技术要求翻译
设备安装技术要求-英文翻译
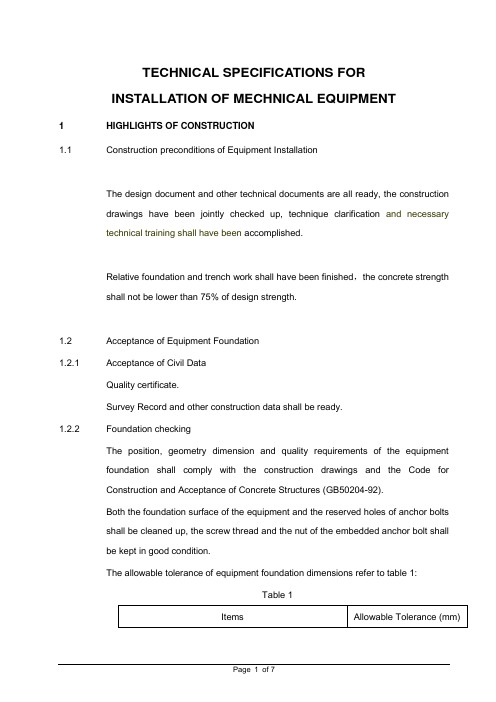
TECHNICAL SPECIFICATIONS FORINSTALLATION OF MECHNICAL EQUIPMENT1 HIGHLIGHTS OF CONSTRUCTION1.1 Construction preconditions of Equipment InstallationThe design document and other technical documents are all ready, the constructiondrawings have been jointly checked up, technique clarification and necessarytechnical training shall have been accomplished.Relative foundation and trench work shall have been finished,the concrete strengthshall not be lower than 75% of design strength.1.2 Acceptance of Equipment Foundation1.2.1 Acceptance of Civil DataQuality certificate.Survey Record and other construction data shall be ready.1.2.2 Foundation checkingThe position, geometry dimension and quality requirements of the equipmentfoundation shall comply with the construction drawings and the Code forConstruction and Acceptance of Concrete Structures (GB50204-92).Both the foundation surface of the equipment and the reserved holes of anchor boltsshall be cleaned up, the screw thread and the nut of the embedded anchor bolt shallbe kept in good condition.The allowable tolerance of equipment foundation dimensions refer to table 1:Table 1Page 1 of 71.3 Unpacking Inspection of EquipmentUnpacking inspection of equipment shall be executed under the supervision of theOwner’s personnel, Contractor shall inspect the following items:Appearance , quantity, specification and model of the equipmentPacking list and other technical dada.During the inspection Contractor shall keep all the records.Equipment , spare parts and special tools shall be carefully kept.1.4 Installation of Equipment1.4.1 Positioning and Aligning of EquipmentThe baseline of installation shall be designated accord with construction drawing andrelating axis, edge line or elevation line before equipment positioning.The allowable tolerance of of the distance from plane installation bench mark toactual foundation axis or between actual shop wall axis and edge line is ±20mm.Refer to Table 2 for the allowable tolerance of plane position and elevation of thepositioning plane, line or point to bench mark:Table2The allowable tolerance of equipment installation refers to table 3: Table 31.4.2 Anchor BoltThe Anchor bolt in the reserved hole shall accord with the requirement ofconstruction drawing and design document; the requirement below must be followedif no other special instructions are available:(1) Anchor bolt shall be vertical in reserved hole free of inclining.(2) The distance between any part of anchor bolt to the hole wall shall be largerthan 15mm, and the bolt end shouldn’t touch hole bottom.(3) The oil dirt and oxidized surface of anchor bolt shall be clear away, a littlegrease shall be applied to the screw thread of the anchor bolt.(4) There shall be no distance between the nut and the gasket, and so are thegasket and the pedestal of the equipment.(5) Bolt shall extend out of nut after nut fastening; the exposed length is about1/3-2/3 of the diameter value of the bolt.(6) The anchor blot shall be fastened while concrete strength in reserved reachesmore than than 75% designed value, the fastening strength shall be evenly.1.4.3 Iron ShimThe shim size for level adjusting of equipment shall accord with the requirement ofconstruction drawings or technical documents.The common wedge shim and flat shim shall be selected according to Appendix 5 ofthe Construction & Acceptance Criterion of Machine & Equipment Installation Works(GB50231-98).1.4.4 GroutingThe grouting between the foundation and pedestal of the equipment/the reservedhole of the anchor bolt shall comply with the Code for Construction and Acceptanceof Concrete Structures (GB50204-92).The grouting place shall be cleaned up before grouting. The concrete grade used forgrouting is one grade higher than that used for foundation or ground. Groundingshouldn’t make anchor bolt inclined or affect installing precision of the equipment.The thickness of grouting layer shall accord with design requirement, commonly notless than 25mm.The outer forms shall be laid before grouting, the distance of outer forms from outeredge of equipment base shouldn’t less than 60mm; Float coat shall be applied to thesurface after removal of forms.The inner forms shall be laid when complete grouting is not needed under equipmentbase and grouting layer would bear load of equipment.1.4.5 Assembly of EquipmentThe assembly of equipment shall accord with the requirement of constructiondrawings, technical documents of manufacturer and Code for Construction &Acceptance of Machine & Equipment Installation Works (GB50231-98).Before the equipment assembly, the Contractor shall be familiar with the equipmentstructure and the technical requirements of equipment assembly. Recheck andcleaning treating on match dimension, relating precision, match face and sliding faceof assembly parts shall be done, and the assembly shall be performed according tomarks and assemble sequence.As to equipment or parts have inner cavity, careful check and clearance must bedone before concealing avoid any foreign substance contained in it.As to oil tank or water tank that difficult to disassembly, check and fix, leakageexamination must be done before assembly.1.4.6 Installation of Equipment AccessoriesThe installation of tower and inner parts of equipment shall accord with therequirement of construction drawings and Code for Construction & Acceptance ofMachine & Equipment Installation Works (GB50231-98).The installation of inner parts of pump shall accord with the requirement ofconstruction drawings and Construction, Code for Construction and Acceptance ofCompressor, Fan and Pump Installation Works (GB50275-98).The installation, pressure testing of accessory pipe shall accord with the requirementof construction drawings and Code for Construction and Acceptance of IndustrialPiping Works (GB50236-98).The installation of accessory ladder, platform shall accord with the requirement ofconstruction drawings and Code for Construction and Acceptance of Steel StructureWorks (GB50205-95).1.4.7 Equipment TestAfter the installation completed, all the welding seams of pressure vessel shall bechecked according to the Assessment on Welding Technology of Pressure Vessel(JB4708-92) and make record.Pressure experiment shall be performed to pressure container accord withconstructing instructions and design requirement after installation.The pressure & leakage test shall be executed according to the ConstructionExplanation and the Design Requirements after the installation of stove type andfamiliar equipments that have water double layer.1.4.8 Cleaning and Purging of EquipmentWhen the installation of pump equipment completed, cleaning and purged of suchequipment must be carried out according to construction drawings and Construction,Checking and Construction, Code for Construction and Acceptance of Compressor,Fan and Pump Installation Works (GB50275-98).The cleaning and purging of static equipment must be performed after installationaccording to construction drawings and Code for Construction & Acceptance ofMachine & Equipment Installation Works (GB50231-98).1.4.9 Test-run of EquipmentThe conditions, contents and procedure shall be ready before equipment test-run, asspecified in Code for Construction & Acceptance of Machine & EquipmentInstallation Works (GB50231-98).Make good test-run record during the test-run operation.After test-run of equipment, turn off power supply, drain out water and vent air andclean as per Code for Construction & Acceptance of Machine & EquipmentInstallation Works (GB50231-98).1.4.10 Taking-over, Inspection and Acceptance of the Equipment Installation WorksAfter all the working procedure of equipment have finished, the Contractor shall packup all the construction documents and perform inspection & acceptance of theEquipment Installation Works under the supervision of relative personnel if thetest-run of equipment is successful and meet the requirements of Design and Relative Specifications.At last the Contractor shall go through the formalities of taking-over procedure.ATTACHED ILLUMINATION:This Standard Is Kept By Technique Department.This Standard Was Prepared By Construction Management Department.THE MAIN DRAFTSMAN OF THIS STANDARD:Xu QingChecked by :Xu Xingguo / Wu BenlunApproved by :。
技术要求翻译
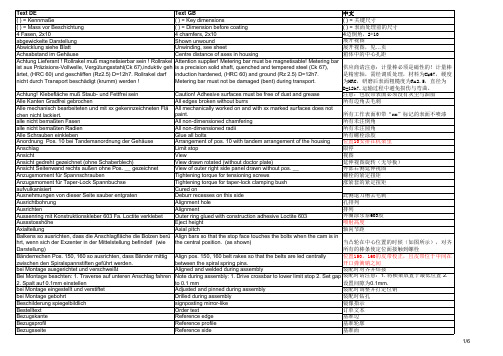
所有未注圆角
Alle Schrauben einkleben
Glue all bolts
所有螺栓涂胶
Anordnung Pos. 10 bei Tandemanordnung der Gehäuse Anschlag
Arrangement of pos. 10 with tandem arrangement of the housing Limit stop
Drilled during assembly
装配时钻孔
Beschilderung spiegelbildlich Bestelltext
signposting mirror-like Order text
镜像指示 订单文本
Bezugskante
Reference edge
基准边
Bezugsprofil
chen nicht lackiert. alle nicht bemaßten Fasen
paint. All non-dimensioned chamfering
所有工作表面和带“xx”标记的表面不喷漆 所有未注倒角
alle nicht bemaßten Radien
All non-dimensioned radii
hrt, wenn sich der Exzenter in der Mittelstellung befindet! (wie the central position. (as shown)
当凸轮在中心位置的时候(如图所示),对齐
Darstellung)
所有的棒条使定位面接触到螺栓
Bänderrechen Pos. 150, 160 so ausrichten, dass Bänder mittig Align pos. 150, 160 belt rakes so that the belts are led centrally
常用技术翻译
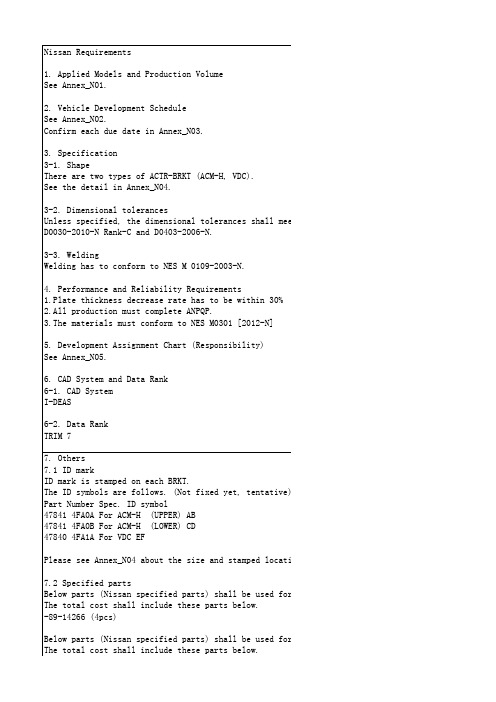
-18316 S3260 (4pcs) -81-10630-2G (2pcs) -89-18306-2A (2pcs)-89-14266 (4pcs)Below parts (Nissan specified parts) shall be used for 47840 4FA1A.The total cost shall include these parts below.-49728 6P00A (4pcs)-18316 S3260 (4pcs)-81-10630-2G (2pcs)-89-18306-2A (2pcs)-89-14266 (2pcs)-82-76625 (2pcs)8. Notes1. This technical sheet gives the supplier the minimum specification of the BRKT for Brake System t quote the cost. If the specifications stated in this RFQ are not enough for the cost quotation, all the unclear items must be informed to Nissan before the cost quotation.2. If there are any difficulties or concerns about BRKT shape for the production, please contact with Nissan engineers and provide counter proposal.3. Nissan will not accept any cost increasing request for design change by the supplier matters without any changes of Nissan specification.4. If you need the 3D data of these BRKT for cost estimation, please inform to Nissan engineer.5. The sample parts (1 part each) for vibration test must be delivered by September 14th.6. To contact Nissan, please send an e-mail below.Driving Control Engineering Development Department (XN0)ISHIZUKA MOTOI : motoi-ishizuka@mail.nissan.co.jp7. Others7.1 ID markID mark is stamped on each BRKT.The ID symbols are follows. (Not fixed yet, tentative)Part Number Spec. ID symbol47841 4FA0A For ACM-H (UPPER) AB47841 4FA0B For ACM-H (LOWER) CD47840 4FA1A For VDC EFPlease see Annex_N04 about the size and stamped location.7.2 Specified partsBelow parts (Nissan specified parts) shall be used for 47841 4FA0A & 47841 4FA0B.The total cost shall include these parts below.-89-14266 (4pcs)Below parts (Nissan specified parts) shall be used for 47840 4FA1A.The total cost shall include these parts below.-49728 6P00A (4pcs)-18316 S3260 (4pcs)-81-10630-2G (2pcs)-89-18306-2A (2pcs)-89-14266 (2pcs)-82-76625 (2pcs)8. Notes1. This technical sheet gives the supplier the minimum specification of the BRKT for Brake System t quote the cost. If the specifications stated in this RFQ are not enough for the cost quotation, all the unclear items must be informed to Nissan before the cost quotation.2. If there are any difficulties or concerns about BRKT shape for the production, please contact with Nissan engineers and provide counter proposal.3. Nissan will not accept any cost increasing request for design change by the supplier matters without any changes of Nissan specification.4. If you need the 3D data of these BRKT for cost estimation, please inform to Nissan engineer.5. The sample parts (1 part each) for vibration test must be delivered by September 14th.6. To contact Nissan, please send an e-mail below.Driving Control Engineering Development Department (XN0)ISHIZUKA MOTOI : motoi-ishizuka@mail.nissan.co.jpwith Nissan engineers and provide counter proposal.3. Nissan will not accept any cost increasing request for design change by the supplier matters without any changes of Nissan specification.).thin 30%012-N]ity)-18316 S3260(4件)-81-10630-2G(2个)-89-18306-2A(2个)ow. ow.-89-14266(4件)以下部分(日产指定的部分)应用于为478404FA1A。
(完整版)英文图纸技术翻译

340121-05-HNOTES :(UNLESS OTHERWISE SPECIFIED):备注:(除非另有说明)1. MATERIAL :RTP 900-P1700 ZC-700458 BLUE (UDEL POLYSULFONE ,COLOR BLUE).材料:RTP 900-P1700 RTP 900-P1700 蓝色(聚砜,蓝色)NO USED OR RECYCLED MATERIAL PERMITTED .不允许使用用过的或者回收的材料PROVIDED RAW MATERIAL LOT CERTIFICATION WITH EACH SHIPMENT WHICH INCLUDES SUPPLIER NAME LOT NUMBER ,AND MATERIAL TYPE OR SPECIFICATION NUMBER .提供每一次交付来料原材料批号认证,包括供应商名称批号,材料类型或者规格编号2. ALL EJECTOR PIN AND GATING VESTIGE TO BE FLUSH OR RECESSED WITHIN .005 OF SURFACE.所有的顶针和水口残留要与部品表面齐平,深入表面最大不能超过0.005INTUITIVE SURGICAL ENGINEER TO APPROVE ALL GATE AND EJECTOR PIN LOCATIONS .要与客户确认水口和顶针位置3. NO CRACKS ,FLASH,SINKS,OR KNIT LINES PERMITTED UNLESS APPROVED BY INTUITIVE SURGICAL . 不能有裂纹,披峰,缩水,熔接线,除非客户同意VISUALLY INSPECT FOR COMPLETE FILL AND IRREGULARITIES肉眼检查一下打满胶的部品和其他不良4. ALL MOLD RELEASE MUST BE APPROVED BY INTUITIVE SURGICAL ENGINEERING PRIOR TOUSE .脱模剂要经过外观工程科同意后使用5. DIAMETRICAL TAPER TO CONFORM TO ISO 594/1-1986 (LUER FITTING ).直径的锥形符合ISO 594/1 - 1986(鲁尔接口配件)USE GO/NOGO GAGE DEFINED IN ISO 594/1-1986 ,FIGURE 3C (ISI PN 710014)TO INSPECT CAVITY .通止规使用参考ISO 594/1-1986,检查前模用FIGURE 3C (ISI PN 710014)6. NOT FULLY DIMENSIONED OBTAIN MISSING INFORMATION FROM CAD FILES .没标注的尺寸参见CAD图纸7. PARTS TO BE CLEAN , WITH NO CONTAMINATION OR LUBRICANT .部品要干净,没有污染物质或润滑剂NO VISIBLE PARTICULATE WHEN EXAMINED WITHOUT MAGNIFICATION .用肉眼检查,不要有可见微粒8. PACKAGE IN CLEAN CLEAR PLASTIC BAGS .包装使用干净的透明塑料袋LABEL PACKAGING WITH INTUITIVE ’S PART NUMBER , REVISION (EG .340121-01-H),PURCHASE ORDER NUMBER,AND QUANTITY.包装标签上要有:直观的零件号,修订版本(如.340121-01-H),采购订单号和数量。
技术要求翻译

The delivery kit should include service kits for commissioning, as well as maintenance for 500 and 1000 hours.
机组调试,和500以及1000小时维保
Warranty: Original manufacturer's warranty
- electronic control system of the compressor unit assemblies in Russian with an alert on the LCD screen about the following parameters: working pressure, fuel level, operating hours counter, air temperature at the outlet of the compressor element and out of the outlet, engine oil pressure, engine oil temperature, number Engine speed, compressor oil level, engine coolant level, ready-to-start state, start state, idle state, load status, refrigerated state Emergency stop status, warm-up status;
带有离心除液的额外柴油滤器
- a system that ensures uninterrupted start-up at a temperature of -25 ° C;
机械图纸中英文翻译

近几年,我厂和英国、西班牙的几个公司有业务往来,外商传真发来的图纸都是英文标注,平时阅看有一定的困难。
下面把我们积累的几点看英文图纸的经验与同行们交流。
1标题栏英文工程图纸的右下边是标题栏(相当于我们的标题栏和部分技术要求),其中有图纸名称(TILE)、设计者(DRAWN)、审查者(CHECKED)、材料(MATERIAL)、日期(DATE)、比例(SCALE)、热处理(HEAT TREATMENT)和其它一些要求,如:1)TOLERANCES UNLESS OTHERWISE SPECIFIAL 未注公差。
2)DIMS IN mm UNLESS STATED 如不做特殊要求以毫米为单位。
3)ANGULAR TOLERANCE±1°角度公差±1°。
4)DIMS TOLERANCE±0.1未注尺寸公差±0.1。
5)SURFACE FINISH 3.2 UNLESS STATED未注粗糙度3.2。
2常见尺寸的标注及要求2.1孔(HOLE)如:(1)毛坯孔:3"DIAO+1CORE 芯子3"0+1;(2)加工孔:1"DIA1";(3)锪孔:锪孔(注C'BORE=COUNTER BORE锪底面孔);(4)铰孔:1"/4 DIA REAM铰孔1"/4;(5)螺纹孔的标注一般要表示出螺纹的直径,每英寸牙数(螺矩)、螺纹种类、精度等级、钻深、攻深,方向等。
如:例1.6 HOLES EQUI-SPACED ON 5"DIA(6孔均布在5圆周上(EQUI-SPACED=EQUALLY SPACED均布)DRILL 1"DIATHRO'钻1"通孔(THRO'=THROUGH通)C/SINK22×6DEEP沉孔22×6例2.TAP7"/8-14UNF-3BTHRO'攻统一标准细牙螺纹,每英寸14牙,精度等级3B级(注UNF=UNIFIED FINE THREAD美国标准细牙螺纹)1"DRILL 1"/4-20 UNC-3 THD7"/8 DEEP 4HOLES NOT BREAK THRO钻1"孔,攻1"/4美国粗牙螺纹,每英寸20牙,攻深7"/8,4孔不准钻通(UNC=UCIFIED COARSE THREAD 美国标准粗牙螺纹)1"-14NS-2THRO攻美国固定特种螺纹M1",每英寸牙数14,精度等级为二级(注NS=NATIONAL SPECIAL THREAD:美国固定特种标准)2.2倒角(CHAMFER)例1/8×45°BEV倒角1/8×45°(注BEV=BEVEI,斜面)1.5×45°CHAM倒角1.5×45°(注CHAM=CHAMFER倒角)2.3方(SQUARE)例 5"SQUARE5"×5"方2.4剖视(SECTION)例 SECTION A-A A-A剖面2.5圆角半径例1"R R1"RADIUS MUST BE SMOOTH AND BLEND INTO FACE圆弧必须光滑且与平面相切2.6加工余量例 DOTTED LINES INDICATED MAX FINISH 1"/8虚线表示最大加工余量1"/82.7零件标记例USE 5"/16 RAISED HAIRLINE LET-TERS MARKING ON ONE SIDE OF BODY用突起高为5"/16的细实线字母在本体一侧打标记3关于铸锻件的技术要求例1.FORGING MUST BE ANNEALED TO BE BELOW 203 BRINELL HARDNESS 锻件必须退火处理,布氏硬度<203例2.NORMALIZE TO 163-207BHNMUST BE FREE OF SCALE & RUST锻件正火处理,布氏硬度163-207,锻件表面不得有氧化皮和锈蚀例3.FORGING TO BE SHOT OR SAND BLASTED锻件需经喷丸或喷砂处理例4.UNLESS OTHERWISE SPECIFIED DRAFT ANGLES 7°未注明锻造拔模斜度7°例5.CAST TO BE FREE OF EXCESSIVE FLASH 铸件不得有过多的毛边例6.DRAFT ANGLE 2° UNLESS OTHER-WISE SPECIFIED 未注明铸造拔模斜度2°总之,看英文机械工程图纸并不是高不可攀,只要坚持常看,熟记部分单词即可。
图纸技术要求英汉翻译

图纸信息1.Dimensions apply after finished.图纸尺寸应用于成品。
2.Unless otherwise specified,the following profile and positional tolerance applies :未注尺寸的,按照轮廓度和位置度公差。
3.Condition part for safe handling per UL#1439. 规定以UL#1439文件安全加工。
4.Surface treatment:electroless nickel .0001-.0002 thk.表面处理:无电沉镍,厚度.0001-.00025.Material:grey cast iron one percent nickel.材料:含1%镍的灰铸铁。
6.Draft adds mass.图样增大面积。
7.Normalize before machining.机加工前正火(热处理,解除内应力)8.Unless otherwise specified,draft angle to be 2°.未注公差,图样角度给到2度。
9.Straight knurl this surface.此表面直纹。
10.Check when restrained to datum A.以A基准检查工件。
11.Inside and outside radii 0.06 typ. 內外R角0.06.12.All bins and walls to be 0.38 thk unless otherwise specified.未注明,加强肋和壁给定0.38厚度.13.Casting to be stress relieved.铸造用来去除內应力。
14. A slip fit hole.间隙配合孔.Press fit.过盈配合。
15.An interference fit.过渡配合。
整车信息安全技术要求英文版
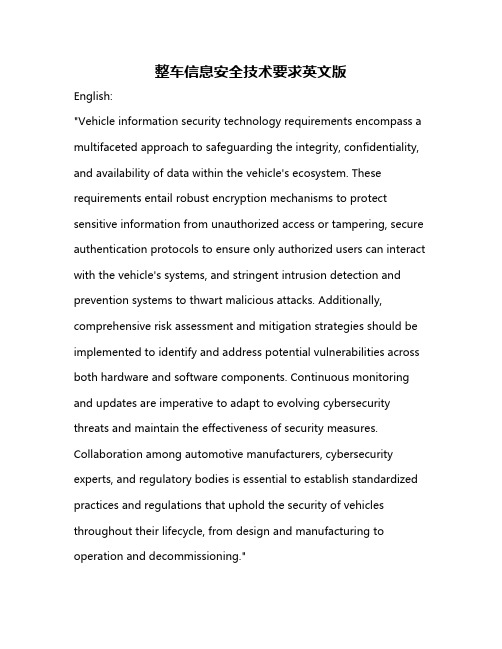
整车信息安全技术要求英文版English:"Vehicle information security technology requirements encompass a multifaceted approach to safeguarding the integrity, confidentiality, and availability of data within the vehicle's ecosystem. These requirements entail robust encryption mechanisms to protect sensitive information from unauthorized access or tampering, secure authentication protocols to ensure only authorized users can interact with the vehicle's systems, and stringent intrusion detection and prevention systems to thwart malicious attacks. Additionally, comprehensive risk assessment and mitigation strategies should be implemented to identify and address potential vulnerabilities across both hardware and software components. Continuous monitoring and updates are imperative to adapt to evolving cybersecurity threats and maintain the effectiveness of security measures. Collaboration among automotive manufacturers, cybersecurity experts, and regulatory bodies is essential to establish standardized practices and regulations that uphold the security of vehicles throughout their lifecycle, from design and manufacturing to operation and decommissioning."中文翻译:"整车信息安全技术要求包括多方面的措施,以保障车辆生态系统内数据的完整性、机密性和可用性。
11.1ptca球囊扩张导管技术要求英文翻译

Technical requirements for medical device product registration number:Disposable Sterile PTCA balloon catheter1、Model / Specifications and divide instructions1、1 ModelPTCA-XX-XXBalloon nominal Diameter mmProduct Name CodeModel mark example:PTCA——10 represents balloon nominal outer diameter is and working length is 10mm of disposable Sterile PTCA balloon catheter1、2 Specifications1、3 Divide instructionsDisposable Sterile PTCA balloon catheter consists of balloon, connecting catheter, tip, support catheter and Handle.According to different balloon diameter to divide the balloon into different specifications and sizes. According to medical device classification rules 6877, the balloon catheter belonging to Class Ⅲ interventional equipment intravascular catheter.2、Performance2、1 AppearanceAs with normal vision or corrected vision at a magnification of times the conditions of inspection, the effective length of the outer catheter should be clean and free of impurities.There should be no processing defects and surface defects on the surface of catheter effective length and end.The inner and outer surface of the distal end components of the catheter should have silicone oil (polydimethylsiloxane) lubricant coating. With normal vision or corrected vision inspection,the outer surface of the catheter should not see the convergence of lubricant droplets.Note:The inner and outer surface of the distal end components of the catheter is the out surface from the tip (figure 1) to the transition weld (figure 7),and the inner surface from guide wire lumen (from the tip (Figure 1 below) to quickly switch ports (figure 5)).2、2 Size requirementsBalloon catheter size requirements reference table1, specification list reference table 2.1、Tip2、Balloon3、Radiopaque ring4、Out catheter5、Quickly switch ports6、Guide wire7、Transition weld8、Hypo Tube(FEP Coated)9、Bending resistant tube 10、Handle 11 Balloon effective length( L) 12、catheter effective lengthPic 1. PTCA balloon catheter schematicPic 2. Tip schematicTable 1 disposable Sterile PTCA balloon catheter size and tolerance requirementsConnector of balloon catheter must be tapered connector.Size should be consistent with GB / T requirements.Physical propertiesBreaking forceBreaking strength of each test section shall comply with the requirements of Table 3.Leakagea) There should no liquid leakage at catheter hub,connection assembly part and other parts of catheter.There should be no leak or signs of damage for catheter or balloon. If prominent or burst,this requirement adapt before hydrated and after hydrated.b)In the continuous process of the suction,air should not enter into the assembly part of catheter. This requirement adapt before hydrated and after hydrated.Ray detectabilityRadiopaque ring should be visible under proven imaging technology which in the clinical use.Tip configurationIn order to reduce damage to blood vessels during the use process,the end of tip should be smooth and have a taper or there is a certain process or via similar finishing.Particulate pollutionBalloon catheter production should under the min particulate pollution conditions, inner and out surface of catheter should be clean and pollution index shall comply with the requirements of GB 8368-2005 in Chapter .Non-hydratableChanges of effective before and after hydration should not exceed 4mm or 1% higher than before hydration(Take min);and max OD changes before and after hydration should not exceed 10%of max OD.Chemical propertiesCorrosion resistanceShall comply with the requirements of YY .Reducing substance(Readily oxidizable substance)The volume difference between test liquid and blank liquid consume potassium permanganate solution [c (KmnO4) = / l] shall not exceed .cThe total content of barium, chromium, copper, lead, tin in the test liquid should not exceed 1μg / ml,Cadmium content should not exceed μg / ml.PHThe difference between test pH value and the control of pH value should be less than .Residual ethylene oxideResidual ethylene oxide of balloon catheter should not more than 10ug/g.Balloon catheter should be sterile.Balloon catheter endotoxin content should not exceed each.3. Test MethodAppearanceWith normal or corrected vision at times magnification inspection,It should meet the requirements of .Size and colorWith general gauge for testing, color with visual. It should meet the requirements of .Physical propertiesBreaking forceThe method according to YY / given in Appendix B, and it shall comply with the requirements of Leakagea) The method according to YY given in Appendix C, and it shall comply with the requirements of a.b) The method according to YY given in Appendix D, and it shall comply with the requirements of b.Ray detectabilityUsing hospital conventional method to perform film.Tip configurationWith normal or corrected vision at times magnification inspection.Particulate pollutionThe method according to GB 8368-2005 given in Appendix chapter, the results should meet the requirements of Non-hydratableAccording to YY specified in ,immerse balloon catheter into(37℃±1℃) two hours and then measure the size, it shall comply with the requirements of Chemical propertiesPreparation of test solution according to GB / Chapter , paragraph 6 a table in the provisions。
日本电器产品技术要求中文翻译

别表第八电器用品安全法令(昭和三十七年政令第三百二十四号)别表第一第六开始到第九以及别表第二第七到第十一表示的交流电使用器具和电机1共同事项(1)材料:①器具使用材料应当满足正常使用的温度,耐正常使用温度是指外壳和支撑带电绝缘物是塑性材料的要满足表第三2(1)ロ(ニ)a或者b的要求,如果产品上采集试验片有困难的话,可以使用相同材质的的试验片检测试验片放置到温升40℃的恒温槽内,用直径5mm钢球,20N的力施力1h后放入常温水内冷却10s后测量,压痕直接小于2mm.②电气绝缘材料以及隔热材料,包括逾预期触及靠近的都应当充分耐温。
吸湿性较小的材料符合別表第四1(1)ロ(イ)到(ト)的要求但是,吸湿性材料如果通常使用状态没有危险发生的可能不受限制③器具的部品及其材料不使用和含有硝化棉等类似的易燃材料,但是乒乓球除外④有电弧产生可能的绝缘物,不能因电弧的产生使绝缘物的变形和绝缘程度的降低⑤铁质或钢制材料(不锈钢除外)应当有电镀、喷涂、喷油等措施进行防锈处理,氧化后没有危险发生可能的不受限制⑥导电材料应满足以下要求a. 插脚及插脚的支撑部分应使用铜或铜合金b插脚及插脚支撑部分以外的部分,应使用:铜、铜合金、不锈钢和不低于用別表第三附表第四规定的试验的电镀钢制品,或者在电气、机械、耐热条件上等同以上的材料但是,在构造上不得不使用非电镀的铁制或钢制弹性材料部品,而又没有危险发生可能的不受此限。
⑦室外使用的外壳材料应该是难以生锈的金属、防锈处理的金属、合成橡胶、陶瓷或者是在80+/-3℃环境中放置1后自然冷却而没发生膨胀、裂纹、破裂等现象的合成树脂(照明设备的灯罩70+/-3℃)但是,不被阳光暴露,而且被雨水浸入没有危险发生可能的不受限制。
⑧电源接线端子使用螺钉材料应是铜或铜合金和不低于用別表第三附表第四规定的试验的电镀钢制品。
⑨接地接线端子材料应该具有足够的机械强度和耐腐蚀能力器具内部使用的接地接线线端符合別表第三附表第四规定的试验要求的电镀钢制品。
曲轴加工的技术要求及发展方向外文翻译
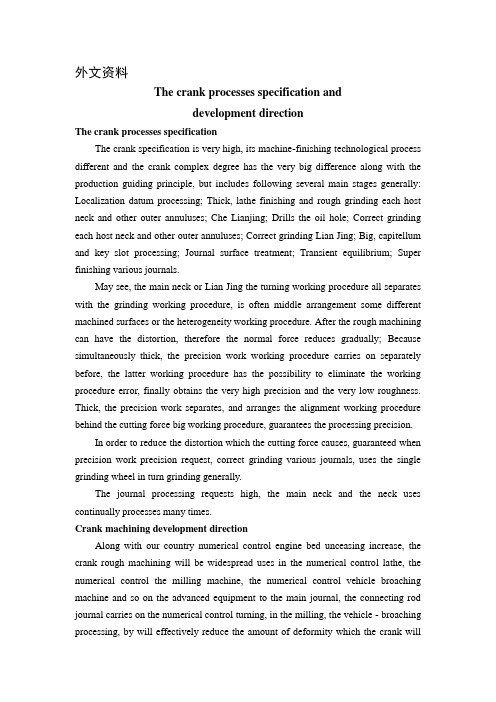
外文资料The crank processes specification anddevelopment directionThe crank processes specificationThe crank specification is very high, its machine-finishing technological process different and the crank complex degree has the very big difference along with the production guiding principle, but includes following several main stages generally: Localization datum processing; Thick, lathe finishing and rough grinding each host neck and other outer annuluses; Che Lianjing; Drills the oil hole; Correct grinding each host neck and other outer annuluses; Correct grinding Lian Jing; Big, capitellum and key slot processing; Journal surface treatment; Transient equilibrium; Super finishing various journals.May see, the main neck or Lian Jing the turning working procedure all separates with the grinding working procedure, is often middle arrangement some different machined surfaces or the heterogeneity working procedure. After the rough machining can have the distortion, therefore the normal force reduces gradually; Because simultaneously thick, the precision work working procedure carries on separately before, the latter working procedure has the possibility to eliminate the working procedure error, finally obtains the very high precision and the very low roughness. Thick, the precision work separates, and arranges the alignment working procedure behind the cutting force big working procedure, guarantees the processing precision.In order to reduce the distortion which the cutting force causes, guaranteed when precision work precision request, correct grinding various journals, uses the single grinding wheel in turn grinding generally.The journal processing requests high, the main neck and the neck uses continually processes many times.Crank machining development directionAlong with our country numerical control engine bed unceasing increase, the crank rough machining will be widespread uses in the numerical control lathe, the numerical control the milling machine, the numerical control vehicle broaching machine and so on the advanced equipment to the main journal, the connecting rod journal carries on the numerical control turning, in the milling, the vehicle - broaching processing, by will effectively reduce the amount of deformity which the crank willprocess. The crank precision work will be widespread uses the CNC control the crankshaft grinding to carry on the correct grinding processing to its journal, this kind of grinder will provide grinding wheel automatic function requests and so on transient equilibrium installment, center rest automatic tracking unit, automatic survey, self-compensating system, grinding wheel automatic conditioning, permanent link speed, will guarantee the grinding quality the stability.In order to satisfy the processing request which the crank enhances day by day, set the very high request to the crankshaft grinding. The modern crankshaft grinding except must have the very high static state, the dynamic rigidity and outside the very high processing precision, but also requests to have the very high grinding efficiency and more flexibilities. In recent years, requested the crankshaft grinding to have the stable processing precision, for this, had stipulated to the crankshaft grinding process capability coefficient Cp≥1.67, this meant reques ted the crankshaft grinding the actual processing common difference to have the common difference which assigned compared to the crank small one half. Along with the modern actuation and the control technology, the survey control, CBN (cubic boron nitride) the grinding wheel and the advanced engine bed part application, for the crankshaft grinding high accuracy, the highly effective abrasive machining has created the condition. One kind calls it the connecting rod neck follow-up grinding craft. Has manifested these new technical synthesis application concrete achievement. This kind of follow-up grinding craft may obviously enhance the crank connecting rod neck the grinding efficiency, the processing precision and the processing flexibility. When carries on the follow-up grinding to the connecting rod neck, the crank take the main journal as the spool thread carries on revolving, and clamps the grinding all connecting rod neck in an attire. In the grinding process, the wheelhead realization reciprocation swing feed, tracks the biased rotation connecting rod neck to carry on the abrasive machining. Must realize the follow-up grinding, X axis besides must have the high dynamic performance, but also must have the enough tracking accuracy, guarantees the shape common difference which the connecting rod neck requests. The CBN grinding wheel application realizes the connecting rod neck follow-up grinding important condition. Because the CBN grinding wheel resistance to wear is high, in the grinding process medium plain emery wheel diameter is nearly invariable, a conditioning may the grinding 600~800 cranks. The CBN grinding wheel also may use the very high grinding speed, may use generally on the crankshaft grinding reaches as high as the120~140m/s grinding speed, the grinding efficiency is very high.Connecting rod processing and trend of development Connecting rod processing methodThe connecting rod decomposes (also called connecting rod breaks) the technical principle uses the material break theory, first artificial has the whole forging connecting rod semi finished materials big end of hole the fissure, forms the initial break source, then expands with the specific method control fissure, achieved the connecting rod The decomposition processing process enable the decomposition the connecting rod cap, the pole adjoining plane to have the complete meshing jig-saw patterned structure, guaranteed the adjoining plane precise docking, tallies, does not need to carry on the adjoining plane again the processing, simultaneously simplified the connecting rod bolt hole structural design and the whole processing craft, has the processing working procedure few, the economical precision work equipment, the nodal wood energy conservation, the product quality high, the production cost low status merit. Main body and the connecting rod cap separate goal.Trend of developmentAt present, the drop for and the die casting connecting rod host, the important status, are facing the powder to forge the steel connecting rod and a powder agglutination steel connecting rod forming craft challenge. Speaking of the domestic present situation, although the powder metallurgy forging industry had certain development, but must provide the mass and the high grade powder metallurgy forging is not mature. Moreover involves the equipment to renew, aspect expense questions and so on technical change, in next one, in long time, domestically produced connecting rod production also by drop forging craft primarily.The connecting rod is one of internal combustion engine main spare parts, its reducing socket two sizes and the shape position errors have many requests, for example: Diameter, roundness, cylindricity, center distance, parallelism, hole and end surface verticality and so on. How does these erroneous project produce the scene in the workshop to examine, always is in the internal combustion engine profession a quite difficult question.In the connecting rod production, domestic mainly has following several examination method at present: With the spindle survey, namely puts on the spindle in connecting rod two, with the aid of in V shape block, plate, dial guage survey.Because the spindle needs to load and unload, therefore between the hole axis has the gap, the measuring accuracy is very low.中文翻译曲轴加工的技术要求及发展方向曲轴加工的技术要求曲轴的技术要求是很高的,其机械加工工艺过程随生产纲领的不同和曲轴的复杂程度而有很大的区别,但一般均包括以下几个主要阶段:定位基准的加工;粗、精车和粗磨各主颈及其它外圆;车连颈;钻油孔;精磨各主颈及其他外圆;精磨连颈;大、小头及键槽加工;轴颈表面处理;动平衡;超精加工各轴颈。
产品说明说的翻译

Linguistic features
objective客 观 性 professional专 业 性 concise简 明 性 appealing号 召 性
Objective
When operating, don’t put your foot on the pedals board constantly, so as not to accidentally step on the switch, causing accident.(某冲床说明书)
电机结构应该具有防爆保护。
过去分词+名词
(说明维修或操作程序及说明有关技术要求)
All cable shall be type SEOW-A or better and U.L. listed for the intended submersible service.
所有电缆都应该是SEOW-A类以上的标准的电缆,并通过美国UL认证可 用于潜水系统。
不完全句结构.仅列出疾病或微生物的名称.
Angina pectoris, Prinzmetal's angina, hypertension
心绞痛,变异性心绞痛,高血压。
The following diseases caused by bacteria including gram-positive and gram- negative bacteria such as Staphylococcus, Streptcoccus, Escherichia coli,Klebsiella pneumoniae...
中央处理器(central processing unit)
自动对焦(auto focus)
手动对焦(manual focus)
基础施工技术要求-英文翻译

TECHNICAL SPECIFICATIONS FOR CONSTRUCTIONQUALITY OF BUILDING GRADE & FOUNDATIONS1 KEY POINTS OF QUA LITY CONTROL1.1 Basic construction conditions of building foundations1.1.1 Geotechnical exploration data of rock and earth engineering.1.1.2 The design document and other technical documents are available, the constructiondrawings have been jointly checked up, the necessary technical delivery andtraining have been accomplished.1.2 Earthwork1.2.1 General requirement:(1) Balance calculation on excavating and filling should be accomplished beforeearthwork construction, considering minimum transporting distance, reasonabletransporting path and reasonable construction procedure and other factorssynthetically, properly allocate the earthwork, reduce repeated excavation andtransportation.(2) Ground drainage and dewatering should be done before excavation(3) The gradient of the site surface should be in accordance with designingrequirement, if without specific requirement, the gradient of drainage directionshould not be less than 2‰. The site surface should be checked per point. Setone checking point every 100~400m2, and check points should not be less than10 points; set 1 point every 20m at length, width and edge slope, not less than 1point each side.(4) The plan position, level elevation and side slope grade should be measuredoften during earthwork construction. Reliable protecting measurement should beapplied to plan-control piling and level-control point, and check or review shouldbe done periodically. Soil shouldn’t be placed at the edge of foundation pit.1.2.2 Excavation of soil:(1) Before excavation, setting-out, drainage and dewatering should be checked,and transporting road of vehicles and dump area of soil should be arrangedreasonably .(2) The construction scheme, environment protecting measurement andsupervision scheme should be worked out according to excavating depth,geological conditions, construction method, environment, project period,climate and ground loading and other information, and the excavation of foundation pit (groove) and underground piping trench should approved by general contractor before excavation.(3) Check plan position, horizontal elevation, grade of side slope, compactness, ,drainage, dewatering system during construction, and observe environmental changes from time to time.(4) Side slope value of temporary earthwork excavation should be in accordancewith the requirement of the following table 1:Table 1 Side slope value of temporary earthwork excavation(5) The quality inspection standard of earthwork excavation should be inaccordance with requirement of following table 2:Table 2 The quality inspection standard of earthwork excavation (mm)1.2.3 Backfill of the earthwork(1) Clear away garbage, root and other sundries at bottom, take out seepage andsilt, and check and accept bottom before backfilling.. Backfill on ploughed soilor soft soil should be made after the foundation has been compacted densely.(2) Check drainage measurement, filling thickness of each layer,water-containing control and compact degree during backfilling, The fillingthickness and compact times should be determined by soil texture, compactcoefficient and applied equipment. If without experimental basis, then inaccordance with requirement of following table 3:Table 3 Delaminating thickness and compact times during backfill construction(3) Check elevation, grade of side slope, compactness and other items afterbackfilling construction with standard in accordance with requirement of the following table 4:Table 4 Quality inspection standard of Backfilling (mm)1.2.41.2.5 Fore-control of Piling Work1.2.6 Check and accept of data: quality certificate of precast-piling provided bymanufacturer1.2.7 Check and accept of arrived materials: Appearance and dimension checking of pilesarrived at construction site.1.2.8 Preparation of piling work:(1) Measurement of control network and Foundation point of level: (thepermissible deviation of piling position is: 20mm for group piling, 10mm forsingle-lined piling.(2) If buildings exist nearby, anti-shock trench (with width of 0.5-0.8mm) andother shock-isolating measurement should be applied to decrease theinfluence to them.(3) Determine piling sequence: generally proceed from center to both symmetricsides or in one direction, from center to the around, from deep to shallow,from big to small and from long to short.(4) Check pilling mechanism:(a) Setting measuring scale at sides or frame of the piling;(b) Setting spring pad between hammer and piling cap, piling cap and piling,such as hardwood, sack, mat, etc.(5) For piles of large length or subject to more than 500 times of hammering,hammering cannot be done until checked the pile body strength is qualifiedand after 28 days aging time.1.3 Middle control of piling work:1.3.1 Lifting control of pre-made piling: the concrete pre-made piling should only be liftedtill the strength of which is larger than 70% design value, and be transported till thestrength of which is up to 100% design value.1.3.2 Process control of piling:(1) Heavy hammer and low beating;(2) The clearance between piling cap and its circumstance should be 5~10mm;(3) Piling hammer, piling cap and piling body shall be on the same centerline ;(4) The deviation of verticality at piling inserting should not exceed 0.5%;(5) When piling tip is into hard clay or sandy soil, focus on controlling theinserting other than the designed pile top elevation. When piling tip enters intosoft soil, focus on controlling pile top elevation other than inserting depth.However, the implementation shall follow the requirements of designdrawings.(6) When reaching the inserting depth but not the designed top elevation,hammer 3 groups more with 10 strokes in each group and inserting depth ofeach group shall not exceed the designed data to verify. The controlledinserting depth shall be defined with related organizations when necessary.(7) Suspend piling in case of the following conditions, while report to supervisor intime:(a) Sharp change of inserting;(b) Sudden inclining/shifting or serious rebounding of pile.(c) Severe crack or crash occurred at pile top or pile body.1.3.3 Control of pile connection:(1) The welding material shall meet the following regulations in case of weldingconnection and steel sheet shall be of low carbon steel.(2) When apply welding connection, fix four angles firstly with spot welding,then weld symmetrically, while ensure quality and size of welding.(3) Refer to Table 5 for quality of welding of pile connection.Table 5:1.4 Check and accept of Construction Quality for Piling (refer to table 7)1.4.1 The quality check of pre-made piling include: piling-making, infiltrate depth,standard of hammer stopping, piling position and verticality;1.4.2 As for grade 1 building foundations or pile foundations of poor geological conditionsor unreliable piling quality, carry out piling quality test.1.4.3 Checking method could be dynamic testing method, or taking drill rock core andpre-buried tube ultrasonic test method for large size piles. Number of test shall bedefined based on the specific conditions.1.4.4 Testing of single pile bearing capacity:1.4.5 In order to ensure vertical bearing capacity of single pile to meet the designrequirement, static loading test and reliable dynamic test shall be made for singlepile based on essentiality, geological conditions, and design requirement andconstruction conditions of the project.1.4.6 Pile foundations of either case stated below shall have static load test to check thevertical bearing of single pile. Piles tested shall not be less than 1% of total piles,and shall not be less than 3 piles in total. Test for 2 piles minimum for total numberof piles less than 50.(a) Grade 1 building foundation piles have no single pile static load test before piling.(b) No single pile static load test before piling yet with one of the following cases:Complicated geological conditions; poor reliability of piling quality; low reliability ofsingle pile vertical pile, class 2 building piled foundation with a high number of piles.1.4.7 Piling foundation works of either case below, reliable vertical load test can beapplied to check the vertical bearing of single pile.(a) Piling foundation of grade I of which static load test has been made on singlepiling before piling;(b) Piling foundation of grade II that doesn’t belong to b) of item 2.5.4.2;(c) Piling foundation of grade III;(d) Auxiliary test of static load test on piling foundation of grade I and II.1.4.8 Allowable tolerance of position of pre-cast pile refer to table 6:Table 6:Table7 Quality test standard of pre-made piling made of RC2 A CCEPTA NCE DOCUMENT OF PILED FOUNDA TION2.1 Acceptance document of piled foundation2.1.1 Geological survey report, construction drawings of piling Foundation, summary ofjointlycheck on piling , design change order and notice of material substitute of the project.2.1.2 The examined and approved changes on construction organization design,constructionscheme and during the implement of them.2.1.3 Piling position setting-out drawings, including check sign sheet of piling position line;2.1.4 Checking report on quality of piling;2.1.5 Check report on bearing of single pile;2.1.6 Handover pile layout drawings and pile top elevation drawings when foundation pitis dug to the designed elevation.2.2 Acceptance document of Aprons2.2.1 Apron reinforcement and concrete construction and record.2.2.2 Record for distance between pile top and apron reinforcements and side piles toedges as well as cover of apron reinforcements.2.2.3 The record of thickness and length of platform and description of appearanceATTACHED ILLUMINATION:This Standard Is Kept By Technique Department.This Standard Was Prepared By Construction Management Department.THE MAIN DRAFTSMAN OF THIS STANDARD:Tan LiChecked by :Wang Yuming / Wu BenlunApproved by :。
技术翻译

1)注在零件尺寸旁的“ AS PURCHASED ” ,应译为“此尺寸装配定或实配”。
2)在轴类零件图上沿轴径方向钻孔尺寸附近标注FILE FLAT.表示以孔中心线为中心修出一个小平面;通常是将小平面尺寸一并标出。
例如FILEFLAT1/2"W×1 1/2"LG或1/8"WIDE FLAT。
3) 6"SQR,正方形边长;1/4"RGH,毛坯尺寸(加工前);I"FIN,成品尺寸(自[132后]。
4)ASS'Y No.8 AS SHOWN,部件8如图所示(正面);ASS'Y No.9 OPP HAND,部件9在相反面或对称位置。
2.技术要求。
用途:表示该产品或零部件用于什么地方材料:一般在机械零件图纸上都要详细列出制造零件的材料的性能要求。
2) CHINA MATERIAL,SIMILAR TO ASTM A-148-65 GRADE 80-40。
表示:中国材料,应相当于ASTM(美国材料试验标准)A-148-65的80-40级。
制造精度:较重要的精度要求通常直接标注在视图上,其余的就给出总的要求。
3) Untolerance dimensions DIN7168 Medium,for welded parts DIN8570-B,for structural steel parts DINl8203-A,未注公差按DIN 7168取中间值,焊接结构件按DIN8570-B,普通钢结构件按DINl8203-A要求执行。
4) STRESS RELIEVE 1200°F—1 1/2 HRS,消除应力退火,温度1200°F,时问1.5小时。
5) RADIOGRAPHIC INSPECTION REQ’D AS NOTED BY “ RT ” AREA To BE RADIOGRAPHED 100%--CASTING TO BE ACCEPTABLE TO ASTM E71-64,CLASS 2,注有RT的区域须进行100%的x射线检测,结果要符合ASTME71—64二级要求,铸件才合格。
ags通用技术条件

ags通用技术条件
AGS是指Aviation Ground Services的缩写,翻译为航空地面服务。
通用技术条件(General Technical Conditions)是指适用于特定领域或行业的一组技术规范和要求。
因此,AGS通用技术条件可以理解为适用于航空地面服务领域的一组技术规范和要求。
通常,AGS通用技术条件可能包括以下方面的内容:
1. 航空地面设备和工具的技术规格:包括机械设备、车辆、液压系统、电气系统等方面的技术要求,确保航空地面服务的正常运作。
2. 安全要求和标准:包括安全操作规程、紧急情况处理流程、风险评估和管理等方面的要求,以确保航空地面服务过程中人员和设备的安全。
3. 环境保护和可持续发展要求:包括噪声控制、废水处理、废物管理等方面的要求,以减少对环境的影响,并促进可持续发展。
4. 质量管理要求:包括设备维护、检修、质量控制和认证等方面的要求,以确保航空地面服务的质量和可靠性。
需要注意的是,AGS通用技术条件可能会因不同地区、国家或组织而有所差异,具体内容可以根据相关标准和法规进行制定和执行。
- 1、下载文档前请自行甄别文档内容的完整性,平台不提供额外的编辑、内容补充、找答案等附加服务。
- 2、"仅部分预览"的文档,不可在线预览部分如存在完整性等问题,可反馈申请退款(可完整预览的文档不适用该条件!)。
- 3、如文档侵犯您的权益,请联系客服反馈,我们会尽快为您处理(人工客服工作时间:9:00-18:30)。
Biegeradius = Blechdicke Biegeradius max. Blechdicke +1mm Bohrung für Blindniet Bohrungen fluchten zueinander Bohrungen und Gewinde vor Lackierung abdecken. Bohrungen und Langloch beidseitig gratfrei Bohrungen und mit XX gekennzeichnete Flächen nicht behandelt Bolzen bei Montage einkleben Bolzen in Hebel mit Loctite 601 eingeklebt Chromoxid umlaufend __ dick Dichtscheiben entfernt Die Klebung des Bandes ist nach den Vorschriften des KlebstoffHerstellers ausgeführt. Dübelbohrung Durchgangsbohrungen dynamisch gewuchtet bei Betriebsdrehzahl e = Lückenweite Einbaulage oben Einbauvorschrift Taper-Lock Spannbuchse nach JW 416-71 Einspeisung Luft für Voreinblasung Einzelheit Energiekette erforderlichenfalls hier trennen, versatzfrei und Oberfläche eingeschliffen erst verstiften, dann verschweißen Fallenschloss Fertigungstoleranzen für Laserschnitte Flankenrichtung Fluchtungsfehler der Paßfedernuten zueinander 0,2mm! für Stifte gasdicht eingeschweißt Gefertigt aus Gegenrad-Unterlagen-Nr. geheftet Geradverzahnung gestreckle Länge Gewinde und mit XX gekennzeichnete Flächen nicht behandelt Gewindefreistich Gezeichnet: SAUGSCHIEBER ZU! (Bohrung 5.2 in POS.30 deckungsgleich mit Bohrung 5.2 in POS.40) gezogen Gleitblech Pos. 560 nach dem Ausrichten zum Quermesser mit Pos. 610 verbohren und mit Pos. 625 verschrauben. Gleitflächen gefettet graviert und schwarz ausgelegt größere Trennblechaussparung an 8 Stellen