压铸工艺及模具复习资料概述
压铸知识培训资料
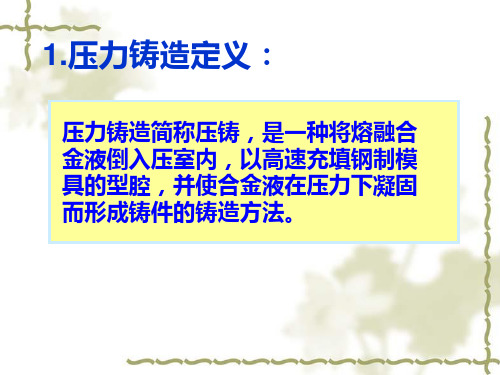
5.压铸机、压铸金属及压铸模具是组成压 铸工艺的3个要素。
卧式压铸机
立式压铸机
6.压铸机分类:
压铸机一般分为热压室压铸机和冷压室压铸机两大类。 冷压室压铸机按其压室结构和布置方式分为卧式压铸机 和立式压铸机(包括全立式压铸机)两种。 热压室压铸机(简称热空压铸机)压室浸在保温溶化坩 埚的液态金属中,压射部件不直接与机座连接,而是装 在坩埚上面。这种压铸机的优点是生产工序简单,效率 高;金属消耗少,工艺稳定。但压室,压射冲头长期浸 在液体金属中,影响使用寿命。并易增加合金的含铁量。 热压室压铸机目前大多用于压铸锌合金等低熔点合金铸 件,但也有用于压铸小型铝、镁合金压铸件。 冷室压铸机的压室与保温炉是分开的。压铸时,从保温 炉中取出液体金属浇入压室后进行压铸。
4.压力铸造适用材料及浇铸温度:
铝合金 铝硅系 610-650℃ 640-680℃ 600-620℃ 610650℃ 铝铜系 630-660℃ 660-700℃ 600-640℃ 630-660℃ 铝镁系 640-680℃ 660-700℃ 640-670℃ 650-690℃ 铝锌系 590-620℃ 620-660℃ 580-620℃ 600-650℃ 锌合金 420-440℃ 430-450℃ 400-420℃ 420-440℃ 镁合金 640-680℃ 660-700℃ 640-670℃ 650-690℃ 铜合金 普通黄铜 910-930℃ 940-980℃ 900-930℃ 900950℃ 硅黄铜 900-920℃ 930-970℃ 910-940℃ 910-940℃
7.压铸模具:
8.压铸工艺知识:
8-1、压力和速度的选择:按铸件结构确定。
8-2、浇注温度:从压定进入型腔时液态金属的平均温度。 8-3、压铸型的温度:在压铸前应进行预热。
压铸知识培训资料
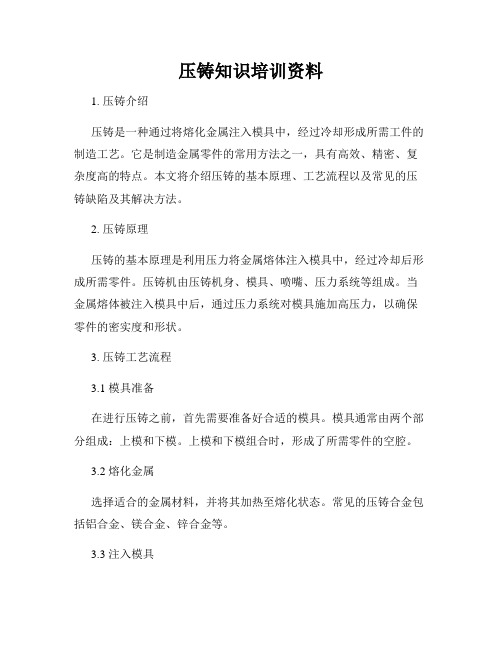
压铸知识培训资料1. 压铸介绍压铸是一种通过将熔化金属注入模具中,经过冷却形成所需工件的制造工艺。
它是制造金属零件的常用方法之一,具有高效、精密、复杂度高的特点。
本文将介绍压铸的基本原理、工艺流程以及常见的压铸缺陷及其解决方法。
2. 压铸原理压铸的基本原理是利用压力将金属熔体注入模具中,经过冷却后形成所需零件。
压铸机由压铸机身、模具、喷嘴、压力系统等组成。
当金属熔体被注入模具中后,通过压力系统对模具施加高压力,以确保零件的密实度和形状。
3. 压铸工艺流程3.1 模具准备在进行压铸之前,首先需要准备好合适的模具。
模具通常由两个部分组成:上模和下模。
上模和下模组合时,形成了所需零件的空腔。
3.2 熔化金属选择适合的金属材料,并将其加热至熔化状态。
常见的压铸合金包括铝合金、镁合金、锌合金等。
3.3 注入模具熔化的金属通过喷嘴注入模具中。
注入时需要保持恰当的温度和压力,以确保金属熔体充分填充模具空腔,并达到所需的形状、尺寸和表面质量。
3.4 冷却固化经过一段时间的冷却,金属熔体会逐渐固化成所需零件。
冷却时间取决于所使用的金属材料和零件的复杂度。
3.5 模具开启冷却固化后,模具会被打开,将成型的零件取出。
此时,零件通常还需经过后续的去毛刺、清洗和表面处理等工艺。
4. 常见压铸缺陷及其解决方法4.1 气孔气孔是指於压铸过程中形成的气体在金属熔体固化时被困住而产生的孔洞。
气孔会影响零件的密实度和强度。
解决方法:- 优化压铸过程中的通风系统,以消除气体积聚的机会。
- 使用合适的压力和注入速度,以确保金属熔体充分填充模具空腔,减少气体残留。
4.2 闪痕闪痕是指在模具接缝处形成的短裂纹或凹陷区域。
闪痕可能会导致零件的密封性能和外观质量下降。
解决方法:- 检查和调整模具的结构,尽可能减少接缝处的压力集中。
- 调整注入速度和压力,以避免压力过高造成闪痕现象。
4.3 密实度不良密实度不良是指零件内部存在过多的空洞或孔隙,导致零件不够坚固。
压铸工艺复习资料
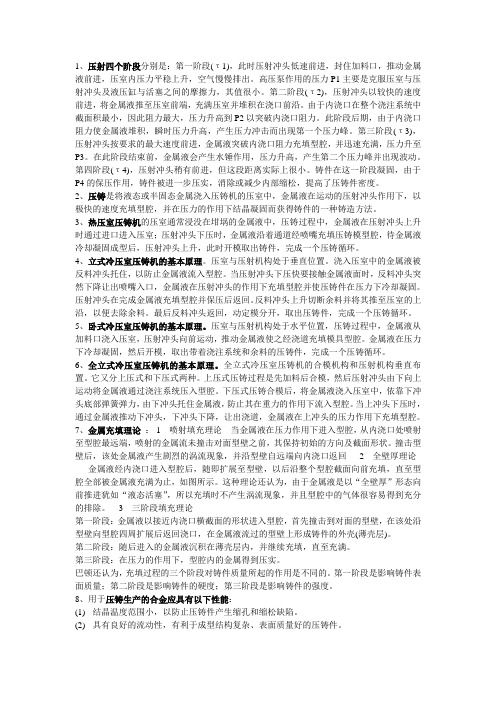
1、压射四个阶段分别是:第一阶段(τ1),此时压射冲头低速前进,封住加料口,推动金属液前进,压室内压力平稳上升,空气慢慢排出。
高压泵作用的压力P1主要是克服压室与压射冲头及液压缸与活塞之间的摩擦力,其值很小。
第二阶段(τ2),压射冲头以较快的速度前进,将金属液推至压室前端,充满压室并堆积在浇口前沿。
由于内浇口在整个浇注系统中截面积最小,因此阻力最大,压力升高到P2以突破内浇口阻力。
此阶段后期,由于内浇口阻力使金属液堆积,瞬时压力升高,产生压力冲击而出现第一个压力峰。
第三阶段(τ3),压射冲头按要求的最大速度前进,金属液突破内浇口阻力充填型腔,并迅速充满,压力升至P3。
在此阶段结束前,金属液会产生水锤作用,压力升高,产生第二个压力峰并出现波动。
第四阶段(τ4),压射冲头稍有前进,但这段距离实际上很小。
铸件在这一阶段凝固,由于P4的保压作用,铸件被进一步压实,消除或减少内部缩松,提高了压铸件密度。
2、压铸是将液态或半固态金属浇入压铸机的压室中,金属液在运动的压射冲头作用下,以极快的速度充填型腔,并在压力的作用下结晶凝固而获得铸件的一种铸造方法。
3、热压室压铸机的压室通常浸没在坩埚的金属液中,压铸过程中,金属液在压射冲头上升时通过进口进入压室;压射冲头下压时,金属液沿着通道经喷嘴充填压铸模型腔,待金属液冷却凝固成型后,压射冲头上升,此时开模取出铸件,完成一个压铸循环。
4、立式冷压室压铸机的基本原理。
压室与压射机构处于垂直位置。
浇入压室中的金属液被反料冲头托住,以防止金属液流入型腔。
当压射冲头下压快要接触金属液面时,反料冲头突然下降让出喷嘴入口,金属液在压射冲头的作用下充填型腔并使压铸件在压力下冷却凝固。
压射冲头在完成金属液充填型腔并保压后返回。
反料冲头上升切断余料并将其推至压室的上沿,以便去除余料。
最后反料冲头返回,动定模分开,取出压铸件,完成一个压铸循环。
5、卧式冷压室压铸机的基本原理。
压室与压射机构处于水平位置,压铸过程中,金属液从加料口浇入压室,压射冲头向前运动,推动金属液使之经浇道充填模具型腔。
压铸模设计考试重点
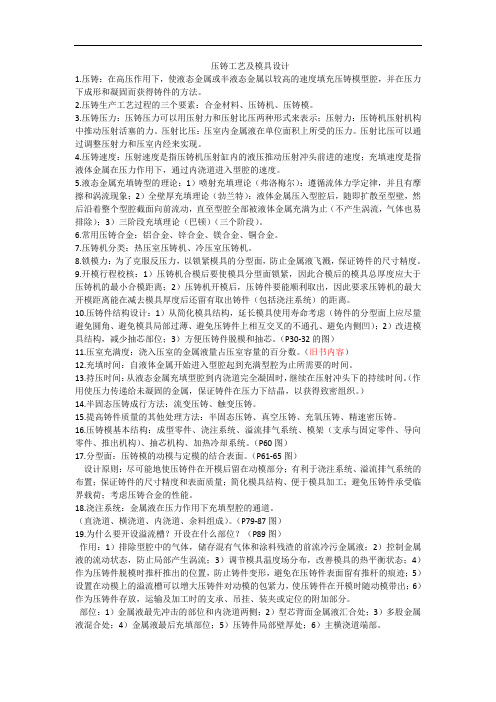
压铸工艺及模具设计1.压铸:在高压作用下,使液态金属或半液态金属以较高的速度填充压铸模型腔,并在压力下成形和凝固而获得铸件的方法。
2.压铸生产工艺过程的三个要素:合金材料、压铸机、压铸模。
3.压铸压力:压铸压力可以用压射力和压射比压两种形式来表示;压射力:压铸机压射机构中推动压射活塞的力。
压射比压:压室内金属液在单位面积上所受的压力。
压射比压可以通过调整压射力和压室内经来实现。
4.压铸速度:压射速度是指压铸机压射缸内的液压推动压射冲头前进的速度;充填速度是指液体金属在压力作用下,通过内浇道进入型腔的速度。
5.液态金属充填铸型的理论:1)喷射充填理论(弗洛梅尔):遵循流体力学定律,并且有摩擦和涡流现象;2)全壁厚充填理论(勃兰特):液体金属压入型腔后,随即扩散至型壁,然后沿着整个型腔截面向前流动,直至型腔全部被液体金属充满为止(不产生涡流,气体也易排除);3)三阶段充填理论(巴顿)(三个阶段)。
6.常用压铸合金:铝合金、锌合金、镁合金、铜合金。
7.压铸机分类:热压室压铸机、冷压室压铸机。
8.锁模力:为了克服反压力,以锁紧模具的分型面,防止金属液飞溅,保证铸件的尺寸精度。
9.开模行程校核:1)压铸机合模后要使模具分型面锁紧,因此合模后的模具总厚度应大于压铸机的最小合模距离;2)压铸机开模后,压铸件要能顺利取出,因此要求压铸机的最大开模距离能在减去模具厚度后还留有取出铸件(包括浇注系统)的距离。
10.压铸件结构设计:1)从简化模具结构,延长模具使用寿命考虑(铸件的分型面上应尽量避免圆角、避免模具局部过薄、避免压铸件上相互交叉的不通孔、避免内侧凹);2)改进模具结构,减少抽芯部位;3)方便压铸件脱模和抽芯。
(P30-32的图)11.压室充满度:浇入压室的金属液量占压室容量的百分数。
(旧书内容)12.充填时间:自液体金属开始进入型腔起到充满型腔为止所需要的时间。
13.持压时间:从液态金属充填型腔到内浇道完全凝固时,继续在压射冲头下的持续时间。
压铸模具设计基础知识

熱室壓鑄鋅合金中的合金元素
---雜質元素-鐵
鋅合金中鐵元素含不能>0.02%,鐵 元素可:
☺ 增加合金的硬度
但同時
增加合金的脆性
和合金中的鋁發生反應形成Al5Fe2金屬間化合物, 造成鋁元素的損耗並形成浮渣
在壓鑄件中出現硬點
2024/2/1
压铸模具设计基础知识
五.壓鑄合金及其性能
熱室壓鑄鋅合金中的合金元素 ---雜質元素-硅
t1:F1為克服磨擦力(壓室中)
壓
t2:開始進入型腔﹐因澆口急減﹐阻力 力
F
增大﹐F2>F1,達到高速充填
t3:(快速增壓階段)快速充填直止充滿
型腔最大值F3為壓射壓力
t4:F4靜壓力﹐對鑄件壓實
時間t
(壓射力與時間關係曲線見右圖)
2024/2/1
压铸模具设计基础知识
六.壓鑄工藝
定義2﹕壓射壓力就是在充模剛結束時壓射沖頭作用在金屬液面上的力。 定義3﹕壓射壓力是以壓射比壓來表示﹐壓射比壓就是充模結束時﹐壓射
沖頭作用于單位面積金屬液面上的壓力。
P ﹕壓射比壓( Pa ) P= F 4F F: 壓射壓力(N)
A πd 2 d ﹕壓室直徑 (m) A﹕沖頭截面積( m 2 )
壓射比壓與壓射壓力成正比﹐與壓射沖頭的截面積成反比。
鋅合金的 壓射比壓
壁厚 =<3mm 30MPa 簡單 40MPa 復雜
壁厚 >3mm 50MPa 簡單 60MPa 復雜
有害雜質元素:鐵(Fe),硅(Si),鉛(Pb),鎘(Gd),錫(Sn)
來源於鋁
來源於鋅
2024/2/1
压铸模具设计基础知识
五.壓鑄合金及其性能
2024/2/1
压铸模复习要点

第一章(i)压力铸造:将熔融的液态金属或半熔融的金属注入压铸机的压室,通过压射冲头的运动,使液态金属在高压作用下,高速通过模具浇注系统填充型腔,在压力下结晶并迅速冷却凝固成形的一种精密铸造方法,简称压铸,也称金属压铸。
(ii)压铸法的两大特点:高压力、高速度优点1) 可压铸形状复杂的薄壁铸件;2) 压铸件的尺寸精度高,表面粗糙度低;3) 材料利用率高;4) 压铸件的强度和表面硬度都较高;5) 生产效率高,生产过程容易实现机械化和自动化;6) 可嵌铸其它材料的零件。
缺点1) 容易产生气孔,不能进行热处理,压铸某些内凹件还比较困难;2) 压铸设备造价高,模具制造复杂,不宜小批量生产;3) 压铸高熔点金属(如铜、黑色金属)时,压铸模的使用寿命低,故黑色金属的压铸很少使用;4) 压铸模的成型部分处在高温、高压及多变应力条件下工作,因此对其材料的性能有特殊的要求。
压铸生产的三要素:压铸合金、压铸机、压铸模(iii)典型的压铸填充理论(一)全壁厚填充理论条件:V<0.3m/s t内/ t件>1/2-2/3特点:1、金属液经内浇口进入型腔后,即扩展至型壁,后沿整个型壁截面向前填充,直到充满为止。
2、排气良好,铸件致密度高。
3、是最理想的一种充填形态。
适合:合金结晶区间较宽,形状简单的铸件。
(二)喷射填充理论条件:V=0.5-15m/s S内/ S件>1/4-1/3特点:1、金属液的充填过程分两个阶段:喷射阶段、涡流阶段。
液体金属进入型腔后保持内浇口形状冲击对面型壁,然后形成涡流,向内浇口方向反向填充。
2、易形成孔洞。
适合:具有缝形浇口的长方形铸件或具有大的充填速度及薄的内浇口的铸件。
(三) 三阶段填充理论条件:V>20-30m/s S内/ S件<1/4-1/2特点:高速金属液射入型腔后,首先冲击对面型壁,沿型腔表面向各方向扩展,并形成压铸件表面的薄壳层,在型腔转角处产生涡流;后续金属液沉积在薄壳层内的空间里,直至填满;金属液完全充满型腔后,在压力作用下,补充熔融金属,压实压铸件。
压铸培训

52108853AA
异常曲线生产的产品
52108853AA
正常曲线及产品
G-BOX
产品探伤有气孔
G-BOX
检查产品,有冷隔缺陷
G-BOX
怀疑料温不够或模温不够,经调整料温、减少开模延 时,无明显改善;后将抽芯冷却水关掉,再生产OK。
G-BOX
怀疑料温不够或模温不够,经调整料温、减少开模延 时,无明显改善;后将抽芯冷却水关掉,再生产OK。
Home
5213606AB
浇口部位气孔:当靠近浇口部位有气孔,且敲掉浇口后,断 口部位能看出明显气孔时,基本上就是浇口套或料筒里进水, 这时需检查浇口套或压射头是否有漏水。检查浇口套时,需 将进水打开,回水关掉,等10分钟左右再观察浇口套是否漏 水。
5213606AB
52108853AA
异常曲线
压铸培训
一、压铸理论知识 1、压铸填充原理 2、压射机构工作原理 3、压射填充过程 二、压铸生产过程 1、压铸工序记录注意事项 2、模具冷却水检查 3、喷涂 三、压铸安全操作规程 四、压铸机工艺参数的调整 五、喷雾机、取件机的调整
压铸填充原理
• 压力铸造(简称压铸) 是将熔化的金属,在 高压作用下,以高速 填充至模具型腔内, 并使金属在此压力下 凝固而形成铸件的一 种方法。高压、高速 是压铸法与其他铸造 方法的根本区别,也 是最重要的特点。
压铸生产过程
• 以8G13为例
Home
模具冷却水检查
在装模具冷却水及接班时,不光 要检查冷却水管有无漏水,还要 检查模芯、模芯与模框之间、浇 口套、浇口套与模框之间有无漏 水,如发现有漏水,应及时上报;
Home
喷涂
• 喷涂后吹气
现车间有很多员工认为:模具温度这么高,喷的脱模剂到模具上 很快就蒸发掉了,不用吹气了,其实这种观点是不对的,喷涂后 吹气目的,是减少多余的脱模剂留在模具型腔内,也就减少模具 型腔内脱模剂挥发而产生的气体。
压铸常识知识点总结
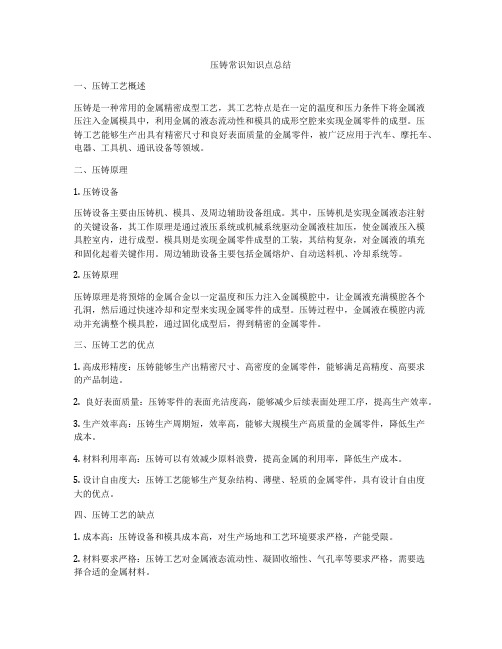
压铸常识知识点总结一、压铸工艺概述压铸是一种常用的金属精密成型工艺,其工艺特点是在一定的温度和压力条件下将金属液压注入金属模具中,利用金属的液态流动性和模具的成形空腔来实现金属零件的成型。
压铸工艺能够生产出具有精密尺寸和良好表面质量的金属零件,被广泛应用于汽车、摩托车、电器、工具机、通讯设备等领域。
二、压铸原理1. 压铸设备压铸设备主要由压铸机、模具、及周边辅助设备组成。
其中,压铸机是实现金属液态注射的关键设备,其工作原理是通过液压系统或机械系统驱动金属液柱加压,使金属液压入模具腔室内,进行成型。
模具则是实现金属零件成型的工装,其结构复杂,对金属液的填充和固化起着关键作用。
周边辅助设备主要包括金属熔炉、自动送料机、冷却系统等。
2. 压铸原理压铸原理是将预熔的金属合金以一定温度和压力注入金属模腔中,让金属液充满模腔各个孔洞,然后通过快速冷却和定型来实现金属零件的成型。
压铸过程中,金属液在模腔内流动并充满整个模具腔,通过固化成型后,得到精密的金属零件。
三、压铸工艺的优点1. 高成形精度:压铸能够生产出精密尺寸、高密度的金属零件,能够满足高精度、高要求的产品制造。
2. 良好表面质量:压铸零件的表面光洁度高,能够减少后续表面处理工序,提高生产效率。
3. 生产效率高:压铸生产周期短,效率高,能够大规模生产高质量的金属零件,降低生产成本。
4. 材料利用率高:压铸可以有效减少原料浪费,提高金属的利用率,降低生产成本。
5. 设计自由度大:压铸工艺能够生产复杂结构、薄壁、轻质的金属零件,具有设计自由度大的优点。
四、压铸工艺的缺点1. 成本高:压铸设备和模具成本高,对生产场地和工艺环境要求严格,产能受限。
2. 材料要求严格:压铸工艺对金属液态流动性、凝固收缩性、气孔率等要求严格,需要选择合适的金属材料。
3. 零件后处理工艺复杂:压铸后的零件可能需要进行除毛刺、研磨、喷漆等后处理工序,工艺复杂。
4. 高能耗:压铸过程需要耗费大量能源,对环境污染和能源消耗都有一定影响。
压铸知识培训资料
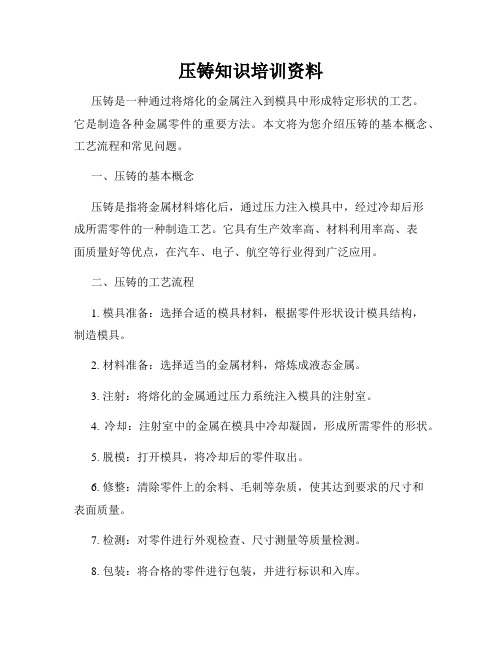
压铸知识培训资料压铸是一种通过将熔化的金属注入到模具中形成特定形状的工艺。
它是制造各种金属零件的重要方法。
本文将为您介绍压铸的基本概念、工艺流程和常见问题。
一、压铸的基本概念压铸是指将金属材料熔化后,通过压力注入模具中,经过冷却后形成所需零件的一种制造工艺。
它具有生产效率高、材料利用率高、表面质量好等优点,在汽车、电子、航空等行业得到广泛应用。
二、压铸的工艺流程1. 模具准备:选择合适的模具材料,根据零件形状设计模具结构,制造模具。
2. 材料准备:选择适当的金属材料,熔炼成液态金属。
3. 注射:将熔化的金属通过压力系统注入模具的注射室。
4. 冷却:注射室中的金属在模具中冷却凝固,形成所需零件的形状。
5. 脱模:打开模具,将冷却后的零件取出。
6. 修整:清除零件上的余料、毛刺等杂质,使其达到要求的尺寸和表面质量。
7. 检测:对零件进行外观检查、尺寸测量等质量检测。
8. 包装:将合格的零件进行包装,并进行标识和入库。
三、常见问题及解决方法1. 模具寿命短:可以采取优化模具结构、改进冷却系统、提高模具材料硬度等方法来延长模具寿命。
2. 压铸零件表面质量差:可以优化注射工艺参数、加强冷却控制、改善模具表面处理等方式来提高表面质量。
3. 冷却不均匀:可以采取优化冷却系统、调整注射参数、改变金属液态注入角度等方法来改善冷却效果。
4. 零件尺寸偏差大:可以优化模具结构、控制注射压力和速度、改进修整工艺等方法来减小尺寸偏差。
通过以上对压铸的基本概念、工艺流程和常见问题的介绍,相信您对压铸知识有了更深入的了解。
压铸技术在现代制造业中扮演着重要角色,掌握这门技术将对您的职业发展和工作效率带来积极的影响。
希望本文能够对您的压铸知识培训有所帮助。
(正文结束)。
压铸工艺与模具设计复习重点

压铸合金基本要求:过热温度不高时具有较好的流动性,便于填充复杂型腔,以获得表面质量良好的压铸件;线收缩率和裂纹倾向性小,以免压铸件产生裂纹,使压铸件有较高的尺寸精度;结晶温度范围小,防止压铸件产生过多的缩孔和缩松;具有一定的高温强度,以防止推出压铸件时产生变形或碎裂;在常温下有较高的强度,以适应大型薄壁复杂压铸件生产的需要;与型壁间产生物理化学作用的倾向性小,以减少粘膜和相互合金化;具有良好的加工性能和一定的抗蚀性。
压铸件尺寸偏差原因:合金本身化学成分的偏差,工作环境温度的高低,金属收缩率的波动,开魔盒抽芯以及推出机构运动状态的稳定程度,模具使用过程的磨损量引起的误差,压铸工艺参数的偏差,压铸机的精度和刚度引起的误差,模具的修理次数及使用期限。
胀型力:压铸过程中,在比压的作用下,金属液充填型腔时,给型腔壁和分型面一定的压力,增压建压时间:金属液在冲模的增压阶段,从充满型腔的瞬时开始至达到预定增压压力所需的时间。
持压时间:金属液充满型腔到凝固之前 增压比压持续的时间。
留模时间:持压时间终了到开模推出压铸件的时间。
压室充满度:浇入压室的金属液占压室容量的百分数。
设计压铸模除了应查阅压铸机的基本参数外还应考虑压铸机的基本结构与压铸模设计相关的内容:压铸机的模具安装尺寸,立式冷室压铸机喷嘴的规格尺寸,卧式冷室压铸机压室的凸台规格尺寸,安装液压抽芯器的支架和连接型芯用的接合器的规格尺寸。
压铸模设计前的必要准备:一:根据产品图对所选用的压铸合金、压铸件的形状、结构、精度和技术要求进行工艺性分析确定机械加工部位加工余量和机械加工时所要采取的工艺措施以及定位基准;二:根据产品图和生产纲领确定压射比压计算锁模力估算压铸件所需要的开模力和推出力以及压铸机的开模距离选定压铸机的型号和规格 三:根据产品图和压铸机的型号规格,对模具结构进行初步分析。
四:绘制压铸件的毛坯图。
压铸模应满足的要求:能获得符合图样要求的压铸件;能适应压铸生产的各种工艺要求并在保证质量和安全生产的前提下尽量采用先进和简单的模具结构;模具所有零件都应满足各自的机械加工工艺和热处理工艺要求;模具构件的刚性良好模具零件间的配合精度选用合理模具造价低廉;浇注系统设计和计算是压铸模设计中一项十分重要的工作,应引起高度重视;在条件许可时压铸件应尽可能实现标准化以缩短设计和制造周期方便管理。
压铸工艺及模具复习题

压铸工艺及模具复习题压铸工艺及模具复习题一、压铸工艺概述压铸工艺是一种常用的金属加工方法,通过将熔融金属注入模具中,在高压下快速凝固形成所需的零件。
压铸工艺具有高效、精确、复杂零件成型等优点,被广泛应用于汽车、航空航天、电子等领域。
二、压铸模具的组成1. 模具基座:支撑模具的主体结构,通常由钢板焊接而成。
2. 上模板:与下模板配合,用于固定模具芯和冷却系统。
3. 下模板:与上模板配合,用于固定模具腔和冷却系统。
4. 模具芯:用于形成零件的内部结构,通常由钢材制成。
5. 模具腔:用于形成零件的外部形状,通常由钢材制成。
6. 冷却系统:用于控制模具温度,提高生产效率和零件质量。
三、压铸工艺的步骤1. 准备工作:包括模具清洁、涂抹模具释放剂等。
2. 熔炼金属:将所需金属加热至熔点,保持一定温度。
3. 注入模具:将熔融金属注入模具腔中,保持一定压力和时间。
4. 冷却固化:待金属在模具中冷却凝固,形成所需零件。
5. 模具开启:将上下模板分离,取出成品零件。
6. 清理模具:清除模具中的残留物,准备下一次生产。
四、模具设计要点1. 零件结构:根据零件的功能和形状,合理设计模具腔和模具芯。
2. 浇口设计:确定合适的浇口位置和形状,以保证金属充填顺畅。
3. 冷却系统设计:合理布置冷却通道,控制模具温度,提高生产效率。
4. 排气系统设计:确保模具内部的气体能够顺利排出,避免气孔等缺陷。
5. 模具材料选择:根据零件材料和使用要求,选择合适的模具材料。
五、模具制造工艺1. 模具加工:根据设计要求,进行车削、铣削、磨削等工艺,制造模具零件。
2. 模具装配:将模具零件进行组装,包括上下模板、模具芯、模具腔等。
3. 模具调试:对装配好的模具进行调试,确保模具的准确性和稳定性。
4. 模具修磨:根据模具使用情况,定期对模具进行修磨,保持其精度和寿命。
六、模具故障及处理方法1. 模具磨损:定期对模具进行修磨,恢复其几何形状和表面质量。
压铸工艺理论概述学习知识

压铸工艺理论概述学习知识一.压铸是压力铸造的简称,其实质量将熔融或半熔融金属注入压铸机的压室,随后在高压作用下,以极高的速度充填压铸型腔,并在压力作用下使其迅速冷却凝固成型的精密铸方法之一。
二.压铸工艺特点:A) 优点:(1)可以制造形状复杂,轮廓清晰,薄壁深腔的金属零件。
(2)压铸件尺寸精度较高。
(3)材料利用率高。
(4)可将其它材料嵌件直接嵌铸在压铸件上。
(5)铸件组织致密,具有较高的强度和硬度。
(6)可以实现自动化生产。
B) 缺点:(1)由于高速充填,快速冷却,型腔中气体来不及排出,致使压铸件常有气孔及氧化夹杂物存在从而降低了压铸件质量。
(2)压铸机及压铸模费用昂贵,不适合小批量生产。
(3)压铸件尺寸受到限制。
(4)压铸合金种类受限制。
三.压铸过程简述:1 ↓ 涂 料↓ 模 喷(刷)压 开→ 具 → 合 模 →铸 →模 → 预 成取 热 浇 注 型件↓ 5 保 温 4 2四.典型的压铸填充理论:(一).金属的填充理论:压铸过程中金属液的填充形态与铸件致密度、气孔率、力学性能、表面粗糙度等质量因素密切相关,在极短的填充瞬间它受到压铸件结构、填充速度、比压、温度、内浇口与压铸件断面厚度之比、合金液的粘度及表面张力、浇注系统的形状等制约。
长期以来人们对它进行了广泛的研究,提出了一些论点,但这些论点都是在特定的试验条件下得到的,有一定局限性,要求人们在应用中具体情况具体分析,使填充理论进一步完善和深化。
金属填充理论归纳起来有如下三种:1.喷射填充理论:当液流在速度、压力不变时,保持内浇口截面的形状喷射至对面型壁,称为喷射阶段;由于对面型壁的阻碍,部分金属呈涡流状态返回,部分金属向所有其他方向喷溅并沿型腔壁由四面向内浇口方向折回,称为涡流阶段。
涡流中容易卷入空气及涂料燃烧产生的气体,使压铸件凝回后形成0.1∽1米的孔洞,降低了压铸件的致密度。
当内浇口截面积S与型腔截面积A之比S/A>(1/3∽1/4)和内浇口速度为0.5∽15米/S,且撞击型腔壁或液流遇到阻碍时容易产生喷射填充。
《压铸工艺及模具》期末知识点总结

1·高压力和高速度是压住时熔融合金充填成形过程的两大特点。
2·压铸的特点,优点:1、压铸件的尺寸精度高,表面粗糙度值第。
2、材料利用率高。
3、可以制造形状复杂、轮廓清晰、薄壁深腔的金属零件。
4、在压铸件上可以直接镶嵌其他材料的零件,以节省闺中材料的加工工时。
5、压铸件组织致密,具有较高的强度和硬度。
6、生产效率高。
缺点:1、压铸件常有气孔及氧化夹杂物存在。
2、不适合小批量生产。
3、压铸件尺寸受到限制。
4、压铸合金种类受到限制。
3·压射比压是压室内金属液在单位面积上所受的压力。
4·压铸过程:1、慢速封孔阶段。
2、充填阶段。
3、增压阶段4、持压阶段。
5·压力峰时间和原因:1、充填阶段压射冲头作用下,液体金属完全充满压室至浇道外的空间,并由于内浇道处的阻力而出现小的峰压。
2、增压阶段,充填结束时,液体金属停止流动,由于动能转变为冲击力,压力急剧上升,并由于增压器开始工作,使压力上升到最高值,时间极短,称为增压建压时间。
6·压铸速度有压射速度和充填速度两个不同概念。
压射速度是指压铸机压射缸内的液压推动压射冲头前进的速度;充填速度是指液体金属在压力作用下,通过内浇道进入型腔的线速度。
7·典型的金属充填理论:喷射充填理论、全壁厚充填理论、三阶段充填理论。
8·压铸合金的分类及主要性质:锌合金:压铸性能很好,填充成形容易,结晶温度范围小、不易产生疏松,浇注温度较低、模具使用寿命较长,不易粘附内壁,不腐蚀模具,但有老化现象和尺寸变化问题。
铝合金,铜合金(略)。
镁合金的特点:1、密度最小。
2、有很高的比强度。
3、良好的刚度和减振性,可减少噪声传递。
4、良好的力学性能。
5、优良的脱模性能。
6、成分和尺寸的稳定性较好,良好的切削性能。
7、极高的氧化性,极易氧化。
9·压铸机分类:按压室浇注方式(冷压室压铸机、热压室压铸机)、按压室的结构和布置方式(卧式压铸机,立式压铸机)10·卧式冷室压铸机的特点:1、金属液进入型腔转折少,压力损耗小,有利于发挥增压机机构的作用。
压铸模具基础知识

(19) 分流锥:
调整直浇道的截面积,改变金属液流向,减少金属液消 耗量。内部设有冷却系统。
材料:H13、SKD61 热处理: HRC43~47
(20) 垫块: 对模具起支承作用,提高后模刚性,减
少生产时由机器冲击波而引的模具瞬间变形制作材料为普 通铸铁或45#钢。位置和尺寸的控制是关键
材料: T8A、T10A、40cr 热处理: HRC 42~47
(5).滑块
作用: 连结型芯和斜销配合作抽芯运动的组件,和斜销配 合 共同完 成抽芯动作。
参数: 滑块的高度B ,宽度C按型芯尺寸决定,.滑块的长 度A与B, C有关,为使滑块工作时稳定要求 A≥0.7C A≥B
材料: T8A、T10A、H13 热处理: HRC 42~47
合金压铸模
压铸模具基础知识
前言
压铸:高温融熔金属液,在高速 高压状态下以一 定的条件快速充填型腔,并在一定压力作 用下快速冷却过程。
压铸模是压铸生产中重要的工艺装备,它对生产能否 顺利进行,铸件质量的优劣起着极为重要作用,它与 压铸生产工艺、生产操作存在着又互相影响互为制约, 关系极密切系。
在压铸机中板上,随中板作并合运动,与定模部分
分开合拢。一般抽芯机构和顶出机构大多在这个部
分。
抽芯机构:
作用: 抽动与开模方向运动不一致成型零件的 活动型芯机构。
抽芯机构主要包括:斜导柱、侧面型芯、滑块、 导 滑槽、限位块、螺杆、弹簧、螺母、螺 钉等部分组成。如下图所示。
(3).斜销
溢流槽
溢流槽的结构形式: (1)布置在模具分型面上的溢流槽 (2)布置在模具型腔内部的溢流槽。 其形式有: 杆形溢流槽 管形溢流槽 环形溢流槽 双级溢流槽 波纹状溢流槽
压铸工艺总结知识点

压铸工艺与模具设计期末考试重点知识点与复习题1、压铸过程循环图:清理模具-喷刷涂料-合模-浇料-压射-凝固-开模-推出-取出铸件。
2、金属填充理论有三种:喷射填充理论、全壁厚填充理论、三阶段填充理论。
3、熔点较低的锌、铝、镁和铜合金为常用的压铸合金。
4、常用压铸铝合金的代号:铝硅合金:ZL101,Y102,ZL103,Y104,ZL105铝镁合金:ZL301,Y302铝锌合金:Y4015、压铸合金与压铸机的选择?铝合金:采用立式冷室压铸机,锌合金:主要采用热室压铸机,镁合金:既可以采用热室压铸机,也可以采用冷室压铸机,铜合金:只采用冷室压铸机6、压铸件的壁厚对铸件质量有何影响?1)薄壁压铸件的致密性好,可相对提高强度和耐磨性2)壁厚增加,内部气孔、缩孔也随之增加,应尽量减小并保持均匀3)太厚质量不好,太薄金属填充不良,铸件成型困难合理的壁厚取决于压铸件的具体结构、合金的性能、并与压铸工艺参数有着密切关系,通常以薄壁和均匀壁厚为佳。
7、压铸件上可以压铸出孔和槽的最小尺寸及深度,受到一定的限制,与形成孔和槽的型芯在型腔中的分布位置有关。
压铸孔和槽的最小尺寸及其深度除受到一定的限制外,在深度方向应带有一定的铸造斜度以便抽芯。
8、分析题:P24-P27其中有两个图要考,判断哪个正确,说明为什么合理?9、压射力:是压铸机压射机构推动压射活塞的力,它来源于高压泵,可以压射压力和压射比压来表示。
压射比压:是压室内金属液在单位面积上所受的压力。
选择压射比压要考虑哪些因素?高的压射比压能提高铸件的致密性,过高的比压会导致粘模应该考虑:1)铸件结构特性(壁厚、形状复杂程度、工艺合理性);2)压铸合金特性(结晶温度范围、流动性、密度、比强度);3)浇道系统(浇道阻力、浇道散热速度);4)排溢系统(排气道布局、排气道截面积);5)内浇道速度;6)温度(合金与压铸模的温度差)选填充速度时:厚壁件高压低速;薄壁件高压高速10、胀型力:压铸过程中,在比压的作用下,金属液充填型腔时,给型腔壁和分型面一定的压力Fz=pbA Fz—模具分型面上的胀型力; pb—压射比压; A—压铸件、浇口和排溢系统在分型面上投影面积总和11、压铸是压力铸造的简称。
压铸工艺及模具设计复习重点考试必过神器
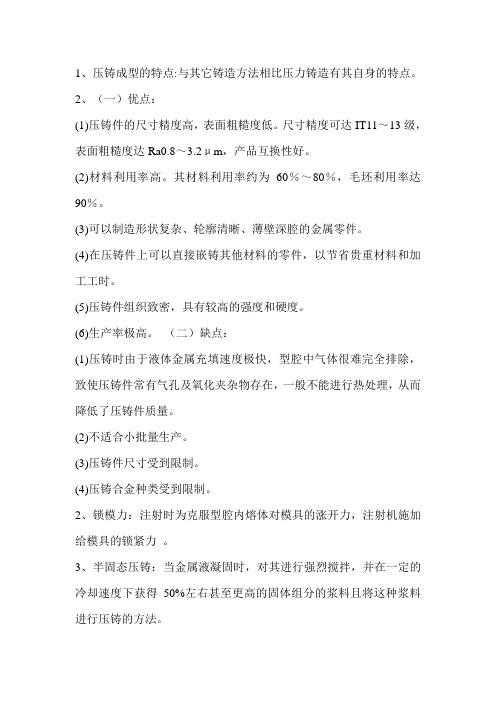
1、压铸成型的特点:与其它铸造方法相比压力铸造有其自身的特点。
2、(一)优点:(1)压铸件的尺寸精度高,表面粗糙度低。
尺寸精度可达IT11~13级,表面粗糙度达Ra0.8~3.2μm,产品互换性好。
(2)材料利用率高。
其材料利用率约为60%~80%,毛坯利用率达90%。
(3)可以制造形状复杂、轮廓清晰、薄壁深腔的金属零件。
(4)在压铸件上可以直接嵌铸其他材料的零件,以节省贵重材料和加工工时。
(5)压铸件组织致密,具有较高的强度和硬度。
(6)生产率极高。
(二)缺点:(1)压铸时由于液体金属充填速度极快,型腔中气体很难完全排除,致使压铸件常有气孔及氧化夹杂物存在,一般不能进行热处理,从而降低了压铸件质量。
(2)不适合小批量生产。
(3)压铸件尺寸受到限制。
(4)压铸合金种类受到限制。
2、锁模力:注射时为克服型腔内熔体对模具的涨开力,注射机施加给模具的锁紧力。
3、半固态压铸:当金属液凝固时,对其进行强烈搅拌,并在一定的冷却速度下获得50%左右甚至更高的固体组分的浆料且将这种浆料进行压铸的方法。
4、流变压铸法:将半固态的金属浆料直接压射到行腔形成压铸件的方法。
5、搅溶压铸法:是将半固态浆料预先制成一定大小的锭块,需要时再重新加热到半固态温度,然后进入压室进行压铸,称为搅溶压铸。
6、胀型力:压铸过程中,填充结束并转为增压阶段时,作用于正在凝固的金属上的比压(增压比压),通过金属(铸件浇注系统,排溢系统)传递型腔壁面,此压力称为胀型力。
7、压力铸造:压力铸造是将熔融状态或者半熔融状态的金属浇入压铸机的压室,在高压力的作用下,以极高的速度充填在压铸模(压铸型)的型腔内,并在高压下使熔融或者半熔融的金属冷却凝固成形而获得铸件的高效益、高效率的精密铸造方法。
8、压射压力:压射压力Fy是压射机构(压射缸内压射活塞)推动压室冲头运动的力,即压射冲头作用于压室中金属液面上的力。
9、压射速度:即压室内压射冲头推动金属液的移动速度(又称冲头速度)10、内浇口速度:是指金属液通过内浇口时的线速度(又称充填速度)11、合金浇注温度:是指金属液从压室进入型腔的平均温度,因测量不便,通常以保温炉内的温度表示。
- 1、下载文档前请自行甄别文档内容的完整性,平台不提供额外的编辑、内容补充、找答案等附加服务。
- 2、"仅部分预览"的文档,不可在线预览部分如存在完整性等问题,可反馈申请退款(可完整预览的文档不适用该条件!)。
- 3、如文档侵犯您的权益,请联系客服反馈,我们会尽快为您处理(人工客服工作时间:9:00-18:30)。
《压铸工艺及模具》复习资料第一章绪论1、压铸:压铸是压力铸造的简称,其实质是在高压作用下,使液态或半液态金属以较高的速度充填压铸模型腔,并在压力下成形和凝固而获得铸件的方法。
(高压和高速是压铸时熔融合金充填成形的过程的两大特点)2、压铸压铸合金的优缺点优点:1)压铸件的尺寸精度高,表面粗糙度值低2)材料利用率高3)可以制造形状复杂、轮廓清晰、薄壁深腔的金属零件4)在压铸件上可以直接嵌铸其他材料的零件5)压铸件组织致密,具有较高的强度和硬度6)生产率极高缺点:1)压铸件常有气孔及氧化夹杂物存在2)不适合小批量生产3)压铸件尺寸受到限制4)压铸合金种类受到限制第二章压铸过程原理及常用压铸合金1、压铸压力:压射力:压铸机压射机构中推动活塞的力压射比压:压室内金属液在单位面积上所受的压力(压射比压变化的三个阶段:Ⅰ、慢速封孔阶段Ⅱ、充填阶段Ⅲ、增压阶段Ⅳ、持压阶段)2、压铸速度:压射速度:压铸机压射缸内的液压推动压射冲头前进的速度充填速度:液体金属在压力作用下,通过内浇道进入型腔的线速度3、三大充填理论:喷射充填理论、全壁厚充填理论、三阶段充填理论(巴顿认为充填过程的三个阶段对铸件质量所起的作用是不同的,第一阶段是铸件的表面质量;第二阶段是铸件的硬度;第三阶段是铸件的强度)4、常用的压铸合金:锌合金、铝合金(最常见)、镁合金、铜合金5、锌合金老化现象的原因:由于铅、锡、镉等杂质在锌中的溶解度过小,从而使这些杂质集中于晶粒边界造成晶间电化学腐蚀。
6、合金材料的性能包括使用性能和工艺性能7、压铸的合金应具有的性质1)高温下有足够的强度和可塑性,无热脆性;2)尽可能小的线收缩率和裂纹倾向,以免压铸件产生裂纹,使压铸件有较高的尺寸精度3)结晶温度范围小,防止压铸件产生过多的缩孔和疏松4)在过热温度不高时有足够的流动性,便于充填复杂型腔,以免获得表面质量良好的铸件5)与型壁产生物理化学作用的倾向小,以减小粘模和相互合金化第三章压铸机1、压铸机的分类按浇注方式分:热压室压铸机和冷压室压铸机冷压室压铸机按压室结构和布置方式又分卧式(应用最多)和立式还有全立式2、压铸机主要由开合模机构、压射机构、动力系统、控制系统等组成3、合模机构形式:液压合模机构、机械合模机构(机械合模机构可分为曲肘合模机构、各种形式的偏心机构、斜楔式机构等)图见书P24.254、锁模力定义:推动动模移动合拢并锁紧模具的力称为锁模力作用:为了克服反压力,以锁紧模具的分型面,防止金属液飞溅,保证铸件的尺寸精度。
5、压射机构作用:将金属液推送进模具型腔,填充成形为压铸件的机构组成部分:压室、压射冲头、压射杆、压射缸及增压器等。
6、现代压铸机的压射机构的主要特点是三级压射(慢速;快速;增压)7、书P28.29第四章压铸件结构设计及压铸工艺1、压铸工艺对压铸件结构的要求(图见书P30~32)(一)从简化模具结构、延长模具使用寿命考虑1、铸件的分型面上应尽量避免圆角2、避免模具局部过薄3、避免压铸件上互相交叉不通孔4、避免内侧凹(二)改进模具结构,减少抽芯部位(三)方便压铸件脱模和抽芯2、压铸件基本结构:壁厚和肋;铸造圆角;脱模斜度;铸孔;压铸镶嵌件(详见书P32~35)3、压铸工艺参数的选择:压铸压力的选择;压铸速度的选择;温度参数的选择;充填、持压和开模时间4、温度参数:浇注温度:从压室进入型腔时液体金属的平均温度压铸模温度:压铸模使用前预热的温度(预热的作用:避免“热冲击”以延长寿命和避免因激冷失去流动性)5、压铸涂料的作用1)高温时保持良好的润滑性能2)减少模具的导热率,保持熔融金属的流动性,从而改善金属的成形性3)保护模具,避免熔融金属对模具的冲刷作用,改善模具工作条件,延长模具使用寿命4)预防粘模(对铝、锌合金而言5)减少铸件与模具成型部分之间的摩擦,从而减少型芯和型腔被磨损并提高铸件表面质量6、压铸件的清理、浸渗、后处理和表面处理压铸件的清理:包括取出浇口、排气槽、溢流槽、飞边和毛刺等;多采用普通多角滚筒和振动埋入式清理装置压铸件的浸渗:压铸件内部缺陷如气孔、针孔、或疏松等,可加入密封剂(浸渗剂)使其具有耐压性(气密性、防水性);常用方法是真空加压法压铸件的后处理:主要是指时效退火和负温时效处理7、半固态压铸的特点1)减少了对压室、压铸型腔和压铸机组成部件的热冲击,因而可以提高压铸模的使用寿命2)由于半固态收缩,所以铸件不易出现疏松、缩孔,故提高了铸件质量3)半固态压铸对薄壁件能良好充模,并可改善铸件表面质量4)节约金属和能量,同时可以改善工作环境,生产率也得到提高8、半固态压铸成形的方法:流变压铸和触变压铸(常见)9、半固态合金的制备方法:机械搅拌法;电磁搅拌法;应变激活法10、其他压铸工艺:真空压铸、充氧压铸、精速密压铸、黑色金属压铸第五章压铸模的基本结构及分型面设计1、压铸模由动模和定模两大部分组成2、压铸模的基本结构(图见书P60)成型零件;浇注系统;溢流、排气系统、模架3、分型面的类型:平直分型面;倾斜分型面;阶梯分型面;曲面分型面(图见书P61)4、分型面选择的基本原则:1)尽可能地使压铸件在开模后留在动模部分2)有利于浇注系统、溢流排气系统的布置3)保证压铸件的尺寸精度和表面质量4)简化模具结构、便于模具加工5)避免压铸机承受临界载荷6)考虑压铸合金的性能第六章浇注系统及溢流、排气系统设计1、浇注系统的结构:主要由直浇道、横浇道、内浇道和余料等部分组成。
(图见书P66)2、浇注系统的分类:一般可分为侧浇道;中心浇道;直接浇道;环形浇道;缝隙浇道;点浇道等浇注系统3、溢流槽的作用1)排除型腔中的气体,储存混有气体和涂料残渣的前流冷污金属液2)控制金属液的流动状态,防止局部产生涡流3)调节模具的温度场分布,改善模具的热平衡状态4)作为压铸件脱模时推杆推出的位置,防止压铸件变形,避免在压铸件表面留有推杆痕迹5)作为压铸件存放、运输及加工时的支承、吊挂、装夹或定位的附加部分4、溢流槽的结构形式:设置在分型面上的溢流槽;设置在型腔内的溢流槽5、排气槽的结构形式:分型面上排气槽的结构形式;利用型芯和推杆间隙设置排气槽的结构形式第七章 成型零件和模架设计1、压铸模成型零件的结构可分为整体式和镶拼式2、整体式结构:优点:模具结构简单;外形尺寸;强度刚度高;不易变形;压铸件表面光滑平整,没有镶拼的痕迹;便于开设冷却水道缺点:适用于型腔较浅的小型单腔压铸模;生产形状较简单、精度要求不高、合金熔点较低的压铸件的模具;压铸件生产批量较小,可不进行热处理的压铸模3、镶拼式结构优点:对于复杂的型腔可以分块进行加工,简化加工工艺,提高模具制造质量,容易满足成型部位的精确要求;能合理使用模具钢,降低模具制造成本;有利于易损坏的更换和修理;更换部分镶块,即可改变压铸模型腔的局部结构,满足不同压铸件的需求;拼接处的适当间隙有利于型腔排气。
缺点:镶块拼合面过多时会增加装配的困难,且难以满足较高的组合尺寸精度;镶块拼合处的缝隙易产生飞边,既影响模具使用寿命,又会增加压铸件去毛刺的工作量;另外还会使模具的热扩散条件变差。
4、压铸件的收缩率(一)实际收缩率:压铸件的实际收缩率实ϕ是指室温下模具成型尺寸与压铸件实际尺寸的差值与模具成型尺寸之比,即%100⨯-=型实型实A A A ϕ(型A 是室温下模具的成型尺寸,实A 是室温下压铸件的实际尺寸)(二)计算收缩率:计算成型零件成型尺寸所采用的收缩率为计算收缩率ϕ,它包括了压铸件收缩值及模具成型零件在工作温度时的膨胀值,即%100'⨯-=AA A ϕ(A ’是计算得到模具成型零件的成型尺寸,A 是压铸件的公称尺寸)5、影响压铸件尺寸精度的主要因素1)压铸件收缩率的影响2)压铸件结构的影响3)模具成型零件制造偏差的影响4)模具成型零件磨损的影响5)压铸工艺参数的影响6、成型尺寸定义:成型零件中直接决定压铸件几何形状的尺寸称为成型尺寸分类:型腔尺寸;型芯尺寸;成型部分的中心距离和位置尺寸三类7、成型尺寸的计算(详见书P112~113)8、压铸模模架的基本结构(图见书P115)9、加热与冷却系统的主要作用使压铸模达到较好的热平衡状态和改善压铸件顺序凝固条件;提高压铸件内部质量和表面质量;稳定压铸件的尺寸精度;提高压铸生产效率;降低模具热交变应力,提高压铸件的使用寿命。
10、模具的加热方法:火焰加热;电加热装置加热;模具温度控制装置加热11、模具的冷却方法:水冷却;风冷却;用传热系数高的合金冷却;用热管冷却;用模具温度控制装置进行冷却第八章 压铸模机构设计1、常用的抽芯机构:机动抽芯;液压抽芯;其他抽芯机构(手动抽芯,活动镶块模外抽芯机构)2、抽芯距:型芯从成型位置抽至不妨碍铸件脱模的位置时,型芯和滑块在抽芯方向上所移动的距离3、影响抽芯力的主要因素1)成型部分表面积越大,所需抽芯力也越大;型芯断面的几何形状越复杂,抽芯力越大2)铸件侧面孔穴多且分布在同一抽芯机构上,因铸件的线收缩大,对型芯的包紧力,因此抽芯力也大3)铸件的成型部分壁较厚,金属冷却凝固的收缩变大,包紧力增加,抽芯力也增大4)活动型芯表面粗糙度值低,加工纹路与抽芯方向相同,可减少抽芯力5)加大活动型芯的脱模斜度,可减少抽芯力……(书P129)4、斜导柱抽芯机构的组成和工作原理(图见书P130){重点}弯销抽芯机构的组成和工作原理(图见书P139)斜滑块抽芯机构的组成和工作原理(图见书P143)5、推出机构的分类、组成分类:机动推出;液压推出;手动推出组成:推出元件、复位元件、限位元件、导向元件、结构元件6、脱模力(推出力):开始脱模的瞬间所需克服的阻力第九章压铸模使用材料的选择及技术要求1、对压铸模使用材料的要求1)具有良好的可锻性和切削性2)高温下具有较高的红硬性、高温强度、高温硬度、抗回火稳定性和冲击韧度3)具有良好的导热性和抗疲劳性4)具有足够的高温抗氧化性5)热膨胀系数小6)具有高的耐磨性和耐蚀性7)具有良好的淬透性和较小的热处理变形率。
----END----2016.6.21。