HLMP-2899中文资料
HLMP-CM30-M00ZZ中文资料
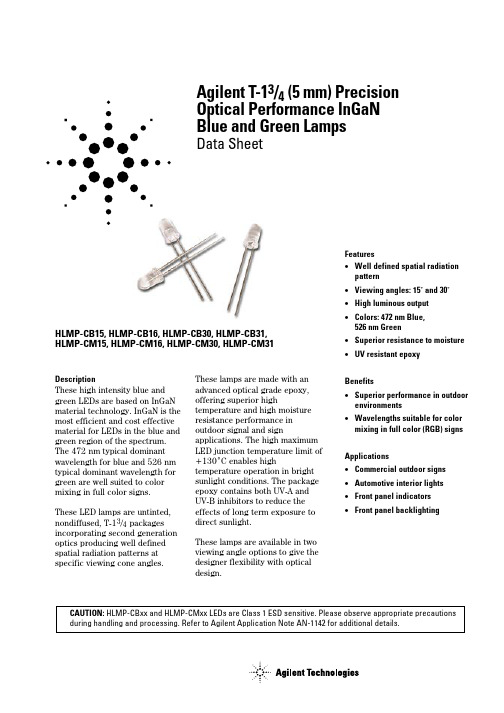
LED IndicatorsDevice Selection GuideColor andTypical Typ. Dominant Min. Luminous Typical ForwardViewing Wavelength Intensity, Iv Voltage Leads with Package Part Number Angleλd (nm)(mcd) at 20 mA(V) at 20 mA Stand-Offs Drawing HLMP-CB15-P00xx15°Blue 472880 3.8No A HLMP-CB15-R00xx15°Blue 4721500 3.5No A HLMP-CB15-QT0xx15°Blue 4721150 3.8No A HLMP-CB16-P00xx15°Blue 472880 3.8Yes B HLMP-CB16-QT0xx15°Blue 4721150 3.8Yes B HLMP-CB30-K00xx30°Blue 472310 3.8No A HLMP-CB30-KN0xx30°Blue 472310 3.8No A HLMP-CB30-M00xx30°Blue 472520 3.8No A HLMP-CB30-MQ0xx30°Blue 472520 3.8No A HLMP-CB30-NRGxx30°Blue 472680 3.8No A HLMP-CB31-M00xx30°Blue 472520 3.8Yes B HLMP-CB31-M0Gxx30°Blue 472520 3.8Yes B HLMP-CB31-NRGxx30°Blue 472680 3.8Yes B HLMP-CM15-S00xx15°Green 5261900 3.8No A HLMP-CM15-SV0xx15°Green 5261900 3.8No A HLMP-CM15-W00xx15°Green 5265500 3.5No A HLMP-CM15-VY0xx15°Green 5264200 3.8No A HLMP-CM16-S00xx15°Green 5261900 3.8Yes B HLMP-CM16-VY0xx15°Green 5264200 3.8Yes B HLMP-CM30-M00xx30°Green 526520 3.8No A HLMP-CM30-MQ0xx30°Green 526520 3.8No A HLMP-CM30-S00xx30°Green 5261900 3.5No A HLMP-CM30-TWAxx30°Green 5262500 3.8No A HLMP-CM31-M00xx30°Green 526520 3.8Yes B HLMP-CM31-TWAxx30°Green 5262500 3.8Yes BTolerance for intensity limit is ±15%.Part Numbering SystemHLMP - X X XX - X X X XXMechanical Options00: BulkDD: Ammo PackYY: Flexi bin, BulkZZ: Flexi bin, Ammo PackColor Bin Selection0: Full color rangeA: Color bin 1 & 2 onlyG: Color bin 2, 3 & 4 onlyMaximum Intensity Bin0: No maximum Iv bin limitOthers: Refer to Intensity Bin Limit TableMinimum Intensity BinRefer to Device Selection GuideViewing Angle and Standoff Options15: 15 degree without standoff16: 15 degree with standoff30: 30 degree without standoff31: 30 degree with standoffColorB: BlueM: GreenPackageC: T-1 3/4 (5 mm) round lampNotes:1. Dimensions in mm.2. Tolerance ±0.1 mm unless otherwise noted.5.80 ± 0.20 (0.039)HLMP-Cx15 and HLMP-Cx30Package Dimensions5.80 ± 0.20 (0.039)HLMP-Cx16 and HLMP-Cx31HLMP-Cx16HLMP-Cx31d = 12.60 ± 0.25 (0.496 ± 0.010) d = 12.22 ± 0.50 (0.481 ± 0.020)Absolute Maximum Ratings at T A = 25˚CParameter Blue and GreenDC Forward Current[1]30 mAPeak Pulsed Forward Current100 mAAverage Forward Current30 mAReverse Voltage (I R = 100 µA) 5 VPower Dissipation120 mWLED Junction Temperature130˚COperating Temperature Range–40˚C to +80˚CStorage Temperature Range–40˚C to +100˚CSoldering Temperature260˚C for 5 secondsNote:1.Derate linearly as shown in Figure 5 for temperatures above 50˚C.Electrical/Optical Characteristics at T A = 25˚CParameter Symbol Min.Typ.Max.Units Test Conditions Forward Voltage V F 3.5 4.0V I F = 20 mAReverse Voltage V R5I R = 100 µAPeak Wavelength Peak of Wavelength of Blue (λd = 472 nm)λpeak470nm Spectral Distribution Green (λd = 526 nm)524at I F = 20 mA Spectral Halfwidth Wavelength Width Blue (λd = 472 nm)∆λ1/235nm at Spectral Power Green (λd = 526 nm)47Point at I F = 20 mA Capacitance C43pF V F = 0, F = 1 MHz Luminous Efficacy Emitted Luminous Blue (λd = 472 nm)ηv75lm/W Power/Emitted Radiant Green (λd = 526 nm)520PowerThermal Resistance RΘJ-PIN240˚C/W LED Junction-to-Cathode LeadFigure 1. Relative intensity vs. wavelength.Figure 2. Forward current vs. forward voltage for devices with 3.5 V typical Vf.Figure 4. Relative luminous intensity vs.forward current.WAVELENGTH – nmR E L A T I V E I N T E N S I T Y1.0 0.9 0.8 0.7 0.6 0.5 0.4 0.3 0.2 0.100302515102.0 3.2520 2.82.4 3.6F O R W A R D C U R R E N TFORWARD VOLTAGE2.62.23.0 3.4 3.81.50.5I N T E N S I T Y N O R M A L I Z E D A T 20 m AI F – FORWARD CURRENT – mA 0515301.0102520Figure 5. Maximum forward current vs.ambient temperature.Figure 6. Spatial radiation pattern – 15˚ lamps.Figure 7. Spatial radiation pattern – 30˚ lamps.I F – F O R W A R D C U R R E N T – m AT A – AMBIENT TEMPERATURE – °C 40804035251510206010052030N O R M A L I Z E D I N T E N S I T Y1.00ANGULAR DISPLACEMENT – DEGREES0.80.60.2-300.41020-20-100300.90.70.50.30.1N O R M A L I Z E D I N T E N S I T Y1.0ANGULAR DISPLACEMENT – DEGREES 0.80.60.2-400.41020-20-10400.90.70.50.30.1-3030520550530D O M I N AN T W A V E L E N G T H – n mFORWARD CURRENT – mA540525535545Figure 8. Color vs. forward current.Figure 3. Forward current vs. forward voltage for devices with 3.8 V typical Vf.2.03.4V F – FORWARD VOLTAGE – V102530 I F – F O R W A R D C U R R E N T – m A4.251520 2.4 3.0 3.82.2 2.8 3.2 4.02.6 3.6Intensity Bin Limits Bin NameMin.Max.K 310400L 400520M 520680N 680880P 8801150Q 11501500R 15001900S 19002500T 25003200U 32004200V 42005500W 55007200X 72009300Y 930012000Z1200016000Tolerance for each intensity bin limit is ± 15%.Color Bin Limits (nm at 20 mA)Blue Color Range (nm)Bin ID Min.Max.1460.0464.02464.0468.03468.0472.04472.0476.05476.0480.0Tolerance for each bin limit is ± 0.5 nm.Green Color Range (nm)Bin ID Min.Max.1520.0524.02524.0528.03528.0532.04532.0536.05536.0540.0Tolerance for each bin limit is ± 0.5 nm.Note:1.All bin categories are established for classification of products. Products may not be available in all bin categories.Please contact your Agilent represen-tatives for further information./semiconductors For product information and a complete list of distributors, please go to our web site.For technical assistance call:Americas/Canada: +1 (800) 235-0312 or (916) 788-6763Europe: +49 (0) 6441 92460China: 10800 650 0017Hong Kong: (+65) 6271 2451India, Australia, New Zealand: (+65) 6271 2394 Japan: (+81 3) 3335-8152(Domestic/Interna-tional), or 0120-61-1280(Domestic Only) Korea: (+65) 6271 2194Malaysia, Singapore: (+65) 6271 2054 Taiwan: (+65) 6271 2654Data subject to change.Copyright © 2003 Agilent Technologies, Inc. Obsoletes 5988-8658ENAugust 1, 20035988-9962EN。
HLMP-K105-MM001资料

AgilentT-13/4 (5 mm), T-1 (3 mm),High Intensity, Double Heterojunction AlGaAs Red LED LampsData SheetHLMP-D101/D105, HLMP-K101/K105DescriptionThese solid state LED lamps utilize newly developed doubleheterojunction (DH) AlGaAs/GaAs material technology. This LED material has outstanding lightoutput efficiency over a wide rangeFeatures• Exceptional brightness • Wide viewing angle• Outstanding material efficiency • Low forward voltage • CMOS/MOS compatible • TTL compatible • Deep red colorApplications• Bright ambient lighting conditions • Moving message panels • Portable equipment • General useof drive currents. The color is deep red at the dominantwavelength of 637 nanometres.These lamps may be DC or pulse driven to achieve desired light output.Package DimensionsA B CSelection GuideLuminous IntensityIv (mcd) at 20 mA2θ1/2[1]Package Package Description Device HLMP-Min.Typ.Max.Degree Outline T-1 3/4 Red Tinted Diffused D10135.270.0–65AD101-J00xx35.270.0–65AD101-JK0xx35.270.0112.865AT-1 3/4 Red Untinted Non-diffused D105138.0240.0–24BD105-M00xx138.0240.0–24BD105-NO0xx200.0290.0580.024BT-1 Red Tinted Diffused K10122.045.0–60CK101-100xx22.045.0–60CK101-IJ0xx22.045.070.460CT-1 Red Untinted Non-diffused K10535.265.0–45CK105-J00xx35.265.0–45CK105-KL0xx56.4110.0180.445CNote:1. θ1/2 is the off axis angle from lamp centerline where the luminous intensity is 1/2 the on-axis value.Part Numbering SystemHLMP - x x xx - x x x xxMechanical Option00: Bulk01: Tape & Reel, Crimped Leads02: Tape & Reel, Straight LeadsA1: Right Angle Housing, Uneven Leads, T1A2: Right Angle Housing, Even Leads, T1B1: Right Angle Housing, Uneven Leads, T-1 3/4B2: Right Angle Housing, Even Leads, T-1 3/4DD, UQ: Ammo PackColor Bin Options0: Full Color Bin DistributionMaximum Iv Bin Options0: Open (no max. limit)Others: Please refer to the Iv Bin TableMinimum Iv Bin OptionsPlease refer to the Iv Bin TableLens Type01: Tinted, Diffused05: Untinted, NondiffusedColor Options1: AlGaAs RedPackage OptionsD: T-1 3/4K: T-1Absolute Maximum Ratings at T A = 25°CParameter ValuePeak Forward Current[1,2]300 mAAverage Forward Current[2]20 mADC Current[3]30 mAPower Dissipation87 mWReverse Voltage (I R = 100 µA) 5 VTransient Forward Current (10 µs Pulse)[4]500 mALED Junction Temperature110°COperating Temperature Range-20 to +100°C Storage Temperature Range-55 to +100°C Wave Soldering Temperature [1.59 mm (0.063 in.) from body]250°C for 3 seconds Lead Solder Dipping Temperature [1.59 mm (0.063 in.) from body]260°C for 5 seconds Notes:1.Maximum I PEAK at f = 1 kHz, DF = 6.7%.2.Refer to Figure 6 to establish pulsed operating conditions.3.Derate linearly as shown in Figure 5.4.The transient peak current is the maximum non-recurring peak current the device can withstand without damaging the LED die and wire bonds. It isnot recommended that the device be operated at peak currents beyond the Absolute Maximum Peak Forward Current.Electrical/Optical Characteristics at T A = 25°CSymbol Description Min.Typ.Max.Unit Test ConditionV F Forward Voltage 1.8 2.2V I F = 20 mAV R Reverse Breakdown Voltage 5.015.0V I R = 100 µAλp Peak Wavelength645nm Measurement at Peakλd Dominant Wavelength637nm Note 1∆λ1/2Spectral Line Halfwidth20nmτS Speed of Response30ns Exponential TimeConstant, e-t/T SC Capacitance30pF V F = 0, f = 1 MHzRθJ-PIN Thermal Resistance260[3]°C/W Junction to Cathode Lead210[4]290[5]ηV Luminous Efficacy80Im/W Note 2Notes:1.The dominant wavelength, λd, is derived from the CIE chromaticity diagram and represents the color of the device.2.The radiant intensity, I e, in watts per steradian, may be found from the equation I e = l V/ηV, where I V is the luminous intensity in candelas and ηV isluminous efficacy in lumens/watt.3.HLMP-D101.4.HLMP-D105.5.HLMP-K101/-K105.Figure 3. Relative luminous intensity vs. dc forward current.Figure 4. Relative efficiency vs. peak forward current.Figure 7. Relative luminous intensity vs. angular displacement. HLMP-D101.Figure 8. Relative luminous intensity vs. angular displacement. HLMP-K101.Intensity Bin LimitsIntensity Range (mcd)Color Bin Min.Max.Red I24.839.6J39.663.4K63.4101.5L101.5162.4M162.4234.6N234.6340.0O340.0540.0P540.0850.0Q850.01200.0R1200.01700.0S1700.02400.0T2400.03400.0U3400.04900.0V4900.07100.0W7100.010200.0X10200.014800.0Y14800.021400.0Z21400.030900.0Maximum tolerance for each bin limit is ± 18%.Mechanical Option MatrixMechanical Option Code Definition00Bulk Packaging, minimum increment 500 pcs/bag01Tape & Reel, crimped leads, minimum increment 1300 pcs (T-1 3/4)/1800 pcs (T-1) 02Tape & Reel, straight leads, minimum increment 1300 pcs (T-1 3/4)/1800 pcs (T-1) A1Right Angle Housing, uneven leads, minimum increment 500 pcs/bagA2Right Angle Housing, even leads, minimum increment 500 pcs/bagB1Right Angle Housing, uneven leads, minimum increment 500 pcs/bagB2Right Angle Housing, even leads, minimum increment 500 pcs/bagDD Ammo Pack, straight leads in 2K incrementUQ Ammo Pack, horizontal leads in 2K incrementNote:All categories are established for classification of products. Products may not be available in all categories. Please contact your local Agilent representative for further clarification/information./semiconductors For product information and a complete list of distributors, please go to our web site.For technical assistance call:Americas/Canada: +1 (800) 235-0312 or (916) 788-6763Europe: +49 (0) 6441 92460China: 10800 650 0017Hong Kong: (+65) 6756 2394India, Australia, New Zealand: (+65) 6755 1939 Japan: (+81 3) 3335-8152 (Domestic/Interna-tional), or 0120-61-1280 (Domestic Only) Korea: (+65) 6755 1989Singapore, Malaysia, Vietnam, Thailand, Philippines, Indonesia: (+65) 6755 2044 Taiwan: (+65) 6755 1843Data subject to change.Copyright © 2004 Agilent Technologies, Inc. Obsoletes 5968-1440ENovember 12, 20045988-2230EN。
Glenair高速八轴接触器产品说明书

®OCTAXIAL CONTACTSEthernet, SuperSpeed USB, HDMI, DisplayPort, SATAFEBRUARY 2018For Series 23 SuperNine ®, Series 80 Mighty Mouse, Series 28HiPer-D ®, Series 791, Series 792, ARINC 600 and EPXB Connectors®Glenair, Inc.1211 Air WayGlendale, CA 91201-2497818-247-6000*****************High-speed octaxial contacts for Ethernet, SuperSpeed USB and multi-gigabit datalinksHIGH-SPEED CONTACT TECHNOLOGYEl Ochito ® WhiteEl Ochito ® BlueEl Ochito ® Red10G Ethernet 1000BASE-T 10GBASE-TSuperSpeed USB 3.0HDMI SATA DisplayPortHigh speed, harsh environment El Ochito®octaxial contacts save size and weight. Suitable for aircraft avionics, weapons systems, satellites, radars,communications equipment and other aerospace/defense gear,El Ochito® contacts are optimized for 10G Ethernet, SuperSpeed USB and other multi-gigabit datalink protocols including HDMI, DisplayPort and SATA.El Ochito Type II Contacts24-26 AWG, Serviceable, Threaded Wire Shield Termination, Integral Contact Release Sleeve© 2018 Glenair, Inc • 1211 Air Way, Glendale, CA 91201 • 818-247-6000 • • U.S. CAGE code 06324 • El Ochito ® Octaxial ContactsDimensions in Inches (millimeters) are subject to change without notice.1000BASE-T, 10GBASE-TSuperSpeed USBHDMI, DisplayPort, SATAData Pair IsolatorData Pair IsolatorFront InsulatorFront InsulatorOuter BodyOuter BodyAlignment KeyAlignment KeyContact Organizer InsulatorContact Organizer InsulatorSocket ContactsPin Contacts SleeveDielectric SleeveType I Pin Contact Type I Socket ContactData Pair Isolator Data Pair IsolatorFront InsulatorFront InsulatorOuter BodyOuter BodyAlignment KeyAlignment KeyContact Release SleeveContact Release SleeveContact Organizer InsulatorContact Organizer InsulatorSocket ContactsPin ContactsRetainer NutRetainer NutO-ringO-ringHeatshrink TubeHeatshrink TubeInner FerruleInner FerruleType II Socket Contact10GBASE-T El Ochito®SuperSpeed USBSATAEl Ochito®Red859-134(GS206)© 2018 Glenair, Inc • 1211 Air Way, Glendale, CA 91201 • 818-247-6000 • • U.S. CAGE code 06324 • El Ochito®Octaxial Contacts© 2018 Glenair, Inc • 1211 Air Way, Glendale, CA 91201 • 818-247-6000 • • U.S. CAGE code 06324 • El Ochito ® Octaxial Contacts Dimensions in Inches (millimeters) are subject to change without notice.5DimensionsEl Ochito ® Type I Pin Contact 858-003, 858-016, 858-028, and 858-030.920(23.37) MAXØ .276/.271(7.01/6.88).060 (1.52).033/.029 (0.84/0.74).305/.295(7.75/7.49)858-003, 858-028-01: .231 (5.87) HEX858-016, 858-028-02, 858-030: .265 (6.73) ROUNDØ .316/.313(8.03/7.95)Ø .219/.217(5.56/5.51)POLARIZATIONKEYPIN NO. DESIGNATION (NOT MARKED ONPART)CABLE (REF)12345678 SHIELD CRIMP FERRULEEl Ochito ® Type II Pin Contact 858-0051.625 (41.28) MAX Ø .316/.313(8.03/7.95)Ø .219/.217(5.56/5.51)CABLE (REF)HEATSHRINKTUBING.033/.029 (0.84/0.74).305/.295(7.75/7.49).060 (1.52)POLARIZATIONKEYPIN NO. DESIGNATION (NOT MARKED ON PART)12345678.313 (7.95) FLATS.320 (8.13) HEXINTEGRAL RELEASE SLEEVESHIELDRETAINER NUTEl Ochito ® Type II Socket Contact 858-0061.950 (49.53) MAX Ø .316/.313(8.03/7.95)CABLE (REF)HEATSHRINKTUBING.033/.029 (0.84/0.74).060 (1.52)POLARIZATIONKEY PIN NO. DESIGNATION (NOT MARKED ON PART)12345678.320 (8.13) HEXINTEGRAL RELEASE SLEEVE.313 (7.95) FLATSØ .288/.284(7.32/7.21).631/.625 (16.02/15.88)SHIELDRETAINER NUTEl Ochito ® Type I Socket Contact 858-004, 858-017, 858-029, and 858-031.770(19.56)MAX .033/.029(0.84/0.74).631/.625(16.02/15.88)POLARIZATIONKEYØ .288/.284(7.32/7.21)Ø .316/.313(8.03/7.95)Ø .276/.271(7.01/6.88)SHIELD CRIMP FERRULE 858-004, 858-029-01: .231 (5.87) HEX858-017, 858-029-02, 858-031: .265 (6.73) ROUNDCABLE (REF).060 (1.52)PIN NO. DESIGNATION (NOT MARKED ONPART)12345678®Octaxial Contacts6© 2018 Glenair, Inc • 1211 Air Way, Glendale, CA 91201 • 818-247-6000 • • U.S. CAGE code 06324 • El Ochito ® Octaxial ContactsDimensions in Inches (millimeters) are subject to change without notice.El Ochito ® Pin Contact 858-009 for ARINC 600 Connectors.515/.505(13.08/12.83)POLARIZATIONKEY.90(22.9) MAX.033/.029 (0.84/0.74)Ø .316/.313(8.03/7.95)Ø .219/.217(5.56/5.51)Ø .276/.271(7.01/6.88).075/.073(1.91/1.85)SHIELD CRIMP858-009-01F: .231 (5.87) HEX 858-009-02F: .265 (6.73) ROUNDPIN NO. DESIGNATION (NOT MARKED ONPART)12345678DimensionsEl Ochito ® Socket Contact 858-010 for ARINC 600 ConnectorsØ .276/.271(7.01/6.88)CABLE (REF).90(22.9)MAX .033/.029(0.84/0.74).600/.590 (15.24/15.00)SHIELD CRIMP858-010-01F: .231 (5.87) HEX 858-010-02F: .265 (6.73) ROUNDPOLARIZATIONKEYØ .288/.284(7.32/7.21)Ø .316/.313(8.03/7.95)PIN NO. DESIGNATION (NOT MARKED ONPART)12345678.075/.073(1.91/1.85)El Ochito ® Pin Contact 858-014 for EN4644 EPXB Connectors.760(19.30) MAXØ .276/.273(7.01/6.93).075/.073(1.91/1.85).033/.029 (0.84/0.74).053/.043 (1.35/1.09).515/.505 (13.08/12.83)SHIELD CRIMP .231 (5.87) HEXØ .316/.313(8.03/7.95)Ø .219/.217(5.56/5.51)POLARIZATIONKEYPIN NO. DESIGNATION (NOT MARKED ONPART)CABLE (REF)12345678El Ochito ® Socket Contact 858-015 for EN4644 EPXB ConnectorsØ .276/.273(7.01/6.53)CABLE (REF).620(15.75)MAX .033/.029(0.84/0.74).600/.590 (15.24/15.00).034/.020 (0.86/0.51)SHIELD CRIMP .231 (5.87) HEXPOLARIZATIONKEYØ .288/.284(7.32/7.21)Ø .316/.313(8.03/7.95)PIN NO. DESIGNATION (NOT MARKED ONPART)12345678.075/.073(1.91/1.85)El Ochito ® Socket Contact 858-032 for Series 791 and 792 Connectors.975 (24.77) MAX.289/.279 (7.34/7.09)POLARIZATIONKEYØ .288/.284(7.32/7.21)Ø .316/.313(8.03/7.95)Ø .276/.271(7.01/6.88) SHIELD CRIMP858-032-01: .231 (5.87) HEX 858-032-02: .265 (6.73) ROUNDCABLE (REF).060 (1.52)PIN NO. DESIGNATION (NOT MARKED ONPART)12345678®Octaxial Contacts© 2018 Glenair, Inc • 1211 Air Way, Glendale, CA 91201 • 818-247-6000 • • U.S. CAGE code 06324 • El Ochito ® Octaxial ContactsDimensions in Inches (millimeters) are subject to change without notice.724 AWG S/UTP Cat 6A CableGlenair Part Number 963-037-24Manufacturer Part Number E6A3824ManufacturerPICS/UTP 24 AWG cable is specially designed for airborne 10 Gigabit Ethernet applications. Twisted pairs are separated by a fluoropolymer spline for reduced crosstalk and attenuation. This 200°C rated cable is Skydrol resistant, RoHS compliant and meets FAA FAR Parts 23 and 25 Appendix F flammability requirements. Laser-markable white PTFE jacket withstands abrasion and chemicals. Meets ANSI/TIA-568-C.2 Category 6A performance up to 246 feet.Construction DetailsCONDUCTOR24 AWG 19X36 SILVER PLATED COPPERFOUR TWISTED PAIRSPFA WIRE INSULATIONPTFE TAPE FLUOROPOLYMER SPLINE SILVER-PLATED COPPER BRAID90% MIN. COVERAGEFOIL SHIELD100% COVERAGEJACKETPTFE WHITE LASER-MARKABLE 0.26 (6.6) NOMINALColor CodePair #1 Blue, White/Blue · Pair #2 Orange, White/Orange · Pair #3 Green, White/Green · Pair #4 Brown, White/BrownSpecificationsImpedance (ohms)100Temperature Rating -55 to +200°CWeight (lbs/100 ft.) 4.6 Capacitance (pF/ft)14.5Minimum Bend Radius (inches).78Velocity of Propagation %70Dielectric Voltage Rating (kV rms) 1.5DC Resistance, Max (ohms/1000 ft.)28.5Max Distance in Feet (m)246 (75)Attenuation Nom / MaxFrequency dB/100 ft.10 MHz2.3 / 2.6100 MHz 7.0 / 8.4250 MHz 11.4/ 13.7500 MHz16.5 / 20.024 AWG S/FTP Cat 6A CableGlenair Part Number 963-033-24Manufacturer Part Number RCN9034-24ManufacturerGoreS/FTP 24 AWG cable has an individual foil shield around each data pair for reduced crosstalk and attenuation. This high data rate Ethernet cable features a unique cable jacket material and high-density construction that significantly reduces weight and diameter. Meets ANSI/TIA 568-C.2 Category 6A requirements up to 80 meters (262 feet). Qualified to SAE AS6070/5-24.Construction DetailsCONDUCTOR24 AWG 19X36 SILVER PLATED COPPER ALLOYWIRE INSULATION ePTFE / PTFE .060 (1.52)OVERALL SHIELDAWG 40 SILVER-PLATED COPPER 92% MIN COVERAGEPAIR SHIELDALUMINIZED POLYAMIDE (ALUMINUM OUT)FILLERFEP/ePTFE .060 (1.52) DIA.JACKETENGINEERED FLUOROPOLYMER EF100WHITE LASER-MARKABLE 0.004 (0.10) WALL 0.260 (6.60) MAX DIAMETERColor CodePair #1 Blue, White/Blue · Pair #2 Orange, White/Orange · Pair #3 Green, White/Green · Pair #4 Brown, White/BrownSpecificationsImpedance (ohms)100 (+10 -5)Temperature Rating -65 to +200°CWeight (lbs/100 ft.) 4.1 Capacitance (pF/ft)12.5Time Delay1.24 ns/ftMaximum Attenuation at 80m LengthFrequency dB 10 MHz 5.9100 MHz 19.1250 MHz 31.1500 MHz 45.3NEXT (minimum)Frequency dB 1 MHz 74.310 MHz 59.2100 MHz 52.3250 MHz 47.9500 MHz 42.224 AWG Category 6A Ethernet Cables 963-037 and 963-033®Octaxial Contacts8© 2018 Glenair, Inc • 1211 Air Way, Glendale, CA 91201 • 818-247-6000 • • U.S. CAGE code 06324 • El Ochito ® Octaxial ContactsDimensions in Inches (millimeters) are subject to change without notice.26 AWG S/UTP Cat 6A CableGlenair Part Number963-003-26Manufacturer Part Number E6A3826Manufacturer PICS/UTP 26 AWG cable is small, lightweight and flexible. Twisted pairs are separated by a fluoropolymer spline for reduced crosstalk and attenuation. This 200°C rated cable is Skydrol resistant, RoHS compliant and meets FAA FAR Parts 23 and 25 Appendix F flammability requirements. Rugged, laser-markable PTFE jacket withstands abrasion and chemicals. Meets ANSI/TIA-568-C.2 Category 6A performance up to 193 feet.Construction DetailsCONDUCTOR26 AWG 19X38 SILVER PLATED HIGH STRENGTH COPPER ALLOYFOUR TWISTED PAIRSPFA WIRE INSULATIONFLUOROPOLYMER TAPE SPLINEFLUOROPOLYMERSILVER-PLATED COPPER BRAID80% MIN. COVERAGEJACKETPTFE WHITE LASER-MARKABLE 0.22 (5.59)Color CodePair #1 Blue, White/Blue · Pair #2 Orange, White/Orange · Pair #3 Green, White/Green · Pair #4 Brown, White/BrownSpecificationsImpedance (ohms)100Temperature Rating -55 to +200°CWeight (lbs/100 ft.) 3.5 Capacitance (pF/ft)14.5Minimum Bend Radius (inches)0.66Velocity of Propagation %70Dielectric Voltage Rating (kV rms) 1.5DC Resistance, Max (ohms/1000 ft.)44.8Max Distance in Feet (m)193 (59)Attenuation Nom / MaxFrequency dB/100 ft.10 MHz2.7 /3.1100 MHz 8.7 / 10.5250 MHz 14.4 / 17.2500 MHz20.7 / 24.926 AWG S/FTP Cat 6A CableGlenair Part Number963-033-26Manufacturer Part Number RCN9047-26Manufacturer GoreS/FTP 26 AWG cable has an individual foil shield around each data pair for reduced crosstalk and attenuation. This high data rate Ethernet cable features a unique cable jacket material and high-density construction that significantly reduces weight and diameter. Meets ANSI/TIA 568-C.2 Category 6A requirements up to 65 meters (213 feet). Qualified to SAE AS6070/6-6.Construction DetailsCONDUCTOR26 AWG 19X38 SILVER PLATED HIGH STRENGTH COPPER ALLOYWIRE INSULATION ePTFE / PTFE .050 (1.27)OVERALL SHIELDAWG 40 SILVER-PLATED COPPER 92% MIN COVERAGEPAIR SHIELDALUMINIZED POLYAMIDE (ALUMINUM OUT)FILLERePTFEJACKETENGINEERED FLUOROPOLYMER EF100WHITE LASER-MARKABLE 0.004 (0.10) WALL 0.220 (5.59) MAX DIAMETERColor CodePair #1 Blue, White/Blue · Pair #2 Orange, White/Orange · Pair #3 Green, White/Green · Pair #4 Brown, White/BrownSpecificationsImpedance (ohms)100 (+10 -5)Temperature Rating -65 to +200°CWeight (lbs/100 ft.) 3.2 Capacitance (pF/ft)12.5Time Delay1.24 ns/ftMaximum Attenuation at 65m LengthFrequency dB 10 MHz 5.9100 MHz 19.1250 MHz 31.1500 MHz 45.3NEXT (minimum)Frequency dB 1 MHz 74.310 MHz 59.2100 MHz 52.3250 MHz 47.9500 MHz 42.226 AWG Category 6A Ethernet Cables 963-003 and 963-033© 2018 Glenair, Inc • 1211 Air Way, Glendale, CA 91201 • 818-247-6000 • • U.S. CAGE code 06324 • El Ochito ® Octaxial Contacts Dimensions in Inches (millimeters) are subject to change without notice.926 AWG S/FTP Cat 6A CableGlenair Part Number963-050Manufacturer Part Number RCN8966-26Manufacturer Gore963-050 is similar to 963-033-26 except with two layer wire insulation compatible with insulation displacement Ethernet connectors. An individual foil shield around each data pair provides reduced crosstalk and attenuation. Meets ANSI/TIA 568-C.2 Category 6A requirements up to 65 meters (213 feet).Construction DetailsCONDUCTOR26 AWG 19X38 SILVER PLATED HIGH STRENGTH COPPER ALLOYWIRE INSULATION ePTFE OVER PTFE .050 (1.27) MAX OVERALL SHIELDAWG 40 SILVER-PLATED COPPER 92% MIN COVERAGEPAIR SHIELDALUMINIZED KAPTON (ALUMINUM OUT)FILLERFEP / ePTFEJACKETENGINEERED FLUOROPOLYMER EF100WHITE LASER-MARKABLE 0.003 (0.08) WALL 0.230 (5.84) MAX DIAMETERColor CodePair #1 Blue, White/Blue · Pair #2 Orange, White/Orange · Pair #3 Green, White/Green · Pair #4 Brown, White/BrownSpecificationsImpedance (ohms)100 (+10 -5)Temperature Rating -55 to +200 °CWeight (lbs/100 ft.) 3.5 Operating Voltage150 VrmsMaximum Attenuation at 65mLengthFrequency dB 10 MHz 5.9100 MHz 19.1250 MHz 31.1500 MHz 45.3NEXT (minimum)Frequency dB 1 MHz 74.310 MHz 59.2100 MHz 52.3250 MHz 47.9500 MHz 42.226 AWG Category 6A Ethernet Cable 963-05010© 2018 Glenair, Inc • 1211 Air Way, Glendale, CA 91201 • 818-247-6000 • • U.S. CAGE code 06324 • El Ochito ® Octaxial ContactsDimensions in Inches (millimeters) are subject to change without notice.SuperSpeed USB CableGlenair Part Number 963-04790 ohm aerospace-grade cable features abrasion-resistant polyurethane jacket and #24 AWG wires for USB power. SuperSpeed data pairs feature low dielectric constant closed cell foam insulation. Each SuperSpeed pair has an aluminized polyester shield.Construction DetailsSUPERSPEED PAIRS90 OHM SHIELDED TWISTEDCONDUCTORS - 26 AWG 19X38 SILVER PLATED COPPERINSULATION - LOW LOSS FOAMED DIELECTRIC INSULATION .041 (1.04)DRAIN - 28 AWG 19X40 SILVER PLATED COPPERSHIELD - AL/POLYESTER,100% COVERAGE, FOIL SIDE INOVERALL SHIELD AWG 40 SILVER-PLATED COPPER 90% MIN COVERAGE POWER PAIRAWG 24 SILVER-PLATED COPPER FEP INSULATION RED/BLACKUTP SIGNAL PAIR90 OHM UNSHIELDED TWISTED 26 AWG 19X38 SILVER PLATEDCOPPER, FEP INSULATION, .037 (0.94)JACKETBLACK POLYURETHANE .237 (6.02)Color CodeSuperSpeed pairs VIO/ORN and BLU/YEL · Power wires RED, BLK · Low speed pair WHT/GRN.SpecificationsImpedance (ohms) High speed pairs Low-speed pair 90 ± 590 ±10Temperature Rating-30 to +105°CVoltage Rating (DWV Vac)300Frequency (GHz)IL (dB/m)NEXT (dB)1.25 1.874.62.5 2.667.75.0 4.053.17.55.753.5High Temperature SuperSpeed USB CableGlenair Part Number 963-110High performance, high temperature cable delivers dependable signal integrity over longer cable lengths. Fluoropolymer jacket can be laser-marked. Low-skew SuperSpeed data pairs have individual braid shields.Construction DetailsSUPERSPEED PAIRS90 OHM SHIELDED TWISTEDCONDUCTORS - 26 AWG 19X38 SILVER PLATED COPPERINSULATION - PTFE OVER ePTFE BINDER - WHITE ePTFEDRAIN - 28 AWG 19X40 SILVER PLATED COPPERSHIELD - 40 AWG SILVER PLATED COPPER BRAIDJACKET - FLUOROPOLYMER, WHITEOUTER SHIELD BINDER - ePTFE UNDER AND OVERAWG 40 SILVER-PLATED COPPER BRAIDPOWER PAIRAWG 24 19/36 SILVER-PLATED COPPER FLUOROPLASTIC INSULATION RED/BLACK TWISTEDUTP SIGNAL PAIR90 OHM UNSHIELDED TWISTED26 AWG 19X38 SILVER PLATED COPPER, FLUOROPLASTIC INSULATIONJACKETFLUOROPOLYMER, NATURAL OVER FLUOROPOLYMER, WHITELASER-MARKABLE .228/.244 (5.8/6.2) DIA.Color CodeSuperSpeed pairs VIO/ORN and BLU/YEL · Power wires RED, BLK · Low speed pair WHT/GRN.SpecificationsImpedance (ohms)90 ± 5Temperature Rating -65 to +200°C Voltage Rating< 50 Vac Dielectric Withstanding Voltage 100 Vac rms Weight57 g/m nominal Attenuation (S0021)Freq. (GHz)dB/m max..625 1.21.25 1.72.5 2.55.0 3.97.5 5.0SuperSpeed USB Cables 963-047 and 963-110© 2018 Glenair, Inc • 1211 Air Way, Glendale, CA 91201 • 818-247-6000 • • U.S. CAGE code 06324 • El Ochito ® Octaxial ContactsDimensions in Inches (millimeters) are subject to change without notice.NEXT (dB)MHz 0250500ACR-F (dB)MHz 0250500ACR-N (dB)MHz 0250500NEXT (dB)MHz 0204060801000250MHz0250500ACR-F (dB)MHz 0204060801000250ACR-F @ Remote (dB)MHz250500ACR-N (dB)MHz -40040800250ACR-N @ Remote (dB)MHz250500Insertion Loss (dB)MHz 0250500ACR-N @ Remote (dB)MHz250500RL @ Remote (dB)MHz 0250500ACR-N (dB)MHz250500ACR-N @ Remote (dB)MHz250500RL (dB)MHz 1000250500RL @ Remote (dB)MHz 250500* Measurement is within the accuracy limits of the instrument.FLUKE DSX-5000MAINFLUKE DSX-5000REMOTE© 2018 Glenair, Inc • 1211 Air Way, Glendale, CA 91201 • 818-247-6000 • • U.S. CAGE code 06324 • El Ochito ® Octaxial ContactsDimensions in Inches (millimeters) are subject to change without notice.SuperSpeed Pair 1USB 3.1 Gen 1 Upper Limit USB 3.1 Gen 1 Lower LimitSuperSpeed Pair 240050060070080090010001100120013001400Time (ps)Test BoardPC Tail Mated Contacts Crimp Area Cable0.3m 1.5m 1.8m USB 3.1 Gen 1 Limit2468Frequency (GHz)NEXT (SuperSpeed Pairs)El Ochito Blue Cable Assembly0-100-20-30-40-50-60-70-800.3m SS10.3m SS21.5m SS11.5m SS21.8m SS11.8m SS2USB 3.1 Gen 1 Limit2468Frequency (GHz)2 mated contacts}2 mated contacts}3 mated contacts }2468Frequency (GHz)NEXT (SuperSpeed to D+/D-)El Ochito ® Blue Cable Assembly0-100-20-30-40-50-60-70-80S (d B )0.3m 1.5m 1.8m USB 3.1 Gen 1 Limit2468Frequency (GHz)FEXT (SuperSpeed to D+/D-)El Ochito ® Blue Cable Assembly0-100-20-30-40-50-60-70-800.3m 1.5m 1.8m USB 3.1 Gen 1 Limit2468Frequency (GHz)Mode Conversion (SCD21)El Ochito ® Blue Cable Assembly-10-20-30-40-50-60-70-80B )0.3m SS10.3m SS21.5m SS11.5m SS2USB 3.1 Gen 1 Limit 1.8m SS11.8m SS2El Ochito® Blue for SuperSpeed USB, pin contact mating faceContact PositionsEl Ochito® Blue for SuperSpeed USB, pin contact mating faceContact Positions®Octaxial ContactsEl Ochito ® Blue-to-SuperSpeed USB Cable Assemblies 8572-0003Wiring Diagram 8572-0003-01El Ochito ® Pin to USB 3.0 A PlugWiring Diagram 8572-0003-04El Ochito ® Socket toUSB 3.0 Micro-B PlugWiring Diagram 8572-0003-02El Ochito ® Socket to USB 3.0 A RecepWiring Diagram 8572-0003-03El Ochito ® Socket to USB 3.0 B Plug8572-0003-01-(XX)OCHITO PIN CONTACT USB 3.0TYPE A PLUG876544321WHT GRN YEL BLU BLK REDVIO DRAIN WIRESORNGND23951768VBUS D-D+GND RX-RX+GND TX-TX+8572-0003-02-(XX)OCHITO SOCKET CONTACT USB 3.0TYPE A RECEP876544321WHT GRN YEL BLU BLK REDVIO DRAIN WIRESORNGND23951768VBUS D-D+GND RX-RX+GND TX-TX+8572-0003-03-(XX)OCHITO SOCKET CONTACT USB 3.0TYPE B PLUG876544321WHT GRN YEL BLU BLK REDVIO DRAIN WIRESORNGND23951768VBUS D-D+GND RX-RX+GND TX-TX+8572-0003-04-(XX)OCHITO SOCKET CONTACT USB 3.0MICRO-B PLUG876545321WHT GRN YEL BLU BLK REDVIO DRAIN WIRESORNGND231061879VBUS D-D+GND RX-RX+GND TX-TX+Plug Adapter Receptacle Adapter®Octaxial ContactsOverall Length Part Number Inches meters 180.45858-020-A-02-18360.91858-020-A-02-3672 1.82858-020-A-02-72120 3.05858-020-A-02-120859-117P Pin AdapterShell SizeA Diameter 1.200 (30.5) MAXØ AHBCDFEGAAGFEDCB HIn.mm.09 (A).65016.511 (B).78019.817 (E) 1.20330.619 (F) 1.26532.121 (G) 1.39035.323 (H) 1.52038.625 (J)1.63541.5859-132P Pin AdapterShell SizeA Diameter 1.200 (30.5) MAX Ø AAG FEDC B HIn.mm.09 (A).71018.011 (B).85021.617 (E) 1.27132.319 (F) 1.33333.921 (G) 1.46037.123 (H) 1.58540.325 (J)1.71143.5859-118S Socket AdapterShell SizeA Diameter 1.200 (30.5) MAXØ AH B D FEG AIn.mm.09 (A).71018.011 (B).85021.617 (E) 1.27132.319 (F) 1.33333.921 (G) 1.46037.123 (H) 1.58540.325 (J)1.71143.5859-133S Socket AdapterShell SizeA Diameter 1.200 (30.5) MAXØ AHBC DFEGAAHGFEDCBIn.mm.09 (A).65016.511 (B).78019.817 (E) 1.20330.619 (F) 1.26532.121 (G) 1.39035.323 (H) 1.52038.625 (J)1.63541.5Overall Length Part Number Inches meters 180.45858-020-B-02-18360.91858-020-B-02-3672 1.82858-020-B-02-72120 3.05858-020-B-02-120El Ochito ® Test Jumpers with Pin ContactsOCHITO PIN CONTACT (858-018)ETHERNET CABLE S/FTP CAT6A, 26 AWG(963-033-26)RJ45 MODULAR PLUGSHIELDED HIGH PERFORMANCECAT6A 10 GIGABIT SPEEDPin Jumper Ordering InformationEl Ochito® Test Jumper SchematicNotes1.858-020 jumper cables are intended only for use in Glenair El Ochito® test adapters. Do not attempt to install in MIL-DTL-38999 type connectors.2. Other cable lengths are readily available. Change the suffix number to the desired length in inches.3. 858-020 jumper cables are fully assembled and 100% electrically tested.4. Length is minimum overall length including contact and plug.5. No tool is required to install or remove contacts.6.Jumper cables are wired per the guidelines of ARINC 664 Part 2 Appendix N.El Ochito ® Test Jumpers with Socket ContactsOCHITO SOCKETCONTACT (858-019)RJ45 MODULAR PLUGSHIELDED HIGH PERFORMANCECAT6A 10 GIGABIT SPEEDETHERNET CABLE S/FTP CAT6A, 26 AWG(963-033-26)Socket Jumper Ordering InformationMATING FACE OF SOCKETCONTACT1234567816782345MATING FACE OF PINCONTACT8763214587654321BRNWHT/BRN BLUE WHT/BLU ORN WHT/ORN GRN WHT/GRN OCHITO PIN OR SOCKETRJ-45El Ochito ® Test Adapters and Jumpers for SuperNine ® ConnectorsInner Contacts (8)Ferrule BushingInner and Outer InsulatorsOuter BodyMounting BlockQ Q QQQ Q QQ Q Q Q QQQQQQQQQQQADDITIONAL RUGGEDIZEDHIGH-SPEED DATALINK SOLUTIONSavailable now from GlenairSUPERSEAL™ IP67 OPEN-FACE RUGGEDIZED FIELD RJ45 SOLUTIONSSUPERSEAL™ IP67 OPEN-FACE RUGGEDIZED FIELD USB 2.0 AND 3.0 SOLUTIONSSeries ITS 5015 type SuperSeal™ RJ45MIL-DTL-28840 type SuperSeal™ RJ45MIL-DTL-38999 Sr. III type SuperSeal™ RJ45Series IPT 26482 typeSuperSeal™ RJ45Series 80 Mighty MouseSuperSeal™ RJ45Series 80 Mighty MouseSuperSeal™ USB Series IPT 26482 typeSuperSeal™ USB MIL-DTL-38999 Sr. III type SuperSeal™ USB MIL-DTL-28840 type SuperSeal™ USBSeries ITS 5015 type SuperSeal™ USBOCTOBYTE™ SERIES RUGGEDIZED ETHERNET CONNECTOR SPEED-MASTER™ 10G+ ETHERNETEthernet Cat7A contacts Ethernet Cat5 contacts Coax contacts Ethernet MVB - WBT contactsSpeed-Master™ modular 10G+ Ethernet technology (shown here in SuperNine®packaging) available now for22D gage contacts and wiresTested for compliance according to EN50173-1 standards for CAT5E and CAT7HIGH-SPEED / RF DATALINK CONTACTSSize #8 differential twinax contactsSize #12 ultra-twinax differential twinaxcontactsSize #8 quadrax contacts Size #12 SMPM type spring-loaded coaxialSize #8 spring-loaded BMB microwave contacts GLENAIR FIBER OPTIC INTERCONNECT SOLUTIONSMIL-DTL-38999 type fiber optic Glenair Front Release (GFR)fiber opticNGCON MIL-PRF-64266fiber optics Eye-Beam™ GLT and GMAexpanded beamMT Ferrule 38999 typefiber optic ARINC 801 type fiber opticGlenair High Density (GHD) fiber optic29© 2018 Glenair, Inc • 1211 Air Way, Glendale, CA 91201 • 818-247-6000 • • U.S. CAGE code 06324 • High-Speed ContactsLaboratory link test and qualification data for harsh-environment Photonic solutions areavailable—just contact the factorySignal aggregation media converter(cutaway view)7-port Ethernet switchSmall form-factor bi-directionalPCB-mount transceivers Lightning-strike protected ARINC 801 F/O to D38999-type media converter Micro-aggregatorD38999 type fiber optic Ethernet media converter DVI copper-to-fiber media converterPCB-mount dual Transmitters, Receivers, and Transceivers RF-over-fiber for SATCOM-based WiFiand IFE systemsAEROSPACE-GRADE TRANSCEIVERS, RECEIVERS, AND MEDIA CONVERTERSSERIES 050 OVERVIEWRuggedized, Small Form-Factor Photonic Interconnect SolutionsEvaluation boards and performance testing available for all systemsGlenair, Inc.1211 Air Way • Glendale, California • 91201-2497Telephone:818-247-6000•Fax:818-500-9912•*****************Telephone:+44-1623-638100Facsimile:+44-1623-638111****************.uk Glenair UK Ltd40 Lower Oakham Way Oakham Business Park Mansfield, Notts NG18 5BY England Telephone:06172 / 68 16 0Facsimile:06172 / 68 16 90***************Glenair GmbH Schaberweg 2861348 Bad Homburg GermanyTelephone:+33-5-34-40-97-40Facsimile:+33-5-61-47-86-10****************Glenair France SARL 7, Avenue Parmentier Immeuble Central Parc #231200 Toulouse FranceTelephone:847-679-8833Facsimile:847-679-8849Glenair Microway Systems 7000 North Lawndale Avenue Lincolnwood, IL 60712Telephone:+46-8-50550000****************Glenair Nordic ABGustav III : S Boulevard 46SE-169 27 Solna Sweden© 2018 Glenair, Inc. Printed in U.S.A.CAT-159Telephone:+34-925-89-29-88Facsimile:+34-925-89-29-87****************Glenair Iberica C/ La Vega, 1645612 Velada SpainTelephone:203-741-1115Facsimile:203-741-0053*****************Glenair Power Products Group 20 Sterling Drive Wallingford, CT 06492Telephone: +39-051-782811Facsimile:+39-051-782259***************Telephone:+82-31-8068-1090Facsimile:+82-31-8068-1092****************Glenair Italia S.p.A.Via Del Lavoro, 740057 Quarto Inferiore – Granarolo dell’Emilia Bologna, ItalyGlenair KoreaB-1304 Gunpo IT Valley 148 Gosan-Ro, Gunpo-Si Kyunggi-Do, Korea 435-733INTERCONNECT SOLUTIONSMISSION-CRITICAL。
约翰·迪尔高效率发动机出货清单说明书
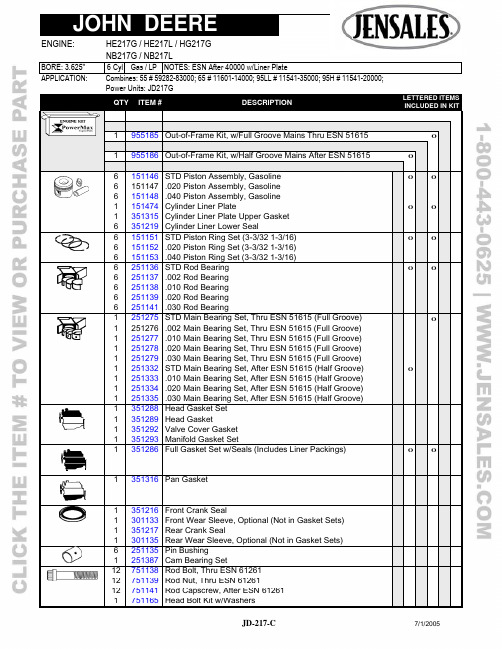
APPLICATION: Combines: 55 # 59282-83000; 65 # 11601-14000; 95LL # 11541-35000; 95H # 11541-20000; Power Units: JD217GQTY ITEM # DESCRIPTION LETTERED ITEMSINCLUDED IN KIT1 955185 Out-of-Frame Kit, w/Full Groove Mains Thru ESN 51615 O1 955186 Out-of-Frame Kit, w/Half Groove Mains After ESN 51615 O 6 151146 STD Piston Assembly, Gasoline O O6 151147 .020 Piston Assembly, Gasoline6 151148 .040 Piston Assembly, Gasoline1 151474 Cylinder Liner Plate O O 1 351315 Cylinder Liner Plate Upper Gasket6 351219 Cylinder Liner Lower Seal6 151151 STD Piston Ring Set (3-3/32 1-3/16) O O 6 151152 .020 Piston Ring Set (3-3/32 1-3/16)6 151153 .040 Piston Ring Set (3-3/32 1-3/16)6 251136 STD Rod Bearing O O 6 251137 .002 Rod Bearing6 251138 .010 Rod Bearing6 251139 .020 Rod Bearing6 251141 .030 Rod Bearing1 251275 STD Main Bearing Set, Thru ESN 51615 (Full Groove) O1 251276 .002 Main Bearing Set, Thru ESN 51615 (Full Groove)1 251277 .010 Main Bearing Set, Thru ESN 51615 (Full Groove)1 251278 .020 Main Bearing Set, Thru ESN 51615 (Full Groove)1 251279 .030 Main Bearing Set, Thru ESN 51615 (Full Groove)1 251332 STD Main Bearing Set, After ESN 51615 (Half Groove) O1 251333 .010 Main Bearing Set, After ESN 51615 (Half Groove)1 251334 .020 Main Bearing Set, After ESN 51615 (Half Groove)1 251335 .030 Main Bearing Set, After ESN 51615 (Half Groove)1 351288 Head Gasket Set1 351289 Head Gasket1 351292 Valve Cover Gasket1 351293 Manifold Gasket Set1 351286 Full Gasket Set w/Seals (Includes Liner Packings) O O1 351316 Pan Gasket1 351216 Front Crank Seal 1 301133 Front Wear Sleeve, Optional (Not in Gasket Sets)1 351217 Rear Crank Seal1 301135 Rear Wear Sleeve, Optional (Not in Gasket Sets)6 251135 Pin Bushing 1 251387 Cam Bearing Set12 751138 Rod Bolt, Thru ESN 6126112 751139 Rod Nut, Thru ESN 6126112 751141 Rod Capscrew, After ESN 612611 751165 Head Bolt Kit w/WashersPower Units: JD217GQTY ITEM # DESCRIPTION LETTERED ITEMSINCLUDED IN KIT1 551159 Rebuilt Camshaft 1 551126 Cam Key12 551127 Tappet6 451132 Exhaust Valve 6 451133 Intake Valve12 451134 Valve Guide 12 451135 Valve Spring6 451136 Rotator: HE217G, HG217G, NB217G24 451137 Valve Keeper (Half)6 351224 Intake Valve Seal6 401132 Exhaust Seat (1.187 x 1.442" x .219") 6 401121 Intake Seat3 451138 Exhaust Rocker Arm, LH3 451139 Exhaust Rocker Arm, RH3 451141 Intake Rocker Arm, LH3 451142 Intake Rocker Arm, RH2 451251 Rocker Arm Shaft2 451144 Rocker Arm Shaft Plug (Cork)1 551128 Cam Gear 1 551129 Crank Gear12 551131 Push Rod1 651141 New Oil Pump 1 651126 Oil Pump Kit (1.875" OAL Gears) 1 NLA Oil Pump Screen, Early Bolt-On Style1 651125 Oil Pump Screen, Late Wire-On Style1 851189 Governor Kit: HE217G, HE217L, HG217G Thru ESN 492871 851158 Governor Kit: HE217G, HE217L, HG217G After ESN 49287 1 851156 Governor Kit: NB217G, NB217L Thru ESN 490241 851157 Governor Kit: NB217G, NB217L After ESN 490241 851159 Thermostat, 160 Degree1 851163 Thermostat, 180 Degree1 851191 Bypass Hose。
Dupline车库计数系统产品描述说明书

•Controller in the Dupline ®zone counting system •Micro Linux PC with ethernet port and web server•Connects up to 120 count sensors via Dupline ®L 13-wire bus•Dupline ®ultrasonic carpark sensors can be used directly on the L 1bus•Loop detectors or photoelectric sensors can be used when connected to a Dupline ®L 1input module•Manages up to 3840 parking spaces in multiple zones •Each zone can have multiple entry and exit points •Easy configuration, monitoring and count adjustment via web server•Mixed systems with zone counting and single space detection possible•Option to detect the split between handicap and stan-dard spaces occupancy•Optional PC software for real-time monitoring and his-torical occupancy data analysisDupline ®CarparkProduct DescriptionOrdering KeyType SelectionHousing Mounting Supply: 24 VDC ± 20%2 DIN DIN-rail GP32950030700Master Zone Counter (MZC) Module Type GP32950030700The GP32950030700 is a programmable unit specially designed for Carpark installa-tions. This controller includes dedicated functions for counting based on the count sensors connected to the L1bus. A web server in the con-troller gives the user a unique opportunity to modify ormonitor the zone count sys-tem using a smartphone or other ethernet based equip-ment. The GP32950030700has no independent functions and only works to g ether with the channel generator GP32900003700.GP32950030700Supply SpecificationsMain Hardware CharacteristicsGP32950030700Data format Selectable: 1 start bit, 7/8data bit, no/odd/even/ par-ity,1/2 stop bit Baud-rate 9600 bits/sInsulationSee the table “Insulation between inputs and out-puts”Number of ports 2Purpose COM1: Modbus slave COM2: Modbus slave TypeMultidrop, bidirectional Connections 2-wire. Max. distance 1000mProtocolMODBUS RTURS485 Communications PortsConnections RJ45 10/100 BaseTX Max. distance: 100mInsulationSee “Insulation between inputs and outputs” table.Rated inputsIP configuration DNSWEB serverEthernet PortHS Bus Specs (right side)Note:The two GP32900003700 modules which drive the L1 and L2 buses must be connected on the right sideof the GP32950030700LEDs IndicationGreen LED:ON ON: power ON OFF: power OFFYellow LEDs:COM 1OFF: no communications on RS485 AFlashing: 200ms ON 600ms OFF , no answer from the slaveFlashing: 200ms ON 200ms OFF , communications OK COM 2OFF: no communications on RS485 BFlashing: 200ms ON 600ms OFF , no answer from the slaveFlashing: 200ms ON 200ms OFF , communications OKBUSOFF: no communication is present on the HSbusON: communication error on HSbusFlashing: communication OK on HSbusBlue LED: USB Not in use Red LED: STATUS Not in useGP32950030700Based Insulation between Inputs and OutputsGeneral SpecificationsPower supply2 screw terminals Cable cross-section area 1.5 mm 2maxScrews tightening torqueMin. 0.4 Nm, Max. 0.8 NmConnectionsMode of OperationThe GP32950030700 is part of the GPMZC-SET and it has no function without the channel generators GP32900003700. Information regarding installa-tion, programming and han-dling the GP32950030700 can be found n the datasheet GPMZC-SET or the MZC installation manual.GP32950030700 Dimensions。
Elko EP 设备名称和型号说明书

SOU-2cos φ ≥ 0.95M M HAL.230VKM MAC12250V / 1ADC14x AC1250V / 8AAC13xAC2250V / 5AAC14250V / 4AAC3250V / 4AAC15250V / 3AAC5b250WDC530V / 2AAC6a250V /4ADC1230V / 8AAC7b250V / 1ADC1330V / 2A02-28/2017 Rev.: 1xDC330V / 3AxDC130V / 8A15 16 18A1 A2 T1 T1 G GUnT1GT1GA1A21516189101112131415161718192015234678Made in Czech RepublicELKO EP, s.r.o.Palackého 493769 01 Holešov, VšetulyCzech RepublicTel.: +420 573 514 211Twilight digital switch with integrated time switch CharacteristicsDescriptionSymbol ConnectionType of loadMat. contacts AgSnO2,contact 8 AType of loadMat. contacts AgSnO2,contact 8 AAC5auncompensatedAC5acompensatedEN• It is used to control lighting based on the level of ambient light intensity and realtime (a combination of twilight switch / light switch and switching clock in oneproduct).• With the possibility to block the function of the twilight switch at a time when thelighting is undesirable or uneconomical.• External light sensor with IP65 protection, adapted for wall mounting (sensor hold-er included) or panel.• Backlit LCD display.• Backup of the set time using the battery.• Easily replace the backup battery without disassembling the device.• Switching mode AUTO:PROGRAM > according to the set program or RANDOM >switches randomly - simulation of the presence of people.• PROGRAM:LIGHT > switches according to the set level of illumination or TIME PRO-GRAM > switches according to the set time program.• Switching mode HOLIDAYS > blocking of the set program.• Switching mode MANUAL > permanently on or off.• Programming can also be done in backup mode (battery power).• In backup mode, relay output contacts do not work.• Automatic transition winter/daylight saving time (by region).• Display languages - CZ / SK / EN / ES / PL / HU / RU.SensorCONTROL OF A DISPLAY WITH BACKLIGHTPower on: Display is illuminated with a backlight for 10 seconds from the last button press.The display continuously shows the settings – date, time, day of the week, contact stateand programme. Permanent on / off is activated by simultaneous presses of the MAN,ESC, OK buttons.After activating the permanent on/off, the display will fl ash briefl y.Backup mode: After 2 minutes, the display switches to the sleep mode, i.e. shows no infor-mation. The display can be activated by pressing any button.1. Supply voltage terminals2. Display with back-light3. Place for seal4. Backup battery plug-in5. Output contact (15-16-18)6. Terminals - sensor (T1)7. Shield connection terminals(if shielded cable is used)8. Control buttons9. Indicates the day in the week10. Status indication11. Display of data / settings menu / light intensity12. ime display13. Control button PRG / +14. Reset15. Control button MAN / -16. Operating modes indication17. 12/24 hours format18. Indication of the switch program19. Control button ESC20. Control button OK. Switches display date / lightintensitySOU-2OK+_OK+_ESCOKoptionslanguageESPAnOLLIGHTTechnical parameters * ERROR - sensor short circuitLight sensorPhotosensor SKS-200 is external and is connected to terminals T1. Sensor is installable to panel (by screw-able transparent cover) to opening with diameter 20 mm. A part of the sensor is a plas-tic holder for placing into the wall or to another place. Length of a line connector to the sensor cannot be more than 50 m. Doublecure cable can be used as wire diameter min. 0.2 - 0.75 mm 2 / with sleeve: 0.25 - 0.34 mm 2 . Protection degree is IP65.To keep this protection:- photosensor SKS-200 cover must be sealed by a rubber circle (part of the sensor)- cable must be of round cross-selection- the opening must be tight to the used cableMode precendencemode precedencedisplay output mode⑥⑥⑥ON / OFF manual control⑥⑥ON / OFF holiday mode ⑥ON / OFF time program lightlightmode with the highest priorityLanguage settingsLight and Time Program can work at the same time on a single channel.Language selectionlanguageoptionsControl descriptionentrance into programming menu+_browsing in menu setting of values+_quick shifting during setting of valuesOK entrance into required menu confi rmationswitch. between display ESCone level upa step backESCback to the starting menuDevice diff ers short and long button press. In the manual marked as:- short button press (<1s) - long button press (>1s)After 30s of inactivity (from the last press of any button) will device automatically returns into starting menu.In the start screen, press OK to toggle between displaying the date or light intensity.The measured value after exceeding 999 is measured in the hundreds of thousands by display-ing the letter …k“ at the end. A comma separates the thousands line.Supply terminals:Supply voltage tolerance:Consumption:Supply voltage tolerance:Backup battery type:OutputNumber of contacts:Rated current:Switched capacity:Switched voltage:Dissipated power (max.):Mechanical life:Electrical life (AC1):Time circuitAccuracy:Minimum interval:Program data stored for:Program circuitIllumination range:Sensor failure indication:Number of program places:Program:Other dataOperating temperature Storage temperature:Dielectrical strength:Operating position:Mounting:Protection degree:Overvoltage cathegory:Pollution degree:Max. cable size (mm 2):Dimensions:Weight:Dimension of sensor:Weight sensor:Standards:A1 - A2AC 230V (50-60 Hz)4 VA / 1.7 W -15 %; +10 %CR 2032 (3V)1x changeover (AgSnO 2)8 A/AC12000 VA/AC1, 240 W/DC250V AC/30V DC0.6 W 30.000.000 ops. 100.000 ops.max. ±1s/ day at 23 °C1 min min. 10 years 10-50000 lx displayed on LCD *100daily, weakly, yearly-10 °C to +55 °C (-4 °F to 131 °F)-30 °C to +70 °C (-22 °F to 158 °F)4 kV (supply - output)3.5 kV (supply - sensor)any DIN rail EN 60715IP40 from front panel/IP20 terminalsIII.2max. 1x 2.5, max. 2x 1.5/with sleeve max. 1x 1.5 90 x 35 x 64 mm (3.5‘‘x 1.4‘‘x 2.5‘‘)142 g (5 oz.)58 x Ø 24 mm (2.3‘‘x Ø 0.9‘‘)16 g (0.5 oz.)EN 61812-1, EN 60669-1, EN 60669-2-115-1815-18Menu overviewLight functions setting.t1- delay time when switching ont2 - delay time when switching offThe value may be entered in a range of 10 to 50,000 lux.After exceeding a value of 9,800 lux, a period separates thethousands line.If the function light is active, then symbol …Auto“ is displayed on the screen.If the entered switching delay is shown on the display …Auto + t“.Ambient light courseSet levelDate and time settingrst day of the week.. Set the number from the set to the current date.rst day of the week.OKOKOKOKOKOKOKOKOKOKOKOKOKOKOKOKOKOKOK*Time programsetting of minutesminutesactivity on a week daymonthminuteshours setting of hoursactivity on a week daylevel or constant ON/OFFlevel or constant ON/OFFor constant ON/OFFprogram *yearly programsetting of the year setting of the month setting of the daysetting of minutessetting of hourslevel or constant ON/OFFCHANGE / DELETE . If you do not want to proceed, press ESC to go to the main settings without any change.If the program memory is full, you will see full on the display.If the programs memory is empty and you want to change or erase a program, the display will read empty.Setting the switching modesWhat you see on the display:- when a random mode is activated - Random - the symbol is lit .- vacation mode HOLIDAY:- the illuminated symbol indicates the vacation mode.- the fl ashing symbol indicates the vacation mode.- the symbol is not illuminated if the vacation mode is not set or has.- when the manual mode is activated, the symbol is lit and the manually controlled channel is fl ashing.Settings optionsTime correction:The shift unit is 0.1s per day.The numeric value refers to seconds per 10 days.Time correction is factory-set and individual for each product so that the real-time clock would run with minimum deviation. The time correction value can be arbitrarily adjusted, but after product RESET, the value returns to factory settings.onon+_on+_OK+ESCOKOKOKOK OK OKOK OK OK ESCOK+_+_OK OKOK+_+_+_+_+_OKOKOKOK+_OK+_PRG OK+_OK OKOKOKOKOKOKOKOKon+_OKOKOKOKOKOK OK OKCR2032+Performed by shortly pressing the hidden RESET button with a blunt-pointed object (e.g. a pencilor screw-driver with a diameter of at most 2 mm).The type of device and software version will be displayed for 1 second, then the device will enterdefault mode. This means that the language is set to EN, all data is zeroed (light function, time/date, user programs, device options function).Resetpress button OK to completethe deleting of all set programsin starting menu (time is shownon display) - press simultaneouslybutton and and displayannounces a notice allDeleting of all programsall16--sep-- 10Battery replacementYou can replace the battery without disassembling the device.- Eject the plug-in module with battery- Remove the original battery- Insert the new battery so that the top edge of the battery (+) is aligned with the Plug-in module- insert the plug-in module into the device - beware of polarity (+ up)16--sep-- 1016--sep-- 10WarningAn example of SOU-2 programmingSettings for switching upon exceeding the range of 1,500 lux. Settings of hysteresis at 10% and off delay at 10 min. Upon a change of the lux switching range each Friday at 12:00 p.m. to 2,000 and each Wednesday at 11:00 a.m. to 1,000 lux.lightlight time prog add addaddprog progday progday proghourhourminuteminuteintensity intensityset (lux)set (lux)set (lux)hysteresis set (%)hysteresis delay delayDevice is constructed for connection in 1-phase main alternating current voltage 230 V andmust be installed according to norms valid in the state of application. Connection according tothe details in this direction. Installation, connection, setting and servicing should be installedby qualifi ed electrician staff only, who has learnt these instruction and functions of the device.This device contains protection against overvoltage peaks and disturbancies in supply. F orcorrect function of the protection of this device there must be suitable protections of higherdegree (A, B, C) installed in front of them. According to standards elimination of disturbanciesmust be ensured. Before installation the main switch must be in position “OFF” and the deviceshould be de-energized. Don´t install the device to sources of excessive electro-magnetic in-terference. By correct installation ensure ideal air circulation so in case of permanent opera-tion and higher ambient temperature the maximal operating temperature of the device is notexceeded. For installation and setting use screw-driver cca 2 mm. The device is fully-electronic- installation should be carried out according to this fact. Non-problematic function dependsalso on the way of transportation, storing and handling. In case of any signs of destruction,deformation, non-function or missing part, don´t install and claim at your seller it is possible todismount the device after its lifetime, recycle, or store in protective dump.。
HLCP-H100中文资料
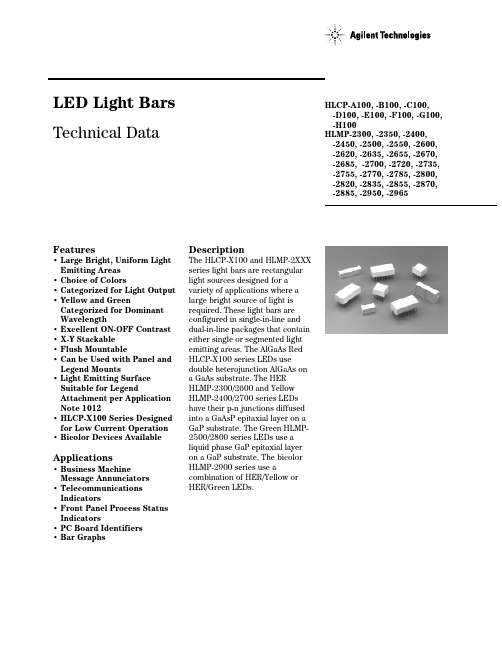
LED Light Bars Technical DataFeatures•Large Bright, Uniform Light Emitting Areas•Choice of Colors •Categorized for Light Output •Yellow and Green Categorized for Dominant Wavelength•Excellent ON-OFF Contrast •X-Y Stackable•Flush Mountable•Can be Used with Panel and Legend Mounts• Light Emitting Surface Suitable for Legend Attachment per Application Note 1012•HLCP-X100 Series Designed for Low Current Operation •Bicolor Devices Available Applications•Business MachineMessage Annunciators •Telecommunications Indicators•Front Panel Process Status Indicators•PC Board Identifiers•Bar Graphs DescriptionThe HLCP-X100 and HLMP-2XXXseries light bars are rectangularlight sources designed for avariety of applications where alarge bright source of light isrequired. These light bars areconfigured in single-in-line anddual-in-line packages that containeither single or segmented lightemitting areas. The AlGaAs RedHLCP-X100 series LEDs usedouble heterojunction AlGaAs ona GaAs substrate. The HERHLMP-2300/2600 and YellowHLMP-2400/2700 series LEDshave their p-n junctions diffusedinto a GaAsP epitaxial layer on aGaP substrate. The Green HLMP-2500/2800 series LEDs use aliquid phase GaP epitaxial layeron a GaP substrate. The bicolorHLMP-2900 series use acombination of HER/Yellow orHER/Green LEDs.HLCP-A100, -B100, -C100,-D100, -E100, -F100, -G100,-H100HLMP-2300, -2350, -2400,-2450, -2500, -2550, -2600,-2620, -2635, -2655, -2670,-2685, -2700, -2720, -2735,-2755, -2770, -2785, -2800,-2820, -2835, -2855, -2870,-2885, -2950, -2965Selection GuideLight Bar Part Number Corresponding Size ofPackage Panel and HLCP-HLMP-Light Emitting AreasOutlineLegend Mount Part No. HLMP-AlGaAs HER Yellow Green A1002300240025008.89 mm x 3.81 mm 1A 2599(.350 in. x .150 in.)B10023502450255019.05 mm x 3.81 mm 1B 2598(.750 in. x .150 in.)D1002600270028008.89 mm x 3.81 mm 2D 2898(.350 in. x .150 in.)E1002620272028208.89 mm x 3.81 mm 4E 2899(.350 in. x .150 in.)F100263527352835 3.81 mm x 19.05 mm 2F 2899(.150 in. x .750 in.)C1002655275528558.89 mm x 8.89 mm 1C 2898(.350 in. x .350 in.)G1002670277028708.89 mm x 8.89 mm 2G 2899(.350 in. x .350 in.)H1002685278528858.89 mm x 19.05 mm 1H 2899(.350 in. x .750 in.)295029508.89 mm x 8.89 mm Bicolor I 2898(.350 in. x .350 in.)296529658.89 mm x 8.89 mm BicolorI2898(.350 in. x .350 in.)Number of Light Emitting AreasPart Numbering SystemHLCP- xx xx-xx x xxHLMP-xx xx-xx x xxMechanical Options[1]00: No mechanical optionColor Bin Options[1,2]0: No color bin limitationB: Color bins 2 & 3 (applicable for yellow devices only)C: Color bins 3 & 4 only (applicable for green devices only)Maximum Intensity Bin[1,2]0: No maximum intensity bin limitationMinimum Intensity Bin[1,2]0: No minimum intensity bin limitationDevice Specific Configuration[1]Refer to respective data sheetColor[1]x1: AlGaAs Red (applicable for HLCP-x100 only)23: High Efficiency Red24: Yellow25: Green26: High Efficiency Red27: Yellow28: Green29: Bicolor (High Efficiency Red/Yellow) OR (High Efficiency Red/Green) Notes:1. For codes not listed in the figure above, please refer to the respective data sheet or contact your nearest Agilent representativefor details.2. Bin options refer to shippable bins for a part-number. Color and Intensity Bins are typically restricted to 1 bin per tube(exceptions may apply). Please refer to respective data sheet for specific bin limit information.Package DimensionsNOTES:1. DIMENSIONS IN MILLIMETRES (INCHES). TOLERANCES ±0.25 mm (±0.010 IN.) UNLESS OTHERWISE INDICATED.2. FOR YELLOW AND GREEN DEVICES ONLY.Internal Circuit DiagramsIAbsolute Maximum RatingsHER Yellow GreenAlGaAs Red HLMP-2300/HLMP-2400/HLMP-2500/ ParameterHLCP-X1002600/29XX2700/29502800/2965Series Series Series Series Average Power Dissipated per LED Chip37 mW[1]135 mW[2]85 mW[3]135 mW[2] Peak Forward Current per LED Chip45 mA[4]90 mA[5]60 mA[5]90 mA[5] Average Forward Current per LED Chip15 mA25 mA20 mA25 mADC Forward Current per LED Chip15 mA[1]30 mA[2]25 mA[3]30 mA[2] Reverse Voltage per LED Chip 5 V 6 V[6]Operating Temperature Range–20°C to +100°C[7]–40°C to +85°C–20°C to +85°C Storage Temperature Range –40°C to +85°CWave Soldering Temperature250°C for 3 seconds1.6 mm (1/16 inch) below BodyNotes:1.Derate above 87°C at 1.7 mW/°C per LED chip. For DC operation, derate above 91°C at 0.8 mA/°C.2.Derate above 25°C at 1.8 mW/°C per LED chip. For DC operation, derate above 50°C at 0.5 mA/°C.3.Derate above 50°C at 1.8 mW/°C per LED chip. For DC operation, derate above 60°C at 0.5 mA/°C.4.See Figure 1 to establish pulsed operation. Maximum pulse width is 1.5 mS.5.See Figure 6 to establish pulsed operation. Maximum pulse width is 2 mS.6.Does not apply to bicolor parts.7.For operation below –20°C, contact your local Agilent sales representative.Electrical/Optical Characteristics at T A = 25°CAlGaAs Red HLCP-X100 SeriesParameter HLCP-Symbol Min.Typ.Max.Units Test ConditionsA100/D100/E100I V37.5mcd I F = 3 mA Luminous Intensityper Lighting Emitting B100/C100/F100/G100615mcdArea[1]H1001230mcdPeak WavelengthλPEAK645nmDominant Wavelength[2]λd637nmForward Voltage per LED V F 1.8 2.2V I F = 20 mA Reverse Breakdown Voltage per LED V R515V I R = 100 µA Thermal Resistance LED Junction-to-Pin RθJ-PIN250°C/W/LEDParameter HLMP-Symbol Min.Typ.Max.Units Test Conditions2400/2700/2720IV 620mcd IF= 20 mALuminous Intensityper Lighting Emitting2450/2735/2755/2770/2950[3]1338mcd Area[1]27852670mcdPeak WavelengthλPEAK583nmDominant Wavelength[2]λd585nmForward Voltage per LED VF 2.1 2.6V IF= 20 mAReverse Breakdown Voltage per LED[5]VR 615V IR= 100 µAThermal Resistance LED Junction-to-Pin RθJ-PIN 150°C/W/LEDHigh Efficiency Red HLMP-2300/2600/2900 SeriesParameter HLMP-Symbol Min.Typ.Max.Units Test Conditions2300/2600/2620IV 623mcd IF= 20 mALuminous Intensityper Lighting Emitting2350/2635/2655/2670/2950[3]1345mcd Area[1]2965[4]1945mcd26852280mcdPeak WavelengthλPEAK635nmDominant Wavelength[2]λd626nmForward Voltage per LED VF 2.0 2.6V IF= 20 mAReverse Breakdown Voltage per LED[5]VR 615V IR= 100 µAThermal Resistance LED Junction-to-Pin RθJ-PIN 150°C/W/LEDYellow HLMP-2400/2700/2950 SeriesHigh Performance Green HLMP-2500/2800/2965 SeriesParameter HLMP-Symbol Min.Typ.Max.Units Test Conditions2500/2800/2820IV 525mcd IF= 20 mALuminous Intensityper Lighting Emitting2550/2835/2855/28701150mcd Area[1]2965[4]2550mcd288522100mcdPeak WavelengthλPEAK565nmDominant Wavelength[2]λd572nmForward Voltage per LED VF 2.2 2.6V IF= 20 mAReverse Breakdown Voltage per LED[5]VR 615V IR= 100 µAThermal Resistance LED Junction-to-Pin RθJ-PIN 150°C/W/LEDNotes:1.These devices are categorized for luminous intensity. The intensity category is designated by a letter code on the side of the package.2.The dominant wavelength, λd , is derived from the CIE chromaticity diagram and is the single wavelength which defines the color of thedevice. Yellow and Green devices are categorized for dominant wavelength with the color bin designated by a number code on the side of the package.3.This is an HER/Yellow bicolor light bar. HER electrical/optical characteristics are shown in the HER table. Yellow electrical/opticalcharacteristics are shown in the Yellow table.4.This is an HER/Green bicolor light bar. HER electrical/optical characteristics are shown in the HER table. Green electrical/opticalcharacteristics are shown in the Green table.5.Does not apply to HLMP-2950 or HLMP-2965.Figure 1. Maximum Allowable Peak Current vs. Pulse Duration.Figure 4. Forward Current vs. Forward Voltage.Figure 5. Relative Luminous Intensity vs. DC Forward Current.AlGaAs RedFigure 2. Maximum Allowed DC Current per LED vs.Ambient Temperature, T J MAX = 110°C.Figure 3. Relative Efficiency (Luminous Intensity per UnitCurrent) vs. Peak LED Current.For a detailed explanation on the use of data sheet information and recommended soldering procedures,see Application Notes 1005, 1027, and 1031.HER, Yellow, GreenFigure 9. Forward Current vs. Forward Voltage Characteristics.Figure 10. Relative Luminous Intensity vs. DC ForwardCurrent.Figure 6. Maximum Allowed Peak Current vs. Pulse Duration.Figure 7. Maximum Allowable DC Current per LED vs.Ambient Temperature, T J MAX = 100°C.Figure 8. Relative Efficiency (Luminous Intensity per Unit Current) vs. Peak LED Current.Intensity Bin Limits (mcd)HLMP-2300/2600/2620 Annunciators (.2 x .4 HER/AlGaAs), HLCP-A100/D100/E100IV Bin Category Min.Max.A 3.00 5.60B 4.508.20C 6.8012.10D10.1018.50E15.3027.80F22.8045.50G36.9073.80Notes:1. Minimum category A for Red L/C AlGaAs (-A100/-D100/-E100).2. Minimum category C for HER (-2300/-2600/-2620).HLMP-2350/2635/2655/2670 Annunciators (.2 x .8 HER/AlGaAs), HLCP-B100/C100/F100/G100 (.4 x .4 HER/AlGaAs)IV Bin Category Min.Max.A 5.4010.90B9.0016.00C13.1024.00D19.7036.10E29.6054.20F44.9088.80G71.90143.80Notes:1. Minimum category A for Red L/C AlGaAs (-B100/-C100/-F100/-G100).2. Minimum category C for HER (-2350/-2635/-2670).HLMP-2685/HLCP-H100 Annunciators (.4 x .8 HER/AlGaAs) IV Bin Category Min.Max.A10.8022.00B18.0027.10C22.0040.80D33.3061.10E50.0091.80F75.10150.00G121.70243.40Notes:1. Minimum category A for Red L/C AlGaAs (-H100).2. Minimum category C for HER (-2685).HLMP-2400/2700/2720 Annunciators (.2 x .4 Yellow)IV Bin Category Min.Max.C 6.1011.20D9.2016.80E13.8025.30F20.7041.40G33.6067.20HLMP-2450/2735/2755/2770 Annunciators (.2 x .8 Yellow & .4 x .4 Yellow) IV Bin Category Min.Max.C13.0022.00D18.0033.00E27.0050.00F40.5081.00G65.60131.20HLMP-2785 Annunciators (.4 x .8 Yellow)IV Bin Category Min.Max.C26.0044.40D36.0066.00E54.0099.00F81.00162.00G131.40262.80HLMP-2500/2800/2820 Annunciators (.2 x .4 Yellow)IV Bin Category Min.Max.C 5.6010.20D8.4015.30E12.6023.10F18.9037.80G30.6061.20H49.5097.90I80.10158.40HLMP-2550/2835/2855/2870 Annunciators (.2 x .8/.4 x .4 Green) IV Bin Category Min.Max.C11.3020.60D17.0031.00E25.4046.50F38.1076.20G61.60123.20H99.81197.67I161.73320.21HLMP-2885 Annunciators (.4 x .8 Green)IV Bin Category Min.Max.C22.2040.80D33.4061.20E50.1091.90F75.10150.30G121.10242.20H196.10383.50I313.70613.60HLMP-2950 Bi-Color Annunciators (.4 x .4 HER/Yellow) IV Bin Category Min.Max.Red Iv CategoriesC11.3020.60D17.0031.00E25.4046.50F38.1076.20G61.60123.20Yellow Iv CategoriesC13.0022.00D18.0033.00E27.0050.00F40.5081.00G65.60131.20HLMP-2965 Bi-Color Annunciators (.4 x .4/.2 x .8 HER/Green) IV Bin Category Min.Max.Red Iv CategoriesD19.7036.10E29.6054.20F44.9088.80G71.90143.80Green Iv CategoriesB7.5013.90C11.3020.60D17.0031.00E25.4046.50F38.1076.20G61.60123.20H100.00200.00Notes:1. Minimum category D for LPE Green (-2965).2. In green mode, the devices are to be color binned into standard color bins, perTable 2. (-2685).Color CategoriesNote:All categories are established for classification of products. Products may not be available in all categories. Please contact your local Agilent representatives for further clarification/information.I AVG I v TIME AVG =I TESTwhere:I TEST =3 mA for AlGaAs Red(HLMP-X000 series)20 mA for HER,Yellow and Green (HLMP-2XXX series)Example:For HLMP-2735 series ηI PEAK = 1.18 at I PEAK = 48 mA12 mA I v TIME AVG =20 mA= 25 mcd[][]ElectricalThese light bars are composed of two, four, or eight light emitting diodes, with the light from each LED optically scattered to form an evenly illuminated light emitting surface.The anode and cathode of each LED is brought out by separate pins. This universal pinoutarrangement allows the LEDs to be connected in three possible configurations: parallel, series, or series parallel. The typical forward voltage values can be scaled from Figures 4 and 9.These values should be used to calculate the current limiting resistor value and typical power consumption. Expected maximum V F values for driver circuit design and maximum power dissipation,may be calculated using the following V F MAX models:AlGaAs Red HLCP-X100 series V F MAX = 1.8 V + I Peak (20 Ω)For: I Peak ≤ 20 mAV F MAX = 2.0 V + I Peak (10 Ω)For: 20 mA ≤ I Peak ≤ 45 mA HER (HLMP-2300/2600/2900),Yellow (HLMP-2400/2700/2900)and Green (HLMP-2500/2800/2900) seriesV F MAX = 1.6 + I Peak (50 Ω)For: 5 mA ≤ I Peak ≤ 20 mA V F MAX = 1.8 + I Peak (40 Ω)For: I Peak ≥ 20 mAThe maximum power dissipation can be calculated for any pulsed or DC drive condition. For DC operation, the maximum powerdissipation is the product of the maximum forward voltage and the maximum forward current. For pulsed operation, the maximum power dissipation is the product of the maximum forward voltage at the peak forward current times the maximum average forward current. Maximum allowable power dissipation for any given ambient temperature and thermal resistance (R θJ-A ) can be deter-mined by using Figure 2 or 7. The solid line in Figure 2 or 7 (R θJ-A of 600/538 C/W) represents a typical thermal resistance of a device socketed in a printed circuitboard. The dashed lines represent achievable thermal resistances that can be obtained through improved thermal design. Once the maximum allowable power dissipation is determined, the maximum pulsed or DC forward current can be calculated.OpticalSize of Light Surface Area Emitting Area Sq. Metres Sq. Feet 8.89 mm x 8.89 mm 67.74 x 10–6729.16 x 10–68.89 mm x 3.81 mm 33.87 x 10–6364.58 x 10–68.89 mm x 19.05 mm 135.48 x 10–61458.32 x 10–63.81 mm x 19.05 mm72.85 x 10–6781.25 x 10–6The radiation pattern for these light bar devices is approximately Lambertian. The luminoussterance may be calculated using one of the two following formulas:I v (cd)L v (cd/m 2) =A (m 2)πI v (cd)L v (footlamberts) =A (ft 2)Refresh rates of 1 kHz or faster provide the most efficientoperation resulting in the maxi-mum possible time average luminous intensity.The time average luminousintensity may be calculated using the relative efficiency character-istic of Figure 3 or 8, ηI PEAK , and adjusted for operating ambient temperature. The time average luminous intensity at T A = 25°C is calculated as follows:(ηI PEAK ) (I v Data Sheet)(1.18) (35 mcd)The time average luminous intensity may be adjusted for operating ambient temperature by the following exponential equation:I v (T A) = I V (25°C)e[K (T –25°C)]Color KAlGaAs Red–0.0095/°CHER–0.0131/°C Yellow–0.0112/°C Green–0.0104/°CExample:I v (80°C) = (25 mcd)e[-0.0112 (80-25)] = 14 mcd.MechanicalThese light bar devices may beoperated in ambient temperaturesabove +60°C without deratingwhen installed in a PC boardconfiguration that provides athermal resistance pin to ambientvalue less than 280°C/W/LED. SeeFigure 2 or 7 to determine themaximum allowed thermalresistance for the PC board,RθPC-A, which will permitnonderated operation in a givenambient temperature.To optimize device opticalperformance, specially developedplastics are used which restrictthe solvents that may be used forcleaning. It is recommended thatonly mixtures of Freon (F113)and alcohol be used for vaporcleaning processes, with animmersion time in the vapors ofless than two (2) minutesmaximum. Some suggested vaporcleaning solvents are Freon TE,Genesolv DES, Arklone A or K. A60°C (140°F) water cleaningprocess may also be used, whichincludes a neutralizer rinse (3%ammonia solution or equivalent),a surfactant rinse (1% detergentsolution or equivalent), a hotwater rinse and a thorough airdry. Room temperature cleaningmay be accomplished with FreonT-E35 or T-P35, Ethanol,Isopropanol or water with a milddetergent.For further information onsoldering LEDs please refer toApplication Note 1027.A/semiconductorsFor product information and a complete list ofdistributors, please go to our web site.For technical assistance call:Americas/Canada: +1 (800) 235-0312 or(916) 788-6763Europe: +49 (0) 6441 92460China: 10800 650 0017Hong Kong: (+65) 6756 2394India, Australia, New Zealand: (+65) 6755 1939Japan: (+81 3) 3335-8152 (Domestic/Interna-tional), or 0120-61-1280 (Domestic Only)Korea: (+65) 6755 1989Singapore, Malaysia, Vietnam, Thailand,Philippines, Indonesia: (+65) 6755 2044Taiwan: (+65) 6755 1843Data subject to change.Copyright © 2004 Agilent Technologies, Inc.Obsoletes 5962-7197EJuly 8, 20045988-2221EN。
Staubli型号大全

史陶比尔集团(英文名:Staubli )创立于1892年(总部位于瑞士),创立于1892年,史陶比尔集团有着100多年的发展历史,是一家在纺织机械,工业快速接头和工业机器人三大领域顶尖地位的世界知名企业。
联系人:王凯文手机:135*52*86*5878Q Q:2*8*5*0*5*9*0*5*8*6座机:010-5243*0161邮箱:2850590586@中国市场常用型号:STAUBLI SENSORDISTRIBUTOR|B27595534STAUBLI union|RCS06??N01143299Staubli 85559752/10 B-30/854502staubli RMP49.06.7102/JVstaubli RBE11.1102/IA/JV/W/ODStaubli 18.564Staubli 18.565Staubli PH08.5103/IA/MA/JVSTAUBLI SPH08.2103/IA/MA/JVSTAUBLI SPH06.2102/IA/MA/JVSTAUBLI SPH06.5102/IA/MA/JVstaubli RMI 209-12-6000-LStaubli RMI 209-12-1000-0-2-03staubli RMI 09 5102 0001 3/8"STAUBLI SBA08.1103STAUBLI SBA08.7103Staubli RBE03.7150.ODStaubli RBE03.1150.ODStaubli SPH06.1103/VB/JV/SPStaubli n00618597Staubli N00618697Staubli RPL08.1252/KRStaubli RPL08.6812/RE/KRStaubli PL08.6812/KRSTAUBLI RBE06.1151 ??IA/HPGSTAUBLI RBE06.1908 ??IA/HPGSTAUBLI RBE06.1101 ??IA/HPGStaubli RBE08.6151Staubli RCS08.1810Staubli RBE06Staubli RCS06Staubli RBE08.6151Staubli RCS08.1810Staubli RMI206.20/ASStaubli AF153.13/ICStaubli ABA15/24Staubli AIRFLEX-S13;125mStaubli ABA15/24Staubli AF153.13/ICStaubli ??AIRFLEX-S13??;75mStaubli ABA15/24Staubli RCS11.8813Staubli HJP09M006/RBE116/ERS081Staubli RBE 08.6151Staubli RBE 08.6251Staubli RBE 08.6252Staubli RBE 11.6813Staubli HJP09M006/RBE116/ERS081STAUBLI QUICKCONNECTOR|CBI09.1102/IA/JVStaubli G1/2" part no.:HPX08.1103/JV/BMB/SP X6CrNiMoTi17-12-2 Staubli G1" part no.:N01221100 type:HPX20.1105/JV/BMR/SPX6CrNiMoTi17-12-2Staubli G3/8 part no.:RBE08.1102/IA/JV/OD/3/FBX6CrNiMoTi17-12-2/Staubli G3/8 partno.:RBE08.1102/IA/JV/OD/3/FB ??X6CrNiMoTi17-12-2/staubli 13184G046Pstaubli 13149G014Pstaubli 13150G014SStaubli RBE11.1153/IC/JE/ODStaubli STA06.1101/SILStaubli SCB04.7201/IC/JK/SPStaubli SCB04.1201/IC/JK/SPSTAUBLI G1/4 RCS08.1101/VDSTAUBLI G1/4 RBE08.6151STAUBLI G1/4 RCS06.1101/VDSTAUBLI G1/4 RBE06.6101Staubli SPC12.2000/IASTAUBLI STAUBLI RMI 200.30Staubli spt 10.7657/L/CGStaubli NYLFLEX12Staubli 108099 SPT10.7103/L/CGStaubli 173150 SPT 10.1657/L/CGStaubli 173156 CGO 05.2416/L/MD/JEStaubli 173157 CGO 05.5416/L/JEStaubli 173245 CGD 05.2416/L/JEStaubli 173247 CGD 05.5416/L/JESTAUBLI CT-E1-15/B;33.4022STAUBLI CT-E1-1.5;33.4023STAUBLI CT-BP1ET;33.0541STAUBLI CT-BP1ET/0.25-0.75AU;33.0143STAUBLI 33.4005STAUBLI CT-BEG;33.4057STAUBLI CS-BT;33.5606-64STAUBLI L1-BL;33.5623STAUBLI CT-AG5;33.1065STAUBLI 33.1021staubli RBE 03.1151/OD/JVstaubli RBE 03.7151/IA/JVstaubli RBE 03.6904staubli RBE 06 1152/OD/JVstaubli RMI 16.7104/JVstaubli RMI 16.1104/JVstaubli RMI 09.7102/JVstaubli RMI 09.1102/JVSTAUBLI B27586150STAUBLI B27586148STAUBLI B27586152STAUBLI B27586151STAUBLI B27586154Staubli PML06.11001/COTStaubli RBE 03.6150staubli R600000005 G4staubli RBE11.7102/45/JEstaubli RBE11.7102/3./JEStaubli CBI06.1101/IAStaubli RMI212.20.1103/JV(with 20st G1/2 connect) Staubli RMI09.512/JVStaubli RMI20049727Staubli RMI20049700Staubli RMF 152.102Staubli RMI 200.30Staubli RMI 09.5102/JVSTAUBLI RBE11.1103/IA/JV/HPLStaubli ADS11.1105/IAStaubli HPX33.7107/JVStaubli SPX08.7103/JVStaubli SPX/PP06.7102/JVStaubli HQ-A2-316??Staubli G1-1/2 STAUBLI?? 87?? Staubli G1/2 STAUBLI?? 89?? Staubli G3/8 STAUBLI?? 90?? Staubli 30.0020 EG-TS-PG36/150 Staubli SPC08.5000/IA/JVStaubli SPC08.2000/IA/JVStaubli SPC08.2000.IA.CDJV Staubli HEL030300STAUBLI HPX 08.1103+HPX 08.7103 STAUBLI HPX 12.1104 +HPX 12.7104 STAUBLI HPX 20.1105 +HPX 20.7105 Staubli K4N002181Staubli K4N001722Staubli K4N001726Staubli K4N001724Staubli K4N00450Staubli RCS08.1816Staubli RBE11.2103Staubli RBE11.1153/IH/JNStaubli N00624312Staubli R60000226Staubli R60111313staubli NGV1 NO01021995Staubli 30.0020 EG-TS-PG36/150 Staubli RMI209.12.1104/JVStaubli RMI09.5102/JVStaubli SPC08.2000.IA.CDJV STAUBLI B27595114STAUBLI B14826136STAUBLI K81556267STAUBLI B23585429STAUBLI B23585432STAUBLI B23586459STAUBLI B23587018STAUBLI B23587078STAUBLI B24582511STAUBLI B27585266STAUBLI B27585714STAUBLI B27595113STAUBLI K81450234STAUBLI K81450235STAUBLI K81556268STAUBLI K81615043STAUBLI K85535599STAUBLI K85536099STAUBLI K86300098STAUBLI 6MTW03-001STAUBLI 6MRW03-001Staubli 103586282staubli 358 0202 ABSTAUBLI RSI 08-1152STAUBLI tuyau HEL 03.03.00 + 2 raccords HEL 03.1150 STAUBLI RBE06.1151/IC/3/FB/VD/JC/ODSTAUBLI RBE06.1151/IC/45/FB/VD/JC/ODSTAUBLI RBE06.1151/IC/6/FB/VD/JC/ODSTAUBLI RBE06.7151/IC/3/JCSTAUBLI RBE06.7151/IC/45/JCSTAUBLI RBE06.7151/IC/6/JCSTAUBLI RSI 08-1152STAUBLI REA081600001STAUBLI SBA 08.1103STAUBLI SBA 08.7103STAUBLI RBE11.6103/45STAUBLI RBE11.6103/6STAUBLI RBE11.1103/ia/6/WSTAUBLI RBE11.1103/ia/45/WSTAUBLI RBE11.7103/IASTAUBLI RBE08.7102/IA/WSTAUBLI RBE08.1102/IA/0D/WSTAUBLI RBE11.1103/IA/0DSTAUBLI RBE11.7103/IA/JESTAUBLI RBE11.1103/IA/JE/0DSTAUBLI RCS-08.1153(G1/2")STAUBLI RCS-08.8103(G1/2")STAUBLI RBE08.6153(G1/2")STAUBLI RBE08.6103(G1/2")staubli SPC05.2000/IA/JVstaubli SPC08.2000/IA/JVstaubli SPC05.5000/IA/JVStaubli B27583359,REA03.2302STAUBLI dashuai2204STAUBLI NO11.198.03Staubli RM1061JVSTAUBLI tuyau HEL 03.03.00 + 2 raccords HEL 03.1150 Staubli RMI 12.1103/JVSTAUBLI S0*******STAUBLI S0*******STAUBLI S0*******STAUBLI RBE03.1100/IA/VD/HPG/JE/OSStaubli KTDEK11 STABU-1008;connector RBE 0.6101/IC Staubli RBE03.7150/IC/JEStaubli RBE03.1904/IC/JEStaubli RBE 11.1103staubli N00628610STAUBLI RBE03.2100/IA/15/HPG/JV/ODSTAUBLI RBE03.2100/IA/75/HPG/JV/ODSTAUBLI RBE03.7100/IA/75/HPG/JVSTAUBLI RBE03.6150/HPGStaubli RBE 03Staubli CBX 09.1102/JV/BF with plugStaubli CBX 09.7102/JV/BF with plugStaubli RMI 09.1102/JV with plugStaubli RMI 09.7102/JV with plugStaubli RBE 03.1251/HPLStaubli RBE 03.6200/HPLSTAUBLI K4N000299STAUBLI K4N000301STAUBLI N00237511STAUBLI N00418810STAUBLI N00428711STAUBLI N00634412STAUBLI N00719710STAUBLI N00728607STAUBLI N00816710STAUBLI N00833607STAUBLI N00919410STAUBLI N00920509Staubli N00642408Staubli N00642308Staubli AIRFLEX08 200MStaubli REE03.1100??JV/0DStaubli REE03.7151Staubli 18.9004 plug-SP1.5/0.5-1.5AGStaubli 18.8004 socket-BP1.5/0.5-1.5Staubli 18.4604 pin carrier-E3-24PE/SStaubli 18.4704 SOCKET CARRIER-E3-24PE/BStaubli 18.0308 socket housing-MGK3VB10-14+MGK3R-M32 Staubli 18.0310 PIN HOUSING-MGK3VS10-14+MGK3R-M32Staubli 18.5618 DST-RG GR.3/14 BUstaubli N00512808staubli N00260306Staubli SPH G1/4 04.5101/MA/IA/JVSTAUBLI NO1210411STAUBLI NO0624312STAUBLI RBE-03-M10X1-S9*******Staubli HPX12.1104 G3/4Staubli HPX20.1105 G1Staubli HPX25.1106 G1 1/4Staubli RBE06.6151/IC/HPISTAUBLI RCS06.1163Staubli AIRFLEX 08 200MStaubli RBE 06.2102/0/ICJTVD SF;QUICK CHANGE BUSHING\G3/8"i DN6 STAUBLI RMI12.1153/JVSTAUBLI RMI12.7152/JVStaubli unvalved plugs rbe03 6904 (no color)Staubli unvalved plugs rbe03 6904 (blue)Staubli plug type:CBI06.7151/IA/JV/REStaubli socket type:CBI06.1810/IA/CNStaubli pipe type:CALOREL-EC10/KBStaubli MCS/MA N-FIXED PLATEStaubli MCS/MA N-MOBILE PLATE。
HLMP-EJ08中文资料
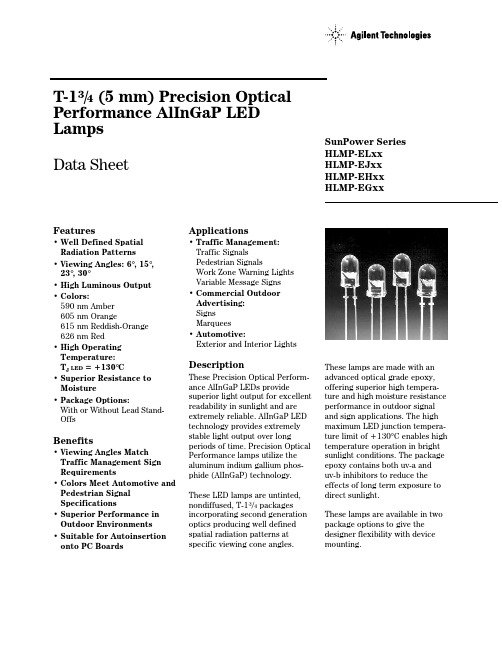
T-13/4 (5 mm) Precision Optical Performance AlInGaP LED LampsData SheetFeatures• Well Defined Spatial Radiation Patterns• Viewing Angles: 6°, 15°, 23°, 30°• High Luminous Output• Colors:590 nm Amber605 nm Orange615 nm Reddish-Orange626 nm Red• High Operating Temperature:T J LED=+130°C• Superior Resistance to Moisture• Package Options:With or Without Lead Stand-OffsBenefits• Viewing Angles Match Traffic Management Sign Requirements• Colors Meet Automotive and Pedestrian Signal Specifications• Superior Performance in Outdoor Environments• Suitable for Autoinsertion onto PC Boards Applications• Traffic Management:Traffic SignalsPedestrian SignalsWork Zone Warning LightsVariable Message Signs• Commercial OutdoorAdvertising:SignsMarquees• Automotive:Exterior and Interior LightsDescriptionThese Precision Optical Perform-ance AlInGaP LEDs providesuperior light output for excellentreadability in sunlight and areextremely reliable. AlInGaP LEDtechnology provides extremelystable light output over longperiods of time. Precision OpticalPerformance lamps utilize thealuminum indium gallium phos-phide (AlInGaP) technology.These LED lamps are untinted,nondiffused, T-13/4 packagesincorporating second generationoptics producing well definedspatial radiation patterns atspecific viewing cone angles.SunPower SeriesHLMP-ELxxHLMP-EJxxHLMP-EHxxHLMP-EGxxThese lamps are made with anadvanced optical grade epoxy,offering superior high tempera-ture and high moisture resistanceperformance in outdoor signaland sign applications. The highmaximum LED junction tempera-ture limit of +130°C enables hightemperature operation in brightsunlight conditions. The packageepoxy contains both uv-a anduv-b inhibitors to reduce theeffects of long term exposure todirect sunlight.These lamps are available in twopackage options to give thedesigner flexibility with devicemounting.Device Selection GuideTypicalViewing Color and Luminous Angle Dominant Lamps Without Standoffs Lamps With Standoffs Intensity Iv (mcd) [1,2] 2θ1/2Wavelength on Leads on Leads@ 20 mA (Deg.)[4](nm), Typ.[3] (Outline Drawing A)(Outline Drawing B)Min.Max.HLMP-EL08-VY000HLMP-EL10-VY000360013800HLMP-EL08-VYK00*360013800HLMP-EL08-VXK00*360010700HLMP-EL08-VX400**360010700HLMP-EL08-VX000360010700HLMP-EL08-WZ000HLMP-EL10-WZ000470018400HLMP-EL08-XZ400**620018400 Amber 590HLMP-EL08-XZ000620018400HLMP-EL08-XZK00*620018400HLMP-EL08-XY000620013800HLMP-EL08-XYK00*620013800HLMP-EL08-X1K00*620024100HLMP-EL08-X1000HLMP-EL10-X1000620024100 6°[5]HLMP-EJ08-WZ000HLMP-EJ10-WZ000470018400 Orange 605HLMP-EJ08-X1000HLMP-EJ10-X1000620024100HLMP-EJ08-Y2000HLMP-EJ10-Y2000800031000HLMP-EH08-UX000HLMP-EH10-UX000275010700HLMP-EH08-VY000HLMP-EH10-VY000360013800 Red-Orange 615HLMP-EH08-WZ000HLMP-EH10-WZ000470018400HLMP-EH08-X1000HLMP-EH10-X1000620024100HLMP-EH08-Y2000HLMP-EH10-Y2000800031000HLMP-EG08-VW00036008300HLMP-EG08-VY000HLMP-EG10-VY000360013800HLMP-EG08-WZ000HLMP-EG10-WZ000470018400 Red 626HLMP-EG08-X1000HLMP-EG10-X1000620024100HLMP-EG08-YZ000800018400HLMP-EG08-Y1000800024100HLMP-EG08-Y2000HLMP-EG10-Y2000800031000 Notes:1. The luminous intensity is measured on the mechanical axis of the lamp package.2.The optical axis is closely aligned with the package mechanical axis.3. The dominant wavelength, λd, is derived from the CIE Chromaticity Diagram and represents the color of the lamp.4. θ1/2 is the off-axis angle where the luminous intensity is one half the on-axis intensity.5.The intensity of narrow viewing angle lamps is measured at the intensity peak.Part numbers in bold are recommended for new designs.*HLMP-xLxx-xxK00 are selected to amber color bins 2 and 4 only.Device Selection Guide (Continued)TypicalViewing Color and Luminous Angle Dominant Lamps Without Standoffs Lamps With Standoffs Intensity Iv (mcd) [1,2] 2θ1/2Wavelength on Leads on Leads@ 20 mA (Deg.)[4](nm), Typ.[3] (Outline Drawing A)(Outline Drawing B)Min.Max.HLMP-EL15-PS000HLMP-EL17-PS0007652900HLMP-EL15-QR00010002200HLMP-EL15-QRK00*10002200HLMP-EL15-QS00010002900 Amber 590HLMP-EL15-QS400**10002900HLMP-EL15-QSK00*10002900HLMP-EL15-QT000HLMP-EL17-QT00010003700 15°HLMP-EL15-QTK00*10003700HLMP-EL15-RU000HLMP-EL17-RU00013004800HLMP-EJ15-PS0007652900 Orange 605HLMP-EJ15-RU000HLMP-EJ17-RU00013004800HLMP-EJ15-SV000HLMP-EJ17-SV00016506300 Red-Orange 615HLMP-EH15-QT000HLMP-EH17-QT00010003700HLMP-EH15-RU000HLMP-EH17-RU00013004800HLMP-EG15-PS0007652900 Red 626HLMP-EG15-QT000HLMP-EG17-QT00010003700HLMP-EG15-RU000HLMP-EG17-RU00013004800HLMP-EL24-MQ0004501730HLMP-EL24-NR000HLMP-EL26-NR0005902200HLMP-EL24-PS000HLMP-EL26-PS0007652900HLMP-EL24-PSK00*7652900HLMP-EL24-PR400**7652200HLMP-EL24-PQK00*7651730 Amber 590HLMP-EL24-QR00010002200HLMP-EL24-QRK00*10002200 23°HLMP-EL24-QS00010002900HLMP-EL24-QSK00*10002900HLMP-EL24-QS400**10002900HLMP-EL24-QT000HLMP-EL26-QT00010003700HLMP-EL24-QTK00*10003700 Notes:1. The luminous intensity is measured on the mechanical axis of the lamp package.2.The optical axis is closely aligned with the package mechanical axis.3. The dominant wavelength, λd, is derived from the CIE Chromaticity Diagram and represents the color of the lamp.4. θ1/2 is the off-axis angle where the luminous intensity is one half the on-axis intensity.5.The intensity of narrow viewing angle lamps is measured at the intensity peak.Device Selection Guide (Continued)TypicalViewing Color and Luminous Angle Dominant Lamps Without Standoffs Lamps With Standoffs Intensity Iv (mcd) [1,2] 2θ1/2Wavelength on Leads on Leads@ 20 mA (Deg.)[4](nm), Typ.[3] (Outline Drawing A)(Outline Drawing B)Min.Max.Orange 605HLMP-EJ24-QT000HLMP-EJ26-QT00010003700HLMP-EJ24-RU000HLMP-EJ26-RU00013004800HLMP-EH26-PS0007652900 Red-Orange 615HLMP-EH24-QT000HLMP-EH26-QT00010003700 23ºHLMP-EH24-RU000HLMP-EH26-RU00013004800HLMP-EG24-PS000HLMP-EG26-PS0007652900 Red 626HLMP-EG24-QT000HLMP-EG26-QT00010003700HLMP-EG24-RU000HLMP-EG26-RU00013004800HLMP-EL30-MQ000HLMP-EL32-MQ0004501730HLMP-EL30-NR000HLMP-EL32-NR0005902200HLMP-EL30-PQ0007651730HLMP-EL30-PQK00*7651730 Amber 590HLMP-EL30-PR0007652200HLMP-EL30-PR400**7652200HLMP-EL30-PRK00*7652200HLMP-EL30-PS000HLMP-EL32-PS0007652900HLMP-EL30-PSK00*7652900 30°HLMP-EJ30-MQ0004501730 Orange 605HLMP-EJ30-NR000HLMP-EJ32-NR0005902200HLMP-EJ30-PS000HLMP-EJ32-PS0007652900HLMP-EH30-MQ000HLMP-EH32-MQ0004501730 Red-Orange 615HLMP-EH30-NR000HLMP-EH32-NR0005902200HLMP-EH30-PS000HLMP-EH32-PS0007652900HLMP-EG30-KN0002701010HLMP-EG30-MQ000HLMP-EG32-MQ0004501730HLMP-EG30-NQ0005901730HLMP-EG30-NR000HLMP-EG32-NR0005902200 Red 626HLMP-EG30-PQ0007651730HLMP-EG30-PR0007652200HLMP-EG30-PS000HLMP-EG32-PS0007652900 Notes:1. The luminous intensity is measured on the mechanical axis of the lamp package.2.The optical axis is closely aligned with the package mechanical axis.3. The dominant wavelength, λd, is derived from the CIE Chromaticity Diagram and represents the color of the lamp.4. θ1/2 is the off-axis angle where the luminous intensity is one half the on-axis intensity.5.The intensity of narrow viewing angle lamps is measured at the intensity peak.Part Numbering SystemHLMP-x x xx-x x x xxMechanical Options00: Bulk PackagingDD: Ammo PackYY: Flexi-Bin; Bulk PackagingZZ: Flexi-Bin; Ammo PackColor Bin Selections0: No color bin limitation4: Amber color bin 4 onlyK: Amber color bins 2 and 4 onlyMaximum Intensity Bin0: No Iv bin limitationMinimum Intensity BinViewing Angle & Lead Stand Offs08: 6 deg without lead stand offs10: 6 deg with lead stand offs15: 15 deg without lead stand offs17: 15 deg with lead stand offs24: 23 deg without lead stand offs26: 23 deg with lead stand offs30: 30 deg without lead stand offs32: 30 deg with lead stand offsColorG: 626 nm RedH: 615 nm Red-OrangeJ: 605 nm OrangeL: 590 nm AmberPackageE: 5 mm RoundNOTES:1. ALL DIMENSIONS ARE IN MILLIMETERS (INCHES).2. LEADS ARE MILD STEEL, SOLDER DIPPED.3. TAPERS SHOWN AT TOP OF LEADS (BOTTOM OF LAMP PACKAGE) INDICATE AN EPOXY MENISCUS THAT MAY EXTEND ABOUT 1 mm (0.040 in.) DOWN THE LEADS.4. RECOMMENDED PC BOARD HOLE DIAMETERS:• LAMP PACKAGE A WITHOUT STAND-OFFS: FLUSH MOUNTING AT BASE OF LAMP PACKAGE = 1.143/1.067 (0.044/0.042).• LAMP PACKAGE B WITH STAND-OFFS: MOUNTING AT LEAD STAND-OFFS = 0.965/0.889 (0.038/0.035).5. FOR DOME HEIGHTS ABOVE LEAD STAND-OFF SEATING PLANE, d, LAMP PACKAGE B, SEE TABLE.BPackage DimensionsA(0.039)(0.039)PART NO.d HLMP-XX1012.37 ± 0.25 (0.487 ± 0.010)HLMP-XX1712.42 ± 0.25 (0.489 ± 0.010)HLMP-XX2612.52 ± 0.25 (0.493 ± 0.010)HLMP-XX3211.96 ± 0.25 (0.471 ± 0.010)Electrical/Optical Characteristics at T A = 25°CParameter SymbolMin.Typ.Max.UnitsTest Conditions Forward VoltageI F = 20 mAAmber (λd = 590 nm) 2.02Orange (λd = 605 nm)V F 1.98 2.4VRed-Orange (λd = 615 nm) 1.94Red (λd = 626 nm) 1.90Reverse Voltage V R 520VI F = 100 µAPeak Wavelength:Peak of Wavelength of Amber (λd = 590 nm)592Spectral Distribution Orange (λd = 605 nm)λPEAK 609nmat I F = 20 mARed-Orange (λd = 615 nm)621Red (λd = 626 nm)635Spectral Halfwidth∆λ1/217nmWavelength Width at Spectral Distribution 1/2 Power Point at I F = 20 mASpeed of Response τs 20ns Exponential Time Constant, e -t/τCapacitanceC 40pF V F = 0, f = 1 MHzThermal Resistance R θJ-PIN240°C/WLED Junction-to-Cathode LeadLuminous Efficacy [1]Emitted LuminousAmber (λd = 590 nm)480Power/Emitted Radiant Orange (λd = 605 nm)ηv370lm/WPowerRed-Orange (λd = 615 nm)260Red (λd = 626 nm)150Note:Absolute Maximum Ratings at T A = 25°CDC Forward Current [1,2,3]............................................................50 mA Peak Pulsed Forward Current [2,3]..............................................100 mA Average Forward Current [3].........................................................30 mA Reverse Voltage (I R = 100 µA).........................................................5 V LED Junction Temperature..........................................................130°C Operating Temperature ..............................................-40°C to +100°C Storage Temperature ..................................................-40°C to +120°C Dip/Drag Soldering Temperature...........................260°C for 6 seconds Through-the-Wave Preheat Temperature......................................145°C Through-the-Wave Solder Temperature.................245°C for 3 seconds [1.59 mm (0.060 in.) below seating plane]Notes:1. Derate linearly as shown in Figure 4.2. For long term performance with minimal light output degradation, drive currentsbetween 10 mA and 30 mA are recommended. For more information on recommended drive conditions, please refer to Application Brief I-024 (5966-3087E).3. Operating at currents below 1 mA is not recommended. Please contact your local representative for further information.sFigure 2. Forward Current vs.Forward Voltage.Figure 3. Relative Luminous Intensity vs. Forward Current.Figure 4. Maximum Forward Current vs. Ambient Temperature. Derating Based on T JMAX = 130°C.Figure 1. Relative Intensity vs. Peak Wavelength.I F – F O R W A R D C U R R E N T – m AT A – AMBIENT TEMPERATURE – °CR E L A T I V E I N T E N S I T Y – %1000θ – ANGULAR DISPLACEMENT – DEGREES8060507020-20-15103040-1051015202590-25-5WAVELENGTH – nmR E L A T I V E I N T E N S I T YR E L A T I V E L U M I N O U S I N T E N S I T Y (N O R M A L I Z E D A T 20 m A )00I F – DC FORWARD CURRENT – mA 403.02.01.51.00.520602.5C U R R E NT – m AV F – FORWARD VOLTAGE – VBin Name Min.Max.K 310400L 400520M 520680N680880P 8801150Q 11501500R 15001900S 19002500T 25003200U 32004200V 42005500W 55007200X 72009300Y 930012000Z 12000160001160002100022100027000Intensity Bin Limits (mcd at 20 mA)Tolerance for each bin limit is ± 15%.Bin Name Min.Max.1584.5587.02587.0589.54589.5592.06592.0594.5Amber Color Bin Limits (nm at 20 mA)Tolerance for each bin limit is ± 0.5 nm.Note:1.Bin categories are established for classification of products. Products Figure 7. Representative Spatial Radiation Pattern for 23° Viewing Angle Lamps.R E L A T I V E I N T E N S I T Y – %1000θ – ANGULAR DISPLACEMENT – DEGREES806050702010304090-20-15-10510152025-25-5R E L A T I V E I N T E N S I T Y – %1000θ – ANGULAR DISPLACEMENT – DEGREES806050702010304090-20-15-10510152025-25-5R E L A T I V E I N T E N S I T Y – %1000θ – ANGULAR DISPLACEMENT – DEGREES806050702010304090-20-15-10510152025-25-5Figure 6. Representative Spatial Radiation Pattern for 15° Viewing Angle Lamps.Data subject to change.Copyright © 2001 Agilent Technologies, Inc. August 13, 2001。
HSMP-3862中文资料
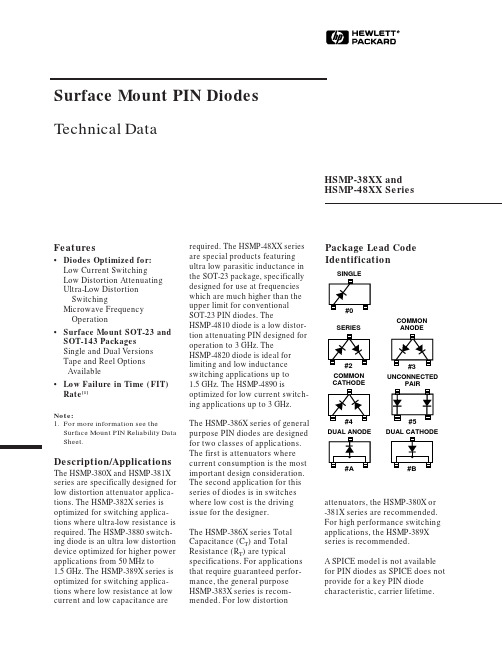
Surface Mount PIN Diodes Technical DataFeatures•Diodes Optimized for:Low Current SwitchingLow Distortion AttenuatingUltra-Low DistortionSwitchingMicrowave FrequencyOperation•Surface Mount SOT-23 and SOT-143 PackagesSingle and Dual VersionsTape and Reel OptionsAvailable•Low Failure in Time (FIT) Rate[1]Note:1.For more information see theSurface Mount PIN Reliability Data Sheet.HSMP-38XX andHSMP-48XX SeriesPackage Lead CodeIdentificationrequired. The HSMP-48XX seriesare special products featuringultra low parasitic inductance inthe SOT-23 package, specificallydesigned for use at frequencieswhich are much higher than theupper limit for conventionalSOT-23 PIN diodes. TheHSMP-4810 diode is a low distor-tion attenuating PIN designed foroperation to 3 GHz. TheHSMP-4820 diode is ideal forlimiting and low inductanceswitching applications up to1.5GHz. The HSMP-4890 isoptimized for low current switch-ing applications up to 3 GHz.The HSMP-386X series of generalpurpose PIN diodes are designedfor two classes of applications.The first is attenuators wherecurrent consumption is the mostimportant design consideration.The second application for thisseries of diodes is in switcheswhere low cost is the drivingissue for the designer.The HSMP-386X series TotalCapacitance (C T) and TotalResistance (R T) are typicalspecifications. For applicationsthat require guaranteed perfor-mance, the general purposeHSMP-383X series is recom-Description/Applications The HSMP-380X and HSMP-381X series are specifically designed for low distortion attenuator applica-tions. The HSMP-382X series is optimized for switching applica-tions where ultra-low resistance is required. The HSMP-3880 switch-ing diode is an ultra low distortion device optimized for higher power applications from 50 MHz to1.5GHz. The HSMP-389X series is optimized for switching applica-tions where low resistance at low attenuators, the HSMP-380X or -381X series are recommended. For high performance switching applications, the HSMP-389X series is recommended.A SPICE model is not available for PIN diodes as SPICE does not provide for a key PIN diode characteristic, carrier lifetime.Absolute Maximum Ratings [1] T A = 25°CSymbol ParameterUnits Absolute Maximum I f Forward Current (1 ms Pulse)Amp 1P t Total Device Dissipation mW [2]250P iv Peak Inverse Voltage —Same as V BRT j Junction Temperature °C 150T STGStorage Temperature°C-65 to 150Notes:1.Operation in excess of any one of these conditions may result in permanent damage to this device.2.CW Power Dissipation at T LEAD = 25°C. Derate to zero at maximum rated temperature.PIN Switching DiodesElectrical Specifications T A = 25°CNearest Maximum Equivalent Minimum Maximum Maximum Shunt Mode Part Package Axial Lead Breakdown Series Total Harmonic Number Marking LeadPart No.Voltage Resistance Capacitance Distortion HSMP-Code [1]Code Configuration 5082-V BR (V)R S (Ω)C T (pF)Hmd (dBc)3820F00Single 3188500.6*0.8*—3822F22Series3823F33Common Anode 3824F44Common Cathode 3880S00Single—100 6.50.40–553890G00Single —1002.50.30**—3892G22Series3893G33Common Anode 3894G44Common Cathode 3895G55Unconnected PairTest ConditionsV R = V BR I F = 5 mA V R = 50 V 2 f o, Z o = 50 W Measure f = 100 MHz f = 1 MHz f o = 400 MHz I R ≤ 10 µA I F = 10 mA*V R = 20 V*P in = +30 dBm V R = 5 V**0 V biasPIN Attenuator DiodesElectrical Specifications T A = 25°C (Each Diode)NearestEquivalent Minimum Maximum Maximum Minimum Maximum Part Package Axial Lead Breakdown Series Total High Low Number Marking LeadPart No.Voltage Resistance Capacitance Resistance Resistance HSMP-Code [1]Code Configuration 5082-V BR (V)R S (Ω)C T (pF)R H (Ω)R L (Ω)3800D00Single 30801002.00.37100083802D22Series3804D44Common Cathode 3810E00Single 3081100 3.00.351500103812E22Series3813E33Common Anode 3814E44Common CathodeTest ConditionsV R = V BR I F = 100 mA V R = 50 V I F = 0.01 mA I F = 20 mA Measure f = 100 MHz f = 1 MHz f = 100 MHz f= 100 MHzI R ≤ 10 µAPIN General Purpose Diodes, Electrical Specifications T A = 25°CNearestEquivalent Minimum Maximum Maximum Part Package Axial Lead Breakdown Series Total Number Marking Lead Part No.Voltage Resistance Capacitance HSMP-Code[1]Code Configuration5082-V BR (V)R S (Ω)C T (pF) 3830K00Single3077200 1.50.3 3832K22Series3833K33Common Anode3834K44Common CathodeTest Conditions V R = V BR I F = 100 mA V R = 50 VMeasure f = 100 MHz f = 1 MHzI R≤ 10 mAHigh Frequency (Low Inductance, 500 MHz – 3 GHz) PIN Diodes, Electrical Specifications T A = 25°CMinimum Maximum Typical Maximum TypicalBreak-Series Total Total Total Part Package down Resis-Capaci-Capaci-Induc-Number Marking Lead Config-Voltage tance tance tance tance Appli-HSMP-Code Code uration V BR (V)R S (Ω)C T (pF)C T (pF)L T (nH)cation 4810EB B Dual100 3.00.350.4 1.0Attenu-Cathode ator 4820FA A Dual Anode500.6*0.75* 1.0 1.0*Limiter 4890GA A Dual Anode100 2.5**0.330.375 1.0SwitchV R = V BR I F = 100 mA V R = 50 V V R = 50 V f = 500 MHz –Measure I F = 10 mA* f = 1 MHz f = 1 MHz 3 GHzI R≤ 10 µA I F = 5 mA**V R = 20 V*V R = 0 V V R = 20 V*PIN General Purpose Diodes, Typical Specifications T A = 25°CCode Minimum Typical Series Typical Total Part Number Marking Lead Breakdown Resistance Capacitance HSMP-Code[1]Code Configuration Voltage V BR (V)R S (Ω)C T (pF)3860L00Single50 3.0/1.5*0.203862L22Series3863L33Common Anode3864L44Common CathodeTest Conditions V R = V BR I F = 10 mA V R = 50 VMeasure f = 100 MHz f = 1 MHzI R≤ 10 µA*I F = 100 mATypical Parameters at T A = 25°CPart Number Series Resistance Carrier Lifetime Reverse Recovery Time Total Capacitance HSMP-R S (Ω)τ (ns)T rr (ns)C T (pF)380X5518005000.32 @ 50 V381X7515003000.27 @ 50 V382X 1.570*70.60 @ 20 V383X20500800.20 @ 50 V388X 3.825005500.30 @ 50 V389X 3.8200*–0.20 @ 5 V Test Conditions I F = 1 mA I F = 50 mA V R = 10 Vf = 100 MHz I R = 250 mA I F = 20 mAI F = 10 mA*I F = 10 mA*90% RecoveryI R = 6 mA*Typical Parameters at T A = 25°C (unless otherwise noted), Single DiodeFigure 2. RF Capacitance vs. Reverse Bias, HSMP-3830 Series.0.150.300.250.200.350.400.45T O T A L C A P A C I T A N C E (p F )REVERSE VOLTAGE (V)Figure 1. RF Capacitance vs. Reverse Bias, HSMP-3810 Series.Figure 3. Resistance at 25°C vs. Forward Bias Current.0.150.300.250.200.35T O T A L C A P A C I T A N C E (p F )REVERSE VOLTAGE (V)R E S I S T A N C E (O H M S )I F – FORWARD BIAS CURRENT (mA)0.010.11101000.010.1110100R F R E S I S T A N C E (O H M S )I F – FORWARD BIAS CURRENT (mA)R F R E S I S T A N C E (O H M S )0.010.1110100I F – FORWARD BIAS CURRENT (mA)Figure 5. RF Resistance vs. Forward Bias Current for HSMP-3810/HSMP-4810.V R – REVERSE VOLTAGE (V)C A P A C I T A N C E (p F )Figure 6. Capacitance vs. Reverse Voltage.Figure 4. RF Resistance vs. Forward Bias Current for HSMP-3800.100010010DIODE RF RESISTANCE (OHMS)Figure 7. 2nd Harmonic Input Intercept Point vs. Diode RFResistance for Attenuator Diodes.I N P U T I N T E R C E P T P O I N T (d B m )12011511010510095908511030I F – FORWARD BIAS CURRENT (mA)Figure 8. 2nd Harmonic Input Intercept Point vs. Forward Bias Current for Switch Diodes.I N P U T I N T E R C E P T P O I N T (d B m )FORWARD CURRENT (mA)Figure 9. Reverse Recovery Time vs. Forward Current for Various Reverse Voltages. HSMP-3820 Series.T r r – R E V E R S E R E C O V E R Y T I M E (n s )110100102030V R = 2V V R = 5VV R = 10VHSMP-382XTypical Parameters (continued)100010010102030T r r - R E V E R S E R E C O V E R Y T I M E (n S )FORWARD CURRENT (mA)Figure 10. Reverse Recovery Time vs. Forward Current for Various Reverse Voltage. HSMP-3830 Series.HSMP-3830V R = 5VV R = 10V V R = 20VR E V E R S E R E C O V E R Y T I M E (n S )FORWARD CURRENT (mA)Figure 11. Typical Reverse Recovery Time vs. Reverse Voltage. HSMP-3880 Series.1020152530T R R - R E V E R S E R E C O V E R Y T I M E (n S )FORWARD CURRENT (mA)Figure 12. Typical Reverse Recovery Time vs. Reverse Voltage. HSMP-3890 Series.1001010.10.01I F – F O R W A R D C U R R E N T (m A )I F – F O R W A R D C U R R E N T (m A )V F – FORWARD VOLTAGE (mA)Figure 14. Forward Current vs. Forward Voltage. HSMP-3810 and HSMP-4810 Series.V F – FORWARD VOLTAGE (mA)Figure 15. Forward Current vs. Forward Voltage. HSMP-3820 and HSMP-4820 Series.1001010.10.01I F – F O R W A R D C U R R E N T (m A )V F – FORWARD VOLTAGE (mA)Figure 16. Forward Current vs.Forward Voltage. HSMP-3830 Series.00.20.40.60.81.01.2I F – F O R W A R D C U R R E N T (m A )V F – FORWARD CURRENT (mA)Figure 17. Forward Current vs.Forward Voltage. HSMP-3880 Series.0.20.40.60.81.01.2V F – FORWARD VOLTAGE (mA)Figure 18. Forward Current vs. Forward Voltage. HSMP-3890 and HSMP-4890 Series.Typical Parameters (continued)Figure 19. Typical RF Resistance vs. Forward Bias Current for HSMP-3860.Figure 20. Forward Current vs. Forward Voltage for HSMP-3860.Figure 21. Typical Capacitance vs. Reverse Bias for HSMP-3860.10001R E S I S T A N C E (O HM S )BIAS CURRENT (mA)10100I F – F O R W A R D C U R R E N T (m A )V F – FORWARD VOLTAGE (V)0200.515C T – C A P A C I T A N C E (p F )V R – REVERSE VOLTAGE (V)0.20.41050.10.30.12 pF** Measured at -20 V C p 0.08 pFR j = 12ΩI 0.9C T = C P + C jI = Forward Bias Current in mAEquivalent Circuit ModelHSMS-3860Typical Applications for Multiple Diode ProductsRF COMMONRF 1RF 1Figure 24. Switch Using Both Positive and Negative Bias Current.Figure 25. Very High Isolation SPDT Switch, Dual Bias.Typical Applications for Multiple Diode Products (continued)INPUT RF IN/OUTFigure 26. Four Diode π Attenuator.Figure 27. High Isolation SPST Switch (Repeat Cells as Required).VOLTAGEBIASFigure 28. Power Limiter Using HSMP-3822Diode Pair.Typical Applications for HSMP-48XX Low Inductance SeriesFigure 29. Internal Connections.HSMP-4820 & HSMP-4890HSMP-48100.5 nH*0.8pF TYPICAL FOR HSMP-3820Figure 30. Equivalent Circuit.*0.8 pF TYPICAL FOR HSMP-3820Figure 32. Equivalent Circuit.Figure 31. Circuit Layout.Microstrip SeriesConnection for HSMP-48XX SeriesIn order to take full advantage of the low inductance of the HSMP-48XX series when using them in series application,both lead 1 and lead 2 should beconnected together, as shown above.Microstrip Shunt Connections for HSMP-48XX SeriesIn the diagram above, the center conductor of themicrostrip line is interrupted and leads 1 and 2 of theHSMP-38XX series diode are placed across the resulting gap. This forces the 0.5 nH lead inductance of leads 1 and 2 to appear as part of a low pass filter, reducing the shunt parasitic inductance andincreasing the maximumavailable attenuation. The 0.3 nH of shunt inductance external to the diode is created by the via holes, and is a good estimate for 0.032" thick material.Co-Planar Waveguide Shunt Connection for HSMP-48XX SeriesCo-Planar waveguide, with ground on the top side of the printed circuit board, is shownin the diagram above. Since it eliminates the need for via holes to ground, it offers lower shunt parasitic inductance and higher maximum attenuation whencompared to a microstrip circuit.GROUND BY TWOVIA HOLES*0.8 pF TYPICAL FOR HSMP-4820Figure 34. Equivalent Circuit.Figure 33. Circuit Layout.*0.8 pF TYPICAL FOR HSMP-4820Figure 36. Equivalent Circuit.Figure 35. Circuit Layout.11Package DimensionsOutline 23 (SOT-23)PC Board FootprintsSOT-23Package CharacteristicsLead Material......................................................................................Alloy 42Lead Finish............................................................................Tin-Lead 85-15%Maximum Soldering Temperature..............................260°C for 5 seconds Minimum Lead Strength..........................................................2 pounds pull Typical Package Inductance ..................................................................2 nH Typical Package Capacitance ..............................0.08 pF (opposite leads)SOT-143Outline 143 (SOT-143)SIDE VIEWEND VIEWDIMENSIONS ARE IN MILLIMETERS (INCHES)DIMENSIONS ARE IN MILLIMETERS (INCHES)PACKAGE MARKING/go/rfFor technical assistance or the location of your nearest Hewlett-Packard salesoffice, distributor or representative call:Americas/Canada: 1-800-235-0312 or 408-654-8675Far East/Australasia: Call your local HP sales office.Japan: (81 3) 3335-8152Europe: Call your local HP sales office.Data subject to change.Copyright © 1999 Hewlett-Packard Co.Obsoletes 5968-3435E5968-5439E (6/99)Profile Option Descriptions-BLK = Bulk-TR1 = 3K pc. Tape and Reel, Device Orientation; See Figures 37 and 38-TR2 = 10K pc. Tape and Reel, Device Orientation; See Figures 37 and 38Tape and Reeling conforms to Electronic Industries RS-481, “Taping of Surface Mounted Components for Automated Placement.”Ordering InformationSpecify part number followed by option under. For example:H SMP -38XX -XXXBulk or Tape and Reel OptionPart NumberSurface Mount PIN Diode Hewlett-PackardUSER FEEDEND VIEWTOP VIEW Figure 37. Options -TR1, -TR2 for SOT-23 Packages.Figure 38. Options -TR1, -TR2 for SOT-143 Packages.END VIEWTOP VIEW。
HLMP-2735中文资料

LED Light Bars Technical DataFeatures•Large Bright, Uniform Light Emitting Areas•Choice of Colors •Categorized for Light Output •Yellow and Green Categorized for Dominant Wavelength•Excellent ON-OFF Contrast •X-Y Stackable•Flush Mountable•Can be Used with Panel and Legend Mounts• Light Emitting Surface Suitable for Legend Attachment per Application Note 1012•HLCP-X100 Series Designed for Low Current Operation •Bicolor Devices Available Applications•Business MachineMessage Annunciators •Telecommunications Indicators•Front Panel Process Status Indicators•PC Board Identifiers•Bar Graphs DescriptionThe HLCP-X100 and HLMP-2XXXseries light bars are rectangularlight sources designed for avariety of applications where alarge bright source of light isrequired. These light bars areconfigured in single-in-line anddual-in-line packages that containeither single or segmented lightemitting areas. The AlGaAs RedHLCP-X100 series LEDs usedouble heterojunction AlGaAs ona GaAs substrate. The HERHLMP-2300/2600 and YellowHLMP-2400/2700 series LEDshave their p-n junctions diffusedinto a GaAsP epitaxial layer on aGaP substrate. The Green HLMP-2500/2800 series LEDs use aliquid phase GaP epitaxial layeron a GaP substrate. The bicolorHLMP-2900 series use acombination of HER/Yellow orHER/Green LEDs.HLCP-A100, -B100, -C100,-D100, -E100, -F100, -G100,-H100HLMP-2300, -2350, -2400,-2450, -2500, -2550, -2600,-2620, -2635, -2655, -2670,-2685, -2700, -2720, -2735,-2755, -2770, -2785, -2800,-2820, -2835, -2855, -2870,-2885, -2950, -2965Selection GuideLight Bar Part Number Corresponding Size ofPackage Panel and HLCP-HLMP-Light Emitting AreasOutlineLegend Mount Part No. HLMP-AlGaAs HER Yellow Green A1002300240025008.89 mm x 3.81 mm 1A 2599(.350 in. x .150 in.)B10023502450255019.05 mm x 3.81 mm 1B 2598(.750 in. x .150 in.)D1002600270028008.89 mm x 3.81 mm 2D 2898(.350 in. x .150 in.)E1002620272028208.89 mm x 3.81 mm 4E 2899(.350 in. x .150 in.)F100263527352835 3.81 mm x 19.05 mm 2F 2899(.150 in. x .750 in.)C1002655275528558.89 mm x 8.89 mm 1C 2898(.350 in. x .350 in.)G1002670277028708.89 mm x 8.89 mm 2G 2899(.350 in. x .350 in.)H1002685278528858.89 mm x 19.05 mm 1H 2899(.350 in. x .750 in.)295029508.89 mm x 8.89 mm Bicolor I 2898(.350 in. x .350 in.)296529658.89 mm x 8.89 mm BicolorI2898(.350 in. x .350 in.)Number of Light Emitting AreasPart Numbering SystemHLCP- xx xx-xx x xxHLMP-xx xx-xx x xxMechanical Options[1]00: No mechanical optionColor Bin Options[1,2]0: No color bin limitationB: Color bins 2 & 3 (applicable for yellow devices only)C: Color bins 3 & 4 only (applicable for green devices only)Maximum Intensity Bin[1,2]0: No maximum intensity bin limitationMinimum Intensity Bin[1,2]0: No minimum intensity bin limitationDevice Specific Configuration[1]Refer to respective data sheetColor[1]x1: AlGaAs Red (applicable for HLCP-x100 only)23: High Efficiency Red24: Yellow25: Green26: High Efficiency Red27: Yellow28: Green29: Bicolor (High Efficiency Red/Yellow) OR (High Efficiency Red/Green) Notes:1. For codes not listed in the figure above, please refer to the respective data sheet or contact your nearest Agilent representativefor details.2. Bin options refer to shippable bins for a part-number. Color and Intensity Bins are typically restricted to 1 bin per tube(exceptions may apply). Please refer to respective data sheet for specific bin limit information.Package DimensionsNOTES:1. DIMENSIONS IN MILLIMETRES (INCHES). TOLERANCES ±0.25 mm (±0.010 IN.) UNLESS OTHERWISE INDICATED.2. FOR YELLOW AND GREEN DEVICES ONLY.Internal Circuit DiagramsAbsolute Maximum RatingsHER Yellow GreenAlGaAs Red HLMP-2300/HLMP-2400/HLMP-2500/ ParameterHLCP-X1002600/29XX2700/29502800/2965Series Series Series Series Average Power Dissipated per LED Chip37 mW[1]135 mW[2]85 mW[3]135 mW[2] Peak Forward Current per LED Chip45 mA[4]90 mA[5]60 mA[5]90 mA[5] Average Forward Current per LED Chip15 mA25 mA20 mA25 mADC Forward Current per LED Chip15 mA[1]30 mA[2]25 mA[3]30 mA[2] Reverse Voltage per LED Chip 5 V 6 V[6]Operating Temperature Range–20°C to +100°C[7]–40°C to +85°C–20°C to +85°C Storage Temperature Range –40°C to +85°CWave Soldering Temperature250°C for 3 seconds1.6 mm (1/16 inch) below BodyNotes:1.Derate above 87°C at 1.7 mW/°C per LED chip. For DC operation, derate above 91°C at 0.8 mA/°C.2.Derate above 25°C at 1.8 mW/°C per LED chip. For DC operation, derate above 50°C at 0.5 mA/°C.3.Derate above 50°C at 1.8 mW/°C per LED chip. For DC operation, derate above 60°C at 0.5 mA/°C.4.See Figure 1 to establish pulsed operation. Maximum pulse width is 1.5 mS.5.See Figure 6 to establish pulsed operation. Maximum pulse width is 2 mS.6.Does not apply to bicolor parts.7.For operation below –20°C, contact your local Agilent sales representative.Electrical/Optical Characteristics at T A = 25°CAlGaAs Red HLCP-X100 SeriesParameter HLCP-Symbol Min.Typ.Max.Units Test ConditionsA100/D100/E100I V37.5mcd I F = 3 mA Luminous Intensityper Lighting Emitting B100/C100/F100/G100615mcdArea[1]H1001230mcdPeak WavelengthλPEAK645nmDominant Wavelength[2]λd637nmForward Voltage per LED V F 1.8 2.2V I F = 20 mA Reverse Breakdown Voltage per LED V R515V I R = 100 µA Thermal Resistance LED Junction-to-Pin RθJ-PIN250°C/W/LEDParameter HLMP-Symbol Min.Typ.Max.Units Test Conditions2400/2700/2720IV 620mcd IF= 20 mALuminous Intensityper Lighting Emitting2450/2735/2755/2770/2950[3]1338mcd Area[1]27852670mcdPeak WavelengthλPEAK583nmDominant Wavelength[2]λd585nmForward Voltage per LED VF 2.1 2.6V IF= 20 mAReverse Breakdown Voltage per LED[5]VR 615V IR= 100 µAThermal Resistance LED Junction-to-Pin RθJ-PIN 150°C/W/LEDHigh Efficiency Red HLMP-2300/2600/2900 SeriesParameter HLMP-Symbol Min.Typ.Max.Units Test Conditions2300/2600/2620IV 623mcd IF= 20 mALuminous Intensityper Lighting Emitting2350/2635/2655/2670/2950[3]1345mcd Area[1]2965[4]1945mcd26852280mcdPeak WavelengthλPEAK635nmDominant Wavelength[2]λd626nmForward Voltage per LED VF 2.0 2.6V IF= 20 mAReverse Breakdown Voltage per LED[5]VR 615V IR= 100 µAThermal Resistance LED Junction-to-Pin RθJ-PIN 150°C/W/LEDYellow HLMP-2400/2700/2950 SeriesHigh Performance Green HLMP-2500/2800/2965 SeriesParameter HLMP-Symbol Min.Typ.Max.Units Test Conditions2500/2800/2820IV 525mcd IF= 20 mALuminous Intensityper Lighting Emitting2550/2835/2855/28701150mcd Area[1]2965[4]2550mcd288522100mcdPeak WavelengthλPEAK565nmDominant Wavelength[2]λd572nmForward Voltage per LED VF 2.2 2.6V IF= 20 mAReverse Breakdown Voltage per LED[5]VR 615V IR= 100 µAThermal Resistance LED Junction-to-Pin RθJ-PIN 150°C/W/LEDNotes:1.These devices are categorized for luminous intensity. The intensity category is designated by a letter code on the side of the package.2.The dominant wavelength, λd , is derived from the CIE chromaticity diagram and is the single wavelength which defines the color of thedevice. Yellow and Green devices are categorized for dominant wavelength with the color bin designated by a number code on the side of the package.3.This is an HER/Yellow bicolor light bar. HER electrical/optical characteristics are shown in the HER table. Yellow electrical/opticalcharacteristics are shown in the Yellow table.4.This is an HER/Green bicolor light bar. HER electrical/optical characteristics are shown in the HER table. Green electrical/opticalcharacteristics are shown in the Green table.5.Does not apply to HLMP-2950 or HLMP-2965.Figure 1. Maximum Allowable Peak Current vs. Pulse Duration.Figure 4. Forward Current vs. Forward Voltage.Figure 5. Relative Luminous Intensity vs. DC Forward Current.AlGaAs RedFor a detailed explanation on the use of data sheet information and recommended soldering procedures,see Application Notes 1005, 1027, and 1031.HER, Yellow, GreenIntensity Bin Limits (mcd)HLMP-2300/2600/2620 Annunciators (.2 x .4 HER/AlGaAs), HLCP-A100/D100/E100IV Bin Category Min.Max.A 3.00 5.60B 4.508.20C 6.8012.10D10.1018.50E15.3027.80F22.8045.50G36.9073.80Notes:1. Minimum category A for Red L/C AlGaAs (-A100/-D100/-E100).2. Minimum category C for HER (-2300/-2600/-2620).HLMP-2350/2635/2655/2670 Annunciators (.2 x .8 HER/AlGaAs), HLCP-B100/C100/F100/G100 (.4 x .4 HER/AlGaAs)IV Bin Category Min.Max.A 5.4010.90B9.0016.00C13.1024.00D19.7036.10E29.6054.20F44.9088.80G71.90143.80Notes:1. Minimum category A for Red L/C AlGaAs (-B100/-C100/-F100/-G100).2. Minimum category C for HER (-2350/-2635/-2670).HLMP-2685/HLCP-H100 Annunciators (.4 x .8 HER/AlGaAs) IV Bin Category Min.Max.A10.8022.00B18.0027.10C22.0040.80D33.3061.10E50.0091.80F75.10150.00G121.70243.40Notes:1. Minimum category A for Red L/C AlGaAs (-H100).2. Minimum category C for HER (-2685).HLMP-2400/2700/2720 Annunciators (.2 x .4 Yellow)IV Bin Category Min.Max.C 6.1011.20D9.2016.80E13.8025.30F20.7041.40G33.6067.20HLMP-2450/2735/2755/2770 Annunciators (.2 x .8 Yellow & .4 x .4 Yellow) IV Bin Category Min.Max.C13.0022.00D18.0033.00E27.0050.00F40.5081.00G65.60131.20HLMP-2785 Annunciators (.4 x .8 Yellow)IV Bin Category Min.Max.C26.0044.40D36.0066.00E54.0099.00F81.00162.00G131.40262.80HLMP-2500/2800/2820 Annunciators (.2 x .4 Yellow)IV Bin Category Min.Max.C 5.6010.20D8.4015.30E12.6023.10F18.9037.80G30.6061.20H49.5097.90I80.10158.40HLMP-2550/2835/2855/2870 Annunciators (.2 x .8/.4 x .4 Green) IV Bin Category Min.Max.C11.3020.60D17.0031.00E25.4046.50F38.1076.20G61.60123.20H99.81197.67I161.73320.21HLMP-2885 Annunciators (.4 x .8 Green)IV Bin Category Min.Max.C22.2040.80D33.4061.20E50.1091.90F75.10150.30G121.10242.20H196.10383.50I313.70613.60HLMP-2950 Bi-Color Annunciators (.4 x .4 HER/Yellow) IV Bin Category Min.Max.Red Iv CategoriesC11.3020.60D17.0031.00E25.4046.50F38.1076.20G61.60123.20Yellow Iv CategoriesC13.0022.00D18.0033.00E27.0050.00F40.5081.00G65.60131.20HLMP-2965 Bi-Color Annunciators (.4 x .4/.2 x .8 HER/Green) IV Bin Category Min.Max.Red Iv CategoriesD19.7036.10E29.6054.20F44.9088.80G71.90143.80Green Iv CategoriesB7.5013.90C11.3020.60D17.0031.00E25.4046.50F38.1076.20G61.60123.20H100.00200.00Notes:1. Minimum category D for LPE Green (-2965).2. In green mode, the devices are to be color binned into standard color bins, perTable 2. (-2685).Color CategoriesNote:All categories are established for classification of products. Products may not be available in all categories. Please contact your local Agilent representatives for further clarification/information.I AVG I v TIME AVG =I TESTwhere:I TEST =3 mA for AlGaAs Red(HLMP-X000 series)20 mA for HER,Yellow and Green (HLMP-2XXX series)Example:For HLMP-2735 series ηI PEAK = 1.18 at I PEAK = 48 mA12 mA I v TIME AVG =20 mA= 25 mcd[][]ElectricalThese light bars are composed of two, four, or eight light emitting diodes, with the light from each LED optically scattered to form an evenly illuminated light emitting surface.The anode and cathode of each LED is brought out by separate pins. This universal pinoutarrangement allows the LEDs to be connected in three possible configurations: parallel, series, or series parallel. The typical forward voltage values can be scaled from Figures 4 and 9.These values should be used to calculate the current limiting resistor value and typical power consumption. Expected maximum V F values for driver circuit design and maximum power dissipation,may be calculated using the following V F MAX models:AlGaAs Red HLCP-X100 series V F MAX = 1.8 V + I Peak (20 Ω)For: I Peak ≤ 20 mAV F MAX = 2.0 V + I Peak (10 Ω)For: 20 mA ≤ I Peak ≤ 45 mA HER (HLMP-2300/2600/2900),Yellow (HLMP-2400/2700/2900)and Green (HLMP-2500/2800/2900) seriesV F MAX = 1.6 + I Peak (50 Ω)For: 5 mA ≤ I Peak ≤ 20 mA V F MAX = 1.8 + I Peak (40 Ω)For: I Peak ≥ 20 mAThe maximum power dissipation can be calculated for any pulsed or DC drive condition. For DC operation, the maximum powerdissipation is the product of the maximum forward voltage and the maximum forward current. For pulsed operation, the maximum power dissipation is the product of the maximum forward voltage at the peak forward current times the maximum average forward current. Maximum allowable power dissipation for any given ambient temperature and thermal resistance (R θJ-A ) can be deter-mined by using Figure 2 or 7. The solid line in Figure 2 or 7 (R θJ-A of 600/538 C/W) represents a typical thermal resistance of a device socketed in a printed circuitboard. The dashed lines represent achievable thermal resistances that can be obtained through improved thermal design. Once the maximum allowable power dissipation is determined, the maximum pulsed or DC forward current can be calculated.OpticalSize of Light Surface Area Emitting Area Sq. Metres Sq. Feet 8.89 mm x 8.89 mm 67.74 x 10–6729.16 x 10–68.89 mm x 3.81 mm 33.87 x 10–6364.58 x 10–68.89 mm x 19.05 mm 135.48 x 10–61458.32 x 10–63.81 mm x 19.05 mm72.85 x 10–6781.25 x 10–6The radiation pattern for these light bar devices is approximately Lambertian. The luminoussterance may be calculated using one of the two following formulas:I v (cd)L v (cd/m 2) =A (m 2)πI v (cd)L v (footlamberts) =A (ft 2)Refresh rates of 1 kHz or faster provide the most efficientoperation resulting in the maxi-mum possible time average luminous intensity.The time average luminousintensity may be calculated using the relative efficiency character-istic of Figure 3 or 8, ηI PEAK , and adjusted for operating ambient temperature. The time average luminous intensity at T A = 25°C is calculated as follows:(ηI PEAK ) (I v Data Sheet)(1.18) (35 mcd)The time average luminous intensity may be adjusted for operating ambient temperature by the following exponential equation:I v (T A) = I V (25°C)e[K (T –25°C)]Color KAlGaAs Red–0.0095/°CHER–0.0131/°C Yellow–0.0112/°C Green–0.0104/°CExample:I v (80°C) = (25 mcd)e[-0.0112 (80-25)] = 14 mcd.MechanicalThese light bar devices may beoperated in ambient temperaturesabove +60°C without deratingwhen installed in a PC boardconfiguration that provides athermal resistance pin to ambientvalue less than 280°C/W/LED. SeeFigure 2 or 7 to determine themaximum allowed thermalresistance for the PC board,RθPC-A, which will permitnonderated operation in a givenambient temperature.To optimize device opticalperformance, specially developedplastics are used which restrictthe solvents that may be used forcleaning. It is recommended thatonly mixtures of Freon (F113)and alcohol be used for vaporcleaning processes, with animmersion time in the vapors ofless than two (2) minutesmaximum. Some suggested vaporcleaning solvents are Freon TE,Genesolv DES, Arklone A or K. A60°C (140°F) water cleaningprocess may also be used, whichincludes a neutralizer rinse (3%ammonia solution or equivalent),a surfactant rinse (1% detergentsolution or equivalent), a hotwater rinse and a thorough airdry. Room temperature cleaningmay be accomplished with FreonT-E35 or T-P35, Ethanol,Isopropanol or water with a milddetergent.For further information onsoldering LEDs please refer toApplication Note 1027.A/semiconductorsFor product information and a complete list ofdistributors, please go to our web site.For technical assistance call:Americas/Canada: +1 (800) 235-0312 or(916) 788-6763Europe: +49 (0) 6441 92460China: 10800 650 0017Hong Kong: (+65) 6756 2394India, Australia, New Zealand: (+65) 6755 1939Japan: (+81 3) 3335-8152 (Domestic/Interna-tional), or 0120-61-1280 (Domestic Only)Korea: (+65) 6755 1989Singapore, Malaysia, Vietnam, Thailand,Philippines, Indonesia: (+65) 6755 2044Taiwan: (+65) 6755 1843Data subject to change.Copyright © 2004 Agilent Technologies, Inc.Obsoletes 5962-7197EJuly 8, 20045988-2221EN。
Dupline-Online程式控制器說明書说明书
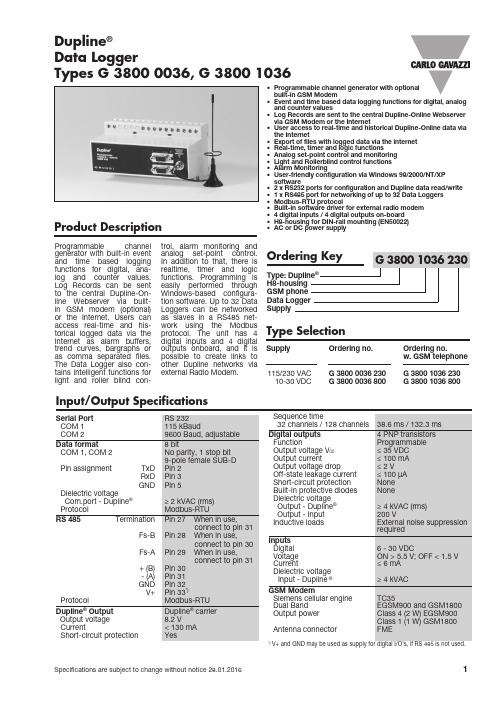
Product De s crip t ion• Programmable channel generator with optional built-in GSM Modem• Event and time based data logging functions for digital, analog and counter values• Log Records are sent to the central Dupline-Online Webserver via GSM Modem or the Internet• User access to real-time and historical Dupline-Online data via the Internet• Export of files with logged data via the internet • Real-time, timer and logic functions• Analog set-point control and monitoring • Light and Rollerblind control functions • Alarm Monitoring• User-friendly configuration via Windows 98/2000/NT/XP software• 2 x RS232 ports for configuration and Dupline data read/write • 1 x RS485 port for networking of up to 32 Data Loggers • Modbus-RTU protocol• Built-in software driver for external radio modem • 4 digital inputs / 4 digital outputs on-board • H8-housing for DIN-rail mounting (EN50022)• AC or DC power supplyProgrammable channel generator with built-in event and time based logging functions for digital, ana-log and counter values. Log Records can be sent to the central Dupline-On-line Webserver via built-in GSM modem (optional) or the Internet. Users can access real-time and his-torical logged data via the Internet as alarm buffers, trend curves, bargraphs or as comma separated files. The Data Logger also con-tains intelligent functions for light and roller blind con-trol, alarm monitoring andIn addition to that, there isrealtime, timer and logic functions. Programming isWindows-based configura-tion software. Up to 32 Data Loggers can be networked as slaves in a RS485 net-work using the Modbusprotocol. The unit has 4 digital inputs and 4 digitaloutputs onboard, and it is possible to create links to other Dupline networks via external Radio Modem.Input/Output Spe c i f i c a t ionsSupplyOrdering no. Ordering no.w. GSM telephone 115/230 VAC G 3800 0036 230 G 3800 1036 230 10-30 VDC G 3800 0036 800 G 3800 1036 800Type Selection Data LoggerTypes G 3800 0036, G 3800 1036Dupline ®G 3800 0036, G 3800 1036Ge ne ral Spe c i f i c a t ions Wiring DiagramsSupply Spe c i f i c a t ionsSupply Spe c i f i c a t ions (cont.)Power dissipation G3******* ≤ 6 W G3******* ≤ 7 WInrush current1 A Rated impulse withstand volt. 800 VDielectric voltageSupply - Dupline ® 500 V Supply - Output 200 VG 3800 0036, G 3800 1036 Mode of OperationLogging functions to Dup-line-OnlineThe G3800x036 Data Logger is a programmable channel gen-erator, which can perform event and time based logging func-tions. Digital signals changing state and analog signals cross-ing a set-point are recorded as events, while analog sig-nals and counter values are logged in regular user-defined time intervals. All Log Rec-ords include the address and description of the signal, and a time and date tag. Logged data are stored in non-volatile mem-ory and are simultaneously sent to the central Dupline-Online Webserver via GSM modem or the Internet. E ach Data Logger has its own unique ID-code that enables the central serv-er to uniquely identify where a log record is coming from and thereby save it at the correct position in the database.If Log Record transmission via the Internet is desired, an external pre-configured RS232-E thernet converter is required ( type E THCONV1).A Data Logger using Internet transmission will continue to re-transmit the Log Record every minute over a 24 hour period until an acknowledge from the central server is received. The data telegrams are encrypted to ensure safe transmission via the Internet.A Data Logger using GSM transmission will continue to re-send the Log Record as an SMS message until the GSM provider returns with an acknowledge that the SMS has been received. The cen-tral server is checking the telephone number of every received SMS data telegram to ensure safe transmission.Users can access real-time and historical logged data via the Internet as alarm buffers, trend curves, bargraphs or as comma separated files. Since data is stored in a central serv-er shared by multiple users with individual usernames and passwords allowing access to own data, there is no need to invest in new IT equipment. Any PC with an Internet connection and a standard browser can be used for data access. The cen-tral server is well-protected by a heavy-duty firewall and data back-up is performed on a daily basis to ensure data preserva-tion.Intelligent functionsThe Data Logger is alsoequipped with intelligent func-tions for lighting control, rollerblind control, temperaturecontrol and alarm monitoring.In addition to that the unit canbe configured to perform real-time, logic and timer functions.The windows based config-uration software is extremelyeasy to use due to the pre-pro-grammed functions.Data Logger configurationThe Data Logger is as defaultconfigured to operate as astandard channel generatorwithout logging and intelligentfunctions. In order to makeuse of the intelligent func-tions the Data Logger must beconfigured by means of theuser-friendly windows-basedconfiguration software. This isincluded in the package andmust be installed on a Win95/98/2000/NT/XP PC. Whenthe configuration is complet-ed the configuration is down-loaded into the Data Logger viaCOM1 (RS232 port). The con-figuration can be saved on a fileand it is also possible to uploadthe configuration from a DataLogger.In order to register the DataLogger for Dupline-Onlineoperation on the Internet, itis necessary to upload to theCentral Server a special config-uration file created by the con-figuration software.GSM Modem OptionThe G3******* Data Loggerhas a built-in GSM Modemwhich enables transmission ofevent and/or time based Logrecords to the Central servervia SMS messages. Alterna-tively, the GSM modem can beused for monitoring and con-trol of Dupline signals via SMSmessages to/from mobile GSMtelephones. There are 3 differentways to use SMS messaging:• The Data Logger can beprogrammed to send outevent based SMS messages.The event can be a channelswitching ON or OFF, orit can be an analog signalcrossing a setpoint.• Requests for status of digitalor analog data can be sentand answered via SMS mes-sages• Status of digital channelscan be controlled by sendingcommands via SMS messa-gesIn order to make use of theGSM modem, the following isrequired:• A SIM-card with the pin-code9090 needs to be insertedinto the slot in the front ofG3*******. The SIM-cardmust be a 3V type.• A GSM antenna needs tobe connected to the FMEconnector on G3*******.If the unit is installed in ametal enclosure, the antennamust be installed outside theenclosure and connectedto the Data Logger via a cable(an antenna of this type is avail-able as accessory).An L E D in the front ofG3******* indicates the statusof the GSM modem. By emit-ting different blink patterns, theL E D indicates “connecting”,“SIMcard missing”, “No net-work found”, “No responsefrom modem”, “SMS sent” and“SMS received”.RS232 portsThe Data Logger is equippedwith two RS232 ports (COM1and COM2) which both can beused by PC’s/PLC’s for read/write of Dupline data using theModbus-RTU protocol. COM1is also used for download andupload of configuration files(created by the Data Loggerconfiguration software) and forfirmware upgrades. If trans-mission of Log Records via theInternet is desired, the exter-nal RS232-E thernet converter(E THCONV1) needs to be con-nected to COM2. The sameis the case if the option for anexternal radio modem is desired.COM1 has a fixed baudrate of115 kBaud, while the baudrateof COM2 is adjustable.RS485 portThe RS485 port enables net-working of up to 32 Data Log-gers with or without automaticdata exchange. This enablescontrol and monitoring of upto 4096 data points. If desired,it is also possible to use Ether-net instead of RS485. In thatcase each Data Logger mustbe equipped with a convert-er. A Modbus Device Addressneeds to be assigned to eachData Logger during configur-ation. In a network with auto-matic data exchange, one DataLogger is configured as RS485Master, and will thus synchron-ize a continual automatic dataexchange between all the DataLoggers. When programmingthe individual Controllers it isthen possible to make refer-ences to signals in other Dup-line networks. For example thewind speed value measured bya sensor in one Dupline net-work, can be used in the rollerblind control function in theother Dupline networks.It is also possible to make e.g.“all lights OFF” functions fora big building by activating asingle pushbutton. A PC orPLC, connected to one of theCOM-ports of the G3800X036operating as RS485 Master,gets access to all 4096 datapoints using the Modbus proto-col. Also, using the PC makes itpossible to change the config-uration in any of the Data Log-gers in the network.In a network without automaticdata exchange, a PC or PLCneed to be RS485 Master andall the Data Loggers will oper-ate as Modbus-RTU slaves.This makes it possible for thePC or PLC to read/write datafrom any of the 32 Data Log-gers. See following RS485 net-working diagram for both oper-ating modes.Modbus-RTU protocolUsing the Modbus-RTU com-mands 2 and 3 through COM1,COM2 or RS485 makes itpossible to read any type ofDupline data (digital, analink,multiplexed analog or counterdata). The status of digital andmultiplexed analog data andreset of counter can be con-trolled via the commands 5, 6and 16. See manual for mem-ory map information.SoftwareThe Dupline Data Access soft-ware package (type no. DUP-DATACC) has been developedspecifically for the MasterGenerator and the Data Logger.It contains two software toolsthat provide easy access froma PC to Dupline digital, analogand counter data via one of theRS232 or RS485 ports. TheDDE-driver provides a Dynam-ic Data xchange interface,which can be used from appli-cations that support client sideDDE such as Microsoft EXCEL.Getting Dupline data into anEXCEL spreadsheet is a simplecopy-and-paste operation. TheDupline ActiveX driver providesan ActiveX interface, which isa Microsoft standard for com-G 3800 0036, G 3800 1036Dupline-Online Principal DiagramPin Assignment, COM1, COM2RS 232 Cable2 3 511 9 79-pin male to controller 15-pin female to radio modem5 916Pin Signal2 T x D3 R x D5 Signal Ground2352359-pin maleto controller9-pin femaleto PCmunication between two prod-ucts. The Dupline ActiveX driver can be used from any develop-ment tool that supports client side ActiveX such as Microsoft Visual Basic, Delphi and Bor-land C++ builder. The Dupline Data Access package can be used on single Data Loggers as well as Data Logger networks. Radio Modem driverThe Data Logger has a built-in driver for control of an external Radio Modem, which can be used to create wireless links where no cable is available in parts of an installation. OneData Logger just be defined asthe central Data Loggers andup to 32 Data Loggers can bedefined as remote Data Log-gers. The central Data Log-ger is continuously pollingand updating the Dupline datafrom all remote Data Loggersvia the radio modem network,and in this way it makes theentire system operate as onebig Dupline network. Apartfrom increased reaction time(depending on the numberof remote Data Loggers), thesystem will operate as if it wasone Data Logger connected toall the I/O-modules with cable.The Data Logger supportsthe Radio Modem type2ASxE and all 3AS types fromthe Finnish manufacturer SATEL(www.satel.fi). Find below anapplication diagram for theRadio Modem option.Note: Analink modules cannotbe used with Radio Modems.On-board I/OThe Data Logger has 4 digit-al inputs and 4 digital outputson-board. These have beenimplemented to reduce the costof remote stations with only afew signals (e.g. in connectionwith an SMS alarm system orradio modem remote stations).The onboard I/O’s are used viathe logic functions of the DataLogger, where they can beassigned to specific channeladdresses.Mode of Operation (cont.)Radio Modem ApplicationCentral MGENRemote MGEN #2Remote MGEN #1RS232AccessoriesRS232-Ethernet Converter ETHCONV1 (preconfigured)Dupline Data Access Software DUPDATACC GSM Antenna 900 MHz ANT11 x Data Logger G 3800 x036 xxx1 x User manual MAN G 3800 0036 ENG 1 x RS 232 cableRS 232-9 M/9 F 1 x Configuration softwareSW G 38xx36Scope of SupplyANT1RS232RS232G 3800 0036, G 3800 1036Dimensions (mm)。
瑞典赫格隆液压马达资料电子版

赫格隆驱动系统以可靠、 高质量产品确保更高的性能。
2高性能的驱动系统博世力士乐的赫格隆直接驱动系统代表着无与伦比的质量和可靠的性能表现,我们用先进的技术和解决方案面对客户遇到的驱动难题。
我们全球的专业技术人员确保驱动系统值得客户的信任,同时,专业的服务工程师致力于提供全方位、及时而专业的客户服务和技术共享。
客户的需求始终是我们研发的动力。
我们注重仔细倾听客户需求,重视客户的每一条意见,并付诸实践。
高性能、灵活、 可靠和简单的交付流程始终是我们坚持的原则。
3赫格隆直接驱动系统包括:一台马达、一个驱动单元以及一套控制 与监测系统。
无论是何种应用,也无论处于何种工况,赫格隆马达 都能提供可靠的功率。
其背后的驱动力来自驱动单元,它采用一台 快速响应的液压泵,能为您的整体驱动系统提高可靠性。
控制与监 测系统是强劲动力背后的 “中枢神经” 。
得益于其灵活方便的安 装,用户只需简单操作就可方便地获得其基本功能和信息。
我们还 提供广泛系列的控制阀,既可以增添系统灵活性,又能增加系统功 能;此外,还有构成全套系统的一些附件供客户选择。
强劲动力尽 在掌握。
驱动系统无论面临的是西伯利亚的严寒还是非洲的酷热, 赫格隆直接驱动系统都能抵御任何环境和各类工业应用的挑战。
其中的驱动单元具有广泛的功率等级和配置可供选用, 并在交付之前经过功能测试。
4客户需要的不是购买某一个产品, 而是要得到能应对某种挑战的最 佳解决方案。
我们往往从仔细倾听客户需求, 利用我们长期以来积 累的经验和创造性思维, 致力于提供客户满意的解决方案。
不凡的实力苛刻的工况需要既坚固耐用又稳定可靠的产品。
但这远远不够。
产 品质量固然重要, 但并非能解决所有难题。
除了质量可靠的产品之 外, 我们拥有另外一种实力, 这种实力源自于我们对人的重视。
这 才是让我们卓尔不群的源泉所在。
经验的结晶您的需求就是我们的任务。
让用户信赖、 安心和方便是我们的准 则。
上海汉霸电火花技术规格表

要说明:HE系列大型精密电火花机床标准配件:机床垫铁、可调夹具、机床灯、过滤纸芯、液位控制器、保险芯子、工具箱、使用说明书、注油枪等。
机型:HE1、HE2、HE3、HE4、HE5(HE5-B双头)、HE6(HE6-B双头)、HE8(HE8-B双头)、HE10(HE10-B双头)详细介绍:HE系列大型精密电火花机床HE5(HE5—B双头)的技术规格:工作台尺寸(长*宽)mm 1700*1000X,Y,Z轴行程mm 1600*800*500最大电机重量kg 400最大工件重量kg 6000工作台面至电极板的最大/最小距离mm 650/1150机床重量kg 12000总输入功率KVA 18(18+18)HE系列大型精密电火花机床HE6(HE6—B双头)的技术规格:工作台尺寸(长*宽)mm 2500*1200X,Y,Z轴行程mm 2100*900*550最大电机重量kg 400最大工件重量kg 8000工作台面至电极板的最大/最小距离mm 650/1200机床重量kg 13000总输入功率KVA 18(18+18)HE系列大型精密电火花机床HE8(HE8—B双头)的技术规格:工作台尺寸(长*宽)mm 2500*1200X,Y,Z轴行程mm 2400*900*650最大电机重量kg 400最大工件重量kg 12000工作台面至电极板的最大/最小距离mm 550/1200机床重量kg 15000总输入功率KVA 18(18+18)HE系列大型精密电火花机床HE10(HE10—B双头)的技术规格:工作台尺寸(长*宽)mm 3600*1200X,Y,Z轴行程mm 3600*900*650最大电机重量kg 400最大工件重量kg 20000工作台面至电极板的最大/最小距离mm 550/1200机床重量kg 20000总输入功率KVA 18(18+18)[文档可能无法思考全面,请浏览后下载,另外祝您生活愉快,工作顺利,万事如意!]。
MB98D81223资料

2M/4M-BYTE 3 V-ONL Y FLASH MINIATURE CARDThe Fujitsu Flash Miniature cards conform to “Miniature Card Specification” pubulished by MCIF; Miniature Card Implementers Forum.The Fujitsu Flash Miniature cards are small form factor Flash memory cards targeted various markets; digital pho-tography, audio recording, hand held PCs and other small portable equipments. Miniature cards’ high performance, small size (38 mm × 33 mm × 3.5 mm), low cost and simple interface are ideal for portable applications that require high speed flash disk drives or eXecute In Place (XIP).The Flash Miniature cards are 5 V-only operational and allow the users to use as ×8 or ×16 organization on low power at high speed.•Small size: 33.0 mm (length) × 38.0 mm (width) × 3.5 mm (thickness)•+3.3 V power supply program and erase•Command control for Automated Program/Automated Erase operation•Erase Suspend Read/Program Capability•128 KB Sector Erase (at ×16 mode)•Any Combination of Sectors Erase and Full Chip Erase•Detection of completion of program/erase operation with Data# Polling or Toggle bit.•Ready/Busy Output with BUSY#•Reset Function with RESET# pin•Write protect function with WP switch•Low VCC Write Inhibit•AIS (Attribute Information Structure) is available from the address “0000H” of Lower Byte.2MB98D81123/81223-15s PACKAGEs DESCRIPTIONDIFFERENCESMB98D81123MB98D81223 Density 2 MB 4 MB Memory Device8 M bit8 M bit Quantity24 Read 1 B unit←Program 1 B unit←Chip Erase 1 MB unit 1 MB unit Sector Erase64 KB unit←Number of Sectors3264 Erase Suspend Read Yes Yes Erase Suspend Program Yes Yes Address A0 to A19A0 to A20 RESET#Yes Yes BUSY#Yes Yes(CRD-60P-M02)MB98D81123/81223-15s PAD ASSIGNMENTSPad No Symbol Pad No Symbol Pad No Symbol Pad No Symbol 1A1816N.C.31A1946CD#2A1617N.C.32A1747N.C.3A1418OE#33A1548BUSY#4N.C.19D1534A1349WE#5CEH#20D1335A1250D146A1121D1236RESET#51RFU7A922D1037A1052D118A823D938VS1#53VS2#9A624D039A754D810A525D240N.C.55D111A326D441A456D312A227N.C.42CEL#57D513A028D743A158D614N.C.29N.C.44N.C.59N.C.15N.C.30N.C.45N.C.60A20 *EX 1V CC EX 2GND EX 3CINS#* :A20 is “N.C.” for MB98D81123.34MB98D81123/81223-15s PAD DESCRIPTIONS* :T ake notice that those pads are connected internally.s PAD LOCATIONSSymbol I/O Pad Name Symbol I/O Pad Name A0 to A20I Address Input BUSY#O Ready/BusyD0 to D15I/O Data Input/Output CD#O Card Detect *CEL#I Card Enable for Lower Byte VS1#, VS2#O Voltage Sense CEH#I Card Enable for Upper Byte N.C.—Non Connection OE#I Output Enable V CC—Power SupplyWE#I Write Enable GND—GroundRESET#I Hardware Reset CINS#OCard InsertionMB98D81123/81223-15s BLOCK DIAGRAMMB98D8112356MB98D81123/81223-15 MB98D812237MB98D81123/81223-15s CHIP AND SECTOR DECODINGERASE SECTOR DECODING TABLESector Address (SA)A 19A 18A 17A 16Sector 151111Sector 141110Sector 13111Total 16 sectors per 1 chip••••••••••••••••Sector 20010Sector 10001Sector 08MB98D81123/81223-15s CHIP CONFIGURATIONThe miniature cards use 2 or 4 pcs of Flash Memory.•2 pcs of Flash Memory are operated simultaneously at 16 bit mode and even number of chip is applied to lower byte and odd number of chip is applied to upper byte.At ×8 bit mode, even address and odd address are selected with CEL# and CEH#.× 16 bit mode1CEL# = “L”, CEH# = “L”::Odd Number of Chip + Even Number of ChipOdd Number of Chip + Even Number of ChipOdd Number of Chip + Even Number of ChipOdd Number of Chip + Even Number of ChipD15 • • • • • • • • • • • • • • D0003h002h001h000h2× 8 bit modeCEL# = “H”, CEH# = “L”::odd Number of Chipodd Number of Chipodd Number of Chipodd Number of ChipD15 • • • •D8003h002h001h000hCEL# = “L”, CEH# = “H”::even Number of Chipeven Number of Chipeven Number of Chipeven Number of ChipD7 • • • • •D0003h002h001h000hMB98D81123/81223-15s FUNCTION DESCRIPTIONS1.Read ModeThe data in the common can be read with “OE#=VIL” and “WE#=VIH”. The address is selected with A0-A20.And CEL# and CEH# select output mode.2.Standby Mode–CEL# and CEH# at “VIH” place the card in Standby mode. D0-D15 are placed in a high-Z state independent of the status “OE#” and “WE#”.3.Output Disable Mode–The outputs are disabled with OE# and WE# at “VIH”. D0-D15 are placed in high-Z state.4.Write Mode1) Common Memory Write–The card is in Write mode with “OE#=VIH” and “WE# and CE#=VIL”.–Commands can be written at the Write mode.–Two types of the Write mode, “WE# control” and “CE# control” are available.mand Definitions–User can select the card operation by writing the specific address and data sequences into the command register. If incollect address and data are written or improper sequence is done, the card is reseted to read mode. See “COMMAND DEFINISION T ABLE”.6.Automated Program Capability–Programming operation can switch the data from “1” to “0”.–The data is programmed on a byte-by-byte or word-by-word basis.–The card will automatically provide adequate internally generated programming pulses and verify the pro-grammed cell margin by writing four bus cycle operation. The card returns to Common Memory Read mode automatically after the programming is completed.–Addresses are latched at falling edge of WE# or CE# and data is latched at rising edge of WE# or CE#. The fourth rising edge of WE# or CE# on the command write cycle begins programming operation.–We can check whether a byte (word) programming operation is completed successfully by sequence flug with BUSY#, Data# Polling or Toggle Bit function. See “WRITE OPERATION STATUS”.–Any commands written to the chip during programming operation will be ignored.7.Automated Chip Erase Capability–We can execute chip erase operation by 6 bus cycle operation. Chip erase does not require the user to program the chip prior to erase. Upon executing the Erase command sequence the chip automatically will program and verify the entire memory for an all zero data pattern prior to electrical erase. The system is not required to provide any controls or timing during these operations.–The card returns to Common Memory Read mode automatically after the chip erasing is completed.–Whether or not chip erase operation is completed successfully can be checked by sequence flug with BUSY#, Data# Polling or Toggle Bit function. See “WRITE OPERATION STATUS”.–Any commands written to the chip during programming operation will be ignored.910MB98D81123/81223-158.Automated Sector Erase Capability–We can execute the erase operation on any sectors by 6 bus cycle operation.–A time-out of 50 µs (typ.) from the rising edge of the last Sector Erase command will initiate the Sector Erase command(s).–Multiple sectors in a chip can be erased concurrently. This sequence is followed with writes of 30H to addresses in other sectors desired to be concurrently erased. The time between writes 30H must be less than 50 µs, otherwise that command will not be accepted. Any command other than Sector Erase or Erase Suspend during this time-out period will reset the chip to Read mode. The automated sector erase begins after the 50µs (typ.) time out from the rising edge of WE# pulse for the last Sector Erase command pulse. Whether the sector erase window is still open can be monitored with D3 and D11.–Sector Erase does not require the user to program the chip prior to erase. The chip automatically programs “0” to all memory locations in the sector(s) prior to electrical erase. The system is not required to provide any controls or timing during these operations.–The card returns to Common Memory Read mode automatically after the chip erasing is completed.–Whether or not sector erase operation is completed successfully can be checked by sequence flug with BUSY#, Data# Polling or T oggle Bit function. The sequence flug must be read from the address of the sector involved in erase operation. See “WRITE OPERATION STA TUS”.9.Erase Suspend–Erase Suspend command allows the user to interrupt the sector erase operation and then do data reads or program from or to a non-busy sector in the chip which has the sector(s) suspended erase. This command is applicable only during the sector erase operation (including the sector erase time-out period after the sector erase commands 30H) and will be ignored if written during the chip erase or programming operation. Writing this command during the time-out will result in immediate termination of the time-out period. The addresses are “don’t cares” in wrinting the Erase Suspend or Resume commands in the chip.–When the Erase Suspend command is written during a Sector Erase operation, the chip will enter the Erase Suspend Read mode. User can read the data from other sectors than those in suspention. The read operation from sectors in suspention results D2/D10 toggling. User can program to non-busy sectors by writing program commands.–A read from a sector being erase suspended may result in invalid data.10. Intelligent Identifier (ID) Read Mode–Each common memory can execute an Intelligent Identifier operation, initiated by writing Intelligent ID com-mand (90H). Following the command write, a read cycle from address 00H retrieves the manufacture code, and a read cycle from address 01H returns the device code as follows. To terminate the operation, it is necessary to write Read/Reset command.11. Hardware Reset–The Card may be reset by driving the RESET# pin to VIL. The RESET# pin must be kept High (VIL) for at least 500 ns. Any operation in progress will be terminated and the card will be reset to the read mode 20 µs after the RESET# pin is driven Low. If a hardware reset occurs during a program operation, the data at that particular location will be indeterminate.–When the RESET# pin is Low and the internal reset is complete, the Card goes to standby mode and cannot be accessed. Also, note that all the data output pins are High-Z for the duration of the RESET# pulse. Once the RESET# pin is taken high, the Card requires 500 ns of wake up time until outputs are valid for read access.–If hardware reset occurs during a erase operation, there is a possibility that the erasing sector(s) cannot be used.12. Data Protection–The card has WP (Write Protect) switch for write lockout.–To avoid initiation of a write cycle during V CC power-up and power-down, a write cycle is locked out for V CC less than 3.2 V. If V CC < V LKO, the command register is disabled and all internal program/erase circuits are disabled.Under this condition the device will reset to the read mode. Subsequent writes will be ignored until the V CC level is greater than V LKO.It is the users responsibility to ensure that the control pins are logically correct to prevent unintentional writes when V CC is above 3.2 V.–If V CC would be less than V LKO during program/erase operation, the operation will stop. And after that, the operation will not resume even if V CC returns recommended voltage level. Therefore, program command must be written again because the data on the address interrupted program operation is invalid. And regarding interrupting erase operation, there is possibility that the erasing sector(s) cannot be used.–Noise pulses of less than 5 ns (typical) on OE#, CE# or WE# will not initiate a write cycle.s FUNCTION TRUTH TABLEH : “H” level, L : “L ” level , X : “H” or “L ”Note:*1.WPSW = Write Protect Switch, NP = NON-PROTECT, P = PROTECTMode RESET#CEH#CEL#OE#WE#WPSW *1Data Input/Output D8 to D15D0 to D7Hardware ResetLX X X X P or NP High-Z High-Z Standby H H H XXP or NPHigh-Z High-Z Read (×8 bit)H L LHP or NPHigh-Z DOUT L H DOUT High-Z Read (×16 bit)L L DOUT DOUT Write (×8 bit)H L HLNPHigh-Z DIN L H DIN High-Z Write (×16 bit)L L DIN DIN Output DisableHL P High-Z High-Z L H High-Z High-Z LLHigh-ZHigh-Zs COMMAND DEFINITION TABLECommand Table for 8-bit ModeNote:CA:Chip Address.(address in chip selected by A20 for MB98D81223)SA:Sector Address (address in 64 KB selected by A16, A17, A18, A19 and A20)P A:Program Address (address to be programmed)RA:Read Address (address to be read)IA:Intelligent ID read address (Manufacture Code 0000H, Device Code 0001H)PD:Programming data RD:Read dataID:Intelligent Identifier (ID) CodeCommandBusCycle 1st Bus Write Cycle 2nd BusWrite/Read Cycle 3rd BusWrite Cycle 4th BusWrite/Read Cycle5th BusWrite Cycle 6th Bus Write CycleRead/Reset 12Write Read CAF0HRARDRead/Reset 24Write Write Write Read CAAAHCA55HCAF0HRARDRead Intelligent ID Codes 4Write Write Write Read CAAAHCA55HCA90HIAIDByte Program4Write Write Write Write CAAAHCA55HCAA0HPAPDSector Erase 6Write Write Write Write Write Write CAAAHCA55HCA80HCAAAHCA55HSA30HChip Erase 6Write Write Write Write Write Write CAAAHCA55HCA80HCAAAHCA55HCA10HSector Erase Suspend 1Write CAB0HSector Erase Resume 1Write CA30HCommand Table for 16-bit ModeNote:CA:Chip Address.(address in chip selected by A20 for MB98D81223)SA:Sector Address (address in 128 KB selected by A16, A17, A18, A19 and A20)P A:Program Address (address to be programmed)RA:Read Address (address to be read)IA:Intelligent ID read address (Manufacture Code 0000H, Device Code 0001H)PD:Programming data RD:Read dataID:Intelligent Identifier (ID) CodeCommandBusCycle 1st Bus Write Cycle 2nd BusWrite/Read Cycle 3rd BusWrite Cycle 4th BusWrite/Read Cycle5th BusWrite Cycle 6th Bus Write CycleRead/Reset 12Write Read CAF0F0HRARDRead/Reset 24Write Write Write Read CAAAAAHCA5555HCAF0F0HRARDRead Intelligent ID Codes 4Write Write Write Read CAAAAAHCA5555HCA9090HIAIDByte Program4Write Write Write Write CAAAAAHCA5555HCAA0A0HPAPDSector Erase 6Write Write Write Write Write Write CAAAAAHCA5555HCA8080HCAAAAAHCA5555HSA3030HChip Erase 6Write Write Write Write Write Write CAAAAAHCA5555HCA8080HCAAAAAHCA5555HCA1010HSector Erase Suspend 1Write CAB0B0HSector Erase Resume 1Write CA3030Hs WRITE OPERATION STATUSHardware Sequence Flag Table(1): Erase Suspended Sector (2): Non-Erase Suspended SectorNotes:*1.Performing successive read operations from the erase-suspended sector will cause D 2, D 10 to toggle.*2.Performing successive read operations from any address will cause D 6, D 14 to toggle.*3.Reading the byte address being programmed while in the erase-suspend program mode will indicatelogic ‘1’ at the D 2, D 10 bit. However, successive reads from the erase-suspended sector will cause D 2,D 10 to toggle.D7, D15 (Data# Polling)The card features Data# Polling as a method to indicate to the host that the Program/Erase Operation are in progress or completed. During the program operation an attempt to read the program address will produce the compliment of the data last written to D 7/D 15. Upon completion of the program operation, an attempt to read the program address will produce the true data last written to D 7/D 15. During the erase operation, an attempt to read the program address will produce a “0” at the D 7/D 15 output. Upon completion of the erase operation an attempt to read the device will produce a “1” at the D 7/D 15 output.For Chip Erase, the Data# Polling is valid after the rising edge of the sixth WE# pulse in the six write pulse sequence. For sector erase, the Data# Polling is valid after the last rising edge of the sector erase WE# pulse.Even if the device has completed the operation and D 7/D 15 has a valid data, the data outputs on D 0 to D 6/D 8 to D 14 may be still invalid. The valid data on D 0 to D 7/D 8 to D 15 will be read on the successive read attempts.The Data# Polling feature is only active during the programming operation, erase operation, sector erase time-out, Erase Suspend Read mode and Erase Supend Program mode.D6, D14 (Toggle Bit I)The card also features the “Toggle Bit” as a method to indicate to the host system that the Program/Erase Operation are in progress or completed.During an Program or Erase cycle, successive attempts to read (OE# or CE# toggling) data from the card will result in D 6/D 14 toggling between one and zero. Once the Program or Erase cycle is completed, D 6/D 14 will stop toggling and valid data will be read on the next successive attempts. During programming, the Toggle Bit is valid after the rising edge of the fourth WE# pulse in the four write pulse sequence. For chip erase, the Toggle Bit is valid after the rising edge of the sixth WE# pulse in the six write pulse sequence. For sector erase, the Toggle Bit is valid after the last rising edge of the sector erase WE# pulse. The Toggle Bit is also active during the sector time out.Either CE# or OE# toggling will cause the D 6/D 14 to toggle.Status D 7, D 15D 6, D 14D 5, D 13D 3, D 11D 2, D 10BUSY#InProgressProgramming D 7#, D 15#Toggle 0010Erasing0Toggle 01Toggle 0Erase Suspend Read(1)1100Toggle *11(2)Data Data Data Data Data 1Erase Suspend Program D 7#, D 15#T oggle *200*1, *30Exceeded Time LimitsProgrammingD 7#, D 15#Toggle 1010Erasing 0Toggle 11N/A 0Erase Suspend ProgramD 7#, D 15#Toggle1N/AD5, D13 (Exceeded Timing Limits)D5/D13 will indicate if the program or erase time has exceeded the specified limits (internal pulse count). Under these conditions D5/D13 will produce a “1”. This is a failure condition which indicates that the program or erase cycle was not successfully completed. Data# Polling is the only operating function of the card under this condition.If this failure condition occurs during sector erase operation, it specifies that a particular sector is bad and it may not be reused, however, other sectors are still functional and may be used for the program or erase operation.The chip must be reset to use other sectors. Write the Reset command sequence to the chip, and then execute Program or Erase command sequence. This allows the system to continue to use the other active sectors in the chip.If this failure condition occurs during the chip erase operation, it specifies that the entire chip is bad or combination of sectors are bad.If this failure condition occurs during the byte programming operation, it specifies that the entire sector containing that byte is bad and this sector may not be reused, (other sectors are still functional and can be reused).The D5/D13 failure condition may also appear if a user tries to program a non blank location without erasing. In this case the card locks out and never completes the card operation. Hence, the system never reads a valid data on D7/D15 bit and D6/D14 never stops toggling. Once the card has exceeded timing limits, the D5/D13 bit will indicate a “1”. Please note that this is not a device failure condition since the device was incorrectly used.D3, D11 (Sector Erase Timer)After the completion of the initial sector erase command sequence the sector erase time-out will begin. D3/D11 will remain low until the time-out is complete. Data# Polling and Toggle Bit are valid after the initial sector erase command sequence.If Data# Polling or the T oggle Bit indicates the card has been written with a valid erase command, D3/D11 may be used to determine if the sector erase timer window is still open. If D3/D11 is high (“1”) the internally controlled erase cycle has begun; attempts to write subsequent commands to the card will be ignored until the erase operation is completed as indicated by Data# Polling or Toggle Bit. If D3/D11 is low (“0”), the card will accept additional sector erase commands. T o insure the command has been accepted, the system software should check the status of D3/D11 prior to and following each subsequent sector erase command. If D3/D11 were high on the second status check, the command may not have been accepted.Refer to T able: Hardware Sequence Flags.D2, D10This T oggle bit, along with D6, can be used to determine whether the card is in the Erase operation or in Erase Suspend.Successive reads from the erasing sector will cause D2 to toggle during the Erase operation. If the card is in the erase-suspended-read mode, successive reads from the erase-suspended sector will cause D2 to toggle. When the card is in the erase-suspended-program mode, successive reads from the byte address of the non-erase suspended sector will indicate a logic ‘1’ at the D2 bit.D6 is different from D2 in that D6 toggles only when the standard Program or Erase, or Erase Suspend Program operation is in progress.BUSY#The card provides a BUSY# open-drain output pin as a way to indicate to the system that the program or erase operation are either in progress or has been completed. If the output is low, the card is busy with either a program or erase operation. If the card is placed in an Erase Suspend mode, the BUSY# output will be high.During programming, the BUSY# pin is driven low after the rising edge of the fourth WE# pulse. During an erase operation, the BUSY# pin is driven low after the rising edge of the sixth WE# pulse. The BUSY# pin will indicatea busy condition during the RESET# pulse.s PROGRAM/ERASE FLOWCHARTs ABSOLUTE MAXIMUM RATINGS *1*1.Permanent device damage may occur if the above Absolute Maximum Ratings are exceeded. Functionaloperation should be restricted to the conditions as detailed in the operational sections of this data sheet.Exposure to absolute maximum rating conditions for extended periods may affect device reliability.s RECOMMENDED OPERATING CONDITIONSs DC CHARACTERISTICSNotes:*1.This value does not apply to CEL#, CEH# and WE#.*2.This value does not apply to CD# and CINS#.ParameterSymbol Value Unit Supply Voltage V CC –0.5 to +5.5V Input Voltage V IN –0.5 to V CC +0.5V Output VoltageV OUT –0.5 to V CC +0.5V Temperature under Bias T A 0 to +60°C Storage T emperatureT STG–30 to +70°CParameterSymbol Min Typ Max Unit V CC Supply Voltage V CC 3.1353.30 3.465V GroundGND 0V Ambient T emperatureT A055°CParameterTest ConditionsSymbol ValueUnit MinTypMax Input Leakage Current *1V CC = V CC max., V IN = GND or V CCI LI ±10µA Output Leakage Current *2V CC = V CC max., V IN = GND or V CC I LO ±10µA Standby CurrentCEL#, CEH#,RESET# = V CC ±0.3 V I SB1—1070µA CEL#, CEH#, RESET# = V IHI SB2 5.0mA Active Read Current V CC = V CC max., CEL#, CEH# = V IL Cycle = 150 ns, I OUT = 0 mA I CC15080mA Program Current Program in progress (×16 mode)I CC260100mA Erase Current Erase in progress (×16 mode)I CC360100mA Input Low Voltage —V IL –0.5—0.6V Input High Voltage —V IH 0.7 V CC—V CC +0.5V Output Low Voltage I OL = 4.0 mA, V CC = V CC min.V OL 0.45V Output High Voltage I OH = –2.0 mA, V CC = V CC min.V OH 2.4V Low V CC Lock-out Voltage—V LKO2.3—2.5Vs CAPACITANCE (T A = 25°C, f = 1 MHz, V IN = V I/O = GND)Parameter Symbol Min Max Unit Input Capacitance *1C IN40pF I/O Capacitance *2C I/O40pF Notes:*1.This value does not apply to CEL#, CEH# and WE#.*2.This value does not apply to VS1#, CD# and CINS#.s AC TEST CONDITIONS•Input Pulse Levels: V IH = 3.0 V, V IL = 0.0 V•Input Pulse Rise and Fall Times: 5 ns•Timing Reference LevelsInput: V IL = 1.5 V, V IH = 1.5 VOutput: V OL = 1.5 V, V OH = 1.5 VOutput Load: 1TTL +100 pFs PROGRAM AND ERASE PERFORMANCESParameter Min Typ Max Unit Byte Program Time *183600µs Chip Programming Time *18.4T.B.D.Sec. Sector Erase Time *2115Sec. Program/Erase Cycles100,000Cycles Notes:*1.Excludes system-level overhead.*2.Excludes 00H programming prior to erasure.s AC CHARACTERISTICS(Recommended operating conditions unless otherwise noted.)READ CYCLE *1Parameter Symbol Min Max Unit Read Cycle Time t RC150ns Card Enable Access Time t CE150ns Address Access Time t ACC150ns Output Enable Access Time t OE75ns Card Enable to Output in Low-Z *2t CLZ5ns Card Disable to Output in High-Z *2t CHZ75ns Output Enable to Output in Low-Z *2t OLZ5ns Output Disable to Output in High-Z *2t OHZ60ns Output Hold from Address Change t OH0ns Ready Time from RESET#t RDY20µs Notes:*1.Rise/Fall time < 5 ns.*2.T ransition is measured at the point of ±500 mV from steady state voltage.PROGRAM/ERASE CYCLENotes:*1.These do not include the preprogramming time.*2.Not 100% tested.ParameterSymbol Min TypMaxUnit Write Cycle Time t WC 150ns Address Setup Time t AS 20ns Address Hold Time t AH 20ns Data Setup Time t DS 50ns Data Hold Timet DH 20ns Read Recovery Time (WE# control)t GHWL 10ns Read Recovery Time (CE# control)t GHEL 10ns Output Enable Hold Time t OEH 10ns Card Enable Setup Time t CS 0ns Card Enable Hold Time t CH 10ns Write Enable Pulse Width t WP 80ns Write Enable Setup Time t WS 0ns Write Enable Hold Time t WH 10ns Card Enable Pulse Widtht CP 100ns Duration of Byte Program Operation (/WE Control)t WHWH18µs Duration of Erase Operation *1 (/WE Control)t WHWH2115s Duration of Byte Program Operation (/CE Control)t EHEH18µs Duration of Erase Operation *1(/CE Control)t EHEH2115s V CC Setup Time *2t VCS 50µs Reset Pulse Width t RP 500ns Busy Delay Timet BSY90nss TIMING DIAGRAMREAD CYCLE TIMING DIAGRAM (WE# = V IH, RESET# = V IH)READ CYCLE TIMING DIAGRAM (continued) (WE# = V IH, RESET# = V IH)READ CYCLE TIMING DIAGRAM (continued) (WE# = V IH, RESET# = V IH)3132PROGRAM CYCLE TIMING DIAGRAM (WE# = CONTROLLED, RESET# = V IH)Notes:*1.See “FUNCTION TRUTH TABLE”.*2.PCMA1/PCMA2 = Command Address for Program, PA = Program Address, PD = Program Data. See “COMMAND DEFINITION TABLE”.PROGRAM CYCLE TIMING DIAGRAM (CE# = CONTROLLED, RESET# = V IH)Notes:*1.See “FUNCTION TRUTH TABLE”.*2.PCMA1/PCMA2 = Command Address for Program, PA = Program Address, PD = Program Data. See “COMMAND DEFINITION TABLE”.3334ERASE CYCLE TIMING DIAGRAM (WE# = CONTROLLED, RESET# = V IH)Notes:*1.See “FUNCTION TRUTH TABLE”.*MA1/CCMA2 = Command Address for Chip Erase, SCMA1/SCMA2 = Command Address for Sector Erase, SA = Sector Address. See “COMMAND DEFINITION TABLE”.ERASE CYCLE TIMING DIAGRAM (CE# = CONTROLLED, RESET# = V IH)Notes:*1.See “FUNCTION TRUTH TABLE”.*MA1/CCMA2 = Command Address for Chip Erase, SCMA1/SCMA2 = Command Address for Sector Erase, SA = Sector Address. See “COMMAND DEFINITION TABLE”.3536DATA# POLLING CYCLE TIMING DIAGRAM (RESET# = V IH)Notes:*1.VA = PA for Programming Cycle, VA = SA for Sector Erase, VA = CA for Chip Erase.*2.See “FUNCTION TRUTH TABLE”.*3.t EHEH1,2 for CE# Control.*4.Program/Erase operation is finished.。
- 1、下载文档前请自行甄别文档内容的完整性,平台不提供额外的编辑、内容补充、找答案等附加服务。
- 2、"仅部分预览"的文档,不可在线预览部分如存在完整性等问题,可反馈申请退款(可完整预览的文档不适用该条件!)。
- 3、如文档侵犯您的权益,请联系客服反馈,我们会尽快为您处理(人工客服工作时间:9:00-18:30)。
Panel and Legend Mounts for LED Light Bars Technical Data
Features
• Firmly Mounts Light Bars in Panels
• Holds Legends for Front Panel or PC Board Applications [1]
• One Piece, Snap-in Assembly • Matte Black Bezel Design Enhances Panel Appearance • Four Sizes Available
• May Be Installed in a Wide Range of Panel Thicknesses • Panel Hole Easily Punched or Milled
Description
This series of black plastic bezel mounts is designed to install Agilent Light Bars in instrument panels ranging in thickness from 1.52 mm (0.060 inch) to 3.18mm (0.125 inch). A space has been provided for holding a 0.13mm (0.005 inch) film legend over the light emitting surface of the light bar module.
Selection Guide
Panel and Legend Mount Part No.Package HLMP-HLCP-HLMP-
Panel Hole Installation Dimensions [2]
Outline
2598B1002350, 2450, 25507.62 mm (0.300 inch) x 22.86 mm (0.900 inch)B 2599A1002300, 2400, 25007.62 mm (0.300 inch) x 12.70 mm (0.500 inch)A 2898
D1002600, 2700, 280012.70 mm (0.500 inch) x 12.70 mm (0.500 inch)
C
C1002655, 2755, 2855
2950, 2965, 2980
2899E1002620, 2720, 282012.70 mm (0.500 inch) x 22.86 mm (0.900 inch)D
F1002635, 2735, 2835G1002670, 2770, 2870H1002685, 2785, 2885
Notes:
1. Application Note 1012 addresses legend fabrication options.
2. Allowed hole tolerance: +0.00 mm, -0.13 mm (+0.000 inch, -0.005 inch). Permitted radius: 1.60 mm (0.063 inch).
Corresponding Light Bar Module
Part No.
HLMP-2598HLMP-2599HLMP-2898HLMP-2899
Mounting Instructions
1. Mill[3] or punch a hole in the
panel. Deburr, but do not
chamfer, the edges of the hole.
2. Place the front of the mount
against a solid, flat surface. A
film legend with outside dimen-sions equal to the outside
dimensions of the light bar
may be placed in the mount or
on the light bar light emitting
surface. Press the light bar into the mount until the tabs snap
over the back of the light
bar[4]. When inserting the
HLMP-2898, align the notched sides of the light bar with the
mount sides which do not have the tabs. (See Figure1.)3. Applying even pressure to the
top of the mount, press the
entire assembly into the hole
from the front of the panel[5].
(See Figure2.)
Note: For thinner panels, the mount may be pressed into the panel first, then the light bar may be pressed into the mount from the back side of the panel. Suggested Punch Sources Hole punches may be ordered from one of the following sources:
Danly Machine Corporation Punchrite Division
15400 Brookpark Road Cleveland, OH 44135
(216) 267-1444
Notes:
3. A 3.18 mm (0.125 inch) diameter mill may be used.
4. Repetitve insertion of the light bar into mount may cause damage to the mount.
5. Repetitive insertion of the mount into the panel will degrade the retention force of
the mount.Ring Division
The Producto Machine Company Jamestown, NY 14701
(800) 828-2216
Porter Precision Products Company
12522 Lakeland Road
Santa Fe Springs, CA 90670 (213) 946-1531
Di-Acro Division
Houdaille Industries
800 Jefferson Street
Lake City, MN 55041
(612) 345-4571
Package Dimensions
Installation Sketches
Figure 1. Installation of a Light Bar into a Panel Mount.
Figure 2. Installation of the Light Bar/Panel Mount Assembly into a Front Panel.
元器件交易网
Data subject to change.
Copyright © 1999 Agilent Technologies, Inc.
Obsoletes 5953-0481E
5963-7038E (11/99)。