鲁奇超大规模甲醇及甲醇制化学技术介绍
甲醇(鲁奇)装置操作规程2019.06.06

甲醇(鲁奇)装置操作规程2019.06.06鲁奇甲醇合成甲醇装置操作规程编制:审核:批准:前⾔根据⼤甲醇分⼚⽣产准备⼯作的需要,为了使操作⼈员熟练掌握甲醇装置装置开⼯要领和⽇后正常操作的规范化编写本操作规程。
本操作规程是根据鲁奇公司提供的技术资料,结合国内诸多以煤为原料制甲醇⼯艺技术,从我⼚⼯艺设计实际出发⽽编写的规范操作的技术⽂件。
内容涉及到本装置⼯艺设计数据和指标、本装置开、停操作法、岗位维护操作、⽣产过程中事故和异常情况处理;以供操作⼈员学习。
引⽤⽂件:1、鲁奇公司提供《设备操作⼿册》译制;2、鲁奇公司提供的⼯艺包;3、设计院提供PSA⼯艺说明书、PID图;4、鲁奇提供PID图;5、西门⼦提供合成压缩机PID图、操作说明;6、沈⿎提供燃料⽓压缩机PID图、操作说明。
本⼿册属于技术标准体系中的⼯艺技术⽂件,编号Q/JS-04-JC-021-2010。
本⼿册由甲醇分⼚起草。
——起草⼈:——校稿⼈:——审核⼈:——审查⼈:——本⼯艺技术操作规程⾃2011年06⽉1⽇开始实施,有效期为⼀年。
⽬录第⼀章压缩、合成岗位操作规程 (6)1.1岗位任务和职责 (6)1.1.1岗位任务 (6)1.1.2岗位职责 (6)1.2岗位管辖范围 (7)1.3正常⼯艺指标 (7)1.4⼯艺流程 (10)1.5开车操作 (11)1.6停车操作 (43)1.7不正常现象及事故处理 (49) 1.8压缩机操作维护管理规定 (59)第⼆章精馏岗位操作规程 (62)2.1岗位任务和职责 (62)2.2岗位管辖范围 (63)2.3正常⼯艺指标 (63)2.4⼯艺流程 (65)2.5开车操作 (66)2.6精馏装置停车操作 (77)2.6.1正常停车 (77)2.6.2紧急停车操作 (78)2.7不正常现象及事故处理 (79)第三章罐区岗位操作规程 (85)3.1岗位任务和职责 (85)3.3正常⼯艺指标 (86)3.4⼯艺流程 (86)3.5开车操作 (87)3.6装置停车操作 (90)3.7不正常现象及事故处理 (90)第四章PSA岗位操作规程 (93)4.1岗位任务和职责 (93)4.2岗位管辖范围 (93)4.3正常⼯艺指标 (94)4.4⼯艺流程 (95)4.5开车操作 (97)4.5.1正常开车 (97)4.5.2正常⽣产维护 (101)4.6PSA装置停车操作 (103)4.6.1正常停车 (103)4.6.2紧急停车操作 (104)4.7不正常现象及事故处理 (104)第五章燃料⽓系统操作规程 (108)5.1岗位任务和职责 (108)5.2岗位管辖范围 (109)5.3正常⼯艺指标 (109)5.4⼯艺流程 (111)5.5开车操作 (112)5.6燃料⽓系统停车操作 (121)5.6.1.1计划长期性停车 (121)5.6.1.2短期临时性停车 (121)5.6.1.3紧急停车 (122)5.6.1.4触发联锁停车 (122)5.7不正常现象及事故处理 (122)第六章其他 (129)6.1与本装置密切相关的重⼤注意事项 (129)6.2设计变更项⽬ (134)6.3合成⽓压缩机特殊设备切换操作 (134)6.4环保的要求 (135)第⼀章压缩、合成岗位操作规程1.1岗位任务和职责1.1.1岗位任务将净化⼯序送来含有CO、CO2、H2的原料⽓经过压缩提压后送⼊甲醇合成反应器,在适宜温度、压⼒、空速和有催化剂存在的条件下⽣成粗甲醇;在将粗甲醇送⼊精馏单元进⾏产品精制的同时,将合成粗甲醇过程中产⽣的驰放⽓送⼊PSA氢回收单元进⾏氢⽓回收。
鲁奇(MTP)三合一项目简介(甲醇制烯烃)
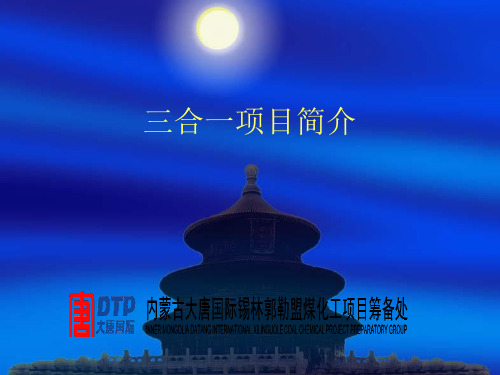
项目的定义
―三合一”是鲁奇公司提出的C1化工一体化概念,即原料(天然气、 油、煤)——中间产品(合成气、甲醇)——C1化工产品装置的一 体化,如图所示。
“三合一”:鲁奇的大甲醇工艺技术和甲醇制丙烯工艺技术
醋酸
甲醛 甲基叔丁基醚
煤
合成气 CO + H2
甲醇
FT费托合成 产品 氢 燃料l
H2S0.43%
第 二 变 换 炉
370℃
48.4T/h, 108℃
Ø3800×1 1000 单重68.4T 催化剂 QCS01:76m3
去气化
分 离 器
脱盐水
低温甲醇洗工艺(Rectisol)
以各种不同原料制取成气的工艺中,都有相
当数量的CO2以及对甲醇合成有害的毒物H2S、 COS等毒物需要除去,这类酸性气体经中合 成气中脱出后又可进一步回收利用。在本项 目里,脱出的CO2经压缩后作为Shell煤气化 工序的粉煤载气,富硫气体(以H2S为主) 经过进一步回收利用生产硫磺。
三合一项目流程框图
克劳斯硫回收
CO2 原料气 H2S
CO变换
低温甲醇洗
压缩
甲醇储存
产品甲醇
甲醇精馏
甲醇合成
H2
MTP反应
气体分离
甲醇/二甲醚
产品精馏
C3- (丙稀、乙 烯
C4+ (LPG、粗 汽油
三合一总布置图-Model
三合一项目物料框图
CO变换工艺
采用五环科技股份有限公司自主开发的高浓度CO
蒸汽加热 去精馏塔 去精馏塔 尾气洗涤
低温甲醇洗-甲醇水分离与尾气处理
甲醇蒸汽去热再生塔
97℃
去废水水处理 405.6kg/h,2 0.1℃, 0.25MPa
煤化工项目鲁奇三合一装置工艺介绍

来自电厂脱盐水 25℃,275t/h
272℃
来自气化
粗合成预热器
260℃
中压蒸汽 266℃
5.1MPa
220
一
1CL.2+
滤
H2:30.6%;
变
SA347
器
CO:9.1%;
换
CO:27.3%; H2O:32.2%
炉
330℃
中压蒸汽过热器
130.6℃, 275t/h
来自CO2吸收段的部分含CO2甲醇和H2S吸收段富硫甲醇送入中压 闪蒸塔T40003中。在此甲醇在中压下闪蒸,有价值的H2和CO闪蒸出 来,再循环气压缩机(C40001)压缩后循环回变换气入口管线。 15
精洗甲醇去洗涤塔
CO2产品送气化 140908Nm3/h,11. 7℃,0.125MPa
粗煤气来自煤气化装置
247244.48Nm3/h 170℃,3.8MPa(a)
H2:17.2%;CO:46.4%; CO2:12%;H2O:23.1%
分 离 器
变换气去低温甲醇洗装置
257600Nm3/h 40℃,3.4MPa(a)
H2:42.5%;CO:18.5%; CO2:37.5%;H2O:3%
11
2.2 低温甲醇洗单元
12
本单元主要的作用是利用甲醇在低温下对酸性
气体溶解度大,可以将其有选择性地吸收的特
性,将来自CO变换单元的变换气中多余的CO2
以及对甲醇合成催化剂有毒害作用的硫化氢等
杂质脱除,使净化后的气体成为适合于甲醇合
成反应所需的净煤气 。
本单元主要是采用一些化工单元操作,属物理
吸收塔T-40002AB从下到上依次可分为预洗段、硫化氢吸收段 和二氧化碳吸收段。
鲁奇百万吨级甲醇合成技术发展和运营优势
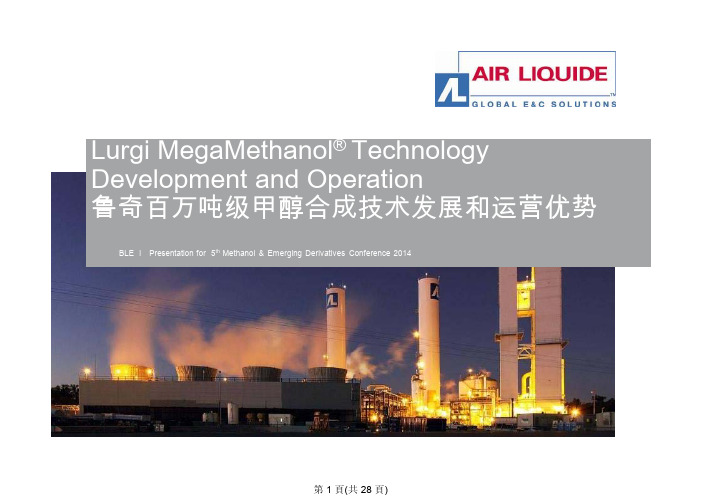
Development and Operation鲁奇百万吨级甲醇合成技术发展和运营优势Agenda议程Lurgi Methanol Technology 鲁奇甲醇技术Advantages of Lurgi’s Methanol Plant Design 鲁奇甲醇装置设计优势Agenda议程Lurgi's Methanol Technology鲁奇甲醇技术Lurgi's Methanol Technology Milestones鲁奇甲醇技术的发展历程Lurgi's MegaMethanol Loop Design鲁奇甲醇技术工艺介绍Water Cooled Methanol Reactor甲醇水冷反应器Gas Cooled Methanol Reactor甲醇气冷反应器Combined Methanol Converter (CMC) Synthesis 两步法甲醇联合转化技术Lurgi's Methanol Technology Milestones 鲁奇甲醇技术的发展历程鲁奇甲醇技术的发展历程1969 First LP-Methanol Catalyst Test1969年鲁奇首次进行低压甲醇技术催化剂工业试验1970 Cooperation with Süd-Chemie for Catalyst Manufacturer 年与催化剂产商南方化学作1970年与催化剂生产商Süd-Chemie南方化学合作1970 Operation of a 100 Tubes-Reactor Demonstration Unit1970年100根列管的示范性甲醇合成装置投入使用1972 First 3 LP-Methanol Plants in Operation1972年三套低压甲醇合成装置首次投入使用鲁奇甲醇技术的发展历程1997 MegaMethanol TM Concept Published1997年鲁奇率先提出MegaMethanol TM百万吨大甲醇概念2014 eleven contracts awarded for MegaMethanol TM plants 年赢得十套百万吨大甲醇的合同2014年赢得十一套百万吨大甲醇的合同2012 6 MegaMethanol TM plants in operation2012年6套百万吨大甲醇装置已投入生产鲁奇甲醇技术的发展历程•TITAN, Trinidad2500 mtpd1997•YPF, Argentina1200 mtpd1999•ATLAS, Trinidad5000 mtpd2000•NPC, 4th Methanol, Iran5000 mtpd2000•METHANEX, Chile 42400 mtpd2002•QAFAC, Qatar6750 mtpd2004•CNOOC, Hainan, China中海油海南2000 mtpd2004•NPC, 5th Methanol, Iran5000 mtpd2004 Methanol Holdco Ltd., 5400mtpd2004•Methanol Holdco Ltd KSA•Shchekinoazot, Russia 1200 mtpd2005•Yangzhou Yulin, China 兖州中国2300 mtpd2005•PETRONAS, Malaysia5000 mtpd2005•DTPOWER, China 大唐5000 mtpd2005•SNCG, China (MTP)神华宁煤MTP 5000mtpd2006mtpd2006•SNCG, China (DME) 神华宁煤DME 2000•Itera, Russia 1800 mtpd2006•Qinghai 青海盐湖工业集团有限公司3000 mtpd2011•Sinopec Zhongtianhechuang 中天合创 2 x 5400 mtpd2011•SNCG CTL 神华宁煤煤制油3000 mtpd2012•Zhong An中安联合煤化5400 mtpd2014Lurgi's MegaMethanol Loop Design 鲁奇大甲醇合成工艺技术Two step Combined Methanol Converter(CMC) Synthesis Loop 两步法甲醇联合转化合成技术Synthesis Gas Compressor RecycleCompressor MP-Steam 中压蒸汽Steam Drum汽包Gas Cooled Reactor MP-Steam 中压蒸汽Purge Gas Crude Methanol Synthesis Boiler FeedWater 合成气驰放气粗甲醇Gas 合成气压缩机循环气压缩机Water Cooled Reactor 水冷反应器气冷反应器Condensate 冷凝液锅炉给水Water Cooled Methanol Reactor 甲醇水冷反应器Quasi isothermal operation,Overheating of Catalyst impossible 近等温操作, 不会发生催化剂过热现象High cooling area per cubicmeter of catalyst !Extremely quick transfer of Reaction Heat 单位体积催化剂具备较高的换热面积,传热效率高Lurgi‘s Water Cooled Methanol Reactor 鲁奇甲醇水冷反应器饱和蒸汽气体入口锅炉给水80% of Reaction Heat converted to MP steam 80%的反应热可转化为中压蒸汽Thermosyphon Circulation -no Pumps (CAPEX plus reliability advantage!)冷媒热虹吸循环-不需要泵(节省设备费用且可靠性高!) Reactor can be totally fabricated in China 反应器完全可以在中国制造催化剂支撑气体出口开车蒸汽催化剂出料口Gas Cooled Methanol Reactor 甲醇水冷反应器Equal length of all headers 总管等长设计Uniform gas distributionUniform cross-section temperature profile 气流均匀分布,横截面温度均匀分布 Tube/header design for diff. pressure –low reactor cost气冷反应器管束根据循环回路压差作为设计压力,降Gas Cooled Methanol Reactor甲醇气冷反应器预热后的合成气水冷反应器出口气体进入气冷反应器低了反应器成本Free expansion of tube bundle管束自由膨胀Operation close to optimum (temperatures)最佳的操作温度Reactor can be totally fabricated in China 反应器完全可以在中国制造反应后积气出口合成气入口人孔催化剂出料口ATLAS METHANOL TRINIDADCMC synthesis in reality两步法甲醇联合转化合成装置Part 2Lurgi Methanol Technology鲁奇甲醇技术Advantages of Lurgi’s Methanol Plant Design 鲁奇甲醇装置设计优势Requirements for highly reactive synthesis gas 高反应活性合成气的必要条件■Chemistry化学CO + 2H 2= CH 3OHH = -90,8 kJ/kmol CO 2+ 3H 2= CH 3OH + H 2OH = -49,6 kJ/kmol■Thermodynamics热力学CO +H =CO +H H =412kJ/kmolRequirements for highly reactive syngas Methanol Formation Reactions 高反应活性合成气的必要条件CO + H2O = CO 2+ H2H =-41,2 kJ/kmol ■Optimum Operating Conditions最优操作条件温度Temperature: 225 -270 °C压力Pressure: 5.0 –9.0 Mpa 化学计量比SN: 2.05Reactions produce heat which has to be removed,otherwise the catalyst will be overheated !This is crucial especially for synthesis gases with high CO content (e.g. coal based syngas)反应所放的热应立即移除,否则催化剂会超温、失活,这对于CO 含量高的合成气尤为关键(例如煤基合成气)Requirements for reactive syngas Methanol Reactor designCAPEX Advantage of Lurgi’s Design 鲁奇工程设计的固定投资成本优势CAPEX advantage of Lurgi’s design 鲁奇工程设计的投资成本优势The low recycle ratio will lead to savings in CAPEX because of smaller catalyst volume, equipment and bulk (piping, valves etc.)低循环比节省固定投资成本,因为可采用体积较小设备,管道和阀Reference Capacity: 1 Train, 5400 t/d装置规模Lurgi RR=1.6Case RR=4.5CAPEX 固定投资成本H t E h A Heat Exchanger Area 换热面积22%100%Piping Weight (Synthesis Loop) 管材重量47%100%Methanol Synthesis Catalyst 催化剂需求量90%100%Recycle Ratio = 1.6Recycle Ratio = 4.5循环比循环比Influence of Recycle Ratio to CAPEX 循环比导致的固定成本比较OPEX Advantage of Lurgi’s Design 鲁奇工程设计的操作成本优势OPEX advantage of Lurgi’s design 鲁奇工程设计的操作成本优势¾The low recycle ratio will lead to savings in OPEX because of smaller utilities requirement低循环比节省操作成本,因为较低的公用工程消耗Reference Capacity: 1 Train, 5400 t/d装置规模Lurgi RR=1.6Case RR=4.5OPEX 操作成本Electricity 电耗60%100%Cooling Water 冷却水消耗40%100%Compressor Power SOR 压缩机功耗70%100%Conclusions 结论Conclusions 结论Advantages of Lurgi‘s design 鲁奇的技术优势The Next Plant to be built by LURGI is with you !Thanks for Your Attention。
国内外甲醇合成生产技术

甲醇合成一、甲醇合成生产技术十分成熟,工艺技术主要分三种:高压甲醇合成(30MPa 以上)、中压甲醇合成(10~15MPa)和低压甲醇合成(5~10MPa)。
目前,单独以产醇为的高压法工艺因其动力消耗高、催化剂活性低以及产品质量差等原因除老合成氨系统转产外,新上装置已逐年减少甚至已被淘汰,而中压法也决大多数出现联醇工艺中,当今世界上最主要的、先进的、能耗低投资省的生产工艺归属于低压合成,由于低压法工艺较之前的高压法工艺在能耗、装置建设和单系列反应器生产能力大型化等方面具有明显的优越性,所以,目前国内外新建装置大多采用低压法,根据单套装置生产能力大小不同,其设计压力主要集中在5~8MPa范围内。
甲醇合成系统包括合成气压缩(等压合成除外)、甲醇合成、热量回收、甲醇分离等。
甲醇合成塔是核心设备,目前先进的低压合成塔主要有以下几种:(1)管壳式甲醇合成塔(2)多段冷激式甲醇合成塔(3)多段径向甲醇合成塔(4)绝热式甲醇合成塔(5)Casale轴径向混合流合成塔二、国内外技术现状甲醇生产的核心技术是甲醇合成反应器(合成塔)的结构与形式、催化床温度控制和热量的转移与利用。
反应器性能的好坏直接影响原料气和动力消耗以及设备能力的发挥,而甲醇合成反应器性能主要取决于其工艺结构,特别是在合成装置向大型化发展以后,其重要性更为突出。
1、国外目前世界上具有低压甲醇先进生产工艺的主要公司和专利商主要有丹麦托普索公司(Topsoe) 、德国鲁奇公司(Lurgi)、林德公司(Linde)、英国帝国化学公司(ICI)、日本三菱公司(MGC)、瑞士卡萨利公司(Casale)等,这些国际知名企业凭借自身的技术特点,相继开发出众多塔型,根据所采用的工艺结构基本上可以分为多段绝热型、冷管型二大类。
而冷管式又可分为气冷式和水冷式二种。
2、国内目前,国内自主开发的塔型主要有林达公司的均温塔,在国内均占有较高的市场份额,已经形成竞争发展的态势。
甲醇制丙烯(MTP)工艺介绍

23
去CO2吸收塔
脱乙烷塔 压缩机
C3制冷剂
195
从脱丙烷塔 来的物流
1
脱乙烷塔
49
保护床
T-60561 C3分离塔
1
LPG
丙烯
24
C5/C6循环回 MTP反应器
CWS CWR MP蒸汽 MP冷凝液 WC WCR
脱丁烷塔塔底 主要是C5、6 及以下产品
1
脱己烷塔
1
汽油稳定塔
24
47
MP蒸汽 MP蒸汽 MP冷凝液 MP冷凝液
22
产品精制(6050)单元工艺流程简图
LPG产品 C4循环去 6040单元 MTP反应器 来液烃 6040单元 来气烃 甲醇
RP
去脱乙 烷塔
RP
萃取塔
SL
C3制冷剂 1
1
TL
脱丁烷塔
C3制冷剂
RP
48
脱丙烷塔
LP蒸汽 LP冷凝液
152
LP蒸汽
RP
LP冷凝液
废水去甲醇回收塔 处理后排出装置
去脱己烷塔经过分 离后出汽油产品
送入激冷塔,用激冷水进行冷却,温度降
至40℃后送至碳氢压缩单元。出激冷塔的
激冷水大部分经过热量回收后循环回激冷
塔,小部分送到甲醇回收塔,回收其中含
有的甲醇,回收的甲醇与新鲜甲醇混合进
入DME反应器。
17
气体冷却和分离(6030)单元工艺流程简图
碱液 火炬
PC
去碳氢压缩单元
WR
E-60312
WR
E-60311A-F
13
反应单元(6010)工艺流程简图
DME反应器 内径:5m 切线高度:10.8m 275℃ 1.60MPa(a)
德国鲁奇60万吨甲醇合成工艺分析

德国鲁奇60万吨甲醇合成工艺分析发布时间:2023-03-28T01:39:27.059Z 来源:《中国科技信息》2023年第1月1期作者:姜豪谨[导读] 目前德国鲁奇公司已广泛采用了两种方法:一步法和二步法。
一步法甲醇的生产采用的是水冷却式反应器,当其规模达到100 t/a 时,通常会有两台。
姜豪谨海洋石油富岛有限公司丙烯腈项目组,572600,海南省摘要:目前德国鲁奇公司已广泛采用了两种方法:一步法和二步法。
一步法甲醇的生产采用的是水冷却式反应器,当其规模达到100 t/a 时,通常会有两台。
两步法的甲醇合成反应采用了水冷式和气冷式相结合的方法,在液相式塔中采用了壳式的催化剂,在气冷塔中采用了一种新型的高效传热方法。
国内目前较为常见的德国鲁奇60万吨甲醇合成工艺为一步法,比其他方法更具优越性,它的转化热量迅速、稳定性好,和等温法较为相似,且与理想的反应曲线十分相近,能有效地保持催化剂的活力,且催化剂运行时间较长,且转化率较高。
关键词:德国鲁奇;60万吨甲醇;合成工艺;化学还原引言:目前甲醇生产企业在国内的规模不断扩大,诸多企业均使用了德国鲁奇的水冷式反应釜技术。
MegaMaxNJ-1催化剂在催化反应中的使用是为了加速反应。
从实际数据来看,MegaMaxNJ-1催化剂具有良好的催化性能,其催化性能和反应性能均满足了甲醇的设计要求。
但在实际应用过程中,可以看出催化剂会对反应产物的反应性能和反应速度产生一定的影响,因此还需要进一步探讨分析德国鲁奇60万吨甲醇合成工艺分析,明确甲醇合成催化剂的加热和还原反应。
1.德国鲁奇60万吨甲醇合成工艺具体分析德国鲁奇60万吨甲醇合成工艺过程中,主要以陶瓷球床层作为催化剂,它被填满在管板下方、反应器外壳和反应器底部的圆锥区域。
在反应釜的底部,约80%的陶瓷球体被填满,直至盖住圆锥的顶部。
当加注后,该合成机在充满水蒸气时,该合成器的内部压力与其上水汽温度成正比关系,从而将被吸收的水分凝结成液态的水,蒸汽凝结物附着于所述催化剂的内部。
煤化工项目鲁奇三合一装置工艺介绍PPT(56张)
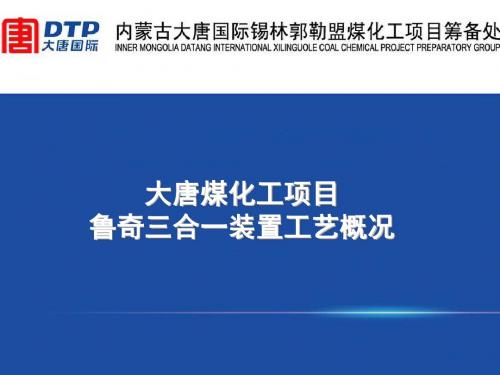
甲醇/二甲醚
产品精馏
压缩
气体分离
MTP 反 应
器
甲醇合成
H2
三塔精馏
6
本界区原料、产品方案
粗煤气: 640万吨/年
二氧化碳: 200万吨/年
甲醇: 168万吨/年
乙烯: 2.3万吨/年
丙烯: 47万吨/年
LPG: 3.64万吨/年
硫磺: 3.8万吨/年
汽油: 18.2万吨/年 7
2、各装置工艺流程简介
15
去再吸收塔
低温甲醇洗-气体洗涤
来自CO变换工段的变换气(温度40℃,压力3.4Mpa(a)),首先 经过一系列换热器换热后被冷却到约10℃,然后通过氨洗涤塔 T40001(,用锅炉给水进行洗涤以降低其NH3 和HCN含量。再经过 变换气最终冷却器(绕管式)后,温度降到-19.9℃,送到并联的 两台吸收塔T-40002AB的底部。
260℃
中压蒸汽 266℃5.源自MPa220℃第600t/h
SA387Gr.1
过
一
1CL.2+
滤
H2:30.6%;
变
SA347
器
CO:9.1%;
换
CO:27.3%; H2O:32.2%
炉
330℃
中压蒸汽过热器
130.6℃, 275t/h
450℃
第
二
变
换
炉
分 40℃ 离 器
除盐水加热器
361℃
H2:38.8%;
大唐煤化工项目 鲁奇三合一装置工艺概况
1
一、三合一装置简介
2
三合一装置是指大唐国际引进德国鲁奇公司的三项专利 技术:低温甲醇洗脱硫脱碳工艺、百万吨级甲醇合成工 艺和甲醇制丙稀MTP工艺 (Methanol to Propylene) 的总称,同时包括CO变换单元。其中甲醇制丙烯装置为 目前世界上首套工业化装置
德国鲁奇

德国鲁奇公司情况时间:2007-09-06 15:11 来源:进入论坛手机读报我要评论公司概况鲁奇公司是化工领域最著名的工程公司之一,与我国化工系统交往由来已久,该公司以煤化工专长而著称,我国引入其固定床加压煤气化技术生产城市煤气和合成氨已有50年。
鲁奇公司随时代变化,在战略上作出较大的调整。
首先,鲁奇公司将煤气化技术转给南非萨索,成立了萨索-鲁奇公司。
其次,鲁奇公司将关注的焦点从煤炭转移到石油和天然气领域,油、气、化学品并重,开发较高附加价值产品。
现有雇员1300名,去年完成销售收入11亿美元。
鲁奇集团(Lurgi Group)包括三部分,即油、气、化学品(Oil•Gas•Chemicals,生命科学(Life Sciences)和金属(Metallurgy)。
鲁奇从有色金属起家,现在向油气方向发展,但中国依然是鲁奇第一大商务活动中心。
鲁奇公司与中咨公司合资成立了北京鲁奇工程咨询公司,近两年已开始运作。
鲁奇公司目前从事业务包括技术研发与工程咨询、项目的可行性研究、市场开发、技术服务等。
鲁奇公司引为自豪的是其研发能力,在1897年就开始申请了第一项专利。
公司有完善的实验、测试装置,满足研发的需求,现有100余套试验设备,可与顾客共同研发,共享成果。
对持有原料,但不明方向的客户,可协助其开发,并确保产品在国际市场上有长久竞争力。
目前公司主要从事研发新工艺,现工艺改造的示范装置,催化剂的分析与评估。
鲁奇公司向油气方向发展最明显的举措是开发出以天然气为原料超大规模生产甲醇的工艺(Lurgi Mega Methanol),其规模可达日产5000吨,目前正在特里尼达和多巴哥以及伊朗建设两套装置。
该工艺过程为:天然气经脱硫、预转化后与氧气混合,经自热转化后与氢气混合合成甲醇。
在甲醇应用上,鲁奇开发了以ZSM5分子筛为催化剂,用甲醇制丙烯的MTP技术,该技术值得借鉴。
鲁奇公司开发的循环硫化床(CFB)技术可用于我国小化肥气化的技术改造,鲁奇公司同意与中方合作,选择一试点进行改造示范。
鲁奇甲醇合成工艺概述
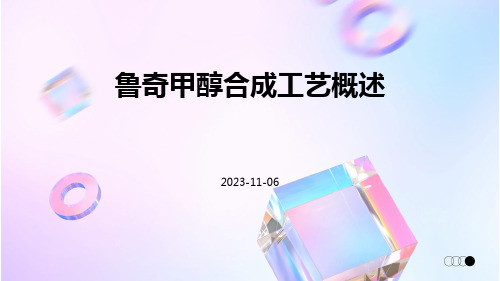
03
气体组成
反应气体组成对反应速率和选择性也 有重要影响。需要根据催化剂的特性 选择合适的氢气和一氧化碳比例,同 时保持适当的氮气含量。
产品分离及精制方法
产品分离
甲醇合成反应后的气体混合物需要进行分离 ,将甲醇从其他气体中分离出来。常用的分 离方法包括低温分离、蒸馏分离和吸附分离 等。
精制
分离出的甲醇还需要进行精制,以去除其中 的水分、二氧化碳和其他杂质,得到高纯度 的甲醇产品。常用的精制方法包括蒸馏、离
02
鲁奇甲醇合成工艺流程
反应原理
甲醇合成的化学反应 使用一氧化碳和氢气作为原料 在催化剂的作用下,通过加热和加压条件进行化学反应
反应原理
生成甲醇和水
鲁奇甲醇合成法 采用高温高压反应条件
反应原理
使用锌铬催化剂或铜基催化剂
主要产品为甲醇和二甲醚
工艺流程图解
包含催化剂、原料、反应条件、分离和 精制等环节的流程图
一般采用蒸馏塔或萃取塔进行分离
主要设备及功能介绍
使产品达到较高的纯度和收率 精制设备 对分离后的粗甲醇进行进一步的处理和提纯
主要设备及功能介绍
一般采用蒸馏、吸附、离子交换等 方法进行精制
VS
使产品达到所需的质量指标和规格 要求
03
鲁奇甲醇合成工艺关键要 素
原料及催化剂选择
原料
甲醇合成反应需要使用一氧化碳、氢气和 氮气作为原料,其中一氧化碳和氢气是主 要原料,氮气作为保护气。
详细描述
某研究院研发的新型催化剂在鲁奇甲醇合成工艺中成功 应用,通过实验研究,该催化剂具有较高的活性、稳定 性及较低的成本,为甲醇合成工艺提供了新的研究方向 和应用前景。
案例三
总结词
鲁奇大甲醇工艺技术特点及影响因素

鲁奇大甲醇工艺技术特点及影响因素摘要:甲醇是最简单的醇类物质,也是最广泛应用的工业原料,随着甲醇需求量的不断增长,合成工艺也朝向多样化、大型化飞速发展。
本文比较常见大甲醇工艺,重点介绍鲁奇的工艺路线和特点,探讨反应影响因素,能够更加深入有效地掌握甲醇工业生产的操作控制。
关键词:甲醇,合成工艺,影响因素,工业生产前言:为充分有效利用煤炭资源,提高煤化工产业规模效益,国内不断引进、研发大甲醇合成技术,煤制甲醇和以甲醇为中间体的深加工产业逐渐朝向大型化、国产化发展,了解鲁奇大甲醇的工艺特点,分析装置运行状况,对甲醇生产路线的使用选择、节能优化、改造维稳具有重要作用。
1常见大甲醇工艺比较甲醇合成生产技术已经十分成熟,国内外工业甲醇生产大多采用低压法,反应压力控制在5~10MPa,世界上具有低压甲醇先进生产工艺的主要公司和专利商主要有丹麦托普索公司(Topsoe)、德国鲁奇公司(Lurgi)、英国戴维(Davy)、日本东洋(TEC)、瑞士卡萨利公司(Casale)等,这些专利商凭借各自技术特点,相继推出众多的反应器塔型、催化剂类型,形成一套长周期稳定运行的生产系统。
表1 常见甲醇合成工艺特点工艺反应器型式配套催化剂优点缺点Lu型式为列管式活性床层反应器rgi换热器,管内装催化剂,管间为沸腾水高,易失效,价格高温差小,单程转化率高,热能利用率高结构复杂,材质要求高,空速高Da vy蒸汽上升式合成塔(SCR),催化剂在壳层,管内产生蒸汽使用寿命长,价格贵材质要求低,反应器结构简单温度波动大,循环量大,流动情况复杂TE CMFR型,双套管水冷型,管内走水活性高,使用寿命长热能利用率高,床层压降低,更易放大生产强制水循环,增加动力消耗Ca sale换热板式等温反应器,换热板内走水装填量大,易烧结床层压降小,换热效率高流程复杂,设备制造难度大,催化剂装卸困难To psoe类似鲁奇水冷反应器,多个反应器并联增加产量活性高,用量少流程简单,设备投资小,生产操作简单规模有限制,反应器结构复杂2鲁奇大甲醇合成工艺介绍德国鲁奇公司是世界上主要的甲醇技术供应商之一,在上世纪70年代就成功开发成功了鲁奇低压法甲醇合成技术。
鲁奇甲醇合成工艺概述

• 由于化学平衡的制约,氢、碳的单程转 化率较低,在产品甲醇充分分离出来之 后未反应的气体要返回甲醇合成反应器, 因而甲醇合成流程由甲醇合成、甲醇的 分离和未反应气的循环三部分组成。甲 醇的精馏则是利用粗甲醇各组分沸点的 差异,经过一系列的精馏过程,最终实 现精甲醇产品的制取及馏出物的达标排 放。
ห้องสมุดไป่ตู้
• 水冷反应器R2001为一管壳式反应器,类 似于列管换热器。管内装满了铜基催化 剂,当混合气体进入催化剂床层后,在 压力约为8.28MPa,温度约为250℃的条 件下H2与CO、CO2反应生成甲醇和水, 同时还有微量的其它有机杂质生成。其 主反应式为:
• CO + 2H2 → CH3OH + Q • CO2 + 3H2 → CH3OH + H2O + Q
中间罐区
• 甲醇合成工段来的粗甲醇先贮存在粗甲 醇贮槽V2112A/B内,由预塔进料泵 P2112A/B送往精馏工序。精甲醇中间槽 V2107A/B的甲醇经分析检验合格后经精 甲醇泵P2107A/B送至成品罐区甲醇成品 储罐D5001A/B/C/D。
成品灌区
• 甲醇贮罐的成品甲醇,分别经由甲醇汽 车灌装泵P5003送往汽车站台装车;经由 甲醇火车灌装泵P5001A/B/C送往火车站 台装车。另外甲醇罐区设有甲醇地下槽 D5002,收集来自于D5001A/B/C/D的含 醇废液,通过甲醇液下泵P5002送往甲醇 精馏工段。
• 预精馏塔T2101塔顶操作温度为72℃,操 作压力为0.04MPaG;塔底操作温度为 79.1℃,操作压力为0.05MPaG。
• 为防止粗甲醇中酸性物质腐蚀塔设备, 用碱液泵P2106A/B在预精馏塔T2101下 部加入一定量的稀碱液,使预精馏塔 T2101底的甲醇PH值保持在8~9。稀碱 液在配碱槽V2113和碱液贮槽V2106中配 制和储存。
MTO和MTP技术简介
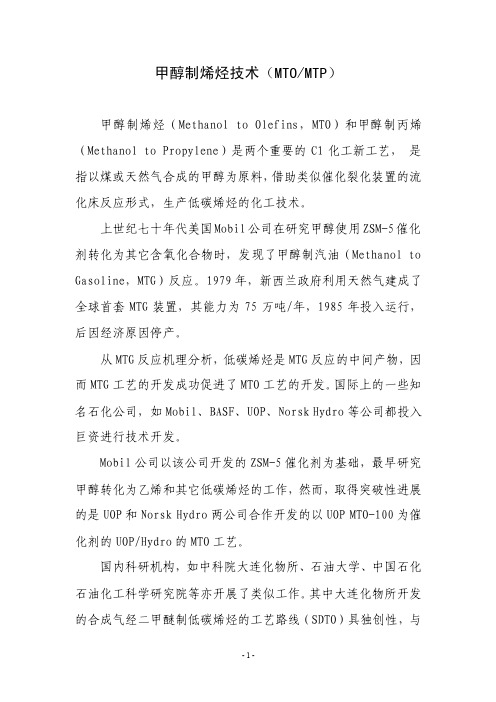
甲醇制烯烃技术(MTO/MTP)甲醇制烯烃(Methanol to Olefins,MTO)和甲醇制丙烯(Methanol to Propylene)是两个重要的C1化工新工艺,是指以煤或天然气合成的甲醇为原料,借助类似催化裂化装置的流化床反应形式,生产低碳烯烃的化工技术。
上世纪七十年代美国Mobil公司在研究甲醇使用ZSM-5催化剂转化为其它含氧化合物时,发现了甲醇制汽油(Methanol to Gasoline,MTG)反应。
1979年,新西兰政府利用天然气建成了全球首套MTG装置,其能力为75万吨/年,1985年投入运行,后因经济原因停产。
从MTG反应机理分析,低碳烯烃是MTG反应的中间产物,因而MTG工艺的开发成功促进了MTO工艺的开发。
国际上的一些知名石化公司,如Mobil、BASF、UOP、Norsk Hydro等公司都投入巨资进行技术开发。
Mobil公司以该公司开发的ZSM-5催化剂为基础,最早研究甲醇转化为乙烯和其它低碳烯烃的工作,然而,取得突破性进展的是UOP和Norsk Hydro两公司合作开发的以UOP MTO-100为催化剂的UOP/Hydro的MTO工艺。
国内科研机构,如中科院大连化物所、石油大学、中国石化石油化工科学研究院等亦开展了类似工作。
其中大连化物所开发的合成气经二甲醚制低碳烯烃的工艺路线(SDTO)具独创性,与传统合成气经甲醇制低碳烯烃的MTO 相比较,CO 转化率高,达90%以上,建设投资和操作费用节省50%~80%。
当采用D0123催化剂时产品以乙烯为主,当使用D0300催化剂是产品以丙烯为主。
一、催化反应机理MTO 及MTG 的反应历程主反应为:2CH 3OH →C 2H 4+2H 2O3CH 3OH →C 3H 6+3H 2O反应历程如下:环烷烃芳烃较高级烯烃异构烷烃正低碳烯烃/ OH 2CH H2OH2O -33H2O H2O -3−→−−−−←−−→−−−−←−−→−++OCH CH 甲醇首先脱水为二甲醚(DME),形成的平衡混合物包括甲醇、二甲醚和水,然后转化为低碳烯烃,低碳烯烃通过氢转移、烷基化和缩聚反应生成烷烃、芳烃、环烷烃和较高级烯烃。
大型煤制甲醇的气化和合成工艺选择

大型煤制甲醇的气化和合成工艺选择发布时间:2022-08-05T02:30:03.539Z 来源:《工程建设标准化》2022年第37卷3月第6期作者:郑宗星[导读] 在中国,国土面积相对较大,能源消耗也非常严重。
郑宗星山东华鲁恒升化工股份有限公司山东省德州市 253005摘要:在中国,国土面积相对较大,能源消耗也非常严重。
因此,有必要提高能源生产、加工和应用的效率,为当今社会的稳定快速发展带来重大帮助。
甲醇是我国社会经济发展中常见的网络资源。
甲醇装置的关键是在其汽化后进行转化,确保其经过净化处理后生成,最后进行精馏塔。
这些都是甲醇涉及的重要装置和实际操作过程。
涉及的风险源也很多,包括高炉煤气、氡气、液氯、压缩天然气、甲醇、硫磺粉和盐酸。
这些是易燃、易爆和有害化学品。
其中,生产装置区为动物保护区。
为了丰富国内煤炭资源,利用煤炭资源进行甲醇的生产和生产十分重要。
现阶段,我国化石能源短缺,工业生产危害明显。
因此,为了解决能源问题,必须以煤制甲醇的方式取代原油的消费。
关键词:大型煤制甲醇;气化;合成;工艺选择1大型煤制甲醇工艺是国情的需要改革开放以来,中国制造业呈现出快速发展的态势。
现阶段,社会经济发展、生产技术和生产效率都在缓慢提高和自主创新。
生产技术的进步促进了社会资源的应用。
在工业生产的发展趋势中,甲醇作为主要的动力能源,受到了我们的高度重视。
随着甲醇生产技术的不断完善,甲醇的生产也发生了很大的变化。
在这种情况下,我们必须根据各种技术方法的应用,为灵活利用网络资源和可持续发展理念打下基础,应对我国社会经济发展对新能源的要求。
因此,有必要充分对应煤基清洁工艺的应用,促进甲醇电能的生产和制造,这是制造业的主要资源。
2大型煤制甲醇的气化工艺选择2.1固定床气化在生产甲醇中使用固定床工艺时,需要对块状煤进行使用,通常来说,在整个生产中,煤炭的转换率并不高,气化程度较低,同时在排放的污水中酚和焦油较多,工艺措施复杂性较强,需要投入较高的工艺成本。