铸轧生产中产生的主要缺陷及消除方法
铸造铸件常见缺陷原因与解决方法分析

铸造铸件常见缺陷原因与解决方法分析前言铸造工艺过程复杂,影响铸件质量的因素很多,往往由于原材料控制不严,工艺方案不合理,生产操作不当,管理制度不完善等原因,会使铸件产生各种铸造缺陷。
常见的铸件缺陷名称、特征和产生的原因,详见下表。
★ 常见铸件缺陷及产生原因★缺陷名称特征产生的主要原因气孔在铸件内部或表面有大小不等的光滑孔洞①炉料不干或含氧化物、杂质多;②浇注工具或炉前添加剂未烘干;③型砂含水过多或起模和修型时刷水过多;④型芯烘干不充分或型芯通气孔被堵塞;⑤春砂过紧,型砂透气性差;⑥浇注温度过低或浇注速度太快等缩孔与缩松缩孔多分布在铸件厚断面处,形状不规则,孔内粗糙①铸件结构设计不合理,如壁厚相差过大,厚壁处未放冒口或冷铁;②浇注系统和冒口的位置不对;③浇注温度太高;④合金化学成分不合格,收缩率过大,冒口太小或太少砂眼在铸件内部或表面有型砂充塞的孔眼①型砂强度太低或砂型和型芯的紧实度不够,故型砂被金属液冲入型腔;②合箱时砂型局部损坏;③浇注系统不合理,内浇口方向不对,金属液冲坏了砂型;④合箱时型腔或浇口内散砂未清理干净粘砂铸件表面粗糙,粘有一层砂粒①原砂耐火度低或颗粒度太大;②型砂含泥量过高,耐火度下降;③浇注温度太高;④湿型铸造时型砂中煤粉含量太少;⑤干型铸造时铸型未刷涂斜或涂料太薄夹砂铸件表面产生的金属片状突起物,在金属片状突起物与铸件之间夹有一层型砂①型砂热湿拉强度低,型腔表面受热烘烤而膨胀开裂;②砂型局部紧实度过高,水分过多,水分烘干后型腔表面开裂;③浇注位置选择不当,型腔表面长时间受高温铁水烘烤而膨胀开裂;④浇注温度过高,浇注速度太慢铸件沿分型面有相对位置错移①模样的上半模和下半模未对准;②合箱时,上下砂箱错位;③上下砂箱错型未夹紧或上箱未加足够压铁,浇注时产生错箱冷隔铸件上有未完全融合的缝隙或洼坑,其交接处是圆滑的①浇注温度太低,合金流动性差;②浇注速度太慢或浇注中有断流;③浇注系统位置开设不当或内浇道横截面积太小;④铸件壁太薄;⑤直浇道(含浇口杯)高度不够;⑥浇注时金属量不够,型腔未充满浇不足铸件未被浇满裂纹铸件开裂,开裂处金属表面有氧化膜①铸件结构设计不合理,壁厚相差太大,冷却不均匀;②砂型和型芯的退让性差,或春砂过紧;③落砂过早;④浇口位置不当,致使铸件各部分收缩不均匀★ 常见铸件缺陷及预防措施★序缺陷名称缺陷特征预防措施1 气孔在铸件内部、表面或近于表面处,有大小不等的光滑孔眼,形状有圆的、长的及不规则的,有单个的,也有聚集成片的。
常见压铸件缺陷及解决方法

常见压铸件缺陷及解决方法一、流痕其他名称:条纹。
特征:铸件表面上呈现与金属液流动方向相一致的,用手感觉得出的局部下陷光滑纹路。
此缺陷无发展方向,用抛光法能去处。
产生原因:1、两股金属流不同步充满型腔而留下的痕迹。
2、模具温度低,如锌合金模温低于150℃,铝合金模温低于180℃,都易产生这类缺陷。
3、填充速度太高。
4、涂料用量过多。
排除措施:1、调整内浇口截面积或位置。
2、调整模具温度,增大溢流槽。
3、适当调整填充速度以改变金属液填充型腔的流态。
4、涂料使用薄而均匀。
二、冷隔,水纹其他名称:冷接(对接),水纹。
特征:温度较低的金属流互相对接但未熔合而出现的缝隙,呈不规则的线形,有穿透的和不穿透的两种,在外力的作用下有发展的趋势。
产生原因:1、金属液浇注温度低或模具温度低。
2、合金成分不符合标准,流动性差。
3、金属液分股填充,熔合不良。
4、浇口不合理,流程太长。
5、填充速度低或排气不良。
6、比压偏低。
排除措施:1、适当提高浇注温度和模具温度。
2、改变合金成分,提高流动性。
3、改进浇注系统,加大内浇口速度,改善填充条件。
4、改善排溢条件,增大溢流量。
5、提高压射速度,改善排气条件。
6、提高比压三、擦伤其他名称:拉力、拉痕、粘模伤痕。
特征:顺着脱模方向,由于金属粘附,模具制造斜度太小而造成铸件表面的拉伤痕迹,严重时成为拉伤面。
产生原因:1、型芯、型壁的铸造斜度太小或出现倒斜度。
2、型芯、型壁有压伤痕。
3、合金粘附模具。
4、铸件顶出偏斜,或型芯轴线偏斜。
5、型壁表面粗糙。
6、涂料常喷涂不到。
7、铝合金中含铁量低于%。
排除措施:1、修正模具,保证制造斜度。
2、打光压痕。
3、合理设计浇注系统,避免金属流对冲型芯、型壁,适当降低填充速度。
4、修正模具结构。
5、打光表面。
6、涂料用量薄而均匀,不能漏喷涂料。
7、适当增加含铁量至~%。
四、凹陷其他名称:缩凹、缩陷、憋气、塌边。
特征:铸件平滑表面上出现的凹瘪的部分,其表面呈自然冷却状态。
铸造缺陷原因及其解决方法

铸造缺陷原因及其解决方法
铸造缺陷是铸造行业经常出现的一类问题,对铸件的功能和使用寿命有负面影响。
在近年来,随着材料科学领域的进步,铸铁、钢、金属等的性能越来越高,越来越多的新型铸造形式和新型工艺方法被开发出来,但是铸造缺陷依然存在,需要及时解决。
铸造缺陷的原因很复杂,主要有以下几类:一是铸件的铸造工艺参数不当,包括铸件尺寸参数不合理,成型材料未能满足要求,流体特性、温度、压力等参数不足;二是模具设计过程中出现问题,包括模具结构设计不当、表面材质不满足要求等;三是原料误差,原料中病害比例高,导致铸件组织结构不稳定,抗拉强度低。
解决铸造缺陷的方法:一是针对工艺参数不当,应采取有效的治理措施,进行工艺参数的优化及控制,在模具设计中加强细部处理或使用更高性能的材料;二是对原材料误差,应采取措施分离优良料和劣料,保证原料质量,增加试验对原料力学和化学性质检测,改善铸件质量;三是在成型前,应做出正确的实验,要求较高,确保模具尺寸精度,应用胶粉注射成型增加工艺性能。
通过科学的铸造工艺参数设计,优质的原材料配置,模具精细设计,合理的实验控制,减少不合格品,增加铸件质量,都可以有效地解决铸造缺陷的问题。
只有把解决这些铸造缺陷的解决方案扎实,从技术、过程、品质等角度进行多方面开展,才能保证铸件的功能以及使用寿命,有助于企业提升铸件的整体质量水平,建立良好的企业形象。
铸造中常见缺陷及其处理方法
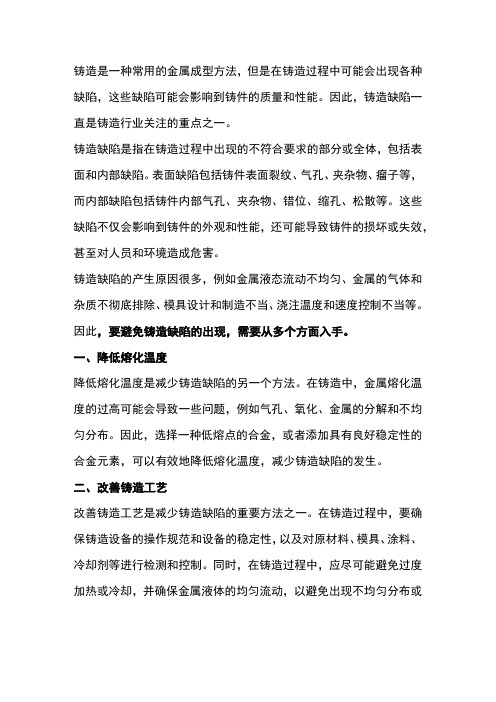
铸造是一种常用的金属成型方法,但是在铸造过程中可能会出现各种缺陷,这些缺陷可能会影响到铸件的质量和性能。
因此,铸造缺陷一直是铸造行业关注的重点之一。
铸造缺陷是指在铸造过程中出现的不符合要求的部分或全体,包括表面和内部缺陷。
表面缺陷包括铸件表面裂纹、气孔、夹杂物、瘤子等,而内部缺陷包括铸件内部气孔、夹杂物、错位、缩孔、松散等。
这些缺陷不仅会影响到铸件的外观和性能,还可能导致铸件的损坏或失效,甚至对人员和环境造成危害。
铸造缺陷的产生原因很多,例如金属液态流动不均匀、金属的气体和杂质不彻底排除、模具设计和制造不当、浇注温度和速度控制不当等。
因此,要避免铸造缺陷的出现,需要从多个方面入手。
一、降低熔化温度降低熔化温度是减少铸造缺陷的另一个方法。
在铸造中,金属熔化温度的过高可能会导致一些问题,例如气孔、氧化、金属的分解和不均匀分布。
因此,选择一种低熔点的合金,或者添加具有良好稳定性的合金元素,可以有效地降低熔化温度,减少铸造缺陷的发生。
二、改善铸造工艺改善铸造工艺是减少铸造缺陷的重要方法之一。
在铸造过程中,要确保铸造设备的操作规范和设备的稳定性,以及对原材料、模具、涂料、冷却剂等进行检测和控制。
同时,在铸造过程中,应尽可能避免过度加热或冷却,并确保金属液体的均匀流动,以避免出现不均匀分布或过热的情况,从而减少铸造缺陷的发生。
三、质量检测和控制质量检测和控制是减少铸造缺陷的关键步骤之一。
在铸造完成后,应对铸件进行全面的检测和控制包括X射线检测、超声波检测、金相分析、硬度测试等。
通过这些检测和控制方法,可以及时发现铸造缺陷,及时采取措施进行修复或重新铸造,从而保证铸件的质量和稳定性。
四、培养专业人才铸造行业的专业人才对于减少铸造缺陷的重要性不言而喻。
铸造行业需要拥有一批专业的技术人员和工人,他们能够理解和掌握铸造技术的各个方面,并能够在实践中灵活应对各种情况。
因此,铸造企业应该加强人才培养和引进工作,提高行业整体素质,从而减少铸造缺陷的发生。
铸轧生产中产生的主要缺陷及消除方法
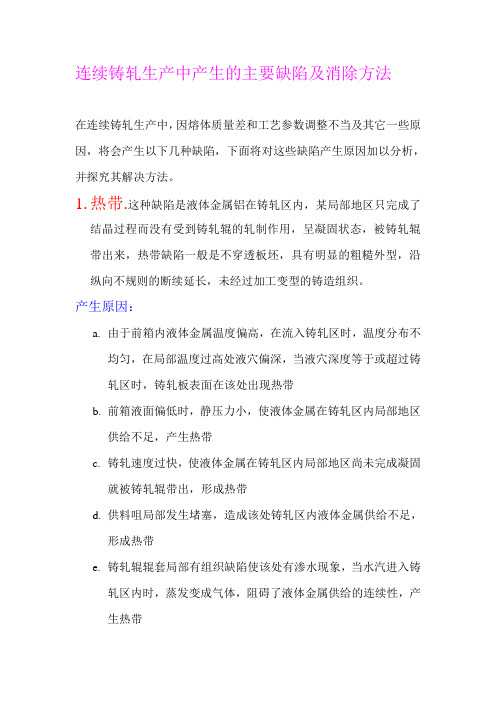
连续铸轧生产中产生的主要缺陷及消除方法在连续铸轧生产中,因熔体质量差和工艺参数调整不当及其它一些原因,将会产生以下几种缺陷,下面将对这些缺陷产生原因加以分析,并探究其解决方法。
1.热带.这种缺陷是液体金属铝在铸轧区内,某局部地区只完成了结晶过程而没有受到铸轧辊的轧制作用,呈凝固状态,被铸轧辊带出来,热带缺陷一般是不穿透板坯,具有明显的粗糙外型,沿纵向不规则的断续延长,未经过加工变型的铸造组织。
产生原因:a.由于前箱内液体金属温度偏高,在流入铸轧区时,温度分布不均匀,在局部温度过高处液穴偏深,当液穴深度等于或超过铸轧区时,铸轧板表面在该处出现热带b.前箱液面偏低时,静压力小,使液体金属在铸轧区内局部地区供给不足,产生热带c.铸轧速度过快,使液体金属在铸轧区内局部地区尚未完成凝固就被铸轧辊带出,形成热带d.供料咀局部发生堵塞,造成该处铸轧区内液体金属供给不足,形成热带e.铸轧辊辊套局部有组织缺陷使该处有渗水现象,当水汽进入铸轧区内时,蒸发变成气体,阻碍了液体金属供给的连续性,产生热带f.新铸轧辊在使用时,由于辊表面油汽残留,产生大量油气,油气进入铸轧区,产生的气体,阻碍液体金属供给的连续性,产生热带。
消除方法:要仔细地观察产生的热带的形貌,判断其产生的原因,针对其产生的原因调整相应的工艺参数,对前3个原因产生的热带,要降低铸轧速度,降低前箱液体金属温度,适当提高前箱液面高度,对第4个原因产生的热带,则要提高前箱液体金属温度,断板跑渣,并用薄钢条(或锯条)插入供料咀咀腔内将堵塞物处理掉,第5个原因产生的热带具有周期性,并始终出现在铸轧辊的同一位置上,这时只有停机换辊,重新立板生产。
2.裂纹(裂口)铸轧板表面的裂口呈月牙形,现场称之为“马蹄形裂口”,这种缺陷分布不规则,连续出现产生原因:产生裂口的主要原因就是在铸轧区内液体金属在进行铸造与轧制过程中,表面与中心线处的温差比较大,表面层温度低,不易变型,中心处温度高,容易变型,从铸造区进入变型区时,金属受轧制作用,表面金属与铸轧辊表面粘着,无滑动,板坯中心部分金属相对于表面金属发生向后滑动,这样由于变型流动的不均匀,致使在液穴的凝固壳外层受到来自不同方向拉应力的作用。
压铸件常见缺陷排除基本措施
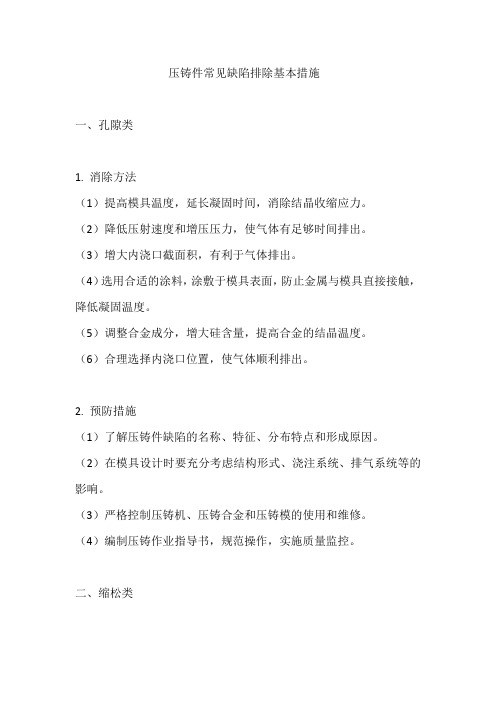
压铸件常见缺陷排除基本措施一、孔隙类1. 消除方法(1)提高模具温度,延长凝固时间,消除结晶收缩应力。
(2)降低压射速度和增压压力,使气体有足够时间排出。
(3)增大内浇口截面积,有利于气体排出。
(4)选用合适的涂料,涂敷于模具表面,防止金属与模具直接接触,降低凝固温度。
(5)调整合金成分,增大硅含量,提高合金的结晶温度。
(6)合理选择内浇口位置,使气体顺利排出。
2. 预防措施(1)了解压铸件缺陷的名称、特征、分布特点和形成原因。
(2)在模具设计时要充分考虑结构形式、浇注系统、排气系统等的影响。
(3)严格控制压铸机、压铸合金和压铸模的使用和维修。
(4)编制压铸作业指导书,规范操作,实施质量监控。
二、缩松类1. 消除方法(1)提高模具温度,促进合金液在压力作用下充型和补缩。
(2)降低压射速度和增压压力,延长补缩时间。
(3)采用高压力射流,减小浇道截面积,提高补缩效率。
(4)采用压铸件热处理工艺,实现局部补缩,消除缩松缺陷。
2. 预防措施(1)了解压铸件缺陷的特征、分布特点和形成原因。
(2)在模具设计时要充分考虑结构形式、浇注系统、排气系统等的影响。
(3)严格控制压铸机、压铸合金和压铸模的使用和维修。
(4)编制压铸作业指导书,规范操作,实施质量监控。
三、偏芯类1. 消除方法(1)调整内浇口位置和大小,改变浇注系统,使充型压力分布均匀。
(2)调整模具温度,减小零件内外温差,减弱热应力。
(3)采用定模或动模定置结构设计,确保定位精度和稳定成型。
(4)采用抽芯结构,减少抽芯受力不均的影响。
(5)在工艺上采取相应措施,如采用二级抽芯等,减小抽芯力。
2. 预防措施(1)了解压铸件缺陷的特征、分布特点和形成原因。
(2)在模具设计时要充分考虑结构形式、浇注系统、排气系统等的影响。
(3)严格控制压铸机、压铸合金和压铸模的使用和维修。
(4)编制压铸作业指导书,规范操作,实施质量监控。
四、裂纹类1. 消除方法(1)调整合金成分,提高收缩率,增强抗裂纹能力。
铸轧铝合金裂边缺陷产生原因及改进措施

铸轧铝合金裂边缺陷产生原因及改进措施1. 引言铸轧铝合金是一种广泛应用于航空、汽车、电子等领域的重要材料。
然而,在生产过程中,铸轧铝合金裂边缺陷的产生成为了一个严重的问题。
裂边缺陷不仅会影响产品的外观和质量,还可能导致零部件在使用过程中的性能损失甚至失效。
深入探讨铸轧铝合金裂边缺陷的产生原因及改进措施,对于提高产品质量和生产效率具有重要意义。
2. 裂边缺陷的产生原因2.1 材料原因铸轧铝合金裂边缺陷的产生与材料的性质有密切关系。
原材料的质量和纯度对铝合金的力学性能和成型性能具有重要影响。
杂质和氧化物的存在会导致合金中存在脆性相,从而增加裂边的产生概率。
合金的熔炼过程中,温度和冷却速率的控制不当也会导致合金组织不均匀,从而进一步增加裂边的发生。
2.2 工艺原因铸轧铝合金的生产过程涉及多个环节,如铸造、加热、轧制等。
在每个环节中,不当的工艺参数设置或操作方法可能会导致裂边缺陷的产生。
铸造过程中,浇注温度过高会导致合金存在大量气孔和夹杂物,增加裂边的概率。
加热过程中,温度梯度过大或保持时间不足,也会导致合金的形态不稳定,导致裂边的形成。
3. 改进措施3.1 优化材料选择在铝合金生产中,选择高质量、纯净度高的原材料是降低裂边缺陷的重要措施之一。
对原材料进行严格的质量检测和筛选,以确保合金中的杂质和氧化物含量尽可能低,并优化熔炼过程的温度和冷却速率,以提高合金的均匀性和稳定性。
3.2 优化工艺参数在各个工艺环节中,优化参数设置和改进操作方法是降低裂边缺陷的关键。
在铸造过程中,控制浇注温度、填充速度和冷却速率,提高铸造的质量稳定性;在加热过程中,控制温度梯度和保持时间,降低合金的形态不稳定性。
3.3 引入先进技术随着科学技术的不断进步,先进的制造技术也逐渐应用于铸轧铝合金的生产中。
利用激光熔化等先进的合金制备技术,可以使合金的组织更加均匀,减少裂边缺陷的发生。
利用先进的在线检测技术,可以及时监测裂边缺陷的发生,实现快速响应和纠正。
铸件生产时的缺陷介绍以及预防措施
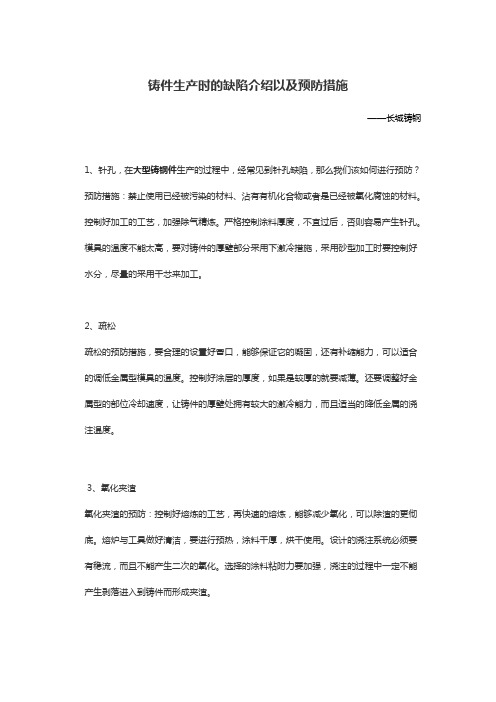
铸件生产时的缺陷介绍以及预防措施
——长城铸钢
1、针孔,在大型铸钢件生产的过程中,经常见到针孔缺陷,那么我们该如何进行预防?预防措施:禁止使用已经被污染的材料、沾有有机化合物或者是已经被氧化腐蚀的材料。
控制好加工的工艺,加强除气精炼。
严格控制涂料厚度,不宜过后,否则容易产生针孔。
模具的温度不能太高,要对铸件的厚壁部分采用下激冷措施,采用砂型加工时要控制好水分,尽量的采用干芯来加工。
2、疏松
疏松的预防措施,要合理的设置好冒口,能够保证它的凝固,还有补缩能力,可以适合的调低金属型模具的温度。
控制好涂层的厚度,如果是较厚的就要减薄。
还要调整好金属型的部位冷却速度,让铸件的厚壁处拥有较大的激冷能力,而且适当的降低金属的浇注温度。
3、氧化夹渣
氧化夹渣的预防:控制好熔炼的工艺,再快速的熔炼,能够减少氧化,可以除渣的更彻底。
熔炉与工具做好清洁,要进行预热,涂料干厚,烘干使用。
设计的浇注系统必须要有稳流,而且不能产生二次的氧化。
选择的涂料粘附力要加强,浇注的过程中一定不能产生剥落进入到铸件而形成夹渣。
铸件缺陷及解决方法
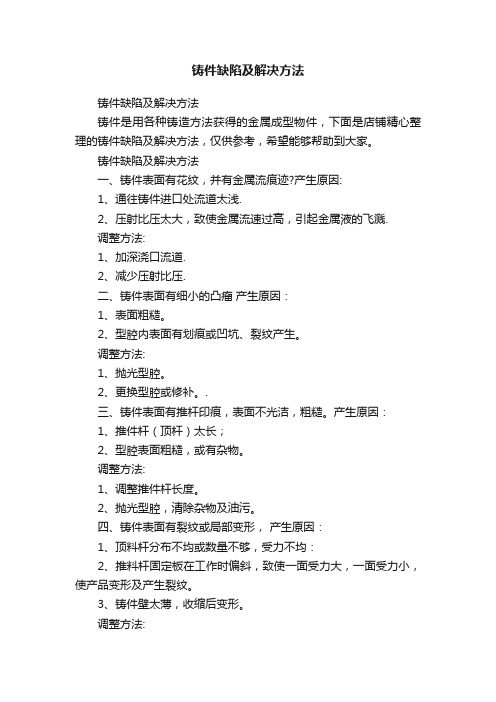
铸件缺陷及解决方法铸件缺陷及解决方法铸件是用各种铸造方法获得的金属成型物件,下面是店铺精心整理的铸件缺陷及解决方法,仅供参考,希望能够帮助到大家。
铸件缺陷及解决方法一、铸件表面有花纹,并有金属流痕迹?产生原因:1、通往铸件进口处流道太浅.2、压射比压太大,致使金属流速过高,引起金属液的飞溅.调整方法:1、加深浇口流道.2、减少压射比压.二、铸件表面有细小的凸瘤产生原因:1、表面粗糙。
2、型腔内表面有划痕或凹坑、裂纹产生。
调整方法:1、抛光型腔。
2、更换型腔或修补。
.三、铸件表面有推杆印痕,表面不光洁,粗糙。
产生原因:1、推件杆(顶杆)太长;2、型腔表面粗糙,或有杂物。
调整方法:1、调整推件杆长度。
2、抛光型腔,清除杂物及油污。
四、铸件表面有裂纹或局部变形,产生原因:1、顶料杆分布不均或数量不够,受力不均:2、推料杆固定板在工作时偏斜,致使一面受力大,一面受力小,使产品变形及产生裂纹。
3、铸件壁太薄,收缩后变形。
调整方法:1、增加顶料杆数量,调整其分布位置,使铸件顶出受力均衡。
2、调整及重新安装推杆固定板。
五、压铸件表面有气孔,产生原因:1、润滑剂太多。
2、排气孔被堵死,气孔排不出来。
调整方法:1、合理使用润滑剂。
2、增设及修复排气孔,使其排气通畅。
六、铸件表面有缩孔:产生原因:压铸件工艺性不合理,壁厚薄变化太大。
金属液温度太高。
调整方法:1、在壁厚的地方,增加工艺孔,使之薄厚均匀。
2、降低金属液温度。
七、铸件外轮廓不清晰,成不了形,局部欠料,产生原因:1、压铸机压力不够,压射比压太低。
2、进料口厚度太大;3、浇口位置不正确,使金属发生正面冲击。
调整方法:1、更换压铸比压大的压铸机;2、减小进料口流道厚度;3、改变浇口位置,防止对铸件正面冲击。
八、铸件部分未成形,型腔充不满,产生原因:1、压铸模温度太低;2、金属液温度低;3、压机压力太小,4、金属液不足,压射速度太高;5、空气排不出来。
调整方法:1、 2、提高压铸模,金属液温度;3、更换大压力压铸机。
干货:铸造五大缺陷及其解决对策

干货:铸造五大缺陷及其解决对策缺陷一:铸造缩孔主要原因有合金凝固收缩产生铸造缩孔和合金溶解时吸收了大量的空气中的氧气、氮气等,合金凝固时放出气体造成铸造缩孔。
解决的办法:1)放置储金球。
2)加粗铸道的直径或减短铸道的长度。
3)增加金属的用量。
4)采用下列方法,防止组织面向铸道方向出现凹陷。
a.在铸道的根部放置冷却道。
b.为防止已熔化的金属垂直撞击型腔,铸道应成弧形。
c.斜向放置铸道。
缺陷二:铸件表面粗糙不光洁缺陷型腔表面粗糙和熔化的金属与型腔表面产生了化学反应,主要体现出下列情况。
(华亨铸件,最专业的的双金属锤头铸造商)1)包埋料粒子粗,搅拌后不细腻。
2)包埋料固化后直接放入茂福炉中焙烧,水分过多。
3)焙烧的升温速度过快,型腔中的不同位置产生膨胀差,使型腔内面剥落。
4)焙烧的最高温度过高或焙烧时间过长,使型腔内面过于干燥等。
5)金属的熔化温度或铸圈的焙烧的温度过高,使金属与型腔产生反应,铸件表面烧粘了包埋料。
6)铸型的焙烧不充分,已熔化的金属铸入时,引起包埋料的分解,发生较多的气体,在铸件表面产生麻点。
7)熔化的金属铸入后,造成型腔中局部的温度过高,铸件表面产生局部的粗糙。
解决的办法:a.不要过度熔化金属。
b.铸型的焙烧温度不要过高。
c.铸型的焙烧温度不要过低(磷酸盐包埋料的焙烧温度为800度-900度)。
d.避免发生组织面向铸道方向出现凹陷的现象。
e.在蜡型上涂布防止烧粘的液体。
缺陷三:铸件发生龟裂缺陷有两大原因,一是通常因该处的金属凝固过快,产生铸造缺陷(接缝);二是因高温产生的龟裂。
1)对于金属凝固过快,产生的铸造接缝,可以通过控制铸入时间和凝固时间来解决。
铸入时间的相关因素:蜡型的形状、铸到的粗细数量、铸造压力(铸造机)。
包埋料的透气性。
凝固时间的相关因素:蜡型的形状。
铸圈的最高焙烧温度。
包埋料的类型。
金属的类型。
铸造的温度。
2)因高温产生的龟裂,与金属及包埋料的机械性能有关。
下列情况易产生龟裂:铸入温度高易产生龟裂;强度高的包埋料易产生龟裂;延伸性小的镍烙合金及钴烙合金易产生龟裂。
铸造常见的缺陷及解决办法

铸造常见的缺陷及解决办法铸造是一种常见的加工方法,用于制造大量金属和非金属产品。
然而,铸造过程中常常会出现一些缺陷,这些缺陷会影响铸件的质量和性能。
本文将介绍几种常见的铸造缺陷及解决办法。
气孔气孔是指在铸件内部或表面上出现的气泡。
这些气泡会影响铸件的强度和密封性能。
气孔的出现原因可能是铸造温度或压力不足,或是砂模中的水分蒸发不充分。
解决气孔的问题,需要改变铸造过程中的温度、压力或砂模中的水分含量。
另外,选择合适的金属合金也是避免气孔出现的重要因素,例如在铸造铝合金时,可以使用特殊的铝合金材料来降低气孔的出现。
毛刺毛刺是指在铸件表面上出现的细小凸起物。
这些毛刺会影响铸件的表面光滑度和密封性能。
毛刺的出现原因可能是砂模中的杂质、铸件表面的耗损或金属液体的流动不充分。
解决毛刺的问题,需要在铸造过程中施加足够的压力和控制金属液体的流动速度。
另外,使用高品质的砂模和特殊的涂料或添加剂也可以有效地减少毛刺的出现。
缩孔缩孔是指在铸件内部或表面上出现的缺陷。
这些缺陷会影响铸件的强度和密封性能。
缩孔的出现原因可能是铸造温度不足、金属合金不均匀、砂模中的气包或铸造中的氧化物等。
解决缩孔的问题需要改变铸造温度、金属合金中元素的成分、砂模的密度和金属液体中的氧化物含量。
此外,在铸造过程中添加特殊的合金和增量剂也可以有效地减少缩孔的出现。
内孔内孔是指在铸件内部出现的缺陷,这些缺陷会影响铸件的强度和密封性能。
内孔的出现原因可能是砂模泥中的气孔或金属液体中的气泡。
解决内孔的问题需要改变铸造过程中的气压和金属液体的流动速度。
此外,在铸造过程中添加特殊的漏铸剂和降泡剂也可以有效地减少内孔的出现。
总之,铸造过程中出现的缺陷会严重影响铸件的质量和性能。
通过改变铸造过程中的温度、压力和砂模的含水量,以及添加特殊的金属合金、涂料、合金和漏铸剂等,可以有效地减少这些缺陷的出现。
因此,在铸造过程中应该尽可能地避免出现这些问题,并采取合适的方法来解决这些问题。
常见铸造缺陷的成因与消除

常见铸造缺陷的成因与消除任何铸造缺陷都直接影响着企业的经济效益与社会效益。
可惜的是,未有一个铸造厂是没有铸造缺陷的。
现列出几种主要(常见)的铸造缺陷,如气孔,缩孔,夹渣及球化不良等来分析它们产生的原因并提出消除措施,与诸君共议。
一气孔(Gas hole)1、产生原因金属液中的气体未彻底释放出来和铸型内的气体侵入进金属液中,从而滞留在凝固后的铸件之内(图1)。
(1)金属液中的气体来源 g 劣质炉料含泥沙、油垢、锈蚀及湿气等,熔炼中生成大量的O、H、N等气体和渣釉;炉温低;精练不够;浇注温度低,浇注时间长及浇注速度慢、浇包潮湿等。
上述因素,都促使金属液表面过早形成氧化膜而凝固,气体虽然挣扎着向外逃逸但却无法实现。
反映在铸件上则成为向上的“梨形”气泡,梨把朝内。
气孔表面光滑。
通常称这种气孔为“析出性气孔”(图2)。
在薄壁件的表皮下或外观形成密集的小圆孔或针孔(图3)。
(2)型腔内气体来源砂型水分≥4.5%,死灰>12%,透气性差;水玻璃砂未干透(仅吹C O2是不够的);树脂砂的树脂量>1.8%,固化剂量也多;消失模厚大,比重大又未干透,涂料层>2㎜且未干透;粗大砂芯樁的过实,未中空,气体未引出型外;合箱后等待浇注时间>8h,或过夜等,使铸型和砂芯返潮。
(3)工艺设计不合理直浇道粗大,金属液不能很快充满或断流而将气体卷入;内浇口喷射,金属液紊乱;冒口处低位,排气孔少;底注,温度场为上低下高,导致金属液迅速形成氧化膜而快速凝固。
上述(2)、(3)所产生的气体在排气不畅且型内压力大的情况下,气体被卷入或钻入未凝固的金属液内。
通称这种气孔为“侵入性气孔”(图4)。
气孔也似梨状而梨把朝外。
2 消除方法消除金属液中可能产生气体的一切因素;提供气体从金属液内和铸型(砂芯)中容易逸出的机会或条件。
应当着重指出的是,彻底排出金属液中的气体是第一位的!具体做法:选用优质、干净干燥的炉料,提高熔炼温度(灰铁1520℃,铸钢1650℃,不锈钢1680℃),充分精炼脱气与静置,高温且快速浇注,消失模浇注温度比砂铸高50℃,因为泡沫燃烧是一个吸热过程,充型前沿的金属液温降比随后之金属液的温降大得多。
铸造缺陷及其解决方法
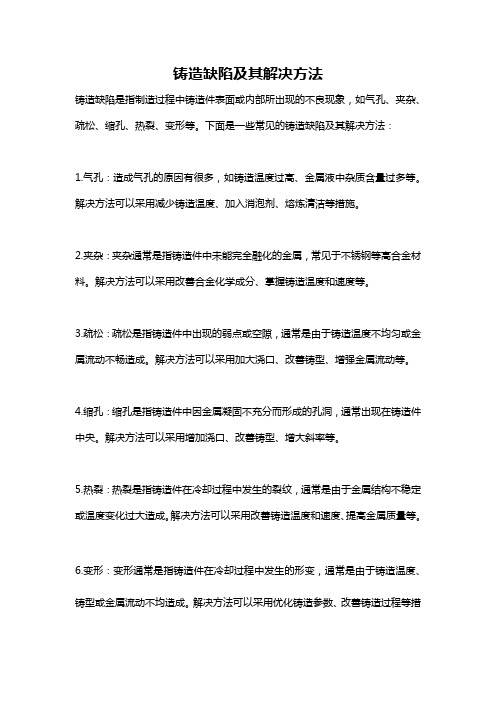
铸造缺陷及其解决方法
铸造缺陷是指制造过程中铸造件表面或内部所出现的不良现象,如气孔、夹杂、疏松、缩孔、热裂、变形等。
下面是一些常见的铸造缺陷及其解决方法:
1.气孔:造成气孔的原因有很多,如铸造温度过高、金属液中杂质含量过多等。
解决方法可以采用减少铸造温度、加入消泡剂、熔炼清洁等措施。
2.夹杂:夹杂通常是指铸造件中未能完全融化的金属,常见于不锈钢等高合金材料。
解决方法可以采用改善合金化学成分、掌握铸造温度和速度等。
3.疏松:疏松是指铸造件中出现的弱点或空隙,通常是由于铸造温度不均匀或金属流动不畅造成。
解决方法可以采用加大浇口、改善铸型、增强金属流动等。
4.缩孔:缩孔是指铸造件中因金属凝固不充分而形成的孔洞,通常出现在铸造件中央。
解决方法可以采用增加浇口、改善铸型、增大斜率等。
5.热裂:热裂是指铸造件在冷却过程中发生的裂纹,通常是由于金属结构不稳定或温度变化过大造成。
解决方法可以采用改善铸造温度和速度、提高金属质量等。
6.变形:变形通常是指铸造件在冷却过程中发生的形变,通常是由于铸造温度、铸型或金属流动不均造成。
解决方法可以采用优化铸造参数、改善铸造过程等措
施。
铸造工艺缺陷及解决措施
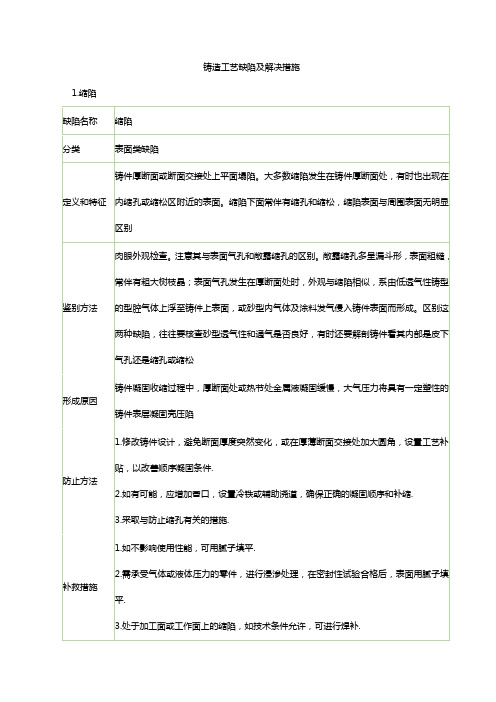
补救措施
概率因子
0.5
缺陷名称
跑火
分类
残缺类缺陷
定义和特征
鉴别方法
形成原因
金属液充型剧烈,易使型芯破裂造成跑火缺陷
防止方法
控制浇温,充型要平稳.
补救措施
概率因子
0.3
4.脉纹
缺陷名称
脉纹
分类
多肉类缺陷
定义和特征
鉴别方法
形成原因
硅砂在573℃发生相变膨胀,浇注时铸型表面易产生裂纹.
形成原因
铸件凝固收缩过程中,厚断面处或热节处金属液凝固缓慢,大气压力将具有一定塑性的铸件表层凝固壳压陷
防止方法
1.修改铸件设计,避免断面厚度突然变化,或在厚薄断面交接处加大圆角,设置工艺补贴,以改善顺序凝固条件.
2.如有可能,应增加冒口,设置冷铁或辅助浇道,确保正确的凝固顺序和补缩.
3.采取与防止缩孔有关的措施.
11.金属液中的氧化物和低熔点化合物与型砂发生造渣反应,生成硅酸亚铁、铁橄榄石等低熔点化合物,降低金属液表面张力并提高其流动性,使低熔点化合物和金属液通过毛细管作用机制,渗入砂粒间隙,并在渗透过程中,不断消蚀砂粒,使砂粒间隙扩大,导致机械粘砂或化学粘砂 12.浇注系统和冒口设置不当,造成铸型和铸件局部过热
3.降低浇包浇注高度.
4.浇注前检查是否漏放压铁或漏紧箱卡和紧箱螺栓.
5.造型时,上型应多扎通气孔并在适当部位设置数量足够的出气冒口.
补救措施
1.单件或小批生产的铸件,可采用打磨或切削加工等方法去掉多余金属.
2.大量生产时,抬型严重的铸件应报废
概率因子
8.型漏(漏箱)
缺陷名称
铸轧铝合金裂边缺陷产生原因及改进措施

《铸轧铝合金裂边缺陷产生原因及改进措施》1. 引言铸轧铝合金在工业生产中具有重要的应用价值,然而在生产过程中,裂边缺陷是较为常见的质量问题之一。
本文将从裂边缺陷产生的原因和可能的改进措施进行探讨,以期加深对这一问题的理解并改进生产工艺。
2. 原因分析2.1 温度控制不当铸轧铝合金在轧制过程中需要严格控制温度,若温度过高或过低都会导致晶界移动不畅,从而形成裂边缺陷。
2.2 润滑不足良好的润滑能够降低金属板材与轧辊之间的摩擦,减少表面缺陷的产生,然而润滑不足会导致裂痕的形成。
2.3 材质问题铸轧铝合金的材质不均匀或含有太多的杂质也会导致裂边缺陷的产生。
2.4 设备故障轧制设备的故障隐患会影响板材的表面质量,从而产生裂边缺陷。
3. 改进措施3.1 加强温度控制通过对轧制温度的严格控制和监测,确保在合适的温度范围内进行轧制,从而减少裂边缺陷的产生。
3.2 改善润滑条件完善润滑系统,保证每一块板材表面都获得均匀的润滑,降低摩擦,减少裂边缺陷的出现。
3.3 优化原材料选择优质的原料,并对原料进行严格的检测和筛选,排除掺杂和不均匀的材料,降低裂边缺陷的风险。
3.4 设备维护对轧制设备进行定期的维护和保养,消除故障隐患,保证设备的正常运行,减少裂边缺陷的产生。
4. 个人观点和理解作为铝合金轧制行业的从业者,我深知裂边缺陷给生产带来的质量和效益损失。
在实际工作中,我也发现了裂边缺陷的产生往往伴随着多种因素的综合作用,解决起来并不容易。
但只要我们采取科学的改进措施,严格把关每个环节,相信裂边缺陷问题是可以得到有效控制和改进的。
5. 总结与展望通过对铸轧铝合金裂边缺陷的原因和改进措施进行全面的分析和讨论,我们不仅更深入地了解了该问题的成因和解决方法,也为今后的生产实践提供了有益的启示。
相信在不久的将来,随着技术的不断升级和管理的不断完善,铸轧铝合金裂边缺陷将会逐步得到有效控制和解决,为行业的发展注入新的动力。
6. 参考文献- 张三, 张四.《铝合金轧制工艺》. 浙江大学出版社, 2005.- 李四, 王五.《钢铁轧制设备维护与故障诊断》. 机械工业出版社, 2010.结语:通过对铸轧铝合金裂边缺陷产生原因及改进措施的探讨,希望能够为相关行业提供一些有益的帮助,指导大家更好地避免和解决这一问题。
铸造缺陷总结汇报

铸造缺陷总结汇报铸造是一种常见的制造工艺,用于制造各种金属制品。
然而,在铸造过程中,常常会出现一些缺陷,这些缺陷会对产品的质量和性能产生不良影响。
因此,及时总结和汇报铸造缺陷是非常重要的,下面我们来详细讨论一下。
首先,铸造缺陷的种类非常多样。
常见的铸造缺陷主要包括气孔、夹杂物、缩孔、疏松、铸钢、铸锻件表面缺陷等。
这些缺陷的产生原因可以是多方面的,比如金属液内含的气体未能完全排出,金属液流动不畅导致夹杂物的进入,铸型砂中水分过多导致疏松缩敛等等。
其次,针对不同种类的铸造缺陷,需要采取相应的解决方法。
对于气孔和夹杂物来说,需要通过提高浇注温度和浇注速度来减少气体的溶解度和夹杂物的进入;对于缩孔和疏松来说,主要应采用合适的浇注系统和优化固化过程,以提高金属液的流动性和减少气体和夹杂物的进入。
至于铸钢和铸锻件表面的缺陷,则需要采用相应的表面处理方法,提高表面的光洁度和平整度。
此外,铸造缺陷的发生与操作人员的技术水平和操作规范密切相关。
因此,在铸造过程中,必须加强操作人员的培训和管理,提高他们的技能水平和操作规范,从而减少铸造缺陷的发生。
同时,还需要加强对原材料的检验和质量控制,以确保原材料的质量符合要求,减少缺陷的发生。
最后,为了及时发现和解决铸造缺陷,必须建立起完善的缺陷检测和处理体系。
在铸造过程中,需要定期对铸造产品进行检测,及时发现并处理缺陷。
对于已经发生的缺陷,需要采取相应的补救措施,以保证产品的质量和性能。
此外,还需要建立起缺陷统计和分析的机制,对不同缺陷的发生频率和原因进行统计和分析,以便进一步改进铸造工艺和提高产品质量。
综上所述,铸造缺陷的总结和汇报对于保证产品质量和提高铸造工艺至关重要。
只有及时总结和汇报铸造缺陷,才能不断改进铸造工艺,提高产品质量,推动企业的发展。
因此,我们应该重视铸造缺陷的问题,加强对其的研究和解决,为企业的可持续发展做出贡献。
铸造产生的缺陷及防止措施
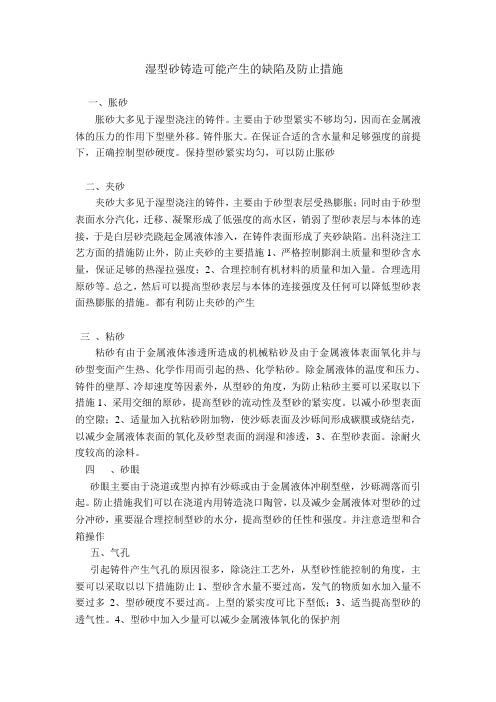
湿型砂铸造可能产生的缺陷及防止措施一、胀砂胀砂大多见于湿型浇注的铸件。
主要由于砂型紧实不够均匀,因而在金属液体的压力的作用下型壁外移。
铸件胀大。
在保证合适的含水量和足够强度的前提下,正确控制型砂硬度。
保持型砂紧实均匀,可以防止胀砂二、夹砂夹砂大多见于湿型浇注的铸件,主要由于砂型表层受热膨胀;同时由于砂型表面水分汽化,迁移、凝聚形成了低强度的高水区,销弱了型砂表层与本体的连接,于是白层砂壳跷起金属液体渗入,在铸件表面形成了夹砂缺陷。
出科浇注工艺方面的措施防止外,防止夹砂的主要措施1、严格控制膨润土质量和型砂含水量,保证足够的热湿拉强度;2、合理控制有机材料的质量和加入量。
合理选用原砂等。
总之,然后可以提高型砂表层与本体的连接强度及任何可以降低型砂表面热膨胀的措施。
都有利防止夹砂的产生三、粘砂粘砂有由于金属液体渗透所造成的机械粘砂及由于金属液体表面氧化并与砂型变面产生热、化学作用而引起的热、化学粘砂。
除金属液体的温度和压力、铸件的壁厚、冷却速度等因素外,从型砂的角度,为防止粘砂主要可以采取以下措施1、采用交细的原砂,提高型砂的流动性及型砂的紧实度。
以减小砂型表面的空隙;2、适量加入抗粘砂附加物,使沙砾表面及沙砾间形成碳膜或烧结壳,以减少金属液体表面的氧化及砂型表面的润湿和渗透,3、在型砂表面。
涂耐火度较高的涂料。
四、砂眼砂眼主要由于浇道或型内掉有沙砾或由于金属液体冲刷型壁,沙砾凋落而引起。
防止措施我们可以在浇道内用铸造浇口陶管,以及减少金属液体对型砂的过分冲砂,重要湿合理控制型砂的水分,提高型砂的任性和强度。
并注意造型和合箱操作五、气孔引起铸件产生气孔的原因很多,除浇注工艺外,从型砂性能控制的角度,主要可以采取以以下措施防止1、型砂含水量不要过高,发气的物质如水加入量不要过多2、型砂硬度不要过高。
上型的紧实度可比下型低;3、适当提高型砂的透气性。
4、型砂中加入少量可以减少金属液体氧化的保护剂六、裂纹铸件裂纹有很多形式,除了合金性质、浇注工艺和铸件表面结构的原因外,各种能够减少砂型膨胀。
铸造缺陷及防止方法

铸造缺陷及防止方法铸造是一种常用的金属加工工艺,可以将熔化的金属倒入铸型中,通过冷却凝固形成所需形状的金属制品。
然而,在铸造过程中,由于多种因素的影响,往往会导致一些缺陷出现在铸件上。
这些缺陷可能会降低铸件的质量和性能,因此有必要研究和防止铸造缺陷的发生。
一、常见的铸造缺陷类型1.气孔:气孔是铸造缺陷中最常见的一种,它是由金属液中残留的气体在凝固过程中形成的小空洞。
气孔会降低铸件的强度和密封性能,并且可能导致泄漏的发生。
2.夹杂物:夹杂物是指固体杂质或其他金属液滴等不溶于基体金属的颗粒物质。
夹杂物会引起局部应力集中和腐蚀等问题,从而降低铸件的耐蚀性和机械性能。
3.砂眼:砂眼是指铸件表面上的凹陷或孔洞,主要由于铸型中的砂粒脱落或重叠造成。
砂眼会影响铸件的外观和尺寸精度,降低其使用价值。
4.缩孔:缩孔是铸件内部或表面上的凹陷,它是由于金属凝固过程中产生的体积收缩引起的。
缩孔会降低铸件的强度和韧性,增加冲击和断裂的风险。
二、铸造缺陷的防止方法1.优化铸造工艺:通过合理设计铸造工艺参数,如浇注温度、浇注速度、浇注方式等,可以减少金属液中的气体吸收,并降低气孔和夹杂物的形成。
2.提高模具质量:优质的模具能够提供良好的液态金属充填条件,并且减少金属液和砂模接触引起的气体和杂质污染。
因此,选择高质量的模具材料和加工工艺非常重要。
3.合理选择铸造材料:根据铸件的要求选择适合的铸造材料,如选用低气性和低杂质含量的金属,可以减少铸造缺陷的发生。
4.加强铸造设备维护:定期检查和维护铸造设备,特别是容易产生污染和损坏的部件,可以减少外来杂质和缺陷的产生。
5.实施严格的质量控制和检验:建立科学的质量控制体系,制定详细的工艺规范和操作规程,严格按照要求进行检验和记录,及时发现和解决潜在的缺陷问题。
总结:铸造缺陷是铸件制造过程中经常面临的问题,但通过合理的措施和方法,可以有效地预防和减少铸造缺陷的发生。
优化铸造工艺、提高模具质量、合理选择铸造材料、加强设备维护以及实施严格的质量控制和检验,是有效预防铸造缺陷的关键。
- 1、下载文档前请自行甄别文档内容的完整性,平台不提供额外的编辑、内容补充、找答案等附加服务。
- 2、"仅部分预览"的文档,不可在线预览部分如存在完整性等问题,可反馈申请退款(可完整预览的文档不适用该条件!)。
- 3、如文档侵犯您的权益,请联系客服反馈,我们会尽快为您处理(人工客服工作时间:9:00-18:30)。
连续铸轧生产中产生的主要缺陷及消除方法
在连续铸轧生产中,因熔体质量差和工艺参数调整不当及其它一些原因,将会产生以下几种缺陷,下面将对这些缺陷产生原因加以分析,并探究其解决方法。
1.热带.这种缺陷是液体金属铝在铸轧区内,某局部地区只完成了
结晶过程而没有受到铸轧辊的轧制作用,呈凝固状态,被铸轧辊带出来,热带缺陷一般是不穿透板坯,具有明显的粗糙外型,沿纵向不规则的断续延长,未经过加工变型的铸造组织。
产生原因:
a.由于前箱内液体金属温度偏高,在流入铸轧区时,温度分布不
均匀,在局部温度过高处液穴偏深,当液穴深度等于或超过铸
轧区时,铸轧板表面在该处出现热带
b.前箱液面偏低时,静压力小,使液体金属在铸轧区内局部地区
供给不足,产生热带
c.铸轧速度过快,使液体金属在铸轧区内局部地区尚未完成凝固
就被铸轧辊带出,形成热带
d.供料咀局部发生堵塞,造成该处铸轧区内液体金属供给不足,
形成热带
e.铸轧辊辊套局部有组织缺陷使该处有渗水现象,当水汽进入铸
轧区内时,蒸发变成气体,阻碍了液体金属供给的连续性,产
生热带
f.新铸轧辊在使用时,由于辊表面油汽残留,产生大量油气,油
气进入铸轧区,产生的气体,阻碍液体金属供给的连续性,产
生热带。
消除方法:
要仔细地观察产生的热带的形貌,判断其产生的原因,针对其产生的原因调整相应的工艺参数,对前3个原因产生的热带,要降低铸轧速度,降低前箱液体金属温度,适当提高前箱液面高度,对第4个原因产生的热带,则要提高前箱液体金属温度,断板跑渣,并用薄钢条(或锯条)插入供料咀咀腔内将堵塞物处理掉,第5个原因产生的热带具有周期性,并始终出现在铸轧辊的同一位置上,这时只有停机换辊,重新立板生产。
2.裂纹(裂口)铸轧板表面的裂口呈月牙形,现场称之为“马
蹄形裂口”,这种缺陷分布不规则,连续出现
产生原因:
产生裂口的主要原因就是在铸轧区内液体金属在进行铸造与轧制过程中,表面与中心线处的温差比较大,表面层温度低,不易变型,中心处温度高,容易变型,从铸造区进入变型区时,金属受轧制作用,表面金属与铸轧辊表面粘着,无滑动,板坯中心部分金属相对于表面金属发生向后滑动,这样由于变型流动的不均匀,致使在液穴的凝固壳外层受到来自不同方向拉应力的作用。
在铸造区,当液穴较浅时,凝固层较坚厚,不易产生裂纹,而当液穴较深时,凝固层不紧固,当变型不均匀而产生的拉应力足够大时,在凝固层的薄弱处开裂进而扩
展形成裂口。
当液体金属过热,或液体金属在保温炉中停留时间长时,熔体内形核质点减少,在晶界处容易产生裂口,当铸轧速度较快或前箱温度较高,铸轧区较大,供料咀唇部破损,使液穴加深时,在铸轧板表面易产生裂口。
消除方法:
a.使用Al-Ti-B晶粒细化剂细化晶体组织,改善加工性能
b.在熔炼过程中,避免熔体过热
c.尽量缩短液体金属的停留保温时间
d.适当降低铸轧速度,降低前箱中液体金属温度
e.当供料咀损坏时,应及时更换供料咀
f.如果没有Al-Ti-B晶粒细化剂,在开始对供料咀时,要控制好铸轧
区,不宜过大
3.气道这种缺陷可以分为轻微和严重两种情况。
在铸轧板的横断
面上,轻微者出现微孔压合,不是连续结晶;严重者出现孔洞,气道是铸轧板生产板材﹑箔材危害较大的缺陷。
产生原因:
产生气道的主要原因是液体金属中氢含量过高,在结晶前沿,由于氢在固体铝中的溶解度很小,致使结晶前沿的液体金属中含氢量更高,此时如果晶粒粗大,树枝状晶发展形成补缩不好的空隙,或者其它夹杂物帮助氢气成核,液体金属中的氢便在此处析出成为氢气泡。
由于铸轧工艺是铸造和轧制相连续,受轧制作用,气体不易进入
到固体中去,在生产过程中,气泡不断接受结晶时排出的过饱和的氢气而逐渐长大,长大到一定时,过饱和氢便源源不断地析出形成气道。
消除方法:
a.加强精炼,降低铝水中氢含量,使其在0.15m l/100gAl以下
并使用Al-Ti-B晶粒细化剂细化晶粒
b.使用过滤装置,滤除铝液中的杂质,减少氢的核质点
c.切卷时跑渣放气
4.晶粒粗大晶粒粗大的铸轧板,其表面经过侵蚀即可见花纹
状组织,它严重影响板材的表面质量和内部质量
产生原因:
a.在熔炼和静止保温时,金属熔体温度过高
b.液体金属在炉内停留保温时间过长
c.铸轧辊冷却强度过低,冷却水温度偏高,冷却水压力偏小,冷
却水流量偏小
消除方法:
a.使用Al-Ti-B晶粒细化剂细化晶粒
b.在熔炼和静止保温过程中,防止熔体过热,并且尽量缩短液
体金属的保温时间,以保存熔体中大量的自发晶粒
c.提高冷却强度,使铸轧区中的晶粒尚未长大即完成凝固过程
5.粘辊
产生原因:
a.铸轧速度过快,前箱温度过高
b.冷却强度低(水压﹑水质﹑流量﹑辊套厚度)
c.热喷涂系统故障或火焰调整不当
d.铸轧辊局部堵塞
消除方法:
a.降低铸轧速度或前箱温度
b.提高冷却强度(增大冷却水流量和压力,降低冷却水温度)
c.保证烤辊系统正常工作,调整好火焰
d.清理铸轧辊内部冷却水通道,防止辊套内部局部堵塞。