平整机组硌印产生的原因分析及解决措施
卷取机张力辊硌印的产生原因及解决措施
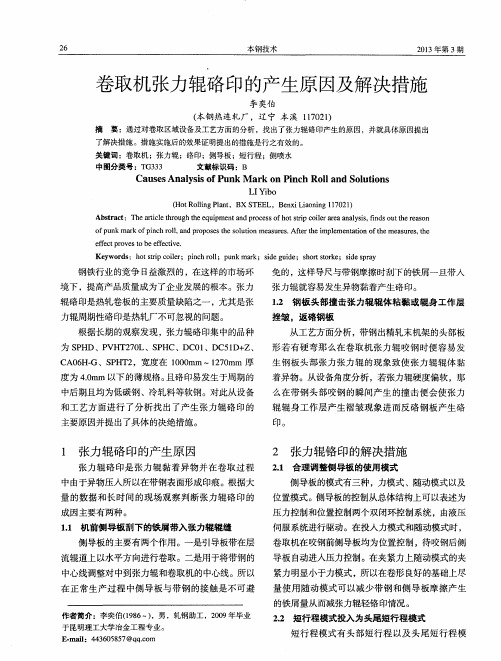
钢铁 行业 的竞 争 日益激烈 的 ,在这 样 的市场环 境 下 ,提 高产 品质量 成 为了企 业发展 的根本 。张力
免 的 ,这 样导 尺与带 钢摩擦 时 刮下 的铁 屑一 旦带 人 张 力辊就 容易 发生异物 黏着 产生硌 印 。
辊硌印是热轧卷板的主要质量缺陷之一 , 尤其是张 力辊周期性硌印是热轧厂不可忽视的问题。 根据长期 的观察发现 , 张力辊硌印集中的品种
2 张力 辊铬 印的解决措施
2 . 1 合 理调 整侧导 板 的使 用模 式 侧导 板 的模 式有三 种 ,力模 式 、随动模 式 以及
量的数据 和长 时间的现场观察判断张力辊硌 印的
成 因主要 有两 种 。 1 . 1 机 前侧 导板 刮 下 的铁 屑 带入 张力辊 辊缝
位置模式 。 侧导板的控制从总体结构上可以表述为 压力控制和位置控制两个双闭环控制系统 ,由液压 伺服系统进行驱动。在投入力模式和随动模式时 , 卷取机在咬钢前侧导板均为位置控制 , 待咬钢后侧 导板 自动进入压力控制。在夹紧力上随动模式的夹
作者简介 :李奕伯( 1 9 8 6 ~) ,男 ,轧钢助工 ,2 0 0 9年毕业 于 昆明理工大学冶金工程专业 。
E- ma i l :4 4 3 6 0 5 8 5 7 @q q . c o m
2 . 2 短行 程模 式投入 为 头尾 短 行程 模式 短行 程模 式 有 头 部 短 行 程 以及 头 尾 短行 程 模
为S P H D、P V H T 2 7 0 L、S P H C、D C 0 1 、DC 5 1 D+ Z、 C A0 6 H— G、S P H T 2 ,宽度在 1 0 0 0 mm 一1 2 7 0 mm 厚
1 . 2 钢板头部撞击张力辊辊体粘黏或辊身工作层 挫皱 。返硌钢板 从工艺方面分析,带钢出精轧末机架的头部板 形若有硬弯那么在卷取机张力辊咬钢时便容易发
影响机械加工表面质量的因素及改进措施

影响机械加工表面质量的因素及改进措施
一、影响机械加工表面质量的因素。
1.机床和刀具破损:机床体系及其附件的破损,会影响刀具的正常安
装及运行,从而产生肉眼可见的小硬斑、节肢及拉伤着痕等。
刀具的破损,也会影响机加工表面的质量,表现在高点、拉伤、刀印等方面,增大机加
工表面质量不稳定性及表面粗糙度。
2.刀具磨损:刀具工作经过一段时间,就会变得锋利变尖,从而影响
机械加工表面质量,表现为断刃,切口拉伤等,给进程控制带来更多的困难,增加了失效率。
3.加工环境:通常条件下,温度、湿度、噪声及污染等外界环境因素,会影响机械加工表面质量,表现为减少刀具的硬度,使刀具失去钝化作用,从而影响机械加工表面的质量。
4.加工工艺:在机械加工过程中,不同的加工工艺选择,会影响机械
加工表面的质量,如使用过大的进给量或过长的切削时间,则会使刀具快
速磨损,影响加工表面质量。
二、改善措施。
1.检查机床及刀具:定期检查机床及刀具的破损情况,及时更换破损
的部件,使刀具能够正常工作。
2.控制刀具磨损:合理控制刀具的运行时间,根据不同材料选择合适
的刀具,以满足机械加工工艺要求,并减少刀具的损。
平整机电火花毛化工作辊辊印成因分析及控制措施
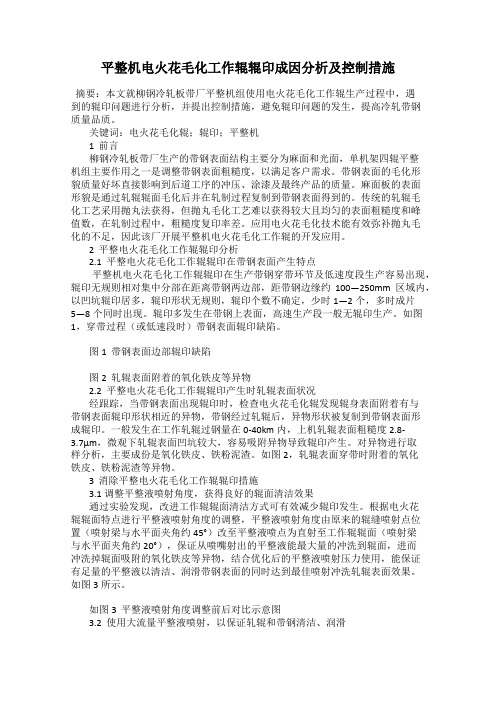
平整机电火花毛化工作辊辊印成因分析及控制措施摘要:本文就柳钢冷轧板带厂平整机组使用电火花毛化工作辊生产过程中,遇到的辊印问题进行分析,并提出控制措施,避免辊印问题的发生,提高冷轧带钢质量品质。
关键词:电火花毛化辊;辊印;平整机1 前言柳钢冷轧板带厂生产的带钢表面结构主要分为麻面和光面,单机架四辊平整机组主要作用之一是调整带钢表面粗糙度,以满足客户需求。
带钢表面的毛化形貌质量好坏直接影响到后道工序的冲压、涂漆及最终产品的质量。
麻面板的表面形貌是通过轧辊辊面毛化后并在轧制过程复制到带钢表面得到的。
传统的轧辊毛化工艺采用抛丸法获得,但抛丸毛化工艺难以获得较大且均匀的表面粗糙度和峰值数,在轧制过程中,粗糙度复印率差。
应用电火花毛化技术能有效弥补抛丸毛化的不足,因此该厂开展平整机电火花毛化工作辊的开发应用。
2 平整电火花毛化工作辊辊印分析2.1 平整电火花毛化工作辊辊印在带钢表面产生特点平整机电火花毛化工作辊辊印在生产带钢穿带环节及低速度段生产容易出现,辊印无规则相对集中分部在距离带钢两边部,距带钢边缘约100—250mm区域内,以凹坑辊印居多,辊印形状无规则,辊印个数不确定,少时1—2个,多时成片5—8个同时出现。
辊印多发生在带钢上表面,高速生产段一般无辊印生产。
如图1,穿带过程(或低速段时)带钢表面辊印缺陷。
图1 带钢表面边部辊印缺陷图2 轧辊表面附着的氧化铁皮等异物2.2 平整电火花毛化工作辊辊印产生时轧辊表面状况经跟踪,当带钢表面出现辊印时,检查电火花毛化辊发现辊身表面附着有与带钢表面辊印形状相近的异物,带钢经过轧辊后,异物形状被复制到带钢表面形成辊印。
一般发生在工作轧辊过钢量在0-40km内,上机轧辊表面粗糙度2.8-3.7μm,微观下轧辊表面凹坑较大,容易吸附异物导致辊印产生。
对异物进行取样分析,主要成份是氧化铁皮、铁粉泥渣。
如图2,轧辊表面穿带时附着的氧化铁皮、铁粉泥渣等异物。
3 消除平整电火花毛化工作辊辊印措施3.1 调整平整液喷射角度,获得良好的辊面清洁效果通过实验发现,改进工作辊辊面清洁方式可有效减少辊印发生。
平整机组带材表面横振纹产生机理与抑制对策
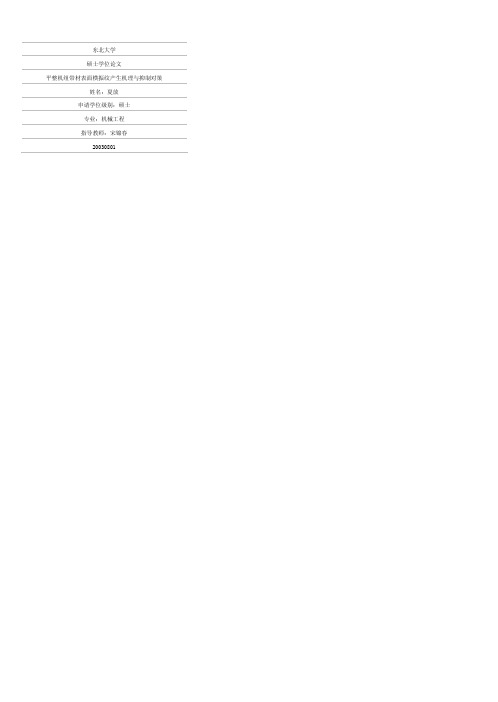
东北大学硕士学位论文平整机组带材表面横振纹产生机理与抑制对策姓名:夏放申请学位级别:硕士专业:机械工程指导教师:宋锦春20030801东北大学硕士学住论文平整机组带材表面横振纹产生机理与抑振对策摘要本篇论文主要叙述了CM04平整机在平整轧钢板的过程中,由于系统中各运动部件存在缺陷而产生冲击振动激起系统固有频率导致该机组不能正常生产或生产出钢板表面出现“横振纹”的不合格产品。
通过第二章中第一节简述了振动信号处理方法,了解如何从时域信号转换成频域信号,在时域、频域中辨识旋转运动部件存在故障的特征频率:第二节介绍了轴承故障产生的机理,利用振动分析法和磨损分析法的综合诊断来确诊工作辊轴承外圈出现疲劳剥落的故障:第三节,简述了机架牌坊间隙过大造成振动的传递使工作辊的垂直振动值偏大;第四节提供了传动侧的支撑轴承磨损(或游隙过大),扁头套与扁头之间配合不当或磨损造成间隙过大,齿式联轴器的内齿、外齿之间啮合不良或间隙不当等导致冲击激起系统的共振;第五节描述了在静态状态下,利用外激励的方式测取系统的固有频率与传动侧存在故障时,冲击能量过大激起系统固有频率的对比。
第六节叙述串联电机可控硅变频、变速的原理,并由此产生的电网谐波对平整机的影响,最后一节总结平整机回转运动部件出现故障对轧板质量的影响,并提出判断故障的依据和采取的对策措施。
东北大学硕士学位论文ABSTRACTABSTRACTThispaperdeclaresthattheunqualifiedrollingproductionwasissuedduetothechatterofthesteelplateduringCM04rollingcausingbytheinherentdefaultsoftherunningpartsandpulsevibration.Thesignalprocessingmethodwasintroducedinthefirstpartofchaptertwoandthefrequencyfeatureextractionidentificationtechnologywasdeclaredforthefaultdiagnosisofrotatingparts.Thefaultmechanismoftherollingbearingwasintroducedinthesecondpartaswellasthecomplicateddiagnosisfortheouterringfaultslocationoftheworkrollusingvibrationanalysisandwearparticlesanalysis.ThesituationoftheextraintervaloftherollingflameWaSbrieflyintroducedinthethirdpartleadingtotheseriousvibrationintheverticaldimctionoftheworkroll.Thereasonanalysisoftheresonancewasillustratedinthefourthpartsuchastheinappropriateinsmllationintervalandthewearintervalofthebeatingofthebackrollaswellastheabnormalgeartransmission.ThecomparisonidentificationmethodWasdemonstratedinthenextpartusingtheouterpulseexcitingmethodfortheinherentfrequencymeasuringagainstthefaultsituationofthedriveside.Thetheoryoftheinvertermotorwasintroducedinthesixthpartandtheelectricharmonicinfluencetotherollingmachine.ThesummaryWas,presentedatlastandthefaultdiagnosistechnologyandthesolutionfortheproductionqualityimprovement.11声明本人声明所呈交的学位论文是在导师的指导下完成的。
平整机支承辊振纹产生机理及抑制措施
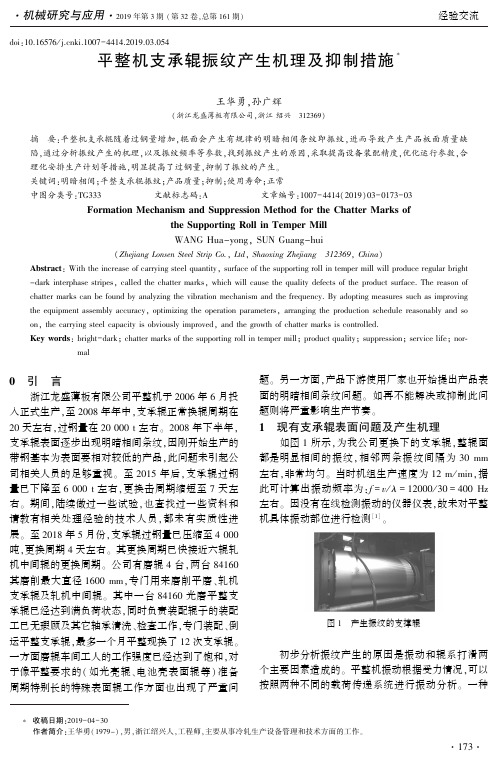
摘 要:平整机支承辊随着过钢量增加ꎬ辊面会产生有规律的明暗相间条纹即振纹ꎬ进而导致产生产品板面质量缺
陷ꎬ通过分析振纹产生的机理ꎬ以及振纹频率等参数ꎬ找到振纹产生的原因ꎬ采取提高设备装配精度ꎬ优化运行参数ꎬ合
理化安排生产计划等措施ꎬ明显提高了过钢量ꎬ抑制了振纹的产生ꎮ
机具体振动部位进行检测 [1] ꎮ
吨ꎬ更换周期 4 天左右ꎮ 其更换周期已快接近六辊轧
机中间辊的更换周期ꎮ 公司有磨辊 4 台ꎬ两台 84160
其磨削最大直径 1600 mmꎬ专门用来磨削平磨、轧机
支承辊及轧机中间辊ꎮ 其中一台 84160 光磨平整支
承辊已经达到满负荷状态ꎬ同时负责装配辊子的装配
工已无瑕顾及其它轴承清洗、检查工作ꎬ专门装配、倒
辊等ꎬ供电电网的频率ꎬ变频控制的调节频率和特征
2019 年第 3 期 ( 第 32 卷ꎬ总第 161 期) 机械研究与应用
推拉力都是与工作辊中心重合ꎬ又花费 50 万重新设
计制造了一台换辊车ꎬ避免换辊车推拉力与工作辊中
频率ꎬ主传动机械扭转系统的固有频率都会产生振动生产ꎬ至 2008 年年中ꎬ支承辊正常换辊周期在
题ꎮ 另一方面ꎬ产品下游使用厂家也开始提出产品表
面的明暗相间条纹问题ꎮ 如再不能解决或抑制此问
题则将严重影响生产节奏ꎮ
20 天左右ꎬ过钢量在 20 000 t 左右ꎮ 2008 年下半年ꎬ
1 现有支承辊表面问题及产生机理
带钢基本为表面要相对较低的产品ꎬ此问题未引起公
the Supporting Roll in Temper Mill
WANG Hua -yongꎬ SUN Guang -hui
( Zhejiang Lonsen Steel Strip Co.ꎬ Ltdꎬ Shaoxing Zhejiang 312369ꎬ China)
冷轧带钢平整时横折印缺陷的产生机理及消除措施

第43卷 第1期 2008年1月钢铁Iron and Steel Vol.43,No.1J anuary 2008冷轧带钢平整时横折印缺陷的产生机理及消除措施马庆龙1, 杨利坡1, 彭 艳1, 刘宏民1, 吴 斌2(1.燕山大学轧制设备及成套技术教育部工程研究中心,河北秦皇岛066004;2.凌源钢铁股份有限责任公司中宽冷带厂,辽宁凌源122500)摘 要:冷轧退火后的带钢在平整过程中产生横折印缺陷,严重影响平整后带钢的表面质量及其力学性能。
通过分析带钢经过张力辊(S 辊)时的受力过程,研究横折印缺陷的产生机理和影响因素,认为退火后的屈服平台和平整机入口前的带钢表面拉应力过大是带钢表面产生横折印缺陷的根本原因。
制定合理的伸长率和张力制度,严格来料质量要求,可以避免横折印缺陷的产生,提高平整带钢的表面质量。
关键词:冷轧带钢;平整;横折印缺陷;张力;伸长率中图分类号:T G335.12 文献标识码:A 文章编号:04492749X (2008)0120045205Form ation Mechanism and E limination of CrossB reaks of Cold Rolled Strip During T emper R ollingMA Qing 2long 1, YAN G Li 2po 1, PEN G Yan 1, L IU Hong 2min 1, WU Bin 2(cation Ministry Engineering Research Center of Rolling Equipment and Complete Technology ,Yanshan University ,Qinhuangdao 066004,Hebei ,China ; 2.Cold Strip Factory ,Lingyuan Ironand Steel Group Co.,Ltd.,Lingyuan 122500,Liaoning ,China )Abstract :Cross breaks are formed on the surface of cold rolled and tempered strip during temper rolling ,which in 2fluence the surface quality and mechanical characteristics of the temper rolled strip.By analyzing the loading of strip at S rolls and formation mechanism and influencing factors of cross breaks ,it was concluded that the main cause of cross breaks is the yield point elongation and the high tensile stress at the entrance of temper rolling mill.It is neces 2sary to establish rational elongation and tension ,control the quality of coming strip strictly ,to avoid cross breaks ,improve the surface quality of strip.K ey w ords :cold strip ;temper rolling ;cross breaks ;tension ;elongation基金项目:国家自然科学基金资助项目(50675186);河北省重大自然科学基金资助项目(E2006001038)作者简介:马庆龙(19772),男,博士生; E 2m ail :jyqlma @ ; 修订日期:2007205214 燕山大学为凌源钢铁股份有限责任公司中宽冷带厂研制了900mm 平整机组。
平整机组产生钢卷层间擦伤的原因及解决措施

平整机组产生钢卷层间擦伤的原因及解决措施?26?2009年第3期平整机组产生钢卷层间擦伤的原因及解决措施热连轧厂高建钢摘要平整机组自投产以来一直存在程度不等的钢卷层间表面擦伤问题.依钢种,规格不同,表面擦,划伤程度不等.表面擦划伤的存在严重影响到热连轧的产品形象,给用户的生产和使用带来不便.特别是薄规格集装箱板和供冷轧的不锈钢热轧卷表面擦伤问题尤为突出.分析解决平整机组造成的钢卷表面擦划伤,是改善平整钢卷表面质量的关键问题之一.通过对工艺,操作方面的探讨,研究并采取有针对性的措施,各工序问必须遵循"张力渐小"原则,热轧卷表面擦伤问题得到很好的控制,下工序的反映也证实了表面擦划伤缺陷呈明显减少的趋势. 关键词平整层间擦划伤张力渐小原则1平整机组生产现状目前平整机组在平整,重卷生产过程中,当穿带完成后,开卷卷筒,卷取卷筒将对带钢施以一定的开卷张力,卷取张力,然后逐渐升速实现正常的通板作业.需平整的钢卷则在升速前,升速中适当施以平整机轧制压力及弯辊力,以保证工艺要求的平整变形率并保证板形平直.调查发现作业过程中装在开卷卷筒上的钢卷在建张,升速,通板过程中,常出现钢卷逐渐卷紧,钢卷端部标记逐渐出现扭曲歪斜的现象,说明钢卷层间存在相对滑动,见图1.钢板的层间滑动势必造成不同程度的表面擦划伤.图l钢卷端部标记出现扭曲歪斜2影响因素分析嚣热轧钢卷"较松",存在层间隙.特别是稳定.钢卷卷紧的过程使钢卷内的"层间不锈钢卷经退火,钢卷的内,外圈更加"松",隙"变小,钢板发生层间的滑动,造成钢板表太钢科技?27?面擦划伤.钢卷端部标记逐渐出现扭曲,歪斜,变形,说明此过程的存在.热轧生产时的卷取温度与平整工序要求的上料温度差异及钢质合金含量的增加,会增加热轧钢卷冷却后"变松"的趋势.2.1钢种线膨胀系数的影响热轧生产时一般卷取温度在600~750~C左右,平整上料温度为常温.热轧钢卷在冷却过程中钢种线膨胀系数造成厚度变化,影响钢卷的层间隙.合金含量增加线膨胀系数增大.钢种线膨胀系数如表1所示.裹1钢种线膨胀系数3擦划伤机理现场调查情况与此分析相一致.不锈钢卷"较松".2.2厚度规格的差异厚度越薄,带钢越长,相对钢卷卷取的"层"数越多.直径越大,"层"数越多,钢卷累计层间隙越大.因此薄规格带钢外径越大,钢卷越"松".2.3退火工序的影响按照下工序的要求,热轧不锈钢卷必须经过退火工序后方可供冷轧厂.在钢卷退火的升温及冷却过程中钢卷各部位受不均匀热影响,使得钢卷内,外圈在退火完成后出现严重的"松卷",层间隙进一步加大,如图2所示. 2.4热轧卷取张力与平整开卷张力的影响热轧卷取张力实际生产中一般控制在5—20MPa,即0.5—2kg/mm,而平整开卷张力实际生产中一般控制在2~6kg/mm.平整开卷张力大于热轧卷取张力,后工序张力大予前工序张力显然不合理.图2退火工序后钢卷出现严重的"松卷"如何尽可能实现轧线卷取张力与平整开卷张力很好的匹配,最大程度减少平整钢卷的表面擦划伤.我们对生产的各环节的工艺,操作,控制结合钢质,规格进行了详尽的分析.热轧生产卷取温度与平整上料温度的温度差异,钢质合金含量的增加,退火工序钢卷各部分温度差异,会增加热轧钢卷"变松"的趋势,薄规格带钢表现尤为明显.轧线生产过程中操作人员必须根据实际?28?2009年第3期轧制板形情况随时对轧机进行调整,以确保实现板形平直.因此轧钢生产中卷取张力不宜过大,否则不利于操作人员对板形的观察, 调整.热轧卷取张力5—20MPa=0.5—2kg/mm,既方便操作人员对板形的观察,调整又可保证良好的卷形.目前是比较合适的,不宜再度降低.因此张力匹配应重点分析平整机组开卷张力的适当减小.从平整机组实际情况分析,平整张力设定单位值为kg/mm,正常生产时为了保证良好的平整效果,保证较高的效率,实际生产中平整机组的前后张力实际给定值较大.小张力卷取的高温热轧钢卷,经平整机组大的开卷张力必然将相对"较松"的钢卷"卷紧",势必造成带钢的层间滑动,从而造成带钢表面程度不等的层间擦划伤.分析产生带钢层间擦划伤的各种因素,可以看出工序问张力不匹配是第一要因.4措施鉴于各生产环节的实际情况,我们采取了以下措施:(1)轧线生产过程中操作人员在便于板形观察,调整的前提下,卷取岗位人员应采用较大的卷取张力≥1.5kg/mm,保证卷紧,卷齐,卷形良好.(2)对极易产生层间表面擦划伤的退火钢卷和42.Omm规格钢卷,必须选择较小的开卷单位张力,一般采用<1.5kg/mm. (3)退火钢卷和≤2.Omm规格钢卷,选择大张力模式下的实际小开卷张力作业控制.目的是采用小加速度值作业,减缓升,降速时的速度突变.(4)将原先的平整通板速度600m/min调整为<300m/min.(5)加强平整机组在线表面质量检查,发现问题及时进行调整.5效果措施实施后,钢卷端部标记扭曲现象未再发生,钢卷表面擦划伤缺陷明显减少.通过几个月的实际生产验证,我们采取的针对性措施是有效的.下工序的反映也证实了表面擦划伤缺陷呈明显减少的趋势.实践证明,上下工序间张力合理匹配是解决钢板层间表面擦划伤的有效途径.表面擦划伤缺陷明显减少,但实际生产中并未达到完全杜绝的目标.还需在今后的工艺,操作方面进一步探讨,研究.相信经过各工序,各专业的共同努力,平整机组产品, 冷轧用料的层间表面擦划伤会得到进一步改善,直至最终消失.6结论在板带生产过程中,热轧,横切,平整,酸洗,冷轧,退火,涂层,镀锌……各工序问必须遵循"张力渐小"原则.即:下一工序的开卷张力不得大于上一工序的卷取张力.否则,下一工序建张过程大的开卷张力必然会将上一工序较小张力卷取的带钢"卷紧",此过程发生带钢层间滑动,极易造成带钢表面的层间擦划伤.参考文献[1]李春胜.《钢铁材料手册》[M].江西科学技术出版社,2004:36—38。
H0475710104平整机横向条纹产生原因及消除研究
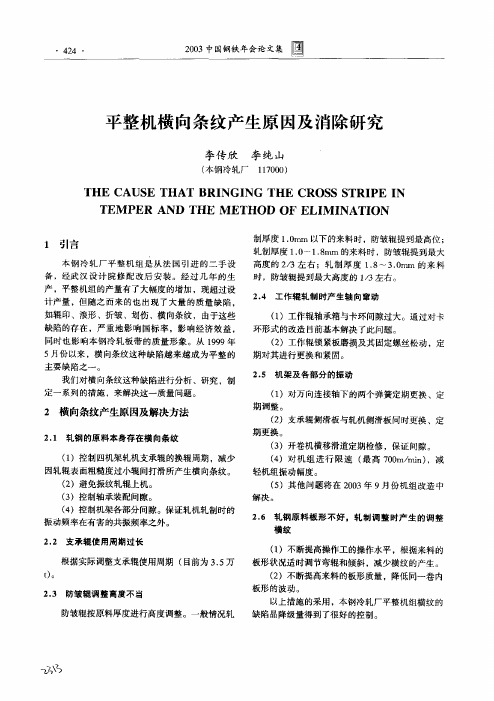
2 中钢年论集回 0 国铁会 文 0 3
平整机横向条纹产生原因及消除研究
李传欣 李纯山
( 本钢冷轧厂 170 100
T HE CAUS THAT NGI E BRI NG HE T CROS S S TRI E P I N
T M ER P E AND HE T MET HOD EL M I OF I NAT ON I
时,防皱辊提到最大高度的 1 乃左右。
计产量, 但随之而来的也出现了大量的质量缺陷, 如辊印、 浪形、 折皱、 划伤、 条纹, 横向 由于这些 缺陷的存在, 严重地影响国标率, 影响经济效益, 同时也影响本钢冷轧板带的质量形象。 19 年 从 99 5 月份以 来, 横向 条纹这种缺陷越来越成为平整的
26 轧钢原料板形不好,轧制调整时产生的调整 .
横纹
支承辊使用周期过长
t)
0
根据实际调整支承辊使用周期 ( 前为 35 目 .万
2.
1 }
防皱辊调整高度不当
防皱辊按原料水平, 根据来料的 板形状况适时调节弯辊和 倾斜, 减少横纹的产生。 ()不断提高来料的板形质量,降低同一卷内 2 板形的波动。 以上措施的 采用, 本钢冷轧厂平整机组横纹的 缺陷品降级量得到了 很好的控制。
25 机架及各部分的振动 . () 连接轴下的两个弹簧定期更换、 1 对万向 定
期调整。
2 横向条纹产生原因及解决方法
21 轧钢的原料本身存在横向条纹 . () 机架轧机支承辊的换辊周期, 1 控制四 减少 因 轧辊表面粗糙度过小辊间打滑所产生横向 条纹。 ()避免振纹轧辊上机。 2 ()控制轴承装配间隙。 3 ()控制机架各部分间隙。保证轧机轧制时的 4 振动频率在有害的共振频率之外。
平整机的原理分析及其缺陷与对策探讨

平整机的原理分析及其缺陷与对策探讨作者:张杰来源:《读天下》2019年第17期摘要:我国钢铁行业是经济建设和国家发展的基础,钢铁企业要不断调整产品结构和进行产品的更新换代才能够实现跨越式发展,平整机技术的加入让钢铁企业更加具有活力,平整机会因其存在一定缺陷导致钢铁企业在生产的过程中受到影响,因此分析其工作原理和找到相应的问题解决对策就显得十分必要。
本文重点分析和研究了平整机的原理和结构,平整机能够对带钢实施平整工艺轧制,进而可以改善板形,经过平整轧制来最大程度控制带钢表面粗糙度,消除带钢屈服应力平台,对于钢铁企业来说可以提高其在激烈市场竞争中的竞争力和带钢的整体质量。
关键词:平整机;轧制线;带钢一、平整机的作用与原理平整机虽然各个行业构成有着不同,但是主要部件大同小异,钢铁行业平整机一般是由工作辊弯辊装置、下支承辊推上装置、上支承辊平衡装置、工作辊快速更换装置、下支承辊传动装置等几部分组成。
工作辊弯辊的主要作用就是让辊缝在规定范围内和板形相适应,上下工作辊需要借助弯辊缸来实现产生负凸度以及正凸度,来解决生产过程中的带钢板形缺陷问题。
轧制力需要下支承辊轴承座传递到推上油缸的压力板上,经过安装的机器上的压力传感器测出轧制力,下辊位置则需要根据机器上传感器来进行测定进而实现控制功能。
上辊位置的需要机器上部装置的测量并对其实行控制,能够在作业的过程中确保带钢能够维持恒定的轧制线高度。
平整机在钢铁企业中为了获得最大的生产效率使其配备一套工作辊快速更换装置,进而可以实现在作业时带钢在机架中能够最快速的自动更换两个工作辊,并且能够尽量将时间控制在两分钟之内。
平整机通常需要由下支撑辊并凭借大小不一的齿轮和万向轴来实现传动,这种简约的结构布置可以最大程度促使平整机工作辊快速更换。
平整机在出口的位置安装了大功率的喷吹装置,因此能够将因为轧制而产生的许多粘在带钢表面的平整介质给吹去。
平整机的重要作用就是钢铁企业实现对带钢平整工艺轧制的目的,最终能够做到对带钢板型的改善,以及应用平整机来控制带钢表面的粗糙度,让带钢表面能够满足规格要求,可以解决带钢因为屈服应力平台而造成的各种质量问题。
机械加工过程中的表面质量与刮痕分析
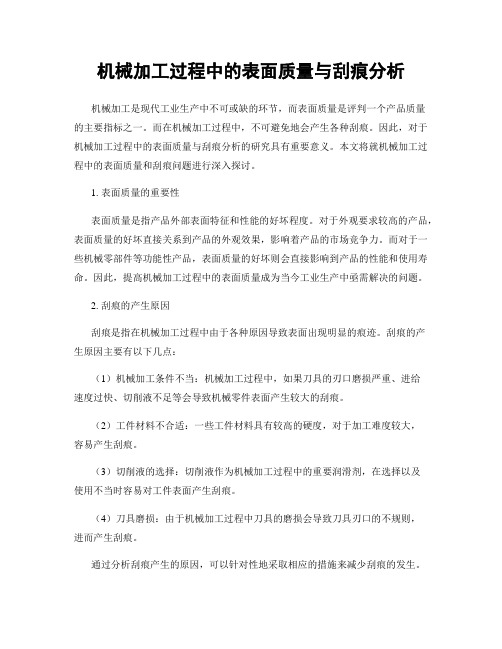
机械加工过程中的表面质量与刮痕分析机械加工是现代工业生产中不可或缺的环节,而表面质量是评判一个产品质量的主要指标之一。
而在机械加工过程中,不可避免地会产生各种刮痕。
因此,对于机械加工过程中的表面质量与刮痕分析的研究具有重要意义。
本文将就机械加工过程中的表面质量和刮痕问题进行深入探讨。
1. 表面质量的重要性表面质量是指产品外部表面特征和性能的好坏程度。
对于外观要求较高的产品,表面质量的好坏直接关系到产品的外观效果,影响着产品的市场竞争力。
而对于一些机械零部件等功能性产品,表面质量的好坏则会直接影响到产品的性能和使用寿命。
因此,提高机械加工过程中的表面质量成为当今工业生产中亟需解决的问题。
2. 刮痕的产生原因刮痕是指在机械加工过程中由于各种原因导致表面出现明显的痕迹。
刮痕的产生原因主要有以下几点:(1)机械加工条件不当:机械加工过程中,如果刀具的刃口磨损严重、进给速度过快、切削液不足等会导致机械零件表面产生较大的刮痕。
(2)工件材料不合适:一些工件材料具有较高的硬度,对于加工难度较大,容易产生刮痕。
(3)切削液的选择:切削液作为机械加工过程中的重要润滑剂,在选择以及使用不当时容易对工件表面产生刮痕。
(4)刀具磨损:由于机械加工过程中刀具的磨损会导致刀具刃口的不规则,进而产生刮痕。
通过分析刮痕产生的原因,可以针对性地采取相应的措施来减少刮痕的发生。
3. 表面质量评估方法对于机械零部件等工件的表面质量进行评估,可以采用以下几种方法:(1)肉眼观察法:即通过直接肉眼观察工件表面的质量进行评估。
这种方法直观简便,但是受到人眼的主观因素影响较大。
(2)光学测量法:通过光学显微镜、投影仪等光学设备对工件表面进行放大观察和测量。
这种方法可以较为准确地评估表面质量,但是对设备的要求较高。
(3)表面粗糙度测量法:通过测量工件表面的粗糙度参数来评估表面质量。
常用的表面粗糙度参数有Ra、Rz等。
这种方法简便易行,但是无法直接评估表面的外观质量。
热连轧平整机板形缺陷分析与对策
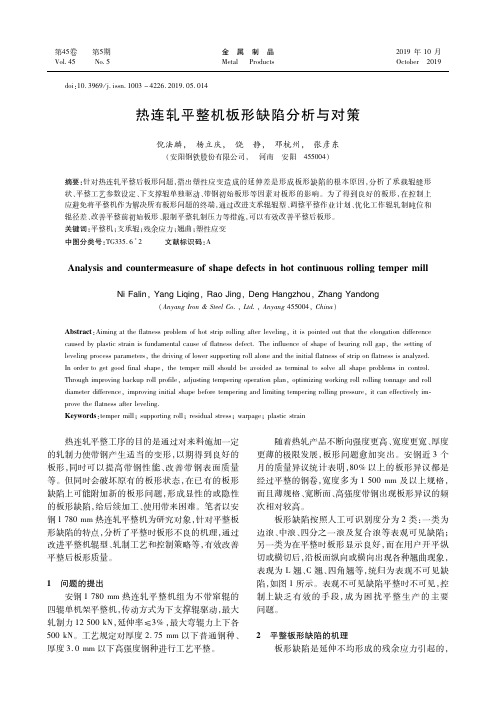
金 属 制 品 Metal Products
doi:10.3969/j.issn.1003-4226.2019.05.014
2019年 10月 October 2019
热连轧平整机板形缺陷分析与对策
倪法麟, 杨立庆, 饶 静, 邓杭州, 张彦东
(安阳钢铁股份有限公司, 河南 安阳 455004)
板形缺陷按照人工可识别度分为 2类:一类为 边浪、中浪、四分之一浪及复合浪等表观可见缺陷; 另一类为在平整时板形显示良好,而在用户开平纵 切或横切后,沿板面纵向或横向出现各种翘曲现象, 表现为 L翘、C翘、四角翘等,统归为表观不可见缺 陷,如图 1所示。表观不可见缺陷平整时不可见,控 制上缺乏 有 效 的 手 段,成 为 困 扰 平 整 生 产 的 主 要 问题。
表观可见板形缺陷主要控制手段就是通过调 整辊型、轧制压力、弯辊调节、张力调节等改善承载 辊缝形状,减小带钢的塑性应变差。辊型的优劣是 决定板形控制能力的关键因素,良好的辊型设计可 以提高辊缝的横向刚度,减少因轧件强度或宽度变 化带来的辊缝形状波动,同时也可以提高弯辊的板 形控制能力。当轧辊出现严重的偏磨损或局部磨 损时,辊 缝 形 状 被 局 部 破 坏,以 上 板 形 调 控 方 法 无效。
1 问题的提出 安钢 1780mm热连轧平整机组为不带窜辊的
四辊单机架平整机,传动方式为下支撑辊驱动,最大 轧制力 12500kN,延伸率≤3%,最大弯辊力上下各 500kN。工艺规定对厚度 2.75mm以下普通钢种、 厚度 3.0mm以下高强度钢种进行工艺平整。
随着热轧产品不断向强度更高、宽度更宽、厚度 更薄的极限发展,板形问题愈加突出。安钢近 3个 月的质量异议统计表明,80%以上的板形异议都是 经过平整的钢卷,宽度多为 1500mm及以上规格, 而且薄规格、宽断面、高强度带钢出现板形异议的频 次相对较高。
平整分卷机组常见表面质量缺陷产生原因及控制措施
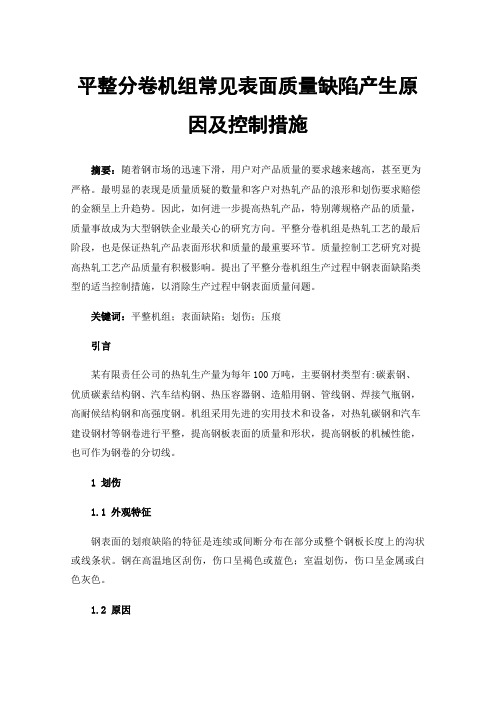
平整分卷机组常见表面质量缺陷产生原因及控制措施摘要:随着钢市场的迅速下滑,用户对产品质量的要求越来越高,甚至更为严格。
最明显的表现是质量质疑的数量和客户对热轧产品的浪形和划伤要求赔偿的金额呈上升趋势。
因此,如何进一步提高热轧产品,特别薄规格产品的质量,质量事故成为大型钢铁企业最关心的研究方向。
平整分卷机组是热轧工艺的最后阶段,也是保证热轧产品表面形状和质量的最重要环节。
质量控制工艺研究对提高热轧工艺产品质量有积极影响。
提出了平整分卷机组生产过程中钢表面缺陷类型的适当控制措施,以消除生产过程中钢表面质量问题。
关键词:平整机组;表面缺陷;划伤;压痕引言某有限责任公司的热轧生产量为每年100万吨,主要钢材类型有:碳素钢、优质碳素结构钢、汽车结构钢、热压容器钢、造船用钢、管线钢、焊接气瓶钢,高耐候结构钢和高强度钢。
机组采用先进的实用技术和设备,对热轧碳钢和汽车建设钢材等钢卷进行平整,提高钢板表面的质量和形状,提高钢板的机械性能,也可作为钢卷的分切线。
1划伤1.1外观特征钢表面的划痕缺陷的特征是连续或间断分布在部分或整个钢板长度上的沟状或线条状。
钢在高温地区刮伤,伤口呈褐色或蓝色;室温划伤,伤口呈金属或白色灰色。
1.2原因在平整生产过程中,辊表面状况不佳,粗糙度低或硬材料高,导致钢锈蚀。
如果平整机前后段的应力不匹配,或者原料卷松卷,张力过大或太小,可能导致带钢在生产过程中张力损失,可能导致带钢表面擦伤。
轧制一定数量的带钢后,当带钢宽度规范变化时,带钢边缘磨损区的相应位置容易拉伤。
切割小体积后,有必要再用头用残馀物穿过钢此外,带钢孔沿带钢的宽度略微弯曲,因此需要重复压力头操作,这很容易导致表面出现划伤。
带钢甩尾后尾处于下扣状态。
对于高强度钢和厚带钢,很难用矫直辊尾压平,造成尾部下扣状态,造成表面划伤。
1.3控制措施确保设备工作正常。
保证所有钢通道、矫直辊、夹送辊和助卷辊的正常运转,消除机械设备的锐角,避免与钢板接触。
谈影响机械加工表面质量的因素与应对措施
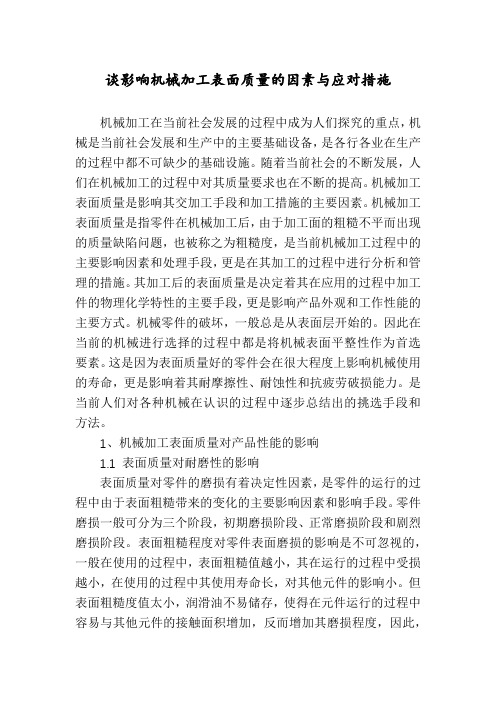
谈影响机械加工表面质量的因素与应对措施机械加工在当前社会发展的过程中成为人们探究的重点,机械是当前社会发展和生产中的主要基础设备,是各行各业在生产的过程中都不可缺少的基础设施。
随着当前社会的不断发展,人们在机械加工的过程中对其质量要求也在不断的提高。
机械加工表面质量是影响其交加工手段和加工措施的主要因素。
机械加工表面质量是指零件在机械加工后,由于加工面的粗糙不平而出现的质量缺陷问题,也被称之为粗糙度,是当前机械加工过程中的主要影响因素和处理手段,更是在其加工的过程中进行分析和管理的措施。
其加工后的表面质量是决定着其在应用的过程中加工件的物理化学特性的主要手段,更是影响产品外观和工作性能的主要方式。
机械零件的破坏,一般总是从表面层开始的。
因此在当前的机械进行选择的过程中都是将机械表面平整性作为首选要素。
这是因为表面质量好的零件会在很大程度上影响机械使用的寿命,更是影响着其耐摩擦性、耐蚀性和抗疲劳破损能力。
是当前人们对各种机械在认识的过程中逐步总结出的挑选手段和方法。
1、机械加工表面质量对产品性能的影响1.1 表面质量对耐磨性的影响表面质量对零件的磨损有着决定性因素,是零件的运行的过程中由于表面粗糙带来的变化的主要影响因素和影响手段。
零件磨损一般可分为三个阶段,初期磨损阶段、正常磨损阶段和剧烈磨损阶段。
表面粗糙程度对零件表面磨损的影响是不可忽视的,一般在使用的过程中,表面粗糙值越小,其在运行的过程中受损越小,在使用的过程中其使用寿命长,对其他元件的影响小。
但表面粗糙度值太小,润滑油不易储存,使得在元件运行的过程中容易与其他元件的接触面积增加,反而增加其磨损程度,因此,在元件制造的过程中要应用各种技术手段进行分析与设计,设计出相应的摩擦值。
1.2表面质量对疲劳强度的影响在金属受到各种因素和荷载的作用之后会产生相应的变形和冷热交替模式,这就使得仅属于产生疲劳强度。
因此,零件的表面质量对疲劳强度影响很大。
轧机标定辊印的成因及解决办法

© 1994-2009 China Academic Journal Electronic Publishing House. All rights reserved. 轧机标定辊印的成因及解决办法戢 亮 一、问题的提出西南铝业集团公司2号1850轧机的电控系统(包括厚度控制系统在内)全部由ABB 公司提供,无论硬件还是软件都是相当成熟的。
但是,随着客户对产品质量的要求越来越高,近年来产品表面质量异议率不断升高。
在对产品表面质量异议的研究中发现,有相当部分可以归结为轧辊的标定辊印。
这种轧辊标定时,在工作辊表面180°对应方向上产生的两条间断或连续性的辊印,严重影响PS 板、瓶盖料、8011、涂层板基等高表面要求产品的生产。
轧机换辊频繁,降低生产效率,经常造成轧机待辊现象。
二、标定过程分析现代轧机的厚度控制系统,大多采用的是电液伺服系统。
为了测量出高精度的辊缝和液压缸位置,测量系统大多数采用的是数字式增量测量仪。
只要轧机机架条件发生了变化(特别是换辊或重新调整轧线后),都会导致测量系统零点发生漂移。
因此,高效率的自动标定系统,对于现代轧机来说是必不可少的。
轧机辊系见图1。
图1 轧机辊系示意图在对轧机自动标定程序进行深入分析后,得到了自动标定执行的顺序流程图(图2)。
基于对标定过程的分析,得出这样的结论:标定辊印的形成肯定是由于接触和力的作用造成的,而且多是在静止状态下的受力造成的。
三、试验及结果在排除了轧制力检测不准,导致标定压力过大的因素后,决定通过修改标定程序,使整个标定程序分解执行(因为整个标定过程的时间很短),然后抽辊观察辊印究竟形成在哪个环节。
通过多次试验,并在试验过程中中断标定执行后立即检测轧辊表面质量,排除了压下过程中,支撑辊和工作辊接触瞬间和工作辊和工作辊接触瞬间的两个标定过程中最有可能产生辊印的时刻。
最终发现影响产品质量的辊印,出现在辊缝打开环节的频图2 自动标定顺序次最高。
平锻机常见问题及解决措施
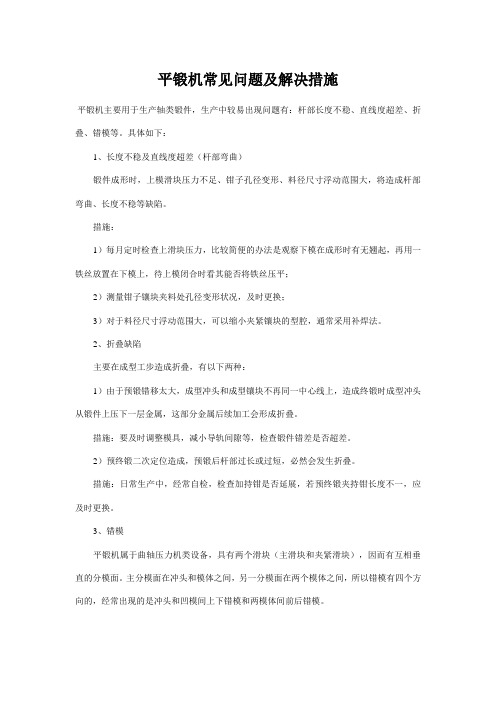
平锻机常见问题及解决措施平锻机主要用于生产轴类锻件,生产中较易出现问题有:杆部长度不稳、直线度超差、折叠、错模等。
具体如下:1、长度不稳及直线度超差(杆部弯曲)锻件成形时,上模滑块压力不足、钳子孔径变形、料径尺寸浮动范围大,将造成杆部弯曲、长度不稳等缺陷。
措施:1)每月定时检查上滑块压力,比较简便的办法是观察下模在成形时有无翘起,再用一铁丝放置在下模上,待上模闭合时看其能否将铁丝压平;2)测量钳子镶块夹料处孔径变形状况,及时更换;3)对于料径尺寸浮动范围大,可以缩小夹紧镶块的型腔,通常采用补焊法。
2、折叠缺陷主要在成型工步造成折叠,有以下两种:1)由于预锻错移太大,成型冲头和成型镶块不再同一中心线上,造成终锻时成型冲头从锻件上压下一层金属,这部分金属后续加工会形成折叠。
措施:要及时调整模具,减小导轨间隙等,检查锻件错差是否超差。
2)预终锻二次定位造成,预锻后杆部过长或过短,必然会发生折叠。
措施:日常生产中,经常自检,检查加持钳是否延展,若预终锻夹持钳长度不一,应及时更换。
3、错模平锻机属于曲轴压力机类设备,具有两个滑块(主滑块和夹紧滑块),因而有互相垂直的分模面。
主分模面在冲头和模体之间,另一分模面在两个模体之间,所以错模有四个方向的,经常出现的是冲头和凹模间上下错模和两模体间前后错模。
1)上下错模。
上下错模靠调节夹持器高度来实现,夹持器固定在上下两块带坡度(1: 10)的垫板间,确定了错移量之后,通过两垫板的一进一出便可实现冲头对准模体。
2)前后错模。
上滑块和固定下模体的后挡板存在安装误差,现有模体没有调节前后错移的机构,故而只能在成形镶块后加垫片进行调整。
三、平整板型不良的原因分析
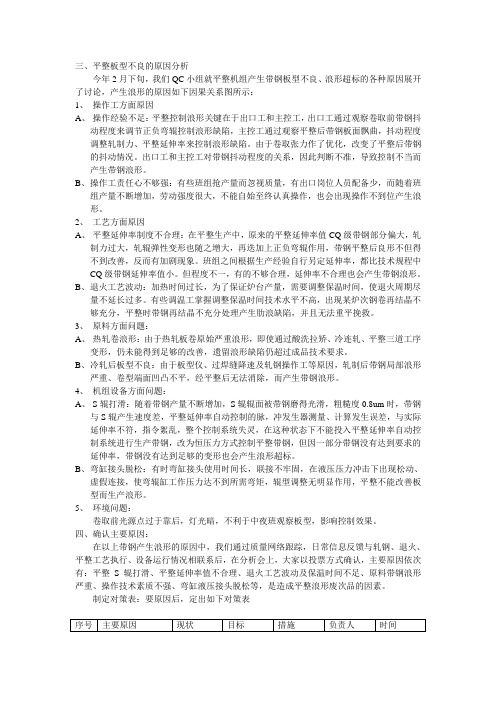
三、平整板型不良的原因分析今年2月下旬,我们QC小组就平整机组产生带钢板型不良、浪形超标的各种原因展开了讨论,产生浪形的原因如下因果关系图所示:1、操作工方面原因A、操作经验不足:平整控制浪形关键在于出口工和主控工,出口工通过观察卷取前带钢抖动程度来调节正负弯辊控制浪形缺陷,主控工通过观察平整后带钢板面飘曲,抖动程度调整轧制力、平整延伸率来控制浪形缺陷。
由于卷取张力作了优化,改变了平整后带钢的抖动情况。
出口工和主控工对带钢抖动程度的关系,因此判断不准,导致控制不当而产生带钢浪形。
B、操作工责任心不够强:有些班组抢产量而忽视质量,有出口岗位人员配备少,而随着班组产量不断增加,劳动强度很大,不能自始至终认真操作,也会出现操作不到位产生浪形。
2、工艺方面原因A、平整延伸率制度不合理:在平整生产中,原来的平整延伸率值CQ级带钢部分偏大,轧制力过大,轧辊弹性变形也随之增大,再迭加上正负弯辊作用,带钢平整后良形不但得不到改善,反而有加剧现象。
班组之间根据生产经验自行另定延伸率,都比技术规程中CQ级带钢延伸率值小。
但程度不一,有的不够合理,延伸率不合理也会产生带钢浪形。
B、退火工艺波动:加热时间过长,为了保证炉台产量,需要调整保温时间,使退火周期尽量不延长过多。
有些调温工掌握调整保温时间技术水平不高,出现某炉次钢卷再结晶不够充分,平整时带钢再结晶不充分处理产生肋浪缺陷,并且无法重平挽救。
3、原料方面问题:A、热轧卷浪形:由于热轧板卷原始严重浪形,即使通过酸洗拉矫、冷连轧、平整三道工序变形,仍未能得到足够的改善,遗留浪形缺陷仍超过成品技术要求。
B、冷轧后板型不良:由于板型仪、过焊缝降速及轧钢操作工等原因,轧制后带钢局部浪形严重、卷型端面凹凸不平,经平整后无法消除,而产生带钢浪形。
4、机组设备方面问题:A、S辊打滑:随着带钢产量不断增加,S辊辊面被带钢磨得光滑,粗糙度0.8um时,带钢与S辊产生速度差,平整延伸率自动控制的脉,冲发生器测量、计算发生误差,与实际延伸率不符,指令絮乱,整个控制系统失灵,在这种状态下不能投入平整延伸率自动控制系统进行生产带钢,改为恒压力方式控制平整带钢,但因一部分带钢没有达到要求的延伸率,带钢没有达到足够的变形也会产生浪形超标。
- 1、下载文档前请自行甄别文档内容的完整性,平台不提供额外的编辑、内容补充、找答案等附加服务。
- 2、"仅部分预览"的文档,不可在线预览部分如存在完整性等问题,可反馈申请退款(可完整预览的文档不适用该条件!)。
- 3、如文档侵犯您的权益,请联系客服反馈,我们会尽快为您处理(人工客服工作时间:9:00-18:30)。
平整机组硌印产生的原因分析及解决措施
李纯山李刚
(本溪钢铁集团公司,辽宁本溪 117000)
摘要:平整机组近期硌印量很大,根据此情况,轧钢分厂在质量检查部门的配合和帮助下,进行现场跟踪和研究。
发现硌印主要产生在平整的带头(也就是精整的最后一包),带头硌印所占硌印量的比例92%以上。
影响冷轧的一组率及合格率,因此找出产生原因、分析、制定解决措施。
关键词:平整机组;硌印缺陷;
The Analysis of Skin-pass Mill Roll-mark
LI Chunshan, LI Gang
(Benxi Iron &Steel CO.LTD,BENXI LIAONING 117000, China)
Abstract: the defect of roll-mark at skin-pass mill is improving recently, in this case, the Roll Branch, is cooperation with Quality Department, found that the roll-mark defect is mainly occur at the head of strip (the last package of Finishing Line), the proportion is more than 92%. The paper analyzes the reason of it and gives the measure to resolve this problem.
Keywords: skin-pass mill, concave-convex defect
我国钢铁工业实现了从计划经济走向市场经济,钢材从短缺达到供需基本平衡,国内、国外市场逐步接轨,特别是冷轧薄板生产线,国内、国外的大、中、小型生产线较多,要想在市场占有一席之地必需生产高质量的冷轧板,我厂平整机组是从法国引进的二手设备,随然经多次改造,但装备水平还很落后,检查手段也不完善,出现了很多表面缺陷,平整硌印就是其中的一项,解决此问题是平整机组的主要任务之一。
1 硌印缺陷的具体形态
所谓硌印就是在冷轧板的板面上凸凹的痕迹,存在于在钢板的任意部位,没有规律。
有轻有重,重者造成判废或切损(主要是伤卷所造成,平整机组无法改善,只能切掉伤卷的部位),轻者判协议或二组(有些是平整S辊黏杂质产生,有些是平整来料表面损伤在生产时由于卷取张力造成伤卷部位的进一步恶化造成的)。
2.硌印产生的部位和原因分析
2.1天车夹具夹锁扣造成的伤卷
(1) 轧制线(CDCM线)打锁扣的位置不对造成锁扣硌印,如图1所示。
作者简介:李纯山,男,轧钢工程师,从事冷轧平整机现场工艺管理、技术管理工作。
图1 锁扣硌印
(2) 罩式炉、平整夹具的虎头位置不对,造成捆带或锁扣硌印,如图2所示。
图2 捆带或锁扣硌印
(3) 平整拆捆带时转地辊造成硌印,如图3所示。
图3 平整拆捆带时转地辊造成的硌印
2.2罩式炉、平整前库伤卷产生硌印
(1) 罩式炉运输链鞍座、翻钢机伤卷造成硌印,如图4所示。
图4 罩式炉运输链鞍座、翻钢机伤卷造成硌印
(2) 天车夹具伤卷外圈造成硌印,如图5所示。
图5 天车夹具伤卷外圈造成硌印
(3) 天车吊运时伤卷芯和边部造成硌印,如图所示。
图6 天车吊运时伤卷芯和边部造成硌印
(4) 溢出边处损伤开卷后造成硌印,如图7所示。
图7 溢出边处损伤开卷后造成硌印
(5) 平整、罩式炉天车夹具底板横移伤卷平整后造成硌印,如图8所示。
图8 平整、罩式炉天车夹具底板横移伤卷平整后造成硌印
2.3平整机本体产生硌印
(1) 准备站翻缸机处由立卷变成卧卷及水平液压缸升起时翻缸机的侧臂伤卷。
(2) 地辊处钢卷下落,及地辊转动时钢卷有两道横印,主动辊出横印较重从动辊横印较轻,另外在切头或压头时划伤较重。
(3) 钢卷运到1#运输链时由于运输小车不在鞍座中心,造成鞍座处伤卷(落到鞍座上钢卷晃动),如图9所示。
图9 鞍座处伤卷
(4)厚料过S辊产生的打折和划伤,如图10所示。
图10 厚料过S辊产生的打折和划伤
(5) 卷取时产生的打折造成的硌印缺陷。
2.4精整天车夹具伤卷产生铬印
主要是在精整入库时天车夹具伤内圈,再薄规格和深冲钢生产时由于内圈伤卷较严重形成大量硌印,如图11所示。
图11精整天车夹具伤卷产生铬印
3 硌印的损伤程度
在以上几种原因下产生的带钢硌印缺陷的严重程度分析如下。
(1)有些卷的锁扣被压(与钢卷外圈一平,由于卷热钢软),主要是在罩式炉出炉造成的。
厚料有1吨左右,薄料有1.5吨左右。
(2)有些卷的锁扣没被压平,主要由罩式炉终冷台吊卷到平车上,或由平车吊到平整前库,或由平整前库吊到翻钢机上这三个环节过程中造成的。
厚料有0.3~0.4吨,薄料有0.5~0.8吨。
(3)罩式炉运输链鞍座、翻钢机伤卷伤3~4圈,但平整卷卷取时这种硌印影响较大。
(主要是张力状态导致缺陷影响层数扩大)
(4)天车夹具伤卷有些是夹具锥头触到钢卷的端面及钢卷内圈附近,有些是夹具虎头触到钢卷的端面及钢卷外圈附近,有些是夹具虎外侧撞伤另一个钢卷伤钢卷外,严重程度不等,对不切边料影响较大,夹具内避伤卷对深冲钢影响较大。
(5)天车吊运时伤卷主要是钢卷放到台车上及钢卷放到平整库夹具与钢卷相碰撞及钢卷与钢卷相撞造成的。
(6)溢出边卷由于溢出边的压倒在平整生产时没撕开,就不吊下处理卷而言,溢出边处产生折边经平整辊辊面有白点,对不切边料影响较大。
溢出边严重者精整切边有时切不掉,也会造成硌印。
(7)平整、罩式炉天车夹具底板横移伤卷,有些卷在夹具横移时把钢卷外圈损伤,平整生产后虽然被压平,但是有折印迹象,这种现象对厚料影响较大。
(8)翻钢机侧臂伤卷、准备站切头划伤,鞍座处伤卷,在卷取时硌印无法消除。
穿带打折及S辊处的打折,平整也很难解决此问题。
(9)虽然加上套筒但是薄料在传动侧仍然经常打小折,而且检查困难。
4 控制措施
通过对平整后带钢硌印缺陷产生的原因分析及严重程度,分别制定改善措施如下。
(1)轧机打锁扣的位置固定(出口侧下方)。
(2)罩式炉、平整夹具的虎头位置固定(虎头方向靠镀锌机组)。
(3)平整拆捆带时如有捆带压地辊情况则禁止转地辊,捆带位置不对可串动运输小车的位(置解决)。
(4)罩式炉运输链鞍座、翻钢机伤卷伤3~4圈,平整在准备站上切头,但由于平整切头一刀只能切半米,影响机组作业率,影响到平整的生产。
(5)夹具伤卷主要通过加强天车工的操作责任心,加大考核力度,不定期进行抽检。
(6)溢出边过平整机组时要求溢出边处开缝过钢,待溢出边过辊缝后分卷;带槽的改进对流盘需要尽快大批投入使用。
(7)翻钢机侧臂加垫(避勉钢卷与翻钢机侧臂直接接处)。
(8)地辊处及1#运输链处要求设备分厂研究加一限位开关,使在这两处小车的下降速度缓慢些,减少冲击。
(9)1#运输链鞍座需要改造,调整合适的鞍座间距。
(10)为防止卷取机处打折,按轧制不同厚度调皮带助卷器的小臂的间隙及定期更换出口S辊上的压辊。
(11)精整天车夹具伤卷,采取平整运输链开到位使精整天车垂直吊运钢卷(主要防止吊运时倾斜造成伤钢卷内圈)或者钢卷加护套的办法。
5 结论
平整机组表面缺陷的减少会使产品一组率、合格率有较大程度的提高,以上所提到产生硌印的因素是结合我厂生产情况、设备情况现场实际跟踪得出的结论,有些因素考虑的不一定全面,制定措施也不一定得利,还需在生产中进一步完善解决,有些设备还需进一步改造,比如:鞍座链节,S辊清扫装置,减少料带来缺陷,这样才能满足现代化冷轧厂的需要,生产高质量冷轧板,为大批量生产汽车板打下坚实的基础。
参考文献
[1] Fause R.钢带开卷、平整和切板[J].冶金设备,2000,4:1001-1269.
[2] 刘新华,洪运涛,乔梁.张力控制技术在邯钢冷轧厂平整机的应用[A].中国金属协会.2003年全国冷轧板
带生产技术研讨会议论文集[C].北京:科学技术信息中心,2003:5.
[3] 吴贵芳,梁治国, 徐金梧.冷轧带钢表面质量自动检测系统的在线应用研究[J].冶金自动化,
2003,(1):51-53.。