晶间腐蚀试验操作规程
晶间腐蚀方法

6.4不锈钢局部腐蚀(晶间腐蚀、点蚀)试验结果与对比6.4.1不锈钢晶间腐蚀试验方法1)沸腾硝酸法(E法,用于304、410S、430、409L)目的:检测304(敏化后)和410S、430、409L(热轧态)的耐晶间腐蚀性能;实验条件:试样在65%硝酸溶液中微沸48h(304)或24h(其他);试样情况:试样表面抛光,并用乙醇清洗;检测:测量失重;腐蚀后的特征形貌;标准:GB 4334.32)硫酸-硫酸铜法(用于奥氏体不锈钢304)目的:检测304(敏化后)的耐晶间腐蚀性能;实验条件:试样在CuSO4+H2SO4+铜屑的微沸溶剂中24h(对于≤18%C r的不锈钢);试样情况:试样表面抛光,并用乙醇清洗;检测:测量失重;腐蚀后的金相特征;溶剂配方:100g CuSO4+100ml H2SO4加蒸馏水稀释至1000ml。
标准:GB 4334.2注1:304不锈钢为热轧后再经650℃、2h处理的敏化态,铁素体不锈钢为热轧态。
注2:以上二法对304都适用;对铁素体不锈钢,试验表明:410、430、409L 在硫酸-硫酸铜溶液中试样表面发生较严重的镀铜现象,故仅采用沸腾硝酸法。
因此,为了便于304与其它3种铁素体不锈钢进行耐晶间腐蚀性能的对比分析,以下以沸腾硝酸法为主,此外还要与晶间腐蚀的电化学试验、分析相结合(参6.7)。
图0-1 晶间腐蚀试验装置图0-2 点蚀试验装置(恒温水浴锅)6.7 不锈钢局部腐蚀的电化学分析与对比6.7.1不锈钢晶间腐蚀电化学试验方法主要目的:对不锈钢耐晶间腐蚀的电化学性能的测定和对比分析,与浸泡试验结果相辅相成。
测试项目:用动电位再活化法测得晶间腐蚀的电化学曲线,可得阳极化环和再活化环的最大电流Ia和Ir,并以其比值Ir/Ia作为耐晶间腐蚀性能的度量。
试样状态:304---650o C 2h、空冷;430、410、409L---热轧态;均经机械抛光。
所用仪器:CHI600C电化学分析仪标准:JIS G0580-1986,ASTM G108,GB/T 15260-1994晶间腐蚀电化学测定方法:采用电化学动电位再活化法(EPR):以0.5mol/L的H2SO4为腐蚀介质(30o C),采用双环EPR法,以6V/h的扫描速度从腐蚀电位[约-400mv(SCE)] 极化到+300mv(SCE),一旦达到这个电位则扫描方向反转,以相同速度降低到腐蚀电位。
不锈钢晶间腐蚀试验规程

1.主题内容与适用范围本标准规定了不锈钢硫酸—硫酸铜试验方法的试验设备,试验条件和步骤,试验结果的评定和试验报告的要求。
本标准适用于本厂不锈钢晶间腐蚀试验。
2.试样的选取2.1 压力加工钢材的试样从同一炉号、同一批热处理和同一规格的钢材中选取。
2.2 焊接试样从产品钢材相同而且焊接工艺也相同的试板上选取。
2.3 试样尺寸及选取方法见表一。
3.试样的制备3.1 试样用锯切取,如用剪刀时,应通过切削或研磨方法除去剪刀的影响部份。
3.2 试样上有氧化皮时,要通过切削或研磨除掉。
需要敏化处理的试样,应在敏化处理后研磨。
3.3 试样切取及表面研磨时,应防止过热,被试验的试样表面粗糙度R a必须小于0.08μm。
不能进行研磨的试样,根据双方协议也可采用其他方法处理。
试样尺寸及选取方法表一mm-35-4. 试样的敏化处理4.1 试样的敏化处理在研磨前进行。
4.2 敏化处理前试样用适当的溶剂或洗涤剂(非氧化物)去油并干燥。
4.3 含碳量大于0.08%,不含稳定化元素的钢种不进行敏化处理。
4.4 对超低碳钢(碳含量不大于0.03%时)或稳定化钢种(添加钛或铌),敏化处理温度为650℃,压力加工试样保温2小时,铸件保温1小时。
4.5 含碳量大于0.03%,不大于0.08%,不含稳定化元素并用于焊接的钢种,应以敏化处理的试样进行试验。
敏化处理制度在协议中另行规定。
4.6 焊接试样直接以焊后状态进行试验。
对焊后还要经过350℃以上热加工的焊接件,试样在焊后还应进行敏化处理,敏化处理制度在协议中另行规定。
5. 试验设备5.1 1容量为1-2L带回流冷凝器的启口—锥形烧瓶。
5.2 使试验溶液能保持微沸状态的加热装置。
6. 试验条件和步骤:6.1 试验溶液:将100g硫酸铜(GB665 分析纯)溶介于700毫升蒸馏水或离子水中,再加入100ml硫酸(GB625 优级纯),用蒸馏水或去离子水稀释至1000ml,配制成硫酸—硫酸铜溶液。
晶间腐蚀试验操作规程

晶间腐蚀试验操作规程1、总则1.1本公司采用的晶间腐蚀试验方法为GB/T4334.5-2000《不锈钢硫酸-硫酸铜腐蚀试验方法》。
1.2本守则对试样的提取、试验设备、试验条件和步骤、试验结果的评定及报告作了规定。
适用于检验奥氏体、奥氏体-铁素体不锈钢在加有紫铜屑的硫酸-硫酸铜溶液中的晶间腐蚀倾向。
2、试样的提取与制备2.1焊接件试样从与产品钢材相同且焊接工艺也相同的试板上提取,应包括母材、热影响区及焊接金属的表面,详见附件。
2.2试样用锯切取,如剪切则应通过切削或研磨方法除去剪切的影响部分。
2.3试样切取及表面研磨时,应防止表面过热。
试验试样表面粗糙度Ra值≯0.8μm,其他检验试样提取详见GB/T4334.5。
(见附件)3、试验仪器、设备、试验溶液3.1试验仪器为容量≥1L的带回流冷凝器的磨口锥形烧瓶。
3.2 600瓦的加热电炉配上一只可调变压器,通过后者调节加热电炉的功率,使本试验溶液能保持微沸状态。
3.3试验溶液配制方法如下:将100g符合GB/T665的分析纯硫酸铜(CuSO4·5H2O)溶解于700ml蒸馏水或去离子水中,再加入100ml符合GB/T625的优级纯硫酸,用蒸馏水或去离子水稀释至1000ml,即配成硫酸-硫酸铜溶液。
4、试验条件和步骤4.1试验前将试样用适当的溶剂或洗涤剂(非氯化物)去油污并干燥。
4.2在充入第3条配制的试验溶液的烧瓶底部铺一层符合GB/T466(纯度不小于99.5%)的紫铜屑或铜粒,然后放置试样。
保证每个试样与紫铜屑接触的情况下,同一烧瓶中允许放几层同一钢种的试样,但试样之间要用上述紫铜屑隔离而互不接触。
4.3试验溶液应高出最上层试样20mm以上。
每次试验都应使用新的试验溶液。
4.3.1仲裁试验时,试验溶液量按试样表面积计算,其量在8ml/Cm²以上。
4.4完成上述工作后,将烧瓶放在加热装置上,在回流冷凝器进水口要一直以冷却水(自来水)流入,出水口畅通放水。
晶间腐蚀试验操作规程

1.1岗位职责
1.1.1按相关晶间腐蚀试验技术标准进行试验。
1.1.2提前五分钟到岗,检查晶腐室水、电及药品的使用情况,做好试验前准备工作。
1.1.3坚守工作岗位不得随便离开,有事应向主管请假。
1.1.4认真填写本职责围的原始记录、对试验结果负责。
1.1.5负责提出药品及器材的购置计划。
宽度为15~25mm的整段管状试样
OD>38,且
壁厚≦5
厚度≦5mm,宽度为15~25mm,周向弧长≧50mm
ISO
—
试样总表面积在15~35cm2之间,按相关产品标准制样。
3.3试样的敏化处理
3.3.1试样的敏化处理在研磨前进行。
3.3.2敏化前试样必须用溶剂式洗涤剂(非氯化物),如丙酮,酒精,去油并干燥,去油后的试样不能用手触摸。
2.主要设备参数及工装
以16%硫酸—硫酸铜腐蚀试验方法为重点,试验采用回流冷凝器、三角烧瓶、1000W电炉、箱式电阻炉、干燥箱、智能工业调节器AI-804、控温精度≦0.2%、双目显微镜。
3.作业流程与操作规程
各标准对16%硫酸—硫酸铜腐蚀试验的适用围的规定如表1所示。
表1 16%硫酸—硫酸铜腐蚀试验的适用围
文件名称:晶间腐蚀作业标准
文件编号:WLCS-QW-Q-005-2010
版号:D
修改:0
生效日期:2010年05月10日
编制单位:品管部
编制: 年 月 日
审核:年 月 日
批准:年 月 日
发放编号:
受控印章:
2.主要设备参数及工装………………………………………………………………( 3 )
3.作业流程与操作规程………………………………………………………………(3~7)
马氏体不锈钢晶间腐蚀试验方法
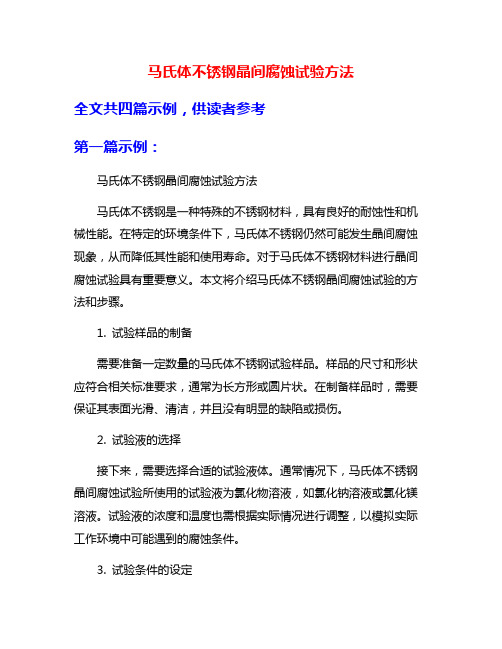
马氏体不锈钢晶间腐蚀试验方法全文共四篇示例,供读者参考第一篇示例:马氏体不锈钢晶间腐蚀试验方法马氏体不锈钢是一种特殊的不锈钢材料,具有良好的耐蚀性和机械性能。
在特定的环境条件下,马氏体不锈钢仍然可能发生晶间腐蚀现象,从而降低其性能和使用寿命。
对于马氏体不锈钢材料进行晶间腐蚀试验具有重要意义。
本文将介绍马氏体不锈钢晶间腐蚀试验的方法和步骤。
1. 试验样品的制备需要准备一定数量的马氏体不锈钢试验样品。
样品的尺寸和形状应符合相关标准要求,通常为长方形或圆片状。
在制备样品时,需要保证其表面光滑、清洁,并且没有明显的缺陷或损伤。
2. 试验液的选择接下来,需要选择合适的试验液体。
通常情况下,马氏体不锈钢晶间腐蚀试验所使用的试验液为氯化物溶液,如氯化钠溶液或氯化镁溶液。
试验液的浓度和温度也需根据实际情况进行调整,以模拟实际工作环境中可能遇到的腐蚀条件。
3. 试验条件的设定在进行晶间腐蚀试验前,需要设定一定的试验条件。
包括试验液的温度、PH值、搅拌速度等参数。
这些条件对试验结果的准确性和可靠性有重要影响,因此需要严格控制。
4. 试验过程的操作将制备好的样品放入试验液中,按照设定的条件进行试验。
在试验过程中,定期检查样品表面的腐蚀情况,记录相关数据。
5. 试验结果的分析试验结束后,对试样表面进行观察和分析,评估晶间腐蚀程度。
通过观察试样的腐蚀痕迹和形貌,可以判断马氏体不锈钢材料的抗腐蚀性能。
6. 结论与建议根据试验结果,制定相关的结论和建议。
如果发现马氏体不锈钢材料存在晶间腐蚀问题,需要及时采取相应的措施进行改善和提升。
选择合适的材料、表面处理或加工工艺等。
马氏体不锈钢晶间腐蚀试验是评估材料性能和耐蚀性的重要手段。
通过严格控制试验条件和分析试验结果,可以及时发现材料存在的问题,并提出相应的改进建议,以保证材料在实际工作环境中具有良好的性能和可靠性。
第二篇示例:马氏体不锈钢是一种具有优良耐腐蚀性能的不锈钢材料,但在某些特定环境下,仍有可能发生晶间腐蚀现象,降低其使用寿命和性能。
不锈钢晶间腐蚀试验与分析

不锈钢晶间腐蚀试验与分析一、实验目的1.掌握影响奥氏体不锈钢晶间腐蚀的因素;2.掌握不锈钢晶间腐蚀试验的方法;二、实验原理18-8 型奥氏体不锈钢在许多介质中具有高的化学稳定性,但在400-800℃范围内加热或在该温度范围内缓慢冷却后,在一定的腐蚀介质中易产生晶间腐蚀。
晶间腐蚀的特征是沿晶界进行浸蚀。
使金属丧失机械性能,致使整个金属变成粉末。
1.晶间腐蚀产生的原因一般认为在奥氏体不锈钢中,铬的碳化物在高温下溶入奥氏体中,由于敏化(400-800℃)加热时,铬的碳化物常于奥氏体晶界处析出,造成奥氏体晶粒边缘贫铬现象,使该区域电化学稳定性下降,于是在一定的介质中产生晶间腐蚀。
为提高耐蚀性能,常采用以下两种方法。
(1)将 18-8 型奥氏体不锈钢碳含量降至 0.03%以下,使之减少晶界处碳化物析出量,而防止发生晶间腐蚀。
这类钢成称为超低碳不锈钢,常见的有00Cr18Ni10。
(2)在 18-8 型奥氏体不锈钢中加入比铬更易形成碳化物的元素钛或铌,钛或铌的碳化物较铬的碳化物难溶于奥氏体中,所以在敏化温度范围内加热时,也不会于晶界处析出碳化物,不会在腐蚀性介质中产生晶间腐蚀。
为固定18-8 型奥氏体不锈钢中的碳,必须加入足够数量的钛或铌,按原子量计算,钛或铌的加入量分别为钢中碳含量的4-8 倍。
2.晶间腐蚀的试验方法晶间腐蚀的试验方法有 C 法、 T 法、 L 法、 F 法和 X 法。
这里介绍容易实现的 C法和 F法。
试样状态:(1)含稳定化元素( Ti 或 Nb)或超低碳( C≤ 0.03%)的钢种应在固溶状态下经敏化处理的试样进行试验。
敏化处理制度为 650℃保温 1 小时空冷。
(2)含碳量大于 0.03%不含稳定化元素的钢种,以固溶状态的试样进行试验;用于焊接钢种应经敏化处理后进行试验。
(3)直接以冷状态使用的钢种,经协议可在交货状态试验。
(4)焊接试样直接以焊后状态试验。
如在焊后要在 350℃以上热加工,试样在焊后要进行敏化处理。
不锈钢晶间腐蚀试验方法
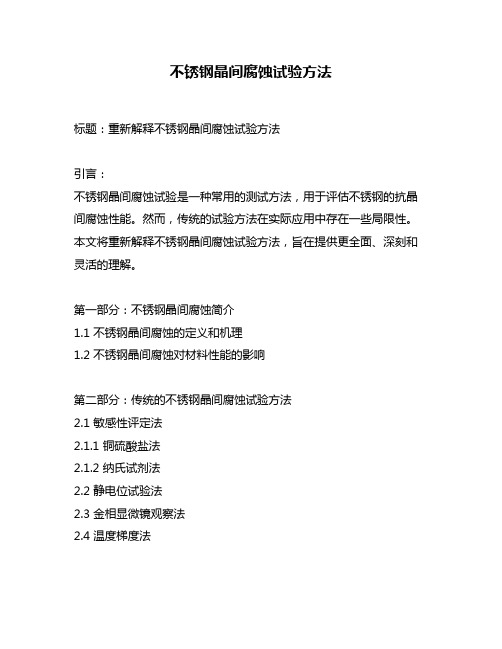
不锈钢晶间腐蚀试验方法标题:重新解释不锈钢晶间腐蚀试验方法引言:不锈钢晶间腐蚀试验是一种常用的测试方法,用于评估不锈钢的抗晶间腐蚀性能。
然而,传统的试验方法在实际应用中存在一些局限性。
本文将重新解释不锈钢晶间腐蚀试验方法,旨在提供更全面、深刻和灵活的理解。
第一部分:不锈钢晶间腐蚀简介1.1 不锈钢晶间腐蚀的定义和机理1.2 不锈钢晶间腐蚀对材料性能的影响第二部分:传统的不锈钢晶间腐蚀试验方法2.1 敏感性评定法2.1.1 铜硫酸盐法2.1.2 纳氏试剂法2.2 静电位试验法2.3 金相显微镜观察法2.4 温度梯度法第三部分:重新解释不锈钢晶间腐蚀试验方法的关键点3.1 试剂的选择和制备3.2 试样的制备和处理3.3 试验条件的优化3.3.1 温度条件3.3.2 电位条件3.4 试验结果的分析和评估第四部分:改进的不锈钢晶间腐蚀试验方法4.1 利用先进材料表征技术4.1.1 扫描电子显微镜(SEM)分析4.1.2 能谱分析(EDS)4.1.3 原子力显微镜(AFM)分析4.2 基于计算机模拟的试验方法4.2.1 分子动力学模拟4.2.2 密度泛函理论模拟结论:通过重新解释不锈钢晶间腐蚀试验方法,我们可以更全面、深刻和灵活地评估不锈钢的抗晶间腐蚀性能。
传统的试验方法在试剂选择、试样处理和试验条件优化等方面存在一些限制,而利用先进的材料表征技术和基于计算机模拟的试验方法可以弥补这些限制。
进一步的研究和创新将有助于提高不锈钢晶间腐蚀试验方法的准确性和可靠性。
观点和理解:在一个快速发展的现代社会中,不锈钢晶间腐蚀试验方法的重新解释是非常重要的。
这些方法不仅对于材料科学和工程领域的研究人员具有重要意义,而且对于工业应用中使用不锈钢的厂商和用户也至关重要。
通过更加准确地评估不锈钢的抗晶间腐蚀性能,我们可以选择合适的材料,提高产品质量,并增加设备的使用寿命。
通过重新解释不锈钢晶间腐蚀试验方法,我们可以更好地理解不锈钢在实际应用中可能遇到的腐蚀问题。
晶间腐蚀试验操作规程

ISO——敏化处理方法有两种:700℃±10℃,保温30min,水冷 或650℃±10℃,保温10min,水冷。敏化处理仅限于奥氏体和双相不锈钢,若无特别规定,采用第一种敏化处理方法。
3.4试验溶液
4.相关文件……………………………………………………………………………(7~8)
5.质量记录……………………………………………………………………………(8 )
6.修订记录……………………………………………………………………………(8)
7.附件…………………………………………………………………………………(8)
1.1.6有责任接收上级主管部门的考核,复查结果。
1.1.7努力钻研技术,熟悉并认真执行标准,掌握好本岗位的操作技能。
1.2权限
1.2.1对职权围的检验任务,按产品的规定有权作出检验结论。
1.2.2对既无产品性能说明,又无技术标准的产品有权拒绝接收检验。
1.2.3有权拒绝外来人员进入试验室,以防药品外流及干扰自已的分析测试工作。
标准
适用围
奥氏体钢不锈钢
双相不锈钢
铁素体不锈钢
GB
适用
适用
——
ASTM
适用于Mo含量≦3%的不锈钢,若Mo%>3%,则应与客户协商是否可用此方法
——
——
ICr%>16%,Mo%≦3%的双相钢
Cr 含量在16%~20%之间,Mo含量在0%~1%之间的铁素体钢
JIS
宽度为15~25mm的整段管状试样
OD>38,且
壁厚≦5
厚度≦5mm,宽度为15~25mm,周向弧长≧50mm
晶间腐蚀检验方法

不锈钢硫酸-硫酸铁腐蚀试验方法(GB4334.2-84)适用于将奥氏体不锈钢在硫酸-硫酸铁溶液中煮沸试验后,以腐蚀率评定晶间腐蚀倾向的一种试验方法。
试验步骤:1)将硫酸用蒸馏水或去离子水配制成50±0.3%(质量百分比)的硫酸溶液,然后取该溶液600ml加入25g硫酸铁加热溶解配制成试验溶液。
2)测量试样尺寸,计算试样面积(取三位有效数字)。
3)试验前后称质量(准确到1mg)。
4)溶液量按试样表面积计算,其量不小于20ml/cm2。
每次试验用新的溶液。
5)试样放在试验溶液中用玻璃支架保持于溶液中部,连续沸煮沸120h。
每一容器内只放一个试样。
6)试验后取出试样,在流水中用软刷子刷掉表面的腐蚀产物,洗净、干燥、称重。
试验结果以腐蚀率评定为W前-W后腐蚀率=──────(g/m2.h)St式中W前──试验前试样的质量(g);W后──试验后试样的质量(g);S──试样的表面积;t──试验时间(h)。
(3)不锈钢65%硝酸腐蚀试验方法(GB4334.3-84)适用于将奥氏体不锈钢在65%硝酸溶液中煮沸试验后,以腐蚀率评定晶间腐蚀倾向的试验方法。
试验步骤:1)试验溶液的配制将硝酸用蒸馏水或去离子水配制成65±0.2%(质量百分比)的硫酸溶液。
2)、3)、4)同硫酸-硫酸铁试验方法。
5)每周期连续煮沸48h,试验五个周期。
试验结果以腐蚀率评定,同硫酸-硫酸铁试验方法。
焊接试样发现刀状腐蚀即为具有晶间腐蚀倾向,性质可疑时,可用金相法判定。
(4)不锈钢硝酸-氢氟酸腐蚀试验方法(GB4334.4-84)适用于检验含钼奥氏体不锈钢的晶间腐蚀倾向。
用在70℃、10%硝酸-3%氢氟酸溶液中的腐蚀率的比值来判定晶间腐蚀倾向。
试验步骤:1)试验溶液:将硝酸和氢氟酸试剂,用蒸馏水或去离子水配制成质量分数为10%的硝酸-3%的氢氟酸试验溶液。
2)、3)同硫酸-硫酸铁试验方法。
4)将支架放入容器中,溶液量按试样表面积计算,其量不少于10ml/cm2。
ASME晶间腐蚀作业指导书

1.5 All wrought products and weld material of austenitic atainless ateels can be evaluated by this test.
⒉Referenced Documents
A370 Test Methods and Definitions for Mechanical Testing of Steel Products
1.4 The copper-copper sulfate-16% sulfuric acid test indicates susceptibility to intergranular attack associated with the precipitationof chromium-rich carbides. It does not detect susceptibility associated with sigma phase. This test may be used to evaluate the heat treatment accorded as-received material. It may also be used to evaluate the effectiveness of stabilizingelement additions(Cb, Ti, and so forth) and reductions in carbon content to aid in resisting intergranular attack.
晶间腐蚀操作规程

晶间腐蚀试验操作规程1.0 目地:制定和规范晶间腐蚀作业指导书,确保试验员按照正确的检测方法操作,防止不合产品入库。
2.0 范围:仅适用于本公司内部试验室人员检测奥氏体不锈钢铜屑-硫酸铜-硫酸测定晶间腐蚀敏感性试验的操作方法及判定标准。
3.0 引用标准:ASTM A262-104.0 试验前的准备工作:4.1试样制备4.1.1 试样按MESC SPE 77/ 302规定,从同一炉浇注的的试块中取样。
含稳定化元素钛的钢种,在该炉最后浇注的试块中取样。
4.1.2试样的尺寸:长度80,宽度12.5,厚度3.5;试样数量2件;注:一个试样做试验用,另一个试样留做空白弯曲。
4.1.3试样的取样方法:原则上采用锯切,如用剪切方法时应通过切削或研磨的方法除去剪切的影响部位。
在试样加工过程中应注意,以免加工过热,加工后的试样表面粗糙度为Ra0.84.1.4试验前应用清洁的溶剂,如丙酮、酒精、乙醚等,或挥发性去污剂将试样表面的油污去除。
4.2试样的敏化处理超低碳或碳稳定化钢种的试样应在650~675℃下进行敏化热处理后再进行测试。
在这一温度范围碳化物析出最大,而一般的敏化处理则是在675℃下保持1小时。
要注意避免试样在敏化处理时渗碳或有氮化物。
热处理最好在空气或中性盐条件下进行。
注——675℃下的敏化处理是为了检测碳稳定化钢种或碳含量小于0.03%的钢种抵抗因碳化物沉淀析出因而产生晶间裂纹的有效性。
4.3试验溶液:在700ml蒸馏水中溶解100g硫酸铜(CuSO4·5H2O),加100ml硫酸(H2SO4, cp, sp gr 1.84),再用蒸馏水稀释到1000ml。
注——该溶液含大约6%重量比的无水CuSO4和16%重量比的H2SO4。
4.4试验仪器4.4.1 需要一个带45/50mm的磨砂玻璃接头的1升锥形瓶,一个带有45/50mm的磨砂玻璃接头的四球(最小的)Allihn冷凝器。
推荐在磨砂玻璃接头处使用硅质润滑剂。
晶间腐蚀试验操作规程(专业研究)

文件名称:晶间腐蚀作业标准文件编号:WLCS-QW-Q-005-2010版号:D修改:0生效日期:2010年05月10日编制单位:品管部编制:年月日审核:年月日批准:年月日发放编号:受控印章:目录1.岗位职责及权限……………………………………………………………………( 3 )2.主要设备参数及工装………………………………………………………………( 3 )3.作业流程与操作规程………………………………………………………………(3~7)3.1试样选取………………………………………………………………………( 3 )3.2试样尺寸及制备………………………………………………………………(3~4)3.3试样的敏化处理………………………………………………………………( 4 )3.4试验溶液………………………………………………………………………( 4 )3.5试验步骤………………………………………………………………………(4~5)3.6试验结果评定…………………………………………………………………( 6 )3.7 35%硫酸-硫酸铜晶间腐蚀试验…………………………………………………( 6 )3.8试验结果处理…………………………………………………………………( 6 )3.9电热恒温干燥箱操作规程和注意事项………………………………………(6~7)3.10电炉操作规程和注意事项……………………………………………………(7 )4.相关文件……………………………………………………………………………(7~8)5.质量记录……………………………………………………………………………(8 )6.修订记录……………………………………………………………………………(8 )7.附件…………………………………………………………………………………(8 )1.岗位职责与权限1.1岗位职责1.1.1按相关晶间腐蚀试验技术标准进行试验。
1.1.2提前五分钟到岗,检查晶腐室水、电及药品的使用情况,做好试验前准备工作。
晶间腐蚀试验操作规程

晶间腐蚀试验操作规程总则1.1本公司采用的晶间腐蚀试验方法为GB/T4334.5-2000《不锈钢硫酸-硫酸铜腐蚀试验方法》。
1.2本守则对试样的提取、试验设备、试验条件和步骤、试验结果的评定及报告作了规定。
适用于检验奥氏体、奥氏体-铁素体不锈钢在加有紫铜屑的硫酸-硫酸铜溶液中的晶间腐蚀倾向。
2、试样的提取与制备2.1焊接件试样从与产品钢材相同且焊接工艺也相同的试板上提取,应包括母材、热影响区及焊接金属的表面,详见附件。
2.2试样用锯切取,如剪切则应通过切削或研磨方法除去剪切的影响部分。
2.3试样切取及表面研磨时,应防止表面过热。
试验试样表面粗糙度Ra值≯0.8μm,其他检验试样提取详见GB/T4334.5。
(见附件)3、试验仪器、设备、试验溶液3.1试验仪器为容量≥1L的带回流冷凝器的磨口锥形烧瓶。
3.2 600瓦的加热电炉配上一只可调变压器,通过后者调节加热电炉的功率,使本试验溶液能保持微沸状态。
3.3试验溶液配制方法如下:将100g符合GB/T665的分析纯硫酸铜(CuSO4·5H2O)溶解于700ml蒸馏水或去离子水中,再加入100ml符合GB/T625的优级纯硫酸,用蒸馏水或去离子水稀释至1000ml,即配成硫酸-硫酸铜溶液。
4、试验条件和步骤4.1试验前将试样用适当的溶剂或洗涤剂(非氯化物)去油污并干燥。
4.2在充入第3条配制的试验溶液的烧瓶底部铺一层符合GB/T466(纯度不小于99.5%)的紫铜屑或铜粒,然后放置试样。
保证每个试样与紫铜屑接触的情况下,同一烧瓶中允许放几层同一钢种的试样,但试样之间要用上述紫铜屑隔离而互不接触。
4.3试验溶液应高出最上层试样20mm以上。
每次试验都应使用新的试验溶液。
4.3.1仲裁试验时,试验溶液量按试样表面积计算,其量在8ml/Cm²以上。
4.4完成上述工作后,将烧瓶放在加热装置上,在回流冷凝器进水口要一直以冷却水(自来水)流入,出水口畅通放水。
晶间腐蚀仪安全操作及保养规程

晶间腐蚀仪安全操作及保养规程晶间腐蚀仪是在半导体行业中常用的设备,它可用于去除芯片表面上的氧化层,使得芯片表面贴附的设备变得更加精确。
然而,在使用晶间腐蚀仪的过程中,必须严格遵守操作规程,以确保操作安全以及设备可靠性。
同时,正确的保养也能够延长设备的使用寿命。
本文将阐述晶间腐蚀仪的安全操作及保养规程。
安全操作准备工作1.操作前请全面了解晶间腐蚀仪的启动、关闭、操作等步骤,并在操作前阅读操作手册。
2.准备必要的防护设备,如手套、护目镜和口罩等。
3.清洁工作台面,确保周围的灰尘等杂物不会进入操作区。
启动设备1.打开工作台的电源开关。
2.确保工作台顶部面板上的所有指示灯均正常,并且安全门紧闭。
3.按下设备启动按钮,启动晶间腐蚀仪。
4.等待晶间腐蚀仪完成自检,确认所有指示灯均正常亮起。
操作设备1.操作前请核对晶间腐蚀仪的操作程序,并设置好相应的工艺参数。
2.穿戴好手套、护目镜和口罩等防护设备后,请通过安全门进入操作区。
3.确认被处理芯片的表面没有油脂、黏附物或残留物,并正确放置于操作区中。
4.启动操作程序,并耐心等待程序执行完毕后,关闭操作程序并取出芯片。
5.离开操作区,关闭安全门和电源开关。
关闭设备1.关闭晶间腐蚀仪的操作程序。
2.取出所有芯片和待处理物,并清理操作区。
3.等待设备冷却后,关闭工作台电源开关。
设备保养1.定期清洗晶间腐蚀仪所用的各类器具,并进行必要的维护。
不要使用强度清洗剂或硬质刷子。
2.避免使用不符合规定的化学品或器具。
3.定期检查晶间腐蚀仪安全门上的夹爪,确保其牢固可靠。
4.定期检查晶间腐蚀仪的电源和数据线,确保接触良好。
5.定期检查晶间腐蚀仪的气体管道,确保其畅通无阻。
6.定期检查晶间腐蚀仪的氨气回收器和排放器,确保其畅通无阻。
7.定期检查晶间腐蚀仪的操作参数,如气体流量、温度等,确保其设置准确。
在使用晶间腐蚀仪的过程中,若出现任何不适当的状况,请立刻暂停操作。
若问题无法得到自行解决,请与相关人员联系,如设备维护人员或售后服务人员等。
cf8m cf3m的晶间腐蚀试验要求
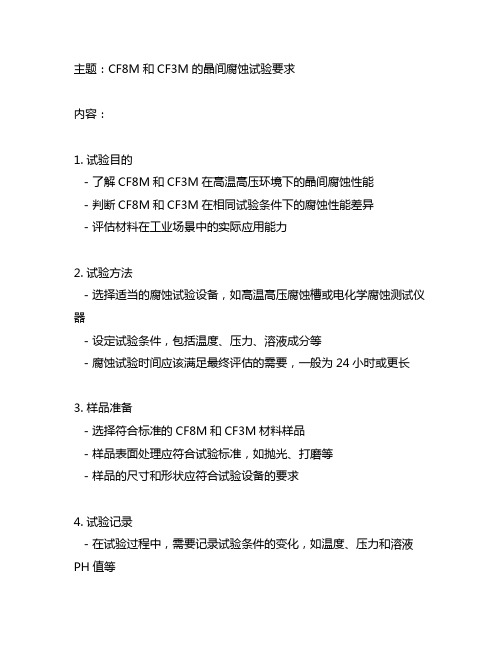
主题:CF8M和CF3M的晶间腐蚀试验要求内容:1. 试验目的- 了解CF8M和CF3M在高温高压环境下的晶间腐蚀性能- 判断CF8M和CF3M在相同试验条件下的腐蚀性能差异- 评估材料在工业场景中的实际应用能力2. 试验方法- 选择适当的腐蚀试验设备,如高温高压腐蚀槽或电化学腐蚀测试仪器- 设定试验条件,包括温度、压力、溶液成分等- 腐蚀试验时间应该满足最终评估的需要,一般为24小时或更长3. 样品准备- 选择符合标准的CF8M和CF3M材料样品- 样品表面处理应符合试验标准,如抛光、打磨等- 样品的尺寸和形状应符合试验设备的要求4. 试验记录- 在试验过程中,需要记录试验条件的变化,如温度、压力和溶液PH值等- 记录样品表面的变化情况,包括腐蚀痕迹和颜色变化- 定期取样进行观察和分析5. 试验结果分析- 对试验结束后的样品进行观察和测量,评估腐蚀程度- 对CF8M和CF3M样品在相同条件下的腐蚀情况进行比较分析 - 结合试验结果和实际应用需求,进行腐蚀性能评估6. 结论和建议- 根据试验结果得出结论,判断CF8M和CF3M的晶间腐蚀性能优劣- 提出针对性的改进建议,如材料配方、表面处理等方法- 结论和建议应该准确客观,为后续材料选择和应用提供参考依据结论:CF8M和CF3M的晶间腐蚀试验要求包括试验目的、方法、样品准备、试验记录、试验结果分析以及结论和建议。
通过严格按照试验要求进行试验,能够得出客观准确的腐蚀性能评估,为材料在工业应用中的选择和改进提供重要参考。
扩展内容:在进行CF8M和CF3M的晶间腐蚀试验时,样品的准备和处理是非常重要的。
需要选择符合标准的CF8M和CF3M材料样品,以保证试验结果的准确性。
这些样品应该具有代表性,能够真实反映材料的腐蚀性能。
样品的表面处理也至关重要。
通常情况下,样品表面需要经过抛光、打磨等处理,以确保试验时的表面质量和一致性,从而消除表面粗糙度带来的影响,使得试验结果更加可靠。
不锈钢晶间腐蚀试验方法
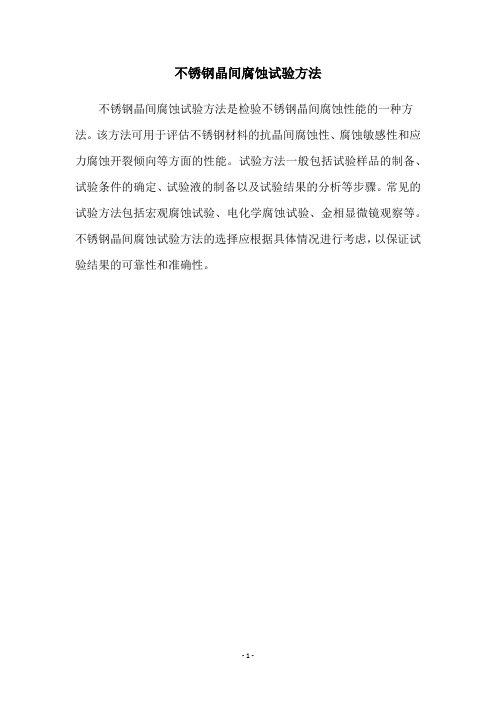
不锈钢晶间腐蚀试验方法
不锈钢晶间腐蚀试验方法是检验不锈钢晶间腐蚀性能的一种方法。
该方法可用于评估不锈钢材料的抗晶间腐蚀性、腐蚀敏感性和应力腐蚀开裂倾向等方面的性能。
试验方法一般包括试验样品的制备、试验条件的确定、试验液的制备以及试验结果的分析等步骤。
常见的试验方法包括宏观腐蚀试验、电化学腐蚀试验、金相显微镜观察等。
不锈钢晶间腐蚀试验方法的选择应根据具体情况进行考虑,以保证试验结果的可靠性和准确性。
- 1 -。
不锈钢复合板复层晶间腐蚀试验方法和标准

不锈钢复合板复层晶间腐蚀试验方法和标准不锈钢复合板是一种类似钢板的结构,它是将不同层材料组合在一起,并形成一种复合结构的板材,这种复合板材具有良好的耐腐蚀性。
不锈钢复合板的主要组成成分如下:钢板固定层、高质量不锈钢保护层和表面涂层。
由于不锈钢复合板连接面采用钉子连接结构,存在晶间腐蚀危险,为此必须提供有效的试验方法和标准来确保不锈钢复合板的使用寿命和安全性。
一、不锈钢复合板晶间腐蚀试验方法1.备试样:将不锈钢复合板样根据相应的尺寸剪切出来,形成与试验要求大小的试样,同时将钢板的边缘处理好,形成平整的边角。
2.开裂检测:裂纹检测采用万能试验机进行测试,将试样放置在试验机上,测量其介电常数以判断试样是否存在裂纹等损伤。
3.蚀试验:通过将试样暴露在恒定温度、恒定盐度的溶液中,以模拟真实的环境条件,然后定期测量溶液中的pH值和电导率等指标,以确定腐蚀损害程度。
二、不锈钢复合板晶间腐蚀标准1.蚀损害水平:对于不锈钢复合板材,采用恒定温度和恒定盐度的溶液进行腐蚀试验,如果腐蚀损害太严重,则不合格;2.疲劳性能:在实际使用中,由于受到动态荷载和负荷的影响,不锈钢复合板可能会造成疲劳损伤,所以,在试验时,应采用充分的实验数据,以模拟实际的使用情况,以确保其在复杂工况下的使用寿命和抗疲劳性能。
三、总结不锈钢复合板是一种类似钢板的结构,它是将不同层材料组合在一起,并形成一种复合结构的板材,这种复合板材具有良好的耐腐蚀性。
由于其采用钉子连接结构,存在晶间腐蚀危险,为此必须提供有效的试验方法和标准来确保不锈钢复合板的使用寿命和安全性。
试验方法主要有裂纹检测、腐蚀试验等,腐蚀标准主要包括腐蚀损害水平和抗疲劳性能等要求。
通过恰当的不锈钢复合板试验方法和标准,可以有效地确保该材料在复杂工况下的安全性和使用寿命。
ASME晶间腐蚀作业指导书

1.Scope
1.1 Practice E—Copper-Copper Sulfate-Sulfuric Acid Test forDetecting Susceptibility to Intergranular Attack in Austenitic Stainless Steels, and
5.3 Specimens of extra-low-carbon and stabilized grades are tested after sensitizing heat treatments at 650 to 675℃,which is the range of maximum carbide precipitation. The most commonly used sensitizing treatment is 1h at 675℃. Care should be taken to avoid carburizing or nitriding the specimens. The heat treating is bestcarriedout in air or neutral salt.
6.4 The time of the test shall be a minimum of 15h, unless a longer time is agreed upon between the purchaser and the producer.If not 15h, the test time shall be specified on the test report. Fresh test solutionwould not be needed if the test were to run 48 or even 72h.(If any adherent copper remains on the specimen, it may be removed by a brief immersion in concentrated nitric acid at room temprature).
晶间腐蚀检测方法
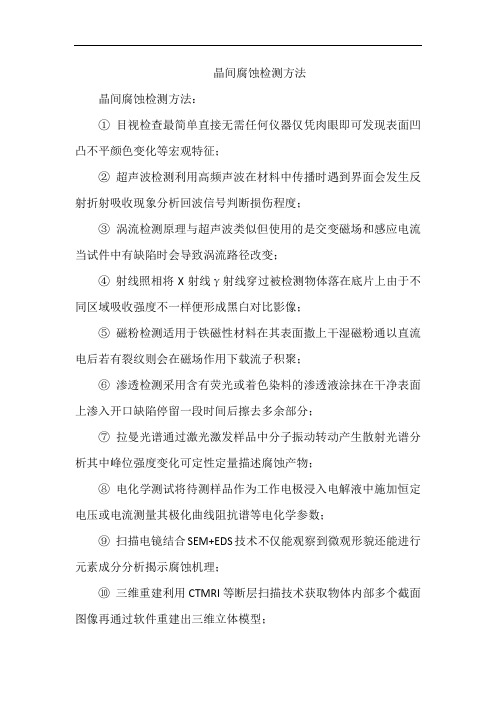
晶间腐蚀检测方法
晶间腐蚀检测方法:
①目视检查最简单直接无需任何仪器仅凭肉眼即可发现表面凹凸不平颜色变化等宏观特征;
②超声波检测利用高频声波在材料中传播时遇到界面会发生反射折射吸收现象分析回波信号判断损伤程度;
③涡流检测原理与超声波类似但使用的是交变磁场和感应电流当试件中有缺陷时会导致涡流路径改变;
④射线照相将X射线γ射线穿过被检测物体落在底片上由于不同区域吸收强度不一样便形成黑白对比影像;
⑤磁粉检测适用于铁磁性材料在其表面撒上干湿磁粉通以直流电后若有裂纹则会在磁场作用下载流子积聚;
⑥渗透检测采用含有荧光或着色染料的渗透液涂抹在干净表面上渗入开口缺陷停留一段时间后擦去多余部分;
⑦拉曼光谱通过激光激发样品中分子振动转动产生散射光谱分析其中峰位强度变化可定性定量描述腐蚀产物;
⑧电化学测试将待测样品作为工作电极浸入电解液中施加恒定电压或电流测量其极化曲线阻抗谱等电化学参数;
⑨扫描电镜结合SEM+EDS技术不仅能观察到微观形貌还能进行元素成分分析揭示腐蚀机理;
⑩三维重建利用CTMRI等断层扫描技术获取物体内部多个截面图像再通过软件重建出三维立体模型;
⑪声发射监测在设备运行状态下安装拾音器捕捉因晶间腐蚀引发的微弱声波信号实现在线预警;
⑫模拟预测基于有限元分析法建立腐蚀模型输入环境介质成分温度应力等边界条件预测服役寿命。
- 1、下载文档前请自行甄别文档内容的完整性,平台不提供额外的编辑、内容补充、找答案等附加服务。
- 2、"仅部分预览"的文档,不可在线预览部分如存在完整性等问题,可反馈申请退款(可完整预览的文档不适用该条件!)。
- 3、如文档侵犯您的权益,请联系客服反馈,我们会尽快为您处理(人工客服工作时间:9:00-18:30)。
GB——试验溶液高于试样20mm以上。仲裁试验时,试验溶液量按试样表面积计算,其量在8ml/cm2以上。
ASTM——溶液应浸没试样,试验溶液量按试样表面积算,其量不少于8mL/cm2。
JIS——同ASTM。
ISO——同ASTM。
ISO——对评定结果有怀疑时,应用金相法观察试样纵向横截面来判别是否是晶间腐蚀并测量腐蚀深度。
3.6.3如果怀疑裂纹时由于弯曲产生的裂纹,可对一未经过腐蚀试验的试样进行同样的弯曲,弯曲后进行比较,便可以认定在腐蚀试验试样上看到的裂纹是否是由于晶间腐蚀造成的。
3.7 35%硫酸-硫酸铜晶间腐蚀试验
此方法仅在ISO和JIS中提及,适用范围:
3.6.2试样不能弯曲或弯曲后晶间腐蚀倾向难以判定,则采用金相法观察。
GB——金相磨片应取自试样的非弯曲部位(焊接接头和焊管除外),经浸蚀后(不得过腐蚀),在150-500倍显微镜下观察,允许晶间腐蚀深度由供需双方协商确定。
ASTM——用金相法在100~250倍显微镜下观察试样的弯曲外表面。
JIS——用100~200倍的金相显微镜观察试样的弯曲外表面。
3.5.2制样,须送金工车间进行机械加工的先加工后去毛刺,尖锐棱边应倒圆,凡试样表面有显着横向刀、磨痕或机械损伤,有明显淬火变形或裂纹以及肉眼可见冶金缺陷的均不允许试验。
3.5.3对需敏化处理的试样进行敏化处理。
3.5.4对试样进行酸洗去除氧化皮。酸洗液为:100℃开水+氢氟酸+硝酸(1000ml+20ml+50ml),配制酸液时应先倒氢氟酸后倒硝酸。
OD>15
80~100
≦20
—
管壁
<4mm
2
管壁厚大于4mm时,一组试样从外壁加工到试样厚度,另一组从从内壁加工到试样厚度,试验后各弯曲其相应的被检验面
管壁
≧4mm
4
ASTM
OD≦38
宽度为25mm的整段管状试样
OD>38
在宽度为25mm的管段上沿周向截取75mm长的部分,即周向弧长为75mm
JIS
3.2.4试样切取及表面研磨时应防止过热。试样的粗糙度必须小于0.8um。
表2
标准
规格(mm)
试样尺寸/mm
试样数量
说明
长
宽
—
—
2
取整段管状试样(内外壁都需检验,如内壁不能弯曲评定时,则用金相法评定)
15≧OD≧5
80~100
—
—
2
取半管状或舟形试样,试验后每个试样均弯曲两个被检验面
标准
适用范围
奥氏体钢不锈钢
双相不锈钢
铁素体不锈钢
GB
适用
适用
——
ASTM
适用于Mo含量≦3%的不锈钢,若Mo%>3%,则应与客户协商是否可用此方法
——
——
ISO
Cr%>16%,Mo%≦3%的奥氏体钢
Cr%>16%,Mo%≦3%的双相钢
Cr含量在16%~20%之间,Mo含量在0%~1%之间的铁素体钢
JIS
同ISO
同ISO
同ISO
3.1试样选取
3.1.1试样应从同一炉号、同一批热处理和同一规格的钢中任意选取,取样部位应按有关标准或技术条件规定取样。
3.1.2铸件试样,从同一炉号钢水浇注的试块中取样。含稳定化元素钛的钢种,在该炉号最末浇注的试样块上取样。
3.1.3试样尺寸按标准规定。厚度>4mm时,内、外壁分别加工至3-4mm。
JIS——管段试样,按压扁试验方法压至平板间距“H”,H=1.09Dt/(0.09D+t),t为壁厚,mm;D为管子的外径,mm。非管段试样,弯至弯角处半径小于试样厚度的1.0倍,弯曲角度≧90°。
ISO——非管段试样,围绕一个半径不超过壁厚的心轴弯曲90°以上。外径不大于60mm的管子,按压扁试验进行压扁,直至压板间距不超过H, H=1.09Dt/ (0.09D +t ), t为名义壁厚,mm;D为管子的外径,mm。
将100g符合GB/T665的分析纯硫酸铜(CuSO4·5H2O)溶解于700mL蒸馏水或去离子水中,再加入100mL符合GB/T625的优级纯硫酸(ISO、JIS及ASTM指出密度为1.84g/mL),用蒸馏水或去离子水稀释至1000mL,配制成硫酸-硫酸铜溶液。
3.5试验步骤
3.5.1根据《检测委托单》验收试样的钢种、炉号、检测内容,填写台帐并做好原始记录。
2.主要设备参数及工装
以16%硫酸—硫酸铜腐蚀试验方法为重点,试验采用回流冷凝器、三角烧瓶、1000W电炉、箱式电阻炉、干燥箱、智能工业调节器AI-804、控温精度≦0.2%、双目显微镜。
3.作业流程与操作规程
各标准对16%硫酸—硫酸铜腐蚀试验的适用范围的规定如表1所示。
表1 16%硫酸—硫酸铜腐蚀试验的适用范围
3.5.5打磨试样,先用60#砂纸粗磨,再用120#砂纸细磨。国标与德标的晶腐样,样的两面都要用手工砂纸磨;横向晶腐两面都要用手工砂纸磨。
3.5.6试验前将试样用适当的溶剂或洗涤剂(非氯化物)除油并干燥。
3.5.7三角烧瓶底座放一层铜屑或铜粒,然后放入试样,保证每个试样与铜屑接触的情况下,同一烧瓶中允许放几层试样,但是试样之间要互不接触,尽量减少离子干挠。(ASTM同一容器中可放3个试样,钢种不同也可以)
3.7 35%硫酸-硫酸铜晶间腐蚀试验…………………………………………………(6)
3.8试验结果处理…………………………………………………………………(6)
3.9电热恒温干燥箱操作规程和注意事项………………………………………(6~7)
3.10电炉操作规程和注意事项……………………………………………………(7)
3.3.3含碳量大于0.030%且不含稳定化元素的钢种不进行敏化处理。
3.3.4对超低碳钢(碳含量不大于0.03%)或稳定化钢种(添加钛或铌)进行敏化处理。
GB——敏化处理温度为650℃,压力加工试样保温两小时,铸件保温一小时,空冷。
ASTM——在650~675℃下热处理,通常采用675℃,保温1h。
文件名称:晶间腐蚀作业标准
文件编号:WLCS-QW-Q-005-2010
版号:D
修改:0
生效日期:2010年05月10日
编制单位:品管部
编制:年月日
审核:年月日
批准:年月日
发放编号:
受控印章:
2.主要设备参数及工装………………………………………………………………(3)
3.作业流程与操作规程………………………………………………………………(3~7)
3.5.9将烧瓶放在加热装置上,通过以冷却水,加热试验溶液,使之保持微沸状态,从溶液达到沸点时开始计时,试验持续时间如下:
GB——试验连续16小时。
ASTM——试验连续15h;
JIS——试验连续16h,仲裁试验20h;
ISO——试验连续20±5h,仲裁试验20h。
3.5.10试验后取出试样,洗净、干燥、弯曲。
OD≦38
宽度为15~25mm的整段管状试样
OD>38,且
壁厚≦5
厚度≦5mm,宽度为15~25mm,周向弧长≧50mm
ISO
—
试样总表面积在15~35cm2之间,按相关产品标准制样。
3.3试样的敏化处理
3.3.1试样的敏化处理在研磨前进行。
3.3.2敏化前试样必须用溶剂式洗涤剂(非氯化物),如丙酮,酒精,去油并干燥,去油后的试样不能用手触摸。
1.1.6有责任接收上级主管部门的考核,复查结果。
1.1.7努力钻研技术,熟悉并认真执行标准,掌握好本岗位的操作技能。
1.2权限
1.2.1对职权范围内的检验任务,按产品的规定有权作出检验结论。
1.2.2对既无产品性能说明,又无技术标准的产品有权拒绝接收检验。
1.2.3有权拒绝外来人员进入试验室,以防药品外流及干扰自已的分析测试工作。
3.1试样选取………………………………………………………………………(3)
3.4试验溶液………………………………………………………………………(4)
3.5试验步骤………………………………………………………………………(4~5)
3.6试验结果评定…………………………………………………………………(6)
3.7.3试验后取出试样,洗净、干燥、弯曲,弯曲方法按3.5.5中规定进行。
3.7.4试验结果评定同3.6。
3.8试验结果处理
3.8.1产品质量必须符合所相应要求的标准后方可出厂。
3.8.2对达不到标准要求的要进行复验。
3.8.3对复验仍达不到要求的产品,由质检科进行改判。
3.8.4做好原始记录,试样上打好钢印。
GB——铜屑或铜粒的纯度不小于99.5%,同一烧瓶中的试样应为同一钢种。
ASTM——铜屑或铜粒为电解级别,同一烧瓶中的试样最好为同一钢种,也可以为不同钢种。
JIS——铜屑或铜粒应为JIS H3100中的C1 100级别,同一烧瓶中的试样可为不同钢种。
ISO——同ASTM,另外溶液中Cu的含量至少为50g/L。
4.相关文件……………………………………………………………………………(7~8)
5.质量记录……………………………………………………………………………(8)
6.修订记录……………………………………………………………………………(8)
7.附件…………………………………………………………………………………(8)
图1
3.6试验结果评定
3.6.1弯曲后的试样在放大镜下观察弯曲试样外表面,有无晶间腐蚀而产生的裂纹。从试样的弯曲部位棱角产生的裂纹,以及不伴有裂纹的滑移线、皱纹和表面粗糙等都不能认为是晶间腐蚀而产生的裂纹。放大镜放大倍数符合以下要求: