中频炉熔炼碳钢的一种脱碳方法[1]
中频炉炼钢操作规程
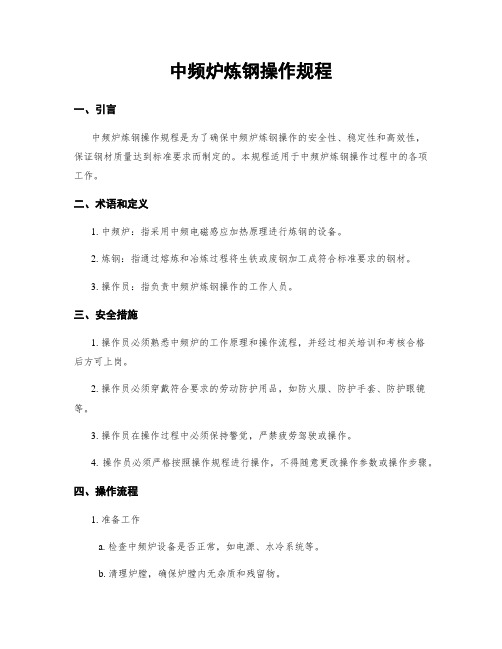
中频炉炼钢操作规程一、引言中频炉炼钢操作规程是为了确保中频炉炼钢操作的安全性、稳定性和高效性,保证钢材质量达到标准要求而制定的。
本规程适用于中频炉炼钢操作过程中的各项工作。
二、术语和定义1. 中频炉:指采用中频电磁感应加热原理进行炼钢的设备。
2. 炼钢:指通过熔炼和冶炼过程将生铁或废钢加工成符合标准要求的钢材。
3. 操作员:指负责中频炉炼钢操作的工作人员。
三、安全措施1. 操作员必须熟悉中频炉的工作原理和操作流程,并经过相关培训和考核合格后方可上岗。
2. 操作员必须穿戴符合要求的劳动防护用品,如防火服、防护手套、防护眼镜等。
3. 操作员在操作过程中必须保持警觉,严禁疲劳驾驶或操作。
4. 操作员必须严格按照操作规程进行操作,不得随意更改操作参数或操作步骤。
四、操作流程1. 准备工作a. 检查中频炉设备是否正常,如电源、水冷系统等。
b. 清理炉膛,确保炉膛内无杂质和残留物。
c. 准备好所需的原料和辅助材料。
2. 开炉操作a. 打开中频炉电源,确保电源稳定。
b. 打开水冷系统,保证冷却效果。
c. 将原料和辅助材料按照配比要求投入炉膛。
d. 启动中频炉加热系统,根据工艺要求设定加热温度和时间。
3. 炉内操作a. 监测炉内温度和压力,确保在安全范围内。
b. 根据工艺要求进行炉内搅拌和冶炼操作。
c. 定期取样检测炉内钢液成分,并调整冶炼参数。
4. 炉后操作a. 冶炼结束后,关闭加热系统和电源。
b. 清理炉膛,清除残留物和杂质。
c. 检查设备是否正常,如有异常及时报修。
d. 做好相关记录和报表。
五、质量控制1. 操作员必须严格按照工艺要求进行操作,确保钢材质量符合标准要求。
2. 定期进行钢液成分分析,确保冶炼参数的准确性和稳定性。
3. 对不合格的钢材及时进行处理,防止流入下道工序。
六、应急措施1. 操作员必须熟悉中频炉的应急停机程序,确保在紧急情况下能够迅速停机。
2. 发生事故或异常情况时,操作员应立即向上级报告,并采取相应的应急措施。
中频炉炼钢工艺流程
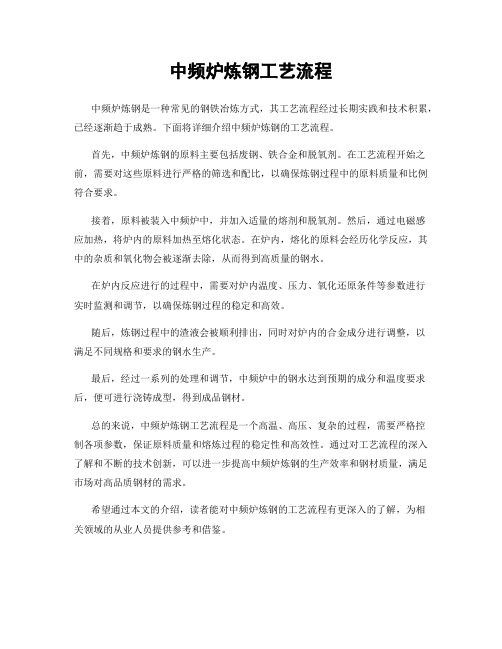
中频炉炼钢工艺流程
中频炉炼钢是一种常见的钢铁冶炼方式,其工艺流程经过长期实践和技术积累,已经逐渐趋于成熟。
下面将详细介绍中频炉炼钢的工艺流程。
首先,中频炉炼钢的原料主要包括废钢、铁合金和脱氧剂。
在工艺流程开始之前,需要对这些原料进行严格的筛选和配比,以确保炼钢过程中的原料质量和比例符合要求。
接着,原料被装入中频炉中,并加入适量的熔剂和脱氧剂。
然后,通过电磁感
应加热,将炉内的原料加热至熔化状态。
在炉内,熔化的原料会经历化学反应,其中的杂质和氧化物会被逐渐去除,从而得到高质量的钢水。
在炉内反应进行的过程中,需要对炉内温度、压力、氧化还原条件等参数进行
实时监测和调节,以确保炼钢过程的稳定和高效。
随后,炼钢过程中的渣液会被顺利排出,同时对炉内的合金成分进行调整,以
满足不同规格和要求的钢水生产。
最后,经过一系列的处理和调节,中频炉中的钢水达到预期的成分和温度要求后,便可进行浇铸成型,得到成品钢材。
总的来说,中频炉炼钢工艺流程是一个高温、高压、复杂的过程,需要严格控
制各项参数,保证原料质量和熔炼过程的稳定性和高效性。
通过对工艺流程的深入了解和不断的技术创新,可以进一步提高中频炉炼钢的生产效率和钢材质量,满足市场对高品质钢材的需求。
希望通过本文的介绍,读者能对中频炉炼钢的工艺流程有更深入的了解,为相
关领域的从业人员提供参考和借鉴。
中频感应电炉熔炼操作规程
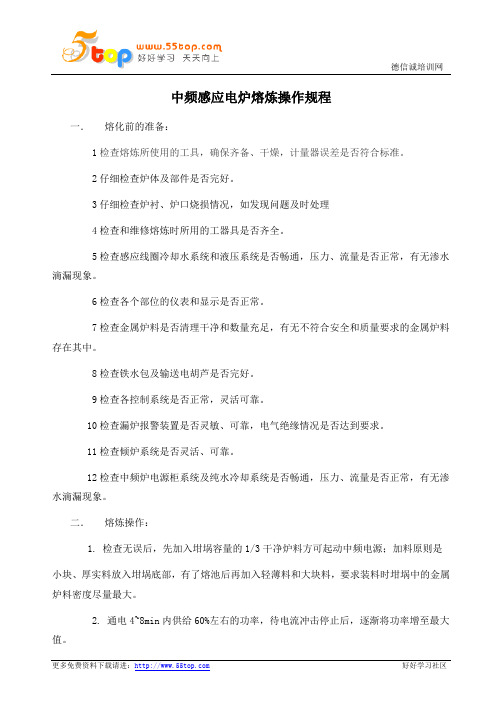
中频感应电炉熔炼操作规程一.熔化前的准备:1检查熔炼所使用的工具,确保齐备、干燥,计量器误差是否符合标准。
2仔细检查炉体及部件是否完好。
3仔细检查炉衬、炉口烧损情况,如发现问题及时处理4检查和维修熔炼时所用的工器具是否齐全。
5检查感应线圈冷却水系统和液压系统是否畅通,压力、流量是否正常,有无渗水滴漏现象。
6检查各个部位的仪表和显示是否正常。
7检查金属炉料是否清理干净和数量充足,有无不符合安全和质量要求的金属炉料存在其中。
8检查铁水包及输送电胡芦是否完好。
9检查各控制系统是否正常,灵活可靠。
10检查漏炉报警装置是否灵敏、可靠,电气绝缘情况是否达到要求。
11检查倾炉系统是否灵活、可靠。
12检查中频炉电源柜系统及纯水冷却系统是否畅通,压力、流量是否正常,有无渗水滴漏现象。
二.熔炼操作:1.检查无误后,先加入坩埚容量的1/3干净炉料方可起动中频电源;加料原则是小块、厚实料放入坩埚底部,有了熔池后再加入轻薄料和大块料,要求装料时坩埚中的金属炉料密度尽量最大。
2. 通电4~8min内供给60%左右的功率,待电流冲击停止后,逐渐将功率增至最大值。
3. 熔炼过程中要经常检查炉衬的烧损情况、中频电源柜上各种仪表、冷却水循环状况;炉膛里不准有炉料架空棚料现象,如有此现象,随时注意捣料,防止“搭桥”。
4. 95%的炉料熔毕时,取钢样进行成分分析,并将其余5%的炉料加入炉内继续熔化。
5.全部炉料溶毕后,降低功率至40%~60%,倾炉扒渣;为防止铁水溢出,铁水液面与炉沿保持50mm的距离。
6. 往铁水液面上加脱氧剂(质量比为:石灰粉:铝粉=2:1)进行扩散脱氧;脱氧过程中可用石灰粉和氟石粉调整炉渣的粘度,使炉渣具有良好的流动性。
7.根据化学分析结果,调整钢液化学成分,其中含硅量应在出钢前10min以内进行调整。
8. 测温,做圆杯试样:测量钢液温度,并作圆杯试样,检查钢液脱氧情况。
9. 钢液温度达到1630~1650°C(高锰钢1520~1560℃),圆杯试样收缩良好时,扒除一半炉渣后,加硅锰各0.15%,镇静一分钟,每吨钢液插铝0.15-0.25%终脱氧,插铝后2~3min以内停电倾炉出钢。
中频炉炼钢操作规程
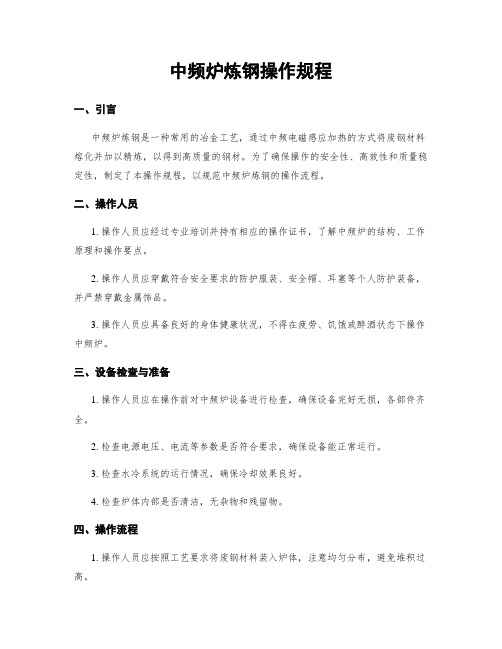
中频炉炼钢操作规程一、引言中频炉炼钢是一种常用的冶金工艺,通过中频电磁感应加热的方式将废钢材料熔化并加以精炼,以得到高质量的钢材。
为了确保操作的安全性、高效性和质量稳定性,制定了本操作规程,以规范中频炉炼钢的操作流程。
二、操作人员1. 操作人员应经过专业培训并持有相应的操作证书,了解中频炉的结构、工作原理和操作要点。
2. 操作人员应穿戴符合安全要求的防护服装、安全帽、耳塞等个人防护装备,并严禁穿戴金属饰品。
3. 操作人员应具备良好的身体健康状况,不得在疲劳、饥饿或醉酒状态下操作中频炉。
三、设备检查与准备1. 操作人员应在操作前对中频炉设备进行检查,确保设备完好无损,各部件齐全。
2. 检查电源电压、电流等参数是否符合要求,确保设备能正常运行。
3. 检查水冷系统的运行情况,确保冷却效果良好。
4. 检查炉体内部是否清洁,无杂物和残留物。
四、操作流程1. 操作人员应按照工艺要求将废钢材料装入炉体,注意均匀分布,避免堆积过高。
2. 打开中频炉的电源开关,设定合适的电流和频率,启动加热过程。
3. 监控炉温的升高情况,确保温度的控制在设定范围内。
4. 当废钢材料完全熔化后,加入适量的合金材料进行精炼,提高钢材的质量。
5. 根据需要,进行合适的调温和保温操作,以保证钢材的质量和成品率。
6. 当炉内钢水达到要求后,关闭电源开关,停止加热过程。
7. 使用合适的工具将炉内的钢水倒出,注意避免烫伤和溅射。
8. 清理炉体内部的残留物和杂质,确保下一次操作的顺利进行。
五、安全注意事项1. 操作人员应严格遵守相关的安全操作规程,不得擅自更改工艺参数。
2. 在操作过程中,严禁将手部或其他物体伸入炉体内部,以免发生意外伤害。
3. 操作人员应保持操作区域的整洁,避免杂物堆积和滑倒等危险情况的发生。
4. 在操作过程中,如发生异常情况或设备故障,应立即停止操作并报告相关负责人。
5. 遵守消防安全规定,确保操作区域的消防设施完好并易于使用。
中频电炉冶炼过程中脱磷、脱硫操作要点

中频电炉冶炼过程中脱磷、脱硫操作要点(总4页)本页仅作为文档封面,使用时可以删除This document is for reference only-rar21year.March一.前言内容导读:中频电炉在铸钢行业中的应用已经极为普遍,特别是在小型砂型铸钢和失蜡熔模精密铸钢中几乎都是采用中频电炉炼钢,由于技术力量的不足,绝大多数企业对中频电炉在熔炼过程中的冶金反应研究较少,以至于形成了一种较为普遍的观点,即中频电炉在钢熔炼过程中只有较弱的冶金反应,难以进行脱磷、脱硫操作,基本上是一种废钢和铁合金的重熔过程。
现实生产当中,很多使用中频电炉冶炼铸钢材质的企业,在遇到原材料出现波动时,造成钢液成份中磷或硫超标,解决问题的方法基本上是倾倒出部分钢液,再加低磷硫的废钢重新配料熔化,常常造成较大的损失,因此,强化中频电炉熔炼过程中的冶金反应,掌握脱磷、脱硫的方法,是一项很有价值的工作。
二.钢水熔炼过程中脱P、脱S的冶金原理(一)脱P的冶金反应原理磷在钢液中以Fe2P的形式存在,在钢液中溶解度很高,容易与自炉渣扩散到钢液中的(FeO)作用并释放热量,反应式:2[P]+5(FeO)→(P2O5)+5[Fe];△H=-260000J磷的氧化物在钢液中溶解度很低,但易溶于炉渣,并与炉渣中的(FeO)反应生成(3FeOP2O5),反应式如下:(P2O5)+3(FeO)→(3FeOP2O5);△H=-127900J(P2O5)和(3FeOP2O5),都是不稳定的氧化物,在冶炼时,温度稍高就会分解,使磷重回钢液,因此,以FeO为主的炉渣脱磷能力很差,为了取得很好的脱P效果,就必须向炉渣中加入强碱性氧化物CaO(石灰),与(P2O5)结合成稳定的磷酸钙,反应式如下:(P2O5)+4(CaO)→[(CaO)4 P2O5];△H=-689700J脱P过程综合反应式如下:2[P]+ 5(FeO)+ 4(CaO)→[(CaO)4 P2O5]+ 5[Fe];△H=-949700J由以上反应式可知,做好脱P工作,注意以下几个方面:(1)钢液氧化性强,炉渣碱度高是脱P的必要条件;(2)控制钢液温度,由于脱磷是放热反应,因此钢液温度低有利于脱P;(3)流动性良好的炉渣能提高渣中的CaO活性,有利于脱P;(4)加强钢液与渣的搅拌,有利于脱P。
中频炉冶炼工艺的要点

中频炉冶炼工艺的要点中频炉冶炼工艺的要点,2)装料1. 炉料的块度及布料原则与冶炼碳钢相同2. 随同炉料装入的合金(镍、铜及其它),应避开电弧区,以减少烧损3. 炉料应装得紧密,以利于导电和导热4. 装入金属料前,先往炉底和炉坡上加入(1-2)%的石灰,以保护炉底,并在熔化期中造渣脱磷 (3)冶炼工艺要点一般低合金钢的冶炼工艺与碳钢基本相同,有关的工艺要求见表9-101表9-101 冶炼低合金钢的工艺要求项目要求备注氧化脱碳量(%) 指炉料较好的条件上,炉料条件较差时应适当增加脱碳量0.30-0.45氧化终点碳(%) 比规格含碳量的下限低0.02-0.04 指在还原期中加入的是低碳铁合金的情况,如用高碳铁合金时,终点碳应再适当降低还原渣各类 C?0.35%的合金钢规定用白渣,要求(feo)采用电石渣或弱电石渣时,在还原末期加硅铁调整成分前5min,必须将电石渣变为白渣 ?0.08%C>0.35%的合金钢可以用电石渣,要求(feo)?0.5%终脱氧插铝量(kg/t钢) 因某些合金元素(特别是钒、钛、硼)本身有脱氧作用,故终脱0.6-0.6氧插铝量比碳钢略低(4)出炉温度表9-102中列出了某些低合金钢的适宜出炉温度,可供参考。
应指出:表中所列出炉温度适用于钢液量为3-5t,钢液出炉以后在钢包中镇静5-10min后,用于浇注中、小铸件的生产条件。
如钢液量以及浇注铸件情况不同时,应适当调节出炉温度。
表9-102 你合金的出炉温度钢号出炉温度(?)ZG16MN 1620-1640ZG20CRMO .1610-1630ZG20MNNO 1600-1620ZG20MNSI 1600-1620ZG35CRMO 1600-1620ZG35MNSI 1590-1610ZG40CR 1590-1610ZG5CRMNMO 1580-1600。
炼钢脱碳工艺流程

炼钢脱碳工艺流程
《炼钢脱碳工艺流程》
炼钢脱碳是炼钢过程中的关键步骤之一,它主要是通过对钢水进行煅烧处理,使钢中的碳含量达到标准要求。
脱碳工艺流程通常包括炉前准备、煅烧浓缩、煅烧保温和煅烧冷却四个阶段。
首先是炉前准备,包括预热炉子、检查炉子装备、准备煅烧过程中需要用到的燃料和辅助材料等。
接着是煅烧浓缩阶段,这个阶段是将钢水置于高温环境中,使得钢水中的气体和杂质排出,从而提高钢水的浓度。
煅烧浓缩的过程中需要控制加热速度和保持温度,以确保钢水中的碳含量得到有效的降低。
接下来是煅烧保温阶段,这个阶段是为了保持钢水的均匀性和稳定性。
在保温过程中,需要根据不同的钢种和碳含量要求来确定保温时间和温度。
最后是煅烧冷却阶段,这个阶段是通过控制冷却速度来降低钢水的温度,使其达到适合下一步工艺处理的温度。
在整个脱碳工艺流程中,需要严格控制各个阶段的温度、气氛和时间,以确保脱碳效果达到要求。
同时还需要监测钢水中的碳含量,根据实时数据来调整工艺参数,以保证最终产品的质量。
总的来说,炼钢脱碳工艺流程是一个复杂而精细的过程,它直接影响着钢材的质量和性能。
只有严格按照标准工艺操作,才能保证脱碳效果达到标准要求,生产出高质量的钢材。
中频炉炼钢操作规程

中频炉炼钢操作规程一、操作目的中频炉炼钢操作规程的目的是确保中频炉炼钢过程的安全、高效和稳定,保证钢材的质量和生产效益。
二、操作范围本操作规程适用于中频炉炼钢操作过程中的各项工作。
三、操作要求1. 设备准备a. 检查中频炉设备是否正常运行,包括电源、水冷系统、感应线圈等。
b. 检查冶炼料、脱氧剂、合金等原料的质量和数量。
2. 炉前准备a. 根据生产计划确定炉次,准备好炼钢所需的原料和辅助设备。
b. 清理炉底和炉墙,确保炉内无杂质和残留物。
3. 炉料装入a. 按照配料比例将冶炼料、脱氧剂和合金等原料装入中频炉。
b. 确保装入的炉料均匀分布,避免出现堆积和堵塞现象。
4. 启动操作a. 按照操作程序启动中频炉,确保电源和水冷系统正常运行。
b. 设置炉温和保温时间,根据炉料的性质和生产要求进行调整。
5. 炉内操作a. 观察炉内温度和炉料的熔化情况,根据需要调整加热功率。
b. 定期检查炉内温度计和压力计的准确性,确保数据的可靠性。
c. 定时采集炉内的样品,进行化验分析,控制炉内成分的稳定性。
6. 出钢操作a. 根据炉内温度和炉料的状态,判断炉料是否已经熔化完成。
b. 打开出钢口,将炼钢渣和钢水顺利排出,确保操作安全和钢水质量。
c. 检查出钢口的密封性和炉底的状况,及时修复和更换损坏部件。
7. 炉后操作a. 关闭中频炉,断开电源和水冷系统,进行设备的清洁和维护。
b. 清理炉内残留物和炉底的渣渣,确保下次操作的顺利进行。
四、操作安全1. 操作人员必须熟悉中频炉的结构和工作原理,严格按照操作规程进行操作。
2. 操作过程中必须佩戴个人防护装备,包括防火服、耐热手套、护目镜等。
3. 炉内温度和压力超过安全范围时,必须立即停止操作,并及时报告相关人员。
4. 炉料装入和出钢过程中,必须确保操作平稳、顺利,避免发生事故和质量问题。
5. 炉后操作时,必须断开电源和水冷系统,避免发生电击和烫伤等意外事故。
五、操作记录1. 每次操作前必须填写中频炉炼钢操作记录表,包括操作人员、操作时间、炉次号等信息。
炼钢脱碳方法

炼钢脱碳方法
1. 物理吸收法。
这种方法最早采用加压水脱除二氧化碳,通过减压将水再生。
这种方法设备简单,但脱碳效率较低,出口二氧化碳一般在2%(体积)以下,且动力消耗较高。
后来发展了甲醇洗涤法、碳酸丙烯酯法、聚乙二醇二甲醚法等,这些方法具有净化度高、能耗低、回收二氧化碳纯度高等优点,还可以选择性脱除硫化氢。
2. 化学吸收法。
这种方法吸收效果好、再生容易,同时还能脱除硫化氢等杂质。
主要方法包括乙醇胺法和催化热钾碱法。
在碳酸钾溶液中添加某些无机或有机物作活化剂,并加入缓蚀剂以降低溶液对设备的腐蚀。
3. 物理脱碳。
搅拌式脱碳是通过机械搅拌来促进脱碳反应进行,这种方法不会改变炉温和炉气成分,对钢质、合金的适应性较好,但成本较高。
氧吹脱碳是通过注氧来增加炉内氧分压,使钢中的碳转化为CO和CO2排除掉,适用于低硫、低磷钢水的脱碳,但操作需谨慎以避免爆炸事故。
4. .化学脱碳。
碱性脱碳利用碱性介质(如石灰、白云石等)与钢水中的碳反应,生成气体CO和CO2来脱除碳,操作简便,成本较低,但对高含硫、高含磷的钢水效果不佳。
气化脱碳是指在一定温度下,通过加入还原剂(如焦炭、氢气等)反应,将钢水中的碳还原为气体CO 和CH4排除,适用于各种钢种,但对生产工艺要求较高。
5.其他方法。
铵化脱碳、微生物脱碳等,这些方法都处于研究和试验阶段,适用于特殊场景和需求。
此外,电孤炉炼钢的脱碳方法包括加入适量的氧化铝和高碳铬铁,控制气氧比例等。
中频炉熔炼碳钢的一种脱碳方法

中频炉熔炼碳钢的一种脱碳方法30~35.2.半烧结屡是烧结层和未烧结屠的过渡区,部分颗粒开始熔台,烧结阿络不完全.作用是缓冲烧结层之应力,阻止烧结层内产生裂纹向外延伸.半烧结层厚度约占坩埚厚35~40.未烧结层与感应线圈之问有一层完全没有烧结的原始}少料,起绝热和对坩埚在加热和冷却时体积膨胀收缩时起缓冲作用.3.烧结方法我们采用烧结温度等于钢液温度的低温烧结法..4.坩埚烧结过程的物理化学反应(1)镁砂由低温到高温的各种物理化学反应温度低于850~C以下时,主要是炉衬材料脱水,温度大于850~C时,碳酸盐开始分解:MgCOa—MgO+CO2}CaCO3一CaO+CO2t温度在850℃~1500~C之间,低熔点化合物开始熔化烧结,网络开始出现,坩埚体积收缩,化台物有MgO?FeaO2,CaO?MgO?SiOl,2CaO?Fe2O3,3Ca:O?MgO?2SiOl,3CaO?A1=O3,4CaO?MgO?Fe203等.这时坩埚体积变化趋于稳定,可适当增大升温速度.温度在1500~17O0℃对,使镁砂中镁橄榄石(2MgSiO2),硅酸盐(2CaOSiO2),镁铝尖晶石(MgOA1.Os)开始熔化形成新的化合物.(2)送电烘炉工艺用术柴燃烧烘炉2~3小时.然后送电,功率分配:30千瓦2小时}40千瓦2小时}60千瓦2小时;80千瓦2小时J100千瓦2小时.这时开始装料,缓慢增加功率到150千瓦,然后增加~jlso千瓦保持3小时.最后加大功率达240千瓦.在烘炉过程中保持20~0/时升温速度,目的使炉衬材料能排除水分.烧结完成后,要连续熔炼2~3炉低碳锕增加炉衬烧结层厚度. 五,结论1.采用旧镁砂做妒衬材科,炉龄达50~80炉次.如加强维护能提高到100余炉次. 2.采用旧镁砂做炉衬材料,材料来源广,价格低,每炉镁砂费用仅100~150元.3.采用干打法打结碱性感应电炉妒衬,提高了炉衬寿命,炉衬材料中加入氧化铝提高了炉衬高温结构强度.(鳊辑:王惠愚)中频炉熔炼碳钢的一种脱碳方法杭州化工机械厂张同义宁波石油阀门厂黄志兴一,问题的提出过去用中颠熔炉炼ZG25钢时,经投料计算熔炼后的锕水,碳含量一般都在要求范围内,偶尔发生碳含量超标时,为了降碳,将钢水倒掉一部分,然后加低碳废锕重熔(表1). 寰15oovg,:l,频妒加废铜降碟数量置熔对要求的锕水l撼精时('()I'k)<mla)古破量l碘古量(%)l')).22~0.a20.500.20~0.25I2oo2406O.).22~0."0.450.I~0.20:I50~lBD20045).22~O.3210.40-0.1OgO.151100~130}16.35 近年来,废钢来源较杂,混料严重.熔炼前虽经投料计算,熔清后,碳含量超标现象时有发生,过去疆用韵倒钢水降碳法,即费时又费料,经过几年的试验,我们找到了一种用气割渣作脱碳剂熔炼zG25锕的方法.众所周知,吹氧或加矿翁脱碳,都是形成FeO,FeO在高温下使碳氧化,生成CO: [C]+(FeO)一{CO)十+[Fe]CO气泡上浮使钢液沸腾,从而使钢水脱碳和净化.当用Z炔一氧气火焰切割破钢时,会生成铸造》1990?8●●●钬的氧化物,称之气割渣坷割ZG25时,气割渣中以FeO为主,有少量SiOz,MnO等.因此,用中频炉炼钢时,用渣作脱碳剂,如同吹氧脱碳一样,也能达到脱碳前目的. 二,用气害l渣脱碳的试验自1987年3月开始,我厂采用气割渣脱碳,经过一段时间试验,取得了一些经验数据,到1988年初已用于生产,效果较好.L加气割渣脱碳的操作(1)首先根据所备炉料的成分,初步计算投炉料置,.注意控制钢水量低于炉领圈,防止沸腾时锕水镒出.(2)待炉料溶请后,炉前取样分析成分,视超碳量,以每公斤气割渣能脱去O.O3~o.05的碳计,考虑加气割渣的量.(3)等炉内钢液温度达1550=C以上后,把气割渣分批(每批不得超过2公斤)加入,同时搅拌,以免发生突然剧烈沸腾.(4)气割渣加完后,再加入适量低碳废钢,锰铁,硅铁和溶剂'碎玻璃待所有投炉辩溶清后,扒渣取样分析.(5)铁水成分合格后,再加些碎玻璃覆盖钢水,使钢水温度选到浇注要求后出钢.2.气翱渣脱碳经验数据我们的试验和生产实践表明,每公斤气割渣的脱碳量在0.03~0.05%之间,最大脱碳量可达0.25.加气割渣对,钢水温度在1550E以上为宜.脱碳速度为每分钟0.O05~0.0057t几个典型炉次的有关数据如表2所示.襄250Okg中频妒中加气■渣脱磺的有关救拇寻器1脱碳时n炉发冒'专誉()2200.22~o.s2l0.^710,30l4I40286一10I4sI501550l255i20.22~0.32I.?.'I'l.8S80.22~0.3210.00?210001B5016O三,加气割渣脱碳的优点1.省时一过去超碳时,采用倒掉部分钢水,再加低碳废钢调整的办法,若超0.o5%g~,须倒掉钢术_l1OOkg,补加废钢1酾嘻,再熔化需3O~40min.若用气割渣脱碳,只需加2kg气割渣再搅拌几下,仅用10mln即可.2.省力用倒钢水加废钢法,操作麻烦费力,而用加气割渣法只需加少量的渣料,简便省力.3.省电加气割渣法比倒钢水法加废钢法省时,加上不用倒掉钢水,二项相加按节省1小时用电计算,250kW的中额炉每小时耗电250kwh,可节省电费40元(计划内用电)或1l7元(计划外甩电).1.可降低原料成本过去为了防止超碳,常采用优质废钢(FG3,FG4)400元/吨,一旦混入杂废钢,钢水含碳量出格,倒钢水后,要补加废钢150~2~Okg而用气割渣脱碳,只需补加废钢50蜒; 左右,以选电炉最佳容量.由于少加了废钢,成本必然下降.又因为加气割渣法可以使用普通废钢(FG5,FOB)3oo~/吨,钢水成本又可进一步降低.综上几项,每熔炼一吨zG25钢,大约可降低成本250~300元.四加气割渣脱碳的局限性根据我们的试验和生产实践,用气割渣脱碳的方法仍限:pZG25,~般适于碳出格0.25% 以下,若钢水超碳量大于此限,则经济效益下降(表2中858炉次).该法是否适合其它牌号的钢种,有待尝试.'鳊辑t田世汪)铸进》1990?8。
中频炉熔炼不锈钢的脱氧
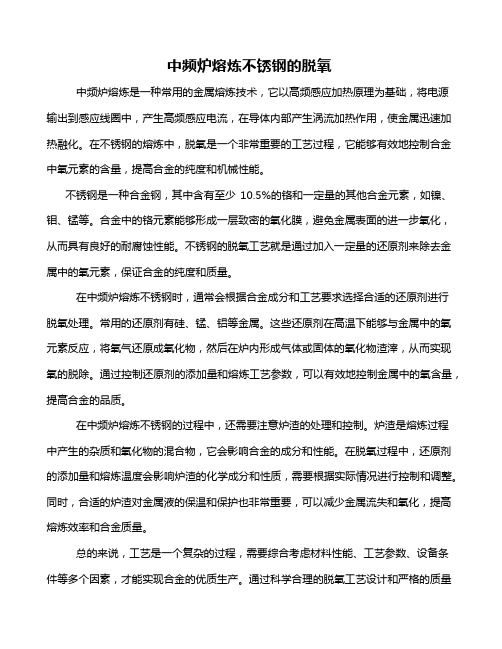
中频炉熔炼不锈钢的脱氧中频炉熔炼是一种常用的金属熔炼技术,它以高频感应加热原理为基础,将电源输出到感应线圈中,产生高频感应电流,在导体内部产生涡流加热作用,使金属迅速加热融化。
在不锈钢的熔炼中,脱氧是一个非常重要的工艺过程,它能够有效地控制合金中氧元素的含量,提高合金的纯度和机械性能。
不锈钢是一种合金钢,其中含有至少10.5%的铬和一定量的其他合金元素,如镍、钼、锰等。
合金中的铬元素能够形成一层致密的氧化膜,避免金属表面的进一步氧化,从而具有良好的耐腐蚀性能。
不锈钢的脱氧工艺就是通过加入一定量的还原剂来除去金属中的氧元素,保证合金的纯度和质量。
在中频炉熔炼不锈钢时,通常会根据合金成分和工艺要求选择合适的还原剂进行脱氧处理。
常用的还原剂有硅、锰、铝等金属。
这些还原剂在高温下能够与金属中的氧元素反应,将氧气还原成氧化物,然后在炉内形成气体或固体的氧化物渣滓,从而实现氧的脱除。
通过控制还原剂的添加量和熔炼工艺参数,可以有效地控制金属中的氧含量,提高合金的品质。
在中频炉熔炼不锈钢的过程中,还需要注意炉渣的处理和控制。
炉渣是熔炼过程中产生的杂质和氧化物的混合物,它会影响合金的成分和性能。
在脱氧过程中,还原剂的添加量和熔炼温度会影响炉渣的化学成分和性质,需要根据实际情况进行控制和调整。
同时,合适的炉渣对金属液的保温和保护也非常重要,可以减少金属流失和氧化,提高熔炼效率和合金质量。
总的来说,工艺是一个复杂的过程,需要综合考虑材料性能、工艺参数、设备条件等多个因素,才能实现合金的优质生产。
通过科学合理的脱氧工艺设计和严格的质量控制,可以提高不锈钢合金的品质和性能,满足不同工业领域的应用需求。
中频炉熔炼技术在不锈钢行业的应用前景广阔,有着较大的发展空间。
轴承钢屑在中频炉中的熔炼脱碳
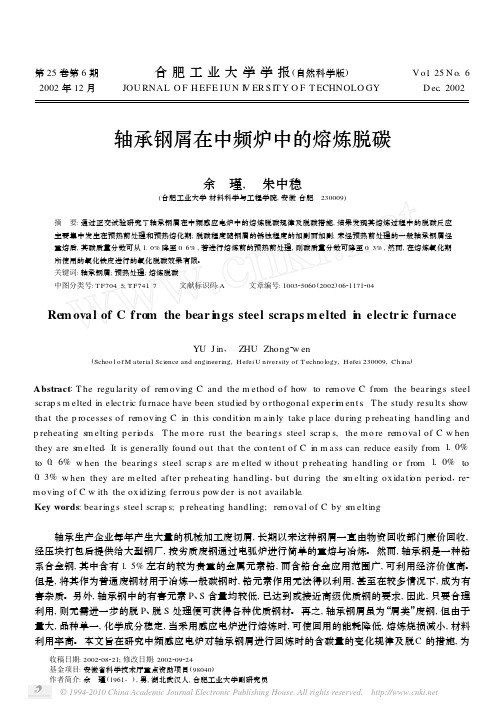
收稿日期:2002208221;修改日期:2002209224基金项目:安徽省科学技术厅重点资助项目(98040)作者简介:余 瑾(1961-),男,湖北武汉人,合肥工业大学副研究员.第25卷第6期合肥工业大学学报(自然科学版)V o l .25N o .62002年12月JOU RNAL O F H EFE I UN I V ER S IT Y O F T ECHNOLO GYD ec .2002轴承钢屑在中频炉中的熔炼脱碳余 瑾, 朱中稳(合肥工业大学材料科学与工程学院,安徽合肥 230009)摘 要:通过正交试验研究了轴承钢屑在中频感应电炉中的熔炼脱碳规律及脱碳措施,结果发现其熔炼过程中的脱碳反应主要集中发生在预热前处理和预热熔化期;脱碳程度随钢屑的锈蚀程度的加剧而加剧;未经预热前处理的一般轴承钢屑经重熔后,其碳质量分数可从1.0%降至0.6%,若进行熔炼前的预热前处理,则碳质量分数可降至0.3%,然而,在熔炼氧化期所使用的氧化铁皮进行的氧化脱碳效果有限。
关键词:轴承钢屑;预热处理;熔炼脱碳中图分类号:T F 704.5;T F 741.7 文献标识码:A 文章编号:100325060(2002)0621171204Rem ova l of C from the bear i ngs steel scraps m elted i n electr ic furnaceYU J in , ZHU Zhong 2w en(Schoo l of M aterial Science and engineering ,H efei U niversity of T echno logy ,H efei 230009,Ch ina )Abstract :T he regu larity of rem oving C and the m ethod of how to rem ove C from the bearings steel scrap s m elted in electric fu rnace have been studied by o rthogonal experi m en ts .T he study resu lts show that the p rocesses of rem oving C in th is conditi on m ain ly take p lace du ring p reheating handling and p reheating s m elting peri ods .T he m o re ru st the bearings steel scrap s ,the m o re rem oval of C w hen they are s m elted .It is generally found ou t that the con ten t of C in m ass can reduce easily from 1.0%to 0.6%w hen the bearings steel scrap s are m elted w ithou t p reheating handling o r from 1.0%to 0.3%w hen they are m elted after p reheating handling ,bu t du ring the s m elting ox idati on peri od ,re 2m oving of C w ith the ox idizing ferrou s pow der is no t availab le .Key words :bearings steel scrap s ;p reheating handling ;rem oval of C by s m elting轴承生产企业每年产生大量的机械加工废切屑,长期以来这种钢屑一直由物资回收部门廉价回收,经压块打包后提供给大型钢厂,按劣质废钢通过电弧炉进行简单的重熔与冶炼。
中频炉熔炼铸造碳钢操作指导书
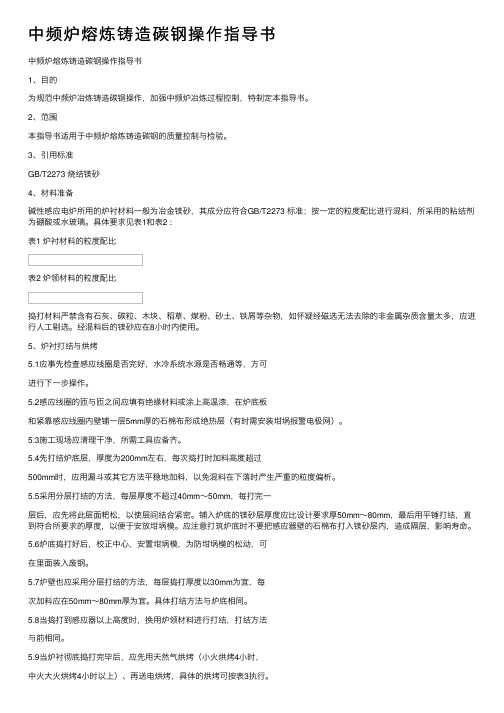
中频炉熔炼铸造碳钢操作指导书中频炉熔炼铸造碳钢操作指导书1、⽬的为规范中频炉冶炼铸造碳钢操作,加强中频炉冶炼过程控制,特制定本指导书。
2、范围本指导书适⽤于中频炉熔炼铸造碳钢的质量控制与检验。
3、引⽤标准GB/T2273 烧结镁砂4、材料准备碱性感应电炉所⽤的炉衬材料⼀般为冶⾦镁砂,其成分应符合GB/T2273 标准;按⼀定的粒度配⽐进⾏混料,所采⽤的粘结剂为硼酸或⽔玻璃。
具体要求见表1和表2 :表1 炉衬材料的粒度配⽐表2 炉领材料的粒度配⽐捣打材料严禁含有⽯灰、碳粒、⽊块、稻草、煤粉、砂⼟、铁屑等杂物,如怀疑经磁选⽆法去除的⾮⾦属杂质含量太多,应进⾏⼈⼯剔选。
经混料后的镁砂应在8⼩时内使⽤。
5、炉衬打结与烘烤5.1应事先检查感应线圈是否完好,⽔冷系统⽔源是否畅通等,⽅可进⾏下⼀步操作。
5.2感应线圈的匝与匝之间应填有绝缘材料或涂上⾼温漆,在炉底板和紧靠感应线圈内壁铺⼀层5mm厚的⽯棉布形成绝热层(有时需安装坩埚报警电极⽹)。
5.3施⼯现场应清理⼲净,所需⼯具应备齐。
5.4先打结炉底层,厚度为200mm左右,每次捣打时加料⾼度超过500mm时,应⽤漏⽃或其它⽅法平稳地加料,以免混料在下落时产⽣严重的粒度偏析。
5.5采⽤分层打结的⽅法,每层厚度不超过40mm~50mm,每打完⼀层后,应先将此层⾯耙松,以使层间结合紧密。
铺⼊炉底的镁砂层厚度应⽐设计要求厚50mm~80mm,最后⽤平锤打结,直到符合所要求的厚度,以便于安放坩埚模。
应注意打筑炉底时不要把感应器壁的⽯棉布打⼊镁砂层内,造成隔层,影响寿命。
5.6炉底捣打好后,校正中⼼,安置坩埚模,为防坩埚模的松动,可在⾥⾯装⼊废钢。
5.7炉壁也应采⽤分层打结的⽅法,每层捣打厚度以30mm为宜,每次加料应在50mm~80mm厚为宜。
具体打结⽅法与炉底相同。
5.8当捣打到感应器以上⾼度时,换⽤炉领材料进⾏打结,打结⽅法与前相同。
5.9当炉衬彻底捣打完毕后,应先⽤天然⽓烘烤(⼩⽕烘烤4⼩时,中⽕⼤⽕烘烤4⼩时以上)、再送电烘烤,具体的烘烤可按表3执⾏。
钢的脱碳反应及脱碳(知识简介)

管件知识(3)钢的脱碳反应钢的脱碳反应——钢液内碳氧化而被除去的反应。
碳对钢的力学性能影响很大,是钢中最重要的合金元素。
除了极少数钢种外,绝大多数钢中含碳量都在1%以下;而生铁含碳一般在3~4.5%范围,因此,脱碳就成为炼钢过程中最重要的反应之一。
脱碳反应产物一氧化碳(在钢液含碳很低时,产物中有少量二氧化碳)气泡穿过钢液排出,强烈搅动熔池,这种现象被称为“沸腾”。
沸腾时,气泡中氢、氮等气体的分压极低,使钢液中溶解的氢、氮等有害杂质向气泡中转移,钢中的非金属夹杂物也随着气泡上升而被除去。
沸腾不仅使钢液温度和化学成分均匀,还增加气相-熔渣-钢液的接触面,加快各种反应的速度。
脱碳引起的沸腾是保证钢质量的一个重要措施,所以一般电炉和平炉炼钢过程中总要有一定的去碳量。
脱碳反应从来就受到冶金工作者的特别重视。
早在1931年,瓦舍(H.C.Vacher)和哈密顿(E.H.Hamilton)开始在实验室条件下测出了1580℃铁液中的碳氧平衡浓度积为0.0025;以后,许多知名的冶金学者如奇普曼(J.Chipman)、申克(H.Schenck)等都研究过脱碳反应。
脱碳反应热力学炼钢脱碳过程中,氧传输到钢液有两种途径:①氧气直接和钢液接触,如转炉炼钢时向熔池吹氧脱碳,其反应是:2C+O2→2CO;[C]代表溶于钢中的碳。
②氧经过炉渣传送到钢液,如平炉和电炉炼钢时,氧化期的脱碳,其反应是:(FeO) 代表渣中的氧化亚铁。
两者都包括钢液中的碳氧反应:。
这是个弱放热反应,其平衡常数K随温度升高而稍有减小。
在炼钢温度下,K 为400~500。
当CO的分压为1大气压时,钢液中碳和氧的平衡浓度积为:m=[%C]·[%O]=0.002~0.0025在炼钢过程前期,炉内温度较低,钢中的硅、锰等元素大量氧化,碳也可能部分氧化,它们都在争夺钢中的氧。
以后,钢中硅、锰含量减少,炉温升高,一直到脱氧前,钢液中的碳氧反应即成为控制钢中氧含量的主要反应。
中频炉冶炼纯铁的脱碳技术

中频炉冶炼纯铁的脱碳技术
中频炉冶炼纯铁的脱碳技术主要有两种方法:氧化脱碳法和还原脱碳法。
1. 氧化脱碳法:
氧化脱碳法是利用氧化剂将含碳铁水中的碳转化为CO或CO2气体而实现脱碳的过程。
在中频炉冶炼纯铁时,常使用氧化剂(如氧气)进行脱碳。
具体步骤如下:
- 首先,将含碳的铁水倒入中频炉中,并加热至适当温度。
- 然后,注入适量的氧气,使其与铁水中的碳反应生成CO或CO2气体。
- 随着气体的排出,碳含量逐渐减少,最终得到低碳或纯铁。
2. 还原脱碳法:
还原脱碳法是通过在冶炼过程中加入还原剂,将铁水中的碳还原出来,从而实现脱碳的过程。
在中频炉冶炼纯铁时,常使用还原剂(如生铁、还原渣等)进行脱碳。
具体步骤如下:
- 首先,将含碳的铁水倒入中频炉中,并加热至适当温度。
- 然后,加入适量的还原剂,将还原剂与铁水中的碳发生反应,使碳被还原出来。
- 随着反应进行,碳含量逐渐减少,最终得到低碳或纯铁。
这两种脱碳技术在中频炉冶炼纯铁过程中都有应用,选择使用哪种方法取决于具体的工艺要求和冶炼条件。
钢热处理中的脱碳
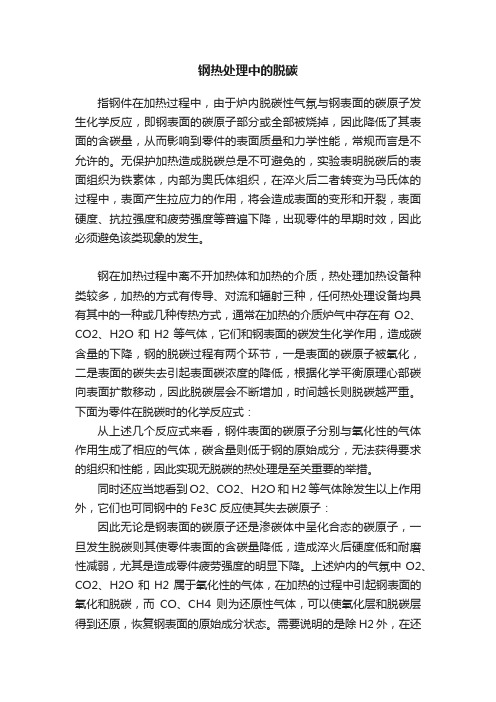
钢热处理中的脱碳指钢件在加热过程中,由于炉内脱碳性气氛与钢表面的碳原子发生化学反应,即钢表面的碳原子部分或全部被烧掉,因此降低了其表面的含碳量,从而影响到零件的表面质量和力学性能,常规而言是不允许的。
无保护加热造成脱碳总是不可避免的,实验表明脱碳后的表面组织为铁素体,内部为奥氏体组织,在淬火后二者转变为马氏体的过程中,表面产生拉应力的作用,将会造成表面的变形和开裂,表面硬度、抗拉强度和疲劳强度等普遍下降,出现零件的早期时效,因此必须避免该类现象的发生。
钢在加热过程中离不开加热体和加热的介质,热处理加热设备种类较多,加热的方式有传导、对流和辐射三种,任何热处理设备均具有其中的一种或几种传热方式,通常在加热的介质炉气中存在有O2、CO2、H2O和H2等气体,它们和钢表面的碳发生化学作用,造成碳含量的下降,钢的脱碳过程有两个环节,一是表面的碳原子被氧化,二是表面的碳失去引起表面碳浓度的降低,根据化学平衡原理心部碳向表面扩散移动,因此脱碳层会不断增加,时间越长则脱碳越严重。
下面为零件在脱碳时的化学反应式:从上述几个反应式来看,钢件表面的碳原子分别与氧化性的气体作用生成了相应的气体,碳含量则低于钢的原始成分,无法获得要求的组织和性能,因此实现无脱碳的热处理是至关重要的举措。
同时还应当地看到O2、CO2、H2O和H2等气体除发生以上作用外,它们也可同钢中的Fe3C反应使其失去碳原子:因此无论是钢表面的碳原子还是渗碳体中呈化合态的碳原子,一旦发生脱碳则其使零件表面的含碳量降低,造成淬火后硬度低和耐磨性减弱,尤其是造成零件疲劳强度的明显下降。
上述炉内的气氛中O2、CO2、H2O和H2属于氧化性的气体,在加热的过程中引起钢表面的氧化和脱碳,而CO、CH4则为还原性气体,可以使氧化层和脱碳层得到还原,恢复钢表面的原始成分状态。
需要说明的是除H2外,在还原性和氧化性的气氛中,如含有水蒸气它将会造成表面的明显脱碳。
作为气体加热介质而言,为了确保加热过程中不出现上述缺陷,应当采用在还原性或保护气氛中完成零件的热处理,这是热处理工作者一直努力的方向,目前陆续开发了一系列的加热方法,实现了不改变零件的表面成分和状态的保护介质的加热。