塑料制品常见缺陷
塑料制品的常见缺陷及改善方法
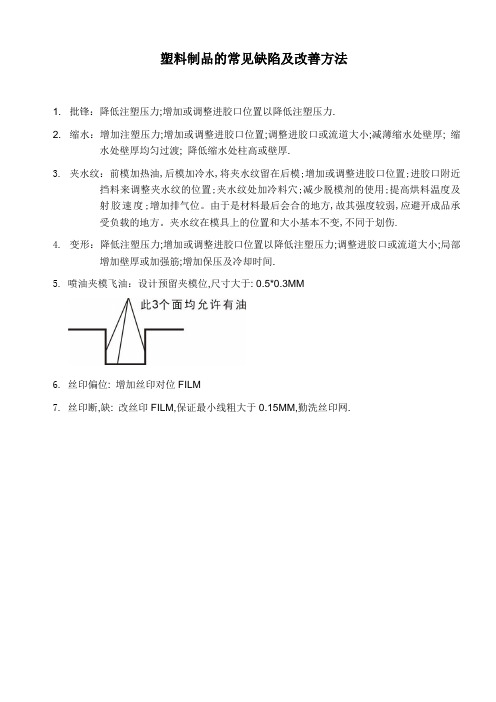
塑料制品的常见缺陷及改善方法
1. 批锋:降低注塑压力;增加或调整进胶口位置以降低注塑压力.
2. 缩水:增加注塑压力;增加或调整进胶口位置;调整进胶口或流道大小;减薄缩水处壁厚; 缩
水处壁厚均匀过渡; 降低缩水处柱高或壁厚.
3.夹水纹:前模加热油,后模加冷水,将夹水纹留在后模;增加或调整进胶口位置;进胶口附近
挡料来调整夹水纹的位置;夹水纹处加冷料穴;减少脱模剂的使用;提高烘料温度及
射胶速度;增加排气位。
由于是材料最后会合的地方,故其强度较弱,应避开成品承
受负载的地方。
夹水纹在模具上的位置和大小基本不变,不同于划伤.
4.变形:降低注塑压力;增加或调整进胶口位置以降低注塑压力;调整进胶口或流道大小;局部
增加壁厚或加强筋;增加保压及冷却时间.
5.喷油夹模飞油:设计预留夹模位,尺寸大于: 0.5*0.3MM
6.丝印偏位: 增加丝印对位FILM
7.丝印断,缺: 改丝印FILM,保证最小线粗大于0.15MM,勤洗丝印网.。
塑胶产品的常见缺陷及分析

塑胶产品的常见缺陷及分析塑料制品是现代生活中不可或缺的一部分。
然而,塑料制品仍然存在一些常见的缺陷,这些缺陷可能导致产品质量下降,甚至无法使用。
下面是一些常见的塑料制品缺陷及其分析。
1.气泡和气孔:塑料制品中的气泡和气孔是由于在制造过程中塑料内部的空气没有完全排除或者在冷却期间塑料表面形成的。
这些气泡和气孔会导致产品表面不光滑,并在应力作用下引起断裂。
减少气泡和气孔的方法包括将塑料完全熔化,并控制良好的冷却过程。
2.毛边和厚度不均:由于模具设计和制造不当,塑料制品的边缘可能会有毛边。
毛边的存在会影响产品的外观和使用寿命。
此外,塑料制品的厚度分布不均匀可能导致产品一些部分容易破裂。
为了解决这些问题,需要优化模具设计,并确保模具制造过程的准确性。
3.烧伤和变色:在注塑过程中,如果温度控制不当,塑料可能会被过热,导致烧伤和变色。
这些问题会影响产品的外观和性能。
要解决这些问题,需要正确控制注塑机的温度和压力,并使用合适的冷却设备。
4.变形和翘曲:塑料制品可能在使用过程中变形或翘曲,这主要是由于应力超过材料的强度限制引起的。
为了避免变形和翘曲,可以通过增加产品的结构设计,加固材料强度或者改变制造过程来提高产品的稳定性。
5.色差:塑料制品可能存在色差,这是由于原料、配方和加工条件的变化引起的。
色差会影响产品的外观一致性。
要解决这个问题,需要优化原料和配方的选择,严格控制加工过程的温度和压力,以确保产品色差的控制在可接受的范围内。
综上所述,塑料制品的常见缺陷包括气泡和气孔、毛边和厚度不均、烧伤和变色、变形和翘曲以及色差。
这些缺陷可能导致产品质量下降,影响外观和性能。
为了解决这些问题,需要优化模具设计、加强原料和配方的控制,严格控制加工过程中的温度和压力。
只有通过严格的质量控制,才能生产出高质量的塑料制品。
塑料件缺陷及改进措施

塑料件缺陷及改进措施塑料件在实际应用中存在一些常见的缺陷,这些缺陷可能会对产品的质量和性能产生负面的影响。
下面将介绍一些常见的塑料件缺陷,并提出相应的改进措施。
1.熔接线痕:在注塑过程中,由于熔融塑料的流动不均匀,容易形成熔接线痕。
这些痕迹可能会导致产品强度降低、疲劳性能差等问题。
改进措施:调整注塑工艺参数,如制定适当的注射速度、保持压力等,以促进塑料的均匀流动,减少熔接线痕的产生。
2.气泡:注塑过程中,由于塑料内含有的气体随着高温熔融逸出,易形成气泡。
气泡会导致产品的密封性能下降、外观质量差等问题。
改进措施:提高注塑设备的真空度,减少气体残留。
此外,在塑料原料中加入消泡剂,能够降低气泡的产生。
3.龟裂:塑料零件在冷却过程中,由于不均匀的收缩率和内应力,易出现龟裂缺陷。
这种缺陷会导致产品的强度下降、易开裂等问题。
改进措施:采用合适的冷却方法,如适当提高冷却介质的温度、均匀冷却等,以减少塑料件的收缩和内应力的产生。
4.比色差:一些塑料件在生产过程中,由于塑料原料的不均匀混合或加工温度控制不当,易形成色差。
这会导致产品的外观质量差,影响产品的整体美观度。
改进措施:严格控制塑料原料的配比,确保原料的均匀混合。
同时,加强对注塑设备的温度控制,保持适当的加工温度,有助于减少温度对产品颜色的影响。
5.纹理不良:在塑料件表面会产生一些不良的纹理,如模具印痕、晶化痕迹等。
这些缺陷会降低产品的表面质量、减少产品的美观度。
改进措施:优化模具的设计和制造工艺,减少模具表面的磨损和粗糙度。
同时,在注塑过程中控制好注塑温度和注塑压力,以减小纹理缺陷的产生。
总而言之,塑料件的缺陷主要体现在熔接线痕、气泡、龟裂、比色差和纹理不良等方面。
为了改善塑料件的质量和性能,应从加工工艺、原料控制、模具改进等方面入手,提高生产工艺的稳定性和可控性。
同时,加强质量检测和监控,及时发现和解决问题,以确保塑料件的质量满足产品要求。
塑料件缺陷范文范文

塑料件缺陷范文范文一、引言塑料制品作为一种重要的工业产品,在我们的日常生活中起着不可或缺的作用。
然而,由于生产过程中的一些问题,塑料件往往会出现一些不可避免的缺陷。
本文旨在探讨塑料件常见的缺陷及其产生的原因,并提出相应的解决方案,以期提高塑料件的质量。
二、塑料件的常见缺陷1.表面缺陷:塑料件表面可能出现划痕、气泡、色差等问题,影响其外观质量。
2.尺寸缺陷:塑料件的尺寸可能与设计要求不符,包括尺寸过大、过小、不均匀等问题。
3.结构缺陷:塑料件的结构可能存在开裂、变形等问题,影响其使用寿命和强度。
4.功能缺陷:塑料件可能存在功能性能不良的问题,如阻力过大、泄漏等。
三、塑料件缺陷产生的原因1.材料选择不当:塑料件的材料选择不恰当会导致其性能不稳定,易出现缺陷。
2.模具设计问题:塑料件的模具设计不合理会导致形状、尺寸等方面的缺陷。
3.生产工艺控制不严:生产过程中的温度、压力、速度等参数控制不严谨会导致塑料件出现缺陷。
4.人为操作错误:操作人员的技术水平、经验丰富程度等因素也会对塑料件的质量产生影响。
四、解决塑料件缺陷的方法1.加强材料选择:选择合适的塑料材料,进行材料测试和性能评估,确保材料质量稳定。
2.优化模具设计:通过精确的模具设计,确保塑料件的形状、尺寸等符合要求。
3.强化生产工艺控制:加强对生产过程中的温度、压力、速度等参数的控制,确保塑料件质量稳定。
4.培训操作人员:对操作人员进行培训,提高其技术水平和责任心,减少人为操作错误的发生。
五、案例分析以汽车塑料件为例,根据上述解决方法,对常见的缺陷进行分析和解决。
1.表面缺陷:选择适合汽车外观要求的塑料材料,完善表面处理工艺,如喷漆、研磨等,修复塑料件表面的划痕和色差。
2.尺寸缺陷:优化模具设计,通过模具参数控制塑料件的尺寸,采用自动化生产流程,减少人为因素对尺寸的影响。
3.结构缺陷:在原材料中添加增强剂,改善塑料件的强度和耐热性,通过模具设计和生产工艺控制,减少自然热应力对塑料件的影响。
塑料件常见缺陷及对策手册
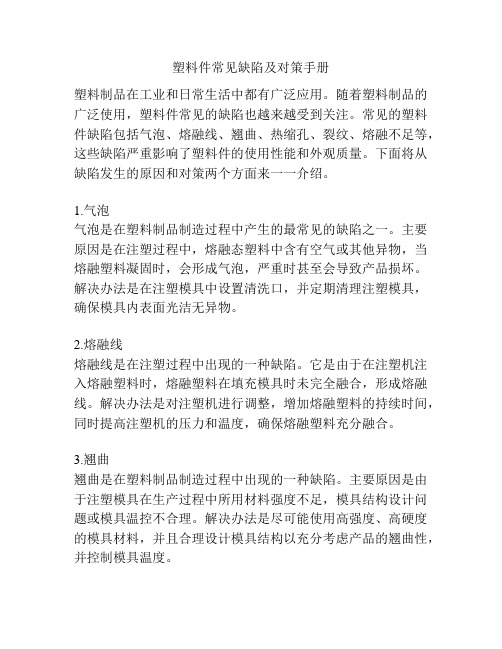
塑料件常见缺陷及对策手册塑料制品在工业和日常生活中都有广泛应用。
随着塑料制品的广泛使用,塑料件常见的缺陷也越来越受到关注。
常见的塑料件缺陷包括气泡、熔融线、翘曲、热缩孔、裂纹、熔融不足等,这些缺陷严重影响了塑料件的使用性能和外观质量。
下面将从缺陷发生的原因和对策两个方面来一一介绍。
1.气泡气泡是在塑料制品制造过程中产生的最常见的缺陷之一。
主要原因是在注塑过程中,熔融态塑料中含有空气或其他异物,当熔融塑料凝固时,会形成气泡,严重时甚至会导致产品损坏。
解决办法是在注塑模具中设置清洗口,并定期清理注塑模具,确保模具内表面光洁无异物。
2.熔融线熔融线是在注塑过程中出现的一种缺陷。
它是由于在注塑机注入熔融塑料时,熔融塑料在填充模具时未完全融合,形成熔融线。
解决办法是对注塑机进行调整,增加熔融塑料的持续时间,同时提高注塑机的压力和温度,确保熔融塑料充分融合。
3.翘曲翘曲是在塑料制品制造过程中出现的一种缺陷。
主要原因是由于注塑模具在生产过程中所用材料强度不足,模具结构设计问题或模具温控不合理。
解决办法是尽可能使用高强度、高硬度的模具材料,并且合理设计模具结构以充分考虑产品的翘曲性,并控制模具温度。
4.热缩孔热缩孔是在塑料制品制造过程中产生的一种缺陷,主要是由于在注塑模具中熔融塑料在凝固过程中由于收缩所产生的孔洞。
解决办法是在注塑模具中设置充气孔,确保熔融塑料能够充分填充模具,减少热缩孔。
5. 裂纹裂纹是在塑料制品制造过程中出现的一种缺陷。
主要原因是由于注塑模具的温度过高或者注塑机的压力过大,在熔融塑料凝固之前就引起了裂纹。
解决办法是控制模具温度和注塑机压力,确保熔融塑料能够充分填充模具,减少裂纹。
6. 熔融不足熔融不足是在塑料制品制造过程中出现的一种缺陷。
主要原因是在注塑模具中填充熔融塑料时,填充不均匀或填充量不足,导致塑料制品没有完全充满模具。
解决办法是控制注塑机的压力和温度,确保熔融塑料能够充分填充模具,减少熔融不足。
塑料件常见缺陷及对策手册

塑料件常见缺陷及对策手册塑料件常见缺陷及对策手册摘要: 塑料件在制造过程中常常会出现不同的缺陷,可能会影响产品的质量和性能。
本手册将列举塑料件常见的缺陷,并提供相应的对策,帮助制造商和工程师有效解决这些问题。
引言: 塑料件是现代工业中常用的制造材料之一,其轻便、耐用以及成本相对较低等优点使它在许多行业中得到广泛应用。
然而,由于制造过程中的一些问题或者材料本身的特性,在塑料件生产中常常会出现一些缺陷。
这些缺陷可能会影响产品的外观、强度和功能等方面。
因此,了解常见的缺陷及其对策是非常重要的。
一、常见缺陷及其对策1. 空气孔: 塑料件表面或内部的气孔通常是由于材料中的气体没有充分排出或者在制造过程中产生的。
这些气孔会对产品的强度和密封性造成影响。
对策:增加塑料件的压力和温度,提高填充速度,增加材料中的气体逸出通道。
2. 熔接痕: 熔接痕通常是由于塑料在填充过程中,两个熔体前线相遇时没有良好地熔合而形成的。
这些痕迹通常在产品表面留下痕迹,并且可能降低强度。
对策:增加填充速度,提高熔体温度,改变模具设计以减少熔接面积。
3. 缩松: 缩松通常是由于塑料在冷却过程中收缩不均匀而形成的。
这些缺陷可能导致产品尺寸不准确或者出现细小的裂纹。
对策:增加冷却时间,改善模具设计,使用符合收缩率要求的塑料。
4. 流痕: 流痕通常是由于填充过程中塑料流动不畅或者遇到障碍物而形成的。
这些痕迹可能在产品表面留下不平整的痕迹,降低产品的外观质量。
对策:增加填充速度,改善模具设计以减少流动阻力,增加模具通道的尺寸。
5. 变形: 塑料件的变形通常是由于内部应力超出材料允许范围或者冷却不均匀而引起的。
这些变形可能导致尺寸不准确、变形或者破裂。
对策:优化模具设计,增加冷却时间,降低制造过程中的应变速度。
6. 色差和污染: 塑料件的色差和污染是由于材料中杂质、填充物或者其他外来物质引起的。
这些问题会影响产品的外观质量。
对策:控制原料的质量,确保生产环境的清洁,适用过滤器和分离器过滤原料。
塑胶件常见的缺陷产生原因及解决办法

塑胶件常见的缺陷产生原因及解决办法一、设计方面的缺陷:1.不合理的尺寸设计:塑胶件的尺寸设计不合理可能导致尺寸偏差过大、尺寸不一致等问题。
解决方法是根据塑胶件的具体用途和要求进行合理的尺寸设计,并进行合适的工艺分析和模流分析。
2.没有考虑到材料的特性:不同塑料材料具有不同的热胀冷缩系数、熔融温度等特性,设计时没有考虑到这些特性可能导致尺寸偏差、变形等问题。
解决方法是根据塑料材料的特性进行合适的设计和模具制造选型。
3.模具设计问题:模具设计不合理或者制造质量不过关可能导致塑胶件的缺陷问题。
解决方法是进行合理的模具设计,并选择专业的模具制造厂家。
4.不合理的壁厚设计:塑胶件的壁厚设计不合理可能导致塑胶件变形、收缩不均匀等问题。
解决方法是根据塑胶件的材料特性和实际使用要求进行合理的壁厚设计。
二、材料方面的缺陷:1.材料质量问题:不合格的原料质量可能导致塑胶件出现异味、颜色不均匀等问题。
解决方法是选择合格的塑料原料供应商,并进行原料的严格检验。
2.材料混合不均匀:塑料材料在加工过程中没有充分混合均匀可能导致塑胶件的颜色不均匀等问题。
解决方法是进行充分的原料预处理和混炼,确保塑料材料的均匀性。
3.熔体温度不均匀:塑料材料在注塑过程中温度不均匀可能导致塑胶件尺寸偏差、表面气泡等问题。
解决方法是调整注塑机的温度控制系统,确保熔体温度均匀稳定。
三、工艺方面的缺陷:1.注塑工艺参数设置不当:注塑过程中,如射胶压力、射胶速度、冷却时间等工艺参数设置不当可能导致塑胶件出现尺寸偏差、气泡、表面缺陷等问题。
解决方法是根据塑料的特性和产品要求进行合理的工艺参数设置。
2.模具温控不均匀:模具温度不均匀可能导致塑胶件出现收缩不一致、尺寸偏差等问题。
解决方法是进行模具温度分析和温控系统的优化。
可以采用热流道模具、快速温度控制系统等技术手段解决问题。
3.模具保养不当:模具的使用寿命长,如果没有进行定期的保养和维修可能导致塑胶件出现模纹、模具磨损等问题。
塑胶常见不良及解决方法

塑胶常见不良及解决方法塑胶是一种常见的材料,广泛应用于各种行业和领域。
然而,由于塑胶的特性以及制造过程中的一些问题,常常会出现一些不良现象。
本文将重点介绍一些常见的塑胶不良及其解决方法。
1.氣泡:塑膠制品中常見的一種不良現象是氣泡,這會在成品表面或内部形成小气囊。
气泡的形成是由于塑胶熔融时含有的空气或挥发物没有充分释放出来。
解决方法包括降低加工温度、增加熔体压力、增加注射速度和使用抗气泡添加剂等。
2.热胀冷缩:塑胶制品在温度变化下会发生热胀冷缩,导致尺寸变化。
这可能会导致配件无法正常连接或安装。
为了解决这个问题,可以采用材料改性或加工工艺改进,如增加冷却时间、降低注射温度等。
3.白化:白化是指塑胶制品表面或内部出现白色斑点或条纹。
这种现象通常是由于塑胶在注射过程中发生气泡聚集或制品未达到均匀熔融所致。
解决方法包括优化注射工艺、增加熔体压力、使用抗白化添加剂等。
4.热裂纹:热裂纹是指在塑胶产品成型过程中出现的裂纹现象。
这通常是由于塑胶在成型过程中存在过大的应力集中,导致塑胶产生裂纹。
解决方法包括改变模具设计、增加冷却时间、预混塑胶料等。
5.变色:变色是指塑胶制品在使用或储存过程中出现颜色变化。
这可能是由于塑胶材料受到光、热、氧化等外界因素的影响所致。
解决方法包括选择适当的防褪色添加剂、合理储存塑胶制品等。
6.毛刺:毛刺是指塑胶制品表面出现不平整、刺状的小颗粒。
这通常是由于模具表面不平整或注射工艺不当所导致的。
解决方法包括优化模具设计、控制注射压力、调整注射速度等。
7.缩水:缩水是指塑胶制品在冷却过程中发生体积收缩。
这可能导致尺寸偏离设计要求。
解决方法包括优化塑胶成型工艺、增加冷却时间和选择合适的材料等。
8.潜伏期延长:有些塑胶在使用一段时间后会发生不良现象,如变形、断裂等。
这可能是由于塑胶受到环境因素、应力或热老化的影响导致的。
解决方法包括选择合适的材料、控制加工温度、降低应力等。
总结起来,塑胶制品的不良现象可能是由于材料、工艺或环境等多种因素造成的。
塑料件常见不良
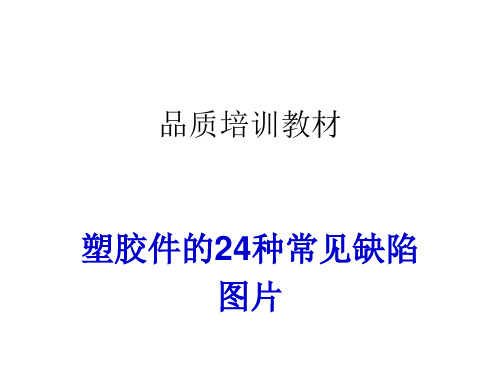
十三、破损/缺口:尤其是对插口不可以有。
破损/缺口
十四、油污:外观件、浅色件特别明显
油污NG!
披锋
毛边
六、多胶:
多胶 NG
七、黑点/异色点:在零件表面有不同的颜色
黑点NG!
八、变形:
平面中间拱起变形
柱子弯曲变形
九、披锋丝(拉丝):
披锋丝(拉丝)NG
十、顶高(顶白):顶针把零件表面顶起
顶高(顶针印)
十一、顶穿(顶破): 顶针把零件表面顶出深坑 甚至零件被顶穿破
顶穿
十二、烧焦:通常表面有细微孔状,色泽发暗
品质培训教材
塑胶件的24种常见分
缩水(凹痕) 缩水(凹痕)
二、气纹:塑料件表面明显的光泽差异
气纹
三、缺料:零件不完整
缺料
四、水口(进胶口)不平整: 所有塑料件都有进胶点, 通常高度小于0.1mm
水口不平
五、披锋(毛边):所有的分型线都会存在, 通常高度小于0.1mm
塑料件常见缺陷及对策手册

塑料件常见缺陷及对策手册
塑料件常见缺陷及对策手册如下:
1. 熔体流动不畅:主要表现为铸件的形状或尺寸变化,可能会影响产品的外观和使用效果。
解决方案包括提高模具温度、加大喷嘴孔径、增加压力等。
2. 表面气泡:主要是由于熔融状态下的气体逸出不完全导致的,会影响产品的外观和质量。
解决方法包括提高熔体温度、增加注射速度、调整模具结构等。
3. 热裂纹:主要是由于材料热应力引起的,会影响产品的性能和寿命。
解决方案包括减少注射压力、降低模具温度、改进模具结构等。
4. 缩孔:主要是由于熔体内部存在气体或材料中含水过多导致的。
解决方案包括预干燥原材料、增加熔体温度、减少注射速度等。
5. 毛边和毛刺:主要是由于模具设计不合理、注射速度过快等原因导致的。
解决方案包括调整模具结构、降低注射速度等。
6. 非均匀收缩:主要表现为铸件形状或尺寸的变化不一致,会影响产品的精度和性能。
解决方案包括增加模具温度、降低注射压力等。
7. 材料老化:主要是由于材料长时间暴露在高温、紫外线等环境下导致的。
解决方案包括选择耐老化的材料、优化制造工艺等。
以上是塑料件常见缺陷及对策手册的简单介绍,具体情况还需要根据实际生产中遇到的具体问题进行分析和处理。
塑胶件常见缺陷

一.塑膠注塑件一般出現的問題:1.粘模(扯模):制品的柱筋及細小多型腔件,在脫模後未能脫模而粘附在模具相應位置;通常因成型壓力偏大,或模具局部粗糙等因素導致.2.走不齊(填充不足):制品結構與所設計的形狀結構不符,局部膠位不滿足,短少,塑件未能完全充滿.通常產生於制品的柱,孔或薄膠位以及離入水口較遠部位,因成型壓力不夠,模濕不足,骨位過薄,局部有油或排氣不夠(困氣)導致膠位不能填充滿.3.多膠:制品結構與所設計的形狀結構不符,局部多出膠位,或塑件表面有點狀物,四周凹陷中間击起,指甲可感覺到,通常由模具成型面碰,崩缺,損傷及細小型芯頂針移位或斷掉導致.4.縮水:制品表面因成型時,冷卻硬化收縮,產生的肉眼可見凹坑或窩狀現象稱為縮水.制品結構的較厚膠位,如骨位,柱位等對應表面,因成型壓力不足,保壓及射膠時間偏短,或模溫偏高,而導致因局部收縮偏大成而造成.、5.夾水紋(熔接痕):熔膠在模腔內流動中分流後再匯合時不充分,不能完全熔合,冷卻後在塑件表面形成的線狀痕跡和線裝熔接縫.因模溫偏低,料溫偏低,制品局部偏薄或模具有粗大型芯及材料流動性不好等都會導致夾水紋產生.溫度及困氣也對其有最大影響.6.烘xx(光影):制品厚薄膠位在熔膠流動時受阻改變方向而形成的光澤不一致現象.通常在水口周圍,塑件表面呈光澤度不夠,顏色灰蒙.制品結構的薄膠位,止口位,扣位與周圍過渡斷差明顯,原料流動性溫差,成型料溫.模溫偏低或射膠壓力速度太大,模具排氣不良,啤塑壓力過高皆易產生烘印.7.披鋒(xx邊):制品的邊,棱,孔,柱端等模具型腔內所有分模線,鑲塊及頂針位相對應位成型後產生較薄的膠料,稱為披鋒,有刺手感覺.合模線,鑲件頂針及活動碰撞位產生較大間隙或成型壓力太大,模具日久磨損,而鎖模不緊,鎖模力不足時易導致披鋒產生.8.氣紋:在入水口位,走膠盡頭及翻水位(在較高寬大骨筋位走膠需改變方向)對應表面形成的與周圍顏色暗,朦的現象.通常因成型射膠速度太大或太小,壓力偏小及模溫偏低,料溫太高導致.9.困氣:制品成型之流程盡頭位置出現的因氣蝕而發亮的現象.模具排氣結構不足,原材料含低分子成分或水分較多,料溫模溫偏高而導致成型時,氣體無法及時排除模腔被壓縮對制品表面造成鋟蝕.10.燒焦:制品表面呈灰白,黃,橙色條狀變色痕跡.通常因困氣或流道,射嘴,料筒有尖銳傷痕位,熔膠在高速流動時受剪切而降解變色,呈燒焦狀.11.混色:制品表面旦線團塊狀與周圍顏色不一致,顏色不均的現象.通常出現在口澆口附近,熔合部位或整個塑件上.原材料和色粉含雜料,或混和不充分,塑化不良導致制品表面顏色不均勻,彩色顏件最容易形成,也與料筒清潔或背壓有關.12.發白:制品水口有脫模時爆裂,發白或不規則斷裂.因成型壓力大,射膠(保壓)(冷卻)時間太長或頂出太快(頂針分佈不合理),水口不光滑等原因導致脫模時水口受力偏大而發生不良,主要發生在透明制品,使用較脆膠料(如PS,PMMA等料).13.水口加工不良:制品水口被剪除偏高,偏低,白化變形,熱剪後卷起及漏加工等.因加工方法不合理,或加工工具不合適,加工不認真,導致水口位加工不合要求,影響外觀或裝配.14.鋸齒邊:加工部位被加工太多或加工面不平滑,因加工方法,工具或人為因素而導致.15.麻點:制品光滑表面出現的細小密集點狀击起,模糊不清晰,指圍感覺不到,稱為麻點.因材料內含有的輔助劑(如防火PC料的陰燃劑),或成型工藝不合理而導致,或原料本身或熔料不好引起.16.拖傷:制品的側邊,孔等位置在脫模時被拖成的痕跡,因制品側邊,孔等位置脫模斜度不夠,蝕紋偏粗或脫出受力偏大導致.17.拖花:出模後造成損傷.通常出現在邊角位上,可能因出模角度與紋路有問題引起.18.拖白:制品的側邊,柱孔等位脫模時產生的發白現象.因制品的側邊,柱孔等位脫模斜度不夠,蝕紋偏粗局部不夠光滑,而導致脫出受力偏大導致.19.頂白:頂針位在脫模頂出時,使對應表面出現發白痕跡或清晰白印,向上击起.因頂針分佈不合理,頂針位結構偏薄.模具頂針過少,或頂出太快,冷卻時間不足,而導致頂傷制品.20.拖絲:水口脫出時,從射嘴拖出的絲狀物未被清除而被成型粘復到焉一制品的表面,呈絲線狀或線狀痕,稱拖絲.因射嘴溫度偏高,或模溫不當,或防流涎裝置不良,或成型工藝不合理導致.21.冷膠:與制品整體膠料未完全融合,有清晰分界線的團塊狀的現象.因模具流道及射嘴等位在上啤時溢出或斷裂遺留的未清除冷膠被成型到下一啤制品外表面所致.22.料花:制品表面細小不規則的冷膠料,稱料花.因模具流道和型腔內遺留有上一啤脫模時的細小碎膠料被成型到下一啤制品上所致.23.氣泡:塑料在充模過程中受到氣體的干擾而在制品表面上呈現中空狀击起,或透明制品膠位內中空泡狀.由塑膠原料水分含量偏大,低分子產物含量偏大,料溫偏高,或背壓不夠,成型工藝不合理,冷卻時間不足等原因造成.24.油漬:制品上附著有模具上的油跡(防銹油,頂針油,或黃油等).在塑件表面呈不規則痕跡,影響塑件光澤度.模具結構位用油太多,清除不夠干凈導致表面產生的斑點狀發亮現狀,稱為油點.頂針及行位,導柱部位用油較多,運動時滴落到模腔內.25.手指印:制品表面有手指印跡.因手指有油污,汗漬而手指接觸到制品表面而產生的印跡.26.膠漬:制品蝕紋部位不規則光亮痕,光滑面呈霧狀,麻點狀不光亮現象.模具表面被細微膠粉遮蓋或被低分子產物遮蔽,而導致制品表面不能清晰表現設計的狀態.27.黑點(雜質點):制品表面的呈不同於制品顏色的點,線狀異物,因原材料,色粉內有異物,或環境中的雜質及模具活動部分損傷的金屬等吸附到模具型腔,而成型到制品表面所致.28.衝紋(流紋):制品表面沿流動(填充)方向呈現的蛇形或放射狀的紋路,呈花紋狀流痕,清晰可見,指圍感覺不到,稱衝紋.因模溫太低或太高,射速過低,或射速過快,半凝固料受到熱熔料推擠而導致.白色件最容易產生.二.塑膠組件一般容易出現的問題:1.尺寸不符:制品尺寸超出圖紙或規定的控制尺寸範圍.因成型時壓力偏大偏小,射膠時間偏長偏短或模具局部鑲件及活動結構位鬆動等原因造成.2.偏位(shift):一般指螺絲柱,孔位等偏離中心,嚴重者會破裂.3.裝配鬆緊:相關制品在組裝時,偏鬆偏緊,影響到產品的使用功能效果或造成生產線裝配困難.因相關制品尺寸超差或結構位不良導致.4.裝配間隙大:相關制品在組裝後,在邊或角位產生間隙(通常以不大0.2mm為合格).因相應制品變形或尺寸超差及局部缺陷導致.5.裝配刮手(段差或錯位):相關制品在組裝後,邊或角位單獨移出,形成斷面差,觸摸刮手.(通常以不大0.2mm為合格)6.裝配卡鍵(JAM KEY):字鈕鍵組裝到相應鈕孔位,字鈕鍵不能順暢按設計功能作回復運動.字鈕孔位有披鋒或尺寸大,按鈕鍵偏大偏小或高度低等原因導致.7.機身不平(變形):相應制品組裝後在自然放置時,機身底部不平(通常以不大於0.2mm腳不平為合格).相關制品因為尺寸超差,扣位不合,收螺絲不平衡,成型及包裝導致扭曲變形而造成.8.虛扣(扣位高低):相關組合件,組裝後扣位未扣實,用手掰開或跌落震機試驗,扣位會張開形成明顯間隙.扣位尺寸超差或整件尺寸超差(模具成型扣位部分鑲件或行位鬆動變形)導致.9.柱爆(xx):柱孔在打螺絲時被打爆裂或發白,或按規定次數重復打螺絲時收不緊(不能受力),柱孔直徑或深度不符,或所用原料機械性能不夠,成型時料溫偏高使機械性能降低而導致.三.塑膠成品一般容易出現的問題:1.噴涂類:(1)塑膠顏色不符:制品外表顏色或蝕紋效果與樣板不一樣(超出一PantoneNo為顏色不符).通常因色粉(色種)配比,原料的底色,料溫的高低造成.(2)顏色不符:噴涂後制品表面顏色不同於樣板或規定的顏色.(通常以一個PantoneNo為標準,超出為不合格).歷為所用油墨色與塑膠件顏色不同,或噴涂層偏厚偏薄導致色差.(3)位置不符:規定噴油的部分未噴或不需噴油的部位被噴上油墨.不明確要求或噴涂工具和程序不合適而導致.(4)粗糙:制品表面噴油層手感不光滑,因噴槍調節不合適,噴涂距離偏近或油墨不符造成.(5)蜂窩點:制品表面噴油層有密集凹陷坑點狀痕.因噴涂方式及噴槍調節不當導致.(6)啞色:指制品表面噴油層不夠光亮,色澤偏暗偏朦.油墨配比不當或噴涂時間距離偏遠或偏近導致.(7)光亮:制品表面噴油層光滑,返光耀眼(通常以樣板程度為標準控制).因油墨配比不當或噴涂層太厚造成.(8)砂紙痕:制品表面噴油層呈現的塊狀條形痕跡.對噴油部位不良缺陷用砂紙加工時,砂紙偏粗,或加工力度偏大導致.(9)有塵:制品表面噴油層呈現,點線狀明顯击起.因制品暴露在環境中時間偏長,環境不夠干凈,油墨不夠純凈而導致.(10)污糟:指制品表面噴油層有不可擦拭清除的髒物,噴槍用壓縮空氣水分含量大,制品表面髒未清除干淨等因素導致噴油後的污糟。
塑料件常见缺陷及对策手册

塑料件常见缺陷及对策手册塑料件是现代工业中较为常见的一种材料,广泛用于各种机械、电子、医疗设备以及家电等领域。
但是,由于塑料本身的特性和生产加工技术不断更新换代,塑料件在生产过程中常出现一些常见缺陷,严重影响产品的质量和使用寿命。
针对这些常见缺陷,本文就提出了一些对策和解决方案,在生产中有所帮助。
1.针孔和气泡针孔和气泡是塑料制品生产中常见的缺陷,往往由于原料中的杂质和空气等引起。
如果针孔和气泡在外观上很明显,不仅会影响产品的美观度,还会导致产品的硬度和韧度变得不均匀,影响产品的机械性能。
针对这一问题,可以采取以下措施:(1) 优化塑料配方的设计,降低原料中的杂质含量;(2) 调节注塑机的注射速度和注塑温度,保证原料流动性良好;(3) 选择合适的模具设计,提高塑料制品的压力和速度,确保产品内部牢固性。
2. 热分解和氧化热分解和氧化是塑料制品在加热后或存放时间较长后表现出来的特点,也是塑料件常见的缺陷之一。
这种缺陷会使得塑料制品变得脆弱和失去抗老化能力,其外观和性能都会明显改变。
针对这一问题,可以采取以下措施:(1) 选用高质量的塑料原料或添加剂,降低其分解和氧化的风险;(2) 保证存储环境温度和湿度适宜,避免对塑料制品的影响;(3) 通过在塑料制品表面覆盖一层防护层来防止空气和其他化学物质对其的侵蚀。
3. 毛边和裂口毛边和裂口是塑料件在加工过程中常见的缺陷,往往由于模具的设计不当或材料的选用不当引起。
如果毛边和裂口很严重,会对产品的安全性造成威胁,同时也会降低产品的使用寿命。
针对这一问题,可以采取以下措施:(1) 优化模具设计,减少毛边和裂口的产生;(2) 使用高质量的塑料原料和添加剂,提高塑料制品的强度和韧性;(3) 增加塑料制品加工的压力和温度,提高塑料制品的内部固结性。
4. 颜色不均匀在塑料制品加工过程中,颜色不均匀是一个常见问题。
如果塑料部件的颜色不均匀,会影响产品的美观度,使得产品的整体质量变差。
塑料制品缺陷及改善措施

塑料制品缺陷及改善措施
随着现代化社会的发展,塑料制品已经成为人们日常生活的必需品,因其成本低廉、易加工、轻便等优点而深受人们喜爱。
但是,由于塑料不易降解,造成了巨大的环境污染和资源浪费。
本文将以塑料制品的缺陷作为主要研究的对象,探讨塑料制品的改善措施。
一、塑料制品的缺陷
1、易碎:尽管塑料制品轻便易携带,但是它具有易碎性。
一旦掉落或者撞击,塑料制品容易出现破裂或变形的现象,影响使用寿命。
2、易老化:塑料制品通常使用寿命比较短。
当塑料制品
受到阳光、氧气、热、光的暴露,会发生老化而失去使用价值。
3、污染环境:塑料制品很难被分解,因此被誉为是环境
的“白色污染源”,严重影响了环境的美观和生态健康。
二、改善措施
1. 选择更加环保的材料
生物可降解材料是一个良好的替代品。
例如,一些聚乳酸等可生物降解塑料可以取代传统的塑料制品。
2. 降低塑料制品的污染
应当建立一个完善的废塑料回收和处理系统。
塑料制品的回收利用应该得到强化和推广,使塑料废弃物得以重生。
3.增强塑料质量
通过改变塑料的配方和工艺,生产高质量的塑料制品,提高其韧性和耐用性。
4. 推广环保理念
我们需要加强宣传,让人们认识到塑料制品的危害,引导人们减少对塑料制品的依赖,采用更加环保的替代品,从而推动环保理念广泛普及。
5.加强管理
政府和相关行业部门应加强对塑料制品的监管,推行生产、销售与使用责任制,加强塑料制品的质量监管工作。
最后,塑料制品的缺陷已经得到广泛关注,因此,我们需要加强塑料制品的改善工作,减少其对环境造成的污染,让其真正成为环保的材料。
塑料件缺陷原因及改进方法

塑料件缺陷原因及改进方法
一、缺陷原因
1、原料质量低
塑料的弹性、热稳定性及耐腐蚀性是由其原料的质量和成形工艺决定的,原料质量低、成分不符合要求,缺乏纯度和着色,以及尺寸误差等,都会导致塑料件使用性能不稳定,影响整体产品质量。
2、成型条件不合理
塑料件的成型条件在很大程度上影响了其使用性能,不合理的成型条件,如温度太低或太高,塑料流动性差,成型时间太短或太长等,都会导致塑料件加工质量不高,从而影响使用性能。
3、模具设计不规范
塑料模具设计不规范,如分流错误,塑料流通不良,塑料不能完全填满模具,从而导致塑料件加工不精细,使用性能受到影响。
4、冷却条件不适宜
塑料件的冷却条件也影响其使用性能,冷却条件不适宜,会导致塑料件加工质量不高,从而影响整体塑料件使用性能。
5、模具结构不当
不当的模具结构,如模具尺寸过大或过小,模具表面平整程度不够,模具夹具不够,都会导致塑料件成型不正确,从而影响使用性能。
二、改进方法
1、改善原料质量
改善原料质量,确保原料的成分纯度,粒度细化和着色,以及尺寸误差等,以确保塑料件质量。
2、优化成型条件
优化成型条件。
塑料常见缺陷及原因

塑料常见缺陷及原因塑料是一种常见的工程材料,被广泛用于各个领域。
然而,由于其特殊的化学结构和生产工艺,塑料制品在生产过程中常常会出现不同的缺陷。
以下是塑料常见的缺陷及其原因的详细解释。
首先,表面缺陷是最常见的塑料缺陷之一。
表面缺陷包括气泡、凹凸不平、划痕和色差等。
这些表面缺陷主要是由于生产过程中的不良操作或不合适的工艺参数造成的。
例如,气泡可以由于塑料熔融不充分、注射速度过快或模具中有挤出气体等原因引起。
凹凸不平和划痕可能是由于模具表面的不平整或不良的冷却系统造成的。
色差可能是由于原料的不均匀混合或加工温度不稳定等原因导致的。
其次,尺寸偏差也是常见的塑料缺陷之一。
尺寸偏差是指塑料制品与设计图纸规定尺寸的差异。
尺寸偏差可能是由于模具磨损、尺寸设计不合理或加工工艺参数设置错误等原因造成的。
例如,模具磨损会导致塑料制品外形尺寸变大,而模具加工误差会导致塑料制品尺寸偏小。
第三,力学性能不合格也是一种常见的塑料缺陷。
塑料制品的力学性能包括强度、硬度、韧性和耐磨性等。
力学性能不合格可能是由于原料选择错误、加工工艺参数设置不当或塑料制品设计不合理等原因造成的。
例如,原料中添加的助剂种类选择不当可能会降低塑料制品的强度和硬度。
加工时的温度、时间和压力等参数设置不当也会影响塑料制品的力学性能。
第四,热稳定性差是另一种常见的塑料缺陷。
热稳定性差指的是塑料在高温环境下易退化和分解。
热稳定性差主要是由于塑料分子链结构不稳定或原料中的添加剂不当导致的。
例如,一些塑料在高温下会发生热氧化反应,导致分子链的断裂和塑料性能的下降。
此外,添加剂的选择错误或使用不当也会降低塑料的热稳定性。
最后,环境适应性差是塑料常见的缺陷之一。
环境适应性差指的是塑料在特定环境条件下易受到化学物质的侵蚀和腐蚀。
环境适应性差可能是由于塑料分子链结构的特殊性质或塑料表面缺陷导致的。
例如,某些塑料对酸、碱、溶剂或紫外线等有强烈的敏感性,容易发生化学反应,导致塑料性能的下降。
常用塑料件之缺陷及识别

常用塑料件之缺陷及识别1.走料不齐:又名缺料,塑料件边缘光滑,形状不规则,有不整齐之感。
常发生在①离水口最边的地方;②又细又长的骨位。
2.缩水:因部品收缩导致塑料件表面有凹痕,不平整,对光看显示波浪状,常发生在①胶件厚度不均的地方;②胶厚部位;③柱位,骨位。
3.披锋:塑料件边缘多出一块很薄的皮,常发生在①分模面;②模具活动芯位;③顶针位,柱位,孔位,扣位。
4.气泡:塑料件表面有一与周围颜色不同的泡泡,一般分为①由未及时排出之气体、空气、水气形成的气泡;②热冷缩引起的真空泡。
透明部品要特别注意。
5.夹纹:两股以上的料流融合时在塑料件表面形成一条很深之熔结痕。
一般发生在多股料汇合处。
6.射纹:从入水口处开始有多条纹痕向外射,尤以透明件为明显。
7.烧胶:表面不平,有深色或黑色焦痕,一般发生在难走胶、易困气的部位。
8.黑点:有黑色之点状杂质在塑料件表面,一般由材料里混有杂料异引起的。
9.哑色:塑料件表面不反光,不亮,朦胧,尤以透明件易发生。
10.变色:与签办颜色不对。
透明件易变色,一般由色粉材料或调试比例不对,或模温不对引起。
11.皱纹:塑料件表面有波浪纹,由于树脂向一边流动一边变更引起的。
12.变形:塑料件扭曲,不平,不直,一股发生在柱位,骨位,细长胶件,盒状胶件。
PP料尤为常见。
13.用错料:与规定用料不同,可以通过查包装标签,塑料件密度(放水中)及燃烧持续性,火焰和烟的颜色进行识别。
14.粘模:塑料件的局部残留模腔,致使塑料件塑料出后结构不完整(但不同于缺胶)或因设计模具顶出装置系统欠缺,致使塑料件难以从模腔中顶出,一般发生在薄壁,胶骨位,扣位,胶柱位上。
15.拖伤:胶件在出模过程中与模腔表面磨擦使胶件表面出现擦花痕迹。
一般发生在多胶、柱高、柱底。
16.多料:因模腔损伤致使胶件表面多出,一般发生在活动科、柱位,顶针位,分模面。
17.混色:因料不干净或温度过高使胶件表面或内部形成与胶件不同的颜色点(混料不均匀以引起)。
塑料制品常见缺陷与解决办法概述
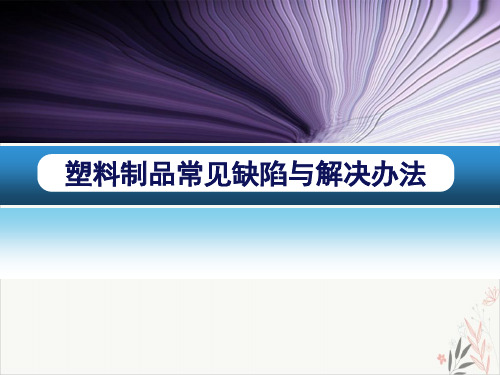
理,脱模时制品受力不均匀
设置
模具强度不够,在成形时发生变 形,使得制品产生附加应力而变 形
加强模具刚性或降低注射 压力
翘曲成因及改善措施 -- 注塑工艺
注射压力过高,沿熔体流动方向上的 分子取向与垂直流动方向上的分子取 向相差较大,这种差异使得制品的内 应力分布不均匀
适当降低注射压力
熔体温度过高,在成形固化时的温度 降较大,制品在急冷过程中会残留大 适当降低熔体温度 量内应力
喷射流成因及改善措施 -- 注塑模具
浇口设计不当
重新布置或改变浇口设计, 引导熔体与侧壁金属模面接 触
浇口或流道截面积较小 冷料井设置不合理
加大浇口与流道尺寸 加大冷料井
喷射流成因及改善措施 -- 注塑工艺
注射速度设置不合理
调整注射速度曲线,使熔体 流前以低速通过浇口,等到 熔体流出浇口外再提高速度
没有冷料井或冷料井设计不 含水分较多,受热后产生大量气体
增加注射速度,减小滞流时间
合理,熔体进入型腔并快速 合理设计冷料井
冷凝,使得熔体流动不畅
短射成因及改善措施 -- 注塑工艺
模具温度太低
注射压力太低 保压时间太短 熔体温度过低 注射速度太慢
调整模具温度使之处于正常 范围
适当加大注射压力 合理控制保压时间 提高熔体温度 适当提高注射速度
原料中水分或可挥发成份含 对原料进行充分干燥,或少
量过多
用含挥发成份过多的原料
加入的润滑剂太少,熔体的 流动性不好
适当增加润滑剂用量
树脂的收缩率过大
尽量选用低收缩率的树脂为 原料
翘曲(Warpage)
❖ 翘曲是指制品产生旋转或扭曲现象,导致平坦的地方有起 伏,直边朝里或朝外弯曲或扭曲,如图所示
塑料制品缺陷及改善措施
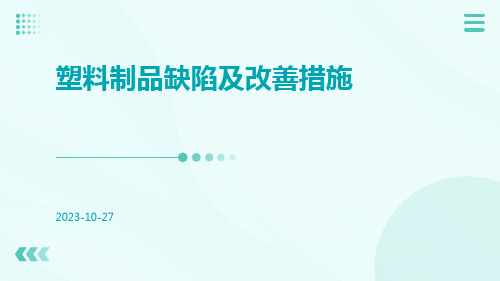
产生原因与危害
产生原因
塑料制品缺陷的产生原因很多,包括原材料质量不好、配方不合理、加工工 艺不当、设备故障、操作失误等。
危害
塑料制品缺陷会严重影响产品的质量、性能和外观,降低产品的使用价值和 寿命,甚至会对人体健康和安全造成威胁。
银纹
银纹是由于塑料在填充过程中混入的空气没有及 时排出而形成的,类似于气泡的一种缺陷。
银纹的产生可能是由于注射压力不足、注射速度 过快、模具温度不当等原因造成的。
银纹通常在塑料制品的表面或内部出现,形状为 细小的条状或网状。
改善措施:可以通过调整注射压力、注射速度和 模具温度来减少银纹的产生。在生产过程中,也 可以通过使用真空装置来帮助排出空气,从而避 免银纹的产生
VS
提高模具制造精度
采用高精度的数控机床等加工设备,提高 模具的制造精度,以减少制品缺陷。
调整生产工艺
优化注塑工艺
根据不同的塑料材料和制品要求,调整注 塑温度、压力和时间等工艺参数,以获得 理想的制品质量。
研究生产工艺优化方案
通过对生产工艺的研究和试验,找出最佳 的生产工艺参数,提高制品的质量和稳定 性。
裂纹
裂纹是由于塑料制品在冷却过程中产生的内应力 超过了塑料的抗拉强度而形成的。
裂纹的产生可能是由于注射速度过快、模具温度 过低、塑料的流动性差等原因造成的。
裂纹通常出现在塑料制品的表面或内部,形状为 线形或网状。
改善措施:可以通过降低注射速度、提高模具温 度、改善塑料的流动性来减少裂纹的产生。另外 ,可以通过调整塑料的配方,加入增韧剂等改性 剂来提高塑料的抗拉强度,从而减少裂纹的产生
常见的塑料制品缺陷有哪些

书山有路勤为径;学海无涯苦作舟
常见的塑料制品缺陷有哪些
常见的塑料制品缺陷有哪些?
答:常见塑料制品缺陷见下:
塑料制品不足:主要由于供料不足、融料填充流动不良,充气过
多及排气不良等原因导致填充型腔不满,塑料制品外形残缺不完整或多型腔时个别型腔填充不满。
尺寸不稳定:主要由于模具强度不良,精度不良、注射机工作不
稳定及成形条件不稳定等原因,使塑料制品尺寸变化不稳定。
气泡:由于融料内充气过多或排气不良而导致塑料制品内残留气体,并呈体积较小或成串的空穴(注意应与真空泡区别)。
塌坑(凹痕)或真空泡:由于保压补缩不良,塑料制品冷却不匀,
壁厚不匀及塑料收缩率大。
飞边过大:由于合模不良,间隙过大,塑料流动性太好,加料过
多使塑料制品沿边缘出现多余薄翅。
熔接不良:由于融料分流汇合时料温下降,树脂与附合物不相溶
等原因,使融料分流汇合时,熔接不良,沿塑料制品表面或内部产生明显的细接缝线。
表面波纹:由于融料沿模具表面不是平滑流动填充型腔,而是成
半固化波动状态沿型腔表面流动或融料有滞流现象。
银丝斑纹:由于料内水分或充气,及挥发物过多,融料受剪切作
用过大,融料与模具表面密合不良,或急速冷却或混人异料或分解变质,而使塑料制品表面沿料流方向出现银白色光泽的针状条纹或云母片妆斑纹(水迹痕)。
专注下一代成长,为了孩子。
- 1、下载文档前请自行甄别文档内容的完整性,平台不提供额外的编辑、内容补充、找答案等附加服务。
- 2、"仅部分预览"的文档,不可在线预览部分如存在完整性等问题,可反馈申请退款(可完整预览的文档不适用该条件!)。
- 3、如文档侵犯您的权益,请联系客服反馈,我们会尽快为您处理(人工客服工作时间:9:00-18:30)。
常用塑料名称及英文代号
随着塑料应用范围的不断扩大,工程塑料和通用塑料之间的界线越来越难分。
例如:聚氯乙烯(PVC)作为耐腐蚀材料已大量用于化工机械中,按用途分它又属于工程塑料。
1)脱模斜度:一般情况下脱模斜度取0.5º,最小为15´--20´。
各种塑料的脱模斜度
模斜度时应注意如下原则:
1)在满足制件尺寸公差要求的前提下,脱模斜度可取得大一些,这样有利于脱模。
2)在塑料收缩率大的情况下应选用较大的脱模斜度。
热塑性塑料的收缩率一般较热固性大,故脱模斜度也相应大一些。
3)当制品辟厚较厚时,因成型时制品的收缩量大,故也应选用较大的脱模斜度。
4)对于较高、较大的制品,应选用较小的脱模斜度。
5)对于高精度的制品,应选用较小的脱模斜度。
6)只是在制品高度很小时才允许不设计脱模斜度。
7)如果要求脱模后制件保持在型芯一边,可有意将制件内表面的脱模斜度设计得比外表面的小。
8)取斜度的方向一般内孔以小端为基准,斜端由扩大方向取得,外形以大端为基准,斜度由缩小方向取得。
欢迎您的下载,
资料仅供参考!
致力为企业和个人提供合同协议,策划案计划书,学习资料等等
打造全网一站式需求。