浸泡过程中应上下前后移动或翻动管件,使内腔溶液不断更换,以提高效果。
必要时取出管件,用水气冲洗后再进行浸泡。
5 化学除油直至管件表面完全被水润湿。
3。
热水漂洗1 除油后的管件从除油槽内取出,浸泡在40℃~60℃左右的热水槽内漂洗,时间5~20分钟。
2 热水槽用钢板制作,内壁铺PVC或聚乙烯。
3 水中氯离子含量小于25ppm。
4。
用水冲洗1 水漂洗过的管件用压力水(压力P≥0。
1Mpa进行冲洗。
2 水中氯离子含量小于25ppm。
5。
钝化1 钝化采用池内槽泡方式,钝化液配方和浸泡时间按照2。
3表任选一种。
2 钝化槽钢板制作,内壁铺防酸塑料。
3 槽内浸泡时,应注意放置的位置,避免管内存留空气。
4 浸泡过程中应上下前后移动或翻动管件,使内腔溶液不断更换,以提高效果。
必要时取出管件,用水气冲洗后再进行浸泡。
6。
干燥经过钝化的管件,要抓紧用洁净的压缩空气或氮气吹干,并且必须有足够的时间(至少2小时使之在空气中自然钝化。
7。
检验管件经钝化后,应进行自检、互检,然后提交质检员按要求进行验收。
8。
保护1 如外表面需要进行油漆的管件,则按照涂装要求进行。
2 检验合格后的管件用塑料塞封口,用三防布进行包扎保护,并进行标识。
相关文章:放眼不锈钢管未来发展的五大市场不锈钢管发展遭遇两大难题不锈钢管之316与304材质比较。
化学清洗技术及应用实例
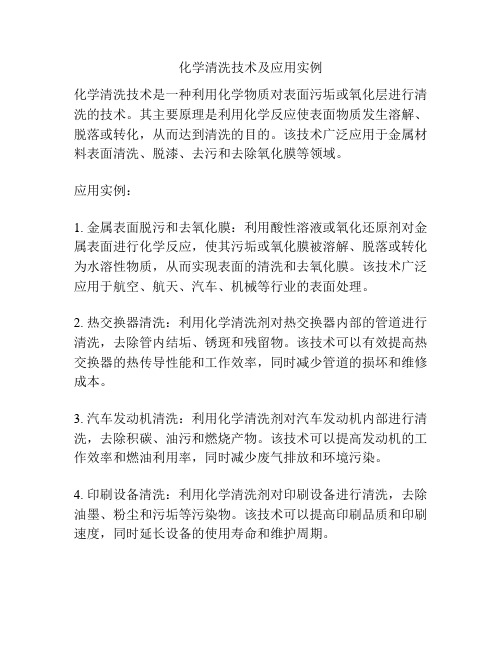
化学清洗技术及应用实例
化学清洗技术是一种利用化学物质对表面污垢或氧化层进行清洗的技术。
其主要原理是利用化学反应使表面物质发生溶解、脱落或转化,从而达到清洗的目的。
该技术广泛应用于金属材料表面清洗、脱漆、去污和去除氧化膜等领域。
应用实例:
1. 金属表面脱污和去氧化膜:利用酸性溶液或氧化还原剂对金属表面进行化学反应,使其污垢或氧化膜被溶解、脱落或转化为水溶性物质,从而实现表面的清洗和去氧化膜。
该技术广泛应用于航空、航天、汽车、机械等行业的表面处理。
2. 热交换器清洗:利用化学清洗剂对热交换器内部的管道进行清洗,去除管内结垢、锈斑和残留物。
该技术可以有效提高热交换器的热传导性能和工作效率,同时减少管道的损坏和维修成本。
3. 汽车发动机清洗:利用化学清洗剂对汽车发动机内部进行清洗,去除积碳、油污和燃烧产物。
该技术可以提高发动机的工作效率和燃油利用率,同时减少废气排放和环境污染。
4. 印刷设备清洗:利用化学清洗剂对印刷设备进行清洗,去除油墨、粉尘和污垢等污染物。
该技术可以提高印刷品质和印刷速度,同时延长设备的使用寿命和维护周期。
浅析管道工程酸洗方法及应用范围分析

浅析管道工程酸洗方法及应用范围分析
管道工程酸洗方法是指利用酸溶液对管道进行清洗的一种方法。
酸洗可以有效地去除管道内壁的氧化皮、油污、焊渣等杂质,达到清洁管道内壁的目的。
酸洗方法主要分为浸泡酸洗和循环酸洗两种。
浸泡酸洗是将管道放入酸溶液中浸泡一段时间,使酸溶液能充分地对管道内壁进行清洗。
这种方法适用于较小直径的管道,可以直接将管道放入酸槽内进行浸泡。
浸泡酸洗的优点是操作简单,清洗效果较好,但时间较长。
在管道工程中,酸洗主要应用于以下几个方面:
1.新建管道工程:在新建管道工程中,管道内壁常常会有油污、焊渣等杂质,这些杂质会影响管道的正常运行和使用寿命。
通过酸洗可以将管道内壁清洗干净,确保管道的正常运行。
2.管道维护保养:在管道使用一段时间后,管道内壁会产生氧化皮等杂质,这些杂质会降低管道的流量和传热效果。
通过定期进行酸洗可以有效地去除这些杂质,保持管道的良好状态。
3.管道修复:在管道发生泄漏、堵塞等故障后,需要进行修复。
在修复过程中,往往需要对管道进行清洗,使修复后的管道能够正常使用。
管道工程酸洗方法是一种常用的管道清洗方法,适用于新建管道工程、管道维护保养和管道修复等场合。
通过酸洗可以有效地去除管道内壁的杂质,保证管道的正常运行和使用寿命。
但在进行酸洗时需要注意安全,避免对环境和人身造成伤害。
管子酸洗工艺技术

管子酸洗工艺技术管子酸洗工艺技术是一种常用于清洗金属管子表面的工艺方法,通过使用酸性溶液来去除管子表面的污垢和氧化物,以达到清洗和去除锈蚀的目的。
管子酸洗工艺技术在金属加工和制造行业广泛应用,对于提高管子的表面质量和延长使用寿命具有重要的意义。
管子酸洗工艺技术的主要步骤包括前处理、清洗和后处理。
首先,进行前处理,包括表面清洗和除油。
表面清洗是为了去除管子表面的尘土和杂质,以确保酸洗过程的顺利进行;除油则是为了去除管子表面的油污,常常采用有机溶剂来进行清洁。
在前处理完成后,开始进行清洗工艺。
酸洗是管子酸洗工艺技术的核心步骤,主要通过浸泡管子在酸性溶液中来去除管子表面的污垢和氧化物。
酸洗过程中,酸洗液的选择是非常重要的,一般采用稀硫酸、盐酸或硝酸等作为酸洗液。
在酸洗液中,管子表面的氧化物和污垢会与酸发生反应,并产生溶解、脱落。
酸洗液的温度和浓度都会对酸洗效果产生影响,一般情况下,较高的温度和浓度会加快酸洗速度,但也会增加酸洗液对管子的腐蚀速度,所以需要根据具体的情况选择合适的酸洗条件。
酸洗完成后,进行后处理是为了去除酸洗液残留和修复管子表面的防腐层。
一般采用水冲洗的方法来去除酸洗液的残留物,并通过钝化剂来修复管子表面的防腐层。
钝化剂可以通过浸泡的方式添加到管子表面,使其在与空气接触时形成一层保护膜,减少进一步的腐蚀。
总的来说,管子酸洗工艺技术是一种有效的金属表面清洗和防腐处理方法。
通过适当的酸洗液和酸洗条件,可以有效地去除管子表面的污垢和氧化物,并保护管子的表面不受进一步腐蚀。
在实际应用中,需要根据具体的管子材质和使用环境选择合适的酸洗工艺参数,以达到最佳的清洗和防腐效果。
浸泡式化学清洗技术在模块化不锈钢管道中的应用
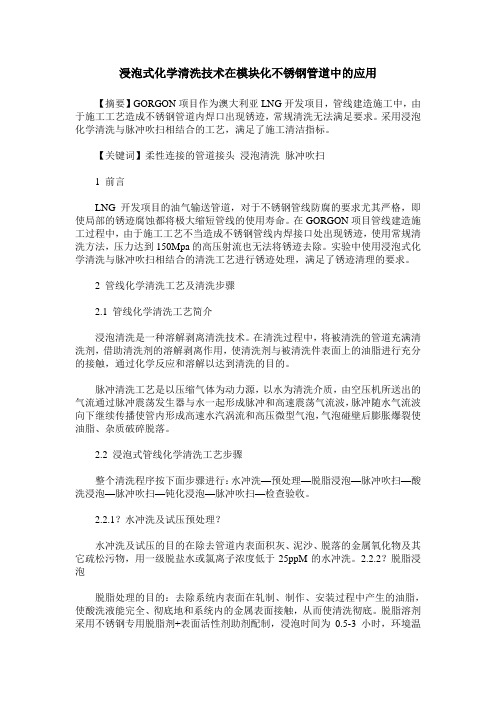
浸泡式化学清洗技术在模块化不锈钢管道中的应用【摘要】GORGON项目作为澳大利亚LNG开发项目,管线建造施工中,由于施工工艺造成不锈钢管道内焊口出现锈迹,常规清洗无法满足要求。
采用浸泡化学清洗与脉冲吹扫相结合的工艺,满足了施工清洁指标。
【关键词】柔性连接的管道接头浸泡清洗脉冲吹扫1 前言LNG开发项目的油气输送管道,对于不锈钢管线防腐的要求尤其严格,即使局部的锈迹腐蚀都将极大缩短管线的使用寿命。
在GORGON项目管线建造施工过程中,由于施工工艺不当造成不锈钢管线内焊接口处出现锈迹,使用常规清洗方法,压力达到150Mpa的高压射流也无法将锈迹去除。
实验中使用浸泡式化学清洗与脉冲吹扫相结合的清洗工艺进行锈迹处理,满足了锈迹清理的要求。
2 管线化学清洗工艺及清洗步骤2.1 管线化学清洗工艺简介浸泡清洗是一种溶解剥离清洗技术。
在清洗过程中,将被清洗的管道充满清洗剂,借助清洗剂的溶解剥离作用,使清洗剂与被清洗件表面上的油脂进行充分的接触,通过化学反应和溶解以达到清洗的目的。
脉冲清洗工艺是以压缩气体为动力源,以水为清洗介质,由空压机所送出的气流通过脉冲震荡发生器与水一起形成脉冲和高速震荡气流波,脉冲随水气流波向下继续传播使管内形成高速水汽涡流和高压微型气泡,气泡碰壁后膨胀爆裂使油脂、杂质破碎脱落。
2.2 浸泡式管线化学清洗工艺步骤整个清洗程序按下面步骤进行:水冲洗—预处理—脱脂浸泡—脉冲吹扫—酸洗浸泡—脉冲吹扫—钝化浸泡—脉冲吹扫—检查验收。
2.2.1?水冲洗及试压预处理?水冲洗及试压的目的在除去管道内表面积灰、泥沙、脱落的金属氧化物及其它疏松污物,用一级脱盐水或氯离子浓度低于25ppM的水冲洗。
2.2.2?脱脂浸泡脱脂处理的目的:去除系统内表面在轧制、制作、安装过程中产生的油脂,使酸洗液能完全、彻底地和系统内的金属表面接触,从而使清洗彻底。
脱脂溶剂采用不锈钢专用脱脂剂+表面活性剂助剂配制,浸泡时间为0.5-3小时,环境温度在-5℃—30℃均可进行。
【涨知识】不锈钢管道的内表面脱脂清洁处理及钝化
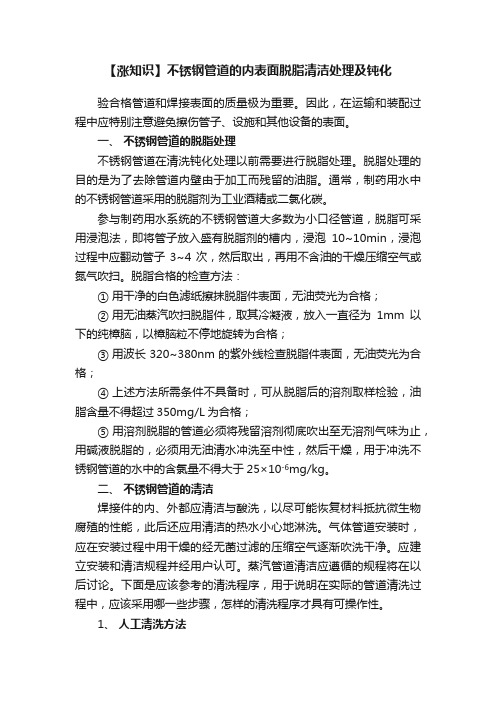
【涨知识】不锈钢管道的内表面脱脂清洁处理及钝化验合格管道和焊接表面的质量极为重要。
因此,在运输和装配过程中应特别注意避免擦伤管子、设施和其他设备的表面。
一、不锈钢管道的脱脂处理不锈钢管道在清洗钝化处理以前需要进行脱脂处理。
脱脂处理的目的是为了去除管道内壁由于加工而残留的油脂。
通常,制药用水中的不锈钢管道采用的脱脂剂为工业酒精或二氯化碳。
参与制药用水系统的不锈钢管道大多数为小口径管道,脱脂可采用浸泡法,即将管子放入盛有脱脂剂的槽内,浸泡10~10min,浸泡过程中应翻动管子3~4次,然后取出,再用不含油的干燥压缩空气或氮气吹扫。
脱脂合格的检查方法:①用干净的白色滤纸擦抹脱脂件表面,无油荧光为合格;②用无油蒸汽吹扫脱脂件,取其冷凝液,放入一直径为1mm以下的纯樟脑,以樟脑粒不停地旋转为合格;③用波长320~380nm的紫外线检查脱脂件表面,无油荧光为合格;④上述方法所需条件不具备时,可从脱脂后的溶剂取样检验,油脂含量不得超过350mg/L为合格;⑤用溶剂脱脂的管道必须将残留溶剂彻底吹出至无溶剂气味为止,用碱液脱脂的,必须用无油清水冲洗至中性,然后干燥,用于冲洗不锈钢管道的水中的含氯量不得大于25×10-6mg/kg。
二、不锈钢管道的清洁焊接件的内、外都应清洁与酸洗,以尽可能恢复材料抵抗微生物腐殖的性能,此后还应用清洁的热水小心地淋洗。
气体管道安装时,应在安装过程中用干燥的经无菌过滤的压缩空气逐渐吹洗干净。
应建立安装和清洁规程并经用户认可。
蒸汽管道清洁应遵循的规程将在以后讨论。
下面是应该参考的清洗程序,用于说明在实际的管道清洗过程中,应该采用哪一些步骤,怎样的清洗程序才具有可操作性。
1、人工清洗方法基本方法是先用干净的布团在管内沿着的一个方向拖擦,或用压缩空气对管内表面进行吹扫,直到管内无污垢为止。
2、化学清洗方法这个方法宜在不锈钢管道的焊接安装完成以后进行,其基本步骤如下:①化学清洗液体的配方按体积分数计:硝酸(HNO3)15%,氢氟酸(HF)1%,水(H2O)83%。
化学清洗方案

化学清洗方案化学清洗方案1. 简介化学清洗是一种利用化学药剂来去除污垢和污染物的技术方法。
它在各种行业中被广泛应用,包括工业、制药、医疗和食品等领域。
化学清洗可以有效去除不同类型的污染物,包括油脂、铁锈、颜料和腐蚀产物等。
本文将介绍几种常用的化学清洗方案及其应用。
2. 酸性清洗方案酸性清洗方案是一种常用的化学清洗方法。
它利用酸性溶液来去除不溶于水的污垢。
酸性清洗方案可以有效去除金属表面的氧化物、铁锈和钙垢等污染物。
常用的酸性清洗剂包括盐酸、硝酸和磷酸等。
**应用场景:**酸性清洗方案适用于金属制品的清洗,如不锈钢管道、金属容器等。
它还可以用于清洗腐蚀性污染物、如钙垢和水垢。
**操作步骤:**1. 配制酸性溶液,一般将酸性清洗剂与水按一定比例混合。
具体比例可以根据清洗对象的污染程度和材料的耐受性来确定。
2. 将清洗溶液倒入清洗容器中。
注意要选择耐酸的容器,防止溶液泄漏或对容器造成腐蚀。
3. 将需要清洗的金属制品放入清洗溶液中,确保完全浸没。
4. 按照清洗剂的要求,进行一定时间的清洗。
清洗时间通常取决于污染的程度,可以从几分钟到几小时不等。
5. 清洗结束后,将金属制品取出并用清水冲洗,以去除残留的清洗剂。
6. 最后,对清洗后的金属制品进行干燥,以防止水珠残留导致二次污染。
3. 碱性清洗方案碱性清洗方案是另一种常用的化学清洗方法。
它利用碱性溶液来去除酸性污染物和油脂等污垢。
碱性清洗剂可以有效去除金属表面的油脂、涂料和氧化物等污染物。
常用的碱性清洗剂包括氢氧化钠和磷酸钠等。
**应用场景:**碱性清洗方案适用于去除金属表面的油脂和涂料,以及一些酸性污染物。
它常被应用于金属制品的表面处理和涂装前的准备。
**操作步骤:**1. 配制碱性溶液,一般将碱性清洗剂与水按一定比例混合。
具体比例可以根据清洗对象的污染程度和材料的耐受性来确定。
2. 将清洗溶液倒入清洗容器中。
注意要选择耐碱的容器,防止溶液泄漏或对容器造成腐蚀。
- 1、下载文档前请自行甄别文档内容的完整性,平台不提供额外的编辑、内容补充、找答案等附加服务。
- 2、"仅部分预览"的文档,不可在线预览部分如存在完整性等问题,可反馈申请退款(可完整预览的文档不适用该条件!)。
- 3、如文档侵犯您的权益,请联系客服反馈,我们会尽快为您处理(人工客服工作时间:9:00-18:30)。
浸泡式化学清洗技术在模块化不锈钢管道中的应用
【摘要】gorgon项目作为澳大利亚lng开发项目,管线建造施工中,由于施工工艺造成不锈钢管道内焊口出现锈迹,常规清洗无法满足要求。
采用浸泡化学清洗与脉冲吹扫相结合的工艺,满足了施工清洁指标。
【关键词】柔性连接的管道接头浸泡清洗脉冲吹扫
1 前言
lng开发项目的油气输送管道,对于不锈钢管线防腐的要求尤其严格,即使局部的锈迹腐蚀都将极大缩短管线的使用寿命。
在gorgon项目管线建造施工过程中,由于施工工艺不当造成不锈钢管线内焊接口处出现锈迹,使用常规清洗方法,压力达到150mpa的高压射流也无法将锈迹去除。
实验中使用浸泡式化学清洗与脉冲吹扫相结合的清洗工艺进行锈迹处理,满足了锈迹清理的要求。
2 管线化学清洗工艺及清洗步骤
2.1 管线化学清洗工艺简介
浸泡清洗是一种溶解剥离清洗技术。
在清洗过程中,将被清洗的管道充满清洗剂,借助清洗剂的溶解剥离作用,使清洗剂与被清洗件表面上的油脂进行充分的接触,通过化学反应和溶解以达到清洗的目的。
脉冲清洗工艺是以压缩气体为动力源,以水为清洗介质,由空压机所送出的气流通过脉冲震荡发生器与水一起形成脉冲和高速震荡气流波,脉冲随水气流波向下继续传播使管内形成高速水汽涡流和高压微型气泡,气泡碰壁后膨胀爆裂使油脂、杂质破碎脱落。
2.2 浸泡式管线化学清洗工艺步骤
整个清洗程序按下面步骤进行:水冲洗—预处理—脱脂浸泡—脉冲吹扫—酸洗浸泡—脉冲吹扫—钝化浸泡—脉冲吹扫—检查验收。
2.2.1?水冲洗及试压预处理?
水冲洗及试压的目的在除去管道内表面积灰、泥沙、脱落的金属氧化物及其它疏松污物,用一级脱盐水或氯离子浓度低于25ppm的水冲洗。
2.2.2?脱脂浸泡
脱脂处理的目的:去除系统内表面在轧制、制作、安装过程中产
生的油脂,使酸洗液能完全、彻底地和系统内的金属表面接触,从而使清洗彻底。
脱脂溶剂采用不锈钢专用脱脂剂+表面活性剂助剂配制,浸泡时间为0.5-3小时,环境温度在-5℃—30℃均可进行。
2.2.3?脱脂后水冲洗
脱脂后水冲洗的目的除去系统内残存的酸性脱脂剂及脱落的杂质,为酸洗创造条件。
在排出管道内的清洗剂时,使用氮气脉冲发生器对管道吹扫,把附着在管道内壁的附着物吹扫并冲洗出来,当ph值在6-8时水冲洗完成,ph值采用ph试纸测定。
在中和处理槽中用naoh或ca(oh)2进行中和处理,ph值达到6-9时,暂时排至当地具有污水处理资质的污水处理厂进一步加药加氧、絮凝处理。
2.2.4?酸洗浸泡
酸洗的目的是利用酸洗液与金属氧化物进行化学反应,生成可溶性物质而除去。
酸洗药剂采用5%硝酸+0.5%氢氟酸+0.5%缓蚀剂lan-826配制而成。
酸洗浸泡的时间为1—8小时,常温即可进行,铁离子含量、酸浓度的测定每30分钟一次。
在排出管道内的清洗剂时,使用氮气脉冲发生器对管道吹扫,把附着在管道内壁的附着物吹扫并冲洗出来。
说明:当酸洗液浓度低于5%,必须补加酸洗液浓度至5%,同时补加还原剂及缓蚀剂lan-826。
当酸洗液铁离子含量高于1000ppm,必须更换酸洗剂,重新配置酸洗药剂。
2.2.5?酸洗后水冲洗
酸洗后水冲洗的目的除去管道内、外表面残存的酸洗剂及脱落的各种污物。
当冲洗水的ph值达到6-8时,可结束水冲洗,每根管道的水冲洗时间最少不小于5分钟(视管道长短而定)ph值采用ph试纸测定。
将废液集中到中和槽中用naoh或ca(oh)2溶液中和,ph值达到7-8时,暂时排至当地具有污水处理资质污水处理厂进一步加药、加氧处理。
2.2.6?钝化浸泡
钝化的目的是通过钝化处理,可在金属表面形成均匀、致密的保护膜。
新的氧化保护膜增强耐腐蚀力。
钝化剂采用不锈钢专用钝化剂,钝化浸泡的时间为0.5小时。
2.2.7?脉冲吹扫
钝化浸泡结束后,用水冲洗管道内的钝化残液,使用氮气脉冲发生器对管道吹扫,把附着在管道内壁的附着物吹扫并冲洗出来,钝化废液进行回收后用naoh中和处理。
当冲洗水的ph值达到6-8时,可结束水冲洗,每根管道的水冲洗时间最少不小于5分钟(视管道长短而定)ph值采用ph试纸测定。
备注:管道浸泡清洗后,用干燥无油的氮气或压缩空气将管道内残存的水吹扫并干燥后,管道两端用韧性好的塑料缠绕薄膜或者用脱脂剂清洗干净后塑料管帽进行密封保护。
所有化学清洗废液均集中至污水池进行处理,污水做到零排放,废水排放达到相关的一级排放标准《污水综合排放标准
(gb8978-99)》、《工业污水排放标准(gb-2)》。
3 管线化学清洗清洁质量要求
3.1 管线化学清洗标准
按照化学清洗行业标准《hg/t2387-2007》的有关规定,清洗要达到以下要求:
被清洗的金属表面清洁,无点蚀,无其他局部腐蚀现象。
均匀腐蚀,试片检测平均腐蚀率应小于
2g/m2﹒h。
形成完整、均匀的钝化膜。
钝化膜的质量采用显蓝测定,变色时间为20-30秒钟。
被清洗的系统中无铁锈、灰尘、污物或其他颗粒存在;金属表面油的最大允许浓度为1g/m2(浓度为1g/m2时,用手指磨擦表面及强白光检查,肉眼无法看到油污,也无法检查到涂抹的痕迹)。
3.2 管线化学清洗的检验
管线化学清洗的检验分为直接检查和间接检查:
直接检查:被检查表面必须干燥且不含:清洗剂、粘附铁锈、焊渣、松散颗粒或纤维屑等。
用干净的脱脂棉布擦洗表面,然后,检查面布确保无油、残渣、污渍、纤维等。
间接检查:无法进行视觉检查的部件,必须从清洗溶剂中取样,在强白光下进行检查,与新的、未经使用的溶剂样品进行比较,并保证对比检查无差别,没有残留物;
样品还必须在紫外光(波长032-038 um)下进行检测,与未经使用的溶剂再次比较。
样品含污染物≥0.1g油/l,将会使溶剂发出荧光(无油脂荧光为合格及无亮点);
清洁度要求及检验要求除满足上述要求外,还必须满足《脱脂工程及验收规范》hgj202-82(以最新版本为准)。
[1] 工业设备化学清洗质量标准[s].中华人民共和国化工行业标准hg/t2387-2007
[2] 工业管道工程施工及验收规范[s].中华人民共和国国家标准gb50235-1997
[3] 中国石油化工集团公司. 石油化工施工安全技术规程[s].石化行业标准sh3505-1999
[4] 污水综合排放标准[s]. 中华人民共和国国家标准
gb8978-1999
[5] 工业污水排放标准[s].中华人民共和国国家标准gb8978-1996。