轴承加工工艺流程
轴承生产工艺流程

轴承生产工艺流程
轴承生产工艺流程:
原材料——内、外圈加工、钢球或滚子加工、保持架(冲压或实体)加工——轴承装配——轴承成品。
轴承内外圈工艺流程:
棒材——下料——锻造——球化退火——车加工——热处理——磨加工——超精加工——零件终检——防锈入库。
钢球的加工过程:
棒料或线材冷冲(有的棒料冷冲后还需冲环带和退火)——挫削、粗磨、软磨或光球——热处理——硬磨——精磨——精研或研磨——终检分组——防锈、包装——入库〈待合套装配〉。
滚子的加工过程:
棒料车加工或线材冷镦后串环带及软磨——热处理——串软点——粗磨外径——粗磨端面——终磨端面——细磨外径——终磨外径——终检分组——防锈、包装——入库(待合套装配〉。
保持架的加工过程:
铸铜件——车内径、外径、端面、倒角——钻孔(或拉孔、镗孔)——去毛刺——酸洗——终检——防锈、包装——入库〈待合套装配〉。
轴承加工工艺流程

轴承加工工艺流程引言轴承是机械设备中常见的零件之一,用于支撑和定位旋转机械的轴。
轴承的加工工艺流程对于轴承的质量和性能有着重要的影响。
本文将介绍轴承加工的一般工艺流程,包括原料准备、车、磨、热处理和装配等环节。
一、原料准备轴承的原材料一般是钢材,根据需要可以选择不同种类和牌号的钢材。
在轴承加工之前,首先需要对原材料进行准备。
原料准备的主要步骤包括材料验收、材料切割和材料成型。
首先,对原材料进行验收,检查原材料的质量和规格是否符合要求。
然后,将原材料切割成适当的长度,以便后续加工操作。
最后,通过冷锻、热锻等成型工艺,将切割好的原材料进一步成型为轴承的预制件。
二、车削加工车削是轴承加工中常用的一种加工方法,主要用于加工轴承的外圆、内圆和面。
车削加工的流程包括设备调整、工件夹持、刀具选择、车削操作和尺寸检测等环节。
在车削加工之前,需要调整车床等设备,保证其正常运转和加工精度。
然后,将轴承安装在车削设备上,并进行夹持。
接下来,选择合适的刀具,根据轴承的要求进行车削操作。
最后,通过尺寸检测,确保车削加工的尺寸精度和表面质量符合要求。
三、磨削加工磨削是轴承加工中另一种常用的加工方法,主要用于提高轴承的精度和表面质量。
磨削加工的流程包括设备调整、砂轮选择、工件夹持、磨削操作和尺寸检测等环节。
在磨削加工之前,同样需要调整磨削设备,保证其正常运转和加工精度。
然后,选择适当的砂轮,根据轴承的要求进行磨削操作。
在磨削过程中,需要注意控制砂轮的磨损和磨削温度,以避免影响磨削效果。
最后,通过尺寸检测,确保磨削加工的尺寸精度和表面质量达到要求。
四、热处理热处理是轴承加工中一个重要的环节,可以改变轴承的组织结构和性能。
常见的热处理方法包括淬火、回火和渗碳等。
热处理的流程包括预热、热处理和冷却等阶段。
在热处理之前,需要对轴承进行预热,以去除表面的污垢和湿气,提高热处理效果。
然后,将轴承放入热处理炉中,进行淬火、回火或渗碳等热处理操作。
轴承的生产工艺流程

轴承的生产工艺流程
轴承是机械设备中常用的零部件之一,其生产工艺流程一般包括原材料准备、加工制造、热处理、清洗防锈和检测等环节。
首先是原材料准备阶段。
轴承的制造原料主要包括钢材、铜材和塑料材料等。
在生产之前,需要对这些原材料进行筛选和测试,确保其符合相关的标准和要求。
接下来是加工制造阶段。
这个阶段主要是将原材料进行加工和成型。
首先,将钢材进行切割,然后通过冷镦、热镦等工艺将其加工成滚珠或滚道等轴承零部件。
同时,还需要对铜材和塑料材料进行注塑或拉伸工艺,用于制造轴承的保持笼和密封圈等部件。
随后是热处理阶段。
热处理是轴承制造中非常重要的一步,它可以改善轴承的物理性能和机械性能。
通过热处理工艺,将加工好的轴承零部件进行加热和冷却处理,从而使轴承具有更好的硬度、韧性和耐磨性等特性。
在热处理之后,需要对轴承进行清洗和防锈处理。
轴承表面常常会残留一些油污和杂质等物质,因此需要用清洗设备对轴承进行清洗,以确保轴承的表面光洁度。
随后,对轴承进行防锈处理,一般采用防锈油或防锈膜进行涂覆,以防止轴承在存放和运输过程中被氧化。
最后是检测和质保阶段。
生产好的轴承需要经过一系列的检测,以确保其质量符合相关的标准和要求。
常见的检测项目包括尺
寸、外观、轴承座及滚珠的脱落等。
同时,还需要对轴承进行质保,确保其使用寿命和性能稳定性。
综上所述,轴承的生产工艺流程主要包括原材料准备、加工制造、热处理、清洗防锈和检测等环节。
通过严格控制每个环节的质量和工艺要求,可以生产出质量稳定、性能优良的轴承产品。
滚动轴承的机械加工工艺过程卡
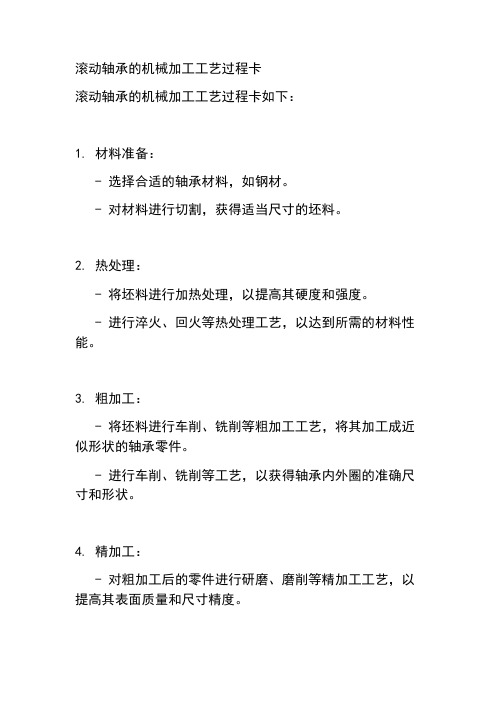
滚动轴承的机械加工工艺过程卡
滚动轴承的机械加工工艺过程卡如下:
1. 材料准备:
- 选择合适的轴承材料,如钢材。
- 对材料进行切割,获得适当尺寸的坯料。
2. 热处理:
- 将坯料进行加热处理,以提高其硬度和强度。
- 进行淬火、回火等热处理工艺,以达到所需的材料性能。
3. 粗加工:
- 将坯料进行车削、铣削等粗加工工艺,将其加工成近似形状的轴承零件。
- 进行车削、铣削等工艺,以获得轴承内外圈的准确尺寸和形状。
4. 精加工:
- 对粗加工后的零件进行研磨、磨削等精加工工艺,以提高其表面质量和尺寸精度。
- 进行研磨、磨削等工艺,以获得轴承内外圈的光滑表
面和准确尺寸。
5. 组装:
- 将精加工后的轴承内外圈与滚动体、保持架等零件进
行组装。
- 使用适当的装配工艺和工具,将各个零件组装在一起,形成完整的轴承。
6. 检测:
- 对组装好的轴承进行检测,以确保其质量和性能符合
要求。
- 进行外观检查、尺寸检测、轴向游隙检测等工艺,以
验证轴承的质量和性能。
7. 表面处理:
- 对检测合格的轴承进行表面处理,如防锈处理、涂层
处理等。
- 进行防锈、涂层等工艺,以提高轴承的耐腐蚀性和使
用寿命。
8. 包装:
- 将经过表面处理的轴承进行包装,以保护其不受损坏。
- 使用适当的包装材料和方法,将轴承包装好,以便运输和存储。
以上是滚动轴承的机械加工工艺过程卡的详细描述,每个步骤都是为了确保轴承的质量和性能,以满足使用要求。
轴承加工工艺流程
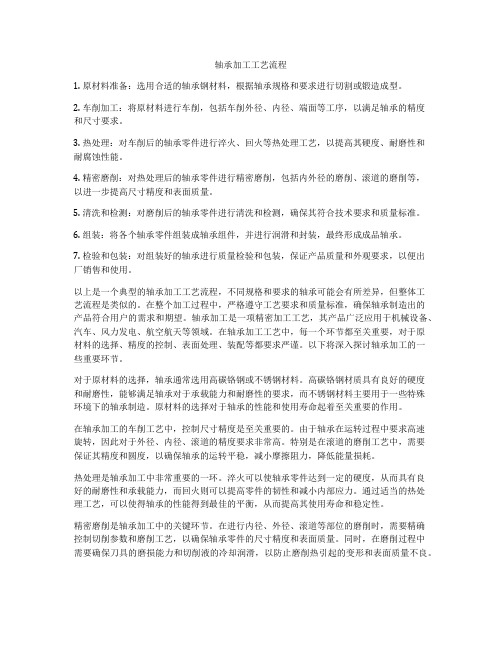
轴承加工工艺流程1. 原材料准备:选用合适的轴承钢材料,根据轴承规格和要求进行切割或锻造成型。
2. 车削加工:将原材料进行车削,包括车削外径、内径、端面等工序,以满足轴承的精度和尺寸要求。
3. 热处理:对车削后的轴承零件进行淬火、回火等热处理工艺,以提高其硬度、耐磨性和耐腐蚀性能。
4. 精密磨削:对热处理后的轴承零件进行精密磨削,包括内外径的磨削、滚道的磨削等,以进一步提高尺寸精度和表面质量。
5. 清洗和检测:对磨削后的轴承零件进行清洗和检测,确保其符合技术要求和质量标准。
6. 组装:将各个轴承零件组装成轴承组件,并进行润滑和封装,最终形成成品轴承。
7. 检验和包装:对组装好的轴承进行质量检验和包装,保证产品质量和外观要求,以便出厂销售和使用。
以上是一个典型的轴承加工工艺流程,不同规格和要求的轴承可能会有所差异,但整体工艺流程是类似的。
在整个加工过程中,严格遵守工艺要求和质量标准,确保轴承制造出的产品符合用户的需求和期望。
轴承加工是一项精密加工工艺,其产品广泛应用于机械设备、汽车、风力发电、航空航天等领域。
在轴承加工工艺中,每一个环节都至关重要,对于原材料的选择、精度的控制、表面处理、装配等都要求严谨。
以下将深入探讨轴承加工的一些重要环节。
对于原材料的选择,轴承通常选用高碳铬钢或不锈钢材料。
高碳铬钢材质具有良好的硬度和耐磨性,能够满足轴承对于承载能力和耐磨性的要求,而不锈钢材料主要用于一些特殊环境下的轴承制造。
原材料的选择对于轴承的性能和使用寿命起着至关重要的作用。
在轴承加工的车削工艺中,控制尺寸精度是至关重要的。
由于轴承在运转过程中要求高速旋转,因此对于外径、内径、滚道的精度要求非常高。
特别是在滚道的磨削工艺中,需要保证其精度和圆度,以确保轴承的运转平稳,减小摩擦阻力,降低能量损耗。
热处理是轴承加工中非常重要的一环。
淬火可以使轴承零件达到一定的硬度,从而具有良好的耐磨性和承载能力,而回火则可以提高零件的韧性和减小内部应力。
轴承制造工艺流程

轴承制造工艺流程轴承是一种旋转运动的零件,广泛应用于各种机械设备中。
轴承的制造工艺流程包括以下几个主要步骤:1.材料准备:轴承的材料一般选用高品质的轴承钢,如GCr15、首先需要从供应商处购买合格的轴承钢材料,并进行材料的检验和鉴定。
2.热处理:轴承钢经过锻造后,需要进行热处理,以提高其硬度和强度。
热处理过程包括均热、淬火和回火等步骤,以使轴承钢具有所需的机械性能。
3.毛坯制备:将经过热处理的轴承钢锻坯进行车削、锯切等操作,将其加工成符合轴承尺寸和几何要求的毛坯。
毛坯可通过铣床、车床和切割等机械设备进行加工。
4.理化分析:对轴承毛坯进行理化分析,以检测其化学成分、机械性能等指标是否符合要求。
常用的检测手段包括金相显微镜、硬度计、冲击试验仪等。
5.精车:对轴承毛坯进行精车,以提高表面质量和尺寸精度。
精车过程可以采用磨床、车床等设备进行,使得轴承表面光滑平整,并控制尺寸在规定的公差范围内。
6.组装:将精车好的轴承外环、内环和滚动体进行组装。
组装过程需要使用适当的工具和设备,以确保各零件的配合间隙、间隔和位置。
7.试验和检测:组装后的轴承进行试验和检测,以验证其性能和质量。
常见的检测项目包括径向游隙、轴向游隙、旋转精度、噪音和振动等。
8.表面处理:对轴承外环和内环表面进行处理,以提高其耐磨、耐腐蚀和润滑性能。
表面处理方式包括电镀、浸油、热处理等。
9.包装和出厂:对合格的轴承进行包装,以便于运输和流通。
包装方式通常包括盒装、木箱装等。
经过包装后,轴承即可出厂销售。
轴承制造工艺流程的每个步骤都需要特定的设备和工艺技术支持,其中精车、组装和检测是关键步骤,直接影响轴承的质量和性能。
进一步提高轴承制造工艺水平,优化流程,提高产品质量,是轴承制造行业面临的挑战和任务。
轴承工艺基本知识

轴承工艺基本知识一.轴承加工过程:锻件→锻造→退火→车加工车内径、外基面→车内外径、基面→软磨平面→软管料磨内外径→细车内径→倒角→车沟→提交车外内径、非基面→车外径、基面→软磨平→软磨外径→倒角→车沟→车牙口→车止动槽→提交→磨加工磨平面→粗、细磨外径→磨外沟→精研外沟→磨坡→修磨外径→清洗磨内平面→磨内外径→磨内沟→磨内径→精研内沟→清洗→装配:装前清洗、退磁、印字→合套(擦套)→压力铆合→成品清洗→压盖→包装二.轴承磨加工:磨加工第一道工序是平面工序,它是基础工序,直接影响下工序的加工质量,精度要求有:平面的平行度、平凸面度及平面的平面度。
这三项是平面加工的主要精度要求,还有磨削的光度及外观质量。
对不同精度等级的产品,精度要求不同,主要有P0;P6;P5及出国产品,出国产品主要是外观要求比较严格。
1.外套工序:1). 磨外径工序:是基础工序,主要精度要求有:尺寸、园度(椭圆、三角、波纹度)、垂直差、锥度、光洁度、表面质量。
对不同等级的产品要求不一样,一般精度要求每级要差1~3μm。
该工序是外沟的加工基准,园度及尺寸是直接影响外沟园度及尺寸的主要因素,垂直差和锥度影响轴承使用过程中的装配和性能。
2). 磨外沟工序:是加工轴承主要工作表面的工序,主要精度要求有:尺寸、园度(椭圆、三角、波纹度)、烧伤、沟曲率R、沟位置、沟侧摆、光洁度、表面质量等。
对不同等级的产品要求不一样,该工序的尺寸要求较松。
由于外沟从1990年以后均采用浮动圆弧支点,故可以改变部分外径园度对外沟园度的影响。
因此外径园度要求一般控制在外沟园度要求的基础上,约小1~2。
实际工作中外沟园度基本保证在外径园度要求上下约1μm左右。
平面的平行度等三项精度影响外沟的沟侧摆。
3). 外沟精研工序:其精度要求与磨外沟工序相同,波纹度和光洁度的要求较高, Ra为0.32,在加工P5(Z1、Z2)产品时,要采用较好的精研油石,粒度要细一些。
一般粗研油石为W14的,精研油石为W3.5混合磨料的。
轴承的工艺流程

轴承的工艺流程轴承是一种常用的机械元件,用于支撑旋转轴的运动。
轴承制造工艺流程包括原材料准备、零件加工、装配和淬火等步骤。
下面简要介绍一下轴承的工艺流程。
首先是原材料的准备。
轴承的主要原材料是钢材,通常使用高碳铬钢或不锈钢制造。
原材料需要经过检验,确保质量符合要求。
然后将原材料切割成适当的尺寸,以备后续加工。
第二步是零件的加工。
首先是球体的加工,将切割好的原材料在机床上进行数控加工,使其成为规定尺寸和形状的球体。
然后对轴承套圈和外圈进行车削、铣削等加工工序,使其能与球体配合运动。
接下来对其他零件如内圈、挡圈等进行相应的加工工艺,以产生与球体和套圈外圈的正确配合关系。
第三步是装配。
在装配过程中,先将内圈和外圈与球体组合一起,然后通过润滑剂和密封圈等配件进行加工,形成完整的轴承。
在装配过程中需要严格控制套圈和球体之间的间隙,以确保轴承的正常运转。
最后是淬火。
淬火是为了提高轴承的硬度和耐磨性能。
在淬火过程中,将轴承加热到适当温度,然后迅速冷却,使其在金相组织上形成马氏体结构,提高硬度。
接下来进行回火处理,以减轻淬火产生的内应力,提高韧性和抗脆性,使轴承具有较好的综合性能。
整个工艺流程中,需要密切关注零件加工精度和装配过程中的质量控制。
只有在确保零件尺寸和形状精度的前提下,才能保证轴承正常运转和使用寿命。
此外,还需要保证装配过程中的清洁环境,避免灰尘、污染等对轴承的影响。
综上所述,轴承工艺流程包括原材料准备、零件加工、装配和淬火等步骤。
通过严格控制每个环节的工艺要求和质量控制,可以生产出高质量的轴承产品。
轴承的质量对机械设备的运行和寿命有着重要的影响,因此轴承制造工艺流程的合理设计和实施非常关键。
轴承组装加工工艺流程
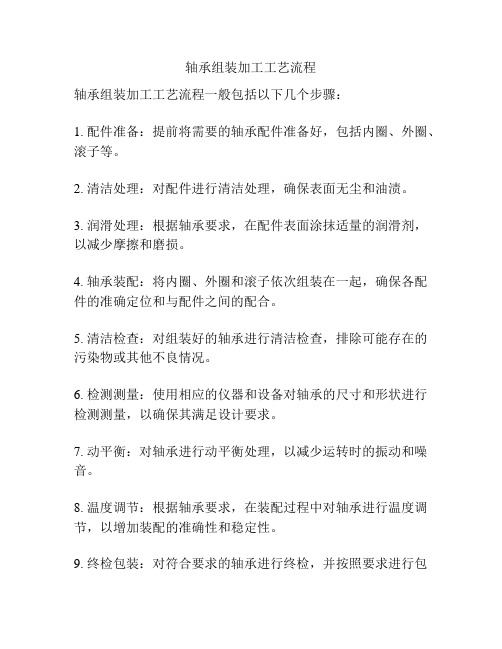
轴承组装加工工艺流程
轴承组装加工工艺流程一般包括以下几个步骤:
1. 配件准备:提前将需要的轴承配件准备好,包括内圈、外圈、滚子等。
2. 清洁处理:对配件进行清洁处理,确保表面无尘和油渍。
3. 润滑处理:根据轴承要求,在配件表面涂抹适量的润滑剂,以减少摩擦和磨损。
4. 轴承装配:将内圈、外圈和滚子依次组装在一起,确保各配件的准确定位和与配件之间的配合。
5. 清洁检查:对组装好的轴承进行清洁检查,排除可能存在的污染物或其他不良情况。
6. 检测测量:使用相应的仪器和设备对轴承的尺寸和形状进行检测测量,以确保其满足设计要求。
7. 动平衡:对轴承进行动平衡处理,以减少运转时的振动和噪音。
8. 温度调节:根据轴承要求,在装配过程中对轴承进行温度调节,以增加装配的准确性和稳定性。
9. 终检包装:对符合要求的轴承进行终检,并按照要求进行包
装,确保轴承在运输过程中不受损坏。
以上是一般的轴承组装加工工艺流程,具体的步骤和要求可能会因不同轴承类型和生产流程而有所差异。
深沟轴承是怎样的工艺
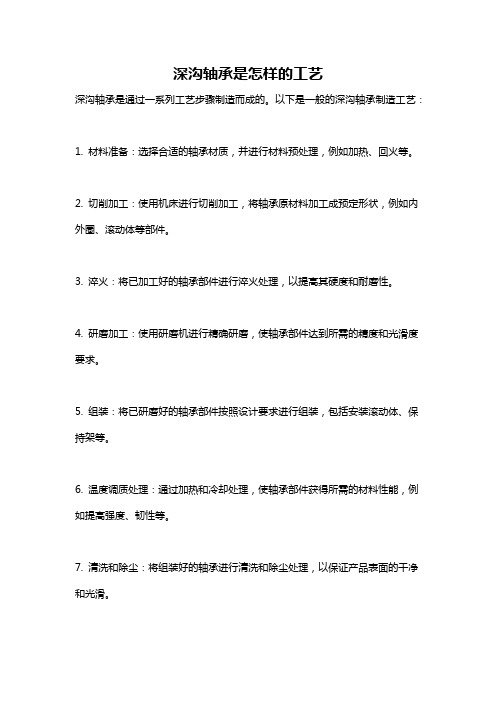
深沟轴承是怎样的工艺
深沟轴承是通过一系列工艺步骤制造而成的。
以下是一般的深沟轴承制造工艺:
1. 材料准备:选择合适的轴承材质,并进行材料预处理,例如加热、回火等。
2. 切削加工:使用机床进行切削加工,将轴承原材料加工成预定形状,例如内外圈、滚动体等部件。
3. 淬火:将已加工好的轴承部件进行淬火处理,以提高其硬度和耐磨性。
4. 研磨加工:使用研磨机进行精确研磨,使轴承部件达到所需的精度和光滑度要求。
5. 组装:将已研磨好的轴承部件按照设计要求进行组装,包括安装滚动体、保持架等。
6. 温度调质处理:通过加热和冷却处理,使轴承部件获得所需的材料性能,例如提高强度、韧性等。
7. 清洗和除尘:将组装好的轴承进行清洗和除尘处理,以保证产品表面的干净和光滑。
8. 检测和检验:对轴承进行各项检测和检验,例如尺寸测量、运转试验等,以确保产品质量。
9. 包装和出厂:对轴承进行包装,包括使用盒装或者盘装方式,并进行标志和贴标签,然后出厂销售。
以上是一般的深沟轴承制造工艺,具体的工艺流程可能会因轴承类型和制造厂商而有所差异。
轴承工艺基本知识

轴承工艺基本知识一.轴承加工过程:锻件→锻造→退火→车加工车内径、外基面→车内外径、基面→软磨平面→软管料磨内外径→细车内径→倒角→车沟→提交车外内径、非基面→车外径、基面→软磨平→软磨外径→倒角→车沟→车牙口→车止动槽→提交→磨加工磨平面→粗、细磨外径→磨外沟→精研外沟→磨坡→修磨外径→清洗磨内平面→磨内外径→磨内沟→磨内径→精研内沟→清洗→装配:装前清洗、退磁、印字→合套(擦套)→压力铆合→成品清洗→压盖→包装二.轴承磨加工:磨加工第一道工序是平面工序,它是基础工序,直接影响下工序的加工质量,精度要求有:平面的平行度、平凸面度及平面的平面度。
这三项是平面加工的主要精度要求,还有磨削的光度及外观质量。
对不同精度等级的产品,精度要求不同,主要有P0;P6;P5及出国产品,出国产品主要是外观要求比较严格。
1.外套工序:1). 磨外径工序:是基础工序,主要精度要求有:尺寸、园度(椭圆、三角、波纹度)、垂直差、锥度、光洁度、表面质量。
对不同等级的产品要求不一样,一般精度要求每级要差1~3μm。
该工序是外沟的加工基准,园度及尺寸是直接影响外沟园度及尺寸的主要因素,垂直差和锥度影响轴承使用过程中的装配和性能。
2). 磨外沟工序:是加工轴承主要工作表面的工序,主要精度要求有:尺寸、园度(椭圆、三角、波纹度)、烧伤、沟曲率R、沟位置、沟侧摆、光洁度、表面质量等。
对不同等级的产品要求不一样,该工序的尺寸要求较松。
由于外沟从1990年以后均采用浮动圆弧支点,故可以改变部分外径园度对外沟园度的影响。
因此外径园度要求一般控制在外沟园度要求的基础上,约小1~2。
实际工作中外沟园度基本保证在外径园度要求上下约1μm左右。
平面的平行度等三项精度影响外沟的沟侧摆。
3). 外沟精研工序:其精度要求与磨外沟工序相同,波纹度和光洁度的要求较高,Ra为,在加工P5(Z1、Z2)产品时,要采用较好的精研油石,粒度要细一些。
一般粗研油石为W14的,精研油石为混合磨料的。
轴承的生产工艺

轴承的生产工艺轴承是一种常见的机械零件,具有在旋转轴上支撑和限制相对运动的功能。
在轴承的生产过程中,需要经历以下几个主要的工艺步骤:材料准备、锻造、车削、磨削、组装和检测。
首先是材料准备阶段。
轴承的主要材料是轴承钢,其主要成分是碳、铬、锰、硅等。
在生产过程中,需要选择合适的轴承钢材料,并进行材料的检测和质量控制。
接下来是锻造工艺。
锻造是将熔融的轴承钢倒入模具中进行成型的过程。
通过锻造,能够使轴承钢的晶粒结构变细,并提高其力学性能和疲劳寿命。
然后是车削工艺。
车削是将已经锻造成型的轴承零件进行加工,使其达到设计要求。
车削过程中,需要使用车床对轴承进行精确的外径、内径和宽度加工,以保证轴承的尺寸精度。
在车削之后,接下来是磨削工艺。
磨削是对已经车削好的轴承零件进行进一步的表面处理和尺寸修整。
通过磨削,能够提高轴承的表面光洁度和形状精度,提高轴承的使用寿命和运行平稳性。
然后是组装工艺。
组装是将各个零件按照一定的顺序组合到一起,形成完整的轴承产品。
在组装过程中,需要注意零件的配合间隙、润滑剂的添加和轴承的安装力度,以保证轴承的正常运行和寿命。
最后是检测工艺。
检测是对已经组装好的轴承产品进行性能和质量的测试和评估。
常见的检测方法包括外观检查、尺寸测量、外径跳动和内径跳动测试以及转动摩擦力测定等。
通过检测,能够发现轴承产品的问题,并及时进行调整和修复。
综上所述,轴承的生产工艺包括材料准备、锻造、车削、磨削、组装和检测等多个环节。
每个环节都十分重要,对最终轴承的品质和性能有着直接影响。
只有通过精细的工艺控制和严格的质量检测,才能生产出高质量的轴承产品。
精密轴承加工工艺
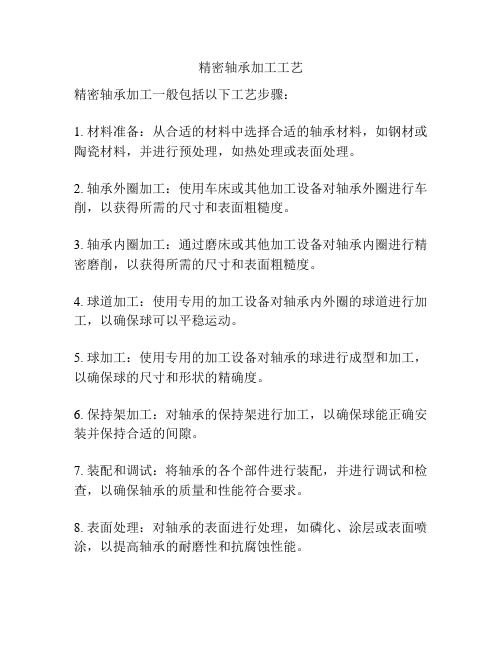
精密轴承加工工艺
精密轴承加工一般包括以下工艺步骤:
1. 材料准备:从合适的材料中选择合适的轴承材料,如钢材或陶瓷材料,并进行预处理,如热处理或表面处理。
2. 轴承外圈加工:使用车床或其他加工设备对轴承外圈进行车削,以获得所需的尺寸和表面粗糙度。
3. 轴承内圈加工:通过磨床或其他加工设备对轴承内圈进行精密磨削,以获得所需的尺寸和表面粗糙度。
4. 球道加工:使用专用的加工设备对轴承内外圈的球道进行加工,以确保球可以平稳运动。
5. 球加工:使用专用的加工设备对轴承的球进行成型和加工,以确保球的尺寸和形状的精确度。
6. 保持架加工:对轴承的保持架进行加工,以确保球能正确安装并保持合适的间隙。
7. 装配和调试:将轴承的各个部件进行装配,并进行调试和检查,以确保轴承的质量和性能符合要求。
8. 表面处理:对轴承的表面进行处理,如磷化、涂层或表面喷涂,以提高轴承的耐磨性和抗腐蚀性能。
9. 检验和测试:对加工好的轴承进行各项检验和测试,如尺寸测量、质量检验和性能测试,以确保轴承达到规定的标准和要求。
以上是一般的精密轴承加工工艺步骤,具体的工艺流程可能因不同的轴承类型和要求而有所差异。
轴承加工工艺流程(附图)

轴承加工工艺流程(附图)轴承就是当代机械设备中一种重要零部件。
它得主要功能就是支撑机械旋转体,降低其运动过程中得摩擦系数,并保证其回转精度.按运动元件摩擦性质得不同,轴承可分为滚动轴承与滑动轴承两大类.轴承可同时承受径向负荷与轴向负荷。
能在较高得转速下工作。
接触角越大,轴向承载能力越高。
那么轴承就是怎么加工出来得呢?轴承制造加工基本过程(以套圈制造基本流程为重点,材料选用高碳铬轴承钢Gcr15SiMn)〈1>滚动体(钢球)制造基本流程:原材料——冷镦—-光磨——热处理—-硬磨——初研——外观—-精研<2〉保持架(钢板)制造基本流程:原材料——剪料——裁环-—光整——成形——整形-—冲铆钉孔〈3>套圈(内圈、外圈)制造基本流程:原材料——锻造——退火——车削——淬火--回火——磨削--装配汇普轴承加工流程图(1)锻造加工:锻造加工就是轴承套圈加工中得初加工,也称毛坯加工。
套圈锻造加工得主要目得就是:(a)获得与产品形状相似得毛坯,从而提高金属材料利用率,节约原材料,减少机械加工量,降低成本。
(b)消除金属内在缺陷,改善金属组织,使金属流线分布合理,金属紧密度好,从而提高轴承得使用寿命。
锻造方式:一般就是在感应加热炉、压力机、扩孔机与整形机组成连线得设备体进行流水作业(2)退火:套圈退火得主要目得就是:高碳铬轴承钢得球化退火就是为了获得铁素体基体上均匀分布着细、小、匀、圆得碳化物颗粒得组织,为以后得冷加工及最终得淬回火作组织准备.Gcr15SiMn退火基本工序:在790—810℃保温2—6h,以10—30℃/h,冷至600℃以下,出炉空冷(3)车削加工:车削加工就是轴承套圈得半成品加工,也可以说就是成型加工.车削加工得主要目得就是:(a)使加工后得套圈与最终产品形状完全相同。
(b)为后面得磨削加工创造有利条件。
车削加工得方法:集中工序法:在一台设备上完成所有车削工序得小批量生产。
分散工序法:在一台设备上完成某一种车削工序得大批量生产。
车床轴承工艺流程

车床轴承工艺流程车床轴承加工工艺流程是指将铸铁、钢、有色金属等材料加工成轴承零件的过程。
下面将介绍一下车床轴承加工工艺的流程。
1. 材料准备:首先需要准备好所需材料,包括轴承外壳和轴承内圈的原材料。
根据设计要求,选择适当的材料,如碳钢、合金钢等。
2. 材料切割:将所需的原材料根据轴承外壳和轴承内圈的尺寸要求切割成相应的坯料。
3. 轴承外壳车削:将轴承外壳的坯料固定在车床上,进行粗车和精车的加工。
首先进行粗车,根据设计图纸上的尺寸要求,将坯料车削成近似形状。
然后进行精车,利用车刀切削剩余的金属,使其达到设计图纸的尺寸精度要求。
4. 轴承内圈车削:将轴承内圈的坯料固定在车床上,进行相同的粗车和精车加工。
粗车和精车的过程与轴承外壳的加工类似,都需要根据设计要求进行切削加工。
5. 轴承孔的加工:将车削好的轴承内圈固定在车床上,进行车削和钻孔的加工。
首先利用车刀将内圈的外径车削成设计要求的直径尺寸,然后利用钻头进行孔的加工,以满足轴承配合的要求。
6. 轴承外径修整:将车床加工后的轴承外壳和轴承内圈进行搭配,通过磨削或研磨等方法,修整轴承外径和轴承内径的尺寸,以确保轴承的配合性能。
7. 热处理:对加工好的轴承进行热处理,以提高其硬度和机械性能。
热处理方式根据材料的特点和工艺要求来选择,常见的热处理方式有淬火、回火等。
8. 清洗和检验:对热处理后的轴承进行清洗,去除表面的油污等杂质。
然后进行外观检验、尺寸检验和硬度检验等工序,以确保轴承的质量和性能符合要求。
9. 组装:将经过检验的轴承组装到轴颈上,通过轴承盖和螺栓等零件进行固定。
10. 表面处理和润滑:对组装好的轴承进行表面处理,例如镀锌、喷涂等。
然后进行润滑处理,加入适量的润滑油或润滑脂,以减少摩擦和磨损。
以上就是车床轴承加工工艺的流程。
在实际生产中,还需要根据具体情况进行调整和改进,以提高加工效率和工件质量。
- 1、下载文档前请自行甄别文档内容的完整性,平台不提供额外的编辑、内容补充、找答案等附加服务。
- 2、"仅部分预览"的文档,不可在线预览部分如存在完整性等问题,可反馈申请退款(可完整预览的文档不适用该条件!)。
- 3、如文档侵犯您的权益,请联系客服反馈,我们会尽快为您处理(人工客服工作时间:9:00-18:30)。
沟道振纹产生的原因及解决方法
产生原因: 1、进给量太大 2、刀具锋利程度不够 3、刀具装夹不牢固 4、机床刚性或者旋转精度不够
解决办法: 1、合理安排进给量 2、改变刀具的锋利风度(修磨或者更换) 3、保持刀具装夹的牢固性 4、增加机床的刚性或主轴的旋转精度
29
沟道刀具的安装
车刀不能伸出刀具太长,防止振纹产生或者崩刀 车刀刀尖与工件中心等高,或者车外圈时,允许
内径:包含内径尺寸、圆度、锥度、壁厚差 宽度:包含宽度尺寸、平面度、平行差、表面粗糙度 沟道:包含沟曲率、沟径、沟位(含对称)、侧摆、圆
度、壁厚差 密封槽:包含口径、底径、中宽(单高)、槽形、圆度、
壁厚差、平行差 成品角:角弧度、轴向尺寸、径向尺寸、轴向装配角、径
向装配角度
(附加工艺:外径槽、内径槽、偏心槽、外球面、挡边、钻孔等等)
13
练习
14
15
1、外径
定义:包含外表面的圆柱体的理论直径 测量内容:外径尺寸、圆度、锥度、垂直
差、壁厚差、表面粗糙度。 测量工具:D913、标准件、百分表。 测量方法:(见下图)
16
测量外:M1083外圆磨床 ▪ 对于软磨外径,尺寸公差及公称尺寸易于
31
5、密封槽
测量内容:口径、底径、中宽、槽形、 圆度、壁厚差、平行差
8
基本术语及其定义
• 基本尺寸:指尺寸设计给定的尺寸(公称尺寸)。 • 实际尺寸:指通过测量所得的尺寸。 • 极限尺寸:允许尺寸变化的两个极限值。 • 尺寸偏差:某一尺寸减去基本尺寸所得的代数差。 • 上偏差:最大极限尺寸减去基本尺寸的代数差。 • 下偏差:最小极限尺寸减去基本尺寸的代数差。 • 偏差可为正、负或零值。 • 公差:允许尺寸的变动量。 • 公差是绝对值,无正负之分。
车刀稍微高于工件中心,允许量为工件直径的1%, 车内圈时,允许车刀稍低于工件中心,允许量为 工件直径的1% 车刀轴线尽量与工件轴线平行 装刀时用的垫片要平整,并且尽量减少实用的片 数 车刀要紧固牢靠
30
密封槽
• 密封槽的车加工是成品轴承的最终工序, 其质量的好坏直接影响轴承的装配,它 的要求项目比较复杂,不同的客户有不 同的要求,因此,密封槽加工应当作为 车加工的重要项目来控制。必须掌握正 确的检测手段和检测方式。由于密封槽 无法返工,因此要合理利用资源,将调 节过程尽量缩短,减少产品报废数量。
控制,形位公差不易控制,常见的形位公 差超差主要原因有:
1、外径变动量过大 2、圆度误差过大 3、垂直差过大 4、锥度过大或过小 5、外径磨伤
18
2、内径
定义:包含圆柱孔内表面的圆柱体的理论直径 测量内容:内径尺寸、圆度、锥度、壁厚差、
垂直度 测量工具:D923、标准件、百分表 测量方法:(见下图)
9
轴承加工中常见形位公差分类及表示符号
形位公差分为形状公差和位置公差 注:形状公差是指实际单一要素的形状所允许的变动量 位置公差是指实际关联要素的位置对基准所允许的 变动量
10
形状公差:平面度用符号“ ”表示; 圆度用符号“ ”表示; 锥度用符号“ ”表示。
位置公差:侧摆用符号“ ”表示; 对称用符号“ ”表示; 垂直度用符号“ ”表示; 壁厚差用符号“ ”表示。
19
测量内径示意图
20
3、宽度
▪ 定义:套圈两端面之间的距离 ▪ 测量内容:宽度尺寸、平面度、平行差、表面
粗糙度
▪ 测量工具:G903、标准件、百分表、刀口尺 ▪ 测量方法:(见下图)
21
测量宽度示意图
22
软磨端面
▪ 加工设备:MZ7650双端面磨床 ▪ 产生报废主要原因: 1、宽度变动量过大 2、平面度不好,表面有凹凸现象 3、产品烧伤 (前两项指标是磨削加工中常见报废产生的
5
密封槽 口径、底径、中宽、槽形、圆度、壁厚差
6
挡 边 直径、挡边宽度、圆度、壁厚差
7
标识槽 槽直径、全槽宽、槽位置、圆度、壁厚差
8
外球面 球半径、对称、圆度、壁厚差
9
油 孔 油孔直径、油孔位置
10 缺 口 缺口弧半径、缺口最大直径、缺口角度
11 成品角 角圆弧R、轴向/径向尺寸、轴向/径向装配角
12
注释:形状公差是指实际单一的形状所允许的变动量 位置公差是指实际关联要素的位置对基准所允许的变动量
11
各工序检查部位及项目
序号 检验部位
检查项目
备注
1
外 径 外径尺寸、圆度、锥度、壁厚差、表面粗糙度
2
内 径 内径尺寸、圆度、锥度、壁厚差、垂直度
3
宽 度 宽度尺寸、平面度、平行度、表面粗糙度
4
沟 道 沟径、沟曲率、沟位、侧摆、圆度、壁厚差
26
沟曲率的检测方式及确定方法
沟曲率用刮色球刮色判定,当小范刮色时 沟道底部白两边红,当大范刮色时底部红 两边白。则判定为沟曲率合格,反之就判 定为不合格。 若大范刮色时底部呈白色,则表示沟曲率 过大; 若小范刮色时两边呈白色,则表示沟曲率 偏小。
27
沟道加工中易出现的废品及解决方法
沟曲率过大或者过小,主要是由刀具原因, 应采取重磨或修磨加以调整 沟径超差,可调整进刀量加以解决 沟位不好,可调整拖板以达到加工要求 侧摆超差,可采取调整工装夹具加以解决 圆度、壁厚差不好,可调整工装夹具、主轴 精度予以解决
主要因素,也是后序加工中定位不好的主 要原因,因此必须严格控制)
23
4、沟道
测量内容:沟曲率、沟径、沟位(含对称)、 侧摆、圆度、壁厚差
测量工具:⑴内圈 刮色球、D022、标准件、 百分表
⑵外圈 刮色球、D012、标准件、 百分表
测量方法:(见下图)
24
测量宽度示意图
25
刮色球大小范的确定 • 大范半径为沟曲率最大极限半径; • 小范半径为沟曲率最小极限半径。
轴承加工工艺流程
1
2
轴承的组成元素
轴承内部一般由外圈、内圈、滚动体和保 持架组成------通常称为四大件
对于密封轴承,再加上润滑剂和密封圈 (或防尘盖)------又称为六大件
3
成品轴承
4
轴承结构
(深沟球轴承)
密封件 外圈
滚动元件 保持架
内圈 密封件
5
6
7
基本工序的基本参数
外径:包含外径尺寸、圆度、锥度、垂直差、壁厚差、表 面粗糙度