冲压模具细部设计检查表
合集下载
冲压模具定期点检表
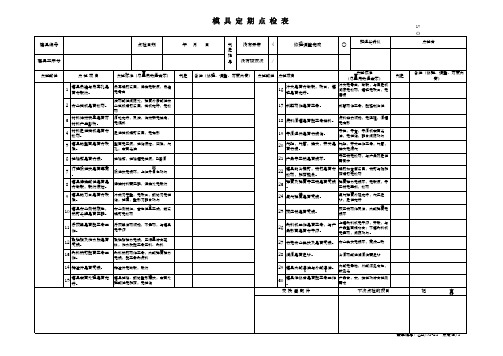
具的各镙钉,销钉是否有 螺钉加套筒紧固,销钉与防脱 落螺钉无松动 松动,脱落现象。 弹簧及弹簧导正销是否受损 弹簧弹力无损坏,无裂痕,导 正销无歪斜,松动 。
氮气弹簧外观完好,气压足 够,定位完好 预压销动作灵活,内部弹簧无 损坏 上模卸料板无干涉,开裂,与
24 氮气弹簧是否受损。 25 预压销是否受损。
模具维修后是否能正常工作 产品首,末,抽检均符合检测 要求 。
交换零部件
下次点检的项目
记 事
表单编号:QR751-21 版本:B/1
NO 修理调整完成 ○
班组长确认 点检者
点检日期
年 月 日
判 定 记 号
没有异常 没有该项次
√
/
点检标准 (尽量用数值表示) 判定 备注(修理、调整、对策内容)
判定
备注(修理、调整、对策内容)
点检部位 点检项目
冲头无弯曲,断裂,与固定板 冲头是否有断裂,缺口,模 间隙无松动,模钮无缺口,无 16 钮是否完好。 磨损
11 12 13
26
卸料板工作是否正常,与产 产品型面相吻合;下模卸料板 品形面是否有干涉。 无晃动,间隙均匀。
27 有无安全垫块及是否受损。 安全垫块无损坏,高度一致 28 润滑是否足够。 29 模具内部清洁与外部清洁。 30
各滑动部位润滑油要足够 内部无异物,外部漆见本色, 铁见光
14 铸造件是否受损。 15 模具表面处理是否完 好。
模 具 定 期 点 检 表
模具编号 模具工序号
点检部位 1 点检项目 模具吊棒与吊耳孔是 否有裂纹。 点检标准(尽量用数值表示)
吊耳螺钉紧固,焊接无裂痕,吊棒 无弯曲 活动部位间隙处,弹簧外露部位安 全档板螺钉紧固,档板完好,无松 动 滑轮完好,灵活,传送架无棱角, 无偏斜 定位挡板螺钉紧固,无变形 型面无压痕,拉伤痕迹,凹陷,气 孔,表面光洁 拉延筋,拉延槽无拉痕,R圆滑 限位块无损坏,上红丹着色均匀 焊接材料要匹配,焊接处无裂纹 冲裁刃平整,无缺口,翻边刃无拉 伤,拉薄,整形刀配合均匀 安全侧销红,黄色位置正确,锁紧 螺钉无松动 浮顶器活动顺畅,不晃动,与模具 无干涉 聚胺脂弹力无损,压缩量符合规 格,优力胶能正常压料、卸料 卸料销钉动作正常,内部弹簧弹力 无损,能正常卸废料 铸造件无断裂,裂纹 模具拉延、翻边整形镶块,表面处 理部位无脱落,无拉伤
氮气弹簧外观完好,气压足 够,定位完好 预压销动作灵活,内部弹簧无 损坏 上模卸料板无干涉,开裂,与
24 氮气弹簧是否受损。 25 预压销是否受损。
模具维修后是否能正常工作 产品首,末,抽检均符合检测 要求 。
交换零部件
下次点检的项目
记 事
表单编号:QR751-21 版本:B/1
NO 修理调整完成 ○
班组长确认 点检者
点检日期
年 月 日
判 定 记 号
没有异常 没有该项次
√
/
点检标准 (尽量用数值表示) 判定 备注(修理、调整、对策内容)
判定
备注(修理、调整、对策内容)
点检部位 点检项目
冲头无弯曲,断裂,与固定板 冲头是否有断裂,缺口,模 间隙无松动,模钮无缺口,无 16 钮是否完好。 磨损
11 12 13
26
卸料板工作是否正常,与产 产品型面相吻合;下模卸料板 品形面是否有干涉。 无晃动,间隙均匀。
27 有无安全垫块及是否受损。 安全垫块无损坏,高度一致 28 润滑是否足够。 29 模具内部清洁与外部清洁。 30
各滑动部位润滑油要足够 内部无异物,外部漆见本色, 铁见光
14 铸造件是否受损。 15 模具表面处理是否完 好。
模 具 定 期 点 检 表
模具编号 模具工序号
点检部位 1 点检项目 模具吊棒与吊耳孔是 否有裂纹。 点检标准(尽量用数值表示)
吊耳螺钉紧固,焊接无裂痕,吊棒 无弯曲 活动部位间隙处,弹簧外露部位安 全档板螺钉紧固,档板完好,无松 动 滑轮完好,灵活,传送架无棱角, 无偏斜 定位挡板螺钉紧固,无变形 型面无压痕,拉伤痕迹,凹陷,气 孔,表面光洁 拉延筋,拉延槽无拉痕,R圆滑 限位块无损坏,上红丹着色均匀 焊接材料要匹配,焊接处无裂纹 冲裁刃平整,无缺口,翻边刃无拉 伤,拉薄,整形刀配合均匀 安全侧销红,黄色位置正确,锁紧 螺钉无松动 浮顶器活动顺畅,不晃动,与模具 无干涉 聚胺脂弹力无损,压缩量符合规 格,优力胶能正常压料、卸料 卸料销钉动作正常,内部弹簧弹力 无损,能正常卸废料 铸造件无断裂,裂纹 模具拉延、翻边整形镶块,表面处 理部位无脱落,无拉伤
冲压模具点检表
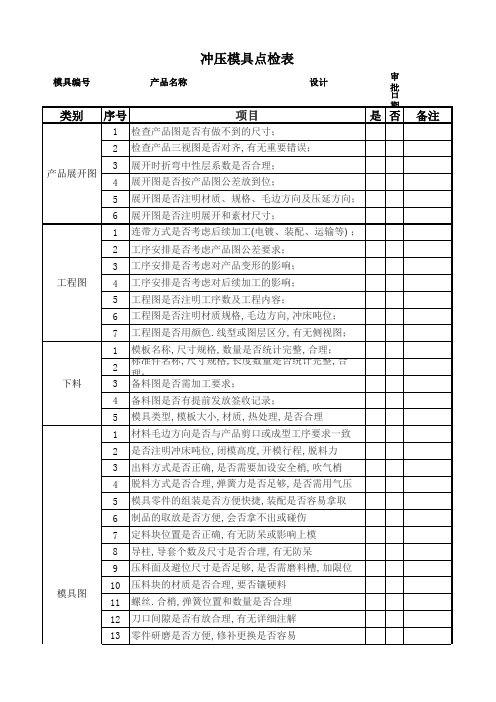
冲压模具点检表
模具编号 产品名称 设计 审批 日期
类别
序号
1 2 3 4 5 6 1 2 3
项目
检查产品图是否有做不到的尺寸; 检查产品三视图是否对齐, 有无重要错误; 展开时折弯中性层系数是否合理; 展开图是否按产品图公差放到位; 展开图是否注明材质、规格、毛边方向及压延方向; 展开图是否注明展开和素材尺寸; 连带方式是否考虑后续加工(电镀、装配、运输等) ; 工序安排是否考虑产品图公差要求; 工序安排是否考虑对产品变形的影响; 工序安排是否考虑对后续加工的影响; 工程图是否注明工序数及工程内容; 工程图是否注明材质规格, 毛边方向, 冲床吨位; 工程图是否用颜色. 线型或图层区分, 有无侧视图; 模板名称, 尺寸规格, 数量是否统计完整, 合理; 标准件名称, 尺寸规格, 长度数量是否统计完整, 合 理; 备料图是否需加工要求; 备料图是否有提前发放签收记录; 模具类型, 模板大小, 材质, 热处理, 是否合理 材料毛边方向是否与产品剪口或成型工序要求一致 是否注明冲床吨位, 闭模高度, 开模行程, 脱料力 出料方式是否正确, 是否需要加设安全梢, 吹气梢 脱料方式是否合理, 弹簧力是否足够, 是否需用气压 模具零件的组装是否方便快捷, 装配是否容易拿取 制品的取放是否方便, 会否拿不出或碰伤 定料块位置是否正确, 有无防呆或影响上模 导柱, 导套个数及尺寸是否合理, 有无防呆 压料面及避位尺寸是否足够, 是否需磨料槽, 加限位 压料块的材质是否合理, 要否镶硬料 螺丝. 合梢, 弹簧位置和数量是否合理 刀口间隙是否有放合理, 有无详细注解 零件研磨是否方便, 修补更换开图
工程图
4 5 6 7 1 2
下料
3 4 5 1 2 3 4 5 6 7 8 9 10 11 12 13
模具编号 产品名称 设计 审批 日期
类别
序号
1 2 3 4 5 6 1 2 3
项目
检查产品图是否有做不到的尺寸; 检查产品三视图是否对齐, 有无重要错误; 展开时折弯中性层系数是否合理; 展开图是否按产品图公差放到位; 展开图是否注明材质、规格、毛边方向及压延方向; 展开图是否注明展开和素材尺寸; 连带方式是否考虑后续加工(电镀、装配、运输等) ; 工序安排是否考虑产品图公差要求; 工序安排是否考虑对产品变形的影响; 工序安排是否考虑对后续加工的影响; 工程图是否注明工序数及工程内容; 工程图是否注明材质规格, 毛边方向, 冲床吨位; 工程图是否用颜色. 线型或图层区分, 有无侧视图; 模板名称, 尺寸规格, 数量是否统计完整, 合理; 标准件名称, 尺寸规格, 长度数量是否统计完整, 合 理; 备料图是否需加工要求; 备料图是否有提前发放签收记录; 模具类型, 模板大小, 材质, 热处理, 是否合理 材料毛边方向是否与产品剪口或成型工序要求一致 是否注明冲床吨位, 闭模高度, 开模行程, 脱料力 出料方式是否正确, 是否需要加设安全梢, 吹气梢 脱料方式是否合理, 弹簧力是否足够, 是否需用气压 模具零件的组装是否方便快捷, 装配是否容易拿取 制品的取放是否方便, 会否拿不出或碰伤 定料块位置是否正确, 有无防呆或影响上模 导柱, 导套个数及尺寸是否合理, 有无防呆 压料面及避位尺寸是否足够, 是否需磨料槽, 加限位 压料块的材质是否合理, 要否镶硬料 螺丝. 合梢, 弹簧位置和数量是否合理 刀口间隙是否有放合理, 有无详细注解 零件研磨是否方便, 修补更换开图
工程图
4 5 6 7 1 2
下料
3 4 5 1 2 3 4 5 6 7 8 9 10 11 12 13
冲压模具检查记录表范例
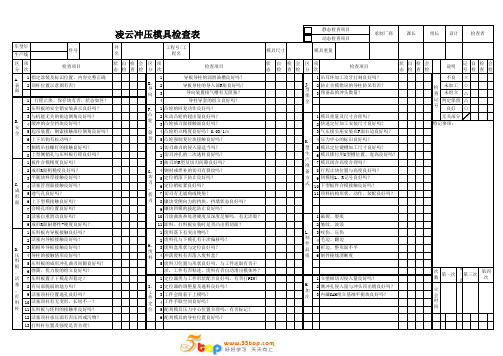
3 预备品的冲头数量?
全
1 模具重量及尺寸合理吗?
2 快速定位加工安装尺寸良好吗?
3 气压接头座安装在F面右边良好吗?
K. 4 压力中心的标识良好吗? 型 5 模具定位键槽加工尺寸良好吗?
生 6 模具锁付用U型槽位置、宽高良好吗?
产 准
7 模具闭合高度合理吗?
备 8 行程止块位置与高度良好吗?
方 9 闭模钮L、R记号良好吗? 式 10 下型板件合模接触良好吗?
12 活塞顶杆承压面有否压凹或污物?
13 打料杆位置及强度是否合理?
1 E. 2 导 向3
4
导板导柱的润滑油槽良好吗? 导板导柱的导入部R角良好吗?
导向装置排气槽有无阻塞? 导柱导套的组立良好吗?
F. 1 凸轮的回复动作良好吗?
凸 2 从动凸轮的超出量良好吗?
轮 、
3 凸轮插刀面接触面良好吗?
斜 4 凸轮组立精度良好吗?0.03/1m
凌云冲压模具检查表
静态检查项目 动态检查项目
承制厂商
课长
组长 设计
检查者
车型年 生产线
件号
件 名
工程号/工 程名
模具尺寸
模具重量
区项 分次
检查项目
状自检会 区项 态检查检 分次
检查项目
状 自 检会 区项 态 检 查检 分次
检查项目
状自检会 态检查检
说明
记自检会 号检查检
A. 1 指定涂装及标识位置、内容完整正确 表 2 顶杆位置示意图有否? 面
11 顶料机构形状、动作、装配良好吗?
1 破裂、裂痕
2 皱纹、波浪
L. 3 咬伤、压伤 制 4 毛边、翻边 件 品 5 折边、整形面不平 质 6 制件棱线清晰度
冲压模具检查表

10 凹模镶块及废料刀的空刀部分与铸件安装面平齐 11 保证刃口的切入量(有效刃口高度≥8mm)空刀1-2mm 12 压料板、顶出器与凹模镶块间隙<0.5mm,没有油污和刮痕 淬火后模具刃口部位硬度符合图纸要求,不允许有软点、烧伤及 13 裂纹 14 异形凹模及带形状处凹模应有防转装置,并符合图纸要求 15 镶块与窝座、止退键之间不能有间隙 16 凸模的废料刀刃口高度应低于凸模刃口的高度≥4mm 17 凸模废料刀的宽度应符合图纸(冲压件宽+10mm) 18 相邻处的凹模刃口与废料刀刃口相接触的高度应低于t+4mm 19 反侧类模具,接触面深确保进入20mm后工作,接触面无间隙 1 2 3 斜锲的固定应符合图纸,检查定位销松紧及挡块的贴合情况 回程键和回程钩起始部位的圆角及安装应符合图纸 斜锲滑动面的间隙<0.03mm 斜锲弹簧应有预压缩,复位良好 滑动压板的间隙<0.03mm以下无摆动 暴露的斜锲弹簧或其它弹顶器,均应有安全护板 安 装 部 分
斜 锲
其 它
4 5 6
顶出器及活动部位须加装防护板 模块重量超过15公斤时应设起重孔,孔位确保起吊时模 3 块保持平衡 气缸与托料杆之间的连接部分要安全、牢固,运动时平 4 稳 5 平衡块安装面应设有加强筋 U形槽的厚度、宽度、个数、位置及托杆孔位置误差≤ 6 ±0.5mm 7 螺纹深度,应符合图纸和国标要求,同时满足强度要求 翻转孔、起重孔,孔径、孔距应符合图纸(应能满足强 8 度要求) 侧销应保证在3根以上,并应使限位板开口向下,锁板 9 厚度5.0mm,要求用2-M10螺钉紧固 10 在存放状态时,应确保导柱或导板的配合量≥40mm 1 气源固定装置及管接规格是否符合图纸 进气、出气管接头应用颜色来区分,进气红色,出气兰 色,软管应夹头固定不能悬空、缠绕及破裂 2 所有调整垫片的大小应合适,并固定在底板上 3 模具应清洗(模具无切屑、废料、油污、红丹粉等) 4 模具加工基准必须保留,并在底板上刻印出坐标值 铭牌的安装、底板铸字区标识(F标识、送料方向箭头 5 、图号、材料)及镶块的图号、材料与底板安装座对应 的件号 6 模具非工作部位倒角2X45° 模具所有部位须按规定色、涂色,涂色要求参照技术 7 协议
中日文冲压模具检查表
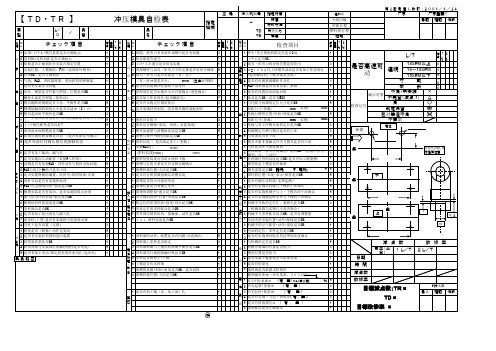
5 mm
3
4 机械侧定位销与模具是否有干涉
3
取 5 与设备是否有干涉
5
L/T
是否高速可 动
連続
18SPM以上 16~18SPM 15SPM以下
寸 動
中 断
减点对象
不良・未安装 不完全(減点 1)
× △
检查记号
良 判定保留
○
○保
已对策但不良
○
不要紧
定位
换模
減1 2 点 L/ L/
TT
0
-
TD
板厚 材料寸法 气垫压力
夹紧内幅 夹紧行程 弹料块行程
承認 確認 作成
TR 模高
送距
分N 类o
检查项目
1 冲头・导正销座的销定位是否2处
減自 1 2 点 主 L/ L/
TT
1
(中心定位NG)
2 切刃・折弯刀的分割位置是否恰当
3
模 具
3
w=10kg以上的模具部品是否有加工作业用孔
1
保 (起吊螺纹孔)(嵌合部品全部)
1 间隙、折弯刀R形状在试模中是否有问题
2 咬合量是否适当
3 2次・3次避让是否切实实施
切
4
背撑钢性与切刃・折弯刀下的支撑是否有充分确保
刃 5 切刃・折弯刀是否有悬挂(有,无)
(有)时⇒量是多少: ・
mm (立会时判断)
6 是否有安装侧冲孔强制下落零件
曲 7 补焊部位是否实施淬火后开裂确认(着色确认)
确 7 防误夹的安装位置・动作・配线是否OK 认 8 机械手的空气配管・动作・强度是否OK
9 空站的定位、零件定位是否OK
1 0
是否有实施相对取出传送带的高度确认
冲压检查表

6
保险盖
1、使用是否完好;2、强度和尺寸是否符合(含备用的)
2、参照说 明书。
2、备用的三个月
7
安全用电
是否有电线破皮、老化以及私拉乱扯现象
1、目测
1个月
8
地脚螺丝
是否有缺失、松动(40T以上的冲床)
1、目测 2、试验
1个月
9
支撑螺丝
是否有缺失、松动(开式可倾冲床)
1、目测 2、试验
1个月
10
电机的固定及支撑螺丝 是否有缺失、松动
1、目测 2、试验
1个月
备注:上表中的各项由安全办全体在冲压部日常巡查或维修工作中安全检查的基本内容。电工负责用电安全及光电保护、双手操作和电机及电箱、操作箱的紧固螺丝
检查; 机修工负责冲床使用(含保险盖)、安全挡板、防护网、地脚螺丝、支撑螺丝的检查。检查出的问题必须有记录、有结果,作为绩效考核的重要依据。
补充说明:
冲压部安全控点检查表
检查日期:
安全控点
检查内容
1
冲床使用
1、是否超负荷;2、螺杆调节是否超出范围
模具安全挡板 1、有否;2、有效性
检查方法
1、检查保 险; 2、目测
1、目测
检查人:
检查周期
现场随时
现场随时
检查结果
2
四要素
防护网 光电保护 双手操作
1、有否;2、有效性 1、有否;2、有效性(含高度调节) 1、有否;2、有效性(16T以上的冲床)
1、目测
1、目测 2、试验 1、目测 2、试验
现场随时 现场随时 现场随时
3
劳保用品
耳塞、眼镜、手套、防护帽、代手工具等是否正确使用
1、目测
冲压模具验收动静态检查表

紧固无松动,无裂纹及破损,重点检查
A
√
/
/
87
安全护板
厚度22∙Omm,操作安全
C
√
/
/
88
销钉
松紧合适,上下各销•半,安装防脱落装置
C
√
√
√
√
89
侧销孔
船销直径+0∙2mm=侧销孔宜径,无兄动
A
/
√
√
Z
90
侧销固定长度
原则上固定25mm根据直径大小现场判定
A
/
√
√
/
91
侧销锁板销钉
锁板按要求安装摞钉孔不允许人工打磨或加工
65
翻边整形刃口面
顺滑,无凸凹不平等缺陷
B
/
/
/
√
66
翻边整形块安装
间隙W0.05mm,无台阶,圆角顺滑一致
B
/
/\
/
√
67
翻边顶出器顶杆
螺钉孔与顶杆壁厚保证3-5M
B
/
/
/
√
冲压模具静态验收检查表
项目
CN200
零件名称
螺母片
备注:符合要求填写,不符合要求填写“X”,不适用填写
*7”具体问题填入“模具问题记录表”
目视
B
/
7
4
/
102
防护板涂黄色
目视
C
√
Z
/
Z
103
取出压料芯前需要先拆除的镶块涂红色
目视
A
/
√
/
/
104
模具存放块外周边涂红色.
目视
A
√
√
A
√
/
/
87
安全护板
厚度22∙Omm,操作安全
C
√
/
/
88
销钉
松紧合适,上下各销•半,安装防脱落装置
C
√
√
√
√
89
侧销孔
船销直径+0∙2mm=侧销孔宜径,无兄动
A
/
√
√
Z
90
侧销固定长度
原则上固定25mm根据直径大小现场判定
A
/
√
√
/
91
侧销锁板销钉
锁板按要求安装摞钉孔不允许人工打磨或加工
65
翻边整形刃口面
顺滑,无凸凹不平等缺陷
B
/
/
/
√
66
翻边整形块安装
间隙W0.05mm,无台阶,圆角顺滑一致
B
/
/\
/
√
67
翻边顶出器顶杆
螺钉孔与顶杆壁厚保证3-5M
B
/
/
/
√
冲压模具静态验收检查表
项目
CN200
零件名称
螺母片
备注:符合要求填写,不符合要求填写“X”,不适用填写
*7”具体问题填入“模具问题记录表”
目视
B
/
7
4
/
102
防护板涂黄色
目视
C
√
Z
/
Z
103
取出压料芯前需要先拆除的镶块涂红色
目视
A
/
√
/
/
104
模具存放块外周边涂红色.
目视
A
√
√
冲压模具点检表
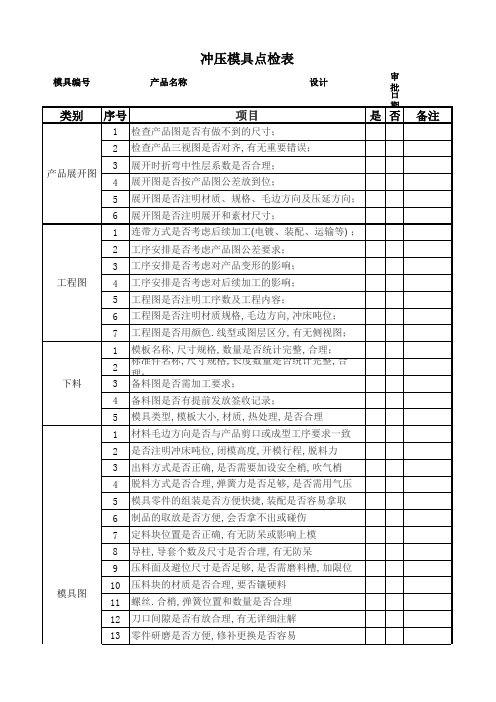
冲压模具点检表
模具编号 产品名称 设计 审批 日期
类别
序号
1 2 3 4 5 6 1 2 3
项目
检查产品图是否有做不到的尺寸; 检查产品三视图是否对齐, 有无重要错误; 展开时折弯中性层系数是否合理; 展开图是否按产品图公差放到位; 展开图是否注明材质、规格、毛边方向及压延方向; 展开图是否注明展开和素材尺寸; 连带方式是否考虑后续加工(电镀、装配、运输等) ; 工序安排是否考虑产品图公差要求; 工序安排是否考虑对产品变形的影响; 工序安排是否考虑对后续加工的影响; 工程图是否注明工序数及工程内容; 工程图是否注明材质规格, 毛边方向, 冲床吨位; 工程图是否用颜色. 线型或图层区分, 有无侧视图; 模板名称, 尺寸规格, 数量是否统计完整, 合理; 标准件名称, 尺寸规格, 长度数量是否统计完整, 合 理; 备料图是否需加工要求; 备料图是否有提前发放签收记录; 模具类型, 模板大小, 材质, 热处理, 是否合理 材料毛边方向是否与产品剪口或成型工序要求一致 是否注明冲床吨位, 闭模高度, 开模行程, 脱料力 出料方式是否正确, 是否需要加设安全梢, 吹气梢 脱料方式是否合理, 弹簧力是否足够, 是否需用气压 模具零件的组装是否方便快捷, 装配是否容易拿取 制品的取放是否方便, 会否拿不出或碰伤 定料块位置是否正确, 有无防呆或影响上模 导柱, 导套个数及尺寸是否合理, 有无防呆 压料面及避位尺寸是否足够, 是否需磨料槽, 加限位 压料块的材质是否合理, 要否镶硬料 螺丝. 合梢, 弹簧位置和数量是否合理 刀口间隙是否有放合理, 有无详细注解 零件研磨是否方便, 修补更换是否容易
是 否
备注产品展开图工程图4 5 6 7 1 2下料
3 4 5 1 2 3 4 5 6 7 8 9 10 11 12 13
模具编号 产品名称 设计 审批 日期
类别
序号
1 2 3 4 5 6 1 2 3
项目
检查产品图是否有做不到的尺寸; 检查产品三视图是否对齐, 有无重要错误; 展开时折弯中性层系数是否合理; 展开图是否按产品图公差放到位; 展开图是否注明材质、规格、毛边方向及压延方向; 展开图是否注明展开和素材尺寸; 连带方式是否考虑后续加工(电镀、装配、运输等) ; 工序安排是否考虑产品图公差要求; 工序安排是否考虑对产品变形的影响; 工序安排是否考虑对后续加工的影响; 工程图是否注明工序数及工程内容; 工程图是否注明材质规格, 毛边方向, 冲床吨位; 工程图是否用颜色. 线型或图层区分, 有无侧视图; 模板名称, 尺寸规格, 数量是否统计完整, 合理; 标准件名称, 尺寸规格, 长度数量是否统计完整, 合 理; 备料图是否需加工要求; 备料图是否有提前发放签收记录; 模具类型, 模板大小, 材质, 热处理, 是否合理 材料毛边方向是否与产品剪口或成型工序要求一致 是否注明冲床吨位, 闭模高度, 开模行程, 脱料力 出料方式是否正确, 是否需要加设安全梢, 吹气梢 脱料方式是否合理, 弹簧力是否足够, 是否需用气压 模具零件的组装是否方便快捷, 装配是否容易拿取 制品的取放是否方便, 会否拿不出或碰伤 定料块位置是否正确, 有无防呆或影响上模 导柱, 导套个数及尺寸是否合理, 有无防呆 压料面及避位尺寸是否足够, 是否需磨料槽, 加限位 压料块的材质是否合理, 要否镶硬料 螺丝. 合梢, 弹簧位置和数量是否合理 刀口间隙是否有放合理, 有无详细注解 零件研磨是否方便, 修补更换是否容易
是 否
备注产品展开图工程图4 5 6 7 1 2下料
3 4 5 1 2 3 4 5 6 7 8 9 10 11 12 13
冲压模具开模可行性检查表
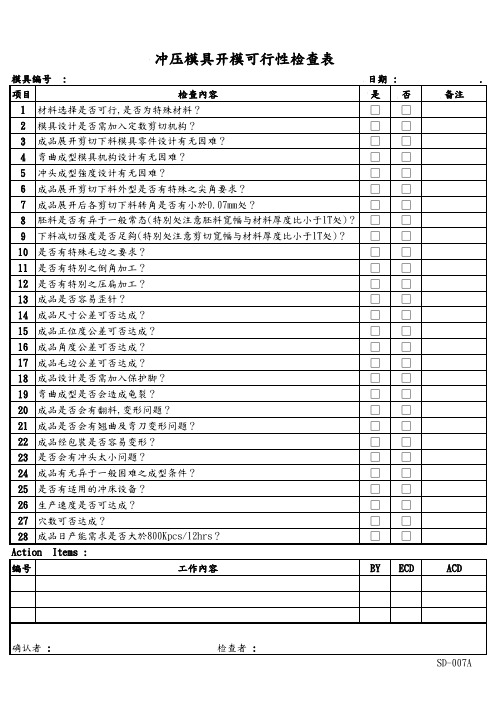
8 胚料是否有异于一般常态(特別处注意胚料宽幅与材料厚度比小于1T处)?
9 下料减切强度是否足夠(特別处注意剪切宽幅与材料厚度比小于1T处)?
10 是否有特殊毛边之要求?
11 是否有特別之倒角加工?
12 是否有特別之压扁加工?
13 成品是否容易歪针?
14 成品尺寸公差可否达成?
15 成品正位度公差可否达成?
16 成品角度公差可否达成?
17 成品毛边公差可否达成?
18 成品设计是否需加入保护脚?
19 弯曲成型是否会造成龟裂?
20 成品是否会有翻料,变形问题?
21 成品是否会有翘曲及弯刀变形问题?
22 成品经包裝是否容易变形?
23 是否会有冲头太小问题?
24 成品有无异于一般困难之成型条件?
25 是否有适用的冲床设备?
冲压模具检查內容
1 材料选择是否可行,是否为特殊材料?
2 模具设计是否需加入定数剪切机构?
3 成品展开剪切下料模具零件设计有无因难?
4 弯曲成型模具机构设计有无因难?
5 冲头成型強度设计有无因难?
6 成品展开剪切下料外型是否有特殊之尖角要求?
7 成品展开后各剪切下料转角是否有小於0.07mm处?
26 生产速度是否可达成?
27 穴数可否达成?
28 成品日产能需求是否大於800Kpcs/12hrs?
Action Items :
编号
工作內容
日期 : 是否 □□ □□ □□ □□ □□ □□ □□ □□ □□ □□ □□ □□ □□ □□ □□ □□ □□ □□ □□ □□ □□ □□ □□ □□ □□ □□ □□ □□
BY ECD
. 备注
ACD
确认者 :
模具点检表

冲压模具日常生产性点检表
生产班组:
时段 点检项目 1、检查模具的产品号及工序号与生产计划是 否相符 点检方法 目视 测量/目视 目视 目视/手感 目视 目视 目视 目视 目视/手感 目视 操作/目视 判断标准 计划与模具实物相符,符合 生产计划 能正常安装,符合《冲压作 业指导书》 无杂质、无异物、无突起 安全销无晃动、丢失 无损坏、断裂 无杂质、无异物、无突起 送料取件正常/与工作台中心 线重合 存放垫平稳支撑模具 安装支点稳定,无晃动 模具外观完好、导向部位清 洁并加注润滑油 安全墩、模具存放块已取 下,无缺失 模具型腔内、上下表面无异 物 无脱落、松动 光滑,清洁/上下行程到位, 无异常 完好 废料滑落顺畅 无异常 6S标准 无异常,无缺损,无晃动 存放垫平稳支撑模具 1 2 3 4 5 6
生 3、检查模具型腔内、上下表面是否清洁,螺栓 产 目视/手感 是否松动、缺失 前 4、检查模具紧固装置状况(如螺栓)导向装 目视/手感 置状况(如导板) 定位装置状况(如定位 块) 5、棉布清理模具型面,涂润滑油,开动寸动 目视/手感 行程空车运行三次 1、检查模具五大装置(工作、紧固、导向、 定位、顶出装置)是否正常 目视 目视 目视/听觉 目视 目视/手感 目视
填写顺序
1
3
2
年 月
12 13 14 157891011
安 2、检查压力机的滑块高度或最大行程是否适 装 合模具的封闭高度及加工行程 前 3、清理压力机的工作台及滑块表面 4、检查模具安全销又没有松动,缺失 5.检查吊装棒及防脱链是否损坏、断裂 1、检查模具上下表面有没有废屑或杂质 2、检查模具安装方向是否正确,安装位置是 安 否对中 装 时 3、检查模具存放垫是否齐备 4、检查模具装模压板或螺钉有没有缺陷,检 查模具是否锁紧 1、检查模具外观与导向部位 2、检查安全墩及模具存放块
生产班组:
时段 点检项目 1、检查模具的产品号及工序号与生产计划是 否相符 点检方法 目视 测量/目视 目视 目视/手感 目视 目视 目视 目视 目视/手感 目视 操作/目视 判断标准 计划与模具实物相符,符合 生产计划 能正常安装,符合《冲压作 业指导书》 无杂质、无异物、无突起 安全销无晃动、丢失 无损坏、断裂 无杂质、无异物、无突起 送料取件正常/与工作台中心 线重合 存放垫平稳支撑模具 安装支点稳定,无晃动 模具外观完好、导向部位清 洁并加注润滑油 安全墩、模具存放块已取 下,无缺失 模具型腔内、上下表面无异 物 无脱落、松动 光滑,清洁/上下行程到位, 无异常 完好 废料滑落顺畅 无异常 6S标准 无异常,无缺损,无晃动 存放垫平稳支撑模具 1 2 3 4 5 6
生 3、检查模具型腔内、上下表面是否清洁,螺栓 产 目视/手感 是否松动、缺失 前 4、检查模具紧固装置状况(如螺栓)导向装 目视/手感 置状况(如导板) 定位装置状况(如定位 块) 5、棉布清理模具型面,涂润滑油,开动寸动 目视/手感 行程空车运行三次 1、检查模具五大装置(工作、紧固、导向、 定位、顶出装置)是否正常 目视 目视 目视/听觉 目视 目视/手感 目视
填写顺序
1
3
2
年 月
12 13 14 157891011
安 2、检查压力机的滑块高度或最大行程是否适 装 合模具的封闭高度及加工行程 前 3、清理压力机的工作台及滑块表面 4、检查模具安全销又没有松动,缺失 5.检查吊装棒及防脱链是否损坏、断裂 1、检查模具上下表面有没有废屑或杂质 2、检查模具安装方向是否正确,安装位置是 安 否对中 装 时 3、检查模具存放垫是否齐备 4、检查模具装模压板或螺钉有没有缺陷,检 查模具是否锁紧 1、检查模具外观与导向部位 2、检查安全墩及模具存放块
冲压模具生产点检表(连续模)

用扳手拧螺栓
镶块松动易损坏模具,伤害操作者
6, 下模刀口无崩刃
目视
刀口崩刃易产生有害毛刺
7, 模具送料导尺无松动,错位
目视、用手晃动导尺 导尺异常会产生送料不准
8, 剥料桥固定可靠,无松动,偏移 9, 导料顶块顺畅无卡死,顶块固定部分无断裂(即顶块不可以被拔出) 10, 切断部分脱料顶销可靠有效(顶销不能卡死,脱料弹簧正常)
目视
要有清晰的产品件号、模具编号
2, 模具上下模正确吻合,无上下模合反,合错现象
目视Байду номын сангаас
上下模合反易损坏模具
3, 吊运模具的装置(螺栓或起吊块)是否安全可靠.(螺栓无松动,弯曲)
用扳手拧螺栓
螺栓松动易出现安全问题
4, 上模导引冲头可靠有效,无缺损,无断裂
目视、用手触摸
导引失效易产生不良品
5, 上下模镶块无松动,缺损
目视、用扳手拧螺栓
目视、用手按动顶 块,用手拔起顶块
用手按动顶销,感知 脱料力
该异常会损坏模具,伤害操作者 该异常会损坏模具,伤害操作者 该异常会损坏模具,产生不良品
11, 模具已安装限位柱,红漆无掉落,模具上无其他物件(工具、螺丝、镶块、产品等)
目视
限位柱可保护模具和冲床
12, 侧冲弹簧有可靠地安全防护装置 13,
3, 生产的日期、零件号刻印是否清晰正确
目视,对照刻印要求 刻印错误会产生不良品
4, 切边或冲孔工位落料顺畅,无废料堆积 5, 误送检知正常,初始挡料块可靠有效,废料和产品完全分开
目视
目 视,接触检知, 观察信号
废料堆积会损坏模具
废料产品混淆会导致分选困难,检知 失效则无法判断少送料现象
冲压模具设计检查表

Presspressure, holdingpressure, press type, Pneumatic connect , electric system, operation requirement are showed on drawing
7.冲压力是否计算,压力中心位置在设计图纸中是否标注提示?
Are all components marked as needed for example, Top/Bottom of die, weight, operations, I.D. tag, paint color show etc.?
注释:
Comments
批准人 :
Approved by
模具工程师(供应商):
9.模具顶出和卸料装置、易损件和工作部分的合理性与可靠性
Were the ejector, stripper plate, interchange and working parts rationality and reliability
10.斜锲和吊锲结构的尺寸是否符合要求?
Structure of cams and cam overhang must meet std.?
Die Engineer (Supplier)
日期:
Date
模具设计方代表:
DesignCo.Rep.
零件制造方代表:
Production Plant Rep.
冲压模具设计审核表(A)
DIEDESIGNREVIEW(A)
零件号:
Part Number
总成号:
Assembly Part#
工程更改号:
EWO#
零件名称:
Part Name
零件图纸号:
7.冲压力是否计算,压力中心位置在设计图纸中是否标注提示?
Are all components marked as needed for example, Top/Bottom of die, weight, operations, I.D. tag, paint color show etc.?
注释:
Comments
批准人 :
Approved by
模具工程师(供应商):
9.模具顶出和卸料装置、易损件和工作部分的合理性与可靠性
Were the ejector, stripper plate, interchange and working parts rationality and reliability
10.斜锲和吊锲结构的尺寸是否符合要求?
Structure of cams and cam overhang must meet std.?
Die Engineer (Supplier)
日期:
Date
模具设计方代表:
DesignCo.Rep.
零件制造方代表:
Production Plant Rep.
冲压模具设计审核表(A)
DIEDESIGNREVIEW(A)
零件号:
Part Number
总成号:
Assembly Part#
工程更改号:
EWO#
零件名称:
Part Name
零件图纸号:
模具设计检查表

第2页/共6页
编号 检查项目 48 敲模孔及模芯螺孔是否合适 49 流道上铝料刻字是否符合指令单要求 50 模芯高出模框高度是否合适 51 模芯插穿位是否已避免直角插穿 52 模芯是否有正面吊环及天侧吊环 模框 53 模框外露的部分是否已倒角(分型面除外) 54 动定模框插穿的部分是否已避空 滑块 56 滑块行程是否合适 57 滑块复位机构是否合适 58 锁紧块是否合适 59 滑块冷却是否合适 60 滑块限位是否合适 61 滑块抽出后是否有足够的安全余量 62 滑块是否需要导向机构 63 斜导柱大小是否合适 64 天侧斜导柱是否干涉喷雾头 65 油缸规格是否合适 66 油缸缸径及行程是否合适 67 油缸支架是否合适 68 油缸联接是否合适 69 油缸油嘴是否符合标准 70 油缸油嘴的接出是否方便无干涉 浇注系统 71 浇道截面是否合适 72 是否需加流道板 73 渣包及排气槽是否合适
第3页/共6页
XXX机械制造有限公司
模具设计自检表
K3编号 项目工程师
设计检查
文件编号: 判定
第4页/共6页
设计检查
判定
第5页/共6页
设计检查
判定模具设计自检表
压铸机 冲头大小
第1页/共6页
编号 检查项目 冷却水路
23 水管装拆是否便捷 24 冷却水位置、尺寸及数量是否合适 25 冷却水是否避免同镶针、镶件及顶针穿透 26 运水是否存在死水 27 水管及运水螺孔是否符合标准 28 水管是否与吊环干涉 29 水管是否与码模夹干涉 30 水管是否与哥棱柱干涉 31 水管是否与螺丝等其他结构与孔干涉 顶出系统 32 针板导柱大小 33 顶出行程是否合适 34 垃圾钉位置、数量及尺寸是否合适 35 模脚尺寸及位置是否合适 36 支撑柱尺寸、数量及位置是否合适 37 回针尺寸及位置是否合适 38 顶针尺寸、数量及位置是否合适 39 是否需选用顶针套 40 顶针、顶针套及镶针避空孔是否符合标准 41 异形顶针是否已做防转 42 顶棍顶出时是否有干涉 模芯 43 缩水率选择 44 模芯厚度是否合适 45 分型线是否经客户批准 46 分型是否避免尖角位 47 精定位选择是否合适
冲压模具检查表--新项目管理要求

三:Hale Waihona Puke 边冲孔三冲压模具检查表
22 23 24 25 26 27 28 29 30 31 32 33 34 35 36 37 38 39 40 41 1 2 3 4 5 6 7 8 9 10 11 12 13 14 15 16 17 18 1 2 3 4 5 6 7 8 9 10 11 12 13 14 15 修边刃口进入量是否足够?(一般按9毫米) 下型的高度可否再高一些以方便废料下滑? 废料滑槽的宽度是否足够?特别注意模具端头和斜楔座下面。 废料滑槽是否要求用3毫米钢板制作? 修边刃口有凸耳的地方是否采取了加强措施? 铸钢修边镶块(含废料刀)是否有加强筋? 废料滑槽和废料盒是否出了图? 修边镶块的背靠是否比镶块矮5毫米?
)
五:斜楔
压料面调整块、平衡块的数量和位置是否合理? 托杆的设置是否平衡? 托杆的设置是否适合用户设备和调试设备?是否考虑了我公司的调试设备? 托杆的突出量、行程是否正确? 凸出量( )行程( ) 安全区的设置是否合理? 凸模的导板与压边圈轮廓是否干涉? 凸模翻转用铸入螺母的高度位置是否设定?凸模重量( )直径( ) 气垫在上死点时,凸模和压边圈的导向长度是否保持50-70以上? 定位机构的位置是否适当?板料在投入时,导向长度是否充分? 压边圈的强度、刚性是否充分? 压印标记销的位置是否正确? C/H孔处下模是否设有加强筋? 排气孔和铸造排气孔的位置是否充分? 内、外压边圈的行程是否适当? 加工压力是否计算?(内压 外压 ) 安全防护板是否设置? 拉延模中排气孔的数量是否足够? 上下模水平方向能否顺利排气? 拉延模顶杆位置是否考虑了淬火垫块? 拉延切口是否可以留下让废料切脱滑出的可能?(缘起yy5-58321/421)
三:拉延
废料能否顺利排除模具?(滑料角不小于25度 ) 加工压力是否计算?压料板的压力是否充分?列出计算过程(F=l*t*Gb*5%) 是否绘出了弹性元件的力线图? 力线图上是否给出了行程关系?且对应处的力是否满足要求? 压料板的行程是否按纵切处(如废料刀)设定?须在主断面画出行程图。 刃口的分块设定是否适量?(是否设有锋利的锐口?) 刃口镶块的高度(底面设定)设置是否合理?是否设置背靠? 冲孔的凸模和镶入的凹模防转设置是否合理?冲头是否易于安装? 非标凸模和镶入式凹模的设置是否合理? 废料刀及凹模和的刃口吃入量祥图是否进行了指示? 凸、凹刃口的螺销钉的大小、位置和数量是否适当?(必须≥12MM规格) 废料刀底座的刚性、强度是否进行了确认? 废料刀的高度是否充分考虑到了滑料的需要? 废料刀的刃口是否比工序件低0.5MM 废料刀刀背是否要求倒大斜面以便于滑料? 废料长度是否符合要求?是否考虑了拉延后可能的最大边缘? 是否设置了压料器与模座的工艺组合凸台? 冲孔、修边刃口是否考虑了产品公差?(按公差带60%或其余要求设计) 修边、冲孔间隙是否合理?(单边按料厚的8%) 是否存在废料刀刃口或刀背相向的情况? 锻件修边镶块背面是否设计了5MM调整垫板? 冲头进入凹模是否满足了5MM? 垂直和倾斜修边刃口交接是否合理? 斜楔冲孔时对废料是否采取了强制退料措施? 冲孔废料过孔是否足够大? 对于比较尖或钝的刃口是否要求处理? 对于可能难以下滑的废料是否采取了强制措施? 但强制装置不能早于压料器工作
冲压模具点检表

向
凸凹模表 面无裂纹 、无杂物
漏料部位 清洁无积
料
导柱顶部 、导套内 部、导板 表面干净
无异物
气动装置无 限位及支
感应器装 漏气、无明 撑套(支
置可靠、 显变形,橡 撑块)无
无松动 胶部位无严 变形、缺
重磨损
损、
废料滑料 板无变形
安全侧销 、安全螺
钉无松 动; 冲孔废料 道无卡滞
班长确认
压前 压后 压前 压后 压前 压后 压前 压后 压前 压后 压前 压后 压前 压后 压前 压后 压前 压后 压前 压后 状态 状态 状态 状态 状态 状态 状态 状态 状态 状态 状态 状态 状态 状态 状态 状态 状态 状态 状态 状态
压前
压后
发生时间
确认人
异常描述
发生时间
异常处置
确认人
1、模具名称及编号栏填写如:“前车门外板”、“K1-8402111-1/5”。 2、检查内容填写时,完好请打“○”;发现异常请打“×”;处理完“×”, 然后在异常记录栏填写,并由班长确认。 3、此表保存期限为1年。
冲压模具点检表生产线体使用设备点检项目模具主体合模标记工作型面辅助装置班长确认点检方法目视目视目视擦拭目视手感目测目测目测目测目测点检基准序号模具编号模具名称点检人日期101112异常描述发生时间确认人异常描述发生时间异常处置确认人模具上下安装面无裂纹料豆等异上下模f标或侧面标指向同向凸凹模表面无裂纹无杂物漏料部位清导柱顶部导套内部导板表面干净无异物感应器装置可靠无松气动装置无漏气无明显变形橡胶部位无严重磨损限位及支撑套支撑块无变形缺损废料滑料板无变形安全侧销安全螺钉无松动
生产线体
使用设备
序 号
模具编号
1
模具名称
凸凹模表 面无裂纹 、无杂物
漏料部位 清洁无积
料
导柱顶部 、导套内 部、导板 表面干净
无异物
气动装置无 限位及支
感应器装 漏气、无明 撑套(支
置可靠、 显变形,橡 撑块)无
无松动 胶部位无严 变形、缺
重磨损
损、
废料滑料 板无变形
安全侧销 、安全螺
钉无松 动; 冲孔废料 道无卡滞
班长确认
压前 压后 压前 压后 压前 压后 压前 压后 压前 压后 压前 压后 压前 压后 压前 压后 压前 压后 压前 压后 状态 状态 状态 状态 状态 状态 状态 状态 状态 状态 状态 状态 状态 状态 状态 状态 状态 状态 状态 状态
压前
压后
发生时间
确认人
异常描述
发生时间
异常处置
确认人
1、模具名称及编号栏填写如:“前车门外板”、“K1-8402111-1/5”。 2、检查内容填写时,完好请打“○”;发现异常请打“×”;处理完“×”, 然后在异常记录栏填写,并由班长确认。 3、此表保存期限为1年。
冲压模具点检表生产线体使用设备点检项目模具主体合模标记工作型面辅助装置班长确认点检方法目视目视目视擦拭目视手感目测目测目测目测目测点检基准序号模具编号模具名称点检人日期101112异常描述发生时间确认人异常描述发生时间异常处置确认人模具上下安装面无裂纹料豆等异上下模f标或侧面标指向同向凸凹模表面无裂纹无杂物漏料部位清导柱顶部导套内部导板表面干净无异物感应器装置可靠无松气动装置无漏气无明显变形橡胶部位无严重磨损限位及支撑套支撑块无变形缺损废料滑料板无变形安全侧销安全螺钉无松动
生产线体
使用设备
序 号
模具编号
1
模具名称
模具设计图检查表
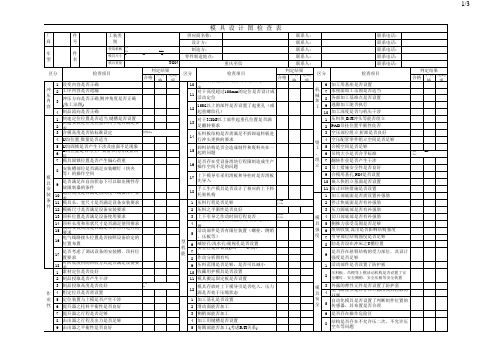
压料板、吊楔等上模活动机构是否设置了安
初接触: 总行程:
)
18 可回收废料的回收方式是否满足设备要求 1 素材定位是否良好 2 制品投取是否产生干涉 3 制品投取高度是否良好 作 业 性 4 粗定位具是否需设置 5 定位装置与上模是否产生干涉 6 提升器之托料平衡性是否良好 7 提升器之行程是否足够 8 击出器之行程及出力是否足够 9 击出器之平衡性是否良好
1 加工基孔是否设置 2 滑动面能否加工 3 侧梢部能否加工 4 加工用键槽是否设置 5 角隅部能否加工(考虑R/H关系)
6 是否存在操作危险区 8
1 活动部件是否设置了防护板 2 全螺钉、安全侧销、安全压板等安全装置 模 具 安 全 3 外露的弹性元件是否设置了防护套 4 电气路接头是否存在外露出模具轮廓的问题 5 自动化模具是否设置了判断制件位置的 传感器,其布置是否合理 结构是否存在不允许压二次、不允许压 空车等问题
12
模具存放时上下模导引是否吃入,压力 源是否处于压缩状态
1/3
模 具 设 计 图 检 查 表
厂 商 车 型 区分 冲 压 内 容 件 号 件 名 工装类 别
使用机械 模具尺寸 模具重量
主: 副: H W TON L
供应商名称: 设计方: 制造方: 零件制造地点: TON 判定结果 合格
不合格 无此项
联系人: 联系人: 联系人: 联系人: 重庆至信 联系人: 判定结果 合格
手工生产模具是否设计了相应的上下料 18 托架机构 1 压料行程是否足够 2 压料之平衡性是否良好 3 上下引导之作动时间行程良否 4 行程停止块是否设置,行程端管是否设置 活动部件是否有限位装置(螺栓、侧销 5 、压板等) 6 减轻孔\浅水孔\窥视孔是否设置 距离: 7 安全区是否设置(□: 8 作动分析图有吗 9 压料范围是否足够,是否可以减小 10 收藏用护模具是否设置 11 模具搬运固定板是否设置
初接触: 总行程:
)
18 可回收废料的回收方式是否满足设备要求 1 素材定位是否良好 2 制品投取是否产生干涉 3 制品投取高度是否良好 作 业 性 4 粗定位具是否需设置 5 定位装置与上模是否产生干涉 6 提升器之托料平衡性是否良好 7 提升器之行程是否足够 8 击出器之行程及出力是否足够 9 击出器之平衡性是否良好
1 加工基孔是否设置 2 滑动面能否加工 3 侧梢部能否加工 4 加工用键槽是否设置 5 角隅部能否加工(考虑R/H关系)
6 是否存在操作危险区 8
1 活动部件是否设置了防护板 2 全螺钉、安全侧销、安全压板等安全装置 模 具 安 全 3 外露的弹性元件是否设置了防护套 4 电气路接头是否存在外露出模具轮廓的问题 5 自动化模具是否设置了判断制件位置的 传感器,其布置是否合理 结构是否存在不允许压二次、不允许压 空车等问题
12
模具存放时上下模导引是否吃入,压力 源是否处于压缩状态
1/3
模 具 设 计 图 检 查 表
厂 商 车 型 区分 冲 压 内 容 件 号 件 名 工装类 别
使用机械 模具尺寸 模具重量
主: 副: H W TON L
供应商名称: 设计方: 制造方: 零件制造地点: TON 判定结果 合格
不合格 无此项
联系人: 联系人: 联系人: 联系人: 重庆至信 联系人: 判定结果 合格
手工生产模具是否设计了相应的上下料 18 托架机构 1 压料行程是否足够 2 压料之平衡性是否良好 3 上下引导之作动时间行程良否 4 行程停止块是否设置,行程端管是否设置 活动部件是否有限位装置(螺栓、侧销 5 、压板等) 6 减轻孔\浅水孔\窥视孔是否设置 距离: 7 安全区是否设置(□: 8 作动分析图有吗 9 压料范围是否足够,是否可以减小 10 收藏用护模具是否设置 11 模具搬运固定板是否设置
冲压件检查基准书细化检查表

无高点、凹坑 56(P27车型)
1/100 0.1 1/100
20 1/100 0.2 1/100 0.2 1/100 0.5 1/100 0.5 1/100 0.2 1/100 0.2 1/100
1/100 0.1 1/100
2 1/100 0.2 1/100
1/100 0.1 1/100
6 1/100 0.2 1/100 0.5 1/100
8 1/100 0.2 1/100 0.2 1/100 0.2 1/100
3 1/100 0.3 1/100
1/100 0.12 1/100
5 1/100 0.2 1/100
1/100 1/100 1/100 0.1 1/100 31 1/100 0.2 1/100 0.2 1/100
散热器架下横梁外板
K2检查基准书细化检查表
零部件号 左右侧第一悬置外板 左电器盒安装板
左右下边梁内板前加强板 后地板前加强梁右连接板 后地板前加强梁座椅左右安装 空调中下安装支架 空调左下安装支架
检查项目 外观 毛刺 孔数检查 检具定位孔孔径20 检具定位孔孔径13 孔径10 长圆孔13*10 孔径13 外观 毛刺 孔数检查 孔径7 孔径7 长圆孔12*7 孔径2-7 孔径2-7 孔径10 长圆孔14*7 尺寸10.5 外观 毛刺 孔数检查 孔径9.5 15*9.5长圆孔 孔径34 尺寸22.7 尺寸9 外观 毛刺 孔数检查 长圆孔19*13 孔径13 孔径7 外观 毛刺 孔数检查 孔径6.3 孔径12.5 尺寸160 尺寸8.4 外观 毛刺 孔数检查 孔径检查6.5 孔径6.5 孔径6.5 外观 毛刺 孔数检查 孔径2-8 孔径3-6.5
0-1.5
2 1/100 1/100
冲压模具细部设计检查表

6 每一下料工程站是否会容易跳屑?
7 安装沖子入块与冲子固定板框口是否有方向性设计?
8 脫料入块与脱料板框口是否有方性设计?
9 下模入块与下模板框口是否有方向性设计?
10 折弯成型冲子与下模折弯成型入块是否有方向性设计?
11 是否需要增加调整偏摆之工程站?
12 是否需要增加調整高低針之工程站?
13 是否需要增加调整扇形之工程站?
actionitems编号工作內容ecdacd冲压模具设计检查表模具编号依据当时之实际状况叙述
冲压模具细部设计检查表
模具编号 :
日期 :
项目
检查內容
1 每一個工程站之排配是否适当
2 下料刀口与冲子加工是否可行?
3 下料刀口与冲子承受强度是否可行?
4 滑块机构设计是否可行
5 每一弯曲工程站成形是否稳定?
14 浮升梢高度设定与排配是否适当?
15 是否需要预留工程站?
Action Items :编号Fra bibliotek工作內容是
否
□
□
□
□
□
□
□
□
□
□
□
□
□
□
□
□
□
□
□
□
□
□
□
□
□
□
□
□
□
□
BY ECD
备注 ACD
※ 依据当时之实际状况叙述:
检查者 :
确认者 :
. SD-011A
冲压模具制造检查表

模具制造方代表:.
Construction Co. Rep
零件制造方代表:
Production Plant Rep.
冲压模具制造审核表(B)
DIE CONSTRUCTION REVIEW( B )
零件号:
Part Number
总成号:
Assembly Part#
工程更改号:
EWO#
零件名称:
Part Name
零件图纸号:
G D & T DWG #
零件图纸更改级别:
Part DWG E/C Level
年型/车型:
Year & Style
零件数模版本号:
Math Data Release #
模具编号:
Die Code
零件供应商:
Part Supplier
SQE ( SGM )
SQE ( SGM ):
电话:
Phone#
DUNS / Z编号:
DUNS / Z Code
模具工程师(供应商pplier)
电话:
D.冲孔头及引孔符合标准
Were the Pierce punch & punch entry as std.
E.斜锲操作平稳,回程装置安装正确
Camoperation is smooth, positive returns are fitted
14.模具的操作安全性
Is the safety cover installed properly
15.所有模具号标牌均正确固定,并按标准上漆
All die ID tags are fitted and painted as std.
注释:
Comments
Construction Co. Rep
零件制造方代表:
Production Plant Rep.
冲压模具制造审核表(B)
DIE CONSTRUCTION REVIEW( B )
零件号:
Part Number
总成号:
Assembly Part#
工程更改号:
EWO#
零件名称:
Part Name
零件图纸号:
G D & T DWG #
零件图纸更改级别:
Part DWG E/C Level
年型/车型:
Year & Style
零件数模版本号:
Math Data Release #
模具编号:
Die Code
零件供应商:
Part Supplier
SQE ( SGM )
SQE ( SGM ):
电话:
Phone#
DUNS / Z编号:
DUNS / Z Code
模具工程师(供应商pplier)
电话:
D.冲孔头及引孔符合标准
Were the Pierce punch & punch entry as std.
E.斜锲操作平稳,回程装置安装正确
Camoperation is smooth, positive returns are fitted
14.模具的操作安全性
Is the safety cover installed properly
15.所有模具号标牌均正确固定,并按标准上漆
All die ID tags are fitted and painted as std.
注释:
Comments
- 1、下载文档前请自行甄别文档内容的完整性,平台不提供额外的编辑、内容补充、找答案等附加服务。
- 2、"仅部分预览"的文档,不可在线预览部分如存在完整性等问题,可反馈申请退款(可完整预览的文档不适用该条件!)。
- 3、如文档侵犯您的权益,请联系客服反馈,我们会尽快为您处理(人工客服工作时间:9:00-18:30)。
项目备注
123456789101112131415
编号
ACD
模具编号 :日期 :检查內容
是否每一個工程站之排配是否适当□□下料刀口与冲子加工是否可行?□□下料刀口与冲子承受强度是否可行?□□滑块机构设计是否可行
□□每一弯曲工程站成形是否稳定?□□每一下料工程站是否会容易跳屑?
□□安装沖子入块与冲子固定板框口是否有方向性设计?□□脫料入块与脱料板框口是否有方性设计?□□下模入块与下模板框口是否有方向性设计?
□□折弯成型冲子与下模折弯成型入块是否有方向性设计?□□□浮升梢高度设定与排配是否适当?□□是否需要增加调整偏摆之工程站?□□是否需要增加調整高低針之工程站?□□冲压模具设计检查表
是否需要预留工程站?
□
□
Action Items :工作內容
BY
ECD
是否需要增加调整扇形之工程站?□ 检查者 :
确认者 : .
※ 依据当时之实际状况叙述:。