转炉半干法塔文除尘技术的应用
干法电除尘在转炉炼钢厂的应用
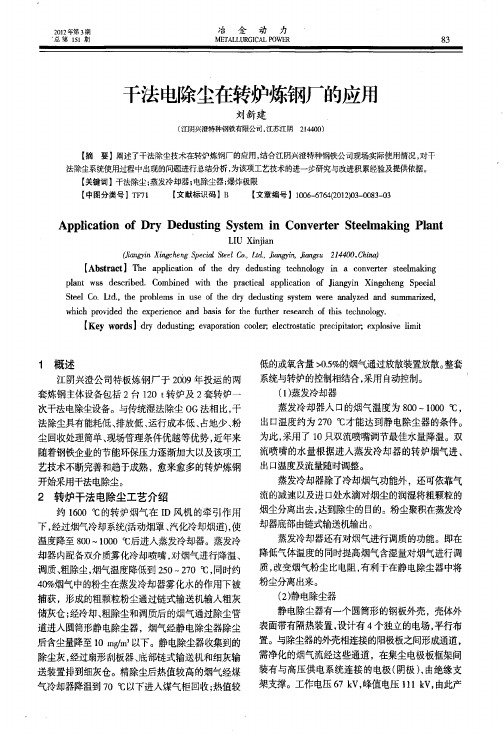
干法电除尘在转炉炼钢厂的应用
刘新建
江阴兴澄特种钢铁有限公司,江苏江阴214400
[摘要]阐述了干法除尘技术在转炉炼钢厂的应用,结合、江阴兴澄特种钢铁公司现场实际使用情况,对干法除尘系统使用过程中出现的问题进行总结分析,为该项工艺技术的进一步研究与改进积累经验及提供依据。
干法除尘;蒸发冷却器;电除尘器;爆炸极限
TF71B1006-6764(2012)03-0083-03
A ppl i cat i on of D r y D edust i ng Syst em i n C onvert er St eel m aki ng P l ant
L I U X i ni i a n
2012年第3期总第151期
@@[1]王岩,邵飞.烟气性质对电除尘器运行的影响[J].高科技与产业化,2009,(12):96-97.
@@[2]陆美丽,胡耀元,马静萌,蒋永福.H2,C O双元体系支链爆炸的特性
与防爆安全指标[J].高校化学工程学报.杭州:浙江大学,2007(2): 94-99.
2012-01-09
作者简介:刘新建(1972-),男,大学学历,工程师,现从事电气设备管理工作。
干法除尘技术在转炉炼钢系统中的应用

【 关键词 】 转炉;干法除尘;烟气温度控 制 中图分 类号 :¥ 6 2 4 . 4 文献识别号 :A 文章编号 l 2 3 0 6 — 1 4 9 9( 2 0 1 3 )2 3 - 0 2 6 0 - 2 我 国现 有 的转炉 煤气净 化与回收系统 多采用 传统 的湿法 除尘系统 ( O G ) ,化控 制水平低钢煤气 回收量较低 ,平均为 7 O ~8 0 m 。 ,净化后 的煤 气含尘量仍达 1 0 0 m g / m 。 ,出煤气柜后 需进 行湿式 电除尘 ,回收系统能耗 较大,吨钢工序 能耗 为 2 3 . 6 k g标煤 。而转炉烟 气的干法除尘系统 ( D D S ) 的 吨钢煤 气 回收 量为 1 0 0 m 3 ,煤气 含尘 量 1 0 m g / m 3 ,吨钢 工序 能耗 仅 为 1 0 k g标煤。因此 ,转炉烟气干法除尘技术被 公认为今后的发展方 向。 中天钢铁集团于 2 0 1 1年初引进 德国鲁 奇公司干法 除尘技术 ,在南厂 区新建三座干法 除尘系统应对三座转炉的生产 。 1 . 千法除尘技术简介及遇到的问题
得 出磁 场 强度 分 布 曲线 如 图 3所示 。从 图 中可 以 看 出 当磁 铁 间距 为 1 6 0 m m
( 接 上 页 )该 越 弱 ;如 果 考 虑 溅 射 速 率 ,优先 设 计 的磁 场 强 度 应 强 些 ,但 溅射功 率等指标并不会 随着 磁场强度 的增加而 增加 ,因为过高 的磁场 强 度会降低靶材利用率。 当前磁约 束磁控 溅射装置 中的永磁铁选 用的是钕铁硼 ,尺寸为 5 0 m m ×5 0 m m ×1 0 m m ,文中矩形平 面靶 的靶长度远大于宽度 , 在整个靶的工作区 域磁场 分布基本 一致。因此对于工 作区域的磁场我们 采用 A N S Y S有 限 元 软件进行分析计算。 2 . 1 磁 铁 厚 度 对 磁 场 的 影 响 文中在A N S Y S模 拟 过 程 中 ,分 别 对 永 磁 铁 的 厚 度 为 l O i , m 、1 5 m m 、 2 0 m m 、2 5 m m时所产生 的磁场 进行模拟对 比 ,最终得 出磁场强度 分布 曲线 如 图 2所示 ,从 图 2中可看 出当磁铁厚度为 1 0 m m时 ,磁铁两端的磁场强 度 与中心点磁场 强度 比值最大 ,且磁场 强度 分布 比较对称 ,也 就是说磁 铁 厚度 为 1 0 m m时磁约束效 果最好 。由此可见 ,磁铁的厚度对磁约束装置 中的磁场强度分布是有一定影响的 ,厚度越大 ,磁约束效果越差。 2 . 2磁 铁 间距 对 磁 场 的 影 响 珏 = _ _
半干法除尘在承钢150t转炉的应用
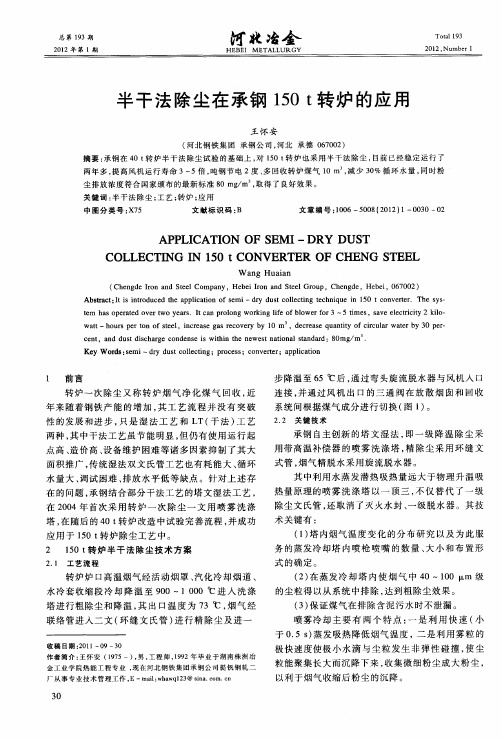
1
前 言
步降温 至 6 5℃后 , 过弯 头旋流 脱水器 与风 机人 口 通
连接 , 通过 风机 出 口 的三通 阀在 放散 烟 囱和 回收 并
转 炉一次 除尘 又 称 转 炉 烟气 净 化 煤 气 回 收 , 近 年 来 随着钢铁 产 能 的增 加 , 工 艺 流 程并 没 有 突 破 其
术关 键有 :
塔 , 随后 的 4 转 炉改 造 中试 验完 善流 程 , 在 0t 并成 功
应用 于 10t 炉除尘 工艺 中。 5 转 2 10t 炉半干 法 除尘技 术方案 5 转
2 1 工 艺 流 程 .
( ) 内烟气 温 度 变化 的分 布 研究 以及 为此 服 1塔 务 的蒸发 冷却塔 内喷 枪 喷 嘴 的数 量 、 大小 和布 置 形 式 的确定 。 ( ) 蒸发 冷 却塔 内使 烟 气 中 4 2在 0~1 0 m 级 0 的尘粒得 以从 系统 中排 除 , 到粗除尘 效果 。 达 ( ) 证煤 气在排 除含 泥污水 时不 泄漏 。 3保
关 键 词 : 干法 除尘 ; 艺 ; 炉 ; 用 半 工 转 应
中 图分 类 号 : 7 X 5 文 献标 识 码 : B 文 章编 号 :0 6— 0 8 2 1 ) 0 3 0 1 0 5 0 ( 0 2 1— 0 0— 2
APP , II CATI ON OF EM I—DRY S DU S T
A b ta t I si tod c d te a plc to f s m i—d y d tc le t e hnqu i 0 tc n re . Th s s sr c : ti nr u e h p i ain o e r us ol ci t c i e n 1 o vet r ng 5 e y— t r a p r td ov rt eas I a o o g wor i ieo l we o ~5 t e e h so e a e e wo y r . tc n pr l n n kng lf fb o rf r3 i s,s v lcrc t io m a e ee tiiy 2 k l— wat— h ur rt n o t e , ic e s sr c v r 0 m ,d c e s a tt fcr u a trb 0 pe — t o spe o fse l n r a e ga e o e y by 1 e r a e qu niy o ic lr wae y 3 r
几种常见转炉煤气的除尘技术汇总

几种常见转炉煤气的除尘技术汇总目前转炉煤气除尘主要分为干法除尘、半干法除尘和湿法除尘。
转炉煤气产生后首先进入汽化冷却烟道,煤气温度由1500℃降至900℃,然后再进入煤气除尘系统。
1除尘技术汇总1干法除尘转炉煤气进入蒸发冷却器,经雾化喷嘴喷出水雾将煤气直接冷却到200℃,喷水量根据煤气放热量精确控制,所喷出的水雾完全蒸发;喷水降温的同时对煤气进行了调质处理,使粉尘的比电阻有利于电除尘器的捕集。
蒸发冷却器可以捕集煤气中30%左右的粉尘(主要为大颗粒粉尘)。
冷却调质后的烟气进入静电除尘器,荷电粉尘在电场力的作用下向集尘极运动并在其上沉积,煤气含尘量进一步降低。
净化后的煤气再送往煤气冷却器降温到70℃左右。
最后根据煤气中一氧化碳和氧气含量决定对其回收或者放散。
2半干法除尘转炉煤气进入蒸发冷却器,蒸发冷却器雾化喷嘴喷入的水雾完全蒸发,吸收煤气热量,煤气冷却降温至200℃,然后送往环缝可调喉口文氏管进行精除尘。
在文氏管喉口处喷入的循环水雾化后和煤气中粉尘充分接触,粉尘被润湿,含尘水滴进入脱水器和煤气分离,煤气得到进一步除尘。
3湿法塔文除尘转炉煤气进入喷淋洗涤塔,喷淋洗涤塔通过喷入大量冷却水将煤气温度降至饱和温度(约70℃)并捕集煤气中粗颗粒的粉尘,达到粗除尘的目的。
然后转炉煤气送往环缝可调喉口文氏管作进一步的精除尘。
在文氏管喉口处喷入的循环水雾化后和煤气中粉尘充分接触,粉尘被润湿,含尘水滴进入弯头脱水器和旋流脱水塔,含尘水滴和煤气分离,实现进一步除尘。
环缝可调喉口文氏管除了起到除尘作用,还兼作调节转炉炉口微差压的作用。
4湿法二文除尘转炉煤气进入溢流文氏管(一文),在溢流文氏管喷入大量冷却水使煤气温度降至饱和温度,同时除去煤气中的粗颗粒的粉尘,再进入重力挡板脱水器脱水。
脱水后进入RD矩形文氏管(二文)进行精除尘,含尘水滴在弯头脱水器、旋流脱水器中和煤气进行分离,转炉煤气实现进一步除尘。
2除尘方式比较1干法静电除转炉煤气干法静电除尘有以下缺点:爆炸问题和二次扬尘问题。
转炉煤气半干法除尘系统工艺
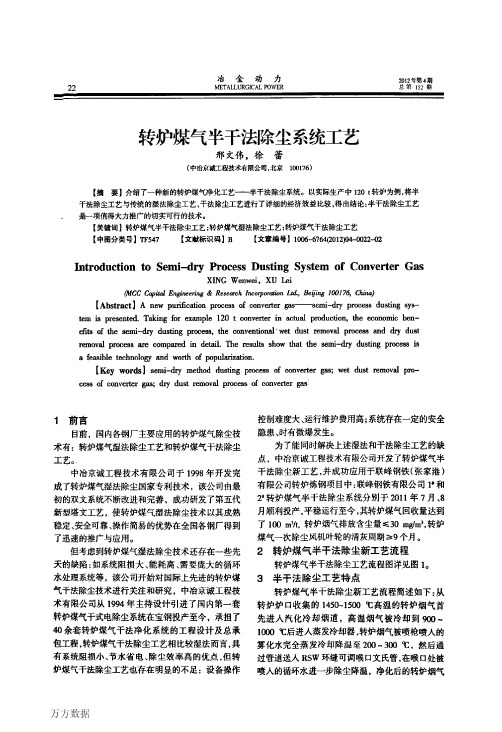
万方数据
转炉煤气半干法除尘系统工艺
作者: 作者单位: 刊名: 英文刊名: 年,卷(期): 邢文伟, 徐蕾, XING Wenwei, XU Lei 中冶京诚工程技术有限公司,北京,100176 冶金动力 Metallurgical Power 2012(4)
本文链接:/Periodical_yjdl201204007.aspx
1育才言 目前,国内各钢厂主要应用的转炉煤气除尘技 术有:转炉煤气湿法除尘工艺和转炉煤气干法除尘 工艺。 中冶京诚工程技术有限公司于1998年开发完 成了转炉煤气湿法除尘国家专利技术,该公司由最 初的双文系统不断改进和完善,成功研发了第五代 新型塔文工艺,使转炉煤气湿法除尘技术以其成熟 稳定、安全可靠、操作简易的优势在全国各钢厂得到 了迅速的推广与应用。 但考虑到转炉煤气湿法除尘技术还存在一些先 天的缺陷:如系统阻损大、能耗高、需要庞大的循环 水处理系统等,该公司开始对国际上先进的转炉煤 气干法除尘技术进行关注和研究,中冶京诚工程技 术有限公司从1994年主持设计引进了国内第一套 转炉煤气干式电除尘系统在宝钢投产至今,承担了 柏余套转炉煤气干法净化系统的工程设计及总承 包工程,转炉煤气干法除尘工艺相比较湿法而言,具 有系统阻损小、节水省电、除尘效率高的优点,但转 炉煤气干法除尘工艺也存在明显的不足:设备操作
收稿日期:2011—12—28 作者简介:蒋卫刚(1968一).男.1993年毕业于武汉钢铁学院煤化工 专业.工程师.现从事燃气生产管理工作。
的高温(650—750℃)煤气,在桥管和集气管内和氨4结语
裹2当日焦化厂焦气现场袭计小时,撇流量抄录数据mⅦ
(上接第23页) 从表1可以看出,以120 t转炉为例。半干法除 尘系统的经济效益虽然略低于干法除尘系统,但较 传统的湿法除尘系统。其每年的经济效益高出约4 百万元。
几种转炉炼钢除尘工艺的对比总结 河北庄泽环保 贾超卫

几种转炉炼钢除尘工艺的对比总结目前转炉炼钢除尘所采用的烟气除尘工艺基本上有三种:湿法除尘、半干法除尘和干法除尘。
这种称谓,我看是以产出的除尘灰的状态来命名的。
产的除尘灰含水就称湿法除尘;产的除尘灰有一部分含水一部分是干燥的就称半干法除尘;产的除尘灰都是干燥的灰就称干法除尘。
一、几种除尘工艺简介1. 湿法除尘湿法除尘是从日本引进来的,最初为“两文两脱”型式,二文是RD 翻板式。
湿法除尘要严格控制进入转炉的白灰粒度,浊环水的水质对除尘系统使用有着至关重要的作用。
2. 半干除尘半干法就是把一文改进成了蒸发冷却器,此处出干灰,减少了浊环水的用量。
半干法除尘是国人将干法与湿法结合运用的结果,是中国特色的转炉除尘工艺。
3.干法除尘干法除尘是上世纪末引进的国外技术。
其中蒸发冷却器和煤气冷却器也使用了水冷却烟气,也不能说完全意义上的“干法”。
目前新建扩建改建的大些容量的转炉,用干法的居多。
小些容量的转炉改用半干法或湿法升级的居多。
随着国家环保要求的严格,各设计院和钢厂也自行研发使用了一些改进的除尘工艺。
如下。
4.目前几种演变的转炉除尘工艺4.1 湿法+湿电其工艺就是在风机前加个湿式电除尘器。
除尘器有卧式两室的也有使用竖式管状电除尘器的。
主要目的是提高系统的除尘效率。
在原有湿法基础上略加投资,见效比较快。
4.2 新6 代湿式除尘其主要工艺为两塔一文三脱式。
是在湿法除尘基础上不断改进的,其综合性能指标比湿法除尘有了较大的提升。
小型转炉改造使用此工艺的比较多。
4.3 干法除尘煤冷前置工艺其工艺就是把煤气回收侧的冷却器“移”到了切换站前(风机后)。
主要是想在煤气回收与不回收时都对这些气体进行洗涤,增加一级除尘效果。
通过使用在回收侧的煤气冷却器看,煤气冷却器确实有一定的洗涤除尘作用。
煤冷前置,使得在烟气放散时多了一级除尘。
4.4 延长汽化烟道降温,使用金属布袋的纯干法除尘延长汽化烟道尽量回收烟气热量,使烟气降到能直接进高温金属布袋除尘器的程度。
炼钢转炉中干法除尘工艺的应用研究
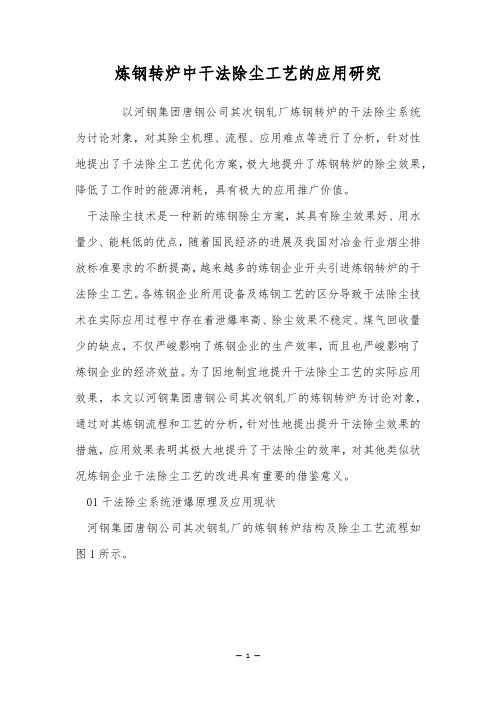
炼钢转炉中干法除尘工艺的应用研究以河钢集团唐钢公司其次钢轧厂炼钢转炉的干法除尘系统为讨论对象,对其除尘机理、流程、应用难点等进行了分析,针对性地提出了千法除尘工艺优化方案,极大地提升了炼钢转炉的除尘效果,降低了工作时的能源消耗,具有极大的应用推广价值。
干法除尘技术是一种新的炼钢除尘方案,其具有除尘效果好、用水量少、能耗低的优点,随着国民经济的进展及我国对冶金行业烟尘排放标准要求的不断提高,越来越多的炼钢企业开头引进炼钢转炉的干法除尘工艺。
各炼钢企业所用设备及炼钢工艺的区分导致干法除尘技术在实际应用过程中存在着泄爆率高、除尘效果不稳定、煤气回收量少的缺点,不仅严峻影响了炼钢企业的生产效率,而且也严峻影响了炼钢企业的经济效益。
为了因地制宜地提升干法除尘工艺的实际应用效果,本文以河钢集团唐钢公司其次钢轧厂的炼钢转炉为讨论对象,通过对其炼钢流程和工艺的分析,针对性地提出提升干法除尘效果的措施,应用效果表明其极大地提升了干法除尘的效率,对其他类似状况炼钢企业干法除尘工艺的改进具有重要的借鉴意义。
01干法除尘系统泄爆原理及应用现状河钢集团唐钢公司其次钢轧厂的炼钢转炉结构及除尘工艺流程如图1所示。
由图1可知,该炼钢转炉的干法除尘系统主要包括蒸发冷却系统、轴流风机、静电除尘系统、切换站及粉尘排放设备、输灰系统等。
在工作时炼钢转炉的烟尘首先在冷却系统内冷却后进行粗除尘,然后再在静电除尘系统中进行精细除尘,完成精除尘后再将烟气转送到煤气柜内。
在该除尘系统中,转炉最初的烟尘内包含了一氧化碳、二氧化碳、氮气、氧气、氢气等,是一种具有易燃易爆特性的有毒气体,在进行降尘的过程中还会加入肯定的水蒸气。
烟尘经过冷却烟道后其温度快速地降低到约70°,而此时烟尘内的氢气含量若大于3%、氧气含量大于2%,则当静电除尘装置发岀静电时产生的电火花将会导致内部的易爆气体发生爆炸,使内部的气体压力急剧增加,使泄露阀进行泄爆。
河钢集团唐钢公司其次钢轧厂炼钢转炉在应用干法除尘工艺后,因所用的炼钢矿石内杂质含量高、设备稳定性不足,导致在实际应用中其干法除尘的泄爆率达到了7.59%,在对煤气进行回收时其整个回收工时达到了197s,且对煤气的回收量仅为51.1m³/t,为了确保生产稳定,导致在炼钢过程中的提枪频率剧增。
转炉第半干法除尘技术

转炉第二代半干法除尘技术介绍1、什么是半干法?半干法是中国发明专利、上海市高新技术。
简单地说,半干法是采用干式蒸发冷却与湿式除尘器(环缝文氏管和/或湿式静电除尘器)相结合的除尘工艺技术。
图1 半干法工艺流程示意图2、为什么要用半干法如图2所示,对于10-100µm只有对于1µm燃烧法中90%的粉尘颗粒大于的S、P、F、As决了干法排放不稳定、维修费用多和卸爆问题。
3、半干法的蒸发冷却器与干法有哪些区别?半干法可以直接选用干法的蒸发冷却器,最好是进行以下改进:●通过喷枪布置改进和增加辅助除尘设计,将粗除尘效率从干法的40%提高到60-80%;●不用蒸汽雾化,因为蒸汽不仅是高能介质,还是除盐除氧的软水,采用蒸汽雾化会全部抵消干法的节能效益,而且还是系统积灰的因素之一;●采用极限蒸发冷却:干法实际蒸发冷却后260ºC,在后部的煤气冷却器仍然采用饱和冷却,排放烟气和回收煤气的湿度都远比湿法高,并且还有循环水。
半干法采用极限蒸发直接冷却到最终的目标温度,使烟气热量不进入排水,既节约新水和循环水量,也为彻底停开湿法的水处理系统创造了条件。
4、半干法为什么能达到极低的粉尘浓度?转炉湿法采用环缝文氏管洗涤除尘可以达到≤10mg/Nm3、甚至更低的粉尘浓度,事实上干法也是通过煤气冷却器的洗涤后才能稳定达到≤10mg/Nm3。
半干法能达到极低的粉尘浓度,比新OG湿法还低、干法也低且稳定(见图3),主要原因:●半干法相当于在湿法除尘的基础上增加了一级粗除尘;●半干法的环缝文氏管与湿法的不同,除尘效率高、阻损小;●5、半干法的环缝文氏管与湿法的主要区别有哪些?如图5所示,目前用于转炉一次除尘的环缝文氏管主要有短径和长径两类:从欧洲、日本等地引进的和仿制的类似产品均为短径,其长度与喉口直径的比约为3,上进气、下驱动。
非金属补偿器高效洗涤塔图6、半干法最早于度采用,使其日趋完善。
大部分用户采用的是所谓的第一代半干法,也就是保留水冲灰,更接近湿法。
转炉烟气半干法除尘工艺
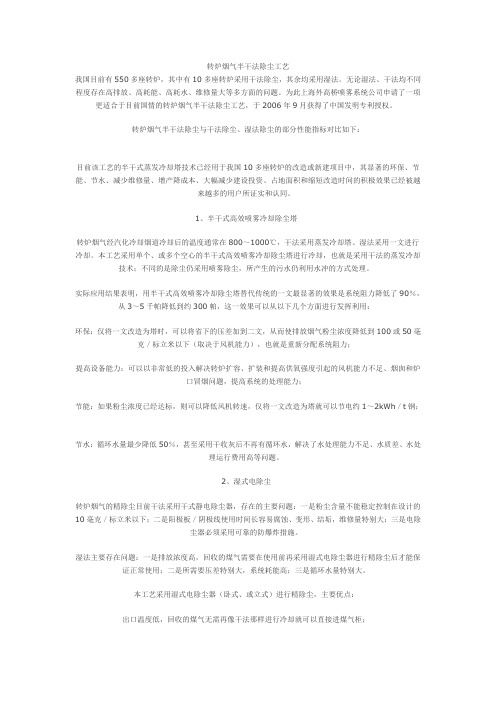
转炉烟气半干法除尘工艺我国目前有550多座转炉,其中有10多座转炉采用干法除尘,其余均采用湿法。
无论湿法、干法均不同程度存在高排放、高耗能、高耗水、维修量大等多方面的问题。
为此上海外高桥喷雾系统公司申请了一项更适合于目前国情的转炉烟气半干法除尘工艺,于2006年9月获得了中国发明专利授权。
转炉烟气半干法除尘与干法除尘、湿法除尘的部分性能指标对比如下:目前该工艺的半干式蒸发冷却塔技术已经用于我国10多座转炉的改造或新建项目中,其显著的环保、节能、节水、减少维修量、增产降成本、大幅减少建设投资、占地面积和缩短改造时间的积极效果已经被越来越多的用户所证实和认同。
1、半干式高效喷雾冷却除尘塔转炉烟气经汽化冷却烟道冷却后的温度通常在800~1000℃,干法采用蒸发冷却塔、湿法采用一文进行冷却。
本工艺采用单个、或多个空心的半干式高效喷雾冷却除尘塔进行冷却,也就是采用干法的蒸发冷却技术;不同的是除尘仍采用喷雾除尘,所产生的污水仍利用水冲的方式处理。
实际应用结果表明,用半干式高效喷雾冷却除尘塔替代传统的一文最显著的效果是系统阻力降低了90%,从3~5千帕降低到约300帕,这一效果可以从以下几个方面进行发挥利用:环保:仅将一文改造为塔时,可以将省下的压差加到二文,从而使排放烟气粉尘浓度降低到100或50毫克/标立米以下(取决于风机能力),也就是重新分配系统阻力;提高设备能力:可以以非常低的投入解决转炉扩容、扩装和提高供氧强度引起的风机能力不足、烟囱和炉口冒烟问题,提高系统的处理能力;节能:如果粉尘浓度已经达标,则可以降低风机转速,仅将一文改造为塔就可以节电约1~2kWh/t钢;节水:循环水量最少降低50%,甚至采用干收灰后不再有循环水,解决了水处理能力不足、水质差、水处理运行费用高等问题。
2、湿式电除尘转炉烟气的精除尘目前干法采用干式静电除尘器,存在的主要问题:一是粉尘含量不能稳定控制在设计的10毫克/标立米以下;二是阳极板/阴极线使用时间长容易腐蚀、变形、结垢,维修量特别大;三是电除尘器必须采用可靠的防爆炸措施。
转炉煤气干法除尘概要
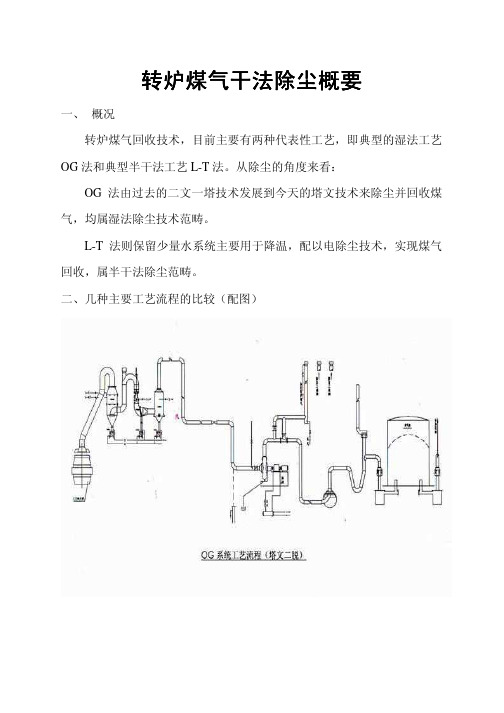
转炉煤气干法除尘概要转炉煤气干法除尘概要一、 概况转炉煤气回收技术,目前主要有两种代表性工艺,即典型的湿法工艺OG法和典型半干法工艺L-T法。
从除尘的角度来看:OG法由过去的二文一塔技术发展到今天的塔文技术来除尘并回收煤气,均属湿法除尘技术范畴。
L-T法则保留少量水系统主要用于降温,配以电除尘技术,实现煤气回收,属半干法除尘范畴。
二、几种主要工艺流程的比较(配图)三、几种主要工艺的优缺点比较OG 法指标L-T 法指标DDH 法指标1、造价低 11、水量少 50~80m 3/h 1、全干、无水 2~2.5 2、实用、可靠、安全2、阻力低6000~7000Pa 2、阻力低 9000Pa 3、实用最广泛 3、无污泥处理系统 3、无污泥处理系统4、排放相对稳定 50mg/Nm 34、显热回收 100kg/t·钢5、煤气含水率低、品质好5、排放稳定 30mg/Nm 36、干法可烧结、回炉 6、抑爆7、流程短 7、煤气干度高、品质好8、干法回用 优点9、控制简单1、水量大 上千吨/h 1、造价高 2~2.5倍 1、造价高2~2.5倍 2、阻力高 2800 Pa 2、易爆 2、阻力波动影响二次 3、污泥系统 3、控制要求高 3、布袋要求高 4、维护量大4、操作要求高5、排放不稳定 50~150mg/Nm 35、钢产量受一定限制6、煤气品质差6、排放受控制、影响大缺点7、二次烟气负荷大四、DDH 法的主要特点DDH 法(英文全称Gas Dry Dedusting & Heat Recovery System ),是针对L-T 法不足而开发的全新技术,其技术特点有如下:1. 抑爆技术针对L-T 法在生产过程中,由于电除尘产生的电火花,而不可避免引起爆炸,进而影响生产节奏这一缺陷,DDH 法采用了密闭袋式除尘器,消除了火花的隐患。
同时,由于取消了水系统降温,在换热器前后设有三重火花捕集的抑爆技术,以消除炉内明火的带入,和使o 2降至最少,低于起爆点。
干法除尘在210t转炉的研究与应用

2 E 2 C耗水量 ; 3 h 2 m / 6
E P细 灰输送 系统 , 加备 用输 灰线 , S 增 取
消 了斗提机 前 的 水平 螺 旋 输 灰 机 , 大 限 度 最
蒸汽耗量 ; h L /
8
8
蒸汽耗量 ; h
8 78 .
减 少 故障停 机 , 全 满 足 了设 备 点 检定 修 的 完
干 法除 尘在 2 0 转 炉 的 研 究 与应 用 1t
2 0转 r 1
摘
王 明 理
要
涟钢 20 转炉煤气 干法 除尘 ( D ) 术应 用两年来 , 1t D S技 设备 安全 稳顺运行 , 保证 了转 炉的正
常生产 。煤气 回收从 8 m / , 0 t逐步提高到 2 1 0 1年的 18m / , 0 t 目前 稳定在 15m / , 1 t煤气含 尘
箱式 消音 器 : 国产 ;
从 工 艺 流 程 和装 备 看 , D D S系 统 较 O G
湿 法 复杂 , 与转 炉 汽 化及 冶 炼 等 工艺 联 系 紧 密 , 锁条件 众 多。应 用 中发 现设计 欠完 善 : 联 转 炉供 氧制 度 、 加料 制度 、 冶炼 操 作 、 煤气 管
加 大细灰 斗提 机 电机功 率 , 1 5 W 调 由 .k 整 为 2 2 W , 决 电 机 过 载 问题 , .k 解 同时 对 斗
提机 的 出 口溜 管 改 造 , 解决 了该 处 积 灰 堵 塞 问题 。
E C区域备件国产化 : 喷枪国产化年节约
成本 3 O万 元 。
表 2 E C喷 枪 国 产 化 前 / 介 质 参 数 及 效 果 V 后
设 定 的 I 机风 量偏 低 , 口返 烟不 仅 D风 炉 存 在安 全 隐患 、 响高层 平 台环境 , 影 同时转 炉
转炉半干法除尘改造减轻了污水处理的负担
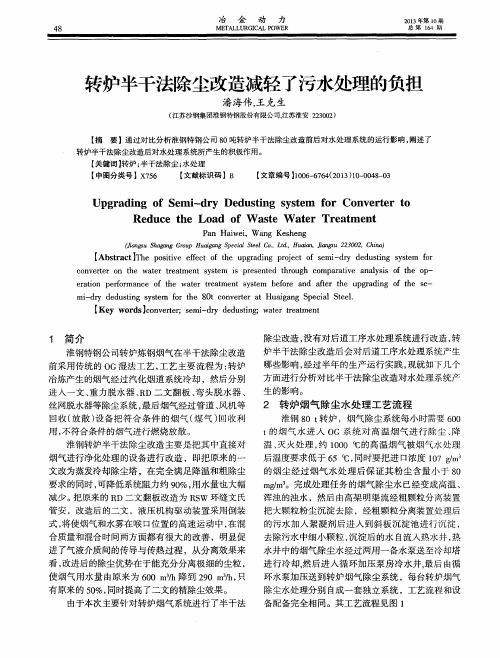
2 转炉烟气 除尘水处理工艺流程
淮钢 8 0 t 转 炉 ,烟气 除尘 系统 每小 时需要 6 0 0
烟气进 行净化处 理 的设备进 行 改造 ,即把原来 的一
文改为蒸发冷却除尘塔 ,在完全满足降温和粗除尘
要求的同时 , 可降低系统阻力约 9 0 %, 用水量也大幅 减少 。 把 原来 的 R D二 文翻板 改造 为 R S W 环缝文 氏 管安 ,改造后 的二文 ,液压机 构驱 动装 置采 用倒 装 式, 将使 烟气 和水雾在 喉 口位置 的高速运 动 中 , 在 混
Pa n Ha i we i ,W a n g Ke s he n g ( J i a n g s u S h a m,  ̄ g G r o u p Hu a i g a r t g却e c i a l S t e e l C o . , L t d . , Hu a i a n ,J i a n g s u 2 2 3 0 0 2 ,C h i ,
方 面进行 分析对 比半 干法 除 尘改造 对水 处理 系统产
生 的影 响。
冶炼产生 的烟气 经过 汽化 烟道 系统冷 却 ,然后 分别
进 入 一文 、 重 力脱 水器 、 R D二 文 翻板 、 弯头 脱水 器 、
丝 网脱水 器等 除尘系统 , 最 后烟 气经 过管 道 、 风机 等
c o n v e r t e r o n t he wa t e r t r e a t me n t s y s t e m i s p r e s e n t e d t h r o u g h c o mp a r a t i v e a na l y s i s o f t h e o p—
干法除尘在韶钢130t转炉的成功应用

干法除尘在韶钢130t转炉的成功应用摘要韶钢炼钢二分厂5#转炉通过技术改造,采用了干法除尘工艺。
该种新工艺对传统的冶炼模式提出了更高的要求。
该文通过对干法除尘工艺的深入研究及时优化冶炼模式,实现了干法除尘系统下转炉的稳定运行。
关键词干法除尘点火泄爆双渣供氧流量0 前言与传统湿法除尘工艺相比干法除尘具有能耗低、占地少、运行成本低、烟尘回收处理容易、煤气烟尘含量低等诸多优势,韶钢积极响应国家节能减排的号召,对炼钢二分厂5#转炉进行干法除尘系统改造。
1. 韶钢130t转炉干法除尘工艺流程介绍韶钢炼钢二分厂建有2座130t顶底复吹转炉,设计生产能力为300万吨/年。
该系统主要由蒸发冷却器、静电除尘器、轴流风机、转换站、煤气冷却器等设备组成。
干法除尘系统工艺流程,见图1。
干法除尘系统的特点及要求由于转炉炼钢具有间断生产的特性,导致冶炼过程中产生的CO 气体和少部分氧气易同时进入到除尘系统中。
一旦两种气体混合并同时达到一定比例,遇到火花或明火时,就会产生燃烧和爆炸。
由于在静电除尘器的阴极极线一端,随时都在放电产生电火花,因此,当转炉烟气通过静电除尘器时极易产生燃烧和爆炸,爆炸发生后将迫使转炉系统停止冶炼。
综合以上各类因素,预防静电除尘器泄爆是确保炼钢系统平稳运行的核心问题,转炉烟气成分的控制,即平衡煤气中的O2和CO含量是解决核心问题的最佳切入点和关键因素,而烟气成分的变化与转炉冶炼工艺存在密切的关系。
干法除尘泄爆原理3.1 静电除尘器工作原理静电除尘器内分4个电场,平行布置,每个电场采用72-90KV的高压供电。
电场在与静电除尘器筒体平行方向上安装极板,极板与极板之间形成气体通道。
同时极板之间布置高压框架,框架中装有极线(阴极)并和高压供电系统连接,顶部连接至绝缘子保温箱。
绝缘子采用电加热,并充满N2,以防止绝缘子由于粉尘积聚或者绝缘体壁的冷凝物(水和气)形成而产生电火花,导致绝缘子击穿。
极线周围存在高强度的电压,由于电晕电压作用,使气体电离,灰尘因受到部分气体离子作用而带上负电,在放电极(极线)和集尘极(极板)之间的电场作用下,向集尘极移动并积聚。
转炉半干法一次除尘工艺操作规程
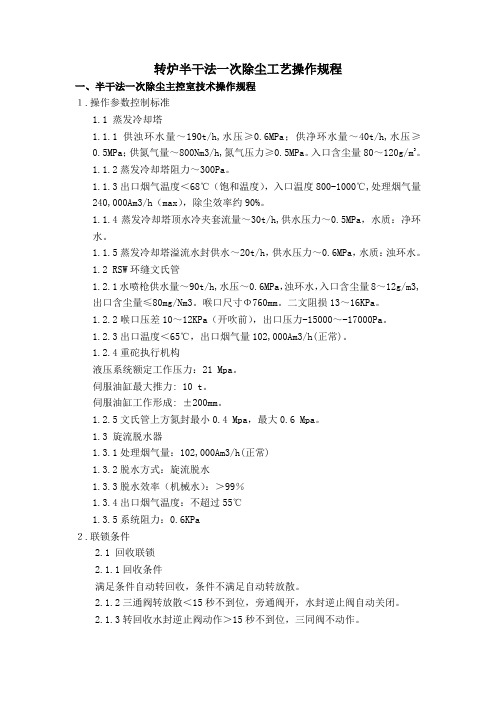
转炉半干法一次除尘工艺操作规程一、半干法一次除尘主控室技术操作规程1.操作参数控制标准1.1 蒸发冷却塔1.1.1供浊环水量~190t/h,水压≥0.6MPa;供净环水量~40t/h,水压≥0.5MPa;供氮气量~800Nm3/h,氮气压力≥0.5MPa。
入口含尘量80~120g/m3。
1.1.2蒸发冷却塔阻力~300Pa。
1.1.3出口烟气温度<68℃(饱和温度),入口温度800-1000℃,处理烟气量240,000Am3/h(max),除尘效率约90%。
1.1.4蒸发冷却塔顶水冷夹套流量~30t/h,供水压力~0.5MPa,水质:净环水。
1.1.5蒸发冷却塔溢流水封供水~20t/h,供水压力~0.6MPa,水质:浊环水。
1.2 RSW环缝文氏管1.2.1水喷枪供水量~90t/h,水压~0.6MPa,浊环水,入口含尘量8~12g/m3,出口含尘量≤80mg/Nm3。
喉口尺寸Φ760mm。
二文阻损13~16KPa。
1.2.2喉口压差10~12KPa(开吹前),出口压力-15000~-17000Pa。
1.2.3出口温度<65℃,出口烟气量102,000Am3/h(正常)。
1.2.4重砣执行机构液压系统额定工作压力:21 Mpa。
伺服油缸最大推力: 10 t。
伺服油缸工作形成: ±200mm。
1.2.5文氏管上方氮封最小0.4 Mpa,最大0.6 Mpa。
1.3 旋流脱水器1.3.1处理烟气量:102,000Am3/h(正常)1.3.2脱水方式:旋流脱水1.3.3脱水效率(机械水):>99%1.3.4出口烟气温度:不超过55℃1.3.5系统阻力:0.6KPa2.联锁条件2.1 回收联锁2.1.1回收条件满足条件自动转回收,条件不满足自动转放散。
2.1.2三通阀转放散<15秒不到位,旁通阀开,水封逆止阀自动关闭。
2.1.3转回收水封逆止阀动作>15秒不到位,三同阀不动作。
2.1.4转回收三通阀>15秒不到位,旁通阀开,三通阀关,水封逆止关。
转炉一次烟气半干法除尘技术升级优化及数值模拟分析

转炉一次烟气半干法除尘技术升级优化及数值模拟分析杨军瑞;杨晓琼【摘要】目前国内大多数转炉一次除尘系统采用的是二文三脱湿法除尘(即OG 法),由于国家环保标准的提高,这种除尘系统的除尘效果已达不到最新的环保标准要求,因此必须对现有的转炉一次除尘系统进行升级改造.目前采用的最多的改造方式是将该系统改造为半干法除尘系统(即洗涤塔+环缝+脱水器的形式).使转炉生产过程中产生的一次烟气经除尘设施净化后排放烟气中含尘浓度小于国家相关规范规定的排放标准.但是,半干法除尘系统也存在很多不足之处,除尘效果也是差强人意.本文在现有的半干法除尘系统基础上,再次进行技术升级改造,提出一种新型的半干法除尘系统,尽可能提高除尘设施的除尘效果,并且做到节水节电、降低能耗.【期刊名称】《能源环境保护》【年(卷),期】2017(031)004【总页数】5页(P41-45)【关键词】转炉;一次除尘;半干法除尘系统;环保标准【作者】杨军瑞;杨晓琼【作者单位】中冶东方工程技术有限公司,山东青岛266555;中铁十九局集团第五工程有限公司辽宁大连116110【正文语种】中文【中图分类】X701中国钢铁产业正处于结构调整和优化升级的时期,面临着日益严峻的资源和环境压力,必须走资源节约型、环境友好型的可持续发展之路。
回收和利用好转炉煤气对于炼钢节能降耗,减轻环境污染意义重大。
在炼钢工艺中,转炉是最主要的炼钢设备,而转炉一次除尘是保障转炉正常生产的基础。
目前,国内很多钢铁企业炼钢转炉一次除尘系统采用的是二文三脱湿法除尘(即OG法),由于国家环保标准的提高,这种除尘系统的除尘效果已达不到最新的环保标准要求,因此必须对现有的转炉一次除尘系统进行升级改造[1~4]。
针对转炉一次除尘系统的改造方法大多分为两种,第一:彻底拆除原有的二文三脱湿法除尘系统(即OG法),新建干法除尘系统(即LT法),改造完成后能够彻底解决转炉一次烟气排放不达标的状况,但是这种改造形式存在造价高、投资大、占地面积大和自动化控制繁杂等缺点,因此很多企业对该种改造形式存在顾虑[5~6]。
钢铁转炉煤气干法除尘技术的应用与优化
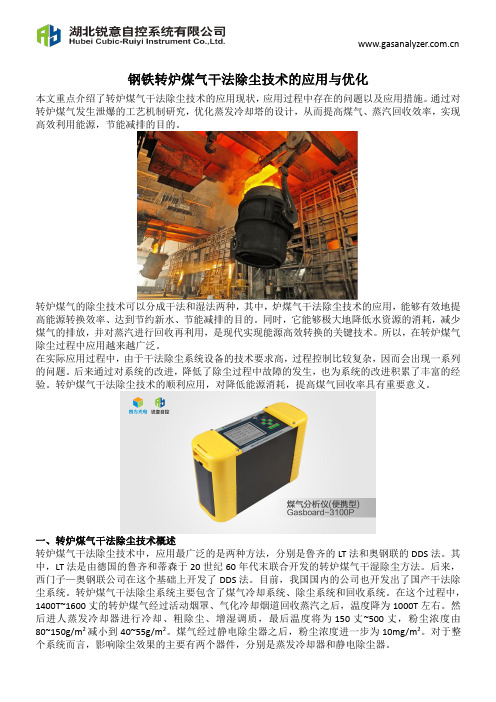
钢铁转炉煤气干法除尘技术的应用与优化本文重点介绍了转炉煤气干法除尘技术的应用现状,应用过程中存在的问题以及应用措施。
通过对转炉煤气发生泄爆的工艺机制研究,优化蒸发冷却塔的设计,从而提高煤气、蒸汽回收效率,实现高效利用能源,节能减排的目的。
转炉煤气的除尘技术可以分成干法和湿法两种,其中,炉煤气干法除尘技术的应用,能够有效地提高能源转换效率、达到节约新水、节能减排的目的。
同时,它能够极大地降低水资源的消耗,减少煤气的排放,并对蒸汽进行回收再利用,是现代实现能源高效转换的关键技术。
所以,在转炉煤气除尘过程中应用越来越广泛。
在实际应用过程中,由于干法除尘系统设备的技术要求高,过程控制比较复杂,因而会出现一系列的问题。
后来通过对系统的改进,降低了除尘过程中故障的发生,也为系统的改进积累了丰富的经验。
转炉煤气干法除尘技术的顺利应用,对降低能源消耗,提高煤气回收率具有重要意义。
一、转炉煤气干法除尘技术概述转炉煤气干法除尘技术中,应用最广泛的是两种方法,分别是鲁齐的LT法和奥钢联的DDS法。
其中,LT法是由德国的鲁齐和蒂森于20世纪60年代末联合开发的转炉煤气干湿除尘方法。
后来,西门子—奥钢联公司在这个基础上开发了DDS法。
目前,我国国内的公司也开发出了国产干法除尘系统。
转炉煤气干法除尘系统主要包含了煤气冷却系统、除尘系统和回收系统。
在这个过程中,1400T~1600丈的转炉煤气经过活动烟罩、气化冷却烟道回收蒸汽之后,温度降为1000T左右。
然后进人蒸发冷却器进行冷却、粗除尘、增湿调质,最后温度将为150丈~500丈,粉尘浓度由80~150g/m2减小到40~55g/m2。
煤气经过静电除尘器之后,粉尘浓度进一步为10mg/m2。
对于整个系统而言,影响除尘效果的主要有两个器件,分别是蒸发冷却器和静电除尘器。
1、蒸发冷却器蒸发冷却器顾名思义是利用水蒸气的蒸发冷却原理来工作的。
和湿法除尘技术相比,这种冷却方式极大地降低了冷却所需要的水量,达到节约水的目的。
福建三钢100吨转炉一次除尘系统半干法改造系统介绍
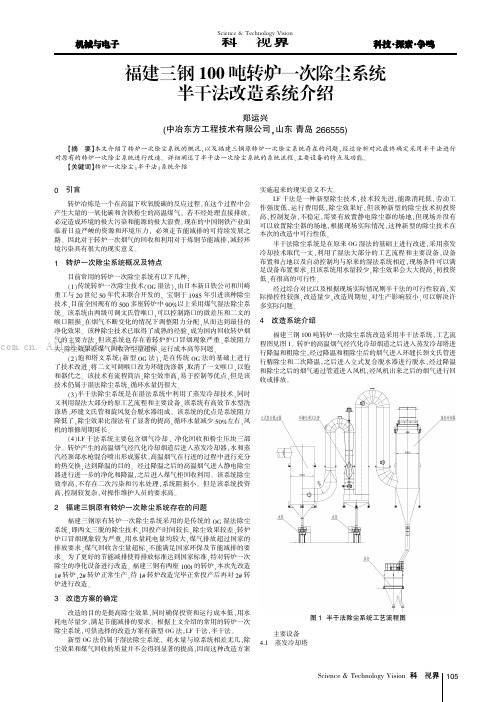
Science &Technology Vision 科技视界0引言转炉冶炼是一个在高温下吹氧脱碳的反应过程,在这个过程中会产生大量的一氧化碳和含铁粉尘的高温煤气,若不经处理直接排放,必定造成环境的极大污染和能源的极大浪费。
现在的中国钢铁产业面临着日益严峻的资源和环境压力,必须走节能减排的可持续发展之路。
因此对于转炉一次烟气的回收和利用对于炼钢节能减排,减轻环境污染具有很大的现实意义。
1转炉一次除尘系统概况及特点目前常用的转炉一次除尘系统有以下几种:(1)传统转炉一次除尘技术(OG 湿法),由日本新日铁公司和川崎重工与20世纪50年代末联合开发的,宝钢于1985年引进该种除尘技术,目前全国现有的500多座转炉中90%以上采用煤气湿法除尘系统。
该系统由两级可调文氏管喉口,可以控制路口的微差压和二文的喉口阻损,在烟气不断变化的情况下调整阻力分配,从而达到最佳的净化效果。
该种除尘技术已取得了成熟的经验,成为国内回收转炉烟气的主要方法,但该系统也存在着转炉炉口冒烟现象严重、系统阻力大、除尘效果差煤气回收含尘量超标、运行成本高等问题。
(2)饱和塔文系统(新型OG 法),是在传统OG 法的基础上进行了技术改进,将二文可调喉口改为环缝洗涤器,取消了一文喉口,以饱和器代之。
该技术有流程简洁,除尘效率高,易于控制等优点,但是该技术仍属于湿法除尘系统,循环水量仍很大。
(3)半干法除尘系统是在湿法系统中利用了蒸发冷却技术,同时又利用湿法大部分的原工艺流程和主要设备,该系统有高效节水型洗涤塔、环缝文氏管和旋风复合脱水器组成。
该系统的优点是系统阻力降低了,除尘效果比湿法有了显著的提高,循环水量减少50%左右,风机的维修周期延长。
(4)LF 干法系统主要包含烟气冷却、净化回收和粉尘压块三部分。
转炉产生的高温烟气经汽化冷却烟道后进入蒸发冷却器,水和蒸汽经顶部水枪混合喷出形成雾状,高温烟气在行进的过程中进行充分的热交换,达到降温的目的。
转炉气的净化及应用
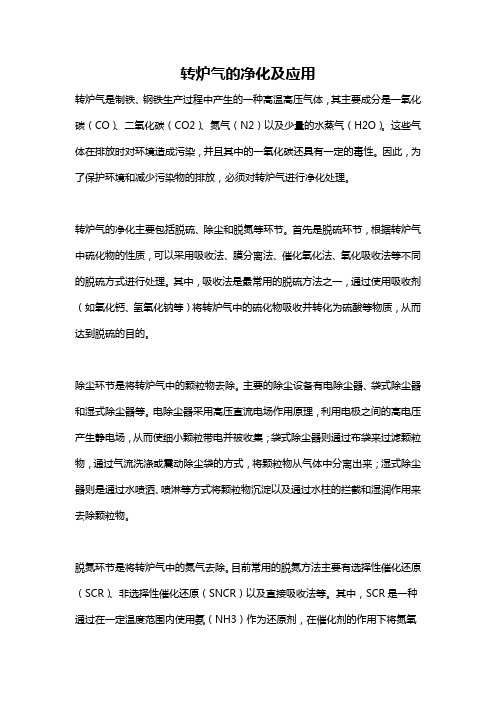
转炉气的净化及应用转炉气是制铁、钢铁生产过程中产生的一种高温高压气体,其主要成分是一氧化碳(CO)、二氧化碳(CO2)、氮气(N2)以及少量的水蒸气(H2O)。
这些气体在排放时对环境造成污染,并且其中的一氧化碳还具有一定的毒性。
因此,为了保护环境和减少污染物的排放,必须对转炉气进行净化处理。
转炉气的净化主要包括脱硫、除尘和脱氮等环节。
首先是脱硫环节,根据转炉气中硫化物的性质,可以采用吸收法、膜分离法、催化氧化法、氧化吸收法等不同的脱硫方式进行处理。
其中,吸收法是最常用的脱硫方法之一,通过使用吸收剂(如氧化钙、氢氧化钠等)将转炉气中的硫化物吸收并转化为硫酸等物质,从而达到脱硫的目的。
除尘环节是将转炉气中的颗粒物去除。
主要的除尘设备有电除尘器、袋式除尘器和湿式除尘器等。
电除尘器采用高压直流电场作用原理,利用电极之间的高电压产生静电场,从而使细小颗粒带电并被收集;袋式除尘器则通过布袋来过滤颗粒物,通过气流洗涤或震动除尘袋的方式,将颗粒物从气体中分离出来;湿式除尘器则是通过水喷洒、喷淋等方式将颗粒物沉淀以及通过水柱的拦截和湿润作用来去除颗粒物。
脱氮环节是将转炉气中的氮气去除。
目前常用的脱氮方法主要有选择性催化还原(SCR)、非选择性催化还原(SNCR)以及直接吸收法等。
其中,SCR是一种通过在一定温度范围内使用氨(NH3)作为还原剂,在催化剂的作用下将氮氧化物还原为氮气和水的方法;SNCR则是通过在高温条件下直接喷射非选择性还原剂(如尿素)到转炉气中,使其与氮氧化物发生反应,转化为氮气等无害物质。
净化处理后的转炉气可以得到高价值的利用。
其中,转炉气中的一氧化碳是一种重要的燃料。
可以通过改造转炉气净化系统,提取并收集其中的一氧化碳,并将其用于燃烧发电、燃料制备等方面。
此外,转炉气中还含有一定量的热能,可以通过余热回收技术将其回收利用,提高能源利用效率。
此外,转炉气的净化处理也对铁矿石还原过程中的环境影响进行了有效的控制。
- 1、下载文档前请自行甄别文档内容的完整性,平台不提供额外的编辑、内容补充、找答案等附加服务。
- 2、"仅部分预览"的文档,不可在线预览部分如存在完整性等问题,可反馈申请退款(可完整预览的文档不适用该条件!)。
- 3、如文档侵犯您的权益,请联系客服反馈,我们会尽快为您处理(人工客服工作时间:9:00-18:30)。
2 关键设备及工作原理
2 1 高效喷雾蒸发洗涤塔
高效喷雾蒸发洗涤塔替代传统湿法除尘的一级 文氏管 ,将塔体、溢流水封与水冷夹套采取一体设
计 ,汽化冷却烟道过来的 9 0 0~ 1 0 0 0℃左右 的高
5 9
3 工 艺 特 点
新型 半 干 法 塔 文 除 尘 技 术 结 合 了干 法 ( L T ) 除尘 和传统 湿法 ( O G)除尘 两种 除尘 技术 的优点 , 同时结合新 疆公 司实 际状况 ,进行 优化 和改进 ,达
,
f \
\ /
—
A Q —
/
1 一大法 兰 ;2一水 冷 夹套 外 侧 ;3一水 冷 夹套 内侧 ;
图1 半 干 法 除 尘 系统 示 意
进行脱水处理 ,滤饼 含水率小 于 2 5 %一 3 0 % ,泥
斗仓储存 ,然后直接装 车运至除尘污泥处理场地 , 与其他固体废弃物 昆 合配 比压制成球 团,当炼钢原
作者简介 :单士宾 ( 1 9 8 2 一) ,男 , 2 0 1 1 年 7月毕业 于j E 京 科技大
莱钢科技
2 0 1 3 年1 0月
转 炉 半 干 法 塔 文 除尘 技 术 的应 用
单 士宾 ,尹彦周 , 范树璐 ( 山钢集 团莱芜钢铁 新疆 有限公 司)
摘 要 :新型半千法塔 文除尘技术在新疆公 司转炉上成功应用 ,自 投产 已 连续安全稳定运行 6个月,烟尘排放 浓度完全达到国家环保要求。截止 目前除尘系统设备和一次除尘风机保持
单士宾 ,等 :转炉 半干 法塔 文除尘 技术 的应用 温烟 气经过 溢 流水封 到达洗 涤塔入 口 ,通过洗 涤塔 人 口的 4支 外 混 双 介 质 喷枪 喷 出 通 过 氮 气 或 蒸 汽
第 5期 ( 总第 1 6 7期 )
过脱水器下部水封排出。
2 . 3 旋 流脱 水器
( 压力 0 . 3 5— 0 . 4 5 M P a )雾化的水蒸汽 ,将烟气温 度快速降到 9 0℃左右 ,然后经过洗 涤塔 内 7支高 压水喷枪对烟气进行粗 除尘 ,可以除去约 9 6 % 的
良 好状 态,系统无积灰结垢 ,实现免维护零故障状 态,完全达到 了安全可靠、投资运行成本
低 、 维护 管理 方便 和环 保 节能 的 目的 。
关键 词 :半干 法 除尘 ;关键 设备 ;工作原 理 ;工 艺特点
0 前 言
新疆公司炼钢厂 2 0 1 3年 3月 1 0日建成投产 , 期工程配备一座 1 2 0 t 转炉,年产钢 1 0 0 万t ,转 炉在吹炼过程中产生大量含一氧化碳和氧化铁等粉 尘的高温烟气 ,考虑新疆公司地处偏远地区,人员
护 的溢流水 封 ,对其 结构形 式进 行改进 ,替 代湿 法 除 尘系统 的一 文 ,易 于装 配调 整 ,有 效补偿 汽化 冷 却 烟道热 涨 、冷缩产 生 的横 向和纵 向位移 ,并起 到 防爆 泄压作 用 ,同时还起 到 内部 烟气 与外部 空气 隔 绝 的作用 。 2 ) 高效 喷雾蒸 发洗 涤 塔 喷枪 设 计 为外 混 双 介
粉尘 ,绝 大部 分 尘 通过洗 涤水 经洗 涤塔下 部 的排 水水 封排 出。此 时 洗 涤塔 出 口烟 气 温 度 稳 定 在 5 5 ℃左 右 ,系统 阻力 约为 4 5 0 P a 。
溢 流水封 结构见 图 2 。 i
,
旋流脱水器主要由壳体 、人孔 、旋流叶片 、防
爆 阀等 组成 ,结构 简单 ,运行 阻力低 ( O . 5—1 k P a 左右 ) ,脱水 效果 好 ,故 障率 低 。解 决 了丝 网脱 水 器易堵 塞 、复挡式 脱水 器结构 复杂 、阻力 偏大 、结 垢 后 不易清 理 的问题 。
的。
半干法除尘系统结构见图 1 。
1 工艺技 术流程
1 . 1 工 艺流 程
活动 烟罩 捕集的转炉烟气经过汽化冷却 烟道
后 ,约 9 0 0—1 0 0 0 o C的高 温 烟 气 经 过 高 效 喷 雾 蒸
发洗涤塔 的初步净化 和冷却后 ,烟气温度 降到约 5 0℃ ,饱和后的烟气经过重砣式可调文 氏管 ( 简 称二文喉 口) 、9 0 。 弯头脱水器 、漩流脱水器进一步
脱 水 净 化 。烟 气 含 尘 量 可 达 到 3 0 mg / N m 以 下 。
净化后的烟气经过煤气 回收 管道进 入离心式鼓 风 机 ,烟气出风机后再经过三通 阀切换 ,经过水封 阀
送至煤气柜或经高空放散塔燃烧放散。
除 尘后 粉尘 全部 以水 冲洗 的方式 进 人 污水处 理 站 ,经 沉淀 浓缩 处理 后 由渣浆 泵加 压至 板框 压滤 机
一
料使用。经过滤澄清后 的 “ 污水 ”在除尘 系统 中
循环使用 ,该系统做到 闭路循 环 ,实现污水零 排 放 ,降低净水消耗。
1 . 2 除 尘 系统 流程
转炉一汽化冷却烟道一 高效喷雾蒸发洗涤塔一 环缝文氏管一9 O 。 弯头脱水器叶旋流脱水器 鼓风
机。
配置少等 因素 ,首 次采用新 型半 干法塔文 除尘技 术 ,对转炉烟气进行冷却 、净化 , 并 回收煤气 ,达 到安全稳定 、操作方便 、节能降耗 、保护环境 的目
4一水 冷 夹套 底 板 ;5一水 封 盖 板 ;6一水 封 挡 板 ;
到投资低 ,除尘效率高、故障率低及便于维护管理
的 目的。
7一水冷 夹套回水管 ;8一水冷 夹套进水管 ;
9一水 封 箱 ;1 0一洗 涤塔 本 体
图 2 溢 流 水 封 结 构 示 意
1 )高效喷雾蒸发洗涤塔与汽化烟道连接取消 干法除尘中的高温补偿器 ,采用价格低廉 、便于维
烟气到达旋流脱水器后 ,温度一般 4 5℃左右 , 此 时的烟气 仍含水 量较 大 。烟气通 过脱水 器 内部 的
\ ]
| /
旋流复挡脱水 、 旋流叶片离心脱水等将烟气中的大 部分水 分离 ,然后 通过 下部 的负压水 封排 出系 统 。
f
-
\ 霉 \ . r