塑胶产品常见缺陷
塑胶件常见缺陷不良分析及对策讲解
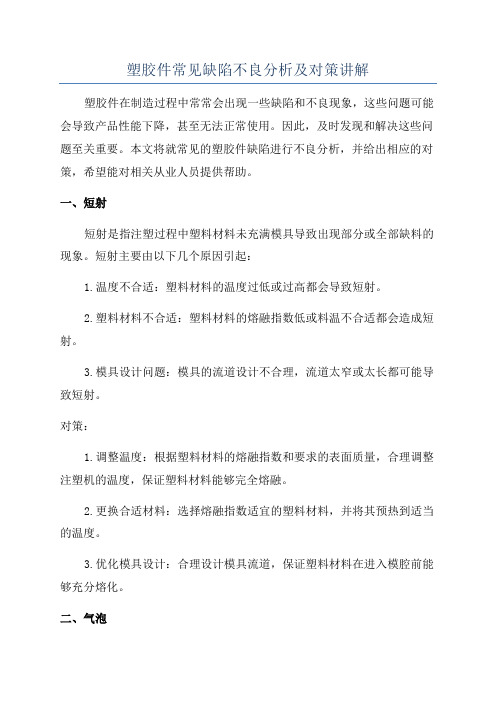
塑胶件常见缺陷不良分析及对策讲解塑胶件在制造过程中常常会出现一些缺陷和不良现象,这些问题可能会导致产品性能下降,甚至无法正常使用。
因此,及时发现和解决这些问题至关重要。
本文将就常见的塑胶件缺陷进行不良分析,并给出相应的对策,希望能对相关从业人员提供帮助。
一、短射短射是指注塑过程中塑料材料未充满模具导致出现部分或全部缺料的现象。
短射主要由以下几个原因引起:1.温度不合适:塑料材料的温度过低或过高都会导致短射。
2.塑料材料不合适:塑料材料的熔融指数低或料温不合适都会造成短射。
3.模具设计问题:模具的流道设计不合理,流道太窄或太长都可能导致短射。
对策:1.调整温度:根据塑料材料的熔融指数和要求的表面质量,合理调整注塑机的温度,保证塑料材料能够完全熔融。
2.更换合适材料:选择熔融指数适宜的塑料材料,并将其预热到适当的温度。
3.优化模具设计:合理设计模具流道,保证塑料材料在进入模腔前能够充分熔化。
二、气泡气泡是指塑胶件表面或内部出现的小气孔或气泡。
气泡可能导致产品外观不良或性能下降。
气泡的产生主要有以下几个原因:1.塑料材料中含有挥发性成分:一些塑料材料中含有挥发性成分,如果注塑温度过高,这些挥发性成分就会挥发出来形成气泡。
2.模具表面不洁净:如果模具表面不干净或有油污等杂质,气泡就会在塑料注入过程中被吸附在塑料中形成。
3.注塑机压力过高:注塑机压力过高会导致空气被压进模具中,形成气泡。
对策:1.调整注塑温度:根据塑料材料的特性,合理调整注塑温度。
温度过高易导致气泡产生,温度过低则容易短射。
2.模具清洁:保持模具表面干净,定期对模具进行清洗,去除杂质和油污。
3.控制注塑机压力:根据塑料材料的特性和模具的要求,合理控制注塑机的压力,避免空气进入模具。
三、热处理不当塑胶件经过热处理后,如果处理不当,可能导致产品性能下降或出现变形等问题。
常见的热处理问题有:1.温度不合适:热处理时,温度不合适会导致产品硬度不均匀或过硬。
塑胶产品的常见缺陷及分析

塑胶产品的常见缺陷及分析塑料制品是现代生活中不可或缺的一部分。
然而,塑料制品仍然存在一些常见的缺陷,这些缺陷可能导致产品质量下降,甚至无法使用。
下面是一些常见的塑料制品缺陷及其分析。
1.气泡和气孔:塑料制品中的气泡和气孔是由于在制造过程中塑料内部的空气没有完全排除或者在冷却期间塑料表面形成的。
这些气泡和气孔会导致产品表面不光滑,并在应力作用下引起断裂。
减少气泡和气孔的方法包括将塑料完全熔化,并控制良好的冷却过程。
2.毛边和厚度不均:由于模具设计和制造不当,塑料制品的边缘可能会有毛边。
毛边的存在会影响产品的外观和使用寿命。
此外,塑料制品的厚度分布不均匀可能导致产品一些部分容易破裂。
为了解决这些问题,需要优化模具设计,并确保模具制造过程的准确性。
3.烧伤和变色:在注塑过程中,如果温度控制不当,塑料可能会被过热,导致烧伤和变色。
这些问题会影响产品的外观和性能。
要解决这些问题,需要正确控制注塑机的温度和压力,并使用合适的冷却设备。
4.变形和翘曲:塑料制品可能在使用过程中变形或翘曲,这主要是由于应力超过材料的强度限制引起的。
为了避免变形和翘曲,可以通过增加产品的结构设计,加固材料强度或者改变制造过程来提高产品的稳定性。
5.色差:塑料制品可能存在色差,这是由于原料、配方和加工条件的变化引起的。
色差会影响产品的外观一致性。
要解决这个问题,需要优化原料和配方的选择,严格控制加工过程的温度和压力,以确保产品色差的控制在可接受的范围内。
综上所述,塑料制品的常见缺陷包括气泡和气孔、毛边和厚度不均、烧伤和变色、变形和翘曲以及色差。
这些缺陷可能导致产品质量下降,影响外观和性能。
为了解决这些问题,需要优化模具设计、加强原料和配方的控制,严格控制加工过程中的温度和压力。
只有通过严格的质量控制,才能生产出高质量的塑料制品。
塑胶件常见缺陷及原因分析
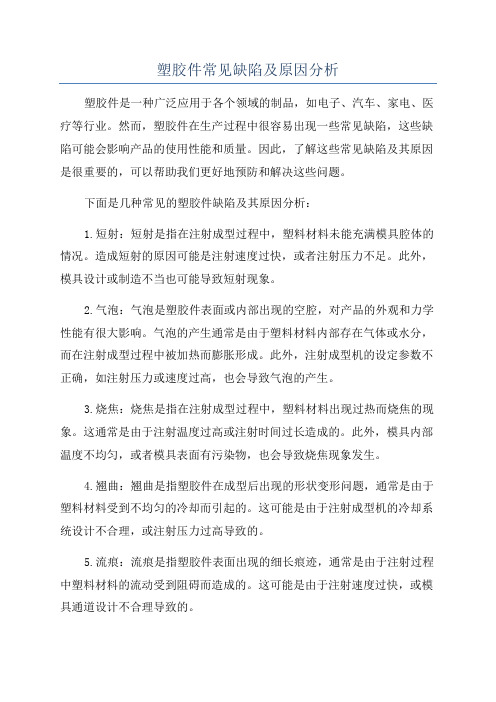
塑胶件常见缺陷及原因分析塑胶件是一种广泛应用于各个领域的制品,如电子、汽车、家电、医疗等行业。
然而,塑胶件在生产过程中很容易出现一些常见缺陷,这些缺陷可能会影响产品的使用性能和质量。
因此,了解这些常见缺陷及其原因是很重要的,可以帮助我们更好地预防和解决这些问题。
下面是几种常见的塑胶件缺陷及其原因分析:1.短射:短射是指在注射成型过程中,塑料材料未能充满模具腔体的情况。
造成短射的原因可能是注射速度过快,或者注射压力不足。
此外,模具设计或制造不当也可能导致短射现象。
2.气泡:气泡是塑胶件表面或内部出现的空腔,对产品的外观和力学性能有很大影响。
气泡的产生通常是由于塑料材料内部存在气体或水分,而在注射成型过程中被加热而膨胀形成。
此外,注射成型机的设定参数不正确,如注射压力或速度过高,也会导致气泡的产生。
3.烧焦:烧焦是指在注射成型过程中,塑料材料出现过热而烧焦的现象。
这通常是由于注射温度过高或注射时间过长造成的。
此外,模具内部温度不均匀,或者模具表面有污染物,也会导致烧焦现象发生。
4.翘曲:翘曲是指塑胶件在成型后出现的形状变形问题,通常是由于塑料材料受到不均匀的冷却而引起的。
这可能是由于注射成型机的冷却系统设计不合理,或注射压力过高导致的。
5.流痕:流痕是指塑胶件表面出现的细长痕迹,通常是由于注射过程中塑料材料的流动受到阻碍而造成的。
这可能是由于注射速度过快,或模具通道设计不合理导致的。
6.缩水:缩水是指塑胶件在成型后出现尺寸缩小的现象。
这可能是由于塑料材料在冷却后收缩所致。
此外,注射成型机的注射温度或冷却时间不合适,也会导致塑胶件尺寸缩水。
针对以上常见缺陷,我们可以采取一些措施来预防和解决这些问题。
首先,合理设计模具,考虑到塑料流动性和冷却效果,以减少缺陷的产生。
其次,在注射成型过程中,选择合适的注射参数,如温度、速度和压力等,以确保塑料材料充满模具腔体。
此外,定期清洗和维护注射成型机和模具,以避免污染物对塑胶件质量的影响。
塑胶件常见的缺陷产生原因及解决办法

塑胶件常见的缺陷产生原因及解决办法一、设计方面的缺陷:1.不合理的尺寸设计:塑胶件的尺寸设计不合理可能导致尺寸偏差过大、尺寸不一致等问题。
解决方法是根据塑胶件的具体用途和要求进行合理的尺寸设计,并进行合适的工艺分析和模流分析。
2.没有考虑到材料的特性:不同塑料材料具有不同的热胀冷缩系数、熔融温度等特性,设计时没有考虑到这些特性可能导致尺寸偏差、变形等问题。
解决方法是根据塑料材料的特性进行合适的设计和模具制造选型。
3.模具设计问题:模具设计不合理或者制造质量不过关可能导致塑胶件的缺陷问题。
解决方法是进行合理的模具设计,并选择专业的模具制造厂家。
4.不合理的壁厚设计:塑胶件的壁厚设计不合理可能导致塑胶件变形、收缩不均匀等问题。
解决方法是根据塑胶件的材料特性和实际使用要求进行合理的壁厚设计。
二、材料方面的缺陷:1.材料质量问题:不合格的原料质量可能导致塑胶件出现异味、颜色不均匀等问题。
解决方法是选择合格的塑料原料供应商,并进行原料的严格检验。
2.材料混合不均匀:塑料材料在加工过程中没有充分混合均匀可能导致塑胶件的颜色不均匀等问题。
解决方法是进行充分的原料预处理和混炼,确保塑料材料的均匀性。
3.熔体温度不均匀:塑料材料在注塑过程中温度不均匀可能导致塑胶件尺寸偏差、表面气泡等问题。
解决方法是调整注塑机的温度控制系统,确保熔体温度均匀稳定。
三、工艺方面的缺陷:1.注塑工艺参数设置不当:注塑过程中,如射胶压力、射胶速度、冷却时间等工艺参数设置不当可能导致塑胶件出现尺寸偏差、气泡、表面缺陷等问题。
解决方法是根据塑料的特性和产品要求进行合理的工艺参数设置。
2.模具温控不均匀:模具温度不均匀可能导致塑胶件出现收缩不一致、尺寸偏差等问题。
解决方法是进行模具温度分析和温控系统的优化。
可以采用热流道模具、快速温度控制系统等技术手段解决问题。
3.模具保养不当:模具的使用寿命长,如果没有进行定期的保养和维修可能导致塑胶件出现模纹、模具磨损等问题。
塑胶件常见成型缺陷及改善策略
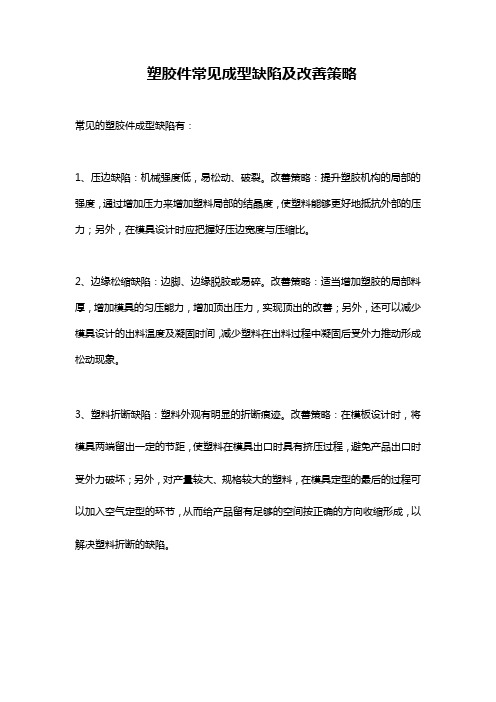
塑胶件常见成型缺陷及改善策略
常见的塑胶件成型缺陷有:
1、压边缺陷:机械强度低,易松动、破裂。
改善策略:提升塑胶机构的局部的强度,通过增加压力来增加塑料局部的结晶度,使塑料能够更好地抵抗外部的压力;另外,在模具设计时应把握好压边宽度与压缩比。
2、边缘松缩缺陷:边脚、边缘脱胶或易碎。
改善策略:适当增加塑胶的局部料厚,增加模具的匀压能力,增加顶出压力,实现顶出的改善;另外,还可以减少模具设计的出料温度及凝固时间,减少塑料在出料过程中凝固后受外力推动形成松动现象。
3、塑料折断缺陷:塑料外观有明显的折断痕迹。
改善策略:在模板设计时,将模具两端留出一定的节距,使塑料在模具出口时具有挤压过程,避免产品出口时受外力破坏;另外,对产量较大、规格较大的塑料,在模具定型的最后的过程可以加入空气定型的环节,从而给产品留有足够的空间按正确的方向收缩形成,以解决塑料折断的缺陷。
塑胶常见不良及解决方法

塑胶常见不良及解决方法塑胶是一种常见的材料,广泛应用于各种行业和领域。
然而,由于塑胶的特性以及制造过程中的一些问题,常常会出现一些不良现象。
本文将重点介绍一些常见的塑胶不良及其解决方法。
1.氣泡:塑膠制品中常見的一種不良現象是氣泡,這會在成品表面或内部形成小气囊。
气泡的形成是由于塑胶熔融时含有的空气或挥发物没有充分释放出来。
解决方法包括降低加工温度、增加熔体压力、增加注射速度和使用抗气泡添加剂等。
2.热胀冷缩:塑胶制品在温度变化下会发生热胀冷缩,导致尺寸变化。
这可能会导致配件无法正常连接或安装。
为了解决这个问题,可以采用材料改性或加工工艺改进,如增加冷却时间、降低注射温度等。
3.白化:白化是指塑胶制品表面或内部出现白色斑点或条纹。
这种现象通常是由于塑胶在注射过程中发生气泡聚集或制品未达到均匀熔融所致。
解决方法包括优化注射工艺、增加熔体压力、使用抗白化添加剂等。
4.热裂纹:热裂纹是指在塑胶产品成型过程中出现的裂纹现象。
这通常是由于塑胶在成型过程中存在过大的应力集中,导致塑胶产生裂纹。
解决方法包括改变模具设计、增加冷却时间、预混塑胶料等。
5.变色:变色是指塑胶制品在使用或储存过程中出现颜色变化。
这可能是由于塑胶材料受到光、热、氧化等外界因素的影响所致。
解决方法包括选择适当的防褪色添加剂、合理储存塑胶制品等。
6.毛刺:毛刺是指塑胶制品表面出现不平整、刺状的小颗粒。
这通常是由于模具表面不平整或注射工艺不当所导致的。
解决方法包括优化模具设计、控制注射压力、调整注射速度等。
7.缩水:缩水是指塑胶制品在冷却过程中发生体积收缩。
这可能导致尺寸偏离设计要求。
解决方法包括优化塑胶成型工艺、增加冷却时间和选择合适的材料等。
8.潜伏期延长:有些塑胶在使用一段时间后会发生不良现象,如变形、断裂等。
这可能是由于塑胶受到环境因素、应力或热老化的影响导致的。
解决方法包括选择合适的材料、控制加工温度、降低应力等。
总结起来,塑胶制品的不良现象可能是由于材料、工艺或环境等多种因素造成的。
塑胶产品外观常见不良分析

塑胶产品外观常见不良分析塑胶产品在生产过程中,由于种种原因可能会产生不良的外观缺陷,这些缺陷会对产品的质量和使用效果造成不利影响,下面就介绍几种常见的塑胶产品外观不良分析。
一、砂眼砂眼是指产品外表面上出现的类似小孔洞的缺陷,通常表现为圆形、椭圆形或不规则形状。
砂眼产生的原因是模具表面有斑点、气孔、异物等缺陷,导致塑料进模不畅或模内气体无法顺畅排出形成,最后留下小孔洞。
二、流痕流痕是指产品表面上出现的细长的纹路,一般与塑料的注射方向垂直,这样的缺陷往往会影响到产品的美观度。
流痕的原因是模具内部的热流动不均匀,某些部位的温度较低,导致塑料注入后无法均匀地流动分布,产生较深的沟痕。
三、气泡气泡是指产品表面或内部出现的像气泡一样的孔隙,它们不仅会让塑胶产品表面看起来不平整,还会降低产品的力学性能和密封性能。
气泡的产生可能是塑料攪拌不均匀或注射速度过快导致的空气混入塑料中,也可能是质量不佳的原料带有微小的空气颗粒。
四、色差色差是指产品颜色不均匀、不合一致标准要求的情况。
彩色塑胶制品通常是由数种颜色的颗粒混合而成,如果混合不均匀或是染料质量不稳定,这些问题就会显现在产品表面,造成色差。
此外,不适当的注塑温度和压力也会影响塑料颜色的均匀度。
五、毛刺毛刺是指产品表面上一些尖锐、突出的小物质,通常是模具零件分离不干净、模具中有棘手的地方,以及产品卡死在模具中发生磨损等造成的。
毛刺的出现不仅影响产品的整体美观度,还会损伤使用者的手部和其他部位。
六、变形变形是指产品在注塑后外观发生了形状和尺寸的变化,这种情况最常见的原因是模具温度不均匀,塑料被过快地冷却,导致变形。
另外,如果产品设计不合理、墙厚不足也会导致变形。
变形不仅会让产品表面看起来不平整,还会导致产品性能不稳定,从而进一步影响产品的生产和使用。
总之,塑胶产品外观缺陷的种类繁多,产生的原因也五花八门如果不及时有效地加以排查和处理,就会直接影响产品的质量和使用效果。
塑胶件的24种常见不良缺陷图片演示幻灯片
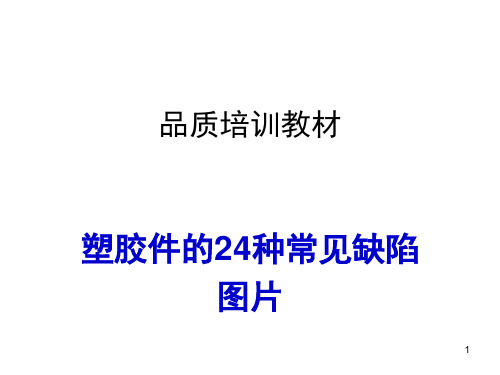
塑胶件的24种常见缺陷 图片
1
一、缩水:
缩水(凹痕)
缩水(凹痕)
2
二、气纹:
气纹
3
三、缺料(走胶不足):
走胶不足
缺料
4
四、水口不平:
水口不平
5
五、披锋(毛边):
披锋
毛边
6
六、夹线(结合线):
夹线 夹线(结合线)
7
七、黑点:
黑点NG!
8
八、变形:
平面中间拱起变形
柱子弯曲变形9Βιβλιοθήκη 九、混色(异色):混色
混色(杂色料)
10
十、划伤(刮伤):
划伤
刮花
11
十一、烧焦:
烧焦
12
十二、拖花(拉伤):
拖花(拉伤)
13
十三、顶高(顶白):
顶高(顶针印)
14
十四、料花:
料花
15
十五、油污:
油污NG!
16
十六、碰伤:
碰伤
17
十七、削伤:
削缺(削伤)
18
十八、气泡:
气泡(透明件中央白泡状)
19
十九、色差(上下盖阴阳色):
上盖色偏哑
下盖色偏亮
20
二十、披锋丝(拉丝):
披锋丝(拉丝)NG
21
二十一、应力痕:
应力痕:因注射时内应力过大而在产品表面形成的光影;
22
二十二、进胶位发蓝:
进胶点发蓝
23
二十三、多胶:
多胶 NG
24
二十四、粘胶:
粘胶 :因模具内侧附着有积炭或脏物导致产品表面少胶;
25
塑胶件常见缺陷产生的原因及解决方法

塑胶件常见缺陷产生的原因及解决方法1.原材料质量问题:塑胶件常见的原材料问题包括原材料中含有杂质、原料失效、原料配比不正确等。
这些问题会导致塑胶件的质量下降和性能降低。
解决方法是对原材料进行严格的检验和筛选,确保原材料的纯度和质量。
2.模具设计问题:模具设计不合理可能导致塑胶件的缺陷,例如模具壁厚不均匀、模腔表面粗糙等。
解决方法是对模具进行合理设计,确保模具的结构和尺寸满足产品要求,并提高模具的制造工艺和加工精度。
3.注塑工艺问题:注塑过程中的工艺参数设置不当会导致塑胶件出现缺陷,例如温度不稳定、压力不均匀、注射速度过快等。
解决方法是优化注塑工艺参数,确保温度、压力、速度等参数的稳定和均匀。
4.模具磨损和损坏:长时间使用会导致模具磨损和损坏,影响塑胶件的质量和外观。
解决方法是加强模具的保养和维护,定期进行模具清洁和润滑,并进行必要的修复和更换。
5.后道工艺问题:塑胶件的后道加工也可能引发缺陷,例如焊接不牢固、喷涂不均匀等。
解决方法是加强后道工艺的控制,提高工艺的稳定性和一致性。
综上所述,要解决塑胶件常见缺陷的问题,需要从原材料选择、模具设计、注塑工艺、模具维护和后道工艺等方面入手,通过优化和控制各个环节,提高产品的质量和性能。
同时,还需要建立健全的质量管理体系,对生产过程进行全面监控和检测,及时发现和解决问题。
最后,还应该加强员工的培训和技能提升,提高操作技术和质量意识,提高产品的一致性和稳定性。
只有通过不断改进和严格控制,才能有效降低塑胶件的缺陷率,提高产品的质量和市场竞争力。
塑胶件常见缺陷及原因分析

塑胶行业-塑胶件常见缺陷塑胶件常见缺陷;1.塑胶成品缺陷;粘模(扯模):制品的柱筋及细少多型腔件,在脱模后;力偏大,或模具局部粗糙等因素导致;缺料(填充不足):制品结构与所设计的形状结构不符;充满,常产生于制品的柱,孔或薄胶位以及离入水口较;力不够,模温不足,骨位过薄,局部有油或排气不够(;充满;多胶:制品结构与所设计的形状结构不符,局部多出胶;间凸起,指甲可感觉到;缩水:制品表面塑胶件常见缺陷1.塑胶成品缺陷粘模(扯模):制品的柱筋及细少多型腔件,在脱模后未能脱模而粘附在模具相应位置因成型压力偏大,或模具局部粗糙等因素导致。
缺料(填充不足):制品结构与所设计的形状结构不符,局部胶位不满足,短少,塑件未能完全充满,常产生于制品的柱,孔或薄胶位以及离入水口较远的部位,因成型压力不够,模温不足,骨位过薄,局部有油或排气不够(困气)导致胶位不能填充满.多胶:制品结构与所设计的形状结构不符,局部多出胶位,或塑件表面有点状物,四周凹陷中间凸起,指甲可感觉到。
通常由模具成型面碰,崩缺,损伤及细小型芯顶针移位或断掉导致。
缩水:制品表面因成型时, 冷却硬化收缩,产生的肉眼可见凹坑或窝状现象称为“缩水".制品结构的较厚胶位如骨位,柱位等对应表面,因成型压力不足,保压及射胶时间偏短,或模温偏高,而导致因局部收缩偏大而造成.夹水纹(熔接痕):熔胶在模腔内流动中分流后再汇合时不充分,不能完全熔合,冷却后在塑件表面形成的线状痕迹和线状熔接缝,模温偏低,料温偏低,制品局部偏薄或模具有粗大型芯及材料流动性不好等都会导致夹水纹的产生,温度及困气也对其有最大影响.烘印(光影):制品结构的厚薄胶位在熔胶流动时受阻改变方向而形成的光泽不一致的现象,通常在水口周围,塑件表面呈光泽度不够,颜色灰蒙。
制品结构的薄胶位,止口位,扣位与周围过渡断差明显,原料流动性差,成型料温、模温偏低或射胶压力速度太大,模具排气不良,啤塑压力过高皆易产生烘印.毛边/飞边(披锋):制品的边棱、孔、柱端等模具型腔内所有分模线,镶块及顶针位相对应位成型后产生较薄的胶料,称为披锋,有刺手感觉,合模线,镶件顶针及活动碰撞位产生较大间隙或成型压力太大,模具日久磨损,而锁模不紧,锁模力不足时易导致披锋产生。
塑胶件常见的缺陷产生原因及解决办法
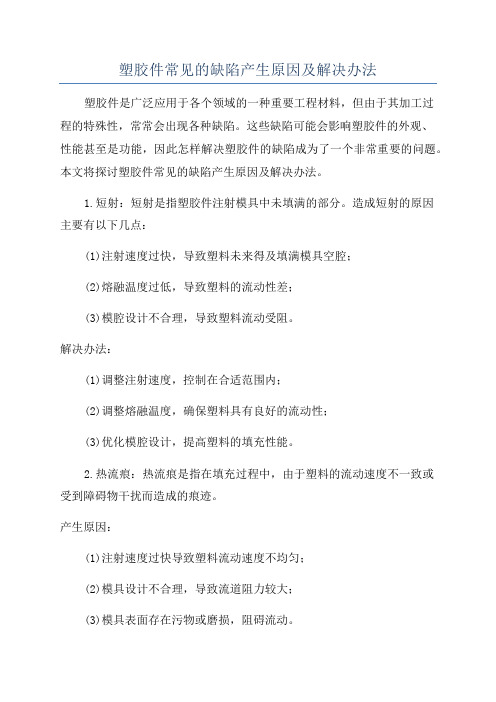
塑胶件常见的缺陷产生原因及解决办法塑胶件是广泛应用于各个领域的一种重要工程材料,但由于其加工过程的特殊性,常常会出现各种缺陷。
这些缺陷可能会影响塑胶件的外观、性能甚至是功能,因此怎样解决塑胶件的缺陷成为了一个非常重要的问题。
本文将探讨塑胶件常见的缺陷产生原因及解决办法。
1.短射:短射是指塑胶件注射模具中未填满的部分。
造成短射的原因主要有以下几点:(1)注射速度过快,导致塑料未来得及填满模具空腔;(2)熔融温度过低,导致塑料的流动性差;(3)模腔设计不合理,导致塑料流动受阻。
解决办法:(1)调整注射速度,控制在合适范围内;(2)调整熔融温度,确保塑料具有良好的流动性;(3)优化模腔设计,提高塑料的填充性能。
2.热流痕:热流痕是指在填充过程中,由于塑料的流动速度不一致或受到障碍物干扰而造成的痕迹。
产生原因:(1)注射速度过快导致塑料流动速度不均匀;(2)模具设计不合理,导致流道阻力较大;(3)模具表面存在污物或磨损,阻碍流动。
(1)调整注射速度,确保塑料流动速度均匀;(2)优化模具设计,减小流道阻力;(3)定期保养模具,确保模具表面光洁无污物。
3.翘曲:翘曲是指塑胶件在冷却过程中由于收缩不均匀而造成的扭曲变形。
产生原因:(1)注射过程中温度分布不均匀,导致冷却速度不均匀;(2)部分材料的收缩率较大,造成不均匀收缩;(3)模具设计不合理,导致冷却不均匀。
解决办法:(1)控制注射过程中的温度分布,确保全面均匀冷却;(2)使用收缩率较小的材料;(3)优化模具设计,确保冷却均匀。
4.气泡:气泡是塑胶件内部或表面存在的气体囊状物。
产生原因:(1)注射过程中,塑料因挤压和高温导致内部气体产生;(2)注射过程中,未充分排除空气导致气泡残留;(3)塑料材料含有挥发性成分,造成气泡。
(1)调整注射过程中的温度和压力,减少气体产生;(2)注射过程中加入真空排气步骤,充分排除空气;(3)选择不含挥发性成分的塑料材料。
5.纹痕:纹痕是塑胶件表面存在的细微沟纹。
塑胶常见的缺陷及产生原因

塑胶常见的缺陷及产生原因塑胶常见的缺陷及产生原因可以总结为以下几个方面:杂质、气泡、熔接线、缩孔、痕迹、烧结、卡模、性能不符等。
首先,杂质是塑胶制品产生缺陷的主要原因之一。
杂质可以是塑胶材料内部的异物或是外界杂质。
塑胶材料内部的杂质可能是在加工过程中未完全混合均匀的其它颜色或类型的塑料,也可能是在材料储存、输送过程中吸附的灰尘、油污等。
外界杂质则可能是生产环境中的灰尘、污渍等通过空气、机械原因等进入塑胶制品中的。
其次,气泡是另一种常见的塑胶制品缺陷。
气泡的产生原因可以是在塑料熔融过程中,加入了不能完全融化的材料,也可能是加入了吸湿材料,在熔融过程中产生气泡。
此外,造成气泡的原因还可能是注塑机的温度不稳定、注射压力不均匀,导致塑料熔融不均匀,进而产生气泡。
熔接线是塑胶制品中常见的缺陷之一。
熔接线是指在注塑过程中,由于二桶注射而造成的两部分塑胶材料的分离边缘。
产生熔接线的原因主要是注塑机温度控制不正确或是注射速度不均匀,使得两个熔融的塑料流体没有完全融合在一起,导致熔接线的出现。
缩孔是塑胶缺陷中较为常见的一种。
缩孔的产生原因可以是由于塑料熔融后在冷却过程中,由于受到内外部压力的影响,导致部分区域发生收缩并形成孔洞。
此外,塑料注射过程中的流动阻力也可能会导致塑胶缩孔的发生。
痕迹是塑胶制品表面出现的划痕、凹痕等不平整的现象。
痕迹的产生原因可能是模具设计不合理,导致模具表面形成划痕;也可能是注塑过程中,塑料注射进入模具时遇到障碍物,导致表面不平整的痕迹。
烧结是塑胶缺陷中较为严重的一种。
烧结是指在注塑过程中,由于注射温度过高或注射时间过长,导致塑料热分解产生烟雾、焦糊等现象。
烧结的原因可能是注射温度过高,使得塑料分解产生焦炭;也可能是注射时间过长,塑料在注射过程中长时间受热,导致热分解。
此外,卡模是塑胶制品常见的缺陷之一。
卡模是指在注塑过程中,塑料在模腔中不能完全填充,造成注塑件部分缺失或形状不完整。
卡模的原因可能是注射速度过快,导致塑料无法完全填充模腔;也可能是注射压力不足,使得塑料无法充分填充模腔。
塑胶产品不良及对策

产品成型缺陷及其对策∙一、填充不足∙二.模腔划痕和擦伤∙三、毛刺过大∙四、缩孔∙五、翘曲、弯曲和扭曲∙六、开裂、裂纹、微裂和发白∙七.熔接痕∙八、波纹∙九、银丝∙十、烧伤∙十一、黑色条纹∙十二、晕色膜(发暗)、光泽不佳∙十三、颜色不匀∙十四、气泡和空洞∙十五、透明度不好∙十六、混入异物∙十七、嵌件镶嵌不良∙十八、脱模不良∙十九、冷料凹痕(蛇行纹)∙二十、脆弱∙二十一、层状剥离一.填充不足一般情况下,填充不足是因塑料流动性不足,不能填充满整个型腔所造成的。
当然也不单纯是这个原因,造成填充不足还可能有多方面的原因。
1.注射成型机注射能力不足这是对注射机的能力估计过高而产生的,由于塑化能力不足或者注射量不足也会发生。
其中,塑化能力不足可通过延长加热时间、增加螺杆转数、提高背压来提高塑化能力。
而注射量不足,如果不换成大注射量的机床就不能解决问题。
2.多型腔有局部填充不足尽管成型机床的能力足够,这种缺陷是因浇口不平而产生的。
有时只是主浇道附近或者浇口粗而短的型腔可加工出合格制件,其余型腔的制件有缺陷。
达到浇口平衡即可消除这种缺陷,也就是加粗浇道直径,使流到浇道末端的压力降减小,同时加大离主浇道较远型腔的浇口。
如果,是由于型腔未完全闭合所致,这时就必须减少每次注射成型的数目。
3.塑料流动性不佳如果塑料流动性不佳,未等流到型腔末端或者未流到溢料槽就已冷凝,因而往往造成填充不足。
为了消除这种缺陷可提高溶料温度,并在熔料冷凝前使熔料流到型腔末端,也可加快注射速度。
也就是说提高料筒温度、提高注射压力,加快注射速度,也可提高模具温度。
在这种场合,塑料良好的流动性特别重要,所以更换流动性好的塑料也是一种解决方法。
4.流动阻力过大阻碍熔料流动的部位有喷嘴、主浇道、浇道、浇口和制件的薄壁处等。
采用如下方法可减小喷嘴流动阻力:加大喷嘴直径,提高喷嘴温度,使用流动阻力较小的喷嘴。
对于主浇道可增大其直径:对于浇道应避免采用流动阻力大的半圆形浇道,而采用圆形或梯形浇道,若增大直径则更好。
塑胶产品常见缺陷及对策
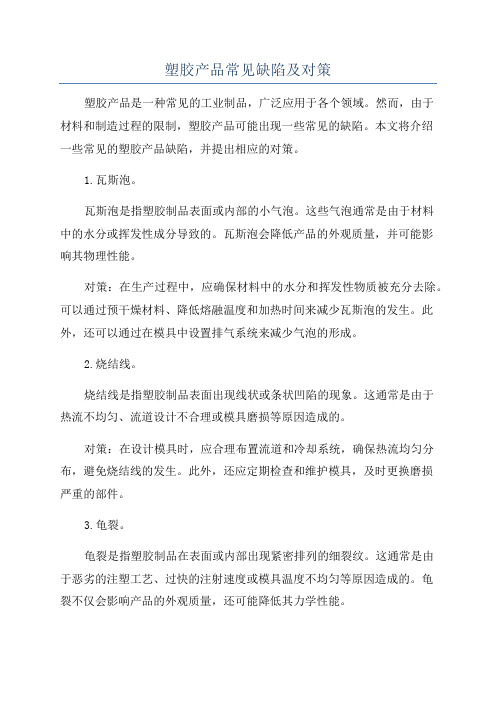
塑胶产品常见缺陷及对策塑胶产品是一种常见的工业制品,广泛应用于各个领域。
然而,由于材料和制造过程的限制,塑胶产品可能出现一些常见的缺陷。
本文将介绍一些常见的塑胶产品缺陷,并提出相应的对策。
1.瓦斯泡。
瓦斯泡是指塑胶制品表面或内部的小气泡。
这些气泡通常是由于材料中的水分或挥发性成分导致的。
瓦斯泡会降低产品的外观质量,并可能影响其物理性能。
对策:在生产过程中,应确保材料中的水分和挥发性物质被充分去除。
可以通过预干燥材料、降低熔融温度和加热时间来减少瓦斯泡的发生。
此外,还可以通过在模具中设置排气系统来减少气泡的形成。
2.烧结线。
烧结线是指塑胶制品表面出现线状或条状凹陷的现象。
这通常是由于热流不均匀、流道设计不合理或模具磨损等原因造成的。
对策:在设计模具时,应合理布置流道和冷却系统,确保热流均匀分布,避免烧结线的发生。
此外,还应定期检查和维护模具,及时更换磨损严重的部件。
3.龟裂。
龟裂是指塑胶制品在表面或内部出现紧密排列的细裂纹。
这通常是由于恶劣的注塑工艺、过快的注射速度或模具温度不均匀等原因造成的。
龟裂不仅会影响产品的外观质量,还可能降低其力学性能。
对策:在注塑工艺中,应控制好注塑温度、注射速度和保压时间,确保塑胶材料在模具中充分流动。
此外,还应合理设计模具和冷却系统,使模具温度均匀分布,避免龟裂的发生。
4.黑点。
黑点是指塑胶制品表面或内部出现的黑色颗粒状或斑点状物质。
这通常是由于材料中的杂质或染料不均匀引起的。
黑点会降低产品的外观质量,并可能影响其物理性能。
对策:在生产过程中,应使用质量可靠的原材料,并进行严格的杂质筛选和质检。
如果发现杂质,应及时清理或更换材料。
此外,还应控制好加料的方式和量,确保染料均匀分散。
5.尺寸偏差。
尺寸偏差是指塑胶制品的实际尺寸与设计尺寸之间的差距。
这可能是由于模具磨损、注塑工艺调整不当或材料热收缩不一致等原因造成的。
对策:在生产过程中,应定期检查和维护模具,确保其尺寸精度。
塑胶件常见缺陷产生原因及改善对策

塑胶件常见缺陷产生原因及改善对策塑胶件是指由塑胶材料制作而成的零件,广泛应用于汽车、家电、电子产品和日常生活用品等领域。
然而,在塑胶件的制造过程中,常常会出现各种缺陷,如气泡、砂眼、短斑、热裂、脱模、射出不完整等。
这些缺陷会降低产品的质量,甚至影响使用安全。
以下是塑胶件常见缺陷的产生原因及改善对策。
1.气泡气泡是塑胶件中最常见的缺陷之一,主要由以下因素引起:-塑料原料中含有水分,造成蒸汽产生气泡。
改善对策是通过加热塑料原料预干燥或使用干燥剂。
-射出过程中模具中的空气未排除干净。
改善对策是增加射出压力和速度,确保模具中的空气能够顺利排出。
-射出过程中塑料材料的熔体温度过高,产生气泡。
改善对策是调整射出温度,确保熔体温度适中。
-高分子量的塑料材料在射出过程中分解产生气体。
改善对策是选择合适的塑料材料。
2.砂眼砂眼是指塑胶件表面出现的小凹陷或凸起,主要由以下原因引起:-模具中存在异物,例如灰尘、沙粒等。
改善对策是保持模具清洁,及时除去异物。
-射出过程中模具表面未润滑充分,塑胶材料无法充分填充模具。
改善对策是增加模具表面的润滑剂,提高材料的流动性。
-射出过程中,模具温度不均匀,造成材料凝固不均匀。
改善对策是调整模具的温度分布,保持均匀加热。
-模具设计不合理,造成材料流动不畅。
改善对策是优化模具结构,提高充型性能。
3.短斑短斑是指塑胶件表面上呈现出短小裂纹的缺陷,造成塑胶件强度下降,主要由以下原因引起:-射出过程中,塑料材料受到过高的剪切力和拉伸力。
改善对策是调整射出速度和压力。
-模具设计不合理,造成材料流动不畅。
改善对策是优化模具结构,提高充型性能。
-射出过程中,塑料材料的熔体温度过高。
改善对策是控制射出温度,避免过热。
4.热裂热裂是指塑胶件在冷却过程中由于温度差异过大,导致塑胶材料发生裂纹,主要由以下原因引起:-模具设计不合理,导致塑胶件壁厚不均匀,造成冷却速度不一致。
改善对策是优化模具结构,保证壁厚均匀。
塑胶件常见缺陷的表现形式和对策
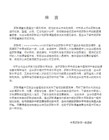
胶件常见缺陷描述
1. 披峰:合模界面挤出树脂。常常是由料温过高,射出压力太高或模具不良所造成的。
2. 走胶不齐(不够胶):模糟射料不中致使射出不良,塑胶件成形不全,压力低,射胶不足所致。
3. 缩水:表面凹痕,常见于胶位厚的地方。是由于射出压力胶量不足,射胶时间不够 ,模温过高所致。
4. 夹水纹:两股以上分流汇合点上生成的发状细线。常由料温低、困气或有碰穿位所造成。
5. 混色:色粉混合或熔融不均所致,使局部颜色与周围颜色不一致。
6. 料花:物料流向之银条。由射速太快、排气不良、料内水份或混料不一所造成。
7. 模花:塑胶件表面(常见于光面)有花痕(每啤货都有)。常常是模表面被轻微划伤。需将模具交给模房省模刨光。
12. 拖胶:胶被拖起,是由于模上有擦花、拖模不顺或调机各级压力不协调所致。
13. 气影:塑胶件表面有雾状痕迹。常出现在水口附近。是由于压力小或速度快所造成。
14. 多胶:塑胶件局部多一些胶,凸起。是由于模具某处少一点、有凹陷或断针、爆裂所致。
15. 反光:整个表面或局部发亮。与混料、熔胶、走胶路线有关。
8. 气泡:制成品内中空有空气。夹气、排气不良所造成的。
9. 0黑点:塑胶件胶体中出现黑色斑点。是原料,色粉中有杂质或料筒未清洗干净所致。
10. 划花(擦花):表面伤痕。是由于货物在拿送或搬运过程中被硬件损伤。
11. 胶屎:塑胶件表面局部无光泽,与周围不一致。是由于模上有冷胶,需省模。
16. 焦纹:塑胶件表面(常见于光面)出现象指纹一样细纹。常由于模上有纹,或各级压力不协调所致。
17. 波浪纹:塑胶的边缘产生象波浪一样的波纹。常于模具表面有轻微损伤。
常用塑胶产品的缺陷及识别.
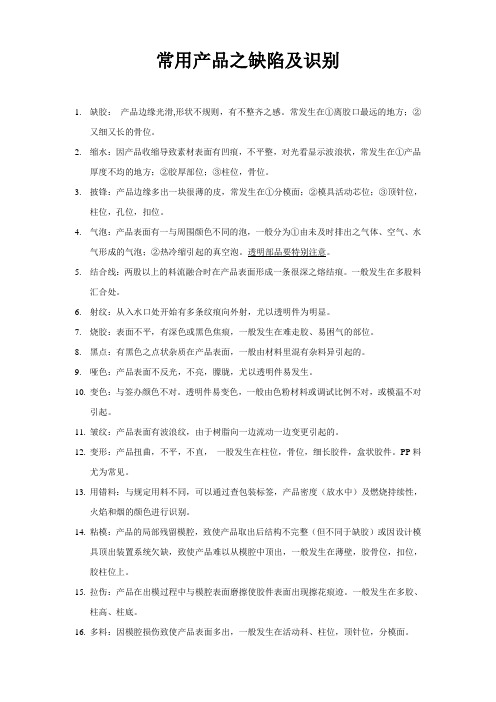
常用产品之缺陷及识别1.缺胶:产品边缘光滑,形状不规则,有不整齐之感。
常发生在①离胶口最远的地方;②又细又长的骨位。
2.缩水:因产品收缩导致素材表面有凹痕,不平整,对光看显示波浪状,常发生在①产品厚度不均的地方;②胶厚部位;③柱位,骨位。
3.披锋:产品边缘多出一块很薄的皮,常发生在①分模面;②模具活动芯位;③顶针位,柱位,孔位,扣位。
4.气泡:产品表面有一与周围颜色不同的泡,一般分为①由未及时排出之气体、空气、水气形成的气泡;②热冷缩引起的真空泡。
透明部品要特别注意。
5.结合线:两股以上的料流融合时在产品表面形成一条很深之熔结痕。
一般发生在多股料汇合处。
6.射纹:从入水口处开始有多条纹痕向外射,尤以透明件为明显。
7.烧胶:表面不平,有深色或黑色焦痕,一般发生在难走胶、易困气的部位。
8.黑点:有黑色之点状杂质在产品表面,一般由材料里混有杂料异引起的。
9.哑色:产品表面不反光,不亮,朦胧,尤以透明件易发生。
10.变色:与签办颜色不对。
透明件易变色,一般由色粉材料或调试比例不对,或模温不对引起。
11.皱纹:产品表面有波浪纹,由于树脂向一边流动一边变更引起的。
12.变形:产品扭曲,不平,不直,一股发生在柱位,骨位,细长胶件,盒状胶件。
PP料尤为常见。
13.用错料:与规定用料不同,可以通过查包装标签,产品密度(放水中)及燃烧持续性,火焰和烟的颜色进行识别。
14.粘模:产品的局部残留模腔,致使产品取出后结构不完整(但不同于缺胶)或因设计模具顶出装置系统欠缺,致使产品难以从模腔中顶出,一般发生在薄壁,胶骨位,扣位,胶柱位上。
15.拉伤:产品在出模过程中与模腔表面磨擦使胶件表面出现擦花痕迹。
一般发生在多胶、柱高、柱底。
16.多料:因模腔损伤致使产品表面多出,一般发生在活动科、柱位,顶针位,分模面。
17.混色:因料不干净或温度过高使胶件表面或内部形成与胶件不同的颜色点(混料不均匀以引起)。
18.混点:成型胶件表面所出现的杂点(如黑点)、焦点。
常见塑胶产品弊端

混色(杂色料)
十、划伤(刮伤):
划伤
Байду номын сангаас刮花
十一、烧焦:
烧焦
十二、拖花(拉伤):
拖花(拉伤)
十三、顶高(顶白):
顶高(顶针印)
十四、料花:
料花
十五、油污:
油污NG!
十六、碰伤:
碰伤
十七、削伤:
削缺(削伤)
十八、气泡:
气泡(透明件中央白泡状)
十九、色差(上下盖阴阳色):
上盖色偏哑
下盖色偏亮
品质培训教材
塑胶件的24种常见缺陷 图片
一、缩水:
缩水(凹痕)
缩水(凹痕)
二、气纹:
气纹
三、缺料(走胶不足):
走胶不足
缺料
四、水口不平:
水口不平
五、披锋(毛边):
披锋
毛边
六、夹线(结合线):
夹线 夹线(结合线)
七、黑点:
黑点NG!
八、变形:
平面中间拱起变形
柱子弯曲变形
九、混色(异色):
二十、披锋丝(拉丝):
披锋丝(拉丝)NG
二十一、应力痕:
应力痕:因注射时内应力过大而在产品表面形成的光影;
二十二、进胶位发蓝:
进胶点发蓝
二十三、多胶:
多胶 NG
二十四、粘胶:
粘胶 :因模具内侧附着有积炭或脏物导致产品表面少胶;
- 1、下载文档前请自行甄别文档内容的完整性,平台不提供额外的编辑、内容补充、找答案等附加服务。
- 2、"仅部分预览"的文档,不可在线预览部分如存在完整性等问题,可反馈申请退款(可完整预览的文档不适用该条件!)。
- 3、如文档侵犯您的权益,请联系客服反馈,我们会尽快为您处理(人工客服工作时间:9:00-18:30)。
成型常见问题与改善
夹水纹
夹水纹改善对策
I工艺:
I1.提高注射速度
I2.增加炮筒温度
I3.增加保压压力
I模具:
I1. 提高模温
I2.增大浇口及流道截面积I3. 改善模具的排气
气纹
气纹的改善对策
I工艺:
I 1. 降低注射速度
I 2. 增加料筒温度
I模具:
I1. 增大浇口截面积
I2. 提高模腔表面温度I3. 加深冷料井
气花
气花的改善对策
I工艺:
I 1. 降低注射速度
I 2 . 充分干燥原料
I 3. 增加料筒温度
I 4. 提高背压
I 5 . 减少抽胶行程
I模具:
I1. 增大浇口及流道的截面积I2. 提高模腔表面温度
皱纹
皱纹改善对策
I工艺
I1.提高注射速度
I2.提高注射压力及保压压力I3.提高料筒温度
I模具
I1.增大浇口及流道截面积
I2.提高模腔表面温度
混色
混色的改善对策
I工艺
I1.提高背压
I2.降低螺杆转速,以增加混炼时间I3.提高料筒温度
I4.增加残量
I机器
I1.选用混炼型喷嘴
I2.选用BM螺杆
缩水
缩水改善对策
I工艺:
I1. 提高注射速度及注射压力
2.提高保压压力及保压时间
3.提高料筒温度
4.提高背压
5.延长冷却时间
I模具:
I1.增大浇口及流道截面积
2. 降低模腔表面温度
3.改善模具排气
顶白
顶白改善对策
I工艺:
I1.降低保压压力及保压时间
I2. 降低顶针压力及顶出速度
I3.延长冷却时间
I模具:
I1. 降低模腔表面温度
I2.检查修复模具的倒扣(undercut)
I3.加大顶针的截面积及改善顶针布置
烧焦
烧焦改善对策
I工艺:
I1.降低注射速度及注射压力I2.降低料筒温度
I3.降低锁模力
I模具:
I1.改善模具排气
I2.防止包气(entrapped air)
走胶
走胶改善对策
I工艺:
I1.提高注射速度及注射压力I2.提高保压压力及保压时间I3.提高料筒温度
I4.提高背压
I模具:
I1.增大浇口及流道截面积
I2.提高模腔表面温度
I3.改善模具排气
披锋
披锋改善对策
I工艺:
I1.降低注射速度及注射压力
2.降低保压压力及保压时间
3.降低背压
4.降低料筒温度
.5.增加锁模力
I模具
I1.降低浇口及流道截面积
2.降低模腔表面温度
3.减少排气槽截面积
变形
变形改善对策
I工艺:
I1.降低保压压力及保压时间I2.降低背压
I3.延长冷却时间
I模具:
I1.增加浇口截面积
I2.均匀模腔表面温度
蛇纹gate
蛇纹的改善对策
I工艺:
I1.降低注射速度
I2.提高炮筒温度
I模具:
I1.加大浇口截面积
I2.移动浇口位置(采用冲击型浇口)
真空泡
真空泡的改善对策
I工艺:
I1.降低注射速度
I2.增加保压压力及保压时间I3.增加背压
I4.降低料筒温度
I模具:
I1.增加浇口截面积
I2.提高模腔表面温度
白线
白线改善对策
I工艺:
I1.增加锁模力
I2.降低保压压力及减少保压时间I4.降低注射速度及注射压力
I4.提高料筒温度
I模具:
I1.提高模腔表面温度
拖白
拖白改善对策
I工艺:
I1.降低保压压力及保压时间I2.降低注射速度及注射压力I模具:
I1.幼化模腔蚀纹
I2.加大出模斜度
拉白
拉白改善对策
I工艺:
I1.降低保压压力及保压时间I2.降低注射速度及注射压力I3.延长冷却时间
I4.降低顶出速度及顶出压力I模具:
I1.加出模斜度
I2.省顺骨位
起皮
起皮改善对策
I工艺:
I1..降低注射速度
I2.充分干燥原料
I3.降低料筒温度
I原料:
I1.检查原料是否混有杂料I模具:
I1.提高模腔表面温度
黑点
黑点改善对策
I工艺:
I1.降低料筒温度
I2.降低背压
I3.降低螺杆转速
I4. 减少残量
I原料:
I1.检查原料是否混有杂料
光泽不一
光泽不一改善对策
I工艺:
I1.提高注射速度及注射压力I2.提高保压压力及保压时间I3.提高料筒温度
I模具:
I1.均匀模腔表面温度
表面斑点
表面斑点改善对策
I工艺:
I1.提高注射速度及注射压力I2.增加螺杆转速
I3.增加背压
I4.提高料筒温度
I模具:
I1.提高模腔表面温度。