卡带式羽叶除沫分离器用于醋酸醋酐项目废气洗涤塔除沫分离方案
含盐废水蒸发器浓缩器结晶器二次蒸汽除沫器采用羽叶除沫分离器方案

含盐废水蒸发器、浓缩器、结晶器二次蒸汽除沫器采用羽叶除沫分离器技术方案诺卫能源技术(北京)有限公司在石化企业生产运行中,会产生各种含盐废水。
企业和环保部门都希望对这些含盐废水进行处理回用。
废水中含有的盐类,往往采用对废水蒸发、浓缩、结晶等工艺过程进行处理,其二次蒸汽则往往需要回收热能并对凝结水进行回用。
含盐废水蒸发、浓缩、结晶设备产生的二次蒸汽,会携带大量溶解有盐类的液滴液沫,对后续热能回收和回用凝结水指标造成显著影响,因而选用抗盐析出结晶堵塞的羽叶式二次蒸汽高效除沫分离器,则成为近年来对传统丝网式除沫器技术升级换代趋势。
请大家结合自身企业蒸发器、浓缩器、结晶器装置二次蒸汽除沫器运行情况进行讨论和经验分享。
有的行业,比如制盐制碱企业生产过程,也需要对盐水进行蒸发浓缩结晶作业,且多采用真空蒸发浓缩结晶工艺,产生大量的二次蒸汽。
真空制盐企业的蒸发结晶器,往往采用多效蒸发器逐级逐步蒸发浓缩操作,前级蒸发器产生的二次蒸汽需要通过蒸气压缩机升压后用作为后续蒸发器提供热能。
有的化工企业,在生产过程中和反应中会副产大量盐水,也需要对这大量盐水进行蒸发浓缩结晶处理,副产固体盐以商品形式对外销售。
比如,不少采用肟化工艺的己内酰胺生产企业,生产过程中会副产大量硫酸铵盐。
数万吨硫酸铵盐,需要通过多效蒸发结晶器进行逐级蒸发、浓缩和结晶工艺,也多采用对前级蒸发器产生的二次蒸汽通过蒸气压缩机升压后,作为后续蒸发器热媒回用。
濒海项目和设备,往往采用海水淡化装置供水。
海水淡化工艺产生的大量含盐废水,也采用与上述类似的多效蒸发结晶器对含盐废水进行处理,二次蒸汽的循环利用工艺也基本相似。
除了含盐碱溶液的蒸发浓缩结晶处理装置会采用MVR多效蒸发结晶器及通过蒸汽压缩机压缩回用二次蒸汽,据了解,不少混合废酸的处理回用上也采用压缩机MVR多效蒸发浓缩器。
比如,一些精细化工企业烷基化装置、硝化、磺化装置,都会产生含水的混合废酸。
混合废酸可能含有硫酸、硝酸、磷酸等强酸和水,需要采取MVR蒸发浓缩方式对混酸进行循环回用。
羽叶除沫器分离器用于硫酸磷酸硝酸混合酸催化装置稀酸浓缩蒸发二次蒸汽分离技术方案

羽叶除沫器用于硫酸磷酸硝酸混酸催化装置稀酸浓缩蒸发二次蒸汽分离技术方案诺卫能源技术(北京)有限公司目前,硫酸/磷酸/硝酸混合二元或三元浓酸催化反应装置,尤其是环化脱水、羟胺化脱水等过程,会产生不少反应生成水逐渐稀释原来的浓酸体系,产生大量混合二元稀酸或三元稀酸。
不少企业把装置排放的混合稀酸直接用氨水中和得到铵盐溶液,再对铵盐稀液进行多级蒸发浓缩结晶制得固体铵盐,对外出售。
比如,己内酰胺装置排放的稀酸就用氨水中和,再经多效蒸发结晶获得固体硫铵副产品,对外销售。
但是,由于硫铵销路有限,价格较低。
而国外有的装置和工艺包,则将混合酸稀液直接通过蒸发浓缩系统进行脱水,获得浓度高的再生混合酸,用较少的发烟酸调和后重新进入反应装置回用。
上述两种混合稀酸处理方式,都涉及到蒸发浓缩装置用于蒸发脱水,或获得固体铵盐直接出售解决,或获得高浓度再生混酸直接回用装置;而解决脱除二次蒸汽携带的酸液沫和盐液沫问题却是共同面对的问题。
请朋友们结合自家蒸发脱水浓缩类似装置,介绍自家二次蒸汽的用途及其对应的二次蒸汽除沫技术,供大家分享提高。
客户己内酰胺装置副产的硫酸铵稀溶液,蒸发结晶浓缩所用的4台直径7600 mm多效蒸发结晶器二次蒸汽除沫采用的是,羽叶高效除沫分离技术内件。
羽叶除沫除雾分离内件,操作弹性大,不易被析出结晶集聚堵塞过流通道,效率高,运行稳定,特别是运行压降很低,尤适于盐碱类溶液减压蒸发场合。
据了解,华东一带不少蒸发器制造厂家还在使用丝网除沫器。
这类传统简易的除沫器用于盐碱类溶液减压蒸发结晶装置时,易于被气相析出的结晶物堵塞、腐蚀,造成运行压降不断升高,要求更高的釜温和热力蒸汽,让连续生产不易稳定维持。
客户硫酸和磷酸稀混酸浓缩蒸发器除沫器,也采用诺卫能源技术公司设计提供的羽叶除沫除雾分离内件组。
客户另一套硫酸磷酸混合稀酸浓缩蒸发工艺,也考虑用羽叶除沫除雾分离内件技术升级其原来的丝网除沫器。
客户的工艺工程师告诉诺卫能源技术公司,其蒸发器二次蒸汽气量大、气速高,温度在100℃左右,原来的丝网除沫内件使用寿命不长,断丝严重,除沫效率不稳定,二次蒸汽带酸太严重。
羽叶分离器用于苯制环己酮装置氧化单元驰放气分离技术升级改造方案

羽叶分离器用于苯制环己酮装置氧化单元驰放气分离技术升级改造方案诺卫能源技术(北京)有限公司罗力目前,国内采用石化精苯为原料制环己酮装置超过十数套。
而氧化单元是装置核心单元之一,事关产品收率和装置运行安全。
氧化装置需要通过驰放气排放积聚的惰性气,而从驰放气分离捕集回收驰放气携带的液滴状原料、半成品和目标产物,需要通过气液分离器来完成。
据统计,已经建成的十数套装置氧化单元驰放气气液分离器,绝大多数沿用丝网式除沫器作为驰放气分离器,其分离运行效率不稳定,运行压降高,易堵塞,非计划停车频发。
业主要求采用羽叶气液高效抗堵塞分离内件对原来丝网式除沫器壳体利旧,对丝网内件进行技术升级改造。
请从事该类装置的朋友们结合自身经历和经验进行讨论。
国内企业从精苯通过加氢、氧化、水合等过程生产环己酮始于上世纪后半叶。
最初,从事该装置工艺设计的单位不多,采用的工艺技术和装备水平,基本停留在上世纪80、90年代水平,工艺技术基本上属于拷贝。
目前的这十数套装置运行中,除却在其它技术贴中讨论过的烷醇酮与废碱液液分离问题,还有氧化单元驰放气气液分离问题困扰。
驰放气挟带的原料和产成品液滴量大,丝网内件运行压降高、堵塞,导致非计划停车频繁,生产效率和运行成本不理想,业主对此十分头疼。
近年来,有不少原来从事环己酮装置生产运行管理的技术人员,从原来单位出来,加入设计单位,以生产实操经验经历而对老工艺开展技术优化升级工作。
氧化单元驰放气液分离器升级改造动力,也有部分此类因素。
下图即为环己酮己内酰胺生产企业要求改造其令生产运行管理人员烦恼不已的原氧化单元驰放气丝网式分离器原图:上述丝网分离器,是由原来系统内设计单位技术设计的,国内还有好些类似情形设备。
前附图驰放气丝网分离器的运行条件如下:1、组成:氧气、氮气及其它有机气体;2、OP: 1Barg;3、OT:196℃;4、气相流量:4000.5Am^3/h;5、气相密度:4.09kg/m^3;6、气相粘度:0.021cp;7、液相流量:2000kg/h;8、液相密度:855.88kg/m^3;9、液相粘度:0.4cp。
环己酮装置尾气吸收塔采用羽叶分离器对丝网除沫器破沫器技术升级改造设计方案

环己酮装置尾气吸收塔采用羽叶分离器对丝网除沫破沫器技术升级改造设计方案诺卫能源技术(北京)有限公司罗力环己酮装置尾气吸收塔,是该装置中的核心设备之一,其设计水平高低及运行情况好坏,直接影响到整个装置收率高低,并影响到尾气焚烧排放系统是否正常达标运行。
有环己酮装置的朋友向我方寻求技术帮助采用羽叶分离器对其环己酮装置尾气吸收塔原来的丝网除沫器破沫器进行技术升级改造。
作为石化企业下游深加工装置项目之一,环己酮装置在国内已经有好几十套装置。
因此,我在这里专贴与大家一起就环己酮装置尾气吸收塔采用羽叶分离器对原来的丝网除沫器破沫器进行技术升级改造情况进行讨论分析。
环己酮装置的设计,国内就这么几家单位。
设计单位的设计水平及新技术新工艺的把握情况,就决定一套环己酮装置的技术工装水平、运行维护成本和项目经济效率和环保情况。
作为本帖实例进行讨论的这套环己酮装置,属于国内中上等规模能力。
讨论核心的这套环己酮装置尾气吸收塔,其流程图片如下:氧化尾气经过洗涤塔初步冷却分离后和来自环己烷蒸馏系统的含烷惰性气体混合,送往吸收塔的底部。
吸收塔釜泵把塔釜液送至吸收塔循环冷却器降温,送往塔中部。
环己酮和环己醇混合物下降经过填料床,吸收上升气体中的环己烷蒸汽。
尾气经过塔顶的破沫器后排往火炬总管高点放空,塔釜料由压力送至皂化单元。
环己酮高压装置吸收塔的作用,是利用环己酮和环己醇的混合液喷洒,以吸收来自氧化系统产生的含有饱和环己烷的氧化尾气。
环己酮和环己醇物流从醇脱氢系统提供,由吸收塔送料泵送往深冷器中冷却,然后进到吸收塔顶部。
附图是业主提供我方的原吸收塔图纸摘录:这套吸收塔由湖南的某公司设计。
全塔直径1600mm,设置两段散堆填料,上部高度5000mm(含分布填料);第二段高度4000mm(含分布填料)。
两段填料的两端分别使用200mm高度的250Y规整填料做为分布填料起到分布和支撑作用。
填料顶部原设置槽式液体分布器,各段床层之间采用收集式液体分布器对液体进行再分布。
催化裂化烟气脱硫脱硝装置洗涤烟气采用羽叶分离除雾除尘升级改造方案

催化裂化烟气脱硫脱硝装置洗涤烟气采用羽叶分离器除沫除尘升级改造方案诺卫能源技术(北京)有限公司罗力在催化裂化装置烟气脱硫脱硝处理工艺,甚至硫酸企业、冶金矿产、循环流化床燃煤锅炉热电等行业企业烟气脱硫脱硝处理工艺,多采用湿法流程。
国内外最为常用的湿法脱硫脱硝工艺包,往往是Exxon公司的WGS工艺包、Dupont-Belco 公司的EDV工艺包,还有国内对前述工艺消化组合而成的Turb-Venturi工艺。
孟山都/孟莫克的Dynamic Wave动力波工艺,是通过Dupont许可其EDV技术给孟山都推广而形成的工艺,与EDV工艺包本质相同。
上述工艺包在国内数十套装置上应用,但在执行国家新近出台最严苛环保排放标准上,仍需要进行把关环节的除沫除尘技术升级改造以满足最基本的避免“落雨”、粉尘超标排放要求。
下面,请大家一起讨论采用羽叶高效气液分离器除沫除尘升级改造。
为便于把有限精力和笔墨投放到重点关注的催化裂化装置烟气排放把关环节的除沫除尘要害节点上,这里对干法脱硝段不做重点讨论。
关于Exxon公司WGS工艺包,其主要包含文丘里钠碱反应吸收环节、洗涤塔直切入口气液固旋流预分离环节、洗涤塔内二次液固捕捉并与烟气深度分离环节和烟气拉拔排放环节等。
其流程简易流程如下图所示:在文丘里钠碱反应吸收环节,适当增加钠碱喷淋量和液气比,均可以实现对酸性气体的满意吸收;但是,钠碱喷淋量增加、液气比增加,不仅会增加运行费用,更会对下游洗涤塔直切入口气液固旋流预分离环节带来挑战,尤其是工艺上侧重于考虑管道压降而忽视直切入口管径与洗涤塔径比例不当造成的气液固旋流分离效率下降。
当直切入口管径与洗涤塔径比例过大,气液固分离效率将明显下降,导致烟气携带的液固负荷后窜,对后续深度紧密捕捉液固携带物造成巨大挑战,甚至堵塞后续分离内件组。
为此,我们在WGS流程图中红色标注点“1#”,采用专利技术流型流态矫正内件,恢复洗涤塔直切入口对气液固的预分离效率。
羽叶分离器用于液化天然气项目吸收塔进气分离器、出气分离器和再生塔尾气分离器设计方案

羽叶分离器用于天然气项目吸收塔进气、出气分离器和再生塔尾气分离器设计方案诺卫能源技术(北京)有限公司罗力在煤层气、焦炉气、管道天然气制LNG项目中,原料气通常需要采用MDEA 塔系吸收处理原料气中的酸性气体,这是对原料气净化处理的核心工序。
进塔原料气分离器(Feeding Gas Separator)、出塔净化气分离器(Outlet Gas Scrubber)和MDEA再生塔顶尾气气涤分离器(KO Drum),则是该工序的核心分离器。
正确选用和合理设计这类分离器,对LNG项目净化工序高效低成本运行有着重要影响。
对于LNG项目MDEA吸收塔原料气进气分离器(Feeding Gas Separator),其主要作用是脱除进塔原料气中携带的凝液,避免凝液进入MDEA吸收塔不断累积,尤其是液态烃类在MDEA吸收塔内聚集后会形成油包水或显著的油相层,阻碍原料气中的酸性气体与MDEA液相界面直接接触传质。
通过脱除进塔原料气水凝液,大大减轻原料气将水带入MDEA吸收塔,可以减小溶剂再生塔工作负荷,节省能耗。
对于LNG项目MDEA吸收塔出塔分离器(Outlet Gas Scrubber),其主要作用是脱除出塔净化气中携带的大量MDEA溶剂液滴液沫,避免MDEA溶剂从吸收塔逃逸进入下游管线和设备,既可以减小溶剂消耗,又可以防犯MDEA溶液在下游管线设备积聚形成液阻,以及导致设备运行故障。
对于LNG项目MDEA再生塔顶尾气分离罐(KO Drum),其主要作用是脱除出塔尾气携带的MDEA和轻烃等液滴液沫,避免这些液相进入下游管线和设备,一方面可以防犯液相在下游管线设备积聚形成液阻,以及导致设备运行故障;另一方面可以降低尾气后续处理费用。
关于LNG项目MDEA吸收塔原料气进气分离器(Feeding Gas Separator),在目前国内已经建成运行的项目中,有的采用卧式双筒式过滤聚结分离器型式,有的采用多因子旋流子母分离器型式,有的采用羽叶高效气液除沫除雾分离器,也有的采用纤维丝网式分离罐或重力沉降式分离罐,甚至有的早期项目没有设置原料气进塔分离罐。
羽叶分离除沫器用于硫铵(硫酸铵)混合酸多效蒸发结晶器二次蒸汽设计方案

羽叶分离除沫器用于硫铵(硫酸铵)混合酸多效蒸发结晶器二次蒸汽设计方案诺卫能源技术(北京)有限公司罗力朋友的企业在生产环节和三废处理过程中,产生大量硫酸铵稀液。
他们找到一家设计单位为其设计提供了系列多效蒸发器,对工厂产生的硫铵液进行分级浓缩结晶,副产硫铵外售。
但是,开车以来,各级蒸发结晶器顶采蒸汽挟带不少铵盐,导致其冷凝废水氨氮严重超标,废水处理单元严重超负荷运转,废水处理装置出水常常不能达标排放,很让人头疼。
据了解,多效蒸发结晶器在不少制盐、海水淡化、浓盐水处理、废水脱硫、己内酰胺生产废盐处理上较多应用,有的结晶器顶采蒸汽及其冷凝水带盐量控制也能较满意,有的企业的蒸发结晶器最初运行也不理想后来改造后也较满意。
请大家介绍谈谈自家蒸发结晶器如何防犯顶采蒸汽带盐的招数,帮帮我朋友的企业出出主意,降低其结晶器浓缩蒸气带盐量。
毕竟,行业都不太景气,如再加上环保排放问题,就雪上加霜。
硫酸铵稀液中是否有煤焦油、磷酸盐等杂质,这类杂质在蒸发结晶过程中要产生泡沫,泡沫占据了气相空间,导致蒸发结晶时,硫酸铵随着不凝气进入后序系统,导致蒸发冷凝液中有硫酸铵。
是否可考虑增加除沫器来解决此问题,但得注意除沫器堵塞,堵塞后的清理要方便。
必须增加除沫器,对蒸发结晶器顶采蒸汽进行雾沫捕集。
为了防犯硫酸铵液沫中的硫酸铵盐结晶析出附着在除沫器上,因此,除沫器设计组态和选型十分重要,还需要按照国外惯例设置双侧喷淋洗涤系统,以防犯万一有结晶附着情形下进行有效洗除。
国外采用的蒸发结晶器,无论是氯碱企业,还是其他类型制盐企业,都配置有专门设计的翅片式除沫器和按照规范设计的双侧喷淋洗涤系统。
此硫酸铵母液不起泡。
对于常规传统蒸发器,挟带是普遍问题,解决起来并不简单,也是不少蒸发器制造厂的头疼的问题。
仅考虑蒸发室的直径和高度,是传统的重力分离认识角度,按原来行业标准只能分离0.6微米以上液滴,不仅难以满足目前越加严格的环保要求,且设备尺寸和造价很高,从运行成本和设备采购成本上不具备技术经济性。
羽叶除沫器分离器用于含盐含高沸物废水多效蒸发器二次蒸汽除沫分离技术方案

羽叶除沫器分离器用于含盐含高沸物废水多效蒸发器二次蒸汽除沫分离技术方案诺卫能源技术(北京)有限公司最近,客户工厂用MVR多效蒸发结晶器处理含盐含有机高沸物废水。
由于废水含有有机高沸物,导致二次蒸汽产生不少泡沫,蒸汽挟带泡沫和液滴进入压缩机,造成二次蒸汽压缩机经常出问题。
工厂希望诺卫能源技术公司利用其羽叶除沫除雾分离器专利技术,在压缩机入口脱除蒸汽挟带的泡沫和液滴。
请使用过MVR多效蒸发器处理含盐废水的朋友,谈谈各自在含盐含有机高沸物等易发泡废水过程中发现的蒸汽中泡沫、含盐液滴液沫对蒸汽压缩机的危害,以及脱除蒸汽中有机泡沫、含盐液滴液沫的可行方案。
MVR工况是,运行温度,80~85℃;运行压力:-50kPaG;废水处理量,45T/h;废水含盐~10%,含发泡性高沸点有机物~0.5%。
出现的问题:二次蒸汽出口挟带不少泡沫及液体,进入二次蒸汽压缩机,造成压缩机带液且有盐在压缩机内析出,造成压缩机停车。
压缩机厂家的技术人员要求对压缩机入口蒸汽脱除泡沫、液滴液沫,干净蒸汽才能进入压缩机。
且,压缩机是按照原工艺要求的入口段吸入压力和排放段压力进行设计制造的,要求脱泡除沫装置总压降(包括自进口、含内件、到出口总压降)不超过2kpa。
操作弹性范围15~130%,定量分离效率4N级临界分离尺寸为5微米。
添加消泡剂的方式已经用过,运行维护费用太高,才不得不接受蒸汽压缩机厂家建议,选用羽叶除沫除雾分离器安装在压缩机入口脱除含盐液滴液沫和有机泡沫。
丝网式除沫器已被公司技术部门和压缩机厂家否定了。
主要原因是含盐蒸汽会有盐结晶析出在丝网上形成结晶硬块堵塞丝网,压降不断增大,除沫效率不断降低,并且需要经常检修更换丝网内件,维护工作量大。
工厂以前用过传统的丝网除雾网,吃过不少亏,很有心得。
现在,都在对丝网除沫器技术升级改造呢。
蒸发室已经够大的了,蒸发室直径7600mm,蒸发室净空高度8250mm。
这么大的蒸发室,蒸发器造价已经够高的了,单靠简单的重力沉降方式脱除液滴液沫和脱泡几乎没有效果的。
羽叶分离器用于变压吸附氢回收之进塔原气除沫设计方案

羽叶分离器用于变压吸附氢回收之进塔原气除沫设计方案诺卫能源技术(北京)有限公司从裂解气中采用变压吸附装置回收氢气,以及从焦炉气/高炉气分离回收氢气,都需要对进塔原气设置抗堵塞性能优异的高效气液除沫分离器。
从事PSA设计、制造的公司以及有PSA变压吸附装置运行的业主都知道,进入PSA装置的原料气除了对酸性气、硫、氧等指标有严格要求外,对原气带液量及携带的粘稠质,也有严格要求。
因此,必须在PSA进气管线上设置抗堵塞性能优异的高效气液分离除沫器。
在石化行业中,对于裂化氢气分离回收往往采用PSA装置。
而进塔原气,由于携带有不少C4+组份,有的业主原气中携带液量有时高达15%,且含有粘稠性降解物和催化剂破碎微小颗粒物。
对于PSA装置进塔的这类裂化氢气原气,其高效气液除沫分离器该选用采用哪些内件配置能满足装置超长周期稳定运行呢?本人根据实际项目设计经验,予以介绍。
这里列举一实例:1、工况温度:24.98 ℃;2、工况压力:5.50MPa(A);3、气相组成:(v%)CO, 9.59;H2, 73.16;CO2, 1.56;N2, 2.72;AR, 1.45;CH4, 8.69;C2H4, 0.71;C2H6, 1.48C3H6, 0.37C3H8, 0.08C4H8, 0.07C4H10, 0.02C5, 0.01C6, 0.04C7, 0.04C8+余量4、卖方应在设计中充分考虑原料气成分中C4+烃类浓度不稳定,导致原料气带液,最大带液量按照总质量流量的15%考虑。
5、内件材质:S30408由于进气带液量达到15%,远超过标准要求的3~5%,则在气液分离器内侧进料口末端强制性要求设置羽叶入口气液分离分布总成。
另外,需要顺便提请注意,对于真空工况气液分离器,由于气相流速很高,气相密度低,在标准中也强制要求在气液分离器内侧进料口末端强制性要求设置羽叶式入口气液分离分布总成。
由于原气携带有高碳粘稠质和破碎催化剂微小颗粒物,二级精密分离羽叶内件组不宜采用传统的纤维丝网式、滤芯式气液分离内件。
高盐废水盐水碱液多效蒸发浓缩结晶装置需要配置的专用羽叶分离除沫器技术方案
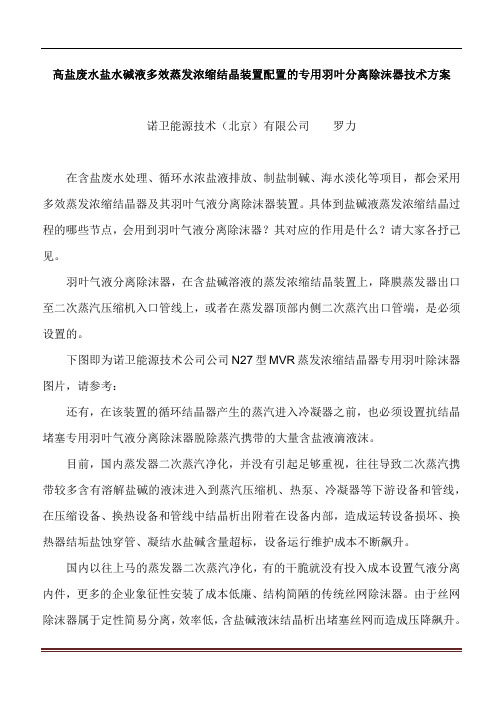
高盐废水盐水碱液多效蒸发浓缩结晶装置配置的专用羽叶分离除沫器技术方案诺卫能源技术(北京)有限公司罗力在含盐废水处理、循环水浓盐液排放、制盐制碱、海水淡化等项目,都会采用多效蒸发浓缩结晶器及其羽叶气液分离除沫器装置。
具体到盐碱液蒸发浓缩结晶过程的哪些节点,会用到羽叶气液分离除沫器?其对应的作用是什么?请大家各抒己见。
羽叶气液分离除沫器,在含盐碱溶液的蒸发浓缩结晶装置上,降膜蒸发器出口至二次蒸汽压缩机入口管线上,或者在蒸发器顶部内侧二次蒸汽出口管端,是必须设置的。
下图即为诺卫能源技术公司公司N27型MVR蒸发浓缩结晶器专用羽叶除沫器图片,请参考:还有,在该装置的循环结晶器产生的蒸汽进入冷凝器之前,也必须设置抗结晶堵塞专用羽叶气液分离除沫器脱除蒸汽携带的大量含盐液滴液沫。
目前,国内蒸发器二次蒸汽净化,并没有引起足够重视,往往导致二次蒸汽携带较多含有溶解盐碱的液沫进入到蒸汽压缩机、热泵、冷凝器等下游设备和管线,在压缩设备、换热设备和管线中结晶析出附着在设备内部,造成运转设备损坏、换热器结垢盐蚀穿管、凝结水盐碱含量超标,设备运行维护成本不断飙升。
国内以往上马的蒸发器二次蒸汽净化,有的干脆就没有投入成本设置气液分离内件,更多的企业象征性安装了成本低廉、结构简陋的传统丝网除沫器。
由于丝网除沫器属于定性简易分离,效率低,含盐碱液沫结晶析出堵塞丝网而造成压降飙升。
不少蒸发装置上采用的丝网除沫器由于堵塞和腐蚀,蒸汽压缩机把丝网撕裂而抽入压缩机内造成核心压缩设备受损严重,维护成本高昂。
诺卫公司针对近年来企业对蒸发器二次蒸汽净化提出技术升级要求,开发出N 系列和P系列蒸发器二次蒸汽专用羽叶除沫分离器。
N系列蒸发器二次蒸汽专用羽叶除沫分离器,主要应用于原有简易丝网除沫器指定安装结构和位置,对蒸汽除沫除盐净化提出中等要求的情形。
而P系列蒸发器二次蒸汽专用羽叶除沫分离器,主要应用于对蒸汽除沫除盐净化提出高要求的情形。
己内酰胺装置副产硫铵废液蒸发结晶器,包括一效结晶器、二效结晶器、三效结晶器和APU结晶器四套,其二次蒸汽净化均采用蒸发结晶器专用羽叶除沫分离器。
羽叶分离器除沫器在甲醇等改扩建项目中的内件升级设计和安装方案

羽叶分离器除沫器在甲醇等改扩建项目中的内件升级设计和安装方案诺卫能源技术(北京)有限公司在2005年以来,国内不少项目按照国外工艺包要求,在循环气压缩机进出口位置气液分离场合采用了羽叶分离器除沫器,比如甲醇合成项目、EO/EG项目、煤制油项目、合成气制乙二醇项目、丙烷脱氢项目、MTO/MTP项目。
现在,不少企业打算在原生产线基础上进行扩能或多条线并线改造,并利用原来的一套羽叶分离器来处理扩能后流量翻倍的气流处理。
为尽量降低改造成本,不少企业考虑对原来叶片式分离器壳体利旧使用,只对内件改造进行投入。
如何在原有安装内件的限制空间内,进行新内件组态设计与安装,请大家一同来讨论。
大家知道,在气液分离除沫场合采用动力学分离器,其在同等设备尺寸限制下的气流处理能力、操作弹性、分离效率、运行压降与运行稳定性、运行维护成本等方面,已经较丝网式、滤网式、膜网式、滤芯式、滤料式气液除沫分离器有很大进步。
不少企业现在开展的扩能改造,或则为了大幅提高产能而摊薄固定成本,或则将原来几条线上采用的丝网式和滤芯式等不同分离型式的气液分离除沫器并线到一起,打算让全部并线后的通过原来的动力学分离除沫器来处理,降低运行维护成本。
对原有动力学分离器的技术升级改造设计,不是简单的技术活。
当初,工艺包要求项目中的气液分离设备,采用综合性能具有明显优势的动力学分离器。
但是,动力学分离内件组的设计与制造成本,相对于原来国内企业普遍采用的简易丝网,要高出不少。
专业的动力学分离器设计方和制造方,正是利用动力学分离内件的组态性能优势,已经将原来动力学分离内件安装空间和分离器壳体内径优化到最低制造成本,从而在成本上大幅缩小与传统丝网式分离器的制造成本方得以被企业接受推广使用的。
在这些已经投用的动力学分离器中,不少属于中高压设备,且壳体采用耐腐蚀的不锈钢或内衬不锈钢材料制造,壳体制造成本超过内件成本,比如甲醇合成单元循环气甲醇分离器,业主在项目改扩建中考虑对该分离器壳体利旧,是理所当然的选择。
双氧水项目精馏装置原有丝网除沫器和折流板除沫器采用羽叶分离器技术升级改造技术方案

下图是双氧水项目产品脱重蒸馏装置专用羽叶分离器安装结构示意图:
下面详细介绍一下羽叶分离器各核心内件组情况: Item 1:预分配聚结内件组(可拆卸结构):配置 G50D 型预分配聚结内件组, SS316L。其作用有三: 其一,进一步对混合流体动能动量进行分配,使混合流体进入后续精密羽叶分 离内件组前具备动力学分离运行条件,确保后续精密羽叶分离内件组处于稳定高效 分离性能区间。 其二,在混合流体进入后续精密羽叶分离内件组之前,对混合流体携带的小微 尺寸重相携带质进行预聚结长大后以进入后续精密羽叶分离内件组深度脱除,保证 分离器产气质量更高。 其三,对后续精密羽叶分离内件组保护作用。在系统改造后运行之初,气流可 能携带的吹除后仍残留的铁屑或者催化剂破碎颗粒物,必须通过预分配聚结内件组 进行拦截保护。
3、从分离级数上看,羽叶分离器在气流通道上设置 4-6 级串行分离单元,任 何从上一级分离单元逃逸的液滴液沫,会被后续串行分离单元连续捕集分离,确保 尾气分离效率和高操作弹性。比如,在遇到某种波动工况情形下,导致第 1 级分离 单元分离效率下降到 85%,也即该单元释出气流中的液滴液沫逃逸率或残存率为 15%(即 100%-85%);气流经串联第 2 级分离单元捕集分离后,该单元气流中液 滴液沫总逃逸率或总体残存率则为 15%*15%;气流又经串联第 3 级分离单元捕集 分离,该单元气流中液滴液沫总体逃逸率或总体残存率则为 15%*15%*15%;气流 再经串联第 4 级分离单元捕集分离,该单元气流中液滴液沫总体逃逸率或总体残存
羽叶分离器,相对于传统结构的丝网除沫器和折流板除沫器,具有如下显著性 能优势:
1、从分离运行机制上看,羽叶分离器高效利用气流本身携带的动能、动量和液 滴表面自由能,协同发挥包括流体动量动能转换分离、矢量分离、聚结分离、表面 自由能捕集分离等多种分离手段,操作弹性大,运行压降低,分离效率稳定。
一种醋酸醋酐减压蒸馏分离装置[实用新型专利]
![一种醋酸醋酐减压蒸馏分离装置[实用新型专利]](https://img.taocdn.com/s3/m/6ad4c7bb85868762caaedd3383c4bb4cf7ecb7b0.png)
(10)授权公告号(45)授权公告日 (21)申请号 201420808741.8(22)申请日 2014.12.19C07C 51/573(2006.01)C07C 53/12(2006.01)(73)专利权人新乡瑞诚科技发展有限公司地址453000 河南省新乡市新乡县朗公庙镇曲水村北(72)发明人祁灿林 张卫勇(54)实用新型名称一种醋酸醋酐减压蒸馏分离装置(57)摘要本实用新型涉及一种醋酸醋酐减压蒸馏分离装置,它包括蒸馏塔,蒸馏塔的上部左侧设置进料管A 和进料管B,进料管A 和进料管B 的末端均设置喷头,蒸馏塔的上部右侧设置真空管,真空管连接真空罐,真空罐连接真空泵,蒸馏塔的顶部设置冷凝管A,冷凝管A 连接冷凝器A,冷凝器A 连接回收装置,蒸馏塔的底部通过法兰盘连接出料管,出料管连接脱色装置,脱色装置的底部通过三通管分别连接冷凝器B 和再沸器,冷凝器B 的端部设置阀门,再沸器的上部设置蒸汽进口,下部设置冷凝汽出口,再沸器的底部与三通管连接,顶部通过管道与蒸馏塔连接,本实用新型将醋酸和酸酐分离,回收醋酸,吸附杂质,不仅回收的酸酐纯度高,还节省了资源。
(51)Int.Cl.(19)中华人民共和国国家知识产权局(12)实用新型专利权利要求书1页 说明书3页 附图1页(10)授权公告号CN 204325196 U (45)授权公告日2015.05.13C N 204325196U1.一种醋酸醋酐减压蒸馏分离装置,它包括蒸馏塔,其特征在于:所述的蒸馏塔的上部左侧设置有进料管A和进料管B,所述的进料管A伸入蒸馏塔的长度比进料管B伸入蒸馏塔的长度长,所述的进料管A和进料管B的末端均设置有喷头,所述的蒸馏塔的上部右侧设置有真空管,所述的真空管连接有真空罐,所述的真空罐连接有真空泵,所述的蒸馏塔的顶部设置有冷凝管A,所述的冷凝管A连接有冷凝器A,所述的冷凝器A连接有回收装置,所述的蒸馏塔的底部通过法兰盘连接有出料管,所述的出料管连接有脱色装置,所述的脱色装置的底部通过三通管分别连接有冷凝器B和再沸器,所述的冷凝器B的端部设置有阀门,所述的再沸器的上部设置有蒸汽进口,下部设置有冷凝汽出口,所述的再沸器的底部与三通管连接,顶部通过管道与蒸馏塔连接。
醋酸裂解制醋酐装置回收工段共沸精馏塔及内件的设计

馏塔,塔顶气相物流(水、醋酸正丁酯)经冷凝后进入油水分离器分层,上层油相中含有大量的醋酸正丁酯和少量水全回流至塔顶。
分层器下层水相含少量共沸剂醋酸正丁酯,进入回收塔进行汽提。
由于醋酸正丁酯带水能力太强,为保证共沸剂与水形成共沸物,需从分层器下层水相补充少量分离水作为回流。
由于进料中含有裂解时生成的灰粉、胶质物,因此产品醋酸不能从塔釜采出,而是在再沸器返回口上几块塔板以气相采出,以确保醋酸的品质。
1.3 工艺模拟根据流程图及进料条件,采用通用的模拟软件进行共沸模拟计算,选用NRTL 方程,并根据文献数据修正热力学模型参数。
为确保回收醋酸的品质,不从塔釜采出醋酸,而是在塔下部侧线气相采出醋酸,侧线采出口设计在底部10层塔板之间。
根据相关工程案例采用42块理论版板,板效率取60%,实际塔板数70块,进料口在塔中间位置,模拟结果摘要如表1所示。
模拟结果的温度梯度与文献报道的基本一致[3]。
1.4 醋酸脱水共沸精馏塔的工艺特点无论是共沸精馏醋酸脱水塔还是简单精馏醋酸脱水塔,塔顶压力均维持在大气压左右。
但由于共沸精馏塔中加入了大量的共沸剂,塔顶温度(88℃)比简单精馏醋酸脱水塔塔顶温度(约100℃)降低了10℃左右。
另外,由于共沸剂的加入,共沸精馏醋酸脱水塔进料口以上醋酸与水的分离过程比简单精馏过程大大加速,共沸精馏醋酸脱水塔进料口以上所需的塔板数远远少于简单精馏醋酸脱水塔,而两种醋酸脱水塔进料口以下的分离0 引言醋酐是一种重要的化工原料,主要用于生产醋酸纤维素和农药、染料、香料等行业。
醋酐生产的方法主要有三种:醋酸热裂解、醋酸甲酯羰基合成法和乙醛氧化法[1]。
某新建醋酸裂解法生产醋酐装置生产过程中,从裂解工段、吸收工段会产生含有醋酸的废水。
废水流量2000kg/h ,其中含55%的醋酸、45%左右的水,同时含有少量的丙酮、醛类及灰粉。
醋酸/水体系相对挥发度不大,是典型的非理想体系,醋酸不仅在液相具有强的缔合作用,且其在汽相中的缔合效应也非常明显。
羽叶分离除雾器用于脱硫塔除沫器技术升级改造方案

羽叶分离除雾器用于脱硫塔除沫器技术升级改造方案诺卫能源技术(北京)有限公司罗力本技术贴针对羽叶分离除雾器用于石油和化工等行业传统脱硫塔除沫器技术升级改造技术方案探讨分析。
在石油炼化、天然气、化工、冶金、制药、环保等行业涉及到的各种脱硫塔、吸收塔所用的除沫器除雾器,从结构上看,往往有丝网纤维块结构、滤芯结构、折流板结构、旋流管结构、填料结构、羽叶分离结构等。
本技术贴以羽叶分离除雾器对传统的脱硫塔设置的填料和丝网除沫器技术升级改造实例进行剖析讨论。
本帖案例实际上是铜陵有色回转窑硫铁矿焙烧产生的高粉尘、高硫含量烟气脱硫塔除沫器技术升级改造,但业主显然对脱硫塔气液分离技术不甚了解而被湖南长沙的一家企业糊弄过。
当然,这也是最近几年的低价中标对业主的遗害。
这里索性先贴出这家湖南企业提供给业主的烟气脱硫塔及其除沫器的布置图以便讨论:富含粉尘和SOx的焙烧烟气,从烟气入口e进入脱硫吸收塔,自下而上进入A 区。
A区是压延孔板波纹规整填料层,烟气与自上而下的有机胺吸收液在此区域进行脱硫吸收。
烟气从A区向上穿进B区域。
B区是有机胺液喷淋洗涤区,由h管口喷入的有机胺液完成再次脱硫吸收。
烟气从B区向上穿进C区域。
C区是脱硫塔气液分离除沫除雾区域,净化后的烟气在脱硫吸收塔上部进行气液分离,然后从脱硫塔顶部烟气出口k排出塔外。
与常规脱硫吸收塔有所不同的是,这里在脱硫塔C区设置的除沫器包含高度450-500mm的PP散堆填料和150mm厚度的丝网除沫器。
但是,常常在波动工况下,脱硫塔顶部排出的烟气,夹带着不少有机胺液进入下游输气管线产生严重积液而严重影响烟气排送不畅,运行压降高,同时造成不少有机胺液损失,装置运行和维护费用也居高不下。
这也是铜陵有色在吃过湖南这家公司的苦头后打算再次技术升级改造的主要原因。
须知,任何气液分离技术,除沫除雾技术,均属于动力学分离技术,不能像国内外不少公司仅凭经验“大概+估计”“拍脑袋”或者“依葫芦画瓢”往往造成装置严重后果。
化工过程模拟与优化课程设计报告 醋酸酐生产过程概念设计

化工过程模拟与优化课程设计报告醋酸酐生产过程概念设计指导老师:钱宇教授陆恩锡教授学生:周亮专业:化学工程2001年5月15日1 .过程设计分析1.1 醋酸酐的相关信息醋酸酐(又称乙酸酐,简称醋酐)为无色易流动液体,有极强的醋酸气味。
有刺激作用。
相对密度(d415)1.080,熔点-73℃,非点139℃,折光指数(20℃)1.3904,水中溶解度(20℃)12%。
易燃烧,遇水分解成醋酸。
溶于乙醇、乙醚、苯和氯仿。
醋酸酐(又称乙酸酐,简称醋酐)是一种重要的有机化工原料,主要用于制造醋酸纤维、醋酸塑料、不燃性电影胶片及人造丝等化工产。
在医药工业中用于制造阿司匹林、合霉素、地巴唑等药物。
此外,在燃料,香料及化工生产中用作强乙酰化剂和脱水剂。
我国从50年代末期开始生产醋酸酐。
上海试剂一厂采用乙酰氧化法首先建成了我国第一套醋酸酐生产装置。
随后,南通醋酸化工厂、山东新华制药厂、吉化公司电石厂等相继建设了十几套生产装置。
1972年合成醋酸酐产量突破万吨达到1.03万吨,1980年为1.43万吨,92年增长到4.04万吨,目前年产量超过7万吨,供需基本持平。
中华人民共和国国家标准GB10668-891.2醋酸酐生产过程的分析1.2.1 醋酸酐的生产方法醋酸酐的各种生产方法示意图:其中最常用的主要工业生产方法有醋酸法、丙酮法、乙醛法等。
本设计拟采用丙酮法进行醋酸酐的生产设计。
丙酮在700~800℃,常压、没有催化剂的条件下进行裂解反应,反应停留时间0.s。
裂解反应管的结焦比乙酸法严重,为了防止结焦,主要采用高铬钢管材,如用含镍钢材,应事先用一氧化碳和氧气混合物进行钝化处理,以防元素镍对结焦的促进作用。
本法丙酮的转化率约为24.4%,生成乙烯酮的选择性为72%,反应信息如下:主反应:CH3CO CH3CH2=C=O+ CH4700℃,1atm;副反应: CH2=C=O CO + 1/2 CH2=CH2700℃,1atm;主反应:CH2=C=O + CH3COOH (CH3CO)2O 80℃,1atm 1.2.2 醋酸酐产品分离过程分析由前面反应可知,在醋酸酐的合成过程中,由于丙酮转化不完全、副反应产物的存在和未反应完全醋酸的存在,必须对反应产物进行分级分离。
顺酐行业废气治理新手段
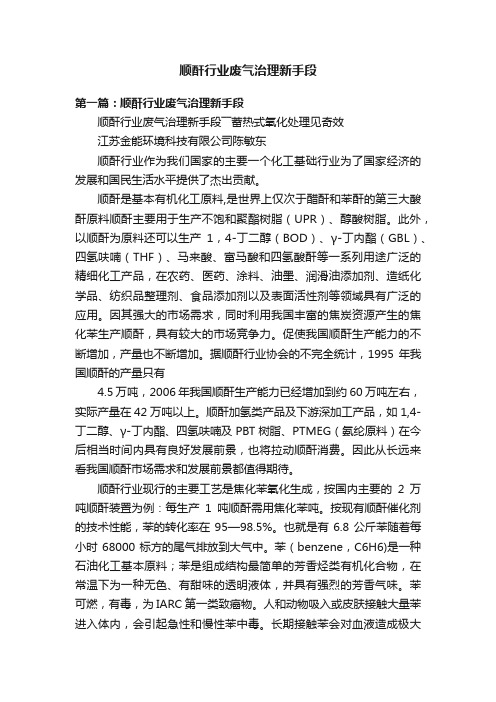
顺酐行业废气治理新手段第一篇:顺酐行业废气治理新手段顺酐行业废气治理新手段――蓄热式氧化处理见奇效江苏金能环境科技有限公司陈敏东顺酐行业作为我们国家的主要一个化工基础行业为了国家经济的发展和国民生活水平提供了杰出贡献。
顺酐是基本有机化工原料,是世界上仅次于醋酐和苯酐的第三大酸酐原料顺酐主要用于生产不饱和聚酯树脂(UPR)、醇酸树脂。
此外,以顺酐为原料还可以生产1,4-丁二醇(BOD)、γ-丁内酯(GBL)、四氢呋喃(THF)、马来酸、富马酸和四氢酸酐等一系列用途广泛的精细化工产品,在农药、医药、涂料、油墨、润滑油添加剂、造纸化学品、纺织品整理剂、食品添加剂以及表面活性剂等领域具有广泛的应用。
因其强大的市场需求,同时利用我国丰富的焦炭资源产生的焦化苯生产顺酐,具有较大的市场竞争力。
促使我国顺酐生产能力的不断增加,产量也不断增加。
据顺酐行业协会的不完全统计,1995年我国顺酐的产量只有4.5万吨,2006年我国顺酐生产能力已经增加到约60万吨左右,实际产量在42万吨以上。
顺酐加氢类产品及下游深加工产品,如1,4-丁二醇、γ-丁内酯、四氢呋喃及PBT树脂、PTMEG(氨纶原料)在今后相当时间内具有良好发展前景,也将拉动顺酐消费。
因此从长远来看我国顺酐市场需求和发展前景都值得期待。
顺酐行业现行的主要工艺是焦化苯氧化生成,按国内主要的2万吨顺酐装置为例:每生产1吨顺酐需用焦化苯吨。
按现有顺酐催化剂的技术性能,苯的转化率在95—98.5%。
也就是有6.8公斤苯随着每小时68000标方的尾气排放到大气中。
苯(benzene,C6H6)是一种石油化工基本原料;苯是组成结构最简单的芳香烃类有机化合物,在常温下为一种无色、有甜味的透明液体,并具有强烈的芳香气味。
苯可燃,有毒,为IARC第一类致癌物。
人和动物吸入或皮肤接触大量苯进入体内,会引起急性和慢性苯中毒。
长期接触苯会对血液造成极大伤害,引起慢性中毒。
引起神经衰弱综合症。
醋酸尾气膜分离纯化装置工艺操作规程

醋酸尾气膜回收纯化装置工艺操作规程1 适用范围本规程适用于造气车间净化岗位醋酸尾气膜回收纯化装置2装置概况说明本普里森膜纯化装置利用醋酸尾气各气体组分在高分子聚合物中的溶解扩散速率不同而进行分离,渗透气(富氢气)直接排放至火炬,非渗透气(主要为CO)经压缩机升压后送至醋酸岗位。
3产品说明3.1 产品气的质量标准:CO纯度>91%3.2 产品用途产品精制气主要用于后工序合成醋酸。
4生产工序说明原料气规格压力:2.8MPa 温度:40℃将醋酸高压吸收塔尾气通过管道输送至膜回收纯化装置膜分离技术说明:膜分离的基本原理就是利用各气体组分在高分子聚合物中的溶解扩散速率不同,因而在膜两侧分压差的作用下导致其渗透通过纤维膜壁的速率不同而分离。
推动力(膜两侧相应组分的分压差)、膜面积及膜的分离选择性,构成了膜分离的三要素。
依照气体渗透通过膜的速率快慢,可把气体分成“快气”和“慢气”。
常见气体中,H2O、H2、 He、H2S、CO2等称为“快气”;而称为“慢气”的则有的CH4及其它烃类、N2、CO、Ar等。
普里森膜分离器的外壳类似一管壳式换热器,内装数万根细小的中空纤维丝。
中空纤维的优点就是能够在最小的体积中提供最大的分离面积,使得分离系统紧凑高效,同时可以在很薄的纤维壁支撑下,承受较大的压力差。
混合气体进入膜分离器壳程后,沿纤维外侧流动,维持纤维内外两侧适当的压力差,则气体在分压差的驱动下,“快气”(氢气)选择性地优先透过纤维膜壁在管内低压侧富集而作为渗透气导出膜分离系统,送至火炬;渗透速率较慢的气体(烃类、CO、N2)则被滞留在非渗透气侧,压力几乎跟原料气的相同,经压缩机增压后送出界区。
本装置设计有一个联锁导流阀门(DV-101)。
在开车期间或联锁动作情况下,将加热后的原料气与膜分离器隔离,从而保护膜分离器。
5工艺流程叙述膜分离的工艺分为预处理(过滤和加热)和膜分离两部分。
预处理稳定流量的醋酸尾气通过管道输送至108膜回收装置区域,进入洗气塔T101,在塔内与塔顶下来的除盐水逆向接触,将气体中夹带的醋酸部分吸收分离后进入洗气塔T102,在塔内与塔顶下来的酸水逆向接触,充分吸收尾气中的醋酸,经洗气塔洗涤过的高压尾气经过除雾器,将可冷凝的液沫雾滴捕集形成液体后排出,再经过联合过滤器进一步将气体中的较小级别的液滴或固体颗粒分离,接着通过列管加热器用低压蒸汽加热至40℃,使原料气远离露点,并恒定膜分离系统的操作温度,通过蒸汽流量调节阀和温度变送器实现原料气温度的控制、指示、报警和联锁,然后经过过滤器X102后最终进入膜分离装置。
- 1、下载文档前请自行甄别文档内容的完整性,平台不提供额外的编辑、内容补充、找答案等附加服务。
- 2、"仅部分预览"的文档,不可在线预览部分如存在完整性等问题,可反馈申请退款(可完整预览的文档不适用该条件!)。
- 3、如文档侵犯您的权益,请联系客服反馈,我们会尽快为您处理(人工客服工作时间:9:00-18:30)。
卡带式羽叶分离器用于醋酸醋酐项目废气洗涤塔除沫分离方案
诺卫能源技术(北京)有限公司
在醋酸、醋酐装置废气处理单元,往往采用洗涤塔洗涤吸收方式洗脱废气中携带的醋酸。
而洗涤塔顶排放尾气,则必须采用卡带式羽叶分离器,以脱除排放气携带的含酸液滴液沫。
请大家结合自身醋酸醋酐装置废气处理装置所采用的气液除沫分离器技术使用情况和运行情况进行讨论。
近年来,化工装置废气排放标准执行日趋严格,要求化工企业在废气处理上下足功夫找到货真价实的环保公司采用货真价实的废气处理技术设备,用于化工装置废气处理。
醋酸、醋酐装置产生的废气处理更不例外。
然而,在废气处理行业,拥有货真价实的废气处理技术设备的环保企业,并非俯首即拾。
比如,华东某一醋酸生产企业在其排放废气处理环节,就曾通过上海一家环保公司提供洗涤塔及其自行配套尾气除沫器来处理工厂废气。
结果,洗涤塔排放的尾气挟带不少含酸液滴液沫,对周边造成明显污染。
当地环保部门要求工厂进行整改。
这家上海环保企业最初为业主提供的洗涤塔顶除沫器,是传统简易丝网式除沫器。
由于洗涤塔尾气外排压力几乎接近大气压,而起初的丝网除沫器运行压降过大,导致尾气憋在塔内排气不畅。
这家供应商又换上一种堆密度降低不少的非标丝网,压降倒是降下来了,但排放尾气挟带明显含酸液滴飘落周边。
且随着运行时间不断增加,丝网除沫器不断腐蚀断丝,排放尾气中含酸液滴飘落越发严重。
于是,上海这家环保公司又通过华东一家除沫器制造厂提供了一套折流板除沫器替换掉丝网除沫器。
但是,业主反映当地环保局检测结果说,排放尾气携带的酸性液滴量没有改善。
确实也有好些业主反馈,他们有的装置上的气液除沫分离内件,从最初采用丝网式,到后来丝网腐蚀支离破碎,再后来换成雪弗龙折流板,都感觉其出口气相中的液滴液沫含量没有多大变化,似乎哪种技术层级的气液除沫分离内件对其除沫分离效果不大。
其实,这些业主朋友们看到的只是表象。
气液除沫分离效果好坏,不仅要看采用的内件型式,更要看其是否通过精准动力学分离设计系统平台获得准确可靠的设计组态结果。
国内除沫器供应商和高校,在5-10年中短期内难以搭建精准的动力
学分离计算设计精准平台系统,其多采用“大概加估计”、拍脑袋方式得出的所谓技术方案和造价。
没有通过精准动力学分离设计系统平台获得准确可靠的设计组态结果,就无法对气液除沫分离实际运行效果提供准确性和可靠性保障。
业主装置上的气液除沫分离内件,很可能从一开始采用丝网,到后来丝网破碎不用,再后来采用的雪弗龙折流板等,都是“大概加估计”“拍脑袋”出来的方案。
虽然有除沫内件东西放在那儿,但自始至终没有发挥明显除沫分离效果。
转件形成一种错觉,有没有都无所谓,习以为常。
实际上,必要的高效气液除沫分离内件十分重要,否则,国内外工艺包也不会在上述节点做出明确的技术要求。
气液分离除沫技术,属于精准动力学分离技术,必须通过精准动力学分离设计系统平台获得准确可靠的设计组态结果,并以此为依据进行内件制造。
并不是选择一种除沫分离内件装进去,就能发挥明显除沫分离效果。
事实上,即便采用最先进的羽叶分离内件组,也必须通过精准动力学分离设计系统平台获得准确可靠的技术方案和精准的组态结构型式作为基本前提条件。
否则,
没有通过精准动力学分离设计系统平台获得完善的技术方案和精准的组态结构型式作为基本前提条件,即便采用黄金打造的内件,也一样形同虚设!
这就是不少业主试用过各类除沫分离内件,却得出除沫分离效果差异不明显的原因所在。
这家环保企业费尽周折,找到我方求助。
这家醋酸装置废气洗涤塔塔顶排放尾气工况如下:
1、运行温度:65℃;
2、运行压力:1.08BarA;
3、尾气排放量:136500kg/h;
4、气相密度:1.05kg/m^3;
5、工况气相粘度:0.019cp;
6、预估气相带液量:1200kg/h;
7、液滴工况密度:980kg/m^3.
鉴于洗涤塔尾气排放压力很低,处理气量较大,且挟带液滴含有醋酸需要及时排净,我方向客户推荐使用卡带式羽叶分离器。
通过NOVEL公司精准动力学气液分离过程计算设计系统平台完成的准确可靠的G50型卡带式羽叶分离器性能参数如下:
1、尾气除沫器类型:G50型羽叶分离器;
2、内件组态形式:羽叶卡带式;
3、运行压降:不超过0.009Bar;
4、分离效率:4N级分离脱除5.82微米及以上尺寸液滴液沫;
5、操作弹性:15%-130%;
6、设备材质:SS316L。
关于卡带式羽叶分离器更多技术信息,请登录诺卫分离技术专网进行了解并直接与NOVEL北京公司联系咨询。