塑胶件常见缺陷
塑胶件常见缺陷不良分析及对策讲解
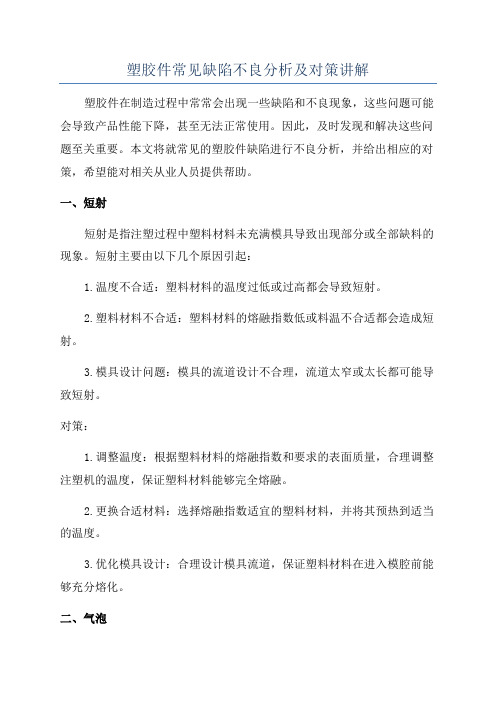
塑胶件常见缺陷不良分析及对策讲解塑胶件在制造过程中常常会出现一些缺陷和不良现象,这些问题可能会导致产品性能下降,甚至无法正常使用。
因此,及时发现和解决这些问题至关重要。
本文将就常见的塑胶件缺陷进行不良分析,并给出相应的对策,希望能对相关从业人员提供帮助。
一、短射短射是指注塑过程中塑料材料未充满模具导致出现部分或全部缺料的现象。
短射主要由以下几个原因引起:1.温度不合适:塑料材料的温度过低或过高都会导致短射。
2.塑料材料不合适:塑料材料的熔融指数低或料温不合适都会造成短射。
3.模具设计问题:模具的流道设计不合理,流道太窄或太长都可能导致短射。
对策:1.调整温度:根据塑料材料的熔融指数和要求的表面质量,合理调整注塑机的温度,保证塑料材料能够完全熔融。
2.更换合适材料:选择熔融指数适宜的塑料材料,并将其预热到适当的温度。
3.优化模具设计:合理设计模具流道,保证塑料材料在进入模腔前能够充分熔化。
二、气泡气泡是指塑胶件表面或内部出现的小气孔或气泡。
气泡可能导致产品外观不良或性能下降。
气泡的产生主要有以下几个原因:1.塑料材料中含有挥发性成分:一些塑料材料中含有挥发性成分,如果注塑温度过高,这些挥发性成分就会挥发出来形成气泡。
2.模具表面不洁净:如果模具表面不干净或有油污等杂质,气泡就会在塑料注入过程中被吸附在塑料中形成。
3.注塑机压力过高:注塑机压力过高会导致空气被压进模具中,形成气泡。
对策:1.调整注塑温度:根据塑料材料的特性,合理调整注塑温度。
温度过高易导致气泡产生,温度过低则容易短射。
2.模具清洁:保持模具表面干净,定期对模具进行清洗,去除杂质和油污。
3.控制注塑机压力:根据塑料材料的特性和模具的要求,合理控制注塑机的压力,避免空气进入模具。
三、热处理不当塑胶件经过热处理后,如果处理不当,可能导致产品性能下降或出现变形等问题。
常见的热处理问题有:1.温度不合适:热处理时,温度不合适会导致产品硬度不均匀或过硬。
塑胶件常见缺陷及原因分析
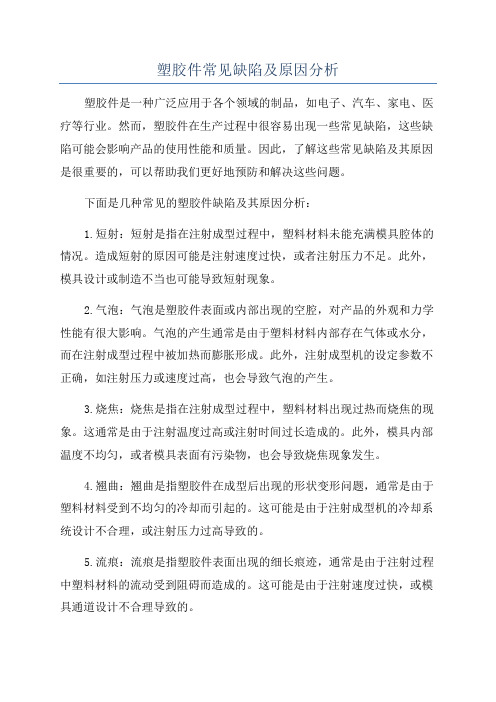
塑胶件常见缺陷及原因分析塑胶件是一种广泛应用于各个领域的制品,如电子、汽车、家电、医疗等行业。
然而,塑胶件在生产过程中很容易出现一些常见缺陷,这些缺陷可能会影响产品的使用性能和质量。
因此,了解这些常见缺陷及其原因是很重要的,可以帮助我们更好地预防和解决这些问题。
下面是几种常见的塑胶件缺陷及其原因分析:1.短射:短射是指在注射成型过程中,塑料材料未能充满模具腔体的情况。
造成短射的原因可能是注射速度过快,或者注射压力不足。
此外,模具设计或制造不当也可能导致短射现象。
2.气泡:气泡是塑胶件表面或内部出现的空腔,对产品的外观和力学性能有很大影响。
气泡的产生通常是由于塑料材料内部存在气体或水分,而在注射成型过程中被加热而膨胀形成。
此外,注射成型机的设定参数不正确,如注射压力或速度过高,也会导致气泡的产生。
3.烧焦:烧焦是指在注射成型过程中,塑料材料出现过热而烧焦的现象。
这通常是由于注射温度过高或注射时间过长造成的。
此外,模具内部温度不均匀,或者模具表面有污染物,也会导致烧焦现象发生。
4.翘曲:翘曲是指塑胶件在成型后出现的形状变形问题,通常是由于塑料材料受到不均匀的冷却而引起的。
这可能是由于注射成型机的冷却系统设计不合理,或注射压力过高导致的。
5.流痕:流痕是指塑胶件表面出现的细长痕迹,通常是由于注射过程中塑料材料的流动受到阻碍而造成的。
这可能是由于注射速度过快,或模具通道设计不合理导致的。
6.缩水:缩水是指塑胶件在成型后出现尺寸缩小的现象。
这可能是由于塑料材料在冷却后收缩所致。
此外,注射成型机的注射温度或冷却时间不合适,也会导致塑胶件尺寸缩水。
针对以上常见缺陷,我们可以采取一些措施来预防和解决这些问题。
首先,合理设计模具,考虑到塑料流动性和冷却效果,以减少缺陷的产生。
其次,在注射成型过程中,选择合适的注射参数,如温度、速度和压力等,以确保塑料材料充满模具腔体。
此外,定期清洗和维护注射成型机和模具,以避免污染物对塑胶件质量的影响。
塑胶件常见的缺陷产生原因及解决办法

塑胶件常见的缺陷产生原因及解决办法一、设计方面的缺陷:1.不合理的尺寸设计:塑胶件的尺寸设计不合理可能导致尺寸偏差过大、尺寸不一致等问题。
解决方法是根据塑胶件的具体用途和要求进行合理的尺寸设计,并进行合适的工艺分析和模流分析。
2.没有考虑到材料的特性:不同塑料材料具有不同的热胀冷缩系数、熔融温度等特性,设计时没有考虑到这些特性可能导致尺寸偏差、变形等问题。
解决方法是根据塑料材料的特性进行合适的设计和模具制造选型。
3.模具设计问题:模具设计不合理或者制造质量不过关可能导致塑胶件的缺陷问题。
解决方法是进行合理的模具设计,并选择专业的模具制造厂家。
4.不合理的壁厚设计:塑胶件的壁厚设计不合理可能导致塑胶件变形、收缩不均匀等问题。
解决方法是根据塑胶件的材料特性和实际使用要求进行合理的壁厚设计。
二、材料方面的缺陷:1.材料质量问题:不合格的原料质量可能导致塑胶件出现异味、颜色不均匀等问题。
解决方法是选择合格的塑料原料供应商,并进行原料的严格检验。
2.材料混合不均匀:塑料材料在加工过程中没有充分混合均匀可能导致塑胶件的颜色不均匀等问题。
解决方法是进行充分的原料预处理和混炼,确保塑料材料的均匀性。
3.熔体温度不均匀:塑料材料在注塑过程中温度不均匀可能导致塑胶件尺寸偏差、表面气泡等问题。
解决方法是调整注塑机的温度控制系统,确保熔体温度均匀稳定。
三、工艺方面的缺陷:1.注塑工艺参数设置不当:注塑过程中,如射胶压力、射胶速度、冷却时间等工艺参数设置不当可能导致塑胶件出现尺寸偏差、气泡、表面缺陷等问题。
解决方法是根据塑料的特性和产品要求进行合理的工艺参数设置。
2.模具温控不均匀:模具温度不均匀可能导致塑胶件出现收缩不一致、尺寸偏差等问题。
解决方法是进行模具温度分析和温控系统的优化。
可以采用热流道模具、快速温度控制系统等技术手段解决问题。
3.模具保养不当:模具的使用寿命长,如果没有进行定期的保养和维修可能导致塑胶件出现模纹、模具磨损等问题。
塑胶件常见成型缺陷及改善策略
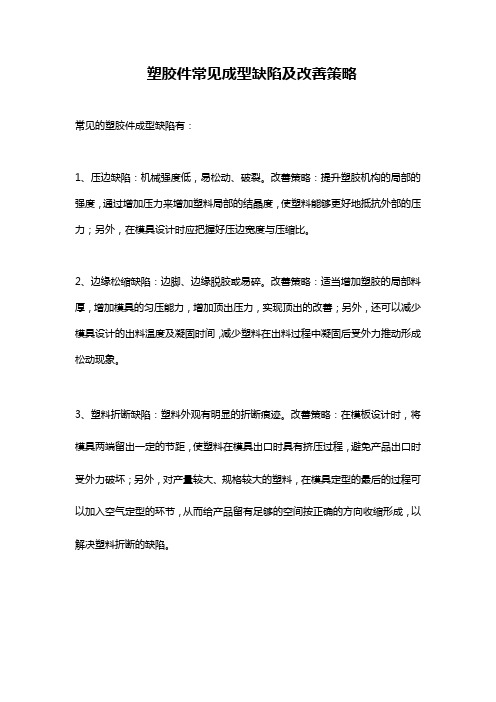
塑胶件常见成型缺陷及改善策略
常见的塑胶件成型缺陷有:
1、压边缺陷:机械强度低,易松动、破裂。
改善策略:提升塑胶机构的局部的强度,通过增加压力来增加塑料局部的结晶度,使塑料能够更好地抵抗外部的压力;另外,在模具设计时应把握好压边宽度与压缩比。
2、边缘松缩缺陷:边脚、边缘脱胶或易碎。
改善策略:适当增加塑胶的局部料厚,增加模具的匀压能力,增加顶出压力,实现顶出的改善;另外,还可以减少模具设计的出料温度及凝固时间,减少塑料在出料过程中凝固后受外力推动形成松动现象。
3、塑料折断缺陷:塑料外观有明显的折断痕迹。
改善策略:在模板设计时,将模具两端留出一定的节距,使塑料在模具出口时具有挤压过程,避免产品出口时受外力破坏;另外,对产量较大、规格较大的塑料,在模具定型的最后的过程可以加入空气定型的环节,从而给产品留有足够的空间按正确的方向收缩形成,以解决塑料折断的缺陷。
塑料件常见不良
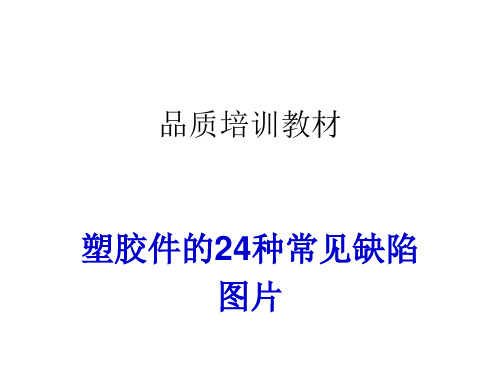
十三、破损/缺口:尤其是对插口不可以有。
破损/缺口
十四、油污:外观件、浅色件特别明显
油污NG!
披锋
毛边
六、多胶:
多胶 NG
七、黑点/异色点:在零件表面有不同的颜色
黑点NG!
八、变形:
平面中间拱起变形
柱子弯曲变形
九、披锋丝(拉丝):
披锋丝(拉丝)NG
十、顶高(顶白):顶针把零件表面顶起
顶高(顶针印)
十一、顶穿(顶破): 顶针把零件表面顶出深坑 甚至零件被顶穿破
顶穿
十二、烧焦:通常表面有细微孔状,色泽发暗
品质培训教材
塑胶件的24种常见分
缩水(凹痕) 缩水(凹痕)
二、气纹:塑料件表面明显的光泽差异
气纹
三、缺料:零件不完整
缺料
四、水口(进胶口)不平整: 所有塑料件都有进胶点, 通常高度小于0.1mm
水口不平
五、披锋(毛边):所有的分型线都会存在, 通常高度小于0.1mm
塑胶产品外观常见不良分析

塑胶产品外观常见不良分析塑胶产品在日常生活中被广泛使用,它们可以用于制作各种产品,如家庭用品、工业部件、玩具等。
由于制作工艺以及原材料的原因,塑胶产品的外观常常会出现一些不良,这不仅会影响产品的美观度,还有可能影响产品的性能和使用寿命。
对于塑胶产品的外观不良分析非常重要。
下面我们将对常见的塑胶产品外观不良进行分析。
一、表面缺陷1. 水波纹水波纹是指塑胶产品表面出现的波纹状不平整,通常是由于注塑时模具温度不均匀或注射压力不稳定造成的。
如果注射速度过快或者模具表面磨损,也会导致水波纹的出现。
水波纹不仅影响塑胶产品外观美观度,还可能降低其强度和耐磨性。
2. 毛刺毛刺是指塑胶产品表面出现的细小而锋利的突起,在注塑工艺中,毛刺通常是由于模具设计不当或者模具磨损严重造成的。
毛刺会影响产品的手感和安全性,同时也会影响产品的使用寿命。
3. 烧结烧结是指塑胶产品表面出现的凹凸不平的现象,通常是由于模具温度设置不当或者注塑过程中料温不均匀导致的。
烧结会影响产品的美观度和尺寸精度,严重时还会导致产品的性能下降。
二、色差1. 色泽不均匀在注塑过程中,如果原料的分散性不好或者混料不均匀,就会导致塑胶产品的表面色泽不均匀。
这不仅会影响产品的外观质量,还会影响产品的一致性和品质稳定性。
三、气泡气泡是指塑胶产品表面或内部出现的空洞状现象,通常是由于注塑过程中原料受潮或者含有挥发性成分,或者注射压力不足造成的。
气泡会影响产品的外观质量和性能稳定性,甚至会导致产品的强度和密封性下降。
四、变形针对上述常见的塑胶产品外观不良,我们可以采取一些措施来进行预防和解决。
对于表面缺陷,我们可以通过优化模具设计,提高模具制造精度和加工质量,以及优化注塑工艺参数来减少水波纹、毛刺和烧结的出现。
对于色差问题,我们可以选择优质的原料并保证混料均匀,严格控制注塑工艺参数,尽量避免色泽不均匀和色斑的出现。
对于气泡和变形问题,我们可以在原料筛选和混合过程中严格控制原料含水量和挥发性成分,保证原料质量。
塑胶件常见缺陷产生的原因及解决方法

塑胶件常见缺陷产生的原因及解决方法1.原材料质量问题:塑胶件常见的原材料问题包括原材料中含有杂质、原料失效、原料配比不正确等。
这些问题会导致塑胶件的质量下降和性能降低。
解决方法是对原材料进行严格的检验和筛选,确保原材料的纯度和质量。
2.模具设计问题:模具设计不合理可能导致塑胶件的缺陷,例如模具壁厚不均匀、模腔表面粗糙等。
解决方法是对模具进行合理设计,确保模具的结构和尺寸满足产品要求,并提高模具的制造工艺和加工精度。
3.注塑工艺问题:注塑过程中的工艺参数设置不当会导致塑胶件出现缺陷,例如温度不稳定、压力不均匀、注射速度过快等。
解决方法是优化注塑工艺参数,确保温度、压力、速度等参数的稳定和均匀。
4.模具磨损和损坏:长时间使用会导致模具磨损和损坏,影响塑胶件的质量和外观。
解决方法是加强模具的保养和维护,定期进行模具清洁和润滑,并进行必要的修复和更换。
5.后道工艺问题:塑胶件的后道加工也可能引发缺陷,例如焊接不牢固、喷涂不均匀等。
解决方法是加强后道工艺的控制,提高工艺的稳定性和一致性。
综上所述,要解决塑胶件常见缺陷的问题,需要从原材料选择、模具设计、注塑工艺、模具维护和后道工艺等方面入手,通过优化和控制各个环节,提高产品的质量和性能。
同时,还需要建立健全的质量管理体系,对生产过程进行全面监控和检测,及时发现和解决问题。
最后,还应该加强员工的培训和技能提升,提高操作技术和质量意识,提高产品的一致性和稳定性。
只有通过不断改进和严格控制,才能有效降低塑胶件的缺陷率,提高产品的质量和市场竞争力。
塑胶件常见缺陷产生的原因及解决方法

塑胶件常见缺陷产生的原因及解决方法一、材料问题1.材料选择不当:选择不适合的塑胶材料或材料质量不达标,容易导致塑胶件的缺陷。
解决方法是根据具体要求选择合适的塑胶材料,并进行必要的材料测试和质量控制。
2.材料批次差异:不同批次的塑胶材料可能存在差异,如流动性、收缩率等,导致成型件的缺陷。
解决方法是进行材料测试和合理的材料配方设计,确保不同批次的材料性能稳定一致。
二、工艺问题1.注塑工艺参数不合理:注塑工艺参数(如注射速度、保压时间等)不合理会导致成型件的缺陷,如短流、气泡等。
解决方法是通过优化注塑工艺参数,使之更加合理和稳定。
2.注塑模具设计和制造问题:模具结构不合理、尺寸精度不达标等问题会导致成型件的缺陷,如模具表面瑕疵、尺寸偏差等。
解决方法是进行合理的模具设计和制造,并进行必要的模具修整和维护。
3.注塑材料温度控制不当:材料温度过高或过低都会导致成型件的缺陷,如熔接线、气泡等。
解决方法是通过调整料筒温度、模具温度等进行合理的温度控制。
4.模具开合不良:模具开合不良或夹模力不足会导致成型件的缺陷,如模具压痕、塌陷等。
解决方法是保持模具开合顺畅,并确保夹模力适当。
三、设计问题1.设计尺寸不合理:设计尺寸过大或过小、壁厚不均匀等问题会导致成型件的缺陷,如尺寸偏差、变形等。
解决方法是根据塑胶件的使用要求和成型工艺特点进行合理的尺寸设计,并进行必要的尺寸优化。
2.设计结构不合理:设计结构复杂、壁薄部位过多等问题容易导致成型件的缺陷,如留痕、焊痕等。
解决方法是简化设计结构、增加加强筋等措施,提高塑胶件的强度和表面质量。
3.装配接口设计不当:塑胶件的装配接口设计不当会导致装配困难、配套件脱落等问题,影响整体使用效果。
解决方法是合理设计装配接口,确保装配紧固可靠。
以上是塑胶件常见缺陷产生的原因及解决方法的概述。
在实际生产中,还需要根据具体情况进行详细分析和解决。
为了确保塑胶件的质量,需要在材料选择、工艺控制和设计优化等方面进行全面的控制和改进。
塑胶产品缺陷及外观检验标准培训
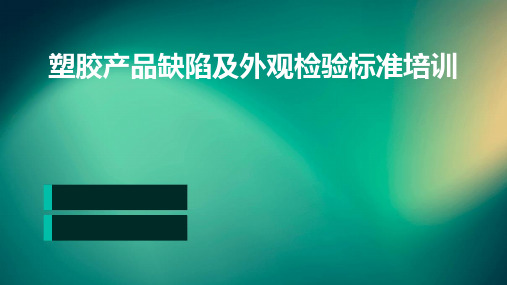
环境因素
生产环境湿度、温度等条件不 符合要求,对产品质量产生不
良影响。
02 塑胶产品外观检验标准
检验方法与工具
目视检验
通过肉眼或放大镜观察塑胶产 品的表面和结构,检查是否存
在缺陷。
触觉检验
通过触摸塑胶产品,感受其表 面和边缘的平滑度、质地等, 判断是否存在缺陷。
测量工具
使用卡尺、千分尺等测量工具 ,对塑胶产品的尺寸进行测量 ,确保符合要求。
素质的要求。
加强与企业的合作
与相关企业建立更紧密的合作关 系,了解企业需求,为企业提供 定制化的培训服务,共同推动行
业发展。
THANKS FOR WATCHING
感谢您的观看
分类
塑胶产品缺陷可以根据产生原因 、表现形式等进行分类,如成型 缺陷、老化缺陷、污染缺陷等。
常见塑胶产品缺陷
气泡
塑胶产品内部存在气体, 导致产品外观不实或透
明度降低。
缩痕
由于模具温度不均或注 射压力不足,导致塑胶 产品表面出现凹陷或凸
起。
银纹
由于塑胶分子排列紊乱 或内应力过大,导致产 品表面出现类似金属光
案例二:喷涂件表面缺陷处理
总结词
喷涂件表面缺陷处理
详细描述
喷涂件表面可能出现的缺陷,如色差、流痕、剥落等,以及如何通过调整工艺参 数和涂料配方来改善表面质量。
案例三:组装件配合面质量检查
总结词
组装件配合面质量检查
详细描述
组装件配合面的常见缺陷,如间隙、错位、松动等,以及如何通过控制组装工艺和零件精度来提高配合质量。
缺陷识别方法
01
02
03
外观检查
通过目视、触摸等方式检 查产品表面是否存在缺陷, 如划痕、凹痕、气泡等。
塑胶件常见缺陷

一.塑膠注塑件一般出現的問題:1.粘模(扯模):制品的柱筋及細小多型腔件,在脫模後未能脫模而粘附在模具相應位置;通常因成型壓力偏大,或模具局部粗糙等因素導致.2.走不齊(填充不足):制品結構與所設計的形狀結構不符,局部膠位不滿足,短少,塑件未能完全充滿.通常產生於制品的柱,孔或薄膠位以及離入水口較遠部位,因成型壓力不夠,模濕不足,骨位過薄,局部有油或排氣不夠(困氣)導致膠位不能填充滿.3.多膠:制品結構與所設計的形狀結構不符,局部多出膠位,或塑件表面有點狀物,四周凹陷中間击起,指甲可感覺到,通常由模具成型面碰,崩缺,損傷及細小型芯頂針移位或斷掉導致.4.縮水:制品表面因成型時,冷卻硬化收縮,產生的肉眼可見凹坑或窩狀現象稱為縮水.制品結構的較厚膠位,如骨位,柱位等對應表面,因成型壓力不足,保壓及射膠時間偏短,或模溫偏高,而導致因局部收縮偏大成而造成.、5.夾水紋(熔接痕):熔膠在模腔內流動中分流後再匯合時不充分,不能完全熔合,冷卻後在塑件表面形成的線狀痕跡和線裝熔接縫.因模溫偏低,料溫偏低,制品局部偏薄或模具有粗大型芯及材料流動性不好等都會導致夾水紋產生.溫度及困氣也對其有最大影響.6.烘xx(光影):制品厚薄膠位在熔膠流動時受阻改變方向而形成的光澤不一致現象.通常在水口周圍,塑件表面呈光澤度不夠,顏色灰蒙.制品結構的薄膠位,止口位,扣位與周圍過渡斷差明顯,原料流動性溫差,成型料溫.模溫偏低或射膠壓力速度太大,模具排氣不良,啤塑壓力過高皆易產生烘印.7.披鋒(xx邊):制品的邊,棱,孔,柱端等模具型腔內所有分模線,鑲塊及頂針位相對應位成型後產生較薄的膠料,稱為披鋒,有刺手感覺.合模線,鑲件頂針及活動碰撞位產生較大間隙或成型壓力太大,模具日久磨損,而鎖模不緊,鎖模力不足時易導致披鋒產生.8.氣紋:在入水口位,走膠盡頭及翻水位(在較高寬大骨筋位走膠需改變方向)對應表面形成的與周圍顏色暗,朦的現象.通常因成型射膠速度太大或太小,壓力偏小及模溫偏低,料溫太高導致.9.困氣:制品成型之流程盡頭位置出現的因氣蝕而發亮的現象.模具排氣結構不足,原材料含低分子成分或水分較多,料溫模溫偏高而導致成型時,氣體無法及時排除模腔被壓縮對制品表面造成鋟蝕.10.燒焦:制品表面呈灰白,黃,橙色條狀變色痕跡.通常因困氣或流道,射嘴,料筒有尖銳傷痕位,熔膠在高速流動時受剪切而降解變色,呈燒焦狀.11.混色:制品表面旦線團塊狀與周圍顏色不一致,顏色不均的現象.通常出現在口澆口附近,熔合部位或整個塑件上.原材料和色粉含雜料,或混和不充分,塑化不良導致制品表面顏色不均勻,彩色顏件最容易形成,也與料筒清潔或背壓有關.12.發白:制品水口有脫模時爆裂,發白或不規則斷裂.因成型壓力大,射膠(保壓)(冷卻)時間太長或頂出太快(頂針分佈不合理),水口不光滑等原因導致脫模時水口受力偏大而發生不良,主要發生在透明制品,使用較脆膠料(如PS,PMMA等料).13.水口加工不良:制品水口被剪除偏高,偏低,白化變形,熱剪後卷起及漏加工等.因加工方法不合理,或加工工具不合適,加工不認真,導致水口位加工不合要求,影響外觀或裝配.14.鋸齒邊:加工部位被加工太多或加工面不平滑,因加工方法,工具或人為因素而導致.15.麻點:制品光滑表面出現的細小密集點狀击起,模糊不清晰,指圍感覺不到,稱為麻點.因材料內含有的輔助劑(如防火PC料的陰燃劑),或成型工藝不合理而導致,或原料本身或熔料不好引起.16.拖傷:制品的側邊,孔等位置在脫模時被拖成的痕跡,因制品側邊,孔等位置脫模斜度不夠,蝕紋偏粗或脫出受力偏大導致.17.拖花:出模後造成損傷.通常出現在邊角位上,可能因出模角度與紋路有問題引起.18.拖白:制品的側邊,柱孔等位脫模時產生的發白現象.因制品的側邊,柱孔等位脫模斜度不夠,蝕紋偏粗局部不夠光滑,而導致脫出受力偏大導致.19.頂白:頂針位在脫模頂出時,使對應表面出現發白痕跡或清晰白印,向上击起.因頂針分佈不合理,頂針位結構偏薄.模具頂針過少,或頂出太快,冷卻時間不足,而導致頂傷制品.20.拖絲:水口脫出時,從射嘴拖出的絲狀物未被清除而被成型粘復到焉一制品的表面,呈絲線狀或線狀痕,稱拖絲.因射嘴溫度偏高,或模溫不當,或防流涎裝置不良,或成型工藝不合理導致.21.冷膠:與制品整體膠料未完全融合,有清晰分界線的團塊狀的現象.因模具流道及射嘴等位在上啤時溢出或斷裂遺留的未清除冷膠被成型到下一啤制品外表面所致.22.料花:制品表面細小不規則的冷膠料,稱料花.因模具流道和型腔內遺留有上一啤脫模時的細小碎膠料被成型到下一啤制品上所致.23.氣泡:塑料在充模過程中受到氣體的干擾而在制品表面上呈現中空狀击起,或透明制品膠位內中空泡狀.由塑膠原料水分含量偏大,低分子產物含量偏大,料溫偏高,或背壓不夠,成型工藝不合理,冷卻時間不足等原因造成.24.油漬:制品上附著有模具上的油跡(防銹油,頂針油,或黃油等).在塑件表面呈不規則痕跡,影響塑件光澤度.模具結構位用油太多,清除不夠干凈導致表面產生的斑點狀發亮現狀,稱為油點.頂針及行位,導柱部位用油較多,運動時滴落到模腔內.25.手指印:制品表面有手指印跡.因手指有油污,汗漬而手指接觸到制品表面而產生的印跡.26.膠漬:制品蝕紋部位不規則光亮痕,光滑面呈霧狀,麻點狀不光亮現象.模具表面被細微膠粉遮蓋或被低分子產物遮蔽,而導致制品表面不能清晰表現設計的狀態.27.黑點(雜質點):制品表面的呈不同於制品顏色的點,線狀異物,因原材料,色粉內有異物,或環境中的雜質及模具活動部分損傷的金屬等吸附到模具型腔,而成型到制品表面所致.28.衝紋(流紋):制品表面沿流動(填充)方向呈現的蛇形或放射狀的紋路,呈花紋狀流痕,清晰可見,指圍感覺不到,稱衝紋.因模溫太低或太高,射速過低,或射速過快,半凝固料受到熱熔料推擠而導致.白色件最容易產生.二.塑膠組件一般容易出現的問題:1.尺寸不符:制品尺寸超出圖紙或規定的控制尺寸範圍.因成型時壓力偏大偏小,射膠時間偏長偏短或模具局部鑲件及活動結構位鬆動等原因造成.2.偏位(shift):一般指螺絲柱,孔位等偏離中心,嚴重者會破裂.3.裝配鬆緊:相關制品在組裝時,偏鬆偏緊,影響到產品的使用功能效果或造成生產線裝配困難.因相關制品尺寸超差或結構位不良導致.4.裝配間隙大:相關制品在組裝後,在邊或角位產生間隙(通常以不大0.2mm為合格).因相應制品變形或尺寸超差及局部缺陷導致.5.裝配刮手(段差或錯位):相關制品在組裝後,邊或角位單獨移出,形成斷面差,觸摸刮手.(通常以不大0.2mm為合格)6.裝配卡鍵(JAM KEY):字鈕鍵組裝到相應鈕孔位,字鈕鍵不能順暢按設計功能作回復運動.字鈕孔位有披鋒或尺寸大,按鈕鍵偏大偏小或高度低等原因導致.7.機身不平(變形):相應制品組裝後在自然放置時,機身底部不平(通常以不大於0.2mm腳不平為合格).相關制品因為尺寸超差,扣位不合,收螺絲不平衡,成型及包裝導致扭曲變形而造成.8.虛扣(扣位高低):相關組合件,組裝後扣位未扣實,用手掰開或跌落震機試驗,扣位會張開形成明顯間隙.扣位尺寸超差或整件尺寸超差(模具成型扣位部分鑲件或行位鬆動變形)導致.9.柱爆(xx):柱孔在打螺絲時被打爆裂或發白,或按規定次數重復打螺絲時收不緊(不能受力),柱孔直徑或深度不符,或所用原料機械性能不夠,成型時料溫偏高使機械性能降低而導致.三.塑膠成品一般容易出現的問題:1.噴涂類:(1)塑膠顏色不符:制品外表顏色或蝕紋效果與樣板不一樣(超出一PantoneNo為顏色不符).通常因色粉(色種)配比,原料的底色,料溫的高低造成.(2)顏色不符:噴涂後制品表面顏色不同於樣板或規定的顏色.(通常以一個PantoneNo為標準,超出為不合格).歷為所用油墨色與塑膠件顏色不同,或噴涂層偏厚偏薄導致色差.(3)位置不符:規定噴油的部分未噴或不需噴油的部位被噴上油墨.不明確要求或噴涂工具和程序不合適而導致.(4)粗糙:制品表面噴油層手感不光滑,因噴槍調節不合適,噴涂距離偏近或油墨不符造成.(5)蜂窩點:制品表面噴油層有密集凹陷坑點狀痕.因噴涂方式及噴槍調節不當導致.(6)啞色:指制品表面噴油層不夠光亮,色澤偏暗偏朦.油墨配比不當或噴涂時間距離偏遠或偏近導致.(7)光亮:制品表面噴油層光滑,返光耀眼(通常以樣板程度為標準控制).因油墨配比不當或噴涂層太厚造成.(8)砂紙痕:制品表面噴油層呈現的塊狀條形痕跡.對噴油部位不良缺陷用砂紙加工時,砂紙偏粗,或加工力度偏大導致.(9)有塵:制品表面噴油層呈現,點線狀明顯击起.因制品暴露在環境中時間偏長,環境不夠干凈,油墨不夠純凈而導致.(10)污糟:指制品表面噴油層有不可擦拭清除的髒物,噴槍用壓縮空氣水分含量大,制品表面髒未清除干淨等因素導致噴油後的污糟。
塑胶件常见的缺陷产生原因及解决办法
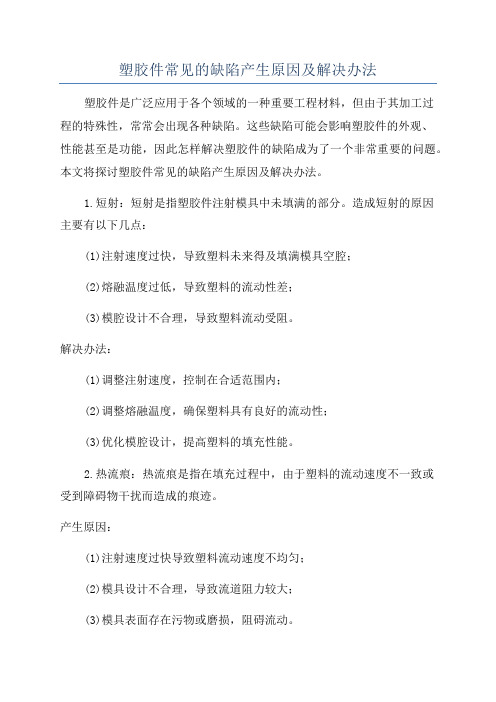
塑胶件常见的缺陷产生原因及解决办法塑胶件是广泛应用于各个领域的一种重要工程材料,但由于其加工过程的特殊性,常常会出现各种缺陷。
这些缺陷可能会影响塑胶件的外观、性能甚至是功能,因此怎样解决塑胶件的缺陷成为了一个非常重要的问题。
本文将探讨塑胶件常见的缺陷产生原因及解决办法。
1.短射:短射是指塑胶件注射模具中未填满的部分。
造成短射的原因主要有以下几点:(1)注射速度过快,导致塑料未来得及填满模具空腔;(2)熔融温度过低,导致塑料的流动性差;(3)模腔设计不合理,导致塑料流动受阻。
解决办法:(1)调整注射速度,控制在合适范围内;(2)调整熔融温度,确保塑料具有良好的流动性;(3)优化模腔设计,提高塑料的填充性能。
2.热流痕:热流痕是指在填充过程中,由于塑料的流动速度不一致或受到障碍物干扰而造成的痕迹。
产生原因:(1)注射速度过快导致塑料流动速度不均匀;(2)模具设计不合理,导致流道阻力较大;(3)模具表面存在污物或磨损,阻碍流动。
(1)调整注射速度,确保塑料流动速度均匀;(2)优化模具设计,减小流道阻力;(3)定期保养模具,确保模具表面光洁无污物。
3.翘曲:翘曲是指塑胶件在冷却过程中由于收缩不均匀而造成的扭曲变形。
产生原因:(1)注射过程中温度分布不均匀,导致冷却速度不均匀;(2)部分材料的收缩率较大,造成不均匀收缩;(3)模具设计不合理,导致冷却不均匀。
解决办法:(1)控制注射过程中的温度分布,确保全面均匀冷却;(2)使用收缩率较小的材料;(3)优化模具设计,确保冷却均匀。
4.气泡:气泡是塑胶件内部或表面存在的气体囊状物。
产生原因:(1)注射过程中,塑料因挤压和高温导致内部气体产生;(2)注射过程中,未充分排除空气导致气泡残留;(3)塑料材料含有挥发性成分,造成气泡。
(1)调整注射过程中的温度和压力,减少气体产生;(2)注射过程中加入真空排气步骤,充分排除空气;(3)选择不含挥发性成分的塑料材料。
5.纹痕:纹痕是塑胶件表面存在的细微沟纹。
塑胶件常见缺陷及原因分析

塑胶行业-塑胶件常见缺陷塑胶件常见缺陷;1.塑胶成品缺陷;粘模(扯模):制品的柱筋及细少多型腔件,在脱模后;力偏大,或模具局部粗糙等因素导致;缺料(填充不足):制品结构与所设计的形状结构不符;充满,常产生于制品的柱,孔或薄胶位以及离入水口较;力不够,模温不足,骨位过薄,局部有油或排气不够(;充满;多胶:制品结构与所设计的形状结构不符,局部多出胶;间凸起,指甲可感觉到;缩水:制品表面塑胶件常见缺陷1.塑胶成品缺陷粘模(扯模):制品的柱筋及细少多型腔件,在脱模后未能脱模而粘附在模具相应位置因成型压力偏大,或模具局部粗糙等因素导致。
缺料(填充不足):制品结构与所设计的形状结构不符,局部胶位不满足,短少,塑件未能完全充满,常产生于制品的柱,孔或薄胶位以及离入水口较远的部位,因成型压力不够,模温不足,骨位过薄,局部有油或排气不够(困气)导致胶位不能填充满。
多胶:制品结构与所设计的形状结构不符,局部多出胶位,或塑件表面有点状物,四周凹陷中间凸起,指甲可感觉到。
通常由模具成型面碰,崩缺,损伤及细小型芯顶针移位或断掉导致。
缩水:制品表面因成型时,冷却硬化收缩,产生的肉眼可见凹坑或窝状现象称为“缩水”。
制品结构的较厚胶位如骨位,柱位等对应表面,因成型压力不足,保压及射胶时间偏短,或模温偏高,而导致因局部收缩偏大而造成。
夹水纹(熔接痕):熔胶在模腔内流动中分流后再汇合时不充分,不能完全熔合,冷却后在塑件表面形成的线状痕迹和线状熔接缝,模温偏低,料温偏低,制品局部偏薄或模具有粗大型芯及材料流动性不好等都会导致夹水纹的产生,温度及困气也对其有最大影响。
烘印(光影):制品结构的厚薄胶位在熔胶流动时受阻改变方向而形成的光泽不一致的现象,通常在水口周围,塑件表面呈光泽度不够,颜色灰蒙。
制品结构的薄胶位,止口位,扣位与周围过渡断差明显,原料流动性差,成型料温、模温偏低或射胶压力速度太大,模具排气不良,啤塑压力过高皆易产生烘印。
塑胶件常见缺陷分析

塑胶件常见缺陷分析:1.翘曲变形:注塑过程中结结晶高分子沿流动方向、取向,导致流动方向与垂直于流动方向收宿不一。
2.熔接痕:由于模具采用多浇口结构,在模具中流动的熔体渐冷后汇合时产生熔接痕。
3.收缩凹陷:由于制品存在加强筋,因壁厚不均而导致收缩不匀的结果。
以上缺陷改善:1.料温:提高料温有利于塑化并降低熔体粘度及流动阻力,浇口冻结速度减缓补宿作用增大(收宿率减小),同时料温升高后,料流前端温度也会相应升高,有利于减轻熔接痕。
2.模温:提高模温可改善充模情况,减轻熔接痕,3.注射压力:注射压力大,制品产生的负收宿,负收宿与其他收宿抵消,降低制品收宿,还可提高熔接痕强度,但注塑压力过大,成型后因制品收宿不一而产生收宿翘曲。
4.增压力和保压力影响:增压既压实阶段,增压力应略低于注射压力,时间较短,保压力大,可增加补料量,从而减少了收宿凹陷,但也使制品残余应力增大,因此为改善制品质量应采用分段逐级下降的保压力。
5.注射速度(时间)影响:合理提高注射速度,缩段注射时间,料流汇合处温度将明显升高,熔接痕相应减轻,但一方面注射速度提高,收缩率增大,另一方面注射速度过大,模腔内气体来不及排出,反而会加强熔接痕,严重会灼伤制品。
6.保压时间影响。
7.冷却时间影响:冷却时间越长,收缩率越小,变形越小。
8.浇口和喷嘴孔:增多和增大浇口和喷嘴孔,制品的增压力和保压力补缩作用明显加强,收缩凹陷减少,熔接痕明显减轻。
9.加强筋:使加强筋转角处壁厚过渡均匀,可减小收缩不均匀,减轻收缩凹陷。
10.精确度控制模温:11.顶出及排气:采用二次顶出,即先用适当气压,通过气动将制品吹出凸模,然后液压顶出制品,用机械手自动取件,在制品产生熔接痕处,开设排气槽,可减轻熔接痕。
12.蛇流纹:当浇口深度比模腔入口深度小很多,而且充模速度很高,熔体流动变成不稳定的射流流动时,前面的射流已凝固,后面的流动熔体充满模腔,在制品表面上就像一条蛇,解决措施是:1)改变工艺条件,降低注射速度,逐渐消除射流效应,提高模温和熔体温度。
塑胶产品常见缺陷及对策
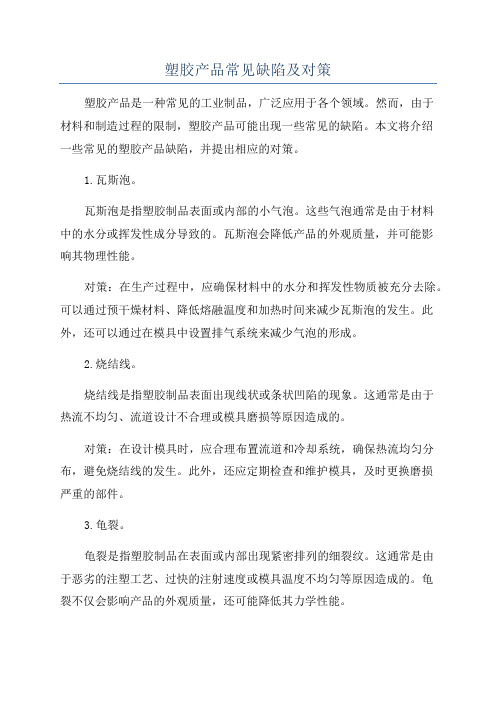
塑胶产品常见缺陷及对策塑胶产品是一种常见的工业制品,广泛应用于各个领域。
然而,由于材料和制造过程的限制,塑胶产品可能出现一些常见的缺陷。
本文将介绍一些常见的塑胶产品缺陷,并提出相应的对策。
1.瓦斯泡。
瓦斯泡是指塑胶制品表面或内部的小气泡。
这些气泡通常是由于材料中的水分或挥发性成分导致的。
瓦斯泡会降低产品的外观质量,并可能影响其物理性能。
对策:在生产过程中,应确保材料中的水分和挥发性物质被充分去除。
可以通过预干燥材料、降低熔融温度和加热时间来减少瓦斯泡的发生。
此外,还可以通过在模具中设置排气系统来减少气泡的形成。
2.烧结线。
烧结线是指塑胶制品表面出现线状或条状凹陷的现象。
这通常是由于热流不均匀、流道设计不合理或模具磨损等原因造成的。
对策:在设计模具时,应合理布置流道和冷却系统,确保热流均匀分布,避免烧结线的发生。
此外,还应定期检查和维护模具,及时更换磨损严重的部件。
3.龟裂。
龟裂是指塑胶制品在表面或内部出现紧密排列的细裂纹。
这通常是由于恶劣的注塑工艺、过快的注射速度或模具温度不均匀等原因造成的。
龟裂不仅会影响产品的外观质量,还可能降低其力学性能。
对策:在注塑工艺中,应控制好注塑温度、注射速度和保压时间,确保塑胶材料在模具中充分流动。
此外,还应合理设计模具和冷却系统,使模具温度均匀分布,避免龟裂的发生。
4.黑点。
黑点是指塑胶制品表面或内部出现的黑色颗粒状或斑点状物质。
这通常是由于材料中的杂质或染料不均匀引起的。
黑点会降低产品的外观质量,并可能影响其物理性能。
对策:在生产过程中,应使用质量可靠的原材料,并进行严格的杂质筛选和质检。
如果发现杂质,应及时清理或更换材料。
此外,还应控制好加料的方式和量,确保染料均匀分散。
5.尺寸偏差。
尺寸偏差是指塑胶制品的实际尺寸与设计尺寸之间的差距。
这可能是由于模具磨损、注塑工艺调整不当或材料热收缩不一致等原因造成的。
对策:在生产过程中,应定期检查和维护模具,确保其尺寸精度。
塑胶件常见缺陷产生原因及改善对策

塑胶件常见缺陷产生原因及改善对策塑胶件是指由塑胶材料制作而成的零件,广泛应用于汽车、家电、电子产品和日常生活用品等领域。
然而,在塑胶件的制造过程中,常常会出现各种缺陷,如气泡、砂眼、短斑、热裂、脱模、射出不完整等。
这些缺陷会降低产品的质量,甚至影响使用安全。
以下是塑胶件常见缺陷的产生原因及改善对策。
1.气泡气泡是塑胶件中最常见的缺陷之一,主要由以下因素引起:-塑料原料中含有水分,造成蒸汽产生气泡。
改善对策是通过加热塑料原料预干燥或使用干燥剂。
-射出过程中模具中的空气未排除干净。
改善对策是增加射出压力和速度,确保模具中的空气能够顺利排出。
-射出过程中塑料材料的熔体温度过高,产生气泡。
改善对策是调整射出温度,确保熔体温度适中。
-高分子量的塑料材料在射出过程中分解产生气体。
改善对策是选择合适的塑料材料。
2.砂眼砂眼是指塑胶件表面出现的小凹陷或凸起,主要由以下原因引起:-模具中存在异物,例如灰尘、沙粒等。
改善对策是保持模具清洁,及时除去异物。
-射出过程中模具表面未润滑充分,塑胶材料无法充分填充模具。
改善对策是增加模具表面的润滑剂,提高材料的流动性。
-射出过程中,模具温度不均匀,造成材料凝固不均匀。
改善对策是调整模具的温度分布,保持均匀加热。
-模具设计不合理,造成材料流动不畅。
改善对策是优化模具结构,提高充型性能。
3.短斑短斑是指塑胶件表面上呈现出短小裂纹的缺陷,造成塑胶件强度下降,主要由以下原因引起:-射出过程中,塑料材料受到过高的剪切力和拉伸力。
改善对策是调整射出速度和压力。
-模具设计不合理,造成材料流动不畅。
改善对策是优化模具结构,提高充型性能。
-射出过程中,塑料材料的熔体温度过高。
改善对策是控制射出温度,避免过热。
4.热裂热裂是指塑胶件在冷却过程中由于温度差异过大,导致塑胶材料发生裂纹,主要由以下原因引起:-模具设计不合理,导致塑胶件壁厚不均匀,造成冷却速度不一致。
改善对策是优化模具结构,保证壁厚均匀。
塑胶件常见缺陷及原因分析

塑胶行业-塑胶件常见缺陷塑胶件常见缺陷;1.塑胶成品缺陷;粘模(扯模):制品的柱筋及细少多型腔件,在脱模后;力偏大,或模具局部粗糙等因素导致;缺料(填充不足):制品结构与所设计的形状结构不符;充满,常产生于制品的柱,孔或薄胶位以及离入水口较;力不够,模温不足,骨位过薄,局部有油或排气不够(;充满;多胶:制品结构与所设计的形状结构不符,局部多出胶;间凸起,指甲可感觉到;缩水:制品表面塑胶件常见缺陷1.塑胶成品缺陷粘模(扯模):制品的柱筋及细少多型腔件,在脱模后未能脱模而粘附在模具相应位置因成型压力偏大,或模具局部粗糙等因素导致。
缺料(填充不足):制品结构与所设计的形状结构不符,局部胶位不满足,短少,塑件未能完全充满,常产生于制品的柱,孔或薄胶位以及离入水口较远的部位,因成型压力不够,模温不足,骨位过薄,局部有油或排气不够(困气)导致胶位不能填充满。
多胶:制品结构与所设计的形状结构不符,局部多出胶位,或塑件表面有点状物,四周凹陷中间凸起,指甲可感觉到。
通常由模具成型面碰,崩缺,损伤及细小型芯顶针移位或断掉导致。
缩水:制品表面因成型时,冷却硬化收缩,产生的肉眼可见凹坑或窝状现象称为“缩水”。
制品结构的较厚胶位如骨位,柱位等对应表面,因成型压力不足,保压及射胶时间偏短,或模温偏高,而导致因局部收缩偏大而造成。
夹水纹(熔接痕):熔胶在模腔内流动中分流后再汇合时不充分,不能完全熔合,冷却后在塑件表面形成的线状痕迹和线状熔接缝,模温偏低,料温偏低,制品局部偏薄或模具有粗大型芯及材料流动性不好等都会导致夹水纹的产生,温度及困气也对其有最大影响。
烘印(光影):制品结构的厚薄胶位在熔胶流动时受阻改变方向而形成的光泽不一致的现象,通常在水口周围,塑件表面呈光泽度不够,颜色灰蒙。
制品结构的薄胶位,止口位,扣位与周围过渡断差明显,原料流动性差,成型料温、模温偏低或射胶压力速度太大,模具排气不良,啤塑压力过高皆易产生烘印。
塑胶件常见缺陷产生的原因及解决方法
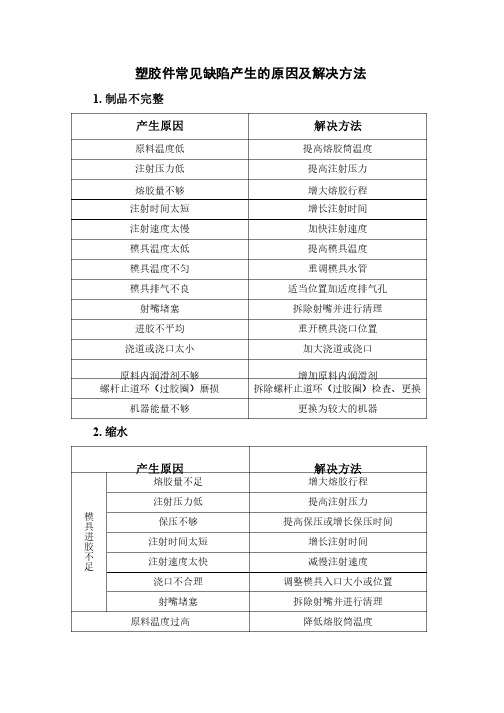
塑胶件常见缺陷产生的原因及解决方法1.制品不完整产生原因解决方法原料温度低原料温度低 提高熔胶筒温度提高熔胶筒温度 注射压力低注射压力低 提高注射压力提高注射压力 熔胶量不够熔胶量不够 增大熔胶行程增大熔胶行程 注射时间太短注射时间太短 增长注射时间增长注射时间 注射速度太慢注射速度太慢 加快注射速度加快注射速度 模具温度太低模具温度太低 提高模具温度提高模具温度 模具温度不匀模具温度不匀 重调模具水管重调模具水管 模具排气不良模具排气不良 适当位置加适度排气孔适当位置加适度排气孔 射嘴堵塞射嘴堵塞 拆除射嘴并进行清理拆除射嘴并进行清理 进胶不平均进胶不平均 重开模具浇口位置重开模具浇口位置 浇道或浇口太小浇道或浇口太小 加大浇道或浇口加大浇道或浇口原料内润滑剂不够原料内润滑剂不够增加原料内润滑剂增加原料内润滑剂螺杆止道环(过胶圈)磨损螺杆止道环(过胶圈)磨损拆除螺杆止道环(过胶圈)检查、更换机器能量不够机器能量不够更换为较大的机器更换为较大的机器2.缩水产生原因解决方法模具进胶不足熔胶量不足熔胶量不足 增大熔胶行程增大熔胶行程 注射压力低注射压力低提高注射压力提高注射压力 保压不够保压不够 提高保压或增长保压时间提高保压或增长保压时间注射时间太短注射时间太短 增长注射时间增长注射时间 注射速度太快注射速度太快 减慢注射速度减慢注射速度 浇口不合理浇口不合理 调整模具入口大小或位置调整模具入口大小或位置 射嘴堵塞射嘴堵塞 拆除射嘴并进行清理拆除射嘴并进行清理 原料温度过高原料温度过高降低熔胶筒温度降低熔胶筒温度模具温度不当模具温度不当 重调模具温度重调模具温度 冷却时间不够冷却时间不够 增加冷却时间增加冷却时间排气不良排气不良 缩水处设排气孔缩水处设排气孔制品本身或其筋、柱过厚制品本身或其筋、柱过厚检讨制品检讨制品 熔胶筒过大熔胶筒过大换较小熔胶筒换较小熔胶筒螺杆止道环(过胶圈)磨损螺杆止道环(过胶圈)磨损拆除螺杆止道环(过胶圈)检查、更换产生原因解决方法填料过饱注射压力太高注射压力太高 降低注射压力降低注射压力 剂量太多剂量太多使用脱模剂使用脱模剂 保压时间太久保压时间太久 减少保压时间减少保压时间 注射速度太快注射速度太快 减慢注射速度减慢注射速度 原料温度过高原料温度过高 降低熔胶筒温度降低熔胶筒温度 进料不均使部分过饱进料不均使部分过饱 变更浇口大小、位置变更浇口大小、位置冷却时间不够冷却时间不够 增加冷却时间增加冷却时间 模具温度过高或过低模具温度过高或过低 调整模温及两侧相对温度调整模温及两侧相对温度模具内有脱模倒角模具内有脱模倒角 修模除去倒角修模除去倒角 模具表面不光模具表面不光打光模具打光模具产生原因解决方法注射压力太高注射压力太高 降低注射压力降低注射压力 原料温度过高原料温度过高 降低熔胶筒温度降低熔胶筒温度 浇道过大浇道过大 修改模具一减小浇道修改模具一减小浇道 浇道冷却不够浇道冷却不够 延长冷却时间或降低熔胶筒温度延长冷却时间或降低熔胶筒温度浇道脱模角不够浇道脱模角不够 修改模具以增加角度修改模具以增加角度浇道凹弧与射嘴之配合不正浇道凹弧与射嘴之配合不正 重新调整其配合重新调整其配合浇道内表面不光或有脱模倒角浇道内表面不光或有脱模倒角修模打光修模打光浇道外孔有损坏浇道外孔有损坏 修模修模无浇道抓锁无浇道抓锁加设浇道抓锁加设浇道抓锁填料过饱填料过饱降低射胶量、射胶时间及速度降低射胶量、射胶时间及速度产生原因解决方法原料温度过高原料温度过高降低熔胶筒温度及模具温度降低熔胶筒温度及模具温度注射压力太高注射压力太高 降低注射压力降低注射压力 填料过饱填料过饱降低射胶量、注射时间及速度降低射胶量、注射时间及速度合模线或模具接触面不良合模线或模具接触面不良检修模具检修模具 锁模压力不够锁模压力不够 增加锁模压力增加锁模压力 制品投影面积过大制品投影面积过大更换为较大机器更换为较大机器产生原因解决方法填料过饱填料过饱 降低注射压力、时间、速度及射胶量降低注射压力、时间、速度及射胶量模具温度太低模具温度太低 提高模具温度提高模具温度 部分倒模角不够部分倒模角不够 修模以增加倒模角修模以增加倒模角有脱模倒角有脱模倒角 修模修模 脱模时不能平衡脱离脱模时不能平衡脱离 修模修模顶针不够或位置不当顶针不够或位置不当 修模增加顶针或更改位置修模增加顶针或更改位置 脱模时模具产生真空现象脱模时模具产生真空现象开模或顶出慢速、加进气设备开模或顶出慢速、加进气设备产生原因解决方法原料熔融不佳原料熔融不佳 提高料温、背压,加快螺杆转速提高料温、背压,加快螺杆转速模具温度太低模具温度太低 提高模具温度提高模具温度 注射速度太慢注射速度太慢 加快注射速度加快注射速度 注射压力太低注射压力太低 提高注射压力提高注射压力 原料不溶或渗有他料原料不溶或渗有他料检查原料检查原料脱模油太多脱模油太多 少量或尽量不用少量或尽量不用浇道及溢口过大或过小浇道及溢口过大或过小 调整模具入口尺寸或改变其位置调整模具入口尺寸或改变其位置模内空气排除不及模内空气排除不及增开排气孔或检查原排气孔是否堵塞增开排气孔或检查原排气孔是否堵塞产生原因解决方法原料熔融不佳原料熔融不佳提高料温、背压,加快螺杆转速提高料温、背压,加快螺杆转速模具温度太低模具温度太低 提高模具温度提高模具温度注射速度太慢或太快注射速度太慢或太快 适当调整注射速度适当调整注射速度 注射压力太高或太低注射压力太高或太低 适当调整注射压力适当调整注射压力原料不洁或渗有他料原料不洁或渗有他料 检查原料检查原料 浇口过小产生射纹浇口过小产生射纹 加大浇口加大浇口制品断面厚薄相差太多制品断面厚薄相差太多变更制品设计或溢口位置变更制品设计或溢口位置产生原因解决方法原料含有水分原料含有水分 烘干、提高背压烘干、提高背压料温过高或模具过热料温过高或模具过热 降低料温、射嘴及前段温度、模具温度原料中其他添加物如润滑剂、原料中其他添加物如润滑剂、染料等分解染料等分解减少其使用量或更换耐温减少其使用量或更换耐温较高之替代品较高之替代品 原料中其他添加物混合不匀原料中其他添加物混合不匀彻底混合均匀彻底混合均匀 注射速度太快注射速度太快 减慢注射速度减慢注射速度 模具温度太低模具温度太低 提高模具温度提高模具温度 原料粒粗细不匀原料粒粗细不匀 使用粒均匀的原料使用粒均匀的原料熔胶筒内夹有空气熔胶筒内夹有空气 降低熔胶筒后段温度、提高背压降低熔胶筒后段温度、提高背压 原料在模内流程不当原料在模内流程不当调整浇口大小及位置使模具温度保持平衡平衡产生原因解决方法模具温度太低模具温度太低 提高模具温度提高模具温度原料之剂量不够原料之剂量不够 增加注射压力、时间、速度及剂量增加注射压力、时间、速度及剂量模内有过多脱模油模内有过多脱模油 擦拭干净擦拭干净模内表面有水模内表面有水 擦拭并看是否漏水擦拭并看是否漏水模内不光模内不光打光打光产生原因解决方法制品顶出时尚未冷却制品顶出时尚未冷却 降低模温、原料温度、延长冷却时间降低模温、原料温度、延长冷却时间 制品定形及厚薄不对称制品定形及厚薄不对称脱模后以定形架固定、改变模具设计脱模后以定形架固定、改变模具设计 填料过多填料过多 降低注射压力、时间、速度及射胶量降低注射压力、时间、速度及射胶量几个浇口进料不平均几个浇口进料不平均 更改浇口更改浇口 顶出机构不平衡顶出机构不平衡 改善顶出系统改善顶出系统 模具温度不均模具温度不均重调模具水管重调模具水管 近浇口部分之原料太松或太紧近浇口部分之原料太松或太紧增加或减少注射时间增加或减少注射时间12.制品内有气孔产生原因解决方法防止过度缩水填料量不足以制品断面肋或柱过厚制品断面肋或柱过厚改变模具设计或浇口位置改变模具设计或浇口位置注射压力太低注射压力太低 提高注射压力提高注射压力 注射时间不足注射时间不足 延长注射时间延长注射时间 浇道、溢口太小浇道、溢口太小 加大浇道及入口加大浇道及入口 注射速度太快注射速度太快 调慢注射速度调慢注射速度 原料含水分原料含水分 彻底干燥彻底干燥 原料温度过高以致分解原料温度过高以致分解降低原料温度降低原料温度模温不平衡模温不平衡调整模温调整模温冷却时间太长冷却时间太长 减少模内冷却时间、使用水浴冷却减少模内冷却时间、使用水浴冷却 水浴冷却过急水浴冷却过急 减短水浴时间或提高水浴温度减短水浴时间或提高水浴温度背压不够背压不够提高背压提高背压熔胶筒温度不当熔胶筒温度不当 降低射嘴及前段温度,提高后段温度降低射嘴及前段温度,提高后段温度产生原因解决方法原料过热部分附着原料过热部分附着熔胶筒管壁熔胶筒管壁 彻底空射、拆除熔胶筒清理、彻底空射、拆除熔胶筒清理、 降低料温、减短加热时间降低料温、减短加热时间 原料混有异物、纸屑等原料混有异物、纸屑等检查原料、彻底空射检查原料、彻底空射射入模内时产生焦斑射入模内时产生焦斑降低注射压力、速度、原料温度,降低注射压力、速度、原料温度, 加强模具排气孔、降低开模压力、加强模具排气孔、降低开模压力、更改入口位置更改入口位置熔胶筒内有使原料熔胶筒内有使原料过热的死角过热的死角检查射嘴与熔胶筒间接触面检查射嘴与熔胶筒间接触面有无间隙或腐蚀现象有无间隙或腐蚀现象产生原因解决方法原料温度过高原料温度过高 降低熔胶筒温度降低熔胶筒温度 螺杆转速太快螺杆转速太快降低螺杆转速降低螺杆转速 螺杆与熔胶筒偏心而产生非常摩擦热螺杆与熔胶筒偏心而产生非常摩擦热检修机器检修机器 射嘴孔过小或温度过高射嘴孔过小或温度过高 重新调整孔径或温度重新调整孔径或温度 熔胶筒或机器过大熔胶筒或机器过大更换为较小的机器更换为较小的机器改变周期产生缺陷加快周期加快周期 短射、缩水、变形、粘模短射、缩水、变形、粘模 减慢周期减慢周期溢料、毛头、粘模、变形、溢料、毛头、粘模、变形、原料过热甚至烧焦原料过热甚至烧焦产生原因解决方法熔胶筒后段温度太高熔胶筒后段温度太高检查循环水,减低后段温度检查循环水,减低后段温度树脂干燥未完全树脂干燥未完全 再干燥填加适当润滑剂再干燥填加适当润滑剂熔胶筒及螺杆磨损熔胶筒及螺杆磨损拆除并更换拆除并更换 胶料料状大小不当胶料料状大小不当 清除料斗进料口清除料斗进料口以其他胶料清洗熔胶筒以其他胶料清洗熔胶筒 背压及熔胶速度不当背压及熔胶速度不当调整重新大熔胶筒降低转速,大熔胶筒降低转速, 小熔胶筒增大转速小熔胶筒增大转速17.射嘴漏胶产生原因解决方法熔胶筒温度过高熔胶筒温度过高 降低熔胶筒温度尤其射嘴段降低熔胶筒温度尤其射嘴段背压调整不当背压调整不当 适当降低背压及螺杆转速适当降低背压及螺杆转速 松退行程不够松退行程不够增加松退时间,更改射嘴头设计增加松退时间,更改射嘴头设计。
- 1、下载文档前请自行甄别文档内容的完整性,平台不提供额外的编辑、内容补充、找答案等附加服务。
- 2、"仅部分预览"的文档,不可在线预览部分如存在完整性等问题,可反馈申请退款(可完整预览的文档不适用该条件!)。
- 3、如文档侵犯您的权益,请联系客服反馈,我们会尽快为您处理(人工客服工作时间:9:00-18:30)。
2011-10-14
VT-PL/PE
40
缺陷: 表面斑点 缺陷:
Defect:Spots on surface
表面斑点
2011-10-14
VT-PL/PE
41
表面斑点改善对策 工艺: 工艺:
1.提高注射速度及注射压力 1.提高注射速度及注射压力 2.增加螺杆转速 2.增加螺杆转速 3.增加背压 3.增加背压 4.提高料筒温度 4.提高料筒温度 模具: 模具: 1.提高模腔表面温度 1.提高模腔表面温度
Defect: weld lines
夹水纹
2011-10-14
VT-PL/PE
3
夹水纹改善对策 工艺: 工艺:
1.提高注射速度 1.提高注射速度 2.增加炮筒温度 2.增加炮筒温度 3.增加保压压力 3.增加保压压力
模具: 模具:
1. 提高模温 2.增大浇口及流道截面积 2.增大浇口及流道截面积 3. 改善模具的排气
原料: 原料:
1.检查原料是否混有杂料 1.检查原料是否混有杂料
2011-10-14
VT-PL/PE
38
缺陷:光泽不一 缺陷:
Defect:G loss differences
光泽不一
2011-10-14
VT-PL/PE
39
光泽不一改善对策 工艺: 工艺:
1.提高注射速度及注射压力 1.提高注射速度及注射压力 2.提高保压压力及保压时间 2.提高保压压力及保压时间 3.提高 3.提高 料筒温度 模具: 模具: 1.均匀模腔表面温度 1.均匀模腔表面温度
模具: 模具:
1.加大 1.加大 浇口截面积 2.移动浇口位置 采用冲击型浇口) 移动浇口位置( 2.移动浇口位置(采用冲击型浇口)
2011-10-14
VT-PL/PE
26
缺陷: 真空泡 缺陷:
Defect:Vacuum
vesicle
真空泡
2011-10-14
VT-PL/PE
27
真空泡改善对策 工艺: 工艺:
模具: 模具:
1.加出模斜度 1.加出模斜度 2.省顺骨位 2.省顺骨位
2011-10-14 VT-PL/PE 34
缺陷: 起皮 缺陷:
Defect: Flaking of surface layer
起皮
2011-10-14
VT-PL/PE
35
起皮改善对策 工艺: 工艺:
1.. 1..降低注射速度 2.充分干燥原料 2.充分干燥原料 3.降低料筒温度 3.降低料筒温度
模具: 模具:
1.提高模腔表面温度 1.提高模腔表面温度
2011-10-14
VT-PL/PE
30
缺陷: 拖白 缺陷:
Defect:DraggingDefect:Dragging-w hitening
拖白
2011-10-14
VT-PL/PE
31
拖白改善对策 工艺: 工艺:
1.降低保压压力及保压时间 1.降低保压压力及保压时间 2.降低注射速度及注射压力 2.降低注射速度及注射压力
模具: 模具:
1.幼化模腔蚀纹 1.幼化模腔蚀纹 2.加大出模斜度 2.加大出模斜度
2011-10-14
VT-PL/PE
32
缺陷: 拉白 缺陷:
Defect:PullingDefect:Pulling-whitening
拉白
2011-10-14
VT-PL/PE
33
拉白改善对策 工艺: 工艺:
1.降低保压压力及保压时间 1.降低保压压力及保压时间 2.降低注射速度及注射压力 2.降低注射速度及注射压力 3.延长冷却时间 3.延长冷却时间 4.降低顶出速度及顶出压力 4.降低顶出速度及顶出压力
19
走胶改善对策 工艺: 工艺:
1.提高注射速度及注射压力 1.提高注射速度及注射压力 2.提高保压压力及保压时间 2.提高保压压力及保压时间 3.提高料筒温度 3.提高料筒温度 4.提高背压 4.提高背压
模具: 模具:
1.增大浇口及流道截面积 1.增大浇口及流道截面积 2.提高模腔表面温度 2.提高模腔表面温度 3.改善模具排气 3.改善模具排气
模具: 模具:
1.改善模具排气 1.改善模具排气 2.防止包气 防止包气(entrapped 2.防止包气(entrapped air)
2011-10-14
VT-PL/PE
18
缺陷: 缺陷:走胶
Defect:incom pletely filled parts
走胶
2011-10-14
VT-PL/PE
VT-PL塑胶件常见缺陷及改善对策 VT-PL塑胶件常见缺陷及改善对策
FM: VT-PL/PE VTPREPARED BY: 周 和 平 APPROVED BY: 叶 铁 波 DATE: Mar 16,2000
2011-10-14 VT-PL/PE 1
2011-10-14
VT-PL/PE
2
缺陷: 夹水纹 缺陷:
1.降低保压压力及保压时间 1.降低保压压力及保压时间 2. 降低顶针压力及顶出速度 3.延长冷却时间 3.延长冷却时间
模具: 模具:
1. 降低模腔 表面温度 2.检查修复模具的倒扣 检查修复模具的倒扣(undercut) 2.检查修复模具的倒扣(undercut) 3.加大顶针的截面积及改善顶针布置 3.加大顶针的截面积及改善顶针布置
原料: 原料:
1.检查原料是否混有杂 1.检查原料是否混有杂 料
模具: 模具:
1.提高模腔表面温度 1.提高模腔表面温度
2011-10-14 VT-PL/PE 36
缺陷: 黑点 缺陷:
Defect: Dark spots
黑点
2011-10-14
VT-PL/PE
37
黑点改善对策 工艺: 工艺:
1.降低料筒温度 1.降低料筒温度 2.降低背压 2.降低背压 3.降低螺杆转速 3.降低螺杆转速 4. 减少残量
2011-10-14
VT-PL/PE
42
VT-PL/PE
6
缺陷: 气花 缺陷: 气花
Defect: air streaks
2011-10-14
VT-PL/PE
7
气花改善对策 工艺: 工艺:
1. 降低注射速度 2 . 充分干燥原料 3. 增加料筒温度 4. 提高背压 5 . 减少 抽 胶行程
模具: 模具:
1. 增大浇口及流道的截面积 2. 提高模腔表面温度
2011-10-14 VT-PL/PE 4
缺陷: 气纹 缺陷:
Defect: air lines
气纹
2011-10-14
VT-PL/PE
5
气纹改善对策 工艺: 工艺:
1. 降低注射速度 2. 增加料筒温度
模具: 模具:
1. 增大浇口截面积 2. 提高模腔表面温度 3. 加深冷料井
2011-10-14
1.增加浇口截面积 1.增加浇口截面积 2.均匀模腔表面温度 2.均匀模腔表面温度
2011-10-14
VT-PL/PE
24
缺陷: 蛇纹 缺陷:
Defect: Jetting
蛇纹
gate
2011-10-14
VT-PL/PE
25
蛇纹改善对策 工艺: 工艺:
1.降低注射速度 1.降低注射速度 2.提高炮筒温度 2.提高炮筒温度
Defect: W hite lines
白线
2011-10-14
VT-PL/PE
29
白线改善对策 工艺: 工艺:
1.增加锁模力 1.增加锁模力 2.降低保压压力及减少保压时间 2.降低保压压力及减少保压时间 4.降低注射速度及注射压力 4.降低注射速度及注射压力 4.提高料筒温度 4.提高料筒温度
模具: 模具:
1.增大浇口及流道截面积 1.增大浇口及流道截面积 2. 降低模腔表面温度 3.改善模具排气 3.改善模具排气
2011-10-14 VT-PL/PE 14
缺陷: 顶白 缺陷:
Defect: visible ejector m arks
顶白
2011-10-14
VT-PL/PE
15
顶白改善对策 工艺: 工艺:
2011-10-14
VT-PL/PE
10
缺陷: 混色 缺陷:
Defect: color streaks
混色
2011-10-14
VT-PL/PE
11
混色改善对策 工艺
1.提高背压 1.提高背压 2.降低螺杆转速 降低螺杆转速, 2.降低螺杆转速,以增加混炼时间 3.提高料筒温度 3.提高料筒温度 4.增加残量 4.增加残量
2011-10-14 VT-PL/PE 20
缺陷:披锋 缺陷:
Defect: flash
披锋
2011-10-14
VT-PL/PE
21
披锋改善对策 工艺: 工艺:
1.降低注射速度及注射压力 1.降低注射速度及注射压力 2.降低保压压力及保压时间 2.降低保压压力及保压时间 3.降低背压 3.降低背压 4.降低 4.降低 料筒温度 .5.增加锁模力 .5.增加锁模力 模具 1.降低浇口及 1.降低浇口及 流道截面积 2.降低模腔 2.降低模腔 表面温度 3.减少排气槽截面积 3.减少排气槽截面积
机器
1.选用混炼型喷嘴 1.选用混炼型喷嘴 2.选用 螺杆 选用BM 2.选用BM螺杆
2011-10-14 VT-PL/PE 12
缺陷: 缩水 缺陷:
Defect: sink m ark
缩水
2011-10-14
VT-PL/PE
13
缩水改善对策 工艺: 工艺: