THE CATALYTIC EFFECT OF CARBONSUPPORTED
异丁烯水合制备叔丁醇
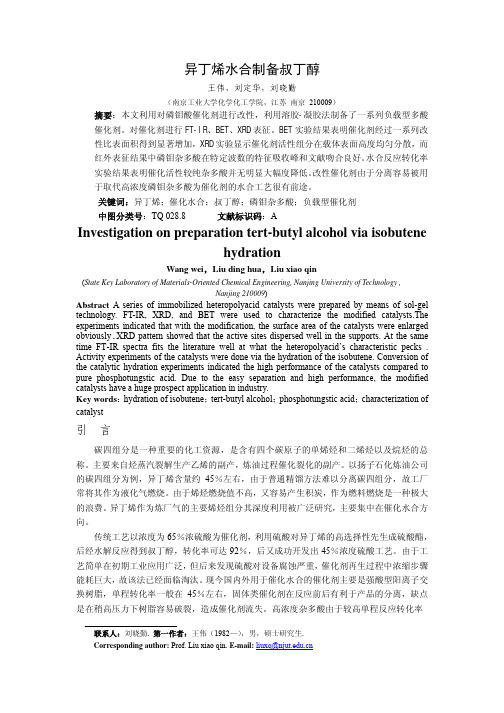
异丁烯水合制备叔丁醇王伟,刘定华,刘晓勤(南京工业大学化学化工学院,江苏南京 210009)摘要:本文利用对磷钼酸催化剂进行改性,利用溶胶-凝胶法制备了一系列负载型多酸催化剂。
对催化剂进行FT-IR、BET、XRD表征。
BET实验结果表明催化剂经过一系列改性比表面积得到显著增加,XRD实验显示催化剂活性组分在载体表面高度均匀分散,而红外表征结果中磷钼杂多酸在特定波数的特征吸收峰和文献吻合良好。
水合反应转化率实验结果表明催化活性较纯杂多酸并无明显大幅度降低。
改性催化剂由于分离容易被用于取代高浓度磷钼杂多酸为催化剂的水合工艺很有前途。
关键词:异丁烯;催化水合;叔丁醇;磷钼杂多酸;负载型催化剂中图分类号:TQ 028.8 文献标识码:AInvestigation on preparation tert-butyl alcohol via isobutenehydrationWang wei,Liu ding hua,Liu xiao qin(State Key Laboratory of Materials-Oriented Chemical Engineering, Nanjing University of Technology ,Nanjing 210009)Abstract A series of immobilized heteropolyacid catalysts were prepared by means of sol-gel technology. FT-IR, XRD, and BET were used to characterize the modified catalysts.The experiments indicated that with the modification, the surface area of the catalysts were enlarged obviously.XRD pattern showed that the active sites dispersed well in the supports. At the same time FT-IR spectra fits the literature well at what the heteropolyacid’s characteristic pecks . Activity experiments of the catalysts were done via the hydration of the isobutene. Conversion of the catalytic hydration experiments indicated the high performance of the catalysts compared to pure phosphotungstic acid. Due to the easy separation and high performance, the modified catalysts have a huge prospect application in industry.Key words:hydration of isobutene;tert-butyl alcohol;phosphotungstic acid;characterization of catalyst引言碳四组分是一种重要的化工资源,是含有四个碳原子的单烯烃和二烯烃以及烷烃的总称。
Catalytic Conversion of Carbon Dioxide into Fuel
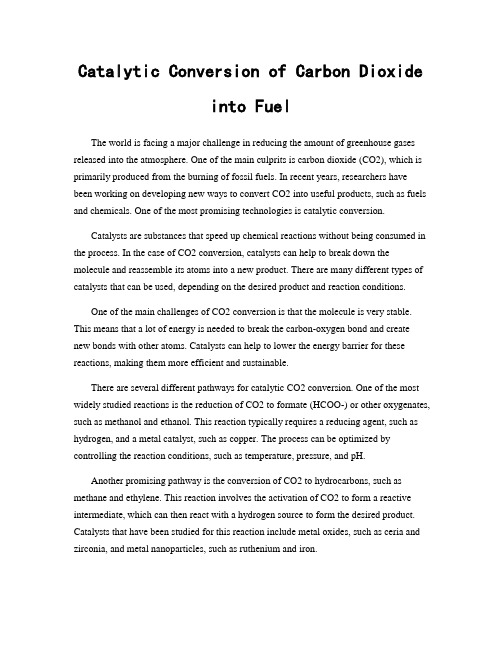
Catalytic Conversion of Carbon Dioxideinto FuelThe world is facing a major challenge in reducing the amount of greenhouse gases released into the atmosphere. One of the main culprits is carbon dioxide (CO2), which is primarily produced from the burning of fossil fuels. In recent years, researchers have been working on developing new ways to convert CO2 into useful products, such as fuels and chemicals. One of the most promising technologies is catalytic conversion.Catalysts are substances that speed up chemical reactions without being consumed in the process. In the case of CO2 conversion, catalysts can help to break down the molecule and reassemble its atoms into a new product. There are many different types of catalysts that can be used, depending on the desired product and reaction conditions.One of the main challenges of CO2 conversion is that the molecule is very stable. This means that a lot of energy is needed to break the carbon-oxygen bond and create new bonds with other atoms. Catalysts can help to lower the energy barrier for these reactions, making them more efficient and sustainable.There are several different pathways for catalytic CO2 conversion. One of the most widely studied reactions is the reduction of CO2 to formate (HCOO-) or other oxygenates, such as methanol and ethanol. This reaction typically requires a reducing agent, such as hydrogen, and a metal catalyst, such as copper. The process can be optimized by controlling the reaction conditions, such as temperature, pressure, and pH.Another promising pathway is the conversion of CO2 to hydrocarbons, such as methane and ethylene. This reaction involves the activation of CO2 to form a reactive intermediate, which can then react with a hydrogen source to form the desired product. Catalysts that have been studied for this reaction include metal oxides, such as ceria and zirconia, and metal nanoparticles, such as ruthenium and iron.One of the key advantages of catalytic CO2 conversion is that it can be integrated with renewable energy sources, such as solar and wind power. In this scenario, excess energy can be used to drive the reactions and produce fuels that can be stored and used when needed. This can help to improve the overall efficiency and sustainability of the energy system.Another advantage is that catalytic CO2 conversion can help to reduce the carbon footprint of industry. By capturing CO2 emissions and converting them into useful products, companies can reduce their reliance on fossil fuels and minimize their environmental impact. This can also help to create new business opportunities and drive innovation in the field.Despite the many benefits, there are still some challenges that need to be addressed when it comes to catalytic CO2 conversion. One of the main issues is scalability. Many of the reactions that have been studied are still in the laboratory stage and have not been scaled up to industrial levels. This requires significant investment in terms of equipment, infrastructure, and supply chain management.Another challenge is the cost of the catalysts. Many of the metals and other materials that are used as catalysts can be expensive and difficult to obtain. This can affect the overall economics of the process and make it less competitive compared to other carbon capture and storage (CCS) technologies.In conclusion, catalytic conversion of CO2 into fuel and other valuable products has the potential to be a game-changer in the fight against climate change. By using catalysts to accelerate reactions and lower energy requirements, the process can be made more efficient and sustainable. With further research and investment, we can unlock the full potential of this technology and create a cleaner, greener future.。
成人高考理科试卷英语
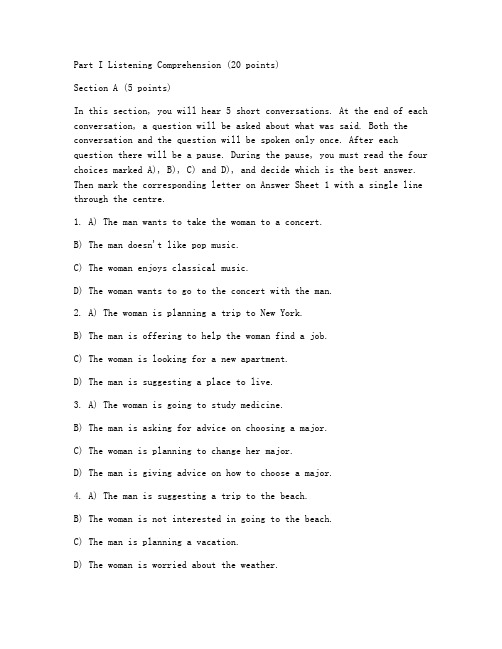
Part I Listening Comprehension (20 points)Section A (5 points)In this section, you will hear 5 short conversations. At the end of each conversation, a question will be asked about what was said. Both the conversation and the question will be spoken only once. After each question there will be a pause. During the pause, you must read the four choices marked A), B), C) and D), and decide which is the best answer. Then mark the corresponding letter on Answer Sheet 1 with a single line through the centre.1. A) The man wants to take the woman to a concert.B) The man doesn't like pop music.C) The woman enjoys classical music.D) The woman wants to go to the concert with the man.2. A) The woman is planning a trip to New York.B) The man is offering to help the woman find a job.C) The woman is looking for a new apartment.D) The man is suggesting a place to live.3. A) The woman is going to study medicine.B) The man is asking for advice on choosing a major.C) The woman is planning to change her major.D) The man is giving advice on how to choose a major.4. A) The man is suggesting a trip to the beach.B) The woman is not interested in going to the beach.C) The man is planning a vacation.D) The woman is worried about the weather.5. A) The man is making a suggestion for a new project.B) The woman is unsure about the project.C) The man is questioning the woman's decision.D) The woman is considering the man's suggestion.Section B (15 points)In this section, you will hear a passage three times. When the passage is read for the first time, you should listen carefully for its general idea. When the passage is read for the second time, you are required to fill in the blanks with the exact words you have just heard in each blank. For blanks 6-8, fill in the missing words. For blanks 9-15, complete the sentences with the information you have just heard.6. ___________ is the most important factor in learning a language.7. Regular practice is essential for ___________.8. The more you practice, the ___________ your speaking skills will become.9. ___________ is also a great way to improve your listening skills.10. ___________ can help you to understand the culture of the language you are learning.11. ___________ with native speakers can greatly improve your speaking skills.12. ___________ is another effective way to improve your language skills.13. ___________ in your own language can also help you to learn a new language.14. ___________ is the key to mastering a new language.15. ___________ is a lifelong process that requires constant practice and dedication.Part II Structure and Vocabulary (20 points)Section A (10 points)There are 10 incomplete sentences in this section. For each sentence there are four choices marked A), B), C) and D). Choose the one that best completes the sentence. Then mark the corresponding letter on Answer Sheet 1 with a single line through the centre.16. I wish I ___________ (go) to the party last night.A) had goneB) goC) wentD) am going17. If I ___________ (have) more time, I would travel to every country in the world.A) hadB) haveC) have hadD) had had18. She ___________ (be) in the classroom if she ___________ (not come) back from the library.A) must; hasB) must; hadC) would; hasD) would; had19. I ___________ (not see) him for years; I can't believe he's back.A) haven'tB) didn'tD) didn't have20. The teacher said that the exam would be postponed until next week because of the bad weather. We ___________ (be) so happy.A) areB) wereC) have beenD) had been21. He ___________ (not tell) me the truth because he was afraid of getting into trouble.A) hadB) wouldn'tC) didn'tD) didn't have22. The students were so excited that they ___________ (not stop) laughing.A) couldB) couldn'tC) wouldD) wouldn't23. If I ___________ (know) the answer, I would have told you.A) knewB) had knownC) would know24. I ___________ (not know) you if I ___________ (not meet) you at the party last night.A) didn't; hadn'tB) didn't; hadC) hadn't; hadD) hadn't; hadn't25. She ___________ (not do) her homework if she ___________ (be) at home.A) would; wasB) would; had beenC) had; wasD) had; had beenSection B (10 points)Complete the following sentences with the appropriate forms of the verbs in brackets.26. The teacher said that the students ___________ (be) in the classroom by 8:00 a.m.27. If I ___________ (be) you, I would take a different approach to the problem.28. They ___________ (not finish) the project by the end of the month.29. The plane ___________ (not take off) because of the heavy fog.30. The book ___________ (not be) written by the author himself.Part III Reading Comprehension (30 points)Section A (10 points)Read the following passage and answer the questions that follow.In recent years, there has been a growing concern about the negative effects of social media on young people. Many experts believe that excessive use of social media can lead to mental health issues, such as anxiety, depression, and low self-esteem. One of the main reasons forthis is the constant comparison with others that social media promotes. Young people often feel pressured to maintain a perfect image, which can lead to feelings of inadequacy.Another concern is the amount of time young people spend on social media. Many experts argue that excessive screen time can disrupt sleep patterns and affect physical health. Additionally, social media can be a sourceof cyberbullying, which can have severe consequences for young people's mental and emotional well-being.Despite these concerns, some experts believe that social media can also have positive effects. For example, it can be a platform for connecting with friends and family, as well as a source of information and support. However, it is important for young people to be aware of the potential risks and to use social media responsibly.31. What is one of the main reasons why social media can have a negative effect on young people's mental health?A) Excessive use of social mediaB) Constant comparison with othersC) Disruption of sleep patternsD) Cyberbullying32. According to the passage, what can be a positive effect of social media?A) Increased anxiety and depressionB) A platform for connecting with friends and familyC) Disruption of physical healthD) Cyberbullying33. What is the author's opinion on the potential risks of social media?A) Social media is entirely harmful.B) Social media has no negative effects.C) Social media can have both positive and negative effects.D) Social media is beneficial for young people.Section B (10 points)Read the following passage and answer the questions that follow.The Internet has revolutionized the way we communicate and access information. One of the most significant changes is the rise of e-commerce. E-commerce refers to the buying and selling of goods and services over the internet. This has led to a significant increase in online shopping, with more and more consumers choosing to make purchases online.There are several reasons for the growth of e-commerce. One of the main reasons is convenience. Online shopping allows consumers to shop fromthe comfort of their homes, saving them time and effort. Additionally, online stores often offer a wider range of products and better prices than traditional brick-and-mortar stores.However, there are also challenges associated with e-commerce. One ofthe biggest concerns is security. Consumers are worried about the safety of their personal and financial information when making online purchases. Another challenge is the lack of personal interaction, which can lead to dissatisfaction with the product or service.Despite these challenges, the growth of e-commerce is expected to continue. As technology continues to evolve, online shopping is likelyto become even more convenient and secure.34. What is one of the main reasons for the growth of e-commerce?A) Increased competitionB) ConvenienceC) Lack of personal interactionD) High prices35. What is one of the biggest concerns associated with e-commerce?A) Lack of personal interactionB) High pricesC) SecurityD) Increased competition36. According to the passage, what is expected to happen to e-commerce in the future?A) It will decline in popularity.B) It will become even more convenient and secure.C) It will face increased competition.D) It will become less popular among consumers.Section C (10 points)Read the following passage and answer the questions that follow.Climate change is one of the most pressing issues of our time. TheEarth's climate is changing at an unprecedented rate, primarily due to human activities. This has led to a variety of environmental problems, such as rising sea levels, extreme weather events, and the loss of biodiversity.One of the main causes of climate change is the burning of fossil fuels, which releases greenhouse gases into the atmosphere. These gases trap heat, leading to the warming of the planet. Another cause is deforestation, which reduces the number of trees that can absorb carbon dioxide from the atmosphere.To address the issue of climate change, governments and organizations around the world are implementing various strategies. One of the most effective strategies is the reduction of greenhouse gas emissions. This can be achieved through the adoption of renewable energy sources, such as solar and wind power, and the promotion of energy efficiency.37. What is one of the main causes of climate change?A) DeforestationB) The burning of fossil fuelsC) Increased carbon dioxide levelsD) Extreme weather events38. What is one of the strategies being implemented to address climate change?A) The use of nuclear powerB) The reduction of greenhouse gas emissionsC) The promotion of deforestationD) The elimination of all fossil fuels39. According to the passage, what is the expected outcome of implementing strategies to reduce greenhouse gas emissions?A) Increased sea levelsB) More extreme weather eventsC) A reduction in the number of treesD) A cooler planetPart IV Writing (20 points)Write an essay of about 200 words on the following topic:The Impact of Technology on EducationIn recent years, technology has had a significant impact on the field of education. Discuss the positive and negative effects of technology on education, and give your own opinion on whether technology has made education better or worse.。
铜-锑双金属合金高效电催化还原二氧化碳制乙烯
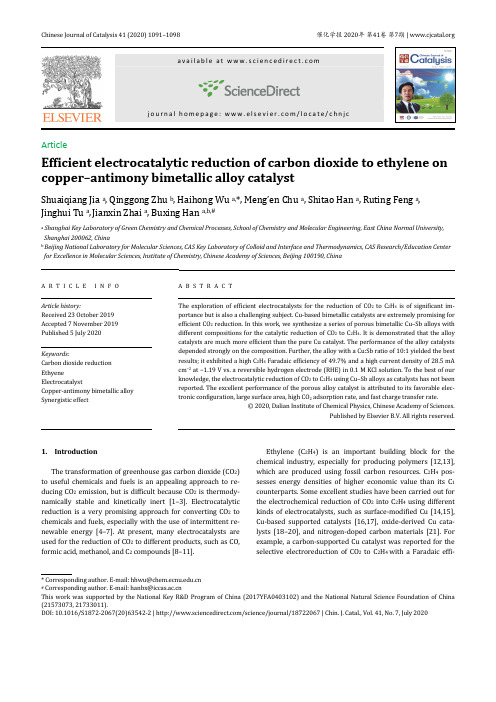
Chinese Journal of Catalysis 41 (2020) 1091–1098催化学报 2020年 第41卷 第7期 | a v a i l ab l e a t w w w.sc i e n c ed i re c t.c o mj o u r n a l h o m e p a g e : w w w.e l s e v i e r.c o m /l o c a t e /c h n j cArticleEfficient electrocatalytic reduction of carbon dioxide to ethylene on copper–antimony bimetallic alloy catalystShuaiqiang Jia a , Qinggong Zhu b , Haihong Wu a,*, Meng’en Chu a , Shitao Han a , Ruting Feng a , Jinghui Tu a , Jianxin Zhai a , Buxing Han a,b,#aShanghai Key Laboratory of Green Chemistry and Chemical Processes, School of Chemistry and Molecular Engineering, East China Normal University, Shanghai 200062, Chinab Beijing National Laboratory for Molecular Sciences, CAS Key Laboratory of Colloid and Interface and Thermodynamics, CAS Research/Education Center for Excellence in Molecular Sciences, Institute of Chemistry, Chinese Academy of Sciences, Beijing 100190, ChinaA R T I C L E I N F OA B S T R A C TArticle history:Received 23 October 2019 Accepted 7 November 2019 Published 5 July 2020The exploration of efficient electrocatalysts for the reduction of CO 2 to C 2H 4 is of significant im-portance but is also a challenging subject. Cu-based bimetallic catalysts are extremely promising for efficient CO 2 reduction. In this work, we synthesize a series of porous bimetallic Cu–Sb alloys with different compositions for the catalytic reduction of CO 2 to C 2H 4. It is demonstrated that the alloy catalysts are much more efficient than the pure Cu catalyst. The performance of the alloy catalysts depended strongly on the composition. Further, the alloy with a Cu:Sb ratio of 10:1 yielded the best results; it exhibited a high C 2H 4 Faradaic efficiency of 49.7% and a high current density of 28.5 mA cm −2 at −1.19 V vs. a reversible hydrogen electrode (RHE) in 0.1 M KCl solution. To the best of our knowledge, the electrocatalytic reduction of CO 2 to C 2H 4 using Cu–Sb alloys as catalysts has not been reported. The excellent performance of the porous alloy catalyst is attributed to its favorable elec-tronic configuration, large surface area, high CO 2 adsorption rate, and fast charge transfer rate.© 2020, Dalian Institute of Chemical Physics, Chinese Academy of Sciences.Published by Elsevier B.V. All rights reserved.Keywords:Carbon dioxide reduction EthyeneElectrocatalystCopper-antimony bimetallic alloy Synergistic effect1. IntroductionThe transformation of greenhouse gas carbon dioxide (CO 2) to useful chemicals and fuels is an appealing approach to re-ducing CO 2 emission, but is difficult because CO 2 is thermody-namically stable and kinetically inert [1–3]. Electrocatalytic reduction is a very promising approach for converting CO 2 to chemicals and fuels, especially with the use of intermittent re-newable energy [4–7]. At present, many electrocatalysts are used for the reduction of CO 2 to different products, such as CO, formic acid, methanol, and C 2 compounds [8–11].Ethylene (C 2H 4) is an important building block for the chemical industry, especially for producing polymers [12,13], which are produced using fossil carbon resources. C 2H 4 pos-sesses energy densities of higher economic value than its C 1 counterparts. Some excellent studies have been carried out for the electrochemical reduction of CO 2 into C 2H 4 using different kinds of electrocatalysts, such as surface-modified Cu [14,15], Cu-based supported catalysts [16,17], oxide-derived Cu cata-lysts [18–20], and nitrogen-doped carbon materials [21]. For example, a carbon-supported Cu catalyst was reported for the selective electroreduction of CO 2 to C 2H 4 with a Faradaic effi-* Corresponding author. E-mail: hhwu@ # Corresponding author. E-mail: hanbx@This work was supported by the National Key R&D Program of China (2017YFA0403102) and the National Natural Science Foundation of China (21573073, 21733011).DOI: 10.1016/S1872-2067(20)63542-2 | /science/journal/18722067 | Chin. J. Catal., Vol. 41, No. 7, July 20201092Shuaiqiang Jia et al. / Chinese Journal of Catalysis 41 (2020) 1091–1098ciency (FE) of 45%, which was 2.3-fold the FE of electrodepos-ited smooth Cu film [16]. Furthermore, a nanometer-sized N-doped graphene quantum dot (NGQD) catalyst showed a C2H4 selectivity of 30% [21]. Although progress is impressive, it is still quite desirable to design highly active and robust elec-trocatalysts that generate C2H4with high current density and selectivity.Recently, Cu-based binary alloys have attracted great atten-tion for their CO2 reduction reaction (CO2RR), as their electron-ic structure and binding energy can be easily modified by add-ing a second metal. This leads to a remarkable enhancement in catalytic activity with respect to different products [22,23]. Some excellent studies have also been carried out on this topic. For example, it was reported that CO2 could be reduced to C2H4 on Ag/Cu nanocrystals [24], with a selectivity of 40% in con-trast to the 12% selectivity obtained on a bulk Cu catalyst. In another study, a CuZn bimetallic catalyst was shown to reduce CO2 to C2H4 with an FE as high as 33.3% at −1.1 V vs. a reversi-ble hydrogen electrode (RHE) [25]. Furthermore, oxide-derived Cu x Zn catalysts have also been used to convert CO2 to C2H5OH with an FE of 29.1% [26]. These studies suggest that Cu-based binary alloys are promising catalysts for enhancing the selec-tivity of CO2RR toward multi-carbon products.In this work, we synthesized a range of bimetallic Cu–Sb al-loys with different compositions and porous morphology through a facile one-step process. The resulting Cu–Sb bimetal-lic alloy exhibited high selectivity toward C2H4 (∼50%) produc-tion at a relatively low applied potential (−1.19 V vs. RHE) with a high current density (28.5 mA cm−2). By combining material characterizations and a series of control experiments, we fur-ther confirmed that the enhanced selectivity toward C2H4 could be attributed to the synergistic effect of Cu and Sb, which pro-duced a higher CO2 adsorption rate and a larger surface area, and facilitated charge and mass transfer. As far as we know, this is the first work to use Cu–Sb alloys for the electrocatalytic reduction of CO2 to produce C2H4.2. Experimental2.1. MaterialsCopper(II) chloride (CuCl2·2H2O, Sinopharm Chemical Rea-gent Co., Ltd.), antimony trichloride (SbCl3, Shanghai Aladdin Biochemical Technology Co., Ltd.), sodium borohydride, sodi-um borohydride (NaBH4) (98%, Sinopharm Chemical Reagent Co., Ltd.), Toray Carbon Paper (CP, TGP-H-60, 19 cm × 19 cm), Nafion D-521 dispersion (5% w/w in water and 1-propanol, ≥ 0.92 meg/g exchange capacity), and Nafion N-117 membrane (0.180 mm thick, ≥ 0.90 meg/g exchange capacity) were pur-chased from Alfa Aesar China Co., Ltd. Both CO2 and N2 had a purity of 99.999%, and were provided by Shanghai Chemistry Industrial Zone Pujiang Special Type Gas Co., Ltd.2.2. Synthetic procedures for Cu–Sb alloysCu–Sb alloys were synthesized via the co-reduction of metal precursors through a facile one-step process using CuCl2·2H2O, SbCl3, and NaBH4as precursors [27,28]. In a typical prepara-tion, 3.5 mmol CuCl2·2H2O and 0.35 mmol SbCl3 were dissolved in 14 mL distilled water. The above solutions were injected into the NaBH4 solution (2.0 M, 20 mL) using the ethanol and H2O mixed solution, and the resulting mixture was stirred in an ice bath. After 4 h, the precipitate was obtained via centrifugation, and washed with 50 mL of water six times. It was then washed with 50 mL of acetone to remove the unreacted precursors and other possible byproducts. The powder was then dried at 60 °C overnight in a vacuum oven. The final product was obtained after cooling to room temperature. The powder was labeled Cu x–Sb y, where x and y represent the relative moles of CuCl2 and SbCl3.Alloys with different molar ratios of Cu to Sb, i.e., the Cu6–Sb1, Cu8–Sb1, Cu10–Sb1, Cu12–Sb1, and Cu15–Sb1 alloys, were prepared by adjusting the amount of precursor.2.3. CharacterizationThe morphology of the samples was characterized using a Hitachi S4800 scanning electron microscope (SEM) at 3 kV, and a FEI Tecnai G2 F30 transmission electron microscope (TEM) operated at 300 kV. A Rigaku Ultima VI X-ray diffractometer was employed to record the X-ray diffraction (XRD) patterns with a scanning speed of 5°/min between 10° and 90°. The diffractometer was operated at 35 kV and 40 mA with Cu Kαradiation. X-ray photoelectron spectroscopy (XPS) data were obtained using an AXIS Supra (XPS) surface analysis instru-ment with an X-ray monochromatic source (combined Al/Ag anode, energy 1486.6/2984.2 eV). The adsorption isotherms of CO2 were determined at 25 °C in the pressure range of 0–1 atm on BELSORP-max II equipment.2.4. Electrode preparationThe method for preparing the electrodes using a Cu–Sb alloy as the catalyst was similar to that used in previous reports [29,30]. Briefly, 6 mg catalyst was dispersed in 350 μL isopro-pyl alcohol and 30 μL Nafion solution (5 wt%) and was soni-cated for 30 min to obtain a homogenous catalyst ink. Then, 64 μL ink was dropped onto a carbon paper (1 × 1 cm2) surface using a micropipette. The electrode was then dried under room temperature. The amount of Cu–Sb catalyst on the electrode was 1 mg cm−2.2.5. Linear sweep voltammetry (LSV) and electrolysisElectrochemical measurements were performed in a gas-tight two-compartment H-cell separated by an ion ex-change membrane (Nafion117) in a three-electrode system ona potentiostat (CHI 660E, Shanghai CH Instruments Co., China).0.1 M KCl solution and 0.1 M KHCO3 solution were utilized as the cathodic and anodic electrolytes, respectively. LSV scans were conducted within a single compartment batch cell with a three-electrode configuration, which consisted of a working electrode, platinum gauze as the counter electrode, and Ag/AgCl (saturated KCl solution) as the reference electrode.Shuaiqiang Jia et al. / Chinese Journal of Catalysis 41 (2020) 1091–10981093Prior to the experiment, the electrolyte was purged with N2 or CO2for at least 30 min, and then the LSV measurement was carried out in the potential range of 0.0 V to –1.19 V vs. RHE at a scan rate of 20 mV s−1[31]. In all measurements, we used Ag/AgCl as the reference electrode, and the potential (vs. Ag/AgCl) was converted to RHE using the following equation [32]:E(RHE) =E(Ag/AgCl ) + 0.197 + 0.059 pH In the electrolysis experiment, the amount of electrolyte was 30 mL, and the electrolytes were bubbled with N2 or CO2 for at least 30 min to form an N2- or CO2-saturated solution. The reac-tion was performed at a constant potential. First, the cathode side was electrochemically reduced using cyclic voltammetry (CV), which ranged from 0 to −1.39 V vs. RHE at a rate of 0.1 V s−1for five cycles to completely reduce the possible oxidized species [33].2.6. Product analysisThe gaseous product was detected by a gas chromatograph (GC; Agilent-7890A) using a flame ionization detector (FID) for hydrocarbons and a thermal conductivity detector (TCD) for H2 and CO. The liquid product was quantified using a nuclear magnetic resonance (NMR) spectrometer (Bruker; Ascend 400–400 MHz) in DMSO-d6with phenol as an internal stand-ard. The gaseous product FE was calculated using:FE = t/Q total×100%where n is the number of electrons involved in the electrode reaction, F is the Faraday constant, A is the integral area of the gaseous product peak in GC, αis the conversion factor deter-mined from the calibration of the GC with standard samples, νis the CO2 inflow rate, t is the electrolytic time, and Q total is the total quantity of electric charge.2.7. Electrochemical active surface area (ECSA) measurementThe ECSA was determined from the capacitive current, which was measured with a double-layer (C dl) charging of the scan-rate dependence of CV (the potential windows were be-tween −0.78 V and −0.88 V vs. RHE). The C dl was estimated by plotting the Δj (j a – j c) at −0.83 V vs. RHE (0.1 M KCl solution) against the scan rates, where j a and j c were the anodic and ca-thodic current densities, respectively. The scan rates were 20, 40, 60, 80, 100, 120, 140, and 160 mV s−1. Briefly, the dou-ble-layer capacitance was measured by conducting CV in a po-tential range where no Faradaic processes occur, and hence the measured current was due to the non-Faradaic process of charging the electrochemical double layer. During the CV scans, the charging current j was linear to the scan rate ν, and the slope of the line was equal to the double-layer capacitance (C dl):C dl = Δj / ν, where the measuring unit of C dl was mF cm–2 [24].2.8. Electrochemical impedance spectroscopy (EIS)The experimental apparatus was the same as that used for the LSV measurements. The EIS measurement was carried out in CO2-saturated 0.1 M KCl solution at an open circuit potential (OCP) with frequencies that ranged from 0.01 Hz to 100 kHz, and the amplitude of the applied voltage was 5 mV. The data obtained from the EIS measurements were fitted by ZView® software (Version 2.9c, Scribner Associates, USA).3. Results and discussion3.1. Catalyst characterizationThe synthesis procedure for Cu–Sb alloys is schematically shown in Fig. 1a. Briefly, the Cu–Sb alloys were prepared through a facile one-step process using copper(II) chloride, antimony trichloride, and sodium borohydride as precursors. The Cu–Sb alloys were obtained after centrifuging and vacuum drying. In this study, we prepared Cu x–Sb y alloys with different Cu and Sb compositions, in which x and y represent the relative atomic numbers of Cu and Sb. The detailed discussion of the procedures for the alloy preparation is given in the experi-mental section.The characterization results of Cu–Sb alloys are shown in Fig. 1b–1e. The SEM images (Fig. 1b and 1c) of Cu and the Cu10–Sb1alloy reveal that porous nanoparticles on a scale of approximately 60 nm were formed. The higher magnification image (the inset) indicates that the particles were composed of small domains of about 5 nm, with numerous interfaces and junctions between them. The results also show that the surface of the Cu10–Sb1 alloy (Fig. 1c) was much rougher than that of pure Cu (Fig. 1b). The high-resolution TEM (HRTEM) imagesshow a polycrystalline structure in such Cu–Sb alloys (Fig. 1d Fig. 1. (a)Schematic illustration of the procedure for preparing Cu–Sb alloys; (b, c) SEM images of pure Cu and Cu10–Sb1, and (d, e) TEM imag-es of pure Cu and Cu10–Sb1; the inset images show pure Cu and the Cu10–Sb1 alloys at high magnification.1094 Shuaiqiang Jia et al. / Chinese Journal of Catalysis 41 (2020) 1091–1098and 1e), demonstrating that grain boundaries existed at the interface of the alloy [34–36]. The HRTEM image of the repre-sentative particle further shows spacings of 0.205 and 0.245 nm, corresponding to (110) plane of cubic Cu(I) oxide and the (111) plane of Cu(0) [37].The XRD patterns of Cu and Cu 10–Sb 1 are shown in Fig. 2. The results show that the Cu diffraction peaks of the (111), (200), and (220) facets and the Cu 2O diffraction peaks of the (110), (111), and (220) facets were present in the alloy sam-ples, indicating the formation of segregated pure metallic Cu and Cu 2O phase in the pure Cu and Cu 10–Sb 1 alloy. The XRD pattern of the Cu 10–Sb 1 alloy showed two distinct sets of dif-fraction peaks arising from the alloy structure of Sb and Cu, indicating the formation of Cu 10–Sb 1 alloy [38].XPS identified the valence states of Cu and Sb in the alloy. The peaks in the spectra indicate chemical binding energies of approximately 932.4, 531.3, and 530.5 eV, corresponding to Cu 2p , Sb 3d , and O 1s , respectively (Fig. 3a). The XPS spectra for Cu 2p 3/2, and for Sb 3d 5/2 and 3d 3/2 (Fig. 3b and Fig. S4) indicate the reduction to the Cu 0 and Sb 0 metallic states. The Cu LMM XAES characterization results of 913.7 eV with respect to Cu + while those reduced at 917.6 are donated by Cu 0 sites (Fig. 3b). The results are consistent with that of the XRD study [39–41]. Previous work has shown that the selectivity in CO 2 catalysis can be affected by the oxidized phase concentration in the sur-face region. With an increasing relative ratio of Cu + to Cu 0, the higher productivity of C 2+ species indicates that Cu + is needed to produce C 2+ products. Furthermore, other elements such as boron were not detected (Fig. 3c), suggesting that the reductant was not incorporated into the Cu–Sb alloys during the synthe-sis.The above results suggest the successful synthesis of Cu–Sb alloys with a porous morphology and nanostructured features. Notably, it can be seen in Fig. S4 that blue-shift occurred in the Cu–Sb alloys, which affected the charge transfer and intera-tomic interaction of the catalyst. Such a phenomenon allows the transformation of a local effect to a global effect, and thus im-pacts the catalytic behavior of the entire Cu domain when in-terfaced with the Sb domain by enhancing its intrinsic activity. The metallic Sb component of the Cu–Sb alloys resulted in changes in, and possibly the strengthening of the electronic interactions in the Cu–Sb alloys. Changes in electronic configu-rations may improve electrocatalytic performance [42]. 3.2. CO 2RR performances of Cu–Sb alloysAn LSV study was conducted to investigate the performanc-es of the Cu–Sb alloys in the potential range from 0.0 V to −1.19 V vs. RHE, and the results are shown in Fig. 4a. The current density over Cu 10–Sb 1 reached a high value of approximately 35.86 mA cm −2 at −1.19 V vs. RHE in CO 2-saturated 0.1 M KCl solution, and was higher than that over the pure Cu electrode, indicating higher activity for the Cu 10–Sb 1 alloy. In addition, the LSV curves using pure Cu and the Cu 10–Sb 1 alloy in N 2-saturated 0.1 M KCl solution were also determined, and the current density was much lower, demonstrating the reduction of CO 2 over the pure Cu and Cu 10–Sb 1 alloy electrodes, and the Cu 10–Sb 1 alloy electrode exhibited better performance for CO 2RR.Constant-potential electrolysis of CO 2 over Cu–Sb alloys was conducted at different applied potentials. After electrolysis at a controlled potential of –1.19 V vs. RHE for 3 h, the gas and liq-uid products were quantified using GC and 1H NMR, respec-tively. Fig. 4b shows the distribution of major CO 2RR products over Cu 10–Sb 1 at different potentials vs. RHE. H 2, CO, and C 2H 4 are the only gaseous products monitored by GC, and no liquid product was detected by NMR. As expected, C 2H 4 was the major2 Theta (degree)I n t e n s i t y (a .u .)Fig. 2. XRD patterns of pure Cu and Cu 10–Sb 1 alloys.Binding Energy (eV)Binding Energy (eV) 200196192188184180c Binding Energy (eV)B 1sFig. 3. (a) XPS survey spectrum; (b) Sb 3d XPS spectrum and Cu LMM Auger spectra; (c) B 1s XPS spectrum of Cu 10–Sb 1 alloys.Shuaiqiang Jia et al. / Chinese Journal of Catalysis 41 (2020) 1091–10981095product at the optimal potential. As the electrolytic potential increased, the FE of C 2H 4 first increased and then decreased. The FE of C 2H 4 reach 49.7% with a partial current density of 28.5 mA cm −2 at −1.19 V vs. RHE (Fig. 4b). The decrease in the FE of C 2H 4 at a high applied potential resulted from the en-hancement in the production rate of H 2 and CO. Fig. 4c and Fig. 4d show the FE and partial current density over the Cu–Sb al-loys with different compositions at the optimal applied poten-tials, respectively. It is evident that both the FE and the partial current density over the alloys were higher than that over the pure Cu and Sb catalysts. For pure Cu, the highest FE for C 2H 4 was only 15.8% (Fig. 4c). For pure Sb, the CO 2RR products were H 2 and CO (Fig. S2), a finding that was similar to that previously reported [43]. Fig. 4c shows that the FE was significantly influ-enced by the composition of the alloys. The Cu 10–Sb 1 alloy ex-hibited the best performance of all the catalysts, and showed a 3.3-fold FE enhancement for C 2H 4 compared with pure Cu of a similar size and shape.When the Sb content was small, the FE of C 2H 4 increased with the content of Sb. When the Sb content was larger than that in Cu 10–Sb 1, the FE decreased with further increases in the Sb content. At the same potential of −1.19 V vs. RHE, the partial current density of C 2H 4 over the other alloy catalysts was also lower than that over the Cu 10–Sb 1 alloy catalyst. These results indicate that the performance of the alloy catalysts could be tuned effectively by the atomic ratios of Cu and Sb in the alloys, suggesting a synergistic effect of Cu and Sb in catalyzing the CO 2 reduction. The surfaces of the Cu–Sb alloys give rise to steps and edges with low-coordinate metal atoms, which promote the adsorption of CO intermediates and facilitate their dimeri-zation to form C 2 products. The review of the literature that concerns C 2H 4 production is illustrated in Table S1. It shows that the Cu 10–Sb 1 alloy is among the most effective catalysts for C 2H 4 production.In addition, long-term electrolysis shows that the FE and current density showed no obvious change during the reduc-tion process (Fig. 4e). From the XRD spectra of Cu 10–Sb 1 after electrolysis (Fig. S1), it can be observed that the composition and structure of Cu 10–Sb 1 show no change. All these results illustrate the stability of Cu 10–Sb 1 under the reaction condi-tions.Electrolytes often play an important role in CO 2 electrore-duction [23]. Therefore, in addition to KCl aqueous electrolytes, we also used other electrolytes that contained different cations and anions to perform a reaction over the Cu 10–Sb 1 alloy. To study the effect of cations, chloride salts with different cations such as 0.1 M KCl, 0.1 M NaCl, and 0.1 M CsCl were used, and the results are illustrated in Fig. 5. The FE of the electrolytes followed the order of KCl > NaCl > CsCl. In the 0.1 M CsCl elec-trolyte, H 2 was the main product compared with KCl electro-lyte. To study the effect of anions, potassium salts with different anions were used, and the electrolysis results over the Cu 10–Sb 1 alloy catalyst are also provided in Fig. 5. 0.1 M K 2HPO 4 also showed excellent performance (40% FE), although it was lower than that of KCl. However, the FE in the 0.1 M KH 2PO 4 electro-lyte was very low when hydrogen was the main product. The102030400.0-0.2-0.4-0.6-0.8-1.0-1.2010203040 a CuPotential (V vs. RHE)C u r r e n t d e n s i t y (m A c m -2)CO 2N 2Cu 10Sb 1Potential (V vs. RHE)F a r a d a i c e f f i c i e n c y (%)C u r r e n t d e ns i t y (mA /c m 2)C 2H 4 F a r a d a i c e f f i c i e n c y (%)C u +S b C u 15-S b1C u 12-S b 1C u 10-S b 1C u 8-S b 1C u 7-S b 1C u 6-S b 1C u 5-S b 1P ur e C u Catalysts Potential (V vs. RHE)C 2H 4 F a r a d a i c e f f i c i e n c y (%)C u r r e n t d e n s i t y (m A c m -2)Time (h)Fig. 4. Electrochemical performances of the Cu–Sb alloy catalysts. (a) LSV curves for pure Cu and Cu 10–Sb 1 electrodes in CO 2 and N 2-saturated 0.1 M KCl electrolyte; (b) FE of the major products and total current densities over Cu 10–Sb 1 at different applied potentials; (c) FE for C 2H 4 over various elec-trocatalysts at −1.19 V vs. RHE; (d) Partial current densities of C 2H 4 at various applied potentials over various electrocatalysts; (e) FE and current densities for C 2H 4 production over Cu 10–Sb 1 electrode at −1.19 V vs. RHE within 4 h.1096 Shuaiqiang Jia et al. / Chinese Journal of Catalysis 41 (2020) 1091–1098above results indicate that both the cation and anion affected the electrochemical reaction, and KCl was the best electrolyte for generating C 2H 4 of all the electrolytes studied in this work. The local buffering capability of cations should increase the rate of any proton-transfer reaction. Therefore, the variation in the activity and selectivity of the CO 2RR reactions with the cat-ion was different. Similarly, the anions influence the reaction. The change in cation size, the pK a for cation hydrolysis, and the pH near the cathode lead to an increase in the local concentra-tion of dissolved CO 2. The consequences of these changes bring about a change in cathode activity, and a change in the FEs for H 2, CH 4, CO, and C 2H 4, in full agreement with the experimental observations of CO 2 reduction over Cu–Sb alloys [44,45].To gain further insights into the excellent performance of the catalysts, single-sweep polarography was used to study the electrochemically active surface area (ECSA) of the catalyst [46]. Based on the Randles–Sevcik equation, the reduction cur-rent density plotted against the square root of the scan rate is illustrated in Fig. 6a. According to the measured double-layer capacitance, Cu 10–Sb 1 has a larger electrochemical active sur-face area than that of pure Cu, which is beneficial to increasing the reduction rate.Electrochemical impedance spectroscopy (EIS) was also performed to provide the charge transfer rate at the elec-trode/electrolyte interface. The Nyquist plot was obtained by running the experiment at an OCP (Fig. 6b). A simple equivalent circuit R(C(RW)) was then used to fit the high and medium frequency data (Fig. 6b insert). The results indicated that the charge transfer resistance (R ct ) of the Cu 10Sb 1 alloy was much lower than that of the pure Cu. Therefore, the Sb in the Cu 10–Sb 1 alloy can improve CO 2 activation and enhance elec-tron transfer to CO 2 to form a reduced CO 2•− intermediate, which is vital for CO 2RR [47,48].In addition, the adsorption ability of CO 2 can also influence the performance of the catalysts for CO 2RR. Hence, we studied CO 2 adsorption over pure Cu and Cu 10–Sb 1 alloys. As shown in Fig. 6c, the CO 2 adsorption capacity of the Cu 10–Sb 1 alloy reached 3.89 cm 3 g –1, which was 1.55 times that of the pure Cu. The results indicated that the Cu 10–Sb 1 alloy could improve CO 2 adsorption capacity, which is favorable to CO 2 reduction.From the results above, we can discuss the main reasons for the excellent electrocatalytic performance of the Cu 10–Sb 1 alloy for CO 2 reduction. Firstly, the interaction of Cu and Sb in the Cu–Sb alloys changed the electronic configuration, which may modify the electrocatalytic properties of the catalyst. Secondly, the alloy had the largest electrochemical surface area and the lowest charge transfer resistance (Fig. 6a and 6b), which im-proves the activity and charge transfer rate [49]. Thirdly, the porous structure of the bimetallic alloy resulted in high acces-sibility of the active sites, and thus facilitated CO 2 adsorption and efficiency (Fig. 6c). Thus, the porous Cu 10–Sb 1 alloy pre-pared in this work was more efficient than pure Cu. 4. ConclusionsIn summary, we have synthesized Cu–Sb alloy electrocata-lysts with a porous morphology for the electrochemical reduc-tion of CO 2. Compared with pure Cu catalysts, the Cu–Sb alloys exhibited much higher activity and selectivity for the electro-reduction of CO 2 to C 2H 4 using 0.1 M KCl solution as the elec-trolyte. The Cu 10–Sb 1 alloys showed a 3.3-fold FE enhancement for C 2H 4 compared with pure Cu of a similar size and shape, andCs ClK ClNa ClK2HP O4F a r a d a i c e f f i c i e n c y (%)ElectrolytesK H2P O4Fig. 5. Product distribution of the Cu 10–Sb 1 alloy catalyst in different electrolytes at −1.19 V vs. RHE.j (m A c m -2)v 1/2(mV 1/2s -1/2)-Z '' (o h m )Z' (ohm)Relative pressure (P/P 0)G a s u p t a k e (c m 3g -1)Fig. 6. Characterizations of the electrochemical performance. (a) Charging current density at −1.19 V vs. RHE plotted against the square root of the scan rate over the Cu 10–Sb 1 alloy and pure Cu. (b) Nyquist plots of pure Cu and the Cu 10–Sb 1 alloy in CO 2-saturated 0.1 M KCl electrolyte; the inset is the electrical equivalent circuit used to simulated the experimental impedance data, and the components are solution resistance (R s ), electron transfer resistance (R ct ), double layer capacitance (C dl ), and Warburg-type impedance (Z w ). (c) Volumetric CO 2 adsorption-desorption isotherm of pure Cu and Cu 10–Sb 1 alloy; solid symbols represent adsorption curve, and hollow symbols represent desorption curve.。
一篇甲醇合成的外文文献原文
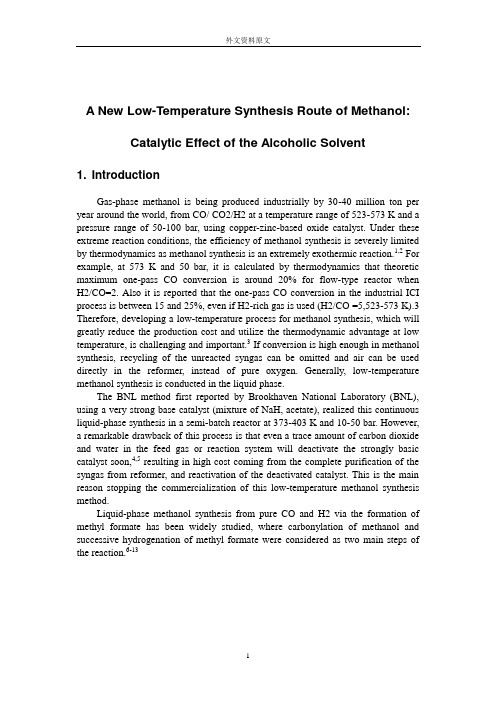
A New Low-Temperature Synthesis Route of Methanol:Catalytic Effect of the Alcoholic Solvent1. IntroductionGas-phase methanol is being produced industrially by 30-40 million ton per year around the world, from CO/ CO2/H2 at a temperature range of 523-573 K and a pressure range of 50-100 bar, using copper-zinc-based oxide catalyst. Under these extreme reaction conditions, the efficiency of methanol synthesis is severely limited by thermodynamics as methanol synthesis is an extremely exothermic reaction.1,2 For example, at 573 K and 50 bar, it is calculated by thermodynamics that theoretic maximum one-pass CO conversion is around 20% for flow-type reactor when H2/CO=2. Also it is reported that the one-pass CO conversion in the industrial ICI process is between 15 and 25%, even if H2-rich gas is used (H2/CO =5,523-573 K).3 Therefore, developing a low-temperature process for methanol synthesis, which will greatly reduce the production cost and utilize the thermodynamic advantage at low temperature, is challenging and important.3 If conversion is high enough in methanol synthesis, recycling of the unreacted syngas can be omitted and air can be used directly in the reformer, instead of pure oxygen. Generally, low-temperature methanol synthesis is conducted in the liquid phase.The BNL method first reported by Brookhaven National Laboratory (BNL), using a very strong base catalyst (mixture of NaH, acetate), realized this continuous liquid-phase synthesis in a semi-batch reactor at 373-403 K and 10-50 bar. However, a remarkable drawback of this process is that even a trace amount of carbon dioxide and water in the feed gas or reaction system will deactivate the strongly basic catalyst soon,4,5 resulting in high cost coming from the complete purification of the syngas from reformer, and reactivation of the deactivated catalyst. This is the main reason stopping the commercialization of this low-temperature methanol synthesis method.Liquid-phase methanol synthesis from pure CO and H2 via the formation of methyl formate has been widely studied, where carbonylation of methanol and successive hydrogenation of methyl formate were considered as two main steps of the reaction.6-13Palekar et al. used a potassium methoxide/copper chromite catalyst system to conduct this liquid-phase reaction in a semi-batch reactor at 373-453 K and 30-65 bar.6 Although the mechanism of BNL method is still controversial, a lot of researchers think that it is similar to the mechanism above.3 However, similar to that in the BNL method, in this process CO2 and H2O act as poisons to the strong base catalyst (RONa, ROK) as well and must be completely removed from syngas, making commercialization of low-temperature methanol synthesis difficult.Tsubaki et al. proposed a new method of low-temperature synthesis of methanol from CO2/H2 on a Cu-based oxide catalyst using ethanol as a kind of “catalytic solvent”, by which methanol was produced in a batch reactor at 443 K and 30 bar.14 This new process consisted of three steps: (1) formic acid synthesis from CO2 and H2; (2) esterification of formic acid by ethanol to ethyl formate; and (3) hydrogenation of ethyl formate to methanol and ethanol. Considering that the water-gas shift reaction at lower temperature is easily con-ducted on Cu/ZnO catalyst,15-25a new route of methanol synthesis from CO/H2 containing CO2, as a more practical way of methanol synthesis, is proposed. It consists of the following fundamental steps:As formic acid was not detected in the products, we suggested the reaction path as step (2). Tsubaki et al. investigated the synthesis reaction of methanol from CO/CO2/H2, using ethanol as reaction medium in a batch reactor and found high selectivity for methanol formation at temperature as low as 423-443 K.26In this communication, the catalytic promoting effects of different alcohols on the synthesis of methanol from CO/ CO2/H2 on Cu/ZnO catalyst were investigated. High yields ofmethanol were realized while some alcohols were utilized.2. Experimental SectionThe catalyst was prepared by the conventional coprecipitation method. An aqueous solution containing copper, zinc nitrates (Cu/Zn in molar ratio=1), and an aqueous solution of sodium carbonate were added simultaneously with constant stirring to 300 mL of water. The precipitation temperature and pH value were maintained at 338 K and 8.3-8.5, respectively. The resulting precipitate was filtrated and washed with distilled water, followed by drying at 383 K for 24 h and calcination at 623 K for 1 h. This precursor was then reduced by a flow of 5% hydrogen in nitrogen at 473 K for 13 h and successively passivated by 2% oxygen diluted by argon. The BET surface area for the catalyst was 59.4 m2/g. The catalyst here is denoted as Cu/ZnO (A).In the experiments using reactant gas of different composition, a commercially available ICI catalyst (ICI 51-2) was also used through the same reduction pretreatment, denoted here as Cu/ZnO (B). The BET surface area for Cu/ZnO (B) was 20.1 m2/g.To confirm the influence of the catalyst passivation, a tailor-made reactor where in situ reduction of the catalyst before ethanol introduction was available, was used to perform the catalyst reduction and reaction; but no difference in reaction behavior was observed. So using passivated catalyst reduced separately had no influence.In the reaction, a closed typical batch reactor with inner volume of 80 mL and a stirrer was used. The stirring speed of the propeller-type stirrer was carefully checked to eliminate the diffusion resistance between gas, liquid, and solid phases. A desired amount of solvent and catalyst was added into the reactor. Then the reactor was closed and the air inside the reactor was purged by reactant gas. A pressurized mixture gas of CO (31.90%), CO2 (5.08%), and H2 (60.08%) was introduced and then the reaction took place at the desired temperature. Ar of 2.94% in the feed gas was used as inner standard. After reaction, the reactor was cooled by ice-water and then the gas inside the reactor was released very slowly and collected in a gas-bag for analysis. The standard reaction conditions were as follows: catalyst=1.0 g; solvent=20 mL; reaction temperature=443 K; initial pressure=30 bar. At the standard reaction temperature of 443 K, the pressure was calculated to be 55 bar, including the vapor pressure of about 10 bar from ethanol.27All products were confirmed on GC-MS (Shimadzu GCMS 1600) and analyzed by two gas chromatographs (Shimadzu GC-8A/FID for liquid products, and GL Science GC-320/TCD for gas products). Conversion or yield was calculated on the basis of all carbon in the feed gas.In the experiments using reactant gas of different composition, where Cu/ZnO (B) was employed, a conventional magnetically stirred batch reactor was used. Thereaction conditions were: temperature=423 K; initial pressure=30 bar; reaction time =2 h; catalyst 0.2 g; alcohol (ethanol): 5 mL.3. Results and DiscussionThe analysis results showed that only CO and CO2 existed in the postreaction gas and only methanol and the corresponding HCOOR were the obtained liquid products. Table 1 listed the results of 13 kinds of alcohols used as reaction solvent separately under the same reaction conditions where Cu/ZnO (A) was employed. For comparison, the results in the cases of no solvent and cyclohexane were also listed in Table 1. The total conversion was the sum of the yields of both methanol and ester. From the table, no activity appeared when cyclohexane was used or no solvent was used. However, in most reactions, when alcohol was used, high activity was observed, suggesting the catalytic promoting effect of alcohol at low temperature. These alcohols lowered the reaction temperature significantly and accelerated the reaction, but did not affect stoichiometry of the overall reaction as in steps (1)-(3) listed above.For the six 1-alcohols from ethanol through 1-hexanol to benzyl alcohol, the conversions to methanol and the corresponding ester (HCOOR) decreased withincreasing carbon number of alcohol molecule. No ester was observed for these first alcohols when their carbon number was more than three. This is in accordance with the rate sequence of different 1-alcohols in the esterification reaction,28 providing the evidence that step (2) was rate-determining. As the concentration of ester, HCOOR, was so low, step (3) was believed to be quicker than step (2). It should be noted that, for all alcohols, they had a large molar ratio of ROH to the total carbon in the feed gas; the difference coming from the influence of molar numbers of different alcoholic solvents can be ignored.Concerning the alcohols with the same carbon number but different structure, the second alcohol had highest activity, as shown in the reactions in 2-propanol, 2-bu-tanol, and 2-pentanol separately. 2-Propanol exhibited highest activity among these three 2-alcohols. For example, at 443 K, the total conversion in the solvent of 2-propanol was high up to 23.46%, among which methanol and 2-propyl formate yields accounted for 13.19% and 10.27%, respectively.For alcohols with larger spatial obstacle, the reaction had lower activity, as shown in the cases of iso-butanol, tert-butyl alcohol, and cyclopentanol. In addition, for ethylene glycol and benzyl alcohol, no activity was observed. But the reason is not very clear now.On the reasons for different behaviors of the alcohols with the same carbon number but different structure, it is considered that different alcohol type affected step(2) by both the electronic effect and spatial effect. For 1-butanol, the electron density of oxygen atom in ROH is lower. As a result, ROH attacked the carbon atom of HCOOCu, the intermediate of step (2), more slowly. But the spatial obstacle of 1-butanol is the smallest among all butanols, and this is favorable to the nucleophilic attack in the esterification reaction. On the other hand, iso-butanol has high electronic density in its oxygen atom and this should accelerate the reaction. But its large molecular volume became a severe spatial obstacle in the nucleophilic attack. So its esterification rate was low. As a balanced effect between electronic factor and spatial factor, 2-butanol exhibited highest activity among 4 butanols, in the rate-determining step (2). As the opposite example, tert-butyl alcohol gave the yield of methanol as low as 5.83% here.It should be pointed out that the accumulated ester (HCOOR) can be easily transferred to methanol and ROH under higher H2 partial pressure. Two experiments were conducted to demonstrate this. One was the hydrogenation of ethyl formate in a batch reactor and the other was the hydrogenation of 2-butyl formate in a flow-type semi-batch autoclave reactor. For the first one, the reaction conditions were similar to those used in the synthesis reaction of methanol described above. A mixture gas of H2 and N2 with a total initial pressure of 30 bar (20 bar H2 and 10 bar N2) was used as feed gas. Ethyl formate (1.5 mL) and 18.5 mL of cyclohexane were mixed and poured into the reactor instead of 20 mL of alcohol. After 2 h reaction, the totalconversion of ethyl formate was 98.20% and the yield of methanol was 83.69%. Methyl formate and CO were byproducts. Methyl formate might come from the transesterification of ethyl formate and the methanol produced. CO might come from the decomposition of ethyl formate. For the latter experiment, 7.5 mL of 2-butyl formate (5 times amount in volume of ethyl formate used in the first experiment) and 12.5 mL of cyclohexane were poured in the reactor. A flow of pure H2 (20 mL/min, 30 bar) was used as flowing gas. After 8 h continuous reaction at 443 K, 96.23% of 2-butyl formate was transferred to methanol and 2-butanol.The total conversions were high while 2-alcohols were utilized. But the yields to ester were also high, especially for 2-pentanol. It is referred that step (3) above was slower if 2-alcohols were used. In other cases, the rate of step (3) was much faster than that of step (2), resulting in the disappearance or very low yield of the corresponding esters.If the water was added to ethanol with the same molar amount as that of CO2 in the feed gas under standard conditions, and the same experiment was conducted, similar results were obtained. Water did not affect the reaction behavior at these reaction conditions. From the reaction mechanism above, water was only an intermediate, similar to the role of CO2 in steps (1)-(3).In Table 2, the influence from various reactant gas composition was investigated at 423 K where catalyst Cu/ZnO (B) was used. It is clear that the total reaction rate increased with the increasing of CO2 content in the syngas. The reaction of CO2 +H2 exhibited the highest reaction rate. It seems that methanol synthesis rate was faster from CO2+H2 than from CO+H2, supporting that step (1) in the reaction mechanism was reasonable. It is interesting that pure CO did not react, indicating carbonylation of alcohol to ester impossible. While using pure CO +H2 as reactantgas, ethyl formate formed but methanol was not obtained. The reaction rate was rather lower than that of CO2-contained syngas. It is hard to determine the reaction route of pure CO +H2 now, as CO insertion to ethanol to form an ester was excluded. Maybe water contained in the ethanol (about 100-150 ppm) reacted with CO to form CO2 and fulfilled steps (1) and (2).4. ConclusionsThe use of alcohol, especially 2-alcohols, as a catalytic solvent in the synthesis of methanol from CO/CO2/H2, not only realized a new low-temperature methanol synthesis method, but also overcame drawbacks of the BNL method and other low-temperature methanol synthesis methods. This effect from accompanying alcoholic solvent decreased greatly the temperature and pressure of the synthesis reaction on Cu/ZnO solid catalyst, via a new reaction path. This method is very promising to become a new technology for low-temperature methanol synthesis where purification of syngas is not necessary. Since the reaction employed conventional solid catalyst, very mild reaction conditions, and syngas containing CO2 and H2O, it might be a promising practical method for methanol synthesis at low temperature.In fact, when the amount (weight) of catalyst was increased, the conversion was increased linearly in our experiments. 50-60% conversion was realized in a flow-type semi-batch reactor, as low-temperature methanol synthesis has no thermodynamic limitation. But in the high-temperature reaction, even the catalyst weight is enhanced, conversion cannot be increased due to intrinsic thermodynamics limitation.In the future, a bubble-column reactor is considered for large-scale synthesis. AcknowledgmentResearch for Future Program from Japan Society for the Promotion of Science (JSPS) is greatly acknowledged (JSPS-RFTF98P01001). EF0100395 References[1]Herman, R. G.; Simmons, G. W.; Klier, K. Stud. Surf. Sci. Catal.1981, 7, 475.[2]Graaf, G. H.; Sijtsema, P.; Stamhuis, E. J.; Oosten, G. Chem.Eng. Sci. 1986, 41, 2883.[3]Marchionna, M.; Lami, M.; Galleti, A. CHEMTECH, 1977, April,27.[4]Haggin, J. Chem. Eng. News 1986, Aug. 4, 21.[5]Brookheaven National Laboratory, U.S. Patents, 4,614,749, 4,-619,946, 4,623,634, 4,613,623 [1986], 4,935,395 [1990].[6]Palekar, V. M.; Jung, H.; Tierney, J. W.; Wender, I. Appl. Catal.1993, 102, 13.[7]Kirk-Othmer. Encyclopedia of Chemical Technology, 2nd ed.;Wiley: New York, 1964; V ol. 13, p 390.[8]Palekar, V. M.; Jung, H.; Tierney, J. W.; Wender, I. Appl. Catal.1993, 103, 105.[9]Wender, I. Fuel Process. Technol. 1996, 48, 189.[10]Onsager, O. T. World Patent 86/03190, 1986.[11] Zhang, H.; Li, H.; Lin, G.; Tsai, K. R. Stud. Surf. Sci. Catal.1996, 101, 1369.[12]Chen, Y. Z.; Chung, B. Z.; Hsieh, C. R. Catal. Lett. 1996, 41,213.[13]Girolamo, M.; Marchionna, M. Ital. Patent MI92/A 002126, 1992[14]subaki, N.; Sakaiya, Y.; Fujimoto, K. Appl. Catal. 1999, 180,L11.[15]Chen, C. S.; Cheng, W. H.; Lin, S. S. Catal. Lett. 2000, 68, 45.[16]Yoshihara, J.; Campbell, C. T. J. Catal. 1996, 161, 776.[17]Fujita, S.; Usui, M.; Ito, H.; Takezawa, N. J. Catal. 1995, 157,403.[18]Bailey, S.; Fromont, G. F.; Snoeck, J. W.; Waugh, K. C. Catal.Lett. 1995, 30, 99.[19]Yoshihara, J.; Parker, S.; Schafer, A.; Campbell, C. T. Catal.Lett. 1995, 31, 313.[20]Oki, S.; Happel, J.; Hnatow, M.; Kaneko, Y. Proc. 5th Int. Congr.Catal. 1973, 1, 173.[21]Oki, S.; Mezaki, R. J. Phys. Chem. 1973, 77, 447; 1973, 77, 1601.[22]Mezaki, R.; Oki, S. J. Catal. 1973, 30, 488.[23]Shchibrya, G. G.; Morozov, N. M.; Temkin, M. I. Kinet. Katal.1965, 6, 1115.[24]Uchida, H.; Isogai, N.; Oba, M.; Hasegawa, T. Bull. Chem. Soc.Jpn. 1967, 40, 1981.[25]Yureva, T. M.; Boreskov, G. K.; Gruver, V. S. Kinet. Katal. 1969,10, 862.[26]Tsubaki, N.; Ito, M.; Fujimoto, K. J. Catal. 2001, 197, 224.[27]Perry, F.; Chilton, T. Chemical Engineers’ Handbook, 5th ed.;McGraw-Hill: New York, 1975; pp 3-62.[28]Morrison, R. T.; Boyd, R. N. Organic Chemistry; Allyn andBacon: Boston, MA, 1973; Chapter 20.。
高产生物膜乳酸菌抗逆性及其抗氧化特性
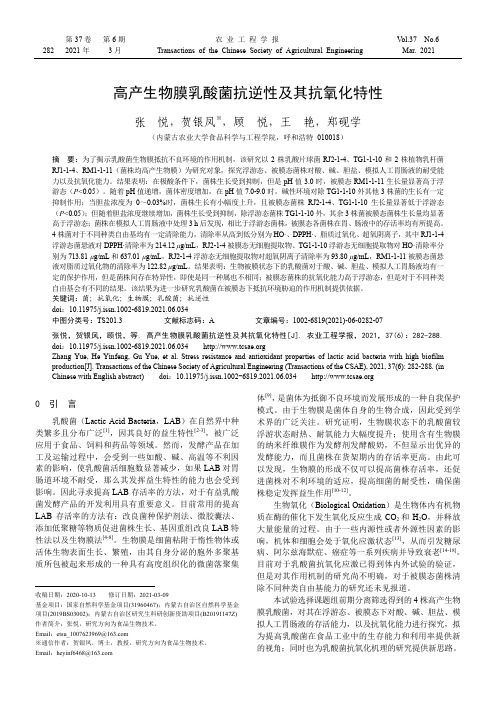
第37卷第6期农业工程学报 V ol.37 No.6282 2021年3月Transactions of the Chinese Society of Agricultural Engineering Mar. 2021 高产生物膜乳酸菌抗逆性及其抗氧化特性张悦,贺银凤※,顾悦,王艳,郑砚学(内蒙古农业大学食品科学与工程学院,呼和浩特 010018)摘要:为了揭示乳酸菌生物膜抵抗不良环境的作用机制,该研究以2株乳酸片球菌RJ2-1-4、TG1-1-10和2株植物乳杆菌RJ1-1-4、RM1-1-11(菌株均高产生物膜)为研究对象,探究浮游态、被膜态菌株对酸、碱、胆盐、模拟人工胃肠液的耐受能力以及抗氧化能力。
结果表明:在极酸条件下,菌株生长受到抑制,但是pH值3.0时,被膜态RM1-1-11生长量显著高于浮游态(P<0.05)。
随着pH值递增,菌体密度增加,在pH值7.0-9.0时,碱性环境对除TG1-1-10外其他3株菌的生长有一定抑制作用;当胆盐浓度为0~0.03%时,菌株生长有小幅度上升,且被膜态菌株RJ2-1-4、TG1-1-10生长量显著低于浮游态(P<0.05);但随着胆盐浓度继续增加,菌株生长受到抑制,除浮游态菌株TG1-1-10外,其余3株菌被膜态菌株生长量均显著高于浮游态;菌株在模拟人工胃肠液中处理3 h后发现,相比于浮游态菌株,被膜态各菌株在胃、肠液中的存活率均有所提高。
4株菌对于不同种类自由基均有一定清除能力,清除率从高到低分别为HO·、DPPH·、脂质过氧化、超氧阴离子,其中RJ1-1-4浮游态菌悬液对DPPH·清除率为214.12 μg/mL,RJ2-1-4被膜态无细胞提取物、TG1-1-10浮游态无细胞提取物对HO·清除率分别为713.81 μg/mL和637.01 μg/mL,RJ2-1-4浮游态无细胞提取物对超氧阴离子清除率为93.80 μg/mL,RM1-1-11被膜态菌悬液对脂质过氧化物的清除率为122.82 μg/mL。
A review of research progress on CO2 capture, storage, and utilization

2A review of research progress on CO capture,storage,and utilization in 34Q156789111213141516171819202122232425262728293031323334353637383940414243444546474849505152535455565758596061626364656667686970717273747576with 58%of the sources being located within the east and south 77central regions.The contributions of large point sources in each 78sector to total CO 2emissions in China are listed in Fig.2[13].With 79rapid development of energy technologies in the 21st century,fos-80sil fuels,especially coal,will still remain the dominant energy0016-2361/$-see front matter Ó2011Elsevier Ltd.All rights reserved.doi:10.1016/j.fuel.2011.08.022⇑Corresponding authors.Q2Address:State Key Laboratory of Coal Conversion,Institute of Coal Chemistry,Chinese Academy of Sciences,Taiyuan 030001,China (Y.Sun).Tel.:+863514049612;fax:+863514041153.E-mail addresses:zhaoning@ (N.Zhao),weiwei@ (W.Wei),yhsun@ (Y.Sun).Please cite this article in press as:L Q1i L et al.A review of research progress on CO 2capture,storage,and utilization in Chinese Academy of Sciences.Fuel(2011),doi:10.1016/j.fuel.2011.08.022source in China for decades to come.Chinese government recognized the huge challenge of CO 2abatement while satisfying ever-increasing energy demand.In the light of this situation,November 26,2009,China officially announced action to control emissions per unit of GDP by 40–45%by 2020,based on 86levels [14].To address this,China is undertaking a range of techni-87cal research and development projects on CCSU,including the na-88tional fundamental research and high-tech programs,as well as a 89large number of international programs.The CCS projects,fun-90dings,and research institutes in China is shown in Table 1.91Since 1990,China had carried out a series of climate change 92projects under framework of national programs,such as China’s 93National Climate Change Program (CNCCP),National Hi-tech R&D949596979899100101102103104105106107108109110111112113114115116117118119120121cooperation with international on CCSU.On the basis of the finical 122support of both Chinese government and CAS,a lot of progresses 123were obtained in several academic institutes in CAS including 124CO 2capture;enhanced oil recovery (EOR)and enhanced coal bed 125methane (ECBM)projects as well as CO 2chemical utilizations.This 126brief review has covered the research progress in CO 2capture,stor-127age,and utilization in CAS.2.The contributions of large point sources in each sector to overall total emissions in China [12].Please cite this article in press as:L Q1i L et al.A review of research progress on CO 2capture,storage,and utilization in Chinese Academy of Sciences.Fuel(2011),doi:10.1016/j.fuel.2011.08.022128129130131132133134135136137aration,and cryogenic fractionation.138 2.1.Amine-based scrubbing solvent139Amine scrubbing is a well known technology for capturing CO 2140from flue gas,which has been widely deployed on a large scale 141across several industries [25–28].The industrially most important142143144145146147148149150151152the environment [30].1532.2.Ionic liquids154Therefore,a nonvolatile solvent that could facilitate CO 2capture 155without the loss of solvent into the gas stream would be advanta-156geous.Ionic liquids (ILs)are commonly defined as liquids whichTable 1CCS projects,fundings,and research institutes in China.China and international cooperation on CCS projects and fundingsResearch institutes aBNLMS–CAS IET–CAS RCEES–CAS ICC–CAS IPE–CAS LICP–CAS CIAC–CAS National High Technology Research and Development Program of China (863)SIC–CAS National Key Basic Research and Development Program of China (973)IGG–CAS China’s National Climate Change Program (CNCCP)IAP–CAS L.L Q1i et al./Fuel xxx (2011)xxx–xxx3Please cite this article in press as:L Q1i L et al.A review of research progress on CO 2capture,storage,and utilization in Chinese Academy of Sciences.Fuel(2011),doi:10.1016/j.fuel.2011.08.022157are composed entirely of ions with a melting point of less than 158100°C.ILs have many unique properties in comparison to other 159solvents as extremely low volatility,broad range of liquid temper-160ature,high thermal and chemical stability,and tunable physico-161chemical characteristics and as a result,ILs have been considered 162as a potential substitute of aqueous amine solutions for CO 2cap-163ture [31–34].164In Changchun Institute of Applied Chemistry,Chinese Academy 165of Sciences (CIAC–CAS),a novel dissolving process for chitin and 166chitosan was developed by using the ionic liquid 1-butyl-3-167methyl-imidazolium chloride ([Bmim]Cl)as a solvent for capturing 168and releasing CO 2.The results showed that the chitin/IL and chito-169170171172173174175176177178179180181182183184185186187188189190191192193194195196197198199200201tant to consider the maximum mass loading when considering the 202support of ILs on inert substrates –yes,these can enhance the ILs’203ability to take up CO 2,but at the expense of cycling an inert sorbent 204round a thermal cycle.The ILs are also monstrously expensive,the 205complex structure,and high cost for preparation,compared to sim-206pler solvents such as MEA or ammonia.Thus,the potential for 207improving CO 2solubilities and reducing cost of the ILs still needs 208to be studied for future applications.In 2010,in Beijing National 209Laboratory for Molecular,Chinese Academy of Sciences (BNLMS–210CAS),Zhang and co-workers first reported on CO 2capture by 211hydrocarbon surfactant liquids.It also found that CO 2had high sol-212ubility in low-cost hydrocarbon surfactant liquids,and the ab-213and the 214215216such as corrosion,at 217regenerable solid sor-218concept for CO 2recov-219into amine-based and 220221222with various so-223as silica gels,activated 224have been shown to phys-225enhance the sorp-226of many amine-based 227In Dalian Institute of 228(DICP–CAS),Zhang 229silica foam (MCF)materi-230with polyethyl-231The results showed that 232having large window 2333.45mmol CO 2/g sorbent 234In Institute of Coal Chem-235Zhao et al.studied 236materials derived 237sorption capabili-238°C and 1bar.The as-pre-239selectivity for CO 2over 240prepared a series of CO 2241pentamine (TEPA)was 242(PMHS)based mesopor-243The highest absorption 24475°C with the 10vol.%245was higher than most 246Desorption could 247in 1h [46].248of amine-based sorbent 249capacity of solid sorbent.250have poor mechanical 251amine-based sorbents 252and require signifi-253processes.254255sorbents for CO 2capture 256Alkali earth metal,such 257form alkali earth metal-258vapor at high tempera-259and post-combus-260simplified process flow 261the calcium looping 262vessel (the carbonator)4L.L Q1i et al./Fuel xxx (2011)xxx–xxxPlease cite this article in press as:L Q1i L et al.A review of research progress on CO 2capture,storage,and utilization in Chinese Academy of Sciences.Fuel(2011),doi:10.1016/j.fuel.2011.08.022the carbonation reaction between CO 2and solid CaO separates CO from coal-combustion flue gas at a temperature between 600°and 650°C.The CaCO 3formed is then passed to another vessel (the calciner),where it is heated to reverse the reaction (900–950°C),releasing the CO 2suitable for sequestration,and regener-ating the CaO-sorbent which is then return to the carbonator.The carbonation process is exothermic,which is matched with the temperature of a steam cycle,allowing recuperation of the heat.In IPE–CAS,the decomposition conditions of CaCO 3particles for CO 2capture in a steam dilution atmosphere (20–100%steam 307308309310311312313314315316317318319320321322323324325326327328329330332333334335336337338339340341342343344345346347348349350351352353354355Fig.3.The process flow diagram of post-combustion capture using the calcium looping cycle [47,48].Please cite this article in press as:L Q1i L et al.A review of research progress on CO 2capture,storage,and utilization in Chinese Academy of Sciences.Fuel(2011),doi:10.1016/j.fuel.2011.08.022strength (998N/cm 2)and exhibited good stability in multiple cy-cles [74,75].Furthermore,the application of a conceptual CO 2cap-ture process using this sorbent was proposed for an existing coal fired power plant [75].However,to optimize CO 2sorption capacity,understand of the interaction between CO 2and the sorbent need to be studied in the further work.Moreover,much work remains before the technology fluidized bed CO 2capture can be commercialized.Simulta-neously,the numerical simulation based on the computational fluid 365dynamics (CFD)method will become a research focus in the future.366 3.CO 2storage367Following the capture and transport process,CO 2can be dis-368posed of in natural sites such as deep geological sequestration,369mineral carbonation,or ocean storage [76].There are three geolog-370ical formations that have also been recognized as major potential 371CO 2sinks:deep saline-filled sedimentary (DSFs),depleted oil 372natural gas reservoirs,and unmineable coal-seams.The geology 373also suggests possibilities for CO 2enhanced oil recovery (CO 374EOR),CO 2enhanced gas recovery (CO 2–EGR)and CO 2enhanced 375coal-bed methane recovery (CO 2–ECBM)projects [12].3763.1.Geological sequestration377Geological storage involves injecting CO 2at depths greater than 3781000m into porous sedimentary formations using technologies 379derived from the oil and gas industry [77].CO 2can be stored in 380supercritical state at depth below 800–1000m,which provides 381the potential for efficient utilization of the space,due to the li-382quid-like density of supercritical CO 2.The point at which CO 2Table 2Performance summary of K-based sorbents capturing CO 2.Material Temperature (°C)CO 2partial pressure (bar)e Total capacity (mmol CO 2/g sorbent)Method f Regenerature temperature (°C)Ref.K 2CO 3/AC a 600.01 1.95TCD g 150[62]K 2CO 3/SiO 2600.010.23TCD g –[62]K 2CO 3/USY 600.010.43TCD g –[62]K 2CO 3/CsNaX 600.01 1.35TCD g –[62]K 2CO 3/Al 2O 3600.01 1.93TCD g 350[62]K 2CO 3/CaO 600.01 1.11TCD g –[62]K 2CO 3/MgO 600.01 2.70TCD g 400[62]K 2CO 3/TiO 2600.01 1.89TCD g 150[62]K 2CO 3/Al 2O 3600.01 1.96TCD g >300[63]Re-KAl(I)30b 600.01 1.86TCD g <200[63]g Fig.5.The schematic diagram of experimental apparatus for the fluidized bed [74,75].6L.L Q1i et al./Fuel xxx (2011)xxx–xxxPlease cite this article in press as:L Q1i L et al.A review of research progress on CO 2capture,storage,and utilization in Chinese Academy of Sciences.Fuel(2011),doi:10.1016/j.fuel.2011.08.022383transforms from critical to supercritical point is 31.1°C and 3847.38MPa [78].CO 2is injected usually in the supercritical form into 385the saline aquifer or depleted oil or gas reservoir.Four major clas-386ses of deep geologic reservoirs present within China have been 387identified and evaluated as candidates for the long-term storage 388of anthropogenic CO 2:deep saline-filled sedimentary (DSFs)for-389mations,depleted gas basins,depleted oil basins with potential 390for CO 2–EOR,and deep unmineable coal seams with potential for 391CO 2–ECBM.Fig.6shows the map of the combined location and ex-392tent of candidate geologic CO 2storage formations in China [13].393Because the CO 2industry is not mature,there are few active CO 2394storage projects which can provide site specific information;hence417China are also potential storage candidates.Recently,other re-418search has also focused on estimating the distance between CO 2419sources and potential sinks.Zheng et al.superimposed the loca-420tions of these 27facilities onto maps of sedimentary basins in each 421of the five regions of China (Huabei,Ordos,Dongbei,Yuwan,and 422Xinjiang).The majority of the candidate CO 2sources are found in 423the Ordos,Huabei and Dongbei regions [85].424The China–UK Near Zero Emissions Coal (NZEC)Initiative exam-425ined options for carbon (CO 2)capture,transport and geological 426storage in China,which was developed under the 2005EU–China 427NZEC Agreement that aims to demonstrate CCS in China and the 428EU [16,86–88].The NZEC Initiative has evaluated the potential to 429430431432433434435436437438439440441442443444445446447448449450451L.L Q1i et al./Fuel xxx (2011)xxx–xxx7Please cite this article in press as:L Q1i L et al.A review of research progress on CO 2capture,storage,and utilization in Chinese Academy of Sciences.Fuel(2011),doi:10.1016/j.fuel.2011.08.022452Kailuan mining area (Hebei Province)and deep saline aquifers in 453the Jiyang Depression (Shandong province)[89,90].The results 454show that the Dagang oilfield is not suitable for large-scale storage,455though could be considered for EOR pilots.The Shengli oilfield was 456considered more promising for storage (472Mt in eight selected 457fields).Storage potential in the Kailuan mining area is 504,000458Mt adsorbed onto the coal and 38,100Mt void storage capacity.459However,the coals have low porosity and permeability that will af-460fect future energy resources [90].The Institute of Geology and Geo-461physics,Chinese Academy of Sciences (IGG–CAS)studied the 462potential for storage in the Jiyang Depression.The results revealed 463that Guantao Formation in the Jiyang Depression has good porosity 464and permeability 465areas was 4662010,in South China 467of Sciences 468storage capacity in 469the Pearl River 470CCS-related 471China [78].There 472saline formations 473tive storage 474including 60Mt in 475large for storaging 476in Guangdong in 477In a word,these 478age of CO 2in deep 479Although this is 480countries,it will 481and there was 482characteristics.483 3.1.2.CO 2–EOR484Although CO 2485oil recovery (EOR)486this process can be 487oil,the cost of CO 2,488the CO 2source [92].489the production of 490be an ideal option 49184commercial or 492tion worldwide [1].493been implemented 494Oil Corporation 495in the Daqing,496ernments of Japan 497out a project to 498plant in China into a 499duced from the 500that between 270501ered by using CO 2502including IGG–CAS 503three large oil fields 504oil reservoirs in the 505were suitable both 506found suitable for 507showed that the 508CO 2storage 509the oil recovery by steam injection has been already applied at Lia-510ohe oil field.Each single well,in average,had conducted 7.6times 511of steam injection-oil recovery processing for EOR propose.The to-512tal recovered oil amounts were 12.06Mt [92].Active oil producing 513fields where CO 2–EOR is technically possible provide credible 514opportunities to initiate CO 2storage demonstration projects.How-515ever,significant further investigations,including detailed site516appraisals would be necessary before such fields can be considered 517as technically and economically suitable for CO 2storage.5183.1.3.CO 2–ECBM519In a similar manner,ECBM recovery can be used to store CO 2520while improving methane recovery.A bright prospect of gas injec-521tion technology for ECBM production has been suggested by Chi-522nese engineers since the late 1990s [94].More recently,a joint 523venture was formed between the China United Coal Bed Methane 524Corporation and the Alberta Research Council of Canada to develop 525a project entitled ‘‘Development of China’s coalbed methane tech-526nology/CO 2sequestration’’[12].This project was initiated in March 527project was performed 528in the anthracitic coals of 529China [95],which is 530in China up to now 531at ICC–CAS in 2005532were investigated based 533An equipment simulated 534middle pressures was 535in coal seam,536behaviors were studied.537coal mine and salt-water 538four coals of various rank 539China were tested for 540one of the most impor-541process.The result 542capacities for methane 543>Bulianta coal >Zhangji 544adsorption isotherms 545lattice model [100].546given to estimate the 547[101],which was 548underground stress is so 5492and CH 4respectively 550the mechanical sta-551of the impact factors of 552stress could be obviously 553of the casing or by using 554and Young’s modulus 555China was also estimated 556prospecting data of coal 557and the replacement ratio 558different ranks,it is esti-559methane resources will 560technology is uti-561in coalbeds is about 562as the total CO 2emission 563also developed 564simulation of the CO 2–565is a lack of knowledge 566due to the complexity 567fluid transport processes.568will be the next 569570571Large amounts of CO 2can also be fixed by a process called min-572eral carbonation,which is natural or artificial fixation of CO 2into 573carbonates.It has been proposed as a promising CO 2sequestration 574technology e.g.the silicate rocks (calcium or magnesium)could be 575turned into carbonates by reacting with CO 2following this mech-576anism [8,105]:577ðMg ;Ca Þx Si y O x þ2y þx CO 2!x ðMg ;Ca ÞCO 3þy SiO 25798L.L Q1i et al./Fuel xxx (2011)xxx–xxxPlease cite this article in press as:L Q1i L et al.A review of research progress on CO 2capture,storage,and utilization in Chinese Academy of Sciences.Fuel(2011),doi:10.1016/j.fuel.2011.08.022580581582583584585586587588589590591592593594595596597598599600601602603604605606607608609610611612613614615616617618619620621622623624625626627628629630631632633634635636637638639hanced by the fact that this method of storage is highly verifiable 640and unquestionably permanent,the grinding energy required to 641produce particles of the size required to react rapidly with the 642acids is large,and the residence times on the order of hours re-643quired to allow carbonation of the solids,via either route,is so long 644that immense reactors would be required,associating environmen-645tal concerns.Furthermore,mineral carbonation will always be646expensive than most applications of geological storage 647important gap in mineral carbonation is the lack of 648onstration plant.649Ocean storage650Captured CO 2also could help reduce the atmospheric 6516526536546556566576586596606616626636646656666676686696706716726736746756766776786796806816826836842685carbonic acid,which would be likely harmful to ocean organisms 686and ecosystems [17].Additionally,it is not known whether the 687public will accept the deliberate storage of CO 2in the ocean as part 688of a climate change mitigation strategy.The development of ocean 689storage technology is generally at a conceptual stage;thus,further 690research and development would be needed to make technologies 691available.3.Reaction mechanism for enhanced carbonation crystallization Q1Please cite this article in press as:L Q1i L et al.A review of research progress on CO 2capture,storage,and utilization in Chinese Academy of Sciences.Fuel(2011),doi:10.1016/j.fuel.2011.08.022692693694695696697698699700701702703704705706707708709710711712713714715716717718719721722723the reaction [131–135],such as in ICC–CAS,Zhao et al.had reported 724a catalyst system composed of KI supported on metal oxides for 725cycloaddition of propylene oxide with CO 2.It was found that the 726activity of KI for cycloaddition was greatly enhanced by ZnO as both 727support and promoter,resulting in a high yield of propylene 728carbonate within a short reaction time.The mechanism is also pro-729posed (Scheme 4)[133].Recently,a large number of catalytic730systems,such as metal oxides,transition metal,ammonium 731well as main group complexes,were reported to be active 732reactions [136–139].In ICC–CAS,the efficient ultrasonic tech-733nique was used for the preparation of amine-functionalized porous 734catalysts for CO 2coupling with epoxide.According to 735study by Zhang and co-workers [140],the reaction conditions 736great influence on the performance and the silanols on the surface 737played an important role in the chemical fixation of CO 2.In addi-738they also proposed the possible reaction mechanism for 739coupling with epoxide over such type of catalysts (Scheme 5).740In recent years,ionic liquids as environmentally benign media 741organic synthesis and catalytic reaction significant progress 7427437447457467477487492750catalyst system without using additional organic solvents was 751achieved in excellent selectivity and TOF (5410h À1)[144].In 752IPE–CAS,an efficient Lewis acid/base catalyst composed of ZnCl 2/753PPh 3C 6H 13Br was developed and showed high activity and selectiv-754ity for the coupling reaction of CO 2and epoxide under the mild 755conditions [145].Sun et al.prepared a series of hydroxyl-function-756alized ionic liquids (HFILs)which showed efficient reactivity andScheme 4.The proposed diagram of reaction mechanism [133].Q1Please cite this article in press as:L Q1i L et al.A review of research progress on CO 2capture,storage,and utilization in Chinese Academy of Sciences.Fuel(2011),doi:10.1016/j.fuel.2011.08.022780781782783784785786787788789790791792793794795796797798799800802803804805806807Please cite this article in press as:L Q1i L et al.A review of research progress on CO 2capture,storage,and utilization in Chinese Academy of Sciences.Fuel(2011),doi:10.1016/j.fuel.2011.08.022CO 2þCH 4¼2CO þ2H 2841842In the past decade,a lot of researches have been devoted to the 843catalytic performance of noble metals,including Pt,Ru,Rh,Pd,844and Ir for this reaction [165–169].It showed that Rh and Ru845exhibited both high activity and stability in CH 4dry reforming,846while Pd,Pt and Ir were less active and prone to deactivation.847Nevertheless,considering the aspects of high cost and limitedPlease cite this article in press as:L Q1i L et al.A review of research progress on CO 2capture,storage,and utilization in Chinese Academy of Sciences.Fuel(2011),doi:10.1016/j.fuel.2011.08.022848availability of noble metals,it is more practical to develop non-849noble metal catalysts which exhibited both high activity and pared with noble metals,Ni-based catalysts have been 851widely investigated because of their high activity and relatively 852low price [170–172].Nevertheless,application of Ni-based cata-853lysts in a large scale process is not so straightforward due to rapid 854carbon deposition,resulting in the deactivation of the catalyst 855[173].It was found that when Ni is supported on a alkaline earth 856metal oxide such as MgO,CaO,and BaO with strong Lewis basi-857city,carbon deposition can be attenuated or even suppressed 858[174]which is because that the support could promote chemi-859sorption of CO 2and thus,accelerated the reaction of CO 2and C 8608618628638648658668678688698708718728738748758768778788798808818828838848858868878888898908918928938948958968974.4.Reaction of CO 2with ethane and propane898Ethylene and propylene are basic raw material in the petrol-899chemical industry.Thermal cracking of hydrocarbons (such as eth-900ane)in the presence of steam is currently the main source of eth-901ylene [181,182].Nevertheless,steam cracking of ethane to 902ethylene is a highly endothermic process that must be performed 903at high temperatures,which means the consumption of a large 904amount of energy.The introduction of CO 2could reduce the extent 905of deep oxidation which results in many byproducts whereas eth-906ylene selectivity drops when oxygen is used as oxidant [183].907Thermodynamics analysis and experimental results have indi-908909910911912913915916917918919920921922923924925926927928929930931932933934935936938939940941L.L Q1i et al./Fuel xxx (2011)xxx–xxx13Please cite this article in press as:L Q1i L et al.A review of research progress on CO 2capture,storage,and utilization in Chinese Academy of Sciences.Fuel(2011),doi:10.1016/j.fuel.2011.08.022969970971972973974975976977978979980981982983984985986987988990991992993994995996997998999100010011002100310041005100610071008100910101011101210131014Please cite this article in press as:L Q1i L et al.A review of research progress on CO 2capture,storage,and utilization in Chinese Academy of Sciences.Fuel(2011),doi:10.1016/j.fuel.2011.08.0221015DMC in supercritical phase was proposed in Scheme 11.Recently,developed a supported Cu-Ni/V 2O 5-SiO 2heterogeneous because the reaction can be carried out in a fixed-bed the side production of water molecules 10341035103610371038103910401041104210431044and theoretical approaches,which enable the development of 1045CO 2selective sorbents.Besides,the sorbent performance,lifetime,10461047104810491050105110521053105410551056105710581059106010611062106310641065Scheme 11.The proposed catalytic reaction mechanism Please cite this article in press as:L Q1i L et al.A review of research progress on CO 2capture,storage,and utilization in Chinese Academy of Sciences.Fuel(2011),doi:10.1016/j.fuel.2011.08.0221066of component costs,specific Chinese market conditions,and other 1067factors impacting costs of deployment in China will be important 1068to consider in greater detail.To propose the storage mechanism,1069monitoring,simulation,risk assessment,control methods as well 1070as engineering design will be studied in future.1071The utilization of CO 2to chemicals has attracted considerable 1072attention as a possible way to manufacture useful commercial 1073chemicals from CO 2in some specific locations (Scheme 12)[222].1074The utilization of CO 2as a raw material in the synthesis of chemi-1075cals was also conducted by CAS,including synthesis of cyclic car-1076bonate from CO 2and epoxide,reaction of CO 2and propylene 1077glycol (PG),CO 2reforming of CH 4,reaction of CO 2and ethane 1078and propane,CO 21079methyl carbonate 1080amount of CO 2can 1081to the order of 1082ent the typical 1083cations is only 1084laminates are used 1085of the materials can 1086and overall net 1087ation.1088and fundamental 1089lue-added chemicals 1090tive net carbon 1091moderate reaction 1092the energy or 1093clear,wind,1094also important to 1095 6.Uncited 1096[201].Q31097Acknowledgments1098This work was 1099vation Programme 1100323);the Ministry of 1101lic of China 1102Climate Change:1103Academy of 1104the Natural Science 1105References1106[1]Mikkelsen M,1107fixation and 11082010;3(1):43–81.1109[2]Xu XC,Song CS,1110separation from 111111121113[3]Shukla R,Ranjith P,1114and caprock 1115[4]Bredesen R,Jordal 1116generation with CO 1117[5]Barelli L,Bidini 1118sorption-enhanced 1119review.Energy 1120[6]Drage TC,1121adsorbents for CO 2capture in gasification.Energy Fuels 2009;23:2790–6.1122[7]Stewart C,Hessami M.A study of methods of carbon dioxide capture and1123sequestration –the sustainability of a photosynthetic bioreactor approach.1124Energy Convers Manage 2005;46:403–20.1125[8]Yang HQ,Xu ZH,Fan MH,Gupta R,Slimane RB,Bland AE,et al.Progress in1126carbon dioxide separation and capture:a review.J Environ Sci 11272008;20(1):14–27.1128[9]Khatri RA,Chuang SSC,Soong Y,Gray M.Thermal and chemical stability of1129regenerable solid amine sorbent for CO 2capture.Energy Fuels 11302006;20(4):1514–20.1131[10]Jin HG,Gao L,Han W,Hong H.Prospect options of CO 2capture technology1132suitable for China.Energy 2009:1–8.1133[11]Hashim H,Douglas P,Elkamel A,Croiset E.Optimization model for energy1134planning with CO 2emission considerations.Ind Eng Chem Res 11352005;44(4):879–90.1136[12]Meng KC,Williams RH,Celia MA.Opportunities for low-cost CO 2storage1137demonstration projects in China.Energy Policy 2007;35(4):2368–78.1138[13]Dahowski RT,Li X,Davidson CL,Wei N,Dooley JJ,Gentiled RH.A preliminary1139cost curve assessment of carbon dioxide capture and storage potential in 1140China.Energy Procedia 2008;1(1):2849–56.1141[14]Wang R,Liu WJ,Xiao LS,Liu J,Kao W.Path towards achieving of China’s 20201142carbon emission reduction target –a discussion of low-carbon energy policies 1143at province level.Energy Policy 2011;39(5):2740–7.1144[15]China’s scientific &technological actions on climate change;2007.<http:///WebSite/CCChina/UpFile/File199.pdf >.1146Pearce J,et al.Carbon capture1147near zero emissions coal 11481149capture and storage for CO 211502010;38(9):5281–9.1151R,Mezghani K,Imashuku S,1152capture utilizing oxy-fuel 1153membrane systems.Int J 11541155and size effects of activated1156Ind Eng Chem Res 11571158to produce hydrogen with1159combustion.Int J Hydrogen 11601161combustion CO 2capture by1162Prog Energy Combust Sci 11631164DA,McMichael WJ.Carbon1165sorbents.Energy Fuels 11661167Park AHA,et al.High efficiency1168based on amine-functionalized 11691170Gimenez A,Sanchez-Biezma A,1171for low cost CO 2capture in 11722008;49(10):2809–14.1173organogels via ‘‘latent’’gelators.1174their ammonium carbamates.11751176and prediction of the solubility1177and mixed alkanolamine 11781179of the structural features1180of CO 2and regeneration in 11811182Svendsen HF.Modeling and1183in aqueous alkanolamine 1184Ind Eng Chem Res 11851186of products of the oxidative1187aqueous monoethanolamine 1188gases.Ind Eng Chem Res 11891190Galindo A,Jackson G,et al.An1191Energy Environ Sci 11921193and thermodynamic11941-n-butyl-3-methylimidazolium 11951196High-pressure phase behavior1197ionic liquids.J Phys Chem B 11981199JF.Anion effects on gas12001201liquids for post-combustion CO 212021203dissolved in ionic liquids as12041205W,Zhang XP.Dual amino-1206for CO 2capture.Chem Eur J 12071208[37]Zhang JM,Zhang SJ,Dong K,Zhang YQ,Shen YQ,Lv XM.Supported absorption1209of CO 2by tetrabutylphosphonium amino acid ionic liquids.Chem Eur J 12102006;12(15):4021–6.1211[38]Sairi NA,Yusoff R,Alias Y,Aroua MK.Solubilities of CO 2in aqueous N-1212methyldiethanolamine and guanidinium trifluoromethanesulfonate ionic 1213liquid systems at elevated pressures.Fluid Phase Equilibria 2011;300(1–12142):89–94.1215[39]Zhang JL,Han BX,Zhao YJ,Li JS,Hou MQ,Yang GY.CO 2capture by1216hydrocarbon surfactant liquids.Chem Commun 2011;47(3):1033–5.16L.L Q1i et al./Fuel xxx (2011)xxx–xxxPlease cite this article in press as:L Q1i L et al.A review of research progress on CO 2capture,storage,and utilization in Chinese Academy of Sciences.Fuel(2011),doi:10.1016/j.fuel.2011.08.022。
乙酸蒸汽催化重整制氢的研究进展
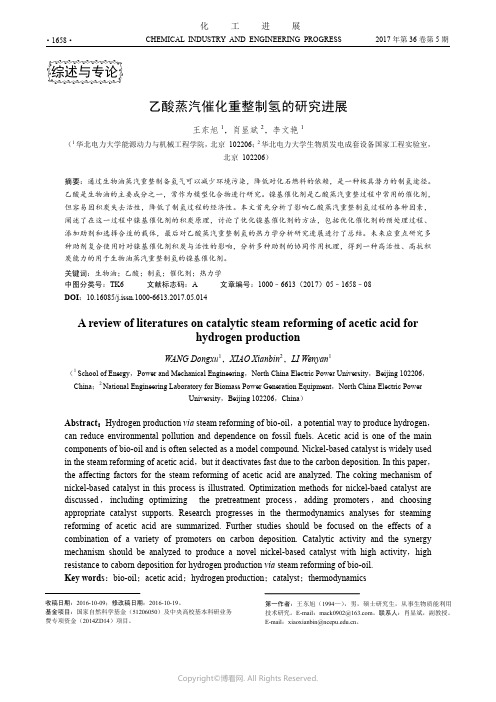
CHEMICAL INDUSTRY AND ENGINEERING PROGRESS 2017年第36卷第5期·1658·化 工 进展乙酸蒸汽催化重整制氢的研究进展王东旭1,肖显斌2,李文艳1(1华北电力大学能源动力与机械工程学院,北京 102206;2华北电力大学生物质发电成套设备国家工程实验室,北京 102206)摘要:通过生物油蒸汽重整制备氢气可以减少环境污染,降低对化石燃料的依赖,是一种极具潜力的制氢途径。
乙酸是生物油的主要成分之一,常作为模型化合物进行研究。
镍基催化剂是乙酸蒸汽重整过程中常用的催化剂,但容易因积炭失去活性,降低了制氢过程的经济性。
本文首先分析了影响乙酸蒸汽重整制氢过程的各种因素,阐述了在这一过程中镍基催化剂的积炭原理,讨论了优化镍基催化剂的方法,包括优化催化剂的预处理过程、添加助剂和选择合适的载体,最后对乙酸蒸汽重整制氢的热力学分析研究进展进行了总结。
未来应重点研究多种助剂复合使用时对镍基催化剂积炭与活性的影响,分析多种助剂的协同作用机理,得到一种高活性、高抗积炭能力的用于生物油蒸汽重整制氢的镍基催化剂。
关键词:生物油;乙酸;制氢;催化剂;热力学中图分类号:TK6 文献标志码:A 文章编号:1000–6613(2017)05–1658–08 DOI :10.16085/j.issn.1000-6613.2017.05.014A review of literatures on catalytic steam reforming of acetic acid forhydrogen productionWANG Dongxu 1,XIAO Xianbin 2,LI Wenyan 1(1 School of Energy ,Power and Mechanical Engineering ,North China Electric Power University ,Beijing 102206,China ;2 National Engineering Laboratory for Biomass Power Generation Equipment ,North China Electric PowerUniversity ,Beijing 102206,China )Abstract :Hydrogen production via steam reforming of bio-oil ,a potential way to produce hydrogen , can reduce environmental pollution and dependence on fossil fuels. Acetic acid is one of the main components of bio-oil and is often selected as a model compound. Nickel-based catalyst is widely used in the steam reforming of acetic acid ,but it deactivates fast due to the carbon deposition. In this paper ,the affecting factors for the steam reforming of acetic acid are analyzed. The coking mechanism of nickel-based catalyst in this process is illustrated. Optimization methods for nickel-baed catalyst are discussed ,including optimizing the pretreatment process ,adding promoters ,and choosing appropriate catalyst supports. Research progresses in the thermodynamics analyses for steaming reforming of acetic acid are summarized. Further studies should be focused on the effects of a combination of a variety of promoters on carbon deposition. Catalytic activity and the synergy mechanism should be analyzed to produce a novel nickel-based catalyst with high activity ,high resistance to caborn deposition for hydrogen production via steam reforming of bio-oil. Key words :bio-oil ;acetic acid ;hydrogen production ;catalyst ;thermodynamics第一作者:王东旭(1994—),男,硕士研究生,从事生物质能利用技术研究。
光催化还原二氧化碳的进展
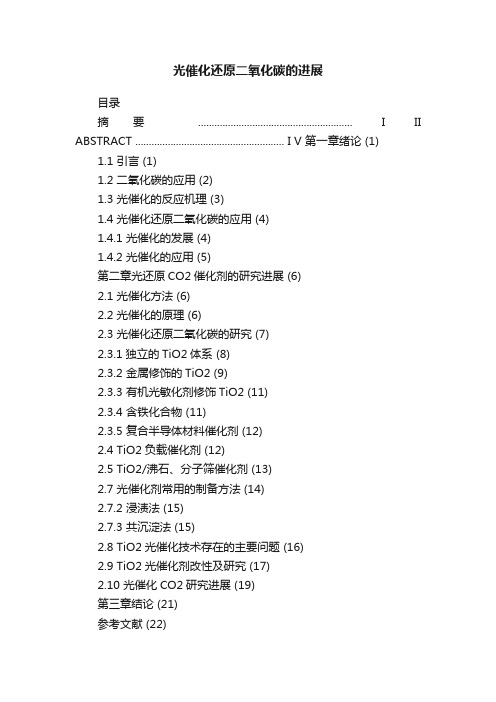
光催化还原二氧化碳的进展目录摘要......................................................... I II ABSTRACT ....................................................... I V 第一章绪论 (1)1.1 引言 (1)1.2 二氧化碳的应用 (2)1.3 光催化的反应机理 (3)1.4 光催化还原二氧化碳的应用 (4)1.4.1 光催化的发展 (4)1.4.2 光催化的应用 (5)第二章光还原CO2催化剂的研究进展 (6)2.1 光催化方法 (6)2.2 光催化的原理 (6)2.3 光催化还原二氧化碳的研究 (7)2.3.1独立的TiO2体系 (8)2.3.2 金属修饰的TiO2 (9)2.3.3 有机光敏化剂修饰TiO2 (11)2.3.4 含铁化合物 (11)2.3.5 复合半导体材料催化剂 (12)2.4 TiO2负载催化剂 (12)2.5 TiO2/沸石、分子筛催化剂 (13)2.7 光催化剂常用的制备方法 (14)2.7.2 浸渍法 (15)2.7.3 共沉淀法 (15)2.8 TiO2光催化技术存在的主要问题 (16)2.9 TiO2光催化剂改性及研究 (17)2.10 光催化CO2研究进展 (19)第三章结论 (21)参考文献 (22)致谢 (23)摘要温室气体CO2是全球变暖的一个主要原因,利用太阳能将CO2还原为烃类等有用资源将对环境保护和人类生活带来巨大的好处。
本文总结了近年来发现的一些可用于CO2光催化还原反应的新型催化剂,主要涉及钙钛矿复合氧化物光催化剂、隧道结构光催化剂、分子筛光催化剂、有机物光催化剂和生物酶催化剂。
从结构特点出发,解释了它们作为还原CO2的光催化剂具有的优势。
另外,对光催化还原CO2涉及的机理也作了相应介绍。
CO2既是一种温室效应气体,又是地球的重要碳源,其合理利用具有重要意义。
一种环境响应型水泥石的抗CO2腐蚀性能
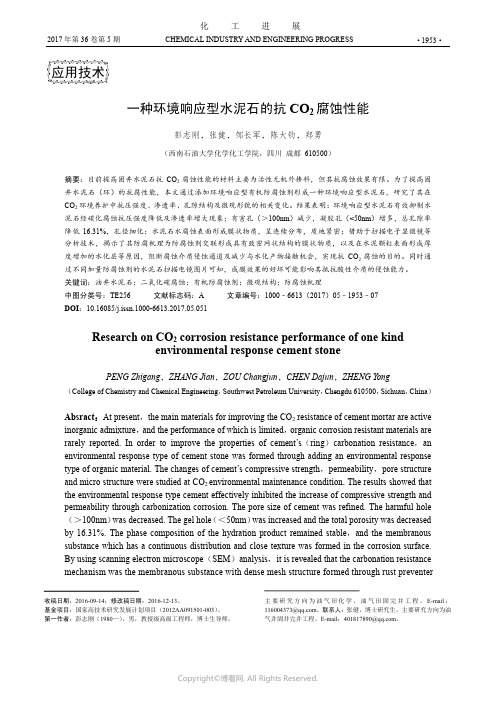
2017年第36卷第5期 CHEMICAL INDUSTRY AND ENGINEERING PROGRESS·1953·化 工 进展一种环境响应型水泥石的抗CO 2腐蚀性能彭志刚,张健,邹长军,陈大钧,郑勇(西南石油大学化学化工学院,四川 成都 610500)摘要:目前提高固井水泥石抗CO 2腐蚀性能的材料主要为活性无机外掺料,但其抗腐蚀效果有限。
为了提高固井水泥石(环)的抗腐性能,本文通过添加环境响应型有机防腐蚀剂形成一种环境响应型水泥石,研究了其在CO 2环境养护中抗压强度、渗透率、孔隙结构及微观形貌的相关变化。
结果表明:环境响应型水泥石有效抑制水泥石经碳化腐蚀抗压强度降低及渗透率增大现象;有害孔(>100nm )减少,凝胶孔(<50nm )增多,总孔隙率降低16.31%,孔径细化;水泥石水腐蚀表面形成膜状物质,呈连续分布,质地紧密;借助于扫描电子显微镜等分析技术,揭示了其防腐机理为防腐蚀剂交联形成具有致密网状结构的膜状物质,以及在水泥颗粒表面形成厚度增加的水化层等原因,阻断腐蚀介质侵蚀通道及减少与水化产物接触机会,实现抗CO 2腐蚀的目的。
同时通过不同加量防腐蚀剂的水泥石扫描电镜图片可知,成膜效果的好坏可能影响其抵抗酸性介质的侵蚀能力。
关键词:油井水泥石;二氧化碳腐蚀;有机防腐蚀剂;微观结构;防腐蚀机理中图分类号:TE256 文献标志码:A 文章编号:1000–6613(2017)05–1953–07 DOI :10.16085/j.issn.1000-6613.2017.05.051Research on CO 2 corrosion resistance performance of one kindenvironmental response cement stonePENG Zhigang ,ZHANG Jian ,ZOU Changjun ,CHEN Dajun ,ZHENG Yong(College of Chemistry and Chemical Engineering ,Southwest Petroleum University ,Chengdu 610500,Sichuan ,China )Absract :At present ,the main materials for improving the CO 2 resistance of cement mortar are active inorganic admixture ,and the performance of which is limited ,organic corrosion resistant materials are rarely reported. In order to improve the properties of cement’s (ring )carbonation resistance ,an environmental response type of cement stone was formed through adding an environmental response type of organic material. The changes of cement’s compressive strength ,permeability ,pore structure and micro structure were studied at CO 2 environmental maintenance condition. The results showed that the environmental response type cement effectively inhibited the increase of compressive strength and permeability through carbonization corrosion. The pore size of cement was refined. The harmful hole (>100nm )was decreased. The gel hole (<50nm )was increased and the total porosity was decreased by 16.31%. The phase composition of the hydration product remained stable ,and the membranous substance which has a continuous distribution and close texture was formed in the corrosion surface. By using scanning electron microscope (SEM )analysis ,it is revealed that the carbonation resistance mechanism was the membranous substance with dense mesh structure formed through rust preventer主要研究方向为油气田化学、油气田固完井工程。
电催化还原CO2生成多种产物催化剂研究进展

化工进展Chemical Industry and Engineering Progress2022年第41卷第3期电催化还原CO 2生成多种产物催化剂研究进展郑元波,张前,石坚,李佳霖,梅苏宁,余秦伟,杨建明,吕剑(西安近代化学研究所,氟氮化工资源高效开发与利用国家重点实验室,陕西西安710065)摘要:电催化还原CO 2生成含碳产物技术,能有效解决CO 2过量导致的温室效应及能源短缺问题。
但是,电催化还原CO 2会生成多种产物,因此,研究制备催化活性较好的高选择性催化剂是研究重点。
本文简述了电催化还原CO 2的基本原理、不同还原产物的形成途径、活性中间体、速控步及活性催化剂,分析了电催化还原CO 2生成不同产物存在的问题。
并且针对催化剂催化活性及催化反应过程中的这些问题,提出了提高催化剂催化活性的方法,总结了催化剂发展趋势,一般策略包括制造纳米结构材料、催化剂负载在高比表面积的载体上、杂原子掺杂、合金化、引入缺陷等,分析了这些方法通过改变电子传输等因素对催化剂活性及选择性的影响。
关键词:电催化;二氧化碳;还原产物;催化剂;改性中图分类号:TQ035文献标志码:A文章编号:1000-6613(2022)03-1209-15Research progress of catalysts for electrocatalytic reduction of CO 2tovarious productsZHENG Yuanbo ,ZHANG Qian ,SHI Jian ,LI Jialin ,MEI Suning ,YU Qinwei ,YANG Jianming ,LYU Jian(State Key Laboratory of Fluorine &Nitrogen Chemicals,Xi ’an Modern Chemistry Research Institute,Xi ’an 710065,Shaanxi,China)Abstract:The electrocatalytic reduction of carbon dioxide (CO 2)to produce carbon-containing products can effectively relieve the greenhouse effect and energy shortage caused by excessive CO 2.However,the electrocatalytic reduction of CO 2could form a variety of products simultaneously,and thus catalysts with both high selectivity and catalytic activity is the focus of such researches.This review briefly describes the basic principles of electrocatalytic reduction of CO 2,the formation pathways of different reductionproducts,the active intermediates,the rate control steps,the active catalysts.The existing problems arealso analyzed,and a method to improve the catalytic activity is proposed.The development trend of the catalyst is summarized and the common strategies include manufacturing nanostructured materials,supporting catalysts on carriers with high specific surface areas,heteroatom doping,alloying,andintroducing defects.The effects of changing the factors such as electron transport by using these methods on the catalyst activity and selectivity are analyzed.Keywords:electrocatalytic;carbon dioxide;reduction product;catalyst;modification综述与专论DOI :10.16085/j.issn.1000-6613.2021-1936收稿日期:2021-09-09;修改稿日期:2021-12-16。
溶胶-凝胶法制备Cu-ZnO-ZrO2催化剂:柠檬酸用量对催化剂性能的影响

等[7] 使用柠檬酸-硝酸盐自燃法改良纯金属和合金
合成技术,Wolf 等[8] 提出了甘氨酸-硝酸盐燃烧法
制备纯镍和铜镍合金的纳米粉末。柠檬酸在溶胶凝胶法制备催化剂的过程中主要有两个作用:一是
作为有机物在燃烧反应中充当燃料;另一个作用是
柠檬酸中的羧酸与金属硝酸盐溶液中的 Cu2+、Zn2+、
本文主要研究在初始ph及凝胶化温度一定的条件下从小于化学计量比等于化学计量比大于化学计量比改变柠檬酸加入量研究凝胶形成过程中cu2zn2zr4与柠檬酸的配位程度以及金属离子与柠檬酸相互交联缩聚逐渐形成三维立体网络结构的差异性对催化剂合成甲醇过程中性能的影响
化
进
展
CHEMICAL INDUSTRY AND ENGINEERING PROGRESS
降低 CO2 排放量并实现其资源化利用的有效手段之
一[1]。因 CO2 加氢合成甲醇反应不易发生,需要在
高温、高压、催化剂的条件下进行热化学反应,铜
基催化剂是目前使用最多的催化剂[2]。制备催化剂
的方法主要有共沉淀法、模板法、浸渍法、溶胶凝胶法,且每种方法都有各自的优缺点[3]。
目前,溶胶-凝胶自燃技术已成为制备高纯度
· 4033 ·
was dissociated from the three-dimensional network, so the grain sizes of the active components of CuO,
ZnO and ZrO2 in the catalyst can be regulated accordingly. When the molar amount of citric acid was
Binder effect on the catalytic activity of MoO3 bulk catalyst reduced by H2

Binder effect on the catalytic activity of MoO 3bulk catalyst reduced by H 2for n -heptanehydroisomerizationLaura Olivia Alemán-Vázquez a ,⇑,Fidencio Hernández-Pérez b ,JoséLuis Cano-Domínguez b ,Andrea Rodríguez-Hernández b ,JoséLuis García-Gutiérrez b ,⇑aInstituto Mexicano del Petróleo,Programa de Procesos de Transformación,Parque Industrial Canacintra,Carretera Pachuca-Cd,Sahagún km 7.5,42186Mineral de la Reforma,Hidalgo,Mexico bInstituto Mexicano del Petróleo,Programa de Procesos de Transformación,Eje Central Lázaro Cárdenas Norte 152,San Bartolo Atepehuacan,07730DF,Mexicoh i g h l i g h t sMoO 3bulk catalysts showed high activity for n -C 7hydroisomerization than MoO 3powder. MoO 3bulk catalyst with SiO 2shows low cracking and high selectivity to pentanes. No carbon deposits are observed in n -C 7hydroisomerization using MoO 3bulk catalysts.a r t i c l e i n f o Article history:Received 14February 2013Received in revised form 17August 2013Accepted 30August 2013Available online 13September 2013Keywords:Hydroisomerization Molybdenum trioxide n -Heptane Catalysis Bulk catalysta b s t r a c tTwo bulk catalysts containing about 70wt.%of molybdenum trioxide and alumina or silica as binder were prepared by a gel method.They were characterized by X-ray diffraction,Raman spectroscopy,TGA in air and textural properties.The MoO 3bulk catalysts were activated in situ by reduction with hydrogen and tested in the hydroisomerization of n -heptane using a fixed bed continuous flow microre-actor coupled to gas chromatograph.The highest catalytic activity for hydroisomerization was obtained with the alumina-based bulk catalyst,although the silica-based bulk catalyst showed lower amounts of cracking products and a higher selectivity to dimethylpentanes.The bulk catalysts resulted more active than MoO 3powder.The results indicate that the acid–base properties of the binder have a desirable effect on the acidity of the molybdenum trioxide powder as hydroisomerization catalyst.Ó2013Elsevier Ltd.All rights reserved.1.IntroductionThe alkanes present in the naphtha fraction of crude oils are predominantly linear or monobranched,and they must be con-verted into highly branched isomers or aromatic compounds through the isomerization and reforming processes in order to im-prove the octane number of gasolines.Existing technologies for isomerization of butane,pentane and hexane has not been applied to heptane and heavier alkanes because the formation of cracking products becomes too high as conversion increases.Molybdenum oxides are important compounds in catalysis.In the case of hydroisomerization,the catalytically active phase appears to be neither MoO 3nor MoO 2but rather a partially reduced molybde-num sub-oxide [1–3].This molybdenum sub-oxide,mixed with other reduction products,can be prepared directly from MoO 3by reduction at low temperature (623K)under flow of a mixture of H 2/n -heptane [1–3],being the reduction of MoO 3a crucial step in the generation of an active catalyst for hydroisomerization reac-tions [4–6].The structures of supported molybdenum oxide species are a function of the specific support,extent of surface hydration–dehy-dration [7–9],surface molybdenum oxide coverage,surface impu-rities,and calcination temperature.Under ambient conditions,the surface metal oxides are extensively hydrated by water molecules adsorbed on the support surfaces and,therefore,possess structures affected by surface water.At elevated temperatures,the catalyst surfaces are dehydrated,and the surface metal oxides undergo sig-nificant structural changes [10].There are many reports about the preparation procedure of supported MoO 3catalysts;the most common way to prepare a MoO 3-based catalyst is to impregnate a molybdenum precursor on the support and subsequent decomposition of this precursor to MoO 3via thermal treatment.The wet impregnation of ammonium heptamolybdate on silica,alumina or silica–alumina0016-2361/$-see front matter Ó2013Elsevier Ltd.All rights reserved./10.1016/j.fuel.2013.08.085⇑Corresponding authors.Tel.:+527717170615;fax:+527717163059.E-mail addresses:laleman@imp.mx (L.O.Alemán-Vázquez),garciajl@imp.mx (J.L.García-Gutiérrez).supports is commonly used for the preparation of MoO3-based cat-alysts[11–19].The details of the preparation method impact mark-edly on essential properties of thefinal catalytic material: morphology of the MoO3deposit,nature and proportion of molyb-denum oxide species,and interaction of molybdenum atoms with the support.In turn,these properties are seen as crucial parame-ters that dictate the performance of the catalyst.However,the intricate relationships between(i)the preparation parameters, (ii)the catalysts properties and,(iii)their activity,remain unclear. It is widely accepted for example that well-dispersed MoO x spe-cies,as opposed to MoO3crystals,are the precursors for active sites.Harsh thermal treatment might also promote the dispersion of molybdenum on the support[20,21]or provoke molybdenum losses.In general,molybdenum oxide is the active component of the catalyst and its loading is evidently crucial.In principle,the amount of active centers could be partially linked to the amount of molybdenum introduced in the formulation[22].Currently,our research group is working in the development of an efficient hydroisomerization process for the production of C6–C8 branched compounds[23–26].Thus,this work is focused on the study of the catalytic activity of H2-reduced MoO3in powder form and extruded with silica or alumina,bulk catalysts,in n-heptane isomerization in order to use as a support for industrial catalysts due to its outstanding surface and mechanical properties,and rel-atively low cost.In addition,the characterization of these catalysts by X-ray diffraction,Raman spectroscopy and textural properties, before and after reaction,was compared with that of powdered molybdenum trioxide evaluated at the same experimental condi-tions with the aim of understanding the reaction mechanisms in-volved in the hydroisomerization process.2.Experimental section2.1.General comments and materialUnless otherwise specified,all solvents and reagents were used without further purification.Molybdenum trioxide(99.5wt.%,Fer-mont),Molybdenum dioxide(99wt.%)boehmite(72.0wt.%,Sasol), formic acid(85.0wt.%,AyT),aqueous colloidal silica(40wt.%, Intercat),ethylene glycol(99wt.%,Aldrich),n-heptane(99.4 wt.%,Merck),hydrogen(99.999+%UHP,Praxair),nitrogen (99.9+%,Praxair).2.2.Catalyst preparationTwo bulk catalysts containing about70wt.%of molybdenum trioxide and alumina or silica as binder were prepared by a gel method.Thus,the required amounts of molybdenum trioxide and ethylene glycol were added to the corresponding amount of aqueous colloidal silica and mixed at296K,the excess water was evaporated by heating with vigorous stirring.When the mixture became too stiff to stir,the paste was extruded into rods of 2mm in diameter.The wet pellets were dried at286K overnight and at383K in air for6h,and then calcined at823K in air for 2h.In the case of alumina-based bulk catalyst,the boehmite was peptized with a1M aqueous solution of formic acid(0.4milli-equivalents of acid per gram of boehmite).The alumina-and sil-ica-based molybdenum catalysts were denoted as Mo–Al and Mo–Si,respectively.2.3.Catalytic experimentsThe catalytic experiments were carried out in afixed bed con-tinuousflow microreactor(stainless steel,9mm i.d.)coupled to gas chromatograph with aflame ionization detector(Agilent 6890equipped with a100-m PetrocTM DH column and Chem Sta-tion/Hydrocarbon ExpertTM PIANO software)for on-line analysis. The n-heptane and hydrogen were fed to the reactor by an Eldex metering pump and a Brooks5850E massflow controller, respectively.The reaction conditions of this study were established from our experimental results obtained previously[23–26]and those re-ported elsewhere[1–6].In a typical experiment,one gram of molybdenum trioxide with a particle size of about20m was intro-duced into the reactor under nitrogen atmosphere at296K and heated to623K at rate of4K/min,and then reduced by a stream of hydrogen(0.1L/min)under a pressure of2kg/cm2at623K for 24h.After hydrogen reduction,a stream of n-heptane(0.083ml/ min)was passed through the catalyst bed at17.5kg/cm2and 623K for12h;this stage is considered as an activation period. The hydroisomerization of n-heptane was performed at18.5kg/ cm2and643K.Reaction products were analyzed on-line by GC at2,4,6and8h of time on stream at643K.Finally,the reactor was cooled down to296K under nitrogenflow and then the cata-lyst was recovered and characterized.The alumina-and silica-sup-ported molybdenum catalysts were evaluated in the same conditions but using1.43gram of sample with a particle size of about20l m in order to maintain the relation of molybdenum trioxide.The catalytic activity of the catalysts was expressed as the transformation rate of n-heptane and the selectivity towards dim-ethylpentanes principally.Thus,the n-heptane conversion,dim-ethylpentanes selectivity and cracking selectivity were calculated using the following equations:Conversion¼ðn C07Àn C f7Þn C07wtwtÂ100Selectivity to dimethylpentanes¼C7isomersn C7wtwtÂ100 Selectivity to cracking¼Total crackingn C07Àn C f7wtwtÂ100where n C07and n C f7are the concentration of n-heptane compound (n-C7)at beginning and end of the catalytic tests,respectively.2.4.CharacterizationThe components of the materials were examined by X-ray dif-fraction(XRD)using a Siemens diffractometer(Model D5000)with Cu K a radiation and a Nifilter.The operating conditions were 35kV and25mA in the angular range4–50°in2h.Phase identifi-cation based on XRD patterns was aided by the ICDD-PDF-2 database.The Raman spectra were recorded in air at296K with a triple monochromator using a Raman spectrometer SPEX model1403 using an Ar+ion laser that delivered20mW of incident radiation. The excitation line of the laser was514.5nm.The Raman signal was detected with a photomultiplier and a standard photon count-ing system.The TGA was carried out with an analyzer Netzsch STA409PC/ PG using air(50mL/min)and20mg of sample,the heating rate was5K/min.Surface area,total pore volume and pore size distribution were determined by BET method using a Micromeritics ASAP-2401 system.The acidity of the catalysts was determined via pyridine and ammonia adsorption followed by diffuse reflectance FTIR spectros-copy using a Nicolet Protege460spectrometer.The spectra were collected in the range of4000–1000cmÀ1averaging50scans at464L.O.Alemán-Vázquez et al./Fuel117(2014)463–469an instrumental resolution of4cmÀ1.Prior toadsorption the sample powder was treated1.33Â10À3Pa and573K for1h and thentemperature.Subsequently,the sample wasor pyridine vapor andfinally heated at573Kfor1h.IR spectra were collected at different323,373,473,and573K.3.Results and discussion3.1.Catalyst characterizationThe X-ray diffraction pattern of the freshFig.1.All the diffraction peaks can be indexednamically stable orthorhombic phase a-MoO35–0508,a=0.3963nm,b=1.3856nm,c=Pbnm).According to the standard XRD pattern,sity of the peaks at2h=12.7,25.6and38.9°,diffraction of(020),(040)and(060)crystalanisotropic growth of the a-MoO3crystals in[27,28].The diffraction peaks with weak intensity at about 2h=23.3,27.2and49.6°,due to(110),(021)and(002)crystalplanes,indicate that crystal growth is slow in these direction.Thus, the MoO3structure consists of MoO6octahedral layers stacked along the[010]direction,favoring platelet crystallites oriented preferentially along this axis[29].The fresh samples of Mo–Si and Mo–Al(Fig.1)showed a similar diffraction pattern to that of the fresh MoO3,but the(020),(040)and(060)diffraction peaks shown an increase in intensity according to the following order: Mo–Al<Mo–Si<MoO3(Fig.1),that is,fresh Mo–Al displays a pat-tern characteristic of randomly oriented crystallites.It is interest-ing to note that the high surface area of the Mo–Si catalyst is due to the presence of amorphous silica in the material.Fig.2shows the XRD patterns corresponding to the spent cata-lysts of MoO3,Mo–Si and Mo–Al.The spent MoO3catalyst dis-the key step to generate the hydroisomerization activity[33]. The diffraction peak at about2h=41.0°is probably due to d(110)diffraction of molybdenum metal phase[34].Fig.3shows the Raman spectra corresponding to fresh samples of MoO3,Mo–Al and Mo–Si.It is observed that these spectra are constituted by several peaks located at992A g-v as(O@Mo),814 B1g-v(Mo A O A Mo),666B3g-v as(OMo3),470B1g-v(OMo3),379B1g-d(O A Mo A O),366A1g-d(O A Mo A O),291B3g-d(O@Mo@O),284 B2g-d(O@Mo@O),245B3g-d(O A Mo A O),217A g-d(O A Mo A O),199 B2g-s(O@Mo@O),156A g-d(O2Mo2)n,130and116cmÀ1(other deformation modes),in good agreement with the spectrum of a-MoO3crystalline phase reported previously[35–37].In general, the peak at992cmÀ1corresponds to the stretching vibration of the molybdenum–oxygen double bonds(terminal unshared oxy-gen atom)along the a-axis,which is indicative of the formation of the layered structure due to the fact that these units are only present in a-MoO3phase[38].The peak at814cmÀ1is for the stretching vibration involving two molybdenum atoms bonded to one oxygen atom(bridging oxygen atom),which results from corner-sharing oxygen atoms common to two MoO6octahedra. Meanwhile,the peak at666cmÀ1is assigned to the stretchingFig.1.X-ray diffraction of fresh catalysts.2.X-ray diffraction of spent catalysts after8h on stream at643K and18.5Fresh Mo-Alvibration of triply coordinated oxygen,which results from edge-shared oxygen atoms between three MoO6octahedra.The Raman spectrum of spent MoO3shows the following fea-tures(Fig.4):(a)Three broad peaks at992,814and666cmÀ1, which indicated the presence of MoO3.The broadening of these peaks suggests that the MoO3shows different degrees of crystalli-zation and/or a low ratio of oxygen to molybdenum[39].(b)Some initial very weak peaks corresponding to deformation and lattice modes of MoO3are not already observed in the spectrum,peaks at470,379,291,245,217,156and130cmÀ1.(c)Six new peaks ap-pear at728,558,490,354A g-d(O@Mo),340A g-d(OMo3),and 226cmÀ1A g-d(Mo A O A Mo),which are associated with the mono-clinic MoO2phase[35–37].Monoclinic MoO2has a rutile-type structure,which is built up by MoO6octahedra units connected by common edges in the direction of the formation of metal–metal bonds[40].In this context,recently,Ou et al.[41]reported the Ra-man spectrum of the H2-reduced MoO3,which shows following major changes,compared with that of the MoO3:(a)Peaks at 154and471cmÀ1vanished;(b)Intensities of peaks at284,666, 821and993cmÀ1reduced;(c)The appearance of a new MoO x H y (hydrogen molybdenum bronze)peak at about204cmÀ1(defor-mation mode)[42].Thus,the spent MoO3catalyst is composed by a mixture of the a-MoO3,monoclinic MoO2and MoO x H y.More-over,the intensity of the two wagging modes at284and291cmÀ1 changed significantly compared with those of the fresh samples, which suggests the presence of oxygen defects preferably in the edge of lamella[43,44],which can promote the catalytic activities. On the other hand,the spent Mo–Si and Mo–Al catalysts show spectra similar to that of the spent MoO3,but some changes are ob-served:(a)Intensities of peaks at666,340,284,204and146cmÀ1 decreased,more evident for spent Mo–Si sample.(b)Intensities of peaks at354and217cmÀ1increased,more appreciable for spent Mo–Al sample.It is interesting to point out that for the three cat-alysts evaluated the XRD and Raman spectra do not indicate the formation of carbonaceous deposits under the experimental condi-tions of this work.In order to corroborate the absence of coke on the spent cata-lyst,the TGA in air of these samples and pure MoO2was carried out(Fig.5).The TGA of MoO2shows three stages of weight gain: (i)An increase of0.61wt.%at the range of373–560K,which can be attributed to adsorption of oxygen.(ii)An increase of 0.80wt.%at around560–594K due to the formation of Mo18O52-type structure[45,46].(iii)A rapid increase of10.90wt.%at tem-peratures between594and800K,which is generated by formationMoO3.The total weight gain of12.30%is in agreement with the calculated value for the oxidation of MoO2to MoO3.Similar results for the oxidation of MoO2to MoO3were obtained by Ressler et al. [45,46],whom observed the formation of a Mo18O52-type structure at373K,with a maximum formation of4.01%at about630K,fol-lowed by a very rapid and complete oxidation of both MoO2and Mo18O52to MoO3in the range of630–710K.By other hand,the TGA of the all spent samples show three stages similar to those of MoO2,namely:(i)At about293–560K,mainly at temperatures below440K,a weight loss due to desorption of water retained in the catalyst during the hydroisomerization process,the formation of water by the reaction between gaseous oxygen and hydrogen contained in the catalyst[47,48],and/or the decomposition of a bronze compound[49,50].(ii)At the range of560–650K,the spent MoO3sample shows an increase of about1.19wt.%due to forma-tion of the Mo18O52-type structure[45,46];the samples of Mo–Si and Mo–Al do not show the presence of Mo18O52-type structure, which may be due to the binder.(iii)At about650–800K,it is ob-served a rapid weight gain due to formation of MoO3.The total weight gain for the spent samples of MoO3,Mo–Si and Mo–Al is 7.63,7.21and5.24wt.%,respectively.These weight gains indicate that the amount of MoO2in the spent samples with respect to the MoO3in the fresh samples was61.70%,83.31%and60.55%to MoO3,Mo–Si and Mo–Al,respectively.The form of the TGA curves indicated the presence of a three dimensional diffusion controlled regime during the regeneration[45].In general,it is reported that during the TPO analysis,the combustion of coke deposited on metallic site and on the support show peaks in the temperature ranges of623–723K and723–873K,respectively[51–53].Thus, the formation of coke on the spent catalysts can be rejected due to the absence of their corresponding signals in the TGA profiles.The textural properties of the catalysts both fresh and spent are showed in Table1.The fresh molybdenum trioxide powder pre-sented a low specific surface area(0.73m2/g),which after8h on stream increased to50.4m2/g.Enlargement of the surface area was caused by formation of pores with volume of about4.Raman spectra of spent catalysts after8h on stream at643K and18.5Fig.5.TGA in air of the spent catalysts.Table1Textural properties of the MoO3,Mo–Si and Mo–Al catalysts.Sample Specific area(m2/g)Pore volume(cm3/g)Pore diameter(Å)Fresh MoO30.730.000738.6Fresh Mo–Si23.10.0679120.8Fresh Mo–Al920.14763.8Spent MoO350.40.04737.2Spent Mo–Si36.10.092101.4Spent Mo–Al116.50.17861.20.047cm3/g.This development of the surface area reveals that strong modifications in the structure of the catalyst occur.This behavior is also observed in the Mo–Si and Mo–Al catalyst.In this work we carried out the H2reduction MoO3according to our previously described method;[26].This catalytic system showed after about10h of time on stream a high conversion of n-heptane(ca.72%)for long time(at least164h)compared to pre-vious works[54–56].Thus,It may consider that the catalyst reached their maximum textural properties under our experimen-tal conditions.In this context,it is reported that the increase of surface area and pore volume of the catalysts during the hydroisomerization process may due to two effects:(i)The formation of a bronze phase,H x MoO3[6,47],and(ii)The collapse of MoO3orthorhombic layered structure into the monoclinic structure of MoO2[31,45,57–59].In thefirst case,it is suggested that H2reduction MoO3at about623K generates a bronze phase,H x MoO3.The bronze phase can be decomposed by an increase of hydrogen in its structure to the molybdenum oxyhydride,MoO x H y,which produces an increase in the surface area due to the formation of pores(micropores) [6,47].The surface area changes markedly,depending on reduction temperature.The decomposition of the bronze phase does not involve the formation of MoO2when is carried out at about 623K.,but these decomposed to Mo4O11and MoO2at about 673K[50,60,61].It should mentioned that MoO2synthesized by MoO3reduction does not develop any microporosity due to the fact that the transformation is not topotactic[62].The second case in-volves the elimination of water from two adjacent OH groups on the(010)plane of MoO3,which are formed from the adsorption and dissociation of hydrogen.The elimination of water generates an increase of oxygen vacancies on the surface,which provokes the formation of crystallographic shear planes in order to stabilize the lattice by removal of point defects.Thus,the resulting molyb-denum sub-oxide,MoO3Àx,shows a disordered shear structure with a MoO3matrix interrupted by irregularly spaced shear planes [24].In order to know more about the MoO3catalysts,the acid prop-erties of these samples were determined by ammonia and pyridine adsorption followed by Fourier transform infrared spectroscopy was carried out(Table2).The ammonia adsorption of the fresh and spent Mo–Si was not performed.In general,the results are in accordance with others studies[63–66].We observed the follow-ing facts:(i)The spent MoO3,spent Mo–Al,spent Mo–Si and MoO2do not show pyridine adsorption under our experimental conditions.(ii)The fresh MoO3does not show pyridine adsorption due to the small pore size of its structure,which restricts diffusion of large molecules into the pore.(iii)The fresh Mo–Si shows strong Lewis acid sites,the fresh Mo–Al shows weak Lewis acid sites.(iv) The fresh Mo–Al has more strong Brönsted acid sites than fresh Mo–Si.(v)The Lewis and Brönsted acid site of the fresh Mo–Al and the fresh Mo–Si are eliminated during and/or after the hydro-isomerization process.(vi)The total acidity(acid sites by ammonia adsorption)of the fresh MoO3at about473–573K(strong acidity) is similar to that of fresh Mo–Al.(vii)The total acidity of the spent MoO3and the spent Mo–Al is similar to that(weak acidity)of MoO2.These facts indicate that the presence of strong Brönsted acid sites in the fresh MoO3phase is important for a good activity of the catalyst in the hydroisomerization process.The strong Lewis acid sites do not appear to strongly influence the catalytic activity. The weak and strong Brönsted acid sites are transformed to water during the process of activation and hydroisomerization, respectively.Thus,the elimination of Bönsted acid sites causesTable2Ammonia and pyridine adsorption followed by FTIR spectroscopy.The values arereferred to the integrated area of the signal.Temperature296K373K473K573KAmmonia adsorptionCatalystFresh MoO348.1337.5716.7610.03Spent MoO38.7 5.69Fresh Mo–Al25.2923.6114.29.64Spent Mo–Al 2.71 5.04MoO2 2.16 4.6Pyridine adsorption,Lewis acidFresh Mo–Al0.230.08Fresh Mo–Si0.830.680.250.08Pyridine adsorption,Brönsted acidFresh Mo–Al0.270.290.260.14Fresh Mo–Si0.420.370.20.05Table3n-Heptane isomerization over MoO3,Mo–Si and Mo–Al catalysts.Parameter MoO3Mo–Al Mo–SiTime on stream(h)246824682468 Temperature(K)643643643643643643643643643643643643 Pressure(bar)18.518.518.518.518.518.518.518.518.518.518.518.5Composition(wt.%)2-2-Dimethylpentane0.080.190.290.310.160.340.510.560.150.270.380.42 2,4-Dimethylpentane 1.48 2.27 2.76 2.94 2.21 2.67 3.00 2.99 1.33 1.48 1.67 1.71 2,2,3-Trimethylbutane0.110.190.250.260.110.130.150.150.060.060.070.08 3,3-Dimethylpentane0.420.80 1.03 1.130.630.88 1.00 1.010.390.460.550.60 2-Methylhexane8.7413.6716.2317.2816.7020.3221.3121.3411.6013.7315.2115.89 2,3-Dimethylpentane 2.48 3.92 4.67 4.94 3.75 4.76 5.08 5.02 2.34 2.69 3.01 3.17 3-Methylhexane9.1614.8517.7918.9918.1022.9924.0824.1712.7815.5617.4218.43 3-Ethylpentane0.06 1.20 1.45 1.54 1.40 1.86 1.95 1.96 1.01 1.24 1.40 1.50 n-Heptane(99.4wt.%)72.5155.7846.8942.6553.6641.9938.2337.8668.0762.0557.2855.05 Total C7products(wt.%)95.0592.8791.3590.0596.7495.9395.3195.0697.7297.5497.0096.85 Conversion(%)27.0643.8852.8357.0946.0157.7661.5461.9131.5237.5842.3844.62 Selectivity to hydroisomerization(%)95.6293.4391.9090.5997.3296.5095.8895.6298.3198.1396.1797.43Cracked products(%)C6+C10.150.280.570.640.190.360.540.590.120.180.270.33 C5+C20.90 1.69 2.10 2.290.580.720.770.880.350.430.600.63 C4+C3 1.80 3.05 3.47 4.360.880.95 1.05 1.120.520.540.680.69 Total cracking(wt.%) 2.85 5.02 6.147.28 1.65 2.02 2.36 2.590.99 1.15 1.56 1.65 Selectivity to cracking(%)10.5911.5011.6812.84 3.61 3.52 3.87 4.21 3.16 3.08 3.70 3.73 Others(wt.%) 1.81 1.81 2.510.53 1.49 1.90 2.17 2.060.96 1.02 1.14 1.16L.O.Alemán-Vázquez et al./Fuel117(2014)463–469467the formation of Lewis acid sites,which has been reported else-where [65].The fact that the catalysts do not exhibit any strong Brönsted acid sites after may due to its instability at atmospheric conditions,which lead to the formation of more stables phases,i.e.,MoO 2.3.2.Catalytic testTable 3and Figs.6–8show the n -heptane conversion,cracking selectivity and dimethylpentanes selectivity versus the time on stream.The n -heptane conversion using MoO 3powder was negligi-ble at the beginning of the test;subsequently the conversion slowly increased with time on stream,after 8h corresponding to a conversion of 62%(Fig.6).The Mo–Si and Mo–Al catalyst show similar behavior for the conversion of n -heptane.The conversion of n -heptane using Mo–Si and Mo–Al at 8h of time on stream was 58%and 70%respectively.The hydrocracking selectivity using MoO 3powder at 2and 8h of time on stream was 11%and 13%,respectively;the Mo–Si and Mo–Al catalysts shown a hydrocrack-ing selectivity of 4%and 6%all time (Fig.7).Table 3shows the selectivity of the three catalysts (Fig.8).In all three cases,it is ob-served that monobranched isomers were produced rapidly and predominated at all conversions,their yield increases proportion-ally to the n -heptane conversion.Monobranched isomers are pri-mary products of the reaction.The selectivity in multibranched,which is low at low conversion,also increases with the conversion.These observations suggest that the formation of multibranched products,for the most part,is consecutive to the formation of monobranched isomers [26].The Mo–Al catalyst showed the best hydroisomerization selectivity.In general,the effect of the binder is evident,that is,the silica and alumina promote a decrease in the amount of cracking products with respect to the molybdenumtrioxide powder.Thus,based on the results indicated above,we proposed the formation of a bifunctional catalyst,being the acidic function necessary to hydrocrack C 7molecules and the metallic function necessary to de-and hydrogenate the C 5–C 3products gen-erated during the hydrocracking to olefinic products.4.ConclusionTwo bulk catalysts containing about 70wt.%of molybdenum trioxide and alumina or silica as binder were prepared by a gel method.The bulk catalysts resulted more active than MoO 3pow-der.The highest activity was obtained with MoO 3bulk catalyst with Al 2O 3as binder,although the MoO 3bulk catalyst with SiO 2shows lower amounts of cracking products and a higher selectivity to dimethylpentanes.The characterization suggests that insertion of hydrogen atoms into the lattice of MoO 3leads to the formation of MoO x H y ,which is the key step to generate the hydroisomeriza-tion activity.Likewise,for the three catalysts,the XRD,Raman spectra and TGA in air do not indicate the formation of carbona-ceous deposits under the experimental conditions of this work.The acid properties of the catalysts indicate that the presence of strong Brönsted acid sites in the fresh MoO 3phase is important for a good activity of the catalyst in the hydroisomerization pro-cess.Likewise,the results indicate that the acid–base properties of the binder have an influence on the activity of the molybdenum trioxide as hydroisomerization catalyst.For practical application Mo–Si catalyst has advantages of both improved mechanical strength and high catalytic properties over the MoO 3.References[1]Ledoux MJ,Del Gallo P,Pham-Huu C,York APE.Molybdenum oxycarbideisomerization catalysts for cleaner fuel production.Catal Today 1996;27:145–50.[2]Blekkan EA,Pham-Huu C,Ledoux MJ,Guille J.Isomerization of n -heptane on anoxygen-modified molybdenum carbide catalyst.Ind Eng Chem Res 1994;33:1657–64.[3]Ledoux MJ,Guille J,Pham-Huu C,Blekkan EA,Peschiera E.Process for theisomerization of straight hydrocarbons containing at least 7carbon atoms using catalysts with a base of molybdenum Patent 5,576,4661996.[4]Ledoux MJ,Meunier F,Heinrich B,Pham-Huu C,Harlin ME,Krause AOI.Part I.n -butane dehydrogenation on unsupported carbon modified MoO 3(MoO x C y ):effect of steam on the catalyst stability.Appl Catal A Gen 1999;181:157–70.[5]Delporte P,Pham-Huu C,Ledoux MJ.Effect of the reaction temperature andhydrocarbon partial pressure on the activity of carbon-modified MoO 3for n -hexane isomerization.Appl Catal A Gen 1997;149:151–80.[6]Bouchy C,Pham-Huu C,Heinrich B,Chaumont C,Ledoux MJ.Microstructureand characterization of a highly selective catalyst for the isomerization of alkanes:a molybdenum oxycarbide.J Catal 2000;190:92–103.[7]Fransen T,Mars P,Gellings PJ.Monolayer and crystal type MoO 3catalysts:their catalytic properties in relation to their surface structures.J Colloid Interface Sci 1979;70:97–104.468L.O.Alemán-Vázquez et al./Fuel 117(2014)463–469。
Hydrogen from catalytic reforming of biomass-derived hydrocarbons in liquid water
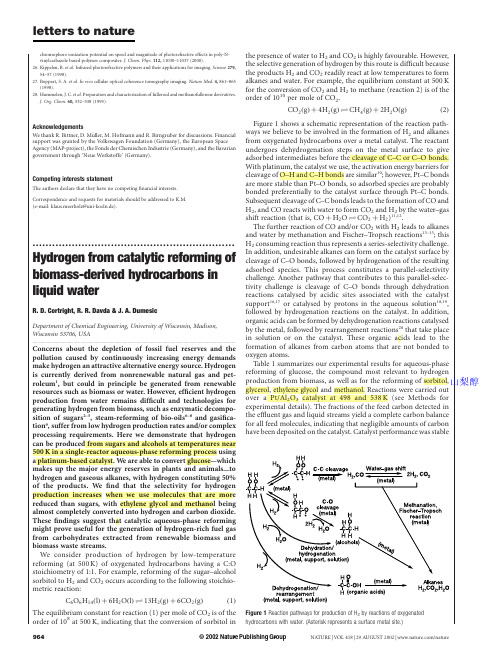
chromophore ionization potential on speed and magnitude of photorefractive effects in poly-N-vinylcarbazole based polymer composites.J.Chem.Phys.112,11030–11037(2000).26.Kippelen,B.et al.Infrared photorefractive polymers and their applications for imaging.Science 279,54–57(1998).27.Boppart,S.A.et al.In vivo cellular optical coherence tomography imaging.Nature Med.4,861–865(1998).28.Hummelen,J.C.et al .Preparation and characterization of fulleroid and methanofullerene .Chem.60,532–538(1995).AcknowledgementsWe thank R.Bittner,D.Mu¨ller,M.Hofmann and R.Birngruber for discussions.Financial support was granted by the Volkswagen Foundation (Germany),the European Space Agency (MAP-project),the Fonds der Chemischen Industrie (Germany),and the Bavarian government through ‘Neue Werkstoffe’(Germany).Competing interests statementThe authors declare that they have no competing financial interests.Correspondence and requests for materials should be addressed to K.M.(e-mail:klaus.meerholz@uni-koeln.de)...............................................................Hydrogen from catalytic reforming of biomass-derived hydrocarbons in liquid waterR.D.Cortright,R.R.Davda &J.A.DumesicDepartment of Chemical Engineering,University of Wisconsin,Madison,Wisconsin 53706,USA.............................................................................................................................................................................Concerns about the depletion of fossil fuel reserves and the pollution caused by continuously increasing energy demands make hydrogen an attractive alternative energy source.Hydrogen is currently derived from nonrenewable natural gas and pet-roleum 1,but could in principle be generated from renewable resources such as biomass or water.However,efficient hydrogen production from water remains difficult and technologies for generating hydrogen from biomass,such as enzymatic decompo-sition of sugars 2–5,steam-reforming of bio-oils 6–8and gasifica-tion 9,suffer from low hydrogen production rates and/or complexprocessing requirements.Here we demonstrate that hydrogen can be produced from sugars and alcohols at temperatures near 500K in a single-reactor aqueous-phase reforming process using a platinum-based catalyst.We are able to convert glucose —which makes up the major energy reserves in plants and animals —to hydrogen and gaseous alkanes,with hydrogen constituting 50%of the products.We find that the selectivity for hydrogen production increases when we use molecules that are more reduced than sugars,with ethylene glycol and methanol being almost completely converted into hydrogen and carbon dioxide.These findings suggest that catalytic aqueous-phase reforming might prove useful for the generation of hydrogen-rich fuel gas from carbohydrates extracted from renewable biomass and biomass waste streams.We consider production of hydrogen by low-temperature reforming (at 500K)of oxygenated hydrocarbons having a C:O stoichiometry of 1:1.For example,reforming of the sugar–alcohol sorbitol to H 2and CO 2occurs according to the following stoichio-metric reaction:C 6O 6H 14ðl Þþ6H 2O ðl ÞO 13H 2ðg Þþ6CO 2ðg Þð1ÞThe equilibrium constant for reaction (1)per mole of CO 2is of the order of 108at 500K,indicating that the conversion of sorbitol inthe presence of water to H 2and CO 2is highly favourable.However,the selective generation of hydrogen by this route is difficult because the products H 2and CO 2readily react at low temperatures to form alkanes and water.For example,the equilibrium constant at 500K for the conversion of CO 2and H 2to methane (reaction 2)is of the order of 1010per mole of CO 2.CO 2ðg Þþ4H 2ðg ÞO CH 4ðg Þþ2H 2O ðg Þð2ÞFigure 1shows a schematic representation of the reaction path-ways we believe to be involved in the formation of H 2and alkanes from oxygenated hydrocarbons over a metal catalyst.The reactant undergoes dehydrogenation steps on the metal surface to give adsorbed intermediates before the cleavage of C–C or C–O bonds.With platinum,the catalyst we use,the activation energy barriers for cleavage of O–H and C–H bonds are similar 10;however,Pt–C bonds are more stable than Pt–O bonds,so adsorbed species are probably bonded preferentially to the catalyst surface through Pt–C bonds.Subsequent cleavage of C–C bonds leads to the formation of CO and H 2,and CO reacts with water to form CO 2and H 2by the water–gas shift reaction (that is,CO þH 2O O CO 2þH 2)11,12.The further reaction of CO and/or CO 2with H 2leads to alkanes and water by methanation and Fischer–Tropsch reactions 13–15;this H 2consuming reaction thus represents a series-selectivity challenge.In addition,undesirable alkanes can form on the catalyst surface by cleavage of C–O bonds,followed by hydrogenation of the resulting adsorbed species.This process constitutes a parallel-selectivity challenge.Another pathway that contributes to this parallel-selec-tivity challenge is cleavage of C–O bonds through dehydration reactions catalysed by acidic sites associated with the catalyst support 16,17or catalysed by protons in the aqueous solution 18,19,followed by hydrogenation reactions on the catalyst.In addition,organic acids can be formed by dehydrogenation reactions catalysed by the metal,followed by rearrangement reactions 20that take place in solution or on the catalyst.These organic acids lead to the formation of alkanes from carbon atoms that are not bonded to oxygen atoms.Table 1summarizes our experimental results for aqueous-phase reforming of glucose,the compound most relevant to hydrogenproduction from biomass,as well as for the reforming of sorbitol,glycerol,ethylene glycol and methanol.Reactions were carried out over a Pt/Al 2O 3catalyst at 498and 538K (see Methods for experimental details).The fractions of the feed carbon detected in the effluent gas and liquid streams yield a complete carbon balance for all feed molecules,indicating that negligible amounts of carbon have been deposited on the catalyst.Catalyst performance was stableFigure 1Reaction pathways for production of H 2by reactions of oxygenated hydrocarbons with water.(Asterisk represents a surface metal site.)山梨醇for long periods of time on stream(for example,1week).Results from replicate runs agree to within^3%.The hydrogen selectivities shown in Table1are defined as the number of H2molecules detected in the effluent gas,normalized by the number of H2molecules that would be present if the carbon atoms detected in the effluent gas molecules had all participated in the reforming reaction.(That is,we infer the amount of converted glucose,sorbitol,glycerol,ethylene glycol and methanol from the carbon-containing gas-phase products and assume that each of the feed molecules would yield2,13/6,7/3,5/2or3molecules of H2, respectively.)Alkane selectivity is defined as the number of carbon atoms in the gaseous alkane products normalized by the total number of carbon atoms in the gaseous effluent stream.Figure2illustrates that the selectivity for H2production improves in the order glucose,sorbitol,glycerol, ethylene glycol,methanol:Figure2also implies that lower oper-ating temperatures result in higher H2selectivities,although this trend is in part due to the lower conversions achieved at lower temperatures.The selectivity for alkane production follows a trend with respect to reactant that is opposite to that exhibited by the H2 selectivity.The gas streams from aqueous-phase reforming of the oxygenated hydrocarbons were found to contain low levels of CO(that is,less than300p.p.m.).For aqueous-phase reforming of glycerol,where analysis of liquid-phase products is more tractable compared to sorbitol and glucose,the major reaction intermediates detected include(in approximate order of decreasing concentration)ethanol, 1,2-propanediol,methanol,1-propanol,acetic acid,ethylene glycol, acetol,2-propanol,propionic acid,acetone,propionaldehyde,and lactic acid.Analysis of the gas phase effluent indicates the presence of trace amounts of methanol and ethanol(about300p.p.m.).High hydrogen yields are only obtained when using sorbitol, glycerol and ethylene glycol as feed molecules for aqueous-phase reforming.Although these molecules can be derived from renew-able feedstocks21–24,the reforming of less reduced and more immediately available compounds such as glucose is likely to be more practical;but hydrogen yields for glucose reforming are relatively low(Table1and Fig.2).However,we expect that improvements in catalyst performance,reactor design,and reaction conditions may increase the hydrogen selectivity for the direct aqueous-phase reforming of sugars.For example,the lower H2 selectivities for the aqueous-phase reforming of glucose,compared to that achieved using the other oxygenated hydrocarbon reactants, are caused at least partially by homogeneous reactions of glucose in the aqueous phase at the temperatures used in this study19.Thus, higher selectivities for H2from aqueous-phase reforming of glucose might be achieved by reactor designs that maximize the number of catalytically active sites(leading to desirable surface reactions)and minimize the void volume(leading to undesirable liquid-phase reactions)in the reactor.Here,using Pt/Al2O3as catalyst,we found that lower glucose concentrations correlated with higher selectivities for hydrogen production,and reforming experiments were therefore conducted at low feed concentrations of1wt%,which corresponds to a molar ratio H2O/C1of165.Processing such dilute solutions is economi-cally not practical,even though reasonably high hydrogen yields are achieved(Table1).However,undesirable homogeneous reactions, as observed with glucose,pose less of a problem when using sorbitol, glycerol,ethylene glycol and methanol,which makes it possible to generate high yields of hydrogen by the aqueous-phase reforming of more concentrated solutions containing these compounds.For example,we have found that upon increasing the feed concen-trations of ethylene glycol or glycerol to10wt%(molar ratio H2O/ C1¼15),it is still possible to achieve high conversions and high selectivities for H2production.(A hydrogen selectivity of97%was achieved with62%conversion of10wt%ethylene glycol;and a hydrogen selectivity of70%was achieved with77%conversion of 10wt%glycerol.)A molar H2O/C1ratio of15is still higher than that typically utilized in conventional vapour-phase reforming of hydro-carbons(molar H2O/C1¼3to5);but our aqueous-phase reform-ing system has the advantage of not requiring energy-intensive vaporization of water to generate steam.Operating at higher reactant concentrations and lower conver-sion levels leads to higher rates of hydrogen production.Rates of hydrogen production are measured as turnover frequencies(that is, rates normalized by the number of surface metal atoms as deter-mined from the irreversible uptake of CO at300K).For example, the turnover frequency for production of hydrogen at498K from a 1wt%ethylene glycol solution is0.08min21for the90%conversion run listed in Table1(weight-hourly space velocity, WHSV¼0.008g of ethylene glycol per g of catalyst per h),but increases to0.7min21for a feed containing10wt%ethylene glycol (run at498K and at a higher WHSVof0.12g of ethylene glycol per g of catalyst per h).The hydrogen selectivity for this latter run is equal to97%at a conversion of62%.The turnover frequency for hydrogen production from10wt%ethylene glycol at498K increased further to7min21when higher space-velocities were used(WHSV¼18g of ethylene glycol per g of catalyst per h)with a highly dispersed3wt%Pt/Al2O3catalyst consisting of smaller alumina particles(63–125m m)to minimize transport limitations. The hydrogen selectivity for this kinetically controlled run was99% at a conversion of3.5%.The rates of formation of H2from aqueous-phase reforming of 10wt%glucose,sorbitol,glycerol,ethylene glycol and methanol at 498K over a3wt%Pt/Al2O3catalyst under conditions to minimize transport limitations and at low conversions of the reactant haveTable1Experimental data for reforming of oxygenated hydrocarbonsGlucose Sorbitol Glycerol Ethylene glycol Methanol ................................................................................................................................................................................................................................................................................................................................................................... Temperature(K)498538498538498538498538498538 Pressure(bar)29562956295629562956 %Carbon in liquid-phase effluent5115391217 2.811 2.9 6.5 6.4 %Carbon in gas-phase effluent50846190839990999494 Gas-phase compositionH2(mol.%)5146615464.8577068.774.674.8 CO2(mol.%)4342353629.73229.1292524.6 CH4(mol.%) 4.07.0 2.5 6.0 4.28.30.8 2.00.40.6 C2H6(mol.%) 2.0 2.70.7 2.30.9 2.00.10.30.00.0 C3H8(mol.%)0.0 1.00.8 1.00.40.70.00.00.00.0 C4,C5,C6alkanes(mol.%)0.0 1.20.00.60.00.00.00.00.00.0 %H2selectivity*50366646755196889999 %Alkane selectivity†14331532193148 1.7 2.7 ................................................................................................................................................................................................................................................................................................................................................................... The catalyst was loaded in a tubular reactor,housed in a furnace,and reduced prior to reaction kinetics studies.The reactor system was pressurized with N2,and the reforming reaction was carried out at the listed reaction conditions.Each reaction condition was run for24h,during which the experimental data were collected.Further experimental details are provided in the Methods.*%H2selectivity¼(molecules H2produced/C atoms in gas phase)(1/RR)£100,where RR is the H2/CO2reforming ratio,which depends on the reactant compound.RR values for the compounds are: glucose,2;sorbitol,13/6;glycerol,7/3;ethylene glycol,5/2;methanol,3.We note that H2and alkane selectivities do not add up to100%,because they are based independently on H-balances and C-balances,respectively.%Carbon in gas and liquid phase effluents add to100%for a complete carbon balance.Slight^deviations from100%are caused by experimental error.†%Alkane selectivity¼(C atoms in gaseous alkanes/total C atoms in gas phase product)£100.been measured to be 0.5,1.0,3.5,7.0and 7.0min 21,respectively.These turnover frequencies correspond to hydrogen production rates of 50,100,350,700,and 700l of H 2(at standard temperature and pressure,273K and 1.01bar)per l of reactor volume per h for each feed molecule,respectively.These rates compare favourably to the maximum rate of hydrogen production from glucose of about 5£1023l of H 2per l of reactor volume per hour by enzymatic routes 5.Normalization of the rates by the mass of catalyst used yields rates of about 3£103,6£103,2£104,4£104,and 4£104m mol g 21h 21for hydrogen production at 498K,from 10wt%glucose,sorbitol,glycerol,ethylene glycol and methanol,respect-ively.These rates can be compared to the maximum value of 7£102m mol g 21h 21reported for hydrogen production from glucose by enzymatic routes.(For this comparison,we have assumed a typical value of 100units per mg of protein,where a unit of enzyme activity corresponds to the amount of enzyme which under stan-dard assay conditions converts 1m mol of substrate per min).If the hydrogen produced were fed to a fuel cell operating at 50%efficiency,the rate of hydrogen production in our reformer would generate approximately 1kW of power per l of reactor volume.Electrical power might thus be generated cost-effectively by an integrated fuel-cell/liquid-phase reformer system fed with a low-cost carbohydrate stream derived from waste biomass (for example,corn stover,wheat straw,wood waste).The practical use of aqueous-phase reforming reactions in this manner would depend on efficient feed recycling strategies and on efficient separation of hydrogen from the gaseous effluent stream.The gaseous effluents separated from the main product hydrogen could be combusted to generate the energy necessary for the liquid-phase-reforming reactor.How-ever,some fuel cell applications might not require extensive puri-fication because the main components in the reformer gas effluent other than hydrogen are CO 2and methane,which can act as diluents 25.Alcohols and organic acids are also present in the gas effluent,but only at trace levels (300p.p.m.and about 5p.p.m.,respectively)which may not lead to irreversible poisoning 26.Reforming reactions between hydrocarbons and water to gen-erate hydrogen are endothermic,and conventional steam-reforming of petroleum thus depends on the combustion of additional hydrocarbons to provide the heat needed to drive the reforming reaction.In contrast,the energy required for the aqueous-phase reforming of oxygenated hydrocarbons may be produced intern-ally,by allowing a fraction of the oxygenated compound to form alkanes through exothermic reaction pathways.In this respect,theformation of a mixture of hydrogen and alkanes from aqueous-phase reforming of glucose,as accomplished in the present study,is essentially neutral energetically,and little additional energy is required to drive the reaction.In fact,the energy contained in these alkanes could be used as a feed to an internal combustion engine or suitable fuel cell;this would allow the use of biomass-derived energy to drive the aqueous-phase reforming of glucose (and biomass more generally)with high yields to renewable energy.While the present findings establish that Pt-based catalysts show high activities and good selectivity for the production of hydrogen from sugars and alcohols by aqueous-phase reforming reactions,improvements are necessary to render the process useful.Highly active catalytic materials that can satisfy the series and parallel selectivity challenges outlined in Fig.1,but at a lower materials cost than for Pt,are particularly desirable.Moreover,new combinations of catalysts and reactor configurations are needed to obtain higher hydrogen yields from more concentrated solutions of glucose,given that glucose is the only compound we have tested that is directly relevant to biomass utilization.We believe that such improvements are possible,for example,by searching for catalysts that exhibit higher activity at lower temperatures,to minimize the deleterious effects of homogeneous decomposition reactions.AMethodsExperiments for the aqueous-phase reforming of glucose,sorbitol,glycerol,ethylene glycol and methanol were performed over a 3wt%Pt catalyst supported on nanofibres of g -alumina (500m 2g 21,Argonide Corp.).The catalyst was prepared by incipient wetness impregnation of alumina with tetraamine platinum nitrate solution,followed by drying at 380K,calcination at 533K in flowing oxygen and reduction at 533K in flowing hydrogen.Chemisorption experiments using carbon monoxide at 300K showed a CO uptake of 105m mol per g of catalyst.A stainless steel tubular reactor (having an inner diameter of 5mm and length of 45cm)was loaded with 4.5g of the pelletized Pt/Al 2O 3catalyst,which was then reduced under flowing hydrogen at 533K.The total pressure of the system was then increased by addition of nitrogen to a value slightly higher than the vapour pressure of water at the reaction temperature.The system pressure was controlled by a backpressure regulator.An aqueous solution containing 1wt%of the oxygenated compound was fed continuously,using a high-performance liquid chromatography (HPLC)pump,at 3.6ml h 21into the reactor heated to the desired reaction temperature.Under these conditions,the WHSV was 0.008g of oxygenated compound per g of catalyst per h through the reactor.The effluent from the reactor was water-cooled in a double-pipe heat exchanger to liquefy the condensable vapours.The fluid from this cooler was combined with the nitrogen make-up gas at the top of the cooler,and the gas and liquid were separated in a stainless-steel vessel (about 130cm 3)maintained at the system pressure.The effluent liquid was drained periodically (every 12h)for total organic carbon (TOC)analysis and for detection of the primary carbonaceous species using gas chromatography and HPLC.The effluent gas stream passed through the back-pressure regulator and was analysed with several online gas chromatographs.The kinetic data for each reaction condition were typically collected over a 24-h period,after which the reaction conditions were changed.The catalyst performance was stable for times on stream of at least 1week.Received 6February;accepted 23July 2002;doi:10.1038/nature01009.1.Rostrup-Nielsen,J.Conversion of hydrocarbons and alcohols for fuel cells.Phys.Chem.Chem.Phys.3,283–288(2001).2.Kumar,N.&Das,D.Enhancement of hydrogen production by enterobacter cloacae IIT-BT 08.ProcessBiochem.35,589–593(2000).3.Woodward,J.et al.Enzymatic hydrogen production:Conversion of renewable resources for energyproduction.Energy Fuels 14,197–201(2000).4.Yokoi,H.et al.Microbial hydrogen production from sweet potato starch residue.J.Biosci.Bioeng.91,58–63(2001).5.Woodward,J.,Orr,M.,Cordray,K.&Greenbaum,E.Enzymatic production of biohydrogen.Nature405,1014(2000).6.Garcia,L.,French,R.,Czernik,S.&Chornet,E.Catalytic steam reforming of bio-oils for theproduction of hydrogen:Effects of catalyst composition.Appl.Catal.A 201,225–239(2000).7.Amphlett,J.C.,Leclerc,S.,Mann,R.F.,Peppley,B.A.&Roberge,P .R.Fuel cell hydrogen productionby catalytic ethanol-steam reforming.Proc.33rd Intersoc.Energy Convers.Eng.Conf.269,1–7(1998).8.Marquevich,M.,Czernik,S.,Chornet,E.&Montane,D.Hydrogen from biomass:Steam reforming ofmodel compounds of fast-pyrolysis oil.Energy Fuels 13,1160–1166(1999).ne,T.A.,Elam,C.C.&Evans,R.J.Hydrogen from Biomass:State of the Art and Research Challenges1–82(National Renewable Energy Laboratory,Golden,CO,2002).10.Greeley,J.&Mavrikakis,M.A first-principles study of methanol decomposition on Pt(111).J.Am.Chem.Soc.124,7193–7201(2002).11.Grenoble,D.C.,Estadt,M.M.&Ollis,D.F.The chemistry and catalysis of the water gas shift reaction.1.The kinetics over supported metal catalysts.J.Catal.67,90–102(1981).12.Hilaire,S.,Wang,X.,Luo,T.,Gorte,R.J.&Wagner,J.A comparative study of water-gas shift reactionover ceria supported metallic catalysts.Appl.Catal.A 215,271–278(2001).13.Iglesia,E.,Soled,S.L.&Fiato,R.A.Fischer-Tropsch synthesis on cobalt and ruthenium.MetalFigure 2Selectivities (%)versus oxygenated hydrocarbon.H 2selectivity (circles)and alkane selectivity (squares)from aqueous-phase reforming of 1wt%oxygenatedhydrocarbons over 3wt%Pt/Al 2O 3at 498K (open symbols)and 538K (filled symbols).The aqueous feed solution was fed to the reactor at a weight-hourly space velocity of 0.008g of oxygenated hydrocarbon per gram of catalyst per hour.High conversions of the reactant were achieved under these conditions (50–99%conversion to gas-phase carbon,as indicated in Table 1)to provide a rigorous test of the carbon mass balance.dispersion and support effects on reaction rate and selectivity.J.Catal.137,212–224(1992).14.Kellner,C.S.&Bell,A.T.The kinetics and mechanism of carbon monoxide hydrogenation overalumina-supported ruthenium.J.Catal.70,418–432(1981).15.Vannice,M.A.The catalytic synthesis of hydrocarbons from H2/CO mixtures over the group VIIImetals V.The catalytic behaviour of silica-supported metals.J.Catal.50,228–236(1977).16.Bates,S.P.&Van Santen,R.A.Molecular basis of zerolite catalysis:A review of theoreticalsimulations.Adv.Catal.42,1–114(1998).17.Gates,B.Catalytic Chemistry(Wiley,New York,1992).18.Eggleston,G.&Vercellotti,J.R.Degradation of sucrose,glucose and fructose in concentrated aqueoussolutions under constant pH conditions at elevated temperature.J.Carbohydr.Chem.19,1305–1318 (2000).19.Kabyemela,B.M.,Adschiri,T.,Malaluan,R.M.&Arai,K.Glucose and fructose decomposition insubcritical and supercritical water:Detailed reaction pathway,mechanisms,and kinetics.Ind.Eng.Chem.Res.38,2888–2895(1999).20.Collins,P.&Ferrier,R.Monosaccharides:Their Chemistry and Their Roles in Natural Products(Wiley,West Sussex,England,1995).21.Li,H.,Wang,W.&Deng,J.F.Glucose hydrogeneration to sorbitol over a skeletal Ni-P amorphousalloy catalyst(Raney Ni-P).J.Catal.191,257–260(2000).22.Blanc,B.,Bourrel,A.,Gallezot,P.,Haas,T.&Taylor,P.Starch-derived polyols for polymertechnologies:Preparation by hydrogenolysis on metal catalysts.Green Chem.2,89–91(2000). 23.Narayan,R.,Durrence,G.&Tsao,G.T.Ethylene glycol and other monomeric polyols from biomass.Biotechnol.Bioeng.Symp.14,563–571(1984).24.Tronconi,E.et al.A mathematical model for the catalytic hydrogenolysis of carbohydrates.Chem.Eng.Sci.47,2451–2456(1992).rminie,J.&Dicks,A.Fuel Cell Systems Explained189(Wiley,West Sussex,England,2000).26.Amphlett,J.C.,Mann,R.F.&Peppley,B.A.On board hydrogen purification for steam reformer/PEMfuel cell vehicle power plants.Hydrogen Energy Prog.X,Proc.10th World Hydrogen Energy Conf.3, 1681–1690(1998).AcknowledgementsWe thank K.Allen,J.Shabaker and G.Huber for assistance in reaction kinetics measurements.We also thank G.Huber for help with catalyst preparation/ characterization and for TOC analyses,and M.Sanchez-Castillo for assistance with analysis of reaction products.We thank M.Mavrikakis and researchers at Haldor Topsøe A/S for reviews and discussion.This work was supported by the US Department of Energy (DOE),Office of Basic Energy Sciences,Chemical Science Division.Competing interests statementThe authors declare competingfinancial interests:details accompany the paper on Nature’s website(/nature).Correspondence and requests for materials should be addressed to J.A.D.(e-mail:dumesic@). .............................................................. Pfiesteria shumwayae killsfishby micropredation notexotoxin secretionWolfgang K.Vogelbein*,Vincent J.Lovko*†,Jeffrey D.Shields*†, Kimberly S.Reece*,Patrice L.Mason*,Leonard W.Haas*&Calvin C.Walker‡*Virginia Institute of Marine Science,The College of William and Mary, Gloucester Point,Virginia23062,USA‡United States Environmental Protection Agency,National Health and Environmental Effects Research Laboratory,Gulf Ecology Division,1Sabine Island Drive,Gulf Breeze,Florida32561,USA†These authors contributed equally to this work ............................................................................................................................................................................. Pfiesteria piscicida and P.shumwayae reportedly secrete potent exotoxins thought to causefish lesion events,acutefish kills and human disease in mid-Atlantic USA estuaries1–7.However,Pfies-teria toxins have never been isolated or characterized8.We investigated mechanisms by which P.shumwayae killsfish using three different approaches.Here we show that larvalfish bioassays conducted in tissue culture platesfitted with polycar-bonate membrane inserts exhibited mortality(100%)only in treatments wherefish and dinospores were in physical contact. No mortalities occurred in treatments where the membrane prevented contact between dinospores andfiing differen-tial centrifugation andfiltration of water from afish-killing culture,we produced‘dinoflagellate’,‘bacteria’and‘cell-free’rvalfish bioassays of these fractions resulted in mortalities(60–100%in less than24h)only in fractions contain-ing live dinospores(‘whole water’,‘dinoflagellate’),with no mortalities in‘cell-free’or‘bacteria’-enriched fractions.Video-micrography and electron microscopy show dinospores swarm-ing toward and attaching to skin,actively feeding,and rapidly denudingfish of epidermis.We show here that our cultures of activelyfish-killing P.shumwayae do not secrete potent exotox-ins;rather,fish mortality results from micropredatory feeding. Massivefish kills in mid-Atlantic USA estuaries involving several million Atlantic menhaden,Brevoortia tyrannus,have been attrib-uted to dinoflagellates of the toxic Pfiesteria complex(TPC)9.Potent ichthyotoxins secreted during Pfiesteria blooms are thought to be responsible for mortality as well as for deeply penetrating,so-called ‘Pfiesteria-specific’skin ulcers in thesefish1,5,9.However,earlier investigations attributed the menhaden ulcers to fungal infec-tions10,11,and Aphanomyces invadans,a highly pathogenic oomy-cete12,is now considered the aetiologic agent13,14.We recently demonstrated that A.invadans is a primary pathogen,able to elicit menhaden ulcer disease in the absence of Pfiesteria species or other environmental stressors15.Thus,the role of Pfiesteria species in menhaden lesion events is now questioned13–16.In contrast to the oomycete-induced ulcers of wild menhaden, laboratory exposure offishes to an unidentified Pfiesteria species elicited rapid,widespread epidermal erosion,osmoregulatory dys-function and death,with potent exotoxins assumed responsible4. However,direct attachment of P.shumwayae dinospores to skin, gills,olfactory organs,the oral mucosa and the lateral line canal, associated with extensive tissue damage,has been observed16.A direct physical association with thesefish tissues had not to our knowledge been previously reported,and this suggested an alterna-tive mechanism of pathogenesis for P.shumwayae.To better under-stand this association and to clarify the consequences of dinospore attachment,we conducted laboratory challenges using a sensitive larvalfish bioassay.We exposed larval sheepshead minnows,Cyprinodon variegatus, to Pfiesteria spp.in six-well tissue culture plates containing poly-carbonate membrane inserts(Millicell).This created two compart-ments within each well(‘in’,inside insert;‘out’,outside insert), allowing separation offish from dinospores across a permeable membrane(Fig.1).Mortalities occurred only in treatments where fish and P.shumwayae dinospores were in direct physical contact (Fig.2a:B in,D in,F).Fish physically separated from dinospores(A in,B out versus in)did not die,even if they resided within the same well as dyingfish in contact with dinospores(B in versus out).Fish in negative controls(C)andfish exposed to a non-pathogenic strainFigure1Experimental design for the membrane insert study using larval Cyprinodon variegatus exposed to Pfiesteria shumwayae(Ps)and P.piscicida(Pp).。
反应温度和停留时间对纤维素水热解产物理化特性的影响_高英

第30卷第17期农业工程学报 V ol.30 No.17 250 2014年9月Transactions of the Chinese Society of Agricultural Engineering Sep. 2014反应温度和停留时间对纤维素水热解产物理化特性的影响高英1,陈汉平2※,袁巧霞1,王贤华2,杨海平2,吴 可1,曹洪亮1(1. 华中农业大学工学院,武汉 430070; 2.华中科技大学煤燃烧国家重点实验室,武汉 430074;)摘要:为了解纤维素在水热降解过程中产物的理化特性及其形成机制,该文对生物质主要组分—纤维素的水热降解特性进行了系统地研究,全面分析了反应温度和停留时间对纤维素水热产物分布的影响,并从产物的化学结构入手,对纤维素水热解机理进行了探索。
随着温度的升高,重质油产率在250℃时达到最大,重质油组分变得复杂,焦炭产率逐渐降低。
随着停留时间的延长重质油产率呈现先增加后降低的趋势,焦炭产率变化趋势较小,然而通过对焦炭的热重、红外、元素、电子扫描显微镜和X射线光电子能谱仪分析表明停留时间的延长可以提高焦炭的化学官能性,这为生物质水热机理的研究提供了依据。
关键词:纤维素;温度;生物质;水热解;重油;水热焦炭doi:10.3969/j.issn.1002-6819.2014.17.032中图分类号:TQ352.78 文献标志码:A 文章编号:1002-6819(2014)-17-0250-09高 英,陈汉平,袁巧霞,等. 反应温度和停留时间对纤维素水热解产物理化特性的影响[J]. 农业工程学报,2014,30(17):250-258.Gao Ying, Chen Hanping, Yuan Qiaoxia, et al. Effect of reactor temperature and residence time on physiochemical performance of cellulose hydrothermal products[J]. Transactions of the Chinese Society of Agricultural Engineering (Transactions of the CSAE), 2014, 30(17): 250-258. (in Chinese with English abstract)0 引 言生物质种类繁多,成分复杂,使得水热转化过程和产物也十分复杂。
p区金属氧化物Ga_(2)O_(3)和Sb_(2)O_(3)光催化降解盐酸四环素性能差异
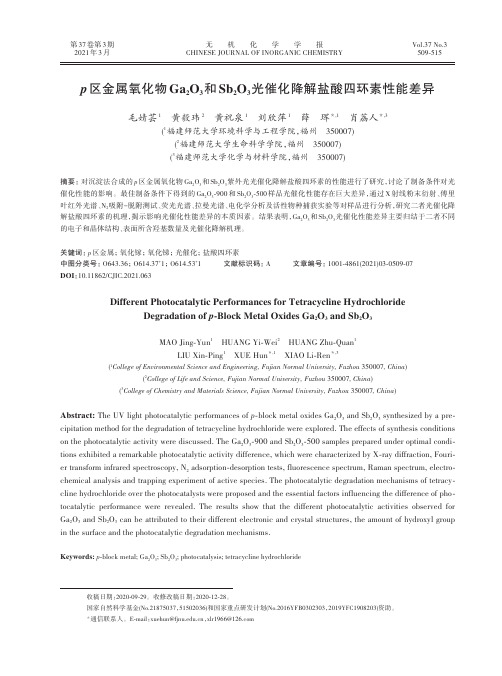
收稿日期:2020⁃09⁃29。
收修改稿日期:2020⁃12⁃28。
国家自然科学基金(No.21875037,51502036)和国家重点研发计划(No.2016YFB0302303,2019YFC1908203)资助。
*通信联系人。
E⁃mail :***************.cn ,***************第37卷第3期2021年3月Vol.37No.3509⁃515无机化学学报CHINESE JOURNAL OF INORGANIC CHEMISTRYp 区金属氧化物Ga 2O 3和Sb 2O 3光催化降解盐酸四环素性能差异毛婧芸1黄毅玮2黄祝泉1刘欣萍1薛珲*,1肖荔人*,3(1福建师范大学环境科学与工程学院,福州350007)(2福建师范大学生命科学学院,福州350007)(3福建师范大学化学与材料学院,福州350007)摘要:对沉淀法合成的p 区金属氧化物Ga 2O 3和Sb 2O 3紫外光光催化降解盐酸四环素的性能进行了研究,讨论了制备条件对光催化性能的影响。
最佳制备条件下得到的Ga 2O 3⁃900和Sb 2O 3⁃500样品光催化性能存在巨大差异,通过X 射线粉末衍射、傅里叶红外光谱、N 2吸附-脱附测试、荧光光谱、拉曼光谱、电化学分析及活性物种捕获实验等对样品进行分析,研究二者光催化降解盐酸四环素的机理,揭示影响光催化性能差异的本质因素。
结果表明,Ga 2O 3和Sb 2O 3光催化性能差异主要归结于二者不同的电子和晶体结构、表面所含羟基数量及光催化降解机理。
关键词:p 区金属;氧化镓;氧化锑;光催化;盐酸四环素中图分类号:O643.36;O614.37+1;O614.53+1文献标识码:A文章编号:1001⁃4861(2021)03⁃0509⁃07DOI :10.11862/CJIC.2021.063Different Photocatalytic Performances for Tetracycline Hydrochloride Degradation of p ‑Block Metal Oxides Ga 2O 3and Sb 2O 3MAO Jing⁃Yun 1HUANG Yi⁃Wei 2HUANG Zhu⁃Quan 1LIU Xin⁃Ping 1XUE Hun *,1XIAO Li⁃Ren *,3(1College of Environmental Science and Engineering,Fujian Normal University,Fuzhou 350007,China )(2College of Life and Science,Fujian Normal University,Fuzhou 350007,China )(3College of Chemistry and Materials Science,Fujian Normal University,Fuzhou 350007,China )Abstract:The UV light photocatalytic performances of p ⁃block metal oxides Ga 2O 3and Sb 2O 3synthesized by a pre⁃cipitation method for the degradation of tetracycline hydrochloride were explored.The effects of synthesis conditions on the photocatalytic activity were discussed.The Ga 2O 3⁃900and Sb 2O 3⁃500samples prepared under optimal condi⁃tions exhibited a remarkable photocatalytic activity difference,which were characterized by X⁃ray diffraction,Fouri⁃er transform infrared spectroscopy,N 2adsorption⁃desorption tests,fluorescence spectrum,Raman spectrum,electro⁃chemical analysis and trapping experiment of active species.The photocatalytic degradation mechanisms of tetracy⁃cline hydrochloride over the photocatalysts were proposed and the essential factors influencing the difference of pho⁃tocatalytic performance were revealed.The results show that the different photocatalytic activities observed for Ga 2O 3and Sb 2O 3can be attributed to their different electronic and crystal structures,the amount of hydroxyl groupin the surface and the photocatalytic degradation mechanisms.Keywords:p ⁃block metal;Ga 2O 3;Sb 2O 3;photocatalysis;tetracycline hydrochloride无机化学学报第37卷0引言盐酸四环素(TC)作为一种四环素类广谱抗生素,被广泛应用于治疗人体疾病及预防畜禽、水产品的细菌性病害,其在世界范围的大量使用致使其在环境中积累[1]。
新课标英语高考试卷
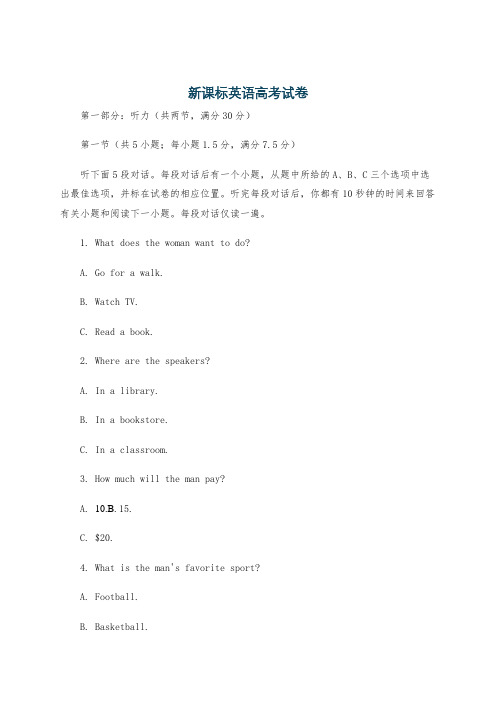
新课标英语高考试卷第一部分:听力(共两节,满分30分)第一节(共5小题;每小题1.5分,满分7.5分)听下面5段对话。
每段对话后有一个小题,从题中所给的A、B、C三个选项中选出最佳选项,并标在试卷的相应位置。
听完每段对话后,你都有10秒钟的时间来回答有关小题和阅读下一小题。
每段对话仅读一遍。
1. What does the woman want to do?A. Go for a walk.B. Watch TV.C. Read a book.2. Where are the speakers?A. In a library.B. In a bookstore.C. In a classroom.3. How much will the man pay?A. 10.B. 15.C. $20.4. What is the man's favorite sport?A. Football.B. Basketball.C. Tennis.5. When will the meeting start?A. At 9:00.B. At 9:30.C. At 10:00.第二节(共15小题;每小题1.5分,满分22.5分)听下面5段对话或独白。
每段对话或独白后有几个小题,从题中所给的A、B、C 三个选项中选出最佳选项,并标在试卷的相应位置。
听每段对话或独白前,你将有时间阅读各个小题,每小题5秒钟;听完后,各小题将给出5秒钟的作答时间。
每段对话或独白读两遍。
听第6段材料,回答第6、7题。
6. What is the relationship between the two speakers?A. Husband and wife.B. Father and daughter.C. Brother and sister.7. What are they going to do this weekend?A. Go to the park.B. Visit their parents.C. See a movie.听第7段材料,回答第8至10题。
山东省部分名校2024届高三下学期2月大联考英语试卷(含答案)
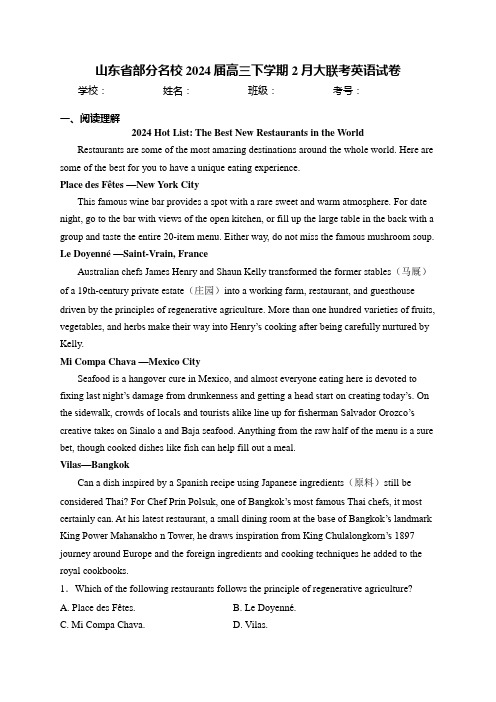
山东省部分名校2024届高三下学期2月大联考英语试卷学校:___________姓名:___________班级:___________考号:___________一、阅读理解2024 Hot List: The Best New Restaurants in the World Restaurants are some of the most amazing destinations around the whole world. Here are some of the best for you to have a unique eating experience.Place des Fêtes —New York CityThis famous wine bar provides a spot with a rare sweet and warm atmosphere. For date night, go to the bar with views of the open kitchen, or fill up the large table in the back with a group and taste the entire 20-item menu. Either way, do not miss the famous mushroom soup. Le Doyenné—Saint-Vrain, FranceAustralian chefs James Henry and Shaun Kelly transformed the former stables(马厩)of a 19th-century private estate(庄园)into a working farm, restaurant, and guesthouse driven by the principles of regenerative agriculture. More than one hundred varieties of fruits, vegetables, and herb s make their way into Henry’s cooking after being carefully nurtured by Kelly.Mi Compa Chava —Mexico CitySeafood is a hangover cure in Mexico, and almost everyone eating here is devoted to fixing last night’s damage from drunkenness and getting a head start on creating today’s. On the sidewalk, crowds of locals and tourists alike line up for fisherman Salvador Orozco’s creative takes on Sinalo a and Baja seafood. Anything from the raw half of the menu is a sure bet, though cooked dishes like fish can help fill out a meal.Vilas—BangkokCan a dish inspired by a Spanish recipe using Japanese ingredients(原料)still be considered Thai? For Chef Prin Polsuk, one of Bangkok’s most famous Thai chefs, it most certainly can. At his latest restaurant, a small dining r oom at the base of Bangkok’s landmark King Power Mahanakho n Tower, he draws inspiration from King Chulalongkorn’s 1897 journey around Europe and the foreign ingredients and cooking techniques he added to the royal cookbooks.1.Which of the following restaurants follows the principle of regenerative agriculture?A. Place des Fêtes.B. Le Doyenné.C. Mi Compa Chava.D. Vilas.2.What does the fisherman Salvador Orozco specialize in?A. Delicious seafood soup.B. Distinct foreign flavors.C. Innovative seafood cooking.D. A treatment for drunkenness.3.Where does the text probably come from?A. A travel magazine.B. A scientific report.C. An advertisement.D. A textbook.Recently, a set of video clips (片段) featuring a man showcasing umbrellas with various creative designs has gone viral on the Internet, even spreading overseas and attracting foreign netizens with the unimaginable “Chinese creativity”, CCTV news reported.In the clips, there are shining laser (激光) reflective umbrellas to dispel darkness, umbrellas with floor-length plastic curtains to prevent one’s clothes from getting wet, twin umbrellas specially designed for couples and many others. All of them are made by the man in the clips, Lei Penglin. 38-year-old Lei has operated an umbrella factory in Shaoxing, Zhejiang Province. Netizens affectionately call him “uncle” due to his performances in the clips.In 2014, Lei established his own factory. At first, his factory received thousands of orders. However, as the competition intensified, Lei had to explore new opportunities. He found thatinto the products and, in 2022, his umbrella with an attached flashlight gained popularity. “Consumers pursue person alized products. So the umbrellas have to function as decorations aside from just preventing sunshine and rain,” Lei said.In the comment section of the product videos, Lei noticed an interesting request with many likes, suggesting to him to make a reflective umbrella for walking in the dark. Following the advice, Lei created the “laser reflective umbrella”, selling over 70,000 units once upon release. From then on, Lei started to attach great importance to comments to absorb new ideas.Presently, Lei spend s several hours reading comments every day. “Basically 300 to 500 comments a day, I will read and reply to them all by myself. Only by carefully observing can I know everyone’s need, and solve the after-selling problems on time,” he said. Several products developed based on the comments have been on shelf. “Almost all the umbrellas made so far can be sold; none have suffered loss,” Lei introduced.In the future, Lei hopes to make some Chinese-style umbrellas that can be paired with Han-style clothing. “I want to try something new and also advocate for our Chinese culture,”Lei added.4.What is the feature of Lei’s umbrellas?A. Conventional.B. Innovative.C. Unimaginative.D. Durable.5.What does the underlined word “infuse” in paragraph 3 mean?A. Divide.B. Burst.C. Integrate.D. Emerge.6.What is Lei’s attitude towards his future career?A. Uncertain.B. Indifferent.C. Dissatisfied.D. Optimistic.7.What contributes most to Lei’s success according to the author?A. Promoting his products through social media.B. Paying attention to customers’ comments and needs.C. Seeking uniqueness to compete with other producers.D. Adding elements of traditional culture to his products.Fountains of lava erupted from the Sundhnúkur volcanic system in southwest Iceland on January 14th, 2024. Lava flows welled up from a new gap, attacking the suburbs of Grindavík with at least three houses in their path burnt down. Nearby, construction vehicles that had been working for weeks to build large earthen dams in an attempt to divert(使转向)the lava’s flow had to pull back.Lava is subject to gravity like other fluids, so it will flow down along a path of steepest descent(斜坡). With the temperature of its molten rock often well above 1,000 degrees Celsius, not much can stand in its way. Humans have tried many ways to stop lava in the past, from attempting to freeze it in place by cooling it with sea water, to using explosive s to cut off its supply. However, no attempt was successful.Most recent efforts have focused instead on building dams in an attempt to divert the lava’s flow toward a different path of steepest descent into a different “lavashed,” where lava would naturally flow. Results have been mixed, but diversion can be successful if the lava flow can be clearly diverted into a distinct area where lava would naturally flow — without threatening a different community in the process. Many attempts to divert lava have failed, however. Barriers built in Italy to stop Mt. Etna’s lava flows in 1992 slowed the flow, but the lava eventually over topped each one.Diverting lava in Grindavík is difficult, in part because the land around Grindavík is relatively flat, making it harder to identify a clear alternative path of steepest descent for redirecting the lava. Icelandic official s reported on January 15th that most of the lava from the main fissure had flowed along the outside the barrier, however a new gap had also openedinside the perimeter(外围), sending lava into a neighborhood. Unfortunately, that implies that Grindavík remains at risk.8.What do we know about the lava erupting from the Sundhnúkur volcanic system?A. It severely affected the downtown area of Grindavík.B. It forced the construction of large earthen dams to suspend.C. It was successfully redirected by the earthen barriers:D. It completely buried a residential area.9.How many ways are mentioned to stop the lava?A. Five.B. Four.C. Three.D. Two.10.The lava flow in Grindavík remains a risk because ________.A. the lava has destroyed many buildingsB. there is no suitable dam to divert the lavaC. the land around Grindavík is relatively flatD. the lava has already entered a populated area11.What is the text mainly about?A. How earthen barrier functions.B. What can be done to prevent lava.C. Why volcanic lava is so hard to stop.D. What lava has brought about in Iceland.At ancient sites across the Amazon River basin, mysterious plots of unusually rich soil dot (点缀) the landscape. Scientists have long debated the origin of this “dark earth”, which is darker in color than surrounding soils and richer in carbon. Some people think this dark earth formed naturally, but the latest research has shown that modern Kuikuro people in Brazil create similar soil around their villages on purpose, which adds evidence to the idea that long-ago Amazons deliberately made such soil too. Perron, an earth scientist at MIT, reviewed interviews of Kuikuro people conducted by a Kuikuro filmmaker in 2018 and found that Kuikuro villagers actively make dark earth by using ash, food bits and controlled burns. “When you plant in hilly land, the soil is weak,” explained elder Kanu Kuikuro in one of the interviews. That is why we throw the ash, manioc peelings and manioc pulp. When comparing soil samples from ancient and modern sites, resear chers found “striking similarities” — both were far less acidic than surrounding soils and contained higher levels of plant-friendly nutrients.Analyses also revealed that dark earth holds twice the amount of carbon as surrounding soils on average. Scans (扫描) of the Xingu region suggest that the area is dotted with dark earth, and that hold as much as about 9 million tons of carbon — the annual carbon emissionsof a small, industrialized country. “This number could roughly equal the annual carbon emissions of the United States when all dark earth across the Amazon is taken into consideration,” Perron says.Figuring out the true value of carbon stored in the Amazon’s dark earth will require more data. Still, the research has significant influences on the Amaz on’s future. The technique highlights how ancient people were able to live in the Amazon by developing sustainable farming that doubled as a carbon-storing technique. With more and more greenhouse gases entering the atmosphere, it could also provide a blueprint for developing methods of sustainably locking atmospheric carbon in the soil, helping fight climate change.12.What can we infer from the dark earth across the Amazon River basin?A. They are more acidic than surrounding soils.B. They contain more organic nutrients.C. They formed naturally.D. They contain less carbon.13.Why does the author mention the annual carbon emissions of the US?A. To explain the difficulty of protecting dark earth.B. To show the wide distribution of dark earth in Amazon.C. To stress the huge carbon-storing capability of dark earth.D. To reveal the large carbon emissions of the United States.14.What does the author stress in the last paragraph?A. The importance of developing sustainable farming.B. The advanced farming technology in ancient tomes.C. A possible solution to climate change.D. A way of green agriculture.15.Which is the best title of the text?A. Urgency of Sustainable DevelopmentB. Facts About the Dark EarthC. Advantages of the Dark EarthD. Wisdom of Ancient Amazons二、七选五16.“Second place is just the first loser.” is a well-known saying from the NASCAR champion Dale Earnhardt.We may not want others to know our thoughts, but many of us think this way, because we are born to compete with each other. ①________ Fortunately, there is a way to solve this problem: instead of always going for gold, aim for the bronze.To expand on the wisdom of Earnhardt, although second place may be the first loser, third place can be the real winner, at least when it comes to happiness and longevity. A 1995 study discovered that bronze winners appeared consistently happier on average than silver medalists, while another research in 2018 studied US athletes in the Olympics from 1904 to 1936 and found that those whose best performance was silver lived to 72 on average. Gold medalists beat this by living to 76. ②________③________ Silver medalists see themselves as the first loser because they compare themselves only with the champions. In contrast, the bronze winners compare downwards with those who have never made it onto the podium at all. ④________ The emotion shows up in improved health and longevity.The worldly happiness strategy of working for gold every day is foolish. Stop spending most of your time feeling like a silver medalist: always pursuing and relying your happiness on a single outcome. ⑤________A. But the first prize went to the bronze winners, who lived to 78.B. Therefore, they feel better about themselves and thus, happier.C. However, if left uncontrolled, this can create conflicts between ourselves and others.D. The social concepts of upward and downward comparison help explain the difference.E. The comparison is not from a feeling of ill will, but because rewards in life are relative.F. Comparing ourselves with the unlucky is a reliable technique for reducing a negative mood.G. Rather, aim for health y competitions where you do your best without expecting to be the absolute winner.三、完形填空(15空)Ashoka, an association founded by Bill Drayton, has fought to end poverty (贫困) and sickness, promoted education and encouraged small businesses. To support these worthyimprove social conditions. An excellent example is an Ashoka project started in 1995 inan income for local farmers there.When Masqsood and Iftekhar from Ashoka began to study the problem of all thepractical progress in bringing about social change by changing the way we look at economic development.17.A. plans B. causes C. attempts D. events18.A. right B. confidence C. permission D. praise19.A. in particular B. in fact C. on purpose D. in turn20.A. avoid B. decline C. accept D. appreciate21.A. professional B. generous C. contributing D. innocent22.A. ambition B. definition C. advice D. purpose23.A. water B. resource C. rubbish D. traffic24.A. attacking B. charging C. counting D. inviting25.A. employ B. create C. leave D. send26.A. hope B. market C. desire D. way27.A. expensive B. effective C. affordable D. profitable28.A. refused B. recognised C. confused D. surprised29.A. permit B. order C. advise D. persuade30.A. set off B. took off C. picked up D. put up31.A. uncertain B. doubtful C. pessimistic D. optimistic四、短文填空32.What’s the first thing ①________ comes into your mind when you think of w heat straw (麦秆)? Most people would probably just see it as a pile of waste in a farmer’s field. However, WuCui, an intangible (非物质的) cultural inheritor, can turn the straw into beautiful and eye-catching ②________ (function) artworks.The earliest straw-weaving products ③________ (discover) at Hemudu Cultural Ruins, a Neolithic cultural site located in eastern China’s Zhejiang Province. The Book of Rites, one ofthe classical ④________ (work) of Confucianism, also records that there were already mats made of cattail grass and professional straw-weaving craftsmen during the Zhou Dynasty. Straw weaving was listed ⑤________ a national intangible cultural heritage in 2008.Straw weaving is a time-consuming process that can take weeks, ⑥________ even months, to complete. Later, industrial goods have taken ⑦________ place of such products, which make low profits, and there are only about 100 individuals ⑧________ (involve) in the work across the country. “The world has changed, and craftsmen need to overstep practicality and pursue the beauty and artistry of straw culture ⑨________ (help) the craft survive and thrive,” Wu says.From her viewpoint, straw weaving should respond to people’s needs and preferences, while still ⑩________ (draw) inspiration from traditional culture.五、书面表达33.上周五晚上你校邀请了一位心理学专家做了一个主题为“珍爱生命,直面挫折”的心理健康讲座活动。
- 1、下载文档前请自行甄别文档内容的完整性,平台不提供额外的编辑、内容补充、找答案等附加服务。
- 2、"仅部分预览"的文档,不可在线预览部分如存在完整性等问题,可反馈申请退款(可完整预览的文档不适用该条件!)。
- 3、如文档侵犯您的权益,请联系客服反馈,我们会尽快为您处理(人工客服工作时间:9:00-18:30)。
THE CATALYTIC EFFECT OF CARBON-SUPPORTED RUTHENIUM ON THE DEPOLYMERIZATION OF HYDROLYTIC LIGNINCaroline E. Burgess, David J. Clifford, and Justin R. HorvathPenn State University, The Energy Institute,209 Academic Projects Bldg., University Park, PA 16803 IntroductionBiomass consists of an assortment of recalcitrant polymers such as cellulose and lignin. Prior to use in gasification streams, these polymers are subjected to degradation/depolymerization reactions for the purpose of liberating smaller, more volatile and reactive species.It is well known that carbohydrates can be depolymerized in an acid hydrolysis reaction with the depolymerization effectively catalyzed using a carbon-supported ruthenium catalyst (1-5). Under relatively mild conditions, carbon-supported ruthenium can also effectively catalyze the hydrogenation of highly hindered aromatic rings, such as those found in rosin (6, 7). More recently, alumina-supported ruthenium and other forms of ruthenium have been studied as hydrodesulfurization and coal liquefaction catalysts (8-11).While it is known that ruthenium can catalyze carbohydrate depolymerization, less is understood when reacting whole biomass, as hydrolytic lignin remains and must be separated from the catalyst. Base hydrolysis at 280-320°C has been used to solubilize and react the hydrolytic lignin to phenolic compounds (2, 12). However, little is known about the effect of the ruthenium on the hydrolytic lignin under the base hydrolysis reaction conditions. In this study, the catalytic effect of ruthenium on the degradation of lignin polymers has been explored.ExperimentalCommercially available hydrolytic lignin was obtained from Aldrich Chemical Co. and used as the starting material. Reagent grade sodium hydroxide and concentrated hydrochloric acid were also obtained from Aldrich. The ruthenium catalyst (5% ruthenium loaded on a carbon support) was obtained from Aldrich.Reactions were performed with and without ruthenium catalyst. For the latter, the catalyst loading was a 1% metal loading. Tubing reactors (~25 mL) were loaded with 1.5 g of hydrolytic lignin and 10 mL of 10% aqueous sodium hydroxide. The reactors were initially purged with nitrogen to remove air and charged to 4.5 MPa with hydrogen gas. An ebulating sand bath was utilized to obtain temperatures of 280, 300 and 320°C in three experiments, each of which had a residence time of 1 hour.The reacted materials were processed according to the flow chart shown in Figure 1. Solid and liquid products were separated by filtration. The liquid material was then acidified to a pH of approximately 2.0 and separated into acid-soluble and acid-insoluble fractions. Acid-soluble compounds were then extracted with diethyl ether, which was then evaporated to determine yield. Not all acid soluble compounds were soluble in diethyl ether. The yield of residual acid-solubles and gases were determined by difference.The ether soluble fraction was analyzed by gas chromatography-mass spectrometry (GC-MS) using a Shimadzu QP-5000 mass spectrometer. The acid-soluble fraction was analyzed using a Chemagnetics M100S solid-state nuclear magnetic resonance (NMR) spectrometer operating at a field strength of 2.4 T and utilizing a spinning speed of 3.5 kHz. The technique of cross polarization with magic angle spinning was employed.To simplify the discussion, the ether-soluble fraction will be referred to as LMW (low molecular weight), the acid-insoluble as HMW (high molecular weight), and the residual soluble material following extraction with diethyl ether as AS-LMW (acid-soluble-low molecular weight) materials.Figure 1: Schematic of procedure to separate products.Results and DiscussionNon-catalytic R eactions. Table 1 shows the conversions and yields of HMW, LMW and AS-LMW/gas fractions for 280, 300 and 320°C reaction conditions. In each case, conversion to either LMW, HMW, or AS-LMW/gas was nearly complete. Shown in Figure 2 are the GC-MS chromatograms for the LMW fraction and in Figure 4 are solid-state 13C-NMR spectra for the HMW fraction. Relative yields, which are listed in Table 1, indicate that as the reaction severity increases, the yield of HMW product and LMW product decreases, while the AS-LMW/gas yield increases, particularly at 320°C.Table 1. Conversion and Yield Data for Reaction of Hydrolytic Lignin With and Without Ruthenium Catalysta All reactions were run for 1 hour, under 4.5 MPa of hydrogen.b Yield determined by difference.ReactionTemp(°C)aCatalyst Conversion(wt %)YieldHMW(wt %)YieldLMW(wt %)Yield AS-LMW /Gas( wt%)b 280 none 99.7 52.0 22.1 25.6 300 none 98.1 38.2 14.6 45.3 320 none 98.6 24.0 8.1 66.5 280 Ru 97.6 22.6 27.5 47.5 300 Ru 90.4 23.6 23.7 43.1 320 Ru 93.5 21.2 16.9 55.4LigninInsolubleResidueSolubleReaction inbase, hydrogenAcidify topH 1-2SolubleLMWExtractionwith etherAcid-solubleAS-LMWEther-solubleLMWGasInsolubleHMWGC-MS analyses of the LMW fraction (Figure 2) show a product distribution of primarily phenols and catechols, which are compounds typical of lignin degradation reactions. At 280°C, guaiacol is a major product, as well as other methoxyl-substituted aromatic compounds. As the reaction temperature increases, the abundance of methoxyl-substituted aromatics dramatically decreases, with 2,6-di-tert-butyl-p-cresol surviving the more degradative conditions.Based on the solid-state NMR data (Figure 4), the HMW fraction was found to undergo reactions consistent with those previously reported in lignin maturation investigations (13-19). The primary reaction results in the loss of methoxyl (Figure 4: 74 ppm) and catechol (Figure 4: 148 ppm) functionality with some preservation of phenol-like moieties (Figure 4: 154 ppm).Catalytic R eactions. When reactions were carried out in the presence of ruthenium catalyst, the conversion was slightly lower than for the corresponding reactions without ruthenium. At all three reaction temperatures, yield of HMW does not change significantly, while the LMW decreases with increasing reaction temperature. However, the depolymerization of the starting material appears to be suppressed under the catalytic reaction conditions at the higher reaction temperature.GC-MS analyses of the LMW fraction (Figure 3) show the fraction is composed primarily of phenols and catechols, similar to non-catalytic reaction conditions. At 280°C, guaiacol is a major product, as well as other methoxyl-substituted aromatic compounds. As the reaction temperature increases, the methoxyl-substituted aromatics dramatically decrease, with 2,6-di-tert-butyl-p-cresol surviving the more degradative conditions.The HMW fraction yield did not change as significantly with temperature. The most notable effect on functional group distributions was the loss of the methoxyl (Figure 5: 74 ppm) moieties, while there was some preservation of catechol (Figure 5: 148 ppm) and phenol (Figure 5: 154 ppm) groups within the structure.Comparison of Non-catalytic and Catalytic R eactions. At 280°C, the extent of depolymerization appears greater for the catalytic reactions. The AS-LMW/gas yield is higher for the catalyzed reaction, and NMR of the HMW fraction shows a greater loss of oxygen functionality when catalyst is in the reaction. The GC-MS data for the LMW also shows fewer oxygen substituted compounds compared to the non-catalytic reaction, another indication of an increased rate of reaction.However, at 300 and 320 °C, the ruthenium appears to suppress the depolymerization of the hydrolytic lignin compared to the non-catalyzed reactions. The AS-LWM/gas yield is lower for the catalytic reactions. Results of NMR analyses suggest that for the non-catalyzed reactions, the HMW fraction loses more oxygen functionality, particularly as phenols and catechols while the aromaticity increases, compared to the catalytic reactions. The GC-MS data obtained for the LMW fractions indicates a lower percentage of oxygenated compounds, with relatively more substituted aromatics, than in the catalytic reactions.So what is the role of the ruthenium under these reaction conditions? Ruthenium is a known hydrogenation catalyst, particularly selective for hydrogenating carbonyl functional groups and hindered aromatics (1, 6, 7). However, the hydrogenation activity is highest at 25-200°C. At temperatures of 200-300°C, it has been reported that dehydrogenation activity of aromatics is more dominant (20-21). The reaction system we are investigating is slightly different in that it is a base hydrolysis as well as a hydrogenation reaction.As observed in the non-catalytic reaction, it is thought that the base participates in breaking the β-O-4 bonds. As radicals are generated through the reaction of the hydrolytic lignin, at 280°C, the ruthenium may be catalyzing the capping of methoxyl radicals with hydrogen and keeping the radicals from re-reacting with the HMW structure. At higher temperatures, the ruthenium appears to promote hydrogenation of the oxygen radicals on the aromatic structures and preserve the phenols and catechols in the HMW structure. It may also function to hydrogenate the carbonyl groups on the generated monomers.While ruthenium catalyst might suppress the complete gasification of the hydrolytic lignin, it does appear to selectively hydrogenate and retain some oxygen in the solid carbonaceous material. The possible result would be less oxygen in the gas products and less CO/CO2 generation. Rather than focusing on the complete depolymerization of lignin, the goal could be to focus on finding value-added applications for the products in order to improve the economics for the entire process.ConclusionsResults indicate that the overall lignin conversion is reduced slightly with increasing temperature compared to non-catalytic reactions. Acid-insoluble compounds retain oxygen functionality, as determined by solid state 13C NMR, when compared to their non-catalytic counterparts. For all reactions, the NMR data showed the oxygen is lost as ether, phenol, and catechol moieties. However, in the non-catalytic reactions, the rate of loss of these moieties and the increase is aromaticity is greater than in the catalytic reactions. If the ruthenium does act to suppress the depolymerization of hydrolytic lignin at higher temperatures, it may selectively suppress loss of oxygen and therefore produce less CO/CO2. In that case, making value added materials from the remaining material could increase the viability of the entire process. Future work will include using an inert gas, such as N2 in the reaction, determining the gas composition and yield with and without hydrogen, and searching for uses of the remaining solid.Acknowledgement. Funding for the project has been provided by the Energy Institute and the Center for Environmental Chemistry and Geochemistry at Penn State University.References(1) Gilman, G. and Cohn, G., Adv. Catalysis,1957, 9, 733.(2) Vasyunina, N.A., Balandin, A.A., Chepigo, S.V., and Barysheva,G.S., Bull. Acad. Sciences USSR (Chem.),1960, 1419.(3) Robinson, J.M., Banuelos, E., Barber, W.C., Burgess, C.E.,Chau, C., Chesser, A.A., Garrett, M.H., Goodwin, C.H.,Holland, P.L., Horne, B.O., Marrufo, L.D., Mechalke, E.J.,Rashidi, J.R., Reynolds, B.D., Rogers, T. E., Sanchez, E.H.,Villarreal, J.S., ACS Div. of Fuel Chem. Preprints,1999, 44 (2),224-227.(4) Robinson, J.M., Herndon, P.T., Holland, P.L., Marrufo, L.D.,Org. Proc. Res. & Dev.,1999,3 (5), 352-356.(5) Robinson, J.M., U.S. Patent No. 5,516,960,“Process forproducing hydrocarbon fuels,”May 14, 1996.(6) Glasebrook, A.L., Hoffman, A.N., and Montgomery, J.B., U.S.Patent No. 2,776, 276,“Rosin hydrogenation,”Jan. 1, 1957 ((asreported by A.E. Rea and M. Bebbington in “AnnotatedBibliography on Ruthenium, Rhodium, and Iridium as Catalysts,”International Nickel Company: New York, 1959).(7) Montgomery, J.B., Hoffman, A.N., Glasebrook, A.L., Thigpen,J.I., Ind. Eng. Chem.,1958, 50, 313.(8) Liaw, S.J., Lin, R.G., Raje, A., and Davis, B.H., Appl. CatalysisA-Gen.,1997, 151 (2), 423.(9) Wojciechowska, M., Pietrowski, M., and Czajka, B., CatalysisToday,2001,65 (2-4), 349.(10) Suzuki, T., Yamada, H., Yunoki, K., and Yamaguchi, H., EnergyFuels,1992, 6 (4), 352.(11) Kondo, K., Kawanishi, T., Ikenaga, N., and Suzuki, T., Fuel,2001, 80 (7), 1015.(12) Burgess, C.E., Robinson, J.M., O’Hara, K., Rashidi, J.R.,Sanchez, E.H., and Greenwood, P.F., ACS Div. of Fuel Chem.Preprints,1998, 43 (2), 335-339.(13) Hayatsu, R., McBeth, R.L., Scott, R.G., Botto, R.E., andWinans, R.E., Org. Geochem., 1984, 6, 463.(14) Pang, L.S., Vassallo, AM., and Wilson, M.A., Org. Geochem.,1990, 16 (4-6), 853.(15) Hatcher, P.G., Org. Geochem.1990,16 (4-6), 959.(16) Hatcher, P.G., Faulon, J-L., Wenzel, K.A., and Cody, G.D.,Energy Fuels,1992, 6, 813.(17) Behar, F. and Hatcher, P.G., Energy Fuels,1995, 9, 984.(18) Buchanan, III, A.C., Britt, P.F., and Struss, J.A., Energy Fuels,1997, 11, 247.(19) Freitas, J.C.C., Bonagamba, T.J., and Emmerich, F.G., EnergyFuels, 1999,13, 53.(20) Borisov, P.R., and Stepanov, S.S., Sci. Reports Moscow StateUniversity, 1936, No. 6, 347 (as reported by A.E. Rea and M.Bebbington in “Annotated Bibliography on Ruthenium,Rhodium, and Iridium as Catalysts,” International NickelCompany: New York, 1959).(21) Holroyd, R., and Peel, D.H.P., U.S. Patent No. 2,411,726,“Catalytic dehydrogenation,”Nov. 26, 1946 ((as reported byA.E. Rea and M. Bebbington in “Annotated Bibliography onRuthenium, Rhodium, and Iridium as Catalysts,” International Nickel Company: New York, 1959).33 Figure 2:and 320°C.Figure 3: GC-MS spectra of LMW for catalytic reactions at 280 and 320°C.Figure 4:13C NMR spectra of unreacted lignin and catalytically reacted HMW at 280 and 300°C.3002001000-100Figure 5:13C NMR spectra of reacted HMW from catalytic reactions at 280, 300, and 320°C.。