AAO工艺
倒置AA0工艺优缺点

倒置AA0工艺优缺点AA0工艺是一种常用的制造工艺,具有一定的优点和缺点。
下面将详细介绍AA0工艺的优缺点。
AA0工艺的优点主要有以下几个方面:1.简单易操作:AA0工艺相对于其他工艺来说比较简单,操作过程相对简单,工人上手难度低,不需要太高的技术要求,且操作过程快捷高效。
2.成本相对较低:相对于其他制造工艺来说,AA0工艺的设备相对简单,投资成本低,生产成本相对较低。
这使得AA0工艺在中小企业中得到广泛应用。
3.适应范围广:AA0工艺适应性广泛,可以用于多种不同材料的加工,无论是金属、非金属还是复合材料,AA0工艺都能有效地应用。
4.生产效率高:AA0工艺操作方便快捷,生产效率高。
可以实现快速、大批量的生产,提高产品的生产速度和供应效率。
5.产品质量稳定:AA0工艺在生产过程中可以实现较高的精度和稳定性,可以保证产品的质量稳定。
这对于需要高质量产品的行业来说尤其重要。
虽然AA0工艺具有许多优点,但也存在一些不足之处:1.能耗较高:AA0工艺在生产过程中需要较高的能源消耗,特别是在高负载和连续生产的情况下,能源消耗量更为明显。
这增加了企业的生产成本,并对环境产生不利影响。
2.操作复杂性:尽管AA0工艺相对于其他工艺来说较为简单,但其操作过程仍然需要有一定的技术要求。
对于操作人员来说,需要一定的培训和经验才能熟练使用该工艺。
3.产生废料:AA0工艺在生产过程中会产生一定数量的废料,特别是在加工过程中需要进行切割和修整的情况下。
这增加了企业的处理成本,并对环境造成一定的污染。
4.限制工件尺寸:AA0工艺在生产过程中对工件的尺寸有一定的限制。
较大尺寸的工件可能无法通过AA0工艺进行加工,这会限制该工艺的应用范围。
5.需要定期维护:AA0工艺设备需要定期进行保养和维护,以确保其正常运行。
这增加了企业的维护成本和维护工作的复杂性。
综上所述,AA0工艺具有诸多优点,如操作简单、成本低、适应范围广、生产效率高和产品质量稳定。
AAO工艺概述范文

AAO工艺概述范文AAO工艺,即铝阳极氧化(Anodizing Aluminum Oxide)工艺,是一种通过对铝金属进行氧化处理得到氧化铝膜的技术。
它是利用铝金属在导电性电解质中的阳极氧化反应,形成均匀且致密的氧化铝膜,然后在表面上形成一种保护膜,以提高铝金属的表面硬度、耐磨性、防腐蚀性和装饰性能。
AAO工艺的应用广泛,涵盖了电子、航空航天、汽车、建筑等众多领域。
特别是在电子领域,AAO工艺被广泛用于半导体器件制备、纳米科技研究和微加工等方面。
它不仅能够提高铝基材的机械性能,还可以改善其导电性能、绝缘性能、热稳定性和光学性能。
AAO工艺的主要步骤包括:预处理、阳极氧化、密封处理和后处理。
首先,需要对铝金属进行预处理,包括去油、脱脂、酸洗等。
然后将铝件作为阳极,放入含有硫酸、草酸等电解质的电解槽中进行氧化反应。
在电解槽中,阳极与电解质形成一对阴阳电极,在外加电压下,阳极表面发生阳极氧化反应,生成氧化铝膜。
氧化铝膜的形成过程是一个电化学反应过程。
电解质中的阳离子会在阳极表面发生氧化反应,生成氧化铝。
同时,阴离子在阳极表面和阳极底部形成疏水层,形成双层结构,阻止进一步的氧化反应。
这种双层结构能够形成很多孔洞,这些孔洞间距均匀,形成有序的规则阵列,被称为孔道阵列膜。
AAO工艺的关键技术是控制氧化铝膜的孔径和孔道间距。
孔洞的形成与电解液中的离子传输速率密切相关。
调节电解质的成分、浓度和温度等参数可以控制膜的微观结构,从而控制孔径和孔道间距。
通过改变这些参数,可以制备出不同孔径、孔道间距和孔洞形状的氧化铝膜。
除了制备氧化铝膜,AAO工艺还可以进行后处理,如染色、封孔和增强等。
染色能够改变氧化铝膜的颜色,增加其装饰性能。
封孔可以填充孔洞,提高氧化铝膜的密度和耐腐蚀性能。
增强指的是对氧化铝膜进行进一步改性,可采用电化学沉积、热处理等方法。
总之,AAO工艺是一种重要的表面处理技术,能够提供耐磨、耐腐蚀和防护功能。
AAO简介

A2/O工艺A2/O工艺亦称A-A-O工艺,是英文Anaerobic-Anoxic-Oxic 第一个字母的简称(生物脱氮除磷)。
按实质意义来说,本工艺称为厌氧-缺氧-好氧法,生物脱氮除磷工艺的简称。
A2/O工艺是流程最简单,应用最广泛的脱氮除磷工艺。
污水首先进入厌氧池,兼性厌氧菌将污水中的易降解有机物转化成VFAs。
回流污泥带入的聚磷菌将体内的聚磷分解,此为释磷,所释放的能量一部分可供好氧的聚磷菌在厌氧环境下维持生存,另一部分供聚磷菌主动吸收VFAs,并在体内储存PHB。
进入缺氧区,反硝化细菌就利用混合液回流带入的硝酸盐及进水中的有机物进行反硝化脱氮,接着进入好氧区,聚磷菌除了吸收利用污水中残留的易降解BOD外,主要分解体内储存的PHB产生能量供自身生长繁殖,并主动吸收环境中的溶解磷,此为吸磷,以聚磷的形式在体内储存。
污水经厌氧,缺氧区,有机物分别被聚磷菌和反硝化细菌利用后浓度已很低,有利于自养的硝化菌的生长繁殖。
最后,混合液进入沉淀池,进行泥水分离,上清液作为处理水排放,沉淀污泥的一部风回流厌氧池,另一部分作为剩余污泥排放。
本工艺在系统上可以称为最简单的同步脱氮除磷工艺,总的水力停留时间少于其他同类工艺。
而且在厌氧-缺氧-好养交替运行条件下,不易发生污泥膨胀。
运行中无须投药,厌氧池和缺氧池只需轻缓搅拌,运行费用低。
该工艺处理效率一般能达到:BOD5和SS为90%~95%,总氮为70%以上,磷为90%左右,一般适用于要求脱氮除磷的大中型城市污水厂。
但A2/O工艺的基建费和运行费均高于普通活性污泥法,运行管理要求高,所以对目前我国国情来说,当处理后的污水排入封闭性水体或缓流水体引起富营养化,从而影响给水水源时,才采用该工艺。
本工艺具有如下特点:(1)本工艺在系统上可以称为最简单的同步脱氮除磷工艺,总的水力停留时间少于其他同类工艺(2)在厌氧(缺氧)、好氧交替运行条件下,丝状菌不能大量增殖,无污泥膨胀之虞,SVI 值一般均小于100 (3)污泥中含磷浓度高,具有很高的肥效(4)运行中勿需投药,两个A断只用轻缓搅拌,并不增加溶解氧浓度,运行费用低本法也存在如下各项的待解决问题(1)除磷效果难于再行提高,污泥增长有一定的限度,不易提高,特别是当P/BOD值高时更是如此(2)脱氮效果也难于进一步提高,内循环量一般以2Q为限,不宜太高(3)进入沉淀池的处理水要保持一定浓度的溶解氧,减少停留时间,防止产生厌氧状态和污泥释放磷的现象出现、但溶解氧浓度也不宜过高,以防循环混合液对缺氧反应器的干扰1.A2O池的检测与控制参数的确定A2O生物除磷脱氮工艺处理污水效果与DO、内回流比r、外回流比R、泥龄SRT、污水温度及PH值等有关。
AAO工艺

缺 氧 段
反硝化反应可在5~27℃进行,反硝化速
率随温度升高而加快,适宜的温度范围为
15~25℃。
14
厌氧段
温度对厌氧释磷的影响不太明 显,在5~30℃除磷效果均很好。
15
4. pH值的影响
在厌氧段,聚磷菌厌氧释磷的适宜pH值 是6~8;在缺氧反硝化段,对反硝化菌脱氮适宜 的pH值为6.5~7.5;在好氧硝化段,对硝化菌适 宜的pH值为7.5~8.5。
混合液回流带入的硝酸盐及进水中的有机物进行反硝化脱
氮,接着进入好氧区,聚磷菌除了吸收利用污水中残留的
易降解BOD外,主要分解体内储存的PHB产生能量供自身
声场繁殖,并主动吸收环境中的溶解磷,此为吸磷,以聚
磷的形式在体内储存。
5
6
简图
混合液回流
进水
厌氧池
缺氧池
好氧池
沉淀池
氧,缺氧区,有机物分别被聚磷 菌 和反硝化细菌利用后浓度已很低,有利于自 养的硝化菌的生长繁殖。最后,混合液进入沉淀 池,进行泥水分离,上清液作为处理水排放,沉 淀污泥的一部风回流厌氧池,另一部分作为剩余 污泥排放。
2
3
AAO工艺流程
4
污水首先进入厌氧池,兼性厌氧菌将污水中的易降
解有机物转化成VFAs(挥发性脂肪酸)。回流污泥带入的
聚磷菌将体内的聚磷分解,此为释磷,所释放的能量一部
分可供好氧的聚磷菌在厌氧环境下维持生存,另一部分供
聚磷菌主动吸收VFAs(挥发性脂肪酸),并在体内储存
PHB(聚羟基丁酸酯)。进入缺氧区,反硝化细菌就利用
厌氧池
10
好氧池
在好氧段,当有机物浓度高 时污泥负荷也较大,降解有机 物的异养型好氧菌超过自养 型好氧硝化菌,使氨氮硝化不 完全,出水中NH+4-N浓度急 剧上升,使氮的去除效率大大 降低。所以要严格控制进入 好氧池污水中的有机物浓度, 在满足好氧池对有机物需要 的情况下,使进入好氧池的有 机物浓度较低,以保证硝化细
AAO工艺简介
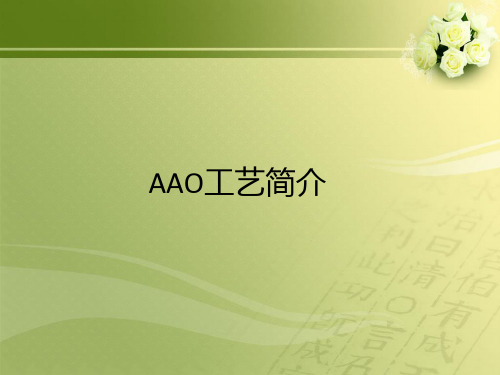
七、生物除磷的影响因素
七、生物除磷的影响因素
七、生物除磷的影响因素
AAO运行影响因素及其分析
(1)污水中可生物降解有机物的影响 聚磷菌本身是好氧菌,在厌氧池中其运动能力很弱,增殖缓慢,只能利用 低分子的有机物,是竞争能力很差的软弱细菌。但当它处于不利的厌氧环境 下,能将贮藏的磷通过水解而释放出来,并利用其产生的能量吸收低分子有 机物,在利用有机物的竞争中比其它好氧菌占优势,聚磷菌成为厌氧段的优 势菌群。因此,污水中可生物降解有机物对聚磷菌厌氧释磷起着关键性的作 用。 在缺氧段,异养型兼性反硝化菌成为优势菌群,将回流混合液中的 硝态氮还原成N2而释放,从而达到脱氮的目的。污水中的可降解有机物浓度 高,则C/N比高,反硝化速率大,缺氧段的水力停留时间HRT短,一般为0.51.0h即可。反之,反硝化速率小,HRT需2-3h。可见污水中的 C/N比值较低时, 则脱氮率不高。 在好氧段,当有机物浓度高时污泥负荷也较大,降解 有机物的异养型好氧菌超过自养型好氧硝化菌,使氨氮硝化不完全 ,出水中 NH4+-N浓度急剧上升,使氮的去除效率大大降低。所以要严格控制进入好氧池 污水中的有机物浓度,在满足好氧池对有机物需要的情况下,使进入好氧池 的有机物浓度较低,以保证硝化细菌在好氧池中占优势生长,使硝化作用完 全。 由此可见,在厌氧池,要有较高的有机物浓度;在缺氧池,应有充足 的有机物,而在好氧池的有机物浓度应较小。
无机氮
是指氨氮、亚硝酸盐氮和硝酸盐氮等,它们一部分是由有机氮经微生物分解转化 作用而产生的,一部分直接来自于施用化肥的农田退水和工业排水。
凯氏氮
是有机氮与氨氮之和,凯氏氮指标可以用来判断污水在进行生物法处理时氮营养 是否充足。
氨氮
在污水中存在的形式有游离氨(NH3)与离子状态铵盐(NH4)两种
AAO的工艺流程

AAO的工艺流程
《AAO的工艺流程》
AAO,即铝阳极氧化,是一种将铝制品表面形成一层致密、硬度高、耐腐蚀的阳极氧化膜的工艺过程。
下面将介绍AAO 的工艺流程。
1. 预处理
首先,铝制品需要经过预处理,包括去油、除锈等工序,以保证表面干净和无杂质。
2. 碱洗
接下来,铝制品会进行碱洗,将其浸泡在碱性溶液中,去除表面的氧化皮、污物和残留物质。
3. 阳极氧化
铝制品经过碱洗后,进入阳极氧化的工艺过程。
铝制品作为阳极,放在硫酸或者柠檬酸的电解液中,通过直流电进行阳极氧化处理,使表面形成致密的氧化膜。
4. 封闭
在阳极氧化后,需要进行封孔处理。
通常采用热水封孔或者镀封孔的方法,以增加氧化膜的致密性和硬度。
5. 整砂
最后,对经过阳极氧化和封闭的铝制品进行整砂处理,使其表面更加光亮、平整。
通过以上工艺流程,铝制品的表面就可以形成一层高质量的阳极氧化膜,具有耐腐蚀、耐磨损、绝缘、装饰等特性,广泛应用于航空航天、电子、建筑等领域。
AAO工艺原理及过程

AAO工艺原理及过程传统活性污泥法是应用最早的工艺,它去除有机物的效率很高,近20年来,水体富营养化的危害越来越严重,去除氮、磷列入了污水处理的目标,于是出现了活性污泥法的改进型AO工艺和AAO工艺。
AO工艺有两种,一种是用于除磷的厌氧—好氧工艺,一种是用于脱氮的缺氧—好氧工艺;AAO工艺则是既脱氮又除磷的工艺。
1、AAO工艺原理及过程A-A-O生物脱氮除磷工艺是传统活性污泥工艺、生物硝化及反硝化工艺和生物除磷工艺的综合。
在该工艺流程内,BOD、SS和以各种形式存在的氮和磷将一并被去除。
该系统的活性污泥中,菌群主要由硝化菌、反硝化菌和聚磷菌组成,专性厌氧和一般专性好氧菌群均基本被工艺过程所淘汰。
在好氧段,硝化细菌将入流中的氨氮及由有机氮氨化成的氨氮,通过生物硝化作用,转化成硝酸盐;在缺氧段,反硝化细菌将内回流带入的硝酸盐通过生物反硝化作用,转化成氮气逸入大气中,从而达到脱氮的目的;在厌氧段,聚磷菌释放磷,并吸收低级脂肪酸等易降解的有机物;而在好氧段,聚磷菌超量吸收磷,并通过剩余污泥的排放,将磷去除。
在以上三类细菌均具有去除BOD的作用,但BOD的去除实际上以反硝化细菌为主。
以上各种物质去除过程可直观地用图所示的工艺特性曲线表示。
污水进入曝气1池以后,随着聚磷菌的吸收、反硝化菌的利用及好氧段好氧生物分解,BOD浓度逐渐降低。
在厌氧段,由于聚磷菌释放磷,TP浓度逐渐升高,至缺氧段升至最高。
在缺氧段,一般认为聚磷菌既不吸收磷,也不释放磷,TP 保持稳定。
在好氧段,由于聚磷菌的吸收,TP迅速降低。
在厌氧段和缺氧段,氨氮浓度稳中有降,至好氧段,随着硝化的进行,氨氮逐渐降低。
在缺氧段,NO3-N瞬间升高,主要是由于内回流带入大量的NO3-N,但随着反硝化的进行,硝酸盐浓度迅速降低。
在好氧段,随着硝化的进行,NO3-N浓度逐渐升高。
2、AAO工艺参数和影响因素A-A-O生物脱氮除磷的功能是有机物去除、脱氮、除磷三种功能的综合,因而其工艺参数应同时满足各种功能的要求。
aao工艺流程详解
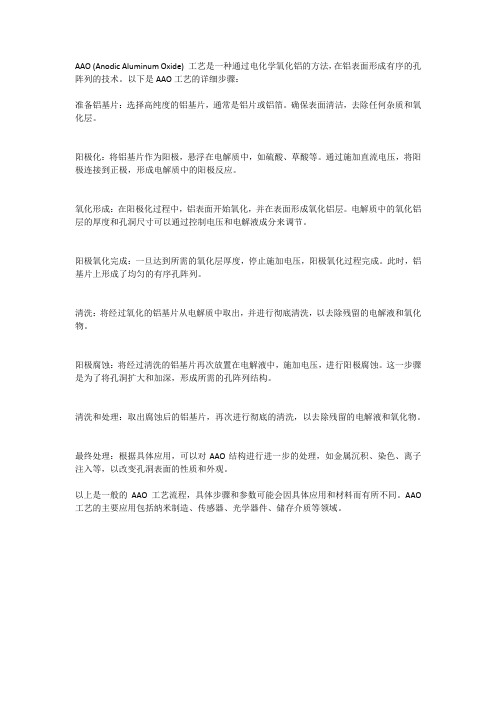
AAO (Anodic Aluminum Oxide) 工艺是一种通过电化学氧化铝的方法,在铝表面形成有序的孔阵列的技术。
以下是AAO工艺的详细步骤:
准备铝基片:选择高纯度的铝基片,通常是铝片或铝箔。
确保表面清洁,去除任何杂质和氧化层。
阳极化:将铝基片作为阳极,悬浮在电解质中,如硫酸、草酸等。
通过施加直流电压,将阳极连接到正极,形成电解质中的阳极反应。
氧化形成:在阳极化过程中,铝表面开始氧化,并在表面形成氧化铝层。
电解质中的氧化铝层的厚度和孔洞尺寸可以通过控制电压和电解液成分来调节。
阳极氧化完成:一旦达到所需的氧化层厚度,停止施加电压,阳极氧化过程完成。
此时,铝基片上形成了均匀的有序孔阵列。
清洗:将经过氧化的铝基片从电解质中取出,并进行彻底清洗,以去除残留的电解液和氧化物。
阳极腐蚀:将经过清洗的铝基片再次放置在电解液中,施加电压,进行阳极腐蚀。
这一步骤是为了将孔洞扩大和加深,形成所需的孔阵列结构。
清洗和处理:取出腐蚀后的铝基片,再次进行彻底的清洗,以去除残留的电解液和氧化物。
最终处理:根据具体应用,可以对AAO结构进行进一步的处理,如金属沉积、染色、离子注入等,以改变孔洞表面的性质和外观。
以上是一般的AAO工艺流程,具体步骤和参数可能会因具体应用和材料而有所不同。
AAO 工艺的主要应用包括纳米制造、传感器、光学器件、储存介质等领域。
AAO工艺特点和运行注意事项

AAO工艺特点和运行注意事项AAO工艺(Anoxic-anaerobic-oxic process)是一种处理工业废水和城市污水的一种生物处理工艺。
它通过将废水依次通入缺氧区、厌氧区和缺氧区,使得废水在不同的环境中接触不同的微生物,从而有效地降解有机污染物和氮磷等无机污染物。
下面将详细介绍AAO工艺的特点和运行注意事项。
1.高效处理能力:AAO工艺充分利用了微生物的生物降解能力,能够高效地降解有机污染物。
同时,AAO工艺还能对氮磷等无机污染物进行去除,使得处理效果更为显著。
2.节省能源:AAO工艺采用了曝气系统,能够提供充分的供氧条件,使得微生物在处理废水时能够充分利用氧气进行降解。
同时,AAO工艺还采用了生物膜系统,能够提高微生物对有机污染物的吸附能力,进一步提升处理能力。
3.操作稳定性好:AAO工艺能够在不同负荷条件下保持较好的操作稳定性。
通过合理的负荷控制和滞留时间的调节,能够避免废水处理过程中的剧烈波动,从而保持系统的稳定运行。
4.占地面积小:AAO工艺采用了生物膜系统,能够大大减小处理装置的体积,从而节省占地面积。
这对于城市污水处理厂等空间有限的场所来说特别适用。
1.控制供氧:AAO工艺需要提供适量的氧气供给微生物进行降解,但供氧过多或过少都会影响处理效果。
因此,在运行过程中需要根据废水的有机负荷和氧化反应的需求,合理控制供氧量。
2.保持良好通气:AAO工艺需要通过曝气系统提供充分的氧气供给微生物,因此需要保持曝气系统的通气正常。
同时,需要定期清洗和维护曝气管道和曝气头,确保曝气效果良好。
3.控制水力负荷:AAO工艺对水力负荷非常敏感,如果负荷过大或过小,都会影响处理效果。
因此,在运行过程中需要根据实际情况合理控制水力负荷,避免废水处理过程中的剧烈波动。
4.定期清洗生物膜:AAO工艺采用了生物膜系统,需要定期清洗生物膜,以去除附着在生物膜上的污染物和生物膜内部的死亡菌体。
同时,需要注意清洗过程中不要破坏生物膜的完整性。
AAO工艺概述
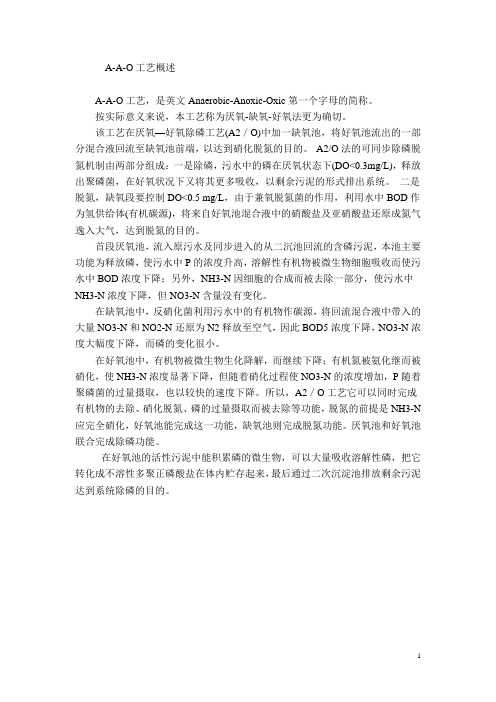
A-A-O工艺概述A-A-O工艺,是英文Anaerobic-Anoxic-Oxic第一个字母的简称。
按实际意义来说,本工艺称为厌氧-缺氧-好氧法更为确切。
该工艺在厌氧—好氧除磷工艺(A2/O)中加一缺氧池,将好氧池流出的一部分混合液回流至缺氧池前端,以达到硝化脱氮的目的。
A2/O法的可同步除磷脱氮机制由两部分组成:一是除磷,污水中的磷在厌氧状态下(DO<0.3mg/L),释放出聚磷菌,在好氧状况下又将其更多吸收,以剩余污泥的形式排出系统。
二是脱氮,缺氧段要控制DO<0.5 mg/L,由于兼氧脱氮菌的作用,利用水中BOD作为氢供给体(有机碳源),将来自好氧池混合液中的硝酸盐及亚硝酸盐还原成氮气逸入大气,达到脱氮的目的。
首段厌氧池,流入原污水及同步进入的从二沉池回流的含磷污泥,本池主要功能为释放磷,使污水中P的浓度升高,溶解性有机物被微生物细胞吸收而使污水中BOD浓度下降;另外,NH3-N因细胞的合成而被去除一部分,使污水中NH3-N浓度下降,但NO3-N含量没有变化。
在缺氧池中,反硝化菌利用污水中的有机物作碳源,将回流混合液中带入的大量NO3-N和NO2-N还原为N2释放至空气,因此BOD5浓度下降,NO3-N浓度大幅度下降,而磷的变化很小。
在好氧池中,有机物被微生物生化降解,而继续下降;有机氮被氨化继而被硝化,使NH3-N浓度显著下降,但随着硝化过程使NO3-N的浓度增加,P随着聚磷菌的过量摄取,也以较快的速度下降。
所以,A2/O工艺它可以同时完成有机物的去除、硝化脱氮、磷的过量摄取而被去除等功能,脱氮的前提是NH3-N 应完全硝化,好氧池能完成这一功能,缺氧池则完成脱氮功能。
厌氧池和好氧池联合完成除磷功能。
在好氧池的活性污泥中能积累磷的微生物,可以大量吸收溶解性磷,把它转化成不溶性多聚正磷酸盐在体内贮存起来,最后通过二次沉淀池排放剩余污泥达到系统除磷的目的。
AAO工艺法时间:2010-10-21来源:中国石油化工信息网1 AAO 法工艺介绍AAO 生物脱氮工艺将传统的活性污泥、生物硝化工艺结合起来, 取长补短, 更有效的去除水中的有机物。
aao处理工艺

aao处理工艺AAO(Anodic Aluminum Oxide)是一种具有非常独特的孔洞结构的纳米材料。
通过在铝金属表面形成一层高质量、均匀的氧化铝膜,并随后在氧化层内部制备出具有纳米级孔洞结构的AOx膜,用于生物传感、储氢等领域。
AAO处理工艺是制备AØx膜的关键步骤,主要包括以下几个方面:1. 铝片处理:AAO膜的制备需要铝片来作为基底,所以铝片的制备很关键。
铝片应去除所有的氧化物和含铁杂质。
加入少量铜可以提高气氛纯度。
2. 氧化:铝片通过氧化步骤,表面形成一层均匀的氧化层。
基本上有三种氧化方式:化学氧化法、电化学氧化法、阳极氧化法。
其中,阳极氧化法就是最常用的方法,因为它可以产生更加均匀的氧化铝层,并且孔道大小可以通过调整阳极电压控制。
3. 蚀刻:在形成均匀氧化铝层后,铝金属在氧化层上面的部分应该被蚀刻掉,让形成的氧化铝膜暴露在空气中,这是制备AØx膜的第一步。
蚀刻步骤可以通过酸侵蚀或高温甲醇氧化(表面生成一层疏水的覆盖层)来实现,以产生疏水或亲水表面。
4. 清洗:清洗步骤非常重要,因为杂质物质会干扰膜的制备过程,并导致质量问题。
清洗步骤通常包括纯化水、丙酮、异三甲苯等溶液的反复浸泡和超声清洗,以确保基底表面纯净。
5. 躁度控制:这个步骤非常难,但是非常关键。
在制备AØx膜过程中,如果产生的气体泡络在孔壁上,孔洞就会产生变形,从而影响膜孔洞的均匀性和大小。
因此,通过调整阴极电压和控制蚀刻时间可以精确控制进入氧化铝膜的电荷量和电流密度,从而调整孔洞大小和间距,以在保持一定厚度下控制成膜质量。
6. 应用:制备出的AØx膜可以应用于多个领域,例如生物传感、模拟微流体实验、储氢等等。
总之,AAO处理工艺是制备AØx膜的主要步骤。
每个步骤的参数都有很大影响,只有精确控制每一步才能获得高质量的AØx膜。
aao工艺流程

aao工艺流程
AAO工艺是指通过阳极氧化法(Anodic Aluminum Oxide)制备具有高度有序的正交排列的纳米孔阵列的一种方法。
该工艺流程主要包括以下几个步骤:
1. 预处理:首先将铝片或铝箔进行表面处理,去除任何杂质和氧化物。
这可以通过机械抛光、电化学抛光、酸洗或碱洗等方法实现。
2. 阳极氧化:将预处理后的铝片放置在电解槽中,通过施加电压和电流来进行阳极氧化。
在这个过程中,铝表面的氧化层会逐渐增厚形成纳米孔阵列。
3. 洗涤:阳极氧化后,需要将铝片进行洗涤,以去除残留的电解液、氧化产物和其他杂质,以保证孔洞的质量。
4. 离子交换:在洗涤后,还需要进行离子交换,以去除阳极氧化过程中形成的氧化物和杂质。
这可以通过电解液转换或离子交换树脂进行。
5. 后处理:最后,可以通过化学改性、蒸发沉积或浸渍等方法对阳极氧化过后的铝片进行后处理,以改变孔洞的尺寸、形状和化学性质。
以上就是AAO工艺的主要流程,该工艺可以制备出具有高度有序纳米孔阵列的铝膜,具有广泛的应用前景,如光学、电子器件、传感器、催化剂等方面。
aao处理工艺

aao处理工艺AAO处理工艺是一种新型的纳米加工技术,它是通过电化学氧化的方法,在铝箔表面形成一层纳米孔阵列,这些孔洞的直径和间距可以通过调整电解液的成分和电解条件来控制。
AAO处理工艺具有孔径精度高、孔洞密度可调、孔洞深度可控、孔洞形状规则等优点,因此在纳米电子学、纳米光学、纳米生物学等领域得到了广泛的应用。
AAO处理工艺的基本原理是利用铝箔表面的氧化层作为电解质,通过电解的方式在氧化层上形成一层纳米孔阵列。
在电解过程中,铝箔作为阳极,电解液中的氧化剂作为阴极,通过电解反应在氧化层上形成一层氧化铝膜。
在氧化铝膜上形成的孔洞是由于氧化铝膜内部的氧化物被电解液中的氧化剂溶解而形成的。
通过调整电解液的成分和电解条件,可以控制孔洞的直径和间距,从而实现对孔洞密度和孔洞形状的控制。
AAO处理工艺在纳米电子学中的应用主要是制备纳米电极和纳米电容器。
由于AAO处理工艺可以制备出孔径精度高、孔洞密度可调的纳米孔阵列,因此可以用来制备纳米电极和纳米电容器。
纳米电极和纳米电容器具有体积小、电容大、电阻小等优点,因此在微电子学和纳米电子学中得到了广泛的应用。
AAO处理工艺在纳米光学中的应用主要是制备纳米光学结构。
由于AAO处理工艺可以制备出孔径精度高、孔洞密度可调的纳米孔阵列,因此可以用来制备纳米光学结构。
纳米光学结构具有光学性质优异、尺寸可控等优点,因此在光学传感、光学通信等领域得到了广泛的应用。
AAO处理工艺在纳米生物学中的应用主要是制备纳米孔阵列。
由于AAO处理工艺可以制备出孔径精度高、孔洞密度可调的纳米孔阵列,因此可以用来制备纳米孔阵列。
纳米孔阵列具有尺寸可控、孔径精度高等优点,因此在生物分子检测、单分子分析等领域得到了广泛的应用。
AAO处理工艺是一种新型的纳米加工技术,它具有孔径精度高、孔洞密度可调、孔洞深度可控、孔洞形状规则等优点,在纳米电子学、纳米光学、纳米生物学等领域得到了广泛的应用。
aao工艺流程原理
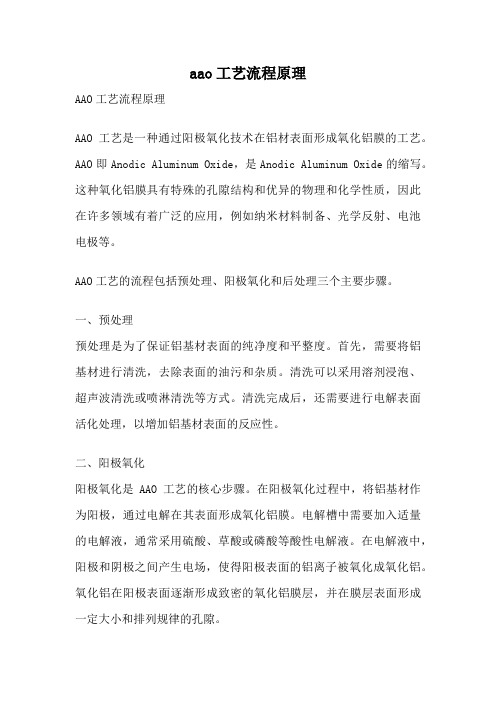
aao工艺流程原理AAO工艺流程原理AAO工艺是一种通过阳极氧化技术在铝材表面形成氧化铝膜的工艺。
AAO即Anodic Aluminum Oxide,是Anodic Aluminum Oxide的缩写。
这种氧化铝膜具有特殊的孔隙结构和优异的物理和化学性质,因此在许多领域有着广泛的应用,例如纳米材料制备、光学反射、电池电极等。
AAO工艺的流程包括预处理、阳极氧化和后处理三个主要步骤。
一、预处理预处理是为了保证铝基材表面的纯净度和平整度。
首先,需要将铝基材进行清洗,去除表面的油污和杂质。
清洗可以采用溶剂浸泡、超声波清洗或喷淋清洗等方式。
清洗完成后,还需要进行电解表面活化处理,以增加铝基材表面的反应性。
二、阳极氧化阳极氧化是AAO工艺的核心步骤。
在阳极氧化过程中,将铝基材作为阳极,通过电解在其表面形成氧化铝膜。
电解槽中需要加入适量的电解液,通常采用硫酸、草酸或磷酸等酸性电解液。
在电解液中,阳极和阴极之间产生电场,使得阳极表面的铝离子被氧化成氧化铝。
氧化铝在阳极表面逐渐形成致密的氧化铝膜层,并在膜层表面形成一定大小和排列规律的孔隙。
三、后处理后处理是为了使得氧化铝膜具有更好的性能和应用价值。
在后处理过程中,首先需要将氧化铝膜进行密封处理,以提高其抗腐蚀性能和机械强度。
密封处理可以采用热水密封、蒸汽密封或阳离子密封等方法。
其次,还可以通过电解染色、阳极氧化再生等方式对氧化铝膜进行改性和再利用。
AAO工艺流程的原理可以简单概括为:通过将铝基材作为阳极,在适当的电解液中进行电解氧化反应,使得铝表面形成氧化铝膜。
这种氧化铝膜具有特殊的孔隙结构和优异的性能,可应用于纳米材料制备、光学反射、电池电极等领域。
总结起来,AAO工艺流程的原理是通过预处理、阳极氧化和后处理三个步骤,将铝基材表面形成氧化铝膜。
这种氧化铝膜具有丰富的应用前景,对于提高材料性能和开发新型功能材料具有重要意义。
AAO工艺原理及过程
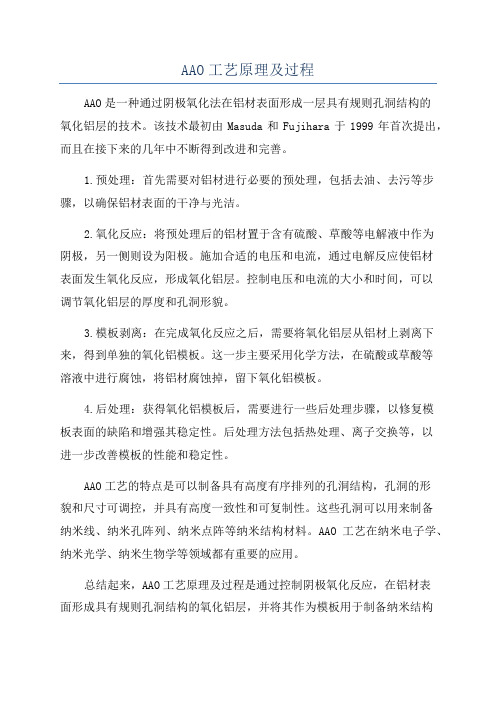
AAO工艺原理及过程
AAO是一种通过阴极氧化法在铝材表面形成一层具有规则孔洞结构的
氧化铝层的技术。
该技术最初由Masuda和Fujihara于1999年首次提出,而且在接下来的几年中不断得到改进和完善。
1.预处理:首先需要对铝材进行必要的预处理,包括去油、去污等步骤,以确保铝材表面的干净与光洁。
2.氧化反应:将预处理后的铝材置于含有硫酸、草酸等电解液中作为
阴极,另一侧则设为阳极。
施加合适的电压和电流,通过电解反应使铝材
表面发生氧化反应,形成氧化铝层。
控制电压和电流的大小和时间,可以
调节氧化铝层的厚度和孔洞形貌。
3.模板剥离:在完成氧化反应之后,需要将氧化铝层从铝材上剥离下来,得到单独的氧化铝模板。
这一步主要采用化学方法,在硫酸或草酸等
溶液中进行腐蚀,将铝材腐蚀掉,留下氧化铝模板。
4.后处理:获得氧化铝模板后,需要进行一些后处理步骤,以修复模
板表面的缺陷和增强其稳定性。
后处理方法包括热处理、离子交换等,以
进一步改善模板的性能和稳定性。
AAO工艺的特点是可以制备具有高度有序排列的孔洞结构,孔洞的形
貌和尺寸可调控,并具有高度一致性和可复制性。
这些孔洞可以用来制备
纳米线、纳米孔阵列、纳米点阵等纳米结构材料。
AAO工艺在纳米电子学、纳米光学、纳米生物学等领域都有重要的应用。
总结起来,AAO工艺原理及过程是通过控制阴极氧化反应,在铝材表
面形成具有规则孔洞结构的氧化铝层,并将其作为模板用于制备纳米结构
材料。
这一工艺具有简单、可控和可扩展性强等特点,广泛应用于纳米科技领域。
AAO的工艺流程

AAO的工艺流程AAO (Anodic Aluminum Oxide) 工艺流程是一种用于生产多孔铝氧化膜的方法。
这种方法可以通过对铝进行阳极氧化处理,形成具有一定孔径和深度的铝氧化膜。
AAO工艺在纳米科技、电子、光学、生物医学等领域有着广泛的应用,因此其工艺流程有着重要的研究价值和应用前景。
AAO工艺流程主要包含以下步骤:1. 铝基片准备:首先,选择优质纯度的铝材料作为底板,通常使用铝片或铝箔。
然后,将铝基片进行机械抛光和清洗处理,以去除表面的杂质和氧化物。
2. 阳极氧化:将准备好的铝基片浸入含有适当电解质的酸性溶液中,并将其作为阳极放入电解槽中。
通过施加直流电流,将阳极氧化反应限制在铝表面,使铝与电解液中的氧化剂发生氧化反应。
在电解液中的氧气发生还原反应,形成氧化铝薄膜。
电流密度和氧化时间的控制可以调节氧化膜的孔径和厚度。
3. 孔径调控:通过改变电解液中的温度、电流密度和氧化时间等参数,可以调控AAO膜的孔径。
一般来说,较高的电流密度和较长的氧化时间可以得到具有较大孔径的AAO膜。
4. 模板去除:在完成阳极氧化后,将AAO膜从电解槽中取出,用溶剂或酸性溶液将铝基片腐蚀去除,从而留下只有氧化铝的孔洞结构。
这样得到的AAO膜具有平整的孔径分布和高度有序的结构。
5. 表面处理:在获得的AAO膜上,可以进行进一步的表面处理,例如陶瓷或金属的镀覆,以提高AAO膜的机械强度和化学稳定性。
6. 应用开发:制备得到的AAO膜可以进一步利用于各种应用领域。
例如,可以将其用作模板,制备纳米材料,如纳米线、纳米颗粒等;也可以用于电子器件中的隔离层、电容器和光学薄膜等。
总结来说,AAO工艺流程是一种制备多孔铝氧化膜的方法,通过阳极氧化和模板去除等步骤,可以得到具有孔径调控、高度有序和平整表面的AAO膜。
AAO膜具有广泛的应用前景,在纳米科技、电子、光学和生物医学等领域有着重要的应用价值。
- 1、下载文档前请自行甄别文档内容的完整性,平台不提供额外的编辑、内容补充、找答案等附加服务。
- 2、"仅部分预览"的文档,不可在线预览部分如存在完整性等问题,可反馈申请退款(可完整预览的文档不适用该条件!)。
- 3、如文档侵犯您的权益,请联系客服反馈,我们会尽快为您处理(人工客服工作时间:9:00-18:30)。
A2/O工艺
A2/O工艺的发展1932年开发的Wuhrmann工艺是最早的脱氮工艺(见图1),流程遵循硝化、反硝化的顺序而设置。
1962年,Ludzack和Ettinger首次提出利用进水中可生物降解的物质作为脱氮能源的前置反硝化工艺,解决了碳源不足的问题。
1973年,Barnard在开发Bardenpho工艺时提出改良型Ludzack-Ettinger脱氮工艺,即广泛应用的A/O工艺(见图2)。
A/O工艺中,回流液中的大量硝酸盐到缺氧池后,可以从原污水得到充足的有机物,使反硝化脱氮得以充分进行。
A/O工艺不能达到完全脱氮,因为好氧反应器总流量的一部分没有回流到缺氧反应器而是直接随出水排放了。
1980年,Rabinowitz和Marais对Phoredox工艺的研究中,选择3阶段的Phoredox工艺,即所谓的传统A2/O工艺(见图5)。
传统的A2O工艺工艺流程是:污水首先进入厌氧池,兼性厌氧菌将污水中的易降解有机物转化成VFAs(挥发性脂肪酸)。
回流污泥带入的聚磷菌将体内的聚磷分解,此为释磷,所释放的能量一部分可供好氧的聚磷菌在厌氧环境下维持生存,另一部分供聚磷菌主动吸收
VFAs(挥发性脂肪酸),并在体内储存PHB(聚羟基丁酸酯)。
进入缺氧区,反硝化细菌就利用混合液回流带入的硝酸盐及进水中的有机物进行反硝化脱氮,接着进入好氧区,聚磷菌除了吸收利用污水中残留的易降解BOD外,主要分解体内储存的PHB产生能量供自身声场繁殖,并主动吸收环境中的溶解磷,此为吸磷,以聚磷的形式在体内储存。
污水经厌氧,缺氧区,有机物分别被聚磷菌和反硝化细菌利用后浓度已很低,有利于自养的硝化菌的生长繁殖。
最后,混合液进入沉淀池,进行泥水分离,上清液作为处理水排放,沉淀污泥的一部风回流厌氧池,另一部分作为剩余污泥排放。
本工艺在系统上可以称为最简单的同步脱氮除磷工艺,总的水力停留时间少于其他同类工艺。
而且在厌氧-缺氧-好养交替运行条件下,不易发生污泥膨胀。
改良A2O的特点就是在厌氧池的前面加上了一个预缺氧池,以更好的达到脱氮除磷的效果,从而达到国家一级A的标准。
对于含磷较高的污水,该工艺是一个不错的选择。
影响A2O工艺出水效果的因素有很多,一般有以下一些方面的因素:
1. 污水中生物降解有机物对脱氮除磷的影响
可生物降解有机物对脱氮除磷有着十分重要的影响,它对A2/O工艺中的三种生化过程的影响是复杂的、相互制约甚至是相互矛盾的。
在厌氧池中,聚磷菌本身是好氧菌,其运动能力很弱,增殖缓慢,只能利用低分子的有机物,是竞争能力很差的软弱细菌。
但由于聚磷菌能在细胞内贮存PHB和聚磷酸基,当它处于不利的厌氧环境下,能将贮藏的聚磷酸盐中的磷通过水解而释放出来,并利用其产生的能量吸收低分子有机物而合成PHB,在利用有机物的
竞争中比其它好氧菌占优势,聚磷菌成为厌氧段的优势菌群。
因此,污水中可生物降解有机物对聚磷菌厌氧释磷起着关键性的作用。
在好氧段,当有机物浓度高时污泥负荷也较大,降解有机物的异养型好氧菌超过自养型好氧硝化菌,使氨氮硝化不完全,出水中NH+4-N浓度急剧上升,使氮的去除效率大大降低。
所以要严格控制进入好氧池污水中的有机物浓度,在满足好氧池对有机物需要的情况下,使进入好氧池的有机物浓度较低,以保证硝化细菌在好氧池中占优势生长,使硝化作用完全。
由此可见,在厌氧池,要有较高的有机物浓度;在缺氧池,应有充足的有机物;而在好氧池的有机物浓度应较小。
2. 污泥龄的影响
A2/O工艺污泥系统的污泥龄受二方面的影响。
首先是好氧池,因自养型硝化菌比异养型好氧菌的最小比增殖速度小得多,要使硝化菌存活并成为优势菌群,则污泥龄要长,经实践证明一般为20~30 d为宜。
但另一方面,A2/O工艺中磷的去除主要是通过排出含高磷的剩余污泥而实现的,如ts过长,则每天排出含高磷的剩余污泥量太少,达不到较高的除磷效率。
同时
过高的污泥龄会造成磷从污泥中重新释放,更降低了除磷效果。
所以要权衡上述二方面的影响,A2/O工艺的污泥龄一般宜为15~20 d。
3. DO的影响
在好氧段,DO升高,硝化速度增大,但当DO>2mg/L后其硝化速度增长趋势减缓,高浓度的DO会抑制硝化菌的硝化反应。
同时,好氧池过高的溶解氧会随污泥回流和混合液回流分别带至厌氧段和缺氧段,影响厌氧段聚磷菌的释放和缺氧段的NO-x-N的反硝化,对脱氮除磷均不利。
相反,好氧池的DO浓度太低也限制了硝化菌的生长率,其对DO的忍受极限为0.5~0.7 mg/L,否则将导致硝化菌从污泥系统中淘汰,严重影响脱氮效果。
所以根据实践经验,好氧池的DO为2 mg/L左右为宜,太高太低都不利。
在缺氧池,DO对反硝化脱氮有很大影响。
这是由于溶解氧与硝酸盐竞争电子供体,同时还抑制硝酸盐还原酶的合成和活性,影响反硝化脱氮。
为此,缺氧段DO<0.5 mg/L。
在厌氧池严格的厌氧环境下,聚磷菌才能从体内大量释放出磷而处于饥饿状态,为好氧
段大量吸磷创造了前提,从而才能有效地从污水中去除磷。
但由于回流污泥将溶解氧和NO-x 带入厌氧段,很难保持严格的厌氧状态,所以一般要求DO<0.2 mg/L,这对除磷影响不大。
4. 混合液回流比RN的影响
从好氧池流出的混合液,很大一部分要回流到缺氧段进行反硝化脱氮。
混合液回流比的大小直接影响反硝化脱氮效果,回流比RN大、脱氮率提高,但回流比RN太大时则混合液回流的动力消耗太大,造成运行费用大大提高。
5. 污泥回流比R
回流污泥是从二沉池底流回到厌氧池,靠回流污泥维持各段污泥浓度,使之进行生化反应。
如果污泥回流比R太小,则影响各段的生化反应速率,反之回流比R太高,A2/O工艺系统中硝化作用良好,反硝化效果不佳,导致回流污泥将大量NO-X-N带入厌氧池,引起反硝化菌和聚磷菌产生竞争,因聚磷菌为软弱菌群,所以反硝化速度大于磷的释放速度,反硝化菌抢先消耗掉快速生物降解的有机物进行反硝化,当反硝化脱氮完全后聚磷菌才开始进行磷的释放,这样虽有利于脱氮但不利于除磷。
据报道,厌氧段NO-X-N<2 mg/L,对生物除磷没有影响,当COD/TKN>10,则NO-X-N浓度对生物除磷也没有多大影响。
相反,如果A2/O工艺系统运行中反硝化脱氮良好,而硝化效果不佳,此时虽然回流污泥中硝态氮含量减少,对厌氧除磷有利,但因硝化不完全造成脱氮效果不佳。
权衡上述污泥回流比的大小对A2/O工艺的影响,一般采用污泥回流比R=(60~100)%为宜,最低也应在40%以上。
6. TKN/MLSS负荷率的影响
好氧段的硝化反应,过高的NH+4-N浓度对硝化菌会产生抑制作用,实验表明TKN/MLSS负荷率应<0.05 kgTKN/kgMLSS•d,否则会影响氨氮的硝化。
7. 水力停留时间HRT的影响
根据实验和运行经验表明,A2/O工艺总的水力停留时间HRT一般为6~8 h,而三段HRT的比例为厌氧段∶缺氧段∶好氧段=1∶1∶(3~4)。
8. 温度的影响
好氧段,硝化反应在5~35℃时,其反应速率随温度升高而加快,适宜的温度范围为
30~35℃。
当低于5℃时,硝化菌的生命活动几乎停止。
有人提出硝化细菌比增长速率μ与温度的关系为:μ=μ0θ(t-20),式中μ0为20℃时最大比增长速率,θ温度系数,对亚硝酸菌θ为1.12、对硝酸菌为1.07。
缺氧段的反硝化反应可在5~27℃进行,反硝化速率随温度升高而加快,适宜的温度范围为15~25℃。
厌氧段,温度对厌氧释磷的影响不太明显,在5~30℃除磷效果均很好。
9. pH值的影响
在厌氧段,聚磷菌厌氧释磷的适宜pH值是6~8;在缺氧反硝化段,对反硝化菌脱氮适宜的pH值为6.5~7.5;在好氧硝化段,对硝化菌适宜的pH值为7.5~8.5。