EV0060中文资料
EPA060资料

ExcelicsEPA060B-70DATA SHEETHigh Efficiency Heterojunction Power FETFeatures• NON-HERMETIC LOW COST CERAMIC 70mil PACKAGE • +26dBm TYPICAL OUTPUT POWER• 9.0dB TYPICAL POWER GAIN AT 12 GHZ • 0.4 dB TYPICAL NOISE FIGURE AT 2GHz• 20 dB TYPICAL ASSOCIATED GAIN AT 2 GHz • 0.3 X 600 MICRON RECESSED “MUSHROOM” GATE • Si 3N 4 PASSIVATION• ADVANCED EPITAXIAL HETEROJUNCTION PROFILE PROVIDES EXTRA HIGH POWER EFFICIENCY, AND HIGH RELIABILITYApplications• High Dynamic Range LNA • DC to 18 GHzELECTRICAL CHARACTERISTICS (T a = 25 O C)SYMBOLS PARAMETERS/TEST CONDITIONS MIN TYP MAX UNITP 1dB Output Power at 1dB Compression f=2GHzVds=6V, Ids=50% Idss f=12GHz24.0 26.0 25.5 dBm G 1dB Gain at 1dB Compression f=2GHz Vds=6V, Ids=50% Idss f=12GHz 17.0 7.0 19.0 9.0dB PAE Power Added Efficiency at 1dB Compression f=2GHz Vds=6V, Ids=50% Idss f=12GHz 5545% IP3 +5dBm P OUT /Tone (5V/50mA) f=2GHz (5V/90mA) 2831dBm NFNoise Figure (5V/50mA) f=2GHz(5V/90mA)0.4 0.6 dB G A Associated Gain (5V/50mA) f=2GHz(5V/90mA) 20.0 20.0 dB Idss Saturated Drain Current Vds=3V, Vgs=0V 110180250mA Gm Transconductance Vds=3V, Vgs=0V 120 190 mS Vp Pinch-off Voltage Vds=3V, Ids=2.0mA -1.0 -2.5 V BVgd Drain Breakdown Voltage Igd=1.0mA -10 -15 V BVgsSource Breakdown Voltage Igs=1.0mA-6-14VRthThermal Resistance 175* oC/W * Overall Rth depends on case mounting.MAXIMUM RATINGS AT 25O CSYMBOLS PARAMETERS ABSOLUTE 1 CONTINUOUS 2 VdsDrain-Source Voltage 10V6V VgsGate-Source Voltage -6V -3V IdsDrain Current Idss 110mA Igsf Forward Gate Current 30mA 5mAPin Input Power 23dBm@ 3dB CompressionTch Channel Temperature 175oC 150 o C TstgStorage Temperature-65/175o C -65/150 o CPtTotal Power Dissipation 780mW 650mWNote: 1 Exceeding any of the above ratings may result in permanent damage.2. Exceeding any of the above ratings may reduce MTTF below design goals.Excelics Semiconductor, Inc., 2908 Scott Blvd., Santa Clara, CA 95054 Phone: (408) 970-8664 Fax: (408) 970-8998 Web Site: All Dimensions In mils.66'*$O O /H D G V0L QEPA060B-70DATA SHEETHigh Efficiency Heterojunction Power FETTypical PerformanceNoise Figure &IP3S-PARAMETERS6V, 1/2 IdssFREQ --- S11 ------ S21 ------ S12 ------ S22 ---(GHz) MAG ANG MAG ANG MAG ANG MAG ANG 1.0 0.863 -58.2 12.375 135.5 0.026 63.8 0.523 -24.4 2.0 0.696 -101.1 9.063 104.4 0.039 49.7 0.433 -41.0 3.0 0.604 -132.0 6.850 82.3 0.049 43.5 0.388 -51.9 4.0 0.555 -159.5 5.508 63.6 0.055 39.1 0.360 -60.8 5.0 0.538 177.3 4.614 47.0 0.065 35.5 0.322 -70.3 6.0 0.534 160.5 4.002 31.8 0.074 30.5 0.288 -84.5 7.0 0.533 141.8 3.532 16.7 0.083 25.3 0.281 -98.4 8.0 0.540 125.9 3.168 2.3 0.092 19.2 0.254 -111.5 9.0 0.582 105.0 2.817 -12.9 0.101 11.6 0.235 -125.6 10.0 0.622 88.1 2.532 -28.1 0.108 2.7 0.220 -148.1 11.0 0.642 74.5 2.370 -43.9 0.119 -8.1 0.225 -176.6 12.0 0.674 60.3 2.195 -60.1 0.129 -19.3 0.238 155.7 13.0 0.727 47.7 1.970 -74.8 0.132 -30.2 0.244 130.0 14.0 0.764 36.4 1.758 -88.3 0.133 -40.6 0.263 110.6 15.0 0.776 22.6 1.618 -104.8 0.137 -54.2 0.316 90.1 16.0 0.790 8.5 1.441 -122.5 0.134 -69.5 0.358 66.2 17.0 0.781 -1.1 1.285 -135.3 0.133 -78.3 0.363 51.0 18.0 0.792 -9.8 1.221 -147.7 0.144 -91.0 0.396 41.9 19.0 0.811 -22.2 1.106 -163.8 0.142 -106.2 0.418 23.9 20.0 0.836 -32.5 1.016 -179.0 0.144 -121.0 0.445 6.7 21.0 0.800 -41.8 0.975 166.9 0.157 -134.6 0.461 -8.4 22.0 0.761 -54.5 0.941 152.3 0.176 -148.9 0.426 -22.5 23.0 0.800 -68.3 0.861 134.7 0.190 -167.5 0.399 -50.3 24.0 0.799 -80.2 0.764 117.1 0.204 173.5 0.417 -78.5 25.0 0.719 -98.1 0.751 103.1 0.239 157.7 0.451 -87.9 26.0 0.718 -119.4 0.750 85.7 0.291 137.6 0.450 -110.4EPA060B-70 @5V, 2GHz(P OUT /Tone = 5dBm)00.20.40.60.8020406080100120140Ids [mA]N F [d B ]10203040I P 3 [d B m ]NF IP3EPA060B-70DATA SHEETHigh Efficiency Heterojunction Power FETS-PARAMETERS5V,50maFREQ --- S11 --- --- S21 --- --- S12 --- --- S22 ---(GHz) MAG ANG MAG ANG MAG ANG MAG ANG1.0 0.948 -57.7 14.366 129.2 0.032 54.0 0.439 -48.42.0 0.739 -100.4 9.162 106.8 0.042 45.1 0.438 -44.93.0 0.656 -132.4 7.008 84.9 0.050 36.7 0.392 -56.74.0 0.619 -155.0 5.629 67.5 0.056 31.8 0.352 -64.75.0 0.597 -176.9 4.740 51.0 0.062 26.9 0.298 -74.46.0 0.577 162.1 4.086 35.5 0.069 22.1 0.284 -90.67.0 0.580 141.7 3.546 21.4 0.075 18.2 0.287 -96.48.0 0.616 122.1 3.145 6.6 0.081 11.3 0.264 -103.59.0 0.618 117.3 2.918 -7.4 0.088 4.0 0.148 -131.410.0 0.633 99.5 2.657 -22.4 0.097 -1.1 0.185 -169.411.0 0.673 76.6 2.345 -36.9 0.101 -10.0 0.208 -168.312.0 0.718 63.1 2.142 -50.5 0.108 -18.0 0.156 179.213.0 0.761 59.0 1.999 -65.3 0.117 -27.9 0.223 117.814.0 0.777 44.3 1.767 -81.5 0.118 -40.9 0.321 97.015.0 0.779 30.7 1.543 -91.8 0.115 -46.4 0.287 96.416.0 0.816 14.8 1.418 -107.4 0.117 -59.0 0.265 77.717.0 0.827 11.9 1.307 -123.3 0.121 -70.7 0.445 49.218.0 0.822 2.7 1.114 -132.8 0.114 -77.5 0.460 49.819.0 0.852 -9.8 1.090 -144.6 0.123 -87.1 0.424 38.220.0 0.868 -19.9 1.001 -158.4 0.122 -99.4 0.442 21.521.0 0.846 -31.4 0.911 -174.9 0.120 -114.7 0.576 9.422.0 0.838 -32.7 0.856 176.8 0.125 -121.6 0.515 9.923.0 0.860 -47.9 0.832 160.7 0.130 -137.4 0.446 -22.924.0 0.835 -66.2 0.763 141.8 0.128 -156.0 0.536 -40.825.0 0.819 -80.1 0.710 126.8 0.130 -170.6 0.536 -41.426.0 0.868 -78.4 0.699 111.8 0.145 174.2 0.383 -78.0EPA060B-70Noise ParametersVds=5V, Ids=50mAFreq. Gamma Opt Nfmin(GHz) (MAG) (ANG) (dB) Rn/502 0.46 44 0.45 0.114 0.35 96 0.55 0.086 0.23 165 0.75 0.068 0.27 -145 0.92 0.0810 0.35 -85 1.37 0.2312 0.46 -58 1.47 0.4414 0.58 -33 1.92 0.8916 0.68 -6 2.47 1.318 0.63 7 3.03 1.7820 0.68 33 3.24 1.8722 0.63 50 3.43 1.8124 0.67 92 3.65 1.5626 0.72 120 3.86 1.16。
北汽新能源汽车EV160学习资料1

电机驱动
C33DB驱动电机控制器采用三相两电平电压源型逆变器。 驱动电机系统的控制中心,又称智能功率模块,以IGBT(绝缘栅双极型晶体管) 模块为核心,辅以驱动集成电路、主控集成电路。对所有的输入信号进行处理, 并将驱动电机控制系统运行状态的信息通过CAN 2.0网络发送给整车控制器。驱 动电机控制器内含故障诊断电路。当诊断出异常时,它将会激活一个错误代码, 发送给整车控制器,同时也会把存储该故障码和数据。 使用以下传感器来提供驱动电机系统的工作信息,包括: 电流传感器:用以检测电机工作的实际电流(包括母线电流、三相交流电流)电压 传感器:用以检测供给电机控制器工作的实际电压(包括动力电池电压、12V蓄电 池电压) 温度传感器:用以检测电机控制系统的工作温度(包括IGBT模块温度、电机控制 器板载温度)
电机驱动
电机驱动
驱动电机系统是纯电动汽车三大核心部件之一,是车辆行驶的主要执 行机构,其特性决定了车辆的主要性能指标,直接影响车辆动力性、经济 性和用户驾乘感受。可见,驱动电机系统是纯电动汽车中十分重要的部件。 驱动电机系统由驱动电动机(DM)、驱动电机控制器(MCU)构成,通过高低 压线束、冷却管路,与整车其它系统作电气和散热连接。(见下图示) 整车控制器(VCU)根据驾驶员意图发出各种指令,电机控制器响应并反馈, 实时调整驱动电机输出,以实现整车的怠速、前行、倒车、停车、能量回 收以及驻坡等功能。电机控制器另一个重要功能是通信和保护,实时进行 状态和故障检测,保护驱动电机系统和整车安全可靠运行。
整车控制器根据车辆运行的不同情况,包括车速、档位、电池SOC值来决定,电 机输出扭矩/功率。 当电机控制器从整车控制器处得到扭矩输出命令时,将动力电池提供的直流电, 转化成三相正弦交流电,驱动电机输出扭矩,通过机械传输来驱动车辆。
Agilent E6000C Mini-OTDR与E6091A Toolkit III的商业说明文件
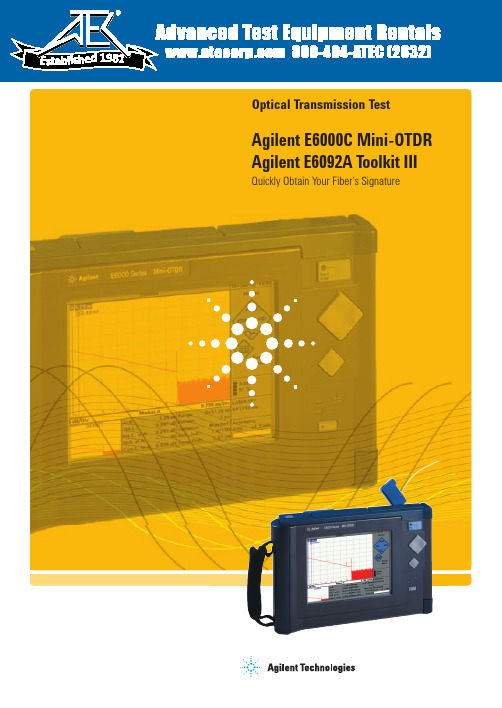
eXtreme Productivity Improvement Agilent E6000C Mini-OTDR Agilent E6092A Toolkit III Quickly Obtain Your Fiber’s Signature Optical Transmission Test1981E6000C Mini-OTDR - E6091A Toolkit III The Mini-OTDR starts making installation and commissioningeasier before you even switch it on. We have trimmed theweight and size to make it easy to carry, put it in a rugged,weather-tolerant housing so you don’t need to worry aboutconditions, and made it rugged by design so it can take therough and tumble of getting it where you need it.And when you get there, a user and task oriented interface offers productive support for qualifying large numbers of fibers in minimal time. The Mini-OTDR is intuitive to use, quick to measure and easy to integrate into your installation process. Acceptance documentationThe effective way to amplify the usefulness of your Mini-OTDR is by applying the post-processing capacity of the Agilent E6091A OTDR Toolkit III. The Toolkit is a powerful but easy to use Windows software that connects to the Mini-OTDR to collect, analyze, organize and store the traces, and to produce thedocumentation you need.Together, Agilent’s Mini-OTDR and theToolkit provide the precise mixture ofcomfort and performance that make theman unbeatable productivity boost foreverybody from untrained operators tocommissioning engineers.Project supportThe Toolkit III provides a comprehensiveset of features to lighten your projectworkload. A project creation wizard getsthe bureaucracy under control from thebeginning. Automatic trace labeling,powerful trace loading filters and batchprocessing help you turn your OTDR datainto acceptance reports in yourcustomer’s format, work orders for splicecrews, or Microsoft Excel data for furtheruse and scrutiny.A range of analysesThe Toolkit III can access and process (orbatch-process) the data from the Mini-OTDR to perform two-way averages, tocompare up to 96 traces, and to analyzeevents such as splices and connectors, orfiber attenuation.Modular designA range of plug-in modulesfor different wavelengths andmeasurements make theMini-OTDR easy to adapt tothe task on hand, and easy toadapt to new demands.High-Visibility screenA brilliant, high-resolutiondisplay makes the Mini-OTDRjust as usable outdoors as in.Ease of useSingle button operation,presets and macros fordifferent fiber types ormeasurement conditions, anOTDR Assistant to guideuntrained users, and a ”scantrace” that provides a pass/failresult, make the Mini-OTDR avaluable addition to yourequipment pool.Your multifunctional maintenance toolKeeping a network running or getting a fiber or cable back up takes more than speed and precision. Having the right application on hand makes the difference.Agilent’s Mini-OTDR provides a selection of tools and features for experts andbeginners alike that speed up preventive maintenance and repair.•Fiber Break Locator to quickly find breaks and bends.•Locate and characterize splice and connector losses.•Multifiber testing for fast high-count cable qualification.•With the built-in light source and the power meter module you can perform power and loss measurement.•Graphical representation of measurement results in event tables, showing loss and reflection, and pass/fail results.•Data transfer is ensured due to certified Bellcore/Telcordia GR-196-CORE standard – your investment is protected •Visual Fault Finder to check patch cords for light leakage.Service and support•Worldwide sales office and online assistance support.Calibration warranty•Standard 2 year guarantee, with an optional 3-year or 5-year calibration warranty.We speak your language•16 languages are available on the support CD, and up to 4 languages of your choice can be loadedonto the Mini-OTDR at any one time,including help text.Multi-Fiber testingThe Mini-OTDR speeds and eases multi-fiber test by integrating multi-fiberfunctionality into the user interface, and automatically assigning appropriate file names and fiber numbers to the stored results – particularly useful in conjunction with the OTDR Toolkit III software – and stored on a PCM Flashdisk.You’re expected to do more with less – provide results faster with fewer resources, increase network performance, boost ROI, rapidly roll out new services – deliver eXtremeProductivity Improvements (XPI). Agilent XPI solutions help you drastically cut the time and cost of installing, testing and maintaining your communications networks. Together with Agilent, gain the eXtreme Productivity Improvements that your business demands!XPIMini-OTDR Module Classes: Agilent’s Recommendation Link length 50 km100 km150 km200 km and moreKEY SPECIFICATIONS •Weight 2.9kg (6.4lb)•Modular Construction- Single Mode Modules for 1310nm,1550nm, 1625nm, 1310/1550nm,1550/1625nm- Multimode Modules for 850/1300nm - Power meter sub-module calibrated for all standard wavelengths,- Visual faultfinder sub-module - Range of optical connectors•Connector and splice losses can be localized within 8 cm, even at a distance of 150 km•High dynamic range – 45dB.•Flash disk storage for 13,000 OTDR traces.•Boots up in 15 seconds.•Battery operation 8 hours.Accessories•Compact keybord for fast reports and text entry•Water- and shock-resistant carry case for mainframe,modules and accessories •Full range of standard connectors (FC/PC,SC, ST,E2000, D4, HMS10, DIN,BICONIC, APC)Agilent E6000C Mini-OTDRAgilent E6091A Toolkit IIIQuickly Obtain Your Fiber’s SignatureChoose your level of expertiseWhile we are proud that presets,automatic fiber characterization, and arange of reference and interactive helpsystems make the Mini-OTDR a tool thatcan be used by an untrained technician,this has not been done at the expense ofthe advanced user. A selectable userexperience level, and full access to all theparameters of a measurement make theMini-OTDR a flexible tool in any hands.Together with Agilent, gain the eXtreme ProductivityImprovements that your business demands!/comms/XPIXPI Argentina+54 11 5811 7115 Australia1800 629 485 Austria+43 (01)25 125 7006 Belgium+32 (0) 2 404 9340 Brazil+55 11 4197 3600 Canada-English 877 894 4414Canada-French877 894 4414China800 810 0189Denmark+45 70 13 15 15Finland+358 (0) 10 855 2100France+33 (0) 825 010 700Germany+49 (0) 18 05 24 63 33Hong Kong800 930 871India1600 112 929Ireland+353 1890 924 204Israel+972 3 6892 500Italy+39 02 92 60 8484Japan0120 421 345Luxemborg+32 (0) 2 404 9340Malaysia1800 888 848Mexico+52 01800 506 4800Netherlands+31 (0) 20 5472111Norway+47 23 25 3720Philippines1800 1651 0170Poland+48 22 723 0066Russia+7 095 797 3963Singapore180****8100South Korea080 769 0800Spain+34 91 631 3300Sweden0200 88 22 55Switzerland-German+41 (0) 1 735 9300Switzerland-Italian+39 (0) 2 92 60 8484Switzerland-French+33 (0) 825 010 700Taiwan0800 047 866Thailand1800 226 008United Kingdom+44 (0) 7004 666666USA800 452 4844This information is subject to change without notice.© Agilent Technologies, Inc. 2002Printed in UK Oct 8, 2002 (C+C)*5988-2238EN*5988-2238ENBundled to meet yourapplication needsOur commitment to your productivity startswith prepared bundles to match the Mini-OTDR to your application, so you can getup and running as quickly as possible.Agilent’s modular approach to connectorsand OTDR accessories gives you theflexibility to adapt your equipment as theneed arises.The installation bundle E6032Aincludes the Mini-OTDR mainframe withcolor display, a 1310/1550 OTDR module45dB, a 64 MB compact flashcard andPCMCIA adapter, PC Reader Scan Disk®,a compact keyboard and the Toolkit III.The maintenance bundle E6031Aincludes the Mini-OTDR mainframe withcolor display, a 1310/1550 OTDR module40dB, the power meter sub module andthe Toolkit III.Agilent E6000C Mini-OTDR InformationWavelength Dynamic Event Attenuation Recommended FiberType Module Range(dB)Deadline Dead Zone Application1310nm30dB3m10m Metropolitan Single-Mode E6001A1310/1550nm30/30dB3m10/12m Metropolitan Single-Mode E6004A1310/1550nm35/34dB3m10/12m Metropolitan/Trunk Single-Mode E6003A1310/1550nm40/39dB3m10/12m Metropolitan/Trunk Single-Mode E6003B1310/1550nm45/43dB3m10/12m Trunk/Undersea Single-Mode E6008B1550/1625nm43/40dB3m12m/14m Trunk/Undersea Single-Mode E6012A850/1300nm18/23dB3m10m LAN Multimode E6009A850/1300nm26/34dB3m10m LAN Multimode E6005A1310/1550/1625nm45/43/40dB3m10/12/14m Metropolitan Single Mode E6013A。
IEC60950中文版

IEC 60950/EN60950(2000版)测试简介机构部分测试(PHYSICAL TESTS)1*、固定力测试(STEADY FORCE TEST)(CLAUSE ,,)General(一般要求)外壳应具有足的机械强度。
若外壳提供了足够的机械防护,对于为满足而提供的内部挡板、罩或类似物,则不要求进行机械强度实验。
对于所有的设备要求通过,,,的测试,对于手持设备还要求通过的跌落实验。
Steady force test , 10N(固定力测试,10牛顿)Components and parts, other than parts serving as an ENCLOSURE (see andsubjected to a steady force of 10N+/-1N。
元器件在承受10N的外加力时,不能影响到安全。
Steady force test , 30N(固定力测试,30牛顿)Parts of an ENCLOSURE located in an OPERATOR ACCESS AREA, which are protected by acover or door meeting the requirements of are subjected to a steady of 30N+/-3N for aperiod of 5s,applied by means of a straight unjointed version of the test finger,of figure 2A(see to the part on or within the equipment.安装在操作人员接触区内的并由满足要求的罩或门来保护的外壳零部件应承受30N+/-3N的恒定作用力持续5s。
Steady force test , 250N(固定力测试,250牛顿)外部防护罩应承受250N+/-10N的恒定力持续5s,该作用力通过能在直径300mm圆形平面上进行接触的适用的实验工具,施加到固定在设备上的防护外壳上。
Exeltech XP600 1100 2000逆变器安装与使用手册说明书
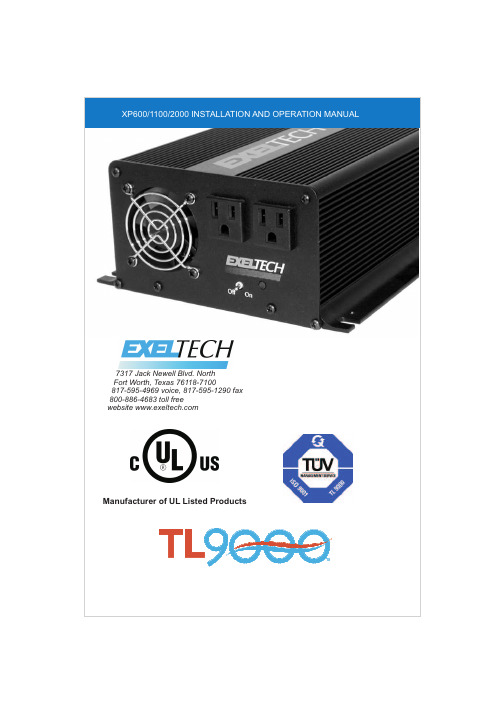
Page 2
XP600/1100/2000 INSTALLATION AND OPERATION MANUAL
Introduction
1.0
Thank you for purchasing the finest sine-wave inverter in the power
conversion industry. Exeltech’s journey to excellence includes the
for several seconds. This guarantees the inverter is disabled, in
the event that the user attempts to clear the short without first
The inverter can maintain a spectrally pure output with any load,
due to a specially designed non-linear control loop in the primary
DC to DC converter. This circuitry is one of three circuits which
Exeltech Inc.
.
Exeltech, Inc.
.
7317 Jack Newell Blvd North
.
Fort Worth, Texas 76118-7100
.
Page 1
XP600/1100/2000 INSTALLATION AND OPERATION MANUAL
Table of Contents
current circuitry insures maximum current does not exceed 300%
EM60000中文资料

(
(
(,
Parameter Supply voltage (VDD - VSS) Input voltage Operating Temperature Storage Temperature Specification -0.3V to +7.0V VSS -0.3V to VDD +0.3V -20°C to 70°C -55°C to 125°C
元器件交易网
8
0?3?&4""@49
Items Operating Voltage Sym VDD VDD Standby Current Operating Current Drive Current of Port 2, 3, 4, 5 Sink Current of Port 2, 3, 4, 5 ISB ISB IOP IOP IOH IOH IOL IOL IOL IOL VIH VIL VIH VIL II II IVO IVO FOSC FOSC Min. 2.4 2.4 9 2 3.5 2.5 1.8 1.4 2 2 Typ. 3 1.5 8 3 3 3 4 Max. 5.5 3.6 5 1.0 5 3 24 12 0.8 0.6 12 5 4 4 8 4 Unit V V µA µA mA mA mA mA mA mA mA mA V V V V μA μA mA mA MHz MHz Condition For EM60001, EM60101, EM60201, EM60301 For EM60600S VDD=4.5V VDD=3V VDD=4.5V, FOSC=6MHz, no load VDD=3V, FOSC=4MHz, no load VDD=4.5V, VOH=2.4V VDD=3V, VOH=2.4V VDD=4.5V, VOL=0.4V VDD=4.5V, VOL=3V VDD=3V, VOL=0.4V VDD=3V, VOL=1.5V VDD=4.5V VDD=4.5V VDD=3V VDD=3V VDD=4.5V VDD=3V VDD=4.5V, VO=0.7V VDD=3V, VO=0.7V VDD=4.5 V VDD=2.4V
EP-600系列微型光纤耦合全能电场探头说明书
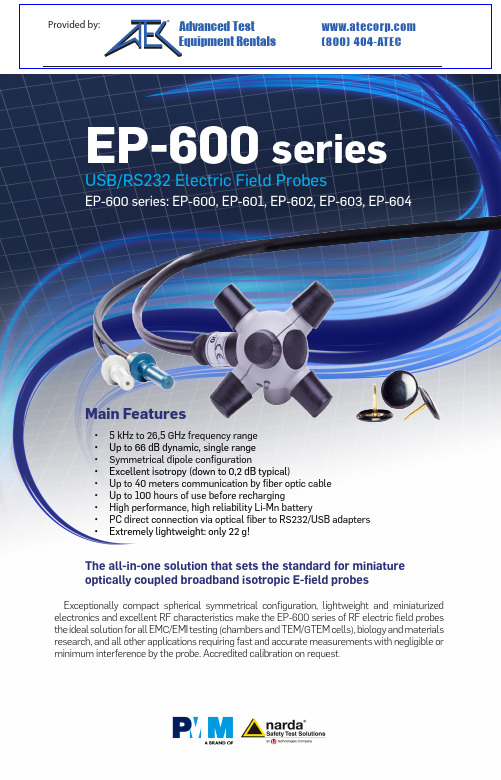
The all-in-one solution that sets the standard for miniature optically coupled broadband isotropic E-field probesExceptionally compact spherical symmetrical configuration, lightweight and miniaturized electronics and excellent RF characteristics make the EP-600 series of RF electric field probes the ideal solution for all EMC/EMI testing (chambers and TEM/GTEM cells), biology and materials research, and all other applications requiring fast and accurate measurements with negligible or minimum interference by the probe. Accredited calibration on request .Main Features• 5 kHz to 26,5 GHz frequency range •Up to 66 dB dynamic, single range •Symmetrical dipole configuration•Excellent isotropy (down to 0,2 dB typical)•Up to 40 meters communication by fiber optic cable •Up to 100 hours of use before recharging• High performance, high reliability Li-Mn battery• PC direct connection via optical fiber to RS232/USB adapters •Extremely lightweight: only 22 g!USB/RS232 Electric Field ProbesEP-600, EP-601, EP-602, EP-603, EP-604USB/RS232 Electric Field ProbesOrdering information:EP-600 Field probe 100 kHz to 9,25 GHz 0,14 to 140 V/m EP-601 Field probe 10 kHz to 9,25 GHz 0,5 to 500 V/m EP-602 Field probe 5 kHz to 9,25 GHz 1,5 to 1500 V/m EP-603 Field probe 300 kHz to 18 GHz 0,17 to 170 V/m EP-604 Field probe 300 kHz to 26,5 GHz 0,4 to 800 V/m Includes: 10 m fiber optic cable, optical/RS232 adapter + RS232/USB adapter, PC utility WIN-EP600, charging fixture, A/C charger, tripod mounting tip, user’s manual,standard calibration certificate.Optional accessories:SB-10 Switching Control BoxFO-EP600/10 Fiber optic cable (10 m)FO-EP600/20 Fiber optic cable (20 m)FO-EP600/40 Fiber optic cable (40 m)TT-01 telescopic extension Accredited certificate TR-02A setIncludes: TR02 plastic column tripod, joint, soft carrying case For full list please refer to the user’s manualE P 600-F E N -81010- S p e c i fi c a t i o n s s u b j e c t t o c h a n g e w i t h o u t n o t i c eResolution SensorsMeasurement mode Sampling rate Digital filtering Internal battery Operation time Recharging timeInternal data memory CommunicationFiber optic connector Fiber optic length Fiber optic to PC PC softwareOperating temperatureTemperature reading resolution Battery voltage reading resolution Probe holder tip0,01 V/mSix monopolesX-Y-Z axis simultaneous sampling 22 to 0,03 samples/s depending on filter settingsLow-pass 2,3 to 28 Hz; 80 dB notch 50/60 Hz 3V, 5 mA/h, Li-Mn rechargeable 100 hours @ 0,4 S/s, 28 Hz filter 48 hours for full operation time Partial charging allowed, e.g.:8 hrs rech. = 12 hrs operation @ 5 S/s 1 hr rech. = 5 hrs operation @ 0,4 S/s Serial no. - Calibration factors & date Firmware versionBidirectional fiber optic link HFBR-050010 m, standard 20/40 m optionsFiber optic to RS232 converter RS232 to USB converterDisplays field, temperature, battery,sampling, filters, averaging, frequency setting, manual data logging as text file -10 °C + 50 °C 0,1 °C 10 mV1/4 20 UNC femaleCOMMON SPECIFICATIONSGenerators/AmplifiersAntennasProbes•3010: EMI Signal Generator 9 kHz to 1 GHz •3030: EMI Signal Generator 9 kHz to 3 GHz•6000N: Power Amplifier 9 kHz to 230 MHz / 10W •6630: USB RF Power Sensor 9 kHz to 3 GHz•BC-01: Biconical Antenna 30 to 200 MHz•BL-01: Biconical Log Periodic Antenna 30 MHz to 6 GHz •DR-01: Double-ridged horn Antenna 6 to 18 GHz •LP-02: Log Periodic Antenna 200 MHz to 3 GHz •LP-03: Log Periodic Antenna 800 MHz to 6 GHz •LP-04: Log Periodic Antenna 200 MHz to 6 GHz •Antenna Set AS-02 (BC01+LP02+TR01)•Antenna Set AS-03 (BC01+LP02+LP03+TR01) •Antenna Set AS-04 (BC01+LP04+TR01)•Antenna Set AS-05 (BC01+LP04+DR01+TR01)•Antenna Set AS-06 (BC01+LP-02+LP03+DR01+TR01)•Antenna Set AS-07 (BL01+TR01)•Antenna Set AS-08 (BL01+DR01+TR01)•RA-01 / RA-01-HV / RA-01-MIL Rod Antenna System•OR03: Optical Programmable Repeater with probesRelated productsSales:Via Leonardo da Vinci, 21/2320090 Segrate (Milano) - ITALY Phone: +39 02 2699871Fax: +39 02 26998700E-Mail:***********************Internet: www.narda-sts.itHeadquarters:Via Benessea, 29/B17035 Cisano sul Neva (SV) - ITALY Phone: +39 0182 58641Fax: +39 0182 586400Main specifications (see the user manual for complete information)Frequency Range FlatnessDynamic RangeOverloadDimensions (overall)Weight (incl. 1 m fiber optic pigtail)EP-600100 kHz to 9,25 GHz Frequency correction OFF 1 to 150 MHz: 0,8 dB 0,5 to 6000 MHz: 1,6 dB 0,3 to 7500 MHz: 3,2 dB Frequency correction ON, typical 0,3 to 7500 MHz: 0,4 dB0,14 to 140 V/m 60 dB single range300 V/m 53mm 23 g10 kHz to 9,25 GHz Frequency correction OFF 0,1 to 150 MHz: 0,4 dB 0,05 to 6000 MHz: 1,6 dB 0,03 to 7500 MHz: 3,2 dB Frequency correction ON, typical 0,05 to 7500 MHz: 0,4 dB 0,5 to 500 V/m 60 dB single range 1000 V/m 53 mm 23 g5 kHz to 9,25 GHz Frequency correction OFF 0,1 to 150 MHz: 0,4 dB 0,05 to 6000 MHz: 1,6 dB 0,03 to 7500 MHz: 3,2 dB Frequency correction ON, typical 0,05 to 7500 MHz: 0,4 dB 1,5 to 1500 V/m 60 dB single range 3000 V/m 53 mm 23 g300 kHz to 18 GHz Frequency correction OFF 3 to 8200 MHz: 1,4 dB 1 to 12000 MHz: 2,4 dB 0,6 to 18000 MHz: 3,8 dB Frequency correction ON, typical 0,3 to 18000 MHz: 0,4 dB 0,17 to 170 V/m 60 dB single range 350 V/m 53 mm 23 g300 kHz to 26,5 GHz Frequency correction OFF 10 to 18000 MHz: 1,8 dB 3 to 23000 MHz: 3,2 dB Frequency correction ON, typical 0,3 to 26500 MHz: 0,4 dB 0,4 to 800 V/m 66 dB single range 1600 V/m 45 mm 22 gEP-601EP-602EP-603EP-604。
CommScope E6000 Converged Edge Router (CER) 产品介绍说

PRODUCT OVERVIEWThe E6000® Converged Edge Router (CER) is a next-generation Converged Cable Access Platform (CCAP ™) that provides cable operators unprecedented advances in channel density, power efficiency, and cost savings in a redundant, integratedarchitecture designed from the ground up for high availability. This powerful design allows operators to converge all services (video, high speed data, and voice), enabling additional savings in capital and operational expenditures along with increased operational efficiency. For Distributed Access Architecture (DAA) solutions, CommScope provides both the CCAP Core andRemote PHY (R-PHY) Device (RPD) defined in the CableLabs® Modular Headend Architecture (MHAv2). In this approach, the PHY layer is moved from the E6000 CER into a node or remote shelf, but the MAC processing, provisioning, and monitoring functions are performed by the E6000 CCAP Core.The Downstream CCAP Core Module (DCCM) has the same MAC processing capacity of the 2nd generation Downstream Cable Access Module (DCAM-2) but without the PHY-layer hardware and related components. The DCCM and DCAM-2 can be used interchangeably to provide downstream MAC processing for the E6000 CCAP Core. The DCCM offers power, weight, and cost savings over the DCAM-2 for Remote PHY applications. Without RF hardware, the DCCM cannot be used for I-CCAP applications. E6000 Release 7.0 and later support “hybrid” operation of Integrated CCAP (I-CCAP) and CCAP Core within the same chassis.Roadmap for future capabilities is subject to change.E6000® Converged Edge RouterDownstream CCAP Core ModuleThe Downstream CCAP Core Module (DCCM) isessentially a DCAM-2 without the RF circuitry. The DCCMis meant only for R-PHY operation for which it providesthe same functionality and capacity as the DCAM-2. TheDCCM and DCAM-2 are interchangeable for R-PHYoperation and can be mixed in the same E6000 chassis.The DCCM supports MAC processing for RPDs withdownstream RF bands up to 1.2 GHz. In addition, theDCCM can support multiple 192 MHz OFDM channelsper Service Group on capable RPDs. Operators receivesignificant benefits in terms of operational simplicity,power, and cost savings by deploying DCCM in R-PHYapplications. Use of DCCM requires the RSM-2 andeither UCAM-2 or UCCM upstream modules.Roadmap for future capabilities is subject to change.SUMMARY OF DCCM FEATURES AND CAPABILITIES (PARTIAL LIST)Downstream MAC Processing for Remote PHY Operation on the E6000 CER Acting as a CCAP CoreNo RF Output —R-PHY Operation OnlyFull Spectrum Capable (MAC processing for channels up to 1.2GHz)Interoperable with DCAM-2 in the Same E6000 ChassisMultiple DOCSIS 3.1 Downstream Channel Support (24 –192 MHz each) —Dependent on Software Release and RPD Capabilities DOCSIS 3.0 Downstream (Annex A and Annex B) Support —Channel Density Dependent on Software Release and RPD Capabilities Video SC-QAM Support for VOD and Broadcast Services —Channel Density Dependent on Software Release and RPD Capabilities Channel Density Scalability via Licensing or Software Upgrades (No Hardware Changes Required)E6000 CCAP Core Interoperable for Multi-Core R-PHY ArchitecturesDeploys with CCAP Core Rear Card (CCRC) –One Required on the Back of the E6000 Chassis for Each DCCMSPECIFICATIONSRemote PHY CapabilitiesFrequency Range (MHz)108 to 1218 (edge to edge)Modulation (QAM)All required by DOCSIS 3.0 and DOCSIS 3.1(Specific software support varies by release)Max OFDM Channel Width (MHz)192 (Multiple channels supported per RPD Service Group)Max SC-QAMs perDownstream Service Group128 (Sum total DOCSIS and IEQ)SC-QAM Data Rate (Mbps)(Max.)30.34 to 55.62 per channelMax Number of DS ServiceGroups per DCCM27SC-QAM RF Output Level(dBmV)Dependent on RPD PhysicalPower-48 VDCPower Consumption (W)135 (typical at 25 °C)Operating Temperature: Short Term °F (°C) Long Term °F (°C)+23 to +131 (-5 to +55) +41 to +104 (+5 to +40)Storage Temperature °F(°C)-40 to +158 (-40 to +70)Operating Humidity(Min.-Max.)5 to 85% (Non condensing)Dimensions(H x W x D) in. (cm)13.8 x 1.2 x 17. 8 (35.0 x 3.0 x 45.3) Weight lbs. (kg) Approx. 5 (2.3)SPECIFICATIONSInstallation Environment (System Level)Management Interfaces100/1000 Mbps Ethernet (RJ-45) plusConsole (serial port, RJ45)RF Connector Access NoneNSI Connector Access RSM-2 ports via front of chassis,RPIC-2Q ports via rear Management Access (System Level)In-band Management with Access Control Lists via any NSI portOut-of-Band Management via dedicated Ethernet port on RPIC-2Q Console (serial) port on RPIC-2QManaging the E6000® CER is typically done via SNMP and/or CLI. The E6000 CER has multiple options available for IPDR, a useful tool for measuring bandwidth usage. Physical maintenance of the E6000 CER is very simple. Air filters, one in the front and another in the rear of the chassis, should be inspected and/or replaced per recommendations in the E6000 CER User Guide.Roadmap for future capabilities is subject to change.Note:Specifications are subject to change without notice.Copyright Statement:©2021CommScope,Inc.All rights reserved.ARRIS,the ARRIS logo and E6000are trademarks of CommScope,Inc.and/or its affiliates.All other trademarks are the property of their respective owners.No part of this content may be reproduced in any form or by any means or used to make any derivative work (such as translation,transformation,or adaptation)without written permission from CommScope,Inc and/or its affiliates (“CommScope”).CommScope reserves the right to revise or change this content from time to time without obligation on the part of CommScope to provide notification of such revision or change.ORDERING CODES (PARTIAL LIST)Part NumberDescriptionPart NumberDescription1000536GEN-2 Duplex Chassis Kit -Two RSM-2s, No CAMs 1000325Router System Module 2 Kit -1 RSM-2 and RPIC-2Q 1000963CCRC -CCAP Core Rear Card (for DCCM and UCCM, active or spare)1001136SYSTEM-PRINCIPAL-CORE LICENSE1000961DCCM -DS CCAP Core Module (only for RPHYapplications; must purchase one of the Initial DS D3.0 MAC License Bundles with this item)1000962UCCM -US CCAP Core Module (only for RPHYapplications; must purchase one of the Initial Upstream D3.0 MAC License Bundles with this item)1000720E6000; 256 Initial DS D3.0 Annex A MAC License Bundle for DCAM-2 -For MAC Channels 1-256 (requires DCAM-2 HW purchase (PN 1000506) or DCCM HW purchase (PN 1000961))1000737E6000; 48 Initial Upstream D3.0 MAC License Bundle for UCAM-2 -For MAC Channels 1-48 (requires UCAM-2 HW purchase (PN 1000445) or UCCM HW purchase (PN 1000962))1000721E6000; 384 Initial DS D3.0 Annex A MAC License Bundle for DCAM-2 -For MAC Channels 1-384 (requires DCAM-2 HW purchase (PN 1000506) or DCCM HW purchase (PN 1000961))1001047E6000; 64 Initial Upstream D3.0 MAC License Bundle for UCAM-2 -For MAC Channels 1-64 (requires UCAM-2 HW purchase (PN 1000445) or UCCM HW purchase (PN 1000962))1001279E6000; 448 Initial DS D3.0 Annex A MAC License Bundle for DCAM-2 -For MAC Channels 1-448 (requires DCAM-2 HW purchase (PN 1000506) or DCCM HW purchase (PN 1000961))1000738E6000; 72 Initial Upstream D3.0 MAC License Bundle for UCAM-2 -For MAC Channels 1-72 (requires UCAM-2 HW purchase (PN 1000445) or UCCM HW purchase (PN 1000962))1000722E6000; 512 Initial DS D3.0 Annex A MAC License Bundle for DCAM-2 -For MAC Channels 1-512 (requires DCAM-2 HW purchase (PN 1000506) or DCCM HW purchase (PN 1000961))1000739E6000; 96 Initial Upstream D3.0 MAC License Bundle for UCAM-2 -For MAC Channels 1-96 (requires UCAM-2 HW purchase (PN 1000445) or UCCM HW purchase (PN 1000962))1000730E6000; 256 Initial DS D3.0 Annex B MAC License Bundle for DCAM-2 -For MAC Channels 1-256 (requires DCAM-2 HW purchase (PN 1000506) or DCCM HW purchase (PN 1000961))1000740E6000; 144 Initial Upstream D3.0 MAC License Bundle for UCAM-2 -For MAC Channels 1-144 (requires UCAM-2 HW purchase (PN 1000445) or UCCM HW purchase (PN 1000962))1000731E6000; 384 Initial DS D3.0 Annex B MAC License Bundle for DCAM-2 -For MAC Channels 1-384 (requires DCAM-2 HW purchase (PN 1000506) or DCCM HW purchase (PN 1000961))1000741E6000; 192 Initial Upstream D3.0 MAC License Bundle for UCAM-2 -For MAC Channels 1-192 (requires UCAM-2 HW purchase (PN 1000445) or UCCM HW purchase (PN 1000962))1001272E6000; 448 Initial DS D3.0 Annex B MAC License Bundle for DCAM-2 -For MAC Channels 1-448 (requires DCAM-2 HW purchase (PN 1000506) or DCCM HW purchase (PN 1000961))1000742E6000; 216 Initial Upstream D3.0 MAC License Bundle for UCAM-2 -For MAC Channels 1-216 (requires UCAM-2 HW purchase (PN 1000445) or UCCM HW purchase (PN 1000962))1000732E6000; 512 Initial DS D3.0 Annex B MAC License Bundle for DCAM-2 -For MAC Channels 1-512 (requires DCAM-2 HW purchase (PN 1000506) or DCCM HW purchase (PN 1000961))1000715E6000 D3.0 Downstream Annex A MAC Processing License (per 8 MHz D3.0 DS channel)1000736E6000 D3.0 Upstream MAC Processing License (per D3.0 US channel)1000716E6000 D3.0 Downstream Annex B MAC Processing License (per 6 MHz D3.0 DS channel)1000743E6000 D3.1 Downstream MAC Processing License (per 1 MHz channel)1000744E6000 D3.1 Upstream MAC Processing License (per 1 MHz channel)Full Price List available from CommScopeCUSTOMER CAREContact Customer Care for product information and sales:•United States: 866-36-ARRIS •International: +1-678-473-5656(rev 04-2021)E6000_CER_DCCM v1.0。
EVERQ6000软起动器说明书
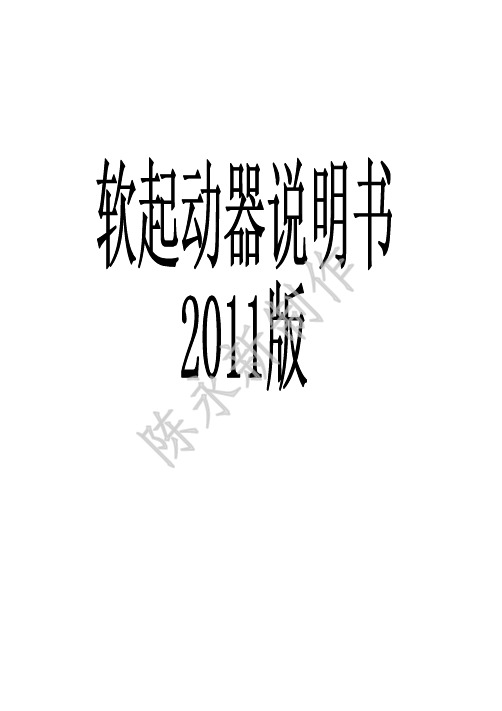
作 启动的星/三角转换、自耦降压、磁控降压等启动设备的理想替代产品。其
性能及可靠性是目前市场上普通软起动器所无法比拟的。
制 它集中了国内同类型软起动器最先进的性能和工艺,采用优质元器件,
并有所创新,因此其性能和可靠性是目前市场上同类型产品无法比拟的。
9.1 启动时跳闸·············································································· 35 9.2 启动后电机自行停机 ····························································· 35 9.3 总是不停的在启动(时间超过 60 秒)······························ 35
新制作 陈永
EVERQ6000 智能软起动器
EVERQ6000 系列智能软起动器概述:
EVERQ6000 旁路型智能软起动器是采用微电子数字控制技术,专为各 种规格的三相异步电动机设计的具有软启动和软停止及多项保护功能的先 进产品。
EVERQ6000 旁路型智能软起动器适用于三相异步鼠笼式电动机。它减 轻了电动机启动及停止带来的电流浪涌对电网的冲击,能更有效的缓冲对电 动机械的损伤,延长电动机使用寿命。
EVERQ6000 系列智能式旁路软起动器适用于交流电 380V, 50Hz (660V,60Hz)三相交流鼠笼型异步电动机,软起动器的主控装置又双极可 控硅与散热片压装而成。需装载壳体内它与外部塑壳断路器及交流接触 器、机内主板(中央控制单元)组成电动机的控制系统电路,能起到电 动机的启动与停止控制和过载、缺相、三项不平衡,过压、欠压等保护 功能。
EGS006 逆变器驱动板用户手册说明书
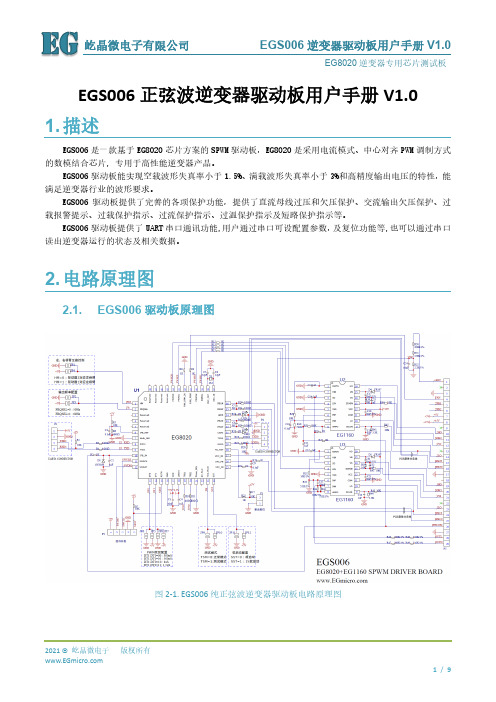
EG8020 逆变器专用芯片测试板
3.3. EGS006 驱动板背面跳线功能设置
序号
跳线名称 标号
设置说明
JP1 当 JP1 短路,既 HM=“0”时,选择驱动器 2 对应左桥臂控制
1
HM
JP4 当 JP4 短路,既 HM=“1”时,选择驱动器 1 对应左桥臂控制
JP6 当 JP6 和 JP8 同时短路,既 DT1:DT0=“00”时:死区时间为 300ns
EGS006 驱动板能实现空载波形失真率小于 1.5%、满载波形失真率小于 3%和高精度输出电压的特性,能 满足逆变器行业的波形要求。
EGS006 驱动板提供了完善的各项保护功能,提供了直流母线过压和欠压保护、交流输出欠压保护、过 载报警提示、过载保护指示、过流保护指示、过温保护指示及短路保护指示等。
器 4 路通道分别测试 RC 滤波后的输出波形,测到的正确波形如图 4-3,图中 CH1 对应 TEST1 滤波后的 波形,CH2 对应 TEST2 滤波后的波形,CH3 对应 TEST3 滤波后的波形,CH4 对应 TEST4 滤波后的波形。
10K TEST1~TEST4输出分 别接一个RC滤波电路
屹晶微电子有限公司
EGS006 逆变器驱动板用户手册 V1.0
EG8020 逆变器专用芯片测试板
EGS006 正弦波逆变器驱动板用户手册 V1.0
1. 描述
EGS006 是一款基于 EG8020 芯片方案的 SPWM 驱动板,EG8020 是采用电流模式、中心对齐 PWM 调制方式 的数模结合芯片, 专用于高性能逆变器产品。
3.4. LED 运行及故障指示
EGS006 驱动板上采用了绿灯 LED 和红灯 LED 作正常运行及故障指示功能,具体定义如下: 绿灯 LED 长亮、红灯 LED 长灭:该状态指示逆变器正常运行输出,无故障。 绿灯 LED 长亮、红灯 LED 快闪烁:该状态指示逆变器正常运行输出,有过载或过流情况,还 未进入到过载或过流保护状态。 红灯 LED 长亮、绿灯 LED 长灭:该状态指示逆变器进入故障保护模式,用户可通过串口通讯 读取具体的故障代码。
EL0600中文资料(everlight)中文数据手册「EasyDatasheet - 矽搜」

Unit
mA V V mW mW mA mA V mW V有效值 °C °C °C
2
芯片中文手册,看全文,戳
数据表
8脚SOP高速的10Mbit / s的逻辑门
光耦合器
EL06XX系列
电气特性(Ta = -40〜85°除非另有规定) C
Input
参数
正向电压
反向电压 体温 向前系数 电压 输入电容
V/µS
VCM=50Vp-p (Fig.14)
IF = 7.5mA , V OH =2.0V,
-
RL=350 , TA=25°C
VCM=400Vp-p (Fig.14)
IF = 7.5mA , V OH =2.0V,
-
RL=350 , TA=25°C
VCM=400Vp-p (Fig.15)
IF = 0mA , V OL=0.8V,
输出电压
输出功率耗散
隔离电压
*1
工作温度
储存温度
焊接温度
*2
IF
CC
VE
VR
PD PC IE IO VO PO VISO TOPR T STG TSOL
20 5.5 5 40 85 5 50 7.0 100 3750 -40 ~ +100 -55 ~ +125 260
注意事项: * 1交流电进行1分钟,RH = 40〜60%RH在本试验中,销1,2,3,4短接在一起,并且销5,6,7和8被短接在一起.
符
Min.
VF
-
VR
5.0
∆V F/∆T A
-
C IN
-
Typ. Max.
Unit
1.4
Vecow PE-6000 用户手册说明书
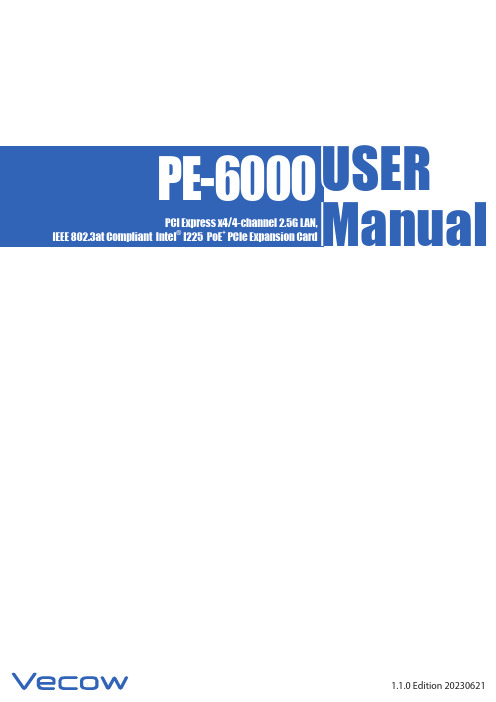
Record of RevisionThis manual is released by Vecow Co., Ltd. for reference purpose only. All product offerings and specifications are subject to change without prior notice. Vecow Co., Ltd. is under no legal commitment to the details of this document. Vecow shall not be liable for direct, indirect, special, incidental, or consequential damages arising out of the use of this document, the products, or any third party infringements, which may result from such use.DisclaimerThis equipment has been tested and found to comply with the limits for a Class A digital device, pursuant to part 15 of the FCC Rules. These limits are designed to provide reasonable protection against harmful interference when the equipment is operated in a commercial environment. This equipment generates, uses, and can radiate radio frequency energy, and if it is not installed and used in accordance with the instruction manual, it may cause harmful interference to radio communications. Operation of this equipment in a residential area is likely to cause harmful interference in which case the user will be required to correct the interference at his own expense.FCCThe products described in this manual comply with all applicable European Union (CE) directives if it has a CE marking. For computer systems to remain CE compliant, only CE-compliant parts may be used. Maintaining CE compliance also requires proper cable and cabling techniques.CEDeclaration of ConformityThis document contains proprietary information protected by copyright. No part of this publication may be reproduced in any form or by any means, electric, photocopying, recording or otherwise, without prior written authorization by Vecow Co., Ltd. The rights of all the brand names, product names, and trademarks belong to their respective owners.Copyright and TrademarksOrder InformationTable of ContentsCHAPTER 1 GENERAL INTRODUCTION 11.1 Overview 11.2 Features 11.3 Product Specification 21.4 Mechanical Dimension 31.4.1 PE-6004 31.4.2 PE-6004 With Heatsink 31.4.3 PE-6004 With Heatsink and Fan 4CHAPTER 2 GETTING TO KNOW YOUR PE-6000 52.1 Packing List 52.2 PE-6004 I/O and Indication 6 CHAPTER 3 GETTING START 10CHAPTER 4 DRIVER INSTALLATION AND SETTING 124.1 Driver Installation 124.2 Jumbo Frame 164.3 Link Aggregation 18APPENDIX A : PoE Guide 21 APPENDIX B : Software Functions 251GENERAL INTRODUCTION1.1 OverviewPE-6004 is a 4-ports 2.5GigE PCIe Expressx4 Expansion Card, supporting IEEE 802.3at PoE+ up to 25.5W power output at 48V DC per port. Powered by Intel® I225 LAN chipset, PE-6004 adopts 4-port Independent 2.5GigE Ethernet controller and it supports up to 2.5Gbps data rate each port with teaming functions, Fault Tolerance, IEEE 802.3ad Link Aggregation and Load Balancing, up to 9KB Jumbo Frame. Vecow PE-6004 is an ideal PCIe expansion card for industrial applications in Scientific Research, real-streaming video, AI Surveillance, real-time inspection, and Industry 4.0/IIoT applications.1.2 Features• Intel® I225 2.5GBASE-T Ethernet Controller supports 4-port independent2.5GigE LAN, up to 2.5Gbps data rate• PCI Express x4 interface, PCIe 3.0 supports up to 8 GT/s• Supports IEEE 802.3at Power over Ethernet (PoE+), up to 25.5W PowerOutput at 48V DC per port, with PoE+ On/Off Control• IEEE 802.3bz (2500BASE-T), IEEE 802.3ab (1000BASE-T), IEEE 802.3u(100BASE-TX), and IEEE 802.3i (10BASE-TX) compliant• Teaming features : Fault Tolerance, IEEE 802.3ad Link Aggregation and LoadBalancing, up to 9KB Jumbo Frame• Time Sensitive Network (TSN) features : IEEE 1588 Precision Time Protocol(PTP), IEEE 802.3AS Precision Timing Synchronization, IEEE 802.1Qav and802.1Qbv• Supports IEEE 802.3az Energy Efficient Ethernet (EEE) and DMA CoalescingPower Management features• Integrated Switching Voltage Regulator (iSVR) and IEEE 802.1q VLANsupported• -25°C to 60°C Operating Temperature1.3 Product Specification1.4 Mechanical Dimension1.4.1 PE-60041.4.2 PE-6004 With Heatsink1.4.3 PE-6004 With Heatsink and Fan2GETTING TO KNOW YOUR PE-60002.1 Packing List2.2 PE-6004 I/O and Indication2.2.1 PoE (Power over Ethernet) PortsPE-6004 is equipped with 4 IEEE 802.3at PoE + ports for transmitting power as much as 25.5W/48V per port and 1G/2.5G GBASE-T gigabit data signals over standard Ethernet CAT-5/CAT-6 cable.Each PoE connection is powered by Intel ® I225-LM 2.5GBASE-T Gigabit Ethernet.Controller and independent PCI express interface to connect with multi-core processor for networking and data transmit optimization. Only when PoE port starts to supply power to power devices, the dedicated LED will be lightened.The pin-outs of LAN 1 and LAN 4 are listed as follows :PoE Power LEDLAN 4LAN 3LAN 2LAN 1PoE Power LEDLAN 4LAN 3LAN 2LAN 1LAN 4LAN 3LAN 2LAN 12.2.2 Power InputThe PE-6004 is also equipped with one 4-pin power plug (12V, 6A max) for additional power supply. For most cases, the power obtained from PCIe bus is sufficient for the PoE devices, and you do not need to supply extra power to the card.In case the external power is needed, you can use 4-pin ATX power connector (+5V/Red, GND/Black, GND/Black, +12V/Yellow) inside the host computer. Please always confirm the polarity before you plug into the onboard 4-pin power plug.CN1 :CN 1Each LAN port is supported by standard RJ-45 connector with LED indicators to present Active/Link/Speed status of the connection.The LED indicator on the left bottom corner lightens in OFF when the cable is properly connected to a 10M/100Mbps Ethernet network; The LED indicator on the left bottom corner lightens in solid green when the cable is properly connected to a 1000Mbps Ethernet network; The LED indicator on the left bottom corner lightens in solid orange when the cable is properly connected to a 2.5Gbps Ethernet network The right LED will keep twinkling/off when Ethernetdata packets are being transmitted/received.2.2.3 PoE Power On/OffJAD1 - JAD4PE-6004 controls PD69104B PoE Power ON/OFF via SMBUS. Jumper JAD1~ JAD14 address setting as below (1-2=H , 2-3=L) :2.2.4 Fan ConnectorFAN1Fan power connector supports for additional thermal requirements. The pinassignments of FAN1 is listed in the following diagram :Pin input :GETTING START3Step 1. Insert PE-6000 golden finger and PCI bracket into PCIe socket carefully.Step 2.Make sure golden finger and PCI bracket are inserted smoothly.Step 3. Make sure the bracket aligns screw hole.Step 4. Fasten the M3 or #6-32 screw.4DRIVER INSTALLATION AND SETTING4.1 Driver InstallationThis section describes :How to install drivers for PE-6004 PoE Card.System OS :Windows 10-64bitStep 1. Execute "Intel PROWin64.exe (25.1 Later version)" and then go "Next"step.Step 2. Select "Modify" and then go to "Next" step.Step 3. Select "Next" step.Step 4. Click the "Install" icon to begin the installation.Step 5. Install wizard completed.Step 6. Select "Finish" step.Once you need this network driver, you could remove this program on Control panel directly.4.2 Jumbo FrameAfter installing the driver for Intel® I225-LM controller, you can get the enhance function that called jumbo frame, please find more instruction as below.Step 1. "Right-click → Device Manager → Network adapters".Step 2. Select anyone "Intel Ethernet Converged Network Adapter I225-LM #xx", right Click and select "Properties", a property dialog appears and Clickon the Advanced page.Step 3. Select the "Jumbo Packet", settings, and select the expected jumbo frame size.4.3 Link AggregationStep 1. Here shows another enhance network function "Teaming".Step 2. You could multi-select network device to get a high performance net.APPENDIX A : PoE GuideA.1 Function DescriptionThe PE-6004 series offers a 4-port PoE +.ALAN 4PoE Power LEDLAN 3LAN 2LAN 1LAN 4LAN 3LAN 2LAN 1Do NOT use these functions in below :1. ECS-4000 : DIO1 (ID = 2), POE (ID = 0)2. ECS-4500, ECS-9000, ECS-9200, ECS-9700, IVH-7700, IVH-9000,IVH-9200 : POE (ID = 0)3. RCS-7000 : GPIO (ID = 0)4. PE-2000 : DIO1 (ID is the same, ID = 0 ~ 7), POE (ID = 0)5. UE-1000 : USB (IDUE-1000 = IDPE-3000 >> 1 & 3 | IDPE-3000 << 2 & 4) PoE ON/OFF vs Slave address setting as below :PE-6004 controls PD69104B PoE Power ON/OFF via SMBUS. Jumper JAD1~ JAD14 address setting as below (1-2=H , 2-3=L) :A.3 SampleSample folder include x32 and x64 versions, as shown below :Sample PE5K.exe, as shown below :A.2 Software Package ContainDistribution folder include x32 and x64 versions, use batch file for installation.There are included as followed :Win7_32.bat :Installation for 32-bit driver Win7_64.bat :Windows update package which driver required (need to restart), and Installation for 64-bit driver Win8_32.bat, Win8_64.bat :Installation for driver, and guideline to Framework 3.5 distribution for sampleWin10_32.bat, and Win10_64.bat :Installation for driver, and installation to Framework 3.5 distribution for sampleUninstall_32.bat, and Uninstall_64.bat :Uninstallation for driver Run batch file as Administrator.Support Windows 7 above.Make sure it is Windows version before installation.Runtime folder includes head file for software developer or System Integration.Sample folder includes sample program, driver library, and API library. Sourcefolder includes sample program source code that compile on Visual Studio 2008.POE group :Read button :Set POE configuration to get POE state.Write button :Set POE configuration to set POE state.POE output text :User setting, POE output state by hexadecimal bitmask - on/off.Use for Write button activate.POE writable text :User setting, POE writable of POE configuration by hexadecimal bitmask - yes/no.Use for Write button activate.POE mode text :User setting, POE mode of POE configuration by hexadecimal bitmask - Auto/Manual.Use for Write button activate.POE input text (read only) :POE input state by hexadecimal bitmask - on/off.Use for Read button activate.POE text (read only) :POE output state with input state and configuration.Use for Write button activate.POE output text (read only) :POE output state with configuration.Use for Write button activate.POE input port texts (read only, port 4 ~ port 1) :POE input port stateUse for Read button activate.POE output port check button(port 4 ~ port 1) :User setting, POE output port stateUse for Write button activate.POE port writable check button(port 4 ~ port 1) :User setting, POE port writable of POE configuration.Use for Write button activate.POE port mode check button(port 4 ~ port 1) :User setting, POE port mode of POE configuration.Use for Write button activate.BAPPENDIX B : Software FunctionsB.1 Driver API GuideIn Runtime folder, on PE6K.h :_DLL_IMPORT_ definition is used on LoadLibrary API for PE5K.dll. PE6K_EXPORTS definition is used on PE5K.dll building.BOOL Initial(BYTE Scan, BYTE ID)Initial card for POEScan : POE ID scan type2 : Auto scan; 1 : Manual setup; 0 : Not detect ID ([3:0]) : POE ID bymanual settingReturn :TRUE (1): Success;FALSE (0): Fail (Driver not exists, or out of range error, or initial error (versionis too old, or card not match))BOOL GetPOEConfig(BYTE ID, BYTE *Auto, BYTE *Mask)Get POE configuration (by variable) ID ([3:0]) : POE IDAuto ([3:0]) : Auto mode, pin setting by hexadecimal bitmask1 : Auto;0 : ManualMask ([3:0]): DC Enable/Disable, pin setting by hexadecimal bitmask1 : Enable;0 : DisableReturn :TRUE (1) : Success;FALSE (0) : Fail (Initial error, or call by pointer error, or hardware problem) BOOL SetPOEConfig(BYTE ID, BYTE Auto, BYTE Mask)Set POE configuration ID ([3:0]) : POE IDAuto ([3:0]): Auto mode, pin setting by hexadecimal bitmask1 : Auto;0 : ManualMask ([3:0]): DC Enable/Disable, pin setting by hexadecimal bitmask1 : Enable;0 : DisableReturn :TRUE (1) : Success;FALSE (0) : Fail (Initial error, or out of range error, or hardware problem)BOOL GetPOE(BYTE ID, BYTE *POE)Get POE inputID ([3:0]) : POE IDPOE ([3:0]) : POE state, pin setting by hexadecimal bitmask1 : On;0 : OffReturn :TRUE (1) : Success;FALSE (0) : Fail (Initial error, or call by pointer error, or hardware problem)BOOL SetPOE(BYTE ID, BYTE POE)Set POE outputID ([3:0]) : POE IDPOE ([3:0]) : POE state, pin setting by hexadecimal bitmask1 : On;0 : OffReturn :TRUE (1) : Success;FALSE (0) : Fail (Initial error, or out of range error, or hardware problem)26©Vecow PE-6000 User Manual Appendix BFor further support information, please visit This document is released for reference purpose only.All product offerings and specifications are subject to change without prior notice.No part of this publication may be reproduced in any form or by any means, electric, photocopying, or recording, without prior authorization from the publisher.The rights of all the brand names, product names, and trademarks belong to their respective owners.© Vecow Co., Ltd. 2020. All rights reserved.。
东莞科尼盛电子有限公司铝电解电容商品说明书
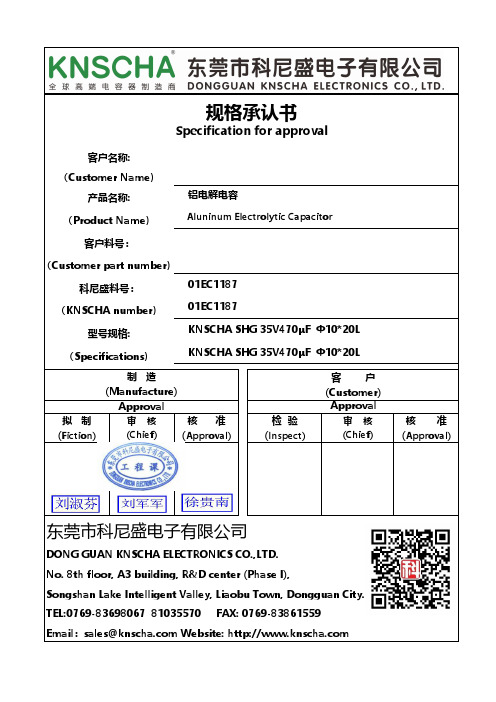
规格承认书Specification for approval 客户名称:(Customer Name)产品名称: 铝电解电容(Product Name) Aluninum Electrolytic Capacitor 客户料号:(Customer part number)科尼盛料号: 01EC1187(KNSCHA number) 01EC1187型号规格: KNSCHA SHG 35V470μF Φ10*20L (Specifications) KNSCHA SHG 35V470μF Φ10*20L制 造(Manufacture)客 户(Customer)Approval Approval拟 制(Fiction)审 核(Chief)核 准(Approval)检 验(Inspect)审 核(Chief)核 准(Approval)东莞市科尼盛电子有限公司DONG GUAN KNSCHA ELECTRONICS CO.,LTD.No. 8th floor, A3 building, R&D center (Phase I),Songshan Lake Intelligent Valley, Liaobu Town, Dongguan City. TEL:0769-8369806781035570FAX************** Email:***********************:SHG SeriesAluminum Electrolytic Capacitors1.Operating Temp. Range2.Electrical CharacteristicsSee Table 1.3.DimensionsФd=0.05 Tinned copper-ply wireSafety Ventφ6.3 or overФD+αmax4.MarkingFollowing items are printed with white color on coffee color sleeve①Rated voltage & Nominal Capacitance ②Polarity (negative) 35V ③Trade Mark 470μF ④series⑤Symbol of Capacitance Tolerance (M)⑥Max Operating Temp.KNSCHA SHG (M )105℃5.MULTIPLIER FOR RIPPLE CURRENT ①.②.No,KNS-200305001(1/5)Example of Marking①②③④⑤⑥F±0.5SleeveL+βmax.15min.4min.φD+0.5φdRubber Bung6.CharacteristicsNo,KNS-200305001(2/5)6-2.Characteristics7Packing methodPackaging shape, size, quantity8Related Standards JIS C 51419Marking on packing box① Item name② Series name ③ Rated Voltage④ Nominal Static Capacitance ⑤ Case size ⑥ Lot No.⑦ QuantityNo,KNS-200305001(3/5)LHW10Leakagecurrent<Condition>Connecting the capacitor with a protective resistor (1kΩ±10Ω) in series for2 minutes, and then, measure leakage current.<CriteriaI : Leakage current (μA)I (μA)≤0.01CVor 3 (μA) whichever is greater,measurement circuit refer to right drawing.C: Capacitance (μF)11Soldeing11-1Soldering by soldering ironTemperature of iron top : 270~350℃ Operating time : within 3 sec.11-2Flow soldering.Preheat : PCB surface temperature 120℃±5℃Solder Temp : 260℃±5℃ Solder Dipping Temp. : 2~4sec.12Cleaning of PC boad after solderingUsing follwing solvents is possible but make sure followingconditionSolventIPA or Alcoholic agent like Pinealpha ST-100S, Cleanthrough 750H, 750L, 710M, 750K,or Technocare FRW-14~17① Cleaning should be made by ultrasonic within 5min, at the temperature less then 60℃.② Control of pollution is necessary (conductivity,pH, specific gravity, water volume)③ Please do not keep near cleaning agent. Please do not store in air-tight container.Please let it dry by hot air at the temperature less than maximum operating temp.13The situation of usingPlease do not use a condenser in the next use environment.① One circumference environment(weatherability) condition.(a) Direct water,salt water and environment oil works or become a dew condensation state.(b) Environment full of harmful gas (a hydrogen chloride, sulfurous acid.nitrous acid hydrochloric acid, ammonia).(c) Ozone, infrared rays and the environment where radioactive rays are done collation of② Vibration shock condition is extreme environment more than rule ranges of deliveryspecifications.14 A country of originA country of origin of an KNSCHA SHG series alminum electrolysis condenser of specifications:China15Effective life for storageStorage conditions:① Temperature range must be between 5-35℃② Relative humidity must be less than 75%③ Must be stored indoor④ Must be free from water, oil or salt water⑤ Must be free from toxic gasses (hydrogen sulfide, sulfurous acid, chlorine, ammonium, etc.)⑥ Must be free from ozone, ultraviolet rays or any other radiation⑦ Must be kept in capacitor original packageNo,KNS-200305001(4/5)Aluminum Electrolytic CapacitorSHG Series StructureControls of ozone layer destructive chemical materialsRegulated materials : CFCs, Halon, Carbon Tetrachloride, 1.1.1-TrichloroethaneThe products and parts do not include the above materialsThe products and parts are not used the above materials on process.The products and parts are not used PBBOs (Poly Bromo Bi-phenyl Oxides ).All materials are mentioned as existing chemical material in the "Law of examineand control of Production of Chemical Material"The products are not listed in Appendix 1 of Export Trade Rule and RegulationA condenser of this series supports RoHS regulation.No,KNS-200305001(5/5)。
Keysight Technologies Scienlab Charging Discovery
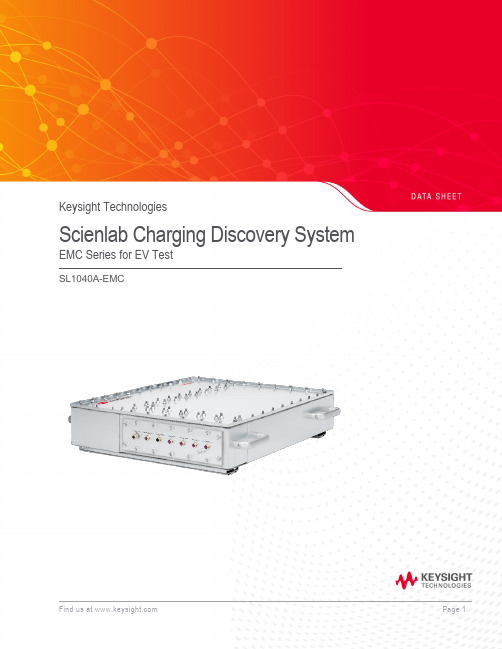
Keysight TechnologiesScienlab Charging Discovery SystemEMC Series for EV TestSL1040A-EMCFind us at Page 1Table of ContentsIntroduction (3)SL1040A-EMC Charging Discovery System EMC Series for EV Test (4)SL1040A-301 Communication Module PLC (11)SL1040A-302 Communication Module GB/T (12)SL1040A-303 Communication Module CHAdeMO (12)EV charging adapters (EMC conform) (13)SL1040A-601 EV charging adapter AC Type 1 (13)SL1040A-602 EV charging adapter AC Type 2 (13)SL1040A-605 EV charging adapter GB/T AC (13)SL1040A-603 EV charging adapter CCS Type 1 (13)SL1040A-604 EV charging adapter CCS Type 2 (13)SL1040A-606 EV charging adapter GB/T DC (13)SL1040A-607 EV charging adapter CHAdeMO (13)Service Options (15)Project Management and Technical Consulting Service (15)Installation Service (15)Commissioning Test (16)Productivity Assistance (16)IntroductionThis data sheet describes the EMC optimized Charging Discovery System (CDS) for EV testing.The EMC Series for EV Test is intended for use inside an anechoic chamber for immunity and emission tests (conducted or radiated) of electric vehicles, during AC or DC charging.Due to the special EMC shielded design and built-in low-noise components, the emission of the CDS is reduced to a minimum level. This enables EMC testing of EVs under real charging conditions without undesired test environment interference. Furthermore, the EMC series of the CDS is immune to external electro-magnetic fields and can be placed close to the specimen during immunity tests (see section “EMC performance”).For EVSE test, see separate data sheet “Scienlab Charging Discovery System - EMC series for EVSE test”.The EMC variant is fully software compatible with the portable CDS. However, Keysight designed it for reliable charging emulation, without extended fault injection, required for conformance testing.Figure 1: Exemplary architecture of test environment EV testNote: This data sheet describes the essential product and its system options. If you need a full solution, contact your local Keysight Sales and Service office for a statement of work proposal including required periphery, installation, and other services.SL1040A-EMC Charging Discovery System EMC Series for EV TestKeysight designed the shielded CDS variant to be used for EMC compliance and homologation tests. This item is the main module which can be extended by optional communication modules (see SL1040A-301, SL1040A-302, SL1040A-303).Figure 2 below shows a three-dimensional view of the shielded housing. During operation the housing is permanently closed with a lid.Figure 2: 3D drawing of EMC optimized Charging Discovery SystemGeneral Functions•Reliable, interoperable emulation of the EVSE charging communication controller (SECC);verified by thousands of successful charging sessions with almost all available EV brands &models.•Easy configuration of charging protocol and operating point through Windows control software Charging Discover (see also corresponding data sheet) or optionally via customer automationsoftware (using the CDS remote interface)•Integrated PWM emulation for Control Pilot circuit of the EVSE signal generator with adjustable positive/negative amplitude, frequency and duty cycle•Integrated emulation of the Proximity Pilot circuit•Real-time capable control PC with high system performance and low dead times. Note: IPC is placed typically outside of the EMC chamber (see section “Real-time PC”)•Portable shielded “galvanized metal” case with grounding contact springs•Isolated interface to Real-time PC via Optical Data Converter (see section “Optical Data Converter”)•Direct support of Scienlab/Keysight power sources and sinksStandards and directivesCDS supports the following charging communication standards:The basic functions include:•AC charging mode according to IEC 61851-1 (PWM)•AC charging mode according to SAE J1772 (PWM)•AC charging mode according to GB/T 18487 (PWM)The following are available when ordering communication modules:•DC fast charging mode according to DIN SPEC 70121 & ISO 15118•AC charging mode according to ISO 15118•DC fast charging mode according to GB/T 27930•DC fast charging mode according to CHAdeMOEMC performance•EMC optimized case for emission and immunity testing•Immunity of CDS rated up to 200 V/m (30 Mhz to 1 Ghz)Figures 3, 4, and 5 show sample EMC measurement results to illustrate the CDS emission performance:Figure 3: Results of conducted emission test between 100 kHz and 30 MHz, with active PLC modemFigure 4: Results of conducted emission test between 30 and 108 MHz, with active PLC modemFigure 5: Results of radiated emission test between 30 MHz and 1 GHz, vertical polarizationInterfacesFigure 6 shows the schematic layout of the EMC optimized communication module and its interfaces:B CADCFigure 6: EMC optimized communication module (exemplary for DC charging)A. Connection from power source to Connection panel:•DC+ and DC- from “Dynamic DC Emulator” (located outside of the EMC chamber) through EMC.Often DC+ and DC- wires are installed underneath the EMC chamber. At Connection panel the cables are connected with LISN (Line Impedance Stabilization Networks) via HV plugs.B. Connection from Connection panel to LISN:•Unipolar DC+ and DC- connection between Lab specific connection panel and LISN (Line Impedance Stabilization Networks) terminals. Note: Cables and connectors are not included with this item.C. Connection from CDS/LISN to EV charging adapter:•DC+ and DC-: standard DC-cables from EV charging adapter•Communication (CP, PP, CAN): via shielded bus system cables by Phoenix ContactD. Connection to electric vehicle:•Via EV charging adapterTechnical Data EMC HousingInterface to operator PC 2x ST-ST gigabit duplex optical fiber cable 50/125 µmMeasurementsReal-time PCThe real-time PC is responsible for the test- and application execution and is normally placed in the control room near the EMC chamber. The technical specifications are shown in the table below:Optical Data ConverterThe Optical Data Converter connects the EMC CDS with the real-time PC. It converts the light wave signals coming from the CDS into digital signals, which are then forwarded to the operator PC via an Ethernet interface.Note: Optical fiber cables are not in the scope of delivery. For connection of the Optical Data Converter with the CDS a separate feedthrough is necessary (through chamber wall). Feedthrough and work for installation are also not in the scope of delivery of this item.Documentation•Operating manual•CE conformity declarationA PLC module supports the following additional functions:•EVSE emulation according to the standards DIN SPEC 70121 (2014) and ISO 15118 (EIM only, Plug & Charge (PnC) will be available as software update in the future)•Recording of all V2G messages and display of the information contained therein in plain text •Manipulation of V2G messages and active delaying of timings (fault insertion)•Testing of the PLC communication for adherence to the PLC level, the standardized frequency bands, the carrier frequencies, and the signal quality/strength•Testing of the EV charging interface for compliance with the standardPin Designation Function Charging interfaceCP Control Pilot PWM controlline plus digitalcommunicationvia PLCPP Proximity Pilot EV testing of thecharging cableconnectionNote: This option does not include electromechanical contacting (plug/inlet).A communication module supports the following additional functions:•EVSE emulation according to GB/T 27930-2011 and -2015 (DC)•Recording of all EV CAN messages and display of the information contained therein in plain text Pin Designation Function Charging InterfaceS+ CAN-High CAN Bus: High levelcommunicationS- CAN-LowCC1 Connection Check 1 EV testing of the charging cable connectionCC2 Connection Check 2 EVSE testing of the charging cable connectionA+ Auxiliary Circuit + EVSE voltage supply* for EVCCA- Auxiliary Circuit - EVSE voltage supply* for EVCCNote: This option does not include electromechanical contacting (plug/inlet).SL1040A-303 Communication Module CHAdeMOA communication module supports the following additional functions:•EVSE emulation according to the CHAdeMO standard (protocol versions: 0.9; 0.9.1; 1.0.0; 1.0.1;1.1; 1.2 and2.0)•Recording of all EV CAN messages and display of the information contained therein in plain text Pin Designation Function Charging interface8 CAN-High CAN Bus: High levelcommunication9 CAN-Low7 Connector proximitydetection (CPD)EV testing of the chargingcable connection4 Vehicle chargepermission (VCP)EV opening for chargingprocess2 Charging sequencesignal 1 (CSS 1)EVSE “start” charging10 Charging sequencesignal 2 (CSS 2)EVSE releasing the chargingprocessNote: This option does not include electromechanical contacting (plug/inlet).EV charging adapters (EMC conform)Adapter for AC chargingAdapter for DC charging* Limited by EV plug manufacturer's certification** All charging adapters have a standard length of 5 m. Other lengths available on request.On the secondary side, all EV charging adapters are equipped with ring cable lugs on the unshielded power wires. The communication wires are equipped with shielded “bus system cables” by Phoenix Contact. The communication wires are equipped with compatible plugs for connection to the CDS separately, as shown in the following exemplary image:DC –DC +Charging communicationFigure 7: Example of DC EV charging adapterService OptionsService demand depends on the chosen hardware configuration, the installation location and its facilities, and especially the scope of testing. For that reason, it is difficult to estimate the exact amount of service required, prior to identifying all relevant requirements of the customer. The following times are estimates for a standard setup. Keysight offers a wide spectrum of services to guarantee a successful project and reduce the ramp-up time for our customers.Project Management and Technical Consulting ServiceProject Management and Consulting Service is mandatory for every project including a construction, integration or customization part. However, Keysight recommends additional service in every Charging Discovery System project, in particular on the first order. By ordering the project management service, an experienced project manager or system specialist is dedicated to your project and acts as direct communication interface from Keysight to the customer’s project team.The project manager takes over the following responsibilities:•Consult the customer with in-depth technical knowledge about the test solution, its application and relevant test standards.•Learn about the customer’s objectives and give guidance how to use the ordered solution best in order to gain maximum benefits.•Evaluation of post-order requirements and change management.•Coordinating and tracking project progress from day one until system handover.•To provide complete and accurate project documentation to the customer.Installation ServiceThe scope of the installation service strongly depends on the customer facility. Keysight can provide full installation options for all products. To get a quote, provide all relevant information and requirements regarding test bench components that require media installation such as grid interface and cooling water supply with your local field engineer.Note: Installation can also be executed by the customer.Commissioning TestThe Commissioning Test guides the customer during first usage of the test bench after installation. Commissioning Test Service is recommended for each test bench project. It includes:•Support in commissioning the test system and instructions on how to use it.•Local presence of experienced test bench engineer during first usage of the test bench.•Consulting of customer personnel with regards to intended usage of the test bench (e.g.initial test with customer specimen, evaluation of test results)•Inspection of hardware/laboratory installation•Initial installation and configuration to the control software Charging Discover as well as hand-on instructions how to use it.•Travel expensesNote: Commissioning Test Service is offered on a daily basis. Keysight recommends at least two days of Commissioning Test Service for each test system.Productivity AssistanceThe Productivity Assistance is offered to support, consult and train the customers operation personnel to reduce ramp-up time during the initial usage of a new test system and any unexpected system behavior during the test bench life cycle. Productivity Assistance is carried out remotely (phone or internet) or on site (on request). It includes:•Direct access to an experienced system specialist via phone/internet.•Trouble-shooting support•Software and programming support & consulting (e.g. how to use, modify or create conformance/interoperability test cases)Note: Keysight recommends at least three days of Productivity Assistance for each test bench project.Learn more at: For more information on Keysight Technologies’ products, applications or services,please contact your local Keysight office. The complete list is available at:/find/contactus。
宏欧威测试仪 macroevtest说明书

More than safe, sure.N E WT ester for checks on electriccar recharging stations andverification of domestic andindustrial electric systemsMor e than safe,sure.MACRO EV TESTMA CROEVTEST , HT's new product for verification and checks on recharging stations for electric cars (EVSE) in compliance with standards IEC/EN 61851-1 and IEC/EN60364-7-722, and for safety tests in private and industrial environmentsRecharging stations: a new way to use electric energy .BUILT-IN CABLETOUCH SCREEN SYSTEMTYPE 2* PLUG * other plugs available on demandWIFICONNECTIONCHECKS ON RECHARGING ST A TIONS FOR ELECTRIC CARSConnection is simple.MacroEVtest is connected through the provided C100EV cable to EV-Test100, which is connected, through an in-built cable provided with type2 plug, to a recharging station.SIMPLIFIESEV-Test100 can simulate the presence of a car beingrecharged and, at the same time, dialogues with MacroEVtest thanks to the new display with touch screen system , peculiar to HT's latest generation devices.SIMULATESTo correctly perform all tests, all you need to do is following the GUIDED PROCEDURE created by HT for this innovative instrument.GUIDESBefore each test, MacroEVtest indicates how the cables must precisely be connected and, at the end of measurement, further to the detected values, it provides evaluations of the tests' outcomes , if compatible or not for the recharging station's safety , indicated by a green or red thumb symbol.CONNECTS› CONTINUITY test of the recharging station's protection conductor › INSULATION test of the recharging station› Verification of the STATUSES of the recharging station › Measurement of OVERALL EARTH RESISTANCE› Verification of the RCD's tripping (test of RCDs type A, B and type B 6ma)› Vehicle not present› Vehicle present but not being charged › Vehicle present and being charged› Events and anomalies which can be detected during the recharging phase › Simulation of a fault on the protection conductor› Indication of the presence of voltages on the EVSE output connector through LED› Verification of the mechanical lock in the connection to the station: it is possible to check that the station, during the recharging phase, blocks the cable release (if the station is provided with this function)TESTSSTANDARDSVERIFICA TION TESTS ANDSIMULA TIONSSAFETY CHECKS ON PRIV A TE AND INDUSTRIAL SYSTEMSThe TFT colour display with touch-screen allows for a new and more versatile use of the instrument.MacroEVtest offers on its display all possible alternatives for the performance of a perfect measurement.The new system adopted by HT allows optimally preparing the instrument, before performing a test, by suggesting the most suitable connections to certify correct and reliable tests .The AUTO function, in the system menu, allows performing the tests very quickly .At the end of each test, further to the measured value,MacroEVtest provides an evaluation of the result , indicating whether it complies or not with standards.All tests can be saved and, in order to create a printablereport , data can be transferred via WiFi to a PC , smart phone or tablet .MEASURESPREPARESVALIDATESIEC/EN 60364STANDARDSTESTS› T est of RCDs type A, type AC also up to 1000 mA and type B. By using the accessory RCDX10, provided with the instrument, it is also possible to test RCDs with external jaws up to 10 A.› Insulation tests up to 1000V › Continuity tests› T ests of overall earth resistance and voltammetric resistance (further than with the provided rods, this latter test can also be performed by means of the optional clamp T2100).› With the appropriate programming guided by the touch-screen system, this device can test theinterruption power, tripping currents, I2t relevant to magneto-thermal switches (MCB) with curves B, C, D, K and fuses type gG and aM› Loop/Line impedance measurements and calculation of the assumed short-circuit current with high resolution (0.1mOhm) in TN systems with the use of the optional accessory IMP57HT ITALIA S.R.L.Via della Boaria, 40 48018 Faenza (RA) ItalyM AD EIT AL YINAccuracy is indicated as ± (% readings + no. of digits*resolution) at 23°C ± 5°C, <80%RHTest current: > 200mA DC for R≤5Ω (calibration included) ; Resolution for DC current :1mA Open-circuit voltage: 4V ≤ V0≤ 12VShort circuit current: <6.0mA at 500V test voltageNominal test current: >1mA if load= 1kΩ*Vnom (Vnom=50V, 100V, 250V, 500V, 1000V)Safety protection: the display shows an error message for input voltage >10VMaximum test current: 5.81A (at 265V); 10.10A (at 457V)Test voltage ranges: 100÷265V (Line-Neutral) / 100÷460V (Line-Line); 50/60Hz ± 5%Protection type: MCB (B, C, D, K), Fuse (gG, aM)RCD type:AC (), A (), B() – General (G), Selective (S) and Delayed () Rated tripping currents (I ∆N):: 6mA, 10mA, 30mA, 100mA, 300mA, 500mA, 650mA, 1000mA Line-PE, Line-N voltage: 100V ÷265V RCD type AC and A, 190V ÷265V RCD type B Frequency:50/60Hz ± 5%RCD Molded type tripping time range [ms] (TT/TN system)x 1/2 x 1 x 2 x 5 AUTOAUTO+\G S G S G SGS GS G SGS6mAAC 999 999 999 999 999 999 160 210 50 150 ✓ ✓ 310 ✓ A 999 999 999 999 999 999 160 210 50 150 ✓ ✓ 310 ✓ B 999 999 999 999 999 999 310 10mAAC 999 999 999 999 999 999 160 210 50 150 ✓ ✓ 310 ✓ A 999 999 999 999 999 999 160 210 50 150 ✓ ✓ 310 ✓ B 999 999 999 999 999 999 310 30mAAC 999 999 999 999 999 999 160 210 50 150 ✓ ✓ 310 ✓ A 999 999 999 999 999 999 160 210 50 150 ✓ ✓ 310 ✓ B 999 999 999 999 999 999 310 100mAAC 999 999 999 999 999 999 160 210 50 150 ✓ ✓ 310 A 999 999 999 999 999 999 160 210 50 150 ✓ ✓ 310 B 999 999 999 999 999 999 310 300mA AC 999 999 999 999 999 999 160 210 50 150 ✓ ✓ 310 A 999 999 999 999 999 999 160 210 50 150 ✓ ✓ 310 B 999 999 999 999 999 999 310 500mA 650mAAC 999 999 999 999 999 999 160 210 50 150 ✓ ✓ 310 A 999 999 999 999 999 999 160 210 310 B1000mAAC 999 999 999 999 999 999 160 210A 999 999 999 999 999 999 BResolution: 1ms, Accuracy: ±(2.0%rdg + 2dgt)RCD Molded type tripping time range [ms] (IT system)x 1/2 x 1 x 2x 5AUTOAUTO+ \GSG S GS G S G S G S G S6mA10mA 30mA AC 999 999 999 999 999 999 160 210 50 150✓ ✓ 310 ✓ A B 100mA 300mA 500mA 650mA AC 999 999 999 999 999 999 160 21050 150 ✓ ✓ 310 AB1000mA AC 999 999 999 999 999 999 160 210ABResolution: 1ms, Accuracy: ±(2.0%rdg + 2dgt)RCD type:AC (), A (), B() – General (G), Selective (S) and Delayed () Rated tripping currents (I ∆N):: 0.3A ÷ 10ALine-PE, Line-N voltage: 100V ÷265V RCD type AC and A, 190V ÷265V RCD type BEarth leakage delay tester RCDs trip out time range [ms] (TT/TN system)x 1/2 x 1 x 2 x 5 AUTO\G S G S GS GSG SG S0.3A ÷ 1.0A AC 999 999 999 999 999 999 200 250 50 150 ✓ ✓ 310 A 999 999 999 999 999 999 200 250 50 150 ✓ ✓ 310 B 999 999 999 999 999 999 310 1.1A ÷ 3.0A AC 999 999 999 999 999 999 200 250 50 150 ✓ ✓ 310 A 999 999 999 999 999 999 200 250 50 150 ✓ ✓ 310 B 999 999 999 999 999 999 3.1A ÷ 6.5A AC 999 999 999 999 999 999 200 250 50 150 ✓ ✓ 310 A 999 999 999 999 999 999 200 250 50 150 ✓ ✓ 310 B 9999999999999999996.6A ÷ 10.0AAC 999 999 999 999 999 999 200 250 A 999 999 999 999 999 999 BResolution: 1ms, Accuracy: ±(2.0%rdg + 2dgt)Earth leakage delay tester RCDs trip out time range [ms] (IT system)x 1/2x 1 x 2x 5 AUTO\ G SG SG S G S G SG S 0.3A ÷ 3.0A AC 999 999 999 999 999 999 200 250 50 150 ✓ ✓310 A B 3.1A ÷ 6.5A AC 999 999 999 999 999 999 200 250 50 150 ✓ ✓ 310 A B 6.6A ÷ 10.0AAC 999 999 999 999 999 999 200 250 A BResolution: 1ms, Accuracy: ±(2.0%rdg + 2dgt)NoTripTest – Non-trip earth loop impedanceN N N N N N N N N N(*) Add 5% to the accuracy if the probe resistances (Rs or Rh) > 100 x RmeasTest current: <10mA – 77.5Hz, Open-circuit voltage: < 20VrmsAllowed crest factor ≤ 3; Frequency: 42.5 ÷ 69.0 HzDISPLAY AND MEMORY:Features: Touch screen, color graphic LCD, 320x240mm Memory: 999 locations, 3 marker levelsCommunication: Optical-USB and built-in WiFiPOWER SUPPLY:Batteries: 6 x 1.2V(rechargeable) type AA or 6 x 1.5V type AA Battery life: > 500 test for each funtionsAuto Power OFF: after 5 min of idleness (disabled)MECHANICAL FEATURES:Dimensions (L x W x H): 225 x 165 x 75mmWeight (included batteries): 1.2kgWORKING ENVIRONMENTAL CONDITIONS:Reference temperature: 23°C ± 5°CWorking temperature: 0°C ÷ 40°CAllowed relative humidity: <80%RHStorage temperature: -10°C ÷ 60°CStorage humidity: <80%RHTEST VERIFIES REFERENCE STANDARDS:Continuity test with 200mA: IEC/EN61557-4Insulation resistance: IEC/EN61557-2Earth resistance: IEC/EN61557-5Fault loop impedance: IEC/EN61557-3RCD test: IEC/EN61557-6Phase sequence: IEC/EN61557-7Multifunction: IEC/EN61557-10Prospective short circuit current: EN60909-0Earth resistance on TN systems: EN61936-1 + EN50522Test on EVSE devices: IEC/EN61851-1, IEC/EN60364-7-722 (with EV-TEST100) GENERAL REFERENCE STANDARDS:Safety of measuring instruments: IEC/EN61010-1, IEC/EN61010-031, IEC/EN61010-2-032 Product type standard: IEC/EN61557-1Technical documentation : IEC/EN61187Insulation: double insulationPollution degree: 2Encapsulation : IP40Overvoltage category: CAT IV 300V~ (to ground), max 415V between inputs Max height of use: 2000m。
CLF1G0060-30和CLF1G0060S-30高频电子部件说明书

CLF1G0060-30; CLF1G0060S-30Broadband RF power GaN HEMTRev. 7 — 5 February 2018Product data sheet 1. Product profile1.1General descriptionThe CLF1G0060-30 and CLF1G0060S-30 are 30W general purpose broadband GaNHEMTs usable from DC to6.0GHz.Table 1.CW and pulsed RF application informationTypical RF performance at T case = 25 ︒C; I Dq=70mA; V DS=50V in a class-AB broadband demoboard.Test signal f P L G pηD(MHz)(W)(dB)(%)1-Tone CW5003015.660.710003013.950.315003013.750.820003012.64925003014.255.61-Tone pulsed [1]5003016.66110003015.85015003015.552.520003014.55025003015.959[1]Pulsed RF; t p=100μs; δ=10%.Table 2.2-Tone CW application informationTypical 2-Tone performance at T case = 25 ︒C; I Dq=150mA; V DS=50V in a class-AB broadbanddemo board.Test signal f P L(PEP)IMD3(MHz)(W)(dBc)2-Tone CW [1]50010-38100010-50150010-45200010-50250010-43[1]2-Tone CW; ∆f=1MHz.1.2Features and benefits⏹Frequency of operation is from DC to 6.0 GHz⏹30 W general purpose broadband RF Power GaN HEMT ⏹Excellent ruggedness (VSWR =10:1)⏹High voltage operation (50 V)⏹Thermally enhanced package1.3Applications2. Pinning information[1]Connected to flange.3. Ordering information⏹Commercial wireless infrastructure(cellular, WiMAX)⏹Industrial, scientific, medical ⏹Radar⏹Jammers ⏹Broadband general purpose amplifier ⏹EMC testing⏹Public mobile radios⏹Defense applicationTable 3.PinningTable 4.Ordering informationType number Package NameDescriptionVersion CLF1G0060-30-flanged ceramic package; 2mounting holes; 2 leads SOT1227ACLF1G0060S-30-earless flanged ceramic package; 2 leadsSOT1227B4. Limiting values5. Thermal characteristics[1]T j is measured via IR scan with case temperature of 85 ︒C and power dissipation of 34W.6. CharacteristicsTable 5.Limiting valuesIn accordance with the Absolute Maximum Rating System (IEC 60134).Symbol ParameterConditionsMin Max Unit V DS drain-source voltage -150V V GS gate-source voltage -8+3V I GF forward gate current external R G = 5 Ω-11mA T stg storage temperature -65+150︒C T jjunction temperaturemeasured via IR scan -250︒CTable 6.Thermal characteristics Symbol ParameterConditions Typ Unit R th(j-c)thermal resistance from junction to caseT j = 200 ︒C[1]3.1K/WTable 7.DC CharacteristicsT case = 25 ︒C; unless otherwise specified.Symbol ParameterConditionsMin Typ Max Unit V (BR)DSS drain-source breakdown voltage V GS =-7 V;I DS =7.2mA 150--V V GS(th)gate-source threshold voltage V DS =0.1 V; I DS =7.2mA-2.4-2-1.6V I DSX drain cut-off current V DS =10V; V GS =3 V - 5.1-A g fsforward transconductanceV DS =10 V; V GS =0V- 1.1-STable 8.RF CharacteristicsTest signal: pulsed RF; f = 3GHz; t p =100μs; δ =10%; RF performance at V DS =50V; I Dq =70mA; T case =25 ︒C; unless otherwise specified in a class-AB production circuit.Symbol Parameter Conditions Min Typ Max Unit ηD drain efficiency P L =30 W 4654-%G p power gain P L =30 W 11.813.5-dB RL in input return loss P L =30 W --7-dB P droop(pulse)pulse droop powerP L =30 W -0.04-dB t r rise time P L =30 W -5-ns t ffall timeP L =30 W-5-ns7. Application information7.1Demo circuitTable 9.List of componentsSee Figure1.Component Description Value RemarksA1GaN bias module v2-AmpleonC1, C10multilayer ceramic chip capacitor8.2 pF ATC 600FC2, C7multilayer ceramic chip capacitor0.8 pF ATC 600FC3electrolytic capacitor100 nF, 50 V SMD 0805C4electrolytic capacitor10 nF, 50 V SMD 0805C5electrolytic capacitor22 pF, 100 V SMD 0805C6electrolytic capacitor 1 nF, 100 V SMD 1206C8multilayer ceramic chip capacitor 1.2 pF ATC 600FC9multilayer ceramic chip capacitor0.5 pF ATC 600FC11multilayer ceramic chip capacitor100 pF ATC 100BC12multilayer ceramic chip capacitor1nF ATC 700BC14electrolytic capacitor1μF, 100V SMD 1206C15electrolytic capacitor10μF, 100V SMD 2220C16electrolytic capacitor10 nF, 200 V SMD 1210C17electrolytic capacitor470 μF, 63 V PCE3667CT-NDE1, E2drain voltage connection-J1RF in connector-J2RF out connector-L1inductor330 nH1008CS-331XJBL2ferrite bead-2743019447L3inductor- 1 turn, 18 AWG,inner diameter= 4.06mm Q1transistor-CLF1G0060-30Q2transistor-NXP BC857BQ3transistor-NXP PSMN8R2-80YSR1resistor10 kΩVishay DaleR2resistor10 ΩVishay DaleR3resistor0.005 ΩRL7520WT-R005-FZ1, Z2, Z3, Z4, Z5, Z6, Z7, Z8, Z9, Z10, Z11, Z12, Z13microstrip lines-Table 9.List of components …continuedSee Figure1.Component Description Value Remarks7.2Application test resultsTable 10.CW and pulsed RF application informationTypical RF performance at T case = 25 ︒C; I Dq=70mA; V DS=50V in a class-AB broadband demo board.Test signal f P L G pηD(MHz)(W)(dB)(%) 1-Tone CW5003015.660.710003013.950.315003013.750.820003012.64925003014.255.6 1-Tone pulsed [1]5003016.66110003015.85015003015.552.520003014.55025003015.959[1]Pulsed RF; t p=100μs; δ=10%.Table 11.2-Tone CW application informationTypical 2-Tone performance at T case = 25 ︒C; I Dq=150mA; V DS=50V in a class-AB broadband demo board.Test signal f P L(PEP)IMD3(MHz)(W)(dBc) 2-Tone CW [1]50010-38100010-50150010-45200010-50250010-43[1]2-Tone CW; ∆f=1MHz.7.3Graphical dataThe following figures are measured in a broadband amplifier demo board from 500MHz to 2500MHz.7.3.11-Tone CW RF performance7.3.21-Tone pulsed RF performance7.3.32-Tone CW performance7.4Bias moduleThe bias module information for the GaN HEMT amplifier is described in application noteAN11130.8. Test information8.1Ruggedness in class-AB operationThe CLF1G0060-30 and CLF1G0060S-30 are capable of withstanding a load mismatchcorresponding to VSWR=10:1 through all phases under the following conditions:V DS=50V; P L=30W(pulsed RF), f=3000MHz.8.2Load pull impedance informationThe measured load pull impedances are shown below. Impedance reference planedefined at device leads. Measurements performed with Ampleon test fixtures. Testtemperature set at 25 ︒C with a pulsed CW signal; t p=100μs; δ=10%; RF performanceat V DS=50V; I Dq=50 mA.Table 12.Typical impedanceTypical values unless otherwise specified.f Z S Z L (maximum P L(M))Z L (maximum ηD)(MHz)(Ω)(Ω)(Ω)2140 1.4 - 4j14 + 5.4j12.5 + 9.7j2500 2.8 - 6j10.5 + 2.5j7.6 + 5.6j2700 2.8 - 7.5j10.7 + 1.3j7.6 + 4.3j3000 3.0 - 10j9.1 + 3.5j7.7 + 4.2j3300 3.0 - 11.5j9.4 + 1.2j7.6 + 2.5j3500 3.0 - 13j9.57.2 + 1.35j3700 3.5 - 14.4j9.4 - 1.1j7.3 - 0.05j4000 3.7 - 20.3j9.3 - 2.4j7.7 - 1.2jZ S is the measured source pull impedance presented to the device. Z L is the measured load pull impedance presented to the device.8.3Packaged S-parameter data Table 13.S-parameterSmall signal; V DS = 50 V; I Dq = 50 mA; Z S = Z L = 50 Ω.f (MHz)S11S21S12S22Magnitude(ratio)Angle(degree)Magnitude(ratio)Angle(degree)Magnitude(ratio)Angle(degree)Magnitude(ratio)Angle(degree)1000.9302-76.39644.515135.220.01619546.8710.7376-43.407 2000.87436-115.4729.415111.960.02125325.2790.55438-65.523 3000.8537-134.9721.0298.8760.02251613.9030.47582-77.762 4000.8464-146.2216.09689.8550.02261 6.65290.44954-86.181 5000.8446-153.5712.91982.7610.022198 1.41920.44849-92.826 6000.84548-158.8110.7176.7390.021498-2.62370.46041-98.482 7000.84785-162.829.088371.3920.020604-5.83520.47921-103.5 8000.85112-166.057.846566.5160.019567-8.3750.50159-108.06 9000.85494-168.77 6.865561.9950.018424-10.3020.5256-112.27 10000.85908-171.15 6.071357.7580.017205-11.6120.5501-116.19 11000.86338-173.27 5.415753.7590.015936-12.2560.57433-119.86 12000.86774-175.22 4.86649.9660.014644-12.1380.59785-123.33 13000.87206-177.04 4.399346.3560.01336-11.1130.62038-126.6 14000.8763-178.75 3.998842.9110.012117-8.98450.64176-129.7 15000.88039179.61 3.652139.6160.010958-5.5050.66191-132.65 16000.88432178.03 3.349636.4590.0099386-0.408680.68081-135.46 17000.88806176.49 3.084133.4280.0091267 6.48930.69846-138.14 18000.8916175 2.849730.5140.008599115.0990.7149-140.7 19000.89493173.53 2.641627.7090.00842424.8530.73019-143.15 20000.89806172.09 2.456225.0050.008633934.740.74438-145.5 21000.90098170.67 2.290222.3950.009211443.730.75755-147.76 22000.9037169.26 2.141119.8720.010151.2080.76975-149.93 23000.90622167.87 2.006717.4290.01123357.0530.78106-152.02 24000.90856166.48 1.885215.0620.01254961.4390.79154-154.04 25000.91072165.11 1.77512.7660.01400164.6350.80125-155.99 26000.91272163.74 1.674810.5340.01555666.9020.81025-157.88 27000.91455162.37 1.58358.36390.01719168.4550.8186-159.71 28000.91623161 1.5001 6.25020.0188969.4590.82634-161.49 29000.91777159.63 1.4237 4.18940.02064270.0390.83353-163.22 30000.91917158.27 1.3535 2.17790.02244170.2880.8402-164.91 31000.92044156.89 1.2890.212520.02428170.2780.84641-166.55 32000.9216155.52 1.2296-1.710.0261670.060.85218-168.16 33000.92264154.14 1.1748-3.59250.02807669.6750.85755-169.73 34000.92357152.75 1.1241-5.43760.03002769.1540.86255-171.27 35000.92441151.35 1.0771-7.24790.03201568.5210.8672-172.78 36000.92515149.94 1.0336-9.02570.03403967.7950.87155-174.2638000.92635147.10.95551-12.4930.03819866.1150.87937-177.1539000.92683145.650.92046-14.1860.04033665.1830.8829-178.5740000.92723144.20.88777-15.8550.04251664.20.88619-179.9741000.92756142.730.85724-17.5010.04473763.1710.88927178.6542000.92781141.240.82871-19.1260.04700362.1010.89215177.2843000.928139.730.802-20.7320.04931560.9940.89484175.9344000.92812138.20.77698-22.320.05167659.8530.89735174.5845000.92818136.660.75351-23.8910.05408758.680.8997173.2546000.92818135.090.73149-25.4470.0565557.4770.9019171.9247000.92812133.50.71079-26.990.05906856.2450.90396170.648000.928131.890.69133-28.5190.06164454.9860.90588169.2849000.92783130.250.67301-30.0380.06427953.6990.90767167.9750000.92761128.590.65576-31.5460.06697552.3870.90935166.6651000.92734126.90.63949-33.0460.06973651.0470.91092165.3552000.92701125.170.62415-34.5370.07256349.6820.91238164.0453000.92664123.420.60968-36.0220.07545948.2910.91375162.7354000.92622121.640.596-37.5010.07842646.8740.91502161.4255000.92576119.830.58307-38.9750.08146745.430.9162160.156000.92525117.980.57085-40.4460.08458343.9590.9173158.7857000.9247116.10.55929-41.9140.08777842.4610.91832157.4558000.92411114.180.54834-43.380.09105340.9350.91927156.1259000.92348112.220.53797-44.8460.09441139.3810.92014154.7760000.92282110.230.52814-46.3110.09785337.7970.92095153.42Table 13.S-parameter …continuedSmall signal; V DS = 50 V; I Dq = 50 mA; Z S = Z L = 50 Ω.f(MHz)S 11S 21S 12S 22Magnitude (ratio)Angle (degree)Magnitude (ratio)Angle (degree)Magnitude (ratio)Angle (degree)Magnitude (ratio)Angle (degree)9. Package outline10. Handling information10.1ESD Sensitivity[1]Classification 1B is granted to any part that passes after exposure to an ESD pulse of 500V, but fails after exposure to an ESD pulse of 1000V.11. Abbreviations12. Revision historyTable 14.ESD sensitivityESD modelClass Human Body Model (HBM); According JEDEC standard JESD22-A114F1B [1]Table 15.AbbreviationsAcronym DescriptionAWG American Wire Gauge CW Continuous WaveEMC ElectroMagnetic Compatibility ESD ElectroStatic Discharge GaN Gallium NitrideHEMT High Electron Mobility Transistor SMD Surface Mounted Device VSWR Voltage Standing-Wave RatioWiMAXWorldwide Interoperability for Microwave AccessTable 16.Revision historyDocument ID Release date Data sheet statusChange notice Supersedes CLF1G0060-30_1G0060S-30 v.720180205Product data sheet-CLF1G0060-30_1G0060S-30 v.6Modifications:•Table 9 on page 4: L1 remark updated •Figure 2 on page 6: L1 value updatedCLF1G0060-30_1G0060S-30 v.620160218Product data sheet-CLF1G0060-30_1G0060S-30#5CLF1G0060-30_1G0060S-30#520150901Objective data sheet -CLF1G0060-30_1G0060S-30 v.4CLF1G0060-30_1G0060S-30 v.420130620Objective data sheet -CLF1G0060-30_1G0060S-30 v.3CLF1G0060-30_1G0060S-30 v.320130327Objective data sheet -CLF1G0060-30_1G0060S-30 v.2CLF1G0060-30_1G0060S-30 v.220130129Objective data sheet -CLF1G0060-30_1G0060S-30 v.1CLF1G0060-30_1G0060S-30 v.120121008Objective data sheet --13. Legal information13.1 Data sheet status[1]Please consult the most recently issued document before initiating or completing a design.[2]The term ‘short data sheet’ is explained in section “Definitions”.[3]The product status of device(s) described in this document may have changed since this document was published and may differ in case of multiple devices. The latest product statusinformation is available on the Internet at URL .13.2 DefinitionsDraft — The document is a draft version only. The content is still under internal review and subject to formal approval, which may result in modifications or additions. Ampleon does not give any representations or warranties as to the accuracy or completeness of information included herein and shall have no liability for the consequences of use of such information.Short data sheet — A short data sheet is an extract from a full data sheet with the same product type number(s) and title. A short data sheet is intended for quick reference only and should not be relied upon to contain detailed and full information. For detailed and full information see the relevant full data sheet, which is available on request via the local Ampleon sales office. In case of any inconsistency or conflict with the short data sheet, the full data sheet shall prevail.Product specification — The information and data provided in a Product data sheet shall define the specification of the product as agreed between Ampleon and its customer, unless Ampleon and customer have explicitly agreed otherwise in writing. In no event however, shall an agreement be valid in which the Ampleon product is deemed to offer functions and qualities beyond those described in the Product data sheet.13.3 DisclaimersLimited warranty and liability — Information in this document is believed to be accurate and reliable. However, Ampleon does not give any representations or warranties, expressed or implied, as to the accuracy or completeness of such information and shall have no liability for the consequences of use of such information. Ampleon takes no responsibility for the content in this document if provided by an information source outside of Ampleon.In no event shall Ampleon be liable for any indirect, incidental, punitive, special or consequential damages (including - without limitation - lost profits, lost savings, business interruption, costs related to the removal or replacement of any products or rework charges) whether or not such damages are based on tort (including negligence), warranty, breach of contract or any other legal theory.Notwithstanding any damages that customer might incur for any reason whatsoever, Ampleon’s aggregate and cumulative liability towards customer for the products described herein shall be limited in accordance with the Terms and conditions of commercial sale of Ampleon.Right to make changes — Ampleon reserves the right to make changes to information published in this document, including without limitation specifications and product descriptions, at any time and without notice. This document supersedes and replaces all information supplied prior to the publication hereof.Suitability for use — Ampleon products are not designed, authorized or Ampleon product can reasonably be expected to result in personal injury, death or severe property or environmental damage. Ampleon and its suppliers accept no liability for inclusion and/or use of Ampleon products in such equipment or applications and therefore such inclusion and/or use is at the customer’s own risk.Applications — Applications that are described herein for any of these products are for illustrative purposes only. Ampleon makes no representation or warranty that such applications will be suitable for the specified use without further testing or modification.Customers are responsible for the design and operation of their applications and products using Ampleon products, and Ampleon accepts no liability for any assistance with applications or customer product design. It is customer’s sole responsibility to determine whether the Ampleon product is suitable and fit for the customer’s applications and products planned, as well as for the planned application and use of customer’s third party customer(s). Customers should provide appropriate design and operating safeguards to minimize the risks associated with their applications and products.Ampleon does not accept any liability related to any default, damage, costs or problem which is based on any weakness or default in the customer’s applications or products, or the application or use by customer’s third party customer(s). Customer is responsible for doing all necessary testing for the customer’s applications and products using Ampleon products in order to avoid a default of the applications and the products or of the application or use by customer’s third party customer(s). Ampleon does not accept any liability in this respect.Limiting values — Stress above one or more limiting values (as defined in the Absolute Maximum Ratings System of IEC60134) will cause permanent damage to the device. Limiting values are stress ratings only and (proper) operation of the device at these or any other conditions above those given in the Recommended operating conditions section (if present) or the Characteristics sections of this document is not warranted. Constant or repeated exposure to limiting values will permanently and irreversibly affect the quality and reliability of the device.Terms and conditions of commercial sale — Ampleon products are sold subject to the general terms and conditions of commercial sale, as published at /terms, unless otherwise agreed in a valid written individual agreement. In case an individual agreement is concluded only the terms and conditions of the respective agreement shall apply. Ampleon hereby expressly objects to applying the customer’s general terms and conditions with regard to the purchase of Ampleon products by customer.No offer to sell or license — Nothing in this document may be interpreted or construed as an offer to sell products that is open for acceptance or the grant, conveyance or implication of any license under any copyrights, patents or other industrial or intellectual property rights.Export control — This document as well as the item(s) described herein may be subject to export control regulations. Export might require a prior authorization from competent authorities.Document status[1][2]Product status[3]DefinitionObjective [short] data sheet Development This document contains data from the objective specification for product development. Preliminary [short] data sheet Qualification This document contains data from the preliminary specification.Product [short] data sheet Production This document contains the product specification.Non-automotive qualified products — Unless this data sheet expressly states that this specific Ampleon product is automotive qualified, the product is not suitable for automotive use. It is neither qualified nor tested in accordance with automotive testing or application requirements. Ampleon accepts no liability for inclusion and/or use of non-automotive qualified products in automotive equipment or applications.In the event that customer uses the product for design-in and use in automotive applications to automotive specifications and standards, customer (a) shall use the product without Ampleon’s warranty of the product for such automotive applications, use and specifications, and (b) whenever customer uses the product for automotive applications beyond Ampleon’s specifications such use shall be solely at customer’s own risk, and (c) customer fully indemnifies Ampleon for any liability, damages or failed product claims resulting from customer design and use of the product for automotive applications beyond Ampleon’s standard warranty and Ampleon’s product specifications.Translations — A non-English (translated) version of a document is for reference only. The English version shall prevail in case of any discrepancy between the translated and English versions.13.4 TrademarksNotice: All referenced brands, product names, service names and trademarks are the property of their respective owners.Any reference or use of any ‘NXP’ trademark in this document or in or on the surface of Ampleon products does not result in any claim, liability or entitlement vis-à-vis the owner of this trademark. Ampleon is no longer part of the NXP group of companies and any reference to or use of the ‘NXP’ trademarks will be replaced by reference to or use of Ampleon’s own trademarks.14. Contact informationFor more information, please visit: For sales office addresses, please visit: /sales15. Contents1 Product profile. . . . . . . . . . . . . . . . . . . . . . . . . . 11.1 General description . . . . . . . . . . . . . . . . . . . . . 11.2 Features and benefits. . . . . . . . . . . . . . . . . . . . 21.3 Applications . . . . . . . . . . . . . . . . . . . . . . . . . . . 22 Pinning information. . . . . . . . . . . . . . . . . . . . . . 23 Ordering information. . . . . . . . . . . . . . . . . . . . . 24 Limiting values. . . . . . . . . . . . . . . . . . . . . . . . . . 35 Thermal characteristics . . . . . . . . . . . . . . . . . . 36 Characteristics. . . . . . . . . . . . . . . . . . . . . . . . . . 37 Application information. . . . . . . . . . . . . . . . . . . 47.1 Demo circuit . . . . . . . . . . . . . . . . . . . . . . . . . . . 47.2 Application test results . . . . . . . . . . . . . . . . . . . 77.3 Graphical data . . . . . . . . . . . . . . . . . . . . . . . . . 87.3.1 1-Tone CW RF performance. . . . . . . . . . . . . . . 87.3.2 1-Tone pulsed RF performance . . . . . . . . . . . . 97.3.3 2-Tone CW performance . . . . . . . . . . . . . . . . 107.4 Bias module . . . . . . . . . . . . . . . . . . . . . . . . . . 108 Test information. . . . . . . . . . . . . . . . . . . . . . . . 108.1 Ruggedness in class-AB operation . . . . . . . . 108.2 Load pull impedance information . . . . . . . . . . 108.3 Packaged S-parameter data. . . . . . . . . . . . . . 129 Package outline. . . . . . . . . . . . . . . . . . . . . . . . 1410 Handling information. . . . . . . . . . . . . . . . . . . . 1610.1 ESD Sensitivity. . . . . . . . . . . . . . . . . . . . . . . . 1611 Abbreviations. . . . . . . . . . . . . . . . . . . . . . . . . . 1612 Revision history. . . . . . . . . . . . . . . . . . . . . . . . 1613 Legal information. . . . . . . . . . . . . . . . . . . . . . . 1713.1 Data sheet status . . . . . . . . . . . . . . . . . . . . . . 1713.2 Definitions. . . . . . . . . . . . . . . . . . . . . . . . . . . . 1713.3 Disclaimers. . . . . . . . . . . . . . . . . . . . . . . . . . . 1713.4 Trademarks. . . . . . . . . . . . . . . . . . . . . . . . . . . 1814 Contact information. . . . . . . . . . . . . . . . . . . . . 1815 Contents. . . . . . . . . . . . . . . . . . . . . . . . . . . . . . 19Please be aware that important notices concerning this document and the product(s)described herein, have been included in section ‘Legal information’.© Ampleon Netherlands B.V.2018.All rights reserved.。
美国Eaton公司PDG23P0060B2NJ型号的电容器说明说明书
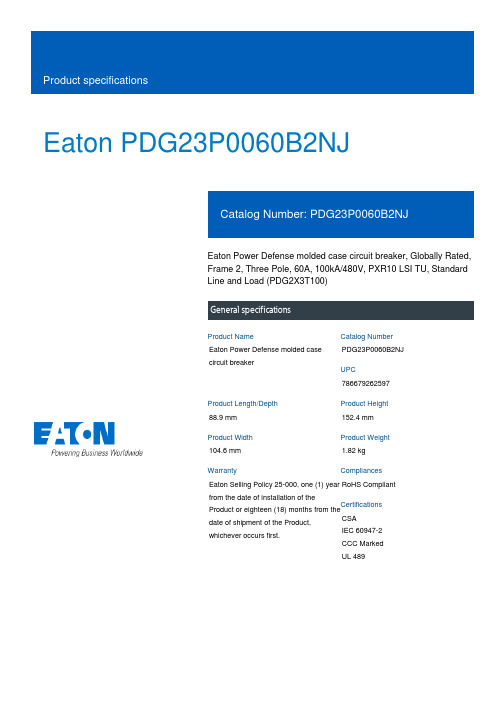
Eaton PDG23P0060B2NJEaton Power Defense molded case circuit breaker, Globally Rated, Frame 2, Three Pole, 60A, 100kA/480V, PXR10 LSI TU, Standard Line and Load (PDG2X3T100)Eaton Power Defense molded case circuit breakerPDG23P0060B2NJ 78667926259788.9 mm 152.4 mm 104.6 mm 1.82 kg Eaton Selling Policy 25-000, one (1) year from the date of installation of theProduct or eighteen (18) months from thedate of shipment of the Product,whichever occurs first.RoHS Compliant CSAIEC 60947-2CCC MarkedUL 489Product NameCatalog Number UPCProduct Length/Depth Product Height Product Width Product Weight WarrantyCompliancesCertifications60 AComplete breaker 2Three-polePD2 Global Class A PXR 10 LSI600 Vac600 VStandard Line and Load100 kAIC at 480 Vac 200 kAIC @240V (UL)100 kAIC Icu/ 70 kAIC Ics/ 220 kAIC Icm @380-415V (IEC) 200 kAIC Icu/ 150 kAIC Ics/ 440 kAIC Icm @240V (IEC) 35/25 kAIC Icu/ 18/13 kAIC Ics @525V South Africa (IEC) 85 kAIC Icu/ 40 kAIC Ics/ 187 kAIC Icm @480V Brazil (IEC) 22 kAIC Icu @125 Vdc 22 kAIC Icu @250 Vdc10 kAIC Icu/ 5 kAIC Ics/ 21 kAIC Icm @690V (IEC) 35/25 kAIC @600V (UL/CSA)100 kAIC Icu/ 65 kAIC Ics/ 220 kAIC Icm @440V (IEC) 100 kAIC @480V (UL) 25 kAIC @600V (UL/CSA)Eaton Power Defense MCCB PDG23P0060B2NJ 3D drawing Power Xpert Protection Manager x32Consulting application guide - molded case circuit breakersAmperage Rating Circuit breaker frame type Frame Number of poles Circuit breaker type Class Trip Type Voltage rating Voltage rating - max TerminalsInterrupt rating Interrupt rating range 3D CAD drawing packageApplication notesPower Xpert Protection Manager x64BrochuresPower Defense technical selling bookletPower Defense molded case circuit breaker selection posterPower Defense brochurePower Defense molded case circuit breakers - Frame 2 product aid CatalogsPower Xpert Release trip units for Power Defense molded case circuit breakersMolded case circuit breakers catalogCertification reportsEU Declaration of Conformity - Power Defense molded case circuit breakersPower Defense Declaration concerning California’s Proposition 65PDG2 CB reportPDG4 CCC certificationPDG4 CB reportInstallation instructionsPower Defense Frame 2 global terminal shield, 3 pole - IL012330EN Power Defense Frame 2 shunt trip UVR instructions - IL012130EN Power Defense Frame 2 clamp terminal (steel), 20A, 3 pole instructions - IL012246EN H03Power Defense Frame 2 handle mech direct rotary handle instructions - IL012134ENPower Defense Frame 2 handle mech variable depth rotary handle instructions - IL012136ENPower Defense Frame 1 IEC and Frame 2 Rotary Mechanism with NFPA Handle Attachment Instructions (IL012260EN).pdfPower Defense Frame 2 tunnel terminal (aluminum), 50A, 3 pole instructions - IL012236EN H03Power Defense Frame 2 locking devices and handle block instructions - IL012149ENPower Defense Frame 2/3/4/5/6 voltage neutral sensor module wiring instructions – IL012316ENPower Defense Frame 2 terminal kit - PDG2X3(2)(4)TA150RF instructions - IL012244EN H01Power Defense Frame 2 terminal kit - PDG2X3(2)(4)TA225RF instructions - IL012245EN H01Power Defense Frame 2 screw terminal_end cap kit, 225A, 3 pole instructions - IL012258EN H01Power Defense Frame 2 Direct Rotary Handle Assy With Interlock VersionInstructions (IL012138EN).pdfPower Defense Frame 2 multi wire connector kit -PDG2X3(2)(4)TA2256W instructions - IL012242EN H01Power Defense Frame 2 PDG2 and PDC(E)9 breaker instructions -IL012106ENPower Defense Frame 2 bell alarm switch instructions - IL012154EN Power Defense Frame 2 Bell Alarm Switch Instructions (IL012154EN).pdf Power Defense Frame 1-2-3-4 IP door barrier assembly instructions -IL012278ENPower Defense Frame 2 tunnel terminal (aluminum), 150A, 3 pole instructions - IL012238EN H03Power Defense Frame 2 box terminal (steel), 100A, 3 pole instructions - IL012234EN H03Power Defense Frame 2 tunnel terminal (aluminum), 100A, 3 pole instructions - IL012237EN H03Power Defense Frame 2 box terminal (aluminum), 225A, 3 pole instructions - IL012235EN H03Power Defense Frame 2 tunnel terminal kits - PDG2X1TA225K instructions- IL012239EN H01Power Defense Frame 2 multi wire connector kit -PDG2X3(2)(4)TA2253W instructions - IL012243EN H01Installation videosPower Defense Frame 2 Handle Mech Variable Depth Rotary Handle Animated Instructions.rhPower Defense Frame 2 TMTU Aux, Alarm, ST and UVR Animated Instructions.rhPower Defense Frame 2 Bell Alarm with PXR Animated Instructions.pdf.rh Power Defense Frame 2 withTMTU, Shunt Trip_UVR Animated Instructions.rhPower Defense Frame 2 Locking Devices and Handle Block Animated Instructions.pdf.rhMultimediaPower Defense Frame 3 Variable Depth Rotary Handle Mechanism Installation How-To VideoPower Defense Frame 2 Variable Depth Rotary Handle Mechanism Installation How-To VideoPower Defense Frame 2 Aux, Alarm, Shunt Trip, and UVR How-To Video Power Defense Frame 2 Direct Rotary Handle Mechanism Installation How-To VideoEaton Power Defense for superior arc flash safetyPower Defense molded case circuit breakersPower Defense Frame 5 Trip Unit How-To VideoEaton Corporation plc Eaton House30 Pembroke Road Dublin 4, Ireland © 2023 Eaton. All Rights Reserved. Eaton is a registered trademark.All other trademarks areproperty of their respectiveowners./socialmediaPower Defense BreakersPower Defense Frame 6 Trip Unit How-To Video Eaton Specification Sheet - PDG23P0060B2NJ Power Defense time current curve Frame 2 - PD2Selling Policy 25-000 - Distribution and Control Products and Services Making a better machineMolded case and low-voltage power circuit breaker health Intelligent circuit protection yields space savings Intelligent power starts with accurate, actionable data Single and double break MCCB performance revisited Safer by design: arc energy reduction techniques Molded case and low-voltage breaker healthSpecifications and datasheetsTime/current curvesWarranty guidesWhite papers。
欧陆EV500变频器使用手册附录1(功能参数一览表)
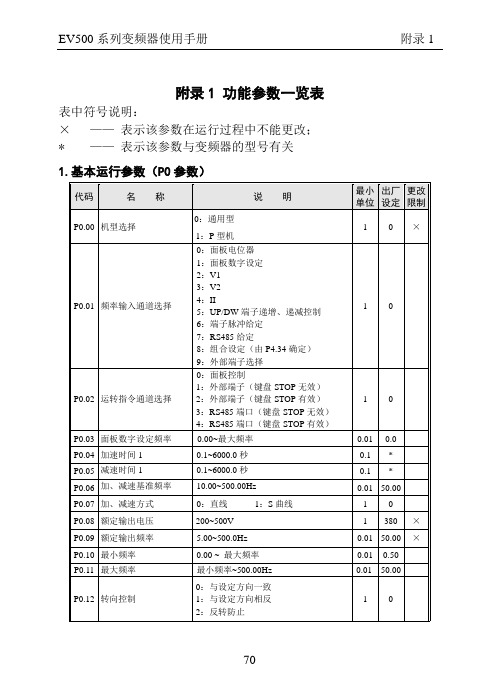
附录1 功能参数一览表表中符号说明:
×——表示该参数在运行过程中不能更改;* ——表示该参数与变频器的型号有关
1.基本运行参数(P0参数)
2. 启动、停止参数(P1参数)
3 .V/F曲线设定及电机参数(P2参数)
4. 外部输入、输出端子定义(P3参数)
5.辅助运行参数(P4参数)
6. 多段速和PLC参数(P5参数)
7. PID参数(P6参数)
8. 摆频参数(P7参数)
9. 保护参数(P8参数)
10. 通讯参数(P9参数)
11. 状态监控参数一览表
EV500系列变频器使用手册 附录1
80
参数d- 13、d- 34显示符号与外部输入端子状态的对应关系如下:
X1X2X3X4LED 亮:表示有效 LED 灭:表示无效
端子状态
端子状态 端子状态 端子状态 输出状态 输出状态
当前输入端子状态:
有效:X1、X4、X5、X6、X7
无效:X2、X3 当前输出端口状态: 有效:Y1 无效:Y2。
ATH006A0XZ;ATH006A0X;ATH006A0X4Z;ATH006A0X4;中文规格书,Datasheet资料
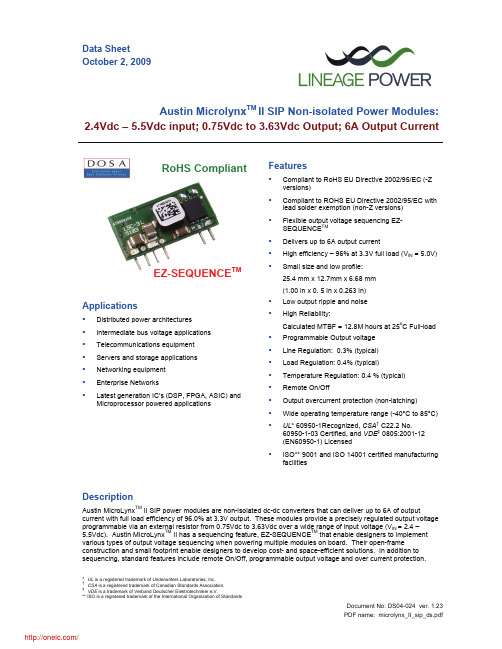
Data SheetOctober 2, 2009Austin Microlynx TM II SIP Non-isolated Power Modules:2.4Vdc – 5.5Vdc input; 0.75Vdc to3.63Vdc Output; 6A Output Current* UL is a registered trademark of Underwriters Laboratories, Inc. †CSA is a registered trademark of Canadian Standards Association. ‡ApplicationsDistributed power architectures Intermediate bus voltage applications Telecommunications equipment Servers and storage applications Networking equipment Enterprise NetworksLatest generation IC’s (DSP, FPGA, ASIC) and Microprocessor powered applicationsFeaturesCompliant to RoHS EU Directive 2002/95/EC (-Z versions)Compliant to ROHS EU Directive 2002/95/EC with lead solder exemption (non-Z versions) Flexible output voltage sequencing EZ-SEQUENCE TMDelivers up to 6A output currentHigh efficiency – 96% at 3.3V full load (V IN = 5.0V)Small size and low profile: 25.4 mm x 12.7mm x 6.68 mm (1.00 in x 0. 5 in x 0.263 in) Low output ripple and noise High Reliability:Calculated MTBF = 12.8M hours at 25oC Full-load Programmable Output voltage Line Regulation: 0.3% (typical) Load Regulation: 0.4% (typical) Temperature Regulation: 0.4 % (typical) Remote On/OffOutput overcurrent protection (non-latching) Wide operating temperature range (-40°C to 85°C)UL * 60950-1Recognized, CSA †C22.2 No.60950-1-03 Certified, and VDE ‡0805:2001-12 (EN60950-1) LicensedISO** 9001 and ISO 14001 certified manufacturing facilitiesDescriptionAustin MicroLynx TMII SIP power modules are non-isolated dc-dc converters that can deliver up to 6A of outputcurrent with full load efficiency of 96.0% at 3.3V output. These modules provide a precisely regulated output voltage programmable via an external resistor from 0.75Vdc to 3.63Vdc over a wide range of input voltage (V IN = 2.4 –5.5Vdc). Austin MicroLynx TM II has a sequencing feature, EZ-SEQUENCE TMthat enable designers to implement various types of output voltage sequencing when powering multiple modules on board. Their open-frameconstruction and small footprint enable designers to develop cost- and space-efficient solutions. In addition to sequencing, standard features include remote On/Off, programmable output voltage and over current protection.RoHS CompliantEZ-SEQUENCE TMAbsolute Maximum RatingsStresses in excess of the absolute maximum ratings can cause permanent damage to the device. These areabsolute stress ratings only, functional operation of the device is not implied at these or any other conditions inexcess of those given in the operations sections of the data sheet. Exposure to absolute maximum ratings forextended periods can adversely affect the device reliability.Parameter Device Symbol Min Max UnitInput Voltage All V IN -0.3 5.8 Vdc ContinuousSequencing voltage All Vseq -0.3 V IN,max Vdc Operating Ambient Temperature All T A -40 85 °C (see Thermal Considerations section)Storage Temperature All T stg -55 125 °CElectrical SpecificationsUnless otherwise indicated, specifications apply over all operating input voltage, resistive load, and temperature conditions.Parameter Device Symbol Min Typ Max UnitOperating Input Voltage V o,set≤ 3.63 V IN 2.4 ⎯ 5.5 Vdc Maximum Input Current All I IN,max Adc (V IN= V IN, min to V IN, max, I O=I O, max ) 6.0Input No Load Current V O,set = 0.75 Vdc I IN,No load 20 mA(V IN = V IN, nom, Io = 0, module enabled) V O,set = 3.3Vdc I IN,No load 45 mA Input Stand-by Current All I IN,stand-by0.6 mA(V IN = V IN, nom, module disabled)Inrush Transient All I2t 0.04 A2sInput Reflected Ripple Current, peak-to-peak(5Hz to 20MHz, 1μH source impedance; V IN, min to V IN, max, I O= I Omax ; See Test configuration section) All 35mAp-pInput Ripple Rejection (120Hz) All 30 dBCAUTION: This power module is not internally fused. An input line fuse must always be used. This power module can be used in a wide variety of applications, ranging from simple standalone operation to being part of a complex power architecture. To preserve maximum flexibility, internal fusing is not included, however, to achieve maximum safety and system protection, always use an input line fuse. The safety agencies require a fast-acting fuse with a maximum rating of 6 A (see Safety Considerations section). Based on the information provided in this data sheet on inrush energy and maximum dc input current, the same type of fuse with a lower rating can be used. Refer to the fuse manufacturer’s data sheet for further information.Electrical Specifications(continued)Parameter Device Symbol Min Typ Max UnitV O, set Output Voltage Set-point All V O, set -2.0 ⎯+2.0 % =25°C)(V IN=IN, min, I O=I O, max, T AV O, set Output Voltage All V O, set –3.0⎯+3.0 %(Over all operating input voltage, resistive load,and temperature conditions until end of life)Adjustment Range All V O 0.7525 3.63 VdcSelected by an external resistorOutput RegulationLine (V IN=V IN, min to V IN, max) All⎯0.3 ⎯% V O, set Load (I O=I O, min to I O, max) All⎯0.4 ⎯% V O, set Temperature (T ref=T A, min to T A, max) All ⎯0.4 ⎯% V O, setOutput Ripple and Noise on nominal output(V IN=V IN, nom and I O=I O, min to I O, maxCout = 1μF ceramic//10μFtantalum capacitors)RMS (5Hz to 20MHz bandwidth) All ⎯10 15 mV rmsPeak-to-Peak (5Hz to 20MHz bandwidth) All ⎯40 50 mV pk-pk External CapacitanceC O, max ⎯⎯1000 μFESR ≥ 1 mΩ AllC O, max ⎯⎯3000 μFESR ≥ 10 mΩ AllOutput Current All I o 0 6 Adc Output Current Limit Inception (Hiccup Mode ) All I O, lim ⎯220 ⎯% I o(V O= 90% of V O, set)Output Short-Circuit Current All I O, s/c ⎯ 2 ⎯Adc(V O≤250mV) ( Hiccup Mode )Efficiency V O, set = 0.75Vdc η81.0 % V IN= V IN, nom, T A=25°C V O, set = 1.2Vdc η87.0 %I O=I O, max , V O= V O,set V O,set = 1.5Vdc η89.0 %V O,set = 1.8Vdc η90.0 %V O,set = 2.5Vdc η93.0 %V O,set = 3.3Vdc η96.0 % Switching Frequency All f sw ⎯300 ⎯kHzDynamic Load Response(dIo/dt=2.5A/μs; V IN = V IN, nom; T A=25°C) All V pk ⎯130 ⎯mVLoad Change from Io= 50% to 100% ofIo,max; 1μF ceramic// 10 μF tantalumPeak DeviationSettling Time (Vo<10% peak deviation) All t⎯25 ⎯μss(dIo/dt=2.5A/μs; V IN = V IN, nom; T A=25°C) All V pk ⎯130 ⎯mVLoad Change from Io= 100% to 50%of Io,max:1μF ceramic// 10 μF tantalumPeak DeviationSettling Time (Vo<10% peak deviation) All t⎯25 ⎯μssElectrical Specifications(continued)Parameter Device Symbol Min Typ Max UnitResponseDynamicLoad(dIo/dt=2.5A/μs; V V IN = V IN, nom; T A=25°C) All V pk ⎯50 ⎯mVLoad Change from Io= 50% to 100% of Io,max;Co = 2x150 μF polymer capacitorsPeak DeviationSettling Time (Vo<10% peak deviation) All t⎯50 ⎯μss(dIo/dt=2.5A/μs; V IN = V IN, nom; T A=25°C) All V pk ⎯50 ⎯mVLoad Change from Io= 100% to 50%of Io,max:Co = 2x150 μF polymer capacitorsPeak DeviationSettling Time (Vo<10% peak deviation) All t⎯50 ⎯μssGeneral SpecificationsParameter Min Typ Max UnitHours =25°C) 12,841,800 Calculated MTBF (I O=I O, max, T Aper Telecordia SR-332 Issue 1: Method 1 Case 3Weight ⎯ 2.8 (0.1) ⎯g (oz.)Feature SpecificationsUnless otherwise indicated, specifications apply over all operating input voltage, resistive load, and temperature conditions. See Feature Descriptions for additional information.Parameter Device Symbol Min Typ Max Unit interfaceSignalOn/OffDevice code with Suffix “4” – Positive logic(On/Off is open collector/drain logic input;Signal referenced to GND - See feature descriptionsection)Input High Voltage (Module ON) All V IH――V IN, max VInput High Current All I IH―― 10 μAInput Low Voltage (Module OFF) All V IL -0.2 ― 0.3 VInput Low Current All I IL― 0.2 1 mA Device Code with no suffix – Negative Logic(On/OFF pin is open collector/drain logic input withexternal pull-up resistor; signal referenced to GND)Input High Voltage (Module OFF) All V IH 1.5 ―V IN,max VdcInput High Current All I IH0.2 1 mA Input Low Voltage (Module ON) All V IL -0.2 ― 0.3 Vdc Input low Current All I IL― 10 μATurn-On Delay and Rise Times)(I O=I O, max , V IN = V IN, nom, T A = 25 o C,All Tdelay ― 3.9 ― msec Case 1: On/Off input is set to Logic Low (ModuleON) and then input power is applied (delay frominstant at which V IN =V IN, min until Vo=10% of Vo,set)All Tdelay ― 3.9 ― msec Case 2: Input power is applied for at least one secondand then the On/Off input is set to logic Low (delay frominstant at which Von/Off=0.3V until Vo=10% of Vo, set)All Trise― 4.2 8.5 msec Output voltage Rise time (time for Vo to rise from 10%of V o,set to 90% of Vo, set)Output voltage overshoot – Startup ― 1 % V O, setI O= I O, max; V IN = 2.4 to 5.5Vdc, T A = 25 o CSequencing Delay timeDelay from V IN, min to application of voltage on SEQ pin All Ts EQ-delay 10 msec Tracking Accuracy (Power-Up: 2V/ms) All |V SEQ –V o | 100 200 mV (Power-Down: 1V/ms) All |V SEQ –V o | 200 400 mV (V IN, min to V IN, max; I O, min to I O, max V SEQ< V o)Overtemperature Protection All T⎯150 ⎯°Cref(See Thermal Consideration section)Input Undervoltage LockoutTurn-on Threshold All 2.2 V Turn-off Threshold All 2.0 VCharacteristic CurvesThe following figures provide typical characteristics for the Austin MicroLynx TM II SIP modules at 25ºC.E F F I C I E N C Y , η (%)E F F I C I E N C Y , η (%)E F F I C I E N C Y , η (%)E F F I C I E N C Y , η (%)E F F I C I E N C Y , η (%)E F F I C I E N C Y , η (%)Characteristic Curves (continued)The following figures provide typical characteristics for the MicroLynx TM II SIP modules at 25ºC.INPUTCURRENT,IIN(A)INOUTPUTCURRENT,OUTPUTVOLTAGEIO(A)(2A/div)VO(V)(1mV/div)TIME, t (5 μs/div)Figure 7. Input voltage vs. Input Current(Vout =2.5Vdc).Figure 10. Transient Response to Dynamic LoadChange from 50% to 100% of full load (Vo = 3.3Vdc). OUTPUTVOLTAGEVO(V)(2mV/div)TIME, t (2μs/div) O UTPUTCURRENT,OUTPUTVOLTAGEIO(A)(2A/div)VO(V)(1mV/div)TIME, t (5 μs/div)Figure 8. Typical Output Ripple and Noise(Vin = 5.0V dc, Vo = 0.75 Vdc, Io=6A).Figure 11. Transient Response to Dynamic LoadChange from 100% to 50% of full load (Vo = 3.3 Vdc). OUTPUTVOLTAGEVO(V)(2mV/div)TIME, t (2μs/div) O UTPUTCURRENT,OUTPUTVOLTAGEIO(A)(2A/div)VO(V)(1mV/div)TIME, t (10μs/div)Figure 9. Typical Output Ripple and Noise(Vin = 5.0V dc, Vo = 3.3 Vdc, Io=6A).Figure 12. Transient Response to Dynamic LoadChange from 50% to 100% of full load (Vo = 3.3 Vdc,Cext = 2x150 μF Polymer Capacitors).Characteristic Curves (continued)The following figures provide typical characteristics for the Austin MicroLynx TM II SIP modules at 25ºC.O U T P U T C U R R E N T , O U T P U T V O L T A G E I O (A ) (2A /d i v ) V O (V ) (100m V /d i v )TIME, t (10μs/div) O U T P U T V O L T A G E , I N P U T V O L T A G E V o (V ) (1V /d i v ) V I N (V ) (2V /d i v )TIME, t (2 ms/div)Figure 13. Transient Response to Dynamic LoadChange from 100% of 50% full load (Vo = 3.3Vdc, Cext = 2x150 μF Polymer Capacitors).Figure 16. Typical Start-Up with application of Vin(Vin = 5.0Vdc, Vo = 3.3Vdc, Io = 6A).O U T P U T V O L T A G E O n /O f f V O L T A G EV O V ) (1V /d i v ) V O n /o f f (V ) (2V /d i v )TIME, t (2 ms/div)O U T P U T V O L T A G E O n /O f f V O L T A G EV O V ) (1V /d i v ) V O n /o f f (V ) (2V /d i v )Figure 14. Typical Start-Up Using Remote On/Off (Vin = 5.0Vdc, Vo = 3.3Vdc, Io = 6A).Figure 17 Typical Start-Up Using Remote On/Off with Prebias (Vin = 3.3Vdc, Vo = 1.8Vdc, Io = 1.0A, Vbias=1.0Vdc).O U T P U T V O L T A G E O n /O f f V O L T A G E V O V ) (1V /d i v ) V O n /o f f (V ) (2V /d i v )TIME, t (2 ms/div)O U T P U T C U R R E N T ,I O (A ) (5A /d i v )TIME, t (5ms/div)F igure 15. Typical Start-Up Using Remote On/Off with Low-ESR external capacitors (7x150uF Polymer) (Vin = 5.0Vdc, Vo = 3.3Vdc, Io = 6A, Co = 1050μF).Figure 18. Output short circuit Current (Vin = 5.0Vdc, Vo = 0.75Vdc).Characteristic Curves (continued)The following figures provide thermal derating curves for the Austin MicroLynx TM II SIP modules.O U T P U T C U R R E N T , I o (A )AMBIENT TEMPERATURE, T A C O U T P U T C U R R E N T , I o (A )AMBIENT TEMPERATURE, T A CFigure 19. Derating Output Current versus Local Ambient Temperature and Airflow (Vin = 5.0, Vo=3.3Vdc).Figure 22. Derating Output Current versus Local Ambient Temperature and Airflow (Vin = 3.3dc, Vo=0.75 Vdc).O U T P U T C U R R E N T , I o (A )AFigure 20. Derating Output Current versus Local Ambient Temperature and Airflow (Vin = 5.0Vdc, Vo=0.75 Vdc).O U T P U T C U R R E N T , I o (A )AMBIENT TEMPERATURE, T A CFigure 21. Derating Output Current versus Local Ambient Temperature and Airflow (Vin = 3.3Vdc, Vo=2.5 Vdc).Test ConfigurationsNOTE: Measure input reflected ripple current with a simulatedsource inductance (L TEST) of 1μH. Capacitor C S offsetspossible battery impedance. Measure current as shownabove.Figure 23. Input Reflected Ripple Current Test Setup. NOTE: All voltage measurements to be taken at the moduleterminals, as shown above. If sockets are used thenKelvin connections are required at the module terminalsto avoid measurement errors due to socket contactresistance.Figure 24. Output Ripple and Noise Test Setup.NOTE: All voltage measurements to be taken at the moduleterminals, as shown above. If sockets are used thenKelvin connections are required at the module terminalsto avoid measurement errors due to socket contactresistance.Figure 25. Output Voltage and Efficiency Test Setup.η= V O. I OV IN. I INx100%Efficiency Design ConsiderationsInput FilteringThe Austin MicroLynx TM II SIP module should beconnected to a low-impedance source. A highlyinductive source can affect the stability of the module.An input capacitance must be placed directly adjacentto the input pin of the module, to minimize input ripplevoltage and ensure module stability.To minimize input voltage ripple, low-ESR polymerand ceramic capacitors are recommended at the inputof the module. Figure 26 shows the input ripplevoltage (mVp-p) for various outputs with 1x150 µFpolymer capacitors (Panasonic p/n: EEFUE0J151R,Sanyo p/n: 6TPE150M) in parallel with 1 x 47 µFceramic capacitor (Panasonic p/n: ECJ-5YB0J476M,Taiyo- Yuden p/n: CEJMK432BJ476MMT) at full load.Figure 27 shows the input ripple with 2x150 µFpolymer capacitors in parallel with 2 x 47 µF ceramiccapacitor at full load.InputRippleVoltage(mVp-p)OutputVoltage(Vdc) Figure 26. Input ripple voltage for various outputwith 1x150 µF polymer and 1x47 µF ceramiccapacitors at the input (80% of Io,max).InputRippleVoltage(mVp-p)OutputVoltage(Vdc) Figure 27. Input ripple voltage for various outputwith 2x150 µF polymer and 2x47 µF ceramiccapacitors at the input (80% of Io,max).分销商库存信息:GEATH006A0XZ ATH006A0X ATH006A0X4Z ATH006A0X4。
- 1、下载文档前请自行甄别文档内容的完整性,平台不提供额外的编辑、内容补充、找答案等附加服务。
- 2、"仅部分预览"的文档,不可在线预览部分如存在完整性等问题,可反馈申请退款(可完整预览的文档不适用该条件!)。
- 3、如文档侵犯您的权益,请联系客服反馈,我们会尽快为您处理(人工客服工作时间:9:00-18:30)。
EV0060 (MP1567)1.2A, 6V, 800KHz Synchronous Rectified Step-Down ConverterEVALUATION BOARDThe Future of Analog IC TechnologyGENERAL DESCRIPTIONThe EV0060 is an evaluation board for theMP1567, a 1.2A, 800KHz DC to DC converter designed for low voltage applications requiring high efficiency. Capable of providing output voltages as low as 0.9V from a 3.3V supply voltage, the MP1567 eliminates the need for a 5V rail, providing over 90% efficiency via synchronous rectification and eliminating heat issues in confined spaces. Soft-start operation protects internal circuitry from hard turn on issues. Switching at 800KHz reduces the size of external components and thereby reduces board space.The MP1567 includes cycle-by-cycle current limiting and under voltage lockout. Internal power switches combined with the tiny 10-pin QFN package provide a solution requiring a minimum of space.ELECTRICAL SPECIFICATIONSParameter Symbol Value Units Input Voltage V IN 2.6 to 6 V Output Voltage V OUT 1.8 V Output CurrentI OUT 1.2AFEATURES• 1.2A Output Current • Synchronous Rectified • Internal 180m Ω and 220m Ω Power Switches • V IN Range of 2.6V to 6V • Over 90% Efficiency• Zero Current Shutdown Mode • Under Voltage Lockout Protection • Soft-Start Operation • Thermal Shutdown• Internal Current Limit (Source & Sink) • Tiny 10-Pin QFN PackageAPPLICATIONS• SOHO Routers, PCMCIA Cards, Mini PCI • Handheld Computers, PDAs • Cell Phones• Digital Video Cameras • Small LCD Displays“MPS” and “The Future of Analog IC Technology”, are Registered Trademarks of Monolithic Power Systems, Inc.EV0060 EVALUATION BOARDDimensions (2.5”X x 2.0”Y x 0.4”Z) Board NumberMPS IC NumberEV0060 MP1567DQ1009080706050403020100E F F I C I E N C Y (%)101001000LOAD CURRENT (mA)MP1567_EC01Efficiency vsLoad CurrentEV0060 – 1.2A, 6V, 800KHz SYNCHRONOUS RECTIFIED STEP-DOWN CONVERTEREVALUATION BOARDEVALUATION BOARD SCHEMATICEV0060 BILL OF MATERIALSQty Ref Value Description PackageManufacturerP/N DistributorP/N 4C1, C4, C6, C9NS Not Stuffed2 C2, C810µF Capacitor 4C3, C7,C10, C11 10nF Capacitor1 C5 4.7nF Capacitor1 D1 Diode MBR0520L1 L16.2µH InductorSumidaCDRH5D181 R1 0Ω1 R2 4.99k Ω Resistor 2 R3, R4 10k Ω Resistor, 1%1 U1Step-Down ConverterQFN10MPSMP1567DKEV0060 – 1.2A, 6V, 800KHz SYNCHRONOUS RECTIFIED STEP-DOWN CONVERTEREVALUATION BOARD PRINTED CIRCUIT BOARD LAYOUTFigure 1—Top Silk Layer Figure 2—Top LayerFigure 3—Bottom LayerEV0060 – 1.2A, 6V, 800KHz SYNCHRONOUS RECTIFIED STEP-DOWN CONVERTEREVALUATION BOARDTYPICAL PERFORMANCE CHARACTERISTICSV IN = 3.3V, V OUT = 1.8V, T A = +25°C, unless otherwise noted.MP1567-TPC01Current Limit vs.Duty CycleV OUT 50mV/div.I LOAD 0.5A/div.MP1567-TPC02Load Transient0.1A to 1A Load StepV SS 1V/div.V OUT 1V/div.I IN0.5A/div.2ms/div.MP1567-TPC03V OUT 1V/div.V SS 1mV/div.I INDUCTOR1A/div.2ms/div.MP1567-TPC04Output Short CircuitI OUT = 1AV SW 2V/div.I INDUCTOR1A/div.MP1567-TPC05Steady State2.52.01.51.00.50C U R R E N T L I M I T (A )20406080DUTY CYCLE (%)EV0060 – 1.2A, 6V, 800KHz SYNCHRONOUS RECTIFIED STEP-DOWN CONVERTEREVALUATION BOARDNOTICE: The information in this document is subject to change without notice. Please contact MPS for current specifications.Users should warrant and guarantee that third party Intellectual Property rights are not infringed upon when integrating MPS products into any application. MPS will not assume any legal responsibility for any said applications.QUICK START GUIDEThe output voltage of this board is set to 1.8V. The board layout accommodates most commonly used inductors and output capacitors.1. Attach the positive and negative ends of the load to the OUT and GND pins respectively.2. Attach an input voltage 2.6V ≤ V IN ≤ 6V and the input ground to the IN and GND pins,respectively. 3. To enable the MP1567 apply a voltage, 2V ≤ V EN ≤ 6V, to the EN pin. To disable the MP1567connect the EN pin to ground. 4. The output voltage V OUT can be changed by varying R3. Calculate the new value using theformula:⎟⎟⎠⎞⎜⎜⎝⎛−×=1V V 4R 3R FB OUT Where V FB = 0.9V and R4 = 10k Ω.For example, for V OUT = 2.5V:Ω=⎟⎠⎞⎜⎝⎛−×Ω=⎟⎟⎠⎞⎜⎜⎝⎛−×=k 78.171V 9.0V 5.2k 101V V 4R 3R FB OUT Therefore use a standard 1% value 17.8k Ω resistor.Note: See Maximum Duty Cycle limits to determine allowable output voltages.。