工程材料液态成型实验报告
工程材料液态成型实验指导书

开放实验指导书大纲实验名称: 工程材料液态成型引言什么是液态成型金属的液态成型常称为铸造,铸造是将金属熔炼成符合一定要求的液体并浇进铸型里,经冷却凝固、清整处理后得到有预定形状、尺寸和性能的铸件的工艺过程。
图-1 铸造示意图一、实验目的1.了解铸造的概念及基本原理;2.了解并掌握铸造的基本工艺及其主要的工艺参数;3.了解并掌握铸造过程中金属从液态到固态转变过程中影响金属性能和铸件质量的一些基本因素;4.了解金属收缩的基本规律,以及常见铸造缺陷缩的形成机理,及其影响因素。
二、实验原理1.铸造的定义铸造过程是指将金属置于熔炼炉内的坩埚中, 加热熔炼成符合一定要求的液体并浇铸到锭模或铸模中,经冷却凝固, 液态金属转变成固态金属, 清整处理后获得一定形状、尺寸的铸件或铸件的工艺过程。
铸造毛胚因近乎成形,而达到免机械加工或少量加工的目的降低了成本并在一定程度上减少了时间.铸造是现代机械制造工业的基础工艺之一.铸造工艺可分为三个基本部分,即铸造金属准备、铸型准备和铸件处理。
铸造金属是指铸造生产中用于浇注铸件的金属材料,它是以一种金属元素为主要成分,并加入其他金属或非金属元素而组成的合金,习惯上称为铸造合金,主要有铸铁、铸钢和铸造有色合金。
2.铸造的分类铸造种类很多,按造型方法习惯上分为:①普通砂型铸造,包括湿砂型、干砂型和化学硬化砂型3类。
②特种铸造,按造型材料又可分为以天然矿产砂石为主要造型材料的特种铸造(如熔模铸造、泥型铸造、铸造车间壳型铸造、负压铸造、实型铸造、陶瓷型铸造等)和以金属为主要铸型材料的特种铸造(如金属型铸造、压力铸造、连续铸造、低压铸造、离心铸造等)两类。
2.1 普通砂型铸造以型砂和芯砂为造型材料制成铸型,液态金属在重力下充填铸型来生产铸件的铸造方法。
钢、铁和大多数有色合金铸件都可用砂型铸造方法获得。
由于砂型铸造所用的造型材料价廉易得,铸型制造简便,对铸件的单件生产、成批生产和大量生产均能适应,长期以来,一直是铸造生产中的基本工艺。
液态成型工艺学试验指导书--造型材料-梁

前言型砂(又称造型材料)泛指各种原沙、粘结剂和附加物等原材料,以及按一定比例,均匀配制而成的型砂、芯砂、涂料、胶合剂等,以用于造型和制芯。
在铸件形成过程中,液体合金会和型(芯)砂制成的铸型(包括涂料层)发生热的、机械的、物理化学的相互作用,易导致铸件产生“三砂两孔”(粘砂、夹砂、胀砂、气孔、砂孔)等缺陷。
因此,所配制的型(芯)砂必须具备优良的工作性能和工艺性能。
而这些性能,在很大程度上由组成型(芯)砂的原材料性能,其中尤以砂和粘结剂的性能所决定。
如砂子的化学成分、矿物成分、含泥量、烧结点、耐火度,粘结剂的发气量、溃散性、退让性、吸湿性、保存性等等。
本书主要阐明部分原材料和型(芯)砂的实验技术,以便重点掌握其检测方法和仪器设备的使用规则,提高分析和独立工作的能力。
为了加大实验研究的力度,以深化对实验内容的理解,特选编了一个综合实验,其一般步骤是:调查研究——实验设计——测试、分析及处理数据——实验报告。
实验一原砂性能测定一、概述:铸造用砂(也称原砂)是型砂的骨干材料,一般使用石英制原砂(硅砂)。
其含泥量、颗粒组成、耐火度、烧结点和化学成分为其最基本质量指标,直接影响着型砂性能和铸件的质量。
因此,生产上按照一定的技术要求选用原砂,并把含泥量、颗粒组成(粒度、粒形、分布状态……)列为常规检验项目之一。
二、实验目的:1.了解铸造用砂的基本性能的测定方法及原理。
2.熟悉有关仪器设备的操作方法和注意事项。
3.重点掌握铸造用砂含泥量的测定原理以及颗粒组成的表示方法。
三、实验内容:1.原砂含泥量测定;2.原砂颗粒组成测定;3.原砂颗粒形状与表面状态的显微镜观察。
四、实验仪器、工具和材料:1.仪器设备1)天平(感量0.1g和0.01g);2)SGH双盘红外线烘干器;3)SXW涡洗式洗砂机以及洗砂杯、虹吸管;4)可调式电炉或烘箱;5)筛砂机;SSD电磁微震筛砂机;SSZ震摆式筛砂机;6)SBS铸造用标准筛;7)MSL双目立体显微镜;2.工具和材料1)刷、牛角勺、吸液管、吸球、漏斗、大小瓷盘等;2)造用砂若干种;3)浓度5%的焦磷酸钠水溶液;4)滤纸(快速)。
液态成型

液态成型1、液态成型主要研究内容。
掌握凝固过程的传热,凝固热力学和动力学,合金的凝固,液态金属的凝固组织及其控制,凝固缺陷及其控制,钢锭及连铸坯的凝固,焊缝的凝固。
2、凝固过程控制的关键。
传热3、液态金属的结构特点。
结构特点:长程无序——不具备平移、对称性;近程有序——相对于完全无序的气体,液体结构表现出局域范围的有序性微观特点:“能量起伏”——液态金属中各微观区域的能量处于此起彼伏,变化不定的状态。
这种微区内的能量短暂偏离其平均能量的现象,叫做能量起伏。
(原子团间能量的不均匀性)“结构起伏”——液体中大量不停“游动”着的局域有序原子团簇时聚时散、此起彼伏(原子团结构的不均匀性)“浓度起伏”——同种元素在不同原子团中分布的不均匀性4、液态金属的流动性及影响因素。
流动性是指熔融金属的流动能力。
1)合金成分纯金属、共晶成分和金属间化合物流动性好,结晶温度范围宽的合金流动性差。
比热容、密度较大的合金流动性好,导热系数小的合金流动性好。
2)结晶潜热潜热约占金属含量热的85%~90%,结晶潜热释放越多,流动性越好。
3)液态金属的粘度及表面张力,粘度越高表面张力越大,液态金属流动性越好5、液态金属的充型能力及影响因素。
充型能力:液态金属充满铸型型腔,获得形状完整、轮廓清晰的铸件的能力,影响因素:金属性质(流动性的影响);铸型性质;浇注条件;铸件结构6、凝固过程传热基本特点。
传热特点为:“一热、二迁、三传”。
“一热”,即在凝固过程中热量的传输是第一位的,是最重要的,它是凝固过程能否进行的驱动力。
“二迁”,指固—液界面和金属—铸型界面,随着凝固进程而发生动态迁移,并使得界面上的传热现象变得极为复杂。
“三传”,即金属的凝固过程同时包含动量传输、质量传输和热量传输,而在热量传输过程中同时存在有导热、对流和辐射传热这三种传热方式。
7、铸件温度场的研究方法。
(1)数学解析法(2)数值计算法(3)测温法铸件温度场的影响因素:1.金属性质的影响因素(1)热扩散率;(2)结晶潜热;(3)液-固相线温度2. 铸型性质的影响(1) 铸型的蓄热系数;(2) 铸型温度3. 浇注条件的影响液态金属的浇注温度4. 铸件结构的影响(1) 铸件壁厚(当量厚度、模数)(2) 铸件的形状8、铸件凝固过程中,若不计液态金属的热阻,金属凝固速度主要受哪三种热阻的控制。
实验报告一-材料成形技术

实验一材料成形技术材料成形制造工艺多利用模型使原材料形成零件或毛坯。
材料成形加工过程中,原材料的形状、尺寸、组织状态,甚至结合状态都会改变。
由于成形精度一般不高,材料成形制造工艺常用来制造毛坯。
也可以用来制造形状复杂但精度要求不太高的零件。
材料成形工艺的生产效率较高。
常用的成形工艺有铸造、锻压、粉末冶金等。
1、不同类型成型技术a. 铸造成型:卡特挖机CAT :1、铸造成型:其原理是铸造是将所需的金属熔化成液体,浇注到铸型中,待其冷却凝固后获得铸件(毛坯)的。
因此,铸造也可以称为液态成形。
铸造是毛坯或机器零件成形的重要方法之一。
2、铸造成形优缺点:优点:(1)适应性广泛,铸件材质、大小、形状几乎不受限制;不宜塑性加工或焊接成形的材料,铸造成形尤具优势。
(2) 可形成形状复杂的零件;(3)生产成本较低。
铸造用原材料来源广泛,价格低廉。
铸件与最终零件的形状相似,尺寸相近,加工余量小。
由于铸造具有如此突出的优点,所以才会经久不衰,且不断发展,直到现在仍然在制造业中得到广泛应用。
缺点:涉及生产工序较多,过程难以精确控制,废品率较高;铸件组织疏松,晶粒粗大,铸件某些力学性能较低;铸件表面粗糙,尺寸精度不高。
工作环境较差,工人劳动强度大。
3、主要工艺特点:铸造是生产零件毛坯的主要方法之一,尤其对于有些脆性金属或合金材料 (各种铸铁件、有色合金铸件等) 的零件毛坯,铸造几乎是唯一的加工方法。
与其它加工方法相比,铸造工艺具有以下特点:(1)铸件可以不受金属材料、尺寸大小和重量的限制。
铸件材料可以是各种铸铁、铸钢、铝合金、铜合金、镁合金、钛合金、锌合金和各种特殊合金材料;铸件可以小至几克,大到数百吨;铸件壁厚可以从0.5毫米到1 米左右;铸件长度可以从几毫米到十几米。
(2)铸造可以生产各种形状复杂的毛坯,特别适用于生产具有复杂内腔的零件毛坯,如各种箱体、缸体、叶片、叶轮等。
(3)铸件的形状和大小可以与零件很接近,既节约金属材料,又省切削加工工时。
(材料成形原理液态成形原理)1.3界面现象

形变
形变是从初始工件形状到成 形结束形状的过程,会受到 材料的韧性、强度和刚度的 影响。
断裂
在成形过程中,材料可能会 发生断裂。这会对成形件的 性能产生不利的影响。
常见的成形技术类型
1 锻造
2 深抽
用压力将材料挤压成形,以产生所需的 形状。
利用模具和加热处理,将材料压成平面 或凸出的形状。
3 挤压
4 投铸
将材料塑料化,从模具压出所需形状。
在熔融状态下,将材料倒入模具中,并 在凝固前使其凝固。
成形后的加工和处理
成形后的部件还需要进一步的加工和处理,以使它们符合最终产品的要求和标准。
切割和打磨
这种加工技术可以使零件更加平整和匀称,以适应其他部件或设计要求。
热处理和冷却处理
通过在材料上施加热量和冷却,可以改变其硬度、强度、弹性和韧性等性质。
温度影响
温度变化会影响传质的 速度,因为更高的温度 意味着分子更具活力。
传质的控制
控制传质是很困难的, 因为往往需要定期进行 测试和分析。
了解流体流动
流体在成形过程中的流动性质是至关重要的,因为它们对成形件的质量产生着深刻的影响。
1
流体特性
流体是由分子和粒子组成的,因此它们的性质非常像,包括表面张力和粘度。
2
方向与速度
流体的方向和速度可以影响成形过程的质量和性质。如果流动不均匀,会留下缺 陷。
3
流移模型
通过研究不同的流体流动模型,可以更好地了解流体的流动行为。
材料性质对成型的影响
不同类型的材料具有不同的化学和物理性质,这些性质会对成形过程产生很大的ห้องสมุดไป่ตู้响。
材料选择
选择材料时,考虑流动性、 温度行为、热膨胀和化学反 应等因素。
材料成形工艺作业——液态成形部分

《材料成形工艺》作业——液态成形部分
班级:________姓名:________学号:____________分数:________
简答题:
1.铸铁件、铸钢件和铸造非铁合金件用的湿型砂各具有什么特点?
2.试归纳总结压力铸造、低压铸造和离心铸造的特点及应用范围。
3.简述浇注系统的主要组成及各部分的主要作用。
分析论述题:
4.在熔模铸造型壳的干燥硬化过程中,硅溶胶型壳通常会出现型壳鼓泡和裂纹,请分析其原因。
5.根据铸件浇注位置的选择原则,分析下面每一组图中那个是合理
的,并论述其理由。
6.根据分型面确定原则,分析下图箱体铸件的Ⅰ、Ⅱ、Ⅲ分型面选
择方案的优劣。
材料成形原理实验报告(3篇)
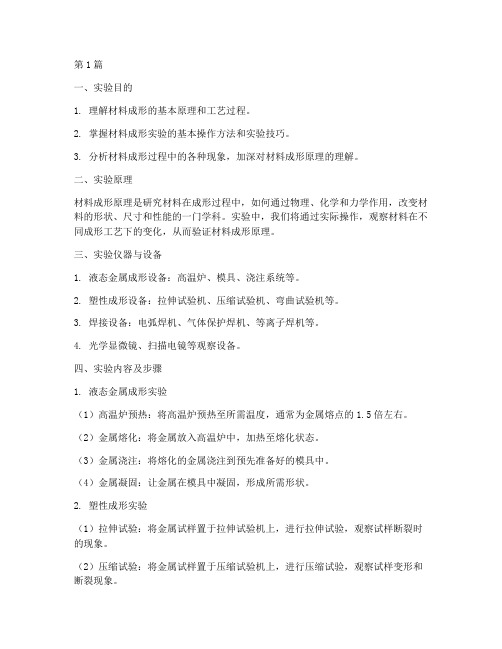
第1篇一、实验目的1. 理解材料成形的基本原理和工艺过程。
2. 掌握材料成形实验的基本操作方法和实验技巧。
3. 分析材料成形过程中的各种现象,加深对材料成形原理的理解。
二、实验原理材料成形原理是研究材料在成形过程中,如何通过物理、化学和力学作用,改变材料的形状、尺寸和性能的一门学科。
实验中,我们将通过实际操作,观察材料在不同成形工艺下的变化,从而验证材料成形原理。
三、实验仪器与设备1. 液态金属成形设备:高温炉、模具、浇注系统等。
2. 塑性成形设备:拉伸试验机、压缩试验机、弯曲试验机等。
3. 焊接设备:电弧焊机、气体保护焊机、等离子焊机等。
4. 光学显微镜、扫描电镜等观察设备。
四、实验内容及步骤1. 液态金属成形实验(1)高温炉预热:将高温炉预热至所需温度,通常为金属熔点的1.5倍左右。
(2)金属熔化:将金属放入高温炉中,加热至熔化状态。
(3)金属浇注:将熔化的金属浇注到预先准备好的模具中。
(4)金属凝固:让金属在模具中凝固,形成所需形状。
2. 塑性成形实验(1)拉伸试验:将金属试样置于拉伸试验机上,进行拉伸试验,观察试样断裂时的现象。
(2)压缩试验:将金属试样置于压缩试验机上,进行压缩试验,观察试样变形和断裂现象。
(3)弯曲试验:将金属试样置于弯曲试验机上,进行弯曲试验,观察试样变形和断裂现象。
3. 焊接实验(1)电弧焊:将金属板置于电弧焊机下,进行电弧焊,观察焊缝成形和焊缝组织。
(2)气体保护焊:将金属板置于气体保护焊机下,进行气体保护焊,观察焊缝成形和焊缝组织。
(3)等离子焊:将金属板置于等离子焊机下,进行等离子焊,观察焊缝成形和焊缝组织。
五、实验结果与分析1. 液态金属成形实验通过液态金属成形实验,我们观察到金属在高温下熔化,浇注到模具中后凝固成所需形状。
在实验过程中,我们掌握了金属熔化、浇注和凝固的基本原理。
2. 塑性成形实验通过塑性成形实验,我们观察到金属在拉伸、压缩和弯曲过程中,会产生不同程度的变形和断裂。
《材料成形原理》1实验

实验五液态金属成形中的结晶裂纹倾向试验一、试验原理结晶裂纹是液态金属成形过程中的主要缺陷之一。
本试验参照压板对接(FISCO)焊接裂纹试验方法,通过人为地改变焊接冶金因素或焊件拘束程度,对不同情况下的液态金属成形中的结晶裂纹敏感性进行了实验比较。
二、试验目的1.了解结晶裂纹的形成机理及宏观特征;2.了解结晶裂纹敏感性的影响因素;3.掌握一种结晶裂纹倾向试验方法。
图1 FISCO试验装置简图1—C型拘束框架;2—试件;3—紧固螺栓;4—齿形底座;5—定位塞片;6—调整板三、试验装置及材料1.直流弧焊机ZX5-400 1台2.FISCO试验装置(如图1所示)1套3.φ4直径J422、J427和J427-FeS(自制)焊条各4~6根4.200×120×12mm低碳钢(或低合金钢)试板12块5.测力扳手1件四、方法及步骤1.将试件两块装入FISCO试验装置中,以相应厚度的塞片来保证对口间隙2~4mm。
测力扳手以120Nm 的扭矩紧固好全部加固螺栓。
2.按图2所示,依次焊接长约40mm 长的试验焊缝,焊缝间距约10mm , 图2 试验焊接位置 焊缝弧坑原则上不填满。
焊接电流:100A ;电弧电压:24V ;焊接速度:150mm/min 。
3.焊接后约10分钟将试件从试验装置中取出。
4.试件冷却到室温后,将试件沿焊缝轴向弯断,观察断面上有无裂纹并测量裂纹长度。
并按下式计算裂纹率: %100L 1C FFF ⨯∑∑=Σ1F ——4条试验焊缝的裂纹长度之和(mm ); ΣL F ——4条试验焊缝的长度之和。
5.使用另两种试验焊条重复以上试验过程,分别计算裂纹率。
6.松开试验装置中的部分(或全部)紧固螺栓,降低试件的拘束程度,重复以上试验,观察裂纹率的变化。
五、试验结果整理将实验结果填入下表:比较各试件裂纹率的测试结果,写出试验报告。
包括: 1.分析熔渣类型或熔渣成分的变化对结晶裂纹倾向的影响;2.分析拘束程度的变化对结晶裂纹倾向的影响。
- 1、下载文档前请自行甄别文档内容的完整性,平台不提供额外的编辑、内容补充、找答案等附加服务。
- 2、"仅部分预览"的文档,不可在线预览部分如存在完整性等问题,可反馈申请退款(可完整预览的文档不适用该条件!)。
- 3、如文档侵犯您的权益,请联系客服反馈,我们会尽快为您处理(人工客服工作时间:9:00-18:30)。
工程材料液态成型实验报告要求
学院:
业:
姓名:学号:
实验时间:2010-04-06
一、实验目的和要求
1•了解铸造工艺的基本过程。
2.通过具体的熔炼浇注工艺,了解基本概念,工艺特点,以用在日常生活中的具体应用。
3•了解一种金属材料(A356)的熔炼基本工序。
二、实验原理
铸造过程是指将金属置于熔炼炉内的坩埚中,加热熔炼成符合一定要求的液体并浇铸到锭模或铸模中,经冷却凝固,液态金属转变成固态金属,清整处理后获得一定形状、尺寸的铸件或铸件的工艺过程。
铸造工艺可分为三个基本部分,即铸造金属准备、铸型准备和铸件处理。
铸造种类很多,按造型方法习惯上分为:①普通砂型铸造,②特种铸造.
根据熔制合金的实际重量W,计算各元素的需要量A
W
A = X Q
100
三、主要仪器设备
实验所用设备包括:加热熔炼炉,熔炼用金属,坩埚,熔炼工具,模具
四、实验内容及实验数据记录
1•了解铸造的基本设备并熟悉其基本操作;
2、配料
熔炼A356铝合金20Kg,A356化学成分:Si 6.5〜7.5% ,Mg0.20〜0.40% ;铝为余量。
根据熔制合金的实际重量W,计算各元素的需要量A
W
A = 100 X Q
计算:Si: A=0.2X 6.5%=0.013kg
Mg:A=0.2 x 0.2%=0.0004kg Si: A=0.2 x (1-6.5%-0.2%)=0.1983kg。