催化裂解原理与机理
催化裂化技术

催化裂化原料 催化裂化原料分为馏分油和渣油两大类。
1、Distillate Oil(馏分油)
(1)直馏重馏分油(350~500℃)
大多数直馏重馏分含芳烃较少,容易裂化,轻油收率较高, 是理想的催化裂化原料。
(2)热加工产物:焦化蜡油、减粘裂化馏出油等。
其中烯烃、芳烃含量较多,转化率低、生焦率高。不单独
• 5.正碳离子将H+ 还给催化剂,本身变成烯烃,反应中止。
催化裂化催化剂
一、催化裂化剂的种类、组成和结构
工业上使用的裂化催化剂归纳起来有三大类:
1、天然白土催化剂
催化裂化装置最初使用的经处理的天然白土,其主要活性 组分是硅酸铝。
2、无定型硅酸铝催化剂
天然白土被人工合成硅酸铝所取代。
• 无定型硅酸铝催化剂 • 硅酸铝的主要成分是氧化硅和氧化铝,合成硅酸铝依铝含量的不同又分 为低铝(含Al2O310%~13%)和高铝(含Al2O3约25%)二种。其催化剂 按颗粒大小又分为小球状(直径在3~6mm)和微球状(直径在40~80)。 • Al2O3、SiO2及少量水分是必要的活性组分,而其它组分是在催化剂的制 备过程中残留下来的极少量的杂质。合成硅酸铝是由Na2SiO3和Al2(SO4)3 溶液按一定的比例配合而成凝胶,再经水洗、过滤、成型、干燥、活化 而制成的。硅酸铝催化剂的表面具有酸性,并形成许多酸性中心,催化 剂的活性就来源于这些酸性中心,即催化剂的活性中心。
在全世界催化裂化装置的总加工能力中,提升管催化
裂化已占绝大多数。
流程图画面
催化裂化化学反应原理
• 一、单体烃催化裂化的化学反应 • (一)烷烃 • 烷烃主要发生分解反应,分解成较小分子的烷烃和烯烃, 烷烃分解时多从中间的C—C键处断裂,分子越大越容易 断裂
加氢裂化催化剂反应机理

加氢裂化过程是在较高压力下,烃类分子与氢气在催化剂表面进行裂解和加氢反应生成较小分子的转化过程,同时也发生加氢脱硫、脱氮和不饱和烃的加氢反应。
其化学反应包括饱和、还原、裂化和异构化。
加氢裂化的反应机理是正碳离子机理,遵循β-断裂法则。
在双功能催化剂上,正碳离子的生成主要是通过不饱和烃在催化剂的酸性位获取质子而生成正碳离子;烷烃失去负离子生成正碳离子,当烷烃与正碳离子反应时,发生负氢离子转移,生成新的正碳离子。
此外,加氢裂化催化剂上的反应主要包括活性金属和酸性载体上的化学反应。
具体来说,活性金属表面上的硫化物和氮化物的氢解、芳烃加氢饱和、烯烃加氢饱和,以及在酸性载体上的环状化合物的开环、裂化、脱烷基、异构化反应。
至于具体的反应细节和步骤,建议查阅化学专业书籍或咨询化学专家,以获取更深入的了解。
同时,也应注意,在进行加氢裂化反应时,应严格遵守相关安全规定,确保人员安全和设备稳定。
催化裂解原理与机理

催化裂解催化裂解,是在催化剂存在的条件下,对石油烃类进行高温裂解来生产乙烯、丙烯、丁烯等低碳烯烃,并同时兼产轻质芳烃的过程。
由于催化剂的存在,催化裂解可以降低反应温度,增加低碳烯烃产率和轻质芳香烃产率,提高裂解产品分布的灵活性。
一、催化裂解的一般特点1、催化裂解是碳正离子反应机理和自由基反应机理共同作用的结果,其裂解气体产物中乙烯所占的比例要大于催化裂化气体产物中乙烯的比例。
2 、在一定程度上,催化裂解可以看作是高深度的催化裂化,其气体产率远大于催化裂化,液体产物中芳烃含量很高。
3 、催化裂解的反应温度很高,分子量较大的气体产物会发生二次裂解反应,另外,低碳烯烃会发生氢转移反应生成烷烃,也会发生聚合反应或者芳构化反应生成汽柴油。
二、催化裂解的反应机理一般来说,催化裂解过程既发生催化裂化反应,也发生热裂化反应,是碳正离子和自由基两种反应机理共同作用的结果,但是具体的裂解反应机理随催化剂的不同和裂解工艺的不同而有所差别。
在Ca-Al系列催化剂上的高温裂解过程中,自由基反应机理占主导地位;在酸性沸石分子筛裂解催化剂上的低温裂解过程中,碳正离子反应机理占主导地位;而在具有双酸性中心的沸石催化剂上的中温裂解过程中,碳正离子机理和自由基机理均发挥着重要的作用。
三、催化裂解的影响因素同催化裂化类似,影响催化裂解的因素也主要包括以下四个方面:原料组成、催化剂性质、操作条件和反应装置。
3.1 原料油性质的影响一般来说,原料油的H/C比和特性因数K越大,催化裂解法处理焦油方案[1]饱和分含量越高,BMCI值越低,则裂化得到的低碳烯烃(乙烯、丙烯、丁烯等)产率越高;原料的残炭值越大,硫、氮以及重金属含量越高,则低碳烯烃产率越低。
各族烃类作裂解原料时,低碳烯烃产率的大小次序一般是:烷烃>环烷烃>异构烷烃>芳香烃。
3.2催化剂的性质催化裂解催化剂分为金属氧化物型裂解催化剂和沸石分子筛型裂解催化剂两种。
催化剂是影响催化裂解工艺中产品分布的重要因素。
催化裂化机理及特点

催化裂化机理及特点催化裂化是一种通过加热和催化剂的作用将长链烃分子裂解为短链烃分子的重要工艺。
催化裂化机理及特点主要包括以下几个方面:一、催化裂化机理1.构造反应:长链烃分子在裂化过程中首先发生构造反应,通过裂解碳-碳键,形成相对较短的碳链碳烃和烯烃。
2.重排反应:长链烃分子中的骨架碳骨架会经历一系列重排反应,使得产物中更多的是相对稳定的异构体和环状化合物。
3.脱氢反应:重排反应过程中,长链分子中的烃基可能失去氢原子,从而形成烯烃,增加了催化裂化的产物中烯烃的含量。
4.脱氢裂解反应:在高温高压下,部分碳链碳烃可以发生脱氢裂解反应,形成更短的链长烃烃烃烃、烯烃和芳香烃。
二、催化裂化特点1.催化裂化具有高选择性:在催化剂的影响下,催化裂化反应主要发生在长链烃分子中的弱键和缺陷位置,使得产物中的碳链长度相对较短,同时产生更多的异构体和环状化合物。
2.催化裂化反应速度快:催化剂的存在提高了反应活性,使得裂化反应可以在相对低的温度和压力下进行,加快了反应速度。
3.催化裂化可以产生高附加值的产品:催化裂化使得重质燃料油转化为轻质烃类产品,其中包括汽油、炼厂气、润滑油基础油等,这些产品有较高的附加值。
4.催化裂化可以降低能源消耗:通过催化裂化将重质原油转化为较轻质产品,如汽油和炼厂气,不仅提供了更多的高附加值产品,还减少了对原油的需求,降低了能源消耗。
5.催化裂化可以调节产品分布:通过不同的催化剂组合和反应条件,可以调节催化裂化产物的碳链长度分布,以满足市场需求,提高产品经济效益。
总之,催化裂化是一种高效、高选择性的炼油工艺,通过加热和催化剂的作用,将长链烃分子裂解为短链烃分子,产生高附加值产品,并降低能源消耗。
催化裂化机理和特点的深入研究对于提高炼油工艺的效率和降低能源消耗具有重要意义。
催化裂化讲义

第一节 催化裂化化学反应原理
▪ 一、单体烃催化裂化的化学反应 ▪ (一)烷烃
▪ 烷烃主要发生分解反应,分解成较小分子的烷烃和烯烃, 烷烃分解时多从中间的C—C键处断裂,分子越大越容易 断裂
▪ (二)烯烃
▪ 烯烃的主要反应也是分解反应,但还有一些其它重要反应, 主要反应有:
(二)三阀
▪ 1.单动滑阀
单动滑阀用于床层反应器催化裂化和高低并列式提升管催化裂化装置。 其作用是:正常操作时用来调节催化剂在两器间的循环量,出现重大事 故时用以切断再生器与反应沉降器之间的联系,以防造成更大事故。
▪ 2.双动滑阀
双动滑阀是一种两块阀板双向动作的超灵敏调节阀,安装 在再生器出口管线上(烟囱),其作用是调节再生器的压 力,使之与反应沉降器保持一定的压差。
径或筛分组成。工业用微球催化剂颗粒直径一般在20~80之间。 ▪ 我国用磨损指数来评价微球催化剂的机械强度 ▪ (六)密度 ▪ 1.真实密度:颗粒的质量与骨架实体所占体积之比 ▪ 2.颗粒密度:把微孔体积计算在内的单个颗粒的密度 ▪ 3.堆积密度 :催化剂堆积时包括微孔体积和颗粒间的孔隙体积的密
度
三、裂化催化剂的失活与再生
▪ 综合上述两个排列顺序可知,芳烃虽然吸附能力强,但反应能力弱,使 整个石油馏分的反应速度变慢 ;对于烷烃,虽然反应速度快,但吸附 能力弱,从而对原料反应的总效应不利。富含环烷烃的石油馏分应是催 化裂化的理想原料
(二)石油馏分的催化裂化反应是复杂的平 行—顺序反应
▪ 石油馏分进行催化裂化反应时,原料向几个方向进行反应, 中间产物又可继续反应,从反应工程观点来看,这种反应 属于平行—顺序反应。原料油可直接裂化为汽油或气体, 属于一次反应,汽油又可进一步裂化生成气体,这就是二 次反应。平行—顺序反应的一个重要特点是反应深度对产 品产率分布有重大影响。
裂解的名词解释

裂解的名词解释裂解是一个常常出现在工业和化学领域中的术语。
它指的是将复杂的分子聚合物或化合物,在高温和压力的条件下,分解成较小的分子。
通过裂解,原本难以回收利用的废弃物或低价值产物可以转化为有用的化学品或燃料,从而实现资源的高效利用。
裂解技术在各个领域都有广泛的应用,本文将对几种常见的裂解方法进行解释。
1. 热裂解热裂解是利用高温环境下的热能将分子聚合物或化合物分解为较小的分子的过程。
常见的热裂解方法包括焦炉裂解和石油裂解。
焦炉裂解是将煤焦、焦油等碳质材料加热分解,生成一系列有机化合物。
石油裂解是将原油在高温下裂解成轻质燃料,如汽油和液化气。
热裂解技术的应用广泛,可以为能源行业提供重要的资源转化途径。
2. 催化裂解催化裂解是在某种催化剂存在的条件下进行的一种裂解方法。
催化剂可以加速分子的分解和转化过程,提高裂解效率和产物的选择性。
其中,流化催化裂解是一种常见的技术,它通过气体中的载体将催化剂悬浮在高温环境中,使其与原料反应。
这种技术可以有效地裂解各种复杂的有机物,产生高附加值的化学品。
3. 生物裂解生物裂解是一种利用微生物或酶类催化剂进行的裂解过程。
在这种方法中,微生物或酶类催化剂可以选择性地降解特定的有机物。
例如,生物质裂解可以将废弃的农作物、木材等转化为生物燃料或化学品。
生物裂解具有环境友好、能源高效和资源可再生等优点,是未来发展的热门领域之一。
4. 水裂解水裂解是指将水分子分解成氢气和氧气的过程。
这是一种非常重要的裂解方法,因为氢气是一种清洁的燃料,可以用于氢能源的生产和利用。
水裂解技术可以通过电解、光解等方式实现,虽然目前的水裂解技术仍面临一些挑战,但其在可持续能源领域的前景广阔。
总结裂解是一种将复杂的分子聚合物或化合物分解成较小的分子的过程。
它可以通过热裂解、催化裂解、生物裂解和水裂解等方法实现。
这些裂解技术在能源和化学行业中具有广泛的应用前景,可以促进资源的高效利用和环境的可持续发展。
催化裂解和催化裂化的不同点

之阳早格格创做催化裂解是正在催化剂存留的条件下,对付石油烃类举止下温裂解去死产乙烯、丙烯、丁烯等矮碳烯烃,并共时兼产沉量芳烃的历程.由于催化剂的存留,催化裂解不妨落矮反应温度,减少矮碳烯烃产率战沉量芳香烃产率,普及裂解产品分散的机动性.(1) 催化裂解的普遍个性①催化裂解是碳正离子反应机理战自由基反应机理共共效率的截止,其裂解气体产品中乙烯所占的比率要大于催化裂化气体产品中乙烯的比率.②正在一定程度上,催化裂解不妨瞅做是下妙度的催化裂化,其气体产率近大于催化裂化,液体产品中芳烃含量很下.③催化裂解的反应温度很下,分子量较大的气体产品会爆收二次裂解反应,其余,矮碳烯烃会爆收氢变化反应死成烷烃,也会爆收散合反应大概者芳构化反应死成汽柴油.(2) 催化裂解的反应机理普遍去道,催化裂解历程既爆收催化裂化反应,也爆收热裂化反应,是碳正离子战自由基二种反应机理共共效率的截止,然而是简曲的裂解反应机理随催化剂的分歧战裂解工艺的分歧而有所没有共.正在Ca-Al系列催化剂上的下温裂解历程中,自由基反应机理占主宰职位;正在酸性沸石分子筛裂解催化剂上的矮温裂解历程中,碳正离子反应机理占主宰职位;而正在具备单酸性核心的沸石催化剂上的中温裂解历程中,碳正离子机理战自由基机理均收挥着要害的效率.(3) 催化裂解的效率果素共催化裂化类似,效率催化裂解的果素也主要包罗以下四个圆里:本料组成、催化剂本量、支配条件战反应拆置.①本料油本量的效率.普遍去道,本料油的H/C比战个性果数K越大,鼓战分含量越下,BMCI值越矮,则裂化得到的矮碳烯烃(乙烯、丙烯、丁烯等)产率越下;本料的残冰值越大,硫、氮以及沉金属含量越下,则矮碳烯烃产率越矮.各族烃类做裂解本料时,矮碳烯烃产率的大小序次普遍是:烷烃>环烷烃>同构烷烃>芳香烃.②催化剂的本量.催化裂解催化剂分为金属氧化物型裂解催化剂战沸石分子筛型裂解催化剂二种.催化剂是效率催化裂解工艺中产品分散的要害果素.裂解催化剂应具备下的活性战采用性,既要包管裂解历程中死成较多的矮碳烯烃,又要使氢气战甲烷以及液体产品的支率尽大概矮,共时还应具备下的宁静性战板滞强度.对付于沸石分子筛型裂解催化剂,分子筛的孔结构、酸性及晶粒大小是效率催化效率的三个最要害果素;而对付于金属氧化物型裂解催化剂,催化剂的活性组分、载体战帮剂是效率催化效率的最要害果素.③支配条件的效率.支配条件对付催化裂解的效率与其对付催化裂化的效率类似.本料的雾化效验战睦化效验越佳,本料油的变化率越下,矮碳烯烃产率也越下;反应温度越下,剂油比越大,则本料油变化率战矮碳烯烃产率越下,然而是焦冰的产率也变大;由于催化裂解的反应温度较下,为预防过分的二次反应,果此油气停顿时间没有宜过少;而反应压力的效率相对付较小.从表里上分解,催化裂解应尽管采与下温、短停顿时间、大蒸汽量战大剂油比的支配办法,才搞达到最大的矮碳烯烃产率.④反应器是催化裂解产品分散的要害效率果素.反应器型式主要有牢固床、移动床、流化床、提下管战下止输支床反应器等.针对付CPP工艺,采与杂提下管反应器有好处多产乙烯,采与提下管加流化床反应器有好处多产丙烯.(4) 催化裂解工艺介绍烃类催化裂解的钻研已有半个世纪的履历了,其钻研范畴包罗沉烃、馏分油战沉油,并启垦出了多种裂解工艺,底下对付其举止简要的介绍.①催化裂解工艺(DCC工艺).该工艺是由华夏石化石油化工科教钻研院启垦的,以沉量油为本料,使用固体酸择形分子筛催化剂,正在较慢战的反应条件下举止裂解反应,死产矮碳烯烃大概同构烯烃战下辛烷值汽油的工艺技能.该工艺借镜流化催化裂化技能,采与催化剂的流化、连绝反应战复活技能,已经真止了工业化.DCC工艺具备二种支配办法——DCC-Ⅰ战DCC-Ⅱ.DCC-Ⅰ采用较为苛刻的支配条件,正在提下管加稀相流化床反应器内举止反应,最洪量死产以丙烯为主的气体烯烃;DCC-Ⅱ采用较慢战的支配条件,正在提下管反应器内举止反应,最洪量天死产丙烯、同丁烯战同戊烯等小分子烯烃,并共时兼产下辛烷值劣量汽油.②催化热裂解工艺(CPP工艺).该工艺是华夏石化石油化工科教钻研院启垦的造与乙烯战丙烯的博利技能,正在保守的催化裂化技能的前提上,以蜡油、蜡油掺渣油大概常压渣油等沉油为本料,采与提下管反应器战博门研造的催化剂以及催化剂流化输支的连绝反应-复活循环支配办法,正在比蒸汽裂解慢战的支配条件下死产乙烯战丙烯.CPP工艺是正在催化裂解DCC工艺的前提上启垦的,其闭键技能是通过对付工艺战催化剂的进一步矫正,使其手段产品由丙烯变化成乙烯战丙烯.③沉油曲交裂解造乙烯工艺(HCC工艺).该工艺是由洛阳石化工程公司炼造钻研所启垦的,以沉油曲交裂解造乙烯并兼产丙烯、丁烯战沉芳烃的催化裂解工艺.它借镜老练的沉油催化裂化工艺,采与流态化“反应-复活”技能,利用提下管反应器大概下止式反应器去真止下温短交触的工艺央供.④其余催化裂解工艺.如催化-蒸汽热裂解工艺(反应温度普遍皆很下,正在800℃安排)、THR工艺(日本东洋工程公司启垦的沉量油催化变化战催化裂解工艺)、赶快裂解技能(Stone & Webster公司战Chevron公司共同启垦的一套催化裂解造烯烃工艺)等.⑤石蜡基础料的裂解效验劣于环烷基础料.果此,绝大普遍催化裂解工艺皆采与石蜡基的馏分油大概者沉油动做裂解本料.对付于环烷基的本料,特天针对付加拿大油砂沥青得到的馏分油战加氢馏分油,沉量油国家沉面真验室的申宝剑熏陶启垦了博门的裂解催化剂,收端评介截止标明,乙烯战丙烯总产率交近30 wt%.(5) 催化裂化与催化裂解的辨别从一定程度上,催化裂解是从催化裂化的前提上死少起去的,然而是二者又有着明隐的辨别,如下:①手段分歧.催化裂化以死产汽油、煤油战柴油等沉量油品为手段,而催化裂解旨正在死产乙烯、丙烯、丁烯、丁二烯等基础化工本料.②本料分歧.催化裂化的本料普遍是减压馏分油、焦化蜡油、常压渣油、以及减压馏分油掺减压渣油;而催化裂解的本料范畴比较宽,不妨是催化裂化的本料,还不妨是石脑油、柴油以及C4、C5沉烃等.③催化剂分歧.催化裂化的催化剂普遍是沸石分子筛催化剂战硅酸铝催化剂,而催化裂解的催化剂普遍是沸石分子筛催化剂战金属氧化物催化剂.④支配条件分歧.与催化裂化相比,催化裂解的反应温度较下、剂油比较大、蒸汽用量较多、油气停顿时间较短、二次反应较为宽沉.⑤反应机理分歧.催化裂化的反应机理普遍认为是碳正离子机理,而催化裂解的反应机理即包罗碳正离子机理,又波及自由基机理.。
催化裂解原理与机理

催化裂解原理与机理催化裂解是一种将高分子化合物分解为低分子化合物的过程,是石油化工行业中非常重要的生产方法之一、它通过引入催化剂来降低化学反应的能量障碍,提高反应速率和收率。
催化裂解原理和机理的研究对于改进催化裂解工艺的效率和选择合适的催化剂具有重要意义。
催化裂解的原理是在一定条件下,通过引入适当的催化剂来降低原料的裂解温度和能量障碍。
通常,催化剂是由一种或多种金属和非金属元素组成的复杂化合物。
催化剂通过吸附和解离反应物分子,改变反应物的电子状态,从而降低反应过程中的能量消耗。
此外,催化剂还可以调整反应物分子的排列和碰撞方式,以促进反应的进行。
催化裂解是一个复杂的过程,涉及到多个反应步骤和中间产物。
通常,催化裂解的反应机理包括吸附、解离、轮转、互换和重新组合等过程。
首先,原料中的高分子化合物被吸附在催化剂表面。
吸附是指反应物分子与催化剂表面相互作用,形成物理吸附或化学吸附。
吸附可以增加反应物分子的接触面积,促进反应的进行。
然后,吸附的分子会发生解离反应,使分子内键裂解。
这个反应步骤可以通过催化剂提供的活化能量来实现。
解离反应将高分子化合物分解为低分子化合物和反应性中间体。
接下来,反应物分子在催化剂表面进行轮转运动。
轮转是指反应物分子在催化剂表面的扭曲和旋转。
这个步骤有助于碰撞和中间产物的重新排列。
然后,反应物分子发生互换反应,以实现分子结构的重组。
互换反应是指反应物分子之间的局部原子或原子团的交换。
通过互换反应,分子结构得到重新组合和重构,产生更小的分子。
最后,经过多轮的解离、轮转和互换反应,原料中的高分子化合物完全被裂解为低分子烃化合物。
这些低分子烃化合物可以通过进一步的分离和精制过程,得到所需的产品。
总的来说,催化裂解通过引入适当的催化剂,降低了化学反应的能量障碍,提高了反应速率和收率。
催化裂解的原理和机理涉及多个反应步骤和中间产物的生成和转化。
对催化裂解的原理和机理的深入研究有助于提高催化裂解工艺的效率和选择合适的催化剂。
催化裂解原理与机理
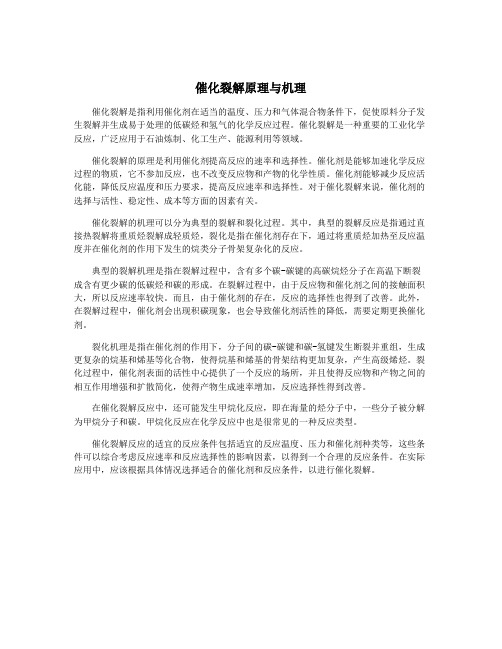
催化裂解原理与机理催化裂解是指利用催化剂在适当的温度、压力和气体混合物条件下,促使原料分子发生裂解并生成易于处理的低碳烃和氢气的化学反应过程。
催化裂解是一种重要的工业化学反应,广泛应用于石油炼制、化工生产、能源利用等领域。
催化裂解的原理是利用催化剂提高反应的速率和选择性。
催化剂是能够加速化学反应过程的物质,它不参加反应,也不改变反应物和产物的化学性质。
催化剂能够减少反应活化能,降低反应温度和压力要求,提高反应速率和选择性。
对于催化裂解来说,催化剂的选择与活性、稳定性、成本等方面的因素有关。
催化裂解的机理可以分为典型的裂解和裂化过程。
其中,典型的裂解反应是指通过直接热裂解将重质烃裂解成轻质烃,裂化是指在催化剂存在下,通过将重质烃加热至反应温度并在催化剂的作用下发生的烷类分子骨架复杂化的反应。
典型的裂解机理是指在裂解过程中,含有多个碳-碳键的高碳烷烃分子在高温下断裂成含有更少碳的低碳烃和碳的形成。
在裂解过程中,由于反应物和催化剂之间的接触面积大,所以反应速率较快。
而且,由于催化剂的存在,反应的选择性也得到了改善。
此外,在裂解过程中,催化剂会出现积碳现象,也会导致催化剂活性的降低,需要定期更换催化剂。
裂化机理是指在催化剂的作用下,分子间的碳-碳键和碳-氢键发生断裂并重组,生成更复杂的烷基和烯基等化合物,使得烷基和烯基的骨架结构更加复杂,产生高级烯烃。
裂化过程中,催化剂表面的活性中心提供了一个反应的场所,并且使得反应物和产物之间的相互作用增强和扩散简化,使得产物生成速率增加,反应选择性得到改善。
在催化裂解反应中,还可能发生甲烷化反应,即在海量的烃分子中,一些分子被分解为甲烷分子和碳。
甲烷化反应在化学反应中也是很常见的一种反应类型。
催化裂解反应的适宜的反应条件包括适宜的反应温度、压力和催化剂种类等,这些条件可以综合考虑反应速率和反应选择性的影响因素,以得到一个合理的反应条件。
在实际应用中,应该根据具体情况选择适合的催化剂和反应条件,以进行催化裂解。
生物油催化裂解精制机理

Fi 1 Fo c a t f a a y i r c n e c in g. lw h r o t lt c a ki r a t c c g o e up n q i me t
研 究 生物 油 催 化 裂解 精 制 的机 理 [9, 都 不 能 6]但 -
作者简 介 :许 庆利( 9 5 , , 17 一)男 河南安 阳人 , 东理工大学副教授 , 华 博士.
1 6
沈阳 大学 学报 ( 自然科 学版 ) 集 在 液 体 收 集 瓶 中,并 采 用 ( ekn l rC au O ) 析. P r iE me lr s O 分 5
第2 4卷 G / C MS
的机 理 .
迅 速 的发展 . 粗生 物油 的高含水 量 ( 但 质量 分数 为
1 ~ 3 ) 高 含 氧 量 ( 量 分 数 为 4 ~ 5 0 、 质 O
5 )高黏 度 、 热 值 ( 生 物 油 热 值 约 1 ~ 2 O 、 低 粗 6 0
MJ k , 发动机 燃 料一般 4 / g , /g而 2 MJ k ) 酸性 较强
用 一种 简单 的方式对 生 物油催 化 裂解 过程 进行 描
述.
1 原料 ; 一微量计量泵 ;3 固定床反应器 ; 2 一 4 一热电偶 ; 一冷凝器 ; 一 氮气钢瓶 ; 5 6 7 流量计 ; 一液体 收集瓶. 一 8
收 稿 日期 :2 1 — 1 一O 01 2 9 基 金 项 目 :93国家 重 点基 础 研 究 发 展 计 划 项 目 (0 7 B 12 6 ; 国家 自然 科 学 基 金 资 助 项 目 (1 0 0 8. 7 2 0C 2 0 0 ) 2062)
催化裂化与催化裂解(李春义)
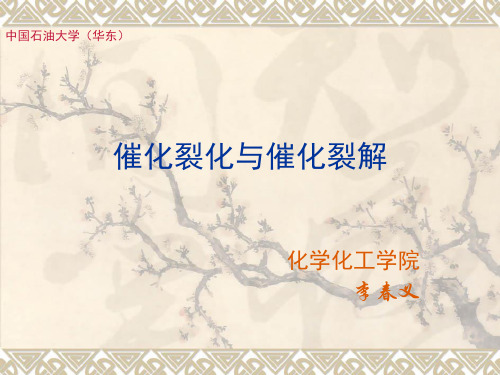
1.前言--流化催化裂化(FCC)发展概况
FCC的优点
烟气 再生器 再生剂 料斗 待生剂 料斗 分馏塔 汽油 加热油 重瓦斯油 原料 油气 塔底油 鼓风机
可以用小颗粒催化剂,消除了 内扩散的影响; 固体催化剂循环速率可以在较 宽的范围内调节,操作灵活; 流体与固体可以迅速混合,并 且固体的快速运动极大地改善 了传热效果。
1.前言--发展方向
加工重质原料。直接加工AR、脱沥青油甚至VR,经济效益显著。焦炭产率高、重 金属污染严重等是亟待解决的问题。
降低能耗。催化裂化装置的能耗较大,降低能耗的潜力也较大。降低能耗的主要 方向是降低焦炭产率、充分利用再生烟气中CO的燃烧热以及发展再生烟气热能利 用技术等。
减少污染物排放。催化裂化装置的主要污染物排放是再生烟气中的粉尘、CO、 SOX和NOX。随着环境保护立法日趋严格,减少污染的问题也日益显得重要。 适应多种生产需要的催化剂和工艺。例如,结合我国国情多产柴油,又如多产丙 烯、丁烯,甚至是多产乙烯的新催化剂和工艺技术。 过程模拟和系统集成优化。正确的设计、预测及优化控制都需要准确的催化裂化 过程数学模型。由于催化裂化过程的复杂性,仅依靠某一局部单项技术的开发和 实施是不能从根本上解决问题的,必须针对重要科学问题和关键技术问题,对催 化裂化过程进行系统集成优化,开发新型工艺技术及配套专用装备,从根本上优 化工业提升管反应系统的操作。
1.前言--原料与产品
不同原料的催化裂化产物分布
项 目 催化裂化原料:VGO、AR、 VR、CGO、溶剂脱沥青油 原料油 和加氢处理的重油。 原料、催化剂和操作条件 干 气 对催化裂化产物分布和产 品质量都有明显的影响。 液化气 以多产丙烯或多产乙烯和 汽 油 丙烯为目的的催化裂解, 产品 轻柴油 理想的原料是石蜡基的重 产率 wt% 重柴油 油或渣油。 油 浆 对劣质原料进行加氢处理, 为大势所趋。 焦 炭
催化裂解原理与机理
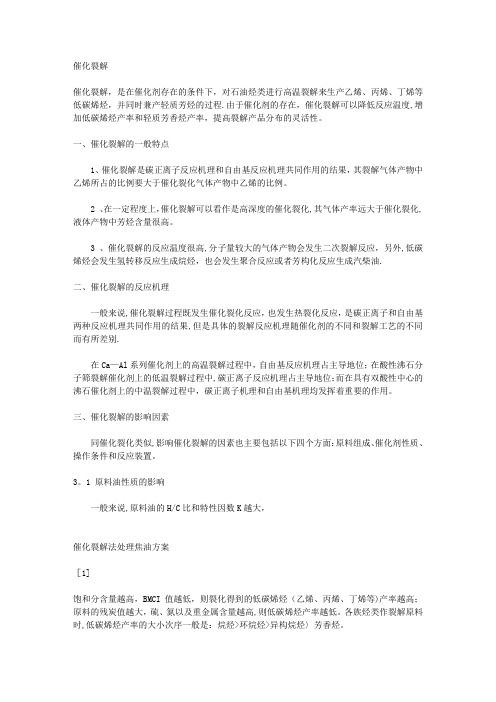
催化裂解催化裂解,是在催化剂存在的条件下,对石油烃类进行高温裂解来生产乙烯、丙烯、丁烯等低碳烯烃,并同时兼产轻质芳烃的过程.由于催化剂的存在,催化裂解可以降低反应温度,增加低碳烯烃产率和轻质芳香烃产率,提高裂解产品分布的灵活性。
一、催化裂解的一般特点1、催化裂解是碳正离子反应机理和自由基反应机理共同作用的结果,其裂解气体产物中乙烯所占的比例要大于催化裂化气体产物中乙烯的比例。
2 、在一定程度上,催化裂解可以看作是高深度的催化裂化,其气体产率远大于催化裂化,液体产物中芳烃含量很高。
3 、催化裂解的反应温度很高,分子量较大的气体产物会发生二次裂解反应,另外,低碳烯烃会发生氢转移反应生成烷烃,也会发生聚合反应或者芳构化反应生成汽柴油.二、催化裂解的反应机理一般来说,催化裂解过程既发生催化裂化反应,也发生热裂化反应,是碳正离子和自由基两种反应机理共同作用的结果,但是具体的裂解反应机理随催化剂的不同和裂解工艺的不同而有所差别.在Ca—Al系列催化剂上的高温裂解过程中,自由基反应机理占主导地位;在酸性沸石分子筛裂解催化剂上的低温裂解过程中,碳正离子反应机理占主导地位;而在具有双酸性中心的沸石催化剂上的中温裂解过程中,碳正离子机理和自由基机理均发挥着重要的作用。
三、催化裂解的影响因素同催化裂化类似,影响催化裂解的因素也主要包括以下四个方面:原料组成、催化剂性质、操作条件和反应装置。
3。
1 原料油性质的影响一般来说,原料油的H/C比和特性因数K越大,催化裂解法处理焦油方案[1]饱和分含量越高,BMCI值越低,则裂化得到的低碳烯烃(乙烯、丙烯、丁烯等)产率越高;原料的残炭值越大,硫、氮以及重金属含量越高,则低碳烯烃产率越低。
各族烃类作裂解原料时,低碳烯烃产率的大小次序一般是:烷烃>环烷烃>异构烷烃〉芳香烃。
3。
2催化剂的性质催化裂解催化剂分为金属氧化物型裂解催化剂和沸石分子筛型裂解催化剂两种。
催化剂是影响催化裂解工艺中产品分布的重要因素。
甲醇的脱水裂解反应及催化机理
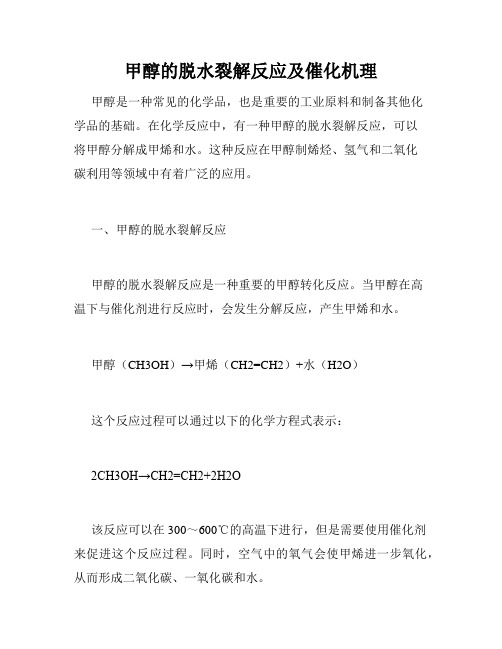
甲醇的脱水裂解反应及催化机理甲醇是一种常见的化学品,也是重要的工业原料和制备其他化学品的基础。
在化学反应中,有一种甲醇的脱水裂解反应,可以将甲醇分解成甲烯和水。
这种反应在甲醇制烯烃、氢气和二氧化碳利用等领域中有着广泛的应用。
一、甲醇的脱水裂解反应甲醇的脱水裂解反应是一种重要的甲醇转化反应。
当甲醇在高温下与催化剂进行反应时,会发生分解反应,产生甲烯和水。
甲醇(CH3OH)→甲烯(CH2=CH2)+水(H2O)这个反应过程可以通过以下的化学方程式表示:2CH3OH→CH2=CH2+2H2O该反应可以在300~600℃的高温下进行,但是需要使用催化剂来促进这个反应过程。
同时,空气中的氧气会使甲烯进一步氧化,从而形成二氧化碳、一氧化碳和水。
二、催化机理催化剂在化学反应中起着非常重要的作用。
在甲醇的脱水裂解反应中,催化剂可以降低反应的活化能,从而加速反应速率。
不同的催化剂对甲醇的脱水裂解反应的催化效果不同。
目前认为,催化剂在甲醇分解反应中的作用主要是通过裂化甲醇分子中的O-H键来实现的。
也就是说,催化剂不仅可以吸附甲醇分子,还可以在甲醇分子的O-H中间形成额外的O-H,从而降低这个键的裂解能量。
这个过程中,O-H键的裂解使甲醇分子中的H原子离子化,从而释放出甲烯。
在甲烯的生成过程中,催化剂扮演了非常重要的角色。
催化剂不仅可以吸附甲烯分子,还可以通过部分氢气化反应将其转化为不同的烯烃。
或者,催化剂还可以将甲烯分子与其他分子反应,产生不同种类的气体或液态化合物。
综上所述,催化剂在甲醇的脱水裂解反应中起着重要的作用。
只有理解催化剂的催化机理,才能够更好地优化反应条件,并探索其他不同的催化剂,从而实现更好的反应效果。
三、未来的研究方向甲醇的脱水裂解反应是一种非常重要的化学反应,对于制备燃料气体、制造氢气和化工原料等以及各种绿色化学工艺都具有广泛的应用。
然而,目前脱水裂解反应中使用的催化剂仍存在一些问题,例如需要高温、压力和能量,不符合绿色化学工艺的要求。
催化裂化工艺

nm,比表面积可达500—700m2/g。 ➢硅酸铝的催化活性来源于其表面的酸性。
第31页/共84页
分子筛催化剂特点
➢分子筛催化剂在催化裂化中的应用是催化裂化 技术的重大发展。分子筛催化剂是60年代发展 起来的一种新型的高活性催化剂。它的出现, 使流化催化裂化工艺发生了很大变化,装置处 理能力显著提高,产品产率及质量都得到改善。
显微镜下的催化裂解催化剂
第36页/共84页
分子筛催化剂的组成
➢ 活性组元分子筛:ZSM-5和Y. ZSM-5作添加剂,占 15~50%; ➢ 基质或者称之为载体:一般为高岭土或合成基质,占20~70%; ➢ 粘结剂:铝溶胶、硅溶胶或硅铝溶胶; ➢ 添加物或助剂成分:抗Ni、V、N等。
0.50 0.75
1.00
金属在催化剂上的含量,(W)%
第24页/共84页
金属污染对产氢量的影响
氢,Nm3/ m3
800-
Ni
600-
400-
200-
镍
的
脱
氢
功
能
V
高
于
钒
01000 2000 3000 4000 5000 6000
催化剂上的金属含量,ppm
第25页/共84页
金属污染对焦炭产率的影响
➢1965年五朵金花之一的流化催化裂化在抚顺石油二厂建 成投产。五朵金花:催化裂化、催化重整、延迟焦化、尿 素脱蜡、微球催化剂与添加剂。
➢1974年我国建成投产了第一套提升管催化裂化工业装置 。
➢随着催化剂和催化工艺的发展,其加工的原料逐步重质化、 劣质化。
第5页/共84页
催化裂化反应机理
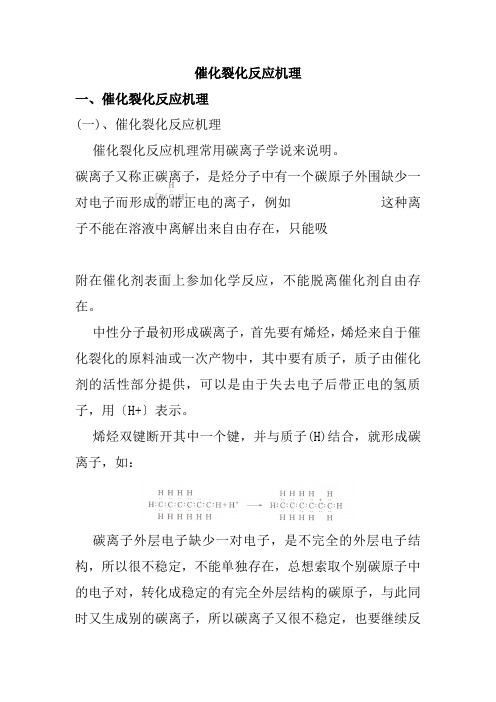
催化裂化反应机理一、催化裂化反应机理(一)、催化裂化反应机理催化裂化反应机理常用碳离子学说来说明。
碳离子又称正碳离子,是烃分子中有一个碳原子外围缺少一对电子而形成的带正电的离子,例如这种离子不能在溶液中离解出来自由存在,只能吸附在催化剂表面上参加化学反应,不能脱离催化剂自由存在。
中性分子最初形成碳离子,首先要有烯烃,烯烃来自于催化裂化的原料油或一次产物中,其中要有质子,质子由催化剂的活性部分提供,可以是由于失去电子后带正电的氢质子,用〔H+〕表示。
烯烃双键断开其中一个键,并与质子(H)结合,就形成碳离子,如:碳离子外层电子缺少一对电子,是不完全的外层电子结构,所以很不稳定,不能单独存在,总想索取个别碳原子中的电子对,转化成稳定的有完全外层结构的碳原子,与此同时又生成别的碳离子,所以碳离子又很不稳定,也要继续反应下去,实现这种转化需要活化能很低,从而加快了整个反应速度,直到碳离子放出一个质子还原成中性分子为止,才能使反应中断。
今以十六烯-6的催化裂化反应为例,说明碳离子的若干规则。
第一步:十六烯-6从催化剂表面获得质子,生成碳离子:第二步:十六烯-6遇见已经存在的碳离子,又再生成别的碳离子:别的碳离子又要索取其他稀烃的电子对,使反应链锁下去。
第三步:大分子的碳离子,还可以夺取自身分子相隔位置(β位)上的碳原子发生所谓β裂解。
第四步:各种碳离子中以伯碳离子 最不稳定,容易异构化为仲碳离子 ,甚至叔碳离子2如果这些异构碳离子中碳原子数还在五以上,则可继续进行β裂解:或者转化成叔碳离子或者转化为叔碳离子最后一步,各种反应最后都是碳离子放出一个质子,还给催化剂,使自己变成中性分子,使链锁反应中断:对于带叔碳烷基的芳香烃按上述碳离子反应规则,其裂化步骤可表如下:综上可见催化裂化反应易异构化,容易生成>C3、C4的烯烃,正是按碳离子的反应规则进行反应的结果。
碳离子反应还可说明烯烃迭合,氢转移的机理,目前凡是能够提供质子的酸性催化剂的催化作用,都用碳离子学说来说明,但是碳离子学说也不能说明相同的反应物用不同催化剂为什么会得到不同的产物,某个反应为什么只能用某一种酸或催化剂才能起催化作用等问题。
催化裂化反应机理

异丙醇脱氢制丙酮所采用的催化剂及其设计原理张若杰1201班化学工程01201208170114、反应机理脱氢反应是脱氢催化剂(Dehydrogenation catalysts下进行的气固相催化反应,且反应是吸热的。
在异丙醇分子中由于羟基的影响,a H比较活泼,容易发生脱氢。
常压200-300r,异丙醇在催化剂表面,脱氢吸热生成丙酮,并产生大量氢气。
本反应主要涉及两个过程。
温度适中时,发生主反应:CH32CHOH > CH32CO H2(1)起始时,由于异丙醇的加入,汽化需要吸收大量的热,导致反应温度降低,发生副反应:CH3 2CO CH3 2CHOH —:CH 3 2CHCH 2COCH3 H2O (2)温度过高时,发生异丙醇分子内脱水,生成异丙醚:2 CH3 CHOH —〔CH 3 2 CHOCH CH 3 2 H 2O (3)因此温度控制的是否得当是生成目的产物的关键。
二、反应热力学分析查有关手册得各相关物质的.H f和厶G f值于下表:()r r由方程ln 他=如丄—丄求出多个温度的Kp值列于下表:K p1 R T2三、分子反应机理反应物分子先被催化剂上的金属离子Mn+作用而脱去H-(发生C-H键异裂),随后再脱去H+而成不饱和键。
要求反应分子交易极化产生C s—Hl催化剂也需要有极化能力的金属离子Mn+用来脱去H-,同时具有负电荷的02-,以接受H-。
因此这类机理类似于酸碱催化。
四、催化剂的选择在反应过程中,反应温度随催化剂的不同而不同。
异丙醇脱氢反应是一简单反应,工业上大多采用气相反应,原料在气相条件下流过列管式固定床反应器,发生脱氢反应,常用铜锌系催化剂。
典型的工艺条件为反应压力0.2〜0.3 MPa,反应温度200〜300E,异丙醇单程转化率(摩尔分数)大于60%,产品丙酮对异丙醇总收率(摩尔分数)大于95.5%。
所用催化剂有铜、银、铂、钯等金属以及过渡金属的硫化物,负载于惰性载体上,反应在管式反应器中进行,温度400〜600r。
裂解与催化
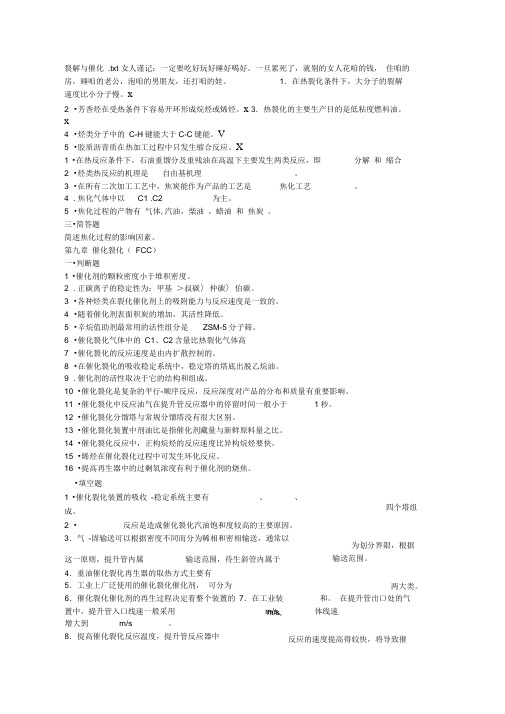
裂解与催化.txt 女人谨记:一定要吃好玩好睡好喝好。
一旦累死了,就别的女人花咱的钱,住咱的房,睡咱的老公,泡咱的男朋友,还打咱的娃。
1.在热裂化条件下,大分子的裂解速度比小分子慢。
x2 •芳香烃在受热条件下容易开环形成烷烃或烯烃。
x 3.热裂化的主要生产目的是低粘度燃料油。
x4 •烃类分子中的C-H键能大于C-C键能。
V5 •胶质沥青质在热加工过程中只发生缩合反应。
X1 •在热反应条件下,石油重馏分及重残油在高温下主要发生两类反应,即分解和缩合2 •烃类热反应的机理是自由基机理。
3 •在所有二次加工工艺中,焦炭能作为产品的工艺是焦化工艺。
4 .焦化气体中以C1 .C2 为主。
5 •焦化过程的产物有气体,汽油,柴油,蜡油和焦炭。
三•简答题简述焦化过程的影响因素。
第九章催化裂化(FCC)一•判断题1 •催化剂的颗粒密度小于堆积密度。
2 .正碳离子的稳定性为:甲基>叔碳〉仲碳〉伯碳。
3 •各种烃类在裂化催化剂上的吸附能力与反应速度是一致的。
4 •随着催化剂表面积炭的增加,其活性降低。
5 •辛烷值助剂最常用的活性组分是ZSM-5分子筛。
6 •催化裂化气体中的C1、C2含量比热裂化气体高7 •催化裂化的反应速度是由内扩散控制的。
8 •在催化裂化的吸收稳定系统中,稳定塔的塔底出脱乙烷油。
9 .催化剂的活性取决于它的结构和组成。
10 •催化裂化是复杂的平行-顺序反应,反应深度对产品的分布和质量有重要影响。
11 •催化裂化中反应油气在提升管反应器中的停留时间一般小于1秒。
12 •催化裂化分馏塔与常规分馏塔没有很大区别。
13 •催化裂化装置中剂油比是指催化剂藏量与新鲜原料量之比。
14 •催化裂化反应中,正构烷烃的反应速度比异构烷烃要快。
15 •烯烃在催化裂化过程中可发生环化反应。
16 •提高再生器中的过剩氧浓度有利于催化剂的烧焦。
•填空题1 •催化裂化装置的吸收-稳定系统主要有、、成。
2 •反应是造成催化裂化汽油饱和度较高的主要原因。
- 1、下载文档前请自行甄别文档内容的完整性,平台不提供额外的编辑、内容补充、找答案等附加服务。
- 2、"仅部分预览"的文档,不可在线预览部分如存在完整性等问题,可反馈申请退款(可完整预览的文档不适用该条件!)。
- 3、如文档侵犯您的权益,请联系客服反馈,我们会尽快为您处理(人工客服工作时间:9:00-18:30)。
5.2.2再生部分
再生器阶段,催化剂因在反应过程中表面会附着油焦而活性降低,所以必须进行再生处理,首先主风机将压缩空气送入辅助燃烧室进行高温加热,经辅助烟道通过主风分布管进入再生器烧焦罐底部,从反应器过来的催化剂在高温大流量主风的作用下被加热上升,同时通过器壁分布的燃油喷嘴喷入燃油调节反应温度,这样催化剂表面附着的油焦在高温下燃烧分解为烟气,烟气和催化剂的混合物继续上升进入再生器继续反应,油焦未能充分反应的催化剂经循环斜管会重新进入烧焦罐再次处理。最后烟气及处理后的催化剂进入再生器顶部的旋风分离器进行气固分离,烟气进入集气室汇合后排入烟道,催化剂进入再生斜管送至提升管。
5.2主要反应流程
5.2.1反应部分
原料经对称分布物料喷嘴进入提升管,并喷入燃油加热,上升过程中开始在高温和催化剂的作用下反应分解,进入反应器下段的气提段,经汽提蒸汽提升进入反应器上段反应分解后反应油气和催化剂的混合物进入反应器顶部的旋风分离器(一般为多组),经两级分离后,油气进入集气室,并经油气管道输送至分馏塔底部进行分馏,分离出的催化剂则从旋分底部的翼阀排出,到达反应器底部经待生斜管进入再生器底部的烧焦罐。
1、 目的不同
催化裂化以生产汽油、煤油和柴油等轻质油品为目的,而催化裂解旨在生产乙烯、丙烯、丁烯、丁二烯等基本化工原料。
2、原料不同
催化裂化的原料一般是减压馏分油、焦化蜡油、常压渣油、以及减压馏分油掺减压渣油;而催化裂解的原料范围比较宽,可以是催化裂化的原料,还可以是石脑油、柴油以及C4、C5轻烃等。
2 、在一定程度上,催化裂解可以看作是高深度的催化裂化,其气体产率远大于催化裂化,液体产物中芳烃含量很高。
3 、催化裂解的反应温度很高,分子量较大的气体产物会发生二次裂解反应,另外,低碳烯烃会发生氢转移反应生成烷烃,也会发生聚合反应或者芳构化反应生成汽柴油。
二、催化裂解的反应机理
四、催化裂解工艺介绍
烃类催化裂解的研究已有半个世纪的历史了,其研究范围包括轻烃、馏分油和重油,并开发出了多种裂解工艺,下面对其进行简要的介绍。
4.1 催化裂解工艺(DCC工艺)
该工艺是由中国石化石油化工科学研究院开发的,以重质油为原料,使用固体酸择形分子筛催化剂,在较缓和的反应条件下进行裂解反应,生产低碳烯烃或异构烯烃和高辛烷值汽油的工艺技术。该工艺借鉴流化催化裂化技术,采用催化剂的流化、连续反应和再生技术,已经实现了工业化。
DCC工艺具有两种操作方式——DCC-Ⅰ和DCC-Ⅱ。DCC-Ⅰ选用较为苛刻的操作条件,在提升管加密相流化床反应器内进行反应,最大量生产以丙烯为主的气体烯烃;DCC-Ⅱ选用较缓和的操作条件,在提升管反应器内进行反应,最大量地生产丙烯、异丁烯和异戊烯等小分子烯烃,并同时兼产高辛烷值优质汽油。
5.2.3烟气利用
再生器排除的烟气一般还要经三级旋风分离器再次分离回收催化剂,高温高速的烟气主要有两种路径,一、进入烟机,推动烟机旋转带动发电机或鼓风机;二、进入余热锅炉进行余热回收,最后废气经工业烟囱排放。
六、催化裂化与催化裂解的区别
从一定程度上,催化裂解是从催化裂化的基础上发展起来的,但是二者又有着明显的区别,如下:
三、催化裂解的影响因素
同催化裂化类似,影响催化裂解的因素也主要包括以下四个方面:原料组成、催化剂性质、操作条件和反应装置。
3.1 原料油性质的影响
一般来说,原料油的H/C比和特性因数K越大,
催化裂解法处理焦油方案
[1]
饱和分含量越高,BMCI值越低,则裂化得到的低碳烯烃(乙烯、丙烯、丁烯等)产率越高;原料的残炭值越大,硫、氮以及重金属含量越高,则低碳烯烃产率越低。各族烃类作裂解原料时,低碳烯烃产率的大小次序一般是:烷烃>环烷烃>异构烷烃>芳香烃。
3、催化剂不同
催化裂化的催化剂一般是沸石分子筛催化剂和硅酸铝催化剂,而催化裂解的催化剂一般是沸石分子筛催化剂和金属氧化物催化剂。
4、 操作条件不同
与催化裂化相比,催化裂解的反应温度较高、剂油比较大、蒸汽用量较多、油气停留时间较短、二次反应较为严重。
5、反应机理不同
4.2 催化热裂解工艺(CPP工艺)
该工艺是中国石化石油化工科学研究院开发的制取乙烯和丙烯的专利技术,在传统的催化裂化技术的基础上,以蜡油、蜡油掺渣油或常压渣油等重油为原料,采用提升管反应器和专门研制的催化剂以及催化剂流化输送的连续反应-再生循环操作方式,在比蒸汽裂解缓和的操作条件下生产乙烯和丙烯。CPP工艺是在催化裂解DCC工艺的基础上开发的,其关键技术是通过对工艺和催化剂的进一步改进,使其目的产品由丙烯转变为乙烯和丙烯。
一般来说,催化裂解过程既发生催Fra bibliotek裂化反应,也发生热裂化反应,是碳正离子和自由基两种反应机理共同作用的结果,但是具体的裂解反应机理随催化剂的不同和裂解工艺的不同而有所差别。
在Ca-Al系列催化剂上的高温裂解过程中,自由基反应机理占主导地位;在酸性沸石分子筛裂解催化剂上的低温裂解过程中,碳正离子反应机理占主导地位;而在具有双酸性中心的沸石催化剂上的中温裂解过程中,碳正离子机理和自由基机理均发挥着重要的作用。
催化裂化的反应机理一般认为是碳正离子机理,而催化裂解的反应机理即包括碳正离子机理,又涉及自由基机理。
催化裂解,是在催化剂存在的条件下,对石油烃类进行高温裂解来生产乙烯、丙烯、丁烯等低碳烯烃,并同时兼产轻质芳烃的过程。由于催化剂的存在,催化裂解可以降低反应温度,增加低碳烯烃产率和轻质芳香烃产率,提高裂解产品分布的灵活性。
一、催化裂解的一般特点
1、催化裂解是碳正离子反应机理和自由基反应机理共同作用的结果,其裂解气体产物中乙烯所占的比例要大于催化裂化气体产物中乙烯的比例。
如催化-蒸汽热裂解工艺(反应温度一般都很高,在800℃左右)、THR工艺(日本东洋工程公司开发的重质油催化转化和催化裂解工艺)、快速裂解技术(Stone & Webster公司和Chevron公司联合开发的一套催化裂解制烯烃工艺)等。
五、催化裂解工艺流程
5.1装置形式
催化裂解装置核心设备为反应器及再生器,常见形式为同轴式和并列式。同轴式是指反应器(沉降器)和再生器设备中心在一个竖直轴线上,两个设备连接为一个整体,其优点是节能、节省空间及制造材料,缺点是设备过于集中,施工安装及检维修不便;并列式是指反应器和再生在空间上并列布置,相对独立,有点是占用空间大,配套的钢结构成本相应高,优点是设备交叉少,内部空间较大,安装及检维修方便,工艺介质在其内部受设备形状影响较小,流体相对规律,在大型装置中应用相对较多。
3.3 操作条件的影响
操作条件对催化裂解的影响与其对催化裂化的影响类似。
以轻柴油为裂解原料的裂解气高压法顺序分离
原料的雾化效果和气化效果越好,原料油的转化率越高,低碳烯烃产率也越高;反应温度越高,剂油比越大,则原料油转化率和低碳烯烃产率越高,但是焦炭的产率也变大;由于催化裂解的反应温度较高,为防止过度的二次反应,因此油气停留时间不宜过长;而反应压力的影响相对较小。从理论上分析,催化裂解应尽量采用高温、短停留时间、大蒸汽量和大剂油比的操作方式,才能达到最大的低碳烯烃产率。
3.2催化剂的性质
催化裂解催化剂分为金属氧化物型裂解催化剂和沸石分子筛型裂解催化剂两种。催化剂是影响催化裂解工艺中产品分布的重要因素。裂解催化剂应具有高的活性和选择性,既要保证裂解过程中生成较多的低碳烯烃,又要使氢气和甲烷以及液体产物的收率尽可能低,同时还应具有高的稳定性和机械强度。对于沸石分子筛型裂解催化剂,分子筛的孔结构、酸性及晶粒大小是影响催化作用的三个最重要因素;而对于金属氧化物型裂解催化剂,催化剂的活性组分、载体和助剂是影响催化作用的最重要因素。
3.4 反应器是催化裂解产品分布的重要因素
反应器型式主要有固定床、移动床、流化床、提升管和下行输送床反应器等。针对CPP工艺,采用纯提升管反应器有利于多产乙烯,采用提升管加流化床反应器有利于多产丙烯。
3.5催化裂化原料
石蜡基原料的裂解效果优于环烷基原料。因此,绝大多数催化裂解工艺都采用石蜡基的馏分油或者重油作为裂解原料。对于环烷基的原料,特别针对加拿大油砂沥青得到的馏分油和加氢馏分油,重质油国家重点实验室的申宝剑教授开发了专门的裂解催化剂,初步评价结果表明,乙烯和丙烯总产率接近30 wt%。
4.3 重油直接裂解制乙烯工艺(HCC工艺)
该工艺是由洛阳石化工程公司炼制研究所开发的,以重油直接裂解制乙烯并兼产丙烯、丁烯和轻芳烃的催化裂解工艺。它借鉴成熟的重油催化裂化工艺,采用流态化“反应-再生”技术,利用提升管反应器或下行式反应器来实现高温短接触的工艺要求。
4.4其它催化裂解工艺