变 压 吸 附 脱 碳 装 置 在 我 厂 的 应 用
210000m3/h变换气变压吸附脱碳装置运行总结

P S A . 预脱碳 装 置的 主要设计 工 艺参数 : 处 理变 换气 能力 变换气 压 力 2 1 0 0 0 0 i n / h ; 1 . 7~ 2 . 1 MP a ;
成 ,每塔 在 每 一 个 循 环 周 期 内都 经 历 吸 附 、1 0 级 压力 均升 降 、顺 放 、逆放 、抽 真 空 、预 升 压 、 最终 升 压 ,共 2 6个 步 骤 。 二 段 吸 附 采 用 2 0 — 5 . 1 1 / V时序 ,与 一 段 类 似 ,只是 压 力 均 升 降 采 用 1 1级 ,抽 真 空 由 4 台真 空 泵 完 成 ,每 塔 在 每 一
半成 品气 C O , 含 量 ≤1 6 . 0 %;
回收率 C O 回收率
>9 I 9 . 5 %; 19 > 7 . 0 %;
N , 回收率 I >9 8 . O %;
时进料吸 附,其 余 1 4台吸附塔 分别进行 均压 、
产品气 C O 纯度
[ 收稿 日期]2 0 1 2 - l l - 0 1 [ 作者简介]卢锦永( 1 9 8 4 一) , 女, 广西柳州人 , 助理工程师 柳州化工股份有限公司净化分厂工艺员。
我公 司 老合成 氨 厂净化 系统 原变 压 吸附脱 碳
顺 放 或逆放 、抽 真空 解 吸 。
装置 ( 简称 P S A脱 碳 装 置 ) 的作 用 是 脱 除 变 换 气中的 C O : ,送 出合格 的净 化气 作 为氨 合成 的原 料 气 ,同时 获 得 产 品 气 C O 供 尿 素 、联 碱 等 工 序使 用 。P S A 脱 碳 装 置 采 用 二 段 法 进 行 串 级 脱 碳 ,处 理气 量为 1 5 0 0 0 0 m / h 。随着 合成 氨产 能 的不 断 扩 大 ,该 装 置 已 不 能 满 足 生 产 的要 求 。 2 0 0 9年底 ,为 了配 合 4 0 0 k t / a合 成 氨 技 改 项 目 的进行 ,公 司 决 定 在 P S A脱 碳 装 置 之 前 增 加 1 套 处理 气量 为 2 1 0 0 0 0 I I 1 / h的 P S A 脱 碳 装 置 ( 简称 P S A . 预脱 碳装 置 ) ,与 P S A脱 碳 装置 串联 运 行 。P S A 一 预 脱碳 装 置 于 2 0 1 1 年 6月 底 投 入生
新型PSA脱碳装置的应用

新型PSA脱碳装置的应用上一篇/ 下一篇 2007-12-25 14:24:19 / 个人分类:网上收集查看( 88 ) / 评论( 2 ) / 评分( 8 / 0 )合成氨变换气中含有约18%--28%的二氧化碳,在进人合成氨精炼工段之前必须将CO2脱除,所得氢气和氮气用来生产合成氨。
合成氨厂采用不同的工艺路线进行变换气脱碳是影响其吨氨消耗的重要因素,因此脱碳是合成氨工艺中的一个重要阶段。
变换气脱除CO2的方法很多,国内中小型合成氨厂最普遍采用的就是碳化法,即将合成工段生产的氨返回碳化工段来吸收变换气中的CO2,得到碳酸氢铵产品,作为商品化肥销售。
但随着化肥行业竞争的加剧和农业生产用肥的季节性变化,碳酸氢铵呈现出严重的供大于求的现象,迫使中小型合成氨厂大幅度压缩碳铵产量,增加液氨产量。
因此如何选择技术先进、经济合理的脱碳工艺是摆在许多小型合成氨厂面前的课题。
常用的脱碳方法有:水洗法、碳酸丙烯酯法、MDEA法、NHD法等湿法脱碳及PSA干法脱碳。
变压吸附法脱除合成氨变换气中CO2工艺自1991年在湖北建阳县化肥厂成功实现工业化以来,10年中已在全国建成各种规模的工业装置近百套,为中、小型合成氨厂改变产品结构、节能增效起了显著的作用。
与传统的湿法脱碳技术相比,变压吸附脱碳技术以自动化程度高、操作方便可靠、操作费用低、适应性强、无设备腐蚀问题等优点而受到众多厂家的青睐。
随着市场竞争日益激烈.中小型合成氨厂要在市场上生存下去就必须提高竞争能力,降低生产成本,因此变压吸附脱碳技术已日益成为目前脱碳技术的首选。
但是该方法也存在有效气体回收率偏低及装置一次性投资较高的缺点。
1、PSA脱碳方法的特点PSA法用于合成氨变换气脱碳的优势比较明显,虽然一次性投资稍高,但从长期生产经营考虑,选用PSA法较为合理。
与其他的湿法脱碳方法相比,PSA法脱碳技术还具有以下特点:(1)工艺流程简单,开停车方便,通常开车后60分钟后即可得到合格的净化气产品;(2)操作中不带液体,无设备腐蚀问题,也不消耗蒸汽,装置运行费用低;(3)CH4在变换气中一般为0.7%--0.9%.经PSA脱碳后CH4可脱除50%左右,使合成系统的弛放气大大减少;(4)以煤为原料的氨厂变换气中一般H2S约为50—200mg/m3,有机硫为20--50μg/m3,在经PSA脱碳后净化气中硫含量可降至1mg/m3以下;(5)由于PSA技术对变换气净化度高(氢氮气中CO2含量≤0.2%),可采用甲烷化代替铜洗,免除铜洗液污染环境,同时气体净化度高,硫化物、观等杂质仅含微量,将延长甲醇催化剂使用寿命:(6)技术成熟可靠,具有十来年长期运行的工业业绩。
变压吸附脱碳应用的总结

个步骤 , 即吸附、 一均降、 二均降 、 三均降、 逆放、 抽
真空 、 均升 、 三 隔离 、 均 升 、 离 、 均 升 、 冲 , 二 隔 一 终
故障, 能 l 只 台真空 泵 运行 , 连接 全开 , 将 把程 序 8 —3— / V、 3双 6—3 / v的运 行 方 式 手 动切 —3双 换 为 8—3 3 单 v 6 —3单 v方 式运 行 , —/ 、 —3 / 切换
D 20Z P 一 .A 9台 N 0 S J 4 0
v、 )6—3 / ( —3— / V 6—3 / V) —3 V 6 3双 、 —3 单 2种
产品气 缓 冲 罐 : 1台 0 0 22O×9 35 V=3 6 、 0
m , 式椭 圆形封头 ; ]立
方 式 。8 —3V方 式 就是 8台吸 附 塔 运 行 时 , —3 / 总有 3台吸 附处 于 吸附状 态 , 其余 5台 吸 附塔 处 于再生 的不 同阶段 , 台吸 附塔 都 经历 相 同的 1 每 2
2 变 压 吸 附脱 碳生产 工艺 该装 置 采用 8台吸附塔 并联 生产 。分 成对 称 的 2列 , 2台解吸 气缓 冲罐 、 由 2台水 环 式真 空 泵 分 为 2 抽真 空 。其流 程如下 : 有 一定压力 ( 组 具 即 12M a和温度 的变 换气 经冷却器 后进 入气水 分 . P ) 离 器 , 离游离 油水 后 的原料 气 经 流量 计 计量 后 分
解 吸气缓 冲罐 : 2台 0 0 100×310 V=19 5 、 .
变压吸附脱碳新工艺在我厂的应用

水 环式 真 空泵 : 2台 2 E3 3 B I0 —0型 ; 1 变 压吸 附脱 碳 新 工艺 程控阀: 4个 D 30 Z P 一16 N 0 S J .A:
l 3个 D 5 z P 一4. A; NlO SJ 0 5个 D 0 Z P 一4. A: N10 SJ 0 5个 D 0 Z P 一4. A N8 S J 0
消耗大 、 本高 和 达不 到设 计 能力 等 问题 , 迫 停 成 被
m
2 变 压 吸 附脱碳 主 要设 备
气 水分 离器 : l台 D 120 H=330 V=2 9 N 0 、 0 、 .
3;
吸 附塔 : 4台 D 22 0 H=800 V=2 3 N 0 、 0 、 4m ;
运行 方 式 之 间的互 相 叨换 可通 过计 算 机 自动 控制 或 由手 动操 作 实现 . 主要工 艺 参数 可在 控 =各
真 空 解吸 气 , 过 真 空 泵抽 出气 体直 接 放空 通
吸附塔 解 吸过 后 , 过 2次 压力 均 衡升 , 经 经
制盘 上显 示 , 际 操 作 l 可 根据 各 重 要 参 数 变 化 实 _ 1 】
附 脱碳装 置 气 体排 放量 , 高 气 体回 收率 提 ( )顺 放气 JC , 量 高达 2 2 , 于该 部 2 O 含 .% 由
分气 体流量 小 , 碳 化工 序无 明显 影 响 , 对 但提高 r
升 压
回收 , 过 管道 送 往 碳 化 工 序 固定 副 塔 。接 着 该 通
吸附 塔与 其 它再 生 过程 中的 吸附 塔进 行 2次 压力 均衡 降 , 然后 进 行 2次顺 向放 压 , 部 分顺 放气 送 这
往气 柜予 以 回收 :
变压吸附脱碳工艺的应用
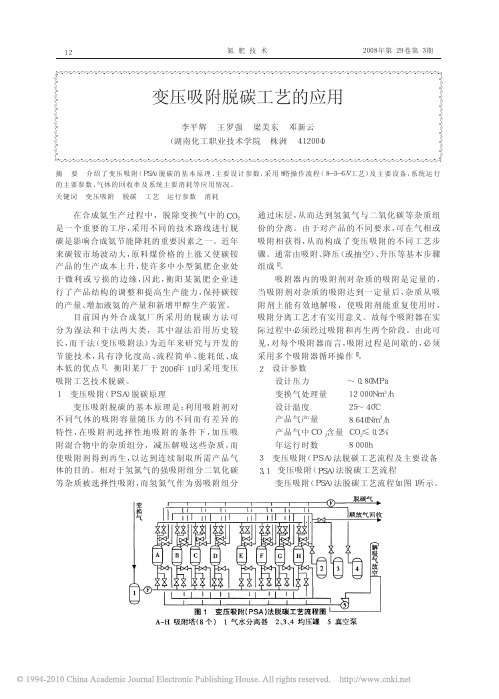
定地送出系统。
变压吸附系统的解吸气来自吸附器的抽真
空阶段, 逆放结束后, 进入抽真空阶段, 真空泵抽
出的解吸气经放空管直接放空。
3.3 主要设备
吸附塔
8台, Φ2 400×7 150, V=23.1m3;
气水分离器 1台, Φ1 000×6 850;
均压罐
3台, Φ1 600×7 150;
水环式真空 泵3台, 2BEC- 42, 132m3/min ( 标
程, 真空泵也可减开1台; 反之, 加负荷时, 则可恢
复为“三塔”流程, 开2台真空泵。
另外, 吸附时间的长短也可以根据生产负荷
的大小灵活调节。高负荷时, 为了降低有效气体
损失率及保证产品气纯度, 吸附时间相应缩短;
反之, 轻负荷时, 则相应延长吸附时间。实际操作
中, 本装置吸附时间根据生产负荷情况控制在适
当的范围内。
该 装 置 由 于 均 压 次 数 多 , 又 有“ 顺 放 ”程 序 ,
因 此 有 效 气 体 损 失 率 低 ,“ 顺 放 ”结 束 时 系 统 压 力
约为2kPa, 如此低的压力为抽真空创造了良好的
条件, 真空度较高, 约- 70kPa, 保证了吸附剂的彻
底解吸。
正常运行后, 对气体组分进行分析检验, 如
指标名称 原料气
吸附剂( 按 10 年计) 循环冷却水 电( 380/220V) 仪表空气
解吸气 + 抽空气 系统压降
单位 Nm3/h kg/h
t/h kW·h Nm3/h Nm3/h MPa
消耗量 12 00
1.6 22.8 182.4 56.7 3 750 0.02 ̄0.04
"""""""""#
变 压 吸 附 脱 碳 装 置 在 我 厂 的 应 用.

收稿日期:"’’& 0 ’( 0 !’
作者简介万:葛方慧数玲(据!(," 0 ),女,助理工程师,从事化工技术管理工作,电话:’!&%()*$$((&。
开启 %: 阀和顺放一缓冲罐进口阀 !$,: 塔结 束吸附步骤后,吸附塔中的部分气体经 %: 和 !$ 阀 进行顺放,回收吸附塔前端的干净气体以提高氢气、 氮气的回收率,顺放过程中吸附器的压力下降,其吸 附 前 沿 朝 出 口 端 方 向 推 进 ,当 吸 附 塔 压 力 降 至 ’ # *% ;8<时 关 闭 !$ 阀 ,顺 放 一 结 束 。过 程 压 力 由 ’ # );8< 下降至 ’ # *% ;8<。 ! # " # # 第一级压力均衡降(简称一均降)
开启 %" 阀,抽真空前期开启阀 23 4 (* 以 23 4 *、23 4 1 为前期的抽真空管道),利用真空泵对吸附 塔进行抽真空,进一步降低 " 塔的压力,使吸附剂 上吸附的杂质进一步解吸,吸附剂进一步再生。在
压力基本相等时,关闭 ) $ ,, &’( 下降至 # $ .) &’(。 ! $ " $ % 第四级压力均衡降(简称四均降)
开启 /" 和 /0 阀," 塔经三均降结束后,接着与 刚结束抽真空步骤的 0 塔以出口端相连进行第四 次压 力 均 衡," 塔 出 口 端 的 气 体 经 /"、/0 进 入 0 塔,均压过程中 " 塔 的 吸 附 前 沿 朝 出 口 端 方 向 推 进,正好到达其出口端。当两台吸附器压力基本相
变压吸附脱碳在合成氨生产中应用的讨论

气体气体组份H 2N 2+ArCO CO 2CH 4O 2∑精脱气51.2620.110.6227.110.700.20100.00中间气65.8326.380.95 5.63 1.030.20100.00净化气73.0624.920.820.011.000.20100.00摘要简要介绍变压吸附脱碳工艺,并介绍变压吸附对进、出口气体组份间比例的改变情况和环境温度对气体收率的影响。
关键词脱碳变压吸附气体组份环境温度变压吸附脱碳在合成氨生产中应用的讨论马迎丽张凡军(山西兰花科创田悦化肥有限责任公司晋城048102)!!!!!!!!!!!!!!!!!!!!!!!!!!!!!!!!!!!!!!!!!!!!!"!!!!!!!!"!!!!!!!!!!!!!!!!!!!!!!!!!!!!!!!!!!!!!!!!!!!!!"!!!!!!!!"1前言兰花田悦公司装置生产能力为年产18×104t合成氨、30×104t 尿素、副产7000t 甲醇。
生产流程是:以煤作原料进行气化制得的半水煤气,含有一定量CO 2,CO 2作为含氧化合物,当有大量H 2存在时,含氧化合物会转化成水,而水又会还原成氢和氧原子,氧原子被催化剂表面吸附,使α-Fe 微晶烧结、表面异变而失活,虽然是暂时性中毒,但每经过一次中毒,催化剂活性都不能恢复到最初的活性。
因此,生产过程中尽可能将CO 2脱除干净。
2工艺简介在合成氨工业生产中,脱除原料气中CO 2一般分为湿法脱碳和干法脱碳两大类。
我公司脱碳采用成都天立公司设计的两段式变压吸附吹扫工艺。
本装置由两个系统组成,即提纯系统(简称一段)和净化系统(简称二段)。
提纯系统采用24个吸附塔,5塔吸附、16次均压吹扫工艺;净化系统采用15个吸附塔,5塔吸附、6次均压吹扫工艺。
现将生产中的点滴经验总结如下,与同行探讨。
3变压吸附对进、出口气体组份间比例的改变该装置于2007年10月试车,在2008年装置满负荷运行时,通过72h 连续生产,对装置运行状况进行了验收,具体情况如下。
变压吸附脱碳装置运行总结

7
变压 吸 附脱 碳 装 置 运行 总结
马蓉 英 王厚 健 (河北 东光化 工有 限公 司 061600)
ቤተ መጻሕፍቲ ባይዱ
0 前言
河北 东 光 化 工 有 限 公 司 “18 ·30工 程 ”于 2009年 7月 23 13生 产 出合 格 尿 素 产 品 ,开 车 一 次成 功 。 装 置 生 产 能 力 为 年 产 180 kt合 成 氨 、 300 kt尿 素 ,脱 碳 系统 采 用抽 真 空 变 压 吸 附 (简 称 VPSA)技 术 ,设计 处 理能 力为 160 000 m /h,总 投 资 4 800万 元 。 目前 运 行 已近 1年 半 的时 间 ,运 行情 况 良好 ,各项 指 标基 本达 到 了设计 要求 。
1 选 择 思 路
2006年 ,河 北 东 光 化 工 有 限 公 司 在 合 成 氨 、 尿 素装置 扩 大产 能 时 ,原来 配套 的湿 法 碳 酸 丙 烯 酯脱 碳装 置设 计 能 力 为 80 kt/a,已不 能 满 足 生 产 的需 要 ,需 增 设 新 装 置 提 高 生 产 能力 。变 压 吸 附 脱 碳 作为 新 型工 艺技 术 ,因操 作简 单 、维 修 率低及 运行 成本 低 等优 势 ,得到 了许 多企 业 的青 睐 ,变 压 吸 附设计 有抽 真 空流 程 和吹扫 流程 。这 2种 工 艺 都有 应用 企业 ,尤 其是 吹 扫流 程 ,山东省 的大部分 企业 都采 用此 流程 。经过 多方 考察 、论 证 ,发 现抽 真空 流程 的气 体 损 失 少 于 吹 扫 流程 ,最 后 确 定采 用抽 真空 流 程 ,处 理 气 量 为 40 000 m /h 总 投 资 约 1 200万元 。2007年 开始 新 建 “l8·30工 程 ” 时 ,从 环保 节 能角 度 出 发 ,脱 碳 系 统 仍 选 用 VPSA 技 术 。该 装 置 由 2套 真 空变 压 吸 附 单元 ,即提 纯 段 (VPSA I)和净 化 段 (VPSAⅡ)组 成 。VPSA I 采 用 1849流程 ,由 18台吸 附塔 ,采用 4塔 吸 附 、 9次 均压 、3塔 抽 真 空 工 艺 组 成 ;VPSA II采 用 18— 4—10流 程 ,由 l8台 吸 附塔 ,采 用 4塔 吸 附 、1O次 均压 、3塔 抽 真 空工艺 组 成 。
变压吸附脱碳技术的应用
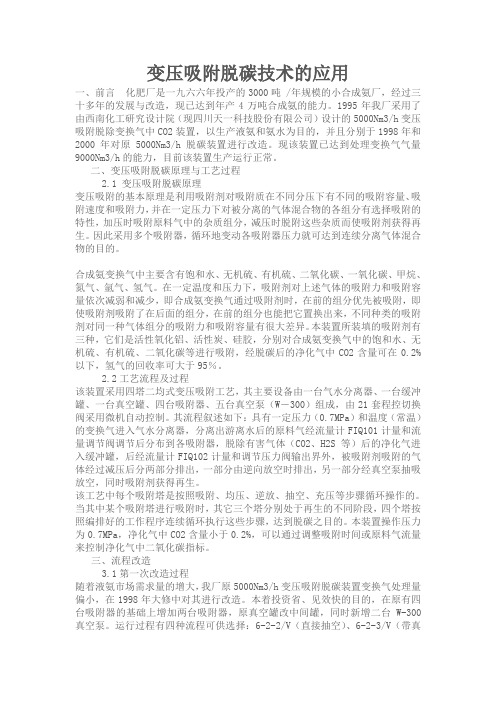
变压吸附脱碳技术的应用一、前言化肥厂是一九六六年投产的3000吨 /年规模的小合成氨厂,经过三十多年的发展与改造,现已达到年产4万吨合成氨的能力。
1995年我厂采用了由西南化工研究设计院(现四川天一科技股份有限公司)设计的5000Nm3/h变压吸附脱除变换气中CO2装置,以生产液氨和氨水为目的,并且分别于1998年和2000年对原5000Nm3/h脱碳装置进行改造。
现该装置已达到处理变换气气量9000Nm3/h的能力,目前该装置生产运行正常。
二、变压吸附脱碳原理与工艺过程2.1 变压吸附脱碳原理变压吸附的基本原理是利用吸附剂对吸附质在不同分压下有不同的吸附容量、吸附速度和吸附力,并在一定压力下对被分离的气体混合物的各组分有选择吸附的特性,加压时吸附原料气中的杂质组分,减压时脱附这些杂质而使吸附剂获得再生。
因此采用多个吸附器,循环地变动各吸附器压力就可达到连续分离气体混合物的目的。
合成氨变换气中主要含有饱和水、无机硫、有机硫、二氧化碳、一氧化碳、甲烷、氮气、氩气、氢气。
在一定温度和压力下,吸附剂对上述气体的吸附力和吸附容量依次减弱和减少,即合成氨变换气通过吸附剂时,在前的组分优先被吸附,即使吸附剂吸附了在后面的组分,在前的组分也能把它置换出来,不同种类的吸附剂对同一种气体组分的吸附力和吸附容量有很大差异。
本装置所装填的吸附剂有三种,它们是活性氧化铝、活性炭、硅胶,分别对合成氨变换气中的饱和水、无机硫、有机硫、二氧化碳等进行吸附,经脱碳后的净化气中CO2含量可在0.2%以下,氢气的回收率可大于95%。
2.2工艺流程及过程该装置采用四塔二均式变压吸附工艺,其主要设备由一台气水分离器、一台缓冲罐、一台真空罐、四台吸附器、五台真空泵(W-300)组成,由21套程控切换阀采用微机自动控制。
其流程叙述如下:具有一定压力(0.7MPa)和温度(常温)的变换气进入气水分离器,分离出游离水后的原料气经流量计FIQ101计量和流量调节阀调节后分布到各吸附器,脱除有害气体(CO2、H2S等)后的净化气进入缓冲罐,后经流量计FIQ102计量和调节压力阀输出界外,被吸附剂吸附的气体经过减压后分两部分排出,一部分由逆向放空时排出,另一部分经真空泵抽吸放空,同时吸附剂获得再生。
变压吸附脱碳装置运行探讨

运行 效 果 , 企 业 的产 品 结构 调 整 、 济 效 益 的 增 加 奠 定 了基 础 。 为 经 关键 词 : 变压 吸 附 ;产 品 结 构 调 整 ;经 济 效 益
中 图 分类 号 :Q 5 .6 T 0 18
文献 标 识 码 : B
文 章 编 号 :0 3— 4 7 2 1 )3— 0 7— 3 10 3 6 (0 1 1 0 5 0
开封永 大化 工有 限公 司原脱 碳装 置 为浓 氨水 吸 收法 , 方 法 的 主 要 优 点 是 可 以 回 收 原 料 气 中 的 该
人 流量 ,00 0 N h 输 入 压 力 , . a 输入 温 3 0 m 0℃ 。其组成 见 表 1 。净化 气 ( 除 C 脱 O 后
% A+ 2 r 0
02 .
N 2
1 7
含 量 5 2
的产 品气 体 ) 输 出流 量 , 13 3N h 净 化 气 质 : 2 8 m / ;
量 , O ≤0 2 ; 出压力 , . 7 MP ( 统压 差 C 2 .% 输 ≥1 5 a 系 ≤0 3MP ) 输 出温度 , 0℃ 。解 吸气 ( 除掉 的 . a ; ≤4 脱 杂质 组分 ) 输 出 流 量 , 1 m / ; 出 压 力 , : 867N h 输 约
河 南 化 工 H N N C E C LI D S R E A H MIA U T Y N
21 0 1年
第2 8卷
处理量 3 0 m / 。工 艺 如下 : 00 0 h 气体 进 入气 液 分 离
2 2 逆 放前期 ( 1 气体 回收影 响脱硫 系统运行 . D )
器分离 掉 游离 水后 进 入 P A 系统 , S 3台吸 附器 同 时 在线吸 附 , 台吸附 器在 一 次 循环 中均需 经 历 吸 附 每 ( 、 放 ( P 、 1 压力 均衡 降 ( 1 、 2级 A)顺 P )第 级 E D) 第 压 力均衡 降 ( 2 ) 第 3级压 力 均衡 降 ( 3 、 4 ED 、 E D) 第 级压 力均衡 降 (AD) 第 5级压力 均衡 降 ( 5 、 F 、 E D) 第 6级压力 均衡 降 ( 6 、 7级 压力 均 衡 降 ( 7 、 E D) 第 E D)
变压吸附技术在钢铁行业的应用

变压吸附气体分离技术在钢铁行业中的应用摘要:变压吸附气体分离技术具有能耗低、流程简单、开停车方便、操作方便、负荷调节灵活等特点,在冶金、化工、环保等领域得到充分的利用。
本文介绍了变压吸附空气分离制氧及变压吸附提纯一氧化碳技术在高炉富氧喷煤、电炉炼钢及钢铁厂尾气综合利用方面的应用情况及由此取得的经济、社会效益。
关键词:变压吸附高炉富氧喷煤电炉炼钢尾气综合利用一、变压吸附气体分离技术简介1、变压吸附气体分离技术简介变压吸附(Pressure Swing Absorption,简称PSA)技术常用于气体混合物的分离,它由美国联合碳化物公司于20世纪60年代首先开发成功,进入70年代后,变压吸附技术获得了迅速的发展,装置数量剧增,规模不断增大,使用范围越来越广,工艺不断完善,成本不断下降,逐渐成为一种主要的、高效节能的气体分离技术。
变压吸附技术在我国的工业应用已有近30年的历史,主要的应用的领域包括:氧气、一氧化碳、氢气、氮气、二氧化碳等的分离提纯。
由于变压吸附气体分离技术具有工艺简单、建设周期短、自动化程度高、开停车灵活、易于操作和维修方便等优点,近年来在气体分离纯化领域得到了广泛应用。
2、变压吸附的基本原理变压吸附的基本原理是根据混合物中不同的吸附质在吸附剂上的吸附量不同,以及同一吸附质在吸附剂上的吸附量随着吸附质的分压不同而变化的原理设计的分离过程。
吸附质在吸附剂上的吸附量在一定温度下是随吸附质分压变化的,这种变化关系用吸附等温线来描述。
B2A1q A2B1q q q图1中A 、B 为两种不同的吸附质在同一温度下的吸附等温线。
从图中可以看出在相同的吸附温度下,A 较B 更容易吸附,A 相对于B 为强吸附组份。
当A 和B 的混合物在高压下(假设A 和B 的分压分别为P A2和P B2)进行吸附,在低压下(假设A 和B 的分压均为P A1和P B1)解吸再生。
当吸附进行到一定阶段时,二者达到吸附平衡,吸附量分别为2A q 和2B q ,2A q >2B q ,因而在吸附阶段吸附床的流出气流中A 的含量小于B ,为富B 气流。
变压吸附技术在合成氨厂的应用

气体 分离技 术 。 自从 2 O世纪 8 O年代初 ,变压 吸附
制 氢成功 实现工业 应用后 ,由于其具 有能 耗低 、流
的吸附 ,其 特点 是 :吸附过程 中没有 化学 反应 ,并 且这种 吸附 是完全 可逆 的 。变 压 吸附工艺过 程 之所
以得 以实现 是 由于吸 附剂在这 种物理 吸 附中所具 有 的两个 性质 :( )对不 同组分 的 吸附能力 不 同 ,有 1 强弱 吸附质 之分 ;( )吸附质 在 吸附剂上 的吸 附容 2 量 随吸附质 的分压 上升 而增加 ,随 吸附温度 上升 而
要为物 理 吸附 。物 理 吸附是指 依靠 吸附剂 与吸 附质 分子 间 的分 子 力 ( 括 范 德 华 力 和 电磁 力 ) 进 行 包
与再生循 环 ,达 到连续 吸 附分离 的 目的。
12 变压 吸 附技 术 的发 展 .
在2 O世纪上 半 叶 ,吸 附分 离 作 为 一个 化 工单 元操作 ,在工业 上作 为一 种辅 助 的工艺过 程开始 得 到应 用 ,其应用 范 围只限于工 业气 体 的干 燥脱水 和 微 量 C 。的 脱 除 。近 4 O O年 来 ,随 着 变 压 吸 附
( rs r wn dopi ,简 称 P A) 技 术 的发 Pes eS igA srt n u o S
展 ,吸附 分离 已成 为一种 简单 、有效 的气 体分离方
法 ,广 泛应 用于化 工 、冶 金 、电子 、医药 、食品等 行业 ,并逐 渐发展 成为继 深冷法 之后 的又一 新兴 的
变压吸 附技术在合成氨厂的应用
毛 薛刚,张玉迅 ,周 洪富,管建平
( 江 江 山化 工股 份 有 限公 司 ,浙 江 江 山 浙 34 0 ) 2 10
变压吸附在沼气脱碳中的应用
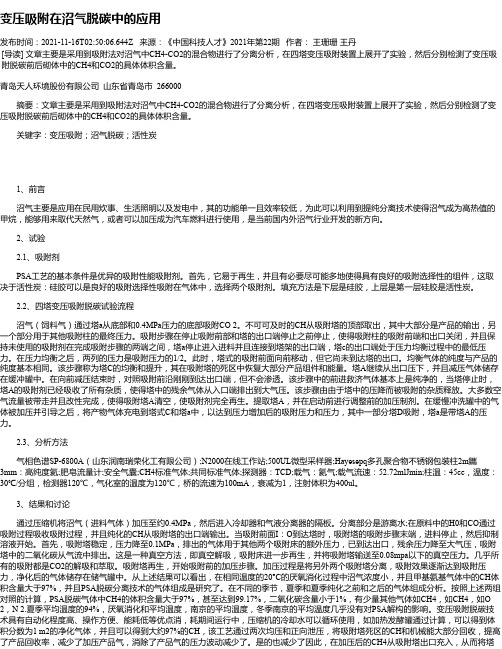
变压吸附在沼气脱碳中的应用发布时间:2021-11-16T02:50:06.644Z 来源:《中国科技人才》2021年第22期作者:王珊珊王丹[导读] 文章主要是采用到吸附法对沼气中CH4-CO2的混合物进行了分离分析,在四塔变压吸附装置上展开了实验,然后分别检测了变压吸附脱碳前后砌体中的CH4和CO2的具体体积含量。
青岛天人环境股份有限公司山东省青岛市 266000摘要:文章主要是采用到吸附法对沼气中CH4-CO2的混合物进行了分离分析,在四塔变压吸附装置上展开了实验,然后分别检测了变压吸附脱碳前后砌体中的CH4和CO2的具体体积含量。
关键字:变压吸附;沼气脱碳;活性炭1、前言沼气主要是应用在民用炊事、生活照明以及发电中,其的功能单一且效率较低,为此可以利用到提纯分离技术使得沼气成为高热值的甲烷,能够用来取代天然气,或者可以加压成为汽车燃料进行使用,是当前国内外沼气行业开发的新方向。
2、试验2.1、吸附剂PSA工艺的基本条件是优异的吸附性能吸附剂。
首先,它易于再生,并且有必要尽可能多地使得具有良好的吸附选择性的组件,这取决于活性炭:硅胶可以是良好的吸附选择性吸附在气体中,选择两个吸附剂。
填充方法是下层是硅胶,上层是第一层硅胶是活性炭。
2.2、四塔变压吸附脱碳试验流程沼气(饲料气)通过塔a从底部和0.4MPa压力的底部吸附CO 2。
不可可及时的CH从吸附塔的顶部取出,其中大部分是产品的输出,另一个部分用于其他吸附柱的最终压力。
吸附步骤在停止吸附前部和塔的出口端停止之前停止,使得吸附柱的吸附前端和出口关闭,并且保持未使用的吸附剂在完成吸附步骤的两端之间,塔a停止进入进料并且连接到塔架的出口端,塔c的出口端处于压力均衡过程中的最低压力。
在压力均衡之后,两列的压力是吸附压力的1/2。
此时,塔式的吸附前面向前移动,但它尚未到达塔的出口。
均衡气体的纯度与产品的纯度基本相同。
该步骤称为塔C的均衡和提升,其在吸附塔的死区中恢复大部分产品组件和能量。
变压吸附节能技术应用
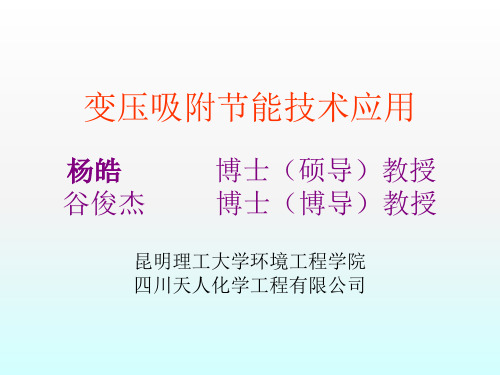
(二)转移抽空技术
使吸附剂利用效率提高30%,真空泵效率提高 40%。
该技术在福建永安公司新建2.6MPa十六塔一段 法装置应用,一次开车成功,创造出一段法全部再生 气二氧化碳平均浓度95.5%的国内先进水平,30%再 生气二氧化碳浓度98.5%。3万3气量132kw电机真空 泵1台。
目前,常规二段法变压吸附脱碳的主要弊端如下 1、顺放气放空有效气气损大约3% 2、二段再生气放空有效气气损大约2% 3、总损失高达5%左右 目前,常规二段法变压吸附脱碳的主要优点如下 1、电耗低 2、投资省 3、启动停止快 4、负荷加减容易 5、环境友好 6、建设周期短 7、自主知识产权
三、我们的创新之处在于以下五点。
(一)特殊均压方法
把原来放空气体中的更多有效气体直接回收进入 本装置,这样可以降低使用外部回收方法所需要的 能耗,而且,气体处理能力完全不会降低。
例一:宜化股份尿素0.8MPa两段法脱碳抽空工 艺改造,使用上述手法,处理气量不变,减少了顺 放气体损失(回收有效气体2%),尿素二氧化碳 浓度提高1%,停掉了置换气压缩机,吨氨节电 15KWH。
该技术在阜丰集团扎兰屯公司新建1.4MPa十二 塔一段法装置应用,一次开车成功,再次创造出一段 法全部再生气二氧化碳平均浓度95.5%的国内先进水 平,30%再生气二氧化碳浓度99.1%。3万6气量 132kw电机真空泵1台。
(三)吸附时间所占的比例减少到合理的最少
这与传统的更长时间吸附的概念完全背道而驰。 这个技术应用到一些已建变压吸附改造证明是十分 有效的。
3、再生气总平均浓度提高4%,有效气损降低2%, 气损减少带来的效益使氨醇总产量增产每天15吨, 总煤电消耗无变化。
变压吸附脱碳装置在氮肥生产中的应用

・
8 ・
2 01 3 年
8 月
变 压 吸 附脱 碳 装 置在 氮肥 生产 中的应 用
郑 高潮
( 安徽 吴 源 化 工 集 团 有 限 公 司 ,安 徽 阜 阳 2 3 6 8 0 0 ) 摘 要 :介 绍 变 压 吸 附脱 碳 的基 本 原 理 、设 计 参 数 、工 艺 流 程 及 主 要 设 备 ,系 统 的运 行 情 况 及 优 化 改
造措施 。
关 键 词 :变 压 吸 附 脱碳 ;运 行情 况 ;优 化 改 造
中 图 分 类 号 :T Q1 1 3 . 2 6 4 文 献标 志码 :B 文 章 编 号 :1 0 0 3 6 4 9 0 ( 2 0 1 3 ) 0 4 — 0 0 0 8 — 0 2
Ap pl i c a t i o n o f PS A De c a r b u r i z a t i 0 n Un i t i n Ni t r o g e n Fe r t i l i z e r Pr o d u c t i o n
‘9 。
4 0℃下 进 入 系 统 ,先 进 入 水 分 离 器 除 去 游 离 水 后 ,经流 量 计 计 量 进 入 由 2 0台 吸 附 器 组 成 的 P S A一1系统 ( 一段 变 压 吸 附) ,该 系 统 在任 何 时
刻 总有 5台 吸 附 器 处 于 吸 附状 态 ,出 口端 获 得 C O 含 量为 8 ~1 2 %的半 成 品气 。半成 品气 经 半 成 品气 缓 冲罐缓 冲后 ,以稳定 的 流量 、压 力输
总氨 1 0 0 0 k t / a ( 甲醇 4 0 0 k t / a ) 、尿素 1 0 0 0 k t / a 、 碳酸 氢 铵 4 0 0 k t / a 等。
变压吸附脱碳(PSA)装置在我厂的使用总结

变压吸附脱碳(PSA)装置在我厂的使用总结
李贞亿
【期刊名称】《气体净化》
【年(卷),期】2005(005)006
【摘要】贵州化肥厂有限责任公司8.13合成新系统自2002年5月26日建成投产后,因脱碳装置采用GV双塔再生工艺,主要存在问题是蒸汽消耗高,吨氨耗蒸汽3.0吨以上;再生部分腐蚀大,开车一年后经常因腐蚀泄漏造成系统停车;吸收能力差,生产负荷在55000Nm2/h的工况下,蒸汽用量稍有减少易引起吸收塔出口CO2超标;运转设备多,调节较复杂,生产操作繁琐;化工原材料消耗及电耗高;一年运行费用在800万元以上,严重制约我厂8.13合成新系统高负荷长周期安全经济运行,为了扭转这一被动局面,公司经调研后决定采用成都天立化工科技有限公司的变压吸附脱碳(PSA)工艺取代GV脱碳双塔再生工艺,于2004年3月份建成投产。
本文对变压吸附脱碳(PSA)装置运行作如下总结:【总页数】2页(P8-9)
【作者】李贞亿
【作者单位】贵州化肥厂有限责任公司,贵州贵阳551415
【正文语种】中文
【中图分类】TQ441.41
【相关文献】
1.变压吸附(PSA)脱碳技术在我厂的应用 [J], 沈建国
2.变压吸附脱碳装置在我厂的使用总结 [J], 强艳波;刘大贵
3.变压吸附脱碳(PSA)提纯装置在我厂的使用总结 [J], 何家明;李贞亿;但功睢
4.变压吸附(PSA)提氢装置使用总结 [J], 周辉南;黄布怡
5.回收PC脱碳闪蒸气及PSA脱碳逆放气装置运行总结 [J], 石锋;王群祥;马中霞因版权原因,仅展示原文概要,查看原文内容请购买。
- 1、下载文档前请自行甄别文档内容的完整性,平台不提供额外的编辑、内容补充、找答案等附加服务。
- 2、"仅部分预览"的文档,不可在线预览部分如存在完整性等问题,可反馈申请退款(可完整预览的文档不适用该条件!)。
- 3、如文档侵犯您的权益,请联系客服反馈,我们会尽快为您处理(人工客服工作时间:9:00-18:30)。
变压吸附脱碳装置在我厂的应用葛慧玲!,赵贵成"(!#新乡市燃料化肥总厂,河南新乡$%&’’";"#新乡树脂厂,河南新乡$%&’!!)摘要:介绍了变压吸附脱碳工艺的原理,详述了其工艺流程和操作步骤。
该装置投入运行后,氢气回收率可达((#)*+,氮气回收率(%#(,+,经济效益显著。
关键词:变压吸附;液氨;脱附中图分类号:-.’")#!%文献标识码:/文章编号:!’’&0&$*,("’’$)’!0’’&!0’"为了适应市场需求,优化产品结构,提高氢气的纯度和回收率,进一步扩大液氨产品的生产规模,新乡市燃料化肥总厂于"’’&年,1)月份对原四塔变压吸附脱碳装置进行了改造,原装置处理变换气量为%’’’23&45,改造后变换气处理量为!%’’’23&45。
该装置与原碳化工段并联生产,即变换气进入碳化工段后产生分流,一部分气体仍走原碳化系统生产碳酸氢铵产品,另一部分气体走脱碳系统。
变压吸附脱碳系统既能脱除变换气中的67",又不消耗气态氨。
现将改造后变压吸附脱碳装置的具体情况做一总结。
但仍收稿日期:"’’&0’(0!’作者简介:葛慧玲(!(,"0),女,助理工程师,从事化工技术管理工作,电话:’!&%()*$$((&。
・!&・河南化工"$$%年第!期万方数据未达到其出口端。
当两台吸附器压力基本相等时,关闭!"阀,一均降结束。
过程压力由#$%!&’(下降至#$)*&’(。
!$"$#第二级压力均衡降(简称二均降)开启)"阀、)+阀,"塔一均降步骤结束后,接着与刚结束三均升步骤的+塔以出口端相连进行第二次压力均衡,"塔出口端的气体经)"、)+进入+塔,均压过程中"塔的吸附前沿朝出口端方向推进,但仍未达到出口端。
当两个塔压力基本相等时,关闭)+阀,二均降结束。
过程压力由#$)*&’(下降至#$,,&’(。
!$"$$第三级压力均衡降(简称三均降)开启中间罐阀门-,并继续开启)"阀,"塔二均降步骤停止后,接着与中间罐以出口端相连进行第三次压力均衡,"塔出口端的气体经)"和-,阀进入中间罐,均压过程中间罐"塔的吸附前沿朝出口端方向推进,但仍未达到其出口端。
当两台容器压力基本相等时,关闭)"阀和-,阀,三均降步骤结束。
过程压力由#$,,&’(下降至#$.)&’(。
!$"$%第四级压力均衡降(简称四均降)开启/"和/0阀,"塔经三均降结束后,接着与刚结束抽真空步骤的0塔以出口端相连进行第四次压力均衡,"塔出口端的气体经/"、/0进入0塔,均压过程中"塔的吸附前沿朝出口端方向推进,正好到达其出口端。
当两台吸附器压力基本相等时,关闭/"、/0阀,四均步骤结束。
过程压力由#$.)&’(下降至#$#1&’(。
!$"$&逆向放压(简称逆放)开启,"阀和放空阀,"塔内逆向步骤的解吸气去放空管道,当压力接近常压(#$#.&’()时,大部分杂质已解吸,吸附剂得到一定程度的再生,关闭,"阀和放空阀,逆放步骤结束。
过程压力由#$#1&’(下降至#$#.&’(。
!$"$’抽真空开启%"阀,抽真空前期开启阀234*(以234*、2341为前期的抽真空管道),利用真空泵对吸附塔进行抽真空,进一步降低"塔的压力,使吸附剂上吸附的杂质进一步解吸,吸附剂进一步再生。
在抽真空中期再开启234--,利用另一抽真空管道上刚结束了对5塔抽真空的真空泵一起进行抽真空,进一步降低"塔的压力;在抽真空后期关闭234*,单独开启234--,由另一抽真空管道上的真空泵对吸附塔进行抽真空,抽真空结束后关闭234--、%",抽真空步骤结束。
过程压力由#$#.&’(下降至真空度#$#1&’(。
!$"$(第四级压力均衡升(简称四均升)开启/"、/6阀,"塔与刚结束三均降步骤的6塔以出口端相连进行第四次压力均衡升,均压过程中"塔的压力升高。
当两台吸附器压力基本相等时,关闭/"、/6阀,四均升步骤结束。
过程压力由真空度#$#1&’(上升至#$#1&’(。
!$"$!)第三级压力均衡升开启)"阀与-,阀,"塔与中间罐以出口端相连进行第三级压力均衡升,均压过程中,"塔压力升高。
当两个塔压力基本相等时,关闭-,阀,三均升步骤结束。
过程压力由#$#1&’(上升至#$-%&’(。
!$"$!!第二级压力均衡升开启)7,继续开启)"阀,"塔与刚结束二均降步骤的7塔进行第二级压力均衡升,均压过程中"塔压力升高。
当两个塔压力基本相等时,关闭)"、)7阀,二均升步骤结束。
过程压力由#$-%&’(上升至#$,,&’(。
!$"$!"隔离此时与吸附器"塔相连的程控阀均处于关闭状态,吸附器的压力保持不变。
过程压力保持在#$,,&’(。
!$"$!*第一级压力均衡升开启!"、!8阀,接着与刚结束顺放一步骤的8塔以出口端相连进行第一级压力均衡升,均压过程中"塔的压力升高。
当两个塔压力基本相等时,关闭!"、!8阀,一均升步骤结束。
过程压力由#$,,&’(上升至#$)*&’(。
!$"$!#最终升压继续开启!"阀和终充流量调节阀,经两次均压升步骤后,"塔最终用产品气通过调节阀限流使其逐步达到吸附压力。
当"塔的压力与吸附压力相一致时关闭!"阀和调节阀,终充步骤结束。
过程压力由#$)*&’(上升至#$1&’(。
八个吸附塔交替进行吸附、再生操作(始终有三个吸附塔处于吸附状态),即可实现气体的连续分离与提纯。
此过程是由程序控制系统通过电脑操作进行周期性地切换阀门而实现。
"工艺设备吸附塔,!".###,1台;水分离器,!"-###,-台;中间缓冲均压罐,!",###,-台;净化气缓冲罐,!",###,-台;真空泵,.98-4,#,,.台;.98!)#4)/-,-台;程控阀,!",##,-.台;!"-!#,,!台;!"-##,1台;!"1#,-#台;全自动化电脑微机操作・.,・河南化工"))#年第!期万方数据!""装置油浆系统结焦原因分析及对策刘再立,梁顶华,赵勇(中原油田石油化工总厂,河南濮阳#$%&’#)摘要:对!""装置油浆系统结焦原因进行分析,提出了有效的防焦措施,(!)*型油浆阻垢剂在我厂应用后,油浆系统运行周期增长&+&,$年,年节约费用-.万+&..万元。
关键词:催化裂化装置;油浆;结焦;油浆阻垢剂中图分类号:(/’*#,#&文献标识码:0文章编号:&..1)1#’%(*..#).&)..11).*催化裂化(!"")装置为重要炼油装置之一,随着我国炼油加工深度的不断提高,作为主要二次加工装置的催化所用原料也随之变得越来越复杂,油浆中芳烃、稠环芳烃含量增加,致使掺炼重油的!""装置结焦现象严重,换热器清洗频繁,装置运转周期明显缩短,能耗增加,处理量降低,轻油收率减少,经济效益明显下降,因此,!""装置油浆系统结焦和积垢问题已成为制约!""装置长周期运行的主要问题。
!油浆系统结焦的原因分析油浆系统结焦除塔底温度较高、油浆含有催化剂颗粒外,主要原因是由于!""油浆中含有一定量的胶质和沥青质及其前体物质,它们以不稳定的非均态中间相存在,在一定条件下,这些物质会发生缠绕、凝降和高分子化,从而在管道、换热器及其它部位粘附、积累,形成油垢和油焦,这些油垢和油焦在高温下很快炭化形成石墨状焦炭。
"防焦措施",!!""装置减少油浆系统结焦的传统手段",!,!增大油浆循环量,降低塔底液面,以减少油浆在塔底的停留时间。
油浆结焦的主要化学过程是聚合反应,减少油浆的停留时间即能减少结焦反应的反应时间。
因此,降低分馏塔塔底液面可以减少油浆结焦。
",!,"降低循环油浆返塔温度,加大油浆返塔下入口量,用急冷油浆急冷,以降低分馏塔底温度。
适宜的塔底温度与进料性质有关,也和反应温度有密切关系,反应温度越高,塔底温度也就越高,油浆相对密度会明显上升,油浆系统的结焦趋向也会增大。
塔底温度与油浆中焦粒含量关系如图&所示,分馏塔塔底温度(液相)通常规定不高于1-.2。
控制塔底温度的措施主要是循环油浆取热量和向塔底打入急冷油。
油浆循环取热量不能小于某一数值,这是因为要尽量减少停留时间,就要保证管线和换热器有一定的流速,同时还要保证一定的取热比例以满足分馏塔操作需要和节能需要。
打入冷油时量要适宜,且不能减少正常的油浆循环量,否则会降低油浆对反应油气的洗涤效果,导致上层挡板结焦或塔盘堵塞。
期万方数据。