4.3 分型面与浇注系统设计
注射模具的基本结构与分类

第4章 注射模具设计
4.1 注射模具的基本结构与分类 4.2 注射模与注射机的关系 4.3 分型面的选择 4.4 型腔数目的确定与排列形式 4.5 注射模具浇注系统设计 4.6 排气和引气系统设计 4.7 注射模具成型零件设计 4.8 注射模具导向机构设计 4.9 脱模机构设计 4.10 注射模具侧向抽芯机构设计 4.11 注射模具温度调节系统设计 4.12 模架设计 4.13 注射模具材料的选用
安装在注射机上的注射模
4.1
4.1.1 注射模的结构组成
4.1
4.1.1 注射模的结构组成
导柱
4.1
4.1.1 注射模的结构组成
4.1
4.1.1 注射模的结构组成
定位圈
4.1
4.1.1 注射模的结构组成 内六角螺钉
4.1
4.1.1 注射模的结构组成 复位杆
4.1
4.1.1 注射模的结构组成 限位钉
4.1
5. 自动脱螺纹的注射模
4.1
6 .推出机构设在定模一侧的注射模
4.9 脱模机构设计
脱模板的另一种结构使用实例
4.1
7 .热流道凝料注射模
4.1
7 .热流道凝料注射模
4.1
7 .热流道凝料注射模
4.1
7 .热流道凝料注射模
4.1
7 .热流道凝料注射模
4.1
单分型面模具三维结构
4.1
2.双分型面注射模
4.1
2.双分型面注射模
4.1
2.双分型面注射模
4.1
2.双分型面注射模
4.1
双分型面模具的模架
流道板
4.1
双分型面注射模
4.1
双分型面注射模
4-3 浇注系统的设计-1

NO44
第四章
注射模设计
流道长度宜短, 因为长的流道不但会造成压力损失,不利于 生产性,同時也浪费材料;但过短, 产品的残余应力增大, 并 且容易产生毛边。 流道长度可以按如下经验公式计算:
D=
D——分流道直徑mm W——产品质量g L——流道長度mm
Chapter 4-3 浇注系统的设计
主流道是熔融塑料最先 经过的流道,它的大小 直接影响熔体的流动速 度和充模时间
Chapter 4-3 浇注系统的设计
NO9
Байду номын сангаас
第四章
②分流道
注射模设计
分流道是介于主流 道和浇口之间的一 段流道
使浇注系统的截面变化 和熔体流动转向的过渡 通道
Chapter 4-3 浇注系统的设计
NO10
第四章
注射模设计
Chapter 4-3 浇注系统的设计
NO42
第四章
注射模设计
梯形截面、U形截面分流道,加工容易,且热量散失和流动阻力 U 也不大,究竟采用哪一种横截面的分流道,既要考虑各种塑料 注射成型的需要,又要考虑制造难易程度:
A: 从传热面积考虑,热固性塑料注射模宜用矩形截面分流道(便于从模具上吸 热),而热塑性塑料宜用圆形截面分流道(防止热量散失) B: 从压力损失考虑,圆形截面分流道最好 C: 从加工方便考虑,宜采用U形、梯形、矩形截面分流道 U
Chapter 4-3 浇注系统的设计
NO24
第四章
注射模设计
(1)主流道的设计 按主流道的轴线与分型面的关系,浇注系统有直浇注系统和横浇 注系统.在卧式和立式注射机中,主流道轴线垂直于分型面,属于 直浇注系统,如图
第六章 分型面的选择与浇注系统设计(江南大学)

(三)、浇口的设计:
位置不合理导致的缺陷:
1.注不满:
(三)、浇口的设计:
位置不合理导致的缺陷:
2.翘曲:
(三)、浇口的设计:
位置不合理导致的缺陷:
3.熔合纹(熔接线):
(三)、浇口的设计:
位置不合理导致的缺陷:
3.熔合纹(熔接线):
(三)、浇口的设计:
位置不合理导致的缺陷:
3.熔合纹(熔接线):
应用CAE优化分析,是解决充填平衡最有效的方法。
注意:冷料井与拉料杆配合使用
拉料杆形状:Z形、倒锥形、球形、蘑菇 形 P124
(一)、主流道与浇口套的设计: 2.浇口套的设计(与注塑机喷嘴的关系):
注意:冷料井与拉料杆配合使用
拉料杆形状:Z形、倒锥形、球形、蘑菇形 P124
(一)、主流道与浇口套的设计: 2.浇口套的设计(与注塑机喷嘴的关系):
详细见P71-73
一、
分型面的选择
一、
分型面的选择
一、
分型面的选择
一、
分型面的选择
一、
分型面的选择
常用分型面的型式:
二、浇注系统的设计:
二、浇注系统的设计: 熔体在浇道内流动:
(一)、主流道与浇口套的设计:
1.主流道设计:
(一)、主流道与浇口套的设计:
1.主流道设计:
(一)、主流道与浇口套的设计: 2.浇口套的设计(与注塑机喷嘴的关系):
另外: 单腔多浇口的平衡 原因:
(四)、浇注系统的平衡进料:
(四)、浇注系统的平衡进料:
1.平衡式浇注系统: 定义:使模具各型腔的流道长度和截面形状相同。 典型形式布置:
(四)、浇注系统的平衡进料:
1.平衡式浇注系统:
浇注系统设计

基本组元的作用:
④ 横浇道 向内浇道分配洁净的金属液; 储留最初浇入的低温金属液和渣液; 使金属液平稳流动,阻渣浮气。
浇注系统设计
基本组元的作用:
⑤ 内浇道 控制金属液的充型速度和方向; 合理分配金属液; 调解铸件各部位的温度和凝固顺序。
浇注系统设计
3.1.2 浇注系统中液体金属的流动状态
各类灰口和球墨铸铁件
浇注系统设计
3.2.1 按组元的断面比例关系分类
④ 封闭开放式浇注系统 F阻 = F横
浇注系统的阻流段为横浇道或横浇道上设置的阻流装置。
形式:
F杯孔 ≥ F直 > F横 < F内
在这种浇注系统中,浇注时金属液是先封闭后开放。
浇注系统设计
浇注系统设计
3.2.1 按组元的断面比例关系分类
⑤ 结构和分布要便于造型和清理,节约金属。
浇注系统设计
2.5.2 机械加工余量
机械加工余量按GB/T6414-1999 确定。
国家标准GB/T6414-1999 中规定,机械加工余量代号为RMA, 等级由精到粗分为A、B、C、D、E、F、G、H、J 、K 10个 等级。
浇注系统设计
浇注系统设计
浇注系统设计
形式:
F杯孔 ≤ F直 < F横 < F内
在这种浇注系统中,浇注时金属液一般是非充满状态。
浇注系统设计
3.2.1 按组元的断面比例关系分类
② 开放式浇注系统(非充满式)
特点: 阻渣效果差,易卷气;
充型平稳,金属氧化轻。
适用: 有色件、球铁件
漏包浇注的铸钢件
浇注系统设计
3.2.1 按组元的断面比例关系分类
③ 半封闭式浇注系统 F阻 = F内
浇注系统的设计

浇注系统设计1 浇注系统的设计要求浇注系统是指在模具中,从注射机喷嘴进人模具处开始到型腔为止的塑料熔体流动通道,分为普通浇注系统和无流道浇注系统。
浇注系统的作用是使塑料熔体平稳有序地填充到型腔中,并在塑料填充和凝固的过程中,把注射压力充分传递到型腔的各个部位,以获得组织致密、外形清晰的塑件。
普通浇注系统(下称浇注系统)一般由主流道、分流道、浇口、冷料井4 部分组成。
单型腔模具有时可省去分流道和冷料井,只有圆锥形的主流道通过浇口和塑件相连。
浇注系统的设计非常重要,设计合理与否对塑件的内在性能质量、尺寸精度、外观质量以及模具结构、成型效率、塑料利用率等都有较大影响。
浇注系统进行设计时,一般应遵循以下基本原则。
( l )适应塑料的成型工艺性能。
了解塑料的成型工艺性能,如塑料熔体的流动特性,温度、剪切速度对猫度的影响,型腔内的压力周期等,使浇注系统适应于所用塑料的成型特性要求,以保证塑件质量。
( 2 )结合型腔布局考虑。
尽可能保证在同一时间内塑料熔体充满各型腔,为此,尽最采用平衡式布局.以便设置平衡式分流道;型腔布t 和浇口开设部位力求沿模具轴线对称,避免在模具的单面开设浇口,以防止模具承受偏载而产生溢料现象;使型腔及浇注系统在分型面上投影的中心与注射机锁模机构的锁模力作用中心相重合.以使锁模可靠、锁模机构受力均匀;型腔排列尽可能紧凑,以减小模具外形尺寸。
( 3 )热量及压力损失要小。
应该尽量缩短浇注系统的流程,特别是对于较大的模具型腔,增加断面尺寸,尽量减少弯折,控制表面粗糙度。
( 4 )有利于型腔中气体的排出。
浇注系统应能顺利地引导塑料熔体充满型腔的各个角落,使型腔及浇注系统中的气体有序排出,保证在充填过程中不产生紊流,避免因气体积存而引起凹陷、气泡、烧焦等塑件成型缺陷。
( 5 )防止型芯变形和嵌件位移。
应尽量避免塑料熔体直接冲击细小型芯和嵌件,以防止熔体冲击力使细小型芯变形,使嵌件位移。
( 6 )保证塑件外观质量。
模具设计与制造:浇注系统设计

四、浇注系统设计
➢ 分流道的长度
分流道长度要尽可能短,弯折要少,以便减少压力损失和热量 损失,节约塑料的原材料和能耗。
经验取值:L1=6~10mm,L2=3~6mm,L3=6~10mm,L尺
寸根据型腔多少和型腔大小而定。
四、浇注系统设计
分流道的表面粗糙度
为保证与分流道接触的外层塑料熔体迅速冷却,形成 绝热层,只有内部熔体平稳流动,分流道的表面粗糙度
优点:在型腔较多时,可缩短分流道的总长度。 缺点:各型腔不是同时充满,因而各型腔塑件的尺寸和性能不一样。
为实现各型腔同时充满的要求,必须将浇口开成不同的尺寸, 须经过多次修模,才有可能达到同时充型的目的。
四、浇注系统设计
分流道设计注意事项
➢分流道开设在分型面上,可单独开在动模板或定模板 上,如图(a);也可同时开在动、定模板上,如图(b)
四、浇注系统设计
分流道尺寸设计 ➢ 分流道的直径
D≥产品最厚壁厚+1.5mm B=1.25D
四、浇注系统设计
分流道直径应适合产品的重量或投影面积。
流道直径(mm) 4 6 8 10 12
产品重量(g) 95 375
375以上 大型
流道直径(mm)
4 6 8 10 12
投影面积(cm2)
10以下 200 500 1200 大型
四、浇注系统设计
浇口套
➢ 原因:主流道与高温熔体接触,和喷嘴反复碰撞, 易损坏。
➢ 好处:可拆卸,更换容易。标准件 ➢ 结构形式:
最常用a)结构 材料:T8、T10,淬火54~58HRC。
四、浇注系统设计
定位圈
保证模具中心与注射机注射压力中心重合。 定位圈与浇口套的关系
四、浇注系统设计
分型面浇注系统设计知识分享
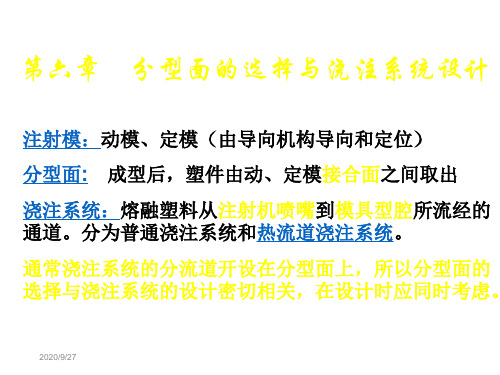
2020/9/27
5、分型面选择应有利于排气
应尽可能使分型面与料流末端重合, 这样才有利于排气。图 (b)。
2020/9/27
2020/9/27
分型面的位置要有利于模具的排气
Байду номын сангаас
6、分型面选择应便于模具零件的加工
图(a)采用一垂直于开模运动方向的平面作为分 型面,凸模零件加工不便,而改用倾斜分型面[图 (b)],则使凸模便于加工。
2020/9/27
2020/9/27
6.1 分型面及其选择
分型面:模具上用以取出塑件和浇注系统凝料的可分离的接触表 面。 一副模具根据需要可能有一个或两个以上的分型面。分型面可能 垂直、平行、倾斜于合模方向。 主分型面:脱模时取出塑件的分型面。 辅助分型面:其他的分型面。
2020/9/27
2. 按注塑机的额定锁模力确定型腔数
第六章 分型面的选择与浇注系统设计
注射模:动模、定模(由导向机构导向和定位) 分型面: 成型后,塑件由动、定模接合面之间取出 浇注系统:熔融塑料从注射机喷嘴到模具型腔所流经的 通道。分为普通浇注系统和热流道浇注系统。 通常浇注系统的分流道开设在分型面上,所以分型面的 选择与浇注系统的设计密切相关,在设计时应同时考虑。
根据注射机的额定锁模力大于将模具分型面胀开的力,得
F≥p(nAn+Aj)
型腔数 n F pAj pAn
式中 F——注射机的额定锁模力,N; p——塑料熔体对型腔的平均压力,MPa;
注射压力的80%,
An——单个塑件的在分型面上的投影面积,mm2; 2020A/9/2j7——浇注系统在分型面上的投影面积,mm2。
浇注系统的设计原则

浇注系统的设计原则
塑料制品质量的好坏,与浇注系统的设计关系甚大,因此,需要重视浇注系统的设计,一般说来,浇注系统的设计必须注意以下几个原则。
(1)必须保证熔料充模过程快而不紊乱,并创造良好的排气条件。
(2)满足所用塑料的成型特性,根据各种塑料的不同成型特性来设计浇注系统。
(3)为使熔体流动阻力减小,应尽量避免熔料正面冲击小直径型芯和脆弱的金属嵌件。
(4)一模多腔时,应使各模腔的容积不致相差太多,否则难以保证制品质量。
(5)要考虑去除、修整进料口是否方便,同时要不影响制品的外表美观。
(6)根据制品的大小、形状、壁厚、技术要求等因素,综合所选分型面,同时考虑浇注系统的形式、进料口数量等。
(7)选择进料口的位置与形状时,应结合塑件的形状和技术要求进行确定。
(8)在大量生产时,要在保证质畺的前提下尽量缩短流程,缩短成型周期。
(9)喷嘴端部的冷料不能进入型腔,在浇注系统中应考虑有储存此冷料的位置。
注塑模具设计手册 345【精选】

Company LOGO
• 3) 扇形浇口
高等学校应用型特色w规ww.c划omp教any材.com
Company LOGO
4) 平缝浇口 5) 环形浇口 6) 盘形浇口
高等学校应用型特色w规ww.c划omp教any材.com
Company LOGO
轮廓处。
高等学校应用型特色w规ww.c划omp教any材.com
Company LOGO
6.1.2 浇注系统的组成及其设计原则 • 1. 浇注系统的组成
高等学校应用型特色w规ww.c划omp教any材.com
Company LOGO
2. 浇注系统设计原则
高等学校应用型特色w规ww.c划omp教any材.com
此种说法是否正确?为什么? • 3. 浇口可分为直接浇口和侧浇口两种。此种说法是
否正确?为什么?
高等学校应用型特色w规ww.c划omp教any材.com
7) 轮辐浇口 8) 爪形浇口
高等学校应用型特色w规ww.c划omp教any材.com
Company LOGO
9) 点浇口 10) 潜伏浇口 11) 护耳浇口(又称分接式浇口、调整片式浇口)
高等学校应用型特色w规ww.c划omp教any材.com
Company LOGO
2. 浇口位置的选择
高等学校应用型特色w规ww.c划omp教any材.com
Company LOGO
6.2 浇注系统的平衡
6.2.1 相同塑件多型腔模具的浇口平衡 6.2.2 不同塑件多型腔模具的浇口平衡
高等学校应用型特色w规ww.c划omp教any材.com
Company LOGO
浇注系统设计方案

流道设计的优化与改进
减少流道阻力
采用大截面、短流程的流道
防止金属液氧化
采用密封式或保护气氛浇注系 统
提高充型能力
采用多浇口、分流道设计
降低能耗
采用热平衡设计,减少热量损 失
04 模具设计
模具材料的选用
01
02
03
耐热性
选择耐热性好的材料,如 钢材、铝合金等,以确保 模具在高温下件结构、生产批量、合金种类、浇注条件
适用场合
直浇道适用于中小型铸件的大批量生产;横浇道适用于大型铸件的 单件、小批量生产;内浇道适用于各种铸件
流道尺寸与形状的确定
流道截面积
满足金属液的流量要求,保证充 型能力
流道长度与宽度
根据铸件大小、浇注温度和速度确 定
流道高度
根据金属液的静压力头和浮力确定
调整工艺参数
调整浇注温度、注射压力和注射速度等工艺 参数,提高浇注质量和效率。
改进模具结构
优化模具冷却、排气和顶出机构,提高模具 使用寿命。
采用先进的浇注技术
如应用热流道技术、顺序阀控制等,提高生 产效率和浇注质量。
浇注系统方案的经济性分析
模具成本
生产成本
评估不同浇注系统方案对模具材料、加工 和装配成本的影响。
排溢系统设计
设计有效的排溢系统,以 排除模具内的气体和溢出 的金属液,防止产品产生 气孔和浇不足等缺陷。
模具冷却系统的设计
冷却水道设计
合理布置冷却水道,以提高模具的冷 却效果,减少冷却时间,提高生产效 率。
冷却介质选择
冷却水道密封
确保冷却水道的密封性,防止冷却液 泄漏,以保证生产安全和产品质量。
根据模具材料和使用条件,选择合适 的冷却介质,如水、油等。
注塑模具结构及设计(浇注系统)

分流道与浇口间尽量不采 用逐渐变窄的形式,会产 生相对大的压力损失
牛角浇口通常设计成如上图所示的形状, 一般都加“火山口”。
牛角(香蕉)浇口
动模潜伏浇口
潜伏浇口的另外一种形状
定模潜伏浇口浇口
动模顶杆潜伏浇口
对于壁薄制品,为了加大普通潜伏浇口的进料口面积, 减小压力损失,可将其加宽,变为矩形截面潜伏浇口
6,浇口位置尽量开在不影响塑件外观的部位,如塑件的边缘,底部,内侧等,并 尽可能便于模具加工。
7,流动比的校核。对于大型塑件,当壁厚相对较小而流动距离过长时,不但内 应力增加,还会因料温降低而造成填充不足,这时须采用增加壁厚或增加浇口 数量及改变浇口位置等措施缩短最大流动距离。最大流动距离由流动通道的最 大流动长度和其厚度之比所确定。流动比随塑料熔体的性质,温度,注射压力, 浇口的种类,形式和开设位置变化。
侧浇口实例
侧浇口剖视
定模渐变 动模渐变
定模平直
侧浇口也可开在制品的底边
不常用
动模平直
侧浇口俯视 前端不变
扇形浇口
前端变小
薄片式浇口
前端变大
中心浇口 中心浇口是直接从中心环形或数股进料,与直接浇口有类同优点。 依形式不同分为环形浇口,轮辐浇口,爪形浇口等
1.适用于筒形件的进料,可避免偏芯. 2.去浇口较麻烦.
●冷料井:也称作冷料穴,目的在于储存充填初始阶段较冷的塑料前 锋冷料,防止冷料直接进入模穴影响充填品质或堵塞浇口。冷料井通常 设置在主流道末端,当分流道长度较长时,在末端也应开设冷料井。
主流道末端的冷料井其直径稍大于主流道大端直径,以利于冷料的流 入,它的底部常设计成Z钩形,球形,锥型,圆环形等,使冷料井兼 有在开模时,与拉料杆一起将主流道从定模中拉出的作用。
浇注系统设计(二)
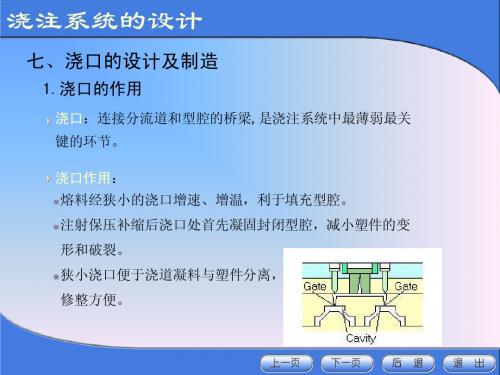
圓 盘 浇 口
浇注系统的设计
七、浇口的设计及制造
3.浇口的计算
薄 膜 浇 口
浇注系统的设计
七、浇口的设计及制造
3.浇口的计算
环状浇口
浇注系统的设计
七、浇口的设计及制造
4.浇口的设计原则
一个好的浇口可以使塑料快速﹑均匀及更好的单方向性流 动﹐并且有着合适的浇口凝固时间。 ⑴防止浇口处产生喷射现象而在 充填过程中产生波纹状痕迹。 防止办法:加大浇口尺寸或采用 冲击型浇口。
浇注系统的设计
七、浇口的设计及制造
3.浇口的计算
护 耳 式 浇 口
浇注系统的设计
七、浇口的设计及制造
3.浇口的计算
侧 浇 口
浇注系统的设计
七、浇口的设计及制造
3.浇口的计算
重 叠 浇 口
浇注系统的设计
七、浇口的设计及制造
3.浇口的计算
扇 形 浇 口
浇注系统的设计
七、浇口的设计及制造
3.浇口的计算
1.浇口的作用
浇口的位置、数量、形状、尺寸等是否适宜直接影响到产品外 观、尺寸精度、物理性能和成型效率。
浇口过小:易造成充填不足(短射)、收缩凹陷、熔接痕等外观 浇口过小
上的缺陷,且成型收缩会增大。
浇口过大:浇口周围产生过剩的残余应力,导致产品变形或破
裂,且浇口的去除加工困难等。
浇注系统的设计
七、浇口的设计及制造
浇注系统的设计
七、浇口的设计及制造
2.浇口的类型及特点பைடு நூலகம்
轮幅浇口 轮幅浇口又称为四点浇口或是十字浇口。 此种浇口适用于管状塑料制品,且浇口 容易去除和节省材料。 缺点:可能会产生熔接痕﹐而且不可能 制造出完善的真圆。 典型的浇口厚度 典型的浇口厚度是0.8至4.8mm﹐宽度为 1.6至6.4mm。
一模四腔透盖注射模具课程设计说明书
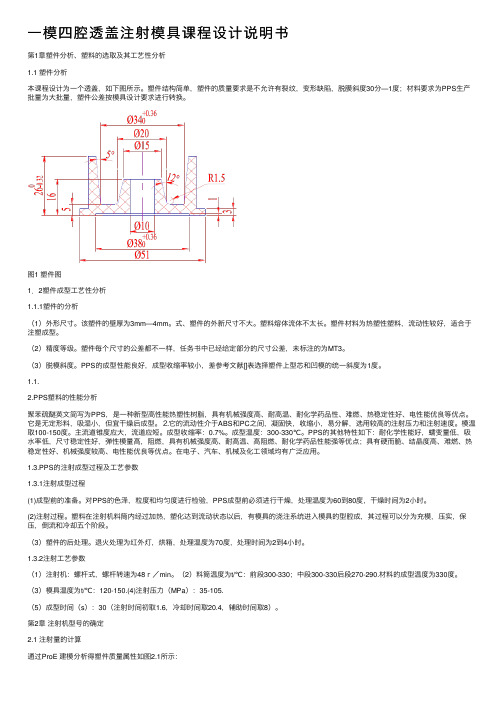
⼀模四腔透盖注射模具课程设计说明书第1章塑件分析、塑料的选取及其⼯艺性分析1.1 塑件分析本课程设计为⼀个透盖,如下图所⽰。
塑件结构简单,塑件的质量要求是不允许有裂纹,变形缺陷,脱膜斜度30分—1度;材料要求为PPS⽣产批量为⼤批量,塑件公差按模具设计要求进⾏转换。
图1 塑件图1.2塑件成型⼯艺性分析1.1.1塑件的分析(1)外形尺⼨。
该塑件的壁厚为3mm—4mm。
式、塑件的外新尺⼨不⼤。
塑料熔体流体不太长。
塑件材料为热塑性塑料,流动性较好,适合于注塑成型。
(2)精度等级。
塑件每个尺⼨的公差都不⼀样,任务书中已经给定部分的尺⼨公差,未标注的为MT3。
(3)脱模斜度。
PPS的成型性能良好,成型收缩率较⼩,差参考⽂献[]表选择塑件上型芯和凹模的统⼀斜度为1度。
1.1.2.PPS塑料的性能分析聚苯硫醚英⽂简写为PPS,是⼀种新型⾼性能热塑性树脂,具有机械强度⾼、耐⾼温、耐化学药品性、难燃、热稳定性好、电性能优良等优点。
它是⽆定形料,吸湿⼩,但宜⼲燥后成型。
⒉它的流动性介于ABS和PC之间,凝固快,收缩⼩,易分解,选⽤较⾼的注射压⼒和注射速度。
模温取100-150度。
主流道锥度应⼤,流道应短。
成型收缩率:0.7%。
成型温度:300-330℃。
PPS的其他特性如下:耐化学性能好,蠕变量低,吸⽔率低,尺⼨稳定性好,弹性模量⾼,阻燃,具有机械强度⾼、耐⾼温、⾼阻燃、耐化学药品性能强等优点;具有硬⽽脆、结晶度⾼、难燃、热稳定性好、机械强度较⾼、电性能优良等优点。
在电⼦、汽车、机械及化⼯领域均有⼴泛应⽤。
1.3.PPS的注射成型过程及⼯艺参数1.3.1注射成型过程(1)成型前的准备。
对PPS的⾊泽,粒度和均匀度进⾏检验,PPS成型前必须进⾏⼲燥,处理温度为60到80度,⼲燥时间为2⼩时。
(2)注射过程。
塑料在注射机料筒内经过加热,塑化达到流动状态以后,有模具的浇注系统进⼊模具的型腔成,其过程可以分为充模,压实,保压,倒流和冷却五个阶段。
浇注系统的设计原则
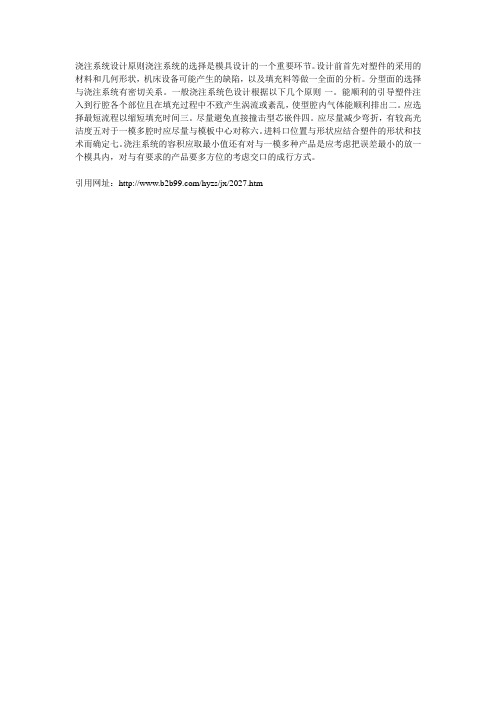
浇注系统设计原则浇注系统的选择是模具设计的一个重要环节。
设计前首先对塑件的采用的材料和几何形状,机床设备可能产生的缺陷,以及填充料等做一全面的分析。
分型面的选择与浇注系统有密切关系。
一般浇注系统色设计根据以下几个原则-一。
能顺利的引导塑件注入到行腔各个部位且在填充过程中不致产生涡流或紊乱,使型腔内气体能顺利排出二。
应选择最短流程以缩短填充时间三。
尽量避免直接撞击型芯嵌件四。
应尽量减少弯折,有较高光洁度五对于一模多腔时应尽量与模板中心对称六。
进料口位置与形状应结合塑件的形状和技术而确定七。
浇注系统的容积应取最小值还有对与一模多种产品是应考虑把误差最小的放一个模具内,对与有要求的产品要多方位的考虑交口的成行方式。
引用网址:/hyzs/jx/2027.htm。
.浇注系统分型
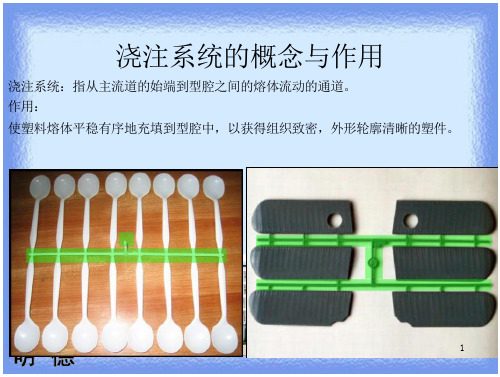
32
⑤点浇口 又称针点浇口或橄榄形浇口,是一种在塑件中央开设浇口时使用的圆形限制性浇 口,由于浇口前后两端存在较大的压力差,能有效地增大塑料熔体的剪切速率并 产生较大的剪切热,从而导致熔体的表观黏度下降,流动性增加,利于充模。常 用于成型各种壳类、盒类的热塑性塑件。
7
主流道尺寸必须恰当。通常对于黏度大的塑料或尺寸较大的塑件,主流道截面尺 寸应设计得大一些;对于黏度小的塑料或尺寸较小的塑件,主流道截面尺寸设计 得小一些。直浇注系统主流道结构及尺寸参数见下图:
8
为便于流道凝料的脱出,内壁粗糙度Ra小于0.4μm,主流道设计成圆锥形,其 锥度α=2°~6°,如果锥度过大,易发生涡流,锥度过小则流道凝料脱出困难
41
4.冷料井设计
冷料井位于主流道正对面 的动模板上,或处于分流 道末端。
作用: 聚集料流前锋的“ 冷料” , 防止“冷料”进入型腔而
影 响塑件质量,开模时又能 将主流道的凝料拉出。
尺寸: 冷料井的直径宜大于主流
道大端直径;长度约为主
流道大端直径。
42
常用冷料井与拉料杆形式:
底部带有推杆的冷料井
38
③尽量避免塑件出现熔合纹
39
④避免在塑件承受弯曲或冲击载荷的部位设置浇口 塑件的浇口附近强度较弱,只能承受一般的拉伸力,而无法承受弯曲和冲击力。 ⑤浇口应开设在不影响型芯稳定性的部位 见右图:
40
⑥浇口应开设在不影响塑件外观的部位 ⑦浇口的设置应避免熔体断裂 当小浇口正对着宽度和厚度很大的模腔时,高速料流通过浇口时会受到很高的剪 切应力,而产生喷射和蛇形流 等熔体断裂现象;若采用如图 (b)所示的搭接浇口, 浇口正 对着型腔壁或型芯的位置,使 高速料流冲击在型腔壁或型芯 上,从而降低熔体流速,改变 流向,使熔体均匀地填充型腔。
- 1、下载文档前请自行甄别文档内容的完整性,平台不提供额外的编辑、内容补充、找答案等附加服务。
- 2、"仅部分预览"的文档,不可在线预览部分如存在完整性等问题,可反馈申请退款(可完整预览的文档不适用该条件!)。
- 3、如文档侵犯您的权益,请联系客服反馈,我们会尽快为您处理(人工客服工作时间:9:00-18:30)。
置(分型面)与 浇注系统的 设计
1
主要内容
1 塑料制件在模具中的位置及分型面设计 2 普通浇注系统设计 3 热流道浇注系统设计
2
一副注射模具主要分成动模和定模两个部分。 动模和定模的接触面称为分型面。 浇注系统:是指熔融塑料从注射机喷嘴射入 到注射模具型腔所流经的通道。 浇注系统分为:普通流道、热流道 普通浇注系统包括主流道、分流道、浇口和 冷料穴等。
21
(3)分型面的选择应保证塑件的精度要求
如图a所示,塑料的双联 齿轮分别在分型面两侧的 动模板和定模板内成型, 由于制造精度和合模精度 的影响,两齿轮的同轴度 将得不到保证;
若按图b选择分型面,塑 件在同一侧型腔内成型, 制造精度得以保证,合模 精度也不受影响,保证了 双联齿轮的同轴度。
22
主流道的设计事项: ⑸ 浇口套与定模板之间的连接力必须足够。 一种用螺钉来固定定位圈,定位圈压紧浇口套的形式,一种 是注塑机固定模板压住定位圈,从而压紧浇口套的形式。
浇口套的结构形式:
浇口套与模板间的配合采用H7/m6的过渡配合,浇口套 与定位圈采用H9/f9配合。
定位圈在模具安装调试时应插入注射机定模板的定位孔 内,用于模具与注射机的安装定位。定位圈外径比注射 机定模板上的定位孔径小0.1-0.2。
10
分型面的形状:
图a平直分型面;图b倾斜分型面;图c阶梯分型面;图d 曲面分型面;图e瓣合分型面,也称垂直分型面。
11
12
平直 分型面
13
阶梯分型面
14
曲面分型面
15
16
斜分型面
17 17
垂直分型面
18 18
1.3.2
分型面的设计原则
由于分型面受到塑件在模具中的成型位置、浇 注系统设计、塑件结构工艺性及尺寸精度、嵌 件的位置、塑件的推出、排气等多种因素的影 响,在选择分型面时应综合分析比较以选出较 为合理的方案。
8
型腔排布形式的选择原则:
应使各型腔都能通过浇注系统从总压力中均等地分得所需的足 够压力,以保证塑料熔体能同时均匀地充填每一个型腔,使各型腔 塑件质量均一稳定。 在生产实践中,有时为了节约和同步生产,往往将成型配套的塑 件设计成多型腔模具。但难免引起一些缺陷,如塑件发生翘曲等。
9
1.3分型面的选择
流道直径(mm) 4 6 8 10 12 产品重量(g) 流道直径(mm) 4 6 8 10 12 投影面积(cm2) 10以下 200 500 1200 大型
95
375 375以上 大型
(2)分流道尺寸设计
流道长度宜短: 长的流道会造成压力损失,不利于 生产性,同時也浪费材料;过短, 产品的残余应力 增大, 并且容易产生毛边。 流道长度可以按如下经验公式计算:
(4)分型面的选择应满足塑件的外观质量要求
在分型面处会不可避免地在塑件上留下溢流飞边的痕迹, 因此分型面最好不要设在塑件光亮平滑的外表面或带圆弧 的转角处,以免对塑件外观质量产生不利的影响。
23
(5)分型面的选择要便于模具的加工制造
通常在模具设计中,选择平直分型面较多。 但为了便于模具的制造,应根据模具的实 际情况选择合理的分型面。
30
浇注系统设计应遵循的基本2)尽量避免或减少产生熔接痕; (3)有利于型腔中气体的排出; (4)防止型芯的变形和嵌件的位移; (5)分流道尽量减少弯折,减少压力损失; (6) 分流道的布局尽量采用平衡式布局,成型 压力的中心尽量在模具和注射机的中心; (7)尽量采用较短的流程充满型腔; (8)流动距离比和流动面积比的校核;
流向杂乱会使工件強度较差,表面的纹路也较不美观。
浇注系统设计原则
2.尽量减小及缩短浇注系统的断面及长度 尽量减少塑料熔体的热量损失与压力损失
减小塑料用量和模具尺寸
3.尽可能做到同步填充 一模多腔情形下,要让进入每一个型腔的熔料能 够同时到达,而且使每个型腔入口的压力相等。
2.2 主流道设计
作用:是连接注射机喷嘴和模具的桥梁,是熔料进入型腔最
31
浇注系统设计原则
1.要能保证塑件的质量(避免常见的充填问题 )
尽量减少停滞现象
停滞现象容易使工件的某些部
分过度保压,某些部分保压不足, 从而使內应力增加许多。
浇注系统设计原则
1.要能保证塑件的质量(避免常见的充填问题 ) 尽量避免出现熔接痕
熔接痕的存在主要会影响外 观,使得产品的表面较差;而出 现熔接痕的地方強度也会较差。
3
1 塑料制件在模具中的位置
1.1 型腔数目的确定
一次注射只能生产一件塑料产品的模具称为单型腔模具。 如果一副模具一次注射能生产两件或两件以上的塑料产品, 则这样的模具称为多型腔模具。
单型腔模具的优点:单型腔模具具有塑料制件的形状和
尺寸一致性好、 成型的工艺条件容易控制 模具结构简单紧凑 模具制造成本低 制造周期短等特点。
D=
D——分流道直徑mm
W——产品质量g
L——流道長度mm
(3)分流道的布置
流道排列的原则 尽可能使熔融塑料从主流道到各浇口的距离相等。 使型腔压力中心尽可能与注射机的中心重合。 流道的布置
不平衡
自然平衡
人工平衡
分 流 道 的 布 局
56
57
58
2.4
51
(2)分流道尺寸设计
B=5-10mm R=0.5B h=1.25R D>=产品最大壁厚+1.5mm
B=5-10mm h=2/3B
(2)分流道尺寸设计
流道的直径过大:浪费材料;冷却时间增长,造成成本 上的浪费。 流道的直径过小:材料的流动阻力大,易造成充填不足,
或者必须增加射出压力才能充填。
流道直径应适合产品的重量或投影面积。
选择分型面时应遵循以下几项基本原则:
19
(1)分型面应选在塑件外形最大轮廓处
塑件在动、定模的方位确定后,其分型面应选在塑件外形的 最大轮廓处,否则塑件会无法从型腔中脱出,这是最基本的 选择原则。
20
(2)分型面的选择应有利于塑件的顺利脱模
由于注射机的顶出装置在动模一侧,所以分型面的选择应尽 可能地使塑件在开模后留在动模一侧。 如图a所示,在分型后,由于塑件收缩包紧在型芯上的原因 而留在定模,这样就必须在定模部分设置推出机构,增加了 模具复杂性;若按图b分型,分型后塑件留在动模,利用注 射机的顶出装置和模具的推出机构即可容易地推出塑件。
主流道、分流道、浇口、冷料穴
28
6.2.1 浇注系统的组成及其设计原则
主流道 分流道 浇口
浇注系统的设计是否适当,直接影响成形品 的外观、物性、尺寸精度和成形周期。
二、浇注系统的作用及设计原则
1、将来自注射机喷嘴的塑料熔体均匀而平稳地输送 到型腔,同时使型腔内的气体能及时顺利排出。 2、在塑料熔体填充及凝固的过程中,将注射压力有 效地传递到型腔的各个部位,以获得形状完整、内 外在质量优良的塑料制件。 浇注系统的设计合理与否对塑件的性能、尺寸、内 外部质量及模具的结构、塑料的利用率等有较大影 响。
44
浇口套的固定形式:
46 46
47
2.2 主流道设计(小结)
主流道:浇注系统中从注射机喷嘴与模具接触处开始到分 流道为止的塑料熔体的流动通道。
主流道设计:圆锥形,锥角α为20-60,小端直径d比注射机 喷嘴直径大0.5~l mm。由于小端的前面是球面,其深度为 3~5 mm,注射机喷嘴的球面在该位置与模具接触并且贴 合,因此要求主流道球面半径比喷嘴球面半径大1~2 mm。 表面粗糙度Ra<0.8µm。浇口套一般采用碳素工具钢 如T8A、T10A等材料,淬火硬度53-57 HRC。
5
1.2型腔的分布
单型腔的模具,塑件在模具中的位置,如图:
6
1.2型腔的分布
多型腔模具型腔的排布形式
平衡式、非平衡式 平衡式包括两个方面:型腔压力平衡、浇注平衡
型腔压力平衡
7
浇注平衡
平衡式布置:主流道到各型腔浇口分流道的长度、截面 形状与尺寸均对应相同,目的:各型腔均匀进料和达到 同时充满型腔。 非平衡式布置:主流道到各型腔浇口的分流道的长度不 相同,这种方式可以缩短分流道的长度,节约塑件的原 材料。为达到同时充满型腔的目的,各浇口的截面尺寸 要制造得不相同。 精度要求高、物理与力学 性能要求均衡稳定的塑料 制件,应尽量选用平衡式 布置的形式。
浇注系统设计原则
1.要能保证塑件的质量(避免常见的充填问题 ) 尽量避免过度保压和保压不足
过度保压
当浇注系统设计不良或操作条件不当,会使
保压不足
熔料在型腔中保压时间过长或是承受压力过
大就是过度保压。 过度保压会使产品密度较大,增加內应力,
甚至出现飞边。
浇注系统设计原则
1.要能保证塑件的质量(避免常见的充填问题 ) 尽量减少流向杂乱
4
多型腔模具的优点: ——在大批量生产的情况下,多型腔模具应 是更为合适的形式,它可以提高生产效率, 降低塑件的整体成本。 型腔数目的确定: ——一种方法是首先确定注射机的型号,再 根据注射机的技术参数和塑件的技术经济 要求,计算出要求选取型腔的数目; ——另一种方法是先根据生产效率的要求和 制件的精度要求确定型腔的数目,然后再 选择注射机或对现有的注射机进行校核。
先经过的部位。
一般都不将主流道直接开在定模板上,而是将其单独设在一 个衬套中,然后将衬套镶入模板内,此衬套称为浇口套。
主流道的设计事项: ⑴主流道进口端与喷嘴头部接触处应做成球面凹坑。
主流道的设计事项: ⑵主流道的锥角取2~4°,对流性差的塑料可增加大 到 6°左右。